DOI:
10.1039/D4RA08446B
(Review Article)
RSC Adv., 2024,
14, 40141-40159
Overview of recent developments in carbon-based nanocomposites for supercapacitor applications
Received
29th November 2024
, Accepted 5th December 2024
First published on 23rd December 2024
Abstract
Energy storage devices are recognized as environmentally friendly technologies. Supercapacitors, known for their high cycle stability, have been proposed as potential alternatives to fossil fuels. Recent studies have focused on selecting suitable electrode materials to achieve energy storage systems with high stability, high specific capacity, and biocompatibility. In particular, carbon-based electrode materials, such as graphene oxide, activated carbon, carbon nanotubes, and carbon-based quantum dots, have attracted considerable attention due to their intrinsic properties, such as high conductivity and stability. However, carbon materials alone exhibit limitations, such as low energy density and low specific capacitance. To address this limitation, the synergistic effect of carbon materials has been combined with other electroactive materials to develop electrode materials with enhanced supercapacitor properties. The present study also investigates the supercapacitor performance of carbon-based nanocomposites. It examines the effect of each carbon material (AC, CNT, GO, rGO) on improving the performance of other electroactive materials, including metal oxides, metal sulfides, MXenes, MOFs, and conductive polymers. This study provides valuable insights for further studies on carbon-based electrode materials for supercapacitor applications.
1. Introduction
With the growth of industry, the demand for fossil fuels has increased. However, the limited supply of these resources, along with the resulting environmental pollution from their combustion, has prompted the need for alternative energy generation and efficient energy storage solutions.1–3 Therefore, suitable alternative technologies to fossil fuels are necessary.4 As efficient energy storage devices, batteries,5 fuel cells,6 and supercapacitors have great potential and have been introduced as alternatives to fossil fuels.1,7,8 In other words, fuel cells, batteries, and supercapacitors, as electrochemical energy storage technologies, have received much attention as alternatives to fossil fuels in the last few decades.9–11 Fuel cells are open systems, where the cathodes are responsible for carrying out charge transfer within the system.12–14 In contrast, batteries and supercapacitors are closed systems, where the mass of the active material in the electrodes participates in redox reactions.15–17 Supercapacitors, however, do not necessarily involve redox reactions; energy storage is often achieved through the electrical double layer.18 Supercapacitor devices, as energy storage solutions, offer several key advantages, such as higher energy density than capacitors and higher power density than batteries.19,20 The typically long lifespan of supercapacitors has led to their extensive use in industry.21 In contrast, batteries may exhibit weaker performance due to reduced power density caused by Faraday reactions.22 Therefore, the use of batteries in industrial applications has limitations, although in some cases, batteries are still used in systems that require high energy density.23 The limitations of using batteries and supercapacitors can be addressed through two general solutions.24 The first approach involves the fabrication of a hybrid system, combining an electrode with pseudocapacitive properties (e.g., metal oxides, metal sulfides, conductive polymers) and an electrode with double electric layer properties (e.g., carbon materials, including graphene, activated carbon).25 The second approach utilizes a two-terminal device, incorporating both a battery electrode and a capacitor electrode.26 Connecting a supercapacitor device to a battery can improve the battery performance, including increasing its life and decreasing voltage instability.27,28 The performance of the supercapacitor device depends on the type of electrode material used, so a smart choice of the electrode material is important for achieving an efficient supercapacitor device.29 Commonly used electrode materials in supercapacitors include metal oxides,30 metal sulfides,31 conductive polymers,32 quantum dots,33 and metal–organic frameworks (MOFs).34 However, these materials used for constructing supercapacitors have limitations too. Consequently, nanocomposites based on carbon compounds have been synthesized to improve the final performance and attain electrode materials with a high specific surface area, better conductivity, and high specific capacitance.35 Carbon materials that have been investigated as electric double-layer capacitors (EDLCs) in supercapacitor systems include activated carbon, carbon nanotubes, and graphene oxide.36 These materials alone have low energy density and low specific capacitance,37 but compositing these materials with e.g., metal oxides,38,39 metal sulfides,40 MOFs,41 and conductive polymers increases their specific surface area and performance.42 Therefore, the compositing of carbon materials with other materials with pseudocapacitive properties can allow obtaining electrode materials with optimal performance.42 Increasing the specific surface area increases the rate of penetration of electrolyte ions, resulting in a shortening of the ion-diffusion pathways.43,44 In this study, our team reviewed recent research on the supercapacitor performance of carbon-based nanocomposites. Specifically, by investigating recent studies on the supercapacitor performance of various carbon-based nanocomposites (carbon/TMO materials, carbon/TMS materials, carbon/conductive polymer materials, carbon/MOF materials, and carbon/MXene materials), the effect of the carbon materials on improving the performance of each quasi-capacitor material was determined.
2. Supercapacitor devices
Supercapacitor systems can be divided into three categories based on the charge-storage mechanism:45 electrochemical double layer (the charge accumulates in the interface between the electrodes),46,47 pseudocapacitors (storage is done through a reversible surface redox process),48 and hybrid capacitors (combination of double electric layer and pseudocapacitor).49
2.1. EDLCs
EDLCs were discovered at the beginning of the 15th century during the study of opposite charges located at the interface of colloidal particles.50 The performance of EDLCs is similar to that of common capacitors, but EDLCs have a higher energy density than capacitors.51 Conventional capacitors are made of a dielectric medium, but in EDLCs, an electrolyte is located between the two electrode layers.52 The energy-storage mechanism of EDLCs is physical. Then, during discharge, electrons move from the negative terminal to the positive terminal, which separates the cations and anions from the surface of the electrons, and so charge transfer does not occur at the electrode/electrolyte interface.53 Three general models were proposed to define the structure of EDLCs (Fig. 1). The first model was proposed by Helmholtz in the 19th century, in which opposite charges accumulate at the interface of the electrode and the electrolyte, and the two plates are separated by a distance similar to in a capacitor. A second model was introduced by Gouy and Chapman, in which a diffusion layer is considered and the specific capacitance increases as the charges approach each other. A third model was proposed by Stern combining the two earlier models (Helmholtz's model and Gouy and Chapman's model), which considers a compressed layer (the Stern layer).55 The commonly used electrode materials for EDLC supercapacitors are carbon materials with a high specific surface area and promising electrical conductivity, including activated carbon, graphene, and carbon nanotubes.53
 |
| Fig. 1 Models for the electrical double layer at a positively charged surface: (a) the Helmholtz model, (b) the Gouy–Chapman model, and (c) the Stern model.54 | |
2.2. Pseudocapacitors
The charge-storage mechanism of pseudocapacitors is faradaic, whereby electron transfer is carried out through the oxidation and reduction of a chemical substance.56 This process can be reversible or irreversible. In the reversible process, the redox reaction is imposed on the electrode surface by applying voltage, which causes the electrolyte ions to diffuse from the solution to the electrode material. Then, the ions of the electrode material return to the electrolyte at the time of discharge. The performance and the specific capacitance of pseudocapacitors depend on the electrode morphology. For example, molybdenum oxide can be synthesized as alpha and beta phases under different conditions, including different temperatures and reaction times. The alpha phase has a sheet or rod morphology while the beta phase has a spherical morphology. The sheet morphology has a larger specific surface area, which allows for a higher specific capacitance.57,58 Pseudocapacitors have a higher specific capacitance than EDLCs, but the stability of pseudocapacitors is lower than EDLCs due to their reliance on faradaic reactions and their shorter cycle life. The general process of pseudocapacitors is voltage-dependent due to the charge-transfer mechanism depending on the voltage.59 Metal oxides, conductive polymers, and metal sulfides are some common electrode materials with pseudocapacitor properties. However, while they have high capacitance, they are generally less stable in charge–discharge cycles.
2.3. Hybrid capacitors
Hybrid devices are intermediates or combinations of EDLCs and pseudocapacitors.60 Hybrid devices are classified into three general categories. The first category is composites, which are fabricated from a combination of carbon materials (graphene, carbon nanotubes, and activated carbon) and pseudocapacitor materials (metal oxides, metal sulfides, and conductive polymers). Composite electrode materials can be used as symmetric or asymmetric systems. In asymmetric systems, composite and carbon materials are used as the positive and the negative electrodes, respectively. The second category is asymmetric devices, which utilize pseudocapacitor materials (metal oxides, conductive polymers) as positive electrodes and carbon materials (graphene, CNT, and active carbon) as negative electrodes. The third category is asymmetric supercapacitors of the battery type. In this type of asymmetric supercapacitor, the positive electrode is a battery material and the negative electrode is a capacitor material.61 The operation of a battery-type supercapacitor in non-ionic electrolytes occurs via several stages. In the first stage, during charging, the negative ions of the electrolyte move toward the positive electrode, and the positive ions of the electrolyte move toward the negative electrode (the volume of ions thus decrease in the electrolyte solution). In the second stage, the ions return to the electrolyte upon discharge, and the volume of ions in the electrolyte solution thus increases. In the third stage, the concentration of negative ions in the electrolyte is constant and the positive ions move toward the positive electrode. Therefore, a constant concentration of positive and negative ions remain in the electrolyte.53
2.4. Supercapacitor techniques
To evaluate the quality of supercapacitors, it is necessary to check certain parameters, such as the specific capacitance, current density, power density, and stability. Therefore, reliable techniques are needed to evaluate these parameters. Using the following three techniques, the electrochemical properties of the supercapacitor can be checked.62
2.4.1 Cyclic voltammetry. Cyclic voltammetry (CV) analysis can be used to check the electrochemical behavior of an electrode material. When the applied voltage is higher than the predicted voltage, the current can be checked using CV analysis (Nernst equation).63 In CV analysis, the electrochemical behavior during the forward and the reverse scan is investigated, which can be distinguished from the pseudocapacitor behavior according to the observed peaks and the general shape of the EDLC behavior diagram for the electrode material.64 This technique examines the material's electrochemical behavior by using working, reference, and counter electrodes in a three-electrode setup in supercapacitor systems.65 The main limitation of cyclic voltammetry is that the thermodynamic aspect is ignored and only the kinetic aspect of the material is considered. The specific capacitance can be calculated using the cyclic voltammetry technique with eqn (1).66 |
 | (1) |
where i, V, m, and ν are the current density, potential region, mass of active materials, and scan rate, respectively.67
2.4.2 Galvanostatic charge/discharge. Galvanostatic charge and discharge analysis examines changes in the potential over time. In this analysis, the electrode material is charged and discharged at a certain time according to the properties of the material type (specific surface, electrical activity, etc.).68 The specific capacity, power density, stability, and energy balance are calculated from the data related to the potential window and the charge and discharge time.69 The general shape of the charge–discharge diagram shows the difference between EDLC and pseudocapacitor behaviors according to the shoulders created by the faradaic currents. Eqn (2)–(4) can be used in galvanostatic charge and discharge analysis to calculate the specific capacity, current density, and power density.70 |
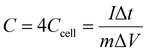 | (2) |
|
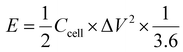 | (3) |
|
 | (4) |
where Ccell (F g−1), m, Δt, E, ΔV, and I are the specific capacitance, total mass of active material, discharge time, energy density, discharge current density, and potential window, respectively.71
2.4.3 Electrochemical impedance spectroscopy (EIS). Impedance analysis can be performed to evaluate the required parameters of supercapacitor devices. The data from impedance analysis are usually processed by suitable software, such as ZView, so an equivalent circuit can be defined for this analysis.72 The elements of this equivalent circuit show the general characteristics of the supercapacitor, such as the equivalent series resistance, the supercapacitor's non-ideal behavior, and the charge-transfer capacitance. Using the results of the impedance analysis, the specific capacitance can be calculated using eqn (5).73 |
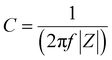 | (5) |
where |Z| and f are the imaginary part of the impedance, and the frequency.
3. Carbon materials
The use of carbon materials with a high specific surface area as a conductive component in carbon-based nanocomposites can improve the performance of other materials (metal oxides, MOFs, metal sulfides, and conductive polymers). In the following, we review different types of carbon materials.74,75
3.1. Carbon onions
Carbon onions are carbon skins with a spherical morphology that were first introduced as carbon nano-onions (CNOs) and later called onion-like carbon (OLC). OLC was discovered by chance in a transmission electron microscopy (TEM) image in 1980 in Sumio Iijima's study investigating carbon black.76 It was later found that OLC with the sp2 network structure allows passing loads faster.77 These materials (OLCs) were later used as EDLC electrode materials in the construction of supercapacitors, and it was found that, compared to other EDLC materials, the energy-storage performance did not have a temperature limit and hence they could be used in a wider temperature range.78 Various synthesis methods have been used to prepare OLCs, including the annealing method and arc-discharge method, which have made large-scale production possible.76 In general, the low cost of OLC synthesis has led to the wide use of these materials in industry.79 The energy density of these materials is up to 10 W h kg−1, which requires activation. Indeed, with activation, the specific capacitance of OLCs increases. However, the activation of OLCs leads to a decrease in the quality of these materials. The use of OLCs as anodes and other pseudocapacitor materials as cathodes in asymmetric supercapacitors can lead to efficient energy-storage systems with a high power density and high energy density.80
3.2. Activated carbon
Activated carbon is a suitable and promising material for use in energy-storage systems. Activated carbon is prepared by chemical (at low temperature in the presence of chemicals such as potassium hydroxide) and physical methods (at high temperature in the presence of carbon dioxide in air).81,82 Studies have been done to improve the electrochemical performance and increase the specific surface of these materials.83,84 Activated carbon can be obtained from various sources, such as sugarcane waste,85,86 coconut cellulose,87 and figs, among which the activated carbon obtained from fig wastes has demonstrated good electrochemical performance (high specific surface area).88 Activated carbon electrode materials offer ideal performance in aqueous electrolytes and organic electrolytes because these organic materials create pores with inappropriate sizes (small) that do not participate in the electrochemical mechanism.89,90
3.3. Carbon nanotubes (CNTs)
Carbon nanotubes (CNTs), discovered in 1991, offer good performance in supercapacitor energy-storage systems due to their high specific surface area, high electrical conductivity, and chemical stability.91–93 The carbon nanotube is a graphene sheet in the form of a small tube (nano size).94,95 Carbon nanotubes can be single-walled (SWNTs),96 multi-walled (MWNTs),97 and double-walled (DWNTs).98 The structure of carbon nanotubes is a height of a few microns and a nano diameter, whose ends are covered with a fullerene structure.99 There are different methods for the synthesis of the different types of carbon nanotubes.100–102 For the synthesis of SWNTs and MWNTs, the methods include carbon monoxide thermal decomposition with a laser pulse,103 and carbon arc discharge.104,105 Also, plasma-enhanced chemical vapor deposition and chemical vapor deposition have been used for the synthesis of parallel single-walled nanotubes and parallel multi-walled nanotubes, respectively.106,107 Among the various types of carbon nanotubes, interwoven carbon nanotubes were the first class of nanotubes studied in supercapacitor systems.108 In addition to intertwined nanotubes, aligned nanotubes have also been used in supercapacitor devices.109,110 This feature of the alignment of carbon nanotubes makes it easy to access the structure of the nanotubes and improve their performance in energy-storage devices.111 Although carbon nanotubes have a lower specific surface area than activated carbon, they have a higher specific capacitance; hence many studies have been conducted on the supercapacitor performance of carbon nanotubes.112 Also, the high specific capacitance of carbon nanotubes compared to activated carbon can be attributed to their high porosity, high conductivity, and upper rate capability.113 Carbon nanotubes have a high specific capacitance at high frequencies because the transmission capability in carbon nanotubes is high. The power density of CNT electrode materials is higher than that of carbon electrode materials, but the energy density is low, which can be modified through compositing them with other electroactive materials.114
3.4. Graphene
Graphene is well known as a monolayer sheet of carbon atoms. In the structure of graphene, each carbon atom has a covalent bond with three adjacent carbons.115,116 Graphene has special electrical and thermal properties, which are provided by its one free electron.116 Recently, there has been considerable focus on graphene as a two-dimensional structure with a thick single-atomized layer as an electrode material in supercapacitor systems.117,118 Graphene electrode materials have a large specific surface, so they have high electrical conductivity and chemical stability. Therefore this material has been widely investigated and used as a distinctive carbon material in energy-storage and production devices.4,119 Also, one of the important reasons for using graphene as an electrode material unlike other carbon materials, such as carbon nanotubes, activated carbon, is that it has no distribution of pores in the solid state.120
3.5. Graphene oxide (GO)
Graphene oxide is a mixture of carbon, oxygen, and hydrogen in variable proportions, which is obtained by combining graphite with strong oxidizers.75,121 The product mass that is maximally oxidized is a solid with the formula C
:
O.122 The presence of oxygen groups in the structure of graphene oxide endows it with a better ability to interact with various materials. This material can be used in various applications, including supercapacitors.123 Hydroxyl and epoxide groups can be attached to graphene oxide to enable graphene oxide to connect these sheets with covalent bonds to many materials and polymers.124 Graphene oxide with a layered structure is one of the most important derivatives of graphene. The layered structure of graphene oxide with a high surface area endows it with suitable supercapacitor properties.125,126
4. Nanocomposites based on carbon materials
Selecting suitable electroactive materials for constructing supercapacitors is important for the final behavior of this system as an efficient energy-storage system. Different carbon materials are the first candidate electrode materials for making supercapacitors, which offer high stability but low specific capacitance. These are combined with metal oxides, metal sulfides, polymers, conductive polymers, and MOFs with suitable supercapacitor behavior as candidate electrode materials for the fabrication of supercapacitors.127 Because the charge-storage mechanism of metal oxides is related to the redox reaction at the electrode/electrolyte interface, they have a high specific capacitance. However, the stability of metal oxides is lower than that of carbon. A suitable method for preparing efficient materials is the synthesis of nanocomposites based on carbon materials and other electroactive materials (metal oxides, metal sulfides, conductive polymers, and MOFs).
4.1. Nanocomposites of carbon materials/metal oxides
Various methods have been used for the synthesis of nanocomposites based on carbon nanotubes and metal oxides, including atomic layer deposition, which typically require a lot of time and cost. Recently, other new methods, including hydrothermal methods, have been used for the synthesis of these nanocomposites. In one study, CNT/Fe2O3 nanocomposites with different weight ratios of CNT were synthesized by hydrothermal method. In this study, the supercapacitor behaviors of Fe2O3 electrode materials, 5 wt% CNT/Fe2O3 nanocomposite electrode materials, and 10 wt% CNT/Fe2O3 nanocomposite electrode materials were investigated. The electrochemical analysis of Fe2O3 and the nanocomposites revealed that the presence of CNT prevented the aggregation of Fe2O3 and increased the conductivity of the nanocomposites. Further investigation of the electrochemical behavior of CNT/Fe2O3 nanocomposites with different weight ratios of CNT (5% and 10%) showed that with the increase in the percentage of CNT from 5% to 10%, the dispersion of Fe2O3 increased, which caused a rise in the penetration rate of electrolyte ions. Finally, the power density, specific capacitance, and stability of the nanocomposite with 10 wt% of CNT were higher than the nanocomposite with 5 wt%.128 In another study, a composite based on graphite and carbon nanotubes (CNT/GT composite) was synthesized by a facile method. Then, at three drying temperatures, zinc oxide (ZnO) was sprayed on to the nanocomposite. The supercapacitor behavior of the nanocomposites was investigated in 1 M KOH electrolyte solutions. The results confirmed the optimal supercapacitor behavior for the nanocomposite prepared at 300 °C. This study confirmed that a careful selection of the temperature conditions could effectively allow obtaining nanocomposites based on carbon materials and metal oxides with ideal supercapacitor behavior. Finally, the CNT/GT/ZnO-300 nanocomposite showed a specific capacitance of 6.99 F g−1 at a scan rate of 25 mV s−1.129 To investigate the effect of the type of electrolyte on the final behavior of nanocomposites based on carbon materials and metal oxides, Thakur et al. synthesized composites based on reduced graphene oxide and titanium oxide (rGO–TiO2 composite) and investigated their electrochemical behavior in different electrolytes. The results showed the improvement of the supercapacitor performance of the composite compared to that of the constituent components. Also, the effect of the type of electrolyte on improving the performance of these nanocomposites was investigated. The results showed specific capacitances of 4.89 F g−1 in H2SO4 electrolyte, 4.89 F g−1 in Na2SO4 electrolyte, and 1.42 F g−1 in KOH electrolyte at the same molarities (1 M) at the same scan rate of 0.05 V s−1.130 The proportion of carbon materials will influence the final performance of the supercapacitor. Sudarto et al. synthesized nanocomposites based on titanium dioxide, activated carbon, and carbon nanotubes (TiO2/CNT/AC) with different ratios of CNTs (0%, 7%, 14%, and 21%). This investigation showed that the increase in the CNT percentage improved the electrical conductivity.131 Hye Kim and colleagues synthesized a zinc oxide/activated carbon nanofiber composite through electrospinning. The supercapacitor performance of the zinc oxide/activated carbon nanofiber electrode materials and activated carbon nanofiber electrode materials were investigated in KOH electrolyte. The results confirmed the synergistic effect between ZnO and ACNF. The high surface area of the activated carbon nanofiber together with the high specific capacitance of zinc oxide promoted the good supercapacitor performance of the composite as an electroactive material.132 Carbon cloth is a suitable substrate for assessing the metal oxide performance in supercapacitor systems. In studies conducted to investigate the performance of hierarchical supercapacitors, Lei et al., using the hydrothermal method, first synthesized NiCo2O4 with a needle structure on carbon cloth (CC/NiCo2O4–N@NiO) and NiCo2O4 with a cut-like structure on carbon cloth (CC/NiCo2O4–S/NiO) (Fig. 2). In the next stage, NiO was grown on CC/NiCo2O4–N@NiO and CC/NiCo2O4–S/NiO. The CC/NiCo2O4–N/NiO showed a specific capacitance of 709 F g−1 while CC/NiCo2O4–S/NiO showed a specific capacitance of 775 F g−1 at the same current density. By examining the morphology of these two core–shell structures by SEM and TEM images and examining the surface by BET analysis, the presence of multiple pores of different sizes in these structures was confirmed, which are beneficial for increasing the penetration of electrolytes and improving the supercapacitor properties. Electrochemical analyses of these two core–shell structures showed redox peaks that were related to faradaic reactions carried out by the core–shell structures. The electrochemical performance of carbon cloth alone was investigated to investigate the effect of carbon cloth on the final performance of these electrode materials. The results of the comparison of the analyses showed the increase in the subsurface area with the presence of carbon cloth. An asymmetric device was fabricated for both core–shell structures grown on carbon fabric using graphene as a negative electrode. Examining the electrochemical results related to both asymmetric devices showed they were highly stable for up to 1000 cycles.133
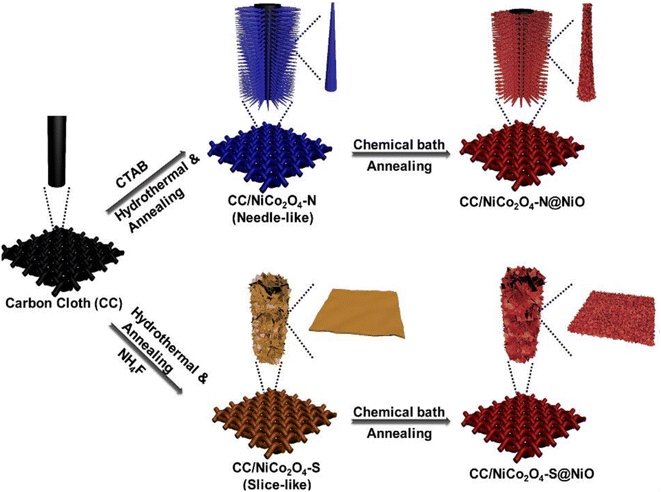 |
| Fig. 2 Schematic of the preparation of CC/NiCo2O4–N@NiO and CC/NiCo2O4–S@NiO.133 | |
Liu et al. prepared a nanocomposite based on carbon nanotubes, graphite foam, and iron oxide (GF/CNT/Fe2O3) as an anode electrode for the manufacture of an asymmetric supercapacitor. According to Fig. 3, carbon nanotubes were first formed on the nickel foam, and then iron oxide was placed on the carbon nanotubes. Investigation of the electrochemical behavior of the GF–CNT/Fe2O3 electrode material utilizing a three-electrode systems showed the EDLC behavior of graphite foam and carbon nanotubes with the quasi-capacitive behavior of iron oxide. The performance of the GF–CNT/Fe2O3 composite with different Fe2O3 ratios (200, 400, and 600) was next investigated. Examining the supercapacitor behavior of the three composites with the different Fe2O3 ratios showed that GF/CNT/200Fe2O3 had a lower current density than the GF/CNT/400Fe2O3 composite. With increasing the percentage of Fe2O3 in the GF/CNT/600Fe2O3 composite, the ionic conductivity decreased. Therefore, the GF/CNT/400Fe2O3 composite was chosen as the negative electrode to make an asymmetric supercapacitor device. Finally, the asymmetric supercapacitor was fabricated using GF/CNT/400Fe2O3 composite as the negative electrode and GF CoMoO4 as the positive electrode (Fig. 3). Investigation of the specific capacitance of the asymmetric device (GF–CNT/Fe2O3//GF–CoMoO4) at different current densities, as shown in Fig. 3c, revealed that with the increase in the current density, the specific capacitance decreased to a small amount, which confirmed the good supercapacitor behavior of the asymmetric device. Also, the asymmetric device (GF–CNT/Fe2O3//GF–CoMoO4) showed 95% stability for up to 5000 cycles. The asymmetric device (GF–CNT/Fe2O3//GF–CoMoO4) with high energy density is an example of an efficient supercapacitor device that was able to overcome the limitations of supercapacitor devices by the careful choice of effective electroactive materials134 (Table 1).
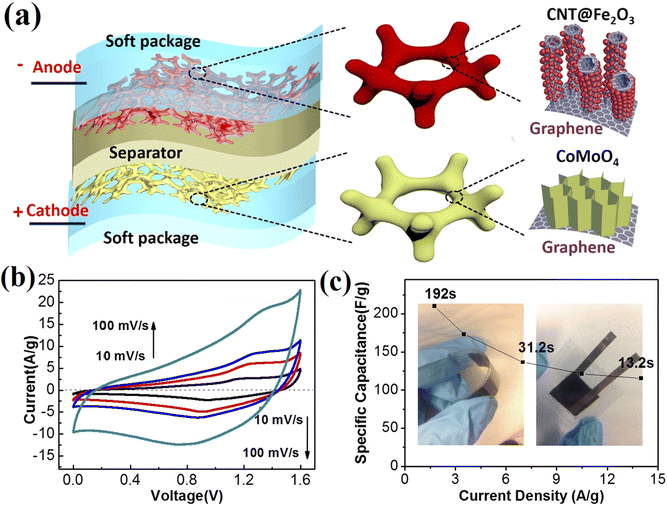 |
| Fig. 3 Electrochemical behavior of the GF–CNT/Fe2O3//GF–CoMoO4 full cell. (a) Schematic of the full-cell package. (b) CV curves, (c) rate capability. | |
Table 1 Investigating the specific capacitance of different types of composites based on carbon materials/metal oxides
Composite |
Specific capacitance |
Current density |
Reference |
Ni(OH)2–MnO2–RGO |
1985 F g−1 |
1 A g−1 |
135 |
Graphene sheet/porous NiO |
400 F g−1 |
2 A g−1 |
136 |
NiO/RGO |
1016.6 F g−1 |
1 A g−1 |
137 |
Carbon-coated mesoporous NiO nanoparticles |
931 F g−1 |
2 A g−1 |
138 |
NiO/Ni/rGO |
2048.3 F g−1 |
1 A g−1 |
139 |
Ni(OH)2/graphene/nickel |
2161 F g−1 |
1 A g−1 |
140 |
Ni(OH)2/AC/CNT |
1038 F g−1 |
1 A g−1 |
141 |
α-Fe2O3/rGO |
970 F g−1 |
1 A g−1 |
142 |
Co3O4 nanowire network coated on a carbon fiber |
1124 F g−1−1 |
0.25 A g−1 |
143 |
Co3O4 nanoparticles on vertically aligned graphene nanosheets |
3560 F g−1 |
1 A g−1 |
144 |
Fe2O3/ACC |
1181 F g−1 |
5 A g−1 |
145 |
Graphene–CeO2 |
110 F g−1 |
1 A g−1 |
146 |
CeO2/MWCNTs |
455.6 F g−1 |
1 A g−1 |
147 |
CeO2/CNTs |
818 F g−1 |
1 mV s−1 |
148 |
Nb2O5/rGO |
620.5 F g−1 |
1 mV s−1 |
149 |
4.2. Nanocomposites of carbon materials/metal sulfides
Metal sulfides are another category of electroactive materials that have been extensively studied in recent years. Metal sulfides have a high specific capacitance, good energy density, and good supercapacitor properties. However, metal sulfides are oxidized in the vicinity of air, which limits the use of metal sulfides as electroactive materials in supercapacitors. As mentioned before, carbonaceous materials are an important candidate for the manufacture of nanocomposite electrode materials for improving the electrical conductivity and the specific surface area. Preparing composites based on metal sulfides and carbon materials prevents the oxidation of metal sulfides, increases the specific surface area, and improves the supercapacitor properties. Shen et al. used a hydrothermal method to cover nickel sulfide on carbon and then put it on to a graphene oxide sheet. Various composites with different percentages of the precursor material were also prepared to achieve optimal electrode materials. The electrochemical behaviors of RGO and CCNS were investigated to determine the effect of each component in the composite on the final performance. The results confirmed the synergistic effect and high specific surface area. Finally, the CCNS–RGO composite showed a specific capacitance of 860.1 F g−1 at 5 mV s−1.150 Vickraman et al. synthesized nickel sulfide and carbon-based nanocomposites with a core–shell structure. In this study, to obtain stable materials, nanocomposites were prepared with different proportions of carbon and nickel sulfide. The nanocomposite with 1% carbon and 0.5% nickel sulfide confirmed the achievement of an electroactive material with good supercapacitor properties (specific capacitance of 1022 F g−1 at 1 A g−1).151 Using a multi-step method, Yang et al. first synthesized nickel oxide coated with carbon and then synthesized a nanocomposite based on nickel oxide coated with carbon with reduced graphene oxide. Finally, the nanocomposite based on nickel sulfide coated with carbon and reduced graphene oxide (Ni3S2–C/rGO) (Fig. 4) was synthesized by sulfonation. The stable structure of the nanocomposite confirmed the achievement of good supercapacitor properties with high conductivity.152
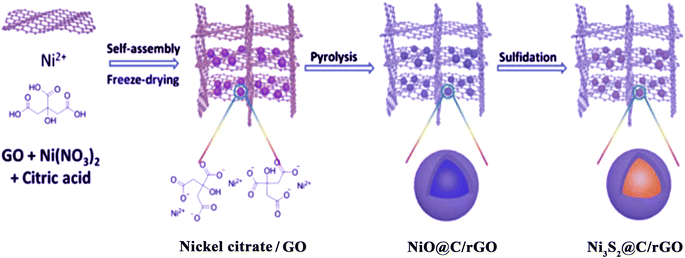 |
| Fig. 4 Schematic of the synthesis of dual carbon-modified Ni3S2–C/rGO.152 | |
In another study, a nanocomposite based on copper-nickel sulfide and carbon nanotubes (obtained by placing copper–nickel sulfide in the structure of carbon nanotubes) was synthesized. The NiCuS/CNT composite demonstrated high stability and power density, and showed a specific capacity of 1110.0 C g−1. Investigation of the performance of the nanocomposite supercapacitors in an asymmetric device revealed a power density of 52.5 W h kg−1 at 750 W kg−1, indicating its potential as an efficient device.153 Sreeja et al. synthesized a composite based on cobalt sulfide (CoS) and two other carbon materials, namely graphene oxide (rGO) and multi-walled carbon nanotubes (MWCNTs), using a hydrothermal method. Investigation of the electrochemical behavior of this nanocomposite showed there was a synergistic effect between the sulfided metal (CoS) and other carbon materials (MWCNTs and rGO). The conductivity created by the carbon materials in this nanocomposite (rGO/MWCNT/CoS) confirmed the achievement of a nanocomposite with ideal supercapacitor properties (with the quasi-capacitance behavior of metal sulfide in addition to the high conductivity of carbon materials). A specific capacity of 612 F g−1 was obtained at a power density of 1 A g−1 for the nanocomposite.154 Raj Xavier et al. synthesized a carbon nanotube-based nanocomposite and two types of metal sulfides (nickel sulfide and cobalt sulfide) using a facile method. Investigation of the supercapacitor properties of the CNTs/NiS/CoS nanocomposite confirmed the low resistance of this nanocomposite. Comparing the impedance of the carbon nanotubes with the CNTs/NiS/CoS nanocomposite showed that the resistance of the CNTs/NiS/CoS nanocomposite was decreased compared to the carbon nanotubes due to the synergistic effect between the components of the nanocomposite.155 Manganese oxide is a commonly used electrode material in supercapacitors due to its biocompatibility and cheapness. However, manganese oxide has a low specific capacitance, which has led to the use of manganese sulfide as an alternative electrode material with good supercapacitor properties. Manganese sulfide with a γ-phase (layered structure) has good supercapacitor properties because its structure provides conditions for more electrolyte ion penetration. Tang et al. synthesized a composite based on manganese sulfide and graphene oxide with the Kirkendall effect. The three-dimensional morphology of the MnS/GO-NH3 composite led to its high-efficiency supercapacitor performance. According to the synthesis route shown in Fig. 5, MnS/GO-NH3, MnS/GO, and Mn (OH)2/GO electrode materials were formed in a single synthesis route. Investigation of the electrochemical behavior of all three materials showed that MnS/GO-NH3 had higher conductivity and specific capacitance. Also, the redox peaks of the MnS/GO-NH3 composite were reduced compared to those of the MnS/GO-NH3 and MnS/GO electrode materials.156
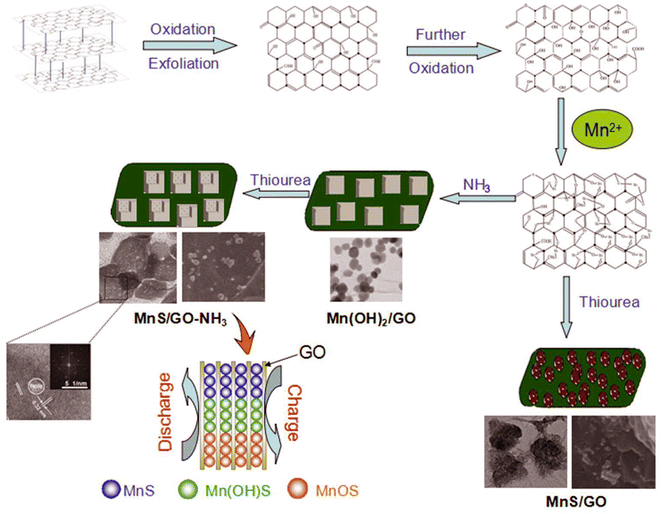 |
| Fig. 5 Schematic of the preparation processes of MnS/GO-NH3 and MnS/GO composites.156 | |
Deng et al. prepared composites based on eggplant-derived carbon materials and NiCo2S4. The electrochemical results showed that the specific capacitance of the composite was 4 times higher than that of NiCo2S4. The composite synthesis (NiCo2S4–carbon derived from eggplant) was done by creating a bond between the polar groups of carbon and the cations. The final morphology of the nanocomposite displayed a flaky structure, which made it possible to achieve an efficient supercapacitor by creating a high surface area (the high surface area was due to carbon derived from eggplant).157 Quan et al. synthesized a nanocomposite based on iron oxide and reduced graphene oxide (α-Fe2O3/rGO) and a nanocomposite based on manganese sulfide and reduced graphene oxide (α-MnS/rGO). Then, an asymmetric device was prepared from these two nanocomposites, which showed a specific capacitance of 161.7 F g−1 at 1 A g−1
158 (Table 2).
Table 2 Investigating the specific capacitance of different types of composites based on carbon materials/metal sulfides
Composite |
Specific capacitance |
Current density |
Reference |
MWCNTs/NiS2 |
2054.28 F g−1 |
2 A g−1 |
158 |
NiCo2S4@CNT |
1123 F g−1 |
0.5 A g−1 |
159 |
C/NiCo2S4 |
1545 F g−1 |
10 A g−1 |
160 |
NiCo2S4/carbon nanotube |
2210 F g−1 |
1 A g−1 |
161 |
NiCo2S4/carbon-filled nickel foam complex |
9.28 F cm−2 |
4 mA cm−2 |
162 |
NiCo2S4/CNTs |
1690 F g−1 |
5 A g−1 |
163 |
CoS2/AC/g-C3N4 |
984 F g−1 |
5 A g−1 |
164 |
CoS/nitrogen-doped carbon |
789 F g−1 |
5 A g−1 |
165 |
CoS2/S, N co-doped porous carbon |
306 F g−1 |
1 A g−1 |
166 |
Co3O4/CoS |
764.2 F g−1 |
1 A g−1 |
167 |
g-CuS/Cc-SC |
1333 mF cm−2 |
2 mA cm−2 |
168 |
CuS–MWCNTs |
2831 F g−1 |
1 A g−1 |
168 |
CuS/CC-4 |
213.8 C g−1 |
0.49 A g−1 |
169 |
CuS/CNT |
1960 F g−1 |
10 mA cm−2 |
170 |
CuS/MWCNT |
396.7 F g−1 |
1 A g−1 |
171 |
ANPC@CuS |
1112.92 F g−1 |
1 A g−1 |
172 |
CuS/carbonized cotton |
4176 mF cm−2 |
2 mA cm−2 |
173 |
CuS/C-dots |
2642 F g−1 |
2 A g−1 |
174 |
CuS/3DG |
249 F g−1 |
4 A g−1 |
175 |
rGO/CuS |
235 C g−1 |
1 A g−1 |
176 |
CuS@CQDs |
920.5 F g−1 |
0.5 A g−1 |
177 |
CuS–CNTs@NF |
467.02 F g−1 |
0.5 A g−1 |
178 |
CC/VAGN/CuS |
342.6 mA h g−1 |
1 A g−1 |
179 |
Cu1.4S/CC |
485 F g−1 |
0.25 A g−1 |
180 |
CuS/C |
719 F g−1 |
1 A g−1 |
181 |
4.3. Nanocomposites of carbon materials/metal–organic frameworks
A metal–organic framework is a crystal structure in which organic ligands link metal ions. Due to their high porosity and the high specific surface, MOFs enable high performance for supercapacitor devices. There are different methods available for the synthesis of MOFs, and the choice of each method creates unique properties. According to the general morphology of MOFs, they show efficient performance in supercapacitor devices as electrode materials. Bimetallic MOFs work better than monometallic MOFs as electrode materials. Electrode materials based on bimetallic MOFs provide good supercapacitor properties, such as simultaneously achieving high energy density and high specific capacitance. The synthesis of composites based on carbon materials and MOFs is an effective method to overcome the limitations observed in monometallic MOFs. The synergistic effect between the MOFs and carbon materials can lead to obtaining efficient electroactive materials.182 Kolekar et al. synthesized composites based on MOF–Zn and reduced graphene oxide by a hydrothermal method (Fig. 6). Electrochemical analysis of the Zn-MOF–rGO composite showed it had a specific capacitance of 205 C g−1 at 1 A g−1.183
 |
| Fig. 6 Schematic of the synthesis of Zn-MOF–rGO.183 | |
In another study, a composite prepared from graphene-like carbon (nitrogen-doped) and a MOF confirmed the synergistic effect between the carbon material and the MOF. The increase in the specific surface due to the carbon compounds and the presence of nitrogen compensated for the lack of conductivity of the MOF compound, with the composite achieving a specific capacitance of 470 F g−1.184 Rai et al. synthesized a nanocomposite based on a copper MOF and reduced graphene oxide. The nanocomposite electrode material displayed a high specific capacitance (366.6 F g−1) and high stability, showing the beneficial synergistic effect from the copper MOF and the reduced graphene oxide.185 An increase in conductivity caused by carbon nanotubes in composites based on MOFs and carbon nanotubes was observed by Wang et al., who also reported that the synergistic effect between the nickel MOF and carbon nanotube) Ni-MOF/CNT(led to a stable electrode material with a specific capacitance of 1765 F g−1.186 The layered structure of a nanocomposite based on a MOF and carbon nanotube (MOF(Ni)/CNT) prepared by the solvothermal method enabled faster electrolyte penetration and increased electrical conductivity. The asymmetric device prepared from these electrode materials demonstrated a specific capacitance of 97 F g−1.187 A nanocomposite based on a MOF (Ni/Co-MOF–rGO) and graphene oxide was prepared using a cobalt MOF as a precursor. The synthesis of the derived MOF and the composite (Ni/Co-MOF–rGO) was performed in one step, and the composite demonstrated a specific capacitance of 860 F g−1.188 However, traditional physical and chemical methods of preparing composites based on MOFs and carbon materials have some disadvantages. This method limits the achievement of a homogeneous composite and sometimes destroys the carbon materials. To overcome this limitation, physical green methods have been used.189 Sulaiman et al. synthesized a nanocomposite based on a copper MOF and reduced graphene oxide by a hydrothermal method. Electrochemical analysis confirmed the resistance of the nanocomposite electrode materials was decreased compared to the individual components (i.e., the reduced graphene oxide and MOF). These use of these electrode materials as the negative electrode in the manufacturing of asymmetric supercapacitors led to a specific capacitance of 483.9 F g−1.190
4.3.1 MOF-derived carbon materials. Carbon materials can be obtained from MOFs, and these MOF-derived carbon materials can have unique performance properties, such as a high specific surface area, for use in energy-storage systems. However, the complex synthesis of MOFs derived from carbon materials limits their performance as electroactive materials for use in industry; in particular, the high cost and the long synthesis method limit the mass production of these materials. To overcome these limitations, Liu et al.191 synthesized a MOF with cobalt ligands by a bottom-up method. The following step involved synthesis of a porous carbon structure (containing cobalt nanoparticles) by thermal decomposition of the MOF (Fig. 7).
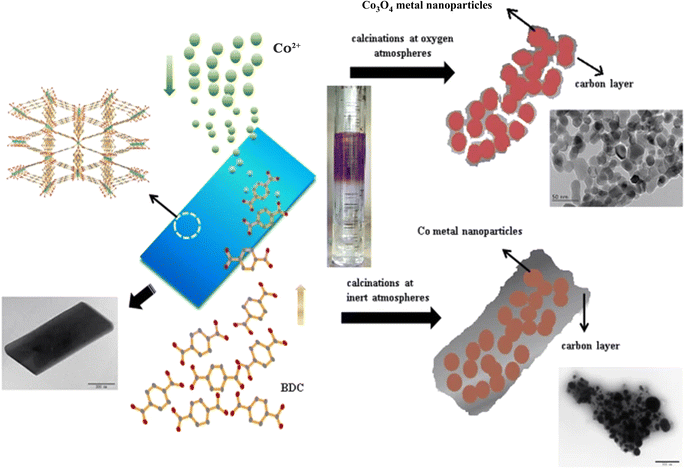 |
| Fig. 7 Schematic of the syntheses of Co-BDC nanosheets and cobalt–carbon composites.191 | |
The carbon structure with high porosity provides abundant active centers for ion transfer and increases the penetration rate of electrolyte ions.191 The type of synthesis of the MOFs affects the final electrochemical behavior of the MOF-derived carbon materials. Mijowska et al. synthesized a MOF (MOF-5) derived from different carbon materials by two different methods (physical and chemical). Then, the carbon nanocomposite derived from the MOF was synthesized in the next step. The results of their electrochemical analyses showed that the nanocomposite derived from the MOF synthesized by the physical method had high stability and displayed a supercapacitor behavior.192 A nanocomposite based on manganese oxide and carbon derived from a MOF was synthesized and its supercapacitor behavior was investigated. As can be seen in Fig. 8a, the CV curve of the MOF-derived nanocomposite in Na2SO4 electrolyte solution showed a pseudocapacitance behavior (apparently inductively coupled with weak redox peaks). Fig. 8b displays the charge–discharge diagram of the nanocomposite, which showed the long discharging time of the nanocomposite, indicating a supercapacitor with a high specific capacitance. Fig. 8c shows the stability of the MOF-derived nanocomposite could be maintained at 94% for up to 5000 cycles. The impedance and the fitted diagrams in Fig. 8d and e confirm the resistance and the supercapacitor behavior of the MOF-derivative nanocomposite. The Ragone plot in Fig. 8f shows the energy density was 15.5 W h kg−1 for the MOF-derived nanocomposite193 (Table 3).
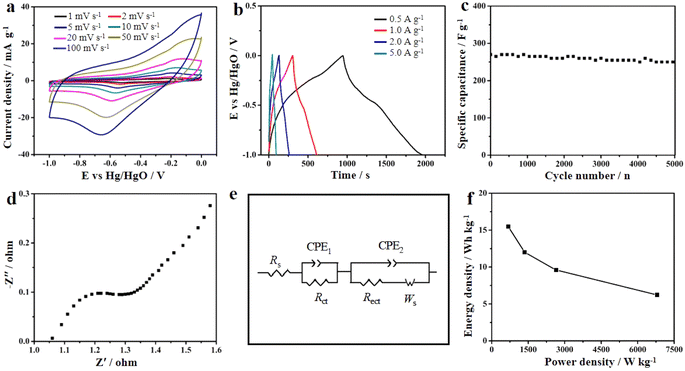 |
| Fig. 8 Electrochemical properties of MnO/C as supercapacitors. (a) CV curves; (b) charge–discharge curves; (c) cycling stability; (d) EIS in a high-frequency region; (e) diagram of an equivalent circuit; and (f) Ragone plot of the symmetrical supercapacitor.193 | |
Table 3 Investigating the specific capacitance of different types of composites based on carbon materials/MOFs and MOF-derived carbon materials
Composite |
Specific capacitance |
Current density |
Reference |
Cu-MOF/rGO |
867.09 F g−1 |
1 A g−1 |
194 |
MOF–CNT |
166.4 F g−1 |
1 A g−1 |
195 |
rGO–NiCo2S4 MOF |
972 F g−1 |
1 A g−1 |
196 |
MOF-NPC/MnO2 |
120 F g−1 |
5 A g−1 |
197 |
Fe-MOF/carbon |
628.5 F g−1 |
1 A g−1 |
198 |
Carbon nanosheet derived from a 2D Cu-MOF |
260.5 F g−1 |
0.5 A g−1 |
199 |
MOF-derived N-doped carbon |
44 F g−1 |
0.67 A g−1 |
200 |
MOF-derived hierarchical carbon network |
385 F g−1 |
0.1 A g−1 |
201 |
γ-CD-MOF |
283.3 F g−1 |
1 A g−1 |
202 |
Nitrogen-doped carbon-enriched MOF |
2727.5 F g−1 |
1.0 A·g−1 |
203 |
G/Co-MOF-derived 3DPC/Co3O4 |
423 F g−1 |
1 A g−1 |
204 |
MOF-derived nanoporous |
545 F g−1 |
1 A g−1 |
205 |
MOF-derived carbon |
174 F g−1 |
1 A g−1 |
206 |
Co-MOF/MX-CNF |
475.4 mA h g−1 |
1 A g−1 |
207 |
MOF-derived phosphorus-doped porous carbons |
168 F g−1 |
1 A g−1 |
208 |
MOF-derived nitrogen-doped porous carbons |
230 F g−1 |
1A g−1 |
209 |
CC/CoNi-MOF |
177.7 F g−1 |
0.21 A g−1 |
210 |
MOF-derived Mn3O4–C/rGO |
382.1 F g−1 |
1 Ag−1 |
211 |
MOF-derived Co9S8/NS–C |
734 F g−1 |
1 Ag−1 |
212 |
NiCo-MOF/MWCNT |
1010 F g−1 |
0.5 A g−1 |
213 |
MOF-derived CNT/NiO |
996 F g−1 |
1 A g−1 |
214 |
MOF-derived NiS2/C |
1572 F g−1 |
0.5 A g−1 |
215 |
MOF-derived Ni–CoP/C |
708.1 F g−1 |
1 A g−1 |
216 |
Ni-MOF-derived NiO/C |
496 C g−1 |
1 A g−1 |
217 |
MOF-67-derived C |
24.7 F cm−2 |
1 mA cm−2 |
218 |
4.4. Nanocomposites of carbon materials/polymers
Polymers are substances of natural and synthetic origin that consist of repeating units. Among the categories related to polymers (organic, inorganic, synthetic, non-elastomer), organic polymers, as conductive polymers, have shown good performance in energy-storage devices. Conductive polymers are called organic metals (common behavior between polymers and metals) as electrode materials with better supercapacitor properties than other inorganic materials. The electrical conductivity of conductive polymers as electrode materials is not the same as the conductivity of other electrode materials (conductive and semiconducting). The conduction mechanism of conductive polymers is not similar to other electroactive materials. In general, the conduction mechanism of conductive polymers is a combination of electrical conductivity and ionic conductivity. Therefore, conductive polymers show a double charge-transfer mechanism, and when the π–π electrons are transferred, a conductive path is created. During the electrochemical reactions performed on the surface of conductive polymers, ions move on the surface of the conductive polymer, which causes a change in the oxidation state219 Among conductive polymers, polyaniline is among the most biocompatible and can be obtained via a facile synthesis method. The high conductivity, low density, and good mechanical properties of polyaniline have made polyaniline a suitable candidate for preparing nanocomposites to improve the performance of semiconductor materials. However, some nanocomposites based on polyaniline and semiconductor materials are less stable due to the swelling caused by the doping process of polyaniline chains. Therefore three-component nanocomposites based on semiconducting materials, polyaniline, and carbon materials have been synthesized to overcome this limitation. Liu et al. synthesized a nanocomposite based on vanadium oxide, conductive polymer, and carbon nanotubes, and the resulting nanocomposite showed an increase in stability and specific capacitance compared to those of the individual components.220 The synergistic effect between polyaniline and carbon nanotubes and NiMnO3 made it possible to achieve a supercapacitor with high stability, high power density, and a specific capacitance of 1276 F g−1.221 The synergistic effect between silver ions, activated carbon, and polyaniline enabled obtaining efficient electrode materials.222
A composite of MWCNTs with polyaniline synthesized by a self-dispersion method enabled obtaining electrode materials that displayed a specific capacitance of 1017 F g−1 due to the synergistic effect between the polyaniline and MWCNTs.223 Composite synthesis based on carbon materials and polyaniline allowed obtaining a flexible supercapacitor that was shown to be stable under mechanical stress. The synthesis of electrode materials based on carbon nanotubes, polyaniline, and graphene was used to prepare flexible supercapacitors with desirable supercapacitor properties.224 Chen et al. reported a three-component nanocomposite synthesized on carbon nanotube fibers in which the shell–shell structured N-CNTs were formed and then polyaniline was deposited on the N-CNTs. The carbon nanotube fibers increased the speed of electron transfer and improved the interaction between the other components (PANI and N-CNTs), while the N-CNTs increased the rate of ion transfer and the rate of electron transfer at the same time. The synergistic effect between the three components of the composite led to it displaying a specific capacitance of 221.3 F g−1.225 Polyaniline's cyclic stability was achieved by preparing a composite based on polyaniline and MWCNTs combined with activated carbon (A-MWCNT/PANI). The carbon materials ensured the polyaniline polymer matrix was homogeneous. In a study conducted by Park et al., activated MWCNTs were used to homogenize the surface of polyaniline to improve the stable cycle. Activation of the MWCNTs increased the specific surface area of nanotubes, which had a great effect on improving the final performance of the nanocomposites. Also, the interactions created between the carbon (π-conjugated) and polyaniline (quinoid ring) components accelerated the charge-transfer process.226 Activated carbon has been used to preserve the polyaniline polymer chain from degradation during charge–discharge cycles, which can enable obtaining stable electrode materials. In many cases, the specific capacitance of polyaniline is higher than the composite based on carbon and polyaniline materials, so the synthesis of nanocomposites based on polyaniline and carbon materials can be performed to increase the cyclic stability of electrode materials.227 To determine the influence of the synthesis method on the final performance of electrode materials based on nanocomposites derived from carbon materials and polyaniline, a study was conducted by Morallón et al. comparing the synthesis of nanocomposite electrode materials obtained by two chemical and electrochemical methods. Two asymmetric devices were prepared from nanocomposites synthesized by electrochemical and chemical methods using activated carbon as the negative electrode. The supercapacitor behaviors of the asymmetric devices were investigated using H2SO4 electrolyte. A better supercapacitor behavior was obtained for the asymmetric device of the nanocomposite prepared by the chemical method, displaying an energy density of 20 W h kg−1.228 A flexible supercapacitor for use in wearable electronics was obtained by Chen et al. based on a composite prepared from activated carbon fiber, polyaniline, and carbon nanosheets. Their investigations into the electrochemical behavior of the active carbon fiber (ACFF) used in the manufacture of wearable electronics showed it had poor electrical conductivity; however, the high porosity of ACFF facilitated the absorption of electrolyte ions, so the low specific capacity of these materials corresponded to the poor electrical conductivity. To improve the performance of ACFF, different ratios of polyaniline (0.5, 0.1, 0.15, and 0.2) were combined with ACFF. CV analysis of the prepared composites confirmed the nanocomposite containing 0.1% polyaniline had higher specific capacitance. To improve the electrical conductivity of nanocomposite based on polyaniline and ACFF a three-component nanocomposite based on polyaniline, ACFF, and carbon nanotube was synthesized. The obtained nanocomposite showed a high specific capacitance of 5476 mF cm−2.229 Activated carbon derived from biomaterials has demonstrated high performance in energy-storage systems. Du et al. synthesized celery-derived activated carbon at 500 °C under CO2 gas. Next, a composite based on polyaniline and celery-derived activated carbon was synthesized. Then nitrogen-doped porous carbon was synthesized by carbonization of the composite formed at 850 °C under nitrogen gas. The electrochemical behavior of the obtained nitrogen-doped porous carbon electrode material was investigated in H2SO4 electrolyte solution and showed a specific capacitance of 402 F g−1.230 Xie et al. reported synthesizing ACFs (fibers substrate of activated carbon) by a hydrothermal method under argon gas and then polyaniline was grown on the ACFs. The ACFs demonstrated increasing electrical conductivity, which led to the achievement of efficient electrode materials with a specific capacitance of 296.3 F g−1.231 Carbon materials, including activated carbon and graphene oxide, which can be added to increase the cyclic stability of polyaniline, have low solubility in water, so choosing hydrophilic carbon materials, such as carbon-based quantum dots, can be a suitable alternative. Thambusamy et al. synthesized quantum dots derived from ascorbic acid, with an aim to take advantage of the high electrical conductivity of ascorbic acid, by a hydrothermal method at 180 °C. Then a PANI–CQD–Cu nanocomposite was synthesized by polymerization from aniline monomer, CuSO4, and CQD derived from ascorbic acid. The conductivity of the PANI was improved by the presence of the CQD surface functional groups along with the redox catalytic property of copper ions. The electrochemical behaviors of the polyaniline and polyaniline–CQD–Cu nanocomposite and polyaniline–copper and polyaniline–CQD composites were investigated in the same electrolyte (1 M H2SO4), with the high supercapacitor performance of the polyaniline–CQD–Cu nanocomposite demonstrated, with a specific capacitance of 1070 F g−1
232 (Table 4).
Table 4 Investigating the specific capacitance of different types of composites based on carbon materials/MOFs and polymers
Composite |
Specific capacitance |
Current density |
Reference |
Mn-CPANI |
329 F g−1 |
1 A g−1 |
233 |
AC/PANI/PVA |
66.6 F g−1 |
1 A g−1 |
234 |
PANI/AC |
35 F g−1 |
1 A g−1 |
235 |
PANI/AC/TiO2 nanowires |
286 F g−1 |
1 A g−1 |
236 |
ACC/PANI |
369 F g−1 |
50 mA g−1 |
237 |
PANI/AC/CuF |
248.3 F g−1 |
1 A g−1 |
238 |
PANI/AC |
549.5 F g−1 |
1 A g−1 |
239 |
PANI/AC |
1250 F g−1 |
1 A g−1 |
240 |
PANI-TU-ACF |
563.8 F g−1 |
1 A g−1 |
241 |
NSAC-PANI-2 |
304 F g−1 |
1 A g−1 |
242 |
PANI/nTiO2/AC |
827 F g−1 |
10 mV s−1 |
243 |
AC/PANI |
437.9 F g−1 |
0.5 A g−1 |
244 |
PANI/GO/CuFe2O4 |
614.76 F g−1 |
0.5 A g−1 |
245 |
PCNT-NMP-40 |
917.3 F g−1 |
1 A g−1 |
246 |
AC//Pani-C |
230 F g−1 |
1 A g−1 |
247 |
rGO/PANI/PB |
336 F g−1 |
1 A g−1 |
248 |
PANI/CNTs |
389.5 F g−1 |
0.5 A g−1 |
249 |
PANI/(TOCNF-SMWCNT) |
546 F g−1 |
1 A g−1 |
250 |
4.5. Nanocomposites of carbon materials/MXenes
The first report of MXene synthesis was recorded in 2011 by Gogotsi et al.251 MXenes consist of the Mn+1AXn phase (n = 1, 2, 3…), where M, A, and X are transition metals, IIIA or IVA elements, and carbon or nitrogen, respectively. Despite having good physical and chemical properties as electrode materials, MXenes have low cyclic stability. The performance of MXenes as electrode material can be improved by the formation of carbon/MXene-based composites. Carbon materials increase the electrolyte diffusion rate by increasing the specific surface area, enabling obtaining electrode materials with high stability and specific capacitance. The synthesis methods of MXenes include electrostatic, hydrothermal, and solvothermal methods. Sathish et al. synthesized N-(Nb2CTx/rGO) using a supercritical fluid method. Nb2CTx synthesized by the supercritical fluid method has better supercapacitor properties than other MXenes. The electrochemical behavior of (Nb2CTx/rGO) was investigated in H2SO4, TEABF4/ACN, and PVA/H2SO4 electrolytes, and the stability of the N-(Nb2CTx/rGO) electrode material in the PVA/H2SO4 electrolyte was recorded as 100% at up to 100
000 cycles. The 2D/2D structure of the N-(Nb2CTx/rGO) composite with high specific surface area suggest its potential use as a commercial electrode material with high stability (100% stability) and provide the basis for further studies in this field.252
6. Conclusion
In this study, by reviewing the electrochemical properties of different types of carbon-based nanocomposites as electrode materials, the effect of each type of carbon material (CNT, AC, CQD, GO, and RGO) on improving the various types of electroactive materials (metal oxides, conductive polymers, MOFs, and metal sulfides) was investigated. The combination of carbon materials with metal oxides reduces the faradaic current while the synergistic effect between the metal oxides and carbon materials enables obtaining electrode materials with high specific capacitance. Carbon materials prevent the oxidation of metal sulfides in the vicinity of air. Composites based on carbon materials and MOFs can enable obtaining electrode materials with a larger specific surface area. Finally, carbon materials can improve the cyclic stability of conductive polymers and prevent the destruction of polymer chains during long charge–discharge cycles. This review study, by comprehensively examining the effect of carbon materials in improving the performance of other electroactive materials, provides insights for further innovative studies by researchers in this field.
Data availability
This manuscript is a review, and all data presented are sourced from cited references.
Conflicts of interest
The authors have no conflict of interest.
Acknowledgements
The authors gratefully acknowledge the University of Payame Noor and University of Economics (UNEC) for the financial support for this research.
References
- H. Nazarpourfard, L. F. Aval and D. P. Dubal, Mater. Adv., 2023, 4, 6152–6174 RSC.
- X. Zhang, H. Zhang, C. Li, K. Wang, X. Sun and Y. Ma, RSC Adv., 2014, 4, 45862–45884 RSC.
- K. H. H. Aziz, F. S. Mustafa, K. M. Omer, S. Hama, R. F. Hamarawf and K. O. Rahman, RSC Adv., 2023, 13, 17595–17610 RSC.
- M. A. Hossain, M. S. I. S. Kawsar Sheikh, K. R. Hossain, X. Yao, C. Bai and X. Wang, Chem. Rev. Lett., 2023, 6, 461–478 Search PubMed.
- L. Zhang, H. Guo, W. Zong, Y. Huang, J. Huang, G. He, T. Liu, J. Hofkens and F. Lai, Energy Environ. Sci., 2023, 16, 4872–4925 RSC.
- Ş. Neaţu, F. Neaţu, I. M. Chirica, I. Borbáth, E. Tálas, A. Tompos, S. Somacescu, P. Osiceanu, M. A. Folgado and A. M. Chaparro, J. Mater. Chem. A, 2021, 9, 17065–17128 RSC.
- Y. Zhong, J. Liu, X. Wu, Z. Guguchia, J.-X. Yin, A. Mine, Y. Li, S. Najafzadeh, D. Das and C. Mielke III, Nature, 2023, 617, 488–492 CrossRef PubMed.
- S. A. Kadam, K. P. Kadam and N. R. Pradhan, J. Mater. Chem. A, 2024, 12, 17992–18046 RSC.
- F. Alimola, N. Arsalani and I. Ahadzadeh, Mater. Chem. Phys., 2024, 319, 129293 CrossRef.
- A. Pramuanjaroenkij and S. Kakaç, Int. J. Hydrogen Energy, 2023, 48, 9401–9425 CrossRef.
- S. Kalnaus, N. J. Dudney, A. S. Westover, E. Herbert and S. Hackney, Science, 2023, 381, eabg5998 CrossRef PubMed.
- C. Lee, W. J. Kort-Kamp, H. Yu, D. A. Cullen, B. M. Patterson, T. A. Arman, S. Komini Babu, R. Mukundan, R. L. Borup and J. S. Spendelow, Nat. Energy, 2023, 8, 685–694 CrossRef.
- T. Cao, K. Huang, Y. Shi and N. Cai, Energy Environ. Sci., 2017, 10, 460–490 RSC.
- K. I. Ozoemena, RSC Adv., 2016, 6, 89523–89550 RSC.
- L. Fagiolari, M. Sampò, A. Lamberti, J. Amici, C. Francia, S. Bodoardo and F. Bella, Energy Storage Mater., 2022, 51, 400–434 CrossRef.
- A. Ray and B. Saruhan, Materials, 2021, 14, 2942 CrossRef PubMed.
- S. B. Mujib, F. Ribot, C. Gervais and G. Singh, RSC Adv., 2021, 11, 35440–35454 RSC.
- M. Yaseen, M. A. K. Khattak, M. Humayun, M. Usman, S. S. Shah, S. Bibi, B. S. U. Hasnain, S. M. Ahmad, A. Khan and N. Shah, Energies, 2021, 14, 7779 CrossRef.
- F. Alimola, N. Arsalani and I. Ahadzadeh, Electrochim. Acta, 2022, 417, 140283 CrossRef.
- A. G. Olabi, Q. Abbas, A. Al Makky and M. A. Abdelkareem, Energy, 2022, 248, 123617 CrossRef.
- Y. Yang, Y. Han, W. Jiang, Y. Zhang, Y. Xu and A. M. Ahmed, Appl. Sci., 2021, 12, 354 CrossRef.
- Y. Li, T. Liu, Y. Liu, F. Meng and Z. Cao, Chem. Eng. J., 2024, 479, 147906 CrossRef.
- T. L. Kulova, V. N. Fateev, E. A. Seregina and A. S. Grigoriev, Int. J. Electrochem. Sci., 2020, 15, 7242–7259 CrossRef.
- H. Xu and M. Shen, Int. J. Energy Res., 2021, 45, 20524–20544 CrossRef.
- H. Shayeghi, F. Monfaredi, A. Dejamkhooy, M. Shafie-Khah and J. Catalão, Int. J. Electr. Power Energy Syst., 2021, 125, 106391 CrossRef.
- N. Arya, Y. Chandran, B. Luhar, P. Kajal, S. Powar and V. Balakrishnan, ACS Appl. Mater. Interfaces, 2023, 15, 34818–34828 CrossRef PubMed.
- J. Cherusseri, D. Pandey and J. Thomas, Batteries Supercaps, 2020, 3, 860–875 CrossRef.
- A. Abdellah, D. Toumi and S. Moreau, Adv. Electr. Electron. Eng., 2022, 20, 154–169 Search PubMed.
- P. Forouzandeh, V. Kumaravel and S. C. Pillai, Catalysts, 2020, 10, 969 CrossRef.
- S. Veeresh, H. Ganesha, Y. Nagaraju, H. Vijeth, M. Vandana, M. Basappa and H. Devendrappa, J. Energy Storage, 2022, 52, 104715 CrossRef.
- X. Chen, Q. Liu, T. Bai, W. Wang, F. He and M. Ye, Chem. Eng. J., 2021, 409, 127237 CrossRef.
- D. J. Ahirrao, A. K. Pal, V. Singh and N. Jha, J. Mater. Sci. Technol., 2021, 88, 168–182 CrossRef.
- M. Vandana, S. Veeresh, H. Ganesh, Y. Nagaraju, H. Vijeth, M. Basappa and H. Devendrappa, J. Energy Storage, 2022, 46, 103904 CrossRef.
- M. Shaheen, M. Z. Iqbal, M. W. Khan, S. Siddique, S. Aftab and S. M. Wabaidur, Energy Fuels, 2023, 37, 4000–4009 CrossRef.
- K. Wang, Z. Wang, J. Liu, C. Li, F. Mao, H. Wu and Q. Zhang, ACS Appl. Mater. Interfaces, 2020, 12, 47482–47489 CrossRef PubMed.
- X. Shi, L. Sun, X. Li, L. Wu, J. Qian, J. Wang, Y. Lin, S. Su, C. Sun and Y. Zhang, J. Colloid Interface Sci., 2022, 606, 135–147 CrossRef PubMed.
- C. Hu, L. Miao, Q. Yang, X. Yu, L. Song, Y. Zheng, C. Wang, L. Li, L. Zhu and X. Cao, Chem. Eng. J., 2021, 410, 128317 CrossRef.
- P. Avasthi, N. Arya, M. Singh and V. Balakrishnan, Nanotechnology, 2020, 31, 435402 CrossRef.
- R. Mohammadi, Chem. Rev. Lett., 2022, 5, 133–140 Search PubMed.
- R. Bian, D. Song, W. Si, T. Zhang, Y. Zhang, P. Lu, F. Hou and J. Liang, ChemElectroChem, 2020, 7, 3663–3669 CrossRef.
- C. Zhang, Q. Wang, W. Zhang, X. Li, Z. Zhu, C. Zhang, A. Xie and S. Luo, Ionics, 2021, 27, 3543–3551 CrossRef.
- J. Ben, Z. Song, X. Liu, W. Lü and X. Li, Nanoscale Res. Lett., 2020, 15, 1–8 CrossRef PubMed.
- Y. Jiang, J. Ou, Z. Luo, Y. Chen, Z. Wu, H. Wu, X. Fu, S. Luo and Y. Huang, Small, 2022, 18, 2201377 CrossRef.
- J. Dai, Y. Lv, J. Zhang, D. Zhang, H. Xie, C. Guo, A. Zhu, Y. Xu, M. Fan and C. Yuan, J. Colloid Interface Sci., 2021, 590, 591–600 CrossRef PubMed.
- N. I. Jalal, R. I. Ibrahim and M. K. Oudah, J. Phys.:Conf. Ser., 2021, 1973, 012015 CrossRef.
- R. Taslim, A. Apriwandi and E. Taer, ACS Omega, 2022, 7, 36489–36502 CrossRef PubMed.
- M. Gaire, B. Subedi, S. Adireddy and D. Chrisey, RSC Adv., 2020, 10, 40234–40243 RSC.
- V. Kushwaha, A. Gupta, R. B. Choudhary, K. Mandal, R. Mondal and P. Singh, Phys. Chem. Chem. Phys., 2023, 25, 555–569 RSC.
- J. Sun, B. Luo and H. Li, Adv. Energy Sustainability Res., 2022, 3, 2100191 CrossRef.
- M. Brza, S. Aziz, H. Anuar and F. Ali, Polym. Test., 2020, 91, 106813 CrossRef.
- S. B. Aziz, M. Hamsan, M. Brza, M. Kadir, S. Muzakir and R. T. Abdulwahid, J. Mater. Res. Technol., 2020, 9, 8355–8366 CrossRef.
- A. S. Asnawi, S. B. Aziz, M. M. Nofal, M. H. Hamsan, M. A. Brza, Y. M. Yusof, R. T. Abdilwahid, S. K. Muzakir and M. F. Kadir, Polymers, 2020, 12, 1433 CrossRef PubMed.
- W. Zhou, Z. Liu, W. Chen, X. Sun, M. Luo, X. Zhang, C. Li, Y. An, S. Song and K. Wang, Batteries, 2023, 9, 128 CrossRef CAS.
- L. L. Zhang and X. Zhao, Chem. Soc. Rev., 2009, 38, 2520–2531 RSC.
- W. Raza, F. Ali, N. Raza, Y. Luo, K.-H. Kim, J. Yang, S. Kumar, A. Mehmood and E. E. Kwon, Nano Energy, 2018, 52, 441–473 CrossRef.
- N. R. Chodankar, H. D. Pham, A. K. Nanjundan, J. F. Fernando, K. Jayaramulu, D. Golberg, Y. K. Han and D. P. Dubal, Small, 2020, 16, 2002806 CrossRef PubMed.
- T. Brezesinski, J. Wang, S. H. Tolbert and B. Dunn, Nat. Mater., 2010, 9, 146–151 CrossRef PubMed.
- L. Wang, L. Gao, J. Wang and Y. Shen, J. Mater. Sci., 2019, 54, 13685–13693 CrossRef.
- Y. Shao, M. F. El-Kady, J. Sun, Y. Li, Q. Zhang, M. Zhu, H. Wang, B. Dunn and R. B. Kaner, Chem. Rev., 2018, 118, 9233–9280 CrossRef PubMed.
- A. Muzaffar, M. B. Ahamed, K. Deshmukh and J. Thirumalai, Renewable Sustainable Energy Rev., 2019, 101, 123–145 CrossRef.
- A. Afif, S. M. Rahman, A. T. Azad, J. Zaini, M. A. Islan and A. K. Azad, J. Energy Storage, 2019, 25, 100852 CrossRef.
- S. Ratha and A. K. Samantara, Supercapacitor: Instrumentation, Measurement and Performance Evaluation Techniques, Springer, 2018 Search PubMed.
- Y. Zhang, Y. Liu, Y. Bai, Y. Liu and E. Xie, RSC Adv., 2020, 10, 35295–35301 RSC.
- N. Kularatna, K. Subasinghage, K. Gunawardane, D. Jayananda and T. Ariyarathna, Electronics, 2021, 10, 1697 CrossRef.
- S. Yadav and A. Sharma, J. Energy Storage, 2021, 44, 103295 CrossRef.
- F. Alimola, N. Arsalani and I. Ahadzadeh, J. Alloys Compd., 2023, 949, 169851 CrossRef.
- K. Sharma, A. Arora and S. K. Tripathi, J. Energy Storage, 2019, 21, 801–825 CrossRef.
- L. Zeng, T. Wu, T. Ye, T. Mo, R. Qiao and G. Feng, Nat. Comput. Sci., 2021, 1, 725–731 CrossRef.
- M. Gaire, K. Liang, S. Luo, B. Subedi, S. Adireddy, K. Schroder, S. Farnsworth and D. B. Chrisey, RSC Adv., 2020, 10, 16817–16825 RSC.
- A. Fernandez, E. Perigo and R. Faria, J. Energy Storage, 2022, 51, 104471 CrossRef.
- C. Zheng, C. Cao, Z. Ali and J. Hou, J. Mater. Chem. A, 2014, 2, 16467–16473 RSC.
- R. Srinivasan, E. Elaiyappillai, E. J. Nixon, I. S. Lydia and P. M. Johnson, Inorg. Chim. Acta, 2020, 502, 119393 CrossRef.
- N. I. Jalal, R. I. Ibrahim and M. K. Oudah, J. Phys.:Conf. Ser., 2021, 1973, 012015 CrossRef.
- R. Ahmad, U. A. Khan, N. Iqbal and T. Noor, RSC Adv., 2020, 10, 43733–43750 RSC.
- R. Aslani and H. Namazi, J. Ind. Eng. Chem., 2022, 112, 335–347 CrossRef.
- S. Iijima, J. Cryst. Growth, 1980, 50, 675–683 CrossRef.
- S. Kaur, A. Krishnan and S. Chakraborty, J. Energy Storage, 2023, 71, 107928 CrossRef.
- J. Xiao, G. Ouyang, P. Liu, C. Wang and G. Yang, Nano Lett., 2014, 14, 3645–3652 CrossRef PubMed.
- D. M. Anjos, J. K. McDonough, E. Perre, G. M. Brown, S. H. Overbury, Y. Gogotsi and V. Presser, Nano Energy, 2013, 2, 702–712 CrossRef.
- J. K. McDonough and Y. Gogotsi, Electrochem. Soc. Interface, 2013, 22, 61 CrossRef.
- E.-S. V. Zran, A. Y. Yobouet, L. Kouakou, P. Marie-Sandrine, A. Trokourey and B. K. Yao, Chem. Rev. Lett., 2022, 5, 178–186 Search PubMed.
- H. Kone, I. A. Goure Bi, J. Ano, Y. Soro, G. H. Briton Bi and B. K. Yao, Chem. Rev. Lett., 2021, 4, 221–231 Search PubMed.
- B. Li, F. Dai, Q. Xiao, L. Yang, J. Shen, C. Zhang and M. Cai, Energy Environ. Sci., 2016, 9, 102–106 RSC.
- F. Cheng, X. Yang, S. Zhang and W. Lu, J. Power Sources, 2020, 450, 227678 CrossRef.
- T. Chaiwon, P. Jannoey and D. A. D. Channei, Key Eng. Mater., 2017, 751, 671–676 Search PubMed.
- S. D. Magar, C. Leibing, J. L. Gómez-Urbano, R. Cid, D. Carriazo and A. Balducci, Electrochim. Acta, 2023, 446, 142104 CrossRef.
- K. Hina, H. Zou, W. Qian, D. Zuo and C. Yi, Cellulose, 2018, 25, 607–617 CrossRef.
- F. Jerez, P. B. Ramos, V. E. Córdoba, M. F. Ponce, G. G. Acosta and M. A. Bavio, J. Environ. Manage., 2023, 330, 117158 CrossRef.
- B. Pant, G. P. Ojha, J. Acharya and M. Park, Diamond Relat. Mater., 2023, 136, 110040 CrossRef CAS.
- S. J. Rajasekaran, A. N. Grace, G. Jacob, A. Alodhayb, S. Pandiaraj and V. Raghavan, Catalysts, 2023, 13, 286 CrossRef.
- S. Wang, F. Chen, G. Zhuang, K. Wei, T. Chen, X. Zhang, C. Chen and P. Du, Nano Res., 2023, 16, 10342–10347 CrossRef.
- V. N. Popov, Mater. Sci. Eng., R, 2004, 43, 61–102 CrossRef.
- B. Ghanavati, A. Bozorgian and J. Ghanavati, Chem. Rev. Lett., 2022, 5, 68–75 Search PubMed.
- M. F. De Volder, S. H. Tawfick, R. H. Baughman and A. J. Hart, science, 2013, 339, 535–539 CrossRef PubMed.
- A. Rashak and F. F. Karam, Chem. Rev. Lett., 2024, 7(8), 719–730 Search PubMed.
- J. Hu, G. Sang, N. Zeng, C. Lv and C. Xu, Sens. Actuators, B, 2022, 356, 131344 CrossRef.
- K. Setiyawan, B. Sugiantoro and N. R. Prabowo, Mater. Sci. Forum, 2021, 1029, 65–72 Search PubMed.
- T. Hiraoka, T. Yamada, K. Hata, D. N. Futaba, H. Kurachi, S. Uemura, M. Yumura and S. Iijima, J. Am. Chem. Soc., 2006, 128, 13338–13339 CrossRef.
- Y. Zhang, J. Wu, S. Zhang, N. Shang, X. Zhao, S. M. Alshehri, T. Ahamad, Y. Yamauchi, X. Xu and Y. Bando, Nano Energy, 2022, 97, 107146 CrossRef.
- R. Shoukat and M. I. Khan, Microsyst. Technol., 2021, 1–10 Search PubMed.
- S. Rathinavel, K. Priyadharshini and D. Panda, Mater. Sci. Eng., B, 2021, 268, 115095 Search PubMed.
- M. Kamel, A. Morsali, H. Raissi and K. Mohammadifard, Chem. Rev. Lett., 2020, 3, 23–37 Search PubMed.
- R. A. Ismail, M. H. Mohsin, A. K. Ali, K. I. Hassoon and S. Erten-Ela, Phys. E, 2020, 119, 113997 CrossRef.
- A. Aabir, M. Y. Naz and S. Shukrullah, in Emerging Developments and Applications of Low Temperature Plasma, IGI Global, 2022, pp. 85–102 Search PubMed.
- L. Hernandez-Tabares, J. G. Darias-Gonzalez, F. J. Chao-Mujica, L. M. Ledo-Pereda, M. Antuch, E. Carrillo-Barroso, J. E. Chong-Quero, E. Reguera and L. F. Desdin-Garcia, J. Nanomater., 2021, 2021, 6550809 Search PubMed.
- Y. Liu, J. He, N. Zhang, W. Zhang, Y. Zhou and K. Huang, J. Mater. Sci., 2021, 56, 12559–12583 CrossRef.
- M. Saeed, Y. Alshammari, S. A. Majeed and E. Al-Nasrallah, Molecules, 2020, 25, 3856 CrossRef.
- K. Yang, M. Luo, D. Zhang, C. Liu, Z. Li, L. Wang, W. Chen and X. Zhou, Chem. Eng. J., 2022, 427, 132002 CrossRef.
- S. Huang, X. Du, X. Li, M. Ma and L. Xiong, Adv. Funct. Mater., 2021, 31, 2104531 CrossRef.
- C. Querne, T. Vignal, M. Pinault, P. Banet, M. Mayne-L'Hermite and P.-H. Aubert, J. Power Sources, 2023, 553, 232258 CrossRef.
- G. Sun, H. Ren, Z. Shi, L. Zhang, Z. Wang, K. Zhan, Y. Yan, J. Yang and B. Zhao, J. Colloid Interface Sci., 2021, 588, 847–856 CrossRef PubMed.
- A. Abdollahi, A. Abnavi, F. Ghasemi, S. Ghasemi, Z. Sanaee and S. Mohajerzadeh, Electrochim. Acta, 2021, 390, 138826 CrossRef.
- B. Dousti, Y. I. Choi, S. F. Cogan and G. S. Lee, ACS Appl. Mater. Interfaces, 2020, 12, 50011–50023 CrossRef.
- T. De Silva, C. Damery, R. Alkhaldi, R. Karunanithy, D. H. Gallaba, P. D. Patil, M. Wasala, P. Sivakumar, A. Migone and S. Talapatra, ACS Appl. Mater. Interfaces, 2021, 13, 56004–56013 CrossRef PubMed.
- L. Wang, H. Yao, F. Chi, J. Yan, H. Cheng, Y. Li, L. Jiang and L. Qu, ACS Nano, 2022, 16, 12813–12821 CrossRef.
- N. B. Mohamed, M. F. El-Kady and R. B. Kaner, Adv. Funct. Mater., 2022, 32, 2203101 CrossRef.
- Y. B. Tan and J.-M. Lee, J. Mater. Chem. A, 2013, 1, 14814–14843 RSC.
- W. Yang, M. Ni, X. Ren, Y. Tian, N. Li, Y. Su and X. Zhang, Curr. Opin. Colloid Interface Sci., 2015, 20, 416–428 CrossRef.
- R. Lakra, R. Kumar, P. K. Sahoo, D. Thatoi and A. Soam, Inorg. Chem. Commun., 2021, 133, 108929 CrossRef.
- H. Yang, S. Kannappan, A. S. Pandian, J.-H. Jang, Y. S. Lee and W. Lu, Nanotechnology, 2017, 28, 445401 CrossRef PubMed.
- S. Korkmaz and İ. A. Kariper, J. Energy Storage, 2020, 27, 101038 CrossRef.
- D. C. Marcano, D. V. Kosynkin, J. M. Berlin, A. Sinitskii, Z. Sun, A. Slesarev, L. B. Alemany, W. Lu and J. M. Tour, ACS Nano, 2010, 4, 4806–4814 CrossRef PubMed.
- A. M. Dimiev and J. M. Tour, ACS Nano, 2014, 8, 3060–3068 CrossRef.
- W. Yu, L. Sisi, Y. Haiyan and L. Jie, RSC Adv., 2020, 10, 15328–15345 RSC.
- J. Song, X. Wang and C.-T. Chang, J. Nanomater., 2014, 2014, 276143 CrossRef.
- S. C. Ray, Applications of Graphene and Graphene-Oxide Based Nanomaterials, 2015, vol. 6, pp. 39–55 Search PubMed.
- R. Aslani and H. Namazi, Int. J. Pharm., 2023, 636, 122804 CrossRef PubMed.
- K. Ponnarasi, P. Elangovan and S. Surender, Results Chem., 2024, 7, 101355 CrossRef.
- A. Subagio, A. Darari, I. S. Hakim, P. Priyono, P. Pardoyo and A. Subhan, 2018.
- M. S. Vidhi, A. K. Singh and O. Thakur, Ionics, 2024, 1–13 Search PubMed.
- J. Sudarto, A. Subagio and R. Yudianti, Makara J. Sci., 2017, 21, 1 CrossRef.
- C. H. Kim and B.-H. Kim, J. Power Sources, 2015, 274, 512–520 CrossRef.
- Y. Ouyang, R. Huang, X. Xia, H. Ye, X. Jiao, L. Wang, W. Lei and Q. Hao, Chem. Eng. J., 2019, 355, 416–427 CrossRef.
- C. Guan, J. Liu, Y. Wang, L. Mao, Z. Fan, Z. Shen, H. Zhang and J. Wang, ACS Nano, 2015, 9, 5198–5207 CrossRef CAS.
- H. Chen, S. Zhou and L. Wu, ACS Appl. Mater. Interfaces, 2014, 6, 8621–8630 CrossRef.
- X. Xia, J. Tu, Y. Mai, R. Chen, X. Wang, C. Gu and X. Zhao, Chem.–Eur. J., 2011, 17, 10898–10905 CrossRef PubMed.
- P. Cao, L. Wang, Y. Xu, Y. Fu and X. Ma, Electrochim. Acta, 2015, 157, 359–368 CrossRef.
- K. Xu, R. Zou, W. Li, Q. Liu, T. Wang, J. Yang, Z. Chen and J. Hu, New J. Chem., 2013, 37, 4031–4036 RSC.
- F. Liu, X. Wang, J. Hao, S. Han, J. Lian and Q. Jiang, Sci. Rep., 2017, 7, 17709 CrossRef.
- L. Wang, X. Li, T. Guo, X. Yan and B. K. Tay, Int. J. Hydrogen Energy, 2014, 39, 7876–7884 CrossRef.
- L. Sui, S. Tang, Y. Chen, Z. Dai, H. Huangfu, Z. Zhu, X. Qin, Y. Deng and G. M. Haarberg, Electrochim. Acta, 2015, 182, 1159–1165 CrossRef.
- L. Chen, D. Liu and P. Yang, RSC Adv., 2019, 9, 12793–12800 RSC.
- L. Yang, S. Cheng, Y. Ding, X. Zhu, Z. L. Wang and M. Liu, Nano Lett., 2012, 12, 321–325 CrossRef PubMed.
- Q. Liao, N. Li, S. Jin, G. Yang and C. Wang, ACS Nano, 2015, 9, 5310–5317 CrossRef.
- J. Li, Y. Wang, W. Xu, Y. Wang, B. Zhang, S. Luo, X. Zhou, C. Zhang, X. Gu and C. Hu, Nano Energy, 2019, 57, 379–387 CrossRef.
- T. Saravanan, M. Shanmugam, P. Anandan, M. Azhagurajan, K. Pazhanivel, M. Arivanandhan, Y. Hayakawa and R. Jayavel, Dalton Trans., 2015, 44, 9901–9908 RSC.
- D. Deng, N. Chen, Y. Li, X. Xing, X. Liu, X. Xiao and Y. Wang, Phys. E, 2017, 86, 284–291 CrossRef.
- Y. Luo, T. Yang, Q. Zhao and M. Zhang, J. Alloys Compd., 2017, 729, 64–70 CrossRef.
- L. Kong, C. Zhang, J. Wang, W. Qiao, L. Ling and D. Long, ACS Nano, 2015, 9, 11200–11208 CrossRef.
- L. Ma, X. Shen, Z. Ji, S. Wang, H. Zhou and G. Zhu, Electrochim. Acta, 2014, 146, 525–532 CrossRef.
- A. S. Justin, P. Vickraman and B. J. Reddy, Curr. Appl. Phys., 2019, 19, 295–302 CrossRef.
- J. He, C. Guo, S. Zhou, Y. Zhao, Q. Wang, S. Yang, J. Yang and Q. Wang, Inorg. Chem. Front., 2019, 6, 226–232 RSC.
- R. Khan, M. Imran, A. M. Afzal, M. W. Iqbal, S. Mumtaz, S. A. Munnaf, M. S. Islam, R. Sajad, N. Muzaffar and M. Yaqoob, ECS J. Solid State Sci. Technol., 2023, 12, 101005 CrossRef.
- N. James, S. Simon and P. Sreeja, Mater. Today: Proc., 2023 Search PubMed , in presss.
- J. R. Xavier, S. Vinodhini and S. S. Chandraraj, J. Cluster Sci., 2023, 34, 1805–1817 CrossRef.
- Y. Tang, T. Chen, S. Yu, Y. Qiao, S. Mu, J. Hu and F. Gao, J. Mater. Chem. A, 2015, 3, 12913–12919 RSC.
- Y. Liu, Z. Li, L. Yao, S. Chen, P. Zhang and L. Deng, Chem. Eng. J., 2019, 366, 550–559 CrossRef CAS.
- J. Meng, Y. Wang, X. Xie and H. Quan, Ionics, 2019, 25, 4925–4933 CrossRef CAS.
- M. Yao, X. Ji, X. Ou, P. Wu and S. Cheng, J. Power Sources, 2022, 543, 231829 CrossRef CAS.
- W. Lu, M. Yang, X. Jiang, Y. Yu, X. Liu and Y. Xing, Chem. Eng. J., 2020, 382, 122943 CrossRef CAS.
- Y. Lu, Z. Zhang, X. Liu, W. Wang, T. Peng, P. Guo, H. Sun, H. Yan and Y. Luo, CrystEngComm, 2016, 18, 7696–7706 RSC.
- S. Hui, T. Ju, X. Lin, Y. Li, Y. Wang and Z. Ying, Dalton Trans., 2020, 49, 12345–12353 RSC.
- Y. Ren, X. Zhou and Z. Liu, J. Mol. Eng. Mater., 2019, 7, 1950004 CrossRef.
- S. Sathish, T. A. Kumaravelu, C.-J. Yang, R. R. Jayapalan, R. Nirmala, C.-L. Dong, B.-H. Lin and R. Navamathavan, J. Alloys Compd., 2024, 985, 174076 CrossRef CAS.
- X. Wang, W. Li, Y. Xue, J. Liu, Y. Yue, C. Zhou, K. Zhu, D. Cao, Y. Chen and G. Wang, J. Energy Storage, 2022, 50, 104220 CrossRef.
- S. Liu, D. Gao, J. Li, K. San Hui, Y. Yin, K. N. Hui and S. C. Jun, J. Mater. Chem. A, 2019, 7, 26618–26630 RSC.
- J. Ning, T. Zhang, Y. He, C. Jia, P. Saha and Q. Cheng, Materials, 2017, 10, 608 CrossRef PubMed.
- K. Jin, M. Zhou, H. Zhao, S. Zhai, F. Ge, Y. Zhao and Z. Cai, Electrochim. Acta, 2019, 295, 668–676 CrossRef.
- W. Zhou, J. Miao, X. Yan, Y. Li, Y. Zhu, W. Zhang, M. Zhang, W. Zhu, M. S. Javed and J. Pan, J. Electroanal. Chem., 2021, 897, 115610 CrossRef.
- Y. Lu, X. Liu, W. Wang, J. Cheng, H. Yan, C. Tang, J.-K. Kim and Y. Luo, Sci. Rep., 2015, 5, 16584 CrossRef PubMed.
- Y. J. Yang, Fullerenes, Nanotubes Carbon Nanostruct., 2017, 25, 497–503 CrossRef.
- C. Wang, S. Wei, Q. Zhu, X. Yang, B. Zhou, Z. Duan, Z. Xie and Y. Hu, J. Energy Storage, 2024, 91, 112021 CrossRef.
- S. Zhai, K. Jin, M. Zhou, Z. Fan, H. Zhao, Y. Zhao, X. Li and Z. Cai, Colloids Surf., A, 2019, 575, 75–83 CrossRef.
- I. Sarasamreen, S. Shajahan, S. A. Kumar, M. A. Haija, R. Ramesh and P. Anbarasan, Diamond Relat. Mater., 2023, 140, 110453 CrossRef.
- Z. Tian, H. Dou, B. Zhang, W. Fan and X. Wang, Electrochim. Acta, 2017, 237, 109–118 CrossRef.
- S. I. El-Hout, S. G. Mohamed, A. Gaber, S. Y. Attia, A. Shawky and S. M. El-Sheikh, J. Energy Storage, 2021, 34, 102001 CrossRef.
- Y. Quan, G. Wang, L. Lu, Z. Wang, H. Xu, S. Liu and D. Wang, Electrochim. Acta, 2020, 353, 136606 CrossRef.
- Y. Quan, M. Zhang, G. Wang, L. Lu, Z. Wang, H. Xu, S. Liu and Q. Min, New J. Chem., 2019, 43, 10906–10914 RSC.
- Y. Zhang, X. Cao, G. Zhuang and X. Chen, J. Electroanal. Chem., 2023, 928, 117033 CrossRef.
- X. He, X. Mao, C. Zhang, W. Yang, Y. Zhou, Y. Yang and J. Xu, J. Mater. Sci.: Mater. Electron., 2020, 31, 2145–2152 CrossRef.
- Z. Shuangsheng, Y. Zongrong, Y. Jiajia and F. Chuan, CIESC J., 2016, 67, 4892 Search PubMed.
- M. N. Khan and C. Jeong, J. Alloys Compd., 2024, 176007 CrossRef.
- Q. V. Thi, S. A. Patil, P. K. Katkar, I. Rabani, A. S. Patil, J. Ryu, G. Kolekar, N. T. Tung and D. Sohn, Synth. Met., 2022, 290, 117155 CrossRef.
- W. Feng, C. Liu, Z. Liu and H. Pang, Chin. Chem. Lett., 2024, 109552 CrossRef.
- M. K. Singh, A. K. Gupta, S. Krishnan, N. Guha, S. Marimuthu and D. K. Rai, J. Energy Storage, 2021, 43, 103301 CrossRef.
- P. Wen, P. Gong, J. Sun, J. Wang and S. Yang, J. Mater. Chem. A, 2015, 3, 13874–13883 RSC.
- S. Sun, Y. Wang, L. Chen, M. Chu, Y. Dong, D. Liu, P. Liu, D. Qu, J. Duan and X. Li, Colloids Surf., A, 2022, 643, 128802 CrossRef CAS.
- M. S. Rahmanifar, H. Hesari, A. Noori, M. Y. Masoomi, A. Morsali and M. F. Mousavi, Electrochim. Acta, 2018, 275, 76–86 CrossRef CAS.
- Y. Zhang, Q. Xie, R. Shao, J. Ding, J. Liu, W. Xu and Y. Wang, J. Energy Storage, 2024, 86, 111156 CrossRef.
- D. Mohanadas, M. A. A. M. Abdah, N. H. N. Azman, J. Abdullah and Y. Sulaiman, Int. J. Hydrogen Energy, 2021, 46, 35385–35396 CrossRef CAS.
- E. Dai, J. Xu, J. Qiu, S. Liu, P. Chen and Y. Liu, Sci. Rep., 2017, 7, 12588 CrossRef PubMed.
- W. Kukulka, K. Cendrowski and E. Mijowska, Electrochim. Acta, 2019, 307, 582–594 CrossRef CAS.
- Y. Qiao, N. Li, M. Dong, P. Jia, C. Ma, T. Zhang and T. Jiao, Nanomaterials, 2022, 12, 4257 CrossRef CAS.
- S. Krishnan, A. K. Gupta, M. K. Singh, N. Guha and D. K. Rai, Chem. Eng. J., 2022, 435, 135042 CrossRef CAS.
- A. H. Anwer, M. Z. Ansari, F. Mashkoor, S. Zhu, M. Shoeb and C. Jeong, J. Alloys Compd., 2023, 955, 170038 CrossRef CAS.
- S. Kumar, S. Sekar, A. K. Kaliamurthy and S. Lee, J. Mater. Res. Technol., 2021, 12, 2489–2501 CrossRef CAS.
- M. Yao, X. Zhao, L. Jin, F. Zhao, J. Zhang, J. Dong and Q. Zhang, Chem. Eng. J., 2017, 322, 582–589 CrossRef CAS.
- B. Ramasubramanian, C. Chinglenthoiba, X. Huiqing, N. Xiping, H. K. Hui, S. Valiyaveettil, S. Ramakrishna and V. Chellappan, Surf. Interfaces, 2022, 34, 102397 CrossRef.
- Z.-X. Li, B.-L. Yang, K.-Y. Zou, L. Kong, M.-L. Yue and H.-H. Duan, Carbon, 2019, 144, 540–548 CrossRef.
- Z. Tang, G. Zhang, H. Zhang, L. Wang, H. Shi, D. Wei and H. Duan, Energy Storage Mater., 2018, 10, 75–84 CrossRef.
- J. Pokharel, A. Gurung, A. Baniya, W. He, K. Chen, R. Pathak, B. S. Lamsal, N. Ghimire and Y. Zhou, Electrochim. Acta, 2021, 394, 139058 CrossRef.
- W. Xu, L.-H. Wang, Y. Chen and Y. Liu, Mater. Today Chem., 2022, 24, 100896 CrossRef.
- D. Huang, L. Chen, L. Yue, F. Yang, H. Guo and W. Yang, J. Alloys Compd., 2021, 867, 158764 CrossRef.
- S. Li, K. Yang, P. Ye, K. Ma, Z. Zhang and Q. Huang, Appl. Surf. Sci., 2020, 503, 144090 CrossRef.
- J. Kim, C. Young, J. Lee, Y.-U. Heo, M.-S. Park, M. S. A. Hossain, Y. Yamauchi and J. H. Kim, J. Mater. Chem. A, 2017, 5, 15065–15072 RSC.
- X. Deng, J. Li, S. Zhu, L. Ma and N. Zhao, Energy Storage Mater., 2019, 23, 491–498 CrossRef.
- T. Kshetri, D. D. Khumujam, T. I. Singh, Y. S. Lee, N. H. Kim and J. H. Lee, Chem. Eng. J., 2022, 437, 135338 CrossRef.
- D. Xu, Q. Ding, J. Li, H. Chen, Y. Pan and J. Liu, Inorg. Chem. Commun., 2020, 119, 108141 CrossRef CAS.
- Y. Pan, Y. Zhao, S. Mu, Y. Wang, C. Jiang, Q. Liu, Q. Fang, M. Xue and S. Qiu, J. Mater. Chem. A, 2017, 5, 9544–9552 RSC.
- S. Xu, R. Liu, X. Shi, Y. Ma, M. Hong, X. Chen, T. Wang, F. Li, N. Hu and Z. Yang, Electrochim. Acta, 2020, 342, 136124 CrossRef CAS.
- R. Wang, Y. Hu, Z. Pan and J. Wang, RSC Adv., 2020, 10, 34403–34412 RSC.
- S. Zhang, D. Li, S. Chen, X. Yang, X. Zhao, Q. Zhao, S. Komarneni and D. Yang, J. Mater. Chem. A, 2017, 5, 12453–12461 RSC.
- X. Wang, N. Yang, Q. Li, F. He, Y. Yang, B. Wu, J. Chu, A. Zhou and S. Xiong, J. Solid State Chem., 2019, 277, 575–586 CrossRef CAS.
- H. Yi, H. Wang, Y. Jing, T. Peng and X. Wang, J. Power Sources, 2015, 285, 281–290 CrossRef CAS.
- J. Zhao, M. Wang, S. Wang, S. Zhang, J. Wang, X. Qiao, J. Mi, M. Ge and Y. Feng, Electrochim. Acta, 2023, 464, 142920 CrossRef CAS.
- J. Gu, L. Sun, Y. Zhang, Q. Zhang, X. Li, H. Si, Y. Shi, C. Sun, Y. Gong and Y. Zhang, Chem. Eng. J., 2020, 385, 123454 CrossRef CAS.
- Z. Zhang, H. Huo, J. Gao, Z. Yu, F. Ran, L. Guo, S. Lou, T. Mu, X. Yin and Q. Wang, J. Alloys Compd., 2019, 801, 158–165 CrossRef.
- G. Duan, S. Zeng, H. Jin, S. He, H. Yang, X. Han, C. Zhang, Y. Huang and S. Jiang, Ind. Crops Prod., 2024, 222, 119616 CrossRef.
- M. G. Tadesse, A. S. Ahmmed and J. F. Lübben, J. Compos. Sci., 2024, 8, 53 CrossRef.
- C. Chen, S. Wei, Q. Zhang, H. Yang, J. Xu, L. Chen and X. Liu, J. Colloid Interface Sci., 2024, 664, 53–62 CrossRef PubMed.
- L. Sajjad, G. Ali, M. A. Mansoor and M. F. Khan, J. Energy Storage, 2023, 72, 108351 CrossRef.
- D. S. Patil, S. Pawar, R. Devan, S. Mali, M. Gang, Y. Ma, C. Hong, J. Kim and P. Patil, J. Electroanal. Chem., 2014, 724, 21–28 CrossRef.
- A. T. Prasannakumar, R. Rohith, V. Manju, R. R. Mohan and S. J. Varma, J. Energy Storage, 2024, 76, 109732 CrossRef.
- X. Liang, L. Zhao, Q. Wang, Y. Ma and D. Zhang, Nanoscale, 2018, 10, 22329–22334 RSC.
- J. Tian, N. Cui, P. Chen, K. Guo and X. Chen, J. Mater. Chem. A, 2021, 9, 20635–20644 RSC.
- S.-Y. Lee, J.-I. Kim and S.-J. Park, Energy, 2014, 78, 298–303 CrossRef.
- A. Olad and H. Gharekhani, Prog. Org. Coat., 2015, 81, 19–26 CrossRef.
- D. Salinas-Torres, J. M. Sieben, D. Lozano-Castello, D. Cazorla-Amorós and E. Morallón, Electrochim. Acta, 2013, 89, 326–333 CrossRef.
- Y. Li and C. Chen, J. Mater. Sci., 2017, 52, 12348–12357 CrossRef.
- W. Du, X. Wang, X. Sun, J. Zhan, H. Zhang and X. Zhao, J. Electroanal. Chem., 2018, 827, 213–220 CrossRef.
- H. Wang and Y. Xie, J. Energy Storage, 2022, 52, 105042 CrossRef.
- E. Shanmugasundaram, V. Ganesan, V. Narayanan, K. Vellaisamy, N. i. Saleh and S. Thambusamy, Nanoscale Adv., 2024, 6, 1765–1780 RSC.
- L. S. Ghadimi, N. Arsalani, A. G. Tabrizi, A. Mohammadi and I. Ahadzadeh, Electrochim. Acta, 2018, 282, 116–127 CrossRef.
- A. Olad and H. Gharekhani, J. Polym. Res., 2016, 23, 1–11 CrossRef.
- L. Li, E. Liu, J. Li, Y. Yang, H. Shen, Z. Huang, X. Xiang and W. Li, J. Power Sources, 2010, 195, 1516–1521 CrossRef.
- Q. Tan, Y. Xu, J. Yang, L. Qiu, Y. Chen and X. Chen, Electrochim. Acta, 2013, 88, 526–529 CrossRef.
- M. Zhong, Y. Song, Y. Li, C. Ma, X. Zhai, J. Shi, Q. Guo and L. Liu, J. Power Sources, 2012, 217, 6–12 CrossRef.
- V. K. Pandey, S. Verma and B. Verma, Chem. Phys. Lett., 2022, 802, 139780 CrossRef.
- M. Selvakumar, Int. J. Hydrogen Energy, 2018, 43, 4067–4080 CrossRef.
- A. Chonat and S. Palatty, Energy Fuels, 2020, 34, 10148–10159 CrossRef.
- H. Wang, J. Xu and Y. Xie, Appl. Surf. Sci., 2023, 637, 157980 CrossRef.
- X. Yang, X. Wang, B. Lu, B. Huang, Y. Xia and G. Lin, Appl. Surf. Sci., 2023, 639, 158191 CrossRef.
- G. Singh, Y. Kumar and S. Husain, Energy Technol., 2023, 11, 2200931 CrossRef.
- Z. Li, S. Bai, K. Chen, Y. Liu, Y. Zhang and S. Liu, Chem. Eng. J., 2024, 481, 148486 CrossRef.
- A. K. Ghasemi, M. Ghorbani, M. S. Lashkenari and N. Nasiri, Electrochim. Acta, 2023, 439, 141685 CrossRef.
- Z. Abbas, M. R. A. Karim, W. Shehzad, N. A. Shama, J. Kumar, S. Karakuş, R. A. Soomro and A. Nafady, Electrochim. Acta, 2023, 471, 143350 CrossRef.
- M. V. Lebedeva and E. N. Gribov, Solid State Ionics, 2023, 401, 116353 CrossRef.
- H. Mohamed, M. Abo-Aly, S. A. Wahab, M. Mousa and A. A. Ali, J. Energy Storage, 2023, 70, 108056 CrossRef.
- X. Tao, S. Ye, K. Zhu, L. Dou, P. Cui, J. Ma, C. Zhao, X. Wei, L. Guo and A. Hojjati-Najafabadi, ACS Appl. Energy Mater., 2023, 6, 8177–8188 CrossRef.
- B. Zhou, H. Li, Z. Li, S. Ji, Y. Li, J. Yang and C. Yang, J. Dispersion Sci. Technol., 2023, 44, 1516–1525 CrossRef.
- Y. Gogotsi and P. Simon, Science, 2011, 334, 917–918 CrossRef PubMed.
- K. Nasrin, M. Arunkumar, N. K. Kumar, V. Sudharshan, S. Rajasekar, D. Mukhilan, M. Arshad and M. Sathish, Chem. Eng. J., 2023, 474, 145505 CrossRef.
|
This journal is © The Royal Society of Chemistry 2024 |
Click here to see how this site uses Cookies. View our privacy policy here.