DOI:
10.1039/D3MA00823A
(Paper)
Mater. Adv., 2024,
5, 267-273
A magnetic Fe@PANI catalyst for the selective oxidation of sulphide under mild and green conditions†
Received
9th October 2023
, Accepted 22nd November 2023
First published on 22nd November 2023
Abstract
The selective oxidation of sulphide to sulfoxide is an important transformation process in the industry. In this work, a novel polyaniline-supported iron catalyst (Fe@PANI) was designed and synthesised for catalyzing the reaction. It was found that the material exhibited magnetism and could be recycled by magnetic separation and reused without deactivation. The magnetic Fe@PANI-catalyzed oxidation reaction of sulphides could selectively form sulfoxides without the generation of sulfones. The inexpensive catalyst and mild and green conditions make the reaction practical for large-scale applications.
Introduction
Sulfoxides are useful synthetic intermediates in the industry because they widely exist in a variety of medicines and pesticides, such as fipronil, lansoprazole and (R)-omeprazole.1 Since sulphides are easily synthesized via nucleophilic substitution or coupling reactions, the oxidation of sulphides is considered to be a direct route to sulfoxides.2 However, traditional synthesis methods encounter several issues, including the reliance on noble metals, excessive ligand consumption, the inability to recycle catalysts, the low conversion rates of catalysts, the use of chemical oxidants/additives, acidic conditions or high reaction temperatures that may be intolerable to the sensitive functional groups of the substrates.3 Moreover, sulfoxides may be easily oxidized to sulfones, and controlling this side reaction is also a great challenge.4 During the past decade, chemists have paid much attention to developing techniques for the selective oxidation of sulphides to sulfoxides under mild and green conditions.5
On the other hand, polyanilines (PANIs) are employed as supports to develop heterogeneous metal catalysts (M@PANIs) for a variety of reactions.6 PANI-supported noble metals, such as Pd, Pt, Ag, and Au are found to be efficient catalysts in coupling reactions with very high catalyst turnover numbers (TONs).7 In comparison with the inorganic supports, PANIs are versatile and their properties can be adjusted by introducing functional groups onto the aniline monomers to improve the catalytic activities of the supported metals.8 Thus, proper aniline monomers may be screened out to develop M@PANI catalysts using relatively cheap metals, such as Cu, Ni, W and Mo.9 Developing iron-based catalysts is an attractive objective because Fe is the cheapest metal on earth and shows good biocompatibility with human beings and animals.10 Although Fe-involved M@PANIs catalysts have already been recently reported, in most cases, Fe existed as Fe3O4 to provide the magnetic property for the materials, and reports on the use of Fe@PANIs catalysts for synthesis purposes are rare.11 Recently, we successfully developed a magnetic Fe@PANIs catalyst for the selective oxidation of sulphides to sulfoxides under green and mild conditions. Herein, we report our findings.
Results and discussion
Fe@PANI materials were synthesized via the traditional oxidative polymerization reaction (Fig. 1). In this method, PANI monomers were initially dissolved in aqueous HCL and Fe3O4 was then added as the iron source. Aqueous ammonium persulfate (APS) was then added to the system to initialize the oxidative polymerization reaction. Iron species were adsorbed onto the generated PANI fibres, which were then isolated via centrifugation.
 |
| Fig. 1 A diagram of the synthesis of Fe@PANI. | |
Using polyaniline and p-fluoroaniline as monomers, we synthesized two types of Fe@PANIs and they were named Fe@PANI-H and Fe@PANI-F, respectively. Inductively coupled plasma mass spectrometry (ICP-MS) analysis indicated that the amount of Fe in Fe@PANI-H and Fe@PANI-F was 4.1% and 1.7%, respectively. The result indicated that introducing electron-withdrawing fluorine into the system could reduce the coordination effect of nitrogen to metals and lead to a decrease in the Fe content.
Fe@PANI materials were synthesized via the traditional oxidative polymerization reaction (Fig. 1). In the method, the PANI monomers were initially dissolved in aqueous HCL, and Fe3O4 was then added as the iron source. Aqueous ammonium persulfate (APS) was then added to the system to initialize the oxidative polymerization reaction. Iron species were adsorbed onto the generated PANI fibres, which were then isolated by centrifugation. Using polyaniline and p-fluoroaniline as monomers, we synthesized two types of Fe@PANIs and they were marked as Fe@PANI-H and Fe@PANI-F. Inductively coupled plasma mass spectrometry (ICP-MS) analysis indicated that the weight contents of Fe in Fe@PANI-H and Fe@PANI-F were 4.1% and 1.7%, respectively. The result indicated that introducing the electron-withdrawn fluorine into the system can reduce the coordination effect of nitrogen to metals and lead to a decrease in Fe content.
The materials were then employed as catalysts In the sulphide oxidation reactions (Fig. 2). Fe@PANI-F shows better catalytic activity than Fe@PANI-H, although the Fe loading is even lower in the reactions (Fig. 2a). Generally, the electron-enriched sulphides were preferable substrates, leading to higher product yields of 2a and 2b than the reactions of electron-deficient ones giving 2c–2e. Introducing electron-withdrawing groups into the aliphatic chain also led to the decreased yield of 2g (vs.2f). The reaction could be retarded by the steric hindrances of the substrates, i.e., the yields of 2h and 2i were lower than those of 2a and 2f. Besides aryl, benzyl- or alkyl-substituted sulphides could also provide the related sulfoxides 2j and 2k, smoothly. Moreover, as a magnetic material, Fe@PANI-F could be magnetically separated after the oxidation reaction of 1a, and it could be reused at least five times to provide 2a in good yields (Fig. 2b). The reaction of methyl(phenyl)sulfane can be enlarged to a 10 mmol scale, giving 2a in 91% yield. Notably, the reaction was specific for generating sulfoxides, and using excess H2O2 (2.0 equiv. vs. 1) did not lead to any sulfone by-products, as indicated by GC-MS. Catalysed by Fe@PANI-F, thiols such as p-methylthiophenol could be sufficiently oxidized to produce p-toluenesulfonic acid only, and by using sufficient H2O2 (4.0 equiv.), its yield could reach 95%.
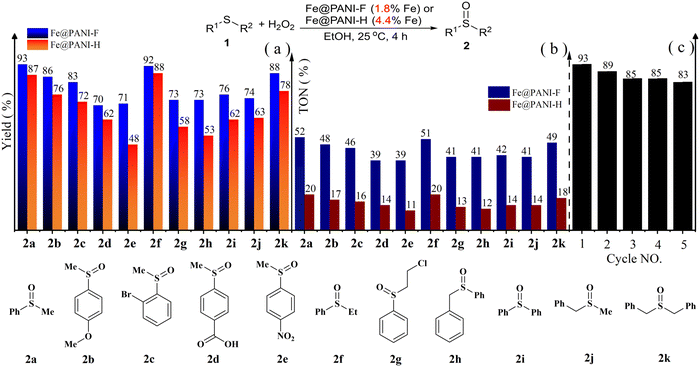 |
| Fig. 2 The Fe@PANIs-catalyzed oxidation reactions of sulphides to sulfoxides: (a) substrate extensions, (b) TON of Fe@PANIs-catalyzed, and (c) catalyst recycling and reuse for the oxidation of 1a. | |
In Fourier transform infrared (FT-IR) spectra of the materials (Fig. 3a), the peaks at 1571 and 1508 cm−1 reflected the C
C stretching vibration of quinone and benzene structures. The peak strength represented the oxidation degree of PANI. The stretching vibration signals of C–N emerge at 1315 and 1240 cm−1, while the stretching vibration of C
N at 1153 cm−1 is the characteristic peak of PANI. The peak at 829 cm−1 is the C–H tensile vibration. The peak at 588 cm−1 is the characteristic peak of Fe–O stretching vibration.12 In addition, C–F stretching vibration is reflected by the signal at 707 cm−1. The introduction of the electron-withdrawing fluorine group causes the signals of stretching and bending vibrations of the chemical bonds to shift to the high-frequency direction. The high electronegativity of the fluorine group results in the increase of the strength of the peaks between 1153 to 1571 cm−1. Comparison of the FT-IR spectra demonstrates that by introducing fluorine, the electron density of the PANI chain decreased, and this may be the reason for the reduced coordination effect of nitrogen in PANI with metals leading to the decreased Fe content. However, the reduced N–Fe coordination may allow the metals to participate in the catalytic oxidation reactions more freely, resulting in the improved catalytic activity of Fe@PANI-F vs. Fe@PANI-H (Fig. 2).
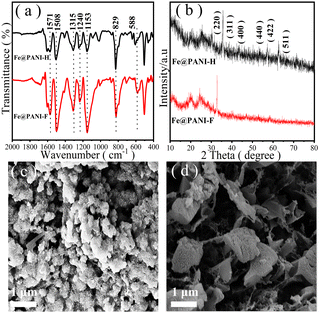 |
| Fig. 3 The characterization of the catalysts: (a) the IR-spectra, (b) XRD patterns, (c) and (d) SEM images of Fe@PANI-H (c) and Fe@PANI-F (d). | |
Powder X-ray diffraction (XRD) patterns of the materials are shown in Fig. 3b. Since PANIs are polymers with low crystallinity, their diffraction peaks are low and wide, and the signals are weak. Two peaks at 2θ = 19.97° and 25.03° are attributed to the planes (020) and (022), respectively.13 The characteristic peaks of planes at (220), (311), (400), (422), (511), (440), and (511) of Fe3O4 can also be observed in the XRD patterns,14 indicating that iron has been successfully loaded into the material and there is no structural change of Fe3O4 during the formation of the composite. The introduction of fluorine enhances the strength of the diffraction peak signal of PANI and leads to the peak shift due to the strong electronegativity of the element.
It has been reported that PANIs were mostly formed by filamentous fibres.15 However, scanning electron microscopy (SEM) images of Fe@PANIs showed that introducing Fe and F may lead to changes in the morphologies and structures of the materials (Fig. 3c and d). In Fe@PANI-H, the accumulation of PANI fibres and amorphous iron particles on its surface presents a uniform particle morphology (Fig. 3c), but for Fe@PANI-F, the surface aggregations are in sheet shape with larger pores, resulting in the enhanced amount of reaction sites that can provide better contact with the reactants (Fig. 3d). Therefore, in comparison with Fe@PANI-H, the catalytic activity of Fe@PANI-F was obviously improved in sulphide oxidation reactions, regardless of the reduced Fe loading (Fig. 2).
The transmission electron microscopy (TEM) image of Fe@PANI-F shows that the outer layer of the particles of the material is covered by transparent matter, reflecting that the PANI-F covers the surface of Fe3O4 (Fig. 4a). Due to the low content of iron, no crystals were detected in the electron diffraction pattern and high-resolution transmission electron microscopy (HR-TEM) image of the material (Fig. 4b and c, respectively). Energy dispersive X-ray (EDX) spectroscopy analysis showed that Fe was involved in the material (Fig. 4d). Element mapping images demonstrated that Fe was successfully included in the skeletons of PANI-F (Fig. 4e).
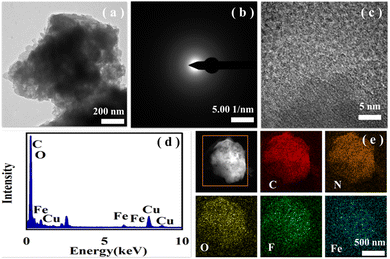 |
| Fig. 4 The characterization of Fe@PANI-F: (a) the TEM image, (b) electron diffraction pattern, (c) HR-TEM image, (d) EDX pattern and (e) element mappings. | |
In the X-ray photoelectron spectroscopy (XPS) spectra of the materials, signals at 284.6, 285.8, and 286.4 eV in the C 1s spectra are attributed to C–C/C–H, C–N/C
N, and C–O in the PANI skeleton (Fig. 5a). In N 1s spectra, the peaks at 398.7 and 401.8 eV correspond to two different chemical states of nitrogen (Fig. 5b). It is also indicated by the O1s spectra that three different states of oxygen are involved in the material, in which Oc is considered to be the adsorbed oxygen, while Ov is the crystal oxygen in Fe3O4, and the signal strength is determined by the oxygen vacancy concentration (Fig. 5c). In Fe2p spectra, two signals emerged at around 711.5 and 724.7 eV, corresponding to Fe2p3/2 and Fe2p1/2, respectively. By analysing Ov and Feδ+ composition in XPS spectra, it is found that the oxygen vacancy concentration in Fe@PANI-F is higher than that in Fe@PANI-H, affording more active sites to improve the catalytic efficiency of the material in the oxidation reactions (Tables S1–S4 in ESI†).16
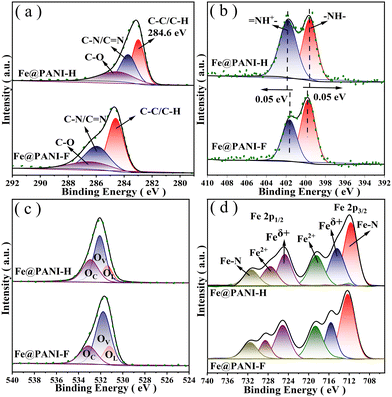 |
| Fig. 5 The XPS spectra of the materials: (a) C1s, (b) N1s, (c) O1s and (d) Fe2p. | |
A series of control experiments were then performed to obtain sufficient information for the mechanism study. First, using stoichiometric H2O2 (1 equiv. vs.1a) resulted in decreased 2a yield (Table 1, entries 2 vs. 1), and this was probably because the EtOH solvent of the reaction as a reductive chemical might have consumed a part of the oxidant. However, considering its green features as well as the cheap price, we continued to use EtOH as the solvent of the reaction. Further enhancing the dosage of H2O2 could hardly enhance the product yield (Table 1, entries 3 vs. 1), but no sulfone by-product was observed by thin-layer chromatography (TLC). The result showed that the reaction condition at 25 °C could resist the over-oxidation reaction of sulfoxide to sulfone. The reaction with PANI-F as a catalyst led to 2a in very poor yield, similar to the results of the blank reaction without a catalyst, showing that Fe was the essential catalyst for oxidation (Table 1, entries 4 and 5). Comparatively, the Fe3O4-catalyzed oxidation of 1a produced 2a in only 28% yield (Table 1, entry 6). Using soluble FeSO4 as a catalyst also led to poor 2a yield (Table 1, entry 7). These results verified that PANI-F was an essential support that could obviously enhance the catalytic activity of Fe. Since the reaction could be restrained by 2,2,6,6-tetramethylpiperidoxyl (TEMPO), it is supposed to be a free radical reaction (Table 1, entry 8).17 Salicylic acid trapping experiment further confirmed that the hydroxyl radical was involved in the process (Fig. S1 in ESI†).18
Table 1 Control experimentsa
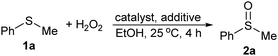
|
Entry |
H2O2/1ab |
Catalyst, additivec |
Yieldd (%) |
0.5 mmol of 1a was employed.
Molar ratio of the employed H2O2/1a.
Percentage (%) of catalytic metal or additive vs.1a inside the brackets.
Yield of 2a on the basis of 1a.
|
1 |
2.0 |
Fe@PANI-F (1.8) |
93 |
2 |
1.0 |
Fe@PANI-F (1.8) |
77 |
3 |
3.0 |
Fe@PANI-F (1.8) |
92 |
4 |
2.0 |
PANI-F (0) |
20 |
5 |
2.0 |
— |
19 |
6 |
2.0 |
Fe3O4 (1.8) |
28 |
7 |
2.0 |
FeSO4 (1.8) |
37 |
8 |
2.0 |
Fe@PANI-F (1.8), TEMPO (100) |
<5 |
Thus, on the basis of the experimental results as well as the literature reports, a plausible mechanism is proposed (Scheme 1). First, as indicated by the XPS spectra, Fe2+ species were involved in the material (Fig. 5d), and it could initiate the free radical chain via the single electron transfer (SET) reaction with H2O2 to furnish the hydroxyl radical.19 Fe2+ was oxidized to Fe3+, which might be reduced by the organic solvent to maintain the Fe2+ content in the catalyst material.20 The reaction of the hydroxyl radical with sulphide (1) led to the radical intermediate 3, which could react with another molecule of H2O2 to produce intermediate 4 and regenerate the hydroxyl radical to continue the radical reaction chain.21 Dehydration of 4 occurred quickly to produce the final product 2. Bearing a S
O, the electron density of sulphur in 2 significantly decreased. Thus, it could hardly react with the hydroxyl radical so the reaction could keep high selectivity at the sulphide generation step, while no sulfone by-product was produced even with an excess of the H2O2 oxidant (Table 1, entry 3).22 PANI-F is undoubtedly good support that can enhance the activity of Fe: (1) in comparison with PANI-H, the surface structure of PANI-F in the sheet shape with larger pores may enhance the number of reaction sites that can better contact with the reactants; (2) the electron-withdrawing features of fluorine group reduces the N–Fe coordination, leading to the metal participating in the catalytic oxidation reactions more freely; (3) the enhanced oxygen vacancy concentration of the catalyst after the introduction of the fluorine group may also provide more active sites for the oxidation reactions.
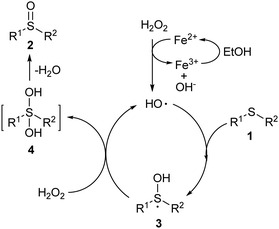 |
| Scheme 1 The possible mechanism of the reaction. | |
Conclusions
In conclusion, we have synthesized a novel Fe@PANI-F material that can be used as an efficient catalyst for sulphide oxidation reaction to selectively produce sulfoxides. The material is magnetic and can be magnetically separated after the reaction. It can be reused at least five times giving good product yields. In comparison with references, the green and mild reaction conditions are the advantages of this method. Moreover, to the best of our knowledge, this is the first example of using magnetic Fe@PANI materials as catalysts for synthesis purposes. Therefore, this work may inspire new ideas for the design of new catalysts in the synthesis industry.
Experimental
General methods
Reagents and solvents were purchased from the reagent suppliers and used directly, as received, without any special treatment. The reagents were analytically pure (AR). The melting points of the products were determined using the WRS-2A digital instrument. Fourier Transform infrared (FT-IR) spectra of the products were obtained using an Antaris II spectrometer. NMR spectra were recorded on a Bruker Avance 400 instrument using CDCl3 as the solvent and Me4Si as the internal standard. Chemical shifts for 1H NMR were referred to internal Me4Si (0 ppm) and J-values are shown in Hz. XPS spectra were measured on the Thermo Fisher Scientific ESCALAB 250Xi X photoelectron spectrometer. The morphologies of the catalysts were analyzed using FE-SEM on a Zeiss_Supra55 field emission scanning electron microscope. HR-TEM images were captured on a Tecnai G2 F30 field emission transmission electron microscope. ICP-MS analysis was performed on a PerkinElmer Optima 7300 DV inductively coupled plasma spectrometer. The crystal structure of the catalyst was studied using the AXS D8 powder diffractometer at an applied current of 40 mA.
Procedures for the preparation of Fe@PANI-F
Fe@PANI-F nanocomposites were fabricated by oxidative polymerization of 4-fluoroaniline using ammonium persulphate (APS) in an acidic medium. To a 250 mL beaker, 4.7 mL of 4-fluoroaniline and 50 mL aqueous HCl (1 mol L−1) were added. After stirring for 10 min, 200 mg of Fe3O4 was added to the beaker. Then, APS solution (2.0 g APS in 40 mL 1 M HCl) was added and stirred to initiate the oxidative polymerization. The mixture was then kept standing at room temperature for 24 h, and neutralized using 1 mol L−1 of aqueous NaOH. The precipitate was separated by centrifugation and washed with deionized water and EtOH 6 times. After drying at 60 °C under vacuum for 24 h, the Fe@PANI-F material was obtained.
General procedures for the Fe@PANI-F-catalyzed selective sulfide oxidation
0.5 mmol of substrate 1, 30 mg of Fe@PANI-F catalyst, and a piece of the magnetic bar were initially added into a 25 mL Schlenk tube. H2O2 could be introduced into the system using two protocols: (1) the solution of 1 mmol of H2O2 (30 wt%) in 2 mL of EtOH was injected into the system at one time; (2) the solution of 1 mmol of H2O2 (30 wt%) in 2 mL of EtOH was injected into the system in four portions during the reaction processes (0.25 mmol of H2O2 was added every 0.5 h). The reaction mixture was stirred at 25 °C for 4 h. After that, a magnet was placed outside the bottom of the reaction tube, while the reaction liquid was being separated. By adding fresh reactants, the recycled catalyst in the Schlenk tube can be directly reused without any purification. The solvent in the reaction liquid was then removed by distillation with a rotary evaporator and the residue was separated by preparative TLC on silica (GF-254) with petroleum ether/EtOAc 1
:
1 to afford the related product 2.
Author contributions
Xiaohe Wu, Ying Chen, and Yiyang Zhang performed the experiments. Xu Zhang wrote the draft in Chinese. Lei Yu led the project, directed the students, and wrote the paper in English based on Zhang's draft.
Conflicts of interest
The authors declare no competing financial interests.
Notes and references
-
(a) Z. Zhou, X. Wu, Z. Lin, S. Pang, S. Mishra and S. Chen, Appl. Microbiol. Biotechnol., 2021, 105, 7695 CrossRef CAS PubMed;
(b) X. Lin, H. Chen and Y.-N. Lin, Ann. Palliat. Med., 2021, 10, 9535 CrossRef PubMed;
(c) T. Andersson, Clin. Pharmacokinet., 1996, 31, 9 CrossRef CAS PubMed.
-
(a) F. Kazemi, S. M. Naghib, Y. Zare and K. Y. Rhee, Polym. Rev., 2021, 61, 553 CrossRef CAS;
(b) R. Szpera, P. G. Isenegger, M. Ghosez, N. J. W. Straathof, R. Cookson, D. C. Blakemore, P. Richardson and V. Gouverneur, Org. Lett., 2020, 22, 6573 CrossRef CAS PubMed;
(c) F. Zhu, Z. Chen and M. A. Walczak, J. Org. Chem., 2020, 85, 11942 CrossRef CAS PubMed;
(d) A. C. Jones, W. I. Nicholson, H. R. Smallman and D. L. Browne, Org. Lett., 2020, 22, 7433 CrossRef CAS PubMed;
(e) A. Varenikov and M. Gandelman, J. Am. Chem. Soc., 2019, 141, 10994 CrossRef CAS;
(f) E. Voutyritsa, I. Triandafillidi and C. G. Kokotos, Synthesis, 2017, 917 CAS;
(g) Z. Qiao and X. Jiang, Org. Lett., 2016, 18, 1550 CrossRef CAS;
(h) K. Kaczorowska, Z. Kolarska, K. Mitka and P. Kowalski, Tetrahedron, 2005, 61, 8315 CrossRef CAS.
-
(a) K.-J. Liu, Z. Wang, L.-H. Lu, J.-Y. Chen, F. Zeng, Y.-W. Lin, Z. Cao, X. Yu and W.-M. He, Green Chem., 2021, 23, 496 RSC;
(b) L. Tang, K. Du, B. Yu and L. He, Chin. Chem. Lett., 2020, 31, 2991 CrossRef CAS;
(c) J. Liu, N. Liu, H. Wang, W. Shi, J. Zhuang and X. Wang, J. Am. Chem. Soc., 2020, 142, 17557 CrossRef CAS PubMed;
(d) Z. Chen, C. Liu, J. Liu, J. Li, S. Xi, X. Chi, H. Xu, I.-H. Park, X. Peng, X. Li, W. Yu, X. Liu, L. Zhong, K. Leng, W. Huang, M. J. Koh and K. P. Loh, Adv. Mater., 2020, 32, 1906437 CrossRef CAS PubMed;
(e) K.-J. Liu, J.-H. Deng, J. Yang, S.-F. Gong, Y.-W. Lin, J.-Y. He, Z. Cao and W.-M. He, Green Chem., 2020, 22, 433 RSC;
(f) R. G. Almeida, R. L. de Carvalho, M. P. Nunes, R. S. Gomes, L. F. Pedrosa, C. A. de Simone, E. Gopi, V. Geertsen, E. Gravel, E. Doris and E. N. da Silva Júnior, Catal. Sci. Technol., 2019, 9, 2742 RSC;
(g) G. K. S. Prakash, A. Shakhmin, K. E. Glinton, S. Rao, T. Mathew and G. A. Olah, Green Chem., 2014, 16, 3616 RSC;
(h) X. Gu, X. Li, Y. Chai, Q. Yang, P. Li and Y. Yao, Green Chem., 2013, 15, 357 RSC;
(i) B. Li, A.-H. Liu, L.-N. He, Z.-Z. Yang, J. Gao and K.-H. Chen, Green Chem., 2012, 14, 130 RSC;
(j) S. E. Martín and L. I. Rossi, Tetrahedron Lett., 2001, 42, 7147 CrossRef;
(k) A. Shaabani, Z. Hezarkhani and E. Badali, RSC Adv., 2015, 5, 61759 RSC.
-
(a) Q. Fan, L. Zhu, X. Li, H. Ren, G. Wu, H. Zhu and W. Sun, Green Chem., 2021, 23, 7945 RSC;
(b) X. Ma, H. Hao, W. Sheng, F. Huang and X. Lang, J. Mater. Chem. A, 2021, 9, 2214 RSC;
(c) C. Li, N. Mizuno, K. Murata, K. Ishii, T. Suenobu, K. Yamaguchi and K. Suzuki, Green Chem., 2020, 22, 3896 RSC;
(d) W. Zhao, C. Yang, J. Huang, X. Jin, Y. Deng, L. Wang, F. Su, H. Xie, P. K. Wong and L. Ye, Green Chem., 2020, 22, 4884 RSC;
(e) F. Yang, X. Chu, J. Sun, Y. Zhang, Z. Li, H. Liu, L. Bai, Y. Qu and L. Jing, Chin. Chem. Lett., 2020, 31, 2784 CrossRef CAS;
(f) X. Lan, Q. Li, Y. Zhang, Q. Li, L. Ricardez-Sandoval and G. Bai, Appl. Catal., B, 2020, 277, 119274 CrossRef CAS;
(g) Z. Cheng, P. Sun, A. Tang, W. Jin and C. Liu, Org. Lett., 2019, 21, 8925 CrossRef CAS PubMed;
(h) S. P. Das, J. J. Boruah, H. Chetry and N. S. Islam, Tetrahedron Lett., 2012, 53, 1163 CrossRef CAS;
(i) S. Hussain, S. K. Bharadwaj, R. Pandey and M. K. Chaudhuri, Eur. J. Org. Chem., 2009, 3319 CrossRef CAS.
-
(a) S. Liang, K. Hofman, M. Friedrich, J. Keller and G. Manolikakes, ChemSusChem, 2021, 14, 4878 CrossRef CAS;
(b) Y. Li, S. A. Rizvi, D. Hu, D. Sun, A. Gao, Y. Zhou, J. Li and X. Jiang, Angew. Chem., Int. Ed., 2019, 58, 13499 CrossRef CAS;
(c) J. Zhang, T. Jiang, Y. Mai, X. Wang, J. Chen and B. Liao, Catal. Commun., 2019, 127, 10 CrossRef;
(d) A. Bezaatpour, E. Askarizadeh, S. Akbarpour, M. Amiria and B. Babaei, Mol. Catal., 2017, 436, 199 CrossRef CAS;
(e) C. Su, R. Tandiana, B. Tian, A. Sengupta, W. Tang, J. Su and K. P. Loh, ACS Catal., 2016, 6, 3594 CrossRef CAS;
(f) S. R. Gogoi, J. J. Boruah, G. Sengupta, G. Saikia, K. Ahmed, K. K. Bania and N. S. Islam, Catal. Sci. Technol., 2015, 5, 595 RSC;
(g) F. Jalilian, B. Yadollahi, M. R. Farsani, S. Tangestaninejad, H. A. Rudbari and R. Habibi, Catal. Commun., 2015, 66, 107 CrossRef CAS;
(h) Y. Kon, T. Yokoi, M. Yoshioka, S. Tanaka, Y. Uesaka, T. Mochizuki, K. Sato and T. Tatsumi, Tetrahedron, 2014, 70, 7584 CrossRef CAS;
(i) J. J. Boruah, S. P. Das, S. R. Ankireddy, S. R. Gogoi and N. S. Islam, Green Chem., 2013, 15, 2944 RSC;
(j) M. Jereb, Green Chem., 2012, 14, 3047 RSC;
(k) B. Yu, A.-H. Liu, L.-N. He, B. Li, Z.-F. Diao and Y.-N. Li, Green Chem., 2012, 14, 957 RSC;
(l) P. Zhang, Y. Wang, H. Li and M. Antonietti, Green Chem., 2012, 14, 1904 RSC;
(m) A. Rostami and J. Akradi, Tetrahedron Lett., 2010, 51, 3501 CrossRef CAS;
(n) C. Yang, Q. Jin, H. Zhang, J. Liao, J. Zhu, B. Yu and J. Deng, Green Chem., 2009, 11, 1401 RSC;
(o) W. Al-Maksoud, S. Daniele and A. B. Sorokin, Green Chem., 2008, 10, 447 RSC;
(p) F. Shi, M. K. Tse, H. M. Kaiser and M. Beller, Adv. Synth. Catal., 2007, 349, 2425 CrossRef CAS;
(q) B. Karimi, M. Ghoreishi-Nezhad and J. H. Clark, Org. Lett., 2005, 7, 625 CrossRef CAS.
-
(a) Z. Zeng, Y. Chen, X. Zhu and L. Yu, Chin. Chem. Lett., 2023, 34, 107728 CrossRef CAS;
(b) A. Yadav, H. Kumar, R. Sharma and R. Kumari, Colloid Interface Sci., 2021, 40, 100339 CrossRef CAS;
(c) F. Kazemi, S. M. Naghib, Y. Zare and K. Y. Rhee, Polym. Rev., 2021, 61, 553 CrossRef CAS;
(d) A. P. M. Udayan, O. Sadak and S. Gunasekaran, ACS Appl. Energy Mater., 2020, 3, 12368 CrossRef CAS.
-
(a) A.-L. Wang, H. Xu, J.-X. Feng, L.-X. Ding, Y.-X. Tong and G.-R. Li, J. Am. Chem. Soc., 2013, 135, 10703 CrossRef CAS;
(b) Q. Dang, Y. Sun, X. Wang, W. Zhu, Y. Chen, F. Liao, H. Huang and M. Shao, Appl. Catal., B, 2019, 257, 117905 CrossRef CAS;
(c) A. Drury, S. Chaure, M. Kröll, V. Nicolosi, N. Chaure and W. J. Blau, Chem. Mater., 2007, 19, 4252 CrossRef CAS;
(d) U. Bogdanović, I. Pašti, G. Ćirić-Marjanović, M. Mitrić, S. P. Ahrenkiel and V. Vodnik, ACS Appl. Mater. Interfaces, 2015, 7, 28393 CrossRef.
- Y. Liu, D. Tang, K. Cao, L. Yu, J. Han and Q. Xu, J. Catal., 2018, 360, 250 CrossRef CAS.
-
(a) Y. Chen, L. Yu and H. Zhou, J. Phys. Chem. C, 2022, 126, 17084 CrossRef CAS;
(b) A. Houdayer, R. Schneider, D. Billaud, J. Ghanbaja and J. Lambert, Synth. Met., 2005, 151, 165 CrossRef CAS;
(c) W. Li, F. Wang, Y. Shi and L. Yu, Chin. Chem. Lett., 2023, 34, 107505 CrossRef CAS;
(d) Y. Zhang, W. Li, Z. Hu, X. Jing and L. Yu, Chin. Chem. Lett., 2024, 35, 108938, DOI:10.1016/j.cclet.2023.108938 , in press.
-
(a) R. Shang, L. Ilies and E. Nakamura, Chem. Rev., 2017, 117, 9086 CrossRef CAS PubMed;
(b) L. Lv and Z. Li, Top. Curr. Chem., 2016, 374, 38 CrossRef PubMed;
(c) B. D. Sherry and A. Fürstner, Acc. Chem. Res., 2008, 41, 1500 CrossRef CAS;
(d) C. Bolm, J. Legros, J. Le Paih and L. Zani, Chem. Rev., 2004, 104, 6217 CrossRef CAS PubMed.
-
(a) B. Goswami and D. Mahanta, ACS Omega, 2021, 6, 17239 CrossRef CAS PubMed;
(b) M. N. Rantho, M. J. Madito and N. Manyala, J. Alloys Compd., 2020, 819, 152993 CrossRef CAS;
(c) Z. H. Dastgerdi, S. S. Meshkat, S. Hosseinzadeh and M. D. Esrafili, J. Inorg. Organomet. Polym. Mater., 2019, 29, 1160 CrossRef CAS;
(d) A. Fatahi, R. Malakooti and M. Shahlaei, RSC Adv., 2017, 7, 11322 RSC;
(e) J. C. Aphesteguy and S. E. Jacobo, J. Mater. Sci., 2007, 42, 7062 CrossRef CAS.
-
(a) D. He, C. Zeng, C. Xu, N. Cheng, H. Li, S. Mu and M. Pan, Langmuir, 2011, 27, 558 Search PubMed;
(b) O. E. Fayemi, A. S. Adekunle, B. E. Kumara Swamy and E. E. Ebenso, J. Electroanal. Chem., 2018, 818, 236 CrossRef CAS.
- H. C. Pant, M. K. Patra, S. C. Negi, A. Bhatia, S. R. Vadera and N. Kumar, Bull. Mater. Sci., 2006, 29, 379 CrossRef CAS.
- S. Erogul, S. Z. Bas, M. Ozmen and S. Yildiz, Electrochim. Acta, 2015, 186, 302 CrossRef CAS.
- T. N. Myasoedova, T. A. Moiseeva, M. A. Kremennaya, A. Tirkeshov and G. E. Yalovega, J. Electron. Mater., 2020, 49, 4707 CrossRef CAS.
- T. Yamashita and P. Hayes, Appl. Surf. Sci., 2008, 254, 2441 CrossRef CAS.
-
(a) Y. Chen, C. Chen, Y. Liu and L. Yu, Chin. Chem. Lett., 2023, 34, 108489 CrossRef CAS;
(b) H. Cao, P. Li, X. Jing and H. Zhou, Chin. J. Org. Chem., 2022, 42, 3890 CrossRef CAS;
(c) W. Zhou, X. Xiao, Y. Liu and X. Zhang, Chin. J. Org. Chem., 2022, 42, 1849 CrossRef CAS.
- J. Huang, R. Qian, S. Wang and H. Cao, Chin. J. Org. Chem., 2021, 41, 1639 CrossRef CAS.
- R. Zhu, Y. Zhu, H. Xian, L. Yan, H. Fu, G. Zhu, Y. Xi, J. Zhu and H. He, Appl. Catal., B, 2020, 270, 118891 CrossRef CAS.
- T. de, M. Augusto, P. Chagas, D. L. Sangiorge, T. C. de, O. Mac Leod, L. C. A. Oliveira and C. S. de Castro, J. Environ. Chem. Eng., 2018, 6, 6545 CrossRef.
-
(a) A. L. Cardona, M. B. Blanco, M. A. Teruel and O. N. Ventura, Environ. Sci.: Atmos., 2023, 3, 1075 CAS;
(b) Q. Ye, M. B. Goss, G. Isaacman-VanWertz, A. Zaytsev, P. Massoli, C. Lim, P. Croteau, M. Canagaratna, D. A. Knopf, F. N. Keutsch, C. L. Heald and J. H. Kroll, ACS Earth Space Chem., 2021, 5, 2013 CrossRef CAS;
(c) T. Berndt, J. Chen, K. H. Møller, N. Hyttinen, N. L. Prisle, A. Tilgner, E. H. Hoffmann, H. Herrmann and H. G. Kjaergaard, Chem. Commun., 2020, 56, 13634 RSC;
(d) T. Berndt, W. Scholz, B. Mentler, L. Fischer, E. H. Hoffmann, A. Tilgner, N. Hyttinen, N. L. Prisle, A. Hansel and H. Herrmann, J. Phys. Chem. Lett., 2019, 10, 6478 CrossRef CAS.
- S. Liu, B. Chen, Y. Yang, Y. Yang, Q. Chen, X. Zeng and B. Xu, Electrochem. Commun., 2019, 109, 106583 CrossRef CAS.
|
This journal is © The Royal Society of Chemistry 2024 |
Click here to see how this site uses Cookies. View our privacy policy here.