A porous dome array evaporator for high-performance photothermal water evaporation and thermoelectric power generation†
Received
9th October 2023
, Accepted 21st November 2023
First published on 21st November 2023
Abstract
Solar powered local interface evaporation has high conversion efficiency, water purification, seawater desalination, power generation and other potentials. However, the ineffective integration and expensive materials of hybrid solar thermal devices undermine the widespread development and practical outdoor use of solar energy. This article proposes a low-cost and sustainable 3D carbonated sucrose evaporator that achieves broadband light absorption, thermal insulation, and high hydrophilicity for high-performance water evaporation and self-desalination. The dome array structure not only effectively reduces the diffuse reflection of light, but also significantly increases the solar evaporation rate with excellent salt resistance and long-term stability. A high evaporation rate of 3.54 kg m−2 h−1 and an efficiency of 95.86% were achieved under one sun illumination, and the evaporation rate was 3.48 kg m−2 h−1 h even in high-salinity brine (15 wt% NaCl solution). In addition, the synergistic coupling of solar-steam and solar-electricity technologies can simultaneously achieve a high evaporation rate of 3.43 kg m−2 h−1 and an output power of 0.48 W m−2, providing great hope for people in developing regions to cope with freshwater and electricity shortages.
1. Introduction
Water resources and energy are important material foundations for the survival and development of human society. In recent years, with increasing world population and industrialization, the shortage of freshwater resources and the energy crisis have become increasingly serious.1–5 In this regard, exploration of renewable energy and efficient freshwater production methods has become a top priority. Desalination technology is considered an effective approach to address the water resource shortage issue. However, commercial desalination technologies are limited in their further application in remote areas due to their high energy consumption, as well as the large and complex nature of their systems. Solar energy, as a sustainable green energy source, has important applications in energy storage, wastewater treatment, and desalination, and can provide a convenient energy source for desalination water treatment technologies. In solar-powered seawater desalination, solar-driven interfacial evaporation technology has become a research hotspot due to its advantages of sustainability, low cost, and high energy efficiency.6–9
The light-to-vapor energy conversion efficiency and interface design are crucial for achieving a high evaporation rate and efficient production of clean water. Early research efforts were primarily focused on improving light absorption,10,11 thermal localization,12–14 optimizing water supply, and reducing thermal losses.15,16 However, these studies have a common characteristic, which is that the temperature of the evaporative surface is higher than the ambient temperature. In this scenario, assuming a vaporization efficiency of 100%, the possibility of breaking the theoretical limit of energy conversion efficiency (1.50 kg m−2 h−1) is very small, far from meeting the requirements of practical applications. In order to overcome the limitations of solar input rates, the focus of research has shifted towards improving the structure and configuration design of photothermal evaporators, leading to the evolution of evaporator design from 2D structures to gradually adopting 3D structures. By utilizing intricately designed 3D evaporators, the evaporation rate has been significantly improved, even surpassing the theoretical limit, through the collection of energy from the surrounding environment and bulk water, as well as the recovery of latent heat and reduction of energy losses.17–19 However, the evaporation performance of most 3D evaporators still does not meet the requirements of practical desalination applications. The main reasons are the material heat loss and surface salt deposition issues. Therefore, a crucial aspect for achieving stable evaporation performance for high salinity wastewater treatment lies in the development of evaporators with a topological structure capable of effectively localizing heat while expelling salt ions.
Besides, current research on 3D photothermal evaporators has focused on expanding the energy input channels to increase the vaporization rate, while ignoring the multi-effect utilization of evaporation-driven water flow, latent heat release, and temperature difference. The latent heat released during the condensation process of steam can be utilized not only for distillation recovery to enhance freshwater productivity but also for power generation. For example, Zhu et al. utilized scalable graphite/nonwoven films to design a co-coupling device for producing clean water and electricity, using the temperature difference generated by steam condensation to generate electricity.20 For better utilization of low-grade heat during steaming, Liu et al. designed an integrated system consisting of 3D porous carbon foam and TE modules.21 The Seebeck effect caused by temperature differences in evaporation and lower water, can be used for co-generating electricity, and an evaporation rate of 1.39 kg m−2 h−1 and a power output of 0.5 W m−2 can be achieved simultaneously under one sun irradiation. Although efficient thermal management and synergies of solar energy for hydropower co-generation have promising applications, there has been little research on low-grade solar power generation under evaporation, while both the cost and performance of synergistic coupling need to be improved. Therefore, the development of a low-cost, easy-to-prepare, salt-tolerant and high-performance hydropower co-generation system can better solve the social problems faced by people today.
Herein, we report a 3D porous dome array sulfuric acid carbonized sucrose (SCS) evaporator that enables efficient synergistic coupling of solar–thermal conversion and power generation (Fig. 1a). The 3D porous dome array structure utilizes its walls to recover energy losses caused by diffuse reflectance and thermal radiation from the 2D bottom portion of the 3D structure, thereby eliminating the energy efficiency limitations imposed by 2D materials on the 3D structure. Besides, by adjusting the height of the distillation device, the introduction of a cold evaporative surface (CES) can extract energy from bulk water to enhance overall solar evaporation. Meanwhile, its porous structure provides a pathway for water transport, and establishes heat transfer boundaries for the water transport layer to minimize heat transfer losses. Based on the excellent synergistic performance of brine transport and photothermal management, the 3D SCS at 4 cm height showed a high evaporation rate of around 3.54 kg m−2 h−1 and solar-to-vapor efficiency of 95.86% under 1 sun illumination. Similarly, a 3D SCS has better acid and alkali resistance, long-term salt resistance and self-cleaning ability compared to many high-performance solar evaporators, and is also very effective in producing fresh water. Importantly, a rational integration of high-efficiency solar-thermal evaporation and harvesting of low-grade heat for thermoelectric (TE) power generation is achieved. This scheme highlights the potential of a 3D SCS as a promising solution for the desalination of brine, and will further advance the practical application of high-quality solar steam-hydroelectric cogeneration.
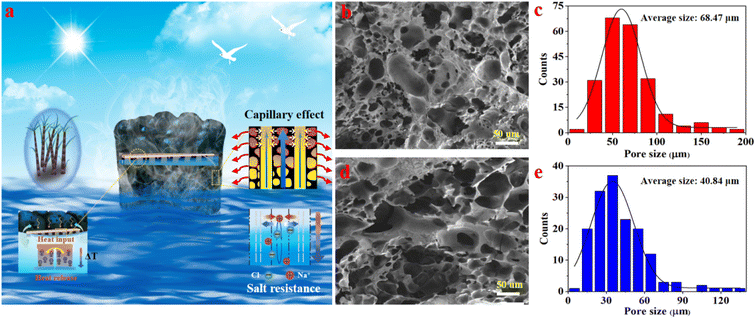 |
| Fig. 1 (a) Schematic diagram of 3D SCS-based photothermal water evaporation and thermoelectric power generation. (b) SEM images and (c) pore size distribution at the top surface of the SCS. (d) SEM images and (e) pore size distribution at the side surface of the SCS. | |
2. Results and discussion
2.1 Preparation and characterization of a 3D SCS evaporator
The 3D porous SCS was prepared by carbonizing sucrose in polytetrafluoroethylene molds by using concentrated sulfuric acid and modified into a dome array structure (Fig. S1†). The carbonization process of concentrated sulfuric acid dehydrates sucrose into a carbon black material with high absorbance and hydrophilicity. Simultaneously generated gases escape through the internal structure, creating interconnected porous 3D channels. Its microstructure is shown in Fig. 1b–e, where the presence of a large number of interconnected pores with diameters ranging from tens to hundreds of microns can be clearly identified. These macroscopic channels can provide strong capillary action, providing fast channels for water transport and salt exchange, which are crucial for durable solar desalination.2,21 In addition, the interacting porous channels provide excellent effective vapor escape capability and are valid candidates for interfacial evaporation technology.
The high light absorption capacity of the SCS can be confirmed from the UV-vis-NIR plots. As shown in Fig. 2a, the SCS in both dry and wet states exhibits similar light absorption efficiency in the ultraviolet and visible wavelength regions, while in the wet state it exhibits stronger light absorption in the near-infrared wavelength region. This is because under wet conditions, the pores of the SCS are filled with water instead of air as under dry conditions. This reduces the difference in refractive index between water and the surface of SCS material, thereby enhancing the light absorption capability of the SCS in the near-infrared wavelength region (∼96%).22 In addition, the thermal conductivity of the SCS in the dry and wet states is 0.316 W m−1 K−1 and 0.557 W m−1 K−1, respectively, which is lower than that of pure water (0.606 W m−1 K−1). Therefore, during the vaporization process, it can effectively suppress heat loss to water and achieve localized heating. The FTIR spectrum (Fig. 2b) showed that the surface functional groups of carbonized sucrose mainly included C–O, O–H and C–C, and the proportion of hydrophilic groups decreased significantly, especially the hydroxyl group, indicating that the deoxygenation reaction had been carried out. The main elemental components C, O and S in the 3D SCS can be confirmed by XPS spectroscopy (Fig. 2c), where C–O, and CSOx hydrophilic groups favor a continuous water supply (Fig. S2†). Its excellent hydrophilicity can be verified through a rapid water penetration experiment (Fig. S3†), and the real-time infrared image of the wetting process is shown in Fig. 2d. Once the SCS comes into contact with water, the wetting process begins immediately and becomes completely wet within 30 s, indicating that a highly hydrophilic SCS can quickly transport water to the evaporation zone from the bottom to the top. Furthermore, water contact angle measurements (Fig. 2e) revealed that water droplets were rapidly absorbed in less than 1 s, benefiting from the porous and rough surface of the SCS. These results indicate that the interconnected porous channels of the 3D SCS have good hydrophilicity and water–air transport capability. The compressive strength of the 3D SCS was tested, which quantitatively demonstrates the mechanical strength, as shown in Fig. S4.† The maximum load of the 3D SCS is up to nearly 300 N, similar to that of bamboo-derived carbon (290 N) and much better than that of mushroom derived carbon (45 N).22 The 3D SCS is also mechanically robust and can withstand over 50 times its weight without cracking, ensuring scalable deployment in practical applications.
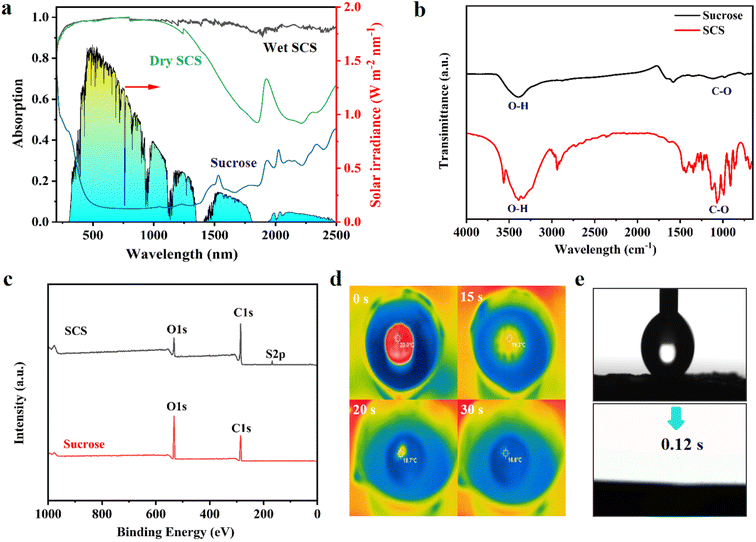 |
| Fig. 2 (a) UV-vis-NIR spectra, (b) FTIR spectra, and (c) XPS spectra of sucrose and the SCS. (d) Infrared photos of the wetting process of the 3D SCS. (e) Water contact angle test of the surface of the 3D SCS. | |
2.2 Evaporation performance of the 3D SCS evaporator
The solar water evaporation performance experiments were carried out under the same environmental conditions (Fig. S5†). To systematically evaluate the performance of the carbonized sucrose solar steam system, an electronic balance was used to monitor the water mass change under 1 sun irradiation, as shown in Fig. 3a. The evaporation rate is normalized by using the projected area of the evaporator and obtained from the slope of the mass change curve under steady-state conditions. The corresponding dark evaporation rate was subtracted to remove the effect of natural evaporation. The 3D SCS evaporator (height: 0.5 cm) exhibits an evaporation rate of 2.75 kg m−2 h−1, which is 1.64 times that of a 2D SCS and 9.48 times that of pure water. The temperature on the surface of the 3D SCS and 2D SCS was measured using an infrared thermal camera (Fig. 3b and c). Under one sun irradiation, the surface temperature of the 3D SCS rapidly increases within 10 minutes and stabilizes at around 57.8 °C, while the highest surface temperature of the 2D SCS is 48.2 °C, indicating that the 3D SCS has a fast and excellent light-to-heat conversion function. The high evaporation performance of the 3D SCS benefited from the porous dome array, which is similar to the meniscus array reported by Yu et al. (Fig. S6†).23 In addition, the evaporation rate of the 3D SCS increases with the increase in array number (Table S1†). On the one hand, these arrays can act as light traps to improve light absorption and reduce radiation heat loss, thereby utilizing more heat for water evaporation. On the other hand, the increase in the number of arrays increases the actual evaporation area, which ultimately results in the highest water evaporation rate. However, as the height of the 3D SCS array increases, the evaporation rate of the evaporator first increases and then decreases (Table S2†). This is because when the array height is too high, it can cause the micro-droplets to become smaller due to the evaporation of water before reaching the top of the array, resulting in a decrease in the evaporation performance of the evaporator. As the spacing between the arrays increases, the micro-meniscus disappears and eventually forms a flat liquid surface, leading to a decrease in the evaporation rate (Table S3†). The array height of the 3D SCS also affects the diameter of the micro meniscus, and its value usually increases with the increase in array height (Fig. S7†). The large-sized micro lunar surface has a high evaporation rate. As the spacing between the arrays increases, the micro meniscus disappears, ultimately forming a flat liquid surface, causing the micro droplets to become smaller or disappear, and the evaporation rate will also decrease. When the 3D SCS adsorbed water, the water between the interlaced dome arrays would appear as a meniscus under the action of capillary force.23 This micro-meniscus can significantly increase the probability of light reflection, effectively reabsorb the energy lost by diffuse reflectance and thermal radiation, and achieve an enlarged water/air interface for steam escape. The different evaporation rates at various points on the meniscus will lead to the Marangoni effect,23 which causes the water reaching the top of the dome array to appear in the form of micro-droplets. These micro-droplets have higher saturated vapor pressure and lower evaporation enthalpy. These advantages enable the 3D SCS dome array evaporator to achieve high evaporation rates.
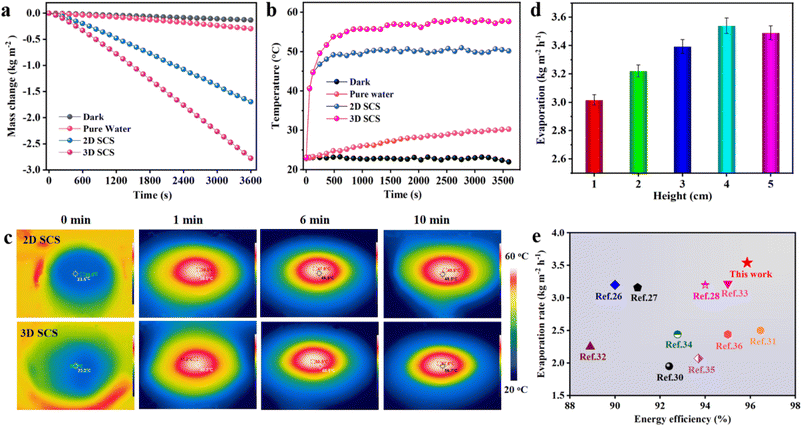 |
| Fig. 3 (a) Mass changes in water over time and (b) temperature of the 3D SCS, 2D SCS, pure water and under dark conditions. (c) Infrared images of the 3D SCS and 2D SCS surface. (d) Evaporation rates of the 3D SCS with different heights. (e) Comparisons of the evaporation rates of this work with reported studies under one sun irradiation. | |
In order to achieve stable and efficient solar-driven interfacial evaporation, it is necessary to consider the balance between heat losses and the water evaporation rate.21,22 The evaporation rates of the 3D SCS with heights from 1 to 5 cm increased with height, and are 3.01, 3.22, 3.39, 3.54 and 3.49 kg m−2 h−1 respectively (Fig. 3d). As shown in Fig. S8,† the 3D SCS with different heights (i.e. CES areas) exhibits different variations in energy transfer processes, resulting in different evaporation rates. When the 3D SCS is exposed to sunlight, the temperature of the top solar evaporation surface (TSES) increases, and thus helps to drive the solar evaporation of water. Simultaneously, due to the cooling effect of water evaporation, the side surface (CES) that does not receive sunlight undergoes a cold evaporation process with surface temperature (TCES) lower than the ambient temperature. Due to the placement of bulk water in a thermally insulated polytetrafluoroethylene flask, any variations in the initial temperature of the bulk water (TW = 23.5 °C) are solely influenced by the direction of heat conduction between the bulk water and the evaporator.17 In the process of solar evaporation, the temperature of the three domains followed the order TSES > TW > TCES. According to the thermodynamic law, the heat generated by the SES would flow to both the CES and the bulk water. Simultaneously, the heat contained in the bulk water would also be transferred to the CES. By constructing a sufficiently large CES, it can not only absorb the conduction heat loss from the SES, but also receive the conduction energy from the bulk water due to the temperature difference. After 1 h of solar evaporation, TW changes with the height of the evaporator as shown in Table S4.† For the 3D SCS with heights ranging from 0.5 to 3 cm, TW increased by 1.1, 0.9, 0.4, and 0.1 °C during the solar evaporation process, with energy losses to the bulk water due to heat conduction being 0.074, 0.060, 0.027, and 0.007 W, respectively. In contrast, for the 3D SCS with heights of 4 and 5 cm, the heat conduction loss can actually be reversed, and an energy extraction of 0.007 and 0.013 W can be obtained from the bulk water, resulting in a decrease in TW of 0.1 and 0.2 °C, respectively. Based on the above data, it is evident that the transition of net heat conduction from negative to positive can be achieved by increasing the surface area of the CES. However, if the height of the 3D SCS is too high, it will result in insufficient water supply, unable to meet the required amount of vaporization, leading to a decrease in the evaporation rate.17 Furthermore, the constructed CES can effectively minimize energy loss from the top SES to the environment, while increasing the energy obtained from the air by the CES, thereby significantly enhancing the overall efficiency of solar evaporation. According to thermodynamics,24,25 the convective and radiative energy loss from the SES to the environment can be expressed respectively as qcon = Ah(TSES − TE) and qrad = Aσε(TSES4 − TE4) (ESI†). Due to the effective heat extraction from the SES by the CES to drive cold evaporation, the surface temperature of the SES decreases to 57.8, 52.0, 48.5, 45.7, 42.5 and 42.3 °C as the surface area of the CES increases with the heights 0.5, 1, 2, 3, 4 and 5 cm of the evaporator. Therefore, the energy loss from the SES to the environment through convection and radiation decreases with the increasing surface area of the CES (Table S5†). For a 4 cm high 3D SCS, the energy loss (0.219 W) is reduced by nearly half compared to a 0.5 cm evaporator (0.429 W). Furthermore, the side CES that always maintains a lower temperature can also absorb energy from the air through radiation and convection. Based on the aforementioned calculation method, the energy gains from air for 1, 2, 3, 4 and 5 cm evaporators are calculated to be 0.017, 0.055, 0.116, 0.190 and 0.243 W, respectively (Table S6†). Based on the above analysis, it can be concluded that the 5 cm 3D SCS obtained a total additional energy gain of 0.256 W from the ambient air and bulk water. This gain exceeds the energy loss (0.217 W), resulting in an elevated evaporation rate that exceeds the theoretical limit. Therefore, in subsequent experiments, the height of the 3D SCS was set to 4 cm, which allowed for the highest solar-to-thermal conversion efficiency and a relatively high evaporation rate, while also saving materials.
The photothermal conversion efficiency of the 3D SCS was calculated by using the following formula:
|
 | (1) |
where
m is the mass flux, Δ
Hequ is the equivalent evaporation enthalpy of water in the SCS,
Po is the solar irradiation power of 1 sun (1 kW m
−2), and
Copt refers to the optical concentration on the absorber surface. Due to the higher evaporation rate of the 3D SCS than the theoretical value (1.5 kg m
−2 h
−1), if the corresponding enthalpy of water evaporation at 42.3–57.8 °C is used, the evaporation efficiency of the 3D SCS will be higher than 1. So, the Δ
Hequ of water in the 3D SCS can be estimated by evaporating water under dark conditions assuming an identical power input (
Uin):
26,27 |
Uin = ΔHvapmo = ΔHequmg | (2) |
where Δ
Hvap and
mo are the evaporation enthalpy and evaporation rate of water under dark conditions and
mg is the evaporation rate of the 3D SCS under the same environmental conditions. In this study, the values of Δ
Hvap and
mo are 2450 kJ kg
−1 and 0.130 kg m
−2 h
−1, respectively. The
mg and calculated
ΔHequ values are displayed in Table S7.
† It is noticed that the value of Δ
Hequ is lower than that of bulk water. To explain this decrease in vaporization enthalpy, we turn to the theory of water clusters.
28 Water can evaporate in the form of individual molecules or in the form of small clusters composed of several to dozens of molecules. When water molecules are confined within the 3D SCS molecular network, they are more likely to escape the network in the form of small clusters rather than as individual molecules. Accordingly, water achieved a lower enthalpy change during evaporation compared to the conventional latent heat. To demonstrate the evaporation of water clusters, we added LiCl (a non-volatile electrolyte that can be loaded with water clusters) to the original bulk water,
28,29 and verified this hypothesis by testing the Li
+ concentration in the condensed water after evaporation. As shown in Fig. S9,
† it can be observed that there is a correlation between the Li
+ concentration in the 3D SCS evaporated condensate and the LiCl concentration in the original water. In contrast, the Li
+ concentration in the traditionally evaporated condensate is lower and unrelated to the Li
+ concentration in the original water. These results suggest that water evaporated from a 3D SCS system is more likely to exist in the form of clusters. According to
eqn (1), when the height of the 3D SCS evaporator is 4 cm, the evaporation rate reaches 3.54 kg m
−2 h
−1, with a maximum
η of 95.86%, which exceeds many reported values of similar materials (
Fig. 3e).
26–28,30–36 Furthermore, the durability of the 3D SCS (4 cm height) was investigated through 10 cycle tests, with each cycle lasting 3600 s under one sun irradiation. As shown in Fig. S10,
† the 3D SCS exhibited a stable water evaporation rate of about 3.54 kg m
−2 h
−1 without significant degradation, proving its durability and stability in efficient steam generation.
2.3 Salt resistance and long-term stability
To further investigate the salt resistance performance of the 3D SCS, synthetic seawater with different salinities was evaluated under one sun irradiation (Fig. 4a). At a salinity of 15 wt%, the evaporation rate remained at 3.48 kg m−2 h−1, indicating that the 3D SCS also has good salt resistance in high-concentration saline water. After absorbing energy, saltwater's temperature increases, which compensates for the higher surface tension and promotes the evaporation process. This ultimately results in a similar evaporation rate to that of distilled water. Besides, a long-term stability test was conducted for 20 days, with a duration of 3600 seconds under one sun irradiation per day. As shown in Fig. 4b, the photothermal evaporation performance of the 3D SCS in 15 wt% brine remains high without salt accumulation on the top surface under one sun irradiation. Due to the presence of large pores and an abundant water supply, the evaporation rate of the 3D SCS will not significantly decrease with increasing salinity. To reveal the salt resistance ability of the 3D SCS, 0.5 g of NaCl was placed on its top surface. Attractively, after 30 min of irradiation, the salt particles were completely dissolved in water (Fig. S11†), demonstrating the good self-desalting ability of the 3D SCS. This excellent demonstration of capillarity can be explained by using the schematic diagram in Fig. 4c. The SCS micron scale porous structure and unique 3D waterway pumping function can achieve reverse ion exchange and salt water transport, and form concentration gradients and reflux.
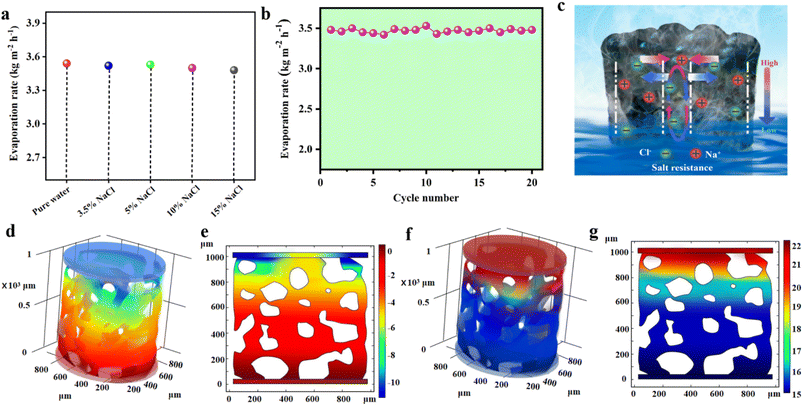 |
| Fig. 4 (a) Evaporation rate of the 3D SCS with 3.5, 5, 10, and 15 wt% NaCl solution. (b) Cycling stability of the 3D SCS evaporator. (c) The schematic diagram of salt resistance. (d and f) 3D steady-state simulations of the relative water pressure and salinity distributions of the 3D SCS. (e and g) 2D longitudinal-section steady-state simulations of the relative water pressure and salinity distributions of the 3D SCS. | |
To further elucidate the salt-rejection mechanism, we employed COMSOL to numerically simulate and analyse the relative water pressure and salinity distribution in the 3D SCS evaporator for solar-powered seawater desalination. As shown in Fig. 4d and e, during the solar evaporation process, a negative relative water pressure is generated at the top of the 3D SCS to ensure continuous water supply to the evaporating surface. This enables the evaporated water at the top of 3D SCS to be promptly and sufficiently replenished through superhydrophilicity and strong capillary action, allowing it to rapidly generate a stable high temperature for evaporation under illumination. As the solubility of salt depends on temperature, it gradually dissolves in water. Through diffusion and convection, high concentrations of salt gradually dissolve from the top evaporative layer and return to the water below. In addition, during the evaporation process, large pore sizes may consider the location for the exchange of salt ion concentrations, and high-salt regions that tend to crystallize can be dissolved by water below in a timely manner. This is not only consistent with the experimental results, but also with the subsequent simulations of salt distribution. The steady-state salt distribution in Fig. 4f and g indicates that when the concentration of saltwater input is 15 wt%, the salt concentration on the evaporative surface of the 3D SCS is 22 wt%, which is lower than the saturation concentration. Therefore, the evaporation and dilution of seawater will be maintained in dynamic equilibrium, and even in different concentrations of seawater, the photothermal evaporation rate of 3D SCS will be the same as that in pure water.
2.4 Wastewater purification and outdoor desalination
Subsequently, water purification tests were carried out on simulated seawater, dye wastewater, and acid–base solutions to evaluate the purification effect of the prepared 3D SCS on wastewater. The purification results of simulated seawater are shown in Fig. 5a. After desalination, the concentrations of Na+, Mg2+, K+, and Ca2+ significantly decreased from 10
810, 1100, 471 and 396 mg L−1 to 1.43, 0.15, 0.69 and 1.82 mg L−1, respectively. The ion retention rate was higher than 99.9%, far lower than the drinking water standards defined by the WHO and EPA, indicating the feasibility of actual seawater purification.37–40 In the industrial dye wastewater experiment simulated by methylene blue (MB) and rhodamine B (RhB) aqueous solutions, the solar-driven generated condensate was very clear (Fig. 5b). It can be proved using the UV vis absorption spectrum that the absorption peaks of RhB (∼547 nm) and MB (∼664 nm) disappeared, and the existence of dye molecules was hardly detected. The 3D SCS also exhibited good purification effects for both acidic and alkaline solutions, and the pH of the purified water was about 7 (Fig. 5c). After 10 acid and alkali cycles of evaporation, the pH of the water approached 7 without significant changes, indicating the acid/alkali stability of the 3D SCS (Fig. S12†). The simulated seawater, domestic water, and condensed water showed resistance values of 0.333, 1.752, and 1.833 MΩ (Fig. S13†), further indicating the excellent purification performance of the 3D SCS in seawater desalination. These results validate that safe drinking water can be directly obtained through the 3D SCS, implying its broad application potential in seawater desalination and sewage treatment.
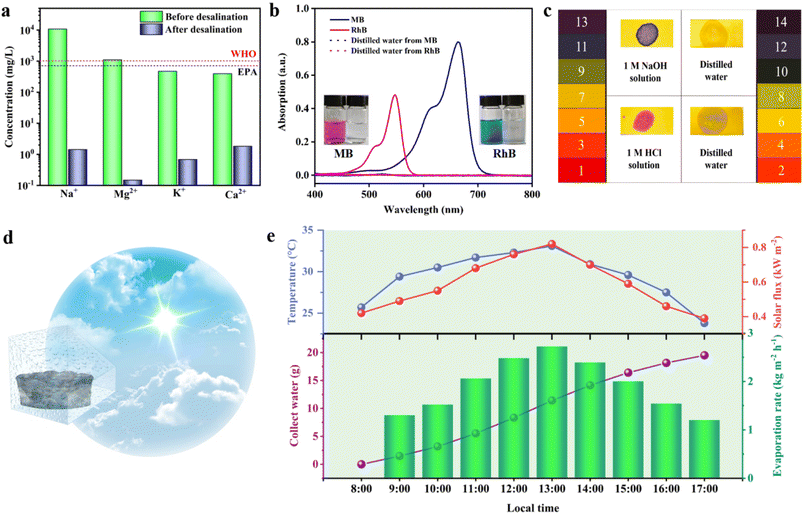 |
| Fig. 5 (a) The ion concentrations of simulated seawater before and after desalination. (b) UV-vis spectra of methyl blue and rhodamine B simulated wastewater before and after purification. (c) The pH values of acid/alkaline aqueous solutions before and after purification. (d) Schematic illustration of the outdoor desalination test based on the 3D SCS. (e) The temperature, solar flux, water production rate, and collected water during the outdoor desalination test. | |
To evaluate the practical desalination performance of the 3D SCS, a full-day outdoor simulated seawater desalination test (3.5 wt% NaCl) was conducted from 8
:
00 to 17
:
00. As shown in Fig. 5d and S14,† the steam generated during the desalination process condenses onto the glass to form water, which flows along the glass wall to the conduit at the bottom of the device for collection. The intensity of sunlight exposure, environmental temperature, freshwater production, and water production rate were recorded at each time period (Fig. 5e). After 9 h of outdoor seawater desalination, 19.52 g of clean water was collected, and the daily water production rate was calculated to be 17.21 kg m−2, which means that the clean water produced by 1 m2 of 3D SCS can meet the daily water consumption of 7 adults (17.21 L). It should be noted that no salt crystals were observed on the 3D SCS array surface during outdoor desalination testing. The above outdoor experiments show that this easy-to-fabricate, low-cost 3D SCS evaporator has great potential for large-scale production of fresh water, which is very suitable for people living in developing regions.
2.5 Thermoelectric power generation
The thermal localization of the solar-driven evaporator can make the temperature of the surface of the 3D SCS higher than that of the water below, and this low-grade heat energy can be used for power conversion.20,21,41 As shown in Fig. 6a, the TE module is integrated into the 3D SCS evaporator, and the Seebeck effect triggered by temperature difference is used to harvest low-grade thermal energy to synergistically generate electricity. The 3D SCS covers the upper side of the TE module in an arched shape. With the aid of the foam frame, the lower side of the TE module is just immersed in a large volume of water (3.5 wt% NaCl), where the two walls of the 3D SCS are in contact with a large amount of water for effective water removal. At this point, the photothermal diffusion through the 3D SCS forms a hot end at the upper end of the TE module, while the lower end of the TE module is cooled by a large amount of water to form a cold end, thereby generating an effective temperature difference and achieving hydropower cogeneration. The temperature differences and the electrical signal outputs of the TE module are recorded in Fig. S15† and 6b, respectively. Under one sun irradiation, the 3D SCS-TE with a height of 1.0 cm was used for water evaporation, and the maximum open circuit voltage VOC obtained was 52 mV, and a temperature difference of 4.9 °C was generated across the TE module. In contrast, a single TE module produces a temperature difference of only 2 °C, obtaining a lower VOC of 23 mV (Fig. 6b). This reveals that part of the heat energy generated by water evaporation is transferred to the upper end of the TE module for thermoelectric conversion. On the other hand, the TE module can also serve as a thermal insulator to isolate the 3D SCS from a large amount of water, thereby reducing thermal convection and radiation losses, and improving the evaporation rate of water. With and without the TE module below, the measured evaporation rates are 3.43 and 3.28 kg m−2 h−1 (Fig. S16†), indicating that the introduction of the TE module does not reduce the solar vaporization performance of the system, and its thermal insulation reduces heat loss.
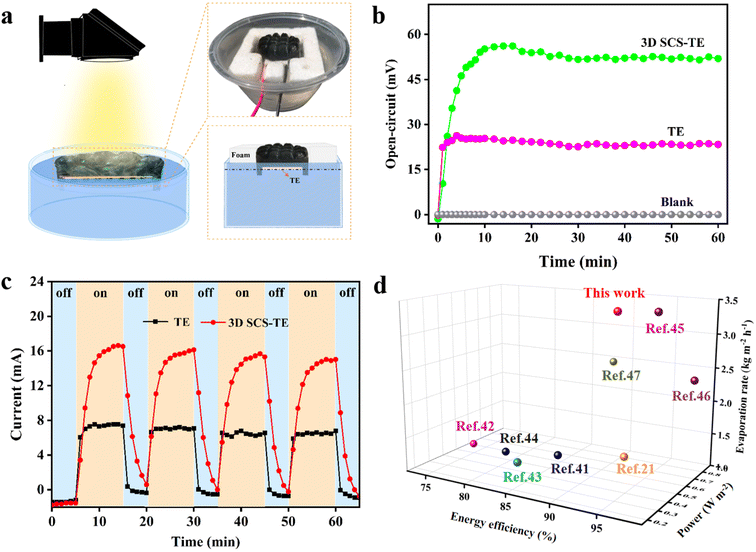 |
| Fig. 6 a) Schematic and photograph of the electricity and steam generation device. (b) The open circuit voltage of the 3D SCS generator and single TE module. (c) The loading current of the 3D SCS generator and single TE module. (d) Comparison of steam and electricity cogeneration strategies. | |
To estimate the theoretical maximum output power of the TE-evaporator, its output current was measured using a multimeter with an external load resistance of 2 Ω (Fig. 6c). Under one sun irradiation, the maximum output current and power of the 3D SCS-TE are 16.5 mA and 0.54 mW, respectively, which is approximately 4.9 times the power of a single TE module. The corresponding output power density of the 3D SCS-TE is 0.48 W m−2, and its vaporization and thermoelectric performance are comparable to or better than those of the reported systems (Fig. 6d).42–47 Furthermore, four light on/off cycle tests validated the 3D SCS-TE photothermal induced thermoelectric power generation. Therefore, the 3D SCS-TE based synergistically coupled thermoelectric power generation system provides a promising way to address the issues in IOT and remote sensing applications.
3. Conclusions
In this study, a self-desalting 3D dome porous evaporator was designed, which realized the synergistic coupling of light-to-heat conversion and low-grade thermoelectric conversion, and helped to cope with the global freshwater and energy crisis. The 3D SCS utilizes its porous dome array structure, super hydrophilicity, and multi-channel waterway design to effectively prevent salt deposition in continuous solar seawater desalination. The height adjustment solves the balance problem that too much water supply will increase heat conduction loss, while insufficient water supply cannot meet the needs of steaming. Under excellent light absorption and effective thermal management, a high evaporation rate of 3.54 kg m−2 h−1 and an efficiency of 95.86% are achieved under one sun irradiation. Evaporation of simulated seawater, dye wastewater, and acid–base solutions can produce safe drinking water while maintaining the stability and self-cleaning function of the evaporator. 1 m2 of a 3D SCS can produce drinking water that meets the daily needs of 7 adults. Moreover, when synergistically coupled with TE modules, a high evaporation rate (3.43 kg m−2 h−1) and electrical output power (0.48 W m−2) can be simultaneously achieved under one sun illumination. This low-cost, sustainable cogeneration strategy provides an effective strategy for addressing freshwater and energy shortages in resource-poor regions.
Author contributions
The manuscript was written through contributions of all authors. All authors have given approval to the final version of the manuscript.
Conflicts of interest
The authors declare no conflict of interest.
Acknowledgements
The work described in this paper was supported by the National Natural Science Foundation of China (22271070), the Project of Improving the Innovation Ability of Medium and Small-Sized Technology-Based Enterprises in Shandong Province (2022TSGC1313), and the Natural Science Foundation of Shandong Province (ZR2021QE241).
References
- P. Sun, W. Zhang, I. Zada, Y. Zhang, J. Gu, Q. Liu, H. Su, D. Pantelic, B. Jelenkovic and D. Zhang, ACS Appl. Mater. Interfaces, 2020, 12, 2171 CrossRef CAS PubMed
.
- C. Song, Z. Jiang, X. Gu, H. Li and J. Shi, J. Colloid Interface Sci., 2022, 616, 709 CrossRef CAS PubMed
.
- X. Meng, X. Peng, J. Xue, Y. Wei, Y. Sun and Y. Dai, J. Mater. Chem. A, 2021, 9, 11013 RSC
.
- X. Wu, M. Robson, J. Phelps, J. Tan, B. Shao, G. Owens and H. Xu, Nano Energy, 2019, 56, 708 CrossRef CAS
.
- Z. Fu, S. Zhou, L. Xia, C. Zhang, N. Zhu, J. Gong, X. Wang, X. Liu, L. Li and W. Xu, Green Chem., 2022, 24, 4812 RSC
.
- X. Zhang, K. Deng, C. Zhang, B. Shang and X. Liu, J. Mater. Chem. A, 2022, 10, 9482 RSC
.
- B. Lv, C. Gao, Y. Xu, X. Fan, J. Xiao, Y. Liu and C. Song, Desalination, 2021, 510, 115093 CrossRef CAS
.
- S. Cheng, Z. Sun, Y. Wu, P. Gao, J. He, Z. Yin, L. Liu and G. Li, J. Mater. Chem. A, 2021, 9, 22428 RSC
.
- H. Guan, T. Fan, H. Bai, Y. Su, Z. Liu, X. Ning, M. Yu, S. Ramakrishna and Y. Long, Carbon, 2022, 188, 265 CrossRef CAS
.
- P. Zhang, J. Li, L. Lv, Y. Zhao and L. Qu, ACS Nano, 2017, 11, 5087 CrossRef CAS PubMed
.
- K. T. Lin, H. Lin, T. Yang and B. Jia, Nat. Commun., 2020, 11, 1389 CrossRef CAS
.
- Y. Zeng, J. Yao, B. A. Horri, K. Wang, Y. Wu, D. Li and H. Wang, Energy Environ. Sci., 2011, 4, 4074 RSC
.
- L. B. Zhang, B. Tang, J. B. Wu, R. Y. Li and P. Wang, Adv. Mater., 2015, 27, 4889 CrossRef CAS PubMed
.
- Z. Li, J. Zhang, S. Zang, C. Yang, Y. Liu, F. Jing, H. Jing, J. Hu, C. Wang and Y. Zhou, Nano Energy, 2020, 73, 104834 CrossRef CAS
.
- H. Liang, Q. Liao, N. Chen, Y. Liang, G. Lv, P. Zhang, B. Lu and L. Qu, Angew. Chem., Int. Ed., 2019, 58, 19041 CrossRef CAS PubMed
.
- Y. J. Li, T. T. Gao, Z. Yang, C. J. Chen, Y. D. Kuang, J. W. Song, C. Jia, E. M. Hitz, B. Yang and L. B. Hu, Nano Energy, 2017, 41, 201 CrossRef CAS
.
- Y. Wang, X. Wu, X. Yang, G. Owens and H. Xu, Nano Energy, 2020, 78, 105269 CrossRef CAS
.
- Y. Shi, R. Li, Y. Jin, S. Zhuo, L. Shi, J. Chang, S. Hong, K. C. Ng and P. Wang, Joule, 2018, 2, 1171 CrossRef CAS
.
- Y. Wang, X. Wu, B. Shao, X. Yang, G. Owens and H. Xu, Sci. Bull., 2020, 65, 1380 CrossRef CAS
.
- X. Li, X. Min, J. Li, N. Xu, P. Zhu, B. Zhu, S. Zhu and J. Zhu, Joule, 2018, 2, 2477 CrossRef
.
- X. Liu, D. D. Mishra, Y. Li, L. Gao, H. Peng, L. Zhang and C. Hu, ACS Sustainable Chem. Eng., 2021, 9, 4571 CrossRef CAS
.
- Y. Sun, Z. Zhao, G. Zhao, L. Wang, D. Jia, Y. Yang, X. Liu, X. Wang and J. Qiu, Carbon, 2021, 179, 337 CrossRef CAS
.
- Z. Yu, R. Gu, Y. Tian, P. Xie, B. Jin and S. Cheng, Adv. Funct. Mater., 2022, 32, 2108586 CrossRef CAS
.
- N. Li, L. Qiao, J. He, S. Wang, L. Yu, P. Murto, X. Li and X. Xu, Adv. Funct. Mater., 2021, 31, 2008681 CrossRef CAS
.
- X. Wu, Z. Wu, Y. Wang, T. Gao, Q. Li and H. Xu, Adv. Sci., 2021, 8, 2002501 CrossRef CAS PubMed
.
- Y. Guo, H. Lu, F. Zhao, X. Zhou, W. Shi and G. Yu, Adv. Mater., 2020, 32, 1907061 CrossRef CAS
.
- Y. Tian, X. Liu, S. Xu, J. Li, A. Caratenuto, Y. Mu, Z. Wang, F. Chen, R. Yang, J. Liu, M. Minus and Y. Zheng, Desalination, 2022, 523, 115449 CrossRef CAS
.
- F. Zhao, X. Zhou, Y. Shi, X. Qian, M. Alexander, X. Zhao, S. Mendez, R. Yang, L. Qu and G. Yu, Nat. Nanotechnol., 2018, 13, 489 CrossRef CAS
.
- H. Abdoul-Carime, F. Berthias, L. Feketeova, M. Marciante, F. Calvo, V. Forquet, H. Chermette, B. Farizon, M. Farizon and T. D. Mark, Angew. Chem., Int. Ed., 2015, 54, 14685 CrossRef CAS PubMed
.
- Y. Geng, W. Sun, P. Ying, Y. Zheng, J. Ding, K. Sun, L. Li and M. Li, Adv. Funct. Mater., 2021, 31, 2007648 CrossRef CAS
.
- Y. Wang, Q. Chang, C. Xue, J. Yang and S. Hu, J. Colloid Interface Sci., 2022, 621, 33 CrossRef CAS PubMed
.
- D. Storer, J. Phelps, X. Wu, G. Owens, N. Khan and H. Xu, ACS Appl. Mater. Interfaces, 2020, 12, 15279 CrossRef CAS PubMed
.
- Y. Kong, H. Dan, W. Kong, Y. Gao, Y. Shang, K. Ji, Q. Yue and B. Gao, J. Mater. Chem. A, 2020, 8, 24734 RSC
.
- F. Yu, Z. Guo, Y. Xu, Z. Chen, M. S. Irshad, J. Qian, T. Mei and X. Wang, ACS Appl. Mater. Interfaces, 2020, 12, 57155 CrossRef CAS PubMed
.
- Y. Xu, X. Xiao, X. Fan, Y. Yang, C. Song, Y. Fanb and Y. Liu, J. Mater. Chem. A, 2020, 8, 24108 RSC
.
- L. Chen, Y. Ding, J. Gong, H. Xie, J. Qu and R. Niu, J. Colloid Interface Sci., 2022, 626, 231 CrossRef CAS
.
- H. Zhang, L. Li, B. Jiang, Q. Zhang, J. Ma, D. Tang and Y. Song, ACS Appl. Mater. Interfaces, 2020, 12, 16503 CrossRef CAS PubMed
.
- J. Li, X. Zhou, Y. Jing, H. Sun, Z. Zhu, W. Liang and A. Li, ACS Appl. Mater. Interfaces, 2021, 13, 12181 CrossRef CAS PubMed
.
- X. Chen, Z. Wu, D. Lai, M. Zheng, L. Xu, J. Huo, Z. Chen, B. Yu and M. Fu, J. Mater. Chem. A, 2020, 8, 22645 RSC
.
- Y. Kong, Y. Gao, B. Gao, Y. Qi, W. Yin, S. Wang, F. Yin, Z. Dai and Q. Yue, Chem. Eng. J., 2022, 445, 136701 CrossRef CAS
.
- L. Zhu, T. Ding, M. Gao, C. Peh and G. Ho, Adv. Energy Mater., 2019, 9, 1900250 CrossRef
.
- P. Yang, K. Liu, Q. Chen, J. Li, J. Duan, G. Xue, Z. Xu, W. Xie and J. Zhou, Energy Environ. Sci., 2017, 10, 1923 RSC
.
- M. Gao, C. K. Peh, H. T. Phan, L. Zhu and G. W. Ho, Adv. Energy Mater., 2018, 8, 1800711 CrossRef
.
- Y. Zhang, S. K. Ravi and S. C. Tan, Nano Energy, 2019, 65, 104006 CrossRef CAS
.
- L. Chen, J. Ren, J. Gong, J. Qu and R. Niu, Chem. Eng. J., 2023, 454, 140383 CrossRef CAS
.
- Z. Fan, J. Ren, H. Bai, P. He, L. Hao, N. Liu, B. Chen, R. Niu and J. Gong, Chem. Eng. J., 2023, 451, 138534 CrossRef CAS
.
- B. Chen, J. Ren, Y. Song, P. He, H. Bai, Z. Fan, R. Niu and J. Gong, ACS Sustainable Chem. Eng., 2022, 10, 16427 CrossRef
.
|
This journal is © The Royal Society of Chemistry 2024 |
Click here to see how this site uses Cookies. View our privacy policy here.