DOI:
10.1039/D4LF00101J
(Review Article)
RSC Appl. Interfaces, 2024,
1, 846-867
Synthesis, properties and biomedical perspective on vitrimers – challenges & opportunities
Received
27th March 2024
, Accepted 24th May 2024
First published on 3rd June 2024
Abstract
A novel class of crosslinked materials known as “vitrimers” has recently bridged the real-time gap between the limitations of thermoplastics and thermoset materials for great possibilities of real-world application. In this line, synthesis methods and properties for biomedical applications are rarely reviewed in the current literature. More importantly, challenges and opportunities for possible real-world biomedical applications need to be addressed to attract researchers in this emerging field. Here, we review the various synthesis methods/schemes for vitrimer preparation to achieve desired properties for specific applications. We have classified these different synthesis methods/schemes into monomers during transesterification, disulfide and imine exchanges, and discuss this focusing on recent examples. Then we discuss exchange-based properties, i.e., recyclability, healing ability, shape memory, and adhesive nature for biomedical prospects, including self-healing coatings, recyclable polymers, 3D printing, and biodegradable medical equipment.
1. Introduction
In the past 100 years, plastics have been one of the main enabling materials for real-world applications. They are more adaptable than any other kind of material, being flexible for processing in large quantities using techniques like hot pressing, extrusion, and molding. Plastics are strong materials that are frequently resistant to oxidation, biodegradation, and moisture.1 Thermoplastics and thermosets are the two primary categories of plastics. Thermoplastics like poly(ethylene terephthalate), polystyrene, polyethylene, and poly(vinyl chloride) may be molted and processed again with ease at high temperatures.2 Meanwhile, thermoset materials, i.e., urea–formaldehyde, silicone resins, epoxy resins, and melamine resins, cannot easily be recycled after being processed once. These materials have substantially excellent mechanical/thermal strength and chemical stability when matched to thermoplastic materials.2,3 By examining their chemical structures, it is possible to comprehend this distinction. Thermoplastics are made up of linear polymeric chains that are primarily held together through intermolecular forces (IMFs).4 Conversely, thermosets enable polymers to be seen as a unfied molecular unit due to their composition of 3D networks with covalent bonds that facilitate the curing process.2 Even at high temperatures, these covalent crosslinks are difficult to break, and the polymer typically breaks down before melting. While the majority of plastics cannot be easily and inexpensively converted back into their individual monomers, thermoplastics can be partially recycled using mechanical methods. However, thermosets can typically have a limited number of uses before being burned up or utilized as filler materials.1 Therefore, there is a need to develop novel plastics with strength and durability comparable to thermosets. This would be essential for a society that relies on recycling and the use of waste as a raw material for the sustainable production of other useful products like bio-plastics, bio-chemicals, fertilizers, and so on.5 The tempting possibilities they provide in many industrial applications have motivated a determined effort to fill the void between thermosets and thermoplastics over the past ten years. The goal is to create a material that can combine the benefits of both types, maintaining its robust mechanical properties over a wide range of temperatures while also exhibiting desirable traits like self-healing, recyclability, and the capacity for simple welding.5,6
The concept of self-healing is not limited in scope; rather, it encompasses a wide range of disciplines, from biomedical advancements to cutting-edge aerospace technologies.7 This idea has the fascinating potential to be used in many different types of materials, which include polymers, ceramics, etc. The potential ramifications of developing self-repairing materials are immense and promise a paradigm shift in how we view and work with materials in many different contexts.7,8 Recyclability intends to assist resource-efficient and environmentally sustainable resource management, whereas self-healing attempts to enable the seamless and potentially automatic mending of fractures and defects. Furthermore, the possibility of welding opens up new avenues for innovative design options, such as intricate shapes and adaptive assembly of various structural components. We assert that the harmonious integration of these attributes ultimately results in enhanced versatility, increased longevity, and lower costs.9
A revolutionary concept in polymer chemistry back in 2011 which sparked a remarkable surge of interest within the scientific community.10 The researchers introduced the concept of vitrimers, recalled the chemistry of crosslinked polymers, and discussed covalently adaptable networks (CANs), which exhibited fluidity resembling that of silica. Initially, the raw components, namely epoxy resin and fatty acid/anhydride, were subjected to heating and curing processes to create vitrimers.11,12 Recently, in addition to the original hydroxyl ester, many other forms of vitrimer dynamic covalent bonds, including disulfide bonds, Schiff bases, urethanes, silyl ethers, and disulfides, have been documented in the scientific literature. Despite their structural variations, both thermoset and vitrimer polymers have a crosslinked network structure. Vitrimers and thermosets differ only in that vitrimers have a crosslinked network of glass-like polymers with dynamic covalent bonds. These bonds can respond reversibly to external stimuli like heat and mechanical force, causing the crosslinking network to rearrange. This results in unique properties such as repairability, stress relaxation, shape change performance, and processability similar to thermoplastic materials.13–16
After removal of external stimuli, the glass-like polymer's dynamic covalent networks remain stable and display exceptional qualities like dimensional stability and other traits seen in thermosetting high-molecular-weight materials. A glass-like polymer to be an innovative type of polymer combines the advantages of thermoplastic and thermosetting materials.17 The reaction mechanisms for crosslinked networks with dynamic covalent connections can be categorized into two main groups: the network disintegration mechanism and the network rearrangement mechanism. As a result of this network breakdown process, the robust covalent bonds in the crosslinked polymer dissolve and reorganize over time. For example, the temperature required for its adducts' reverse breakdown is higher than that for the furan and maleimide forward addition reaction. Upon completion of the breakdown reaction, the crosslinking points within the network of these materials dissolve and yield soluble small molecules known as prepolymers. The crosslinking spots are established, and a crosslinked structure is produced when the reaction is completed. According to the mechanism of network rearrangement, the robust covalent linkages in the structure simultaneously dissociate and recombine while remaining in dynamic equilibrium. Despite the occurrence of the dynamic reaction, the crosslinked network formed through the process of network rearrangement remains intact and exhibits the properties of being insoluble and incapable of melting in inactive solvents.18 It is important to note that the vitrimer relies on the process of rearranging its network structure, and the term solid-state plasticity refers to the vitrimer's ability to exhibit flexible behavior during dynamic reactions. Vitrimers possess an extensive network of crosslinks and a constrained dynamic reaction rate. These elements hinder thermoplastic polymers from flowing at high temperatures. A few articles have also supported the pioneering assertion that fractured vitrimers utilise conventional moulding machinery. In the literature, hot pressing at high temperatures over a prolonged period is one of the most common vitrimer reprocessing methods discussed.2
Here, we elucidate how vitrimers emerge as a promising solution to address the inherent limitations posed by traditional thermosets and thermoplastics. Here, we delve into the fundamental principles underpinning the synthesis of vitrimers, highlighting the essential conditions that guide their formation. Vitrimers can also be divided into categories based on the monomers that were used to prepare them, such as transesterification, disulphide, imine linked, ester lined, and so on. Furthermore, in-depth discussion is also given regarding characteristics of vitrimers that make them particularly suitable for a wide range of biomedical applications. The tunable mechanical properties, biocompatibility, shape memory, and self-healing characteristics of vitrimers open novel avenues in various fields such as tissue engineering, drug delivery, and biodegradable implants. Nonetheless, challenges associated with achieving precise control over properties of vitrimers and their long-term stability in biological environments warrant thorough investigation. We conclude by shedding light on the prospects of vitrimers in biological applications, envisioning a transformative path toward innovative medical technologies and therapeutic interventions.
1.1 Fundamentals of vitrimers
Vitrimers and studies of polymer chemistry are a category of materials that are distinguished by their dynamic covalent connections. These bonds can be broken and then reformed without causing any significant change to the material's overall structure. The manufacture of vitrimers often involves the use of particular reactants that can undergo reversible reactions, enabling the end product to exhibit dynamic behavior. Based on the type of vitrimer being synthesized and the desired properties of the material, the reactants used in the process can be changed. A typical strategy, however, is to use multifunctional monomers with reversible covalent bonds. These monomers can undergo exchange reactions thereby allowing the material to create a dynamic network. Reactants such as multifunctional epoxy monomers are frequently utilized in the synthesis of vitrimers. In the presence of a catalyst, epoxy functional groups (–O–CH2–CH2–O–) in epoxy monomers can undergo ring-opening reactions. By introducing specific reversible bonds into the epoxy monomers, such as disulfide bonds or boronic ester bonds, the resultant vitrimer can exhibit dynamic properties.14 Additionally, in vitrimer synthesis, multifunctional thiols, amines, and acids can also be employed since they can take part in reversible reactions with the epoxy monomer. These reactants can enhance the vitrimer network's dynamic behavior by adding more reversible bonds.15 The Diels–Alder process is utilized so that reversible bonds can be incorporated into the vitrimer network. Typical Diels–Alder reactants include a diene and a dienophile. A cycloaddition reaction between the diene and dienophile may produce a reversible adduct. Diels's Alder reaction reactants include 1,5-cyclooctadiene, maleimide, and others.16 Furthermore, transalkylation processes also involve the transfer of alkyl groups between various compounds, resulting in the formation of reversible bonds. One example of a reactant used in transalkylation processes is a bisphenol monomer, which contains two phenol groups susceptible of reversible alkylation.17 In certain vitrimer systems, particular exchangeable bonds are introduced to enable the material to behave dynamically. For instance, disulfide bonds can be inserted into the vitrimer network, which can then carry out reversible disulfide exchange procedures, for example, a multifunctional epoxy monomer with disulfide bonds.18 Following the selection of the monomers, they proceed through a preparation step in which the required reactive functional groups are added via synthesis or modification. This step ensures that the monomers have the required chemical structure and reactivity for subsequent polymerization. The next crucial step is the selection of catalysts or triggers that facilitate the exchange or rearrangement of covalent bonds within the network. The choice of catalysts or triggers is dependent on the specific dynamic bond chemistry involved in the vitrimer system. Examples include the use of thermal energy in Diels–Alder processes or transition metal complexes in disulfide exchange reactions.19 An additional crucial step in the synthesis of vitrimers is the choice of appropriate solvents. Solvents are selected based on their compatibility with the monomers, catalysts, and triggers, as well as their ability to dissolve the reactants and facilitate effective mixing. The chosen solvents must be capable of dissolving the monomers and provide a favourable environment for the subsequent polymerization reactions.20 Depending on the vitrimer system, a different polymerization technique such as crosslinking processes, chain-growth polymerization, or step-growth polymerization may be used; this process results in the formation of a crosslinked vitrimer with robust covalent bonds, which contributes to the unique properties of vitrimers.21
The properties of the vitrimer may also be further improved by using processes such as annealing, curing, shaping, or other techniques, which in turn optimize the crosslinking and dynamic bond rearrangement within the vitrimer network. These steps in the processing process are essential to obtaining the necessary mechanical strength, shape-memory qualities, self-healing capacities, and other relevant properties.22 Additionally, application-specific modifications can be made to tailor the vitrimer formulation and synthesis to match the special needs for a certain application. In order to improve particular qualities or functionalities, adjusting the monomer composition and crosslink density or incorporating additives or fillers is usually applied (Fig. 1).14
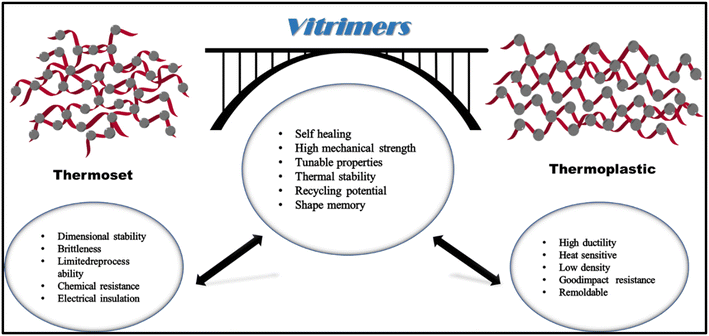 |
| Fig. 1 Vitrimers as bridge materials between thermoset and thermoplastic materials. | |
Finally, ongoing research and development efforts continue to explore new trimer-related chemistries, techniques, and applications. Investigating novel monomers, catalysts, and triggers, and developing innovative synthesis techniques are all part of this effort to expand the utility of vitrimers in various fields. The detailed explanation provides readers a comprehensive grasp of the synthesis of vitrimers and emphasizes the significance of each step in achieving the desired properties and performance of these dynamic polymer materials.23 Due to the development of new synthesis methods and novel reactants, vitrimer research is thus still growing. Depending on the desired properties of the vitrimers and the objectives of the research or application, several particular reactants may be selected. Fig. 2 illustrates the schematic diagram for the synthesis of vitrimers, which incorporates all of the aforementioned stages.
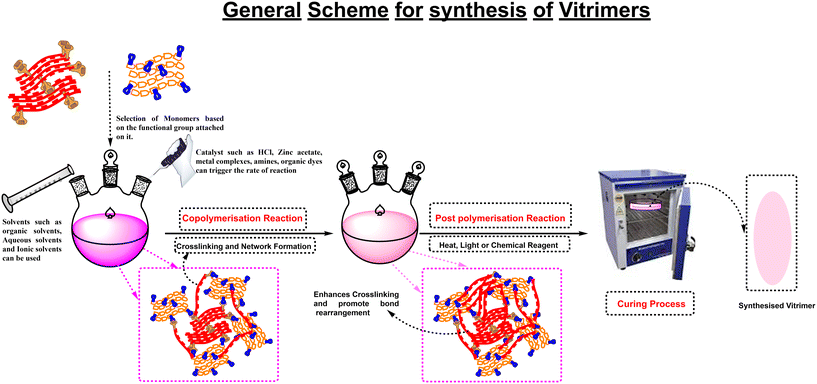 |
| Fig. 2 General scheme for vitrimer synthesis: copolymerization and post-polymerization methods followed by a curing process to obtain the synthesized product. | |
2. Synthesis methods of vitrimers based on the monomer type
Vitrimers are classified into various types. This review focuses on the classification of vitrimers according to the various monomers required for synthesis. Different forms of vitrimers are generated with various connections when a wide range of monomers are changed. According to the type of monomer employed in the synthesis, there are various types of synthesis procedures.
2.1 Direct copolymerization method
Direct copolymerization is an interesting process for the construction of dynamic networks because it is possible to obtain the desired structure in a single step with precisely defined molar mass, chemical composition, and chain architecture. However, this approach is only applicable in certain circumstances. For instance, polyolefin-based materials for the production of multifunctional polymers necessitate a balance between the chemistry of the exchangeable linkage, the reactive species, and the polymerization conditions.3 The efficiency of the catalytic system is another problem with the direct synthesis of polyolefin vitrimers. Although coordination catalysts and late transition-metal catalysts have substantially less polar functional group tolerance, the former are renowned for their incredibly high stereoselectivity, excellent control over molar mass, and exceptional catalytic activity. Additionally, being more tolerant of functional monomers, the latter group has shown considerably lower reaction yields. They use ligands based on di-imine and either Ni(II) or Pd(II) as the metal center. Additionally, copolymerizing polar monomers like acrylates with olefins invariably results in a variety of short and long branches and high yields.11
2.2 Transesterification method
Transesterification synthesis is a widely employed method for the preparation of vitrimers. This involves the exchange of ester groups within the polymer network, resulting in the dynamic covalent bond formation that imparts the material's unique properties.19 The ester groups in the polymer backbone are exchanged for new ester groups during the transesterification process. This exchange results in a rearrangement of the polymer network because older ester linkages are broken and new ones are formed.20 The reaction occurs in the presence of catalysts and at high temperatures. The transesterification synthesis of vitrimers has garnered much attention in recent years due to its ability to produce materials with unique and desirable properties. In the transesterification synthesis of vitrimers, a wide range of monomers is used to introduce the ester groups necessary for the dynamic covalent bond formation. The choice of monomers plays an important role in determining the properties and performance of the resulting vitrimer material.5
Vitrimer fabrication using dynamic transesterification (DTER) through ester bonds and hydroxy groups has been extensively studied. This is primarily due to two reasons.21 Firstly, this mechanism is applicable to various thermosetting polymers that are commercially available, particularly epoxy resins which are widely used. Secondly, the DTER reaction occurs at relatively high temperatures (>120 °C), allowing for the development of solid polymers with high temperature tolerance.22 Recently, this mechanism has been used to create many thermoplastics such as polybutylene terephthalate (PBT), polyethylene (PE), polylactic acid (PLA), etc. These studies extend the vitrimer impression to the realm of conventional plastics, opening up new possibilities for a wider range of applications.20
In addition, DTER reactions increase temperatures, modify the network structure, and cause thick and bending of materials. The rate of DTER can be analysed by measuring stress relaxation, which quantifies the decline in internal tension over time caused by a fixed deformation.10 The phenomenon of stress relaxation is commonly seen in linear polymer materials due to the movement of molecular segments. Traditional thermosetting polymers, which are made up of covalent connections that are resistant to heat, only show a restricted ability to release stress. This limited stress relaxation is influenced by physical interactions such as hydrogen bonding and physical entanglement, as well as factors like crosslink density and free volume.10,23 Polymer structures with a higher number of chemical connections, reduced crosslink density, and increased free volume demonstrate a propensity to relax at a faster rate.23,24 Some examples of monomers commonly used in transesterification-based vitrimer synthesis are indicated in Fig. 3(a).
 |
| Fig. 3 Examples of monomers used in the (a) transesterification, (b) disulfide linked, (c) imine linked, and (d) boronic exchange mechanisms for vitrimer synthesis [3–29]. | |
Lignin, which may be found in a wide variety of plant species, is the natural polymer that comes in second place in terms of abundance. In 2018, Zhang and colleagues created lignin-based vitrimer materials by reacting ozonated lignin (Oz-L) with epoxy produced from sebacic acid (Se-EP) in a catalytic amount of zinc acetate. The tensile strength, modulus, and Tg of the lignin vitrimer were all improved by increasing the lignin content. On the zinc acetate as a catalyst, transesterification exchange reactions (TERs) can be effectively generated.25 The results suggested that as the temperatures exceeded 160 °C, the lignin vitrimer displayed rapid stress relaxation in the crosslinked network, which results in superior shape-changing, malleability properties, shape-memory, self-healing, etc. Additionally, these lignin-vitrimers are used as adhesives. When these materials possessed aluminium sheets, the Se-EP/Oz-L adhesive failed cohesively, and the lap-shear strength was evaluated to be 6.3 MPa. This work presents the development of a bio-inspired vitrimer using a simple but adaptable methodology, as well as the possible application of vitrimer materials as recoverable adhesives (Fig. 4).16,25
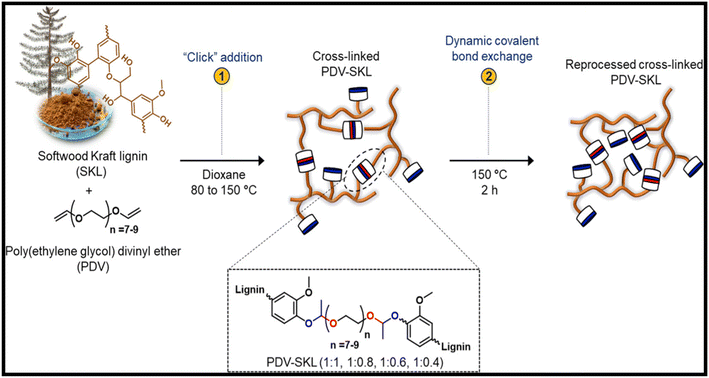 |
| Fig. 4 Schematic of lignin-based vitrimers (PDV-SKL) and their recovery through catalyst-free dynamic acetal exchange reactions.25 Adapted under a Creative Commons Attribution License 4.0 (CC BY 4.0). | |
Engineered plastics made from fossil fuels can be replaced by circular materials made from biomaterials, but industrial-scale production demands rapid and resource-efficient synthetic techniques. Here, a sequence of lignin-based vitrimers with a gel content greater than 95% are effectively made in a one-pot method and thermally activated. Softwood kraft lignin (SKL) is added to a “click” reaction to poly(ethylene glycol) divinyl ether (PDV) without using a catalyst, as shown in ref. 26. The vitrimers are formed on dynamic acetal covalent networks. By changing the lignin content from 28 to 50 weight percent, it was demonstrated that the mechanical properties of vitrimers could be altered throughout an extensive range.2 The tensile strength and elongation at break of the vitrimer with the lowest lignin content (28 wt%) were 3.3 MPa and 35%, respectively, while these values were 50.9 MPa and 1.0% for the vitrimer with the highest lignin content (50 wt%). These vitrimers also demonstrated outstanding performance as adhesives for numerous substrates such as aluminium and wood, with a lap shear test strength of 6.0 and 2.6 MPa. Additionally, over 90% of the adhesion performance of the vitrimer adhesives was preserved during recycling, contributing a promising opportunity for their use in circular materials.26
Researchers have recently begun to pay more attention to green materials because they offer promising bio-based raw materials, which can be used to make vitrimeric materials that are both affordable and sustainable. There have been recent claims of reusable and recyclable green vitrimeric mixtures. Materials like cellulose, chitosan, chitin, and other materials will not only assist in lowering the cost of the product but also make it simple to expand the uses of vitrimers in many industries.27 Zhao et al. fabricated a vitrimer from in situ polymerization of bis (6-membered cyclic carbonate) (BCC) and 1,3-propanediol (PD). Under ideal circumstances, materials based on transcarbonation exchange exhibit self-healing and reprocessing behavior, which are helpful for achieving recycling in safe environments. They also exhibit excellent mechanical properties. The vitrimer had a tensile strength of 42.7 MPa in a 1/0.5 ratio of bis (6-membered cyclic carbonate) to 1,3-propanediol (PD). Both form memory and self-healing function with 70% efficacy at 150 °C. Additionally, independently cut specimens were reconnected after being heated at 170 °C for 2 h at 4 MPa, yielding an 80% healing efficiency. Under benign conditions (I.M. HCl solution, 90 °C, 36 h), the material demonstrates complete recycling, and natural cellulose and polycarbonate may be recovered via a straightforward filtration procedure (Fig. 5).27
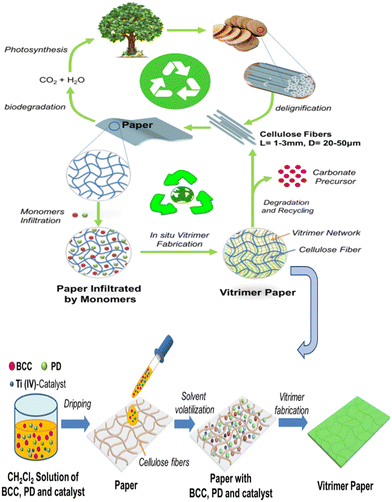 |
| Fig. 5 Schematic diagram for fabrication of a paper-reinforced polycarbonate vitrimer.27 Copyright (2019), ACS. | |
Furthermore, recently in 2019 Zhao and co-workers combined nanopapers containing cellulose nanofibrils (CNFs) with vitrimer nanoparticle colloidal dispersions (VP) for the first time to create mechanically coherent nanopaper materials. Low glass transition was achieved utilizing transesterification procedures, which were combined with hydrophobic vitrimers consisting of fatty acids and polydimethylsiloxane (PDMS).28 By increasing the vitrimer content, the total ductility is increased, and the crosslinking and transesterification reactions are activated to restore the stiffness. One of the primary issues with CNF-based materials, their hydrophilicity, can be addressed thanks to this interfacial crosslinking, which has been highlighted by mechanical tests and microscopy. The addition of a hydrophobic vitrimeric phase shields CNFs from water interactions and thereby the system's water intake is kept to a minimum and significantly increases its mechanical resistance. The synthesis route of CNF vitrimers is shown in Fig. 6 given below. This can be effectively used to produce switchable and adaptive characteristics in bioinspired nanocomposites.28
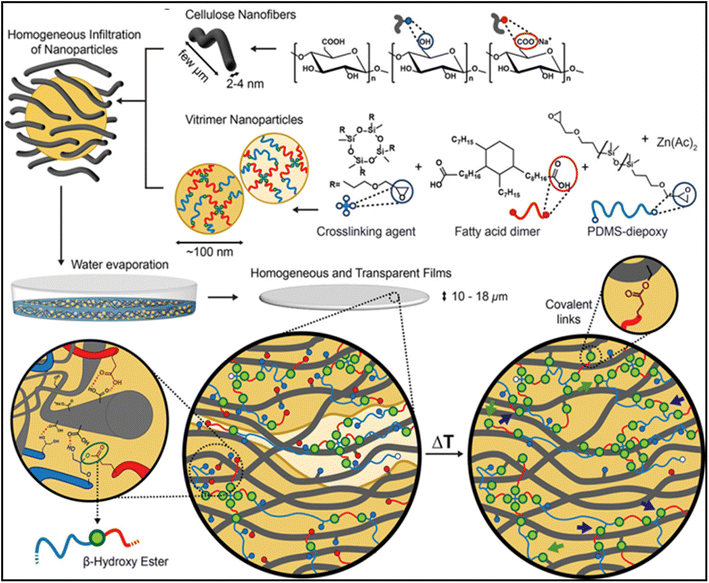 |
| Fig. 6 Synthesis route for CNF/vitrimer nanocomposites by aqueous mixing of PDMS-based low Tg vitrimer nanoparticles (VP) with CNFs.19 Copyright (2019), ACS. | |
2.3 Disulfide exchange
Disulfide exchange is a key process involved in the amalgamation of vitrimers. In disulfide exchange synthesis, sulfur atoms are exchanged across various polymer chains which results in breaking and reformation of S–S linkages. The disulfide exchange reaction in vitrimer synthesis offers several advantages.29 Firstly, it enables the material to be reshaped, allowing it to be molded or reprocessed into different shapes and forms. Secondly, it facilitates the repair of damaged or broken parts by simply heating and rejoining the fractured sections. Additionally, because the polymer may be depolymerized and reassembled into new products, the disulfide exchange reaction's reversible nature makes it possible to recycle vitrimer materials.30 In the disulfide exchange reaction, different monomers with disulfide functional groups are used to synthesize vitrimers. These monomers serve as building blocks for the polymer backbone and provide the necessary dynamic bonding sites for the exchange process. Some commonly used disulfide-containing monomers are shown in Fig. 3(b).
In recent research in 2023, bio-inspired disulfide vitrimers vitrimer made from diepoxy eugenol and cystamine via the epoxy–amine polycondensation method. To boost the crosslinking density within the material, tris(2-aminoethyl)amine (TREN) was used into the formulation in various amounts. Even though TREN decreased the amount of disulfide groups in the vitrimers, the relaxation rate was recorded at its highest at a 25% proportion. The materials that were created demonstrated high thermal stability (T1% % > 210 °C) and Tgs ranging from 74.9 °C (for the 100% Cys material) to 102.9 °C (for the 50% Cys material).31 The disulfide bonds in cystamine promoted the exchange reaction, and the addition of TREN accelerated the exchange rate. Over the course of less than 8.5 minutes, all materials rapidly release 63% of the initial stress. It is interesting to note that the material with higher relaxation rates is not necessarily the 100% Cys material. The exchange process was catalyzed by the addition of TREN and the resulting increase in tertiary amines in the crosslinked structure. The 75% Cys material, which likewise had the quickest relaxing rate of 63% in just 1.03 min, balanced the S–S bond and tertiary amine ratios. These findings imply that the vitrimers made from DEPOEU-based materials have tremendous potential for use as coatings, adhesives, and composite materials.31
Krishnakumar et al. [2020] created a multifunctional catalyst-free disulfide exchange promoted epoxy/PDMS/GO nanocomposite that offers a novel method for obtaining a lower temperature self-healing material, which is currently of focus. In this study, epoxy vitrimers containing polydimethylsiloxane (PDMS) and graphene oxide (GO) – with the help from disulfide exchange – were used. The synthesis route of the epoxy–PDMS–GO nanocomposite is shown in Fig. 7. Certain mechanical parameters of the epoxy vitrimer were examined after addition of PDMS and GO nanofillers, which results in variation in mechanical strength, strain at break, and modulus. The pristine epoxy (EP-p) specimen exhibits healing behaviour at 80° C for 5 min, whereas specimens EP-2 and EP-2-0.5 exhibit healing at 60° C for 5 min. In addition, the measured flexural modulus is useful for quantifying the mechanical characteristics and healing effectiveness due to a decline in flexural modulus after each cycle of healing. Overall, the combination of thermoset and thermoplastic properties in vitrimeric materials has contributed to polymeric research.32
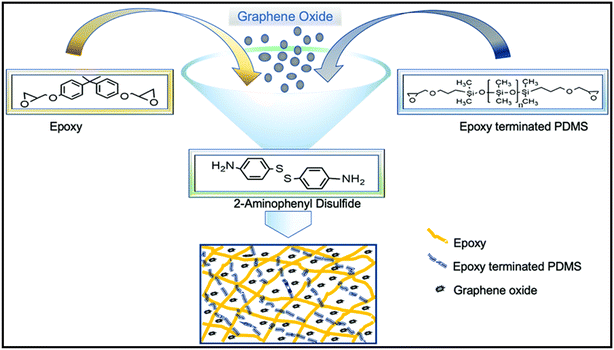 |
| Fig. 7 Synthesis method cum route for epoxy–PDMS–GO nanocomposite synthesis under certain experimental conditions.23 Adapted under a Creative Commons Attribution License 3.0 (CC BY 3.0). | |
Similar work was done in 2022 by Kim and co-workers,33 who created self-healing S-vitrimers that are epoxy-based vitrimers without the use of a catalyst. Three control experiments were conducted to look at the variables influencing self-healing behavior. Control experiments showed that despite the S-vitrimer's ability to repair itself predominantly through a disulfide exchange reaction, hydrogen bonds also play a part in the process. The results indicate that the S-vitrimer healed more effectively when treated for a longer period and at a higher temperature. The S-vitrimer showed an 80% healing efficiency, especially after 96 hours of healing at room temperature. The S-vitrimer also demonstrated an 80% healing efficiency after being exposed to 60 °C for 48 hours. Therefore, the disulfide exchange vitrimer can be demonstrated to be a self-healing matrix.
2.4 Imine exchange
Imine exchange vitrimers are a class of dynamic covalent polymers that possess the ability to undergo bond exchange reactions through imine linkages. The key feature of imine exchange vitrimers is their dynamic covalent chemistry.29 Imine linkages are formed by the reaction between an amine (NH2) and a carbonyl (C
O) functional group, resulting in a carbon–nitrogen double bond (C
N). The imine exchange reaction involves breaking and reforming these C
N bonds, enabling the material to rearrange its structure and properties under external stimuli.30 Some of the monomers used for the imine exchange reactions are shown in Fig. 3(c).
A solvent-free, bulk polymerization environmentally-friendly approach to producing a sequence of partially bio-based, resilient, and versatile poly(amide–imine) vitrimers have also been made.25 These novel poly(amide–imine) vitrimers exhibited a unique blend of remarkable mechanical properties, thermal stability, and deformation resistance, which were achieved by incorporating dynamic covalent networks of amide bonds. The abundance of H bonds and the presence of amide bonds from hexanedioxamide-diester (HDODE) impart a subtle crystalline structure to the crosslinked P(Am–In)s.34 The tensile strength and T5% of P(Am–In)s show a notable improvement when going from P(A0I3) to P(A1.5I1.5), increasing by 132% and 17.2 °C, respectively, and reaching peak values of 45.1 and 2.6 MPa and 298.0 °C. Due to the presence of H-bonds, P(A1.5I1.5) also exhibits a higher creep resistance compared to P(A0I3), with the former demonstrating zero creep at 60 °C and the latter experiencing 14% creep at a lower temperature of 30 °C. The incorporation of dynamic imine bonds shows good reprocessability, self-healing capabilities, and degradability upon the poly(amide–imine) networks. However, the recycled P(Am–In)s display unsatisfactory tensile properties, especially after the second reprocessing, imposing limitations on their potential reutilization. To address this concern, investigating the impact of crystallization on stress relaxation and exploring the synergistic interplay between amide and imine bonds hold promising avenues. This study aims to provide a ground-breaking design method for polyimine vitrimers by improving the tensile properties of recycled P(Am–In)s, paving the way for impactful practical applications.34
Furthermore, in the year 2018, Thomas Vidil and co-workers35 synthesized imine exchange poly(ethyleneimine)-based vitrimers. These include mono and diglycidyl ethers. These vitrimers are made by reacting poly(ethyleneimine) with either aldehydes or ketones. They have been shown to have good thermal stability, mechanical properties, and shape-memory properties. Another example of an imine exchange vitrimer is poly(4-vinylpyridine) in which the imine exchange reaction between poly(4-vinylpyridine) and aldehydes or ketones is reversible. Hence, the vitrimer can be melted and re-solidified without breaking down. This makes it a promising material for applications where shape-memory or self-healing properties are desired.36 In conclusion, imine exchange vitrimers represent an exciting and promising class of materials with a broad range of applications. Their dynamic covalent chemistry, self-healing, recyclability, tunable mechanical properties, and shape memory effects make them attractive for industries seeking advanced materials with improved performance and sustainability. As research in this field continues to progress, we can expect further innovations and novel applications for these intriguing materials.36
2.5 Boronic ester exchange
Boronic esters can undergo a reaction called transesterification, in which the alcohol group of one boronic ester is exchanged for the alcohol group of another boronic ester catalyzed by acids or bases. When a network of boronic esters is heated, the transesterification reaction can occur, which allows the network to be remolded or repaired. Fig. 3(d)28 shows the monomers used for the synthesis using the boron ester exchange method.37 In recent work boronic ester28 based vitrimers have been synthesised using transesterification process. The vitrimer made from diphenyl boronic acid reacted with diols resulting in a polymer with a high degree of dynamic crosslinking. This allowed the polymer to be remolded or repaired when heated. The vitrimer could be remolded at temperatures above 100 °C. They also showed that the vitrimer was repaired by heating it to 150 °C and then applying pressure. They came to a conclusion that the vitrimer was a promising new material with potential applications in a variety of fields, including adhesives, composites, and soft robotics.37 Polymers containing boron have a wide range of uses due to their distinctive characteristics. The use of reversible B–O linkage in organoboron species allows for the efficient production of several self-healing/healable and reprocessable polymers. Due to their water instability, the boron ester or boroxine linkages in polymers have a limited range of applications.38 Based on these exchange reactions, examples of bio-vitrimers are listed in Table 1.
Table 1 Classification of vitrimers on the basis of monomers and the reaction type with desired properties
S. no. |
Vitrimer type |
Monomers |
Reaction |
Properties |
References |
|
Lignin-based epoxy vitrimers |
Glycidyl etherified enzymatic hydrolysis lignin (GEL)/diglycidyl ether bisphenol A (DGEBA) with dodecanedioic acid as a curing agent in the presence of a zinc catalyst |
Transesterification reaction |
Elongation at break decreased from 301.1% to 182.6% |
39
|
Tensile strength increased from 4.9 MPa to 16.4 MPa |
Mechanical properties |
Self-healing and reprocessing |
Shape memory |
|
TOTGE–CA vitrimers |
Tung maleic triacid (TMTA) derived from tung oil (TO) was epoxidized, and TO-based triglycidyl ester TOTGE with terminal epoxy groups was obtained |
1. Esterification reaction |
Tensile strength of 47.05 ± 1.52 MPa |
40
|
2. Diels–Alder reaction |
3. Epoxidation reaction |
T
g value of 85.5 °C |
Good self-healing |
Physical recycling |
Chemical degradation |
Recycling and shape memory properties |
|
Bio-based vitrimer-like polyurethane |
Castor oil, vanillin, m-xylylene diamine and 4,4′-dicyclohexylmethane diisocyanate |
Imine exchange reaction |
Superior mechanical properties |
39
|
Good solvent resistance |
Good thermal stability |
Excellent reprocessability |
Rapidly degradable and antibacterial properties |
|
Fully bio-based epoxy vitrimers |
Ferulic acid-based hyperbranched epoxy resin |
Dynamic transesterification |
High tensile strength (126.4 MPa) |
40
|
T
g (94 °C) |
Fast stress relaxation (a relaxation time of 45 s at 140 °C) |
Retention of tensile strength (above 88.3%) upon recycling |
Excellent weldability, malleability, and programmability |
|
Acylhydrazone vitrimeric |
Glycidyl vanillin and aliphatic dihydrazides of different chain lengths |
Imine metathesis |
High Tg and fast relaxation based on poly(acylhydrazone) |
41
|
Very short relaxation times |
Good recycling and self-healing abilities |
Hydrolyzed in an acidic medium |
|
Biobased polyimine elastomeric vitrimers |
Di- and trifunctional polyetheramines and a furan-based dialdehyde |
Imine exchange reactions |
Good stability in neutral and basic solutions due to their cross-linked structures |
42
|
Completely dissolved in acidic solution due to the acid-catalyzed hydrolysis of imine bonds |
Reduce the relaxation time to improve processability and recyclability, but they also lead to a higher creep deformation, which can be a severe drawback for industrial applications |
High thermal stability, tunable mechanical properties, and interesting reprocessability |
|
Biobased epoxy vitrimer (Gte-VA) |
Glycerol triglycidyl ether (Gte) and an imine-containing hardener (VA) |
Amine–imine reversible exchange reaction |
Young's modulus of 1.6 GPa and tensile strength of 62 MPa |
43
|
Excellent reprocessability, recyclability |
UV shielding performance |
|
Polyester |
β-Activated ester-based vitrimers that can be thermally reprocessed at ∼150 °C under catalyst-free conditions are reported |
Transesterification |
Adequate tensile strength (11.3–33.0 MPa), elongation (80–290%), and resilience |
21
|
Self-healing, recycleable, and reprocessing |
|
Polylactide based vitrimers |
Hydroxyl-terminated star-shaped poly-lactide samples that were cross-linked with methylenediphenyl diisocyanate |
Transesterification |
Fractures in uniaxial tensile testing were healed by compression molding and exhibited up to 67% recovery of ultimate elongation, up to 102% recovery of tensile strength, and up to 133% recovery of tensile modulus values |
44
|
|
Catalyst-free polyhydroxyurethane vitrimers |
Six-membered cyclic carbonates and amines |
Transcarbamoylation |
Mechanical properties competitive with traditional PU thermosets, reconfigurable |
45
|
Reshaping and repair that will enhance their long-term utility |
Thermosets with outstanding properties |
|
Dioxaborolane-based polyisoprene vitrimers |
Polyisoprene was then transformed into a vitrimer by reactive extrusion, either in the presence of mono-azidoformate dioxaborolane and subsequent crosslinking with bis-dioxaborolane, or in a single step using a bis-azidoformate dioxaborolane crosslinker |
Reactive extrusion |
Show excellent creep resistance at room temperature and present good mechanical properties |
45
|
|
Reprocessable-acid degradable polycarbonate vitrimers |
Hydroxyl-functionalized polycarbonate networks that undergo the reaction at elevated temperatures in the presence of catalytic Ti(IV) alkoxides |
Transcarbonation exchange reaction |
Repairable polymers with more facile end-of-life degradation compared to other vitrimers and conventional thermosets |
46
|
|
Polyurethane vitrimers from chemical recycling of poly(carbonate) |
Hydroxyl N,N′-diphenylene-isopylidenylbiscarbamate (DP-biscarbamate), containing phenolic carbamate |
Grinding and compression molding |
Polyurethane vitrimers exhibited superb mechanical properties including 14.9 MPa and over 3000% elongation at break. Furthermore, these PU vitrimers featured low activation energies of approximately 95 kJ mol−1 and a dissociation temperature of 120 °C due to the presence of phenolic–carbamate groups from recycled moieties |
47
|
|
Vinylogous urethane/urea vitrimers derived from aromatic alcohols |
2,2,6-Trimethyl-4H-1,3-dioxin-4, bisphenol-A, resorcin, 2,7-naphthalenediol, and 1,1,1-tris(4-hydroxyphenyl)ethane are introduced as raw materials for vinylogous urethane vitrimers |
Fast condensation and substitution reactions |
Short stress-relaxation times of up to 0.7 s at 130 °C |
48
|
Activation energies of ca. 45–150 kJ mol−1 |
Reprocessing, reshaping, shape-memory and self-healing properties |
|
Polydimethylsiloxane (PDMS) |
Catalyst-free network with poly(dimethylsiloxane)etherimide (PDMS–NH2), terephthalaldehyde (TA), and tri(2-aminoethyl)amine (TREA) |
Condensation reaction |
Malleable and capable of self-healing, mechanical properties, and breaking/mold pressing cycles. Particularly, besides heating, this vitrimer-like PDMS can also be recycled and reshaped |
49
|
|
Poly(hexahydrotriazine) (PHT) |
Amines and aldehydes/ketones |
Transamidation |
Self-healing capabilities |
50
|
Thermally reprocessable |
High mechanical strength |
|
Polythiourethane vitrimers |
Polythiol and diisocyanates |
Thiol–isocyanate exchange |
Excellent self-healing capabilities, |
51
|
Enhanced mechanical properties |
Chemical resistance |
|
Polybenzoxazine |
Isosorbide and 4-hydroxy propionic acid, paraformaldehyde, mono-ethanolamine |
Solvent free Fischer esterification |
High thermal stability |
52
|
Flame retardant |
Good mechanical strength |
|
Poly oxime ester vitrimers |
Polyol, multifunctional carbonyl compound and oxime groups |
Condensation reaction |
Dynamic reversibility |
53
|
Thermal reprocessing |
Good mechanical strength |
Chemical resistance and potential for self-healing |
2.6 Vitrimers with supramolecular exchanges
Dynamic covalent exchange bonds employed in vitrimers have the ability to incorporate multiple types of dynamic exchange bonds, which can be either covalent or non-covalent. This feature provides several benefits to the network.18 These factors encompass accelerated stress relaxation, heightened resistance to creep or tension, and the ability to respond to various stimuli or even govern dynamism in a perpendicular manner. Vitrimers contain two categories of dynamic covalent exchange bonds.50
2.6.1 Vitrimers with dual dynamic covalent exchange bonds.
Dual dynamic covalent bonding in vitrimers involves the integration of multiple reversible chemical connections into the polymer network, allowing for the dynamic exchange and rearrangement of the material's structure.18 This method improves the adaptability and effectiveness of the material by merging the beneficial characteristics of several covalent connections.42 Below is an elaborate elucidation of the concept of dual dynamic covalent bonding in vitrimers. Conventional vitrimers utilize only one specific sort of covalent bond, such as transesterification or disulfide exchange, to create their dynamic properties. Dual dynamic covalent bonding expands on this idea by integrating various forms of reversible bonds into the polymer network.6,54–56 Recently, a new hardening agent was obtained by integrating disulfide and imine bonds by the Schiff base reaction (4-AFD-VAN).57 This hardener was then used to create an EP vitrimer with dual-dynamic covalent links. In comparison with the vitrimer containing a single disulfide (EVP-4-AFD), the EP vitrimer developed (EPV-4-AFD-VAN) demonstrated a reduced activation energy and a more rapid stress relaxation. In addition, EPV-4-AFD-VAN exhibited a maximum tensile strength of 71.5 MPa and maintained a recovery ratio of around 90.0% throughout the course of three cycles. EPV-4-AFD-VAN, like conventional thermoset EP, has excellent solvent resistance, high breakdown strength, and favourable dielectric characteristics.57
In other studies, aliphatic and aromatic glycidyl esters have been cured using amine-curing agents that include disulfide bonds.48,58 This process results in the creation of dynamic hydroxyl esters. In addition to the hydroxyl esters that are produced, the cross-linked network also incorporates dynamic disulfide bonds to create dual dynamic vitrimers. The produced glycidyl esters have a significantly enhanced curing reactivity as a result of the reduced activation energy. Furthermore, the process of enhancing and strengthening is accomplished by incorporating aromatic glycidyl esters into dual dynamic vitrimers, without compromising the ability to cure and reprocess the material. The dual dynamic vitrimers demonstrate superior reprocessing capabilities and distinctive rheological properties when compared to single dynamic vitrimers. This is attributed to the exchange reactions between transesterification and disulfide exchange that occur at elevated temperatures. As a result, they can be reprocessed in just 5 minutes at a temperature of 180 °C.48
2.6.2 Additional non-covalent interactions.
In addition to dual dynamic networks, vitrimers can have dynamic covalent exchange bonds and non-covalent interactions like metal coordination, pi–pi stacking or hydrogen bonding. Researchers have investigated the possibility of enhancing the creep resistance of vitrimers by incorporating some permanent cross-links into the material.59 Nevertheless, the addition of an excessive number of permanent covalent cross-links would make the polymer incapable of being recycled.60 For instance, in recent work transesterification vitrimers containing up to 40 mol% of crosslinks exhibited complete reprocessability and more than 65% resistance to creep. However, when the number of permanent crosslinks was increased to 60 mol%, the reprocessability of the material deteriorated.61
Incorporating expendable hydrogen bonds into these networks can enhance the mechanical properties of the vitrimers. In recent work, new vitrimer have been synthesised by including expendable hydrogen bonds and exchangeable β-hydroxyl ester connections into the vitrimeric network.61 The bonds and connections were formed by utilizing sebacic acid as a cross-linker with ENR, and to commence the simultaneous grafting with N-acetylglycine (NAg) by the chemical interaction between epoxy and carboxyl groups. By using different weight ratios of NAg compared to ENR, ranging up to 8 wt%, the recovery ratios of the initial mechanical parameters are remarkably high, with a value of 90%.58 In addition, stress–strain curve investigations have demonstrated that the mechanical properties of the vitrimer with 4 wt% NAg are well-preserved even after being recycled once, twice, or three times, in comparison with ENR. The exceptional outcomes of the mechanical property experiment are attributed to the sacrificial and reversible characteristics of hydrogen bonds, which effectively disperse substantial mechanical energy during stretching.58
The combination of two crosslinking systems in vitrimers will result in synergistic effects, leading to notable improvements in mechanical strength, creep resistance, and solvent resistance.18,61 In order to create a highly efficient dual cross-linked dynamic system, it is advantageous to incorporate two reversible bonds with significantly differing activation energies (active temperatures). Considering the external stimuli-responsiveness characteristics of vitrimeric materials, it would be desirable to incorporate two exchangeable bonds that individually respond to different stimuli,62 enabling the resulting vitrimers to adjust attributes in a customized manner. Furthermore, it is imperative to have a strong compatibility between the two crosslinking systems.
3. Properties of vitrimers suitable for biomedical applications
The distinct properties of vitrimers render them exceptionally valuable for a variety of biomedical applications. With their inherent biocompatibility, especially when derived from bio-based sources, vitrimers offer a safe and harmonious interaction with biological systems, making them ideal candidates for implants, drug delivery systems, and tissue engineering.63–66 Their remarkable self-healing capabilities hold significant potential in extending the lifespan of biomedical devices, as implants and other components autonomously mend minor damage over time, reducing the need for frequent replacements and associated invasive procedures. Additionally, vitrimers' recyclability addresses the issue of medical waste, enabling the creation of reusable devices that can be reprocessed multiple times and promoting sustainability within the healthcare industry.5,34
The shape memory attribute of vitrimers presents opportunities for minimally invasive interventions, where devices can be inserted in a compact form and then transform into their intended shape inside the body, reducing patient discomfort and recovery time.67 Furthermore, regulated medication administration is made possible by vitrimers' receptiveness to environmental triggers, such as changes in temperature or pH, which enhances therapeutic precision and minimizes side effects. The customizable mechanical and chemical properties of vitrimers allow for the tailored design of materials that closely match the characteristics of specific tissues, facilitating best possible cell growth and tissue regeneration in applications like tissue engineering.4,36 By integrating vitrimers into smart implants and medical devices, it is now possible to create advanced solutions that can adapt to physiological changes, offer real-time monitoring, and transmit vital patient data for more personalized and effective healthcare.37,38 This convergence of properties also holds promise for reducing the frequency of surgical interventions, particularly for materials like sutures that possess both self-healing and shape memory capabilities, thereby diminishing the risks associated with repeated surgeries. Essentially, vitrimers are versatile and innovative materials that have the potential to revolutionize many aspects of the biomedical field, from improving patient care to promoting sustainability and innovation in medical technology.21,42,50
3.1 Recycling and self-healing ability
Vitrimers show recycling and self-healing ability because they have dynamic covalent bonds. This means that the bonds in the polymer can be broken and reformed, which allows the polymer to be remolded or repaired. The dynamic covalent bonds in vitrimers are typically based on reversible reactions, such as transesterification or thiol–ene click chemistry.68 These responses are triggered by heat, light, or other stimuli. When the bonds are broken, the polymer can be remolded or repaired. Once the bonds are reformed, the polymer regains its original properties. The recycling and self-healing abilities of vitrimers make them promising materials for a variety of applications.60 For example, vitrimers could be used to make recyclable plastics, self-healing adhesives, and soft robots.69 A eugenol-based boronic ester vitrimer was made using the renewable resource diols from eugenol and a diphenyl boronic acid. Although the resulting polymer is highly crosslinked, the bonds that connect the crosslinks are dynamic. This, when heated to 150 °C, allows the polymer to remold or mend by pressing. This boronic ester vitrimer based on eugenol is a sustainable material choice because it is straightforward to recycle. This boronic ester vitrimer based on eugenol can also self-heal or recover after damage. Therefore, it is a good material for applications where durability is important.70 For instance, specific stimuli or even without them can cause the intrinsic materials to self-heal repeatedly. The self-healing material poly(propyleneoxide)-based benzoxazine with various weight ratios of acid functionalized benzoxazine. Utilizing a polydimethylsiloxane matrix containing benzoxazines, the self-healing characteristic of polybenzoxazines is based on metal–ligand interactions and additional supramolecular attraction. The same research team also discovered that polysulfone (PSU) matrices can benefit from the use of benzoxazine monomers as self-healing agents. Therefore, this biomaterial has the potential to be exploited for enhanced applications since the cytotoxicity value of the synthesized monomer was so low at low doses.71 The synthesis route is shown in Fig. 8.
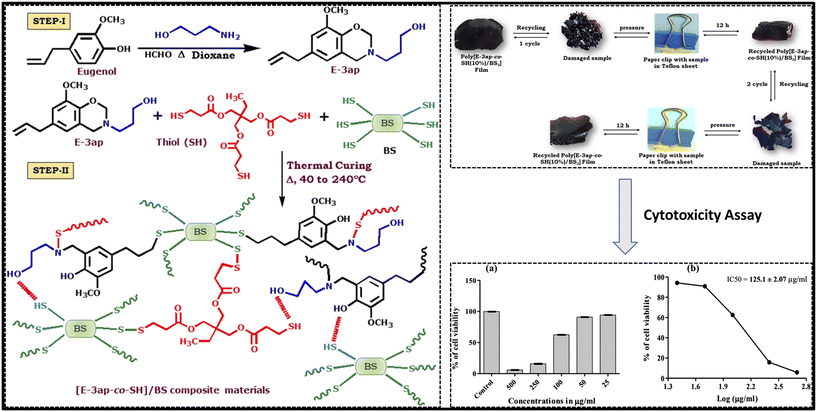 |
| Fig. 8 Graphic representation of (step-I) synthesis of the E-ap benzoxazine monomer and (step-II) thermal ring opening polymerization and crosslinking of poly[E-3ap-co-SH]/BS composite materials.59 Adapted under a Creative Commons Attribution License 3.0 (CC BY 3.0). | |
3.2 Covalent adaptable networks (CANs)
The dynamic covalent adaptive network (DCAN) is a novel paradigm that enhances thermosets' capacity for self-healing. The DCAN accomplishes this through both associative and dissociative exchange channels.2 For instance, a thermosetting material being self-healable based on the thermo-reversible Diels–Alder reaction, in which furan and maleimide moieties detach at higher temperature and then reconstitute to the bicyclic Diels–Alder-product at lower temperature.72 Numerous different chemistries that induce significant changes in the flow of the material can be used to repair thermosetting polymers. These chemicals crosslink density to decrease nonlinearly with temperature. These changes can then be reversed upon cooling, restoring the material's strength.73 An associative dynamic covalent adaptive network (ADCAN) has a more constant crosslink density during bond exchange, as demonstrated during the breaking and reformation of bonds, and this is because of the fixed crosslink density. Additionally, compared to dissociative dynamic covalent adaptive network (D.D.C.A.N) exchanges, which exhibit the greatest change in the macromolecular structure, these concurrent dynamic exchanges' macromolecular structure alters very little while their bonds are being exchanged.74
3.3 Sustainable matrix for composition
Because vitrimers have the sustainable matrix for composition characteristic, they can be made from renewable resources, such as plant-based oils or starches. This makes vitrimers sustainable choice materials, as they can be produced without the use of fossil fuels. Examples of these vitrimers include the poly(lactic acid) vitrimer, poly(ε-caprolactone) vitrimer, and so on. The benefits of using vitrimers that are made from renewable resources include: they are more sustainable than vitrimers that are made from fossil fuels. They are often biodegradable, which means that they can be broken down by natural processes. They can be produced using less energy, which reduces greenhouse gas emissions.75 The intriguing class of materials known as poly(lactic acid) (PLA) vitrimers combines the biodegradable and renewable nature of PLA with the dynamic and reprocessable characteristics of vitrimers. This is widely used for sustainable packaging materials. PLA vitrimers could be used to create flexible or rigid packaging materials with improved reprocessability and durability. This would allow for more efficient recycling and reduced environmental impact compared to traditional single-use plastics. And also in biomedical applications, PLA is already used in some medical implants due to its biocompatibility. Incorporating vitrimer properties could enhance the reprocessability and reshaping capabilities of biomedical devices, potentially reducing the need for replacements.44 In another example, poly(ε-caprolactone) PCL with the idea of three dimensional printing vitrimer ink was investigated and reported as a reprocessable and novel category of vitrimers.65 This may be due to the fused deposition modeling based three dimensional (FDM-3D) printing that is most widely available for creating a vitrimer from poly(ε-caprolactone). The synthesis, repairability and recyclability of a novel class of four dimensional printable vitrimers have been designed to meet the environmental challenges.65 In order to maintain poly(ε-caprolactone) crystallinity and maximize transesterification efficiency, the network components are precisely regulated in the report. Importantly, it has been demonstrated that the resulting urethane network–poly(ε-caprolactone) vitrimers exhibit rapid self-healing, are easy to weld, and are repeatable. The printing and the extrusion-based vitrimer are represented in Fig. 9.76
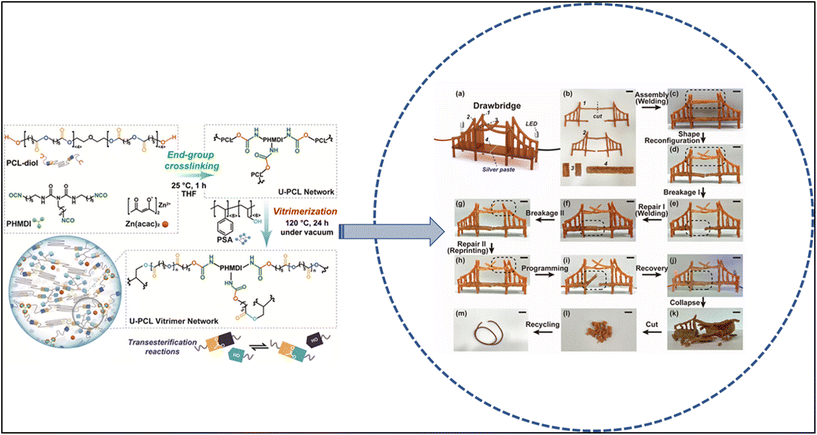 |
| Fig. 9 Schematic representation of a 4D printing process of a U-PCL vitrimer via filament extrusion and handheld FDM-based 3D printing, and its multiple functions including shape reconfiguration, self-healing, repair by welding and reprinting, and recycling.65 Adapted under a Creative Commons Attribution License 4.0 (CC BY 4.0). | |
3.4 Stimuli response
Vitrimers exhibit stimuli-responsive properties due to their dynamic covalent bond exchange behavior, which allows them to undergo reversible structural changes in response to specific external triggers or stimuli. These properties make vitrimers highly adaptable and versatile materials with a wide range of potential applications.77 Vitrimers exhibit stimuli-responsive properties due to their dynamic covalent bond exchange behavior, which allows them to undergo reversible structural changes in response to specific external triggers or stimuli. In reaction to external stimuli including temperature, light, electric or magnetic fields, pH, moisture, and chemicals, smart polymers can change their forms, dimensions, chemical compositions, and physical properties in real time. They have attracted a lot of attention due to the quickly rising demand for technology applications such as actuators, sensors, and programmable medication delivery systems. Researchers have begun to develop multi-stimuli responsive polymers (MSRPs) and multifunctional polymers (MFPs) over the past ten years.78 Both anticipate the materials' adaptability and capacity to grow in a variety of applications. Despite the fact that both fields have made considerable strides, they still have a common issue in that there are usually just two or three stimuli or functionalities available. The few exceptions are based on supramolecular chemistry or gels. In addition to being inappropriate for use as engineering materials, these materials are usually heat- or solvent-sensitive.79 Photovitrimers are vitrimers that respond to light and are used to create materials that change their properties in response to light exposure. For example, a photovitrimer is used to create a window that darkens when exposed to sunlight, while thermovitrimers respond to heat and are used to create materials whose properties alter in response to temperature changes.
3.5 Shape memory
Vitrimers show shape memory properties because of their reversible dynamic covalent bonds. These bonds allow the vitrimer chains to be rearranged under an external stimulus, which includes heat or light. Once the stimulus is removed, the vitrimer chains return to their original shape. Two external stimuli are necessary for one-way shape memory to function. Two things are necessary for any shape programming: the application of an external load and the heat–cool cycle, which are both necessary for the material's phase shifting and deformation, respectively.67 The geometry of the objects is commonly modified just from batch to batch on assembly and sorting lines. Because of their shape memory ability, vitrimers are perfect for a wide range of applications, including: surgical sutures with a heat-activated tightening mechanism, as phase shifting materials in robotics, recyclable plastics that can be returned to their original shape after being melted down, and self-healing materials that can repair themselves after damage.80,81 Vitrimers composed of bisphenol A glycidyl methacrylate (BISGMA) monomers are an example of vitrimers that exhibit shape memory properties. BISGMA-based vitrimers have a high glass transition temperature and a low melting temperature, which make them ideal for applications that require shape memory. BISGMA-based vitrimers are made up of two types of molecules: BISGMA and a reactive diluent. A crosslinking agent called BISGMA forms a network of bonds between the molecules. A chemical that can interact with BISGMA to produce dynamic covalent connections is the reactive diluent.82 When a BISGMA-based vitrimer is deformed, the dynamic covalent bonds are broken. This allows the molecules to move around and the vitrimer to change its shape. However, the dynamic covalent bonds can also reform over time, causing the vitrimer to return to its original shape. The kind of reactive diluent employed can affect the shape memory effect of vitrimers made from BISGMA. Diluents with weaker dynamic covalent bonds will reform more slowly, giving the vitrimer a longer shape memory effect. Diluents with stronger dynamic covalent bonds will reform more quickly, giving the vitrimer a shorter shape memory effect.82 The polyurethane vitrimer is yet another significant shape memory vitrimer. Polyurethane vitrimers are made up of two types of molecules: isocyanates and polyols. Isocyanates are molecules that have a reactive group called an isocyanate group. Polyols are molecules that have multiple hydroxyl groups. When isocyanates and polyols react, they form a network of bonds between the molecules.38 These bonds are dynamic covalent bonds, which means that they can be broken and reformed under different conditions. When a polyurethane vitrimer is deformed, the dynamic covalent bonds are broken. This allows the molecules to move around and the vitrimer to change shape.83
3.6 Adhesive nature
Crosslinking agents and reactive diluents are the two types of molecules that give vitrimers their sticky properties. The crosslinking agent forms a network of bonds between the molecules, while the reactive diluent can react with the crosslinking agent to form dynamic covalent bonds. The dynamic covalent bonds in a vitrimer can interact with the molecules in the other material to cause a reaction.84 This creates a strong bond between the vitrimer and other materials effectively, thereby gluing them together. The adhesive properties of vitrimers are controlled by the type of crosslinking agent and reactive diluent used. Crosslinking agents with more reactive groups will form stronger bonds, while reactive diluents with weaker dynamic covalent bonds will reform more slowly.84 For example, epoxy vitrimers are made up of epoxy resin and a reactive diluent. Epoxy resin is a crosslinking agent that forms a network of bonds between the molecules. The reactive diluent can react with the epoxy resin to form dynamic covalent bonds.85 When an epoxy vitrimer is brought into contact with another material, the dynamic covalent bonds can react with the molecules in the other material. This creates a strong bond between the epoxy vitrimer and the other material, effectively joining them together. Epoxy vitrimers have good adhesive properties and hence they are used in high-performance applications. They are also relatively easy to process, which makes them a good choice for a variety of applications.85 Another important example was polyurethane vitrimers: polyurethane vitrimers are made from isocyanates and polyols. Isocyanates are molecules that have a reactive group called an isocyanate group. Polyols are molecules that have multiple hydroxyl groups.85 When isocyanates and polyols react, they form a network of bonds between the molecules. These bonds are dynamic covalent bonds, which means that they can be broken and reformed under different conditions. When a polyurethane vitrimer is brought into contact with another material, the dynamic covalent bonds can react with the molecules in the other material. This creates a strong bond between the polyurethane vitrimer and the other material, effectively gluing them together. Polyurethane vitrimers have good adhesive properties used in soft robotics applications. They are also relatively lightweight and flexible, which makes them a good choice for these applications. The synthesis of these adhesive vitrimers is represented in Fig. 10.85Table 2 given below describes various bio-vitrimers classified on the basis of monomers required and the suitable properties associated with them.
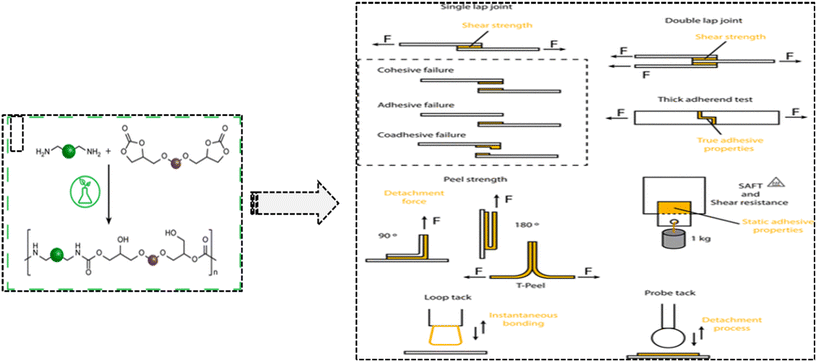 |
| Fig. 10 Schematic representation for evaluation of polyurethane vitrimers as adhesion materials for soft robotics applications.70 Adapted under a Creative Commons Attribution License 4.0 (CC BY 4.0). | |
Table 2 Different types of lab synthesised vitrimers for biomedical and other applications
S. no |
Vitrimer type |
Examples |
Applications |
Reference |
1. |
Epoxy-based vitrimers |
Diels–Alder-based epoxy vitrimers |
Adhesives, coatings, composite materials |
25
|
Anhydride-based epoxy vitrimers |
Resins, thermosetting materials |
2. |
Polyurethane vitrimers |
Diels–Alder-based polyurethane vitrimers |
Foams, coatings, flexible materials |
86
|
Disulfide-based polyurethane vitrimers |
Self-healing materials, adhesives |
3. |
Polyester vitrimers |
Dynamic ester exchange vitrimers |
Fibers, textiles, packaging |
87
|
Esterification-based vitrimers |
Films, adhesives, 3D printing |
4. |
Polyimine vitrimers |
Schiff base-based vitrimers |
Coatings, membranes, drug delivery systems |
42
|
|
Dynamic imine exchange vitrimers |
Self-healing materials, electronic encapsulation |
5. |
Polysulfide vitrimers |
Disulfide exchange-based vitrimers |
Sealants, adhesives, elastomers |
88
|
6. |
Silicon-based vitrimers |
Dynamic siloxane exchange vitrimers |
Optics, electronics, medical devices |
47
|
Sila-Michael addition vitrimers |
High-temperature applications |
7. |
Thermoplastic elastomers |
Polyolefin-based vitrimers |
Elastomers, automotive parts, consumer goods |
6, 24 |
Sulfur-containing thermoplastics |
Tires, footwear, automotive parts |
8. |
Phenolic vitrimers |
Phenolic resin-based vitrimers |
Composites, insulating materials |
47, 48 |
Reversible phenol-formaldehyde vitrimers |
Thermosetting plastics, adhesives |
9. |
Cellulose-based vitrimers |
Dynamic covalent cellulose derivatives |
Biodegradable materials, packaging |
89
|
3.7 Catalytic properity
Vitrimers possess exceptional adaptability and functionality due to their catalytic feature, which arises from their dynamic and reversible covalent bonds, having the ability to undergo significant chemical rearrangements when exposed to specific stimuli, with the help of catalysts or environmental conditions.18,90 Han et al. produced hyperbranched epoxy (HBE) prepolymers and then reacted them with succinic anhydride to create a catalyst-free epoxy vitrimer system. It has been proven that the curing process during the preparation of the cross-linked materials and the TER (thermal expansion ratio) in the final cross-linked materials occur correctly without the need for an external catalyst.52,91 They linked this behavior to the many free –OH groups in HBE, which act as both the reactive component and catalyst in both the curing and TER processes. When the temperature is higher than 120 °C, the TER is triggered to facilitate rapid stress relaxation of the cross-linked network. Furthermore, the epoxy vitrimers demonstrate glass transition temperatures (Tgs) ranging from 70 to 96 °C, exceptional resistance to high temperatures, and mechanical characteristics comparable to those of conventional epoxy materials.91
3.8 3D printers
3D printing is a highly accurate fabrication technology used to build sophisticated 3D items with intricate geometric shapes. Nevertheless, traditional 3D objects created using the layer-by-layer manufacturing approach had limited mechanical durability, hence imposing constraints on their practical application in engineering.68 The integration of 3D printing technology and vitrimers enables the creation of recyclable 3D devices that possess intricate structures and precise control over the manufacturing process. This is achieved without compromising the durability of the objects, making them suitable for widespread use in different industries such as actuator production, shape memory polymers (SMPs), and electronic/optical materials.92
Shi et al. developed a novel thermosetting vitrimer epoxy ink and a 3D printing technique capable of producing epoxy parts with intricate 3D shapes. During the initial printing phase, a thick ink is partially cured and then applied to intricate 3D structures at a higher temperature.58 This is followed by a two-step process of curing the ink in an oven. In order to undergo recycling, the printed epoxy pieces are completely dissolved in an ethylene glycol solvent within a sealed container at an elevated temperature. The polymer solution, which has been dissolved, is recycled for the subsequent printing cycle under comparable printing circumstances.58 This trial has shown that the ink possesses capability of printing up to four times while maintaining excellent printability. Furthermore, the vitrimer epoxy is suitable for repairing 3D printed objects without the need for applying pressure.58
4. Progressive aspects for diverse applications of vitrimers
In this section, we have discussed on-going research and development activities on vitrimers around the world in different fields.68 Some of the diverse applications of vitrimers are discussed below to be taken into consideration for their progressive aspects in the future:
• Materials science: to broaden the variety of uses for vitrimers in sectors like automotive and aerospace, researchers are now looking into new formulations and processing methods. Vitrimers can be reprocessed without losing their properties. They are thus a more environmentally friendly substitute for conventional materials, which are frequently difficult or impossible to recycle. They are also self-healable after being damaged. This means that they can repair themselves without human intervention. For applications involving materials exposed to harsh environments or that are vulnerable to deterioration, this feature is valuable. Vitrimers also show good adhesive properties, as discussed above. This makes them useful for applications where materials need to bond and be programmed to return to a specific shape after being deformed. This property is valuable for soft robotics and medical implants.59
• Coatings and adhesives: companies are investing in research to optimize the performance of vitrimer-based coatings and adhesives, enabling applications in areas such as corrosion protection and bonding. They are widely used in coatings and adhesives due to their self-healing properties. Vitrimers can exhibit self-healing behavior due to their reversible covalent bonds. When a coating or adhesive made from vitrimers is damaged or cracked, the dynamic bonds can rearrange and heal the material, restoring its integrity.85 This property is precious in applications where maintaining structural integrity is crucial, such as automotive coatings or aerospace adhesives. In addition, these vitrimers show improved durability. The ability of vitrimers to heal themselves leads to enhanced durability and longevity of coatings and adhesives. This is especially advantageous in environments with high mechanical stress, temperature variations, or exposure to harsh chemicals. Likewise, they have tailorable properties. Engineered vitrimers have specific properties based on the choice of monomers and cross-linkers. This allows for the customization of coatings and adhesives to meet the exact requirements of a particular application, such as desired adhesion strength, flexibility, or thermal stability.85
• Electronics: researchers in the electronics industry are integrating vitrimers into flexible and self-repairing electronic components, which could lead to advancements in wearable technology and flexible displays. They are exploring this electronic industry because they contribute towards self-healing electronics; the ability of vitrimers to undergo reversible reactions and self-healing makes them valuable for electronic components that may experience mechanical stress, wear and tear, or damage during use.6 Self-healing properties can extend the lifespan of electronic devices and reduce the need for repairs or replacements. They are good at creating flexible and stretchable electronics. Vitrimers are engineered to have flexible and stretchable properties, making them suitable for applications where conformability to irregular surfaces or mechanical flexibility is required. This is particularly relevant for wearable electronics, flexible displays, and other bendable electronic devices. An example of this is the polyurethane vitrimer.93 In order to keep their properties at high temperatures, vitrimer materials can exhibit good thermal stability, which was demonstrated by the fact that several vitrimers were thermally stable. This quality is crucial for electronic components that could produce heat while operating or be exposed to hot conditions. An example of this is the epoxy vitrimer.93 Along with this, researchers also continue to use these highly flexible and self-healing materials in the automotive industry, sports and recreation, consumer goods, and so on. Due to their capacity for self-healing, which facilitates simple recycling and reduces environmental impact in the near future, they are also being investigated for use as environmentally friendly materials.
5. Challenges and future perspectives
Presently, to the best of the authors' knowledge designing vitrimers with precise properties for specific applications is a major challenge due to poor technical understanding. This may be due to the poor availability of facts cum literature on finding the right combination of monomers, cross-linkers, and catalysts to achieve the desired performance characteristics. Therefore, more knowledge is needed on processing techniques and developing scalable and efficient processing techniques for vitrimers, especially with complex shapes and large-scale production as per the industrial need, which is a major challenge in terms of their real-world utility.94 Another challenge includes matching their standard with thermosetting materials in terms of their mechanical qualities, such as strength, stiffness, and toughness, which restricts some high-performance applications. Controlling the kinetics of the reversible reactions in vitrimers is another crucial challenge for getting the best healing and processing qualities in line with the reaction kinetics. It is a significant difficulty, though, to balance the pace of the dynamic bonding and debonding processes.83
Nevertheless, challenges like optimizing the balance between dynamic behavior and mechanical strength, as well as fine-tuning their biocompatibility, remain areas of active exploration. Understanding the long-term stability and degradation mechanisms of vitrimer-based materials in various environments is crucial to ensuring their reliability and durability in the future. Adding exchangeable covalent connections to polymer networks is a great possibility for their use in biological applications. Leveraging their reversible bonds makes researchers envision smart drug delivery systems that respond to specific physiological cues. Additionally, the dynamic properties of vitrimers may help in the development of self-healing materials, which is essential for creating robust biomedical devices. Vitrimers are set to transform the interface between materials science and biology, providing new vistas for customized biomedical applications as scientific understanding grows and difficulties must be overcome. The process of discovering new materials and designing them could be sped up in the future by using computational techniques to forecast and optimize the properties of vitrimer materials. Industry adoption – in the near future, sectors like automotive, aerospace, electronics, and consumer goods may adopt vitrimers more frequently as research advances and production methods advance. However, there is a lot of potential for solving these problems and opening up new doors in materials science and a variety of sectors in the continuous study and development of vitrimers.
6. Conclusions
As a result of reversible chemical reactions occurring within the substance, vitrimers have special qualities that make them adaptable like polymers while retaining the structural integrity of conventional covalent bonds. On the basis of the unique properties of vitrimers, they can be explored for developing advanced formulations with enhanced features in terms of improved mechanical strength, higher thermal stability, and more tailored responsiveness. Likewise, the integration of multiple functionalities into vitrimer materials including self-sensing capabilities, electromagnetic interference shielding, and energy storage, expands their potential applications. Importantly, they draw great attention and inspiration for future work in biomedical applications as they have a great possibility of biomimetic nature and self-healing properties similar to human tissue and are highly biocompatible. Their ability to undergo controlled reshaping offers promising avenues in tissue engineering, where tailored 3D structures can facilitate cell growth and regeneration.
Conflicts of interest
There are no conflicts to declare.
Acknowledgements
We thank the Material Application Research Lab (MARL), Nano Sciences & Material, Central University of Jammu, for providing us with all the necessary facilities and permission to complete this project. Gagandeep Kaur wants to thank the Central University of Jammu for providing support in their PhD work. We want to thank Prof Seeram Ramakrishna & Dr. Sundarrajan Subramanian, NUS Centre for Nanotechnology and Sustainability, Department of Mechanical Engineering, National University of Singapore, Singapore 11758, Singapore for their contribution and help in this research work.
References
- B. R. Elling and W. R. Dichtel, Reprocessable Cross-Linked Polymer Networks: Are Associative Exchange Mechanisms Desirable?, ACS Cent. Sci., 2020, 6, 1488–1496, DOI:10.1021/acscentsci.0c00567.
- B. M. Dufort and M. W. Tibbitt, Design of moldable hydrogels for biomedical applications using dynamic covalent boronic esters, Mater. Today Chem., 2019, 12, 16–33, DOI:10.1016/j.mtchem.2018.12.001.
- G. M. Scheutz, J. J. Lessard, M. B. Sims and B. S. Sumerlin, Adaptable Crosslinks in Polymeric Materials: Resolving the Intersection of Thermoplastics and Thermosets, J. Am. Chem. Soc., 2019, 141, 16181–16196, DOI:10.1021/jacs.9b07922.
- F. Van Lijsebetten, J. O. Holloway, J. M. Winne and F. E. Du Prez, Internal catalysis for dynamic covalent chemistry applications and polymer science, Chem. Soc. Rev., 2020, 49, 8425–8438, 10.1039/d0cs00452a.
- B. Krishnakumar, A. Pucci, P. P. Wadgaonkar, I. Kumar, W. H. Binder and S. Rana, Vitrimers based on bio-derived chemicals: Overview and future prospects, Chem. Eng. J., 2022, 433, 133261, DOI:10.1016/j.cej.2021.133261.
- Y. Yang, Y. Xu, Y. Ji and Y. Wei, Functional epoxy vitrimers and composites, Prog. Mater. Sci., 2021, 120, 100710, DOI:10.1016/j.pmatsci.2020.100710.
- J. Luo, Z. Demchuk, X. Zhao, T. Saito, M. Tian, A. P. Sokolov and P. F. Cao, Elastic vitrimers: Beyond thermoplastic and thermoset elastomers, Matter, 2022, 5, 1391–1422, DOI:10.1016/j.matt.2022.04.007.
- K. L. Chong, J. C. Lai, R. A. Rahman, N. Adrus, Z. H. Al-Saffar, A. Hassan, T. H. Lim and M. U. Wahit, A review on recent approaches to sustainable bio-based epoxy vitrimer from epoxidized vegetable oils, Ind. Crops Prod., 2022, 189, 115857, DOI:10.1016/j.indcrop.2022.115857.
- M. Ahmadi, A. Hanifpour, S. Ghiassinejad and E. Van Ruymbeke, Polyolefins Vitrimers: Design Principles and Applications, Chem. Mater., 2022, 34, 10249–10271, DOI:10.1021/acs.chemmater.2c02853.
- W. Li, L. Xiao, J. Huang, Y. Wang, X. Nie and J. Chen, Bio-based epoxy vitrimer for recyclable and carbon fiber reinforced materials: Synthesis and structure-property relationship, Compos. Sci. Technol., 2022, 227, 109575, DOI:10.1016/j.compscitech.2022.109575.
- R. Xiao and W. M. Huang, Heating/Solvent Responsive Shape-Memory Polymers for Implant Biomedical Devices in Minimally Invasive Surgery: Current Status and Challenge, Macromol. Biosci., 2020, 20, 1–40, DOI:10.1002/mabi.202000108.
- R. Xiao and W. M. Huang, Heating/Solvent Responsive Shape-Memory Polymers for Implant Biomedical Devices in Minimally Invasive Surgery: Current Status and Challenge, Macromol. Biosci., 2020, 20, 1–40, DOI:10.1002/mabi.202000108.
- Y. Shi, Y. Hong, J. Hong, A. Yu, M. W. Lee, J. Lee and M. Goh, Bio-based boronic ester vitrimer for realizing sustainable and highly thermally conducting nanocomposites, Composites, Part B, 2022, 244, 110181, DOI:10.1016/j.compositesb.2022.110181.
- G. Kaur and P. Kumar, Ibuprofen tagged imine RT-COF-1 as customisable vehicle for controlled drug delivery application, Inorg. Chem. Commun., 2022, 145, 110043, DOI:10.1016/j.inoche.2022.110043.
- Z. Zhou, X. Su, J. Liu and R. Liu, Synthesis of Vanillin-Based Polyimine Vitrimers with Excellent Reprocessability, Fast Chemical Degradability, and Adhesion, ACS Appl. Polym. Mater., 2020, 2, 5716–5725, DOI:10.1021/acsapm.0c01008.
-
G. Kaur and D. Kumar, Recent trends on synthesis and application of COFs - Challenges and future perspectives, ( n.d.) Search PubMed.
- T. Liu, B. Zhao and J. Zhang, Recent development of repairable, malleable and recyclable thermosetting polymers through dynamic transesterification, Polymer, 2020, 194, 122392, DOI:10.1016/j.polymer.2020.122392.
- L. Hammer, N. J. Van Zee and R. Nicolaÿ, Dually crosslinked polymer networks incorporating dynamic covalent bonds, Polymers, 2021, 13, 1–34, DOI:10.3390/polym13030396.
- M. Giebler, C. Sperling, S. Kaiser, I. Duretek and S. Schlögl, Epoxy-anhydride vitrimers from aminoglycidyl resins with high glass transition temperature and efficient stress relaxation, Polymers, 2020, 12, 1–14, DOI:10.3390/POLYM12051148.
- W. Alabiso and S. Schlögl, The impact of vitrimers on the industry of the future: Chemistry, properties and sustainable forward-looking applications, Polymers, 2020, 12(8), 1660, DOI:10.3390/POLYM12081660.
- S. Debnath, S. Kaushal and U. Ojha, Catalyst-Free Partially Bio-Based Polyester Vitrimers, ACS Appl. Polym. Mater., 2020, 2, 1006–1013, DOI:10.1021/acsapm.0c00016.
- W. Li, L. Xiao, J. Huang, Y. Wang, X. Nie and J. Chen, Bio-based epoxy vitrimer for recyclable and carbon fiber reinforced materials: Synthesis and structure-property relationship, Compos. Sci. Technol., 2022, 227, 109575, DOI:10.1016/j.compscitech.2022.109575.
- T. Liu, B. Zhao and J. Zhang, Recent development of repairable, malleable and recyclable thermosetting polymers through dynamic transesterification, Polymer, 2020, 194, 122392, DOI:10.1016/j.polymer.2020.122392.
- M. Chen, L. Zhou, Y. Wu, X. Zhao and Y. Zhang, Rapid Stress Relaxation and Moderate Temperature of Malleability Enabled by the Synergy of Disulfide Metathesis and Carboxylate Transesterification in Epoxy Vitrimers, ACS Macro Lett., 2019, 8, 255–260, DOI:10.1021/acsmacrolett.9b00015.
- S. Zhang, T. Liu, C. Hao, L. Wang, J. Han, H. Liu and J. Zhang, Preparation of a lignin-based vitrimer material and its potential use for recoverable adhesives, Green Chem., 2018, 20, 2995–3000, 10.1039/c8gc01299g.
- A. Moreno, M. Morsali and M. H. Sipponen, Catalyst-Free Synthesis of Lignin Vitrimers with Tunable Mechanical Properties: Circular Polymers and Recoverable Adhesives, ACS Appl. Mater. Interfaces, 2021, 13, 57952–57961, DOI:10.1021/acsami.1c17412.
- W. Zhao, Z. Feng, Z. Liang, Y. Lv, F. Xiang, C. Xiong, C. Duan, L. Dai and Y. Ni, Vitrimer-Cellulose Paper Composites: A New Class of Strong, Smart, Green, and Sustainable Materials, ACS Appl. Mater. Interfaces, 2019, 11, 36090–36099, DOI:10.1021/acsami.9b11991.
- F. Lossada, J. Guo, D. Jiao, S. Groeer and E. Bourgeat-lami, Vitrimer Chemistry Meets Cellulose Nanofibrils: Bioinspired Nanopapers with High Water Resistance and Strong Adhesion, Biomacromolecules, 2018, 20, 1045–1055, DOI:10.1021/acs.biomac.8b01659.
- J. Zheng, Z. M. Png, S. H. Ng, G. X. Tham, E. Ye, S. S. Goh, X. J. Loh and Z. Li, Vitrimers: Current research trends and their emerging applications, Mater. Today, 2021, 51, 586–625, DOI:10.1016/j.mattod.2021.07.003.
- I. Azcune, A. Huegun, A. Ruiz de Luzuriaga, E. Saiz and A. Rekondo, The effect of matrix on shape properties of aromatic disulfide based epoxy vitrimers, Eur. Polym. J., 2021, 148, 110362, DOI:10.1016/j.eurpolymj.2021.110362.
- B. Krishnakumar, R. V. S. P. Sanka, W. H. Binder, V. Parthasarthy, S. Rana and N. Karak, Vitrimers: Associative dynamic covalent adaptive networks in thermoset polymers, Chem. Eng. J., 2020, 385, 123820, DOI:10.1016/j.cej.2019.123820.
- B. Krishnakumar, M. Singh, V. Parthasarthy, C. Park, N. G. Sahoo, G. J. Yun and S. Rana, Nanoscale Adv., 2020, 2726–2730, 10.1039/d0na00282h.
- G. Kim, C. Caglayan and G. J. Yun, Epoxy-Based Catalyst-Free Self-Healing Elastomers at Room Temperature Employing Aromatic Disulfide and Hydrogen Bonds, ACS Omega, 2022, 7(49), 44750–44761, DOI:10.1021/acsomega.2c04559.
- K. Liang, G. Zhang, J. Zhao, L. Shi, J. Cheng and J. Zhang, Malleable, Recyclable, and Robust Poly(amide-imine) Vitrimers Prepared through a Green Polymerization Process, ACS Sustainable Chem. Eng., 2021, 9, 5673–5683, DOI:10.1021/acssuschemeng.1c00626.
- T. Vidil, M. Cloître and F. Tournilhac, Control of Gelation and Network Properties of Cationically Copolymerized Mono- and Diglycidyl Ethers, Macromolecules, 2018, 51, 5121–5137, DOI:10.1021/acs.macromol.8b00406.
- J. Raczkowska, Y. Stetsyshyn, K. Awsiuk, J. Zemła, A. Kostruba, K. Harhay, M. Marzec, A. Bernasik, O. Lishchynskyi, H. Ohar and A. Budkowski, Temperature-responsive properties of poly(4-vinylpyridine) coatings: influence of temperature on the wettability, morphology, and protein adsorption, RSC Adv., 2016, 6(90), 87469–87477, 10.1039/C6RA07223B.
- S. L. Diemer, M. Kristensen, B. Rasmussen, S. R. Beeren and M. Pittelkow, Simultaneous disulfide and boronic acid ester exchange in dynamic combinatorial libraries, Int. J. Mol. Sci., 2015, 16, 21858–21872, DOI:10.3390/ijms160921858.
- X. Zhang, S. Wang, Z. Jiang, Y. Li and X. Jing, Boronic Ester Based Vitrimers with Enhanced Stability via Internal Boron-Nitrogen Coordination, J. Am. Chem. Soc., 2020, 142, 21852–21860, DOI:10.1021/jacs.0c10244.
- B. Xue, R. Tang, D. Xue, Y. Guan, Y. Sun, W. Zhao, J. Tan and X. Li, Sustainable alternative for bisphenol A epoxy resin high-performance and recyclable lignin-based epoxy vitrimers, Ind. Crops Prod., 2021, 168, 113583, DOI:10.1016/j.indcrop.2021.113583.
- Y. Z. Xu, P. Fu, S. L. Dai, H. B. Zhang, L. W. Bi, J. X. Jiang and Y. X. Chen, Catalyst-free self-healing fully bio-based vitrimers derived from tung oil: Strong mechanical properties, shape memory, and recyclability, Ind. Crops Prod., 2021, 171, 113978, DOI:10.1016/j.indcrop.2021.113978.
- A. Roig, A. Petrauskaité, X. Ramis, S. De la Flor and À. Serra, Synthesis and characterization of new bio-based poly(acylhydrazone) vanillin vitrimers, Polym. Chem., 2022, 13, 1510–1519, 10.1039/d1py01694f.
- R. Hajj, A. Duval, S. Dhers and L. Avérous, Network Design to Control Polyimine Vitrimer Properties: Physical Versus Chemical Approach, Macromolecules, 2020, 53, 3796–3805, DOI:10.1021/acs.macromol.0c00453.
- Y. Y. Liu, G. L. Liu, Y. D. Li, Y. Weng and J. B. Zeng, Biobased High-Performance Epoxy Vitrimer with UV Shielding for Recyclable Carbon Fiber Reinforced Composites, ACS Sustainable Chem. Eng., 2021, 9, 4638–4647, DOI:10.1021/acssuschemeng.1c00231.
- J. P. Brutman, P. A. Delgado and M. A. Hillmyer, Polylactide vitrimers – Supporting Information, ACS Macro Lett., 2014, 3, 1–10, DOI:10.1021/mz500269w.
- D. J. Fortman, J. P. Brutman, C. J. Cramer, M. A. Hillmyer and W. R. Dichtel, Mechanically Activated, Catalyst-Free Polyhydroxyurethane Vitrimers, J. Am. Chem. Soc., 2015, 137, 14019–14022, DOI:10.1021/jacs.5b08084.
- R. L. Snyder, D. J. Fortman, G. X. De Hoe, M. A. Hillmyer and W. R. Dichtel, Reprocessable Acid-Degradable Polycarbonate Vitrimers, Macromolecules, 2018, 51, 389–397, DOI:10.1021/acs.macromol.7b02299.
- S. W. Chen, J. H. Yang, Y. C. Huang, F. C. Chiu, C. H. Wu and R. J. Jeng, A facile strategy to achieve polyurethane vitrimers from chemical recycling of poly(carbonate), Chem. Eng. J. Adv., 2022, 11, 100316, DOI:10.1016/j.ceja.2022.100316.
- P. Haida, G. Signorato and V. Abetz, Blended vinylogous urethane/urea vitrimers derived from aromatic alcohols, Polym. Chem., 2022, 13, 946–958, 10.1039/d1py01237a.
- Z. Feng, B. Yu, J. Hu, H. Zuo, J. Li, H. Sun, N. Ning, M. Tian and L. Zhang, Multifunctional Vitrimer-Like Polydimethylsiloxane (PDMS): Recyclable, Self-Healable, and Water-Driven Malleable Covalent Networks Based on Dynamic Imine Bond, Ind. Eng. Chem. Res., 2019, 58, 1212–1221, DOI:10.1021/acs.iecr.8b05309.
- L. Chen, S. Zhu, I. Toendepi, Q. Jiang, Y. Wei, Y. Qiu and W. Liu, Reprocessable, reworkable, and mechanochromic polyhexahydrotriazine thermoset with multiple stimulus responsiveness, Polymers, 2020, 12, 1–13, DOI:10.3390/polym12102375.
- F. Gamardella, S. De la Flor, X. Ramis and A. Serra, Recyclable poly(thiourethane) vitrimers with high Tg. Influence of the isocyanate structure, React. Funct. Polym., 2020, 151, 104574, DOI:10.1016/j.reactfunctpolym.2020.104574.
- A. Adjaoud, L. Puchot and P. Verge, High-Tgand Degradable Isosorbide-Based Polybenzoxazine Vitrimer, ACS Sustainable Chem. Eng., 2022, 10, 594–602, DOI:10.1021/acssuschemeng.1c07093.
- C. He, S. Shi, D. Wang, B. A. Helms and T. P. Russell, Poly(oxime-ester) Vitrimers with Catalyst-Free Bond Exchange, J. Am. Chem. Soc., 2019, 141, 13753–13757, DOI:10.1021/jacs.9b06668.
- F. Directions, Controlled Drug Delivery Systems: Current Status and, Molecules, 2021, 26, 5905 CrossRef.
- K. L. Chong, J. C. Lai, R. A. Rahman, N. Adrus, Z. H. Al-Saffar, A. Hassan, T. H. Lim and M. U. Wahit, A review on recent approaches to sustainable bio-based epoxy vitrimer from epoxidized vegetable oils, Ind. Crops Prod., 2022, 189, 115857, DOI:10.1016/j.indcrop.2022.115857.
- M. Ahmadi, A. Hanifpour, S. Ghiassinejad and E. Van Ruymbeke, Polyolefins Vitrimers: Design Principles and Applications, Chem. Mater., 2022, 34, 10249–10271, DOI:10.1021/acs.chemmater.2c02853.
- J. Zheng, Z. M. Png, S. H. Ng, G. X. Tham, E. Ye, S. S. Goh, X. J. Loh and Z. Li, Vitrimers: Current research trends and their emerging applications, Mater. Today., 2021, 51, 586–625, DOI:10.1016/j.mattod.2021.07.003.
- Q. Shi, K. Yu, X. Kuang, X. Mu, C. K. Dunn, M. L. Dunn, T. Wang and H. Jerry Qi, Recyclable 3D printing of vitrimer epoxy, Mater. Horiz., 2017, 4, 598–607, 10.1039/c7mh00043j.
- J. Zheng, Z. M. Png, S. H. Ng, G. X. Tham, E. Ye, S. S. Goh, X. J. Loh and Z. Li, Vitrimers: Current research trends and their emerging applications, Mater. Today, 2021, 51, 586–625, DOI:10.1016/j.mattod.2021.07.003.
- L. Hammer, N. J. Van Zee and R. Nicolaÿ, Dually crosslinked polymer networks incorporating dynamic covalent bonds, Polymers, 2021, 13, 1–34, DOI:10.3390/polym13030396.
- G. Singh, R. Singh, N. George, G. Singh, G. Kaur Sushma, G. Kaur, H. Singh and J. Singh, ‘Click’-synthesized PET based fluorescent sensor for Hg(II), Pb(II) and Cr(III) recognition: DFT and docking studies, J. Photochem. Photobiol., A, 2023, 441, 114741, DOI:10.1016/j.jphotochem.2023.114741.
- B. P. Krishnan, K. Saalwaechter, V. K. Adjedje and W. H. Binder, Design, synthesis and characterization of vitrimers with low topology freezing transition temperature, Polymers, 2022, 14(12), 2456 CrossRef CAS PubMed.
- G. Singh, N. George, R. Singh, G. Singh, J. D. Kaur, G. Kaur, H. Singh and J. Singh, CuAAC-Derived Selective Fluorescent Probe as a Recognition Agent for Pb(II) and Hg(II): DFT and Docking Studies, ACS Omega, 2022, 7, 39159–39168, DOI:10.1021/acsomega.2c05050.
- G. Singh, N. George, R. Singh, G. Singh, J. D. Kaur, G. Kaur, H. Singh and J. Singh, CuAAC-Derived Selective Fluorescent Probe as a Recognition Agent for Pb(II) and Hg(II): DFT and Docking Studies, ACS Omega, 2022, 7, 39159–39168, DOI:10.1021/acsomega.2c05050.
- R. Balu, N. K. Dutta and N. Roy Choudhury, Plastic Waste Upcycling: A Sustainable Solution for Waste Management, Product Development, and Circular Economy, Polymers, 2022, 14(22), 4788, DOI:10.3390/polym14224788.
- F. I. Altuna, C. E. Hoppe and R. J. J. Williams, Shape memory epoxy vitrimers based on DGEBA crosslinked with dicarboxylic acids and their blends with citric acid, RSC Adv., 2016, 6(91), 88647–88655, 10.1039/C6RA18010H.
- F. Directions, Controlled Drug Delivery Systems: Current Status and, Molecules, 2021, 26, 5905 CrossRef.
- M. Hayashi, Implantation of recyclability and healability into cross-linked commercial polymers by applying the vitrimer concept, Polymers, 2020, 12(6), 1322, DOI:10.3390/POLYM12061322.
- W. Gu, F. Li, T. Liu, S. Gong, Q. Gao, J. Li and Z. Fang, Recyclable, Self-Healing Solid Polymer Electrolytes by Soy Protein-Based Dynamic Network, Adv. Sci., 2022, 9, 1–8, DOI:10.1002/advs.202103623.
- T. Liu, C. Hao, L. Wang, Y. Li, W. Liu, J. Xin and J. Zhang, Eugenol-Derived Biobased Epoxy: Shape Memory, Repairing, and Recyclability, Macromolecules, 2017, 50, 8588–8597, DOI:10.1021/acs.macromol.7b01889.
- A. Chernykh, T. Agag and H. Ishida, Effect of polymerizing diacetylene groups on the lowering of polymerization temperature of benzoxazine groups in the highly thermally stable, main-chain-type polybenzoxazines, Macromolecules, 2009, 42, 5121–5127, DOI:10.1021/ma900505d.
- B. Krishnakumar, R. V. S. P. Sanka, W. H. Binder, V. Parthasarthy, S. Rana and N. Karak, Vitrimers: Associative dynamic covalent adaptive networks in thermoset polymers, Chem. Eng. J., 2020, 385, 123820, DOI:10.1016/j.cej.2019.123820.
- W. Denissen, J. M. Winne and F. E. Du Prez, Vitrimers: Permanent organic networks with glass-like fluidity, Chem. Sci., 2016, 7, 30–38, 10.1039/c5sc02223a.
- T. F. Scott, A. D. Schneider, W. D. Cook and C. N. Bowman, Chemistry: Photoinduced plasticity in cross-linked polymers, Science, 2005, 308, 1615–1617, DOI:10.1126/science.1110505.
- M. A. Lucherelli, A. Duval and L. Avérous, Biobased vitrimers: Towards sustainable and adaptable performing polymer materials, Prog. Polym. Sci., 2022, 127, 101515, DOI:10.1016/j.progpolymsci.2022.101515.
- J. Joe, J. Shin, Y. S. Choi, J. H. Hwang, S. H. Kim, J. Han, B. Park, W. Lee, S. Park, Y. S. Kim and D. G. Kim, A 4D Printable Shape Memory Vitrimer with Repairability and Recyclability through Network Architecture Tailoring from Commercial Poly(ε-caprolactone), Adv. Sci., 2021, 8, 1–11, DOI:10.1002/advs.202103682.
- Q. Chen, X. Yu, Z. Pei, Y. Yang, Y. Wei and Y. Ji, Multi-stimuli responsive and multi-functional oligoaniline-modified vitrimers, Chem. Sci., 2016, 8, 724–733, 10.1039/C6SC02855A.
- S. J. Toal and W. C. Trogler, Polymer sensors for nitroaromatic explosives detection, J. Mater. Chem., 2006, 16, 2871–2883, 10.1039/b517953j.
- J. R. Kumpfer and S. J. Rowan, Thermo-, photo-, and chemo-responsive shape-memory properties from photo-cross-linked metallo-supramolecular polymers, J. Am. Chem. Soc., 2011, 133, 12866–12874, DOI:10.1021/ja205332w.
- M. Guerre, C. Taplan, J. M. Winne and F. E. Du Prez, Vitrimers: directing chemical reactivity to control material properties, Chem. Sci., 2020, 11, 4855–4870, 10.1039/d0sc01069c.
- T. X. Wang, H. M. Chen, A. V. Salvekar, J. Lim, Y. Chen, R. Xiao and W. M. Huang, Vitrimer-like shape memory polymers: Characterization and applications in reshaping and manufacturing, Polymers, 2020, 12, 1–28, DOI:10.3390/polym12102330.
- S. Kashef Tabrizian, W. Alabiso, U. Shaukat, S. Terryn, E. Rossegger, J. Brancart, J. Legrand, S. Schlögl and B. Vanderborght, Vitrimeric shape memory polymer-based fingertips for adaptive grasping, Front. Robot. AI, 2023, 10, 1–13, DOI:10.3389/frobt.2023.1206579.
- Y. Tao, X. Liang, J. Zhang, I. M. Lei and J. Liu, Polyurethane vitrimers: Chemistry, properties and applications, J. Polym. Sci., 2022, 1–21, DOI:10.1002/pol.20220625.
- S. Ciarella and W. G. Ellenbroek, Swap-driven self-adhesion and healing of vitrimers, Coatings, 2019, 9, 1–12, DOI:10.3390/COATINGS9020114.
- F. Van Lijsebetten, S. Engelen, E. Bauters, W. Van Vooren, M. M. J. Smulders and F. E. Du Prez, Recyclable vitrimer epoxy coatings for durable protection, Eur. Polym. J., 2022, 176, 111426, DOI:10.1016/j.eurpolymj.2022.111426.
- A. Gomez-Lopez, S. Panchireddy, B. Grignard, I. Calvo, C. Jerome, C. Detrembleur and H. Sardon, Poly(hydroxyurethane) Adhesives and Coatings: State-of-the-Art and Future Directions, ACS Sustainable Chem. Eng., 2021, 9, 9541–9562, DOI:10.1021/acssuschemeng.1c02558.
- M. Nozohour Yazdi, Y. Yamini, H. Asiabi and A. Alizadeh, A metal organic framework prepared from benzene-1,3,5-tricarboxylic acid and copper(II), and functionalized with various polysulfides as a sorbent for selective sorption of trace amounts of heavy metal ions, Microchim. Acta, 2018, 185, 1–8, DOI:10.1007/s00604-018-3059-0.
- M. Nozohour Yazdi, Y. Yamini, H. Asiabi and A. Alizadeh, A metal organic framework prepared from benzene-1,3,5-tricarboxylic acid and copper(II), and functionalized with various polysulfides as a sorbent for selective sorption of trace amounts of heavy metal ions, Microchim. Acta, 2018, 185, 1–8, DOI:10.1007/s00604-018-3059-0.
- S. S. Nadar, L. Vaidya, S. Maurya and V. K. Rathod, Polysaccharide based metal organic frameworks (polysaccharide–MOF): A review, Coord. Chem. Rev., 2019, 396, 1–21, DOI:10.1016/j.ccr.2019.05.011.
- J. Han, T. Liu, C. Hao, S. Zhang, B. Guo and J. Zhang, A Catalyst-Free Epoxy Vitrimer System Based on Multifunctional Hyperbranched Polymer, Macromolecules, 2018, 51, 6789–6799, DOI:10.1021/acs.macromol.8b01424.
- J. Han, T. Liu, C. Hao, S. Zhang, B. Guo and J. Zhang, A Catalyst-Free Epoxy Vitrimer System Based on Multifunctional Hyperbranched Polymer, Macromolecules, 2018, 51, 6789–6799, DOI:10.1021/acs.macromol.8b01424.
- T. Garg, O. Singh, S. Arora and R. S. R. Murthy, Dendrimer- a novel scaffold for drug delivery, Int. J. Pharm. Sci. Rev. Res., 2011, 7, 211–220 CAS.
- V. Schenk, K. Labastie, M. Destarac, P. Olivier and M. Guerre, Vitrimer composites: current status and future challenges, Mater. Adv., 2022, 3, 8012–8029, 10.1039/d2ma00654e.
- V. Schenk, K. Labastie, M. Destarac, P. Olivier and M. Guerre, Vitrimer composites: current status and future challenges, Mater. Adv., 2022, 3, 8012–8029, 10.1039/d2ma00654e.
|
This journal is © The Royal Society of Chemistry 2024 |
Click here to see how this site uses Cookies. View our privacy policy here.