DOI:
10.1039/D4RA06047D
(Paper)
RSC Adv., 2024,
14, 37676-37687
Enhancing the capacity of Mn-rich cathodes by kinetics control for lithium-ion batteries†
Received
21st August 2024
, Accepted 21st October 2024
First published on 25th November 2024
Abstract
High energy density cathodes have been widely explored in recent years in the area of lithium-ion batteries, which suffer from sluggish kinetics and structural degradation. Herein, the kinetics of the charge transfer process on the cathode material was accelerated via synergistic lanthurizing and Li/Mn optimization method, thereby delivering layered-spinel biphase and improved electrochemical performance. The available capacity was greatly enhanced from 57.4 mA h g−1 for the pristine material to 233.4 mA h g−1 for the modified material with a voltage of 1.5–4.8 V. Based on the electrochemical and structural characterization, the improved capacity and rate performance were attributed to the engineered structural design with enhanced electrochemical kinetics. Electrochemical impedance spectroscopy results indicated that modification tuning could effectively lower the activation energy of the charge transfer process by nearly 45%. This synergistic approach widens the method for enhancing the energy density of oxide cathodes.
Introduction
Lithium-ion batteries with high energy density rely on the high-voltage operation of oxide cathodes to gain extra capacity.1,2 Mn-rich cathode has been proposed as a replacement for the commercial layered cathode as it is inexpensive and safer.3,4 Unfortunately, the poor kinetics and structural stability lead to a severe decrease in the rate performance and capacity, thus hindering further commercial applications.5–7 The main reason affecting the electrochemical performance of Mn-rich oxide material is kinetics.8–10 The charge compensation at high voltage for oxygen anion and transition metal (TM) cation bi-center redox increases the available capacity.10,11 However, with a high ratio of lithium (de)intercalation, the oxygen atoms become unstable. The undesirable oxygen gas released from the cathode material directly reduces the available capacity.12,13 Because the organic electrolyte is chemically reactive at high voltage, the cathode/electrolyte side reaction could still lose oxygen atoms and thicken the cathode electrolyte interphase (CEI). Therefore, the undesired oxygen side reaction leads to sluggish kinetics, leading to poor lithium-ion diffusion at high voltage.14,15 It further results in fast impedance growth, accelerated structural degradation, and battery failure.
Extensive efforts have been devoted to tackling the issues mentioned above, including the modification of the surface with protective layers,16–18 design of the cathode structure,19–21 introduction of functional electrolyte additives,22 and application of a solid-state electrolyte.23,24 Doping is one of the most widely used methods to enhance the electrochemical performance of cathode materials. Various dopant elements, such as Al, Ti, Fe, and Mg, have been examined in Mn-rich cathode oxide.25–27 However, the lithium ion diffusion kinetics and surface stability of the cathodes decrease with increased oxygen redox reaction. In this regard, investigations on the simultaneous modification of the structure and surface with a synergetic strategy have been recently reported.28
Herein, an effective engineering strategy is proposed to tailor the Mn-rich Li2MnO3 (LMO) cathode material via the La–O bond and layered-spinel biphase simultaneously (Fig. 1). Pristine LMO material has been confirmed to present severe oxygen release.29,30 Replacing the weakly bonded surface oxygen with a stable La–O bond has been proposed to prevent the oxygen release.31,32 Because of the biphase framework and favorable ionic transport network, the modified Mn-rich material delivers a high specific capacity of 233.4 mA h g−1. Based on X-ray diffraction (XRD), transmission electron microscopy (TEM), and Raman spectroscopy, the modified Mn-rich material presents a layered-spinel biphase. The galvanostatic intermittent titration technique (GITT) data and temperature-varied electrochemical impedance spectroscopy (EIS) data analyses demonstrated that the notable improvement in the electrochemical performance is due to the favorable lithium-ion diffusion process. This study emphasizes the importance of fast kinetics on the charge transfer process and provides a promising path for the rational design of LMO materials to achieve high energy density and high rate performance.
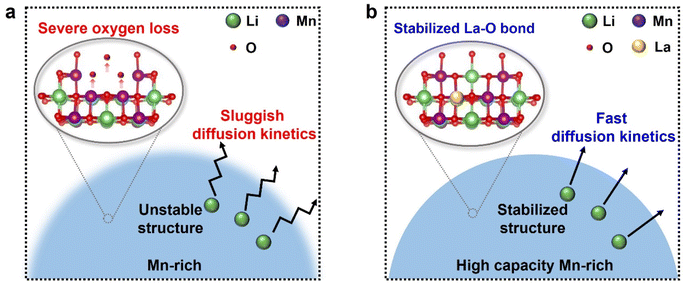 |
| Fig. 1 The Mn-rich cathode cycled at high voltage enables high available capacity. (a) However, high voltage electrochemical cycling leads to severe oxygen loss, which results in sluggish lithium ion diffusion kinetics. (b) Herein, we constructed a highly stable structure with La doping and Li/Mn optimization, which delivers stabilized structure and fast lithium-ion diffusion kinetics. | |
Experimental
Synthesis of LMO series cathode materials
The cathode materials Li2MnO3 (LMO), Li2Mn0.99La0.01O3−δ (La0.01), Li2Mn0.97La0.03O3−δ (La0.03), Li2Mn0.95La0.05O3−δ (La0.05), and Li2Mn1.97La0.03O5−δ (LMLO) were synthesized via a high-temperature solid-state method. The raw materials Li2CO3, MnO2, and La2O3 were placed in an agate tank according to the stoichiometric ratio, soaked in acetone, and mixed via ball milling for 3–4 hours. The uniformly mixed slurry was dried and pressed into a sheet at a pressure of 90 MPa and then calcined at 750 °C for 24 hours in a muffle furnace. After the high-temperature calcination, the obtained samples were taken out, ground into powder, and named as the cathode materials. The synthesis of the reference Li2Mn4O9 material has been reported in previous works.33,34 The precursor was calcined at 400 °C for 32 hours in air.
Electrochemical measurement
Aluminum sheet was punched into a circular plate with a diameter of 14 mm and cleaned with 0.1 M NaOH solution and 0.1% H2C2O4 solution. Taking the synthesized cathode material as the active material, acetylene black as the conductive agent, and polyvinylidene fluoride (PVDF) as the binder in a weight ratio of 8
:
1
:
1, the mixture was sequentially added into the mill tank with N-methyl-2-pyrrolidone (NMP) as the dispersant. The mixture was milled at a high speed of 350 rpm for 2–3 hours to obtain a uniform slurry. The slurry was coated on the treated aluminum sheet and dried at 120 °C in a vacuum drying oven overnight to obtain the cathode electrode. The weight of the active material was 3–5 mg in the cathode electrode.
To test the electrochemical performance, we assembled the CR2032 coin-type cell in a glovebox filled with inert argon gas (H2O < 0.01 ppm, O2 < 0.01 ppm). The cells were assembled with a self-made electrode, Celgard 2300 as the separator, lithium metal foil as the counter electrode, and 1.0 M LiPF6 in a mixed solvent (the volume ratio, EC
:
DEC
:
EMC = 1
:
1
:
1) as the electrolyte. The galvanostatic charge–discharge test was conducted on a battery cycler (CT-3008W, Neware, China). After standing at room temperature for 8 hours, the cell underwent long-term cycling and electrochemical tests such as rate performance, GITT, etc. The EIS and cyclic voltammetry (CV) tests were conducted on the an electrochemical workstation (Shanghai Chenhua CHI760E, and VERSASTAT 4). The frequency range of the EIS test was 0.01 Hz to 100 kHz with a voltage amplitude of ±5 mV. The scanning rate of the CV test was 0.1 mV s−1. The GITT test was conducted with charge/discharge at a current density of 25 mA g−1 for 10 minutes and the rest for 40 minutes.
Structural characterization
The XRD data were collected on a Rigaku Ultima IV powder X-ray diffractometer using Cu Kα radiation (λ = 1.5406 Å) source. Rietveld refinement was performed using the General Structure Analysis System (GSAS) software with the EXPGUI interface.35 Schematic diagrams were drawn using the VESTA software.36 Raman spectroscopy (Horiba LabRaman HR evolution) was conducted at an activated wavelength of 633 nm and power of 7 mW. The differential scanning calorimetry (DSC) (NETZSCH, STA409PC) measurements for the charged LMO and LMLO electrodes were carried out at a heating rate of 5 °C min−1. The scanning electron microscopy (SEM) and assorted energy dispersive spectroscopy (EDS) measurements were performed (Mira, Tescan) to characterize the morphology of the particle and elemental mapping of the materials. Transmission electron microscopy (TEM) technique was applied using a JEM-2100F TEM instrument. The stoichiometry of the elemental compositions for the cathode materials was examined by inductively coupled plasma atomic emission spectrometry (ICP-AES).
Results and discussion
Structural design and material characterization
The general structural design for the high-capacity Mn-rich cathode is outlined in Fig. 2a. The pristine Li2MnO3 (LMO) was viewed as Li[Li1/3Mn2/3]O2, wherein one-third of the transition metal (TM) layer site is occupied by the lithium atom. For the LMLO material, the combination of layered-spinel (Li atom in tetrahedral site) biphase and rare element La doping (with stabilized La–O bond) suggests enhanced structural stability. The pristine LMO and modified materials were synthesized via a simple one-step solid-state method.37
 |
| Fig. 2 (a) Proposed crystal atomic structure of the bulk architecture for LMO and LMLO materials. (b) SEM image for the LMLO material. (c and d) TEM image for the LMLO material. (e) XRD patterns and Rietveld refinement for the LMO material. (f) XRD patterns for LMO, LMLO and Li2Mn4O9 materials. | |
The SEM images for pristine LMO and modified LMLO material are presented in Fig. S1† and 2b. It shows that both materials deliver irregular ball shapes with a diameter of 100–200 nm, which is consistent with the TEM image for the LMLO material (Fig. 2c). The coexistence of layered and spinel phases in the LMLO material was characterized via the TEM method (Fig. 2d). Lattice fringes in the bulk region with a d-spacing of 0.474 nm can be ascribed to the (001) facet of layered structure. In some regions, the transition metal ions occupy part of the lithium-ion layer, forming a crystal plane with a d-spacing of 0.236 nm, which is consistent with the (222) facet of the spinel phase (space group Fd
m).38,39 The elemental content was detected via inductively-coupled plasma-atomic emission spectrometry (ICP-AES). The ICP-AES data (Table 1) indicates that the compositions of the as-synthesized compounds are close to that of the targeted compositions, which is consistent with the SEM-EDS results (Table S1†).
Table 1 Target vs. measured Li
:
Mn
:
La atomic ratio of pristine and modified materials by ICP-AES
Material |
Target Li : Mn : La |
Measured Li : Mn : La |
LMO |
2.00 : 1.00 : 0.00 |
2.021 : 1.011 : 0.000 |
La0.01 |
2.00 : 0.99 : 0.01 |
2.008 : 0.992 : 0.011 |
La0.03 |
2.00 : 0.97 : 0.03 |
2.011 : 0.971 : 0.031 |
La0.05 |
2.00 : 0.95 : 0.05 |
2.020 : 0.952 : 0.052 |
LMLO |
2.00 : 1.97 : 0.03 |
2.010 : 1.973 : 0.031 |
The XRD profiles of LMO series materials are presented in Fig. S2.† All LMO series materials present Li2MnO3-like diffraction patterns in the range of 10°–90°, leading to the monoclinic phase (space group C2/m).7,40 The Rietveld-refined XRD data for the LMO material is presented in Fig. 2e, and the unit cell parameters calculated by the General Structure Analysis System (GSAS) are listed in Tables S2 and S3.† For pristine LMO material, the peaks at about 18° are characteristic of a layered rhombohedral LiMO2 phase, the relatively weak reflections between 20° and 23° are assigned as the Li2MnO3-like phase (Fig. 2e and S1†). For the XRD patterns of LMLO material (Fig. 2f), the extra diffraction peaks at 36.4° and 44.2° can be attributed to the spinel Li2Mn4O9 phase (or some spinel-like phases),34 which indicates that the modified material delivers a layered-spinel biphase, consistent with the TEM results. The extra peak at about 33° for the LMLO material may come from the La-containing compound, which needs further confirmation.
Electrochemical performance
The electrochemical activity was detected via galvanostatic charge–discharge measurement. The initial charge–discharge curves for LMO series materials are presented in Fig. 3a. Under a voltage window of 1.5–4.8 V, the pristine LMO electrode presents a characteristic 4.5 V voltage plateau during charging, which is associated with the activation process and delivers a discharge capacity of 57.4 mA h g−1.8 After La doping, the discharge capacity increases to 72.1 mA h g−1, 182.8 mA h g−1, and 99.6 mA h g−1 for La0.01, La0.03, and La0.05 electrodes, respectively. This indicates the positive effect of La doping on the electrochemical performance. It is worth noting that the modified LMLO material delivers an extremely enhanced capacity of 233.4 mA h g−1 and special charge–discharge curves with new discharge voltage plateaus at 4.0 V and 2.8 V, which are characteristic features for the spinel phase.41 The enhanced reversible capacity in the LMLO material suggests suppressed irreversible oxygen release after the synergistic modification. The cycling performance of the LMO series was obtained with a current density of 25 mA g−1 in the voltage range between 2.0 V and 4.8 V (Fig. 3b). It shows that the LMLO material delivers higher capacity than that of the other three materials during the whole cycling process. The discharge capacities of the pristine and La-modified materials gradually increase in the initial 10 cycles, which can be ascribed to a gradual activation process to utilize more lithium ions.42,43 At the 100th charge–discharge cycle, the available capacity for LMO and LMLO is 13.5 mA h g−1 and 118.1 mA h g−1, respectively. It is worth noting that the capacity decay remains obvious upon extensive cycles in LMO systems. The conventional LMO delivers poor cycling, which is related to Mn dissolution, surface interaction, structural evolution, etc.30,44,45 Further improvements could be gained through other modifications such as surface coating, which is beyond the scope of this work.
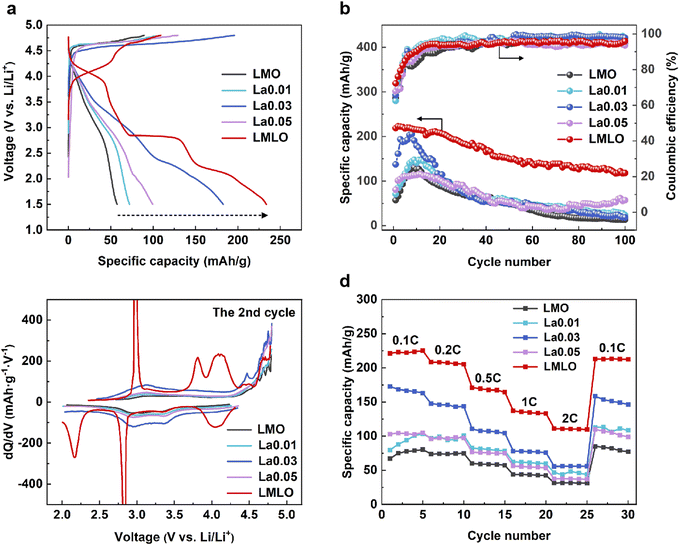 |
| Fig. 3 Galvanostatic charge–discharge curves for LMO series cathodes. (a) Initial charge–discharge curves with voltage between 4.8 V and 1.5 V at a current density of 25 mA g−1. (b) Specific capacity and coulombic efficiency evolution during the cycling process with voltage between 4.8 V and 2.0 V. (c) dQ/dV curves for the 2nd cycle. (d) Rate performance. | |
Differential capacity against voltage (dQ/dV) curves for LMO series materials under the voltage range of 2.0–4.8 V were analyzed (Fig. 3c). After the activation process in the initial cycle, the pristine LMO electrode delivers a broad hump due to the partial overlap of cathodic and anionic redox. The peak pairs at the 2.5–4.4 V region belong to the redox of Mn2+/Mn4+ in the layered cathode material.46 Above 4.5 V, the peak pairs mainly belong to the oxygen redox reaction.14 For comparison, the modified LMLO electrode presents peak pairs at about 3.0 V and 4.0 V, indicating that the spinel phase exists in the LMLO material. As for the rate performance, LMO series materials were evaluated between 2.0 V and 4.8 V with 0.1 C, 0.2 C, 0.5 C, 1 C, and 2 C rates (1 C = 200 mA g−1), respectively (Fig. 3d). The La-modified materials deliver higher specific capacity than that of the pristine LMO at all rates. When cycled at 2 C rate, the available capacity for LMO and LMLO is 31.5 mA h g−1 and 111.1 mA h g−1, respectively. Upon returning to the 0.1 C rate, the LMLO material ensures a capacity of 213.0 mA h g−1, which is 251% that for the LMO material (85.0 mA h g−1).
To explore the effect of La doping and Li/Mn optimization, the charge–discharge curves during the cycling process for LMO and LMLO electrodes were compared (Fig. S3†). It is notable that during the cycling process, the charge curves for the Mn-rich LMO electrode change to S-type curves. For the LMLO electrode, the initial charge–discharge curves contain the specific 4.0 V and 2.8 V discharge voltage plateaus, which are well sustained during cycling, suggesting the coexistence of layered phase and spinel phase in the modified LMLO material.
The corresponding differential capacity against voltage (dQ/dV) curves for LMO and LMLO at different cycles under the voltage range of 2.0–4.8 V were further analyzed (Fig. S3c and d†). Pristine LMO delivers an oxidation peak at about 4.5 V, which can be linked to the activation of the Li2MnO3 component accompanied by irreversible oxygen release.47 Besides, the anodic peaks (at about 3.0 V) gradually shift to lower potential during cycling, indicating a sharp voltage decay with increasing cycle number for pristine LMO (Fig. S3c†). For comparison, the peaks at about 2.8 V (discharge process) are maintained well for the LMLO material during the cycling process (Fig. S3d†). The comparison of the normalized charge–discharge profiles is presented in Fig. S4.† The pristine LMO shows severe voltage decay upon cycling (Fig. S4a†). The voltage decay has been ascribed to the structural degradation, low-voltage redox couples, and so on.48 In contrast, the modified LMLO material presents improved voltage evolution (Fig. S4b†), which supports the advantage of synergetic modification.
Electrochemical characterization
To study the Li-ion transport behavior under synergetic modification, the EIS technique for cells after 100 cycles was examined to investigate the Li+ transfer property (Fig. 4a).28 The EIS spectra were fitted based on the equivalent circuit model (Fig. S5†), and the corresponding fitting data is shown in Fig. 4b.49 It shows that the Rct in LMLO is lower than that in LMO material, which is a good explanation for the better rate capability gained above. The reduced Rct would come from the reduced interfacial side reaction after layered-spinel phases modification.
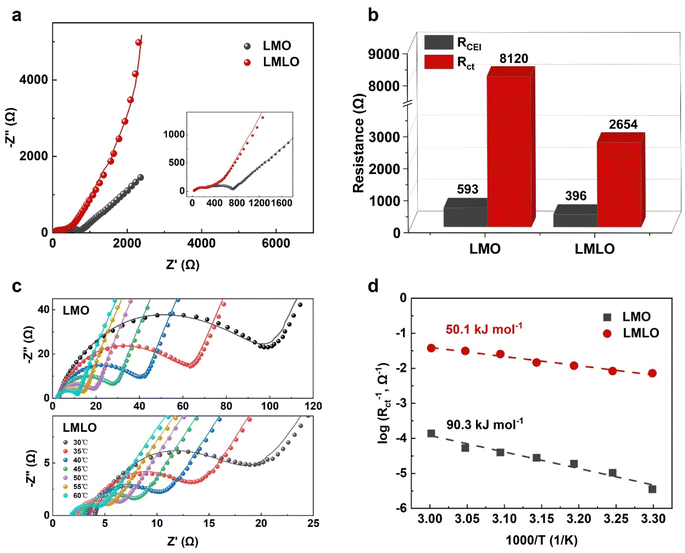 |
| Fig. 4 (a) Nyquist plots of the EIS data for LMO and LMLO materials after 100 cycles and (b) corresponding fitting results of RCEI and Rct. (c) Rct obtained from variable temperature EIS data for LMO and LMLO materials and (d) corresponding activation energy (Ea) of the charge transfer process. | |
To further study the impact of modification on the charge transfer process, EIS at varied temperatures was adopted to monitor the cell impedance (Fig. 4c and S6†). The values of Rct can be obtained via equivalent circuit fitting from Nyquist profiles at different temperatures (Table S4†).49 According to the Arrhenius relationship that charge transfer resistance (Rct) follows (Note S1†), the value of activation energy (Ea) could be obtained.50 As shown in Fig. 4d, the calculated Ea for LMO and LMLO electrodes is 90.3 kJ mol−1 and 50.1 kJ mol−1, respectively. This indicates that the synergistic La doping and Li/Mn optimization could effectively enhance the kinetics of lithium-ion diffusion. The facilitated Li+ transport across the electrolyte/electrode interface should be attributed to the stabilized structure and mitigated side reaction.
Cyclic voltammetry at different scan rates (ranging from 0.3 mV s−1 to 1.1 mV s−1) was carried out to investigate the Li+ diffusion kinetics (Fig. 5a and b). The Li+ diffusion coefficients of LMO and LMLO were evaluated by following the Randles–Sevcik equation
|
Ip = 2.69 × 105n3/2AD1/2v1/2C0
| (1) |
where
n refers to the number of electrons transferred per molecule (1.0 for lithium ions),
A refers to the surface area of the cathode, and
C0 refers to the bulk concentration of lithium ions.
51 Hence, by fitting the
Ip–
v1/2 curve and comparing the slope, the apparent diffusion kinetics of the materials can be well contrasted. As plotted in
Fig. 5c and d, the anodic peak current slope of the LMLO electrode is 0.0287, which is higher than that of the LMO electrode (0.0204). As for the cathodic peak current, the slope of the LMLO electrode (0.0245) is higher than that of the LMO electrode (0.0228). It indicates faster lithium-ion transportation kinetics
via bulk modification, which is consistent with the improved rate performance and enhanced cycling stability.
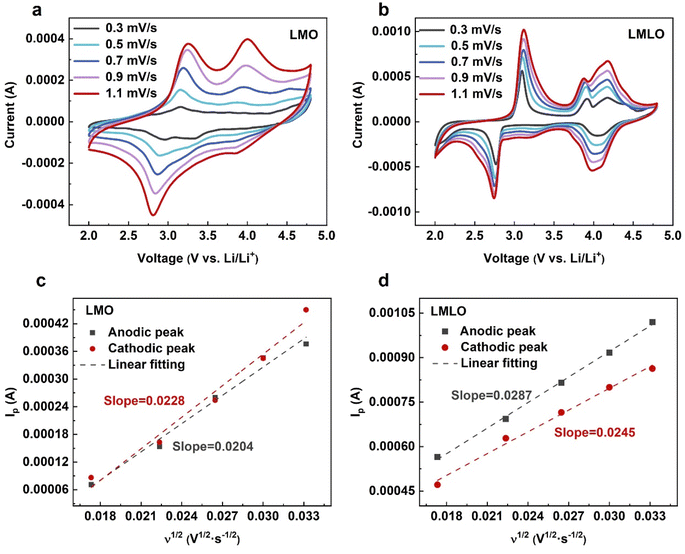 |
| Fig. 5 CV curves for (a) LMO and (b) LMLO with different scan rates. The corresponding Ip–ν1/2 profiles for (c) LMO and (d) LMLO materials. | |
The kinetics of the redox reactions that take place during the charge/discharge process was further verified by the galvanostatic intermittent titration technique (GITT, Fig. 6a). In the GITT test, a short current pulse was applied and then removed, followed by a sharp voltage increase (decrease) and achievement of the thermodynamic equilibrium potential. The kinetics of lithium-ion diffusion could be investigated by comparing the overpotential between the initial state and the final state of the open circuit voltage (OCV) test at the selected voltage.52 As shown in Fig. 6b, LMLO delivers a smaller potential drop (186 mV) than that of pristine LMO (678 mV) at a voltage of about 4.5 V. The difference in the OCV value clearly shows accelerated kinetics of lithium-ion diffusion for LMLO in the 4.5 V region. Upon charging to a higher voltage (Fig. 6c and d), the lower overpotential (273 mV for 4.6 V, 240 mV for 4.7 V) for the LMLO electrode than that of the pristine LMO electrode (606 mV for 4.6 V, 312 mV for 4.7 V) also confirms the positive effect of the modification. Here, based on the equation
|
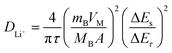 | (2) |
a series of
DLi+ values
versus charge/discharge voltage was generated (
Fig. 6e and f).
53 The results show that the modified LMLO electrode delivers enhanced
DLi+ value.
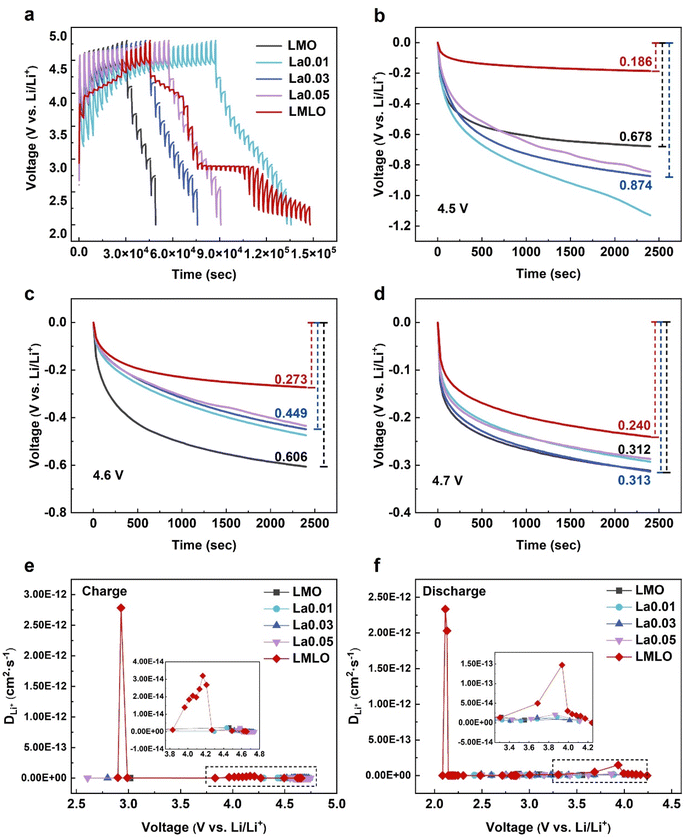 |
| Fig. 6 Hysteresis and kinetics of LMO series cathodes. (a) GITT voltage profiles for LMO series materials. (b–d) Time-elapsed OCV during rest periods at various voltages depicted in (a). DLi+ for (e) the charge process and (f) the discharge process from the GITT data in (a). | |
Structural evolution after modification
Thermal stability is an important indicator for practical application.54 The DSC measurements were conducted with LMO and LMLO materials charged to 4.8 V. As shown in Fig. 7a, the LMO electrode presents a large exothermic peak at 228 °C with a high heat flow of 29.3 J g−1, while the main peak for LMLO electrode shifts to a higher temperature of 239 °C with a much lower heat flow of 5.0 J g−1. This result reveals that lanthurizing and Li/Mn optimization can significantly improve the thermal stability of the Mn-rich LMO cathode.
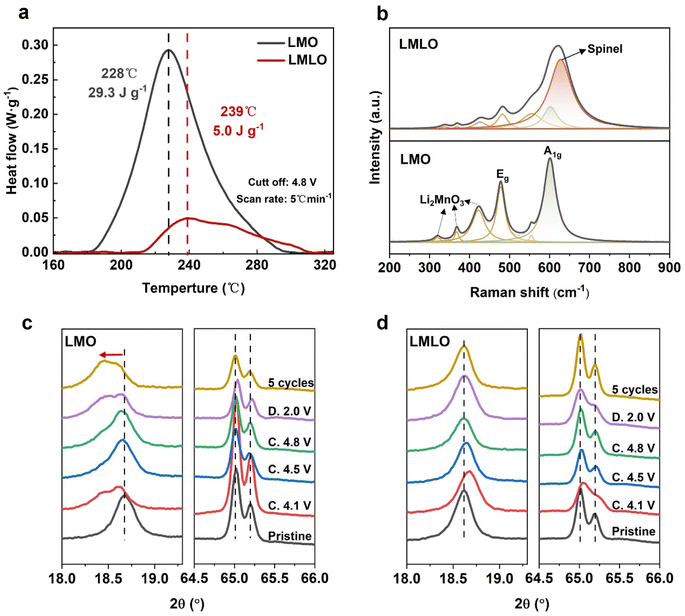 |
| Fig. 7 Structural evolution for the modified material. (a) Differential scanning calorimetry data for charged LMO and LMLO electrodes. (b) Raman spectra of LMO and LMLO materials. (c and d) The ex situ XRD patterns for (c) LMO material and (d) LMLO material in the pristine state, initial charge–discharge process, and after cycling. | |
To confirm the formation of spinel phases, Raman spectra were obtained for the LMO and LMLO materials (Fig. 7b).33,55,56 The Raman band appearing at about 400 cm−1 can be assigned to the monoclinic Li2MnO3 phase. The other two significant Raman peaks appear at about 473 and 593 cm−1 in the spectra, which results from the bending Eg and stretching A1g modes in the Li2MnO3 phase, respectively. It is worth noting that the LMLO material delivers a new peak at about 630 cm−1, which can be attributed to the spinel phase. It indicates the mixed structure of the layered and spinel phases after modification, which consists of the XRD patterns.
To understand the mechanism of how the spinel phase improves the cycling performance, the structural evolution during charge–discharge was monitored. Fig. 7c and d show the ex situ XRD results corresponding to the (003) reflections, representing the unit cell change along the c-axis. In Fig. 7c, the (003) reflection of LMO shifts to a lower angle when charged to 4.1 V, which is likely caused by the coulombic repulsion of the anion layers. Besides, the (003) reflection of LMO splits into two peaks at a voltage of 4.1 V, indicating the appearance of a new phase. With further Li+ removal (charge to 4.5 V, 4.8 V), the (003) reflections undergo an aggressive shift to higher angles, suggesting a drastic contraction of the c-axis due to the phase transition. For comparison, the modified LMLO delivers a more stable peak evolution upon cycling (Fig. 7d). Upon discharge to 2.0 V, the (003) reflection of LMO shifts to a lower angle, which is lower than that of LMLO.
In addition, the batteries were cycled for 5 cycles, and the positive electrodes were taken out for the XRD tests. In Fig. 7c, the (003) reflections of the LMO samples shifted to a lower diffraction angle after 5 cycles. In detail, the (003) reflections of LMO contain a broad shoulder, which is mainly due to the presence of two different phases with close lattice parameters, indicating that a two-phase transition reaction occurs in LMO. As for LMLO, the almost identical shape of the (003) reflections indicates a quasi-single-phase process (Fig. 7d). The continuous single-phase reaction makes lattice contraction to have a buffer process, thus reducing the structural damage. The (003) reflection of LMLO is well sustained, suggesting that the modified LMLO has a more enhanced reversible lattice shrinkage, which is favorable for maintaining the structural integrity during electrochemical cycling.
Based on the characterization results, Fig. 8 proposes the synergistic effect of modification during electrochemical cycling. Pristine LMO material delivers limited capacity due to sluggish kinetics and is accompanied by interfacial side reaction (Fig. 8a). For comparison, a spinel phase is in situ formed and coexists with the bulk layered phase on the modified material (Fig. 8b). The layered-spinel biphase ensures accelerated kinetics, as evidenced by the GITT, CV and EIS results. Besides, the biphase with stabilized La–O bond would mitigate the irreversible oxygen release, which suppresses the interfacial side reaction and further enhances the available capacity. Meanwhile, during the cycling process, the structural evolution is stabilized after modification, as evidenced by the ex situ XRD data.
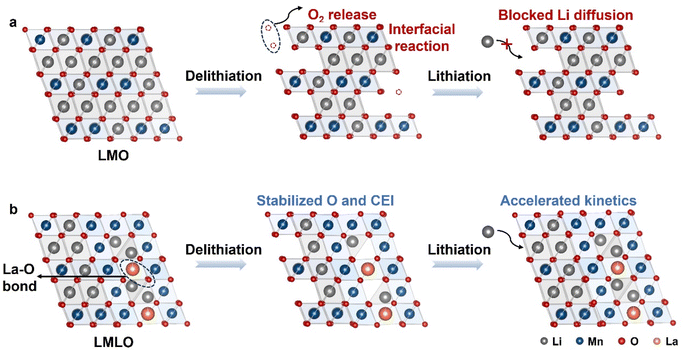 |
| Fig. 8 Proposed mechanism of (a) LMO and (b) LMLO materials during the electrochemical process. | |
Conclusions
To summarize, we have demonstrated a synergistic approach for accelerated kinetics and for realizing high-capacity cycling. We showed that the modified LMLO phase can enhance the Li-ion diffusion. Electrochemical characterization demonstrated that the modified Mn-rich cathode could deliver an enhanced available capacity of 233.4 mA h g−1 at a voltage of 1.5–4.8 V. Our lanthurizing and delithiation approach accelerates the lithium-ion diffusion kinetics and widens the strategies for enhancing the energy density.
Declarations
The author declares that there is no relevant competitive economic interest or personal relationship between them that will hinder the work of this article.
Data availability
The authors confirm that the data supporting the findings of this study are available within the article and its ESI.†
Conflicts of interest
The authors declare no competing financial interest.
Acknowledgements
This research was financially supported by Zhuhai Natural Science Foundation (Grant no. ZH22017003210080PWC), Science Foundation of Faculty of Comprehensive Health Industry (no. 2023DJKCY013), Zhuhai College of Science and Technology Three Levels Talent Construction Project, and College Students' Innovation and Entrepreneurship Training Program (202413684009X, DC2024084).
References
- W. Lee, S. Muhammad, C. Sergey, H. Lee, J. Yoon, Y. M. Kang and W. S. Yoon, Advances in the cathode materials for lithium rechargeable batteries, Angew. Chem., Int. Ed., 2020, 59(7), 2578–2605 CrossRef CAS PubMed.
- T. Kim, W. Song, D.-Y. Son, L. K. Ono and Y. Qi, Lithium-ion batteries: outlook on present, future, and hybridized technologies, J. Mater. Chem. A, 2019, 7(7), 2942–2964 RSC.
- J. Zheng, S. Myeong, W. Cho, P. Yan, J. Xiao, C. Wang, J. Cho and J. G. Zhang, Li-and Mn-rich cathode materials: challenges to commercialization, Adv. Energy Mater., 2017, 7(6), 1601284 CrossRef.
- Y. Chen, Z. Xie, Q. Lv, N. Zhu, S. Shang, N. Wang, Y. Jin and W. Yan, Facilitating structural stability of the Li-rich layered cathode materials by cation rearrangements and Li vacancies, Appl. Surf. Sci., 2023, 639, 158203 CrossRef CAS.
- L. Zeng, H. Liang, B. Qiu, Z. Shi, S. Cheng, K. Shi, Q. Liu and Z. Liu, Voltage decay of Li-rich layered oxides: mechanism, modification strategies, and perspectives, Adv. Funct. Mater., 2023, 33(25), 2213260 CrossRef CAS.
- W. Yang, Oxygen release and oxygen redox, Nat. Energy, 2018, 3(8), 619–620 CrossRef CAS.
- B. Qiu, M. Zhang, Y. Xia, Z. Liu and Y. S. Meng, Understanding and controlling anionic electrochemical activity in high-capacity oxides for next generation Li-ion batteries, Chem. Mater., 2017, 29(3), 908–915 CrossRef CAS.
- S. Kang, D. Choi, H. Lee, B. Choi and Y.-M. Kang, A mechanistic insight into the oxygen redox of Li-rich layered cathodes and their related electronic/atomic behaviors upon cycling, Adv. Mater., 2023, 35(43), 2211965 CrossRef CAS PubMed.
- S. Sharifi-Asl, J. Lu, K. Amine and R. Shahbazian-Yassar, Oxygen release degradation in Li-ion battery cathode materials: mechanisms and mitigating approaches, Adv. Energy Mater., 2019, 9(22), 1900551 CrossRef.
- S. Saha, G. Assat, M. T. Sougrati, D. Foix, H. Li, J. Vergnet, S. Turi, Y. Ha, W. Yang and J. Cabana, Exploring the bottlenecks of anionic redox in Li-rich layered sulfides, Nat. Energy, 2019, 4(11), 977–987 CrossRef CAS.
- E. McCalla, A. M. Abakumov, M. Saubanère, D. Foix, E. J. Berg, G. Rousse, M.-L. Doublet, D. Gonbeau, P. Novák and G. Van Tendeloo, Visualization of O-O peroxo-like dimers in high-capacity layered oxides for Li-ion batteries, Science, 2015, 350(6267), 1516–1521 CrossRef CAS PubMed.
- K. Zhou, S. Zheng, H. Liu, C. Zhang, H. Gao, M. Luo, N. Xu, Y. Xiang, X. Liu, G. Zhong and Y. Yang, Elucidating and mitigating the degradation of cationic-anionic redox processes in Li1.2Mn0.4Ti0.4O2 cation-disordered cathode materials, ACS Appl. Mater. Interfaces, 2019, 11(49), 45674–45682 CrossRef CAS PubMed.
- S. Liu, H. Yue, Y. Mo, L. Luo, X. Wu, S. Yang, Y. Huang and G. Yuan, Retarding the capacity fading and voltage decay of Li-rich Mn-based cathode materials via a compatible layer coating for high-performance lithium-ion batteries, RSC Adv., 2024, 14(36), 26142–26151 RSC.
- X. He, J. Wu, Z. Zhu, H. Liu, N. Li, D. Zhou, X. Zhou, H. Zhang, D. Bresser, Y. Fu, M. J. Crafton, B. D. McCloskey, Y. Chen, K. An, P. Liu, A. Jain, J. Li, W. Yang, Y. Yang, M. Winter and R. Kostecki, Chemical and structural evolution of Li-Mn-rich layered electrodes under different current densities, Energy Environ. Sci., 2022, 15, 4137 RSC.
- Q. Li, Z. Yao, E. Lee, Y. Xu, M. M. Thackeray, C. Wolverton, V. P. Dravid and J. Wu, Dynamic imaging of crystalline defects in lithium-manganese oxide electrodes during electrochemical activation to high voltage, Nat. Commun., 2019, 10(1), 1692 CrossRef PubMed.
- X. D. Zhang, J. L. Shi, J. Y. Liang, Y. X. Yin, J. N. Zhang, X. Q. Yu and Y. G. Guo, Suppressing surface lattice oxygen release of Li-rich cathode materials via heterostructured spinel Li4Mn5O12 coating, Adv. Mater., 2018, 30(29), 1801751 CrossRef PubMed.
- X. Qu, H. Huang, T. Wan, L. Hu, Z. Yu, Y. Liu, A. Dou, Y. Zhou, M. Su, X. Peng, H.-H. Wu, T. Wu and D. Chu, An integrated surface coating strategy to enhance the electrochemical performance of nickel-rich layered cathodes, Nano Energy, 2022, 91, 106665 CrossRef CAS.
- J. Wu, Z. Chen, J. Cheng, Q. Wen, W. Gao, X. Wang and C. Tuo, Accelerating Li+ intercalation kinetics through synergetic modification in Li-rich cathode, J. Mater. Sci., 2023, 58, 16785–16796 CrossRef CAS.
- B. M. de Boisse, J. Jang, M. Okubo and A. Yamada, Cobalt-free O2-type lithium-rich layered oxides, J. Electrochem. Soc., 2018, 165(16), A3630–A3633 CrossRef.
- X. Li, Y. Qiao, S. Guo, K. Jiang, M. Ishida and H. Zhou, A new type of Li-rich rock-salt oxide Li2Ni1/3Ru2/3O3 with reversible anionic redox chemistry, Adv. Mater., 2019, 31(11), 1807825 CrossRef PubMed.
- D. Liu, X. Fan, Z. Li, T. Liu, M. Sun, C. Qian, M. Ling, Y. Liu and C. Liang, A cation/anion co-doped Li1.12Na0.08Ni0.2Mn0.6O1.95F0.05 cathode for lithium ion batteries, Nano Energy, 2019, 58, 786–796 CrossRef CAS.
- K. Xu, Electrolytes and interphases in Li-ion batteries and beyond, Chem. Rev., 2014, 114(23), 11503–11618 CrossRef CAS PubMed.
- Y. Wu, K. Zhou, F. Ren, Y. Ha, Z. Liang, X. Zheng, Z. Wang, W. Yang, M. Zhang, M. Luo, C. Battaglia, W. Yang, L. Zhu, Z. Gong and Y. Yang, Highly reversible Li2RuO3 cathodes in sulfide-based all solid-state lithium batteries, Energy Environ. Sci., 2022, 15(8), 3470–3482 RSC.
- X. Qu, Z. Yu, D. Ruan, A. Dou, M. Su, Y. Zhou, Y. Liu and D. Chu, Enhanced electrochemical performance of Ni-rich cathode materials with Li1.3Al0.3Ti1.7(PO4)3 coating, ACS Sustain. Chem. Eng., 2020, 8(15), 5819–5830 CrossRef CAS.
- S. Wang, Y. Li, J. Wu, B. Zheng, M. J. McDonald and Y. Yang, Toward a stabilized lattice framework and surface structure of layered lithium-rich cathode materials with Ti modification, Phys. Chem. Chem. Phys., 2015, 17(15), 10151–10159 RSC.
- C.-C. Wang and A. Manthiram, Influence of cationic substitutions on the first charge and reversible capacities of lithium-rich layered oxide cathodes, J. Mater. Chem. A, 2013, 1(35), 10209–10217 RSC.
- R. Yu, X. Wang, Y. Fu, L. Wang, S. Cai, M. Liu, B. Lu, G. Wang, D. Wang and Q. Ren, Effect of magnesium doping on properties of lithium-rich layered oxide cathodes based on a one-step co-precipitation strategy, J. Mater. Chem. A, 2016, 4(13), 4941–4951 RSC.
- X. Yang, M. Lin, G. Zheng, J. Wu, X. Wang, F. Ren, W. Zhang, Y. Liao, W. Zhao, Z. Zhang, N. Xu, W. Yang and Y. Yang, Enabling stable high-voltage LiCoO2 operation by using synergetic interfacial modification strategy, Adv. Funct. Mater., 2020, 30(43), 2004664 CrossRef CAS.
- J. Rana, J. K. Papp, Z. Lebens-Higgins, M. Zuba, L. A. Kaufman, A. Goel, R. Schmuch, M. Winter, M. S. Whittingham, W. Yang, B. D. McCloskey and L. F. J. Piper, Quantifying the capacity contributions during activation of Li2MnO3, ACS Energy Lett., 2020, 5(2), 634–641 CrossRef CAS.
- J. Wu, X. Zhang, S. Zheng, H. Liu, J. Wu, R. Fu, Y. Li, Y. Xiang, R. Liu, W. Zuo, Z. Cui, Q. Wu, S. Wu, Z. Chen, P. Liu, W. Yang and Y. Yang, Tuning oxygen redox reaction through inductive effect with proton insertion in Li-rich oxides, ACS Appl. Mater. Interfaces, 2020, 12(6), 7277–7284 CrossRef CAS PubMed.
- M. Cai, Y. Dong, M. Xie, W. Dong, C. Dong, P. Dai, H. Zhang, X. Wang, X. Sun, S. Zhang, M. Yoon, H. Xu, Y. Ge, J. Li and F. Huang, Stalling oxygen evolution in high-voltage cathodes by lanthurization, Nat. Energy, 2023, 8(2), 159–168 CrossRef CAS.
- J. Wan, J. Zhu, Y. Xiang, G. Zhong, X. Liu, Y. Li, K. H. L. Zhang, C. Hong, J. Zheng, K. Wang and Y. Yang, Revealing the correlation between structure evolution and electrochemical performance of high-voltage lithium cobalt oxide, J. Energy Chem., 2021, 54, 786–794 CrossRef CAS.
- J. Wu, Z. Cui, J. Wu, Y. Xiang, H. Liu, S. Zheng, W. Yang and Y. Yang, Suppression of voltage-decay in Li2MnO3 cathode via reconstruction of layered-spinel coexisting phases, J. Mater. Chem. A, 2020, 8(36), 18687–18697 RSC.
- Y. J. Hao, Q. Y. Lai, L. Wang, X.-Y. Xu and H. Y. Chu, Electrochemical performance of a high cation-deficiency Li2Mn4O9/active carbon supercapacitor in LiNO3 electrolyte, Synth. Met., 2010, 160(7), 669–674 CrossRef CAS.
- B. H. Toby, EXPGUI, a graphical user interface for GSAS, J. Appl. Crystallogr., 2001, 34(2), 210–213 CrossRef CAS.
- K. Momma and F. Izumi, VESTA 3 for three-dimensional visualization of crystal, volumetric and morphology data, J. Appl. Crystallogr., 2011, 44, 1272–1276 CrossRef CAS.
- T. Matsunaga, H. Komatsu, K. Shimoda, T. Minato, M. Yonemura, T. Kamiyama, S. Kobayash, T. Kato, T. Hirayama, Y. Ikuhara, H. Arai, Y. Ukyo, Y. Uchimoto and Z. Ogumi, Dependence of structural defects in Li2MnO3 on synthesis temperature, Chem. Mater., 2016, 28(12), 4143–4150 CrossRef CAS.
- D. Luo, X. Ding, J. Fan, Z. Zhang, P. Liu, X. Yang, J. Guo, S. Sun and Z. Lin, Accurate control of initial coulombic efficiency for lithium-rich manganese-based layered oxides by surface multicomponent integration, Angew. Chem., Int. Ed., 2020, 59(51), 23061–23066 CrossRef CAS PubMed.
- X.-D. Zhang, J.-L. Shi, J.-Y. Liang, Y.-X. Yin, J.-N. Zhang, X.-Q. Yu and Y.-G. Guo, Suppressing surface lattice oxygen release of Li-rich cathode materials via heterostructured spinel Li4Mn5O12 coating, Adv. Mater., 2018, 30(29), 1801751 CrossRef PubMed.
- C. Delmas, C. Fouassier and P. Hagenmuller, Structural classification and properties of the layered oxides, Physica B+C, 1980, 99(1), 81–85 CrossRef CAS.
- J. B. Goodenough and K.-S. Park, The Li-ion rechargeable battery: a perspective, J. Am. Chem. Soc., 2013, 135(4), 1167–1176 CrossRef CAS.
- L. Xiao, J. Xiao, X. Yu, P. Yan, J. Zheng, M. Engelhard, P. Bhattacharya, C. Wang, X.-Q. Yang and J.-G. Zhang, Effects of structural defects on the electrochemical activation of Li2MnO3, Nano Energy, 2015, 16, 143–151 CrossRef CAS.
- P. Yan, L. Xiao, J. Zheng, Y. Zhou, Y. He, X. Zu, S. X. Mao, J. Xiao, F. Gao and J.-G. Zhang, Probing the degradation mechanism of Li2MnO3 cathode for Li-ion batteries, Chem. Mater., 2015, 27(3), 975–982 CrossRef CAS.
- F. Dogan, J. R. Croy, M. Balasubramanian, M. D. Slater, H. Iddir, C. S. Johnson, J. T. Vaughey and B. Key, Solid state NMR studies of Li2MnO3 and Li-rich cathode materials: proton insertion, local structure, and voltage fade, J. Electrochem. Soc., 2015, 162(1), A235–A243 CrossRef CAS.
- Y. Denis, K. Yanagida, Y. Kato and H. Nakamura, Electrochemical activities in Li2MnO3, J. Electrochem. Soc., 2009, 156(6), A417–A424 CrossRef.
- D. Luo, H. Zhu, Y. Xia, Z. Yin, Y. Qin, T. Li, Q. Zhang, L. Gu, Y. Peng, J. Zhang, K. M. Wiaderek, Y. Huang, T. Yang, Y. Tang, S. Lan, Y. Ren, W. Lu, C. M. Wolverton and Q. Liu, A Li-rich layered oxide cathode with negligible voltage decay, Nat. Energy, 2023, 8, 1078–1087 CrossRef CAS.
- X. H. Zhang, S. Cao, R. Z. Yu, C. Li, Y. Huang, Y. Wang, X. Y. Wang and G. R. Chen, Improving electrochemical performances of Li-rich layered Mn-based oxide cathodes through K2Cr2O7 solution treatment, ACS Appl. Energy Mater., 2019, 2(2), 1563–1571 CrossRef CAS.
- E. Hu, X. Yu, R. Lin, X. Bi, J. Lu, S. Bak, K.-W. Nam, H. L. Xin, C. Jaye, D. A. Fischer, K. Amine and X.-Q. Yang, Evolution of redox couples in Li- and Mn-rich cathode materials and mitigation of voltage fade by reducing oxygen release, Nat. Energy, 2018, 3(8), 690–698 CrossRef CAS.
- W. Dudan, W. Fei, Z. Huanhuan, L. Yupeng, Y. Nachuan and C. Kanghua, Electrochemical performance improvement of Li2MnO3 cathode materials by MgF2 coating, J. Electrochem., 2020, 26(2), 289–297 Search PubMed.
- W. Zhang, X. Sun, Y. Tang, H. Xia, Y. Zeng, L. Qiao, Z. Zhu, Z. Lv, Y. Zhang, X. Ge, S. Xi, Z. Wang, Y. Du and X. Chen, Lowering charge transfer barrier of LiMn2O4 via nickel surface doping to enhance Li+ intercalation kinetics at subzero temperatures, J. Am. Chem. Soc., 2019, 141(36), 14038–14042 CrossRef CAS PubMed.
- Y. Wei, J. Cheng, D. Li, Z. Zeng, H. Liu, H. Zhang, F. Ji, X. Geng, J. Lu and L. Ci, A structure self-healing Li-rich cathode achieved by lithium supplement of Li-rich LLZO coating, Adv. Funct. Mater., 2023, 33(22), 2214775 CrossRef CAS.
- Y. Yue, N. Li, L. Li, E. E. Foley, Y. Fu, V. S. Battaglia, R. J. Clément, C. Wang and W. Tong, Redox behaviors in a Li-excess cation-disordered Mn–Nb–O–F rocksalt cathode, Chem. Mater., 2020, 32(11), 4490–4498 CrossRef CAS.
- S. Lou, Q. Liu, F. Zhang, Q. Liu, Z. Yu, T. Mu, Y. Zhao, J. Borovilas, Y. Chen, M. Ge, X. Xiao, W.-K. Lee, G. Yin, Y. Yang, X. Sun and J. Wang, Insights into interfacial effect and local lithium-ion transport in polycrystalline cathodes of solid-state batteries, Nat. Commun., 2020, 11(1), 5700 CrossRef CAS PubMed.
- Q. Fan, K. Lin, S. Yang, S. Guan, J. Chen, S. Feng, J. Liu, L. Liu, J. Li and Z. Shi, Constructing effective TiO2 nano-coating for high-voltage Ni-rich cathode materials for lithium ion batteries by precise kinetic control, J. Power Sources, 2020, 477(30), 228745 CrossRef CAS.
- C. M. Julien and M. Massot, Lattice vibrations of materials for lithium rechargeable batteries III. Lithium manganese oxides, Mater. Sci. Eng., B, 2003, 100(1), 69–78 CrossRef.
- C. S. Johnson, N. Li, J. T. Vaughey, S. A. Hackney and M. M. Thackeray, Lithium–manganese oxide electrodes with layered–spinel composite structures xLi2MnO3·(1−x)Li1+yMn2−yO4 (0<x<1, 0⩽y⩽0.33) for lithium batteries, Electrochem. Commun., 2005, 7(5), 528–536 CrossRef CAS.
|
This journal is © The Royal Society of Chemistry 2024 |
Click here to see how this site uses Cookies. View our privacy policy here.