Life cycle assessment of chitosan modified Ni–Fe layered double hydroxide for arsenic(III) sequestration in aqueous medium: comparison of the impacts of adsorbent recycling, instrument use and source of energy†
Received
6th October 2023
, Accepted 10th June 2024
First published on 11th June 2024
Abstract
Evidence of arsenic in potable water is a huge global concern for human well-being. For the adsorption of arsenic from groundwater, a promising material Ni–Fe layered double hydroxide modified using chitosan (NFC) was synthesized in a lab-scale study. In the original research, two pollutant-adsorbent contact approaches, i.e., magnetic stirrer and ultrasonicator, were utilized to accomplish maximum pollutant removal, and the latter was found to give better results. The current work utilized OpenLCA software and the ReCiPe Midpoint (H) (v1.02) approach to conduct a Life Cycle Assessment (LCA), which assesses and compares the environmental effects of both techniques. The synthesis of 1 kg of NFC and treatment of 1000 L of water contaminated with As(III) from a 50 mg L−1 initial concentration to its WHO acceptable limit served as the basis for evaluations. Environmental effects of handling used materials were taken into account. Furthermore, environmental impacts arising from recycling of the adsorbent were also determined. According to the LCA analysis, the use of electricity and chemicals mainly nickel and liquor ammonia were the main causes of the environmental effects, especially in the global warming potential, human toxicity potential, freshwater ecotoxicity potential, and marine ecotoxicity potential categories. The manufacture of the nanomaterial was the most energy-intensive step of the process, which indicates that energy consumption needs to decrease during scaling up. As electricity consumption is optimized for large-scale operations, there is potential for an increased relative contribution of chemicals to environmental impacts. Furthermore, two distinct electrical sources were chosen to perform sensitivity analysis. The environmental effects of the current development process and application were contrasted with those of granular activated carbon (GAC) and it was found to have fewer negative effects than LDH. It can be concluded that energy and chemical optimization should take precedence in the manufacture of future materials.
Environmental significance
The presence of arsenic in drinking water is extremely concerning for everyone's health. In a lab-scale study for the removal of As(III) from contaminated water, a promising material Ni–Fe layered double hydroxide modified using chitosan (Ni–Fe/Ch) was synthesized for the adsorptive removal of As(III) from contaminated water. The prepared adsorbent in the presence of ultrasonic waves showed exceptionally good results compared to those obtained using a magnetic stirrer in the initial investigation of decontamination of As(III) from waste water. The current paper uses the OpenLCA software and ReCiPe Midpoint method to conduct their life cycle assessment and compare the environmental effects of the two techniques. Evaluations were based on the synthesis of 1 kg of Ni–Fe/Ch and the treatment of 1000 L of water contaminated with As(III) from an initial concentration of 50 mg L−1 to its WHO permitted limit. The implications of processing used materials on the environment have been considered along with the environmental effects of recycling and reusing the adsorbent that were calculated using the ReCiPe Midpoint method and sensitivity analysis was also performed. It is important to mention that to date no data have been reported on LCA analysis of Ni–Fe LDH and only a handful of studies have been performed on all the layered double hydroxides combined. In our study, we found that the major hotspot having the maximum environmental impact was the synthesis part due to the use of electricity and toxic chemicals such as nickel nitrate and liquor ammonia. In order to achieve “real-world impact,” the current study examines the effect of adsorbent synthesis and application for the detoxification of arsenic-contaminated water on environmental sustainability.
|
1 Introduction
The technique of adsorption has been crucial to wastewater treatment since activated carbon was introduced as a standard adsorbent in 1940.1 Although the superior adsorption capacity of activated carbon is undeniable, its high production costs and additional need for pricey chemicals for regeneration prompted researchers to hunt for alternative effective and affordable adsorbent materials. Anionic clays, which are layered double hydroxides (LDHs) in their native state, are a large family of layered minerals.
Recently, interest in the use of layered double hydroxides (LDHs) as adsorbents has been growing fast owing to their peculiar properties viz., ion-exchange capacity, extensive surface area and anion selectivity.2 LDHs, alternatively referred to as anionic clays, consist of positively charged layers resembling brucite, with anionic species or molecules intercalated within the interlayer region.3 The interlayer space of LDHs can accommodate a wide range of anionic species, making them promising materials for various applications such as water treatment, environmental remediation, and catalysis.4 Heavy metal ions, such as Pb2+, Cd2+, and Cu2+, are toxic and harmful to human and animal health, and their removal from water is a significant challenge.5 LDHs have been effective in removing heavy metal ions from water through ion exchange and adsorption mechanisms.6–8 In addition to heavy metal ions, LDHs have also been used for the removal of organic pollutants such as pharmaceuticals, dyes, and pesticides, which are persistent and harmful to the environment.9
Nevertheless, LDHs are still in their early development stages, and most of these innovative adsorbents are only being studied in laboratories. To develop these materials sustainably, it is necessary to have knowledge about the feasibility of producing adsorbents, their environmental emissions, performance, and effects on health of the public.
Life cycle assessment (LCA) is a tool used to analyse the likely environmental impacts of a service or product throughout its entire lifespan. LCA is also used to provide preliminary assessments for emerging technologies, which allow the re-designing and improvement of a product or a process by evaluating its environmental performance.10 In a published study, Gonzalez and co-authors performed LCA of nanomaterial-based adsorbents (nano-TiO2, granular activated carbon and silicate-titanate nanotubes-chitosan beads (STNTs-Ch beads)) for Cd removal.11
In our previous study, we synthesized a composite of layered double hydroxide for the adsorption of arsenic from water in a lab-scale study.12 Arsenic was selected as the pollutant of choice because of its hazardous properties, particularly when it combines with heavy metals. Industrial wastewater, laden with heavy metals, is recognized as a significant environmental hazard, posing threats to both microorganisms and human well-being. Excessive concentrations of heavy metals primarily disrupt vital biological processes and the production of crucial macromolecules within living organisms. Within this array of pollutants, arsenic's presence in aquatic ecosystems has long been a matter of global concern. Inorganic arsenic ions typically exist in two prevalent oxidation states: As(V) and As(III). Since LDHs containing Mg, Ca, and Al have drawbacks such as bulk mass loss and high solubility in water leading to heavy metal discharge, Ni–Fe LDH was selected due to its poor solubility product (pKsp = 60.81).12 Chitosan intercalated Ni–Fe layered double hydroxide (Ni–Fe LDH/Ch), synthesized by the co-precipitation method, reduced the concentration of arsenic in natural water by 62% and was reused up to 5 consecutive cycles. In this study, we aim to use LCA analysis on this new adsorbent to extract information on the key factors involved in its synthesis process, as well as offer a basis for comparing its environmental impact to that of other similar materials that are currently being used or intended for the same purpose. According to our assessment, this would be the first study on LCA performed on synthesis and use of Ni–Fe LDH/chitosan. As it is, the literature on LCA on layered double hydroxides is very scarce and only a handful of studies have been reported so far. Hence, making comparisons can be challenging since prior studies have focused on evaluating similar materials for different utilities. For example, silica nanospheres were studied for use in insulating materials, while other adsorbents were developed to remove As(III)but had a different structure from LDHs, such as a carbon-based adsorbent.13,14 Additionally, comparing the new adsorbent to commercial products may not always be useful due to differences in their usage scales. Despite these challenges, granular activated carbon was selected for comparison due to its wide industrial-scale application.
2 Methods
The current research examined the full life cycle of the process, from production to use and recycling, but did not include the disposal phase. The purpose was to gather relevant information to promote scaling up of the process in a sustainable manner. The study evaluated the environmental impacts of every step of the process, including the production, use for arsenic adsorption, recycling, and reuse of the adsorbent. A sensitivity analysis was conducted by assuming the North-Indian electricity supply as the base and comparing it with renewable sources of electricity supply mix. The study also compared the impacts of producing and using Ni–Fe LDH/chitosan with those of the industrial standard i.e., granular activated carbon (GAC).
LCA was conducted according to the International Organization for Standardization's methodology (ISO 14040:2006, ISO 14044:2006), which comprises four key phases: (i) goal and scope definition, (ii) the life cycle inventory analysis (LCI), (iii) the life cycle impact assessment (LCIA) phase and (iv) the interpretation of the results, including sensitivity analysis.
2.1. Goal and scope definition
The objective of this study is to ascertain the environmental impact connected to the production, application, and recycling of a novel adsorbent, Ni–Fe LDH/Ch.12 It was envisaged that the data gathered would let the process be scaled up sustainably. Envisioning that collected data will aid sustainable scaling is crucial. It ensures proactive planning, identifies scalability challenges, and demonstrates a commitment to sustainability, fostering economic growth and community development. This emphasis motivates stakeholders to prioritize data gathering for successful project development. A flowchart of the entire procedure, from the creation of Ni–Fe LDH/Ch to its use and recycling (desorption and regeneration), is shown in Fig. 1. In our previous investigation, we studied the effects of recycling six times and found that the composite's adsorption ability remained intact until the fifth cycle. As a result, we chose five recycling cycles as the basis for our current study. Each recycling cycle, from stage I to stage III, is considered one recycling time or 1REC since the adsorbent is created and recycled once. Similarly, 5REC refers to five recycling cycles or the scenario where the material is created and recycled five times. NREC refers to stages I through III, during which the Ni–Fe LDH/Ch was not recycled. The functional unit (FU) here was taken as 1 kg Ni–Fe LDH/Ch which has an adsorption capacity of 93.15 mg g−1.
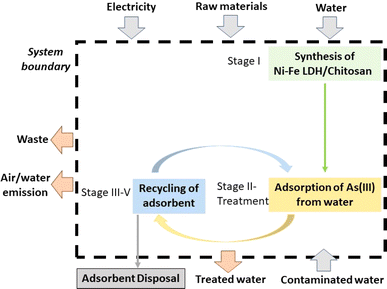 |
| Fig. 1 System boundaries for the current LCA in a cradle-to-use approach of 1 kg of Ni–Fe LDH/chitosan composite for arsenic removal from water. | |
Fig. 1 displays the system boundary, which outlines the entire life cycle of Ni–Fe LDH/Ch in cradle-to-use, including adsorbent production (stage I, green box), (stage II, yellow box) use, and 5 cycles of recycling (stage III–V, blue box). The cradle stage involves the extraction of raw materials, which comprises all the chemicals required for the process, such as acetic acid, nickel nitrate, ferric nitrate, etc.Table 1 details the life cycle inventory. During stage II, Ni–Fe LDH/Ch was utilized to remove As(III) from the solution, but the disposal of the spent adsorbent was not considered in the system because that part hasn't been studied. Additionally, treating the waste generated at any stage and desorbed As(III) in stage V were not included. This LCA study is preliminary, and more investigations will be carried out as the required data become known. This study can be combined with future cradle-to-grave studies, including end-of-life treatment and application facilities. Table 1 also provides a description of the waste generated at each stage, which is also shown in Fig. 1.
Table 1 Life cycle inventory of 1 kg Ni–Fe LDH/Ch synthesis and its use for As(III) removal
Stage |
Inputs |
Outputs/waste |
Chemicals and energy |
Quantity |
Chemicals and energy |
Quantity |
Stage I |
Acetic acid |
0.28 L |
Ni–Fe LDH/Ch |
1 kg |
Chitosan |
0.28 kg |
Water |
Nickel chloride |
5.55 kg |
Ferric chloride |
2.31 kg |
Urea |
1.28 L |
Liquor ammonia |
7.14 L |
Electricity |
25.42 kW h |
Water |
50 L |
Stage II |
Ni–Fe LDH/Ch |
1 kg |
Ni–Fe LDH/Ch–As |
1.005 kg |
Electricity (ultrasonicator) |
0.08 kW h |
Electricity (magnetic stirrer) |
0.0057 kW h |
Stage III–V |
Ni–Fe LDH/Ch–As |
1 kg |
Ni–Fe LDH/Ch–As |
Electricity |
29 kW h |
HCl (98% v/v) |
5 L |
2.2. Assumptions and limitations
Applied assumptions in this LCA analysis are listed below:
(i) Transporting the materials from the business to the lab was not taken into account due to a lack of primary data.
(ii) Transporting raw materials to the company was not taken into account due to a lack of primary data.
(iii) North India (base case) was considered the geographical coverage for electricity and renewable energy sources as the alternative case as the university campus lies in the northern part of India.
(iv) The “market process for electricity, medium voltage” was selected for modelling as recommended when using supply mixes as this selection aligns with best practices in modeling electricity supply chains, particularly when considering medium voltage scenarios.
(v) “Transformation processes” were selected for all chemicals from the ecoinvent database. The materials needed to make a product, as well as materials derived from resource extraction and accompanying emissions, were included. Losses associated with transportation were not taken into account.
(vi) The production of some chemicals was based on ecoinvent. The following processes were used based on our literature search:
(a) Nickel chloride was assumed to be produced from the reaction of nickel concentrate with hydrochloric acid.
(b) Ferric chloride was assumed to be produced from the reaction of iron pellets with hydrochloric acid.
(c) Chitosan: Indian chitosan production reported by Muñoz et al. (2018) was selected since it was the sole research that provided publicly available primary data.
2.3. Inventory analysis of the life cycle
Table 1 shows the inputs and outputs for every stage (I–V) which were obtained from primary data. The data were then recalculated to 1 kg Ni–Fe LDH/Ch, which is the assigned functional unit (FU) in this study. Additional experiments were conducted to calculate chemical consumption, and the energy consumption was theoretically calculated based on equipment information provided by the manufacturer.
For comparison with a widely used adsorbent, granular activated carbon (GAC) was selected. Ecoinvent (version 3.5) provided GAC data and only synthesis steps for both the adsorbents were compared due to different usages for both the adsorbents. Since recycling was not performed in the aforementioned experiments and we lacked data to analyse the environmental impacts arising from the created nanoadsorbent, use, recycling and disposal were excluded from the comparison.
2.4. Description of Ni–Fe LDH/Ch production and recycling stages
The production and recycling of Ni–Fe LDH/Ch involved several stages, and this study emphasizes both the theoretical and experimental data used. The steps are pictorially represented in Fig. 2.
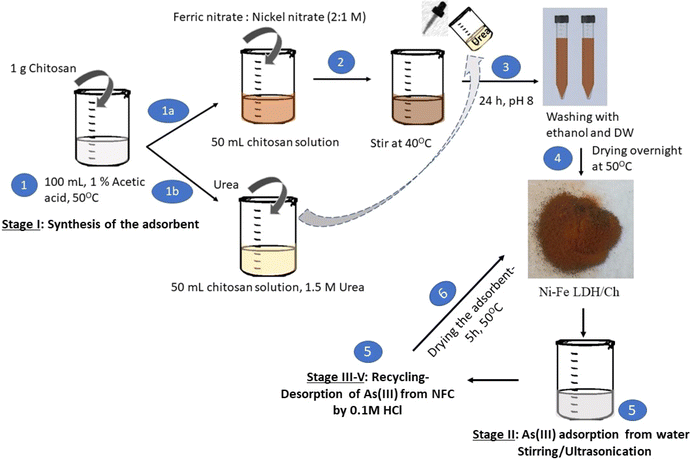 |
| Fig. 2 Steps of synthesis of Ni–Fe LDH/chitosan and its utilization for removal of As(III) in aqueous solution. | |
Stage I: 100 mL of chitosan solution was made by thoroughly homogenizing chitosan (1 g) in glacial acetic acid (1%) at 60 °C while stirring continuously. The chitosan solution was divided into two equal portions; urea solution (1.5 M) was appended to 1 part and 50 mL of nickel and ferric nitrate (1
:
2 M ratio) was added to the other portion. The latter was then vigorously stirred at 40 °C while adding urea solution dropwise. After bringing the pH to 8 through addition of NH4OH (2 M) dropwise, it was held at 24 h stirring. The LDH washing was performed with distilled water and ethanol until the solution pH reached 7. Finally, it was kept overnight at 50 °C until dried and a brown powder was obtained.
Stage II: the composite was utilized for adsorptive removal of As(III) from water by two methods. First one was by simple stirring and the other was in the presence of ultrasonic waves which removed around 62% and 75% of arsenic from water, respectively.
Stage III–V: this stage comprises recycling and reuse of the adsorbent. Desorption of arsenic was performed by soaking the spent adsorbent in 0.1 M HCl solution for 1 hour followed by drying for 5 h in a hot air oven before reusing.
2.5. Life cycle impact assessment
The LCA research was performed using the OpenLCA software (version 1.11), and database ecoinvent (version 3.4) served as the source for the procedures applied. The attributional model method (also called the allocation at the point of substitution (APOS) system model in ecoinvent) was used, wherein the load is proportionally attributable to the different processes. This system was used to early get an in-depth understanding of the various environmental implications of this LCA. The ReCiPe Midpoint (H) (v1.02) approach was then used to model the data that had been collected.15 This method was selected as it conveys the uncertainties of the model, offers thorough method documentation, includes a range of impact categories, and the European Commission supports its implementation.16 The accuracy of the input data is crucial in a LCA study, especially when based on laboratory-scale data, because such studies inherently carry potential errors. Laboratory-scale data often involve controlled environments that do not fully replicate real-world conditions, leading to discrepancies in the results. These controlled settings might not account for variations in material quality, process efficiencies, and operational scales that occur in actual industrial applications. Additionally, small-scale experiments can have measurement uncertainties and may overlook broader environmental interactions. Therefore, ensuring precise and accurate input data is vital to minimize these errors and provide a more reliable and applicable LCA study.17–19
2.6. Comparison with granular activated carbon used for treating wastewater
The outcomes of the current LCA analysis were contrasted with those obtained for granular activated carbon (GAC). GAC was selected as the choice of comparison due to its widespread use in industries.
2.7. Sensitivity analysis
Indian power production in the northern grid, medium voltage served as the basic case in this LCA model, which has largely fossil fuel (∼55% coal) based electricity in it. For comparison, a sensitivity analysis was performed using the renewable energy product, medium voltage supply mix.
2.8. Cost analysis
The primary factor in determining whether a technology is accessible to the local community is its operating cost of treatment. The price of energy input and raw materials for the entire process has been considered for the economic evaluation of synthesis of Ni–Fe LDH/Ch. The economic analysis did not account for the cost of human resources. 1 kg of adsorbent produced at the lab-scale was calculated using eqn (1): | Cost = a × Cch + b × Caa + c × CNC × d × CFC + e × CU + f × CLA + g × electricity | (1) |
Here, Cch, Caa, CNC, CFC, CU, and CLA are the weights in kg of chitosan, acetic acid, nickel chloride, ferric chloride, urea and liquor ammonia used and Celectricity is the amount of energy used in kW h. Coefficients of cost a to g are set in accordance with the Indian market in 2022. Moreover, the overall amount of electricity used during the treatment process (Celectrcity) is equal to the sum of the electricity used during heating, stirring and drying.
3 Results
3.1. Environmental impact assessment
To make comparisons between the various effect categories easier, Fig. 3 displays the relative impact of different scenarios. The results for water, electricity and chemicals were given in percentages (Tables S1–S3†) in order to identify which inputs in stage I–V had how much impact. Table 2 summarizes the values of various important environmental impacts. The environmental impacts from using a magnetic stirrer and an ultrasonicator in stage III were calculated separately for comparison. Fig. 3(a) and (b) depict the category-wise impact results in the cases of the stage I–II magnetic stirrer and stage I–II ultrasonicator, respectively. Detailed results are given in Tables S1 and S2 in ESI.† As can be observed from both graphs, electricity had the maximum contribution in categories such as eutrophication and global warming while in toxicity categories (HTPnc, HTPc, FETP, and METP) liquor ammonia and nickel concentrate contributed heavily. It was observed that there wasn't much difference in the values of impacts from the ultrasonicator as compared to the magnetic stirrer for adsorptive removal of As(III).This was mainly because there wasn't much increase in electricity consumption by the former. Stage I, or the synthesis of the adsorbent, contributed the most to the sum total of all the impacts, whereas stages II–V alone had the least contribution. The results clearly demonstrate that electricity made the maximum contribution to most of the outcomes produced for stage I. This was mainly because heat exchangers did not recover the heat arising from the process during stage I.
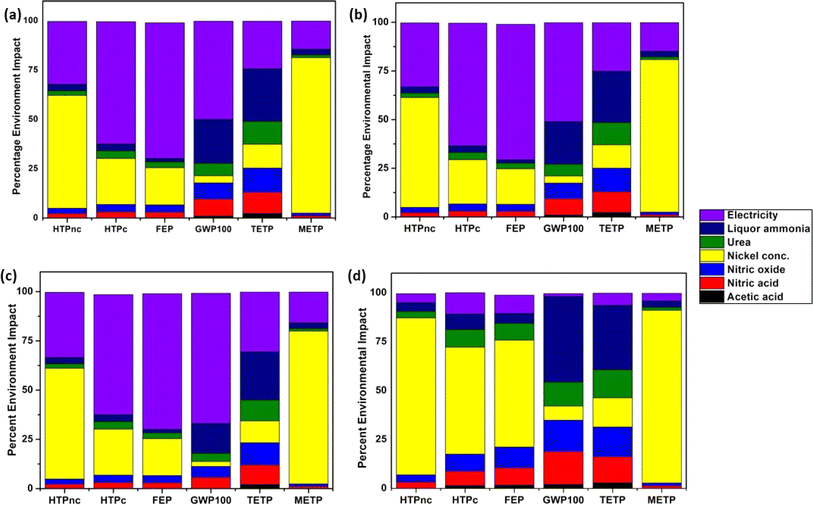 |
| Fig. 3 Environmental impacts associated with different energy scenarios, (a) magnetic stirrer (coal-NREC), (b) ultrasonicator (coal-NREC), (c) ultrasonicator (coal-5REC), and (d) ultrasonicator (solar-NREC). | |
Table 2 Impact category results (ReCiPe Midpoint method) (H) (v1.02) for the seven categories. The functional unit is 1 kg of the composite
Impact category |
Unit |
Stage I–III (magnetic stirrer-NREC) |
Stage I–III (ultrasonicator-NREC) |
Stage I–V (ultrasonicator-5REC) |
GWP potential (100 years) (GWP100) |
kg CO2 eq. |
61.23 |
62.58 |
90.29 |
Human toxicity-carcinogenic (HTPc) |
kg 1,4 DCB eq. |
2.53 |
2.6 |
2.52 |
Human toxicity-non-carcinogenic (HTPnc) |
kg 1,4 DCB eq. |
102.85 |
104.3 |
104.24 |
Marine eutrophication potential (MEP) |
kg N eq. |
0.00273 |
0.00280 |
0.0033 |
Freshwater eutrophication potential (FEP) |
kg P eq. |
0.03377 |
0.03480 |
0.0337 |
Terrestrial ecotoxicity potential (TETP) |
kg 1,4 DCB eq. |
113.22 |
114.43 |
122.75 |
Marine ecotoxicity potential (METP) |
kg 1,4 DCB eq. |
8.36 |
8.41 |
8.453 |
Table 2 compares the effects of recycling the adsorbent (5REC) to a non-recycling scenario (NREC). The results are expressed as absolute values. When an adsorbent is recycled five times (5REC), it is assumed that it has been used five times while NREC denotes a single use. For both scenarios, the adsorbent would only be created once. The consequences of NREC and 5REC shown in Fig. 3(c) increased proportionally since the synthesis stage (stage I) had the most overall impacts. LCA findings for the seven effect categories examined for NREC and 5REC are shown in Table 2. In Table S3,† the findings for each step are listed. As can be seen from Table 2 and Fig. 3(c), there was an appreciable increase in the overall impacts of all the categories specifically GWP100 and ecotoxicity when recycling was performed five times. This was because the differences between electricity consumption in NREC and 5REC are considerable in absolute terms (Table 1). Specifically, the adsorbent drying step in the hot air oven after each cycle of use resulted in a lot of energy input. This electricity consumption is then multiplied by 5 for each cycle. This suggests that in NREC, stages I–II, especially the synthesis part, are the ones most responsible for the overall impact. However, in 5REC, stages III–V are leading with high values for energy demand causing greater impacts. This is in contrast to LCA study on nanomaterial-based adsorbents for lab-scale Cd removal.20 They reported only a small increase in the values of almost all impact categories even after 4 cycles of recycling. This was due to not much increase in electricity consumption in the recycling stages as they did not take into account electricity consumed in drying or reused their adsorbent without drying in the previous stage. According to their study, the environmental effects were unmistakably worse when the adsorbent is not recycled, even if a virgin material offers 100% removal in comparison to 86% with a sorbent after recycling four times. Their findings highlighted the value of recycling in minimizing the environmental effect. 100% removal capacity will be significant only when effluent includes high amounts of As(III) (for example, >10 mg L−1). However, in our case, we considered it imperative to completely dry the adsorbent for its activation prior to the next use.
In all the categories, energy was the dominant or second-most dominant input (Tables S1–S3†). Much of electricity was utilized by heating on the magnetic stirrer and drying the adsorbent in the hot air oven. This suggests that it is important to carefully check the amount of electricity used in the procedure. It is clear from the aggregate results for each stage that electricity contributed most to the impact in all the studied categories. Depending on the manner of production and the composition of the grid, this could be the outcome of the processes that came before the creation of electricity (see sensitivity analysis below). Apart from this, chemicals such as nickel concentrate used in making nickel nitrate and liquor ammonia made the biggest contribution to all impact categories, especially to global warming, human carcinogenic toxicity, and marine and freshwater eutrophication (see Tables S1–S4†).
3.2. Implications and challenges of optimizing energy consumption
This study, which is in line with earlier LCA studies on nanoadsorbents, revealed that electricity is the process is one of the hotspots having the greatest environmental impact.21 Gifford and co-workers revealed a high energy requirement (>50% of the total) for the synthesis of Ti-AX resin containing precipitated nano-TiO2, 3.6 kW h kg−1 Ti-AX. Kazemi and coworkers detailed the lab-scale production of two nano-adsorbents, including superparamagnetic graphene oxide functionalized using thiol and Fe3O4@SiO2 (Fe3O4@SiO–NH–SH), and reported a requirement of 4–5 MW h kg−1 electricity.22 According to Caramazana-González, the manufacturing of lab-scale nanospheres with silica coating required 900 kW h kg−1 while the production of nano-TiO2 produced from titanium oxysulphate at the industrial scale required 28 kW h kg−1 of TiO2.23,24
Stage I electricity can be improved by modifying the adsorbent synthesis or using a renewable source of energy. However, the adjustment must not compromise the shape of the LDH composite to provide appropriate quality of the adsorbent as it will affect its performance.25 The change could be made by lowering the reaction time or synthesis temperature. Fossil fuel intensive energy sources cause a lot of damage to the environment by releasing greenhouse gases such as carbon monoxide and carbon dioxide. Therefore, it is very important to use renewable sources of energy. The campus of Amity University, Noida, Uttar Pradesh, is powered by solar energy as well. Therefore, a sensitivity analysis was conducted comparing the impacts of both sources of energy.
3.3. Comparison with granular activated carbon with regard to the environmental impacts
Based on the information mentioned in the literature, two more materials were identified for a rough comparison to the synthesis. Granular activated carbon (GAC) usually made from coconut shells, peat or coal is a commercially used adsorbent. GAC was selected due to its commercial use in industries. Only the impacts arising from synthesis of GAC and the current adsorbent were compared due to non-availability of the LCA data of As(III) removal using GAC. The LCA data on GAC here were referred to from a previous publication on adsorptive removal of Cd(II) and Pb(II) ions using GAC.26Table 3 shows the results for all impact categories for the synthesis (stages I–II). In every impact category during synthesis, GAC had the fewest negative effects. The functional unit is the mass of each adsorbent which was taken as 4.17 g and the environmental impact was recalculated using OpenLCA software accordingly. The difference in impact of both the adsorbents was almost 100% in the marine and terrestrial toxicity categories. This was due to the usage of hazardous chemicals in the synthesis of Ni–Fe layered double hydroxide.
Table 3 Results for the seven impact categories for Ni–Fe LDH/chitosan and granular activated carbon (GAC)
Impact category |
Unit |
Ni–Fe LDH/Ch |
Granular activated carbon |
GWP potential (100 years) (GWP100) |
kg CO2 eq. |
0.25 |
0.0071 |
Human toxicity-carcinogenic (HTPc) |
kg 1,4 DCB eq. |
0.01 |
0.0003 |
Human toxicity-non-carcinogenic (HTPnc) |
kg 1,4 DCB eq. |
0.42 |
0.0047 |
Marine eutrophication potential (MEP) |
kg N eq. |
1.14.10–5 |
3.12.10–7 |
Freshwater eutrophication potential (FEP) |
kg P eq. |
0.00014 |
4.8.10–6 |
Terrestrial ecotoxicity potential (TETP) |
kg 1,4 DCB eq. |
0.47 |
0.0009 |
Marine ecotoxicity potential (METP) |
kg 1,4 DCB eq. |
0.034 |
0.00024 |
3.4. Sensitivity analysis using different electricity sources
Significant disparities between the North Indian electricity grid and renewable energy sources were shown by the sensitivity analysis (Fig. 4). Table S4† provides more details for both the sources on the results of all effect categories. Fig. 4 demonstrates that when the North Indian electricity mix was taken as opposed to renewable electricity, the impact on freshwater eutrophication (FEP) and global warming (GWP100) increased substantially. The increase was more profound in the said categories and not so much in ecotoxicity categories such as METP and TETP. This was due to the fact that electricity was only a secondary source and that the nickel concentrate in the chemicals was imparting a significant level of toxicity. Nickel and ammonia made the biggest contribution to impact categories, especially to terrestrial and marine ecotoxicity potential, human carcinogenic toxicity, and freshwater and marine eutrophication (see Table 4). This suggests that it is important to check the amount of chemicals used in the procedure carefully. Rest, emission of carbon dioxide was 50% greater in the northern electricity grid than in the others due to its more fossil fuel (especially coal) intensive nature. It is clear from the aggregate results for each stage that electricity contributed most to the impact in all the studied categories. Depending on the manner of production and composition of the grid, this could be the outcome of the processes that came before the creation of electricity.
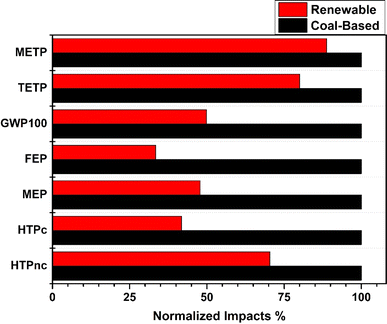 |
| Fig. 4 Comparison of impacts using ‘ultrasonicator (coal-NREC)’ and ‘ultrasonicator (renewable-NREC)’. In each category, the y-axis value for the scenario having the maximum impact was set to 100%. | |
Table 4 Comparison of the results for the seven categories for the removal of As(III) by using coal as the energy base and a renewable source of energy
Impact category |
Unit |
Stage I–III (coal-based energy) |
Stage I–III (renewable source) |
GWP potential (100 years) (GWP100) |
kg CO2 eq. |
62.58 |
31.21 |
Human toxicity-carcinogenic (HTPc) |
kg 1,4 DCB eq. |
2.6 |
1.086 |
Human toxicity-non-carcinogenic (HTPnc) |
kg 1,4 DCB eq. |
104.3 |
73.411 |
Marine eutrophication potential (MEP) |
kg N eq. |
0.00280 |
0.00134 |
Freshwater eutrophication potential (FEP) |
kg P eq. |
0.034806 |
0.01164 |
Terrestrial ecotoxicity potential (TETP) |
kg 1,4 DCB eq. |
114.43 |
91.5354 |
Marine ecotoxicity potential (METP) |
kg 1,4 DCB eq. |
8.41 |
7.45976 |
3.5. Cost analysis for Ni–Fe LDH/chitosan synthesis
Any technology's treatment cost is essential for serving a large community. Running cost of the treatment process is affected by the number of chemicals used and the electricity utilised in the process, according to an economic analysis of the approach. Adsorption technology's ongoing costs are INR 131.42 per L of water. The amount of adsorbent needed, however, is dependent on the contaminant's initial concentration. Hence, the cost of any treatment procedure heavily depends on the influent pollutant concentration. Lower arsenic concentrations will result in a decrease in this price.27,28 Gupta and co-workers also explored the intermediate use of used adsorbents, which could possibly lower the overall operational cost of treatment.29
4 Conclusion
Based on laboratory scale data, a life cycle assessment of Ni–Fe LDH/Ch, an adsorbent designed to remove As(III) from wastewater, was conducted. The synthesis of the nanomaterial served as the system's focal point for its utilization and recycling. Throughout this phase, electricity was the primary input. When expanding this operation, it is important to take measures to improve energy efficiency and choose energy sources that have minimal negative effects on the environment. Our research compared the environmental impact of our production system to that of GAC and found that ours had the fewest negative effects. In an ideal scenario, integrating energy recovery throughout the entire production process could optimize energy utilization for large-scale production. Our study highlighted electricity as the primary factor influencing the environmental impacts, and the role of chemicals in stage I may have been overlooked but could prove crucial later on. Specifically, we noticed that the use of chemicals for 1 kg of adsorbent had hazardous impacts on the environment, especially nickel and liquor ammonia, which were major contributors to toxicity categories.
Additionally, our study found that multiple recycling and reusing of the adsorbent added significantly to its negative environmental effects due to added electricity consumption for drying before each use. Our sensitivity analysis revealed that carbon dioxide emissions from renewable power sources were significantly lower than those from the Indian northern grid electricity mix with a higher share of fossil fuel-based electricity. For future production of LDHs, tracking mass loss at the microgram level is necessary to consider the possible effects of nanoparticles on the environment, given their toxicity as reported in various studies.
End-of-life phases and maintenance studies can also be added to future industrial applications to produce complementary data. However, due to a lack of information in the recent scientific literature, some stages were left out of our study, and our results should be interpreted with caution. Lab size data are less definitive than those from large-scale commercial operations.
Abbreviations
Ni–Fe LDH/Ch | Ni–Fe layered double hydroxide/chitosan |
NFC | Ni–Fe LDH/chitosan |
AHNPs | Aluminum hydroxide/oxide nanoparticles |
GAC | Granular activated carbon |
AP | Acidification potential |
GWP | Global warming potential (100 years) |
EP | Eutrophication potential |
ADP (E) | Abiotic depletion potential (elements) |
ODP | Ozone depletion potential |
ADP (F) | Abiotic depletion potential (fossil) |
HTP | Human toxicity potential |
FAETP | Fresh water aquatic eco-toxicity potential |
MAETP | Marine aquatic eco toxicity potential |
POCP | Photochemical ozone creation potential |
TETP | Terrestrial eco toxicity potential |
HHPA | Human health particulate matter |
HT (NC) | Human toxicity non-carcinogenic |
HT (C) | Human toxicity carcinogenic |
Res. (FF) | Resources (fossil fuels) |
DCB | 1,4-dichlorobenzene |
Data availability
The datasets used and/or analysed during the current study are available from the corresponding author on reasonable request.
Author contributions
KB conceptualized and performed the analysis and wrote the manuscript. CSS helped with editing and making graphs and figures. RS proofread the manuscript and supervised the work.
Conflicts of interest
The authors declare that they have no competing interests.
Acknowledgements
The authors acknowledge the support of the Ministry of Commerce and Industries, India. The content is solely the responsibility of the authors and does not necessarily represent the official views of the funding agency. The authors are grateful to the Amity Institute of Biotechnology, Amity University, Uttar Pradesh, India, for providing the laboratory facilities.
References
- X. Li, S. Chen, X. Fan, X. Quan, F. Tan and Y. Zhang,
et al., Adsorption of ciprofloxacin, bisphenol and 2-chlorophenol on electrospun carbon nanofibers: in comparison with powder activated carbon, J. Colloid Interface Sci., 2015, 447, 120–127 CrossRef CAS PubMed.
- J. Kameliya, A. Verma, P. Dutta, C. Arora, S. Vyas and R. S. Varma, Layered Double Hydroxide Materials: A Review on Their Preparation, Characterization, and Applications, Inorganics, 2023, 11(3), 121 CrossRef CAS , Available from: https://www.mdpi.com/2304-6740/11/3/121/htm.
- Z. P. Xu, G. S. Stevenson, C.-Q. Lu, Q. M. L. Gao, P. F. Bartlett and P. P. Gray, Stable Suspension of Layered Double Hydroxide Nanoparticles in Aqueous Solution, J. Am. Chem. Soc., 2005, 128(1), 36–37, DOI:10.1021/ja056652a.
- X. Gao, Y. Peng, L. Guo, Q. Wang, C. Y. Guan and F. Yang,
et al., Arsenic adsorption on layered double hydroxides biochars and their amended red and calcareous soils, J. Environ. Manage., 2020, 271, 111045 CrossRef CAS PubMed.
- J. Q. Jiang, S. M. Ashekuzzaman, J. S. J. Hargreaves, A. R. McFarlane, A. B. M. Badruzzaman and M. H. Tarek, Removal of arsenic (III) from groundwater applying a reusable Mg-Fe-Cl layered double hydroxide, J. Chem. Technol. Biotechnol., 2015, 90(6), 1160–1166, DOI:10.1002/jctb.4607.
- N. R. Biata, S. Jakavula, G. P. Mashile, A. Nqombolo, R. M. Moutloali and P. N. Nomngongo, Recovery of gold(III) and iridium(IV) using magnetic layered double hydroxide (Fe3O4/Mg-Al-LDH) nanocomposite: equilibrium studies and application to real samples, Hydrometallurgy, 2020, 197, 105447 CrossRef CAS.
- Y. Hu, C. Pan, X. Zheng, F. Hu, L. Xu and G. Xu,
et al., Prediction and optimization of adsorption properties for Cs+on NiSiO@NiAlFe LDHs hollow spheres from aqueous solution: kinetics, isotherms, and BBD model, J. Hazard. Mater., 2021, 401, 123374 CrossRef CAS PubMed.
- H. Lu, T. Lu, H. Zhang, Y. Qiu, D. Yin and Z. Zhu, Enhanced adsorption performance of aspartic acid intercalated Mg-Zn-Fe-LDH materials for arsenite, Dalton Trans., 2018, 47(14), 4994–5004 RSC , Available from: https://rsc.66557.net/en/content/articlehtml/2018/dt/c8dt00199e.
- K. Bisaria, S. Sinha, R. Singh and H. M. N. Iqbal, Recent advances in structural modifications of photo-catalysts for organic pollutants degradation – a comprehensive review, Chemosphere, 2021, 284, 131263 CrossRef CAS PubMed.
- M. Gifford, M. Chester, K. Hristovski and P. Westerhoff, Reducing environmental impacts of metal (hydr)oxide nanoparticle embedded anion exchange resins using anticipatory life cycle assessment, Environ. Sci.: Nano, 2016, 3(6), 1351–1360 RSC , Available from: https://rsc.66557.net/en/content/articlehtml/2016/en/c6en00191b.
- M. N. Garcia Gonzalez, R. Quiroga-Flores and P. Börjesson, Life cycle assessment of a nanomaterial-based adsorbent developed on lab scale for cadmium removal: comparison of the impacts of production, use and recycling, Clean. Environ. Syst., 2022, 4, 100071 CrossRef.
- K. Bisaria, S. Sinha, H. M. N. Iqbal and R. Singh, Ultrasonication expedited As(III) adsorption onto chitosan impregnated Ni–Fe layered double hydroxide biosorbent: optimization studies and artificial intelligence modelling, Environ. Res., 2022, 212, 113184 CrossRef CAS PubMed.
- E. Nishikawa, M. G. C. da Silva and M. G. A. Vieira, Cadmium biosorption by alginate extraction waste and process overview in Life Cycle Assessment context, J. Cleaner Prod., 2018, 178, 166–175 CrossRef CAS.
- T. Gao, B. P. Jelle, L. I. C. Sandberg and A. Gustavsen, Monodisperse hollow silica nanospheres for nano insulation materials: synthesis, characterization, and life cycle assessment, ACS Appl. Mater. Interfaces, 2013, 5(3), 761–767, DOI:10.1021/am302303b.
- M. A. J. Huijbregts, Z. J. N. Steinmann, P. M. F. Elshout, G. Stam, F. Verones and M. Vieira,
et al., ReCiPe2016: a harmonised life cycle impact assessment method at midpoint and endpoint level, Int. J. Life Cycle Assess., 2017, 22(2), 138–147, DOI:10.1007/s11367-016-1246-y.
- L. Chen, R. E. O. Pelton and T. M. Smith, Comparative life cycle assessment of fossil and bio-based polyethylene terephthalate (PET) bottles, J. Cleaner Prod., 2016, 137, 667–676 CrossRef CAS.
-
S. Maranghi, M. L. Parisi, R. Basosi and A. Sinicropi, LCA as a Support Tool for the Evaluation of Industrial Scale-Up, Life Cycle Assessment in the Chemical Product Chain: Challenges, Methodological Approaches and Applications, 2020, pp. 125–143, DOI:10.1007/978-3-030-34424-5_6.
- F. Piccinno, R. Hischier, S. Seeger and C. Som, From laboratory to industrial scale: a scale-up framework for chemical processes in life cycle assessment studies, J. Cleaner Prod., 2016, 135, 1085–1097 CrossRef CAS.
- F. Arfelli, D. Maria Pizzone, D. Cespi, L. Ciacci, R. Ciriminna and P. Salvatore Calabrò,
et al., Prospective life cycle assessment for the full valorization of anchovy fillet leftovers: the LimoFish process, Waste Manage., 2023, 168, 156–166 CrossRef CAS PubMed.
- M. N. Garcia Gonzalez, R. Quiroga-Flores and P. Börjesson, Life cycle assessment of a nanomaterial-based adsorbent developed on lab scale for cadmium removal: comparison of the impacts of production, use and recycling, Clean. Environ. Syst., 2022, 4, 100071 CrossRef.
- M. Gifford, M. Chester, K. Hristovski and P. Westerhoff, Reducing environmental impacts of metal (hydr)oxide nanoparticle embedded anion exchange resins using anticipatory life cycle assessment, Environ. Sci.: Nano, 2016, 3(6), 1351–1360 RSC , Available from: https://rsc.66557.net/en/content/articlehtml/2016/en/c6en00191b.
- A. Kazemi, N. Bahramifar, A. Heydari and S. I. Olsen, Life cycle assessment of nanoadsorbents at early stage technological development, J. Cleaner Prod., 2018, 174, 527–537 CrossRef CAS.
- P. Caramazana-González, P. W. Dunne, M. Gimeno-Fabra, M. Zilka, M. Ticha and B. Stieberova,
et al., Assessing the life cycle environmental impacts of titania nanoparticle production by continuous flow solvo/hydrothermal syntheses, Green Chem., 2017, 19(6), 1536–1547 RSC , Available from: https://rsc.66557.net/en/content/articlehtml/2017/gc/c6gc03357a.
- T. Gao, B. P. Jelle, L. I. C. Sandberg and A. Gustavsen, Monodisperse hollow silica nanospheres for nano insulation materials: synthesis, characterization, and life cycle assessment, ACS Appl. Mater. Interfaces, 2013, 5(3), 761–767, DOI:10.1021/am302303b.
- J. He, M. Wei, B. Li, Y. Kang, D. G. Evans and X. Duan, Preparation of layered double hydroxides, Struct. Bonding, 2005, 119, 89–119, DOI:10.1007/430_006.
- E. Asuquo, A. Martin, P. Nzerem, F. Siperstein and X. Fan, Adsorption of Cd(II) and Pb(II) ions from aqueous solutions using mesoporous activated carbon adsorbent: equilibrium, kinetics and characterisation studies, J. Environ. Chem. Eng., 2017, 5(1), 679–698 CrossRef CAS.
- V. K. Rathore and P. Mondal, Competitive Adsorption of Arsenic and Fluoride onto Economically Prepared Aluminum Oxide/Hydroxide Nanoparticles: Multicomponent Isotherms and Spent Adsorbent Management, Ind. Eng. Chem. Res., 2017, 56(28), 8081–8094, DOI:10.1021/acs.iecr.7b01139.
- L. S. Thakur and P. Mondal, Techno-economic evaluation of simultaneous arsenic and fluoride removal from synthetic groundwater by electrocoagulation process: optimization through response surface methodology, Desalin. Water Treat., 2016, 57(59), 28847–28863, DOI:10.1080/19443994.2016.1186564.
- S. Gupta, R. Lanjewar and P. Mondal, Enhancement of hydrocarbons and phenols in catalytic pyrolysis bio-oil by employing aluminum hydroxide nanoparticle based spent adsorbent derived catalysts, Chemosphere, 2022, 287, 132220 CrossRef CAS PubMed.
|
This journal is © The Royal Society of Chemistry 2024 |
Click here to see how this site uses Cookies. View our privacy policy here.