DOI:
10.1039/D4RA03174A
(Paper)
RSC Adv., 2024,
14, 23662-23671
Synthesis of azelaic acid copolyester plasticizers and their application in PVC
Received
29th April 2024
, Accepted 15th July 2024
First published on 29th July 2024
Abstract
A series of 2-methyl-1,3-propanediol (MPO) modified azelaic acid and hexylene glycol copolyester (PHMAZ) plasticizers with varying contents were synthesized using a direct esterification melt polycondensation method, and their structures were characterized systematically. Analysis using infrared spectroscopy and nuclear magnetic resonance spectroscopy confirmed the synthesis of the designed copolyester structure. Gel permeation chromatography (GPC) tests indicated that the number average molecular weight of each copolyester sample ranged between 2000 and 3000. These copolyesters were used to plasticize polyvinyl chloride (PVC) resin, and the glass transition temperature of the plasticized PVC samples was tested using a differential scanning calorimeter (DSC). Further characterization of the plasticizing effects was conducted using an electronic universal testing machine. The research results showed that as the content of MPO increased, the plasticizing effect of the copolyester initially increased and then decreased. Specifically, the copolyester containing 45% MPO, PHMAZ-45, demonstrated the best plasticizing effect on PVC, with the glass transition temperature of the plasticized PVC system around −35 °C, elongation at break at 908.4%, and a plasticizing efficiency of 254.5%. Additionally, this new type of copolyester plasticizer uses bio-based raw materials, exhibits excellent plasticizing effects, and the preparation process is stable and controllable. It holds promising potential to replace traditional volatile and toxic phthalate esters, presenting significant industrial application value.
1. Introduction
Polyvinyl chloride is the world's most widely produced general plastic and has the advantages of good impact resistance, corrosion resistance, wear resistance, insulation and low processing cost.1–13 It is widely used in industrial products, daily necessities, agriculture, building materials, medical equipment, military industry, electronic devices, etc.1,4,10,14–27 PVC is a basic chemical material. With the continuous advancement of technological reforms and the support of national policies, the PVC market has become more prosperous, which in turn has promoted the research and development of plasticizers.
Plasticizers can be inserted into polymer molecules to increase the distance between polymer molecules and reduce the intermolecular force, which can greatly improve the processability of PVC and make it have good weather resistance and mechanical properties.16,23,28–32 For a long time, the plasticizers used for PVC have mainly been phthalates, and the most widely used is dioctyl phthalate (DOP),10,11,33–35 but it is easy to migrate out and is toxic, which will affect the application performance of the product, and many animal experiments have shown that DOP is potentially carcinogenic,36–41 and its application in most daily products has been banned in many countries. Therefore, the development of new non-toxic migration-resistant plasticizers has become a research hotspot.20,42–45
With the improvement of market requirements, research on various plasticizers has gradually developed. Among them, polyester plasticizers have higher molecular weight and good compatibility with PVC. They are inserted between macromolecule segments and are not easy to migrate, making it easier to improve PVC. The processing performance of products has received widespread attention.46 In the foreign plasticizer market, polyester plasticizers account for more than 12%,47 while the development of polyester plasticizers in China is mostly in the research stage. Lindström et al.48,49 synthesized linear polyglycol adipate and branched polyglycol adipate and applied them as plasticizers to PVC. The results showed that the addition of both types of polyester plasticizers significantly enhances the compatibility of the plasticizers with PVC, the extraction resistance, and the mechanical properties of PVC products. Yin et al.50 synthesized low molecular weight isosorbide adipic acid and isosorbide alcohol suberic acid polyester plasticizer. It is found that this polyester plasticizer has good compatibility with PVC, good heat resistance and improved plasticizing efficiency. Gao et al.51 proposed polyhexyl succinate as a PVC plasticizer. Since polyester has a higher molecular weight and more polar groups, compared with dioctyl phthalate, polyester the interaction with PVC is stronger, giving PVC higher thermal stability and plasticizing efficiency. The above polyester plasticizers are synthesized by melt polymerization, but the production process is complicated or the plasticizer's plasticizing effect is not excellent enough. Therefore, new environmentally friendly polyester plasticizers with good plasticizing effects and simple preparation processes are developed agents are of great significance.52
The plasticizer PHMAZ prepared in this article is a series of new copolyesters synthesized from azelaic acid (AZA), 1,6-hexanediol (HDO) and 2-methyl-1,3-propanediol (MPO). Plasticizer, azelaic acid, also known as “azalea acid”, is often used as a plasticizer and in the chemical synthesis of polyamide resins. Bio-based azelaic acid is mostly extracted from crops such as rye and wheat.53 Currently, bio-based azelaic acid synthesized from vegetable oil has been industrialized.54–57 Azelaic acid polyester is used in the plasticizer industry and is environmentally friendly. Azelaic acid polyester plasticizers are also widely used in film and sheet, cables and wires, coatings, and nylon industries.58–61 The copolyester plasticizer synthesized in this article is a bio-based polyester plasticizer, which is a type of non-toxic, degradable and environmentally friendly plasticizer. It can be used in PVC instead of DOP and meets the requirements of sustainable development.
2. Experimental
2.1. Reagents and instruments
Azelaic acid (AZA), analytical grade, Shanghai Aladdin Biochemical Technology Co., Ltd; 1,6-hexanediol (HDO), analytical grade, Sinopharm Chemical Reagent Co., Ltd; 2-methyl-1,3-propanediol (MPO), analytical grade, Sinopharm Chemical Reagent Co., Ltd; high concentration hydrolysis-resistant titanium catalyst (KBS-4), analytical grade, Titanium Technology (Liaoning) Co., Ltd; polyvinyl chloride (PVC), industrial grade, Shaanxi Northwest Yuan Chemical Group.
ALC-2103 electronic analytical balance, Sartorius Scientific Instruments (Beijing) Co., Ltd; DF-101S instantaneous constant temperature heating magnetic stirrer, Shanghai Lichenbangxi Instrument Technology Co., Ltd; SU-70C internal mixer, Changzhou Suyan Technology Co., Ltd; Bruker Tenso (II) Fourier transform infrared spectrometer, Bruker Company, Germany; DSC-822e differential scanning calorimeter, Mettler Company, Switzerland; AVANCE NEO 400M (Bruker) nuclear magnetic resonance spectrometer, Bruker Company, Germany; XLB-DY flat plate vulcanizing machine, Qingdao Huabo Machinery Technology Co., Ltd; CMT6104 microcomputer controlled electronic universal testing machine, Shenzhen Xinsansi Material Testing Co., Ltd.
2.2. Preparation and structural characterization experiments of azelaic acid copolyester plasticizer
2.2.1. Preparation of azelaic acid copolyester plasticizer. Connect an instant heating magnetic stirrer, a three-necked flask, a thermometer, a condenser, and a nitrogen cylinder in sequence. Then, add bio-based nonanedioic acid, 1,6-hexanediol, and 2-methyl-1,3-propanediol into a 500 ml three-necked flask in an acid-to-alcohol ratio of 1
:
1.1. Place the flask in an oil bath set at 120 °C. Once the chemicals in the flask have completely melted, increase the temperature to 180 °C, activate the magnetic stirring, and add 0.1 wt% of titanate-based catalyst. Start the nitrogen gas flow to carry out the esterification reaction under nitrogen protection. Observe until the water output significantly decreases, then raise the temperature to 190 °C and maintain for 10 minutes until no water is produced, indicating the completion of esterification. The principle of esterification is shown in Fig. 1 and 2, resulting in the final oligomeric polyester plasticizer. A series of new polyester plasticizers PHMAZ was prepared, varying the proportion of MPO in the alcohol, including PHAZ, PHMAZ-15, PHMAZ-20, PHMAZ-25, PHMAZ-30, PHMAZ-45, and PHMAZ-50.
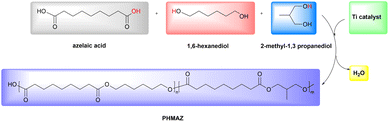 |
| Fig. 1 The esterification principle of PHMAZ. | |
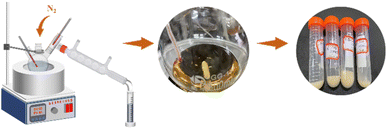 |
| Fig. 2 Copolyester plasticizer preparation process. | |
2.2.2. Plasticizer infrared spectrum test. Fourier transform infrared spectroscopy is used to analyze the structure of polyester, and the wave number range is set to 4000–500 cm−1; before testing the sample, the background spectrum must be scanned to eliminate the influence of humidity and other impurities in the air. The samples can be tested separately, and the background spectrum must be scanned again for each sample tested.
2.2.3. Hydrogen NMR testing of plasticizers. The internal structure of polyester molecules was tested using hydrogen nuclear magnetic resonance spectroscopy, with deuterated chloroform (CDCl3) as the solvent, tetramethylsilane (TMS) as the chemical shift internal standard, and the resonance frequency was 500 MHz.
2.2.4. Molecular weight and distribution testing of plasticizers. In the experiment, gel permeation chromatography was used to detect various molecular weights and molecular weight distributions of copolyester plasticizers. In the experiment, hexafluoroisopropanol (HFIP) was used as the mobile phase, narrow distribution polymethyl methacrylate was used as the standard sample, and the temperature was set at 40 °C for experimental detection.
2.2.5. Analysis of thermal properties of plasticizers. When testing the thermal stability of the polyester plasticizer sample, the temperature was raised from 30 °C to 600 °C at a heating rate of 10 °C min−1 to obtain the thermal weight loss curve (TG) of the plasticized PVC sample. The weight loss curve is differentially processed, and finally the differential thermal weight loss curve (DTG) is obtained.
2.3. Preparation and performance characterization of PVC resin samples plasticized with copolyester plasticizer
2.3.2. Differential scanning calorimetry (DSC) testing of plasticized PVC resin samples. The glass transition temperature was measured using a differential scanning calorimeter. Rise from −60 °C to 190 °C at a heating rate of 10 °C min−1 and stay for 10 minutes. Then reduce the temperature from 190 °C to −60 °C at a cooling rate of 10 °C min−1.
2.3.3. Thermal gravimetric (TG) testing of plasticized PVC resin samples. When testing the thermal stability of PVC samples plasticized with polyester plasticizer, the temperature was raised from 40 °C to 600 °C at a heating rate of 10 °C min−1 to obtain the thermal weight loss curve (TG) of the plasticized PVC samples. Then perform differential processing on the thermogravimetric curve, and finally obtain the differential thermogravimetric curve (DTG).
2.3.4. Mechanical property testing of plasticized PVC resin samples. The tensile properties and elongation at break were tested using a universal testing machine using standard GB/T 1040.2-2006 (50 mm min−1). The mechanical data obtained are the average of at least three test results.
3. Experimental results and discussion
3.1. Copolyester plasticizer test results and analysis
3.1.1. Infrared spectrum and analysis of copolyester plasticizer. Fig. 4 presents the FTIR spectra of PHAZ and PHMAZ-15 to PHMAZ-50. A broad absorption peak at 3500 cm-1 indicates the presence of –OH groups at the polyester chain ends, suggesting that diols were used in excess during the synthesis process, serving as a chain terminator. Near 2930 cm−1, characteristic absorption peaks of methyl and methylene groups on the polyester chains are observed; a strong absorption peak near 1750 cm−1 indicates the intense absorption of the C
O bond; moreover, the strong absorption peak at 1170 cm−1 is a typical feature of C–O–C bond stretching vibrations in esters, further confirming the presence of ester groups. Based on these spectral data, we can preliminarily conclude that the synthesis of PHMAZ copolyesters was successful.
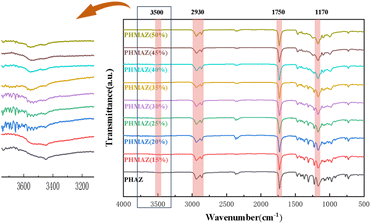 |
| Fig. 4 FTIR spectra of PHAZ and PHMAZ. | |
3.1.2. Nuclear magnetic hydrogen spectra and analysis of plasticizers. In the H NMR spectra (Fig. 6) of the PHAZ and the PHMAZ-15 to PHMAZ-50 series, we observed six distinct hydrogen characteristic peaks corresponding to the hydrogen atoms in positions a, b, c, d, e, and f within the two repeating units A and B as depicted in Fig. 5. Specifically, the peak in the chemical shift range of 2.25 to 2.40 ppm corresponds to the hydrogen atom at position a in repeating unit A; the peak in the range of 1.26 to 1.68 ppm is attributed to the hydrogen atom at position b; the peaks within the range of 3.95 to 4.13 ppm correspond to the two hydrogen atoms at position c in unit A; the peak from 2.10 to 2.23 ppm indicates the hydrogen at position d; the peak ranging from 0.88 to 0.90 ppm identifies the hydrogen at position e; and the peaks from 4.03 to 4.13 ppm reveal the two hydrogen atoms at position f in unit A. The successful detection of these characteristic peaks not only confirms the synthesis of the described copolyester plasticizers but also clearly delineates the structural features within the various repeating units.
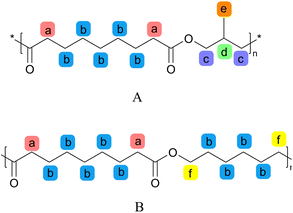 |
| Fig. 5 Two structural units of PHMAZ copolyester. | |
In addition, in the process of melt condensation polymerization to form copolyester, due to the difference in boiling point of raw material acid and alcohol, the degree of volatilization of acid and alcohol with nitrogen is different. Therefore, it is necessary to conduct a detailed study on the molecular chain structure of PHMAZ copolyester with different proportions through NMR spectroscopy to obtain MPO The relationship between the feeding ratio of HDO and the copolymerization ratio in the molecular structure determines whether the synthesized sample meets the experimental needs. In the two repeating structural units A and B, the number of H at the c position in each A repeating structural unit is equal to the number of H at the f position in each B repeating structural unit. Therefore, the H at the c position and the H at the f position The ratio of the number is the ratio of the relative integrated areas of the corresponding peaks, that is, the ratio of the two copolymerized repeating structural units A and B.
In the HNMR analysis results of the PHMAZ-15 sample, the c and f peaks were integrated using MestReNova software. The integration area of the c peak was compared with that of the f peak (if the integration area includes decimals, it is rounded off). From this comparison, the ratio of the two copolymer repeating units, A and B, was calculated to be 1
:
9, leading to the determination that the molar ratio of repeating unit A to the total repeating units is 1
:
10. Similarly, this method can be used to calculate the ratios of other copolymer repeating units within the copolymer. Detailed calculation results are provided in Table 1.
Table 1 Comparison of copolyester feed ratio and copolymerization unit ratio
Sample |
PHAZ |
PHMAZ-15 |
PHMAZ-20 |
PHMAZ-25 |
PHMAZ-30 |
PHMAZ-35 |
PHMAZ-40 |
PHMAZ-45 |
PHMAZ-50 |
Feed ratio [MPO/(MPO + HDO)]/% (mole fraction) |
0 |
15 |
20 |
25 |
30 |
35 |
40 |
45 |
50 |
Copolymer structural unit ratio [A/(A + B)]/% (mole fraction) |
0 |
10.00 |
16.67 |
20.00 |
25.05 |
27.03 |
30.58 |
34.72 |
39.68 |
Table 1 displays the ratios of copolyester raw materials to repeating units for different samples. It is observed that as the amount of MPO increases, the proportion of Type A repeating units also rises correspondingly, indicating that the reaction is proceeding normally. However, it is also evident from the table that the proportion of Type A repeating units consistently remains lower than the addition ratio of MPO. This suggests that in the esterification reaction with nonanedioic acid, MPO is less readily involved compared to 1,6-hexanediol. This phenomenon is also reflected in the preparation process of copolyester plasticizers, where an increase in MPO leads to a corresponding prolongation of the reaction time.
3.1.3. Test analysis of molecular weight and distribution results of copolyester plasticizer. Fig. 7 shows the molecular weight and its distribution results for the synthesized polyester plasticizer samples, which demonstrated that the number average molecular weight of all samples remained below 3000 and exhibited an increasing then decreasing trend. This phenomenon can be attributed to the incremental addition of MPO in the plasticizer, where the increasing presence of methyl groups leads to a weakening of intermolecular forces. Being non-polar, methyl groups reduce the polar interactions between molecules, thereby decreasing the degree of polymerization and resulting in a reduction in molecular weight. Low molecular weight polyester plasticizers more easily intercalate into PVC molecular chains, weakening the interactions between large PVC molecular chains while providing effective lubrication and increasing the mobility of the PVC chains. Consequently, this results in improved plasticizing effects and higher plasticizing efficiency. In contrast, high molecular weight polyester plasticizers struggle to intercalate into PVC molecular chains and fail to provide significant lubrication, hence exhibiting lower plasticizing efficiency. A possible explanation for the increased molecular weight in PHMAZ-50 could be that the increase in methyl groups facilitates mild crosslinking reactions among molecules, forming intermolecular bridges (crosslinking) that subsequently increase the overall molecular weight. As per the data from Fig. 7, the dispersity index of the plasticizer is less than 2, indicating a relatively narrow and uniform molecular weight distribution.
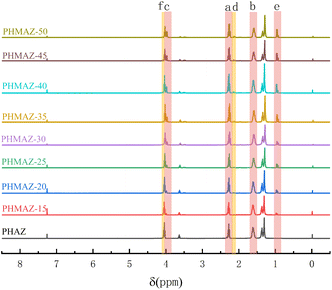 |
| Fig. 6 HNMR spectra of PHAZ and PHMAZ. | |
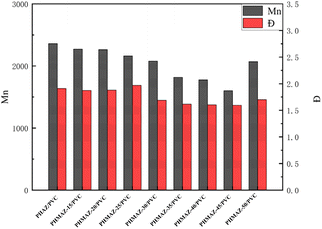 |
| Fig. 7 Molecular weight and molecular weight distribution index graph of polyester plasticizers. | |
3.1.4. Thermogravimetric test results and analysis of copolyester plasticizer. In order to further investigate the thermal performance of the PHMAZ series copolyester plasticizers, this study detailed the analysis of the TG and DTG curves for both PHAZ and PHMAZ series polyester copolyester plasticizers (Fig. 8 and 9). The graphs demonstrate that all samples show good thermal stability before reaching 300 °C, with their mass remaining relatively stable. Analyzing the data from Fig. 8, a significant peak in mass loss was noted between 300 °C and 400 °C, marking the main phase of thermal decomposition for these materials. As the temperature advances beyond 400 °C, the mass loss of the samples tends to halt and stabilizes, indicating that the residual mass remains steady. It is noteworthy that both PHAZ and PHMAZ series display highly similar performance on the TG and DTG curves, suggesting that the introduction of MPO and its concentration variations exert a limited influence on the materials' thermal stability.
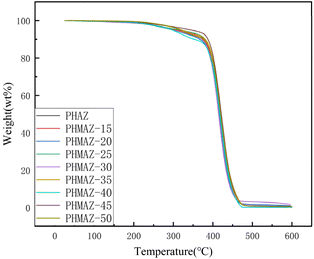 |
| Fig. 8 TG curves of PHAZ and PHMAZ. | |
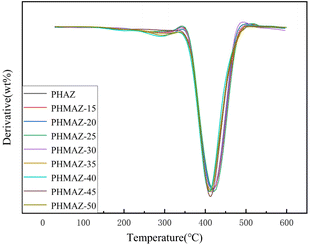 |
| Fig. 9 DTG curves of PHAZ and PHMAZ. | |
Based on the curves in Fig. 8 and 9, the thermal performance data of the copolyester plasticized PVC system are presented in Table 2, where Tonset is the degradation temperature at which the sample degrades by 5 wt%, Tmax is the temperature corresponding to the maximum rate of thermal degradation, and W600°C is the percentage of the residual mass of the sample at 600 °C. The data in the table show that the Tonset, Tmax, and W600°C of PHMAZ copolyester vary minimally with the increase in the content of the MPO.
Table 2 TGA data of copolyester plasticizers
|
PHAZ |
PHMAZ-15 |
PHMAZ-20 |
PHMAZ-25 |
PHMAZ-30 |
PHMAZ-35 |
PHMAZ-40 |
PHMAZ-45 |
PHMAZ-50 |
Tonset/°C |
310.0 |
299.3 |
298.3 |
315.8 |
298.3 |
322.7 |
295.2 |
341.1 |
317.6 |
Tmax/°C |
424.1 |
423.6 |
421.0 |
424.8 |
420.0 |
412.1 |
411.3 |
418.1 |
418.0 |
W600°C/% |
0.7 |
1.1 |
0.9 |
0. 48 |
1.6 |
0.6 |
0.48 |
0.5 |
0.6 |
In conclusion, this indicates that the addition of MPO and its concentration variations have limited impact on the thermal stability of the PHMAZ series copolyester plasticizers, which exhibit good thermal stability and thermal decomposition performance.
3.2. Plasticized PVC resin sample test results and analysis
3.2.1. DSC test results and analysis of plasticized PVC resin samples. Fig. 10 shows the DSC thermograms of PVC samples plasticized with PHAZ and the PHMAZ-15 to PHMAZ-50 series. The glass transition temperatures of PVC samples treated with the PHMAZ series plasticizers are roughly −35 °C, significantly lower than those plasticized with PHAZ. This observation suggests that the addition of MPO decreases the glass transition temperature of the plasticized PVC samples. In conjunction with the measured molecular weights of the plasticizers, depicted in Fig. 8, the incorporation of MPO leads to a reduction in both the molecular weight of the plasticizers and their glass transition temperatures. This is because plasticizer molecules with lower molecular weights have a greater free volume, which allows the ends of the molecular chains to move more freely, resulting in a lower glass transition temperature. Conversely, higher molecular weight plasticizers increase molecular entanglement, which hinders the movement of the molecular chains, thus leading to a higher glass transition temperature.
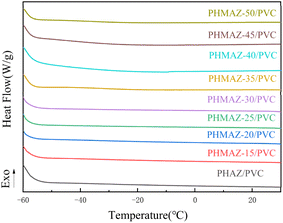 |
| Fig. 10 DSC curves of PHAZ and PHMAZ plasticized PVC samples. | |
3.2.2. Thermogravimetric test results and analysis of plasticized PVC resin samples. Fig. 12 and 13 show the TG and DTG curves for PVC samples labeled PHAZ, and PHMAZ-15 to PHMAZ-50, across a temperature range from 0 °C to 600 °C. The graphs reveal that all samples maintain a relatively stable mass until about 250 °C with no significant weight loss observed. This phase of stability indicates that these materials might exhibit stable performance at normal operating temperatures. However, as the temperature continues to rise from 250 °C to 500 °C, the mass of all samples declines rapidly, with two distinct peaks visible between 250 °C and 500 °C in Fig. 11, representing the decomposition of PVC and the plasticizer respectively. This thermal behavior suggests that the materials begin to lose their structural integrity, which requires careful temperature monitoring in practical applications. Above 500 °C, the mass of all samples approaches stability. The TG and DTG curves of both the PHAZ and PHMAZ series show highly similar behaviors, indicating that the addition of MPO does not affect the thermal performance of the plasticized PVC.
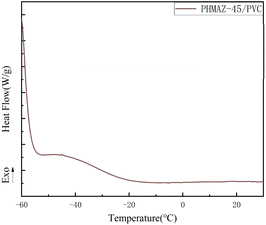 |
| Fig. 11 DSC curve of PHMAZ-45 plasticized PVC sample. | |
According to the curves from Fig. 12 and 13, the thermal performance data for the polyester-plasticized PVC system is as presented in Table 3, which includes Tonset (the temperature at which 5 wt% of the sample has degraded), Tmax (the temperature corresponding to the maximum rate of thermal degradation), and W600°C (the percentage of the sample's residual mass at 600 °C). The data show minor variations in Tonset, Tmax, and W600°C with increasing content of the modifying third monomer MPO.
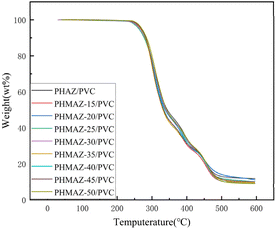 |
| Fig. 12 TG curves of PVC samples plasticized by PHAZ and PHMAZ. | |
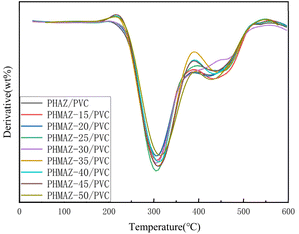 |
| Fig. 13 DTG curves of PVC samples plasticized by PHAZ and PHMAZ. | |
Table 3 TGA data of plasticizer PVC samples
|
PHAZ |
PHMAZ-15/PVC |
PHMAZ-20/PVC |
PHMAZ-25/PVC |
PHMAZ-30/PVC |
PHMAZ-35/PVC |
PHMAZ-40/PVC |
PHMAZ-45/PVC |
PHMAZ-50/PVC |
T10%/°C |
277.2 |
279.8 |
280.1 |
280.2 |
280.8 |
267.3 |
268.3 |
269.1 |
270.1 |
T50%/°C |
340.2 |
339.2 |
344.7 |
333.4 |
339.1 |
308.1 |
310.3 |
310.3 |
312.4 |
W600°C/% |
10.1 |
9.1 |
11.9 |
9.1 |
11.2 |
9.5 |
9.1 |
10.1 |
9.0 |
In summary, this indicates that the addition of MPO and variations in its content have a limited impact on the thermal stability of the PVC plasticized with the PHMAZ series copolyester plasticizers.
3.2.3. Test results and analysis of mechanical properties of plasticized PVC resin samples. Fig. 14 shows the tensile strength and elongation at break data for PVC samples treated with PHAZ and PHMAZ-15 to PHMAZ-50 plasticizers, as tested using a universal testing machine. The data reveals that the elongation at break exhibits an initial increase followed by a decrease with rising MPO content, with PHMAZ-45/PVC achieving the highest average elongation at break of 908.4%. This indicates that the plasticizing effect improves and then diminishes as the ratio of MPO containing methyl groups increases, with the optimal plasticizing performance observed in PHMAZ-45. This phenomenon could be due to the non-polar methyl functional groups in the MPO side chains enhancing the volumetric effect of the plasticizer, thereby improving the plasticizing effect. However, when the methyl content becomes excessive, the flexible segments in the polyester chain are significantly reduced, and the polarity of the low molecular weight polyester increases, consequently reducing the plasticizing effect.
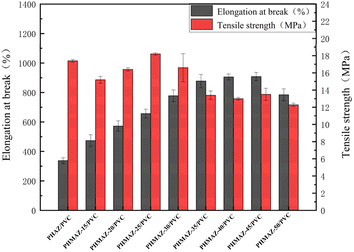 |
| Fig. 14 Mechanical properties graph of PVC samples plasticized with PHAZ and PHMAZ. | |
The mechanical property values are summarized in Table 4. The tensile properties can directly explain the flexibility of the plasticized PVC splines, while the elongation at break can directly reflect the plasticizing effect of the plasticizer of the plasticized PVC splines. There are generally two methods for calculating plasticization efficiency. One is based on the elongation at break. The other is based on the glass transition temperature. Since it is difficult to measure the glass transition temperature of plasticized PVC samples, this experiment uses the elongation at break to achieve plasticizing efficiency. Calculate that on the premise that the elongation at break of pure PVC is 0, the ratio of the elongation at break of PVC plasticized by polyester plasticizer to the elongation at break of DOP plasticized PVC is the elongation of polyester plasticizer. Plastic efficiency, the calculation formula is as follows:
Table 4 Mechanical property date of plasticizers
|
Stress/MPa |
Strain/% |
EΔεμ/% |
PHAZ/PVC |
17.4 |
337.9 |
94.6 |
PHMAZ-15/PVC |
15.2 |
473.7 |
132.7 |
PHMAZ-20/PVC |
16.4 |
572.6 |
160.4 |
PHMAZ-25/PVC |
18.2 |
676.9 |
189.6 |
PHMAZ-30/PVC |
16.6 |
798.0 |
223.5 |
PHMAZ-35/PVC |
13.4 |
877.6 |
245.8 |
PHMAZ-40/PVC |
13 |
905.8 |
253.7 |
PHMAZ-45/PVC |
13.5 |
908.4 |
254.4 |
PHMAZ-50/PVC |
12.28 |
784.7 |
219.8 |
Among them, is the plasticizing efficiency, is the elongation at break of PVC after plasticizing with polyester plasticizer, is the elongation at break of PVC after plasticizing with DOP (calculated based on the elongation at break of DOP/PVC sample of 357%).
Table 4 presents the mechanical performance data of PVC samples treated with different plasticizers, including tensile strength, elongation at break, and plasticization efficiency. The data reveal that variations in MPO content within the PHMAZ series of plasticizers significantly affect the plasticizing effect on PVC samples. Notably, the PVC samples plasticized with PHMAZ-45 exhibit an elongation at break as high as 908.4% and a plasticization efficiency reaching 254.5%, demonstrating the most effective plasticization performance.
4. Conclusions
In the esterification reaction of nonanedioic acid, MPO is more difficult to participate compared to 1,6-hexanediol. This is reflected in the preparation of copolyester plasticizers, where the product content of the MPO esterification reaction with nonanedioic acid remains consistently lower than the amount of MPO added, and the reaction time extends as the MPO content increases.
As the content of MPO in the PHMAZ series of copolyester plasticizers increases, their molecular weight decreases, making these plasticizers more easily insertable into the PVC molecular chains. This change reduces intermolecular interactions and enhances the mobility of the chains, thereby effectively improving the plasticizing effect and efficiency. Conversely, plasticizers with higher molecular weights find it difficult to achieve this effect. As for PHMAZ-50, its increased molecular weight may be due to the introduction of methyl groups that cause slight cross-linking reactions between molecules, thereby increasing the overall molecular weight.
Both the TG and DTG curves of the PHMAZ series copolyester plasticizers and those of the plasticized PVC samples show a high degree of similarity, indicating that the added amount of MPO does not significantly affect the thermal performance or the plasticizing effect of the copolyester plasticizers. Additionally, the PHMAZ series copolyester plasticizers exhibit good thermal stability.
Variations in MPO content within the PHMAZ series of plasticizers significantly affect the plasticizing effect on PVC samples. Notably, the PVC samples plasticized with PHMAZ-45 exhibit an elongation at break as high as 908.4% and a plasticization efficiency reaching 254.5%, demonstrating the most effective plasticization performance.
In conclusion, the synthesized copolyester plasticizer PHMAZ offers significant advantages such as simplicity of synthesis and controllable processes. It effectively lowers the glass transition temperature of plasticized PVC materials and enhances the mechanical properties of PVC, providing excellent plasticizing effects. Among them, PHMAZ-45 shows the best plasticizing effects; its elongation at break increased by more than double compared to the DOP/PVC sample, which had an elongation at break of 357%. Therefore, PHMAZ copolyester plasticizers hold the potential to replace DOP in the plasticization of PVC materials, leading to industrial applications.
Data availability
The raw/processed data required to reproduce these findings cannot be shared at this time as the data also form part of an ongoing study.
Author contributions
Conceptualization: Liyan Wang and Hong Chen; writing – original draft: Wanjing Zhang and Liying Guo; writing – review & editing: Yaoyao Bai and Xin Qiao.
Conflicts of interest
There are no conflicts to declare.
Acknowledgements
This work was supported by the National Natural Science Foundation of China (22278271), Liaoning Shengda Environmental Resources Group Co., Ltd.
References
- D. Garcia, R. Balart, J. E. Crespo and J. Lopez, Mechanical properties of recycled PVC blends with styrenic polymers, J. Appl. Polym. Sci., 2006, 101(4), 2464–2471 CrossRef CAS.
- N. Yarahmadi, I. Jakubowicz and L. Martinsson, PVC floorings as post-consumer products for mechanical recycling and energy recovery, Polym. Degrad. Stab., 2003, 79(3), 439–448 CrossRef CAS.
- D. Braun, PVC—origin, growth, and future, J. Vinyl Addit. Technol., 2001, 7(4), 168–176 CrossRef CAS.
- G. Matuschek, N. Milanov and A. Kettrup, Thermoanalytical investigations for the recycling of PVC, Thermochim. Acta, 2000, 361(1–2), 77–84 CrossRef CAS.
- N. Sombatsompop and S. Thongsang, Rheology, morphology, and mechanical and thermal properties of recycled PVC pipes, J. Appl. Polym. Sci., 2001, 82(10), 2478–2486 CrossRef CAS.
- M. J. Slapak, J. M. van Kasteren and B. A. Drinkenburg, Hydrothermal recycling of PVC in a bubbling fluidized bed reactor: the influence of bed material and temperature, Polym. Adv. Technol., 1999, 10(10), 596–602 CrossRef CAS.
- D. Braun, Recycling of PVC, Prog. Polym. Sci., 2002, 27(10), 2171–2195 CrossRef CAS.
- S. Nakamura, K. Nakajima, Y. Yoshizawa, K. Matsubae-Yokoyama and T. Nagasaka, Analyzing polyvinyl chloride in Japan with the waste input− output material flow analysis model, J. Ind. Ecol., 2009, 13(5), 706–717 CrossRef CAS.
- Z. Xiaodan, Y. Xu and X. Shiai, Preparation and application in PVC of novel organic/inorganic composite UV absorber, J. Funct. Polym., 2019, 32(3), 398–404 Search PubMed.
- N. Ranjan, Chitosan with PVC polymer for biomedical applications: a bibliometric analysis, Mater. Today: Proc., 2023, 81, 894–898 CAS.
- J. Li, S.-H. Jin, G.-C. Lan, Z.-S. Xu, L.-T. Wang and N. Wang, et al., Research on the glass transition temperature and mechanical properties of poly (vinyl chloride)/dioctyl phthalate (PVC/DOP) blends by molecular dynamics simulations, Chin. J. Polym. Sci., 2019, 37, 834–840 CrossRef CAS.
- C. Xue, H. Nan, Y. Lu, H. Chen, C. Zhao and S. Xu, Effects of inorganic-organic surface modification on the mechanical and thermal properties of poly (vinyl chloride) composites reinforced with fly-ash, Polym. Compos., 2021, 42(4), 1867–1877 CrossRef CAS.
- O. K. Gohatre, M. Biswal, S. Mohanty and S. K. Nayak, Study on thermal, mechanical and morphological properties of recycled poly (vinyl chloride)/fly ash composites, Polym. Int., 2020, 69(6), 552–563 CrossRef CAS.
- F. P. La Mantia, Recycling of PVC and Mixed Plastic Waste, ChemTec Publishing, 1996 Search PubMed.
- S. Moulay, Chemical modification of poly (vinyl chloride)—Still on the run, Prog. Polym. Sci., 2010, 35(3), 303–331 CrossRef CAS.
- Y. Ma, S. Liao, Q. Li, Q. Guan, P. Jia and Y. Zhou, Physical and chemical modifications of poly (vinyl chloride) materials to prevent plasticizer migration-Still on the run, React. Funct. Polym., 2020, 147, 104458 CrossRef CAS.
- C. Wang, Y. Han, W. Wang, J. Liu, N. Wang and B. Hou, Polyvinyl chloride/epoxy double layer powder coating enhances coating adhesion and anticorrosion protection of substrate, Prog. Org. Coat., 2021, 158, 106335 CrossRef CAS.
- D. Garcia, R. Balart, L. Sanchez and J. Lopez, Compatibility of recycled PVC/ABS blends. Effect of previous degradation, Polym. Eng. Sci., 2007, 47(6), 789–796 CrossRef CAS.
- F. Burat, A. Güney and M. O. Kangal, Selective separation of virgin and post-consumer polymers (PET and PVC) by flotation method, Waste Manage., 2009, 29(6), 1807–1813 CrossRef CAS PubMed.
- F. Chiellini, M. Ferri, A. Morelli, L. Dipaola and G. Latini, Perspectives on alternatives to phthalate plasticized
poly (vinyl chloride) in medical devices applications, Prog. Polym. Sci., 2013, 38(7), 1067–1088 CrossRef CAS.
- E. Linde and U. W. Gedde, Plasticizer migration from PVC cable insulation–The challenges of extrapolation methods, Polym. Degrad. Stab., 2014, 101, 24–31 CrossRef CAS.
- M. C. Fernandes, V. A. Pereira, A. C. Fonseca, A. Ramalho, J. F. Coelho and R. Barros, et al., Synthesis and characterization of biobased polyester PVC plasticizers to industrial manufacturing of tubes, J. Appl. Polym. Sci., 2021, 138(37), 50941 CrossRef CAS.
- B. Shah and V. Shertukde, Effect of plasticizers on mechanical, electrical, permanence, and thermal properties of poly (vinyl chloride), J. Appl. Polym. Sci., 2003, 90(12), 3278–3284 CrossRef CAS.
- A. Hamid, M. Khan, F. Hussain, A. Zada, T. Li and D. Alei, et al., Synthesis and physiochemical performances of PVC-sodium polyacrylate and PVC-sodium polyacrylate-graphite composite polymer membrane, Z. Phys. Chem., 2021, 235(12), 1791–1810 CrossRef CAS.
- X. Zhang, Z. Mao and J. Zhang, Significant improvement of the low-temperature toughness of PVC/ASA/NBR ternary blends through the concept of mismatched thermal expansion coefficient, J. Polym. Eng., 2019, 39(10), 902–908 CrossRef CAS.
- K. Gaurav, R. Singh, B. K. Tiwari and R. Srivastava, Novel proton exchange membranes based on PVC for microbial fuel cells (MFCs), J. Polym. Eng., 2019, 39(4), 360–367 CrossRef CAS.
- M. Singh, D. Somvanshi, R. K. Singh, A. K. Mahanta, P. Maiti and N. Misra, et al., Functionalized polyvinyl chloride/layered double hydroxide nanocomposites and its thermal and mechanical properties, J. Appl. Polym. Sci., 2020, 137(27), 48894 CrossRef CAS.
- X. Wang, M. Song, S. Liu, S. Wu and A. M. Thu, Analysis of phthalate plasticizer migration from PVDC packaging materials to food simulants using molecular dynamics simulations and artificial neural network, Food Chem., 2020, 317, 126465 CrossRef CAS PubMed.
- A. Descat, M. Lecoeur, M. Kouach, L. Goossens, T. Aurélie. and P. Odou, et al., Simultaneous determination of di(2-ethylhexyl) phthalate and diisononylcyclohexane-1,2-dicarboxylate and their monoester metabolites in four labile blood products by liquid chromatography tandem mass spectrometry, J. Pharm. Biomed. Anal., 2020, 181, 113063 CrossRef CAS PubMed.
- E. H. Immergut and H. F. Mark, Principles of Plasticization, ACS Publications, 1965 Search PubMed.
- H. B. Pyeon, J. E. Park and D. H. Suh, Non-phthalate plasticizer from camphor for flexible PVC with a wide range of available temperature, Polym. Test., 2017, 63, 375–381 CrossRef CAS.
- J. S. Choi and W. H. Park, Effect of biodegradable plasticizers on thermal and mechanical properties of poly (3-hydroxybutyrate), Polym. Test., 2004, 23(4), 455–460 CrossRef CAS.
- G. Szarka and B. Iván, Thermal properties, degradation and stability of poly (vinyl chloride) predegraded thermooxidatively in the presence of dioctyl phthalate plasticizer, J. Macromol. Sci., Part A, 2013, 50(2), 208–214 CrossRef CAS.
- L. J. Stolp, M. Grass and D. R. Kodali, Castor Epoxy Fatty Acid Alkyl Ester Estolides as Bioplasticizers for Poly (Vinyl Chloride), J. Am. Oil Chem. Soc., 2021, 98(3), 297–304 CrossRef CAS.
- H. Tong and J. Hai, Sustainable synthesis of bio-based hyperbranched ester and its application for preparing soft polyvinyl chloride materials, Polym. Int., 2019, 68(3), 456–463 CrossRef CAS.
- C. Jie, L. Zengshe and N. Xiaoan, et al., Synthesis and application of a novel environmental plasticizer based on cardanol for poly (vinyl chloride), J. Taiwan Inst. Chem. Eng., 2016, 65, 488–497 CrossRef.
- T. T. Bui, G. Giovanoulis, A. P. Cousins, J. Magnér, I. T. Cousins and C. A. de Wit, Human exposure, hazard and risk of alternative plasticizers to phthalate esters, Sci. Total Environ., 2016, 541, 451–467 CrossRef CAS PubMed.
- Y.-M. Lee, J.-E. Lee, W. Choe, T. Kim, J.-Y. Lee and Y. Kho, et al., Distribution of phthalate esters in air, water, sediments, and fish in the Asan Lake of Korea, Environ. Int., 2019, 126, 635–643 CrossRef CAS PubMed.
- Z.-M. Zhang, H.-H. Zhang, Y.-W. Zou and G.-P. Yang, Distribution and ecotoxicological state of phthalate esters in the sea-surface microlayer, seawater and sediment of the Bohai Sea and the Yellow Sea, Environ. Pollut., 2018, 240, 235–247 CrossRef CAS PubMed.
- Q. Zhang, J. Song, X. Li, Q. Peng, H. Yuan and N. Li, et al., Concentrations and distribution of phthalate esters in the seamount area of the Tropical Western Pacific Ocean, Mar. Pollut. Bull., 2019, 140, 107–115 CrossRef CAS PubMed.
- K. Khosravi and G. W. Price, Determination of phthalates in soils and biosolids using accelerated solvent extraction coupled with SPE cleanup and GC–MS quantification, Microchem. J., 2015, 121, 205–212 CrossRef CAS.
- D. Y. Kim, G. H. Kim, G. M. Nam, D. G. Kang and K. H. Seo, Oil resistance and low-temperature characteristics of plasticized nitrile butadiene rubber compounds, J. Appl. Polym. Sci., 2019, 136(32), 47851 CrossRef.
- D. Lithner, Å. Larsson and G. Dave, Environmental and health hazard ranking and assessment of plastic polymers based on chemical composition, Sci. Total Environ., 2011, 409(18), 3309–3324 CrossRef CAS PubMed.
- C. J. Hines, N. B. Hopf, J. A. Deddens, M. J. Silva and A. M. Calafat, Occupational exposure to diisononyl phthalate (DiNP) in polyvinyl chloride processing operations, Int. Arch. Occup. Environ. Health, 2012, 85, 317–325 CrossRef CAS PubMed.
- M. C. Fernandes, V. A. Pereira, A. C. Fonseca, A. Ramalho, J. F. Coelho and R. Barros, et al., Synthesis and characterization of biobased polyester PVC plasticizers to industrial manufacturing of tubes, J. Appl. Polym. Sci., 2021, 138(37), 50941 CrossRef CAS.
- J. Choi and S. Y. Kwak, Hyperbranched poly(epsilon-caprolactone) as a nonmigrating alternative plasticizer for phthalates in flexible PVC, Environ. Sci. Technol., 2007, 41(10), 3763–3768 CrossRef CAS PubMed.
- W. He, G. Zhu, Y. Gao, H. Wu, Z. Fang and K. Guo, Green plasticizers derived from epoxidized soybean oil for poly (vinyl chloride): continuous synthesis and evaluation in PVC films, Chem. Eng. J., 2020, 380, 122532 CrossRef.
- A. Lindström and M. Hakkarainen, Miscibility and surface segregation in PVC/polyester blends—The influence of chain architecture and composition, J. Polym. Sci., Part B: Polym. Phys., 2007, 45(13), 1552–1563 CrossRef.
- A. Lindström and M. Hakkarainen, Environmentally friendly plasticizers for poly (vinyl chloride)—Improved mechanical properties and compatibility by using branched poly (butylene adipate) as a polymeric plasticizer, J. Appl. Polym. Sci., 2006, 100(3), 2180–2188 CrossRef.
- B. Yin and M. Hakkarainen, Oligomeric isosorbide esters as alternative renewable resource plasticizers for PVC, J. Appl. Polym. Sci., 2010, 119(4), 2400–2407 CrossRef.
- C. Gao, X. Zhang, J. Sun, Z. Yuan, S. Han and Y. Liu, et al., Poly (hexane succinate) plasticizer designed for poly (vinyl chloride) with a high efficiency, nontoxicity, and improved migration resistance, J. Appl. Polym. Sci., 2018, 135(25), 46388 CrossRef.
- J. E. Koroly and E. M. Beavers, Polymeric plasticizers-preparation and characterization of a series of terminated polyesters, Ind. Eng. Chem., 1953, 45(5), 1060–1063 CrossRef CAS.
- E. Brenna, D. Colombo, G. Di Lecce, F. G. Gatti, M. C. Ghezzi and F. Tentori, et al., Conversion of oleic acid into azelaic and pelargonic acid by a chemo-enzymatic route, Molecules, 2020, 25(8), 1882 CrossRef CAS PubMed.
- G. A. D. L. Izeppi, J.-L. Dubois, A. Balle and A. Soutelo-Maria, Economic risk assessment using Monte Carlo simulation for the production of azelaic acid and pelargonic acid from vegetable oils, Ind. Crops Prod., 2020, 150, 112411 CrossRef.
- A. Bieser, G. Borsotti, F. Digioia, A. Ferrari and A. Pirocco, Continuous process for the production of derivatives of
saturated carboxylic acids, US Pat., 8846962, 2014 Search PubMed.
- C. Bastioli, G. Borsotti, A. Merlin and T. Milizia, Process for the catalytic cleavage of vegetable oils, US Pat., 8222438, 2012 Search PubMed.
- E.-J. Seo, Y. J. Yeon, J.-H. Seo, J.-H. Lee, J. P. Boñgol and Y. Oh, et al., Enzyme/whole-cell biotransformation of plant oils, yeast derived oils, and microalgae fatty acid methyl esters into n-nonanoic acid, 9-hydroxynonanoic acid, and 1, 9-nonanedioic acid, Bioresour. Technol., 2018, 251, 288–294 CrossRef CAS PubMed.
- A. Todea, C. Deganutti, M. Spennato, F. Asaro, G. Zingone and T. Milizia, et al., Azelaic acid: a bio-based building block for biodegradable polymers, Polymers, 2021, 13(23), 4091 CrossRef CAS PubMed.
- M. N. Baharu, A. A. H. Kadhum, A. A. Al-Amiery and A. B. Mohamad, Synthesis and characterization of polyesters derived from glycerol, azelaic acid, and succinic acid, Green Chem. Lett. Rev., 2015, 8(1), 31–38 CrossRef CAS.
- R. Frische, K. Hegwein and J. Volkheimer, Method of producing dicarboxylic acids suitable for synthesis of polymers or polyamides, US Pat., 6362368, 2002 Search PubMed.
- A. Kulik, A. Martin, M.-M. Pohl, C. Fischer and A. Köckritz, Insights into gold-catalyzed synthesis of azelaic acid, Green Chem., 2014, 16(4), 1799–1806 RSC.
|
This journal is © The Royal Society of Chemistry 2024 |
Click here to see how this site uses Cookies. View our privacy policy here.