DOI:
10.1039/D3SC05022J
(Review Article)
Chem. Sci., 2024,
15, 1953-1965
Toward three-dimensionally ordered nanoporous graphene materials: template synthesis, structure, and applications
Received
25th September 2023
, Accepted 23rd December 2023
First published on 26th December 2023
Abstract
Precise template synthesis will realize three-dimensionally ordered nanoporous graphenes (NPGs) with a spatially controlled seamless graphene structure and fewer edges. These structural features result in superelastic nature, high electrochemical stability, high electrical conductivity, and fast diffusion of gases and ions at the same time. Such innovative 3D graphene materials are conducive to solving energy-related issues for a better future. To further improve the attractive properties of NPGs, we review the template synthesis and its mechanism by chemical vapor deposition of hydrocarbons, analysis of the nanoporous graphene structure, and applications in electrochemical and mechanical devices.
1. Introduction
Carbon materials have industrial applications owing to their excellent features such as electrical conductivity, chemical and thermal stability, light weight, and low cost of preparation.1 Nevertheless, the actual structures of carbon materials have not been well documented until recently, except for their chemical composition. Recent developments in analytical technologies for probing the structure of carbon materials, such as transmission electron microscopy,2–4 Raman spectroscopy,5–7 and high-sensitivity temperature-programmed desorption methods,8,9 have enabled understanding of the actual three-dimensional (3D) structure of carbon materials at the molecular and atomic levels.
With the developed tools for nanoscale analysis, the synthesis and understanding of nanostructured carbon materials have further expanded their fields and applications. Various synthesis methods have been investigated with the aid of advanced nanostructural analysis for nanostructured carbon materials, including arc discharge,10 template carbonization,2,11 conversion of graphene oxides12,13 to their reduced analogs,13,14 fine organic synthesis,15,16 topochemical pyrolysis,17–19 and chemical vapor deposition (CVD).20–24 Consequently, many advanced carbon materials, including carbon fibers, carbon nanotubes (CNTs), graphenes, structural graphite, and carbon foams have been developed with improved physicochemical properties, and they are growing at a compound average growth rate (CAGR) of ∼6% with an annual global market of 3 billion USD in 2015.25 They are extensively used as adsorbents,26 catalysts,27–33 catalyst supports,34 conductive additives,35–37 and anode materials38 in batteries, supercapacitors,39,40 polymer-electrolyte fuel cells (PEFCs),41 and photothermal conversion.42
In this context, the chemical science of two-dimensional (2D) graphene and its zero-dimensional (0D) and one-dimensional (1D) analogs has been extensively studied in recent decades. Graphene,43 a 2D-carbon material, was originally prepared by exfoliation, and its synthesis, analysis, and applications have been extensively investigated.44–48 Single-plate graphene materials have high electrical conductivity and high thermal/chemical stability; therefore, they are suitable for practical applications in energy-related devices. A class of 1D-graphene, carbon nanotubes49,50 and cylindrical analogs,51 has also been investigated for electrochemical and catalysis applications owing to their high electrical conductivity.52
A challenging aspect is the synthesis of the corresponding 3D graphene materials53–55 from a 2D scaffold.13 Reducing the dimension of 2D graphene can be used to develop 3D graphene; the 0D analog of the fullerene family,56 a good electron acceptor,57 can be used as a building block to develop 3D-analogs.58 Catalytic carbonization has also been successfully applied to prepare 3D graphene architecture.23,29,59 However, the precise synthesis of 3D-ordered graphene materials with well-defined negatively curved 3D networks60,61 remains an emerging topic since British scientists predicted imaginary carbon frameworks with 8-membered rings in hexagons to achieve a 3D structure with low strain.53 These materials are highly symmetric and possess highly ordered nanostructures that provide various fascinating functions (vide infra). For example, material surfaces for the adsorption of gases should be as homogeneous as possible with respect to the structure and chemical composition62 for better and faster reactions, and imaginary 3D-ordered carbon frameworks should meet these criteria. The novel electronic nature of these frameworks makes them appealing for various applications.
In this review, we provide an overview of recent progress in the synthesis, structural characterization, and application of electrochemical and mechanical devices of 3D-ordered porous graphene material nanostructures. The remainder of this paper is organized as follows: in Section 2, we discuss typical synthetic procedures using templating carbonization on nanostructured precursor materials, such as zeolite and alumina. We then focus on the reaction mechanism of the carbon growth mechanism of CH4-CVD on alumina and the structure of the resultant 3D graphene, directed toward achieving a periodically ordered graphene nanostructure (Fig. 1). In Section 3, we provide an overview of how the 3D continuous nature of porous graphene drives its potential applications in electric double-layer capacitors, next-generation Li-ion batteries, and refrigeration devices based on mechanical force. In Section 4, we summarize this review and describe our outlook for further fundamental and application studies on 3D-ordered graphenes in the near future.
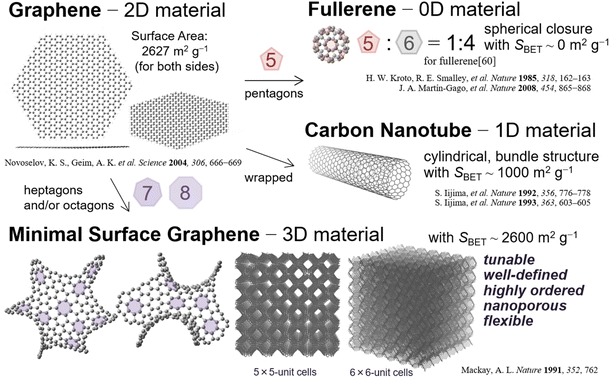 |
| Fig. 1 Schematic of structurally well-defined graphene analogs with various dimensions of materials, including 3D graphene materials.59 Gravimetric surface area of [60]fullerene is derived from the literature.70 | |
2. Synthesis and structure of templated carbons
A template method (alias dictus nanocasting)63 has been explored for the synthesis of well-defined nanostructured materials. The chemical and physical properties of the obtained nanomaterials can be tuned by using the synthesis procedure as well as the precursor materials,2 and CVD is a powerful method to precisely control nanostructures at the atomic level.64 For example, Ito and co-workers reported sophisticated macroporous (>50 nm) 3D graphene materials using CVD of benzene on a porous Ni template.23 The material maintains the electronic nature of pristine 2D graphene, and its analogs with structural defects, including substitutional defects and adatoms of nitrogen and sulfur, work efficiently as catalysts.28,29,65 owing to their high electrical conductivity. Recently, the effects of structural topology66,67 and mechanical68 and electronic properties69 have also been well studied. Thus, these materials are excellent candidates for developing ideal 3D graphene materials. However, we recognized that a 3D single-layered graphene architecture with a large pore size and high surface area (>2000 m2 g−1) sometimes collapses and reduces the structural regularity of the grown carbons during the template removal process using aqueous acids, as previously reported,22 leading to stacked carbon layers. Hereafter, we focus on porous graphene analogs with a narrow pore distribution (<20 nm).
2.1 Zeolite-templated carbon (ZTC)
Zeolites are a class of inorganic materials composed of SiO2 and Al2O3 (aluminosilicates) with alkali metals as countercations. They exhibit high surface areas with highly ordered micropores and are widely used in catalysts.71–76 The catalytic ability and structural regularity of zeolites77,78 are enticing features for their use as templates for synthesizing nanostructured carbon materials. In 2000, Kyotani and co-workers reported the synthesis of zeolite-templated carbon (ZTC) using Y zeolite (faujasite, FAU) as the template material.11 The studies used Y zeolite with a porous diamond-like framework of spherical cavities (supercage, ∼1.3 nm in diameter):79 ZTC was prepared by transcription of the structural information of zeolites. A composite of furfuryl alcohol and Y zeolite powder was heated, followed by treatment with propylene at 600–800 °C for CVD to achieve the ordered porous structure of single-walled nanographene derivatives.79 Thermal annealing at 900 °C for 3 h ensures a more robust 3D structure.79,80 After CVD, the resulting material was washed with HF and HCl solutions to obtain the ZTCs. This procedure allowed the ZTC to retain the highly ordered microstructure of the zeolite with carbon architecture.
Ordered microporous structures provide a high surface area, large micropore volume, and fast diffusion rate of gases and electrolytes despite the narrow pore width. These features are suitable for gas physisorption81 and electric double-layer capacitor82 applications. The XRD pattern of the carbon material synthesized using Y zeolite as a template shows a peak at 2θ = 6.26°, which corresponds to the 111 diffraction of the parent Y zeolite at 2θ = 6.19°. This XRD pattern indicates that the original ordered structure of Y zeolite is maintained in the carbon material. The sharp diffraction peak indicates that the carbon material has excellent long-range order with a periodicity of 1.41 nm, which is the same as the 111 spacing of the Y zeolite. The adsorption isotherm shows a sharp increase in N2 adsorption as P/P0 increases in the low-pressure region and quickly reaches a plateau, indicating that the microporous structure exhibits a minimal number of mesopores or macropores. Both sides of the single-walled graphene-like ZTC surface can act as solid–liquid or solid–gas interfaces. In addition, edges also contribute to the surface area of ZTC, which reaches a gravimetric surface area (Sg) of >3000 m2 g−1. This feature enables efficient uptake of CH4 (ref. 26) and H2.81
Porous carbon materials with the structural 3D regularity of the original parent material can also be synthesized by carbonization using other zeolites and inorganic nanomaterials. Acidity, as confirmed by pyridine-IR spectroscopy, plays an important role in controlling the quality of ZTCs.83 N-Doped84,85 and B/N-doped85 ordered carbon materials have also been prepared using zeolite-templated methods. They demonstrate the feasibility of the templating method for preparing ordered carbonaceous materials.
2.2 Nanoporous graphene (NPG)
2.2.1 Synthesis.
The CVDs of gaseous unsaturated carbon sources with C
C triple bonds, such as acetylene, and C
C double bonds, such as propylene, have been investigated to prepare templated carbons.11,87 The resultant periodically arranged microstructured carbon cages enable efficient diffusion of gases and electrolytes.23 Typically incompatible high surface area, fast diffusion of gases and electrolytes, electrical conductivity, and structural flexibility are realized using the templated method. However, control of uniform single-layer graphene growth is difficult, with significant amounts of fragile oxygen-rich edge sites being formed to reduce the chemical and electrochemical stability of the obtained carbon materials.
By contrast, aliphatic hydrocarbons such as CH4 are relatively inert for carbon deposition reactions.88 It is expected that the efficient catalytic deposition of CH4 on an ordered 3D template can achieve ideal 3D graphene with tailored micro-porosity.
Nanosized γ-alumina is a promising template material for synthesizing nanoporous graphene (NPG) materials since it is one of the most efficient catalysts for catalytic C–H activation.89 CH4-CVD takes place on alumina nanoparticles (ANPs) with the initial associative dissociation of CH4 as the kinetic bottleneck,59 and this is followed by acid etching and annealing86,90–93 to give NPGs as minimally stacked porous graphene analogs (Fig. 2). The resultant NPGs have a high surface area (>1800 m2 g−1), high electric conductivity, elastic properties, and a sponge-like mesoporous framework.
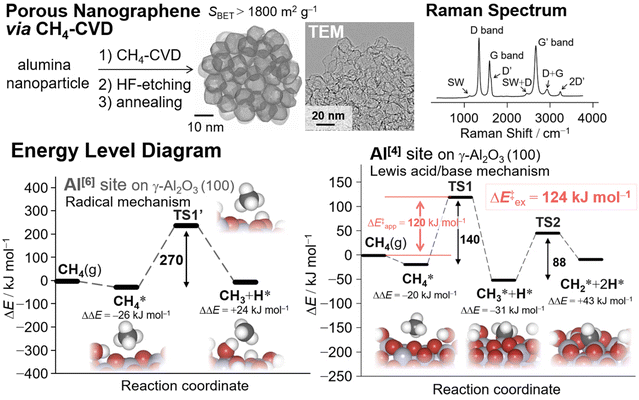 |
| Fig. 2 (Top) Schematic of the synthesis of nanoporous graphene materials via CH4-CVD59 on Al2O3 nanoparticles and their analysis86 (reprinted with permission from ref. 86. Copyright 2023 Royal Society of Chemistry). (Bottom) Energy level diagrams of the initial CH4 activation on the Al[6] site and Al[4] site of the γ-Al2O3 (100) surface during CH4-CVD for the synthesis of NPGs.59 | |
The use of inert CH4 enabled us to selectively synthesize single-layered porous graphene materials. Density functional theory (DFT) calculations coupled with experimental kinetic analysis using thermogravimetry (TG) techniques revealed that the dehydration and subsequent surface activation of γ-ANPs by CH4 are crucial in controlling surface chemistry.59 According to the DFT calculations, the original octahedral site (Al[6]) coordinated with six atoms of surrounding oxides affords a radical mechanism in the initial CH4 activation, with an activation energy (ΔE‡) of 270 kJ mol−1. Further elimination of surface oxides eventually leads to more reactive tetrahedral sites (Al[4]). The surface with oxygen vacancies provides a favorable reaction pathway for proton transfer (PT) reactions via the Lewis acid/base mechanism, with a calculated apparent ΔE‡ of 120 kJ mol−1. This theoretical value agrees well with the experimental value of 124 kJ mol−1 obtained from the Arrhenius plot using the TG technique.59 This PT step is the kinetic bottleneck for the entire reaction. Subsequent PT results in the formation of surface methylene species
. DFT calculations also demonstrated that further carbon chain growth to form heavier aliphatic hydrocarbons by adding or inserting
species is thermodynamically and kinetically feasible.94 θ-ANPs are also applicable as template materials.86,92
To improve the efficiency of the synthesis and quality of the resultant NPGs and achieve ideal 3D graphene materials, it is essential to find new templates that realize (i) efficient catalytic activation of CH4 at lower reaction temperatures, (ii) better structural regularity of the resultant NPGs, and (iii) easy removal of the templates after the CVD process. CH4-CVD on nanostructured oxides, including γ-ANPs and zeolites, requires high temperatures above 800 °C for a sufficient rate of carbonization.59 Such a high temperature can easily damage the structural order over time.101Fig. 3a shows the dependence of CH4 partial pressure on the rate of CH4-CVD carbonization on γ-ANPs. We found that the rate of carbonization decreased when the reaction reached the single-layer carbonization on γ-ANPs. Faster carbonization through better surface catalysis, as shown in Fig. 3b-1, is required to lower the reaction temperature and improve selectivity. Screening of catalysts using thermogravimetric analysis (TGA) is a promising approach.
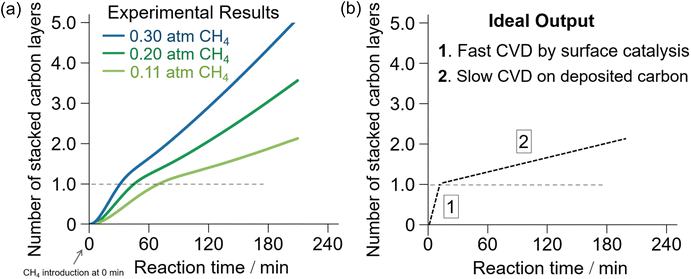 |
| Fig. 3 (a) TGA of CH4-CVD on γ-Al2O3 nanoparticles at 900 °C with different partial pressures of CH4.59 (b) Expected ideal output of the TGA of CH4-CVD with enhanced surface catalysis for selective synthesis of single-layered porous graphene materials with improved integrity of “graphene nature”. | |
The economical preparation of carbon materials is also important for practical applications.102 Template materials investigated to date, such as nanostructured silica,103,104 γ-ANPs,59,86 θ-ANPs,92 and zeolite,11 require the use of hazardous HF aqueous solutions for their removal after CVD, which makes the synthetic process tedious. For practical industrial applications, HF should be replaced with the less hazardous HCl. Catalytically active MgO105–107 is a promising template material24,108,109 that does not require HF during template etching. Investigating the dissolution of ANPs and zeolites in benign and safe ways is crucial for the practical application of NPGs.
2.2.2 Structure.
NPGs exhibit high surface area and very few edge sites. Table 1 summarizes the physicochemical properties of representative carbon materials. Another important feature of meso-structured elastic carbons is their highly flexible carbon framework. The bulk modulus of NPG is less than 1 GPa, and this value is a magnitude smaller than those of typical “soft” materials such as zeolite (14 GPa) and the relatively soft class of metal–organic-frameworks (7.7 GPa).99
Table 1 Summary of the physicochemical properties of materials
Materials |
S
BET/m2 g−1 |
d
p,BJH/nm |
V
p/mL g−1 |
σ/S cm−1 |
N
edge
/mmol g−1 |
K
|
Total |
Microa |
Mesob |
Obtained from the DA plot.
V
meso = Vtotal − Vmicro.
Concentration of edge sites (Nedge) calculated by using TPD.
Bulk moduli (K), or otherwise, the calculated Young's modulus in parentheses.
At an applied pressure of 90 MPa.
Ideal values are shown in parentheses.
|
NPC (this work) |
2300 |
9.2 |
5.30 |
0.85 |
4.5 |
0.52e (powder) |
3.1 |
0.9 GPa |
NPG (this work) |
1910 |
9.0 |
4.10 |
0.70 |
3.4 |
0.97e (powd.)92–18 (sheet)95 |
0.16 |
0.3 GPa |
Macroporous graphene23 |
∼1260 (ref. 42) |
25 (ref. 69)–200 (ref. 23) |
— |
— |
— |
∼106 (ref. 23 and 67) |
— |
<0.1 GPa (ref. 68) |
Graphene |
(2627)f |
— |
— |
— |
— |
(106) |
— |
1.0–2.3 TPa (ref. 96–98) |
SWCNTs |
1300 (ref. 95) |
— |
3.0 (ref. 95) |
— |
— |
6.8 (ref. 95) |
0.48 (ref. 95) |
(1.2 GPa)99 |
MSC30 |
2841 |
2.3 |
1.6 |
0.92 |
0.7 |
1.29e |
2.3 (ref. 100) |
1.57 GPa |
The surface area of NPGs mainly comprises the basal plane of single-layer graphene extended over the 3D nanospace instead of the edge sites.92 The surface area of NPGs obtained by using a γ-ANP template reached 1800–2300 m2 g−1, and this lies between that of single-layered graphene (2627 m2 g−1) and stacked bilayer graphene (1314 m2 g−1).59 Temperature-programmed desorption (TPD)8 of NPGs was investigated, and it showed much fewer edge sites on NPGs when compared with typical activated carbons and carbon black.86,92 The electrochemical stability of NPGs also confirms that the above-mentioned structure has fewer terminal edge sites.92
The Raman spectra of NPGs indicate that they consist mostly of hexagonal aromatic rings, but some pentagons and heptagons exist, which introduce curvature to the NPGs in their grain boundaries.86 An intense G band at approximately 1587 cm−1, as in typical graphene110,111 (Fig. 2), coupled with a high specific surface area (SBET ∼2000 m2 g−1) and a weak 002 diffraction in the XRD pattern indicate the presence of a single-layered graphene structure in NPGs.86 The red-shifted G′ band at ∼2670 cm−1, compared with that of typical graphite,110,111 corroborates the presence of a single-walled graphene structure.44,110 The red-shifted G′ band may also reflect the value of Young's moduli96 by the introduction of curvature. In general, a relatively sharp D band (Fig. 2) in the Raman spectra can be mainly attributed to edges,6,7 but TPD analysis indicates a very low occurrence of edges.86,92 Therefore, the prominent D band of the NPGs is mainly attributed to in-plane disorder instead of edges.
The type of disorder can be qualitatively analyzed using the intensity ratio between the D and D′ bands, ID/ID′.112 The ID/ID′ of NPGs is ca. 5. This indicates that these NPGs have both vacancies and grain boundaries since the ID/ID′ values lie between those of graphene dominantly with vacancies (∼7) and grain boundaries (∼3.5).112 The shoulder peak at ∼1150 cm−1 in the Raman spectra proves the existence of Stone–Wales (SW) defects,5,112–115 while the small peak at ∼2460 cm−1 can be attributed to the SW + D band.
The mean distance between the defects R can be related to the intensity ratio of the D and G bands, ID/IG(R):116
| 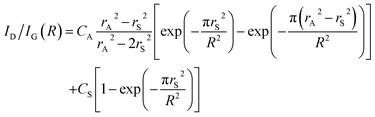 | (1) |
where
rS = 1.00 nm is the mean radius of the structurally disordered region and
rA = 3.00 nm is the mean radius of the activated region, where the graphitic structure is mostly conserved. However, its symmetry-breaking structure enhances the D band.
CA = 4.2 and
CS = 0.87 are parameters that describe the strength of the influences of the structurally disordered and activated regions on the intensity of the D band, respectively.
116 Based on this equation, the mean density of vacancy defects per hexagon of the graphene framework was 10
−2 for nanoporous carbons (NPCs) obtained by CH
4-CVD and subsequent acid etching, whereas annealing of NPCs reduces the defect density to 10
−3 to afford the corresponding NPGs without any loss of porosity.
86
The small peaks at ∼1150 cm−1 in the Raman spectra originate from heptagons and pentagons5,113 in the grain boundaries117 and surface defects118,119 within continuous graphene-based materials59,92 rather than edge sites. The domain boundary often contains 5- and 7-membered rings,3–5,117–119 which result in the curved structure shown in Fig. 4.
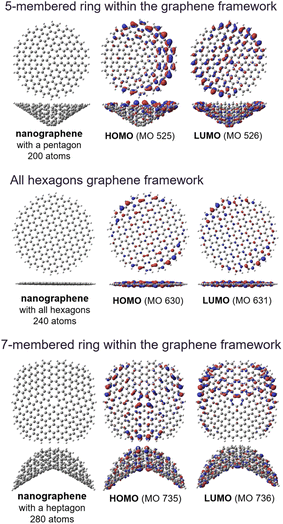 |
| Fig. 4 Optimized geometries of nanographene models, and the corresponding Kohn–Sham highest molecular orbital (HOMO) and lowest molecular orbital (LUMO) obtained using the DFT method. | |
Fig. 4 shows the geometries and molecular orbitals of nanographene models having a pentagon and heptagon as a structural defect. Both the HOMOs and LUMOs of the structural models were relatively localized around the edges of the curved nanographene structures, and the excellent chemical and electrochemical stability of the NPGs can be explained by the reduced presence of reactive edges, as confirmed by TPD analysis.92,100
3. Application of ordered porous graphene materials
3.1 Electric double-layer capacitors (EDLCs)
The most common application of highly ordered nanoporous carbon materials is electric double-layer capacitors (EDLCs):1,39,100 EDLCs are extensively used in electric vehicles and other industrial fields. There are two important prerequisites for achieving efficient EDLCs. First, a high surface area of carbon materials is required to achieve EDLCs with high energy density, as Sg and Sv are directly related to the gravimetric and volumetric capacities, respectively.120 This can be realized by high porosity and small pore size because EDLCs can be charged in principle through the physisorption of electrolyte ions onto the nanopore surfaces of a carbon electrode.120 Importantly, this often causes a lower efficiency of mass transportation within nanostructured materials because the ions have to be transferred from the outside into the porous architecture of the electrode materials before physisorption in the EDLCs can occur (Fig. 5).40
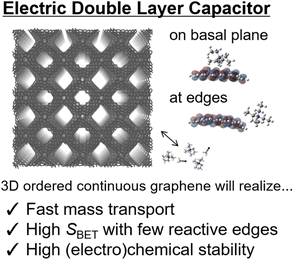 |
| Fig. 5 Schematic of electric double-layer capacitor (EDLC) application of high-quality 3D continuous graphene materials. Edge sites are electrochemically reactive,39 and therefore, NPGs with suppressed edges will be highly promising for EDLC applications. | |
3D structural regularity helps overcome these issues. For example, despite their microporous structure, ZTCs facilitate the efficient conveyance of ions under electrochemical conditions owing to their highly ordered architecture. This results in a high gravimetric capacitance of 140–190 F g−1 even at a high current of up to 20 A g−1.39,121 Ideal 3D graphene materials with such structural regularity and a continuous graphene architecture will realize highly efficient EDLCs in terms of energy efficiency and stability.
Liu and co-workers used ZTCs with different pore sizes as theoretical models to study the effect of pore geometry on capacitance.122 According to their study, the charge compensation per carbon (CCpC) determines the capacitance, and a high CCpC tends to be related to a small radius of curvature of graphene. Tang and co-workers used NPGs with different graphene-stacking layers (the specific surface area changed accordingly) to explore the influence of the specific surface area on the total capacitance and the origin of the total capacitance of 3D porous graphene.123
These results suggest that the origin of the capacitance is highly related to the specific surface area, pore structure, and surface chemistry of the carbon materials.124–129 The critical factor for obtaining carbon materials with large capacitance is the presence of fewer graphene-stacking layers in the carbon frameworks with appropriate surface modification to ensure a large electrical double-layer capacitance. The ordered and well-defined structures of ideal 3D graphene materials are particularly interesting in exploring the origin of capacitance and methods to improve them further.
3.2 Next-generation Li-ion batteries
Since their first introduction by the Sony Corporation in 1991,130 lithium-ion batteries (LIBs) have been highly important energy-storage techniques for use in mobile phones and electrical vehicles.131 For achieving the electrification of heavy-duty vehicles and aircraft and storing solar energy in smart grids, developing much better secondary batteries with much higher specific energy will be necessary.132 Air–metal batteries, including Li–O2 systems with Li-rich oxides as cathode materials, are promising candidates because of their high theoretical energy density.133 For practical application, the challenges of Li–O2 batteries are (i) handling of electronically insulating and insoluble Li2O2 as the discharge product, (ii) low discharge capacity of Li–O2 compared to theoretical capacity, and (iii) poor electrochemical cycling owing to chemical degradation.134–142 For better electrical conduction, graphene and its analogs have been frequently used as conductive additives in cathode composites.140,143–146 Ideally, 3D analogs of graphene materials would be suitable for achieving better electrical conductivity and supporting the reactants at the same time.
NPGs are promising scaffolds for novel LIBs because they have a high electron conductivity of up to 18 S cm−1 and excellent electrochemical stability owing to fewer reactive edge sites. NPGs also exhibit flexibility with an extremely low bulk modulus of <1 GPa. NPGs with large pore volumes and flexible nanopores have been applied as conductive additives in all-solid-state Li–S batteries,92 with better electrochemical performance than MSC30-based cells. The 3D continuous graphene structure in the NPGs annealed at 1800 °C under an inert atmosphere results in higher electrochemical stability and better cycling.86 In addition, the nano-confinement effect of insulating sulfur in conductive NPGs realizes durable three-phase contact (Fig. 6).92 This strategy can also be applied to other batteries with different active materials. Tailor-made 3D ordered nanopores with an arbitrary pore size and structure provide improved nano-confinement and clear-cut structure–activity relationships for better battery systems, including Li–O2 systems, when coupled with catalytic centers102,147,148 with better morphology for controlling cathode–electrolyte interaction149 and electrochemical cycling.
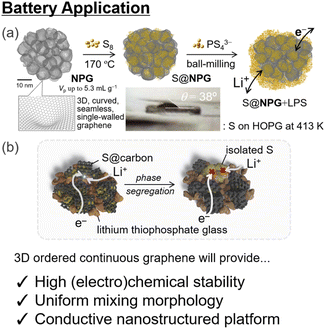 |
| Fig. 6 (a) Schematic of battery application of nanoporous graphene materials and (b) proposed degradation pathway which could be avoided by using the nano-confinement effect of NPGs92 (reprinted with permission from ref. 92. Copyright 2021 American Chemical Society). 3D-ordered continuous graphene provides a precise structure–activity relationship, which is conducive to better understanding and control of applications. | |
Powder-type NPGs have the potential problem of grain-boundary resistance and are difficult to handle. Pelletization of the template materials affords monolith-type NPGs after CH4-CVD, thereby improving the connection of the grown nanographenes.150
3.3 Refrigeration based on mechanical force
Efforts to achieve ideal 3D graphene materials would also be beneficial for high-efficiency refrigeration systems. The introduction of curvature into single-layered graphene substantially reduces Young's modulus (Y). For example, the aforementioned ZTC and NPGs have a bulk modulus that is three orders of magnitude smaller than that of pristine single-layered graphene (Table 1).
We demonstrated that the nanopores of carbon materials could be reversibly deformed upon external pressurization up to 500 MPa and that the elastic properties are supported by quasi-linear stress–strain curves with nearly no loss in energy. In the presence of water or alcohol vapor, the gas–liquid equilibrium is significantly and compulsively altered upon deformation of the nanopores (Fig. 7a). This phenomenon could be used for refrigeration based on mechanical-force-induced phase transition of adsorbate (RMPTA) systems.99 NPGs with small Y values are a promising class of materials for RMPTA combined with water and alcohols as environmentally friendly adsorbates because the coefficient of performance (COP) is proportional to the reciprocal of the Young's modulus of the material (Y−1). Slow diffusion of molecules is a general issue related to the application of porous materials,31,151 but ideal 3D graphene materials with structural regularity can achieve fast diffusion of gases and a more flexible 3D continuous graphene structure simultaneously.
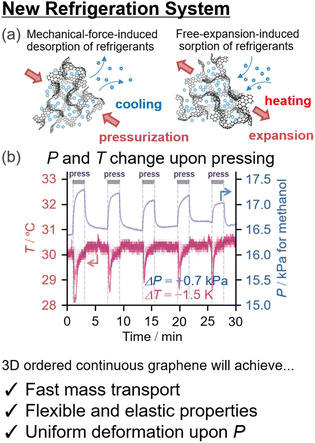 |
| Fig. 7 (a) Schematic of a new refrigeration system based on the flexible deformation of ordered nanoporous graphene materials152 upon pressurization,99 and (b) time-course of gas-phase pressure and temperature on the surface of the materials.99 | |
New ordered 3D NPG materials will realize better refrigeration systems based on the new operating principle with a uniform hierarchical structure (nm-to-mm scale) and resilience against deformation upon pressurization during the refrigeration cycle. A major impediment to efficient RMPTA systems is the uneven deformation of porous carbon materials under external pressurization. As shown in Fig. 7b, a sharp drop in temperature is observed during the compulsive liquid–gas phase transition upon pressurization, whereas nearly no heating is discernible despite the total recovery of the gas-phase pressure upon release. This irreversibility could be because of the lack of local structural robustness toward nonuniform stress. The uneven and irreversible structural changes in the nanopores are partly attributed to the structural heterogeneity of the NPGs owing to the inheritance of the irregular secondary particle structure appearing in their template materials, such as Al2O3 and zeolites. Another issue is the low thermal conductivity, and uniform nanographene growth in NPGs can also be achieved through improved CVD chemistry (Fig. 3b).
4. Conclusion and outlook
Since the proposal of Mackay crystals, several carbon materials have been reported to achieve high surface areas, structural regularity, and functionality. ZTCs are a class of carbon materials with a highly ordered 3D structure and a high specific surface area, while NPGs are extraordinary pluripotent materials with high electrochemical stability owing to fewer electrochemically active edges, a high electrical conductivity of up to 18 S cm−1 because of seamless and 3D-developed single graphene sheets, and highly flexible mechanical structure with a bulk modulus of less than 1 GPa. We investigated a general strategy for synthesizing high-quality and continuous 3D nanographene materials using CH4-CVD on nanosized oxide surfaces, where the least stacking of nanographene was achieved to ensure a high surface area with suppressed edge sites. Further investigation will expand the scope of template materials, including ordered oxides101,103 for synthesizing innovative 3D porous graphene materials in due course. However, challenges remain in achieving better homogeneity of nanographene growth and control of the hierarchical structure for better applications. As for 2D graphene growth,153,154 better control of CVD chemistry by suitable surface catalysis101,155 including well-controlled defects and dispersed metal-containing reactive sites coupled with computational chemistry156,157 will be crucial for better 3D graphene materials toward minimal surface graphene.53,158
A comprehensive understanding of the structure of NPGs has been one of the central issues in this field. Recent progress in the advanced characterization of carbon materials has accelerated our understanding and control of the nanostructure of advanced carbon materials. We addressed the qualification and quantification of surface defects in NPGs by TPD86 and Raman spectroscopy,159–161 whereas Poisson statistics are useful for quantitatively determining the distribution of graphene layers86,162–164 in continuous 3D graphenes. The complementary and convincing direct observation of defects by electron microscopy techniques3,165–167 will result in a much deeper understanding of the nanostructure. These insights into the atomic level structure of NPGs including the chemical and topological defects will be conducive to further control of high-quality NPGs. Advanced characterization, including computational168,169 and experimental (Raman spectroscopy,86 angle-resolved photoemission spectroscopy,23,170 X-ray absorption fine structure spectroscopy,171,172 electron energy loss spectroscopy,173 X-ray photoelectron spectroscopy,171 steady-state absorption spectroscopy, and neutron diffraction174) approaches (Fig. 8), will provide a more sophisticated understanding and control of novel 3D graphene materials at the atomic level.
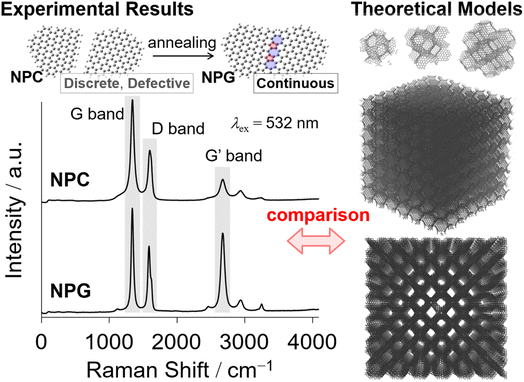 |
| Fig. 8 Schematic of the integration of experimental results and computational chemistry, and modeling for molecular understanding of the obtained ordered porous 3D graphene materials. Various spectroscopic techniques are of interest for elucidating the structure at the atomic level in a self-consistent manner, including Raman spectroscopy,86 angle-resolved photoemission spectroscopy,23,170 X-ray absorption fine structure spectroscopy,171,172 electron energy loss spectroscopy,173 X-ray photoelectron spectroscopy,171 steady-state absorption spectroscopy, and neutron diffraction.174 | |
The successful application of NPGs and potential applications of ideal 3D graphene materials in supercapacitors, LIBs, and new refrigeration systems are also discussed in this review. Ideal 3D graphene materials will realize otherwise incompatible properties at the same time, namely, high electronic conductivity, ordered nanoporosity, flexibility, and high chemical and electrochemical stability. The realization of structural regularity of NPGs can produce these features simultaneously, and it is anticipated that such unprecedented carbon materials will have new unexplored applications, including catalyst supports in gas-phase catalysis (for example, CO2 hydrogenation175 and CH4 activation73,78) as “hydrophobic analogs” of zeolites. A systematic investigation of tuned pore sizes122,141 could also be considerably interesting for identifying otherwise hidden scientific aspects for many applications, including catalysis and batteries. Mechanical-force-induced changes in the nanopores of current NPGs (Fig. 7) occur nonuniformly because of the uneven structure of current carbon materials. Therefore, continued efforts to create ordered porous graphene materials with uniform hierarchical structures from the micro- to macro-scale will help improve the efficiency of these applications. The combination of innovative synthesis, advanced characterization, and unexplored applications will open a new route for achieving more energy-efficient systems using next-generation NPGs.
Data availability
All data associated with this study will be available upon request to the authors.
Author contributions
The manuscript was written with the contributions of all authors, and all authors approved the final version.
Conflicts of interest
There are no conflicts to declare.
Acknowledgements
This work was supported by Grants-in-Aid (19K15281), the Ebara-Hatakeyama Memorial Foundation, and the Ensemble Grant for Early Career Researchers at Tohoku University. K. Y. is grateful for financial support from the Building of Consortia for the Development of Human Resources in Science and Technology funded by MEXT and Core Research for Evolutional Science and Technology of the Japan Science and Technology Agency (JST CREST, Grant No. JPMJCR16P3). DFT calculations were performed using the TSUBAME3.0 supercomputer (Tokyo Institute of Technology) and the Research Center for Computational Science (Okazaki, Japan, project: 23-IMS-C251). We thank Prof. Dr T. Kyotani, Prof. Dr Y. Ito, Dr A. Gubarevich, Prof. Dr H. Nishihara, and Prof. Dr A. Gabe for helpful discussions.
Notes and references
- F. Béguin, V. Presser, A. Balducci and E. Frackowiak, Adv. Mater., 2014, 26, 2219–2251 CrossRef PubMed
.
- T. Kyotani, N. Sonobe and A. Tomita, Nature, 1988, 331, 331–333 CrossRef
.
- A. Hashimoto, K. Suenaga, A. Gloter, K. Urita and S. Iijima, Nature, 2004, 430, 870–873 CrossRef CAS PubMed
.
- C.-T. Toh, H. Zhang, J. Lin, A. S. Mayorov, Y.-P. Wang, C. M. Orofeo, D. B. Ferry, H. Andersen, N. Kakenov, Z. Guo, I. H. Abidi, H. Sims, K. Suenaga, S. T. Pantelides and B. Özyilmaz, Nature, 2020, 577, 199–203 CrossRef CAS PubMed
.
- T. Fujimori, K. Urita, T. Ohba, H. Kanoh and K. Kaneko, J. Am. Chem. Soc., 2010, 132, 6764–6767 CrossRef CAS PubMed
.
- C. Casiraghi, A. Hartschuh, H. Qian, S. Piscanec, C. Georgi, A. Fasoli, K. S. Novoselov, D. M. Basko and A. C. Ferrari, Nano Lett., 2009, 9, 1433–1441 CrossRef CAS PubMed
.
- A. K. Gupta, T. J. Russin, H. R. Gutiérrez and P. C. Eklund, ACS Nano, 2009, 3, 45–52 CrossRef CAS PubMed
.
- T. Ishii, S. Kashihara, Y. Hoshikawa, J.-i. Ozaki, N. Kannari, K. Takai, T. Enoki and T. Kyotani, Carbon, 2014, 80, 135–145 CrossRef CAS
.
- K. Matsumura, T. Kinumoto, T. Tsumura and M. Toyoda, Carbon Lett., 2019, 29, 109–114 CrossRef
.
- E. G. Gamaly and T. W. Ebbesen, Phys. Rev. B, 1995, 52, 2083–2089 CrossRef CAS PubMed
.
- Z. Ma, T. Kyotani and A. Tomita, Chem. Commun., 2000, 2365–2366 RSC
.
- C. Su, M. Acik, K. Takai, J. Lu, S.-j. Hao, Y. Zheng, P. Wu, Q. Bao, T. Enoki, Y. J. Chabal and K. Ping Loh, Nat. Commun., 2012, 3, 1298 CrossRef PubMed
.
- H. Jahandideh, J.-R. Macairan, A. Bahmani, M. Lapointe and N. Tufenkji, Chem. Sci., 2022, 13, 8924–8941 RSC
.
- N. Morimoto, T. Kubo and Y. Nishina, Sci. Rep., 2016, 6, 21715 CrossRef CAS PubMed
.
- G. Otero, G. Biddau, C. Sánchez-Sánchez, R. Caillard, M. F. López, C. Rogero, F. J. Palomares, N. Cabello, M. A. Basanta, J. Ortega, J. Méndez, A. M. Echavarren, R. Pérez, B. Gómez-Lor and J. A. Martín-Gago, Nature, 2008, 454, 865–868 CrossRef CAS PubMed
.
- J. Cai, P. Ruffieux, R. Jaafar, M. Bieri, T. Braun, S. Blankenburg, M. Muoth, A. P. Seitsonen, M. Saleh, X. Feng, K. Müllen and R. Fasel, Nature, 2010, 466, 470–473 CrossRef CAS PubMed
.
- S. Fa, M. Yamamoto, H. Nishihara, R. Sakamoto, K. Kamiya, Y. Nishina and T. Ogoshi, Chem. Sci., 2020, 11, 5866–5873 RSC
.
- M. Yamamoto, K. Takahashi, M. Ohwada, Y. Wu, K. Iwase, Y. Hayasaka, H. Konaka, H. Cove, D. Di Tommaso, K. Kamiya, J. Maruyama, F. Tani and H. Nishihara, Catal. Today, 2021, 364, 164–171 CrossRef CAS
.
- T. Yoshii, K. Chida, H. Nishihara and F. Tani, Chem. Commun., 2022, 58, 3578–3590 RSC
.
- M. Inagaki, S. Kobayashi, F. Kojin, N. Tanaka, T. Morishita and B. Tryba, Carbon, 2004, 42, 3153–3158 CrossRef CAS
.
- T. Morishita, T. Tsumura, M. Toyoda, J. Przepiórski, A. W. Morawski, H. Konno and M. Inagaki, Carbon, 2010, 48, 2690–2707 CrossRef CAS
.
- Z. Chen, W. Ren, L. Gao, B. Liu, S. Pei and H.-M. Cheng, Nat. Mater., 2011, 10, 424–428 CrossRef CAS PubMed
.
- Y. Ito, Y. Tanabe, H. J. Qiu, K. Sugawara, S. Heguri, N. H. Tu, K. K. Huynh, T. Fujita, T. Takahashi, K. Tanigaki and M. Chen, Angew. Chem., Int. Ed., 2014, 53, 4822–4826 CrossRef CAS PubMed
.
- M. Inagaki, M. Toyoda, Y. Soneda, S. Tsujimura and T. Morishita, Carbon, 2016, 107, 448–473 CrossRef CAS
.
- Advanced Carbon Materials Market Size, Share & Trends Analysis Report By Product (Carbon Fibers, Carbon Nanotubes), By Application (Aerospace & Defense, Energy, Automotive), By Region, And Segment Forecasts, 2016–2024, Grand View Research, Inc., 2013–2015.
- S. Choi, M. A. Alkhabbaz, Y. Wang, R. M. Othman and M. Choi, Carbon, 2019, 141, 143–153 CrossRef CAS
.
- Y. Zheng, Y. Jiao, J. Chen, J. Liu, J. Liang, A. Du, W. Zhang, Z. Zhu, S. C. Smith, M. Jaroniec, G. Q. Lu and S. Z. Qiao, J. Am. Chem. Soc., 2011, 133, 20116–20119 CrossRef CAS PubMed
.
- H. J. Qiu, Y. Ito, W. Cong, Y. Tan, P. Liu, A. Hirata, T. Fujita, Z. Tang and M. Chen, Angew. Chem., Int. Ed., 2015, 54, 14031–14035 CrossRef CAS PubMed
.
- Y. Ito, W. Cong, T. Fujita, Z. Tang and M. Chen, Angew. Chem., Int. Ed., 2015, 54, 2131–2136 CrossRef CAS PubMed
.
- Y. Ito, T. Ohto, D. Hojo, M. Wakisaka, Y. Nagata, L. Chen, K. Hu, M. Izumi, J.-i. Fujita and T. Adschiri, ACS Catal., 2018, 8, 3579–3586 CrossRef CAS
.
- H. Cui, Y. Guo and Z. Zhou, Small, 2021, 17, 2005255 CrossRef CAS PubMed
.
- A. Gabe, A. Takatsuki, M. Hiratani, M. Kaneeda, Y. Kurihara, T. Aoki, H. Mashima, T. Ishii, J.-i. Ozaki, H. Nishihara and T. Kyotani, ACS Catal., 2022, 12, 892–905 CrossRef CAS
.
- H. Itoi, S. Kameoka, C. Matsuoka, Y. Goto, M. Miyaji, H. Ohmi, S. Miyake, T. Ishii, H. Iwata and Y. Ohzawa, J. Phys. Chem. C, 2023, 127, 14723–14732 CrossRef CAS
.
- T. Yoshii, D. Umemoto, M. Yamamoto, Y. Kuwahara, H. Nishihara, K. Mori, T. Kyotani and H. Yamashita, ChemCatChem, 2020, 12, 5880–5887 CrossRef CAS
.
- T. Hakari, Y. Sato, S. Yoshimi, A. Hayashi and M. Tatsumisago, J. Electrochem. Soc., 2017, 164, A2804–A2811 CrossRef CAS
.
- B.-S. Zhao, L. Wang, S. Liu, G.-R. Li and X.-P. Gao, ACS Appl. Mater. Interfaces, 2022, 14, 1212–1221 CrossRef CAS PubMed
.
- M. Iwao, H. Miyamoto, H. Nakamura, E. Hayakawa, S. Ohsaki and S. Watano, Adv. Energy Sustainability Res., 2023, 2200206 CrossRef
.
- A. Inoo, J. Inamoto and Y. Matsuo, ACS Appl. Mater. Interfaces, 2022, 14, 56678–56684 CrossRef CAS PubMed
.
- R. Tang, M. Yamamoto, K. Nomura, E. Morallón, D. Cazorla-Amorós, H. Nishihara and T. Kyotani, J. Power Sources, 2020, 457, 228042 CrossRef CAS
.
- P. Chang, K. Matsumura, J. Zhang, J. Qi, C. Wang, T. Kinumoto, T. Tsumura, M. Chen and M. Toyoda, J. Mater. Chem. A, 2018, 6, 10331–10339 RSC
.
- R. Borup, J. Meyers, B. Pivovar, Y. S. Kim, R. Mukundan, N. Garland, D. Myers, M. Wilson, F. Garzon, D. Wood, P. Zelenay, K. More, K. Stroh, T. Zawodzinski, J. Boncella, J. E. McGrath, M. Inaba, K. Miyatake, M. Hori, K. Ota, Z. Ogumi, S. Miyata, A. Nishikata, Z. Siroma, Y. Uchimoto, K. Yasuda, K.-i. Kimijima and N. Iwashita, Chem. Rev., 2007, 107, 3904–3951 CrossRef CAS PubMed
.
- Y. Ito, Y. Tanabe, J. Han, T. Fujita, K. Tanigaki and M. Chen, Adv. Mater., 2015, 27, 4302–4307 CrossRef CAS PubMed
.
- K. S. Novoselov, A. K. Geim, S. V. Morozov, D. Jiang, Y. Zhang, S. V. Dubonos, I. V. Grigorieva and A. A. Firsov, Science, 2004, 306, 666–669 CrossRef CAS PubMed
.
- A. C. Ferrari, J. C. Meyer, V. Scardaci, C. Casiraghi, M. Lazzeri, F. Mauri, S. Piscanec, D. Jiang, K. S. Novoselov, S. Roth and A. K. Geim, Phys. Rev. Lett., 2006, 97, 187401 CrossRef CAS PubMed
.
- K. S. Kim, Y. Zhao, H. Jang, S. Y. Lee, J. M. Kim, K. S. Kim, J.-H. Ahn, P. Kim, J.-Y. Choi and B. H. Hong, Nature, 2009, 457, 706–710 CrossRef CAS PubMed
.
- H. Chen, W. Zhu and Z. Zhang, Phys. Rev. Lett., 2010, 104, 186101 CrossRef PubMed
.
- R. Munoz and C. Gomez-Aleixandre, Chem. Vap. Deposition, 2013, 19, 297–322 CrossRef CAS
.
- H. Ago, K. Kawahara, Y. Ogawa, S. Tanoue, M. A. Bissett, M. Tsuji, H. Sakaguchi, R. J. Koch, F. Fromm, T. Seyller, K. Komatsu and K. Tsukagoshi, Appl. Phys. Express, 2013, 6, 075101 CrossRef
.
- P. M. Ajayan and S. Iijima, Nature, 1992, 358, 23 CrossRef
.
- S. Iijima and T. Ichihashi, Nature, 1993, 363, 603–605 CrossRef CAS
.
- T. Kyotani, L.-f. Tsai and A. Tomita, Chem. Mater., 1996, 8, 2109–2113 CrossRef CAS
.
- T. W. Ebbesen, H. J. Lezec, H. Hiura, J. W. Bennett, H. F. Ghaemi and T. Thio, Nature, 1996, 382, 54–56 CrossRef CAS
.
- A. L. Mackay and H. Terrones, Nature, 1991, 352, 762 CrossRef
.
- Y. Ito, Y. Tanabe, K. Sugawara, M. Koshino, T. Takahashi, K. Tanigaki, H. Aoki and M. Chen, Phys. Chem. Chem. Phys., 2018, 20, 6024–6033 RSC
.
- J. W. Martin, C. de Tomas, I. Suarez-Martinez, M. Kraft and N. A. Marks, Phys. Rev. Lett., 2019, 123, 116105 CrossRef CAS PubMed
.
- H. W. Kroto, J. R. Heath, S. C. O'Brien, R. F. Curl and R. E. Smalley, Nature, 1985, 318, 162–163 CrossRef CAS
.
- T. Higashino, T. Yamada, M. Yamamoto, A. Furube, N. V. Tkachenko, T. Miura, Y. Kobori, R. Jono, K. Yamashita and H. Imahori, Angew. Chem., Int. Ed., 2016, 55, 629–633 CrossRef CAS PubMed
.
- F. Pan, K. Ni, T. Xu, H. Chen, Y. Wang, K. Gong, C. Liu, X. Li, M.-L. Lin, S. Li, X. Wang, W. Yan, W. Yin, P.-H. Tan, L. Sun, D. Yu, R. S. Ruoff and Y. Zhu, Nature, 2023, 614, 95–101 CrossRef CAS PubMed
.
- M. Yamamoto, Q. Zhao, S. Goto, Y. Gu, T. Toriyama, T. Yamamoto, H. Nishihara, M. Tamura, K. Tomishige, A. Aziz, R. Crespo-Otero, D. Di Tommaso, T. Kyotani and K. Yamazaki, Chem. Sci., 2022, 13, 3140–3146 RSC
.
- T. Kiryu and M. Koshino, Phys. Rev. B, 2019, 99, 085443 CrossRef CAS
.
- A. Dechant, T. Ohto, Y. Ito, M. V. Makarova, Y. Kawabe, T. Agari, H. Kumai, Y. Takahashi, H. Naito and M. Kotani, Carbon, 2021, 182, 223–232 CrossRef CAS
.
- N. P. Stadie, J. J. Vajo, R. W. Cumberland, A. A. Wilson, C. C. Ahn and B. Fultz, Langmuir, 2012, 28, 10057–10063 CrossRef CAS PubMed
.
- H. Tüysüz, E. L. Salabaş, C. Weidenthaler and F. Schüth, J. Am. Chem. Soc., 2008, 130, 280–287 CrossRef PubMed
.
- W. Xu, G. S. Jung, W. Zhang, A. T. S. Wee and J. H. Warner, Mater. Today Nano, 2022, 18, 100183 CrossRef CAS
.
- Y. Ito, H. J. Qiu, T. Fujita, Y. Tanabe, K. Tanigaki and M. Chen, Adv. Mater., 2014, 26, 4145–4150 CrossRef CAS PubMed
.
- I. Di Bernardo, G. Avvisati, C. Chen, J. Avila, M. C. Asensio, K. Hu, Y. Ito, P. Hines, J. Lipton-Duffin, L. Rintoul, N. Motta, C. Mariani and M. G. Betti, Carbon, 2018, 131, 258–265 CrossRef CAS
.
- I. Di Bernardo, G. Avvisati, C. Mariani, N. Motta, C. Chen, J. Avila, M. C. Asensio, S. Lupi, Y. Ito, M. Chen, T. Fujita and M. G. Betti, ACS Omega, 2017, 2, 3691–3697 CrossRef CAS PubMed
.
- H. Kashani, Y. Ito, J. Han, P. Liu and M. Chen, Sci. Adv., 2019, 5, eaat6951 CrossRef CAS PubMed
.
- Y. Tanabe, Y. Ito, K. Sugawara, M. Koshino, S. Kimura, T. Naito, I. Johnson, T. Takahashi and M. Chen, Adv. Mater., 2020, 32, 2005838 CrossRef CAS PubMed
.
- A. Martínez-Alonso, J. M. D. Tascón and E. J. Bottani, Langmuir, 2000, 16, 1343–1348 CrossRef
.
- A. A. Gabrienko, S. S. Arzumanov, A. V. Toktarev, I. P. Prosvirin, D. Freude, J. Haase and A. G. Stepanov, J. Phys. Chem. C, 2022, 126, 16204–16214 CrossRef CAS
.
- W. Gao, L. Guo, Q. Wu, C. Wang, X. Guo, Y. He, P. Zhang, G. Yang, G. Liu, J. Wu and N. Tsubaki, Appl. Catal., B, 2022, 303, 120906 CrossRef CAS
.
- A. Oda, M. Horie, N. Murata, K. Sawabe and A. Satsuma, Catal. Sci. Technol., 2022, 12, 5488–5494 RSC
.
- D. Plessers, A. J. Heyer, H. M. Rhoda, M. L. Bols, E. I. Solomon, R. A. Schoonheydt and B. F. Sels, ACS Catal., 2023, 13, 1906–1915 CrossRef CAS PubMed
.
- J. Li, M. Gao, W. Yan and J. Yu, Chem. Sci., 2023, 14, 1935–1959 RSC
.
- P. Xiao, Y. Wang, K. Nakamura, Y. Lu, T. De Baerdemaeker, A.-N. Parvulescu, U. Müller, D. De Vos, X. Meng, F.-S. Xiao, W. Zhang, B. Marler, U. Kolb, R. Osuga, M. Nishibori, H. Gies and T. Yokoi, ACS Catal., 2023, 13, 11057–11068 CrossRef CAS
.
- K. Nakamura, P. Xiao, R. Osuga, Y. Wang, S. Yasuda, T. Matsumoto, J. N. Kondo, M. Yabushita, A. Muramatsu, H. Gies and T. Yokoi, Catal. Sci. Technol., 2023, 13, 2648–2651 RSC
.
- B. Ipek, M. J. Wulfers, H. Kim, F. Göltl, I. Hermans, J. P. Smith, K. S. Booksh, C. M. Brown and R. F. Lobo, ACS Catal., 2017, 7, 4291–4303 CrossRef CAS
.
- T. Kyotani, Bull. Chem. Soc. Jpn., 2006, 79, 1322–1337 CrossRef CAS
.
- Z. Ma, T. Kyotani and A. Tomita, Carbon, 2002, 40, 2367–2374 CrossRef CAS
.
- A. Gabe, M. Ouzzine, E. E. Taylor, N. P. Stadie, N. Uchiyama, T. Kanai, Y. Nishina, H. Tanaka, Z.-Z. Pan, T. Kyotani and H. Nishihara, J. Mater. Chem. A, 2021, 9, 7503–7507 RSC
.
- A. Kajdos, A. Kvit, F. Jones, J. Jagiello and G. Yushin, J. Am. Chem. Soc., 2010, 132, 3252–3253 CrossRef CAS PubMed
.
- T. Aumond, H. Vezin, I. Batonneau-Gener, S. Compère, Y. Pouilloux, A. Le Person, A. Moissette and A. Sachse, Small, 2023, 2300972 CrossRef CAS PubMed
.
- C. Portet, Z. Yang, Y. Korenblit, Y. Gogotsi, R. Mokaya and G. Yushin, J. Electrochem. Soc., 2009, 156, A1 CrossRef CAS
.
- H. Itoi, H. Nishihara and T. Kyotani, Langmuir, 2016, 32, 11997–12004 CrossRef CAS PubMed
.
- K. Yamazaki, S. Goto, S. Yoshino, A. Gubarevich, K. Yoshida, H. Kato and M. Yamamoto, Phys. Chem. Chem. Phys., 2023, 25, 32972–32978 RSC
.
- H. Liu, Z.-Z. Pan, A. Aziz, R. Tang, W. Lv and H. Nishihara, Adv. Funct. Mater., 2023, 33, 2303730 CrossRef CAS
.
- M. Danielis, S. Colussi, C. de Leitenburg, L. Soler, J. Llorca and A. Trovarelli, Angew. Chem., Int. Ed., 2018, 57, 10212–10216 CrossRef CAS PubMed
.
- R. Wischert, C. Copéret, F. Delbecq and P. Sautet, Angew. Chem., Int. Ed., 2011, 50, 3202–3205 CrossRef CAS PubMed
.
- K. Pirabul, Z.-Z. Pan, R. Tang, S. Sunahiro, H. Liu, K. Kanamaru, T. Yoshii and H. Nishihara, Bull. Chem. Soc. Jpn., 2023, 96, 510–518 CrossRef CAS
.
- T. Xia, T. Yoshii, K. Nomura, K. Wakabayashi, Z.-Z. Pan, T. Ishii, H. Tanaka, T. Mashio, J. Miyawaki, T. Otomo, K. Ikeda, Y. Sato, M. Terauchi, T. Kyotani and H. Nishihara, Chem. Sci., 2023, 14, 8448–8457 RSC
.
- M. Yamamoto, S. Goto, R. Tang, K. Nomura, Y. Hayasaka, Y. Yoshioka, M. Ito, M. Morooka, H. Nishihara and T. Kyotani, ACS Appl. Mater. Interfaces, 2021, 13, 38613–38622 CrossRef CAS PubMed
.
- H. Nishihara, T. Simura, S. Kobayashi, K. Nomura, R. Berenguer, M. Ito, M. Uchimura, H. Iden, K. Arihara, A. Ohma, Y. Hayasaka and T. Kyotani, Adv. Funct. Mater., 2016, 26, 6418–6427 CrossRef CAS
.
- Q. Zhao, M. Yamamoto, K. Yamazaki, H. Nishihara, R. Crespo-Otero and D. Di Tommaso, Phys. Chem. Chem. Phys., 2022, 24, 23357–23366 RSC
.
- K. Nomura, H. Nishihara, N. Kobayashi, T. Asada and T. Kyotani, Energy Environ. Sci., 2019, 12, 1542–1549 RSC
.
- J.-U. Lee, D. Yoon and H. Cheong, Nano Lett., 2012, 12, 4444–4448 CrossRef CAS PubMed
.
- J.-W. Jiang, J.-S. Wang and B. Li, Phys. Rev. B, 2009, 80, 113405 CrossRef
.
- C. Lee, X. Wei, J. W. Kysar and J. Hone, Science, 2008, 321, 385–388 CrossRef CAS PubMed
.
- K. Nomura, H. Nishihara, M. Yamamoto, A. Gabe, M. Ito, M. Uchimura, Y. Nishina, H. Tanaka, M. T. Miyahara and T. Kyotani, Nat. Commun., 2019, 10, 2559 CrossRef PubMed
.
- R. Tang, K. Taguchi, H. Nishihara, T. Ishii, E. Morallón, D. Cazorla-Amorós, T. Asada, N. Kobayashi, Y. Muramatsu and T. Kyotani, J. Mater. Chem. A, 2019, 7, 7480–7488 RSC
.
- Y. Liu, E. H. Osta, A. S. Poryvaev, M. V. Fedin, A. Longo, A. Nefedov and N. Kosinov, Carbon, 2023, 201, 535–541 CrossRef CAS
.
- H. Cui, M. Jiao, Y.-N. Chen, Y. Guo, L. Yang, Z. Xie, Z. Zhou and S. Guo, Small Methods, 2018, 2, 1800144 CrossRef
.
- S. Inagaki, T. Nakao, T. Miki, N. Kuroda and Y. Kubota, Microporous Mesoporous Mater., 2017, 241, 123–131 CrossRef CAS
.
- S. Fujii, A. Yoshida, T. T. Chuong, Y. Minegishi, K. Pirabul, Z.-Z. Pan, Y. Nishina, T. Kyotani, H. Nishihara, K. Masumoto, G. D. Stucky and T. Itoh, ACS Appl. Eng. Mater., 2023, 1, 1426–1435 CrossRef CAS
.
- T. Ito and J. H. Lunsford, Nature, 1985, 314, 721–722 CrossRef CAS
.
- D. J. Driscoll, W. Martir, J. X. Wang and J. H. Lunsford, J. Am. Chem. Soc., 1985, 107, 58–63 CrossRef CAS
.
- T. Ito, J. Wang, C. H. Lin and J. H. Lunsford, J. Am. Chem. Soc., 1985, 107, 5062–5068 CrossRef CAS
.
- Y. Tian, X. Zhu, M. Abbas, D. W. Tague, M. A. Wunch, J. P. Ferraris and K. J. Balkus, ACS Appl. Energy Mater., 2022, 5, 6805–6813 CrossRef CAS
.
- S. Sunahiro, K. Nomura, S. Goto, K. Kanamaru, R. Tang, M. Yamamoto, T. Yoshii, J. N. Kondo, Q. Zhao, A. G. Nabi, R. Crespo-Otero, D. Di Tommaso, T. Kyotani and H. Nishihara, J. Mater. Chem. A, 2021, 9, 14296–14308 RSC
.
- A. Gupta, G. Chen, P. Joshi, S. Tadigadapa and P. C. Eklund, Nano Lett., 2006, 6, 2667–2673 CrossRef CAS PubMed
.
- R. Kostić, M. Mirić, T. Radić, M. Radović, R. Gajić and Z. Popović, Acta Phys. Pol., A, 2009, 116, 718–721 CrossRef
.
- A. Eckmann, A. Felten, A. Mishchenko, L. Britnell, R. Krupke, K. S. Novoselov and C. Casiraghi, Nano Lett., 2012, 12, 3925–3930 CrossRef CAS PubMed
.
- T. Fujimori, L. R. Radovic, A. B. Silva-Tapia, M. Endo and K. Kaneko, Carbon, 2012, 50, 3274–3279 CrossRef CAS
.
- K. Yamazaki, N. Niitsu, K. Nakamura, M. Kanno and H. Kono, J. Phys. Chem. A, 2012, 116, 11441–11450 CrossRef CAS PubMed
.
- S. K. Tiwari, S. K. Pandey, R. Pandey, N. Wang, M. Bystrzejewski, Y. K. Mishra and Y. Zhu, Small, 2023, 2303340 CrossRef CAS PubMed
.
- M. M. Lucchese, F. Stavale, E. H. M. Ferreira, C. Vilani, M. V. O. Moutinho, R. B. Capaz, C. A. Achete and A. Jorio, Carbon, 2010, 48, 1592–1597 CrossRef CAS
.
- Z.-L. Li, Z.-M. Li, H.-Y. Cao, J.-H. Yang, Q. Shu, Y.-Y. Zhang, H. J. Xiang and X. G. Gong, Nanoscale, 2014, 6, 4309–4315 RSC
.
- J. C. Meyer, C. Kisielowski, R. Erni, M. D. Rossell, M. F. Crommie and A. Zettl, Nano Lett., 2008, 8, 3582–3586 CrossRef CAS PubMed
.
- K. V. Bets, V. I. Artyukhov and B. I. Yakobson, ACS Nano, 2021, 15, 4893–4900 CrossRef CAS PubMed
.
- H. Itoi, H. Nishihara, T. Kogure and T. Kyotani, J. Am. Chem. Soc., 2011, 133, 1165–1167 CrossRef CAS PubMed
.
- H. Nishihara, H. Fujimoto, H. Itoi, K. Nomura, H. Tanaka, M. T. Miyahara, P. A. Bonnaud, R. Miura, A. Suzuki, N. Miyamoto, N. Hatakeyama, A. Miyamoto, K. Ikeda, T. Otomo and T. Kyotani, Carbon, 2018, 129, 854–862 CrossRef CAS
.
- Y. M. Liu, C. Merlet and B. Smit, ACS Cent. Sci., 2019, 5, 1813–1823 CrossRef CAS PubMed
.
- R. Tang, K. Nomura, K. Inoue, M. Kotani, T. Kyotani and H. Nishihara, Electrochim. Acta, 2022, 429, 141009 CrossRef CAS
.
- J. Chmiola, G. Yushin, Y. Gogotsi, C. Portet, P. Simon and P. L. Taberna, Science, 2006, 313, 1760–1763 CrossRef CAS PubMed
.
- H. Ji, X. Zhao, Z. Qiao, J. Jung, Y. Zhu, Y. Lu, L. L. Zhang, A. H. MacDonald and R. S. Ruoff, Nat. Commun., 2014, 5, 3317 CrossRef PubMed
.
- J. Chen, Y. Han, X. Kong, X. Deng, H. J. Park, Y. Guo, S. Jin, Z. Qi, Z. Lee, Z. Qiao, R. S. Ruoff and H. Ji, Angew. Chem., Int. Ed., 2016, 55, 13822–13827 CrossRef CAS PubMed
.
- R. Futamura, T. Iiyama, Y. Takasaki, Y. Gogotsi, M. J. Biggs, M. Salanne, J. Ségalini, P. Simon and K. Kaneko, Nat. Mater., 2017, 16, 1225–1232 CrossRef CAS PubMed
.
- C. Prehal, C. Koczwara, N. Jäckel, A. Schreiber, M. Burian, H. Amenitsch, M. A. Hartmann, V. Presser and O. Paris, Nat. Energy, 2017, 2, 16215 CrossRef CAS
.
- C. Cui, Y. Gao, J. Li, C. Yang, M. Liu, H. Jin, Z. Xia, L. Dai, Y. Lei, J. Wang and S. Wang, Angew. Chem., Int. Ed., 2020, 59, 7928–7933 CrossRef CAS PubMed
.
- C. Masquelier, Nat. Mater., 2011, 10, 649–650 CrossRef CAS PubMed
.
- J. M. Tarascon and M. Armand, Nature, 2001, 414, 359–367 CrossRef CAS PubMed
.
- H. Hafiz, K. Suzuki, B. Barbiellini, N. Tsuji, N. Yabuuchi, K. Yamamoto, Y. Orikasa, Y. Uchimoto, Y. Sakurai, H. Sakurai, A. Bansil and V. Viswanathan, Nature, 2021, 594, 213–216 CrossRef CAS PubMed
.
- X. Chi, M. Li, J. Di, P. Bai, L. Song, X. Wang, F. Li, S. Liang, J. Xu and J. Yu, Nature, 2021, 592, 551–557 CrossRef CAS PubMed
.
- Z. Wu, Y. Tian, H. Chen, L. Wang, S. Qian, T. Wu, S. Zhang and J. Lu, Chem. Soc. Rev., 2022, 51, 8045–8101 RSC
.
- T. Liu, J. P. Vivek, E. W. Zhao, J. Lei, N. Garcia-Araez and C. P. Grey, Chem. Rev., 2020, 120, 6558–6625 CrossRef CAS PubMed
.
- J. Li, J. Fleetwood, W. B. Hawley and W. Kays, Chem. Rev., 2022, 122, 903–956 CrossRef CAS PubMed
.
- S. Lee, J. Choi, M. Kim, J. Park, M. Park and J. Cho, Chem. Sci., 2022, 13, 6159–6180 RSC
.
- Y.-X. Zhao, J.-H. Wen, P. Li, P.-F. Zhang, S.-N. Wang, D.-C. Li, J.-M. Dou, Y.-W. Li, H.-Y. Ma and L. Xu, Angew. Chem., Int. Ed., 2023, 62, e202216950 CrossRef CAS PubMed
.
- W. Sun, V. Küpers, F. Wang, P. Bieker and M. Winter, Angew. Chem., Int. Ed., 2022, 61, e202207353 CrossRef CAS PubMed
.
- Z. Shen, W. Yu, A. Aziz, K. Chida, T. Yoshii and H. Nishihara, J. Phys. Chem. C, 2023, 127, 6239–6247 CrossRef CAS
.
- H. Liu, Z. Shen, Z.-Z. Pan, W. Yu and H. Nishihara, ACS Appl. Mater. Interfaces, 2023, 15, 40397–40408 CrossRef CAS PubMed
.
- W.-J. Kwak, Rosy, D. Sharon, C. Xia, H. Kim, L. R. Johnson, P. G. Bruce, L. F. Nazar, Y.-K. Sun, A. A. Frimer, M. Noked, S. A. Freunberger and D. Aurbach, Chem. Rev., 2020, 120, 6626–6683 CrossRef CAS PubMed
.
- Y. Li, J. Qin, Y. Ding, J. Ma, P. Das, H. Liu, Z.-S. Wu and X. Bao, ACS Catal., 2022, 12, 12765–12773 CrossRef CAS
.
- J. Han, X. Guo, Y. Ito, P. Liu, D. Hojo, T. Aida, A. Hirata, T. Fujita, T. Adschiri, H. Zhou and M. Chen, Adv. Energy Mater., 2016, 6, 1501870 CrossRef
.
- B. J. Bergner, A. Schürmann, K. Peppler, A. Garsuch and J. Janek, J. Am. Chem. Soc., 2014, 136, 15054–15064 CrossRef CAS PubMed
.
- Z. Su, I. Temprano, N. Folastre, V. Vanpeene, J. Villanova, G. Gachot, E. V. Shevchenko, C. P. Grey, A. A. Franco and A. Demortière, Small Methods, 2023, 2300452 CrossRef PubMed
.
- T. He, Y. Chen, Q. Liu, B. Lu, X. Song, H. Liu, M. Liu, Y.-N. Liu, Y. Zhang, X. Ouyang and S. Chen, Angew. Chem., Int. Ed., 2022, 61, e202201007 CrossRef CAS PubMed
.
- Z. Xi, J. Han, Z. Jin, K. Hu, H.-J. Qiu and Y. Ito, Small, 2023, 2308045 CrossRef PubMed
.
- M. L. Holekevi Chandrappa, J. Qi, C. Chen, S. Banerjee and S. P. Ong, J. Am. Chem. Soc., 2022, 144, 18009–18022 CrossRef CAS PubMed
.
- W. Yu, Z. Shen, T. Yoshii, S. Iwamura, M. Ono, S. Matsuda, M. Aoki, T. Kondo, S. R. Mukai, S. Nakanishi and H. Nishihara, Adv. Energy Mater., 2023, 2303055 Search PubMed
.
- N. Yamato, N. Kumagai, M. Okahira, S. Kosaka, S. Kodama, R. Yamamoto, A. Yamamoto, K. Takao and M. Yamamoto, Chem. Commun., 2022, 58, 12106–12109 RSC
.
- H. Nishihara, Q.-H. Yang, P.-X. Hou, M. Unno, S. Yamauchi, R. Saito, J. I. Paredes, A. Martínez-Alonso, J. M. D. Tascón, Y. Sato, M. Terauchi and T. Kyotani, Carbon, 2009, 47, 1220–1230 CrossRef CAS
.
- L. Sun, G. Yuan, L. Gao, J. Yang, M. Chhowalla, M. H. Gharahcheshmeh, K. K. Gleason, Y. S. Choi, B. H. Hong and Z. Liu, Nat. Rev. Methods Primers, 2021, 1, 5 CrossRef CAS
.
- J. Dong, L. Zhang and F. Ding, Adv. Mater., 2019, 31, 1801583 CrossRef PubMed
.
- K. Kim, T. Lee, Y. Kwon, Y. Seo, J. Song, J. K. Park, H. Lee, J. Y. Park, H. Ihee, S. J. Cho and R. Ryoo, Nature, 2016, 535, 131–135 CrossRef CAS PubMed
.
- S. Maeda, Y. Harabuchi, H. Hayashi and T. Mita, Annu. Rev. Phys. Chem., 2023, 74, 287–311 CrossRef CAS PubMed
.
- K. Takahashi, J. Ohyama, S. Nishimura, J. Fujima, L. Takahashi, T. Uno and T. Taniike, Chem. Commun., 2023, 59, 2222–2238 RSC
.
- M.-W. Wang, W. Fan, X. Li, Y. Liu, Z. Li, W. Jiang, J. Wu and Z. Wang, ACS Nano, 2023, 17, 20734–20752 CrossRef PubMed
.
- T. J. Booth, F. Pizzocchero, H. Andersen, T. W. Hansen, J. B. Wagner, J. R. Jinschek, R. E. Dunin-Borkowski, O. Hansen and P. Bøggild, Nano Lett., 2011, 11, 2689–2692 CrossRef CAS PubMed
.
- M. S. H. Boutilier, C. Sun, S. C. O'Hern, H. Au, N. G. Hadjiconstantinou and R. Karnik, ACS Nano, 2014, 8, 841–849 CrossRef CAS PubMed
.
- H. Kraus, D. Simin, C. Kasper, Y. Suda, S. Kawabata, W. Kada, T. Honda, Y. Hijikata, T. Ohshima, V. Dyakonov and G. V. Astakhov, Nano Lett., 2017, 17, 2865–2870 CrossRef CAS PubMed
.
- T. X. Nguyen and S. K. Bhatia, Langmuir, 2004, 20, 3532–3535 CrossRef CAS PubMed
.
- F. Ming and A. Zangwill, Phys. Rev. B, 2011, 84, 115459 CrossRef
.
- A. Karlsson, H. Grennberg and S. Johansson, RSC Adv., 2023, 13, 781–789 RSC
.
- K. Suenaga, H. Wakabayashi, M. Koshino, Y. Sato, K. Urita and S. Iijima, Nat. Nanotechnol., 2007, 2, 358–360 CrossRef CAS PubMed
.
- C. Zhang, W. Shen, K. Guo, M. Xiong, J. Zhang and X. Lu, J. Am. Chem. Soc., 2023, 145, 11589–11598 CrossRef CAS PubMed
.
- T. Ishikawa, F. Tanaka, K. Kurushima, A. Yasuhara, R. Sagawa, T. Fujita, R. Yonesaki, K. Iseki, T. Nakamuro, K. Harano and E. Nakamura, J. Am. Chem. Soc., 2023, 145, 12244–12254 CrossRef CAS PubMed
.
- E. Braun, Y. Lee, S. M. Moosavi, S. Barthel, R. Mercado, I. A. Baburin, D. M. Proserpio and B. Smit, Proc. Natl. Acad. Sci. U. S. A., 2018, 115, E8116–E8124 CrossRef CAS PubMed
.
- K. Takahashi and L. Takahashi, J. Phys. Chem. Lett., 2023, 14, 4726–4733 CrossRef CAS PubMed
.
- A. J. H. Jones, L. Gammelgaard, M. O. Sauer, D. Biswas, R. J. Koch, C. Jozwiak, E. Rotenberg, A. Bostwick, K. Watanabe, T. Taniguchi, C. R. Dean, A.-P. Jauho, P. Bøggild, T. G. Pedersen, B. S. Jessen and S. Ulstrup, ACS Nano, 2022, 16, 19354–19362 CrossRef CAS PubMed
.
- O. Endo, F. Matsui, W.-J. Chun, M. Nakamura, K. Amemiya and H. Ozaki, Surf. Sci., 2021, 711, 121874 CrossRef CAS
.
- Y. Muramatsu, Y. Ota and T. Okada, Anal. Sci., 2023, 39, 67–76 CrossRef CAS PubMed
.
- R. Li, X. Yang, M. Ma and J. Zhang, Small, 2023, 19, 2206580 CrossRef CAS PubMed
.
- Z. Sofer, P. Šimek, O. Jankovský, D. Sedmidubský, P. Beran and M. Pumera, Nanoscale, 2014, 6, 13082–13089 RSC
.
- Y. Wang, W. Wang, R. He, M. Li, J. Zhang, F. Cao, J. Liu, S. Lin, X. Gao, G. Yang, M. Wang, T. Xing, T. Liu, Q. Liu, H. Hu, N. Tsubaki and M. Wu, Angew. Chem., Int. Ed., 2023, 62, e202311786 CrossRef CAS PubMed
.
|
This journal is © The Royal Society of Chemistry 2024 |
Click here to see how this site uses Cookies. View our privacy policy here.