Upcycled waxes from mixed polyolefins for hot-melt adhesive (HMA) applications†
Received
20th March 2024
, Accepted 4th September 2024
First published on 9th September 2024
Abstract
Upcycled waxes are blended with poly(ethylene-co-vinyl acetate) (EVA) to make hot-melt adhesives (HMAs). Herein, we report partially recycled HMAs that were prepared by blending EVA with upcycled waxes obtained from mix waste polyolefins. First, waste mixed polyolefins (such as high-density, low-density, and linear low-density polyethylene and polypropylene) were converted into waxes in high yields reaching up to 92%. The obtained upcycled waxes were used as an additive for HMAs along with gum rosin. The thermal properties and seal strength of the HMAs containing upcycled waxes were compared with those of commercially available HMAs. The HMA made from upcycled wax was found to be as efficient in seal strength as the commercially available HMA. This upcycling of plastic waste for use in HMAs is yet another way of promoting circularity in single-use plastics.
Sustainability spotlight
The ecosystem is seriously threatened by the growing volume of mixed plastic waste that is improperly disposed of. The major plastic waste is polyolefins, such as polypropylene and polyethylene. This work offers an innovative, sustainable solution to this problem by upcycling waste mixed polyolefin into waxes that can be used in hot-melt adhesive (HMA) applications. By upcycling and recycling plastic waste, this sustainable strategy not only reduces plastic waste but also promotes circularity. Our work is in line with UN Sustainable Development Goals (SDGs) 9 (Industry, Innovation and Infrastructure), 12 (Responsible Consumption and Production), and 13 (Climate Action) because we use upcycled waxes made from plastic waste. Through sustainable advancements like this, we contribute to a more resource-efficient and environmentally conscious future.
|
Introduction
Hot melt adhesives (HMAs) are thermoplastic adhesives that are applied as melt-adhesives via heating, which gain strength upon cooling.1–3 HMAs are inexpensive, solvent-free, water-resistant, and are compatible with high-speed manufacturing processes, and thus they are widely employed in numerous industries.1,3 HMAs have been widely used in the packaging sector, and their adoption has experienced rapid growth over the years.4 In the furniture industry, HMAs connect metal to metal, and one of the key advantages of these adhesives is that they are reversible (dismantlable adhesives).5,6 In addition, HMAs are used in the production of mattresses, as glue for wood, thick paper, nonwovens, and for connecting plastics.7 HMAs are also used as adhesives where disassembly is desirable after use, as they can provide reversible adhesion.8–11
HMAs are composed of copolymer poly(ethylene-co-vinyl acetate) (EVA), a plasticizer, and an adhesive, which is made up of tackifiers, waxes, and optionally inorganic fillers.12 Waxes comprise up to 30 wt% of the adhesive formulation. For HMAs, waxes are required to decrease the viscosity of the melt adhesive to offer better flow and uniform surface coverage during adhesive applications, as well as to reduce the application temperature.13 Waxes also enhance the hardening rate of the adhesives and improve their cohesive strength, thus speeding up the manufacturing process.14–17
The most commonly utilized waxes used in HMA formulations are Fischer–Tropsch (F–T) waxes, microcrystalline waxes, and paraffin waxes.15 Paraffin wax is soft and has a low melting temperature. F–T waxes are more suitable for HMAs designed for high-temperature applications. When wax is melted, it reduces the viscosity of the mixture, thereby making it easier to mix the components. When it cools, it crystallizes and forms a structural network that gives the HMA its hardness and strength.18 Using viscoelastic properties and failure mode measurements, the impact of wax on the adhesive strengths and miscibility with EVA/rosin can be determined.19–21 The pivotal role of wax in the adhesion performance of HMAs has been relatively well-explored in the past.15,22,23
Mixed plastics are difficult to recycle and end up in landfills. Nearly 60% of all plastic waste is made of polyolefins (PE and PP). PE alone makes up over 50% of the weight of all polymers in mixed plastic waste (MPW).24,25 Efforts to develop chemical recycling strategies for PE have often focused on the conversion of these materials into gas and oil through pyrolysis. We have recently reported the conversion of HDPE into upcycled waxes in a very high yield (up to 93%),26 as well as the upcycling of wax from mixed polyethylene (high-density and low-density polyethylene) at almost the same yield.27 The initial cost estimation analysis suggests that these newly reported plastic-to-wax conversions offer a practical approach for waste plastic upcycling.
Herein we report waxes obtained in high yield from mixed HDPE, linear low-density polyethylene (LLDPE), low-density polyethylene (LDPE), and polypropylene (PP). Both temperature and time were controlled during this process to obtain waxes as the major product with tailored melting temperatures. The obtained waxes were tested as hot melt adhesive formulation additives. In addition, we investigated the effect of using various recycled waxes at different weight percentages (wt%) in HMAs, and the best waxes and wt% were validated via thermal sealing temperature and seal strength. Our wax-derived HMA can be used in the huge HMA market valued at over 7.49 billion USD in 2023 and is projected to grow from 7.89 billion USD in 2024 to 11.76 billion USD by 2032, exhibiting a compound annual growth rate (CAGR) of 5.2% during the forecast period.28
Experimental
Materials
The waste plastics were obtained from Michigan State University (MSU) Surplus and Recycling Center, Michigan, United States. Different sized HDPE, LDPE, LLDPE and PP bottles and plastics were obtained from a local store and identified based on their resin identification code. These plastics were then washed with detergents to remove any fats, then cut into flakes, and subsequently dried at room temperature. Finally, they were ground into a powder to obtain the MWP, which would be used for subsequent pyrolysis experiments. Sodium chloride (NaCl) was purchased from Fisher Chemical. EVA and gum rosin natural resin were purchased from Sigma Aldrich.
General procedure of wax recovery
An autoclave reactor was filled with mixed waste plastics (ground) and 10 wt% of NaCl. The autoclave reactor was completely wrapped with aluminum foil to maintain the pyrolysis temperature inside the reactor, and the reactor was heated using a heating mantle at 450 °C (see Table 1) for the optimized operation time. The wax was upcycled using hot-water dispersion, to ensure the complete dissolution of NaCl, followed by cooling, and then the solid wax was collected from the top of the water surface (ESI, Fig. 1†). The obtained waxes were washed several times with DIO water and dried in an oven at 40 °C for 24 h.
Table 1 Pyrolysis conditions, pyrolytic wax yields, and characterization details.a
Exp.# |
Pyrolysis condition |
Pyrolytic crude waxb (wt%) |
Wax thermal propertiesd |
M
w g mol−1 |
Mixing |
Time/temp. |
Oil/volatile materialsc |
Waxc |
T
m (°C) |
T
c (°C) |
T
d (°C) |
MWP: mixed waste plastic.
Isolated yield using boiling water.
Calculated from TGA analysis.
Predicted based on the melting temperature using: https://www.engineeringtoolbox.com/hydrocarbon-boiling-melting-flash-autoignition-point-density-gravity-molweight-d_1966.html. *Denotes samples that were treated with a shorter pyrolysis time.
|
Blank |
MWP blank |
136 |
117 |
447 |
|
Wax A |
MWP (10 g)/NaCl (1 g) |
2 h/450 °C |
84% |
109 |
96 |
425 |
1011 |
2.4% |
81.6% |
Wax B |
3 h/450 °C |
81% |
106 |
91 |
422 |
975 |
1.6% |
79.4% |
Wax C |
4 h/450 °C |
60% |
93 |
77 |
413 |
703 |
3.6% |
56.4% |
Wax D |
5 h/450 °C |
30% |
38 |
30 |
175 |
282 |
3.6% |
26.4% |
Wax E |
MWP (30 g)/NaCl (3 g) |
8 h/450 °C |
93% |
118 |
106 |
426 |
1441 |
2.8% |
90.2% |
Wax F |
MWP (50 g)/NaCl (5 g) |
12/450 °C |
82% |
109 |
97 |
413 |
1011 |
4.1% |
77.9% |
Methodology for creating an adhesive blend
Three ingredients were used to create a hot melt adhesive. The first ingredient was the polymer ethylene-vinyl acetate (EVA) 40 wt%, with a melt index of 41–63° min−1 and 190 °C/2.16 kg, and it was obtained in pellet form (Sigma Aldrich, St. Louis, MO). The second ingredient was gum rosin natural resin, which was in coarse powder form (Sigma Aldrich, St. Louis, MO). The third ingredient we used was the wax created from mixed waste plastic by the pyrolysis process mentioned for the wax-E sample in a closed reactor/autoclave at 425 °C. The reason for selecting the wax-E sample is the scale of the process. The three components were melted and blended in a 100 mL beaker at a temperature of 210 °C for 60 min at a stirrer speed of 350 rpm. Blends were prepared in the ratio of 40/30/30 for EVA/gum rosin/wax solution by dissolving the components in chloroform (at a concentration of 5% by volume) (Fisher Scientific, Hampton, NH). Chloroform was used to reduce the viscosity while mixing the molten blends. The blend was then vacuum-dried at room temperature for 24 h to remove solvent residue. A schematic representation of the HMA preparation process is shown in Fig. 3. EVA was the main component of the adhesive, gum rosin acted as the tackifier for the adhesive's composition, and the mixed waste wax was used as the rheology modifier or plasticizer.
Methodology to create a glue gun stick
The adhesive blend was reheated in a 100 mL beaker at 210 °C and poured inside a commercially available hollow Teflon tube with an inner diameter of 9 mm to mold it into the shape of a glue gun stick cast inside the tube. The molten glue blend inside the Teflon tube was then kept in a refrigerator for 24 h to attain the shape of the glue stick, as shown in Fig. 3. After cooling and attaining the shape after 24 h, the tube was cut to remove the glue gun stick.
Results and discussion
Synthesis of upcycled waxes
MPW, which is commonly sent to landfills, was used as feedstock for upcycled waxes. As a general strategy, 10 grams of MPW were pyrolyzed with 10 wt% sodium chloride for different time periods, such as 2.0, 3.0, 4.0, and 5.0 h, as shown in Table 1. The role of table salt in promoting pyrolysis processes has been recently reported.26,27 After pyrolysis, the resultant waxes were upcycled via a hot-water dispersion approach (Fig. S1†). This hot-water dispersion approach is simple and very effective, as the sodium chloride can be easily separated from wax. The obtained waxes are ready to use for HMA applications, and sodium chloride can be reused for pyrolysis after the necessary drying step. The upcycled waxes obtained from this process varied from hard to soft based on the pyrolysis reactor residence time. The obtained wax yields were 84%, 81%, 60%, and 30% (these waxes are respectively denoted as Wax A, Wax B, Wax C, and Wax D, as shown in Table 1) corresponding to pyrolysis operation times of 2.0, 3.0, 4.0, and 5.0 h, respectively. The gas and oil contents increased with the operation time, and the softness of the obtained wax increased as well. For 30 g of MPW, the pyrolysis process was conducted for 8 h at 450 °C. During these experiments performed at the 30 g MPW scale, the yield of the upcycled wax was 93% (this wax is denoted as Wax E, as shown in Table 1). In another trial conducted with 50 g of MPW and 12 h of pyrolysis time, the yield of the resultant wax (Wax F) was 82%, as shown in Table 1. Photographs of the obtained waxes are shown in Fig. 1a.
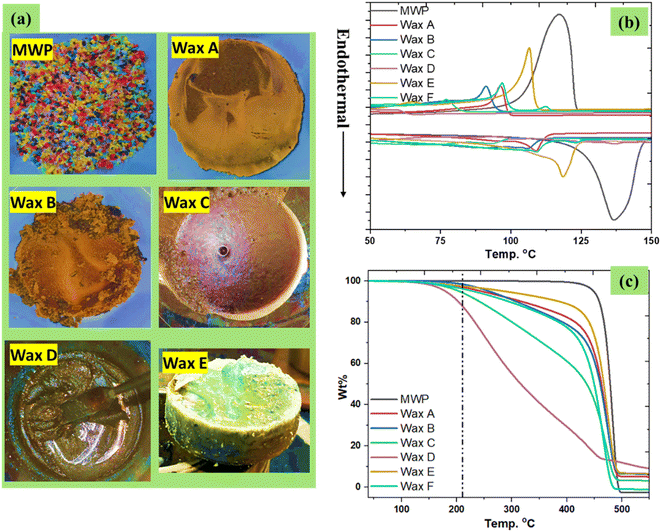 |
| Fig. 1 Wax formation from MWP and their thermal analysis. (a) Photographs of the obtained pyrolytic waxes obtained from MWP, including Wax (A–E). (b) DSC curves of the obtained waxes from the MWP (c) TGA curves of the obtained waxes from MWP, with a heating rate of 10 °C min−1 under a nitrogen atmosphere. | |
The DSC analysis revealed the melting temperature (Tm) and the crystallization temperature (Tc) of the resulting waxes (Fig. 1b). Meanwhile, the MPW sample was found to have Tm and Tc values of 136 and 117 °C, respectively.
In general, the Tm and Tc of the resulting waxes are decreased by increasing the pyrolysis reaction time. For the 10 g scale experiments, the obtained Waxes A, B, and C exhibited Tm values of 109, 106 and 93 °C and Tc values o 96, 91, and 77 °C, respectively. Meanwhile, Wax D was viscous, and thus, it did not exhibit clear Tm and Tc temperatures. Wax E which was obtained from a larger-scale experiment using 30 g of MPW showed Tm and Tc values of 118 and 106 °C, while viscous Wax D did not show a clear Td temperature. Meanwhile, Wax F, which was obtained from the pyrolysis of 50 g of MPW for 12 h, exhibited Tm and Tc temperatures of 109 and 97 °C, respectively, which are similar to those of Wax A. The thermal stability of the resulting waxes was investigated with TGA analysis (Fig. 1c). The MPW sample decomposed at 447 °C, while the decomposition temperatures (Td) of the obtained waxes after pyrolysis were found to be 425, 422 and 413 °C for Wax A, Wax B, and Wax C, respectively, while Wax D had a Td of 175 °C. Wax E obtained from the 30 g scale experiment showed high thermal stability with a Td value of 426 °C. Recently, we had conducted a revenue analysis of upcycled wax, which shows an annual revenue of 14.87 million USD from 8400 tons of wax from mixed plastic. However, comparative studies are required to assess the economic feasibility of HMAs made from 30% recycled waxes. The same revenue could be achieved when these waxes are used for HMA applications.26,27
The obtained waxes also contained some low molecular weight volatile hydrocarbons. To quantify the actual wax amount, we excluded volatile contents from them. This was done by attributing any losses occurring at temperatures below 210 °C to volatile components. A temperature of 210 °C was selected because commercial paraffin waxes degrade at 210 °C and above.29–31 Consequently, 210 °C was used as the starting point to calculate the actual upcycled wax yield without any low molecular weight hydrocarbons. Losses detected above 210 °C were attributed to solid wax, while losses observed below these values were classified as liquid volatile compounds. Consequently, after deducting the volatile component contents, the actual wax contents for Wax A, Wax B, Wax C, and Wax D were found to be 81.6, 79.4, 56.4, and 26.4 wt%, respectively.
Proton nuclear magnetic resonance (1H-NMR) analysis revealed that the obtained waxes were mainly composed of saturated hydrocarbon chains, with a signal corresponding to terminal methyl-protons observed at 0.89 ppm and a signal corresponding to the methylene protons of the backbone chain at 1.26 ppm. The ratio of unsaturated protons (∼1%) is attributed to the presence of alkene protons at 4.6, 4.9, 5.4, and 5.8 ppm, representing both terminal and internal (–C
C–) bonds, and there are no aromatic protons visible in the spectra of the waxes (Fig. S1–S5†).
GC-MS analysis was also performed on the dichloromethane (DCM) soluble fractions of pyrolytic waxes (Wax A–Wax E). Prior to the GC-MS analysis, the wax was dissolved in DCM and then diluted 1000-fold in DCM. GC-MS analysis indicates that a normal series of hydrocarbon peaks was obtained (Fig. 2). The GC-MS of Wax C- and Wax D-soluble fractions showed a hydrocarbon distribution range of C15–C34, which is the range found in diesel fuel. For Wax B, the hydrocarbon was saturated, lacking carbon–carbon double bonds, with a carbon distribution range of C18–C34 (Fig. 2c and d). The hard waxes, such as Wax A and Wax E, showed random hydrocarbon distributions and possessed both saturated and unsaturated chains (Fig. 2a and e).
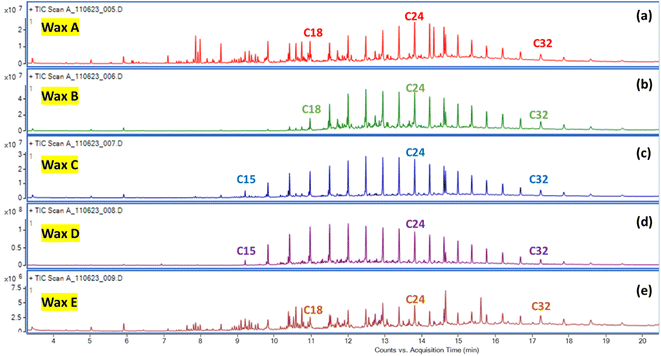 |
| Fig. 2 GC-MS analysis of the DCM soluble fractions of (a) Wax A, (b) Wax B, (c) Wax C, (d) Wax D, and (e) Wax E. | |
Creating an adhesive blend
EVA was mixed with gum rosin (a natural resin) and upcycled Wax E in a weight ratio of 40/30/30, respectively. To ensure a thorough mixing, hot mixing was performed at 210 °C for 1 h with stirring. To make a glue stick, the molten blend is cast into a Teflon tube to form a glue gun stick-like shape, as shown in Fig. 3. The Teflon tube was chosen because of its non-sticky nature.
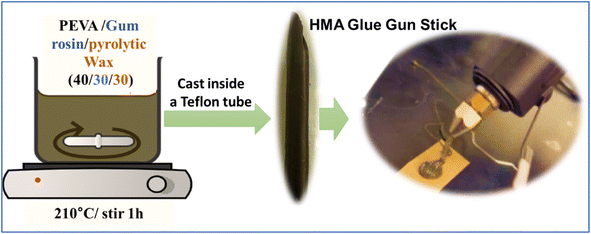 |
| Fig. 3 The schematics of preparation of a HMA using upcycled wax. | |
The physical characteristics of the commercial HMA (CHMA) and lab-made HMA (LHMA) adhesive blend were visually compared and are presented in Table S1.† The shape and consistency of both CHMA and LHMAs were very similar, and both samples became viscous fluids when they were heated. The set time for both adhesives was approximately 3–7 seconds.
Considering the growing need for resource conservation, there is an increased emphasis on incorporating recyclable content in new plastic articles sold in the market. This work involves the use of recycled low-cost wax derived from mixed-waste plastics, which offers economic benefits as well as conserves virgin wax materials that are currently used in HMAs. Additionally, there is a global push for mandatory recycled content, particularly in Europe and North America.32 The U.S. Plastic Pact33 has set a target of 30% recycled content in new plastic articles, and this presents a significant opportunity for our HMA to incorporate 30% recycled materials—a key selling point. The HMA market was valued at over 7.49 billion USD in 2023. It is projected to grow from 7.89 billion USD in 2024 to 11.76 billion USD by 2032, exhibiting a CAGR of 5.2% during the forecast period. Given this substantial growth, we foresee a clear path toward the commercialization of sustainable, recyclable HMAs.
Thermal characteristics of HMAs
Fig. 4 shows DSC and TGA curves and depicts data in table format. The DSC analysis, shown in Fig. 4A and B, shows that the thermal properties of LHMA resemble those of CHMA. For example, LHMA and CHMA have melting temperatures (Tm) of 118 and 108 °C, respectively. The crystallization temperature (Tc) of LHMA was found to be 106 °C, while that of CHMA was observed at 95 °C. The Tm and Tc of LHMA are typically the same as those of the upcycled Wax E, which represents 30 wt% of the HMA composition. The difference in melting and crystallization temperatures between CHMA and LHMA is attributed to the differences in compositions and types of waxes blended with the adhesives. The higher Tm of our LHMA provides it with advantages for use in the packaging line of corrugated fiberboard (CFB) boxes and cartons, even during warm seasons of the year, as well as during storage in warehouses.
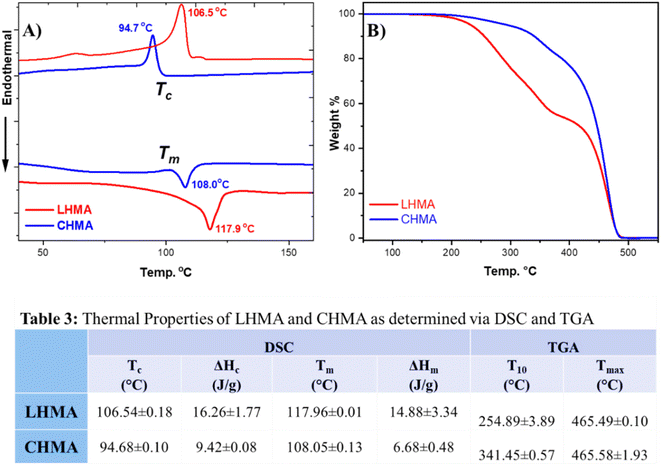 |
| Fig. 4 Up: (A) DSC curves recorded during the second heating cycle and cooling cycle of LHMA (red) and CHMA (blue) types of adhesives; (B) TGA curves recorded the degradation of the sample up to 600 °C, with LHMA shown in red and CHMA shown in blue; down: Table 3 the thermal properties of LHMA and CHMA were determined via DSC and TGA. | |
We can observe the difference in the TGA curves between the CHMA and LHMA, as shown in Fig. 4C. CHMA shows a simple degradation pattern, while LHMA shows more curves and undergoes degradation at different stages of temperature. This could be attributed to the fact that CHMA contains PE waxes, while LHMA has waxes derived from both PP and PE. Inherently, PP is sensitive to high temperature, which could be the reason for LHMA's different behavior compared to that of CHMA. However, LHMA undergoes degradation only above 200 °C, which is well above the processing, application, and service temperatures of HMAs.
Efficacy and sealing strength of HMAs
To examine the peel strength of the adhesives made in this investigation, the force and tensile strength at maximum weight were recorded for thermally sealed samples during different time intervals (see Fig. 5), and the values are reported in Table S2.† The maximum force required for sealing peel-off (3.77 ± 0.32 lbf) was observed after 48 h for the lab-made sample.
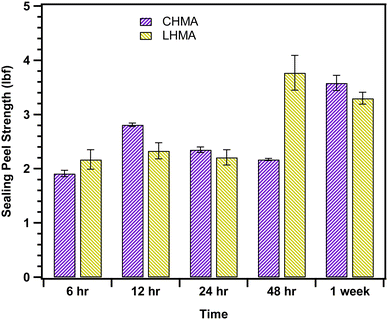 |
| Fig. 5 Sealing peel strengths (in lbs) of CHMA (commercially available hot-melt adhesives) and LHMA (lab-made hot-melt adhesives) samples that had been stored for various lengths of time after thermal sealing. | |
The results show that an optimal composition was obtained when we used 30 wt% upcycled Wax E along with EVA and gum rosin. The tensile strength and sealing force were very similar for LHMA and CHMA. Except in case of 48 h mark, there was a gradual increase in the sealing strength and force required to peel off the sealing in both CHMA and LHMA. The consistent sealing strength of the adhesives over different periods suggests stable adhesion, even after one week. This indicates that our lab-made adhesive is equally effective in performance as its commercially available counterpart during storage.
Conclusion
In conclusion, we have developed an efficient method for converting mixed waste polyolefins into upcycled waxes at scales reaching up to 50 g. The structures and the thermal properties of the obtained waxes were successfully investigated with NMR, GCMS, TGA, and DSC characterization, respectively. The obtained upcycled waxes were used to formulate a HMA, which was compared to the commercial HMA. The HMA produced from upcycled waxes exhibited a melting point of 117.69 °C and a maximum degradation temperature of 465.49 °C, closely matching the properties of commercially available HMA glue sticks. The sealing strength of LHMA and CHMA is very similar, with forces in the range of 2–3 lbf. The upcycling of waste polyolefins into HMAs was successfully achieved, and these adhesives were comparable to a commercially available adhesive, thus demonstrating that this approach offers yet another way to increase circularity. Further studies that would be helpful include several-month aging tests and measurements of the softening point of HMAs and their heat stability. Also, life cycle assessment and techno-economic analysis will be required to validate the environmental benefits and economic viability of this work.
Data availability
The data supporting this article have been included in the ESI.†
Conflicts of interest
The authors have filed a US patent application for this work.
Acknowledgements
We wish to thank CONAGRA for its generous partial financial support for this study.
References
-
S. Gharde, G. Sharma and B. Kandasubramanian, in Progress in Adhesion and Adhesives, 2021, pp. 1–28, DOI:10.1002/9781119846703.ch1.
-
I. Benedek, Pressure-sensitive Formulation, CRC Press, 2020 Search PubMed.
- W. Li, L. Bouzidi and S. S. Narine, Current research and development status and prospect of hot-melt adhesives: A review, Ind. Eng. Chem. Res., 2008, 47, 7524–7532 CrossRef CAS.
-
S. E. Selke, J. D. Culter, R. A. Auras, and M. Rabnawaz, Plastics packaging: properties, processing, applications, and regulations, Carl Hanser Verlag GmbH Co KG, 2021 Search PubMed.
- S. Wang, Z. Liu, L. Zhang, Y. Guo, J. Song, J. Lou, Q. Guan, C. He and Z. You, Mater. Chem. Front., 2019, 3, 1833–1839 RSC.
- P. Waites, Moisture-curing reactive polyurethane hot-melt adhesives., Pigm. Resin Technol., 1997, 26, 300–303 CrossRef CAS.
-
T. A. Hatzinikolaou, Adhesion of ethylene vinyl acetate copolymers to metals, University of Bath, United Kingdom, 1985 Search PubMed.
- N. Hori, K. Asai and A. Takemura, Effect of the ethylene/vinyl acetate ratio of ethylene-vinyl acetate emulsion on the curing behavior of an emulsion polymer isocyanate adhesive for wood, J. Wood Sci., 2008, 54, 294–299 CrossRef CAS.
- N. S. Baer, N. Indictor and W. H. Phelan, An evaluation of poly (vinyl acetate) adhesives for use in paper conservation, Restaurator, 1978, 2, 121–138 Search PubMed.
- Y. Shen, Z. Chen, Y. Zhou, Z. Lei, Y. Liu, W. Feng, Z. Zhang and H. Chen, Solvent-free electrically conductive Ag/ethylene vinyl acetate (EVA) composites for paper-based printable electronics, RSC Adv., 2019, 9, 19501–19507 RSC.
- A. C. Backman and K. A. H. Lindberg, Interaction between wood and polyvinyl acetate glue studied with dynamic mechanical analysis and scanning electron microscopy, J. Appl. Polym. Sci., 2004, 91, 3009–3015 CrossRef CAS.
-
R. D. Dexheimer and L. R. Vertnik, Hot-melt Adhesives, in Adhesives in manufacturing, Routledge, 2018, pp. 325–352 Search PubMed.
- S. Mapari, S. Mestry and S. T. Mhaske, Developments in pressure-sensitive adhesives: A review, Polym. Bull., 2021, 78, 4075–4108 CrossRef CAS.
- J. P. Kalish, S. Ramalingam, H. Bao, D. Hall, O. Wamuo, S. L. Hsu, C. W. Paul, A. Eodice and Y.-G. Low, An analysis of the role of wax in hot melt adhesives, Int. J. Adhes. Adhes., 2015, 60, 63–68 CrossRef CAS.
- D. Robertson, A. van Reenen and H. Duveskog, A comprehensive investigation into the structure-property relationship of wax and how it influences the properties of hot melt adhesives, Int. J. Adhes. Adhes., 2020, 99, 102559 CrossRef CAS.
- P. Denk, E. Ortner and A. Buettner, Characterization of odorants in waxes for hot melt adhesives using sensory and instrumental analyses, Int. J. Adhes. Adhes., 2019, 95, 102406 CrossRef CAS.
- J. P. Kalish, S. Ramalingam, O. Wamuo, O. Vyavahare, Y. Wu, S. L. Hsu, C. W. Paul and A. Eodice, Role of n-alkane-based additives in hot melt adhesives, Int. J. Adhes. Adhes., 2014, 55, 82–88 CrossRef CAS.
- A. V. Kostyuk, N. M. Smirnova, S. V. Antonov and S. O. Ilyin, Rheological and adhesion properties of hot-melt adhesives based on hydrocarbon resins and poly(ethylene-vinyl acetate), Polym. Sci., Ser. A, 2021, 63, 283–295 CrossRef CAS.
- Y.-J. Park, H.-S. Joo, H.-S. Do and H.-J. Kim, Viscoelastic and adhesion properties of EVA/tackifier/wax ternary blend systems as hot-melt adhesives, J. Adhes. Sci. Technol., 2006, 20, 1561–1571 CrossRef CAS.
- M. L. Barrueso-Martínez, T. del Pilar Ferrándiz-Gómez, M. D. Romero-Sánchez and J.
M. Martín-Martínez, Characterization of EVA-based adhesives containing different amounts of rosin ester or polyterpene tackifier, J. Adhes., 2003, 79, 805–824 CrossRef.
- G. Estan-Cerezo and J. M. Martín-Martínez, Thermal, viscoelastic and adhesion properties of EVA (ethylene-co-vinyl acetate) hot melts containing polypropylene waxes of different nature, J. Adhes. Sci. Technol., 2015, 29, 875–889 CrossRef CAS.
- D. Robertson, A. van Reenen, H. Duveskog and F. Brady, A comparative study of the application-based properties of hot melt adhesives (HMAs) formulated with different waxes, Int. J. Adhes. Adhes., 2021, 111, 102974 CrossRef CAS.
- H.-H. Chu, W.-H. Huang, K. S. Chuang and B.-H. Shen, Adhesion and viscoelastic property of poly (ethylene-co-vinyl acetate) based hot melt adhesives-effects of tackifier and wax, Int. J. Adhes. Adhes., 2020, 99, 102586 CrossRef CAS.
- A. A. Adelodun, A. G. Adeniyi, J. O. Ighalo, D. V. Onifade and L. T. Arowoyele, Thermochemical conversion of oil palm Fiber-LDPE hybrid waste into biochar, Biofuels, Bioprod. Biorefin., 2020, 14, 1313–1323 CrossRef CAS.
- J. M. Soto, G. Blázquez, M. Calero, L. Quesada, V. Godoy and M. Á. Martín-Lara, A real case study of mechanical recycling as an alternative for managing of polyethylene plastic film presented in mixed municipal solid waste, J. Cleaner Prod., 2018, 203, 777–787 CrossRef CAS.
- M. Shaker, T. S. Muzata, S. S. Hamdani, I. Wyman, C. Saffron and M. Rabnawaz, Chemical upcycling of high-density polyethylene into upcycled waxes as rheology modifiers and paper coating materials, J. Cleaner Prod., 2024, 467, 142943 CrossRef CAS.
- M. Shaker, S. S. Hamdani, T. S. Muzata and M. Rabnawaz, Driving selective upcycling of mixed polyethylene waste with table salt, Sci. Rep., 2024, 14, 14371 CrossRef CAS.
- Hot melt adhesives market size, share & industry analysis, by raw material (ethylene vinyl acetate (EVA), polyolefin, styrenic block copolymers (SBC), polyurethane (PU), polyester, and others), by application (packaging, assembly, woodworking, transportation, building & construction, footwear & leather, nonwovens, bookbinding, and others), and regional forecast, 2024–2032 source: https://www.fortunebusinessinsights.com/industry-reports/hot-melt-adhesives-market-101724, 2024.
- K.-S. Jaw, C.-K. Hsu and J.-S. Lee, The thermal decomposition behaviors of stearic acid, paraffin wax and polyvinyl butyral, Thermochim. Acta, 2001, 367–368, 165–168 CrossRef CAS.
- P. Samyn and V. K. Rastogi, Stabilization of an aqueous bio-based wax nano-emulsion through encapsulation, Nanomaterials, 2022, 12(23), 4329 CrossRef CAS PubMed.
- A. Khan, P. Saikia, R. Saxena, D. Rakshit and S. Saha, Microencapsulation of phase change material in water dispersible polymeric particles for thermoregulating rubber composites—a holistic approach, Int. J. Energy Res., 2020, 44, 1567–1579 CrossRef CAS.
- Plastic waste and recycling in the EU: facts and figures, source https://www.europarl.europa.eu/topics/en/article/20181212STO21610/plastic-waste-and-recycling-in-the-eu-facts-and-figures#:%7E:text=InJune2019CtheEU, approved it in April 2024, 2018.
- The U.S. Plastics Pact, source https://usplasticspact.org/, 2024.
|
This journal is © The Royal Society of Chemistry 2024 |
Click here to see how this site uses Cookies. View our privacy policy here.