DOI:
10.1039/D4RA06187J
(Paper)
RSC Adv., 2024,
14, 36771-36781
Direct dimethyl carbonate synthesis from CO2 and methanol over a flower-like CeO2 catalyst with 2-cyanopyridine as a dehydrating agent in continuous packed-bed reactor
Received
27th August 2024
, Accepted 31st October 2024
First published on 18th November 2024
Abstract
A flower-like CeO2 catalyst was successfully synthesized using an acrylamide graft copolymerized on glucose under hydrothermal conditions and used for the direct synthesis of dimethyl carbonate (DMC) from CO2 and CH3OH in a packed-bed reactor with 2-cyanopyridine as a dehydrating agent. The synthesized flower-like CeO2 exhibited both basicity and acidity properties with values of 300 μmol g−1 and 80 μmol g−1, respectively, according to CO2-TPD and NH3-TPD results. The effect of reaction parameters such as reaction temperature, feed ratio, catalyst quantity, and operating pressure on the DMC production over the flower-like CeO2 catalyst was investigated. The optimum conditions were found to be a temperature of 120 °C, catalyst weight of 1.0 g, CH3OH
:
CO2 ratio of 1
:
1, and pressure of 30 bar, which provided the highest CH3OH conversion, DMC selectivity, and DMC yield of 86.6%, 99.3%, and 86.0%, respectively. Furthermore, no changes were observed in the structure, morphology, and particle size of the flower-like CeO2 catalyst after the DMC synthesis reaction, indicating that the synthesized catalyst was resistant to the reaction test under such optimum reaction conditions.
1. Introduction
Climate change is a major issue caused by increasing carbon dioxide (CO2) emissions into the atmosphere, and significant attention is being paid globally to reducing these emissions by converting CO2 into value-added fuels or chemicals. The conversion of CO2 to dimethyl carbonate (DMC) has received a lot of attention because DMC is an environmentally friendly and low toxicity chemical. DMC stands out as a remarkably versatile molecule with multifaceted chemical reactivity and serves as an exemplary green chemical methylating agent and solvent, finding wide application across various industries. It is also one of the green chemicals that is the raw material to produce electrolytes used in lithium-ion batteries due to its high dielectric constant and potential gasoline additives due to its high oxygen content and good blending properties as compared to methyl tert-butyl ether (MTBE).1,2 Traditionally, DMC has been produced by several methods such as the phosgenation of methanol3 and the oxidative carbonylation of methanol.4 However, both procedures have significant disadvantages, such as the high toxicity of phosgene and the utilization of hazardous CO. As a result, the direct synthesis of DMC from methanol (CH3OH) and CO2 (reaction (1)) is considered one of the most promising ways to effectively utilize carbon resources and reduce greenhouse gas emissions, yielding just water as a byproduct. |
 | (1) |
Direct DMC synthesis from CH3OH and CO2 is considered a green and sustainable route; however, it typically yields low amounts of DMC due to thermodynamic limitations (ΔG = +26 kJ mol−1), DMC hydrolysis, and catalyst deactivation. Water removal from the reaction system is expected to shift the reaction equilibrium toward DMC synthesis resulting in enhanced DMC yield. Therefore, the catalytic activity can be boosted by water removal using several dehydrating strategies including dehydration of methanol before the reaction,5 the use of organic molecules6 or inorganic (zeolite) materials7 as a dehydrating agent, and the use of a membrane reactor.8 Several studies have reported the use of different dehydrating agents such as CH3I,9 butylene oxide,10 acetonitrile,11 and 2-cyanopyridine12–16 for water removal from the DMC synthesis reaction. Honda and co-workers16 examined the use of various dehydrating agents for direct DMC synthesis from CH3OH and CO2 using CeO2 catalyst in a batch system. They found that the use of 2-cyanopyridine as a dehydrating agent resulted in excellent catalytic activity. Moreover, 2-picolinamide product from the reaction between 2-cyanopyridine and water can be easily removed from the reaction mixture and recyclable back to 2-cyanopyridine by a dehydration reaction over a catalyst.
One of the challenges for researchers is to find suitable catalyst materials that could improve the catalytic activity for the synthesis of DMC. Generally, acid and basic sites are required for the synthesis of DMC from CO2 and CH3OH. CH3OH molecules are activated at both acid and basic sites, while CO2 molecules are adsorbed at the basic site of the catalyst. Therefore, the development of catalysts with high acidity and basicity properties are an interesting area that is currently being investigated.3,17 So far, many studies on the direct DMC synthesis with homogeneous and heterogeneous catalysts have been published. However, homogeneous catalysts have many disadvantages such as being difficult to recycle, requiring the co-catalyst as a support to increase activity, which leads to high processing costs, as well as easily forming water as a side effect, which decomposes the catalyst and leads to deactivation.18,19 Therefore, heterogeneous catalysts received more attention because they can overcome these disadvantages and exhibit higher stability compared to homogeneous catalysts. There are many types of metal oxides such as CeO2, ZrO2, SiO2, Al2O3 TiO2 and ZnO20,21 as well as some mixed metal oxides such as CeO2–ZrO2, TiO2–CeO2, CeO2–ZnO, ZrO2–MgO and MgO–SiO28,10,22–25 have been reported as heterogeneous catalyst for the direct DMC synthesis. Among these catalysts, cerium oxide (CeO2) has gained a lot of attention and has become a favorable choice due to its acid–base properties, redox properties, suitable crystal structure, high oxygen storage capacity and high oxygen vacancies26–29 which induce ability in CO2 adsorption and CH3OH activation led to increased catalytic activity. P. Kumar et al.30 investigated the synthesis of DMC from CO2 and CH3OH over CeO2 catalyst using a molecular sieve as a dehydrating agent in a batch reactor. They found that the catalytic performance was correlated with the basic and acidic properties of the CeO2 catalyst, resulting in a DMC yield of 2.046 mmol DMC per g cat. at a reaction temperature of 120 °C, pressure of 150 bar, and reaction time of 4 h. D. Stoian et al.31 studied the efficiency of the direct DMC synthesis from CO2 and CH3OH over the CeO2 catalyst with the presence of 2-cyanopyridine as a dehydrating agent in both batch and continuous operations. They reported that high DMC yield was observed due to the right balance in basicity and acidity properties of CeO2 catalyst. Furthermore, it has been reported that CeO2 not only acts as an excellent catalyst in DMC synthesis but also in dehydration reaction of dehydrating agent (2-cyanopyridine, 2-CP) to remove water byproduct in both batch and continuous operations.12,15
Recently, the synthesis of CeO2 catalyst with a special morphology such as nanorods,32 nanotubes,33 nanocubes,34 nanoplates35 and nanospheres36 have received great attention. The different crystal facets exposed on the surface of CeO2 nanostructures were strongly controlled by their morphologies, resulting in differential properties that can influence the interaction between the CeO2 surface and the adsorbed reactants, as well as the catalytic performance. Wang et al.28 investigated nano-CeO2 catalysts with various morphologies (spindle, rod, cube, and octahedron) for the DMC synthesis from CH3OH and CO2 and found that spindle-like CeO2 provided better catalytic efficiency than other morphologies because the spindle-like CeO2 displayed more active (111) planes and acid–base sites, resulting in higher DMC yield. Three dimensional (3D) CeO2 hierarchical structures, such as flower-like assembled from 1D or 2D structures, have a significant impact on performance improvements. It provided high active surface areas that facilitated surface reactions, high specific surface area and high surface-to-bulk ratio.37–39 Moreover, CeO2 catalyst with flower-like morphology has been rarely reported for direct DMC synthesis reaction from CH3OH and CO2.
Therefore, this study is interested in synthesizing a flower-like CeO2 catalyst using a graft copolymerization reaction between acrylamide and glucose under hydrothermal treatments and applied for the direct synthesis of DMC from CO2 and CH3OH reaction with 2-cyanopyridine as a desiccant in a continuous tubular packed-bed reactor. The synthesized catalyst was characterized by XRD, SEM, BET, CO2-TPD, O2-TPD and NH3-TPD techniques. Furthermore, the effect of reaction parameters such as temperature, feed (CH3OH
:
CO2) ratio, catalyst weight and pressure on catalytic performance for the DMC synthesis are also investigated.
2. Methodology
2.1. Catalyst preparation
A synthetic procedure is as follows: 3.6 g of glucose was dissolved in 180 mL of distilled water and stirred until completely dissolved at room temperature. 2.12 g of acrylamide and 4.34 g of cerium(III) nitrate hexahydrate were then added to the previous solution until became transparent. Subsequently, the pH of the solution was adjusted to 10–12 by adding 8–10 mL of 28–30% wt. ammonia solution and vigorously stirring. The solution was changed from a transparent solution to a viscous gel. After 5 h of continuous stirring, the brown gel was transferred to a hydrothermal bomb and stored in the oven at 180 °C for 72 h. The hydrothermal bomb was naturally cooled to room temperature. The brown suspension was washed three times with distilled water and once with ethanol using a centrifuge at 9000 rpm for 10 min before being dried overnight at 60 °C. Finally, the obtained suspension was calcined in two steps: first, at 600 °C for 12 h under Ar gas flow. Second, at 400 °C for 10 h with an air flow and a heating rate of 2 °C min−1.
2.2. Catalyst characterization
The crystalline structure of the synthesized and spent catalysts were characterized using X-ray diffraction (XRD, Rigaku TTRAX III diffractometer) with Cu Kα radiation (λ = 1.5418 Å) at an accelerating voltage of 40 kV and current of 30 mA. The scanning range of 2θ was set from 20° to 90° with a step width of 0.02°. The morphology of the CeO2 samples was investigated using Thermo Scientific Phenom Pharos G2 Desktop Field Emission Gun-Scanning Electron Microscope (FEG-SEM) with an accelerating voltage of 10 kV. Textural properties of the synthesized catalyst were studied by nitrogen physisorption technique at −196 °C using Quantachrome Autosorb-1. Prior to the measurements, the sample was degassed in vacuum to clean the catalyst surface. The specific surface area was determined using the Brunauer–Emmett–Teller (BET) method. The basicity and acidity of the synthesized catalyst were characterized using CO2- and NH3-temperature programmed desorption (TPD), respectively. Before starting the TPD study, the catalyst sample was packed into a quartz reactor and first pretreated at 150 °C for 1 h with a flow rate of 100 mL min−1 Argon gas (Ar) and then cooled to room temperature. After pretreatment, the sample was exposed to the corresponding gas mixtures at different temperatures. Individually, 100 mL min−1 of 5% vol. CO2/Ar was fed at 100 °C (CO2-TPD) or 50 mL min−1 of 5% vol. NH3/Ar was fed at 50 °C (NH3-TPD) to the system for 2 h, then cooled to room temperature by continuing the gas flow and left overnight. During the TPD process, the temperature was increased by 5 °C min−1 from 25 to 700 °C under Ar flow rate of 100 mL min−1. The gas (CO2 or NH3) desorption profiles were measured using a real-time quadrupole mass spectrometer gas analyzer (GSD 320, OmniStar). O2-temperature programmed desorption (O2-TPD) was also measured on the above instrument. The sample (1.0 g) was first pretreated with 100 mL min−1 of 10% O2/Ar at 700 °C for 1 h and then cooled to ambient temperature. After that, the sample was flushed with Ar to eliminate excess/physisorption of oxygen. The oxygen desorption amount was continuously monitored using an on-line mass spectrometer (GSD 320, OmniStar) in the presence of 100 mL min−1 of Ar, while the temperature was ramped up from room temperature to 800 °C at a heating rate of 5 °C min−1.
2.3. Catalytic performance test
The catalytic activity of the CeO2 catalyst for the synthesis of DMC from CH3OH and CO2 were evaluated by using a continuous tubular packed-bed reactor. The schematic for the DMC synthesis is shown in Fig. 1. One gram of catalyst was packed inside a stainless-steel tube between a thin layer of quartz wool (I.D. = 10 mm, O.D. = 13 mm). The heater temperature is measured by a K-type thermocouple located along the wall of the reactor near the catalyst bed and the system pressure is determined by a pressure gauge and controlled by a back pressure regulator (BPR). 2-Cyanopyridine (2-CP) as a dehydrator was dissolved in CH3OH at a stoichiometric molar ratio (2-CP
:
CH3OH = 1
:
2).12 In the experiment, gaseous CO2 was introduced into the reactor through a mass flow regulator to increase the pressure of the system to the desired reaction pressure. The molar feed (CH3OH
:
CO2) ratio was adjusted differently (1
:
2, 1
:
1, and 2
:
1). Separation of products is divided into two steps using 2-stage condensers. The first step captures the unwanted substance with a high boiling point (2-CP, 2-picolinamide) and the other captures the desired product substance (DMC, CH3OH). The gas and liquid products analysis were performed by gas chromatography (Shimadzu GC-2014, FID-TCD detector).
 |
| Fig. 1 Schematic illustration of the reaction system for direct synthesis of dimethyl carbonate. | |
3. Results and discussion
3.1. Catalyst characterizations
3.1.1. Structural analysis. The X-ray diffraction patterns of the flower-like CeO2 catalyst before and after the reaction testing are shown in Fig. 2. The fluorite structure of CeO2 (PDF No. 01-075-8371) was presented as a major crystalline phase in the flower-like CeO2 catalyst before the reaction at 2θ of 28.5, 33.1, 47.5, 56.3, 59.1, 69.4, 76.7, 79.1, and 88.4°, corresponding to (111), (200), (220), (311), (222), (400), (331), (420), (422) planes, consistent with the literature.37–39 It indicated that the calcination of the Ce(OH)CO3 complex at 400 °C under air flow resulted in a complete formation of the CeO2 structure. After reaction testing, the spent flower-like CeO2 catalyst was calcined again at 400 °C under air flow and then analyzed using XRD. The XRD patterns of the spent CeO2 structure remained unchanged. This confirmed that the CeO2 catalyst was resistant to the reaction test at the reaction temperature of 120 °C and reaction pressure of 10 bar. The crystallite sizes of CeO2 before and after the reaction can be determined using the Scherrer equation, obtaining values of 16.8 and 15.6 nm, respectively. These crystallite sizes were close to Z. Zongcheng et al.40 who reported crystallite sizes of flower-like CeO2 of 15.6 nm.
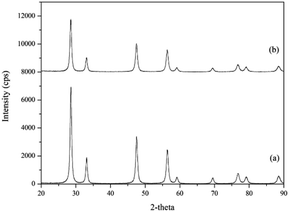 |
| Fig. 2 XRD diffractograms of the flower-like CeO2 catalyst: (a) before and (b) after reaction. | |
3.1.2. Morphology and particle size analysis. The morphology and particle sizes of the synthesized flower-like CeO2 catalyst prepared by hydrothermal treatments and calcined at 400 °C (before reaction) and the spent flower-like CeO2 calcined at 400 °C (after reaction) were examined by SEM images as shown in Fig. 3 and 4, respectively. It was found that the synthesized flower-like CeO2 in Fig. 3 appeared as three-dimensional (3D) flower-like mesoporous microspheres with a diameter of 3–4 μm. The microspheres consist of numerous petal-like plates with thickness of less than 100 nm connected to each other to form an open porous structure. Furthermore, there were no changes in the morphology and particle size of the spent flower-like CeO2 after reaction (Fig. 4) when compared to the catalyst before the reaction (Fig. 3). This indicated that the flower-like shape of the CeO2 catalyst was resistant to the reaction test at the reaction temperature of 120 °C and reaction pressure of 30 bar, which was consistent with the XRD data.
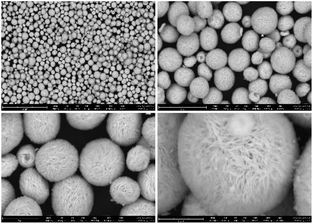 |
| Fig. 3 SEM image of the synthesized flower-like CeO2 catalyst (before reaction). | |
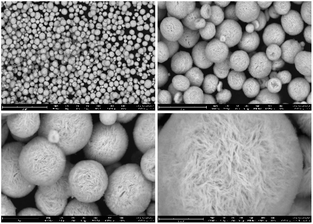 |
| Fig. 4 SEM image of the spent flower-like CeO2 catalyst (after reaction). | |
Different morphologies of CeO2 expose distinct crystal facets on the surface, resulting in varied surface properties such as particle size, surface area, and acid–base sites, as well as differing catalytic activities. The cubic fluorite structure of CeO2, as confirmed by XRD results, typically comprises three crystal facets: (100), (110), and (111). The surface properties of CeO2 vary depending on these exposed facets, which have distinct oxygen vacancy formation energies, leading to varying quantities of oxygen vacancies or defects on different planes.41,42 The synthesis of CeO2 with different morphologies or exposed facets is influenced by the preparation conditions employed. For instance, polycrystalline CeO2 can be prepared by the thermal decomposition of cerium nitrate,43 which mainly terminates with the (111) surface while octahedra, rods, and cubes morphologies can be synthesized by hydrothermal synthesis.44 The octahedra, sheets, spheres and spindle-like morphologies also expose the (111) plane while cubes expose the (100) plane and the rods consist of the (110) and (100) surfaces.28,45–47 From Fig. 3 and 4, the flower-like structure of the CeO2 catalyst was formed by numerous nanosheets, indicating that the observed flower-like CeO2 exposed the (111) surface plane. Z. Zongcheng et al.40 used HR-TEM to analyze the crystal facets of the flower-like CeO2 and found lattice spacings corresponding to the (111) planes of CeO2 which were consistent with Q. Wang et al.48
3.1.3. Porosity analysis. The N2 adsorption–desorption isotherm as shown in Fig. 5 was used to characterize the porous properties of the synthesized flower-like CeO2 catalyst. The synthesized catalyst exhibited a type-IV isotherm with a hysteresis loop, attributed to capillary condensation in the mesopores, indicating the presence of a mesoporous structure in the flower-like CeO2 catalyst, which was consistent with the SEM data. The appeared hysteresis loop related to the mesoporous with tapered plate pore type with four opening sides (Fig. 5, inset). The flower-like CeO2 catalyst had a specific BET surface area of 26.06 m2 g−1. The total pore volume and average pore diameter were 0.122 m3 g−1 and 93.61 Å, respectively.
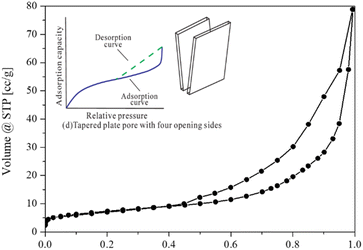 |
| Fig. 5 N2 adsorption–desorption isotherm of the flower-like CeO2 catalyst and isotherm for tapered plate pore with four opening sides (inset).49 | |
3.1.4. Possible mechanism of the flower-like CeO2 microspheres formation. The flower-like CeO2 microspheres were produced by calcining a flower-like Ce(OH)CO3 microspheres twice.50,51 The initial step was calcination at 600 °C for 12 h under inert gas to decompose Ce(OH)CO3, followed by calcination at 400 °C for 10 h under air environment to oxidize Ce2O3 into CeO2 structure, as described in eqn (2) and (3). The flower-like Ce(OH)CO3 microspheres were synthesized via acrylamide graft copolymerization on glucose, with cerium(III) nitrate hexahydrate as a Cerium source. Under basic conditions, cerium salts precipitated to generate cerium hydroxide [Ce(H2O)x(OH)y], and acrylamide could be graft-copolymerized onto glucose to form graft-copolymers.50 Nevertheless, in the hydrothermal process, these graft copolymers were easily decomposed, yielding many various N-containing organic molecules. As a result, a plausible formation mechanism is proposed: the created N-containing organic molecules interacted with [Ce(H2O)x(OH)y] particles to form Ce(OH)CO3–N–R hybrids, which subsequently self-assemble to form the flower-like Ce(OH)CO3 microspheres.51 |
 | (2) |
|
 | (3) |
3.1.5. Basicity, acidity and oxygen vacancies analysis. It has been reported that acid and basic sites presented on the surface of the catalysts have been identified as active sites for DMC synthesis from CH3OH and CO2. The CO2-TPD profile as shown in Fig. 6 showed the interaction between adsorbate (gaseous CO2) and absorbent (flower-like CeO2) in the temperature ranges of 25–700 °C. At 100–200 °C, which is the optimum temperature for DMC synthesis, CO2 was desorbed at low temperature and considered as weak basic site. This had a significant effect on DMC production. The calculated amount of basic site on the flower-like CeO2 catalyst surface was 300 μmol g−1. The NH3-TPD profile of the flower-like CeO2 catalyst in the temperature ranges of 25–700 °C is shown in Fig. 7. The desorbed NH3 from the surface of the flower-like CeO2 catalyst occurred in a wide peak ranging from 40 to 700 °C, corresponding to the weak, medium and strong acid site, with a total NH3 quantity of 80 μmol g−1. As a result, it can be confirmed that CeO2 catalysts have both basic and acidic sites, allowing them to behave as bifunctional acid–base catalysts. The CeO2 catalyst surface consists of three types of surface-active sites that coexist on its surface, including (i) oxygen vacancies as redox sites, (ii) coordinately unsaturated Ce cations near the oxygen vacancies as Lewis's acid sites, and (iii) nearby oxygen ions as Lewis's basic sites.27 The presence of oxygen vacancies within the flower-like CeO2 catalyst was investigated using the O2-TPD technique, as shown in Fig. 8. The O2-TPD profile of the catalyst exhibited two desorption peaks at 400–600 °C and 600–800 °C. The lower temperature peak (400–600 °C) is attributed to desorbed oxygen that adsorbed on oxygen vacancies, which readily desorb from the surface. The higher temperature peak (600–800 °C) could be assigned to oxygen within the bulk lattice of the catalyst.52
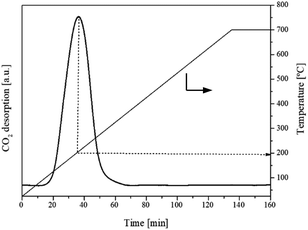 |
| Fig. 6 CO2-TPD profile of the flower-like CeO2 catalyst. | |
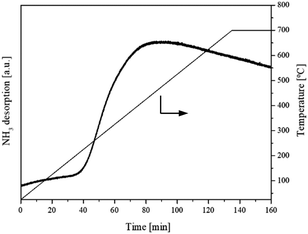 |
| Fig. 7 NH3-TPD profile of the flower-like CeO2 catalyst. | |
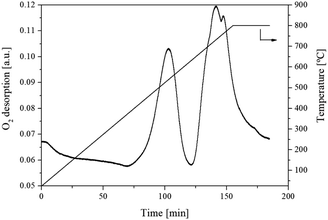 |
| Fig. 8 O2-TPD profile of the flower-like CeO2 catalyst. | |
3.2. Catalytic behavior
As described earlier, 2-cyanopyridine (2-CP), dissolved in CH3OH at a 2-CP
:
CH3OH molar ratio of 1
:
2, was utilized as a dehydrator to remove water from the reaction system and push the reaction equilibrium towards DMC synthesis. The hydration of 2-cyanopyridine gives 2-picolinamide (2-PA) product (eqn (4)), which is also catalyzed by the CeO2 catalyst. The produced 2-picolinamide can be readily desorbed from the catalyst surface, easily removed from the reaction mixture and dehydrated to obtain 2-cyanopyridine. However, the generated 2-picolinamide can interact with CH3OH to produce methyl picolinate (2-MP) and ammonia by-products, as shown in eqn (5).14 |
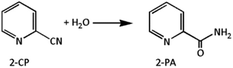 | (4) |
|
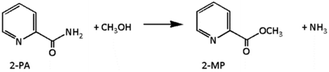 | (5) |
Tamura et al.13 proposed a possible reaction mechanism of 2-cyanopyridine hydration by CeO2 catalyst which can be also used to described in this work as shown in Scheme 1. The hydration occurs by dissociating H2O to produce Hδ+ and OHδ− ions on the surface of CeO2 catalyst (step 1). In step 2, nitrile and Ce–OHδ− are in equilibrium with the nitrile – Ce–OHδ− adsorption complex. In step 3, OHδ− and Hδ+ on the CeO2 surface were attached to the cyano group of 2-CP, forming an amide (2-PA). In addition, the effects of reaction parameters such as temperature (3.2.1), feed ratio (CH3OH
:
CO2) (3.2.2), catalyst amount (3.2.3) and pressure (3.3.4) on the DMC production over the flower-like CeO2 catalyst were investigated to optimize the reaction conditions.
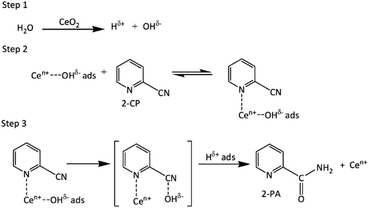 |
| Scheme 1 Proposed reaction mechanism for the 2-cyanopyridine (2-CP) hydrolysis to form 2-picolinamide (2-PA) over the CeO2 catalyst during the DMC synthesis from CH3OH and CO2.13 | |
3.2.1. Effect of reaction temperature. The influence of reaction temperature on the catalytic activity of the flower-like CeO2 catalyst was investigated at various temperatures ranging from 100 to 140 °C (Fig. 9) while the reaction pressure, molar feed ratio and catalyst weight were 10 bar, 1
:
1 and 1.0 g, respectively. The results showed that the CH3OH conversion, space-time yield of DMC and DMC yield increased from 32.0 to 33.9%, 15.5 to 16.4 mmol g−1 h and 31.8 to 32.4%, respectively, when the reaction temperature increased from 100 to 120 °C. This increase in DMC yield and CH3OH conversion means that reactant molecules have higher kinetic energy at higher temperatures, allowing more molecules to pass the activation energy barrier and produce the products. On the contrary, the CH3OH conversion, DMC selectivity, and DMC yield declined dramatically with further increasing operating temperature. This was primarily due to the decrease in CO2 adsorption on the catalyst surface, as well as the increased rates of the side reactions to produce by-products such as dimethyl ether (DME) from DMC decomposition and CH3OH dehydration, dimethoxymethane (DMM) from the reaction of CH3OH with formaldehyde (HCHO), and methyl formate (MF) from the interaction between CH3OH and formic acid (HCOOH) at high reaction temperatures14,53,54 as shown in Scheme 2. Moreover, methyl carbamate (MC) was also formed at such high temperatures from the reaction between ammonia (from reaction (5)) and DMC.14 The optimal temperature for this reaction is therefore reported at 120 °C.
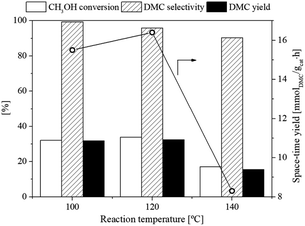 |
| Fig. 9 Effect of reaction temperature on CH3OH conversion, DMC selectivity, and DMC yield of the flower-like CeO2 catalyst using 2-CP as dehydrating agent (10 bar, CH3OH : CO2 = 1 : 1). | |
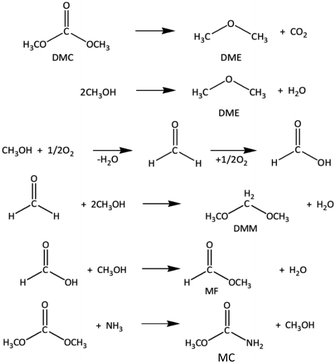 |
| Scheme 2 Reaction of possible by-products formation during the direct synthesis of DMC from CH3OH and CO2 at high temperatures.14,53,54 | |
3.2.2. Effect of feed (CH3OH
:
CO2) ratio. The impact of the initial molar ratio (CH3OH
:
CO2) on the CH3OH conversion, DMC selectivity, and DMC yield with different feed ratios of 1
:
2, 1
:
1, and 2
:
1 was investigated. The operating temperature of 120 °C, catalyst weight of 1.0 g and pressure of 10 bar were used for this experiment. The result shown in Fig. 10 revealed that the feed ratio of 1
:
1 provided the best performance with the CH3OH conversion, DMC selectivity, and DMC yield of 33.9, 95.8, and 32.4%, respectively. The molar ratios of 2
:
1 and 1
:
2 showed relatively lower performances possibly due to the too-high (ratio of 2
:
1) and too-low (ratio of 1
:
2) of CH3OH concentrations reduced the reaction rate because the active sites were covered with CH3OH (ratio of 2
:
1) or CO2 (ratio of 1
:
2) and thus could not be accessed by another reactant in those active sites. Furthermore, the by-product DME was also produced from the CH3OH dehydration reaction at the molar ratio of 2
:
1.
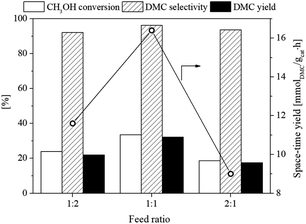 |
| Fig. 10 Effect of feed ratio (CH3OH : CO2) on CH3OH conversion, DMC selectivity, and DMC yield of the flower-like CeO2 catalyst using 2-CP as dehydrating agent (10 bar, 120 °C). | |
3.2.3. Effect of catalyst weight. The influence of catalyst amount on the catalytic performance of the flower-like CeO2 catalyst for the DMC synthesis from CH3OH and CO2 was investigated using catalyst amounts varied at 0.5 and 1.0 g. The other experimental conditions including an operating temperature of 120 °C, a pressure of 10 bar, and a feed ratio (CH3OH
:
CO2) of 1
:
1 were chosen for this study. The results of this investigation are displayed in Fig. 11. The CH3OH conversion, DMC selectivity, and DMC yield increased from 19.3 to 33.9%, 94.6 to 95.8%, and 18.2 to 32.4%, respectively, when the catalyst amount increased from 0.5 to 1.0 g. The observed enhancement can be described as an increase in the concentration of active sites with increasing catalyst dosage. The impact of the catalyst weight of more than 1.0 g was not examined in this work; however, excess catalyst amounts have been reported to be inefficient because of excessive active centers or mass transfer limitations that promoted the side reaction formation, resulting in significantly reduced DMC yield.55,56
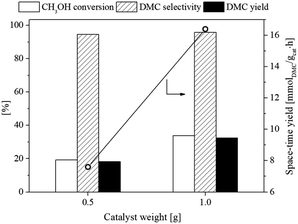 |
| Fig. 11 Effect of catalyst contents on CH3OH conversion, DMC selectivity, and DMC yield of the flower-like CeO2 catalyst using 2-CP as dehydrating agent (10 bar, 120 °C, CH3OH : CO2 = 1 : 1). | |
3.2.4. Effect of reaction pressure. The influence of operating pressure on the catalytic performance of the flower-like CeO2 catalyst for the DMC production from CH3OH and CO2 was investigated. Fig. 12 illustrates the CH3OH conversion, DMC selectivity, DMC yield and space-time yield at different reaction pressures (10, 20 and 30 bar), with the reaction temperature of 120 °C, molar feed ratio of 1
:
1 and the catalyst amount of 1.0 g. The results revealed that increasing operating pressures from 10 to 30 bar improved CH3OH conversion, space-time yield of DMC and DMC yield from 33.9 to 86.6%, 16.4 to 32.0 mmol g−1 h and 32.4 to 86.0%, respectively. This was mainly due to the ability of CH3OH and CO2 molecules to fully adsorb on the active sites of the catalyst resulted in a shift in chemical equilibrium towards DMC production at high operating pressures.
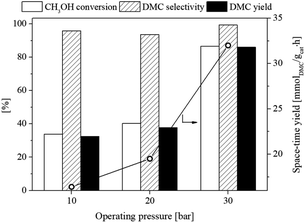 |
| Fig. 12 Effect of operating pressure on CH3OH conversion, DMC selectivity, and DMC yield of the flower-like CeO2 catalyst using 2-CP as dehydrating agent (120 °C, CH3OH : CO2 = 1 : 1). | |
The results exhibited that the reaction temperature of 120 °C, catalyst weight of 1.0 g, CH3OH
:
CO2 ratio of 1
:
1 and operating pressure of 30 bar were the optimum conditions for the DMC synthesis using the flower-like CeO2 catalyst, providing the highest CH3OH conversion, DMC selectivity, and DMC yield of 86.6%, 99.3%, and 86.0%, respectively. Many works from recent years reported CeO2 with different morphologies as one of the best catalysts for DMC synthesis, as shown in Table 1.
Table 1 Comparison of catalytic activity of the present catalyst (flower-like CeO2) with the other reported catalysts in the direct DMC synthesis from CO2 and CH3OH
Catalyst |
Reaction conditions |
DMC yield rate (mmolDMC gcat.−1 h−1) |
Ref. |
Commercial CeO2 |
Fixed-bed reactor, 0.3 g catalyst, 2-CP : CH3OH = 1 : 2, CH3OH : CO2 = 1 : 2.5, 30 bar CO2, 120 °C |
11.1 |
12 |
CeO2 (calcination of Ce(OH)4) |
Autoclave reactor, 0.1 g catalyst, CH3OH : CO2 = 192 : 200 mmol, 130 °C |
1.8 |
58 |
Commercial CeO2 |
Autoclave reactor, 0.34 g catalyst, CH3OH : 2-CP: = 2 : 1, 5 MPa CO2, 120 °C |
23.3 |
16 |
Spherical-CeO2 |
Autoclave reactor, 0.17 g catalyst, 2-CP : CH3OH = 1 : 1, 5 MPa CO2, 110 °C |
31.0 |
59 |
CeO2 (calcination of Ce(NO3)3·6H2O) |
Autoclave reactor, 1.0 g catalyst, 742 mmol CH3OH, 16 MPa CO2, 250 °C |
CeO2: 2.27 |
60 |
Nanorod-CeO2 |
Nanorod: 2.88 |
Flower-CeO2 |
Flower: 3.11 |
Commercial CeO2 |
Autoclave reactor, 0.34 g catalyst, CH3OH: 2-CP = 1 : 5, 5 MPa CO2, 120 °C |
12.1 |
14 |
Spindle-CeO2 |
Autoclave reactor, 0.1 g catalyst, 2-CP : CH3OH = 1 : 2, 5 MPa CO2, 150 °C |
Irregular: 79.0 |
57 |
Cube-CeO2 |
Cube: 78.5 |
Rods-CeO2 |
Rod: 95.5 |
Irregular-CeO2 |
Spindle: 152.5 |
Amorphous-CeO2 |
Autoclave reactor, 0.1 g catalyst, 15 mL CH3OH, 50 mmol 2-CP, 5 MPa CO2, 140 °C |
Amorphous: 116.9 |
15 |
Octahedron-CeO2 |
Rod: 126.2 |
Rod-CeO2 |
Octahedron: 21.8 |
Cube-CeO2 |
Cube: 3.2 |
Octahedrons-CeO2 |
Autoclave reactor, 0.1 g catalyst, 15 mL CH3OH, 5 MPa CO2, 140 °C |
Octahedron: 0.35 × 10−3 |
28 |
Rods-CeO2 |
Rod: 2.6 × 10−3 |
Cubes-CeO2 |
Cube: 1.7 × 10−3 |
Spindle-CeO2 |
Spindle: 4.0 × 10−3 |
Flower-CeO2 |
Packed-bed reactor, 1.0 g catalyst, 2-CP : CH3OH : CO2 = 1 : 2 : 1, 30 bar CO2, 120 °C |
32.0 |
This work |
3.2.5. Recycling study. The reusability of the catalyst is important for their practical application. As presented in Fig. 13, the fresh flower-like CeO2 catalyst for the DMC synthesis from CO2 and methanol with CH3OH
:
CO2 molar ratio of 1
:
1 using 2-CP as dehydrating agent at temperature of 120 °C and pressure 30 bar displays CH3OH conversion, space-time yield of DMC and DMC yield of 86.6%, 32.0 mmol g−1 h and 86.0%, respectively. Then, the used flower-like CeO2 catalyst was calcined at 400 °C to remove impurity products and reactants on the catalyst surface before being put into the next reaction. The results showed that a significant loss of catalytic activity was not observed after two runs, indicating that the catalyst could be easily recovered.
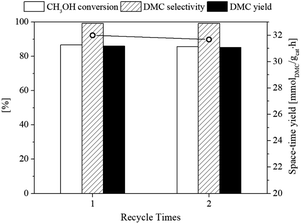 |
| Fig. 13 Recycling of the flower-like CeO2 catalyst for the DMC synthesis using 2-CP as dehydrating agent (30 bar, 120 °C, CH3OH : CO2 = 1 : 1). | |
3.3. The relationship between the catalyst properties (crystal facet and acid–base sites) and the reaction mechanism
It has been reported that the morphology, crystal facet, and acid–base sites of the catalyst were a crucial factor in achieving the highest catalytic activity for DMC synthesis. S. Wang et al.28 and P. Unnikrishnan et al.57 investigated the direct synthesis of DMC from methanol and CO2 using various CeO2 morphology catalysts. They observed that high DMC yields and methanol conversion were induced by the synergism between the exposed (111) plane, defect sites and acid–basic sites, which was controlled by CeO2 shape. As mentioned in the morphology analysis section, the flower-like morphology of the synthesized CeO2 catalyst indicated the (111).
Crystal facet, which was the most active plane for the DMC production from CO2 and CH3OH. J. Jiang et al.61 performed a comprehensive study on the catalytic mechanisms of the DMC synthesis from CO2 and methanol on CeO2 (111) and (110) surfaces. They found that the reaction pathways computed on the (111) and (110) surfaces exhibited high catalytic activity toward DMC synthesis. However, different rate-limiting steps were observed. The rate-determining step of the (111) surface was the regeneration of oxygen vacancy via the dehydration process, whereas that of the (110) surface was the esterification of monomethyl carbonate (reaction (10)). The rate-limiting step on the (111) facet can be accelerated more easily than the (110) plane by using a dehydrating agent to remove water from the active site (oxygen vacancy) of the catalyst. These results suggested that the (111) facet was more reactive for DMC synthesis than the (110) facet in the presence of a desiccant. S. Wang et al.28 reported that spindle-like CeO2 produced the highest DMC yields, followed by nanorods and nanocubes morphologies, because the spindle-like with (111) facet contained a large specific surface area, amounts of acid–basic sites and number of defect sites than nanocubes (100) and nanorods [(111) and (100)], indicating that the crystal facet of (111) plane was the active factor for the DMC formation.
It is well-known that the acidity, basicity, and redox characteristics of CeO2 catalyst promote the CH3OH activation and the CO2 adsorption on its surface. The CO2-TPD and NH3-TPD results in Fig. 6 and 7 revealed that the synthesized flower-like CeO2 displayed both basicity and acidity properties with amounts of 300 μmol g−1 and 80 μmol g−1, respectively. It has been reported that both basic and acid sites activated CH3OH molecules, however only basic sites activated CO2 molecules, which are critical steps in the direct synthesis of DMC from CH3OH and CO2. The reaction mechanism of the DMC synthesis from CH3OH and CO2 is shown in the reaction (6)–(11).62
|
CH3OH → CH3O(ads)− + H(ads)+ (over basic site)
| (6) |
|
CO2 → CO2(ads) (over basic site)
| (7) |
|
CH3O(ads)− + CO2(ads) → CH3OCO2(ads)− (over basic site)
| (8) |
|
CH3OH → CH3(ads)+ + OH(ads)− (over acid site)
| (9) |
|
CH3OCO2(ads)− + CH3(ads)+ → (CH3O)2CO
| (10) |
|
H(ads)+ + OH(ads)− → H2O
| (11) |
In the presence of the CeO2 catalyst, CO2 and CH3OH molecules are firstly adsorbed on its surface. CO2 is adsorbed on the surface at the basic site without dissociation (CO2(ads)) while CH3OH is adsorbed and activated to form methoxide ions (CH3O(ads)−) and hydrogen ions (H(ads)+) at the basic site and to form methyl ions (CH3(ads)+) and hydroxide ions (OH(ads)−) at the acid site on the CeO2 surface. The methoxide species interacts with adsorbed CO2 to produce methoxycarbonyl ions (CH3OCO2(ads)−). Finally, the methoxycarbonyl ions react with methyl ions to generate dimethyl carbonate ((CH3O)2CO, DMC), while hydrogen ions react with hydroxide ions to form water (H2O). Dimethyl carbonate and water products are desorbed from the catalyst surface, regenerating the active site. The produced H2O can be eliminated from the reaction mixture by adding a dehydrating agent (2-cyanopyridine, 2-CP) led to an increase in the DMC yield. According to the reaction mechanism, the acidity and basicity properties of the catalyst, as well as the appearance of the (111) crystal facet in the presence of a dehydrating agent, had a significant impact on the catalytic efficiency of the DMC synthesis from CO2 and CH3OH.
4. Conclusions
In this study, the flower-like CeO2 catalyst was successfully synthesized using graft copolymerization reaction between acrylamide and glucose under hydrothermal conditions. XRD and SEM results confirmed the complete formation of the flower-like CeO2 catalyst with the crystal facet of (111) plane. When compared with the spent flower-like CeO2 after DCM synthesis reaction, there were no changes in the structure, morphology and particle size which indicated that the flower-like CeO2 catalyst was resistant to the reaction test at reaction temperature of 120 °C and reaction pressure of 10 bar. Furthermore, the N2 adsorption–desorption technique revealed a mesoporous structure in the flower-like CeO2 catalyst, which was consistent with the SEM data, with a specific BET surface area of 26.06 m2 g−1. The CO2-TPD and NH3-TPD results revealed that the synthesized flower-like CeO2 displayed both basicity and acidity properties with amounts of 300 μmol g−1 and 80 μmol g−1, respectively. The catalytic activity of the flower-like CeO2 catalyst in producing DMC from CH3OH and CO2 was investigated using continuous packed-bed reactor. 2-Cyanopyridine (2-CP) was utilized as a dehydrator to remove water from the reaction system and push the reaction equilibrium toward the DMC synthesis side. The effect of reaction parameters such as temperature, feed ratio, catalyst amount and pressure on DMC production over the flower-like CeO2 catalyst was investigated. The results exhibited that the reaction temperature of 120 °C, catalyst weight of 1.0 g, CH3OH
:
CO2 ratio of 1
:
1 and operating pressure of 30 bar were the optimum conditions for the DMC synthesis, providing the highest CH3OH conversion, DMC selectivity, and DMC yield of 86.6%, 99.3%, and 86.0%, respectively. The outstanding catalytic activity of the synthesized flower-like CeO2 catalyst for the DMC synthesis was attributed to the synergistic effect of the exposed (111) crystal plane, basicity, and acidity properties on its surface. Therefore, the catalyst could be designed to possess a suitable shape, with a mainly exposed active (111) plane, a high surface area, and a large amount of defect, basic, and acid sites, to improve catalytic performance for DMC synthesis from CO2 and CH3OH.
Data availability
The data that support the findings of this study are available on request.
Conflicts of interest
The authors confirm that there is no conflict of interest.
Acknowledgements
This research has received funding support from the NRCT (contract number N41A640149), King Mongkut's University of Technology North Bangkok (contract number KMUTNB-FF-66-52), and NSRF via the Program Management Unit for Human Resources & Institutional Development, Research and Innovation (contact number B48G660108).
References
- D. Wang, X. Zhang, Y. Gao, F. Xiao, W. Wei and Y. Sun, Fuel Process. Technol., 2010, 91, 1081–1086 CrossRef CAS
. - T. Zhao, X. Hu, D. Wu, R. Li, G. Yang and Y. Wu, ChemSusChem, 2017, 10, 2046–2052 CrossRef CAS PubMed
. - D. Delledonne, F. Rivetti and U. Romano, Appl. Catal., A, 2001, 221, 241–251 CrossRef CAS
. - X. Ding, X. Dong, D. Kuang, S. Wang, X. Zhao and Y. Wang, Chem. Eng. J., 2014, 240, 221–227 CrossRef CAS
. - T. Sakakura, Y. Saito, M. Okano, J. C. Choi and T. J. Sako, Org. Chem., 1998, 63, 7095–7096 CrossRef CAS PubMed
. - J. C. Choi, K. Kohno, Y. Ohshima, H. Yasuda and T. Sakakura, Catal. Commun., 2008, 9, 1630–1633 CrossRef CAS
. - J. C. Choi, L. N. He, H. Yasuda and T. Sakakura, Green Chem., 2002, 4, 230–234 RSC
. - C. F. Li and S. H. Zhong, Catal. Today, 2003, 82, 83–90 CrossRef CAS
. - S. Fang and K. Fujimoto, Appl. Catal., A, 1996, 142, 8–10 CrossRef
. - V. Eta, P. Mäki-Arvela, J. Wärn, T. Salmi, J. P. Mikkola and D. Y. Murzin, Appl. Catal., A, 2011, 404, 39–46 CAS
. - M. Honda, A. Suzuki, B. Noorjahan, K. I. Fujimoto, K. Suzuki and K. Tomishige, Chem. Commun., 2009, 4596–4598 RSC
. - A. Bansode and A. Urakawa, ACS Catal., 2014, 4, 3877–3880 CrossRef CAS
. - M. Tamura, H. Wakasugi, K. I. Shimizu and A. Satsuma, Chem.–Eur. J., 2011, 17, 11428–11431 CrossRef CAS
. - M. Honda, M. Tamura, Y. Nakagawa, K. Nakao, K. Suzuki and K. Tomishige, J. Catal., 2014, 318, 95–107 CrossRef CAS
. - S. P. Wang, J. J. Zhou, S. Y. Zhao, Y. J. Zhao and X. B. Ma, Chin. Chem. Lett., 2015, 26, 1096–1100 CrossRef CAS
. - M. Honda, M. Tamura, Y. Nakagawa, S. Sonehara, K. Suzuki, K. I. Fujimoto and K. Tomishige, ChemSusChem, 2013, 6, 1341–1344 CrossRef CAS PubMed
. - H. J. Lee, W. Joe and I. K. Song, Korean J. Chem. Eng., 2012, 29, 317–322 CrossRef CAS
. - D. Wang, F. Shi and L. Wang, Catalysts, 2024, 14, 1–18 CAS
. - A. Li, Y. Pu, F. Li, J. Luo, N. Zhao and F. J. Xiao, J. CO2 Util., 2017, 19, 33–39 CrossRef CAS
. - A. Kojcinovic, B. Likozar and M. Grilc, J. CO2 Util., 2022, 66, 102250 CrossRef CAS
. - N. A. M. Razali, K. T. Lee, S. Bhatia and A. R. Mohamed, Renewable Sustainable Energy Rev., 2012, 16, 4951–4964 CrossRef CAS
. - K. Tomishige and K. Kunimori, Appl. Catal., A, 2002, 237, 103–109 CrossRef CAS
. - K. Tomishige, Y. Furusawa, Y. Ikeda, M. Asadullah and K. Fujimoto, Catal. Lett., 2001, 76, 71–74 CrossRef CAS
. - Z. Fu, Y. Zhong, Y. Yu, L. Long, M. Xiao, D. Han, S. Wang and Y. Meng, ACS Omega, 2018, 3, 198–207 CrossRef CAS PubMed
. - K. H. Kang, C. H. Lee, D. B. Kim, B. Jang and I. K. Song, J. Nanosci. Nanotechnol., 2014, 14, 8693–8698 CrossRef CAS
. - J. Ederer, P. Janoš, M. Šťastný, J. Henych, K. Ederer, M. Š. Slušná and J. Tolasz, J. Environ. Chem. Eng., 2021, 9, 106229 CrossRef CAS
. - X. Ren, Z. Zhang, Y. Wang, J. Lu, J. An, J. Zhang, M. Wang, X. Wang and Y. Luo, RSC Adv., 2019, 9, 15229–15237 RSC
. - S. Wang, L. Zhao, W. Wang, Y. Zhao, G. Zhang, X. Ma and J. Gong, Nanoscale, 2013, 5, 5582–5588 RSC
. - Y. Cao, H. Cheng, L. Ma, F. Liu and Z. Liu, Catal. Surv. Asia, 2012, 16, 138–147 CrossRef CAS
. - P. Kumar, P. With, V. C. Srivastava, R. Gläser and I. M. Mishra, J. Environ. Chem. Eng., 2015, 3, 2943–2947 CrossRef CAS
. - D. Stoian, F. Medina and A. Urakawa, ACS Catal., 2018, 8, 3181–3193 CrossRef CAS
. - F. Meng, F. Lu, L. Wang, J. Cui and J. Lü, Sci. Adv. Mater., 2012, 4, 1018–1023 CrossRef CAS
. - G. Chen, C. Xu, X. Song, W. Zhao, Y. Ding and S. Sun, Inorg. Chem., 2008, 47, 723–728 CrossRef CAS
. - L. He, Y. Yu, C. Zhang and H. He, J. Environ. Sci., 2011, 23, 160–165 CrossRef CAS PubMed
. - H. Imagawa and S. Sun, J. Phys. Chem. C, 2012, 116, 2761–2765 CrossRef CAS
. - Z. Yang, D. Han, D. Ma, H. Liang, L. Liu and Y. Yang, Cryst. Growth Des., 2010, 10, 291–295 CrossRef CAS
. - B. J. Zong, Mater. Sci.: Mater. Electron., 2017, 28, 2458–2461 CAS
. - J. Wei, Z. Yang and Y. Yang, CrystEngComm, 2011, 13, 2418–2424 RSC
. - R. Yu, L. Yan, P. Zheng, J. Chen and X. Xing, J. Phys. Chem. C, 2008, 112, 19896–19900 CrossRef CAS
. - Z. Zhan, X. Liu, H. He, L. Song, J. Li and D. Ma, J. Rare Earths, 2013, 31, 750–758 CrossRef CAS
. - D. Zhang, X. Du, L. Shi and R. Gao, Dalton Trans., 2012, 41, 14455–14475 RSC
. - M. Ziemba, C. Schilling, M. V. Ganduglia-Pirovano and C. Hess, Acc. Chem. Res., 2021, 54, 2884–2893 CrossRef CAS
. - A. Filtschew, K. Hofmann and C. Hess, J. Phys. Chem. C, 2016, 120, 6694–6703 CrossRef CAS
. - H. X. Mai, L. D. Sun, Y. W. Zhang, R. Si, W. Feng, H. P. Zhang, H. C. Liu and C. H. Yan, J. Phys. Chem. B, 2005, 109, 24380–24385 CrossRef CAS PubMed
. - X. Niu and F. Tu, J. Mater. Sci.: Mater. Electron., 2017, 28, 2141–2146 CrossRef CAS
. - S. Y. Yao, W. Q. Xu, A. C. Johnston-Peck, F. Z. Zhao, Z. Y. Liu, S. Luo, S. D. Senanayake, A. Martínez-Arias, W. J. Liu and J. A. P. Rodriguez, Chem. Chem. Phys., 2014, 16, 17183–17195 RSC
. - Y. Ma, J. Liu, M. Chu, J. Yue, Y. Cui and G. Xu, Catal. Lett., 2022, 152, 872–882 CrossRef CAS
. - Q. Wang, S. Liu, S. An, X. Song, X. Liang, Z. Wang and Y. Mu, J. Mater. Sci.: Mater. Electron., 2021, 32, 26425–26438 CrossRef CAS
. - B. Xue, J. Zhang, X. Tang, C. Yang, Q. Chen, X. Man and W. Dang, Petrochem. Res., 2016, 1, 191–204 Search PubMed
. - C. Sun, J. Sun, G. Xiao, H. Zhang, X. Qiu, H. Li and L. Chen, J. Phys. Chem. B, 2006, 110, 13445–13452 CrossRef CAS
. - H. Li, G. Lu, Q. Dai, Y. Wang, Y. Guo and Y. Guo, ACS Appl. Mater. Interfaces, 2010, 2, 838–846 CrossRef CAS PubMed
. - Y. Yang, Z. Hu, K. Liu, R. Mi, D. Li, X. Yong and H. Yang, RSC Adv., 2019, 9, 4682–4692 RSC
. - M. Álvarez, P. Marín and S. Ordóñez, Fuel Process. Technol., 2023, 247, 107805 CrossRef
. - M. Yuan, M. Dong, Z. Tian, Y. Che, Y. Tian, Y. Qiao, J. Zhang and D. Li, J. Energy Inst., 2022, 103, 47–53 CrossRef CAS
. - A. H. Tamboli, N. Suzuki, C. Terashima, S. Gosavi, H. Kim and A. Fujishima, Catalysts, 2021, 11, 1–16 CrossRef
. - F. Wang, T. Wan, B. Da, X. Liang, N. Liu, Q. Ma, J. Xu and B. Xue, Res. Chem. Intermed., 2024, 50, 651–667 CrossRef CAS
. - P. Unnikrishnan and S. Darbha, J. Chem. Sci., 2016, 128, 957–965 CrossRef
. - Y. Yoshida, Y. Arai, S. Kado, K. Kunimori and K. Tomishige, Catal. Today, 2006, 115, 95–101 CrossRef CAS
. - W. Donphai, O. Phichairatanaphong, R. Fujii, P. Li, T. Chang, M. Yabushita, Y. Nakagawa and K. Tomishige, Mater. Today Sustainable, 2023, 24, 100549 CrossRef
. - W. Guo, L. Zheng, X. Gao, W. Yang, Y. Li, W. Sun, S. Gao, Y. Wang, X. Ding, L. Wu and T. Fang, Appl. Catal., A, 2023, 662, 1–12 Search PubMed
. - J. Jiang, C. M. Marin, A. K. Both, C. L. Cheung, L. Li and X. C. Zeng, Phys. Chem. Chem. Phys., 2021, 23, 16150–16156 RSC
. - K. Almusaiteer, Catal. Commun., 2009, 10, 1127–1131 CrossRef CAS
.
|
This journal is © The Royal Society of Chemistry 2024 |
Click here to see how this site uses Cookies. View our privacy policy here.