DOI:
10.1039/D4SC04884A
(Edge Article)
Chem. Sci., 2024,
15, 16637-16644
Size disproportionation among nanocluster transformations†
Received
23rd July 2024
, Accepted 15th September 2024
First published on 20th September 2024
Abstract
Controllable transformation is a prerequisite to the in-depth understanding of structure evolution mechanisms and structure–property correlations at the atomic level. Most transformation cases direct the directional evolution of nanocluster sizes, i.e., size-maintained, size-increased, or size-reduced transformation, while size disproportionation was rarely reported. Here, we report the Au-doping-induced size disproportionation of nanocluster transformation. Slight Au-doping on the bimetallic (AgCu)43 nanocluster produced its trimetallic derivative, (AuAgCu)43, following a size-maintained transformation. By comparison, the (AgCu)43 nanocluster underwent a size-disproportionation transformation under heavy Au alloying, leading to the formation of size-reduced (AuAgCu)33 and size-increased (AuAgCu)56 nanoclusters simultaneously. Such a size disproportionation among the nanocluster transformations was verified by the thin-layer chromatography analysis. This work presented a novel nanocluster transformation case with a size disproportionation characteristic, expected to provide guidance for the understanding of cluster size evolutions.
1 Introduction
Metal nanoclusters, bridging organometallic complexes and plasmonic nanoparticles, have emerged as a captivating subject of study owing to their atomically precise structures, discrete electronic energy levels, and strong quantum size effect.1–6 The physicochemical properties of metal nanoclusters display a notable sensitivity to their structures, rendering them ideal platforms for investigating atomic-defined correlations between structures and properties.7–18 Besides, various potential applications based on such ultrasmall nanomaterials have been found in catalysis, optoelectronics, phototherapy, chemical sensing, and so on.19–25 The controllable preparation of metal nanoclusters is a prerequisite to their follow-up research and downstream applications.1–3 To date, several efficient approaches have been proposed to trigger nanocluster transformations and dictate nanocluster structures, mainly including heteroatom doping, ligand exchanging, counterion substituting, intercluster assembling, and environmental regulation.26–35
Based on nanocluster transformations from precision to precision, several mechanisms of structural evolutions have been mapped out at the atomic level.26–30 Because of the thermodynamic and kinetic factors, most transformation cases direct the directional evolution of nanocluster sizes, i.e., size-maintained, size-increased, or size-reduced transformation,31–46 while size disproportionation was rarely reported, probably due to that separation and crystallization of poly-dispersed cluster products were difficult. Disproportionation usually refers to a reaction in which oxidation and reduction processes happen simultaneously, leading to one part of the molecule being oxidized while another part being reduced.47 To date, the concept of disproportionation has been extended to the field of nanomaterial study, where one nanomolecular precursor could convert to two or more different nanomolecular products with individually increasing and decreasing sizes.48,49 It is important and necessary to construct an atomically precise platform for exploring size disproportionation among nanocluster transformations, which hopefully allows for an in-depth understanding of nanocluster size evolutions.
Herein, we report the size disproportionation of the nanocluster transformation induced by the Au-alloying process (Scheme 1). The slight Au doping to the Ag26Cu17(SR)30(PPh3)7 nanocluster ((AgCu)43 for short SR = 4-(trifluoromethylthio)phenol) with a core@shell configuration gave rise to a structure-maintained trimetallic Au2Ag24Cu17(SR)30(PPh3)7 nanocluster ((AuAgCu)43 for short), which was cocrystallized together with Cl1Ag8Cu6(SR)12(PPh3)6 in the crystal lattice. Furthermore, the Au2Ag24Cu17(SR)30(PPh3)7 nanocluster underwent size disproportionation under heavy Au doping, producing size-increased Au2Ag27Cu27S3(SR)30(PPh3)9Cl11 ((AuAgCu)56 for short) and size-reduced Au1Ag18Cu14S2(SR)14(PPh3)6 ((AuAgCu)33 for short). The atomically precise structures of such nanoclusters were determined by single-crystal X-ray diffraction (SC-XRD). Furthermore, the thin-layer chromatography (TCL) tests suggested that the (AuAgCu)56 and (AuAgCu)33 nanoclusters were generated simultaneously from the (AuAgCu)43 precursor induced by the Au alloying, further demonstrating size disproportionation. This work not only described the heteroatom doping of the (AgCu)43 nanocluster in detail but also revealed the size disproportionation phenomenon in nanoclusters.
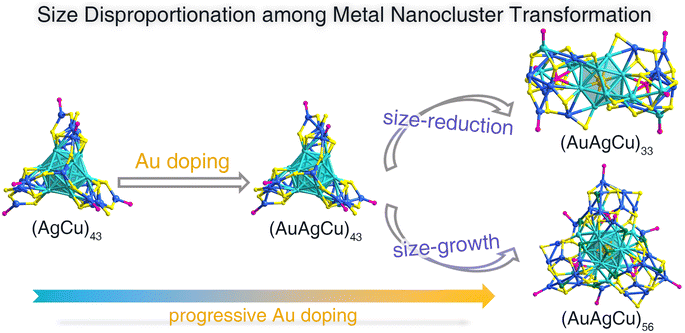 |
| Scheme 1 Illustration of size disproportionation among the nanocluster transformations. Progressive Au doping induced successive nanocluster transformation from the (AgCu)43 precursor into the size-maintained (AuAgCu)43 nanocluster and then into size-disproportionated (AuAgCu)56 and (AuAgCu)33 nanoclusters. | |
2 Experimental methods
2.1 Materials
All following reagents were purchased from Sigma-Aldrich and used without further purification, including cupric acetylacetonate (Cu(C5H7O2)2, 98% metal basis), silver nitrate (AgNO3, 99% metal basis), chloro(triphenylphosphine)gold(I) (Au(PPh3)Cl, 98%), 4-trifluoromethyl phenylthiophenol (C7H5F3S, 98%), triphenylphosphine (C18H15P, 99%), sodium borohydride (NaBH4, 99%), methanol (HPLC grade), dichloromethane (HPLC grade), hexane (HPLC grade), and toluene (HPLC grade).
2.2 Preparation of the (AgCu)43 nanocluster
30 mg of AgNO3 was dissolved in a mixed solution of 5 mL of MeOH and 20 mL of CH2Cl2, and 70 mg of Cu(C5H7O2)2 was added to this solution. After 20 minutes, 50 mg of PPh3 and 50 μL of 4-trifluoromethyl phenylthiophenol were added. Then, 5 mL of the aqueous solution of NaBH4 (8 mg mL−1) was added. The reaction was proceeded for 12 hours. The obtained solution was centrifuged at 10
000 rpm for 3 minutes, and the supernatant was collected and evaporated to get the crude product. The crude product was washed three times with hexane and methanol to get the (AgCu)43 nanocluster.
2.3 Preparation of the (AuAgCu)43·(AgCu)14 nanocluster
The as-prepared (AgCu)43 nanocluster (10 mg) was dissolved in 50 mL of toluene. The solution was vigorously stirred with a magnetic stir bar for 10 minutes. Then, 150 μL of Au(PPh3)Cl solution (dissolved in toluene, 5 mg mL−1) was added. The reaction was allowed to proceed for two hours. After that, the organic phase was rotavaporated under vacuum, and the precipitate was redissolved in CH2Cl2, producing the (AuAgCu)43·(AgCu)14 nanocluster as determined by SC-XRD.
2.4 Preparation of (AuAgCu)33 and (AuAgCu)56 nanoclusters
The as-prepared (AgCu)43 nanocluster (10 mg) was dissolved in 50 mL of toluene. The solution was vigorously stirred with a magnetic stir bar for 10 min. Then, 800 μL of Au(PPh3)Cl solution (dissolved in toluene, 5 mg mL−1) was added. The reaction was allowed to proceed for two hours. After that, the organic phase was rotavaporated under vacuum, and the precipitate was redissolved in CH2Cl2. Then, thin-layer chromatography was used to separate and obtain (AuAgCu)33 and (AuAgCu)56 nanoclusters.
2.5 Crystallization of (AgCu)43, (AuAgCu)43·(AgCu)14, (AuAgCu)33 and (AuAgCu)56 nanoclusters
Single crystals of (AgCu)43, (AuAgCu)43·(AgCu)14, (AuAgCu)33, and (AuAgCu)56 nanoclusters were cultivated at room temperature by diffusing n-hexane into the CH2Cl2 solution of each nanocluster. After a week, crystals were collected, and the structures of these nanoclusters were determined.
2.6 Characterization
The optical absorption spectra of nanoclusters were recorded using an Agilent 8453 diode array spectrometer.
Electrospray ionization mass spectrometry (ESI-MS) measurements were performed using a Waters XEVO G2-XS QTof mass spectrometer. The sample was directly infused into the chamber at 5 μL min−1. For preparing the ESI samples, nanoclusters were dissolved in CH2Cl2 (1 mg mL−1) and diluted (v/v = 1
:
1) using CH3OH.
X-ray photoelectron spectroscopy (XPS) was performed on a Thermo ESCALAB 250 equipped with a monochromated Al Kα (1486.8 eV) 150 W X-ray source, a 0.5 mm circular spot size, a flood gun to counter charging effects, and the analysis chamber base pressure lower than 1 × 10−9 mbar. The data were collected with FAT = 20 eV.
2.7 X-ray crystallography
The data collection for single-crystal X-ray diffraction (SC-XRD) of all nanocluster crystal samples was carried out on a Stoe Stadivari diffractometer under nitrogen flow, using graphite-monochromatized Cu Kα radiation (λ = 1.54186 Å). Data reductions and absorption corrections were performed using the SAINT and SADABS programs, respectively. The structure was solved by direct methods and refined with full-matrix least squares on F2 using the SHELXTL software package. All non-hydrogen atoms were refined anisotropically, and all the hydrogen atoms were set in geometrically calculated positions and refined isotropically using a riding model. All crystal structures were treated with PLATON SQUEEZE. The diffuse electron densities from these residual solvent molecules were removed.
3 Results and discussion
The (AgCu)43 nanocluster was prepared with a one-pot synthetic procedure by directly reducing the Ag–Cu-SR-PPh3 complexes with NaBH4 (see the ESI† for more details). Au(PPh3)Cl with a concentration of 5 mg mL−1 was controllably added to the toluene solution of the (AgCu)43 nanocluster to trigger nanocluster transformation. The slight introduction of Au(PPh3)Cl (150 μL) gave rise to a size-maintained (AuAgCu)43 nanocluster. By comparison, heavy Au doping (800 μL) resulted in the size disproportionation of the nanocluster framework, and a size-increased (AuAgCu)56 nanocluster and a size-reduced (AuAgCu)33 nanocluster were obtained. Single crystals of these nanoclusters were cultivated at room temperature by diffusing n-hexane into the CH2Cl2 solution of each nanocluster, and their crystal structures were determined by SC-XRD. The X-ray photoelectron spectroscopy (XPS) results of these nanoclusters were collected to further verify the successful introduction of Au heteroatoms into the cluster framework (Fig. S1 and S2†).
The chemical formulae of (AgCu)43, (AuAgCu)43, and (AuAgCu)33 nanoclusters were characterized by electrospray ionization mass spectrometry (ESI-MS; Figs. S1–S5†). However, the mass signal of the (AuAgCu)56 nanocluster was not detected in the positive or negative ion mode of ESI-MS, probably because of its difficulty in ionizing. Indeed, several PPh3 ligands were detached from the surface of (AgCu)43, (AuAgCu)43, and (AuAgCu)33 nanoclusters to assist their ionization, and thus mass signals of “cluster–xPPh3” molecules were detected.50–52 Besides, the ESI-MS results also demonstrated that several positions in the frameworks of (AgCu)43, (AuAgCu)43, and (AuAgCu)33 alloy nanoclusters were co-occupied by different metals. For example, the mass peaks of the bimetallic (AgCu)43 nanocluster were assigned to chemical formulae of “AgxCu43−x(SR)30(PPh3)6” where x ranged from 14 to 38 (Fig. S3†), illustrating that a large number of metal positions were co-occupied by Ag and Cu.53 Such a phenomenon also existed in analyzing the ESI-MS results of trimetallic (AuAgCu)43 and (AuAgCu)33 nanoclusters (Fig. S4 and S5†). Of note, in the single-crystal analysis process, each position was confined as the metal with the highest proportion for a better understanding of the nanocluster structures.
Structurally, the overall structure of the (AgCu)43 nanocluster contained a coplanar Ag23 kernel that was composed of two Ag13 icosahedral cores sharing a triangular Ag3 surface (Fig. 1A). Such a biicosahedral Ag23 kernel was stabilized by three Cu5Ag1(SR)8(PPh3)2 motif structures via Cu–S or Cu–Ag interactions, producing an Ag26Cu15(SR)24(PPh3)6 structure (Fig. 1B and C). Two Cu-based terminals, Cu1(SR)3 and Cu1(SR)3(PPh3)1, were anchored onto both ends of the above-mentioned structure (Fig. 1D–F), forming the complete Ag26Cu17(SR)30(PPh3)7 framework (Fig. 1G). The overall configuration of (AgCu)43 was similar to those of Au2Ag42(SAdm)27 and Au1Ag21(dppf)3(SAdm)12 nanoclusters from the top view (Fig. 1H and I).54,55
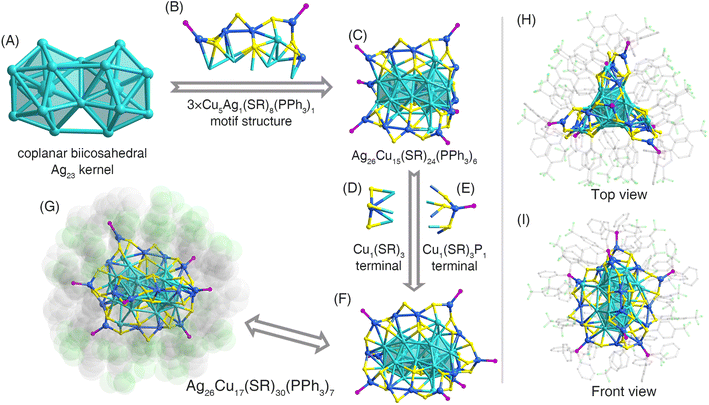 |
| Fig. 1 Structure analysis of a Ag26Cu17(SR)30(PPh3)7 nanocluster. (A) The coplanar biicosahedral Ag23 kernel. (B) Three Cu5Ag1(SR)8(PPh3)2 motif structures. (C) The Ag26Cu15(SR)24(PPh3)6 structure. (D and E) Cu1(SR)3 and Cu1(SR)3(PPh3)1 terminal units. (F and G) Overall structure of the Ag26Cu17(SR)30(PPh3)7 nanocluster. (H and I) Top view and front view of the Ag26Cu17(SR)30(PPh3)7 nanocluster. Color labels: light blue, Ag; blue, Cu; yellow, S; magenta, P; grey, C; green, Cl. For clarity, all H atoms are omitted. | |
The size-maintained transformation from the bimetallic (AgCu)43 nanocluster into its trimetallic derivative, (AuAgCu)43, was triggered by slight Au-alloying, i.e., introducing 0.75 mg of Au(PPh3)Cl to the solution containing 10 mg of the cluster. Of note, a Cl1Ag8Cu6(SR)12(PPh3)6 ((AgCu)14 for short) nanocluster was also obtained with this Au-alloying process, contributing a cocrystallized system together with the (AuAgCu)43 nanocluster (see below). Actually, we have also tried to add 0.25 or 0.5 mg of Au(PPh3)Cl to the same cluster solution, which also yielded the (AuAgCu)43·(AgCu)14 cocrystallized system, while the yield was decreased relative to the 0.75 mg Au(PPh3)Cl addition. The (AuAgCu)43 nanocluster followed the same configuration as that of the (AgCu)43 precursor, while the innermost two Ag cores of the biicosahedral Ag23 kernel in (AgCu)43 were substituted by the introduced Au heteroatoms along with the Au doping (Fig. 2A–C). The corresponding bond lengths between (AgCu)43 and (AuAgCu)43 nanoclusters were compared (Fig. S6†). Although the average bond length of M(icosahedral kernel)–Ag(icosahedral surface) was the same between two 43-metal-atom nanoclusters, the bond lengths in (AuAgCu)43 nanoclusters were more uniform (Fig. S6A†). Besides, most bond lengths of Ag(icosahedral surface)–Ag(icosahedral surface) in (AgCu)43 were much larger than those in (AuAgCu)43. By comparison, several corresponding peripheral M–S bonds (M = Ag/Cu) were extended along with the Au doping (Fig. S6B–D†). In this context, the (AuAgCu)43 nanocluster possessed a tighter internal connection than (AgCu)43, yet exhibited a looser surface connection, potentially attributed to the incorporation of gold heteroatoms with the biicosahedral kernel.
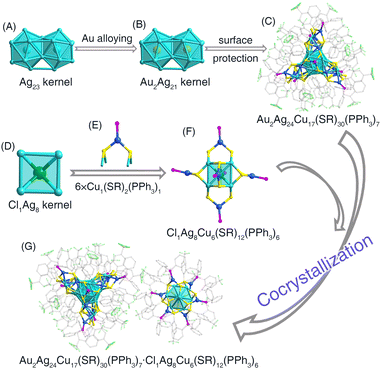 |
| Fig. 2 Structure analysis of the Au2Ag24Cu17(SR)30(PPh3)7·Cl1Ag8Cu6(SR)12(PPh3)6 cocrystallized nanocluster. (A and B) Au doping-induced alloying from the Ag23 kernel to the Au2Ag21 kernel. (C) Overall structure of the Au2Ag24Cu17(SR)30(PPh3)7 nanocluster. (D) Hexahedral Cl1Ag8 kernel. (E) Six Cu1(SR)2(PPh3)1 surface motif structures. (F) Overall structure of the Cl1Ag8Cu6(SR)12(PPh3)6 nanocluster. (G) Cocrystallized Au2Ag24Cu17(SR)30(PPh3)7 and Cl1Ag8Cu6(SR)12(PPh3)6 nanoclusters. Color labels: light blue, Ag; blue, Cu; yellow, S; magenta, P; grey, C; green, Cl. For clarity, all H atoms are omitted. | |
The (AgCu)14 cluster molecules were observed in the crystal lattice of (AuAgCu)43 with a mole ratio of 1/2 of (AgCu)14/(AuAgCu)43. The (AgCu)14 nanocluster should be generated along with the Au alloying and could be attributed to the decomposition of some (AgCu)43 nanoclusters. The structure of the (AgCu)14 nanocluster could be divided into two components: the cubic Cl1Ag8 kernel and six Cu1(SR)2(PPh3)1 surface structures (Fig. 2D and E). Each face of the Ag8 cube was capped with a Cu1(SR)2(PPh3)1 unit (Fig. 2F). From the perspective of the crystalline assembly, the cocrystallization system of (AuAgCu)43 and (AgCu)14 nanoclusters displayed an “AA′B–AA′B” packing pattern along the c-axis (Fig. 2G and S7†). Abundant intramolecular and intermolecular interactions were observed among nanoclusters in the crystal lattice. Specifically, for 18 nanocluster molecules (six (AgCu)14 and twelve (AuAgCu)43) in a unit cell, each (AgCu)14 nanocluster was enveloped by five (AuAgCu)43 nanocluster molecules, while each (AuAgCu)43 nanocluster was surrounded by four (AgCu)14 and four (AuAgCu)43 nanocluster molecules (Fig. S8†). Abundant intramolecular π⋯π, C–H⋯π, and C–H⋯F interactions were also observed in (AuAgCu)43 and (AgCu)14 nanoclusters at the molecular level (Fig. S8†). Furthermore, several intermolecular C–H⋯π and C–H⋯F interactions were detected between adjacent (AgCu)14 and (AuAgCu)43 nanoclusters, with an average distance of 2.889 Å for C–H⋯π and 2.765 Å for C–H⋯F (Fig. S10†). These weak forces collectively contributed to the formation of the cocrystallized system.
The (AgCu)43 nanocluster underwent size disproportionation induced by a heavy Au-doping process, leading to the formation of size-reduced (AuAgCu)33 and size-increased (AuAgCu)56 nanoclusters. The (AuAgCu)56 cluster molecules were crystallized in a P21/c space group, whereas the (AuAgCu)33 molecules were crystallized in the P
space group. The structure anatomies of (AuAgCu)33 and (AuAgCu)56 are illustrated in Fig. 3. The overall structure of (AuAgCu)33 comprised an icosahedral Au1Ag12 kernel that was enwrapped by two Ag3Cu7(SR)8(PPh3)2 surface structures and six bridging SR ligands, making up an Au1Ag18Cu14(SR)14(PPh3)6 structure (Fig. 3A–D). Then, Au1Ag18Cu14(SR)14(PPh3)6 was stabilized by two bare sulfur ligands, likely derived from the thiol, forming the framework of the Au1Ag18Cu14S2(SR)14(PPh3)6 nanocluster (Fig. 3E–G).56,57 Besides, the structure of (AuAgCu)56 contained a biicosahedral Au2Ag21 kernel that was the same as that in (AuAgCu)43 (Fig. 3H). Such a planar Au2Ag21 kernel was capped by three Ag2Cu8(SR)8(PPh3)2Cl2 side motif structures, three Cu1(SR)2(PPh3)1Cl1 surface motif structures, and two bridging Cl ligands to constitute an Au2Ag27Cu27(SR)30(PPh3)9Cl11 structure (Fig. 3I–L). Furthermore, three bare S ligands were arranged inside the Au2Ag27Cu27(SR)30(PPh3)9Cl11 structure, making up the final Au2Ag27Cu27S3(SR)30(PPh3)9Cl11 framework (Fig. 3M–O). The complete structure of (AuAgCu)33 or (AuAgCu)56 was triple axisymmetric with a C3 symmetry axis passing through the center of the Au1Ag12 kernel or the Au2Ag21 kernel, respectively (Fig. S11†). The bond lengths between (AuAgCu)33 and (AuAgCu)56 nanoclusters were compared, and we found that most corresponding bonds in (AuAgCu)56 were slightly longer than those in (AuAgCu)33 (Fig. S12†).
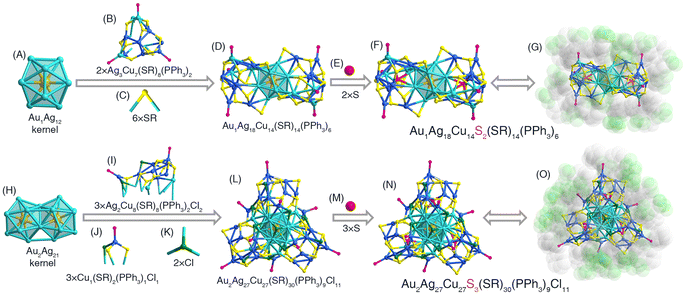 |
| Fig. 3 Structure analyses of (AuAgCu)33 and (AuAgCu)56 nanoclusters. (A) Icosahedral Au1Ag12 kernel. (B) Two Ag3Cu7(SR)8(PPh3)2 surface structures. (C) Six bridging SR ligands. (D) The Au1Ag18Cu14(SR)14(PPh3)6 structure. (E) Two bare sulfur ligands. (F and G) Overall structures of the Au1Ag18Cu14S2(SR)14(PPh3)6 nanocluster. (H) Biicosahedral Au2Ag21 kernel. (I) Three Ag2Cu8(SR)8(PPh3)2Cl2 motif structures. (J) Three Cu1(SR)2(PPh3)1Cl1 surface structures. (K) Two bridging Cl ligands. (L) The Au2Ag27Cu27(SR)30(PPh3)9Cl11 structure. (M) Three bare sulfur ligands. (N and O) Overall structures of the Au2Ag27Cu27S3(SR)30(PPh3)9Cl11 nanocluster. Color labels: light blue, Ag; blue, Cu; yellow, S in thiol ligands; red, bare S ligands; magenta, P; grey, C; green, Cl. For clarity, all H atoms are omitted. | |
The nanocluster transformation was also detectable by analyzing the optical absorption. The ultraviolet-visible (UV-vis) spectrum of (AgCu)43 showed continuous optical absorptions with four peaks centered at 445, 537, 662, and 765 nm (Fig. 4A, blue line). After slight Au alloying, tetrametallic (AuAgCu)43 exhibited inapparent blue-shifts relative to (AgCu)43, and four peaks at 444, 535, 659, and 763 nm were observed (Fig. 4A, purple line). For the size disproportionation process, three absorption peaks at 421, 515, and 621 nm were observed for (AuAgCu)56 (Fig. 4A, green line) and two UV-vis signals at 417 and 541 nm for (AuAgCu)33 (Fig. 4A, brown line).
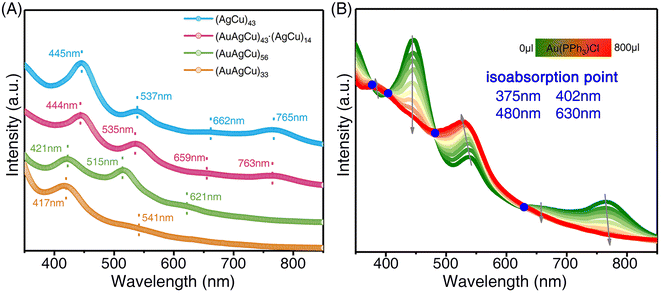 |
| Fig. 4 Comparison of the optical absorption properties. (A) UV-vis absorption spectra of (AgCu)43 (blue line), (AuAgCu)43·(AgCu)14 (purple line), (AuAgCu)56 (green line), and (AuAgCu)33 (brown line) nanoclusters. (B) Au doping-dependent UV-vis absorption of the size disproportionation process. | |
To further explore the size disproportionation reaction, Au doping-dependent UV-vis absorption was monitored (Fig. 4B). The absorption peaks at 445, 662, and 765 nm decreased with increasing Au doping. Additionally, the peaks at 582 nm underwent a blue shift to 537 nm, and a new absorption peak emerged at 383 nm. Besides, four isoabsorption points, centering at 375, 402, 480, and 630 nm, were observed. Such isoabsorption points demonstrated that the nanocluster transformation followed an in situ distortion-transformation pattern at the beginning of the Au-alloying process. In addition, since the nanocluster transformation products of the size disproportionation reaction should be a mixture, thin-layer chromatography (TLC) was exploited to separate the nanocluster mixture (Fig. S13†).58 Two separated TLC bands were observed, and the corresponding products were determined as (AuAgCu)33 and (AuAgCu)56 nanoclusters by referring to the optical absorption of pure products. For the thermal stability of the obtained (AuAgCu)56 or (AuAgCu)33 nanoclusters, both nanoclusters were stable at 60 °C. However, the nanoclusters underwent decomposition with a further increase in temperature (Fig. S14†).
Considering that the size disproportionated (AuAgCu)56 and (AuAgCu)33 nanoclusters might not generate simultaneously but could convert into each other, we added AuPPh3Cl to the solution of (AuAgCu)56 or (AuAgCu)33 nanoclusters. (AuAgCu)56 maintained its optical absorption with the addition of AuPPh3Cl, while (AuAgCu)33 gradually decomposed in the presence of AuPPh3Cl (Fig. S15†), and no (AuAgCu)56 was separated by TLC from these decomposition products. In this context, the (AuAgCu)56 and (AuAgCu)33 nanoclusters were not generated in the chronological order but were transformed from the same cluster precursor (AuAgCu)43 at the same time, further indicating size disproportionation among the nanocluster transformations. Collectively, the transformation from (AuAgCu)43 into (AuAgCu)33 and (AuAgCu)56 could be summarized as a size disproportionation reaction-(AuAgCu)43 was transformed into a size-reduced (AuAgCu)33 nanocluster and a size-increased (AuAgCu)56 nanocluster in the presence of heavy Au dopants.
4 Conclusions
In summary, a bimetallic (AgCu)43 nanocluster underwent selective size transformations under the controllable Au doping process. The slight Au alloying gave rise to a size-maintained transformation from (AgCu)43 into (AuAgCu)43, which was cocrystallized with (AgCu)14 in the same crystalline unit cell. By comparison, the heavy Au alloying resulted in a size-disproportionation transformation from (AgCu)43 into size-increased (AuAgCu)56 and size-reduced (AuAgCu)33. The thin layer chromatography results demonstrated the generation of (AuAgCu)56 and (AuAgCu)33 nanoclusters from (AgCu)43 simultaneously, further suggesting size disproportionation among the nanocluster transformations. This work presented an important cluster platform for studying the size-maintained and size-altered transformations of metal nanoclusters, allowing for some new insights into cluster structure evolutions.
Data availability
The data that support the findings of this study are available in the ESI† of this article.
Author contributions
C. Z. and L. L. carried out experiments and analyzed the data. F. L. assisted the data analysis. X. K. and M. Z. designed the project, analyzed the data, and wrote the manuscript.
Conflicts of interest
There are no conflicts to declare.
Acknowledgements
We acknowledge the financial support of the NSFC (22371003, 22101001, and 22471001), the Ministry of Education, the University Synergy Innovation Program of Anhui Province (GXXT-2020-053), and the Scientific Research Program of Universities in Anhui Province (2022AH030009).
Notes and references
- R. Jin, C. Zeng, M. Zhou and Y. Chen, Chem. Rev., 2016, 116, 10346–10413 CrossRef CAS PubMed.
- I. Chakraborty and T. Pradeep, Chem. Rev., 2017, 117, 8208–8271 CrossRef CAS PubMed.
- M. F. Matus and H. Häkkinen, Nat. Rev. Mater., 2023, 8, 372–389 CrossRef CAS.
- X. Kang and M. Zhu, Chem. Soc. Rev., 2019, 48, 2422–2457 RSC.
- S. Kenzler and A. Schnepf, Chem. Sci., 2021, 12, 3116–3129 RSC.
- E. L. Albright, T. I. Levchenko, V. K. Kulkarni, A. I. Sullivan, J. F. DeJesus, S. Malola, S. Takano, M. Nambo, K. Stamplecoskie, H. Häkkinen, T. Tsukuda and C. M. Crudden, J. Am. Chem. Soc., 2024, 146, 5759–5780 CrossRef CAS PubMed.
- K. Isozaki, K. Iseri, R. Saito, K. Ueda and M. Nakamura, Angew. Chem., Int. Ed., 2024, 63, e202312135 CrossRef CAS PubMed.
- M. Bai, L. Qin, X.-M. Z, M. Wu, L.-Y. Yao and G.-Y. Yang, J. Am. Chem. Soc., 2024, 146, 12734–12742 CrossRef CAS PubMed.
- Y. Koizumi, K. Yonesato, S. Kikkawa, S. Yamazoe, K. Yamaguchi and K. Suzuki, J. Am. Chem. Soc., 2024, 146, 14610–14619 CrossRef CAS PubMed.
- H. Yi, S. Song, S. M. Han, J. Lee, W. Kim, E. Sim and D. Lee, Angew. Chem., Int. Ed., 2023, 62, e202302591 CrossRef CAS PubMed.
- D. Arima, S. Hidaka, S. Yokomori, Y. Niihori, Y. Negishi, R. Oyaizu, T. Yoshinami, K. Kobayashi and M. Mitsui, J. Am. Chem. Soc., 2024, 146, 16630–16638 CrossRef CAS PubMed.
- L.-J. Liu, F. Alkan, S. Zhuang, D. Liu, T. Nawaz, J. Guo, X. Luo and J. He, Nat. Commun., 2023, 14, 2397 CrossRef CAS PubMed.
- Q. You, X.-L. Jiang, W. Fan, Y.-S. Cui, Y. Zhao, S. Zhuang, W. Gu, L. Liao, C.-Q. Xu, J. Li and Z. Wu, Angew. Chem., Int. Ed., 2024, 63, e202313491 CrossRef CAS PubMed.
- S. Takano, H. Hirai, T. Nakashima, T. Iwasa, T. Taketsugu and T. Tsukuda, J. Am. Chem. Soc., 2021, 143, 10560–10564 CrossRef CAS PubMed.
- J.-H. Huang, Y.-J. Liu, Y. Si, Y. Cui, X.-Y. Dong and S.-Q. Zang, J. Am. Chem. Soc., 2024, 146, 16729–16736 CrossRef CAS PubMed.
- C. A. Hosier and C. J. Ackerson, J. Am. Chem. Soc., 2019, 141, 309–314 CrossRef CAS PubMed.
- C. Zhang, W.-D. Si, Z. Wang, A. Dinesh, Z.-Y. Gao, C.-H. Tung and D. Sun, J. Am. Chem. Soc., 2024, 146, 10767–10775 CrossRef CAS PubMed.
- X. Luo, J. Kong, H. Xiao, D. Sang, K. He, M. Zhou and J. Liu, Angew. Chem., Int. Ed., 2024, 63, e202404129 CrossRef CAS PubMed.
- B. Alamer, A. Sagadevan, M. Bodiuzzaman, K. Murugesan, S. Alsharif, R.-W. Huang, A. Ghosh, M. H. Naveen, C. Dong, S. Nematulloev, J. Yin, A. Shkurenko, M. Abulikemu, X. Dong, Y. Han, M. Eddaoudi, M. Rueping and O. M. Bakr, J. Am. Chem. Soc., 2024, 146, 16295–16305 CrossRef CAS PubMed.
- Z. Liu, J. Chen, B. Li, D.-e. Jiang, L. Wang, Q. Yao and J. Xie, J. Am. Chem. Soc., 2024, 146, 11773–11781 CrossRef CAS PubMed.
- T. Kawawaki, Y. Kataoka, M. Hirata, Y. Akinaga, R. Takahata, K. Wakamatsu, Y. Fujiki, M. Kataoka, S. Kikkawa, A. S. Alotabi, S. Hossain, D. J. Osborn, T. Teranishi, G. G. Andersson, G. F. Metha, S. Yamazoe and Y. Negishi, Angew. Chem., Int. Ed., 2021, 60, 21340 CrossRef CAS PubMed.
- W.-Q. Shi, L. Zeng, R.-L. He, X.-S. Han, Z.-J. Guan, M. Zhou and Q.-M. Wang, Science, 2024, 383, 326–330 CrossRef CAS PubMed.
- X. Wang, B. Yin, L. Jiang, C. Yang, Y. Liu, G. Zou, S. Chen and M. Zhu, Science, 2023, 381, 784–790 CrossRef CAS PubMed.
- G. Deng, H. Yun, M. S. Bootharaju, F. Sun, K. Lee, X. Liu, S. Yoo, Q. Tang, Y. J. Hwang and T. Hyeon, J. Am. Chem. Soc., 2023, 145, 27407–27414 CrossRef CAS PubMed.
- Q. Liu, X.-Y. Zhai, R.-J. Jian and L. Zhao, Chem. Sci., 2024, 15, 11311–11320 RSC.
- X. Wei, H. Li, H. Li, Z. Zuo, F. Song, X. Kang and M. Zhu, J. Am. Chem. Soc., 2023, 145, 13750–13757 CrossRef CAS PubMed.
- X. Wei, K. Chu, J. R. Adsetts, H. Li, X. Kang, Z. Ding and M. Zhu, J. Am. Chem. Soc., 2022, 144, 20421–20433 CrossRef CAS PubMed.
- R. Saito, K. Isozaki, Y. Mizuhata and M. Nakamura, J. Am. Chem. Soc., 2024, 146, 20930–20936 CrossRef CAS PubMed.
- C. Zhang, W.-D. Si, Z. Wang, C.-H. Tung and D. Sun, Angew. Chem., Int. Ed., 2024, 63, e202404545 CrossRef CAS PubMed.
- F. Sun, L. Qin, Z. Tang, G. Deng, M. S. Bootharaju, Z. Wei, Q. Tang and T. Hyeon, Chem. Sci., 2023, 14, 10532–10546 RSC.
- Z. Wang, R. K. Gupta, F. Alkan, B.-L. Han, L. Feng, X.-Q. Huang, Z.-Y. Gao, C.-H. Tung and D. Sun, J. Am. Chem. Soc., 2023, 145, 19523–19532 CrossRef CAS PubMed.
- X. Kang, L. Huang, W. Liu, L. Xiong, Y. Pei, Z. Sun, S. Wang, S. Wei and M. Zhu, Chem. Sci., 2019, 10, 8685–8693 RSC.
- P. Chandrashekar, G. Sardar, T. Sengupta, A. C. Reber, P. K. Mondal, D. Kabra, S. N. Khanna, P. Deria and S. Mandal, Angew. Chem., Int. Ed., 2024, 63, e202317345 CrossRef CAS PubMed.
- Y. Saito, A. Suda, M. Sakai, S. Nakajima, Y. Shichibu, H. Kanai, Y. Ishida and K. Konishi, Chem. Sci., 2024, 15, 11775–11782 RSC.
- J. Liu, Y. Sato, V. K. Kulkarni, A. I. Sullivan, W. Zhang, C. M. Crudden and J. E. Hein, Chem. Sci., 2023, 14, 10500–10507 RSC.
- S. Gratious, S. Mukherjee and S. Mandal, J. Phys. Chem. Lett., 2022, 13, 9014–9027 CrossRef CAS PubMed.
- T.-A. D. Nguyen, Z. R. Jones, D. F. Leto, G. Wu, S. L. Scott and T. W. Hayton, Chem. Mater., 2016, 28, 8385–8390 CrossRef CAS.
- K. Yonesato, S. Yamazoe, S. Kikkawa, D. Yokogawa, K. Yamaguchi and K. Suzuki, Chem. Sci., 2022, 13, 5557–5561 RSC.
- A. Jana, M. Jash, A. K. Poonia, G. Paramasivam, M. R. Islam, P. Chakraborty, S. Antharjanam, J. Machacek, S. Ghosh, K. N. V. D. Adarsh, T. Base and T. Pradeep, ACS Nano, 2021, 15, 15781–15793 CrossRef CAS PubMed.
- J. A. Kephart, C. G. Romero, C.-C. Tseng, K. J. Anderton, M. Yankowitz, W. Kaminsky and A. Velian, Chem. Sci., 2020, 11, 10744–10751 RSC.
- L.-L. Yan, L.-Y. Yao, M.-Y. Leung and V. W.-W. Yam, CCS Chem., 2021, 3, 326–337 CrossRef CAS.
- L. Yang, X.-Y. Wang, X.-Y. Tang, M.-Y. Wang, C.-Y. Ni, H. Yu, Y.-L. Song, B. F. Abrahams and J.-P. Lang, Sci. China: Chem., 2022, 65, 1094–1099 CrossRef CAS.
- Z. Wang, H.-F. Su, C.-H. Tung, D. Sun and L.-S. Zheng, Nat. Commun., 2018, 9, 4407 CrossRef PubMed.
- Z. Wang, Y.-J. Zhu, Y.-Z. Li, G.-L. Zhuang, K.-P. Song, Z.-Y. Gao, J.-M. Dou, M. Kurmoo, C.-H. Tung and D. Sun, Nat. Commun., 2022, 13, 1802 CrossRef CAS PubMed.
- Z. Wang, J.-W. Liu, H.-F. Su, Q.-Q. Zhao, Mo. Kurmoo, X.-P. Wang, C.-H. Tung, D. Sun and L.-S. Zheng, J. Am. Chem. Soc., 2019, 141, 17884–17890 CrossRef CAS PubMed.
- Y. Li, H. K. Kim, R. D. McGillicuddy, S.-L. Zheng, K. J. Anderton, G. J. Stec, J. Lee, D. Cui and J. A. Mason, J. Am. Chem. Soc., 2023, 145, 9304–9312 CrossRef CAS PubMed.
- T. Ree, J. Chem. Educ., 1971, 48, 467 CrossRef CAS.
- S. Zhu, L. Yang, Y. Long, M. Gao, T. Huang, W. Hang and X. Yan, J. Am. Chem. Soc., 2010, 132, 12176–12178 CrossRef CAS PubMed.
- A. Letzel, B. Gökce, A. Menzel, A. Plech and S. Barcikowski, Appl. Surf. Sci., 2018, 435, 743–751 CrossRef CAS.
- L. G. AbdulHalim, M. S. Bootharaju, Q. Tang, S. Del Gobbo, R. G. AbdulHalim, M. Eddaoudi, D.-e. Jiang and O. M. Bakr, J. Am. Chem. Soc., 2015, 137, 11970–11975 CrossRef CAS PubMed.
- X. Kang, S. Wang and M. Zhu, Chem. Sci., 2018, 9, 3062–3068 RSC.
- Y. Niihori, N. Takahashi and M. Mitsui, J. Phys. Chem. C, 2020, 124, 5880–5886 CrossRef CAS.
- X. Kang, Y. Li, M. Zhu and R. Jin, Chem. Soc. Rev., 2020, 49, 6443–6514 RSC.
- S. Jin, X. Zou, L. Xiong, W. Du, S. Wang, Y. Pei and M. Zhu, Angew. Chem., Int. Ed., 2018, 57, 16768 CrossRef CAS PubMed.
- X. Zou, S. He, X. Kang, S. Chen, H. Yu, S. Jin, D. Astruc and M. Zhu, Chem. Sci., 2021, 12, 3660–3667 RSC.
- D. Crasto, S. Malola, G. Brosofsky, A. Dass and H. Häkkinen, J. Am. Chem. Soc., 2014, 136, 5000–5005 CrossRef CAS PubMed.
- X. Wei, C. Xu, H. Li, X. Kang and M. Zhu, Chem. Sci., 2022, 13, 5531–5538 RSC.
- A. Ghosh, J. Hassinen, P. Pulkkinen, H. Tenhu, R. H. A. Ras and T. Pradeep, Anal. Chem., 2014, 86, 12185–12190 CrossRef CAS PubMed.
Footnotes |
† Electronic supplementary information (ESI) available: Fig. S1–S15 and Tables S1–S4. CCDC 2370220–2370223. For ESI and crystallographic data in CIF or other electronic format see DOI: https://doi.org/10.1039/d4sc04884a |
‡ C. Z. and L. L. contributed equally to this work. |
|
This journal is © The Royal Society of Chemistry 2024 |
Click here to see how this site uses Cookies. View our privacy policy here.