DOI:
10.1039/D3TA07761F
(Paper)
J. Mater. Chem. A, 2024,
12, 4086-4098
Electrochemical surface reconstruction of nickel cobalt pyrophosphate to Ni/Co-hydroxide-(oxy)hydroxide: an efficient and highly durable battery-type supercapacitor electrode material†
Received
14th December 2023
, Accepted 3rd January 2024
First published on 4th January 2024
Abstract
Developing transition metal-based electrode materials with high charge storage ability and excellent cycle life is a substantial challenge for supercapacitor applications. This report demonstrates an improved specific capacitance and excellent cycling stability for a Ni/Co-hydroxide-(oxy)hydroxide electrode material obtained from the electrochemical reconstruction of a Ni/Co-pyrophosphate precursor. Herein, we have prepared a series of nickel/cobalt pyrophosphate (NixCo100−x 600) (x = 90, 80, 70, 60, 50, 0) materials through a simple co-precipitation method followed by thermal annealing. Upon electrochemical treatment, the developed nickel/cobalt pyrophosphate materials were transformed into porous Ni/Co-hydroxide-(oxy)hydroxides. This is due to the etching of pyrophosphate anions with electrochemical cycling, confirmed by rigorous physical characterization. Among them, Ni-rich electrodes showed higher specific capacitance values due to the dominant intercalation redox behavior (battery-type storage), yet they suffer from poor cycle stability. In contrast, Co-rich electrodes display low specific capacitance and excellent capacitance retention as the charge storage mainly occurs through surface redox processes. Interestingly, the incorporation of an adequate amount of cobalt into the nickel system has dramatically improved the charge storage ability as well as cycling stability owing to the synergistic effect between Ni and Co redox centers and the balanced charge storage phenomenon contributed by both the surface and intercalation redox processes. Especially, the material developed from Ni60Co40 600 has exhibited a maximum specific capacitance of 566 F g−1 at 1 A g−1 current density and achieved an excellent capacitance retention of 84% (∼99% coulombic efficiency) up to 10
000 cycles. Further, the corresponding hybrid device (Ni60Co40 600//AC) has displayed an operational voltage window of 1.6 V and achieved a maximum energy density of 14.9 W h kg−1 at 794.5 W kg−1 power density and could retain ∼86% of its initial capacity even after 25
000 cycles, thereby indicating the suitability of the electrode for practical applications.
Introduction
The modern world demands the inevitable use of energy storage systems (ESSs) in devices ranging from small electronic gadgets to heavy electric vehicles.1–4 In this context, two potential candidates, i.e., batteries and supercapacitors (SCs), are found to be promising owing to their high energy and power output, respectively.5,6 Although SCs possess high power density, they still suffer from low specific energy compared to batteries.7 To boost the energy density of SCs, the development of high specific capacity electrode materials and the construction of hybrid devices with a wide operational voltage window (V) is important.8–10 In this context, battery-type electrodes are emerging as suitable alternatives due to their promising specific capacity compared to pseudo-capacitors and electrochemical double-layer capacitors (EDLCs).11,12 These materials store charges through intercalation and surface redox processes.13,14
Recently, Ni-based materials have been vastly explored for SCs due to their relatively cheap, earth-abundant nature, and battery-like charge storage nature.15 However, the poor cycling stability is a major bottleneck for Ni systems due to aggregation in longer cycles. Especially, nickel based sulfides (NixSy),16,17 selenides (NixSey),18,19 phosphides (NixPy),20,21 phosphates (Nix(PO4)y),22etc. delivered promising capacitance but suffer from poor cycling stability. There are a few reports that tried to enhance the cycling stability of the aforementioned materials. For instance, Nath et al. improved the cycling stability of nickel sulfide–nickel hydroxide structures by composite formation with thiophene and pyrrole-based copolymers.23 The co-polymer improves the stability by limiting the aggregation of the active material. Further, the stability can be improved by tuning the morphology of Ni-based materials. Recently, Zhu and coworkers boosted up the cycling stability of flower-type Ni(OH)2 particles through composite formation with ZnO flakes through electrodeposition.24 In the composite structure, the individual ZnO and Ni(OH)2 mutually prop each other, demonstrating excellent stability and morphology retention during a long run. In another report, Chen et al. demonstrated that cobalt incorporation in nickel selenide aids in the improvement of the cycling stability.25 In this context, different Co based materials are found to be promising candidates for supercapacitors.26,27 Especially, Co based LDHs28,29 and oxyhydroxides30 show excellent specific capacities and cycling stabilities.
Further, to improve charge storage, the development of highly porous electrodes with a larger number of metal centers is highly desired. In this context, electrochemical reconstruction of the precursor material is one of the ingenious strategies to enhance the electrochemical activity and stability. The reconstruction process is generally associated with the etching of functional moieties from the precursor materials during the electrochemical preconditioning process. The etching of the chemical groups (anionic and cationic) usually results in the exposure of more metal centers towards electrolytes and leads to facile transformation of metal precursors to their corresponding hydroxide/oxyhydroxide species. For instance, Liu et al. reported the transformation of trimetallic vanadium–cobalt–iron nitrides into their (oxy)hydroxide species by a surface reconstruction process via V etching.31 Similarly, P etching assists in the conversion of a NiCoP pre-catalyst to Ni(Co)OOH active species by surface reconstruction during the water oxidation reaction.32 In another report, Han et al. observed that cobalt iron phosphide displayed good electrochemical activity upon a bulk surface reconstruction process via etching of phosphorus.33 Recently, our group has reported enhanced electrochemical activity due to porous hydroxide-(oxy)hydroxide formation by a structural reconstruction process via etching of phosphate and vanadate ions.34,35 Yet, the etching-based reconstruction phenomenon is majorly limited for water oxidation catalysts and scarcely reported for supercapacitor applications. Our idea is to develop transition metal pyrophosphates and evaluate their potential for supercapacitor applications. Metal pyrophosphates (MxP2O7) possess interesting structures and are evolving as promising candidates for SCs due to their cost effectiveness, wide operational voltage window, and high redox activity.36 The presence of pyrophosphate units can make the materials more porous through the etching of anionic moieties during electrochemical cycling. Further, there are very few reports on pyrophosphate systems explored for energy storage applications. For instance, Senthilkumar et al. studied the aqueous hybrid device performance of Ni2P2O7 and graphitic carbon, which displays a good operating voltage window of 1.6 V.37 Similarly, Wang and co-workers developed a porous Ni2P2O7 nanowire, which shows a good specific capacity of 772.5 F g−1.38 Despite achieving high specific capacities, the above systems lack in good cycling stability. Our idea is to introduce an appropriate amount of cobalt into nickel pyrophosphate to improve the capacity retention and stability. We presume that cobalt incorporation enhances the surface storage kinetics, thereby improving the cycling stability.
In this work, we have discussed the synthesis of amorphous nickel cobalt pyrophosphate (P2O74−) which upon electrochemical bulk structural reconstruction generates active nickel–cobalt hydroxide-(oxy)hydroxide via etching of pyrophosphate ions. A series of bimetallic pyrophosphates NixCo100−x 600 (x = 100, 90, 80, 70, 60, 50, 0) are prepared by the co-precipitation method using water and ethylene glycol as solvents followed by thermal annealing. Interestingly, the introduction of Co into the Ni system improved both the charge storage ability and retention rate by controlling both the intercalation and surface redox phenomena. Particularly, the material developed after the reconstruction of Ni60Co40 600 manifests a maximum specific capacitance of 566 F g−1 at 1 A g−1 current density and a good capacitive retention of 84% up to 10
000 cycles. The transformation of Ni60Co40 600 to Ni,Co(OOH) via phosphate etching and synergistic effects between Ni and Co centers was found to be the primary reason for the observed result. Further, a hybrid device was assembled using Ni60Co40 600 and activated charcoal (AC). The hybrid device (Ni60C40 600//AC) provides an operational voltage window of 1.6 V and delivers a maximum energy density of 14.9 W h kg−1 at 794.5 W kg−1 power density. Additionally, the Ni60C40 600//AC device displayed excellent capacitive retention of 86% even after 25
000 cycles, indicating the potential of the developed material for practical applications.
Results and discussion
All the pyrophosphate materials were initially synthesized by a co-precipitation process using Co(NO3)2·6H2O, NiCl2·6H2O, and (NH4)2HPO4 as precursors. The above chemicals were dissolved in a water and ethylene glycol mixture and converted into ammonium metal hydrate. Subsequently, calcination at 600 °C results in desired pyrophosphate materials (see the details in the ESI†). For simplicity, the sample codes along with the Ni and Co ratio and the reaction temperature are summarized in Table 1.
Table 1 Sample codes for the as-prepared pyrophosphate materials with different Ni/Co ratios and reaction conditions
Sample codes |
Ni/Co |
Reaction temperature |
Co100 RT |
0/100 (only Co) |
Room temperature (RT) |
Ni100 RT |
100/0 (only Ni) |
RT |
Ni60Co40 RT |
60/40 |
RT |
Ni100 600 |
100/0 |
600 °C |
Co100 600 |
0/100 |
600 °C |
Ni90Co10 600 |
90/10 |
600 °C |
Ni80Co20 600 |
80/20 |
600 °C |
Ni70Co30 600 |
70/30 |
600 °C |
Ni60Co40 600 |
60/40 |
600 °C |
Ni50Co50 600 |
50/50 |
600 °C |
Characterization
The phase information of the synthesized materials was identified by PXRD analysis. The diffraction patterns of as-prepared Co100 RT and Ni100 RT closely matched with the standard patterns of ammonium cobalt phosphate hydrate ([NH4]CoPO4·H2O) (JCPDS No. # 01-089-6598) and ammonium nickel phosphate hydrate ([NH4]NiPO4·6H2O) (JCPDS No. # 00-021-0034), respectively (Fig. S1a†). Upon calcination, Co100 RT and Ni100 RT at 600 °C were converted into the corresponding pyrophosphate and denoted as Co100 600 and Ni100 600, respectively. The PXRD pattern of Co100 600 matched well with the monoclinic phase of Co2P2O7 (JCPDS No. # 01-079-0825, P21/c space group), whereas Ni100 600 displayed amorphous nature (Fig. 1a). This observation has been reported previously.37–40 Additionally, Ni100 RT was calcined at 800 °C, and the PXRD pattern of the resulting sample (Ni100 800) matched with that of a pure phase of Ni2P2O7 (JCPDS No. # 01-074-1604). The above results confirm that Ni100 600 is very likely the amorphous phase of Ni2P2O7. The amorphous nature of Ni60Co40 600 might be caused by the presence of higher Ni content in the system. Similar diffraction patterns are observed for the samples prepared with varying Ni/Co ratios except for Ni50Co50 600 which resembles the Co100 600 pattern (Fig. S1b†). Further, thermogravimetric analysis (TGA) of Ni100 RT and Ni60Co40 RT gives information about calcination temperatures required for the pyrophosphate formation. The calculated mass loss up to 600 °C is around 26% and 26.54% for Ni100 RT and Ni60Co40 RT, respectively. This is maintained up to 800 °C in a static air atmosphere (Fig. S2†). The weight loss is associated with the elimination of ammonia and structural water molecules and results in the transformation of [NH4]NiPO4·6H2O to Ni2P2O7.38,41,42 Furthermore, the PXRD pattern of the post TGA-analyzed Ni100 RT sample, denoted as Ni100 (post TGA), displays a small peak at ∼29°, confirming the formation of Ni2P2O7 (Fig. 1a). Subsequently, the chemical functional groups present in the materials were studied by Fourier-transformed infrared (FTIR) analysis. The FTIR spectra of Ni100 (post TGA) and all the annealed samples show two characteristic vibrational modes for PO3 and P–O–P units (Fig. 1b and S3†). The band in the 1061–1084 cm−1 and 568–585 cm−1 regions can be attributed to PO3 stretching and bending modes, respectively. In addition, a weak band noted in the 944–983 cm−1 region and a strong band appearing around the 737–752 cm−1 region are identified to be P–O–P bridge vibrations, confirming the presence of P2O74−.43–46 To understand the porosity and surface area of the as-prepared materials, nitrogen adsorption desorption experiments were performed. Co100 600, Ni100 600, and Ni60Co40 600 show a type-IV isotherm and H3 hysteresis loop, manifesting mesoporous nature and slit-like pore configuration in the materials (Fig. S4†).47 The surface area values are found to be 32, 12, and 14 m2 g−1 for Ni100 600, Co100 600, and Ni60Co40 600, respectively. In addition, the pore size distribution (PSD) was analyzed from the BJH distribution (Fig. S5†). The measured pore diameters for Ni100 600 and Co100 600 are 7.6 nm and 2.1 nm, respectively. The above values further corroborate the feasibility of enhanced intercalation or diffusion of electrolyte ions in Ni100 600 compared to Co100 600. Notably, an adequate quantity of Co introduction into the Ni system modulates the porosity in Ni60Co40 600 (Table S1†). This helps regulate the charge storage mechanism by keeping the surface storage and intercalation phenomenon at an optimum level.
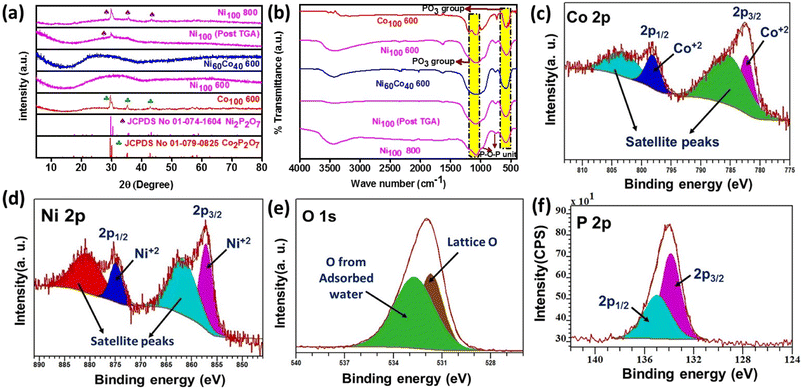 |
| Fig. 1 (a) PXRD pattern and (b) FTIR spectra of Ni100 600, Co100 600, Ni60Co40 600, Ni100 800, and Ni100 (post TGA). The standard XRD patterns of Ni2P2O7 (JCPDS No. # 01-074-1604) and Co2P2O7 (JCPDS No. # 01-079-0825) are shown in (a). High-resolution XPS analysis of (c) Co 2p, (d) Ni 2p, (e) O 1s, and (f) P 2p for as-prepared Ni60Co40 600. | |
Chemical state analysis
The chemical state information of the elements present in Ni60Co40 600 was obtained from X-ray photoelectron spectroscopic (XPS) analysis. The XPS survey scan of Ni60Co40 600 confirms the presence of Ni, Co, O, and P elements in the material (Fig. S6†). Further, peak fitting of the Co 2p spectrum shows two main peaks positioned at 782.3 (2p3/2) and 798.2 eV (2p1/2). The binding energy (BE) difference of 15.9 eV between the peaks confirms the Co2+ state (Fig. 1c).48,49 This is further supported by the characteristic satellite signals of Co2+ positioned at 785.6 and 803.4 eV. In the Ni 2p spectrum, the 857.2 and 874.9 eV peaks correspond to Ni 2p3/2 and 2p1/2, respectively. The noted peak separation of 17.7 eV suggests the presence of nickel in a +2 valence state (Fig. 1d).50,51 Additionally, the characteristic satellite peaks for Ni 2p noted at 862 and 880.7 eV confirm that nickel is present as Ni2+. The O 1s scan gives two peaks centered at 531.7 and 532.7 eV ascribed to lattice oxygen and adsorbed water molecules, respectively (Fig. 1e).34 The peak fitted P 2p spectrum gives two peaks (due to spin–orbit splitting) at 134 and 134.9 eV for 2p3/2 and 2p1/2, respectively. The observed peak separation of about 0.9 eV indeed authenticates the presence of a pyrophosphate ligand in the precursor framework (Fig. 1f).52 These aforementioned studies confirm the formation of bimetallic nickel cobalt pyrophosphate.
Morphological analyses
The morphology of the as-prepared materials was studied by field emission scanning electron microscopy (FESEM) and transmission electron microscopy (TEM). As shown in Fig. S7(a and b),† Co100 RT displays a hierarchical floret-like assembly, presumably formed through the self-assembly of micro-petals. Fig. S7(c and d)† display random floppy-kind architectures (size ∼30–60 nm) for Ni100 RT. However, the observed morphology of Ni60Co40 RT is similar to that of Ni100 RT (Fig. S7(e and f)†). Further, the calcined samples show isotropic morphological conversion along with some cracks throughout the surface. These pores could be attributed to the elimination of structural water and ammonia molecules (supported by TGA analysis) (Fig. 2a and b). Further, the Ni-rich system retained its initial particle-like texture even after calcination at 600 °C (Fig. S8(a–d)†). Interestingly, upon calcination of Ni60Co40 RT, the initial particles are rearranged and transformed into inter-connected network-like morphology with extended connectivity in Ni60Co40 600 (Fig. 2c). Similar observation was made in the Ni70Co30 600 material (Fig. S8(e and f)†). Meanwhile the Ni50Co50 600 resembles Co100 600 (Fig. S8(g and h)†). Further, the TEM analysis of Ni60Co40 600 confirms the network-like morphology with long-range connectivity among the particles (Fig. 2(d–g)). EDS analysis corroborates the presence of Ni, Co, O, and P elements in Ni60Co40 600 (Fig. 2h). In addition, the ICP-AES analysis shows that the Ni
:
Co ratio is 0.52
:
0.48 in the as-prepared Ni60Co40 600 (Table S2†).
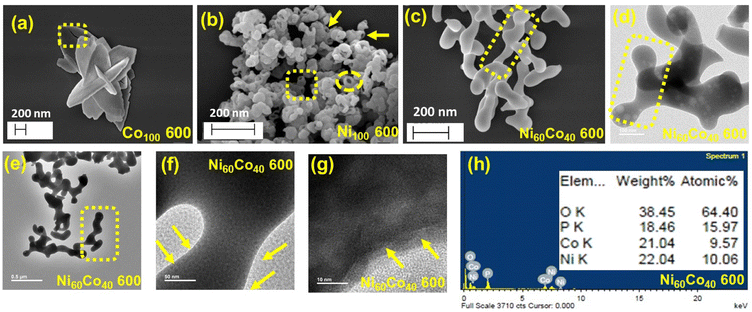 |
| Fig. 2 FESEM images of as-prepared (a) Co100 600, (b) Ni100 600, and (c) Ni60Co40 600, (d–g) TEM images and (h) EDS (Energy-dispersive X-ray spectroscopy) analysis for Ni60Co40 600. | |
Electrochemical activation
The precursors were drop-cast on carbon paper and activated through electrochemical preconditioning using cyclic voltammetry (CV) at a 50 mV s−1 scan rate in the voltage window 0–0.65 V (vs. Ag/AgCl) in 1 M KOH (see the details in the ESI†). Interestingly, CV results show a continuous increase in the current density up to ∼200 cycles for Ni100 600, Co100 600, and Ni60Co40 600 (Fig. 3(a–c)). Especially an observable improvement in the current density is noticed in the 200th cycle compared to the 1st cycle (Fig. 3(d–f)). This can be attributed to the occurrence of major structural reconstruction during electrochemical preconditioning. For instance, Allam and coworkers have studied a bimetallic Ni–Co oxy phosphide supercapacitor and emphasized the in situ generation of (oxy)hydroxide through structural reconstruction.53 Further, during preconditioning, well-distinguished redox peaks characteristic of Co2+/Co3+, Co3+/Co4+, and Ni2+/Ni3+ redox couples are observed with stepwise increment in the current density. The CV curves illustrate the faradaic nature of the charge storage and the exposure of more Ni and Co centers to the electrolyte during activation.54,55 Similar results are observed for different compositions of Ni/Co optimized samples (Fig. S9†). The aforementioned results strongly suggest that metal pyrophosphates are likely converted into electrochemically active hydroxide-(oxy) hydroxide (M(OH)2/MOOH) (M = Ni, Co) species mostly through surface reconstruction (vide infra). This phenomenon has been earlier reported during electrochemical processes in some electrocatalysts.56 Among all the prepared materials, Ni60Co40 600 manifests the maximum area under CV curves during electrochemical preconditioning. To optimize the electrolyte concentration, we have performed the CV and GCD tests of Ni60Co40 600 in 0.5 M, 1 M and 2 M KOH electrolytes. We observed the highest redox current and maximum specific capacitance in 1 M KOH (Fig. S10†) and hence 1 M KOH was chosen for further electrochemical studies. To get more information, detailed structural analyses were performed on the electrochemically activated Ni60Co40 600 sample.
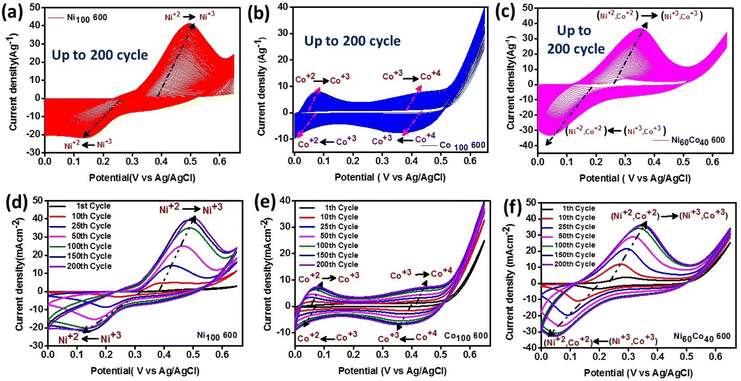 |
| Fig. 3 CV curves indicate current density improvement during preconditioning (1 to 200 cycles) for (a and d) Ni100 600, (b and e) Co100 600 and (c and f) Ni60Co40 600. | |
Post preconditioning characterization
To examine the chemical state, morphology, and elemental content of Ni60Co40 600 after preconditioning, ex situ studies like XPS, FESEM, HRTEM, and ICP-AES were performed. The XPS survey scan of the electrochemically activated Ni60Co40 600 electrode material confirms the presence of Ni, Co, and O, and a trace amount of P after preconditioning (Fig. S11†). Further, the deconvoluted Co 2p spectrum shows peaks at 780.5 eV (2p3/2) and 795.6 eV (2p1/2). The noted BE difference of 15.1 eV between the two peaks corroborates Co3+ formation.57 Additionally, the two peaks observed at 781.8 eV (2p3/2) and 797.4 eV (2p1/2) with a peak separation of ∼16 eV suggest the presence of Co2+ (Fig. 4a).47,58,59 Further, after activation, all Ni2+ centers transformed to Ni3+, which was confirmed by the presence of characteristic Ni3+ peaks at 855.9 eV (2p3/2) and 873.7 eV (2p1/2) (Fig. 4b).60 The peak fitted O 1s spectra display three peaks at 529.6, 531.3, and 532.6 eV, which are assigned to lattice oxygen, O from the hydroxyl group in an alkaline environment and adsorbed water molecules, respectively (Fig. 4c).48,61 These observations further validate the formation of MOOH (M = Ni, Co) during the preconditioning process. Interestingly, the P 2p spectrum shows an observable decrease in phosphorus content compared to the as-prepared material (Fig. 4d). This implies the etching of P (likely as pyrophosphate) during preconditioning. Further ICP-AES analysis was performed with the electrolyte sequentially collected after 0, 25, 50, 100, 150, and 200 CV cycles of preconditioning for the Ni60Co40 600 sample. Interestingly, the amount of P in the aliquots gradually increased from 0 to 150 cycles in the electrolyte. This observation confirms that P etches out likely as P2O74− during the electrochemical preconditioning of the working electrode (Fig. S12 and Table S3†). Interestingly, electrochemical preconditioning results in a noticeable change in the morphology of the material. The FESEM study (on the carbon paper loaded material) on the electrochemically preconditioned Ni60Co40 600 indicates that the initial network structure transformed into an agglomerated texture (Fig. S13†). Further, close inspection of TEM images revealed the formation of a porous flake-like morphology, which could be beneficial for better charge storage (Fig. 4e and f). The HRTEM image and its corresponding FFT pattern additionally support the existence of (210) and (009) planes characteristic of NiOOH (JCPDS No. # 00-027-0956) and CoOOH (JCPDS No. # 07-0169), respectively (Fig. 4g).62,63 Moreover, the appearance of the (101) plane in the FFT pattern confirms the formation Ni,Co(OOH) in the activated material (Fig. 4h).64,65 Based on our understanding and literature survey, we believe that the formation of Ni,Co hydroxide/(oxy)hydroxide from Ni,Co pyrophosphates is facilitated by the phosphate etching during the electrochemical process (detailed chemical mechanism is given in the ESI, page no. S24†).
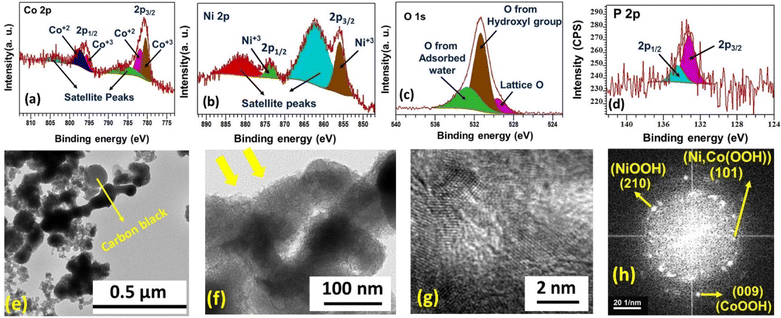 |
| Fig. 4 XPS spectrum of (a) Co 2p, (b) Ni 2p, (c) O 1s, and (d) P 2p after preconditioning of Ni60Co40 600, and (e and f) TEM images, (g) HRTEM image and (h) corresponding FFT pattern of Ni60Co40 600 after electrochemical preconditioning. In the inset of figure (e), the sphere represents the carbon black used for the preparation of the working electrode. | |
Electrochemical performance of the activated material.
The reconstructed materials (active materials) after electrochemical preconditioning were evaluated for supercapacitor performance. Initially, CV measurements of all the activated materials were recorded at a 5 mV s−1 scan rate (within 0–0.65 V vs. Ag/AgCl). The CV results reveal that the area under the CV curve for the sample Ni100 600 is higher compared to the Co100 600 sample demonstrating higher charge storage ability in the former (Fig. 5a). Upon Co incorporation the charge storage ability was altered. Especially, the material obtained after preconditioning of Ni60Co40 600 displays maximum charge storage ability compared to Co100 600, Ni100 600, and all Ni/Co materials with different compositions (Fig. 5a and S14†). Further, the CVs of all activated materials were recorded at varying scan rates (5 to 50 mV s−1). A significant increase in the redox current is noted for the activated Ni60Co40 600 with increasing scan rate and the cathodic and anodic peaks shifted toward more negative and positive potential regions, respectively. The notable peak-to-peak gap at a high scan rate indicates that charge storage is principally diffusion-controlled (Fig. S15†). A similar behaviour was observed for all other materials with different Ni/Co compositions (Fig. S16†). Subsequently, the specific capacity (Cs) of all activated materials has been measured from their CV curves (see eqn (1) and (2), ESI†). Among all the materials, electrochemically activated Ni60Co40 600 displays the highest Cs value. Further, with increasing scan rates, the Cs value decreases, which is attributed to insufficient time for the charge cumulation towards the electrode (Fig. 5b and S17†).66 Meanwhile, the Co incorporation into the nickel system increased the capacitive retention rate. For example, the activated Co100 600 and Ni100 600 retained 72% and 44% of their initial specific capacity, respectively, at a 50 mV s−1 scan rate. Interestingly, after cobalt incorporation, the retention rate increased to 52% in Ni60Co40 600 at the same scan rate (Fig. 5b).
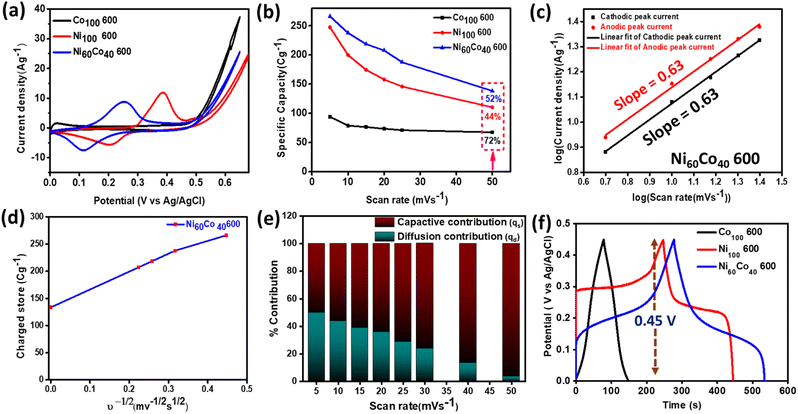 |
| Fig. 5 (a) CV curves, (b) plot of Csvs. scan rate for activated Ni100 600, Co100 600, and Ni60Co40 600 samples, (c) b value estimation (within the 5 to 25 mV s−1 scan rate range), (d) Csvs. ν−1/2 plot for activated Ni60Co40 600, (e) the bar diagram showing % contribution from diffusion and capacitive processes at 5 to 50 mV s−1 scan rates and (f) GCD curves for Ni100 600, Co100 600, and Ni60Co40 600 recorded at 1 A g−1. | |
Mechanism.
Post Co incorporation into Ni systems, the observed increase in the area under the CV curve and redox current density is ascribed to the synergistic interaction of Ni and Co centers in the bimetallic system. This has enthused us to look into the mechanistic details of charge storage trajectory occurring in different electrochemically activated materials. This is done by calculating the b value, which is estimated from the slope of the log(peak current) vs. log (scan rate) plot using the power law (eqn (1) and (2)).67 | log(i) = log(a) + b log(ν) | (2) |
where ν denotes the scan rate (mV s−1), i is the cathodic (ic) or anodic (ia) peak current (mA), and a and b are variable parameters. The b value specifies the behaviour of charge storage. For example, when the b value is ∼1, the i(= ic or ia) is linearly proportional to the scan rate (i ∝ ν), which signifies that the material stores the charge by a surface redox process (pseudo capacitor). Meanwhile, a b value of ∼0.5 indicates intercalation redox or diffusion control behaviour (battery-type capacitor).5 The estimated b values for Ni100 600 and Co100 600 are 0.5 and 0.98, indicating that charge storage mainly occurs through intercalation (battery-type) and surface redox (pseudocapacitive nature) processes, respectively. Interestingly, gradual incorporation of Co into the Ni system increases the b value successively (Fig. S18).† This indicates that Co modulates the charge storage phenomenon by increasing the surface contribution to the Ni system.
Especially, the b value for the activated Ni60Co40 600 is 0.63, suggesting that the material stores the charge through both intercalation and surface redox processes (Fig. 5c). Further, Trasatti's method was adopted to quantify both diffusion and capacitive contributions towards the charge storage of the materials. Generally, Trasatti's method correlates the diffusion (qd) and surface (qs) stored charges with varying scan rates. The total charge (qt) accumulated under the CV curve is a combination of the capacitive component (qs) and diffusive component (qd) (eqn (3) and (4)).68
Normally, the qs linearly varies with the scan rate (ν) due to quicker kinetics at the electrode surface compared to the bulk. On the other hand, the qd component varies as the inverse square root of scan rate (ν−1/2). Generally, at a low scan rate due to sufficient time for diffusion, intercalation kinetics are dominant. Further, at a high scan rate (ν → ∞) the entire contribution predominately arises from the surface of the electrode (capacitive contribution).69 Finally, the y-axis intercept from the qtvs. ν−1/2 plot (at 5 to 20 mV s−1) gives the information of qs (Fig. 5d). Subsequently, the bulk contribution (qd) is obtained by subtracting qs from qt. The contributions of qs and qd for Ni100 600 and Co100 600 are shown as a bar diagram in Fig. S19.† At a low scan rate (5 mV s−1), Ni100 600 and Co100 600 show 79.4% and 42.6% diffusion contributions, respectively (Fig. S20†). These outcomes further support the inherent diffusion behaviour of the Ni system over the Co system and correlate with the estimated b value (vide supra). Interestingly, after the incorporation of an optimum quantity of Co into the Ni system, the activated Ni60Co40 600 shows a 49.8% diffusion contribution (at a 5 mV s−1 scan rate). Further, at a high scan rates Ni60Co40 600 displays 28.9% (25 mV s−1) and only 3.5% (50 mV s−1) diffusion contribution indicating predominant surface contribution towards the charge storage at a very high scan rate (Fig. 5e and S21).†
The galvanostatic charge–discharge (GCD) curves of all electrochemically activated materials were recorded at 1 A g−1 current density within the voltage window of 0–0.45 V. In the case of Ni100 600, the GCD curve shows a long plateau, indicating battery-type charge storage or intercalation redox characteristics.70 In contrast, Co100 600 shows a quasi-triangular GCD profile suggesting surface redox or intrinsic pseudocapacitive behaviour. Interestingly, the GCD curve for Ni60Co40 600 contains both a plateau and distorted quasi-triangular shape (Fig. 5f). Similar results are noticed for materials with different Ni/Co ratios (Fig. 6a). These results further support that Co incorporation into Ni systems results in both intercalation and surface contributions towards charge storage, i.e., intercalation type pseudocapacitance (Fig. S22†).
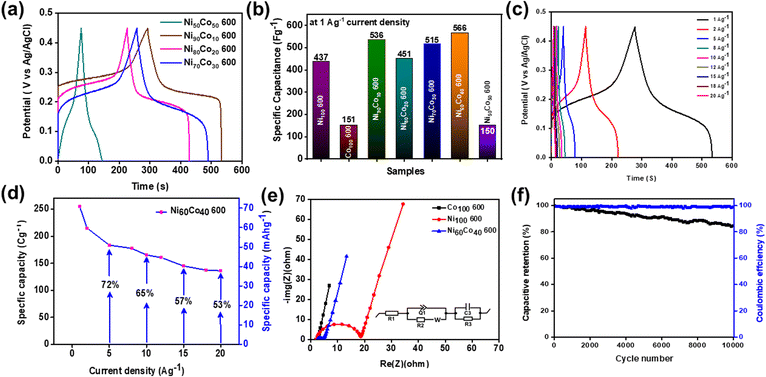 |
| Fig. 6 (a) GCD curves (recorded within 0–0.45 V and 1 A g−1), (b) bar diagram showing the Csp for the as-prepared material with different Ni/Co ratios, (c) GCD curves of activated Ni60Co40 600 at various current densities (1–20 A g−1), (d) Csvs. current density plot, (e) Nyquist plot for activated Ni100 600, Co100 600 and Ni60Co40 600 (inset shows the Randles circuit for impedance data fitting, where R, W, C, and Q parameters are the resistor, Warburg impedance, capacitor, constant phase element, respectively), and (f) durability test of activated Ni60Co40 600, performed at constant 10 A g−1 current density (up to 10 000 cycles). | |
Besides, the GCD profiles display a small iR drop associated with internal solution resistance and electrical contacts between the electrode and current outlets. Among the different activated materials, Ni60Co40 600 delivered the maximum discharge time and highest specific capacitance (Csp) value. The calculated Csp values (recorded at 1 A g−1 current density) of the respective materials are shown as a bar diagram in Fig. 6b. Subsequently, the GCDs of all activated materials were measured at different current densities (1 to 20 A g−1) (Fig. 6c and S23).† The calculated specific capacity (Cs) value of electrochemically activated Ni60Co40 600 is 254.79 C g−1 (70.77 mA h g−1) at 1 A g−1 current density. Further, with increasing current densities, the Cs values decreased (Fig. 6d and S24).† This is due to limiting diffusion time in a faster charge–discharge process.71 On the other hand, the activated Ni60Co40 600 could retain 72% of its initial capacity at 5 A g−1 current density and 53% at 20 A g−1 indicating the good rate capability of Ni60Co40 600 (Fig. 6d). Further the diffusion and interfacial charge transfer resistance (Rct) of the developed materials were monitored using electrochemical impedance spectroscopy (EIS) at the open circuit potential (OCP). The Nyquist plot of electrochemically activated Co100 600, Ni100 600, and Ni60Co40 600 displays a semicircle and a vertical line in the high and low frequency zones, respectively (Fig. 6e). At high frequencies, the real axis intersection denotes equivalent series resistance (ESR) due to interfacial connections between the electrode material/current outlet and the inherent resistance of the electrolyte ions. At low frequency, the semicircle diameter and vertical line slope represent Rct and Warburg impedance (Zw) associated with diffusion kinetics, respectively.68,72 Interestingly, after introduction of the requisite amount of Co, the semicircle diameter decreased in activated Ni60Co40 600 compared to Ni100 600. This observation indicates that cobalt incorporation into Ni systems helps in improving the charge transfer kinetics. Further, the observed ∼70° slope of the vertical line for Ni60Co40 600 manifests facile diffusion kinetics of electrolyte ions during charge storage.
Cycling stability is another important parameter to evaluate the suitability of the materials for supercapacitors. All the activated Ni/Co materials were subjected to continuous 5000 GCD cycles at 10 A g−1 current density. The activated Ni100 600 shows only a 39% retention rate which suggests poor electrochemical robustness of the Ni system. Meanwhile Co100 600 shows 96% capacitive retention indicating good stability (Fig. S25a†).
Interestingly, after gradual Co incorporation into the Ni system, cycling stability increases effectively. Especially, the activated Ni60Co40 600 displays an excellent retention rate of 94% (up to 5000 cycles). The retention rate for other materials with different Ni/Co compositions is shown in Fig. S25b.† From the above results, a 3D scatter plot is drawn showing the b value (both cathodic and anodic) and % capacitive retention to understand the relationship between the charge storage procedure and stability (Fig. S26).†
The 3D plot further proves that gradual Co incorporation increases the b value and surface contribution to the overall charge storage process. In addition, the plot shows an increase in the stability of the Ni system with Co incorporation. Further, among all the activated materials, Ni60C40 600 offers the best performance (Table S4).† This has encouraged us to extend the cycling stability test for longer cycles. The activated Ni60Co40 600 shows a retention rate of 84% up to 10
000 cycles at 10 A g−1 current density and ∼99% coulombic efficiency indicating excellent cycling stability and reversibility, respectively (Fig. 6f). The observed high stability value for Ni60Co40 600 is found to be better compared to other reported pyrophosphate materials (see Table S7).† Further, the stability test indicates that the final GCD curve shows only a little decrease in the plateau region as well as in the discharge time compared to the first cycle (Fig. S27 and S28).† This could be assigned to mild suppression of electrolyte migration channels present into the material during long GCD cycles.
Characterization after the electrochemical stability test
Meticulous physical characterization has been performed on the material after the stability studies. The XPS spectrum of the deconvoluted P 2p spectrum displays no characteristic signal indicating that the material's surface is devoid of any P (Fig. S29†). In addition, the P 2p XPS spectra of the as-prepared Ni60Co40 600, after preconditioning treatment and post-stability measurement, are compared in Fig. 7a. The results clearly indicate the etching of P (likely as P2O74−) during preconditioning. In addition, the XPS study confirms the existence of Co2+ and Co3+ along with Ni3+ even after a long-term durability experiment (Fig. S30).†. The peak position values are shown in Table S5.† The post-stability Co, Ni 2p, and O 1s XPS spectra closely match the XPS results obtained after preconditioning, revealing the structural robustness of the activated material. The above results further indicate the possible formation of M(OH)2/MOOH species (M = Ni, Co) in the post-stability material. Duan et al. demonstrated similar P etching through an electrochemical transformation from FePO4 in a nickel rich system to NiFe-OOH.73 Recently, Shreenivasa et al. noticed the absence of P in the post-XPS spectra owing to the surface reconstruction of BiPO4 to Bi2O3.74 Further, ICP-AES analysis of as-prepared Ni60Co40 600, after preconditioning and post stability testing, further proves that the majority of P etching occurs from the as-prepared material during the preconditioning and hardly any change is noted after stability (Table S6).† The mechanism of the etching phenomenon is summarised and mentioned in detail in the ESI.† The TEM images of the post stability Ni60Co40 600 sample display retention of the porous flake-like morphology as acquired after preconditioning (Fig. 7(b and c)). Moreover, the HRTEM image and the corresponding FFT pattern show (210), (111), and (101) planes, which corroborates the formation of NiOOH and Ni,Co(OOH), respectively (Fig. 7d).62,64,65,75 Further, the EDS study and elemental mapping analyses confirmed the presence of Co, Ni, O, and C (from the carbon paper substrate) and significant loss of P in the material after the extended durability test (Fig. S31).† The results above strongly support the formation of redox-active M(OH)2/MOOH (M = Ni, Co) species through structural reconstruction of NiCo pyrophosphate.
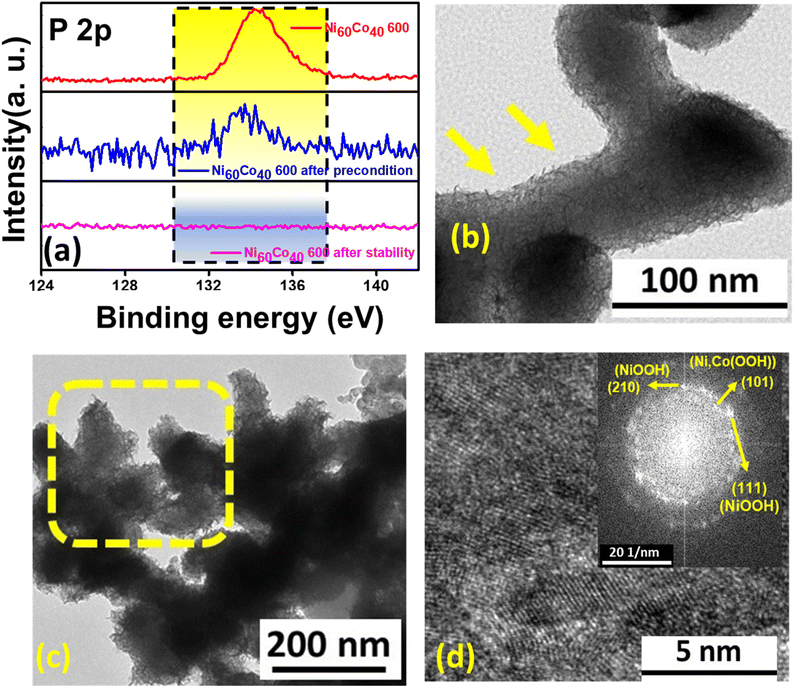 |
| Fig. 7 (a) Comparison of total P intensity in the as-prepared material, after preconditioning and after stability testing, (b and c) TEM images, and (d) HRTEM image and corresponding FFT pattern (inset). | |
Further, to understand the importance of Ni,Co hydroxides/oxyhydroxides derived through electrochemical reconstruction of the corresponding pyrophosphates, Ni,Co hydroxides were directly prepared (synthesis and characterisation are given in ESI page no. S22, Fig. S32 and S33†) and their activity was evaluated. The electrochemically activated Ni60Co40 600 displays better reconstruction (Fig. S34(a–d))† and a higher area under the CV curve, compared to the as-synthesized hydroxides, manifesting better charge storage ability of the reconstructed material (Fig. S34e).† In addition, the GCD curves additionally support that activated Ni60Co40 600 has a higher discharge time than the as-prepared Ni,Co hydroxide (Fig. S34f).† The calculated Csp for Ni,Co hydroxide is 220 F g−1 (at 1 A g−1), which is much lower than that of Ni60Co40 600, indicating the suitability of pyrophosphate as an efficient precursor material for supercapacitor applications (Fig. S34g).†
Further, the PXRD analysis was performed on the carbon paper-supported material to unveil the phase formation at charged and discharged states. The broad diffraction peaks between ∼36 and 39° and ∼65 and 66.8° for the charged electrode indicate the formation of (Ni,Co(OOH)) (NiOOH JCPDS No. # 00-027-0956 and CoOOH JCPDS No. # 07-0169) (Fig. S35a).†.76,77 In the case of the discharged electrode, the broad peaks observed between ∼37 and 38.6° and ∼61.4 and 63° suggest the formation of nickel cobalt hydroxide (Ni,Co(OH)2) (Ni(OH)2 JCPDS No. # 01-073-1520 and Co(OH)2 JCPDS No. # 00-045-0031) (Fig. S35b).† Therefore, the proposed charged and discharged reaction could be attributed as follows (eqn (5) and (6)).
| (Ni,Co(OH)2) + OH− → (Ni,Co(OOH)) + H2O + e− (charging) | (5) |
| (Ni,Co(OOH)) + H2O + e− → (Ni,Co(OH)2) + OH− (discharging) | (6) |
Hybrid device performance
The noted high cycling stability and good charge storage capability of Ni60Co40 600 motivated us to construct an asymmetric hybrid device. The hybrid device was fabricated in a two-electrode setup using Ni60Co40 600 as the positive electrode and activated charcoal (AC) as the negative electrode (Fig. S36).† Initially, the CVs of positive and negative electrodes were separately recorded in a three-electrode setup. AC shows an EDLC nature, whereas activated Ni60Co40 600 shows battery-type behaviour within their operational voltage window of −1 to 0 V and 0–0.6 V, respectively (Fig. 8a). Before constructing the device, the mass balance between positive and negative electrodes was maintained by the charge/mass balance equation (ESI†). Subsequently, a Ni60Co40 600//AC hybrid device was constructed with a series connection between Ni60Co40 600 and AC. The voltage window of the hybrid device was determined by recording the CVs (5 mV s−1 scan rate) at 1.2 to 1.8 V. The CV result suggests that Ni60Co40 600//AC has achieved a maximum operational voltage window of 1.6 V without any polarization (Fig. S37a).† The CVs of the hybrid device were recorded by varying the scan rates (10 to 100 mV s−1 within 0 to 1.6 V), which display both EDLC and redox behaviour (Fig. 8b).78 The 1.6 V operational voltage window for the Ni60Co40 600//AC hybrid device is further confirmed by recording the GCD in separate voltage windows (Fig. S37b).† Subsequently, the GCDs of the Ni60Co40 600//AC hybrid device were collected at different current densities (1 to 20 A g−1) at 1.6 V (Fig. 8c). The noted specific capacitance (specific capacity) value for the Ni60Co40 600//AC device is 42 F g−1 (18.79 mA h g−1) at 1 A g−1, which could retain about 14.37 F g−1 (6.22 mA h g−1) at 20 A g−1 current density, indicating a reasonable retention rate (Fig. 8d). The power and energy densities of the hybrid device were calculated from different GCD values (Fig. S38).† It is clear from the Ragone plot shown in Fig. 8e that the hybrid device displays a maximum of 14.9 W h kg−1 energy density at a power density of 794.5 W kg−1. The value obtained for the carbon paper deposited substrate is quite comparable with values reported in the literature for other pyrophosphate-based materials (Table S8).† In addition, the hybrid device could retain 5.1 W h kg−1 energy density at a high-power density of 15
965.2 W kg−1. Further, the hybrid device shows 86% capacitive retention and ∼99% coulombic efficiency up to 25
000 GCD cycles, implying excellent cycling stability and good chemical reversibility (Fig. 8f). The comparison of the electrochemical activity, including long term stability performance of the developed Ni60Co40 600//AC device with the reported pyrophosphate-based hybrid devices is illustrated in Table S8.† The data support the impressive cycling stability and capacitive retention of the Ni60Co40 600//AC hybrid device compared to other systems, mainly using a cost-effective carbon substrate.
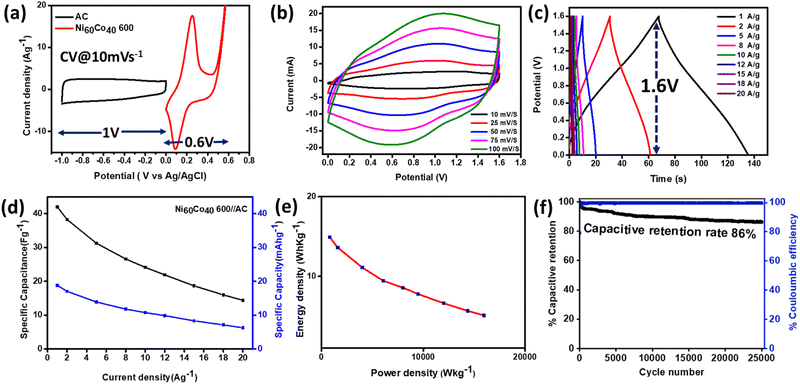 |
| Fig. 8 CVs of AC and Ni60Co40 600 measured in a 3-electrode setup, (b) CVs of the Ni60Co40 600//AC hybrid device measured at varying scan rates, (c) GCD curves for Ni60Co40 600//AC recorded at individual current density (within 0–1.6 V), (d) variation of Csp and Csvs. current density, (e) Ragone plot and (f) cycling stability test (at 10 A g−1 current density) of the hybrid device. | |
Conclusions
This work demonstrated an electrochemically induced surface reconstruction process for developing an efficient charge storage material. A simple co-precipitation process using different proportions of nickel and cobalt salts, followed by annealing, produced a series of amorphous bimetallic NiCo pyrophosphate precursors. Electrochemically induced reconstruction of the prepared bimetallic pyrophosphates resulted in the formation of highly porous Ni/Co hydroxide-(oxy)hydroxide species. Among the different pyrophosphate precursors, Ni-rich materials showed strong intercalation or battery-type charge storage behaviour and high specific capacitance compared to Co-rich systems. In contrast, the Co-rich system provides good cycling stability over the Ni system owing to predominant surface redox charge storage. Interestingly, introducing the requisite amount of Co into Ni systems improves the specific capacitance (due to the synergistic effect) and the cycling stability by modulating the intercalation and surface redox contribution towards the charge storage process. Particularly, the material obtained from the reconstruction of Ni60Co40 600 showed a maximum specific capacitance of 566 F g−1 at 1 A g−1 current density through both intercalation and surface redox processes. Further, the material displayed 84% retention of its initial capacity after 10
000 cycles, suggesting good cycling stability. In addition, the Ni60C40 600//AC hybrid device showed a maximum operational voltage window of 1.6 V with an energy density of 14.9 W h kg−1 at 794.5 W kg−1 power density. Further, the hybrid device retained 86% of its initial capacity after 25
000 cycles, suggesting excellent stability. These results indicate that the Ni60C40 600//AC hybrid device is a potential candidate for practical applications. To our knowledge, this is the first detailed report on an electrochemically induced structurally reconstructed pyrophosphate material for supercapacitor applications. We strongly envision that the work unlocks the potential of the reconstruction strategy using transition metal pyrophosphates, which can be extended to other earth-abundant transitional metal-based pyrophosphate materials for energy storage applications.
Author contributions
A. R., H. R. Inta, and V. M. conceptualized the scheme of this work. A. R. carried out all the synthesis, total physical characterization, and entire electrochemical measurements. H. R. Inta, S. Ghosh, and V. M. constantly assisted A. R. during manuscript writing. A. M., H. V. S. R. M. Koppisetti, and B. R. Verma constantly aided A. R. in performing the HRTEM, FESEM, XPS, and ICP-AES studies. S. Bag, S. Ghosh, and A. R. performed the BET study. The whole work was supervised by V. M. together with valuable suggestions. Before submission, all authors have given assent to the final version of the manuscript.
Conflicts of interest
The authors reveal no conflict of interest.
Acknowledgements
A. R., Heramba V. S. R. M. Koppisetti, H. R. Inta, A. M., and B. R. Verma thank DST-inspire & CSIR, UGC, respectively, for their fellowship. S. Ghosh thanks SERB-N-PDF (PDF/2017/001728/ES). The author V. M. acknowledges DST, India (DST/TMD/MES/2K17/70) for the project funding. The authors thank IISER Kolkata for instrumental facilities, including HRTEM (DIST-FIST facility). A. R. acknowledges SAIF, IIT Bombay for ICP-AES, and NIIST-Trivandrum for the XPS facility. A. R. also thanks Antarip Mitra, Viplove Mishra, Jaydeep Kumar, Khusboo S. Paliwal, Ashok Kumar Mahato, and Soumalya Debnath for their kind help and valuable suggestions.
Notes and references
- M. S. Islam and C. A. J. Fisher, Chem. Soc. Rev., 2014, 43(1), 185–204 Search PubMed.
- E. Pomerantseva, F. Bonaccorso, X. Feng, Y. Cui and Y. Gogotsi, Science, 2019, 366(6468), 969 CrossRef PubMed.
- Z. S. Iro, C. Subramani and S. S. Dash, Int. J. Electrochem. Sci., 2016, 11, 10628–10643 CrossRef CAS.
- B. Y. Guan, L. Yu, X. Wang, S. Song and X. W. Lou, Adv. Mater., 2017, 29, 1605051 CrossRef PubMed.
- D. P. Chatterjee and A. K. Nandi, J. Mater. Chem. A, 2021, 9, 15880–15918 RSC.
- V. Augustyn, P. Simon and B. Dunn, Energy Environ. Sci., 2014, 7(5), 1597–1614 RSC.
- P. Simon, Y. Gogotsi and B. Dunn, Science, 2014, 343, 1210–1211 CrossRef CAS PubMed.
- H. Khani and D. O. Wipf, ACS Appl. Mater. Interfaces, 2017, 9, 6967–6978 CrossRef CAS PubMed.
- J.-C. Liu, Z.-H. Huang and T.-Y. Ma, Small Struct., 2020, 1, 2000020 Search PubMed.
- Y. Deng, Y. Ji, H. Wu and F. Chen, Chem. Commun., 2019, 55, 1486–1489 RSC.
- B. Zhao, D. Chen, X. Xiong, B. Song, R. Hu, Q. Zhang, B. H. Rainwater, G. H. Waller, D. Zhen, Y. Ding, Y. Chen, C. Qu, D. Dang, C.-P. Wong and M. Liu, Energy Storage Mater., 2017, 7, 32–39 Search PubMed.
- J. Cherusseri, D. Pandey and J. Thomas, Batter. Supercaps, 2020, 3, 860–875 CrossRef CAS.
- Y. Gogotsi and R. M. Penner, ACS Nano, 2018, 12, 2081–2083 CrossRef CAS PubMed.
- J. S. Ko, C. H. Lai, J. W. Long, D. R. Rolison, B. Dunn and J. Nelson Weker, ACS Appl. Mater. Interfaces, 2020, 12, 14071–14078 CrossRef CAS PubMed.
- W. Xu, X. Zhao, F. Zhan, Q. He, H. Wang, J. Chen, H. Wang, X. Ren and L. Chen, Energy Storage Mater., 2022, 53, 79–135 CrossRef.
- Q. Xia, L. Si, K. Liu, A. Zhou, C. Su, N. M. Shinde, G. Fan and J. Dou, Molecules, 2023, 28, 4307 CrossRef CAS PubMed.
- N. M. Santhosh, K. K. Upadhyay, P. Strazar, G. Filipic, J. Zavasnik, A. Mao de Ferro, R. P. Silva, E. Tatarova, M. F. Montemor and U. Cvelbar, ACS Appl. Mater. Interfaces, 2021, 13, 20559–20572 CrossRef CAS PubMed.
- H. Reddy Inta, H. V. S. R. M. Koppisetti, S. Ghosh, A. Roy and V. Mahalingam, ChemElectroChem, 2023, 10, 1–11 CrossRef.
- S. Wu, Q. Hu, L. Wu, J. Li, H. Peng and Q. Yang, J. Alloys Compd., 2019, 784, 347–353 CrossRef CAS.
- D. Wang, L.-B. Kong, M.-C. Liu, W.-B. Zhang, Y.-C. Luo and L. Kang, J. Power Sources, 2015, 274, 1107–1113 CrossRef CAS.
- Y. Jia, D. Hu, X. Wang, H. Zhang and P. Du, J. Energy Storage, 2022, 50, 104713 CrossRef.
- S. S. Patil, J. C. Shin and P. S. Patil, Ceram. Int., 2022, 48, 29484–29492 Search PubMed.
- A. R. Nath, B. Madhu, A. Mohan and N. Sandhyarani, J. Energy Storage, 2022, 46, 103833 CrossRef.
- M. Zhang, R. Zang, M. Zhang, R. Liu, X. Zhu, X. Li, H. Cui and H. Zhu, J. Alloys Compd., 2022, 911, 164865 Search PubMed.
- H. Chen, S. Chen, M. Fan, C. Li, D. Chen, G. Tian and K. Shu, J. Mater. Chem. A, 2015, 3, 23653–23659 RSC.
- X. Zhao, L. Mao, Q. Cheng, J. Li, F. Liao, G. Yang, L. Xie, C. Zhao and L. Chen, Chem. Eng. J., 2020, 387, 124081 CrossRef CAS.
- Y. Li, B. Huang, X. Zhao, Z. Luo, S. Liang, H. Qin and L. Chen, J. Power Sources, 2022, 527, 231149 CrossRef CAS.
- B. Huang, W. Wang, T. Pu, J. Li, J. Zhu, C. Zhao, L. Xie and L. Chen, J. Colloid Interface Sci., 2018, 532, 630–640 CrossRef CAS PubMed.
- H. Wang, Q. He, F. Zhan and L. Chen, J. Colloid Interface Sci., 2023, 630, 286–296 CrossRef CAS PubMed.
- H. Wang, X. Ren, J. Chen, W. Xu, Q. He, H. Wang, F. Zhan and L. Chen, J. Power Sources, 2023, 554, 232309 CrossRef CAS.
- D. Liu, H. Ai, J. Li, M. Fang, M. Chen, D. Liu, X. Du, P. Zhou, F. Li, K. H. Lo, Y. Tang, S. Chen, L. Wang, G. Xing and H. Pan, Adv. Energy Mater., 2020, 10(45), 1–9 Search PubMed.
- W. Zou, C. Sun, K. Zhao, J. Li, X. Pan, D. Ye, Y. Xie, W. Xu, H. Zhao, L. Zhang and J. Zhang, Electrochim. Acta, 2020, 345, 136114 Search PubMed.
- X. Han, C. Yu, Y. Niu, Z. Wang, Y. Kang, Y. Ren, H. Wang, H. S. Park and J. Qiu, Small Methods, 2020, 4, 1–10 Search PubMed.
- R. Kumar, H. R. Inta, H. V. S. R. M. Koppisetti, S. Ganguli, S. Ghosh and V. Mahalingam, ACS Appl. Energy Mater., 2020, 3, 12088–12098 CrossRef CAS.
- A. Mondal, S. Ganguli, H. R. Inta and V. Mahalingam, ACS Appl. Energy Mater., 2021, 4, 5381–5387 CrossRef CAS.
- S. S. Patil and P. S. Patil, Chem. Eng. J., 2023, 455, 140639 Search PubMed.
- B. Senthilkumar, Z. Khan, S. Park, K. Kim, H. Ko and Y. Kim, J. Mater. Chem. A, 2015, 3, 21553–21561 RSC.
- Y. Zhou, C. Liu, X. Li, L. Sun, D. Wu, J. Li, P. Huo and H. Wang, J. Alloys Compd., 2019, 790, 36–41 CrossRef CAS.
- P. Suganya, A. Venkadesh, J. Mathiyarasu and S. Radhakrishnan, J. Solid State Electrochem., 2019, 23, 3429–3435 CrossRef CAS.
- A. G. Meguerdichian, T. Jafari, M. R. Shakil, R. Miao, L. A. Achola, J. Macharia, A. Shirazi-Amin and S. L. Suib, Inorg. Chem., 2018, 57, 1815–1823 CrossRef CAS PubMed.
- H. Pang, Y.-Z. Zhang, Z. Run, W.-Y. Lai and W. Huang, Nano Energy, 2015, 17, 339–347 CrossRef CAS.
- C. Wei, C. Cheng, S. Wang, Y. Xu, J. Wang and H. Pang, Chem.–Asian J., 2015, 10, 1731–1737 CrossRef CAS PubMed.
- N. Zhang, C. Chen, Y. Chen, G. Chen, C. Liao, B. Liang, J. Zhang, A. Li, B. Yang, Z. Zheng, X. Liu, A. Pan, S. Liang and R. Ma, ACS Appl. Energy Mater., 2018, 1(5), 2016–2023 CrossRef CAS.
- B. Boonchom and N. Vittayakorn, Mater. Lett., 2010, 64, 275–277 Search PubMed.
- V. Ramakrishnan, S. N. Kalkura and P. Rajagopal, Pramana, 1990, 34, 555–560 CrossRef CAS.
- A. Ait Salah, F. Gendron, K. Zaghib, M. M. K. Benkhaouja and C. M. Julien, J. Electrochem. Soc. Proc., 2008, 14, 165–172 Search PubMed.
- S. Ghosh, A. Mondal, G. Tudu, S. Ghosh, H. V. S. R. M. Koppisetti, H. R. Inta, D. Saha and V. Mahalingam, ACS Sustain. Chem. Eng., 2022, 10(22), 7265–7276 CrossRef CAS.
- S. Ghosh, R. Jana, S. Ganguli, H. R. Inta, G. Tudu, H. Koppisetti, A. Datta and V. Mahalingam, Nanoscale Adv., 2021, 3, 3770–3779 RSC.
- M. Mgolombane, O. M. Bankole, E. E. Ferg and A. S. Ogunlaja, Mater. Chem. Phys., 2021, 268, 124733 CrossRef CAS.
- S. Ghosh, H. R. Inta, M. Chakraborty, G. Tudu, H. V. S. R. M. Koppisetti, K. S. Paliwal, D. Saha and V. Mahalingam, ACS Appl. Nano Mater., 2022, 5, 7246–7258 CrossRef CAS.
- H. Li, Y. Yu, M. B. Starr, Z. Li and X. Wang, J. Phys. Chem. Lett., 2015, 6, 3410–3416 Search PubMed.
- R. Mahajan, R. Prakash, R. J. Choudhary and D. M. Phase, Phys. Scr., 2021, 96(7), 075808 CrossRef.
- A. A. Saleh, D. M. Sayed, L. A. V. Nagle-Cocco, G. Divitini, L. G. Ghanem, C. Ducati and N. K. Allam, ACS Appl. Energy Mater., 2022, 5(6), 7661–7673 CrossRef CAS.
- Y.-T. Lu, Y.-J. Chien, C.-F. Liu, T.-H. You and C.-C. Hu, J. Mater. Chem. A, 2017, 5(39), 21016–21026 RSC.
- B. Lu, D. Cao, P. Wang, G. Wang and Y. Gao, Int. J. Hydrogen Energy, 2011, 36(1), 72–78 Search PubMed.
- A. Sivanantham, P. Ganesan, A. Vinu and S. Shanmugam, ACS Catal., 2020, 10(1), 463–493 CrossRef CAS.
- C. Yuan, H. G. Wang, J. Liu, Q. Wu, Q. Duan and Y. Li, J. Colloid Interface Sci., 2017, 494, 274–281 Search PubMed.
- A. Mondal, H. R. Inta, A. Roy, A. Kumar Mahato and V. Mahalingam, ACS Appl. Nano Mater., 2023, 6, 12040–12049 CrossRef CAS.
- C. Alex, S. C. Sarma, S. C. Peter and N. S. John, ACS Appl. Energy Mater., 2020, 3(6), 5439–5447 CrossRef CAS.
- H. R. Inta, S. Ghosh, A. Mondal, G. Tudu, H. V. S. R. M. Koppisetti and V. Mahalingam, ACS Appl. Energy Mater., 2021, 4(3), 2828–2837 CrossRef CAS.
- H. V. S. R. M. Koppisetti, S. Ganguli, S. Ghosh, H. R. Inta, G. Tudu and V. Mahalingam, ACS Appl. Energy Mater., 2022, 5(2), 1681–1689 Search PubMed.
- Q. Zhang, C. Zhang, J. Liang, P. Yin and Y. Tian, ACS Sustain. Chem. Eng., 2017, 5(5), 3808–3818 CrossRef CAS.
- Q. Song, J. Wang, Q. Sun, X. Wang, Z. Zhu, C. Pei, H. Li, Z. Luo, X. Huang and W. Huang, Chem. Commun., 2020, 56(71), 10285–10288 RSC.
- Z. Y. Wang, L. Wang, S. Liu, G. R. Li and X. P. Gao, Adv. Funct. Mater., 2019, 29, 1901051 CrossRef.
- X. Liu, K. Ni, B. Wen, R. Guo, C. Niu, J. Meng, Q. Li, P. Wu, Y. Zhu, X. Wu and L. Mai, ACS Energy Lett., 2019, 4, 2585–2592 CrossRef CAS.
- S. J. Marje, P. R. Deshmukh, J. L. Gunjakar, C. D. Lokhande and U. M. Patil, Energy Fuels, 2021, 35(17), 14110–14121 CrossRef CAS.
- K. Wang, S. Wang, J. Liu, Y. Guo, F. Mao, H. Wu and Q. Zhang, ACS Appl. Mater. Interfaces, 2021, 13, 15315–15323 Search PubMed.
- T. S. Mathis, N. Kurra, X. Wang, D. Pinto, P. Simon and Y. Gogotsi, Adv. Energy Mater., 2019, 9, 1–13 Search PubMed.
- S. Kaipannan, K. Govindarajan, S. Sundaramoorthy and S. Marappan, ACS Omega, 2019, 4, 15798–15805 Search PubMed.
- K. V. Sankar, Y. Seo, S. C. Lee and S. Chan Jun, ACS Appl. Mater. Interfaces, 2018, 10, 8045–8056 CrossRef CAS PubMed.
- G. Nagaraju, G. S. Raju, Y. H. Ko and J. S. Yu, Nanoscale, 2016, 8, 812–825 RSC.
- S. S. Rabbani, H. Mustafa, A. Zafar, S. Javaid, M. A. Bakar, A. Nisar, Y. Liu, S. Karim, H. Sun, S. Hussain, Z. Zafar, Y. Faiz, F. Faiz, Y. Yu and M. Ahmad, Electrochim. Acta, 2023, 446, 142098 CrossRef CAS.
- R. Duan, Y. Li, S. Wang, J. Gong, Y. Tong and W. Qi, J. Phys. Chem. Lett., 2022, 13, 1446–1452 CrossRef CAS PubMed.
- L. Shreenivasa, A. Siddaramanna, Y. Kalegowda, A. Syed, N. Marraiki and P. S. Adarakatti, Solid State Sci., 2022, 124, 106803 CrossRef CAS.
- J. Liu, W. Qiao, Z. Zhu, J. Hu and X. Xu, Small, 2022, 18, 2202434 CrossRef CAS PubMed.
- M. Gao, Y. Li, J. Yang, Y. Liu, Y. Liu, X. Zhang, S. Wu and K. Cai, Chem. Eng. J., 2022, 429, 132423 CrossRef CAS.
- S. Ganguli, S. Ghosh, G. Tudu, H. Koppisetti and V. Mahalingam, Inorg. Chem., 2021, 60, 9542–9551 CrossRef CAS PubMed.
- C. Lu, Y. Yan, T. Zhai, Y. Fan and W. Zhou, Batter. Supercaps, 2020, 3, 534–540 CrossRef CAS.
|
This journal is © The Royal Society of Chemistry 2024 |
Click here to see how this site uses Cookies. View our privacy policy here.