DOI:
10.1039/D4RA04601C
(Paper)
RSC Adv., 2024,
14, 30886-30895
The development of anti-freezing and anti-evaporating conductive organohydrogel for flexible strain-sensing electronic devices
Received
24th June 2024
, Accepted 23rd September 2024
First published on 27th September 2024
Abstract
The hydrogels got hot attention from the researchers due to their excellent flexibility, mechanical properties, conductivity, and response to external stimuli, however, their applications are hampered due to a lack of water retention properties and anti-freezing ability. In this study, the organohydrogel was designed from the two solvents system (DMSO and water) in which acrylamide (Amm) and acrylic acid (AA) work as monomers and Arabic gum (AG) works as biopolymers. The functional groups, surface morphology, mechanical properties, rheological properties, anti-freezing properties, and strain-sensing properties of the fabricated organohydrogel were studied. The DMGA6 organohydrogel showed good mechanical properties with fracture stress of 197 kPa, fracture strain of 593%, cyclic stability to five cycles at 400% strain without relaxation time, excellent rheological performance (elastic behavior), anti-freezing properties (−54.6 °C), the response time of 65 ms with a gauge factor of 8.86 at 500% strain. The organohydrogel can detect different human motions like bending of the finger, elbow, neck, and wrist at normal and harsh temperatures. Additionally, the organohydrogel can also detect the mood of humans, etc. The designed organohydrogels can be used in strain-sensing smart electronic devices for writing, drawing, etc. as an electronic pen.
1. Introduction
The strain-sensing devices received considerable attention from scientists in the field of human motion monitoring,1 artificial intelligence,2 human health, soft robotics,3,4 and electronic skin5,6 which convert the mechanical deformation into measurable electrical signals and record them in real-time.7 However, there are strain-sensing materials used that are not valuable in the case of conduction, softness, stretchability, time response, and durability. Therefore, hydrogels were designed to fulfill the above demands and can be easily used for strain-sensing purposes.8
Hydrogels are soft materials characterized by a three-dimensional (3D) network structure, known for their flexibility, stretchability, conductivity, and excellent biocompatibility.9 Due to these properties, they hold significant potential as the next generation of flexible strain sensors.10 However, conventional hydrogels typically have weak mechanical strength, largely because of their high water content, which considerably restricts their practical applications.11
Many methods have been developed recently by researchers to enhance the mechanical characteristics of hydrogels.12 Creating a multi-layer network is an easy and efficient method.13–16 Liu and colleagues synthesized multi-networked composite hydrogels consisting of bio-derived phytic acid (PA), chitosan (CS), and polyvinyl alcohol (PVA). In this structure, the first cross-linked network formed through interactions between the hydroxyl groups of PVA. The second network arose from the bonding between PA and the hydroxyl groups of PVA, while the third network resulted from the interaction between the amide groups of PA and CS. These composite hydrogels demonstrated strong mechanical properties, rapid response time, and recyclability.17 Nevertheless, these composite hydrogels mainly suffer from low stretchability and bear a large hysteresis loop because the inorganic nano-particles usually cannot distribute uniformly and aggregate easily in the polymer network.14,18 Therefore, fabricating a hydrogel-based strain sensor simultaneously with excellent self-recovery property, high stretchability and mechanical strength still remains a challenge.
Furthermore, the mechanical characteristics of the hydrogels can be efficiently enhanced through immersion in solution of salt or through the simple addition of salt ions, therefore increasing the inter-substrate interaction via the salting effect.17 However, their use at high and low temperatures is limited due to the lack of anti-evaporating and anti-freezing abilities. The researchers are trying to develop such types of hydrogels that can be used in harsh conditions like at high and low temperatures conditions.19 The hydrogels in which only water is used as a solvent, can easily dried (at high temperature) and frozen (at low temperature) when exposed to the open environment and therefore denied the application in strain sensing devices.20 Previously, different types of solvents were used like dimethyl sulfoxide (DMSO) and glycerin which convert the hydrogel concept to organohydrogel or organogel, which enhanced and reduced its boiling point and freezing point respectively.21,22
The challenging problem for the organohydrogel is its mechanical and conducting properties. The poor mechanical and conducting properties hampered its practical applications. The introduction of biopolymers like Arabic gum (AG) having multiple hydroxyl groups increases the cross-linking densities and mechanical properties.23 Furthermore, sensing occurred based on conducting materials, AlCl3. Al3+ was not only involved in the installment of conducting abilities but also increased mechanical properties due to the formation of interaction with hydroxyl groups of AG, acrylic acid (AA),24,25 and amide group of acrylamides (Amm).26
Herein, a novel anti-freezing and anti-evaporating organohydrogel was designed through one pot free radical polymerization, in which ammonium per sulphate (APS) was used as an initiating moiety. The APS polymerized the monomer acrylamide and acrylic acid. The DMSO and water were used as a double solvent system with a ratio of 1
:
4, which converts the hydrogel system into organohydrogel. Aluminum ion (Al3+) was added which not only involved the conducting properties of the organohydrogel but also enhanced the mechanical properties by interaction with acrylamide (Amm), acrylic acid (AA), and biopolymer Arabic gum (AG). By adding the AG to the polymeric system its mechanical properties were increased.
2. Materials and preparation of organohydrogel
2.1. Materials
Acrylic acid (AA) was purchased from Deajung, acrylamide (Amm) was obtained from Acros organic, Arabic gum (AG) and ammonium per sulphate (APS) were purchased from Sigma Aldrich, aluminum chloride (AlCl3) and dimethyl sulfoxide (DMSO) were purchased from Scharlau and deionized water was synthesized in the polymer laboratory. All the chemicals were analytical grade and used without any further purification.
2.2. Preparation of organohydrogel
The organohydrogel (OH) was prepared by one pot-free radical polymerization where two solvents (distilled water and DMSO with a 4
:
1 ratio) were selected. 0.5 g of AlCl3 was added to the two solvent systems, after the dissolution of AlCl3, 2 g of acrylamide (Amm) and 500 μL acrylic acid (AA) were added to the system. To prevent agglomeration, the biopolymer Arabic gum (AG) was slowly added to the solution. When all the components were completely dissolved 0.07 g ammonium persulphate (APS) was added and stirred until all the chemicals were dissolved. After that organohydrogel was poured into a plastic mold having 7 cm length and 3 cm width and placed in the oven at 60 °C for 1.5 h to complete polymerization. After polymerization, the organohydrogels were passed through three freeze and thaw cycles for 3 h at room temperature and 0 °C. The organohydrogels were then stored in the sample bags for characterization and applications. For comparison, different percentages of organohydrogels were synthesized concerning AG. The 0, 2, 4, and 6 (DMGA0, DMGA2, DMGA4, and DMGA6) in the organohydrogels showed the percent amount of the AG concerning Amm. For the comparison of the anti-freezing and anti-evaporating properties, a hydrogel without DMSO was also prepared to keep other compositions the same as DMGA6.
2.3. Mechanical testing
To investigate the mechanical properties of the organohydrogel, the universal testing machine (UTM, testometric, England with 500 kg load cell) was used at ambient temperature. The organohydrogel was cut in known dimensions of 40 mm length, 10 mm width, and 1 mm thickness. The test speed was 50 mm/mint. The toughness of the organohydrogel was determined through stress–strain curve by applying eqn (1) and the young modulus was determined from the stress–strain curve from 0% strain to 25% strain. The cyclic and anti-fatigue resistance of the synthesized organohydrogel were investigated by passing the samples through different cycles at different strains. The dissipated energy of the fabricated gels was measured from the cyclic stress–strain curve by applying eqn (2); |
 | (1) |
|
 | (2) |
In the above equations, the U indicates the toughness of the organohydrogel, σ shows the stress applied on the gel, ε is the strain while the ΔU showed dissipated energy obtained from the loading and unloading of the organohydrogel.
2.4. Rheological study
To report the viscoelastic behavior of the designed organohydrogel, the gel was passed through Anton paar rheometer (Physica MCR 301) with tool cell 25 mm. Two tests were conducted, the frequency sweep at the range of 0.1 rad s−1 to 100 rad s−1 and the amplitude sweep from 0.01 to 1000% strain at ambient temperature.
2.5. Water retention test of organohydrogel
To study the water retention performance, the organohydrogel was kept in an open environment for 20 days and the water retention capacity was determined by using eqn (3); |
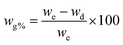 | (3) |
where wg% is the remaining percent weight of the gel, we are the weight before and wd is the weight after drying.
The anti-freezing properties of the organohydrogels were studied through differential Scanning calorimetry (DSC TA Q20). The organohydrogels were cooled from 20 °C to −60 °C at the rate of 10 °C per mint, maintained for 5 minutes, and then heated up to 20 °C at the same rate under a nitrogen atmosphere.
2.6. Porosity and functional groups study
The surface morphology and porosity of the fabricated organohydrogels were analyzed through scanning electron microscopy (SEM, Joel, Japan). The functional group verification inside the organohydrogels was confirmed from the Fourier-transformed infrared spectroscopy (FTIR) at 400 cm−1 to 4000 cm−1 (PerkinElmer). For the SEM and FTIR analysis, the samples were dried through freeze and thaw cycles.
2.7. Strain sensing performances of organohydrogel
The sensing properties and human motion of the synthesized gel were studied by designing an electrode system through an electrochemical workstation (Netherlands). The organohydrogels were cut in rectangular shapes with 5 mm width, 15 mm length, and 1 mm thickness. For the human motion gel was attached to the different parts of the human and connected to AUTOLAB. The current was converted into resistance through Ohm's law and further, the resistance was converted into relative resistance by following eqn (4). |
 | (4) |
where ΔR is the relative resistance, R is the resistance at% strain while Ro is the resistance at 0% strain.
3. Results and discussion
In the formation of organohydrogel, water, and DMSO were used as a dual solvent system with a 4
:
1 ratio. The addition of DMSO brings excellent water retention behavior in the hydrogel. DMSO has lone pair electrons on oxygen atoms which interact with the hydrogen of the water molecule and make the organohydrogel environmentally stable and tolerant.27 Both Amm and AA undergo polymerization at 60 °C after the addition of APS to the reaction mixture.28,29 A biopolymer Arabic gum (AG) is involved in the physical cross-linking with Amm and AA, resulting in the interpenetrating network (Fig. 1a). The introduction of Al3+ not only involves the improvement of electrical properties of the organohydrogel but also interacts with the carbonyl group of AA, amide group of Amm, and hydroxyl groups of AG to further boost the mechanical properties of the organohydrogels30,31 (Fig. 1b). The AG contains a large number of hydroxyl groups which involved in the non-covalent bond (hydrogen bonding) formation.32
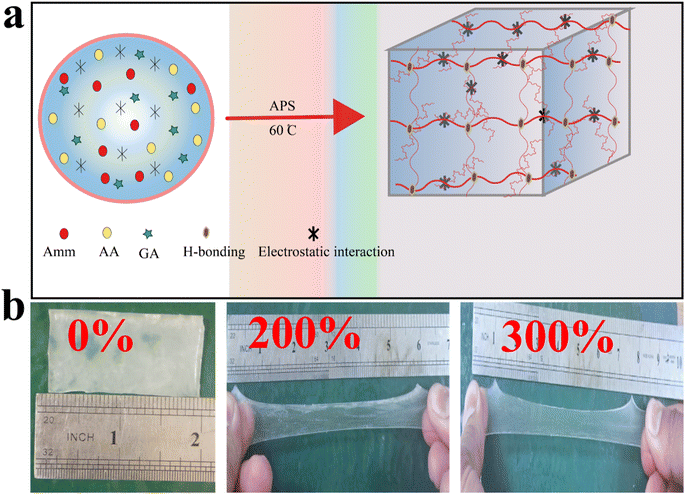 |
| Fig. 1 (a) Structural presentation of polymeric chain inside the organohydrogel (b) physical appearance of the mechanical behavior of the organohydrogel. | |
The functional group identification in the fabricated organohydrogel was studied through FTIR in the range between 400 cm−1 to 4000 cm−1. It is noted in Fig. 2a that the stretching vibration of OH− of AA was reported previously at 3423 cm−1, which is shifted to 3373 cm−1 indicating the involvement in hydrogen bonding with other groups.33,34 The symmetric stretching vibration of C–O was observed at 1013 cm−1 which indicates the presence of AA in the polymeric system.35 The presence of NH and C
O groups correlated with Amm and AA in the polymeric network was further confirmed by the appearance of peaks at 3180 cm−1 and 1666 cm−1 respectively.36
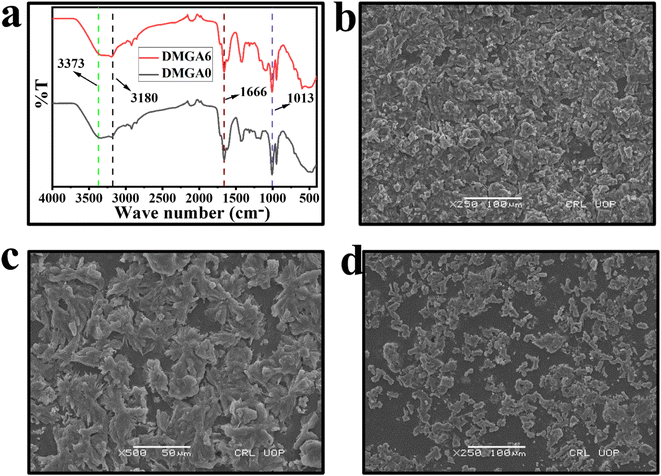 |
| Fig. 2 (a) FTIR. SEM images of (b) DMGA2 (c) DMGA4 (d) DMGA6 of synthesized organohydrogels. | |
The surface morphology and porosity of the organohydrogels were studied through scanning electron microscopy (SEM). All the samples showed a clear cracked and porous structure which gives a green sign for the transportation of ions within the network (Fig. 2b–d). The SEM results also show a decrease in porous nature by increasing the amount of AG in the organohydrogel network structure.
3.1. Mechanical performance of organohydrogel
The mechanical properties of fabricated organohydrogels were studied through a universal testing machine (UTM). The hydrogels were cut in known dimensions with a length of 40 mm, width of 10 mm, and thickness of 1 mm. It is noted in Fig. 3a that by adding the amount of AG in the polymeric system its mechanical properties increase. The hydrogel having no AG (DMGA0) has low fracture stress (39 kPa) and fracture strain (342%). When the amount of AG increased from 0% to 6%, there was a 73% in fracture strain (from 342% to 593%) while a 405% in fracture stress (39 kPa to 197 kPa) increase occurred in the synthesized organohydrogels (Fig. 3a–c). The toughness and young modulus of the prepared hydrogels were also determined from the stress–strain curve. The toughness and young modulus were similarly enhanced with the addition of the AG in the organohydrogels (Fig. 3d). This increase is due to the existence of noncovalent physical interactions among various groups in the hydrogel network.
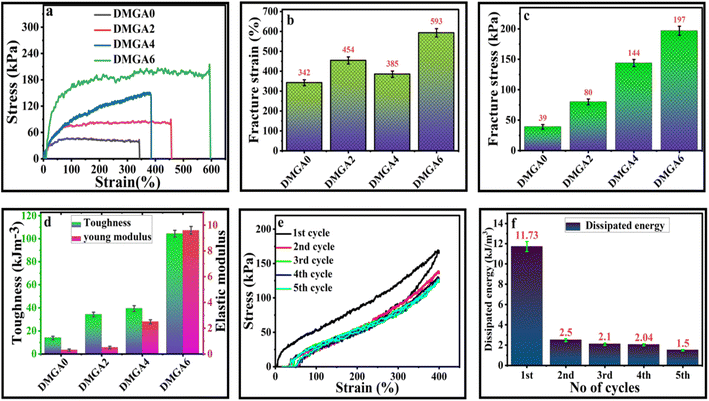 |
| Fig. 3 Mechanical performance of organohydrogel. (a) Stress–strain curve (b) fracture strain (c) fracture stress, (d) young modulus and toughness (e) cyclic stability of DMGA6 (f) dissipated energy of DMGA6. | |
The cyclic stability and dissipated energy of the DMGA6 organohydrogel were also studied by loading and unloading of organohydrogel at 400%. It is indicated in Fig. 3e that up to five cycles, no breakage of the organohydrogel was observed. The results show that the prepared organohydrogels have good anti-fatigue resistance to applied stress/pressure. During the cyclic and anti-fatigue investigation, the dissipated energy was measured which is the released energy during the loading and unloading process. The results show that during 1st cycle maximum energy dissipated (11.73 kJ m−3), which was reduced to 2.5 kJ m−3 for the 2nd cycle (Fig. 3f). The difference in dissipated energy between 1st and 2nd cycles occurred due to the arrangement of polymeric chains inside the organohydrogel. For the 2nd cycle, the polymeric network was ready for the external force and thus it detected low dissipated energy. Similarly, for the 3rd, 4th, and 5th cycles, 2.1 kJ m−3, 2.04 kJ m−3, and 1.5 kJ m−3 respectively comparable same dissipated energy was observed due to reliance on the polymeric network.
3.2. Rheological investigation of organohydrogel
Different rheological tests were conducted to investigate the viscoelastic nature of the designed organohydrogels. The frequency sweep was performed to measure the storage (G′) and loss (G′′) moduli. The G′ shows the elastic nature while the G′′ shows the viscous nature of the materials. In Fig. 4a it is clear that the organohydrogel having a high amount of AG (DMGA6) showed a higher G′ (9.10 kPa) than DMGA0 (8 kPa) at the entire angular frequency range. These results showed that by adding the amount of AG, the viscous behavior of organohydrogels shifts into an elastic nature. Similarly, the elastic nature of the designed organohydrogel was further confirmed by the damping factor (the ratio of loss modulus and storage modulus).7,37 The DMGA0 showed a higher damping factor than DMGA6 due to low interconnected polymer density linkages or interactions inside the polymer network (Fig. 4b). Furthermore, the critical strain of organohydrogel was also studied through an amplitude test (Fig. 4c). The results indicate being elastic DMGA6 has high G′′ than DMGA0. The critical strain (below which reversible deformation is possible) of the prepared organohydrogel is 46.2% which is much better than the previous study.19,28
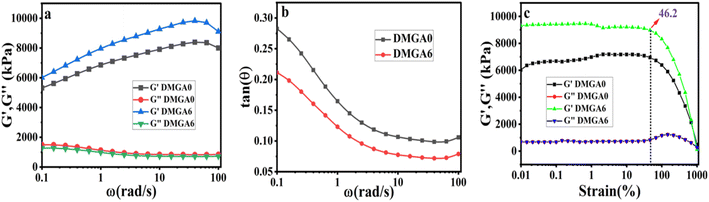 |
| Fig. 4 Rheological investigation. (a) Frequency sweep test (b) damping factor (c) amplitude sweep test. | |
3.3. Anti-evaporating and anti-freezing properties of organohydrogel
One of the limitations associated with hydrogels is their use at harsh environmental conditions i.e. high and low temperatures. The designed organohydrogels from two solvent systems showed resistance to both evaporation and freezing. To study anti-evaporation and anti-freezing properties, a hydrogel without DMSO was also fabricated by keeping all other components and conditions the same. The hydrogel (without DMSO) and DMGA6 were taken in the same weight (1.35 g) and placed in the open environment for 20 days. It is noted in Fig. 5a that after one day 54% of weight loss occurred in the hydrogel without DMSO while in the DMGA6 organohydrogel, 11.11% weight loss was observed. This retention property in the organohydrogel is produced due to DMSO which has a lone pair of electrons and interacts with the water molecules through physical forces. After 6 days the hydrogel without DMSO became hard by reducing weight up to 61.48% and useless for the practical strain sensing application. On the other hand, DMGA6 organohydrogel decreased its weight up to 48.14% in 20 days, with good stretching behavior, and was utilized for strain sensing purposes. The retention property of these organohydrogels is much better than the previously reported work.38 Similarly, the anti-freezing properties of the designed hydrogels were studied through DSC. The results shown in Fig. 5b indicate that the hydrogel (without DMSO) gives a freezing point of −12.4 °C, while for DMGA6 (with DMSO), the freezing point shifted from −12.4 °C to −54.6 °C. This shift in freezing point occurred due to physical interactions among DMSO and water molecules.
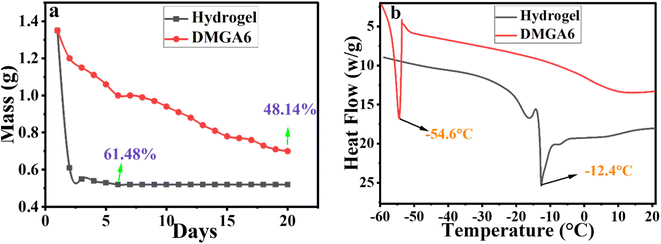 |
| Fig. 5 (a) anti-evaporating ability of the hydrogels (b) anti-freezing behavior of the hydrogels. | |
3.4. Organohydrogel as a strain sensor
Besides mechanical strength, anti-evaporating, and anti-freezing ability, these organohydrogels are a good choice for strain-sensing applications and smart electronic devices. The sensing property in the synthesized organohydrogel occurs due to two factors, one is Al3+ ions and the second is interconnected pores inside the gel. The organohydrogel was cut rectangular in length of 15 mm and width of 7 mm and connected with potentiostat for applied chronoamperometry analysis at 1 V, to study strain sensitivity concerning the organohydrogel elongation. In the result, it became clear that when the length of organohydrogel increases the gap among pores also increases as a result increment in the relative resistance was noted. Organohydrogel was passed at different strain ranges of 50% to 400%, and an increase in relative resistance was detected (Fig. 6a). The cyclic stability and anti-fatigue resistance of the fabricated organohydrogel were also studied. The designed samples were passed for multiple cycles at 200% strain for 200 s. The results given in Fig. 6b showed that there was no breakage of organohydrogel occurred. The current flow stability in the fabricated organohydrogel was studied through slow and fast stretching, there is no notable difference observed in the relative resistance (Fig. 6c). In smart sensing devices, the response time of the designed material is important. In Fig. 6d and e it is clear that the response time of the organohydrogel is 0.1 s and the recorded recovery time is 0.1 s, which is an excellent response of the gel compared to a previous study.7,39 The sensitivity of the DMGA6 organohydrogel was also studied through the gauge factor (Gf).40 It is noted in Fig. 6f that the DMGA6 organohydrogel gives a Gf = 9.86 at 500% strain which indicates excellent strain response compared to previous studies.41,42
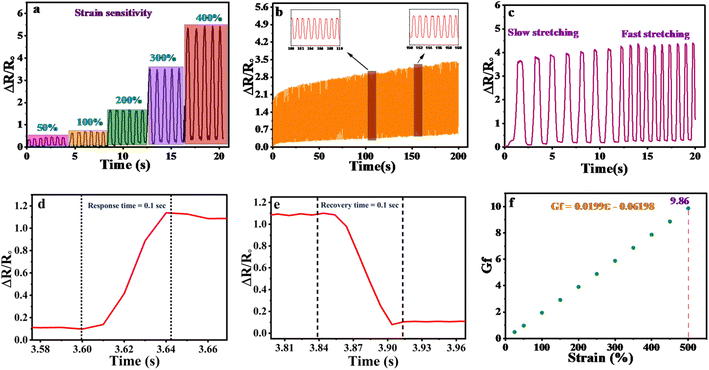 |
| Fig. 6 Strain sensitivity. (a) With respect to % strain (b) multiple cycles (c) slow fast stretching (d and e) response and recovery time (f) gauge factor. | |
3.5. Organohydrogel response to human motion
Being excellent strain sensing performance at room temperature, organohydrogel can be used for the detection of large and small physiological human motions. For this DMGA6 organohydrogel was attached to the different human joints and face parts. It is noted in Fig. 7a that by changing the angle of the finger, a clear variation occurred in the relative resistance. The deflection in the relative resistance was observed based on the strain sensing principle. An increase in the length of the organohydrogel through finger motion causes an increase in the distance among the pores, as a result, the passage of ions becomes difficult, and an increase in the relative resistance was noted. Similarly, when the finger was bent at different angles like 30°, 60°, and 90°, the same response was observed (Fig. 7b). Furthermore, the sensitivity of organohydrogel was also elaborated towards human wrist (Fig. 7c), elbow (Fig. 7d), and ankle (Fig. 7e and f) motions, the results confirm the sensitive behavior of the prepared materials toward these motions.
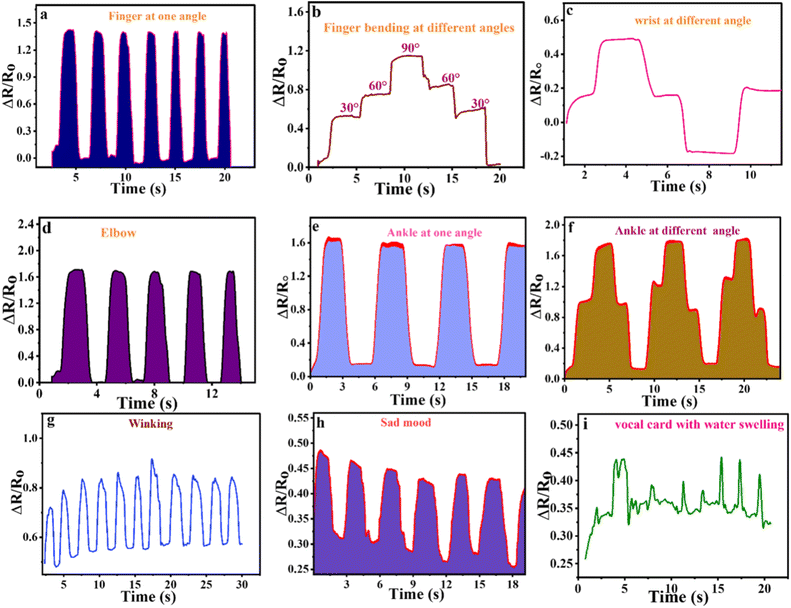 |
| Fig. 7 Detection of human motion, (a) finger response at a single angle (b) finger response at different angles (c) wrist response at different angle (d) elbow response at one angle (e) ankle response at one angle (f) ankle response at different angles (g) winking of the eye, (h) organohydrogel response to sad mood, (i) organohydrogel response to water swelling at the vocal card. | |
The response towards physiological face expression was also studied through the DMGA6 organohydrogel. The organohydrogel was attached to the face skin near to eye and started the winkling of the eye. The stimuli in the relative resistance were observed (Fig. 7g), similarly, the sad mood was also studied as the organohydrogel was attached to the human forehead (Fig. 7h). The vocal sensing was studied by drinking water and organohydrogel was attached to the human vocal card (Fig. 7i). The results indicate that the designed organohydrogels can successfully detect different small and large physiological human motions. The results attributed that our designed organohydrogel shows better responses to humans small and large motions as compared with the literature.43–45
3.6. Application of dry organohydrogel
After the anti-evaporating study, the neat hydrogel (without DMSO) was unable for practical application, while the DMGO6 organohydrogel was still able for practical application and used for human motion detection. The organohydrogel was attached to the cheek and response towards smiling mood was elaborated. The results are given in Fig. 8 a show that dry organohydrogel can respond successfully like the initial original organohydrogel. Similarly, the organohydrogel was attached to the neck and up-down motion was recorded, again variation in the relative resistance was observed (Fig. 8b). Furthermore, for the sensing of the balloon size, the dry organohydrogel was attached to the balloon, and an increase in its size was noted by entering air, as the size of the balloon increased organohydrogel length also increased as a result increase in the relative resistance was noted (Fig. 8c). The organohydrogel can also show a response towards writing on its surface. The results indicate that the organohydrogel showed an excellent response to the word PAKISTAN (Fig. 8d). This result showed that organohydrogel can be used for the smart electronic pad.
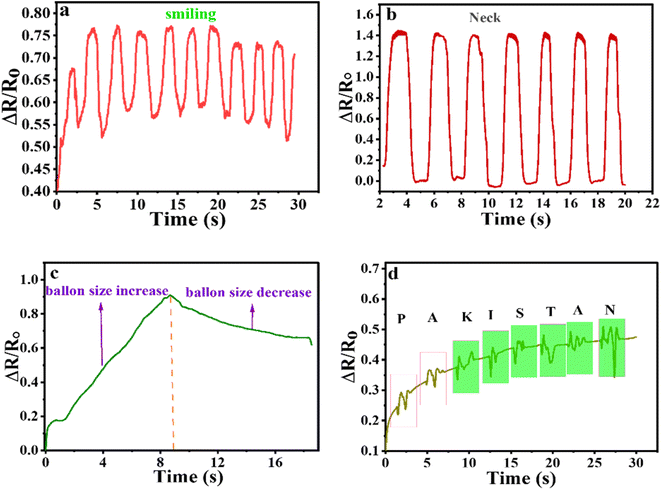 |
| Fig. 8 Application of dry DMGO6 organohydrogel, (a) response towards smiling (b) response towards the up-down motion of neck (c) response towards swelling of the balloon (d) behaves as an electronic note pad. | |
3.7. Organohydrogel as an electronic pen
Besides good mechanical properties, and excellent anti-freezing, and anti-evaporating properties, DMGA6 organohydrogel is a good choice for the selection of an electronic pen. For this, the DMGA6 organohydrogel was attached to the iron rod and applied on the phone screen by using the “Electronic Signature Maker App”. It is clear from Fig. 9a–e, that the designed organohydrogel can successfully show response just like the human finger, and can be applied as an electronic pen that can write and draw anything on the surface of the screen.
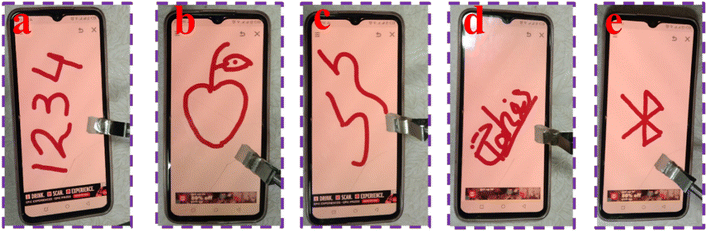 |
| Fig. 9 The use of organohydrogel as an electronic pen for (a) writing (b) drawing (c) language identification (d) signature (e) bluetooth symbol. | |
4 Conclusion
In summary, organohydrogels were successfully fabricated in which water and DMSO were used as dual solvents to make the organohydrogel environmentally tolerant. The introduction of Arabic gum increased the mechanical properties such as fracture strain from 343% to 593%, fracture stress from 39 kPa to 197 kPa, and cyclic stability with five cycles at 400% without resting time. With the addition of DMSO, the hydrogel concept shifts to organohydrogel, and its freezing point was shifted from −12.4 °C to −54.6 °C. The organohydrogel showed strain sensitivity from 50% to 400% with a response time of 65 ms and gauge factor 9.86 at 500% strain. The fabricated organohydrogel in both normal and dry states can detect different human motions like finger bending, wrist bending, necking bending, elbow bending, and facial expressions like sad mood, smiling mood, etc. The designed organohydrogel behaved as an electronic pen in writing, drawing, etc. on the surface of smart sensing devices at high and low-temperature ranges. These hydrogels can be applied successfully in smart electronic devices that can work at harsh temperature conditions in the near future.
Data availability
This work is original research, with primary research/new data available in figures.
Conflicts of interest
The authors declare no conflict of interest to exists.
References
- T. Zhu, et al., Multifunctional hydrophobic fabric-based strain sensor for human motion detection and personal thermal management, J. Mater. Sci. Technol., 2023, 138, 108–116 CrossRef.
- Q. J. Sun, et al., Advanced Functional Composite Materials toward E-Skin for Health Monitoring and Artificial Intelligence, Adv. Mater. Technol., 2023, 8(5), 2201088 CrossRef CAS.
- X. Dai, et al., Soft Robotic-Adapted Multimodal Sensors Derived from Entirely Intrinsic Self-Healing and Stretchable Cross-Linked Networks, Adv. Funct. Mater., 2023, 33(44), 2304415 CrossRef CAS.
- M. Zarei, et al., Advances in biodegradable electronic skin: Material progress and recent applications in sensing, robotics, and human–machine interfaces, Adv. Mater. Technol., 2023, 35(4), 2203193 CAS.
- J. Xu, et al., Stretchable, Adhesive, and Bioinspired Visual Electronic Skin with Strain/Temperature/Pressure Multimodal Non-Interference Sensing, ACS Appl. Mater. Interfaces, 2023, 15(28), 33774–33783 CrossRef CAS PubMed.
- Y. Yu, et al., Carbon Dots-Based Ultrastretchable and Conductive Hydrogels for High-Performance Tactile Sensors and Self-Powered Electronic Skin, Small, 2023, 19(31), 2204365 CrossRef CAS PubMed.
- R. Ullah, et al., Guar gum reinforced conductive hydrogel for strain sensing and electronic devices, Int. J. Biol. Macromol., 2023, 246, 125666 CrossRef CAS PubMed.
- L. Zhu, et al., Polyelectrolyte microgels-enhanced double-crosslinking polyacrylamide hydrogel sensing with stretchable, transparent, and fast response, Eur. Polym. J., 2023, 200, 112517 CrossRef CAS.
- L. Jiang, et al., Three-dimensional printing and injectable conductive hydrogels for tissue engineering application, Tissue Eng., Part B, 2019, 25(5), 398–411 CrossRef CAS PubMed.
- Z. Liu, et al., Functionalized fiber-based strain sensors: pathway to next-generation wearable electronics, Nano-Micro Lett., 2022, 14(1), 61 CrossRef CAS PubMed.
- L. Hu, et al., Hydrogel-based flexible electronics, Adv. Mater., 2023, 35(14), 2205326 CrossRef CAS PubMed.
- F.-L. Yi, et al., Polyacrylamide hydrogel composite E-skin fully mimicking human skin, ACS Appl. Mater. Interfaces, 2021, 13(27), 32084–32093 CrossRef CAS PubMed.
- Y. Yue, Nanocomposite hydrogels for strain sensing based on optical and electrical signals: a, reviewChem. Commun., 2023, 59(58), 8894–8910 CAS.
- X. Sun, F. Yao and J. Li, Nanocomposite hydrogel-based strain and pressure sensors: a review, J. Mater. Chem. A, 2020, 8(36), 18605–18623 RSC.
- M. A. U. Khalid and S. H. Chang, Flexible strain sensors for wearable applications fabricated using novel functional nanocomposites: a review, Compos. Struct., 2022, 284, 115214 CrossRef CAS.
- M. Maturi, et al., Synthesis of ultrasmall single-crystal gold–silver alloy nanotriangles and their application in photothermal therapy, Nanomaterials, 2021, 11(4), 912 CrossRef CAS PubMed.
- Z. Li, et al., High-strength, anti-freeze, transparent and recyclable composite organohydrogel for flexible strain sensor, React. Funct. Polym., 2023, 190, 105644 CrossRef CAS.
- A. Tuli and A. P. Singh, Polymer-based wearable nano-composite sensors: a review, Int. J. Polym. Anal. Charact., 2023, 28(2), 156–191 CrossRef CAS.
- L. Ara, et al., Ion–electron based poly(Amm-co-BA)@GO conductive hydrogels for wearable strain sensors, Sens. Actuators, A, 2023, 364, 114782 CrossRef CAS.
- J. Huang, et al., Highly stable and reliable capacitive strain sensor for wearable electronics based on anti-dry hydrogel electrode, Mater. Today Phys., 2023, 35, 101123 CrossRef.
- X. Tao, et al., Recyclable, anti-freezing and anti-drying silk fibroin-based hydrogels for ultrasensitive strain sensors and all-hydrogel-state super-capacitors, Mater. Today Chem., 2023, 32, 101624 CrossRef CAS.
- Y. Hao, et al., Fish Scale Biomimetic Multifunctional Antifreeze Organogel for Flexible Strain Sensor Applications, ACS Appl. Polym. Mater., 2023, 6(1), 141–153 CrossRef.
- W. Xiao, et al., Cellulose nanocrystal based self-healing and anti-freezing arabic gum hydrogels using betaine/CaCl2 anti-freeze strategy, Cellulose, 2023, 30(12), 7667–7680 CrossRef CAS.
- Z. J. Da, Research progress of flexible hydrogel sensor, Advances in Computer, Signals Systems, 2023, 7(1), 12–14 Search PubMed.
- Y. Tian, et al., Compressible, anti-freezing, and ionic conductive cellulose/polyacrylic acid composite hydrogel prepared via AlCl3/ZnCl2 aqueous system as solvent and catalyst, Int. J. Biol. Macromol., 2023, 253, 126550 CrossRef CAS PubMed.
- C. Liu, et al., Comprehensive investigation of AlCl3-based electrolytes for rechargeable aluminum-ion battery, in International Conference on Optical Technology, Semiconductor Materials, and Devices (OTSMD 2022), SPIE, 2023 Search PubMed.
- M. Li, et al., An environmentally tolerant, highly stable, cellulose nanofiber-reinforced, conductive hydrogel multifunctional sensor, Carbohydr. Polym., 2022, 284, 119199 CrossRef CAS PubMed.
- L. Ara, et al., Hydrophobically associated ionic conductive hydrogels as strain, pressure, and an electronic sensor for human motions detection, Sens. Actuators, A, 2023, 362, 114618 CrossRef CAS.
- B. Kamaliya, P. N. Dave and P. M. J. Macwan, Rheological investigations and swelling behaviour of hydrogels based on gum ghatti-cl-poly (N-isopropyl acrylamide-co-acrylic acid)/CoFe2O4 nanoparticles, Polym. Bull., 2023, 80(6), 6923–6944 CrossRef CAS.
- Y. Tian, et al., Compressible, anti-freezing, and ionic conductive cellulose/polyacrylic acid composite hydrogel prepared via AlCl3/ZnCl2 aqueous system as solvent and catalyst, Int. J. Biol. Macromol., 2023, 126550 CrossRef CAS PubMed.
- N. A. Ahmed, et al., Removal of astrazon red dye from wastewater using eggshell/graphene oxide embed in (Gum Acacia/Acrylamide) hydrogel nanocomposites synthesized by gamma irradiation, J. Inorg. Organomet. Polym. Mater., 2023, 33(11), 3617–3637 CrossRef CAS.
- C. Wu, et al., Fabrication of composite hydrogels by assembly of okara cellulose nanofibers and gum Arabic in ionic liquids: structure and properties, J. Mol. Liq., 2022, 349, 118132 CrossRef CAS.
- J. Ren, et al., An anti-swellable hydrogel strain sensor for underwater motion detection, Adv. Funct. Mater., 2022, 32(13), 2107404 CrossRef CAS.
- Y. Wu, et al., Facile fabrication of flexible alginate/polyaniline/graphene hydrogel fibers for strain sensor, J. Eng. Fibers Fabr., 2022, 17, 15589250221114641 CAS.
- L. Zhang, et al., Preparation of tough and anti-freezing hybrid double-network carboxymethyl chitosan/poly(acrylic amide) hydrogel and its application for flexible strain sensor, J. Mater. Sci. Technol., 2022, 57(41), 19666–19680 CrossRef CAS.
- K. Cheng, et al., Mechanically robust and conductive poly(acrylamide) nanocomposite hydrogel by the synergistic effect of vinyl hybrid silica nanoparticle and polypyrrole for human motion sensing, Adv. Compos. Hybrid Mater., 2022, 5(4), 2834–2846 CrossRef CAS.
- R. Ullah, L. A. Shah and M. T. J. Khan, Cellulose nanocrystals boosted hydrophobically associated self-healable conductive hydrogels for the application of strain sensors and electronic devices, Int. J. Biol. Macromol., 2024, 129376 CrossRef CAS PubMed.
- M. Khan, et al., Hydrophobically associated functionalized CNT-reinforced double-network hydrogels as advanced flexible strain sensors, ACS Appl. Polym. Mater., 2022, 4(10), 7397–7407 CrossRef CAS.
- D. Yu, et al., A low-modulus, adhesive, and highly transparent hydrogel for multi-use flexible wearable sensors, Colloids Surf., A, 2023, 659, 130752 CrossRef CAS.
- M. Sher, et al., Xanthan gum toughen ionically conductive hydrogels for flexible and artificial epidermis sensors with multifunctionality and self-healability, Sens. Actuators, A, 2024, 115199 CrossRef CAS.
- Y. Xin, et al., Tough, healable, and sensitive strain sensor based on multiphysically cross-linked hydrogel for ionic skin, Biomacromolecules, 2023, 24(3), 1287–1298 CrossRef CAS PubMed.
- G. Huang, et al., Tough, self-healing double network hydrogels crosslinked via multiple dynamic non-covalent bonds for strain sensor, J. Polym. Sci., 2023, 61(15), 1675–1687 CrossRef CAS.
- X. Chen, et al., Metal-Free and Stretchable Conductive Hydrogels for High Transparent Conductive Film and Flexible Strain Sensor with High Sensitivity, Macromol. Chem. Phys., 2020, 221(10), 2000054 CrossRef CAS.
- S. A. Fraser and W. E. Van Zyl, A wearable strain sensor based on electroconductive hydrogel composites for human motion detection, Macromol. Mater. Eng., 2022, 307(7), 2100973 CrossRef CAS.
- X. Di, et al., A bio-inspired, ultra-tough, high-sensitivity, and anti-swelling conductive hydrogel strain sensor for motion detection and information transmission, Mater. Horiz., 2022, 9(12), 3057–3069 RSC.
|
This journal is © The Royal Society of Chemistry 2024 |
Click here to see how this site uses Cookies. View our privacy policy here.