DOI:
10.1039/D4EE03541K
(Review Article)
Energy Environ. Sci., 2025,
18, 130-154
Engineering Ir-based catalysts for high current density applications in proton exchange membrane water electrolyzers
Received
8th August 2024
, Accepted 15th November 2024
First published on 27th November 2024
Abstract
The proton exchange membrane water electrolyzers (PEMWEs) are promising for the conversion and storage of renewable energy. Understanding the performance and durability of PEMWEs is crucial for engineers and researchers aiming to enhance the market adoption of this technology. Despite their potential, PEMWEs encounter challenges in large-scale and long-term deployment due to high costs and durability concerns in acidic environments. This review delves into the activation and degradation mechanisms of PEMWE components during the oxygen evolution reaction (OER), underscoring the importance of developing efficient PEMWE systems for industrial-scale hydrogen production. We explore recent advancements in engineering Ir-based catalysts for acidic OER, identifying existing gaps for practical application. A detailed overview of various modification techniques for Ir-based catalysts, such as electronic structure engineering, morphology engineering, and support engineering, is presented. Additionally, the critical influence of catalyst coating methods on membrane electrode assembly is discussed. The review also covers performance degradation in PEMWEs, detailing the degradation sources of anode catalysts, membranes, and bipolar plates. By analyzing degradation causes and mechanisms, we highlight effective strategies to enhance component longevity. Moreover, we expand our focus towards the industrialization of PEMWEs operating at high current density. Concluding with an outlook on unresolved challenges, this review offers promising directions for future research aimed at realizing practical PEMWE systems.
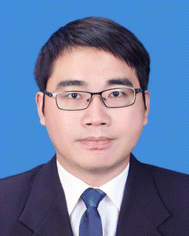
Yang Song
| Dr. Yang Song earned his PhD from the University of Chicago in 2021, where he conducted research under the guidance of Prof. Wenbin Lin. He joined the SINOPEC Research Institute of Petroleum Processing in 2023 and was appointed as an Institute Expert in 2024. His research centers on catalyst development for PEM water electrolyzers and the design of advanced electrochemical reactors. |
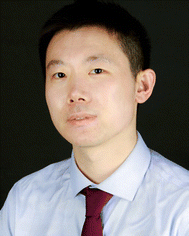
Hongwu Chen
| Dr. Hongwu Chen received his PhD in Chemistry from Tsinghua University in 2022, where he studied under the supervision of Prof. Chun Li. He joined the SINOPEC Research Institute of Petroleum Processing as a Research Associate the same year. His research focuses on catalyst development for electrochemical CO2 reduction and chemical upgrading, as well as the design of electrochemical reactors. |
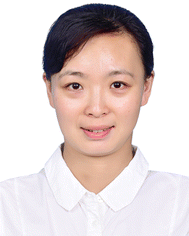
Xue Yang
| Dr. Xue Yang received her PhD from Tianjin University in 2009 and joined the SINOPEC Research Institute of Petroleum Processing the same year. In 2021, she was appointed as a Research Fellow and now leads the Electrochemistry and Hydrogen Energy Team within the Research Center for Renewable Energy. Her research focuses on PEM water electrolysis, PEM fuel cells, and innovations in the electrochemical industry. |
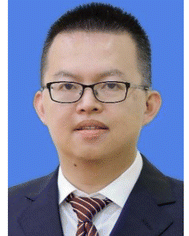
Wei Lin
| Prof. Wei Lin received his PhD from Peking University in 2005 before joining the SINOPEC Research Institute of Petroleum Processing the same year. He currently serves as a Professor and Vice President of the Research Institute of Petroleum Processing at SINOPEC. His research focuses on developing catalysts and reactors for practical electrochemical reaction systems. |
Broader context
Hydrogen energy is vital to a sustainable future, offering versatility and environmental benefits. Proton exchange membrane water electrolyzers (PEMWEs) are key to green hydrogen production, excelling in rapid adaptation to fluctuating renewable energy, making them ideal for advancing green hydrogen technology. However, the efficiency of typical PEMWEs in hydrogen production is often hindered by the sluggish kinetics of the oxygen evolution reaction (OER), coupled with challenges related to large-scale and long-term deployment, such as high costs and durability issues in acidic environments. Addressing these challenges, the focus on anodic catalyst engineering within PEMWEs, particularly for high current density applications, emerges as a promising approach. This comprehensive review delves into the activation and degradation mechanisms of PEMWE components during OER, highlighting recent advancements in engineering Ir-based catalysts for acidic OER and summarizing performance degradation in PEMWEs. It identifies existing gaps in practical applications and expands the discussion towards the industrialization of PEMWEs operating at high current densities, aiming to bridge the gap between academic research and industrial demands. We anticipate that this review will offer valuable directions for future research aimed at realizing practical PEMWE systems.
|
1. Introduction
The increasing consumption of fossil fuels and their associated greenhouse gas emissions are exacerbating global warming and climate change, posing significant risks to public health and the environment.1,2 Recognizing this, governments worldwide are shifting their focus towards hydrogen (H2) as a cornerstone of a sustainable energy future.3,4 From only two countries with hydrogen strategies in June 2019, the count rose to 17 by November 2021, with over 20 others in the process of developing their strategies.5 Hydrogen is heralded for its versatility across numerous industries and its potential to significantly reduce greenhouse gas emissions.6 Sustainable H2 production through water electrolysis is considered as a pivotal method for achieving a clean, green hydrogen cycle, with the main technologies being alkaline water electrolyzer (AWE),7,8 proton exchange membrane (PEM) water electrolyzer (PEMWE),9,10 anion exchange membrane (AEM) water electrolyzer (AEMWE),11 and solid oxide electrolysis cell (SOEC).12 While AWE faces challenges such as prolonged startup times and adaptability issues to renewable energy fluctuations,13,14 AEMWE technology is hindered by the poor electrochemical stability of its components.15,16 Conversely, PEMWEs are prized for their rapid response to changing energy conditions, positioning them as a leading solution for integrating hydrogen production with renewable energy sources and pushing the frontier of green hydrogen technology (Fig. 1a).17–19
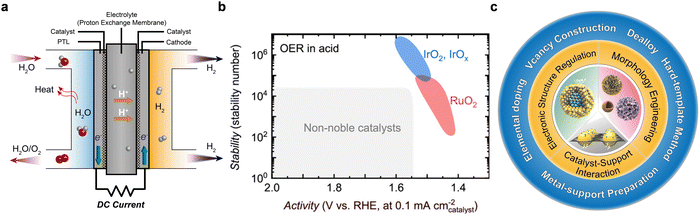 |
| Fig. 1 (a) Principles of operation for PEMWE. (b) Benchmarking IrO2 against other catalysts for activity and stability in OER applications. Reproduced with the permission from ref. 20. Copyright 2023, American Chemical Society. (c) Strategies for modifying Ir-based OER catalysts focus on enhancing the intrinsic activity of the catalyst, innovating nanostructures, and optimizing catalyst–support interactions. | |
Despite the rapid advancements in PEMWE technologies over recent decades, it still confronts several obstacles hindering its widespread adoption in industrial settings.5,21 A critical aspect of enhancing PEMWE efficiency lies in improving the anodic oxygen evolution reaction (OER). The current challenge is the sluggish kinetics of OER in commonly used anodic catalysts, combined with their limited durability under highly corrosive conditions, significantly impeding the practical application of PEMWE technologies.22–24 Since the 1950s, extensive investigations have been directed towards elucidating the OER mechanism in a variety of metals.25,26 A link between activity and stability of monometallic oxides for use as catalysts in OER in acidic media has been established: the most active oxides (Os ≫ Ru > Ir > Pt ≫ Au) exhibit increased dissolution rates up to orders of magnitude and thus least stable (Au ≫ Pt > Ir > Ru ≫ Os).27 For this reason, Ir-based electrocatalysts have emerged as potential candidates for the application in water electrolysis owing to their relatively high activity and stability under high voltage (>1.6 V) and acidic (pH < 1) working conditions in PEMWEs.28–30 In addition, in the context of the OER in PEMWEs, the stability number (S-number) is a critical metric for assessing catalyst durability, especially for IrO2 and similar materials in acidic environments. Defined as the ratio of evolved oxygen molecules to dissolved catalyst atoms, the S-number provides a benchmark for the ability of a catalyst to maintain structural integrity during OER.31,32 Essentially, it indicates the number of cycles or hours a catalyst can sustain before significant degradation affects its performance. A high S-number suggests that a catalyst possesses exceptional durability, resisting dissolution and degradation over prolonged OER cycles at high current densities. Recent benchmark studies have shown that, compared to other catalysts, IrO2 typically exhibits a high S-number due to its robustness in acidic conditions, reinforcing its status as a preferred choice for PEMWEs (Fig. 1b).20,33
However, the high cost and scarcity of Ir (∼$206 per g, <9000 kg per year production rate) present a significant obstacle for scaling up to gigawatt (GW) plants.34,35 A basic estimation suggests that each GW plant would require about 500 kg of Ir, assuming a standard loading of 2 mgIr cm−2 of active area and operation at 4 W cm−2.36 Studies have shown that Ir-based catalysts have the intrinsic OER activity necessary to achieve an energy density of ∼0.01 gIr kW−1 at 1.79 V, which implies a potential reduction in Ir usage in PEMWE systems by a factor of ∼50, to ∼0.04 mgIr cm−2.37 Therefore, reducing the Ir loading while enhancing the OER performance is critical. The current iridium loading of ∼2–4 mg cm−2 must be dramatically reduced to less than 0.5 mg cm−2 to meet the rapidly developed PEM electrolyzer market. Concurrently, the instability of OER catalysts at higher potential also pose technical barriers to the commercialization of PEMWE technology. Specifically, the enhancement of the activity of current commercial Ir catalysts is a prerequisite to attain high energy conversion efficiencies at substantial current densities, in alignment with the 2026 US Department of Energy (DOE) target, (<1.8 V@3 A cm−2, H2 production cost <$2 kgH2−1).38,39 In this review, we delve into the challenges and opportunities that have shaped the development of PEMWE technologies over the past decades. Initially, our discussion centers on the evolution of engineering strategies for Ir-based OER catalysts. This encompasses three main areas: modifying the catalyst electronic structure, innovating the catalyst morphology, and optimizing catalyst–support interaction (Fig. 1c). These approaches aim to minimize iridium usage, boost mass activity, and improve electrochemical stability. We then explore the practical applications within PEMWE, focusing on membrane electrode assembly (MEA) methods and testing conditions. Understanding the degradation mechanisms of key components, including catalysts, membranes, porous transport layers (PTL), and bipolar plates (BPPs), and devising strategies to mitigate these issues is crucial. It is this comprehensive understanding that propels PEMWE technology forward, positioning it as a cornerstone in the future energy landscape. Additionally, we provide a detailed overview of the degradation mechanisms and outline corresponding mitigation strategies for components such as catalysts, membranes, PTL, and BPPs. This insight is vital for advancing PEMWE technology and securing its role in future energy systems. To conclude, we offer discussions and perspectives on the design of cost-effective iridium-based catalysts. The aim for this timely review is to contribute to the development of iridium-based catalysts that exhibit optimal OER activity and stability under PEMWE operating conditions, thereby supporting large-scale hydrogen production from renewable, clean energy sources.
2. Catalyst engineering
2.1. Engineering of catalyst electronic structure
The catalytic activity of electrocatalysts is significantly influenced by their electronic structure. This structure can be effectively modulated through approaches such as heteroatoms doping and crystal phase engineering. Elemental doping, for instance, has been shown to optimize the d-band center of Ir and the p-band center of oxygen, thereby fine-tuning the adsorption energy at the active center for oxygen intermediates.40–42 This process can introduce surface strain and valence changes due to the varying ionic valence and radius of the dopant elements compared to Ir, consequently altering the OER performance.43,44 For example, Hao et al.45 reported the synthesis of a grain boundary (GB)-Ta0.1Tm0.1Ir0.8O2−δ electrocatalyst (Fig. 2a). This was achieved by doping Ta and Tm atoms into the IrO2 lattice, inducing compressive strain. This strain leads to a downward shift in the d-band center of Ir, reducing the adsorption energy of the *O intermediate on Ir active sites. As a result, the torsion-strained Ta0.1Tm0.1Ir0.8O2−δ exhibited an exceptionally low oxygen evolution overpotential, maintaining stable operation at 1.5 A cm−2 for 500 h, even with a minimal catalysis load of 0.2 mg cm−2. Calculating the S-number based on the dissolution of metal elements, as monitored by including inductively coupled plasma mass spectrometry (ICP-MS), reveals that GB-Ta0.1Tm0.1Ir0.8O2−δ exhibited the highest S-number (>6 × 107), indicating its exceptional durability (Fig. 2b). Density functional theory (DFT) calculations were further performed to further elucidate the OER mechanism. The DFT results showed that GB-Ta0.1Tm0.1Ir0.8O2−δ exhibited the lowest energy barriers for the OER, indicating that the catalytic energy barrier can be fine-tuned through the combination of strain and doping (Fig. 2c). Comparatively, RuO2 is more reactive for OER than IrO2, but IrO2 offers superior stability in acidic conditions. This is due to tendency of RuO2 to rapidly convert to RuO4 under high current density conditions during the OER process.46 A promising approach to leverage these properties is the development of mixed oxides of IrO2 and RuO2. The synergistic effect between Ir and Ru is anticipated to enhance or maintain the activity of Ir sites while stabilizing Ru, allowing more Ru sites to be functional. In line with this, commercial Ir0.7Ru0.3O2 catalysts have achieved a balance between activity and stability. Further, Wang et al.47 advanced this by developing a nanostructured iridium catalyst through electrochemical leaching of Ru from metallic Ir–Ru. The electrochemically oxidized Ir0.7Ru0.3Ox demonstrated a 13-fold increase in reactivity compared to the thermally treated Ir0.7Ru0.3O2. Furthermore, MEA measurements revealed that using Ir0.7Ru0.3Ox as the anode catalyst required only 1.683 V to achieve 1 A cm−2 at 80 °C, with negligible cell voltage change after 400 h@1 A cm−2. To optimize the performance of the Ir0.7Ru0.3Ox catalyst even further, Siracusano et al.48 employed a combined approach of hot acid pretreatment and thermal treatment. The resulting catalyst, with a low MEA loading of less than 0.34 mgIr+Ru cm−2, achieved 3 A cm−2@1.8 V with an enthalpy efficiency greater than 80% (Fig. 2d). Impressively, the voltage degradation rate was just 23 μV h−1 for 3 A cm−2 over 1000 h (Fig. 2e). Increasing the efficiency of Ir in PEMWE systems can be achieved not only by alloying Ir with Ru, but also by incorporating other transition metals such as Ni, Co, Fe, etc.49,50 Among these, Ni has emerged as particularly promising for its ability to enhance the OER specific activity of Ir.51,52 Similar to Ru, an acid-leaching step is often employed to remove surface Ni, resulting in an Ir-rich surface on the alloy catalyst particles. This leaching of Ni is thought to create lattice vacancies on the surface of the catalyst. These vacancies may introduce d-band holes in the Ir elements and holes on oxygen ligands near these vacancies, potentially boosting the intrinsic catalytic activity towards OER.52 A significant advancement was made by Alia et al.53 in 2018, who developed Ir–Ni nanowires through galvanic displacement deposition on a Ni nanowire precursor. This catalyst demonstrated not only heightened intrinsic activity but also a high specific electrochemical surface area, making it particularly efficient. Impressively, the catalyst layer (CL) could achieve a performance of 1 A cm−2 at 1.6 V, even with an Ir loading as low as 0.1 mgIr cm−2. More recently, Yeo et al.54 developed a de-alloyed, self-supporting three-dimensional (3D) nanoporous IrNi (DNP-IrNi) catalyst demonstrating a 248 mV OER overpotential at 10 mA cm−2 in acidic electrolytes and notable catalytic stability (Fig. 2f). The Tafel plots of the catalysts offer further insights into their catalytic performance. As shown in Fig. 2g, the Tafel slopes follow the order: DNP-IrNi (38 mV dec−1) < HDNP-IrNi (56 mV dec−1) < IrOx (111 mV dec−1). While the complexity of the multiple steps in the OER process makes it challenging to deduce the exact mechanism solely from the Tafel slope, a lower slope value suggests that a smaller potential increase is required to achieve the same current density, indicating favorable electrocatalytic kinetics. In a PEMWE setup, DNP-IrNi, with an Ir loading of 0.67 mg cm−2, achieved an impressive performance of 1.88 A cm−2@1.7 V, significantly outperforming commercial IrOx catalysts (Fig. 2h). At a higher cell voltage of 2.0 V, the electrolyzer reached a current density of 6.5 A cm−2. And a 100-h stability test at 2 A cm−2 showed a degradation rate of 1.58 mV h−1, confirming its remarkable stability.
 |
| Fig. 2 (a) Comparative schematic of synthesizing GB-Ta0.1Tm0.1Ir0.8O2−δ nanocatalyst using fast pyrolysis (top) and producing nanoparticles without GB via slow pyrolysis (bottom). (b) S-number for the various nanocatalysts. (c) The correlation between overpotentials and the p-band center was analyzed, both with and without applied strain. Reproduced with permission from ref. 45. Copyright 2021, Springer Nature. (d) Polarization curves showing the performance of a low catalyst loading MEA before and after a 1000-h operation at 3 A cm−2 and 80 °C. (e) Long-term durability tests at 1 and 3 A cm−2 for low catalyst loading MEA in an electrolysis cell. Reproduced with permission from ref. 48. Copyright 2017. Elsevier. (f) Schematic illustration of creating a 3D dealloyed nanoporous IrNi (DNP-IrNi). (g) OER Tafel plots of DNP-IrNi, HDNP-IrNi, and IrOx, respectively. (h) Polarization curves for a single cell. Reproduced with permission from ref. 54. Copyright 2022, Royal Society of Chemistry. | |
Overall, doping Ir with other elements optimizes its electronic structure and the adsorption or desorption energy of oxygen species, leading to enhanced OER activity. Additionally, this strategy effectively reduces the cost of the catalyst by incorporating less expensive elements. Consequently, element doping in the construction of Ir-based catalysts is viewed as one of the most promising approaches for designing high-performance OER catalysts for PEMWE systems.
2.2. Engineering of catalyst morphology
Nanomaterials, with their distinctive structures, have garnered significant attention in the field of catalysis due to their exceptional performance. One of their key advantages is the large specific surface area, which facilitates increased exposure of active sites and enhances the utilization of noble metals.55,56 In PEMWE systems, the nanostructure of Ir catalysts plays a crucial role in determining overall performance. Specifically, nano-structural modifications can increase the electrochemical surface area and improve mass transfer capabilities under high current densities, critical factors for OER performance. Many nanostructured Ir-based catalysts have synthesized and compared, including nanoparticles,57,58 nanoneedles,59 nanosheets,60,61 and nanorods.62 Recently, Chatterjee et al.63 made a significant contribution by successfully synthesizing porous Ir nanosheets (npIrx-NS) with a thickness of 60–100 nm and an average pore size of 5–10 nm (Fig. 3a and b). This was achieved using a top-down electrochemical processing technique. These npIrx-NS, with an ultralow loading of 0.06 mgIr cm−2, demonstrated remarkable performance as an anodic CL in PEMWE. As shown in Fig. 3c, they achieved a cell voltage of just 1.98 V to reach a high current density of 2.4 A cm−2 at 80 °C, also showing stability over 50
000 accelerated stress testing (AST) cycles (1.3–2.0 V, 0.17 mgIr cm−2). Expanding on this, Kim et al.64 employed solvent-assisted 3D printing techniques to develop woodpile (WP)-structured Ir catalysts, composed of highly ordered Ir nanowire building blocks (Fig. 3d). This WP structure not only maintains the electrochemically active surface area (ECSA) but also enhances the utilization efficiency of extended surface area of the 3D WP catalyst. Regarding the bubble removal mechanism in the OER process, fast Fourier transformation (FFT, Fig. 3e) and dynamic light scattering (DLS, Fig. 3f) analyses reveal additional factors beyond simple bubble detachment from catalytic surfaces. The open and ordered 3D structure reduces the residence time of bubbles within the catalyst layer, while prolonged residence times lead to more pronounced bubble coalescence within the fluid, which can affect catalytic performance. Remarkably, the 30-layer WP 1200 catalysts achieved a maximum current density of 5.2 A cm−2@2.0 V and displayed a mass activity of 140 A mg−1@1.8 V, which is 30 times higher than that of state-of-the-art commercial Ir nanoparticle catalysts (Ir black). Additionally, IrO2 with a rutile phase remains the commercial anode catalyst for PEMWE. The IrO2 loading on the MEA is ∼2–2.5 mgIr cm−2, but there is an urgent push to reduce this by improving the catalytic activity of IrO2. Lim et al.59 developed a molten salt method to synthesize ultrathin IrO2 nanoneedles, a process both facile and scalable. These nanoneedles displayed significantly enhanced OER performance compared to conventional nanoparticles. With a low loading of approximately 0.38 mgIr cm−2 on MEA, they showed excellent operational performance, achieving a high current density of 3 A cm−2 at 1.82 V with negligible degradation after 90 h. Furthermore, aerosol synthesis has emerged as a potent method for preparing highly porous and ordered nanostructures.65–67 Faustini et al.66 developed a ultraporous Ir0.7Ru0.3O2 nanocatalyst. The material can be easily synthesized from aqueous solutions using an industrially scalable spray-drying technique based on an evaporation-driven self-assembly mechanism. The carefully engineered porous hierarchical structure enhances the accessibility of reactants and products to nanoparticle surfaces, significantly boosting catalytic performance. The resulting highly porous Ir0.7Ru0.3O2 catalyst demonstrates superior performance compared to commercial iridium oxide (Fig. 3g). Moreover, these highly porous particles were proven to be ideal building blocks for integration into catalyst layers, effectively avoiding the limitations commonly associated with discrete nanoparticles. With a catalyst loading of 1.8 mg cm−2, calcined at 450 °C, it achieves a low cell voltage of 1.85 V, reaching a high current density of 2 A cm−2 at 80 °C (Fig. 3h). In all, the nanostructure of iridium catalysts influences their electronic state and intrinsic activity, as well as the mass transport process, thereby impacting the practical performance in PEMWEs (Table 1).
 |
| Fig. 3 (a) Schematic showing low-resistance electron pathway of npIrx-NS from the catalyst to the current collector. (b) Scanning electron microscopy images of npIrx-NS created from Ni95Ir5 in 2 M H2SO4 + 0.5 M HCl. (c) Polarization curves of npIrx-NS (red) vs. TKK IrO2 (black) at 0.06 mgIr cm−2 anode loading. Reproduced with permission from ref. 63. Copyright 2021, Wiley-VCH. (d) Illustration of a WP-structured Ir thin film with meso- and macropores for OER. (e) FFT amplitude spectra of currents recorded at the scanning electrochemical microscopy tip, showing that higher peak frequencies correspond to faster O2 bubble formation and detachment cycles. (f) DLS analysis spectra showing the size distribution of O2 bubbles generated by the WP and PWP catalysts. Reproduced with permission from ref. 64. Copyright 2020, Springer Nature. (g) Synthesis process schematic with scanning transmission electron microscopy images post-spray drying and post-calcination at 450 °C. (h) Polarization curves at 80 °C and atmospheric pressure, showing 0.5 mg cm−2 Pt/C cathode and 2 mg cm−2 IrOx (blue) and 1.8 mg cm−2 Ir0.7Ru0.3Ox (orange) anodes calcined at 450 °C. Reproduced with permission from ref. 66. Copyright 2019, Wiley-VCH. | |
Table 1 Recently reported state-of-the-art OER electrocatalysts and their performance in a single PEMWE
Anode catalysts |
Membrane |
Loading (mg cm−2) |
Cell activity |
Stability |
Ref. |
GB-Ta0.1Tm0.1Ir0.8O2−δ |
Nafion 117 |
0.2 |
1.935@2 A cm−2 |
500 h@1.5 A cm−2 |
45
|
Ir0.7Ru0.3Ox (EC) |
Nafion 212 |
1.0 |
1.683@1 A cm−2 |
400 h@1 A cm−2 |
47
|
IrRuOx |
Aquivion (95 μm) |
0.34 |
1.8 V@3 A cm−2 |
1000 h@3 A cm−2 |
48
|
Ir–Ni nanowires |
NA |
0.1 |
1.6 V@1 A cm−2 |
13.5 h@1.6 V |
53
|
DNP-IrNi |
Nafion 212 |
0.67 |
2.0 V@6.5 A cm−2 |
100 h@2.0 A cm−2 |
54
|
npIrx-NS |
Nafion 117 |
0.06 |
1.98 V@2.4 A cm−2 |
50 000 AST cycles (1.3–2.0 V) |
63
|
30-Layer WP 1200 |
Nafion 212 |
0.045 |
2.0 V@5.2 A cm−2 |
NA |
64
|
IrO2 nanoneedles |
Nafion 117 |
3.43 |
2.1 V@2 A cm−2 |
200 h@2 A cm−2 |
59
|
Porous Ir0.7Ru0.3O2 |
Nafion 115 |
1.8 |
1.85 V@2 A cm−2 |
NA |
66
|
IrO2@TiO2 |
Nafion 212 |
0.4 |
1.67 V@ 1 A cm−2 |
150 h@2 A cm−2 |
68
|
IrO2/TNO |
Nafion 117 |
0.2 |
1.832 V@1 A cm−2 |
100 h@1 A cm−2 |
69
|
Ir/Nb2O5−x |
Nafion 115 |
1.8 |
1.686 V@2 A cm−2 |
2000 h@2 A cm−2 |
70
|
RuOx |
Nafion 212 |
2.0 |
1.733 V@1 A cm−2 |
50 h@1 A cm−2 |
38
|
RuO2 |
Nafion 117 |
1.2 |
1.85 V@1 A cm−2 |
300 h@2 A cm−2 |
71
|
LMCF |
Nafion 212 |
0.26 |
2.3 V@2 A cm−2 |
100 h@0.21 A cm−2 |
72
|
2.3. Engineering of catalyst–support interaction
Increasing the efficiency of Ir and IrO2 in PEMWE can be achieved by dispersing them on suitable supports, thereby enhancing iridium utilization.73 Considering the need for cost-effective, highly active, and stable anode catalysts in PEMWE, the ideal support should exhibit several key features: (i) a large Brunauer–Emmett–Teller (BET) surface area with a highly porous structure; (ii) excellent electrical conductivity; (iii) strong corrosion resistance and long-term stability under oxidative and acidic conditions; (iv) affordability.74 Addressing these criteria, the most extensively studied support material is TiO2, with the IrO2@TiO2 being commercialized for practical applications. A notable example is the novel IrO2 coated TiO2 core–shell microparticles (IrO2@TiO2) developed by Pham et al.,68 which serve as an efficient OER catalyst. PEMWEs using IrO2@TiO2 as the anodic catalyst, with a loading of 0.4 mgIr cm−2, attained 1 A cm−2@1.67 V at 80 °C (Fig. 4a). IrO2@TiO2 demonstrated a S-number slightly lower than that of IrO2 (Alfa Aesar) and IrO2/TiO2 (Umicore). However, when compared to other benchmark materials such as commercial hydrous iridium oxide (S-number of ∼104) and RuO2 nanoparticles (S-number of ∼103),32 IrO2@TiO2 showed significantly higher stability than RuO2 and comparable stability to hydrous iridium oxide. Therefore, considering both energy efficiency and catalyst utilization, IrO2@TiO2 emerges as a suitable choice for practical applications. Moreover, a durability test in a single cell (0.5 mgIr cm−2, N212 membrane) demonstrated an overall degradation rate of only 0.49 mV h−1 during a 150-h constant current hold at 2 A cm−2 (Fig. 4b). However, the conductivity of TiO2 is relatively low, necessitating a high Ir content (usually >40 wt%) to fully cover the support and improve conductivity. To optimize this, various studies have focused on enhancing conductivity of TiO2 through metal doping, such as niobium (Nb),69,75 tantalum (Ta),76 and tungsten (W).77 For instance, Lv et al.69 introduced Nb doping into TiO2, creating an oxygen-deficient Ti0.9Nb0.1O2−x support for IrO2 (noted as IrO2/TNO-Hx, x corresponds to the hydrogenation temperature) anode catalysts. The catalyst, with a low IrO2 loading of 0.2 mgIr cm−2 (N117 membrane), exhibited optimal OER activity (1.832 V@1 A
cm−2) and maintained stability for 100 h at 1 A
cm−2, outperforming unsupported IrO2 (Fig. 4c). To gain further insights into the impact of oxygen vacancies on OER performance, electrochemical impedance spectroscopy (EIS) measurements were conducted to analyze the resistance components (Fig. 4d). The EIS Nyquist plots presented data for unsupported IrO2, IrO2/TiO2, IrO2/TNO, and IrO2/TNO-Hx samples in single cells at 0.1 A cm−2. Among these, the Rct value of IrO2/TNO-H750 is the lowest at 0.20 Ω cm2, followed by IrO2/TNO-H600 (0.23 Ω cm2), IrO2/TNO-H900 (0.28 Ω cm2), IrO2/TNO (0.30 Ω cm2), IrO2/TiO2 (0.32 Ω cm2), and unsupported IrO2 (0.35 Ω cm2). This trend is attributed to the role of oxygen vacancies, which act as charged species, enhancing charge transfer between adsorbate and absorbent and thus improving the OER activity of IrO2/TNO-Hx (x = 600, 750, 900) samples. Furthermore, other oxides like Nb2O5,70 Ta2O5, and SnO2 are also promising supports. Recently, Shi et al.70 reported that Nb2O5−x supported Ir catalysts (Fig. 4e), which underwent dynamic oxygen species migration between IrOx and Nb2O5−x during OER, exhibited high activity and stability. These catalysts require just 1.839 V to achieve 3 A cm−2 (Fig. 4f, surpassing the DOE 2025 target). And by monitoring dissolved Ir in the electrolyte using inductively coupled plasma optical emission spectrometry (ICP-OES), the S-number of Ir/Nb2O5−x was calculated to be 1.6 × 105, which is ∼7.3 times higher than that of Ir nanoparticles (2.2 × 104), indicating a significantly prolonged lifetime for Ir/Nb2O5−x. The Gibbs free energy diagram for the adsorbate evolution mechanism on IrOx, IrOx/Nb2O5−x (without migration), and IrOx/Nb2O5−x (with migration) illustrated how
migration dynamically regulated the Ir electronic structure (Fig. 4g). DFT calculations further confirmed that the catalyst/support interface suppresses Ir over-oxidation and leaching via oxygen migration, thereby greatly enhancing the catalytic stability of Ir/Nb2O5−x (Fig. 4i). The stability of Ir/Nb2O5−x was further tested at increasing current densities (2 to 6 A cm−2) using chronopotentiometry to evaluate performance under high currents and oxidation potentials. Remarkably, cell voltage remained stable at 1.937, 2.026, and 2.123 V at 4, 5, and 6 A cm−2, respectively, over 150 h (Fig. 4h), and showed almost no decay over 2000 h at 2 A cm−2, demonstrating strong potential for high-current applications.
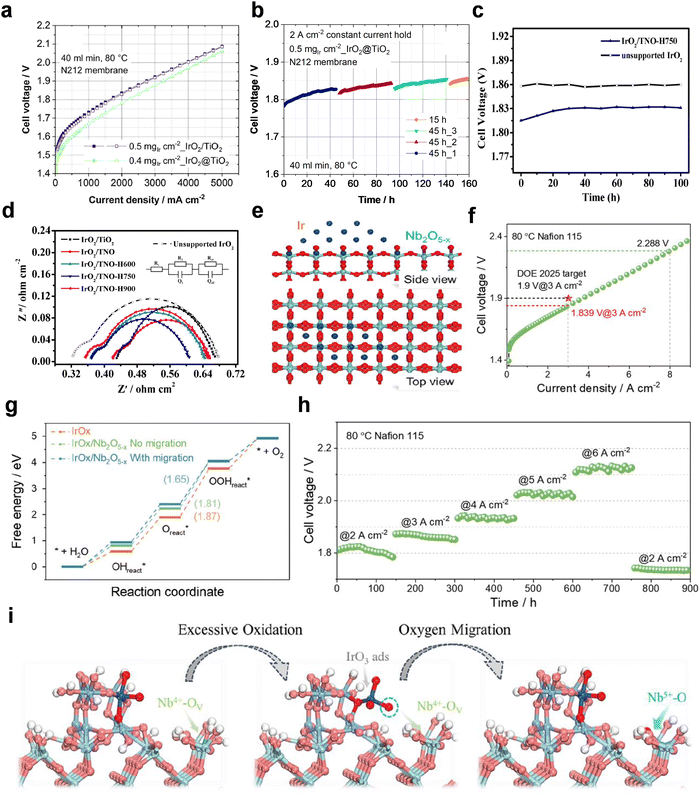 |
| Fig. 4 (a) Polarization curves using IrO2@TiO2versus IrO2/TiO2, with loadings of 0.4 mgIr cm−2 and 0.5 mgIr cm−2 respectively, using a 50.8 μm thick Nafion 212 membrane. (b) Voltage stability of IrO2@TiO2-based MEAs at 0.5 mgIr cm−2 and 2 A cm−2 over 150 h. Reproduced with permission from ref. 68. Copyright 2020, Elsevier. (c) Durability tests at 1 A cm−2 and 80 °C for unsupported IrO2 and IrO2/TNO-H750. (d) Nyquist diagrams of IrO2/TiO2, IrO2/TNO, IrO2/TNO-Hx (x = 600, 750, 900), and unsupported IrO2 at 0.1 A cm−2 and 80 °C. The inset shows the corresponding equivalent circuit model. Reproduced with permission from ref. 69. Copyright 2019, Wiley-VCH. (e) Schematic of the Ir/Nb2O5−x structure. (f) Polarization curve at 80 °C using a Nafion 115 membrane. (g) Gibbs free energy diagram for the adsorbate evolution mechanism on IrOx, IrOx/Nb2O5−x (without migration), and IrOx/Nb2O5−x (with migration). (h) Chronopotentiometric curves for PEMWE with Ir/Nb2O5−x at steady current density. (i) Proposed pathway for over-oxidation and recovery of Ir on Ir/Nb2O5−x, incorporating the dynamic migration of oxygen species. Reproduced with permission from ref. 70. Copyright 2022, Wiley-VCH. | |
Therefore, oxide supports can effectively inhibit the degradation of active centers and adjust the adsorption energy of oxygen species on Ir-based catalysts through metal–support interactions. The presence of these supports modifies the catalyst's electronic structure through charge redistribution. Additionally, stabilized oxides can enhance the vacancy formation energy in IrO2, thereby boosting the overall stability.
3. Key components and their degradation in PEM electrolyzers
PEMWE technology has established a significant presence in commercial water electrolysis, owing to its rapid dynamic response, high hydrogen purity, and compact design. The first journal publication on PEMWE dates back to 1973 by Russell et al., who demonstrated the impressive capabilities of their PEMWE at General Electric Company.78 Over the past 50 years, PEM technology has been commercialized by various electrolyzer manufacturers, including Giner Inc., Proton OnSite, Siemens, and Hydrogenics (now Cummins), focusing on hydrogen production development.79 The typical PEMWE systems comprise PEM, CL (cathode and anode electrocatalysts), PTL, and BPPs (Fig. 5a).80 The most widely used membrane in this context is the perfluorosulfonic acid (PFSA)-based PEM, noted for its high proton conductivity.81,82 At the anode side, feed water decomposes into oxygen, protons, and electrons. The protons then move to the cathode side through the PEM, combining with electrons from the current collector to produce high-purity hydrogen. Concurrently, the generated oxygen and hydrogen exit the cell sequentially through the catalyst surface, PTL, and BPPs. The efficiency of a PEMWE, especially at high current densities, is significantly influenced by its contact and interface structure. This section will delve into the components of the PEMWE setup, discussing the corresponding degradation mechanisms and their mitigation strategies.
 |
| Fig. 5 (a) Diagram showing the stack structure and essential materials of PEMWE. (b) Process illustration for roll-to-roll direct CL coating on membranes. Reproduced with permission from ref. 83. Copyright 2020, Elsevier. (c) Diagram of RSDT components and the associated liquid delivery system. Reproduced with permission from ref. 84. Copyright 2011, Springer. (d) Comparative schematics of CCM, PTE-type MEA, and DMD-MEA technologies. Reproduced with permission from ref. 85. Copyright 2020, Elsevier. | |
3.1. Membrane electrode assembly methods
The design of the stack is crucial in enhancing both the performance and longevity of PEMWE systems. This is achieved by minimizing ohmic and mass losses and reducing cell degradation. The MEA, comprising a PEM, cathode/anode CL, and two PTLs, are core components to these systems. They primarily influence the electrochemical reactions occurring at the triple-phase boundary between the electrolyte, catalysts, and gaseous species.
CLs are typically fabricated using ink dispersions, created by blending the catalyst and ionomer with a mixture of solvents and water. This ink is then applied as a thin coating onto a substrate, which may be a membrane, decal, or gas diffusion layer, and subsequently dried. The viscosity of the catalyst ink is largely affected by catalyst–ionomer interactions. Enhanced ionomer adsorption on the catalyst surface can optimize the ink's viscosity, making it more suitable for industrial-scale fabrication. For MEAs, the catalyst ink can be deposited either directly on the PEM, resulting in a catalyst coated membrane (CCM) configuration, or on anode PTL, also known porous transport electrode (PTE).80 Common CCM fabrication techniques include direct spray,86,87 decal method,88–90 roll to roll fabrication (Fig. 5b),83,91 and reactive spray deposition technology (RSDT, Fig. 5c).84 The ultrasonic spraying method, which employs a catalytic ink printer with an ultrasonication nozzle, is typically used to maintain the catalyst particles in suspension. Though simpler, direct spraying onto the membrane must be done cautiously to prevent solvent impregnation and the consequent swelling of the membrane, which could lead to deactivation through cracking or delamination of the active layer. Additionally, magnetron sputtering can be employed to deposit particles onto a substrate. For instance, Hrbek et al.92 used this technique to create a low Ru–Ir content (0.158 mg cm−2) thin film for water electrolysis, achieving impressive stability over 1272 h of operation without a significant drop in reactivity. RSDT is a flame-based technology that combines catalyst fabrication and CL deposition in one step, which is a new technology that was first reported in 2009 for the deposition of electrolyte and cathode materials in solid oxide fuel cells.93 Yu et al.94 utilized RSTD process to develop CCMs that operated for over 4500 h of operation with an anode catalyst loading of 0.08 mgIr cm−2. The high performance is attributed to a high ratio of IrIV to IrIII in RSDT-synthesized IrOx nanoparticles. PEMWE is now benefiting from automated and continuous roll-to-roll manufacturing processes, previously used in PEMFC technologies, which is the most promising fabrication approach that can meet the cost and volume target set by the growing demand for PEMWE soon. PTE, in contrast, are typically prepared via direct spray, electrodeposition, ink-jetting, atomic layer deposition, and sputtering.2,95 The production process demands precise attention to ensure optimal contact between the coating materials and substrates, thereby enhancing electrical performance. A thinner CL generally yields higher mass activity. For example, a cathode with a Pt CL deposited by sputter deposition can be significantly thinner (15–90 nm) than conventional CLs, resulting in a mass activity that is 58 times higher than that of a conventional CCM at 1.6 V.96 Additionally, sputtering catalysts directly onto the PTL can increase catalyst utilization efficiency and reduce costs compared to CCM. Spraying catalysts on PTL, for instance, allows for thick and even deposition, which helps prevent wrinkling of the PEMs.97
Innovative assembly methods are being explored to further improve the overall performance of PEMWE. Stähler et al.98 pioneered the direct membrane deposition (DMD) technique for MEA fabrication in PEMWE systems. They produced MEAs using a single slot die coating device, sequentially depositing the cathode CL, a thin membrane (∼20 μm), and the anode CL, followed by hot-pressing the resulting CCM. Holzapfel et al.85 later adopted the DMD approach for PEMWE–MEAs, applying the membrane directly onto the cathode electrode via spray coating (Fig. 5d). Their DMD–MEAs, comprising a membrane-cathode compound assembled with an anode electrode (a porous titanium fiber substrate coated with IrO2), demonstrated excellent electrochemical performance. Although they exhibited slightly higher activation losses compared to reference CCMs, DMD–MEAs showed reduced ohmic and mass transport losses. Compared to PTE-type MEAs, DMD also showed improvements in all three loss mechanisms. Future research will focus on gas crossover and performance analysis in low catalyst-loaded DMD–MEAs. This novel method offers a new approach for MEA preparation.
3.2. Degradation mechanisms of PEMWEs
PEMWE is an advanced and effective solution to the hydrogen energy technology. A better understanding of the performance and durability of PEMWE is critical for both scientists and engineers to further advance this technology for its market penetration, and for the manufacturers of PEMWE to implement quality control procedures for the production line or on-site process monitoring. Therefore, a comprehensive understanding of the degradation mechanisms and the corresponding mitigation strategies of components, including catalysts, membranes, PTL, and BPPs, is pivotal, moving the PEMWE technology forward to become a key element in future energy blueprint.
3.2.1 Degradation mechanisms of CL.
In PEMWE environments, catalyst stability and durability face challenges due to factors like high anodic overpotential, strong oxidizing conditions, low pH, and elevated temperatures. These challenges can lead to catalyst dissolution, proton exchange sites blocking by metal ions, agglomeration, and support passivation/corrosion. Such issues result in poor contact between the CL and electrodes, and altered interfaces between the membrane and CL, decreasing the ECSA and increasing electrical resistance.
Catalyst dissolution/agglomeration.
Long-term operation in high anodic potential (>1.6 V) and low pH conditions can cause Ir catalyst dissolution (Fig. 6a and b).39 The dissolution mechanism, involving intermediates like IrO2OH and HIrO2 (eqn (1)–(7)), is not fully agreed upon in the literature. | HIrO2 + 3H+ → Ir3+ + 2H2O | (1) |
| HIrO2 → IrO2 + H+ + e− | (2) |
| IrO2 + H2O → IrO2OH + H+ + e− | (3) |
| 2IrO2OH → 2HIrO2 + O2↑ | (4) |
| IrO2OH → IrO3 + H+ + e− | (5) |
| IrO3 + H2O → IrO42− + 2H+ | (6) |
Specifically, eqn (1) describes the dissolution of the iridium intermediate, HIrO2, under acidic conditions. H+ facilitates the oxidation of HIrO2, producing Ir3+ and water. This dissolution contributes to the loss of active Ir species, which can reduce catalyst durability under prolonged high-potential operation. The presence of Ir3+ indicates that iridium is susceptible to leaching in the acidic electrolyte. In the next oxidation reaction, HIrO2 is converted to IrO2, releasing the H+ and e−. IrO2 is generally more stable under typical OER conditions, but this transformation represents a step where further oxidation can occur, contributing to higher oxidative states and potential catalyst degradation (eqn (2)). In eqn (3), IrO2 interacts with water to form the hydroxylated intermediate IrO2OH, along with the release of the H+ and e−. This reaction suggests the initial stages of surface oxidation, which could increase the likelihood of structural changes and oxidation beyond Ir4+, eventually leading to the formation of higher oxidation states that promote dissolution. Eqn (4) shows the dimerization and subsequent dissociation of the hydroxylated species IrO2OH to produce HIrO2 and O2. Eqn (5) represents the further oxidation of IrO2OH to form IrO3. The formation of IrO3, especially under high anodic potentials, suggests an oxidative environment that promotes Ir instability. According to Kasian et al.,99 IrO3 formation is a critical factor contributing to Ir dissolution, as it introduces a higher oxidation state that is less stable in acidic media. As shown in eqn (6), IrO3 is further oxidized in the presence of water to produce IrO42− and releases protons. IrO42− is a highly soluble species, which means that once Ir reaches this oxidation state, it can readily dissolve in the electrolyte. This dissolution significantly reduces the active Ir content of the catalyst and impairs its OER activity. Additionally, eqn (7) indicates the decomposition of IrO3 back to IrO2 with the release of oxygen. While this reaction can mitigate some Ir loss by regenerating IrO2, the recurring formation and decomposition cycle accelerates Ir degradation over time. Additionally, the metallic Ir could aso be oxidized to Ir3+, leading to catalysts degradation. And Yu et al.100 discovered that dissolved Ir ions can migrate through the Nafion 117 membrane, reprecipitating and affecting the anode/membrane interface and cathode. Recent work utilizing ex situ ICP-MS analysis and detailed physicochemical characterization of the CL/membrane interfaces has further advanced the understanding and accurate quantification of anode catalyst losses under realistic PEMWE operating conditions.101,102 Mechanical damage during assembly, gas-bubble formation, and catalyst agglomeration also impacts CL stability. Limiting bubble size can significantly increase stability.100 While catalyst agglomeration, involving particle growth mechanisms like redeposition, Ostwald ripening, and coalescence, could lead to ECSA loss (Fig. 6c).103
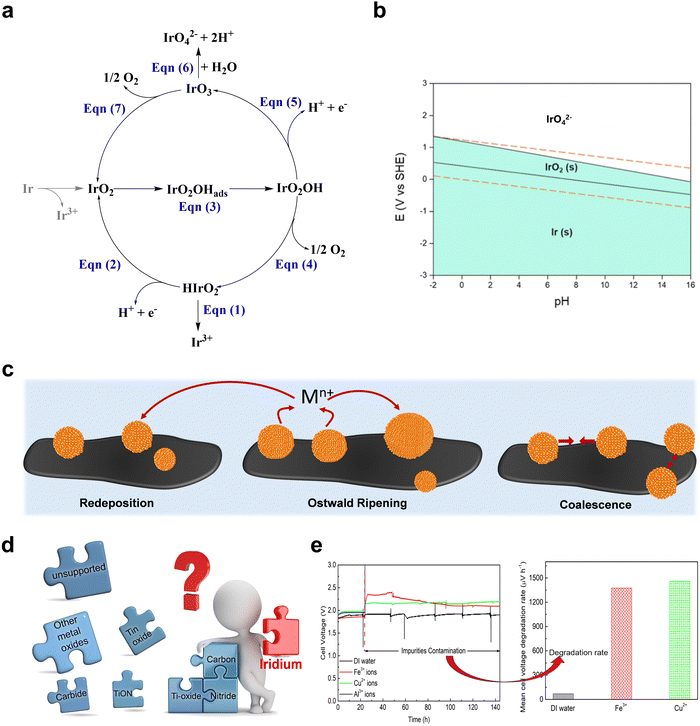 |
| Fig. 6 (a) Proposed mechanism for Ir dissolution during OER. (b) Pourbaix diagram of Ir. Reproduced with permission from ref. 39 Copyright 2023. Royal Society of Chemistry. (c) Proposed mechanism for catalytic particle enlargement. (d) Supports for Ir-based catalysts in OER. (e) Impact of cationic impurities on PEMWE performance. Reproduced with permission from ref. 104. Copyright 2020, Elsevier. | |
Metallic cations poisoning.
Metallic cation poisoning, involving elements like Fe3+, Cu2+, Al3+, and Ti4+, is a prevalent issue in PEMWEs (Fig. 6e).104 These impurities often stem from feed water, corrosion in water pipes and cell components, or other external sources. Once inside the system, these cations infiltrate the CL, occupying ion exchange sites in both the electrolyte membrane and the ionomer within the CL. This leads to increased overpotential at both cathode and anode sites.105 Moreover, the catalyst surfaces, particularly Pt at the cathode, are susceptible to blockage by these cations, causing metal or metal oxide precipitation.106 However, this type of poisoning is mostly reversible. The impurities can typically be eliminated by immersing the MEA in a liquid acid solution, such as H2SO4.105
Catalyst support passivation.
When examining supported catalysts in PEMWE systems, the degradation mechanisms become increasingly complex. One notable issue is the passivation of the catalyst support, often due to the formation of a poorly conductive oxide shell on the support surface. This shell leads to heightened ohmic resistance at the contact interface. The research conducted by Moriau and colleagues systematically investigated the passivation of various supports commonly used to stabilize Ir for OER in acidic PEMWE (Fig. 6d).107 Moreover, it has been observed that certain impurities, such as fluoride ions (F−), can dissolve TiO2 supports during polarization, adding another layer of complexity to the degradation process.108
Mitigation strategies.
For a PEMWE cell, catalyst mixed with ionomer forming a porous CL in MEAs, plays a significant role in long-term stability. Apparently, the choice of suitable catalyst and catalyst support, with optimized CL structure are of the upmost importance. As for the latter one, factors like mechanical stress from bubble formation and detachment, electronic stress because of the applied current and increased current by blocked sites, the support passivation, and the contact resistance between the catalyst and support as well as membrane, could all weaken the catalyst adhesion. Consequently, researchers have developed the fabrication of CL through direct synthesis of IrOx nanoparticles by a flame-based reactive spray deposition method, which enables IrOx to embed into Nafion ionomer, thus forming a CL with high porosity and good transport network connection for gas, liquid, and solid phases.94 They found that an optimal low loading of 0.08 mgIr cm−2 for the fabricated anode, which exhibited 1.8 A cm−2 at 1.875 V using N117 as the membrane. The cell showed long-term durability of 4500 h operation without significant voltage loss. Another is the nanostructured thin film (NSTF) catalyst developed by 3M which are catalyst of unique structure with high activity. The NSTF catalyst is prepared by growing perylene red whiskers on a special temporary substrate, and then the catalyst is deposited on it in a rod-like array structure. The whisker cores out of perylene are single crystals, having highly uniform surface for subsequent coating with catalytic materials like Ir. The preparation process allows the catalyst to be deposited uniformly, and NSTF catalysts can also be mass produced by roll-to-roll. And the NSTF catalysts are reported to be less sensitive to agglomeration and corrosion due to the special catalyst morphology and the absence of carbon support. With only 0.25 mgIr cm−2 loading, Lewinski et al.109 reported that the synthesized NSTF catalyst approached the peak current density of 20 A cm−2, and the durability test was performed by holding at a current density of 2 A cm−2 for 5000 h with the voltage loss rate of only 6.8 μV h−1. Currently, NSTF catalysts has been well-developed in fuel cells, and it is believed to be commercialized in PEMWE soon.110
3.2.2 Degradation mechanisms of membranes.
The membrane in PEMWE systems serves two crucial functions: it separates the produced H2 and O2 gases and facilitates proton transfer between electrodes to complete the operational circuit. For effective performance, the membrane in PEMWE must possess outstanding chemical and mechanical stability, thermal resilience, high proton conductivity, and resistance to gas crossover.3,13 Consequently, the membrane is vital for both the safe operation and the energy efficiency of the system. To guarantee optimal performance and longevity of PEMWE systems, a comprehensive understanding of the complex degradation mechanisms is essential.111 Although numerous studies have been done on the degradation mechanisms of membrane in PEMFCs (Fig. 7a), the related research in PEMWEs is still in its infancy.106 This part will explore the well-recognized degradation pathways, mainly including chemical, mechanical degradation, and thermal degradation.
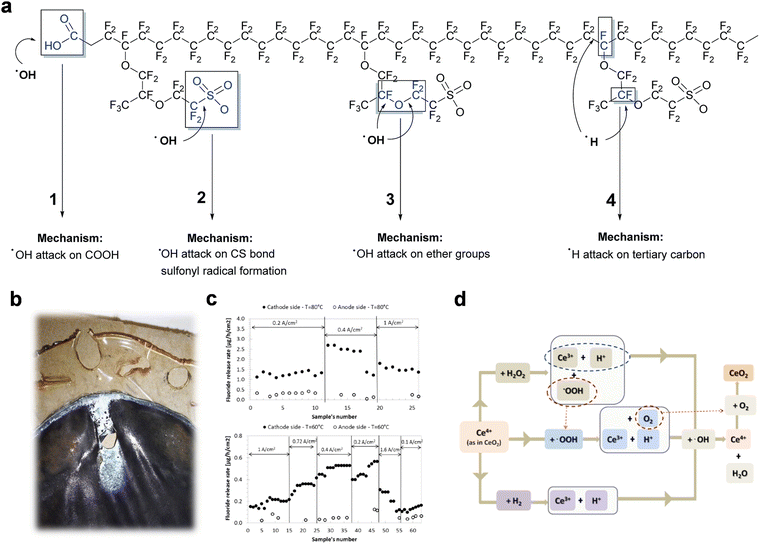 |
| Fig. 7 (a) Overview of the radical attack mechanism on the Nafion® polymer structure. Reproduced with permission from ref. 106. Copyright 2017, Royal Society of Chemistry. (b) Image of MEA post-perforation. Reproduced with permission from ref. 112. Copyright 2012, Elsevier. (c) Fluoride-ion release rates at the anode and cathode in tests at 60 °C and 80 °C across varying current densities. Reproduced with permission from ref. 113. Copyright 2015, Elsevier. (d) Scavenging mechanism of CeO2 and the regeneration of Ce3+ active sites. Reproduced with permission from ref. 114. Copyright 2012, National Academy of Sciences. | |
Chemical degradation.
Gas crossover, particularly oxygen permeating through the membrane to the cathode, is widely recognized as a critical issue in PEMWE systems. This process leads to a two-electron reduction, producing hydrogen peroxide (H2O2). The situation worsens when H2O2 interacts with contaminated metal ions such as Fe2+, triggering a Fenton reaction that generates radical species (e.g., HO˙, HOO˙). These oxidizing agents aggressively attack the PFSA structure of the membrane, causing severe degradation.115 This degradation manifests as fluoride and sulfur release, membrane thinning, and increased mechanical failure, which in turn exacerbates hydrogen crossover from cathode to anode, posing significant safety risks. Chandesris et al.113 developed a 1D PEMWE model incorporating membrane chemical degradation to investigate the effects of temperature and current density on this degradation. By analyzing the fluoride release rate in the effluent water from both anode and cathode sides, they observed that degradation predominantly occurs on the cathode side and is heavily influenced by temperature. As for current density, its impact is less straightforward: degradation rate is low at very low current densities, increases to a peak at a slightly higher current density, and then decreases.113,116 Additionally, metallic ions like Fe3+, Cu2+, and Al3+, originating from corrosion and impurities in feed water, can significantly impair the PFSA membrane.104,117 These ions disrupt proton transport, leading to increased ohmic resistance. For instance, cell performance deterioration was observed during Fe3+ ion contamination tests, largely due to higher affinity of Fe3+ for the sulfonate groups in the Nafion membrane compared to H+.118 This interaction reduces effective triple-phase boundaries and proton conductivity.
Mechanical degradation.
Mechanical degradation, a result of mechanical forces, often leads to premature membrane failure. Long-term testing indicates that time-dependent deformation, including creep and microcrack formation in Nafion membranes, is a key issue. This is due to the stress repeatedly exerted on the membrane, with uneven compression exacerbating this deformation. The repeating membrane expansion and contraction weaken it over time, leading to changes in dimensions, poor contact with electrodes, and pinhole defects. These pinholes, caused by localized stress, significantly shorten the lifespan of PFSA membranes by initiating cracks. Hydrogen crossover, resulting from the PTL puncturing the membrane, could cause intense local heating that gradually damages the membrane. Specifically, Masson et al.119 conducted a study on a polyethylene-based membrane, designed as a cost-effective alternative to Nafion. Their research included analyzing the performance of membrane under various conditions and executing a 3000-h continuous operation degradation test at 2 A cm−2. Throughout this test, parameters such as the device voltage, gas concentrations at the electrodes, and Faraday efficiency were monitored. The study determined that membrane perforation, leading to localized degradation, was predominantly due to local overheating (Fig. 7b).112 More recently, Siracusano et al.120 performed a long-term degradation test, starting with a 200-h conditioning period at 1 A cm−2 followed by 800 h at 3 A cm−2, showed a mean voltage increase of 90 μV h−1. The study concluded that continuous high current density operation, especially above 2 A cm−2, greatly contributes to membrane thinning. In industrial settings, PEMWE often operates under high pressure, especially for automotive applications requiring storage pressures of several hundred bars. At these pressures, mechanical failures like membrane creep are more concerning than chemical degradation, and gas cross-permeation becomes a critical issue. Finally, inadequate water circulation can lead to early system failure due to uneven water distribution or starvation. Excessive water flow can damage the system through high pressure, while insufficient flow causes uneven distribution and hot spots. This leads to irregular electric current and membrane swelling, intensifying the degradation process.
Thermal degradation.
The general working temperature of a PEMWE is 60–80 °C. And temperatures above 80 °C significantly accelerate membrane thinning.116 Thermal degradation usually occurs alongside mechanical and chemical degradation. The research has extensively demonstrated that temperature exerts a more significant impact on membrane thinning compared to current density. In this context, Chandesris et al.113 delved into the effects of temperature and current density on membrane degradation (Fig. 7c). They conducted an analysis of the fluoride-ion release rate in the effluent water at both the anode and cathode during experiments conducted at temperatures of 60 °C and 80 °C across various current densities (ranging from 0.1 to 3 A cm−2). The findings revealed a pronounced increase in membrane chemical degradation with rising temperatures. As for current density, its impact was found to be smaller and more complex. At very low current densities, the rate of degradation was low. However, as current density increased, the degradation rate reached a maximum at relatively low current densities before decreasing. The observed reduction in degradation rate at high current densities has been attributed to a lower molar percentage of O2 on the cathode side. Subsequent studies by Guillet and colleagues have further supported these findings.116
Mitigation strategies.
Reinforcement of the PEM can enhance its structural stability, and the methods for reinforcement generally include physical strengthening and chemical modification. Physical strengthening includes membrane annealing, uniaxial stretching, and structural compositing. For example, annealing of PFSA polymer can improve the crystallinity of the polymer. Uniaxial stretching can effectively increase the Young's modulus, reduce area expansion, and slightly improve proton conductivity. Structural composite reinforcement involves using mechanically stable organic or inorganic porous materials as supports, combined with PFSA polymers as proton conductors to create a composite. This serves to increase structural strength and facilitate proton conduction. For instance, using polytetrafluoroethylene (PTFE) porous membranes as support material can provide the composite membrane with good mechanical strength and dimensional stability, preventing delamination of the catalytic layer from the membrane due to excessive swelling from water absorption. Thus, PFSA/PTFE reinforced composite membranes not only enhance the mechanical stability and durability of the membrane but also reduce the thickness of the PEM from 25–100 μm to 8–18 μm. This has become a widely applied technology in the field of PEM.
Chemical modification reinforcement is achieved by chemically cross-linking the membrane material, which stabilizes the polymer structure, reducing dimensional swelling and enhancing mechanical stability. Reducing the groups in PFSA polymers that are susceptible to free radical attacks is one method to enhance the chemical stability of PEMs. Short-side-chain resin PEMs, compared to their long-side-chain counterparts, lack a tertiary carbon (–CF) and an ether linkage carbon atom (–O–CF2), which decreases the sites vulnerable to attacks and reduces the sensitivity of short-side-chain resin PEMs to free radical attacks. This has been confirmed by some studies. Danilczuk et al.121 compared the chemical durability of Nafion membranes (with an equivalent weight, EW, of 1100), 3M membranes (EW = 850), and Aquivion membranes (EW = 830). They found that the 3M and Aquivion membranes exhibited better stability, attributed to the absence of ether groups and tertiary carbons in the side chains. Introducing radical scavengers into PEM to reduce the concentration of radicals like peroxides is another effective measure to mitigate the chemical degradation of PEMs. Common radical scavengers used for this purpose include metal oxides such as CeO2, MnO2.106 These materials can help reduce the impact of harmful free radicals within the PEM, thereby enhancing its chemical stability and longevity. Prabhakaran et al.114 examined the CeO2 as an example to understand the mechanism of radical scavengers in eliminating free radicals through a fluorescent molecular probe in conjunction with the in situ fluorescence spectroscopy. They proposed that the scavenger properties of ceria are mediated at oxygen vacancies or defects in the lattice structure. Thus, the hydroxyl radical could be scavenger by Ce3+ ions, which are further oxidized to Ce4+. And the oxidized Ce3+ is regenerated in acidic media through the mechanism as shown in Fig. 7d. This regeneration of the Ce3+ form appears to be an important factor for CeO2 mitigation ability. Moreover, as the flow of gases through the membrane increases with increasing pressure inside the electrolyzer, safety issues can occur at high pressures. Klose et al.122 introduced a CL within the membrane, enabling the gases passing through to react and reduce at the platinum sites, thereby producing water within the membrane itself. This setup underwent a stability assessment for 245 h at the current density of 1 A cm−2. The modification of the membrane demonstrated effectiveness in terms of safety, significantly minimizing the gas flow through the membrane.
3.2.3 Degradation mechanisms of BPPs.
The BPPs in PEMWEs primarily serve functions such as supplying reactants (H2O), discharging products (O2, H2), conducting electrons, and providing mechanical support. They must possess low electrical resistance, provide insulation between the anode and cathode chambers to prevent gas mixing, have high mechanical and chemical stability, facilitate fluid distribution, and since they also help facilitate heat transfer, they need to have high thermal conductivity as well. Their multifunctionality and the complex environment they operate in make them highly susceptible to degradation and attenuation. Currently, high-performance BPPs generally use titanium as a base. However, they are still prone to hydrogen embrittlement, passivation, and corrosion, especially under high current densities (>3 A cm−2) and strong oxidizing conditions.
Hydrogen embrittlement.
Hydrogen embrittlement of commercial pure titanium has been reported in the literature.123 As the PEMWE operates over a long period, some hydrogen permeation can occur. This permeating hydrogen can react with the titanium-based electrodes, forming titanium hydride (TiH2), which is relatively brittle. As the extent of hydrogen embrittlement increases, the bipolar plates may even be at risk of cracking under high pre-tightening forces and operational pressures. Back to early 2002, Briant et al.123 have systematically studied the hydrogen embrittlement of commercial purity Ti. They found that when exposed to gaseous hydrogen at elevated temperatures the grade 2 titanium would readily form hydrides and the material became very brittle, which may lead to mechanical failure of BPPs.
Passivation.
In high-potential, high-humidity, and oxygen-rich environments, the thickness of the oxide layer on the surface of titanium BPPs increases over time. This increase in the oxide layer thickness leads to a rise in contact resistance, which in turn hinders the efficient conduction of electrons.124 This phenomenon can impact the overall performance and efficiency of the PEMWE systems. Therefore, titanium plates are usually coated with precious metals, such as Pt or Au, to achieve durability and performance requirements in the high potential range and oxidation environment. Despite the effectiveness of precious metals in PEMWE, their high cost, particularly for MW and GW scale electrolyzers, significantly restricts their widespread practical application. Consequently, there is a pressing need to research and develop low-cost coating materials to make PEMWE technology more economically viable and accessible.
Corrosion.
When titanium BPPs are in a strong acidic environment and exposed to F−, a reaction like the one described in eqn (8) occurs, causing the corrosion resistant TiO2 film on the surface of the BPPs to be eroded.108 | TiO2 + 4H+ + 6F− → TiF62− + H2O | (8) |
Mitigation strategies.
Due to passivation and corrosion being the primary occurrences in the actual operation of PEMWE, and the high cost of electrodes, current research on anti-degradation focuses on the surface treatment processes and the selection of base materials for the electrodes. Up to now, titanium plates are typically coated with precious metals to reduce the interfacial contact resistance and thus increasing the efficiency. In terms of base material selection, Gago et al.125 have employed vacuum spraying techniques on stainless steel to deposit a dense layer of titanium coating, followed by the deposition of a Pt thin film on the titanium layer using physical vapor deposition (PVD) to create a coated stainless steel that achieves good corrosion resistance with a low load of precious metals. As for surface treatment processes, nitride coatings, as a novel surface treatment method, can effectively cover all exposed surfaces with a low rate of pinhole defects. Moreover, the TiN formed on the surface exhibits strong resistance to hydrogen permeation in high-pressure environments, which can significantly alleviate hydrogen embrittlement.126 However, the coating cost and the process quality control to minimize coating defects are challenging for the BPPs application. Furthermore, a possible hazard associated with methods of protective coating is the alteration of the coating structure when the PEMWE functions in environments of thermal cycling, uneven current distribution, or thermal imbalances across the active zone. The base material and the coating might undergo expansion at varying speeds owing to the disparities in their coefficients of thermal expansion.
4. Cost reduction of PEMWE technology for practical applications
Commercial application of PEMWE technology relies on the cost reduction which makes the whole system for green hydrogen production profitable. The possible approaches to decrease the expenses may stem from the reduction in capital expenditures (CapEx) and operating expenses (OpEx), where several strategies may be employed. Reducing OpEx requires a reduction in the energy consumed and delicate control of the reaction conditions which could maximize the durability of the electrolyzer, and we have discussed the degradation of the critical components in the previous part. While regarding the CapEx, lowering the loading of materials used to deliver fixed amount of the hydrogen produced are the essential goal to achieve. Usage of less noble metal catalysts by the development of low-Ir content catalysts are discussed early in this review. And we have also mentioned the importance of catalyst morphology modification to enhance the mass transport in catalyst layer and to reduce the energy consumed for hydrogen production. Herein, we highlighted the approaches to optimize the components inside PEM electrolyzer to make it suitable for high current density operation without sacrificing the performance and durability,127,128 which is of highly importance for the reduction of CapEx.129
4.1. PEM with higher ionic conductivity
The ionic resistance of proton exchange membrane significantly contributes to high-frequency resistance of PEM electrolyzer, thereby reducing the efficiency of PEMWE.130 Employing thinner proton exchange membrane is a critical approach to mitigating ohmic resistance. However, the strategy comes at the expenses of higher hydrogen permeation131 and faster membrane degradation,130,132 raising the risk of forming explosive H2/O2 mixture. Besides, the mechanical integrity of PEM under high differential pressure is also compromised,133 differing markedly from the conditions in fuel cells.
Commercial PEM providers including Fumatech and GORE, proposed two technologies to address the issues: incorporating expanded polytetrafluoroethylene (ePTFE) or polyether ether ketone (PEEK) to enhance mechanical strength, and doping the membrane with Pt black to catalyze hydrogen oxidation, thereby lowering hydrogen content in oxygen (ξH2).134 The ξH2 of 2 vol% could serve as a boundary condition for the optimization of PEM thickness in the future.135 Theoretical analysis revealed that when the operating current density is larger than 250 mA cm−2, the safe ξH2 could be fulfilled even for the PEM thickness thinner than 50 μm.135 As illustrated in Fig. 8a, the optimal PEM thickness is plotted against the power input of the electrolyzer, owing to the varied hydrogen crossover tendency at different current densities. Moreover, we envisage that if the hydrogen permeation could be completely mitigated by incorporating the hydrogen recombination catalyst in the membrane, an electrolysis efficiency margined optimal PEM thickness should be adopted in the state-of-the-art technology. Nonetheless, substantial efforts are still required on the development of high-performance MEA to achieve the goal.
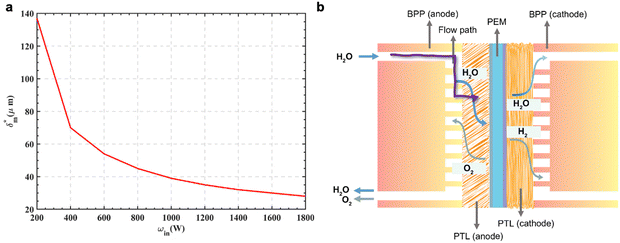 |
| Fig. 8 The optimization of PEM thickness and mass transport process to improve the performance and reduce the expenses. (a) Optimal membrane thickness calculated under different input power of the PEMWE. Reproduced with permission from ref. 135. Copyright 2024, Elsevier. (b) The structure of PEMWE unit and the mass transport paths indicated by the purple arrow, which highlights the influences of flow path and PTL. Reproduced with permission from ref. 136. Copyright 2023, Royal Society of Chemistry. | |
4.2. CL and PTL with better mass transport
Mass transport in the CL, PTL and flow field is essential for PEMWE operating at high current density.137–139 The adequate supply of H2O on anodic catalyst surface makes OER possible, and maintaining the water content in pPEM brings higher proton conductivity (Fig. 8b).136
Permeation-controlled rather than diffusion-controlled oxygen transport in anodic PTL is proposed as the possible mechanism for two-phase flow in PEMWE.140 The formation of stable gas channels within the PTL, where the replacement of water-filled pores with oxygen happens, underscores the importance of precisely tuning the pore size distribution, pore tortuosity, and hydrophilicity of the pore surfaces. At the industrial scale, the expense of PTL is a significant consideration alongside the improvement of electrolyzer performance.
Water and oxygen transport in CL is another important physical process which affects the accessibility of water on reaction sites and water supply to the PEM. As mentioned in this review, creating 3D nanostructure of CL mitigates gas blinding and therefore improves the mass transport. However, visualizing gas bubble detachment from electrodes may lead to different conclusions regarding surface bubble blockage.141 Driven by the reduction of surface energy, smaller bubbles that detach from the catalyst surface tend to coalesce, and the resulting large bubbles adheres near the surface before eventually being release. Observing larger bubbles might indicate better mass transport. The mechanism of mass transport enhancement in nanostructured electrode should be revisited in future studies. In terms of the practical PEMWE devices, the ionomer content and the distribution of catalyst and ionomer should be optimized to facilitate the transport of H2O and O2.
4.3. Flow field for enhanced thermal transport
Thermal management in industrial-scale PEMWE is crucial for maintaining the appropriate temperature at MEA, avoiding the hotspot formation and thermal degradation.142,143 Operating at higher current density leads to higher Joule heating within the reaction area, thereby exacerbating the thermal failure. Widely employed approach for heat transport enhancement inside PEMWE is increasing the flow rate through the BPPs.142 However, the flow resistance rapidly increases with the flow rate, causing unavoidable mechanical energy loss that lowers overall efficiency of the whole system. Possible remedies to this include the design of the flow direction in BPPs to enhance the thermal transport, and the incorporation of a cooling fluid for the temperature control, akin to the structure in PEMFC.144–146 These strategies are important for the advancements of PEMWE technology towards industrial scale, which should be focal topics in future research.
Optimization of the entire system of PEMWE has the potential to revolutionize the technology, aligning it more effectively with the massive supply of intermittent renewable electricity. Despite the significant advancements in catalysts, numerous aspects of the PEMWE and the balance of plants still require further studies to reduce the expenses associated with green energy operation, and the related discussion goes beyond the scope of this review. In the following section, the possible research topics of catalyst engineering that are important for reducing the expenses and pushing the technology to real world application are prospected.
5. Conclusions and prospects
As hydrogen gains importance as a clean, renewable fuel and chemical feedstock, advancing its sustainable production has become a major research focus. Among the various water electrolysis technologies, the PEMWE system stands out due to its unique advantages (Fig. 9). This review begins by surveying the current research on critical PEMWE components, including anode electrocatalysts, the PEM, and BPPs, with an emphasis on recent advances in anode electrocatalysts development. Furthermore, we analyze the essential role of catalyst coating techniques in the PEMWE assembly process. While substantial progress has been made in PEMWE technology, high component costs and susceptibility to harsh operational conditions continue to pose major barriers to widespread adoption. This review explores these challenges in depth, addressing issues such as anode catalyst degradation, membrane and mechanical failures, and corrosion of BPPs and PTLs, which are essential to tackle for reducing costs and improving system durability (Fig. 10a).
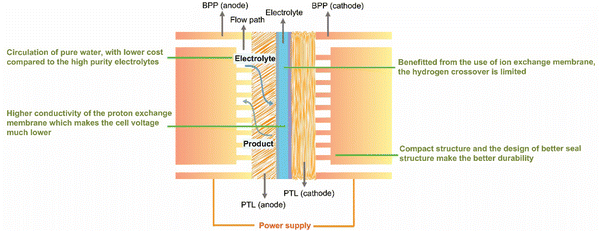 |
| Fig. 9 Advantages of PEMWE technology for renewable energy-powered hydrogen production. | |
 |
| Fig. 10 (a) Key materials research for PEMWE. (b) Iridium market price over the past decade. (c) Total cost breakdown for 1 MW PEMWE system. Reproduced with permission from ref. 147. Copyright 2021, Wiley-VCH. | |
The reduction in CapEx for PEMWE could be realized from various aspects. First, reduce the iridium content in anodic catalysts. Common methods include the incorporation of doping elements and development of stable substrates. Second, reduce the catalyst loading on MEA. This usually requires a higher surface area for catalyst that ensures the better coating homogeneity and existence of sufficient reaction active sites. Third, increase the current density to lower the use of catalytic materials or area of PTL or BPP to obtain certain amount of hydrogen. Finally, prolong the lifetime for the PEMWEvia the design or modification of catalyst composition, microstructure, radical scavenger in PEM and development of coating materials for PTL and BPP. Herein, some crucial challenges that should be overcome in the future are briefly introduced.
5.1. Reducing the catalyst cost
Ir-based catalysts have emerged as the top choice for OER in PEMWEs, currently the only product in commercial use. However, due to the scarcity of Ir (with global production only ∼5–10 tons annually) and high cost (∼$206 per g), there is a pressing need to significantly reduce iridium usage in OER applications for scalability (Fig. 10b).28,36 A promising strategy involves utilizing supported catalysts with enhanced electronic conductivity and optimized iridium density. Innovations such as atomically dispersed Ir sites, Ir-based alloys, and Ir clusters on supports have demonstrated promising electroactivity for OER in both neutral and acidic conditions. Further enhancement of their performance and durability could make these catalysts viable for industrial-scale PEMWE applications. Additionally, leveraging 1D or 2D nanomaterials like nanorods, nanoparticles, and nanosheets offers another pathway to lower iridium usage without compromising durability.
While reducing Ir loading on the MEA is a valuable strategy for cost reduction in PEMWE technology, alternative catalyst systems such as Ru-based and noble-metal-free catalysts are increasingly proposed as viable low-cost candidates. Ru-based catalysts are particularly promising due to their higher intrinsic activity compared to Ir counterparts.38,71 This increased activity is attributed to favorable binding energies of Ru for key reaction intermediates (*OOH, *O, and *OH), which enhance catalytic performance. Moreover, Ru is significantly less costly than Ir, priced at approximately $17 per g by the end of 2022. This cost advantage positions Ru as a compelling choice for scaling up PEMWE technology. However, the susceptibility of Ru to leaching under OER conditions poses a considerable challenge. Ru-based catalysts demonstrate an S-number (103–104) markedly lower than that of Ir-based catalysts, indicating limited stability in these conditions.148 The underlying mechanism for this vulnerability may be related to the lattice oxygen mechanism in RuOx, where the high covalency of Ru–O bond facilitates bond breakage. To address this, Ping et al.149 introduced a Si-doped RuO2 catalyst, in which robust Si–O bonds stabilize the catalyst by inhibiting oxygen vacancy formation, yielding a more durable OER catalyst suitable for acidic environments. This development highlights promising pathways, yet further research is needed to enhance long-term stability. Noble metal-free catalysts also present an intriguing avenue for PEMWE. For instance, La- and Mn-doped cobalt spinel catalysts, as developed by Chong et al.,72 exhibited promising stability under OER conditions. The formation of an O* covered surface stabilizes the phase III of the material, as revealed by the Pourbaix diagram, thus enabling more stable performance. Nonetheless, Ru-based and noble-metal-free catalysts remain in the early stages of research. While promising, these catalysts do not yet meet the rigorous requirements for high-power-density PEMWE applications. The technology still relies heavily on Ir-based catalysts for stable, large-scale performance. Even so, we believe that the transition to Ir alternatives is not only desirable but inevitable. Reducing reliance on scarce Ir resources will be essential for achieving the scale required for giga-factory levels of PEMWE production, as current trends in material science and technology development suggest.
For Ir-based scenario, ideally, the MEA should deliver a performance of 1.6 V@3 A cm−2 at 65 °C, with stability exceeding 80
000 h and total platinum group metal loading below 0.125 mg cm−2. As illustrated in Fig. 10c, the cost composition of a 1 MW PEMWE serves as a model case.150 BPPs in PEM stacks are a major cost factor, often incorporating multiple functions and requiring advanced materials like Au or Pt-coated titanium. Innovations in this area are crucial for enhancing performance, durability, and cost-effectiveness. Current research focuses on substituting titanium with less expensive materials while maintaining functionality through coatings. For the core component, the CCM, rare metals like Ir, although constituting less than 10% of the total cost of a PEMWE system, could become a bottleneck in scaling PEMWE production without a significant increase in iridium supply. Therefore, it is necessary to minimize the use of precious metals or develop alternative materials.
5.2. Resolving the conflict between stability and activity
The investigation into Ir-based catalysts, known for their exceptional stability and high catalytic efficiency, is crucial for advancing the affordability and industrial viability of PEMWEs. Given the operational demands of high temperatures (60–80 °C) and high current densities, there is a need for catalysts that not only exhibit superior catalytic performance but also maintain effective electron/mass transfer and durability within the cell stack. Enhancing catalytic stability in acidic environments can be achieved through various strategies, such as alloying, applying oxidation layers, employing nano-structuring techniques, and incorporating corrosion-resistant materials. Furthermore, the fundamental activity of Ir-based catalysts in the OER is significantly influenced by the interplay between hydroxyl (*OH) and peroxyl (*OOH) intermediates. Altering this interplay presents a promising yet challenging route towards pioneering high-efficiency OER catalysts.151 The use of highly active Ir catalysts could lower the operational overpotential, potentially decreasing the rate of Ir corrosion and enhancing overall stability. Thus, understanding the relationship between stability and catalytic activity is highly desired. For example, Kim and colleagues have introduced the activity-stability factor (ASF), a novel parameter that evaluates the performance and endurance of iridium oxide catalysts under consistent overpotential conditions.152 This approach has led to the identification of materials that strike an optimal balance between catalytic efficiency and longevity. With the adoption of AST protocols and machine learning techniques, the accurate assessment of degradation and prediction of the operational lifespan of PEMWEs for commercial use is expected to accelerate the industrialization process.
5.3. Bridging the gap between academic research and industrial demands
In the context of PEMWEs, the academic community is committed to pushing the limits of catalyst activity, while the industrial sector needs to balance cost, stability, and safety.147,153 Industrial applications require PEMWEs to operate stably under fluctuating conditions for over ten years, which places extremely high demands on the operational stability of the electrolyzers. However, academic research typically only conducts short-term stability tests (<5000 h), which do not fully address the long-term durability issues of concern to the industrial sector.111,154 Moreover, special attention needs to be paid to the balance between technology scaling up and down during the scaling process: the synergistic effects of heat transfer, mass transfer, and charge transfer become more complex in large-scale electrolyzers, simply scaling up the technology often leads to significant performance losses.155 Therefore, constructing effective small-scale electrolyzer research systems that accurately simulate actual operating conditions, and deepening the understanding of the different factors that affect electrolyzer performance, can provide important support for the scaling and application of new technologies. Facing the challenge of renewable energy variability, there is a need to expand the operational range of PEMWE.156,157 Meanwhile, to reduce the cost of hydrogen, PEMWEs need to be able to operate stably and efficiently under low load and overload conditions. Although hundreds of MW PEMWEs have been installed globally, there is still insufficient performance data under actual fluctuating power conditions, which also points to future research directions. (Fig. 11)
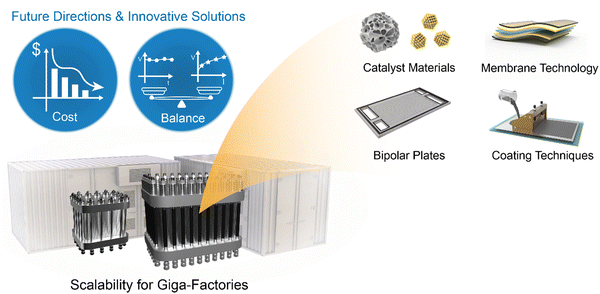 |
| Fig. 11 Future directions and innovative solutions for advancing PEMWE technology. | |
Moreover, enhancing the economic feasibility of hydrogen production via PEMWE requires significant reductions in both capital and operational expenses. The PEMWE market is projected to grow swiftly from its current capacity of <0.5 GW per year to ∼40 GW per year by 2030, followed by a more gradual increase to ∼350 GW per year by 2050. Consequently, the total PEMWE capacity is expected to reach ∼2200 GW by 2050.39 Optimizing and integrating key components such as the anode, PEM, PTLs, and BPPs are essential steps toward this goal. Future research should focus on overcoming existing limitations by exploring strategies like reducing catalyst load, operating at higher current densities and temperatures, and employing cost-effective non-titanium structural materials. For instance, operating at temperatures above 90 °C can markedly boost cell performance, and adopting coated, non-titanium materials like stainless steel could dramatically cut costs. Ultimately, merging experimental insights with computational findings will pave the way for more affordable, efficient, and durable PEMWE systems, opening avenues for the large-scale commercialization of hydrogen production facilities.
Author contributions
Y. Song and H. W. Chen conceived the topic and wrote the manuscript. C. Wang proposed the concept and collected data from the literature. X. D. Wang, and Y. X. Yuan wrote part of the manuscript. All members contributed to the discussion and revision of the manuscript. X. Yang and W. Lin revised the manuscript and supervised the project.
Data availability
No primary research results, software or code have been included and no new data were generated or analyzed as part of this review.
Conflicts of interest
The authors declare no conflicts of interest.
Acknowledgements
This work was supported by research grants from Ministry of Science and Technology of the People's Republic of China (no. 2021YFB4000205). We also thank Dr. Houpeng Wang, and Dr. Yuxiao Zhang for their participation in the revision of the manuscript.
References
- H. S. Baker, R. J. Millar, D. J. Karoly, U. Beyerle, B. P. Guillod, D. Mitchell, H. Shiogama, S. Sparrow, T. Woollings and M. R. Allen, Higher CO2 concentrations increase extreme event risk in a 1.5 °C world, Nat. Clim. Change, 2018, 8(7), 604–608 CrossRef CAS.
- M. Chatenet, B. G. Pollet, D. R. Dekel, F. Dionigi, J. Deseure, P. Millet, R. D. Braatz, M. Z. Bazant, M. Eikerling, I. Staffell, P. Balcombe, Y. Shao-Horn and H. Schäfer, Water electrolysis: from textbook knowledge to the latest scientific strategies and industrial developments, Chem. Soc. Rev., 2022, 51(11), 4583–4762 RSC.
- R.-T. Liu, Z.-L. Xu, F.-M. Li, F.-Y. Chen, J.-Y. Yu, Y. Yan, Y. Chen and B. Y. Xia, Recent advances in proton exchange membrane water electrolysis, Chem. Soc. Rev., 2023, 52(16), 5652–5683 RSC.
- L. Li, P. Wang, Q. Shao and X. Huang, Metallic nanostructures with low dimensionality for electrochemical water splitting, Chem. Soc. Rev., 2020, 49(10), 3072–3106 RSC.
- R. J. Ouimet, J. R. Glenn, D. De Porcellinis, A. R. Motz, M. Carmo and K. E. Ayers, The Role of Electrocatalysts in the Development of Gigawatt-Scale PEM Electrolyzers, ACS Catal., 2022, 12(10), 6159–6171 CrossRef CAS.
- Z.-Y. Yu, Y. Duan, X.-Y. Feng, X. Yu, M.-R. Gao and S.-H. Yu, Clean and Affordable Hydrogen Fuel from Alkaline Water Splitting: Past, Recent Progress, and Future Prospects, Adv. Mater., 2021, 33(31), 2007100 CrossRef CAS.
- K. Zeng and D. Zhang, Recent progress in alkaline water electrolysis for hydrogen production and applications, Prog. Energy Combust. Sci., 2010, 36(3), 307–326 CrossRef CAS.
- F. Guo, Y. Wu, H. Chen, Y. Liu, L. Yang, X. Ai and X. Zou, High-performance oxygen evolution electrocatalysis by boronized metal sheets with self-functionalized surfaces, Energy Environ. Sci., 2019, 12(2), 684–692 RSC.
- Y. Chen, C. Liu, J. Xu, C. Xia, P. Wang, B. Y. Xia, Y. Yan and X. Wang, Key Components and Design Strategy for a Proton Exchange Membrane Water Electrolyzer, Small Struct., 2023, 4(6), 2200130 CrossRef CAS.
- C. Wang and L. Feng, Recent advances and perspectives of Ir-based anode catalysts in PEM water electrolysis, Energy Adv., 2024, 3(1), 14–29 RSC.
- N. Du, C. Roy, R. Peach, M. Turnbull, S. Thiele and C. Bock, Anion-Exchange Membrane Water Electrolyzers, Chem. Rev., 2022, 122(13), 11830–11895 CrossRef CAS.
- M. Ni, M. K. H. Leung and D. Y. C. Leung, Technological development of hydrogen production by solid oxide electrolyzer cell (SOEC), Int. J. Hydrogen Energy, 2008, 33(9), 2337–2354 CrossRef CAS.
- K. Zhang, X. Liang, L. Wang, K. Sun, Y. Wang, Z. Xie, Q. Wu, X. Bai, M. S. Hamdy, H. Chen and X. Zou, Status and perspectives of key materials for PEM electrolyzer, Nano Res. Energy, 2022, 1, 9120032 CrossRef.
- N. Wang, D.-D. Ma, S.-H. Zhou, M.-K. Hu, X. Li, X.-T. Wu and Q.-L. Zhu, Heterointerface engineering of Ru/RuS2 on N/S-doped hollow mesoporous carbon for promoting alkaline hydrogen evolution, Chin. Chem. Lett., 2023, 34(7), 107788 CrossRef CAS.
- C. Santoro, A. Lavacchi, P. Mustarelli, V. Di Noto, L. Elbaz, D. R. Dekel and F. Jaouen, What is Next in Anion-Exchange Membrane Water Electrolyzers? Bottlenecks, Benefits, and Future, ChemSusChem, 2022, 15(8), e202200027 CrossRef CAS.
- D. Hua, J. Huang, E. Fabbri, M. Rafique and B. Song, Development of Anion Exchange Membrane Water Electrolysis and the Associated Challenges: A Review, ChemElectroChem, 2023, 10(1), e202200999 CrossRef CAS.
- S. S. Kumar and H. Lim, Recent advances in hydrogen production through proton exchange membrane water electrolysis – a review, Sustainable Energy Fuels, 2023, 7(15), 3560–3583 RSC.
- A. Makhsoos, M. Kandidayeni, B. G. Pollet and L. Boulon, A perspective on increasing the efficiency of proton exchange membrane water electrolyzers– a review, Int. J. Hydrogen Energy, 2023, 48(41), 15341–15370 CrossRef CAS.
- Z. Pei, H. Zhang, D. Luan and X. W. Lou, Electrocatalytic acidic oxygen evolution: from catalyst design to industrial applications, Matter, 2023, 6(12), 4128–4144 CrossRef CAS.
- C. Wei, Z. Wang, K. Otani, D. Hochfilzer, K. Zhang, R. Nielsen, I. Chorkendorff and J. Kibsgaard, Benchmarking Electrocatalyst Stability for Acidic Oxygen Evolution Reaction: The Crucial Role of Dissolved Ion Concentration, ACS Catal., 2023, 13(21), 14058–14069 CrossRef CAS.
- Y. Liu, X. Liang, H. Chen, R. Gao, L. Shi, L. Yang and X. Zou, Iridium-containing water-oxidation catalysts in acidic electrolyte, Chin. J. Catal., 2021, 42(7), 1054–1077 CrossRef CAS.
- J. Gao, Y. Liu, B. Liu and K.-W. Huang, Progress of Heterogeneous Iridium-Based Water Oxidation Catalysts, ACS Nano, 2022, 16(11), 17761–17777 CrossRef CAS.
- C. Wang, F. Yang and L. Feng, Recent advances in iridium-based catalysts with different dimensions for the acidic oxygen evolution reaction, Nanoscale Horiz., 2023, 8(9), 1174–1193 RSC.
- J. Song, C. Wei, Z.-F. Huang, C. Liu, L. Zeng, X. Wang and Z. J. Xu, A review on fundamentals for designing oxygen evolution electrocatalysts, Chem. Soc. Rev., 2020, 49(7), 2196–2214 RSC.
- J. Shan, Y. Zheng, B. Shi, K. Davey and S.-Z. Qiao, Regulating Electrocatalysts via Surface and Interface Engineering for Acidic Water Electrooxidation, ACS Energy Lett., 2019, 4(11), 2719–2730 CrossRef CAS.
- A. Grimaud, O. Diaz-Morales, B. Han, W. T. Hong, Y.-L. Lee, L. Giordano, K. A. Stoerzinger, M. T. M. Koper and Y. Shao-Horn, Activating lattice oxygen redox reactions in metal oxides to catalyse oxygen evolution, Nat. Chem., 2017, 9(5), 457–465 CrossRef CAS PubMed.
- N. Danilovic, R. Subbaraman, K.-C. Chang, S. H. Chang, Y. J. Kang, J. Snyder, A. P. Paulikas, D. Strmcnik, Y.-T. Kim, D. Myers, V. R. Stamenkovic and N. M. Markovic, Activity–Stability Trends for the Oxygen Evolution Reaction on Monometallic Oxides in Acidic Environments, J. Phys. Chem. Lett., 2014, 5(14), 2474–2478 CrossRef CAS PubMed.
- C. Mittelsteadt, E. Sorensen and Q. Jia, Ir Strangelove, or How to Learn to Stop Worrying and Love the PEM Water Electrolysis, Energy Fuels, 2023, 37(17), 12558–12569 CrossRef CAS.
- D. Galyamin, Á. Tolosana-Moranchel, M. Retuerto and S. Rojas, Unraveling the Most Relevant Features for the Design of Iridium Mixed Oxides with High Activity and Durability for the Oxygen Evolution Reaction in Acidic Media, JACS Au, 2023, 3(9), 2336–2355 CrossRef CAS.
- J. Gao, S. X. Tan, Y. Liu, B. Liu and K.-W. Huang, Revisiting the Activity Gap of Iridium Electrocatalysts for Acidic Water Oxidation, J. Phys. Chem. Lett., 2023, 14(28), 6494–6505 CrossRef CAS PubMed.
- J. Edgington and L. C. Seitz, Advancing the Rigor and Reproducibility of Electrocatalyst Stability Benchmarking and Intrinsic Material Degradation Analysis for Water Oxidation, ACS Catal., 2023, 13(5), 3379–3394 CrossRef CAS.
- S. Geiger, O. Kasian, M. Ledendecker, E. Pizzutilo, A. M. Mingers, W. T. Fu, O. Diaz-Morales, Z. Li, T. Oellers, L. Fruchter, A. Ludwig, K. J. J. Mayrhofer, M. T. M. Koper and S. Cherevko, The stability number as a metric for electrocatalyst stability benchmarking, Nat. Catal., 2018, 1(7), 508–515 CrossRef CAS.
- T. Weber, V. Vonk, D. Escalera-López, G. Abbondanza, A. Larsson, V. Koller, M. J. S. Abb, Z. Hegedüs, T. Bäcker, U. Lienert, G. S. Harlow, A. Stierle, S. Cherevko, E. Lundgren and H. Over, Operando Stability Studies of Ultrathin Single-Crystalline IrO2(110) Films under Acidic Oxygen Evolution Reaction Conditions, ACS Catal., 2021, 11(20), 12651–12660 CrossRef CAS.
- P. C. K. Vesborg and T. F. Jaramillo, Addressing the terawatt challenge: scalability in the supply of chemical elements for renewable energy, RSC Adv., 2012, 2(21), 7933–7947 RSC.
- Z. Lei, T. Wang, B. Zhao, W. Cai, Y. Liu, S. Jiao, Q. Li, R. Cao and M. Liu, Recent Progress in Electrocatalysts for Acidic Water Oxidation, Adv. Energy Mater., 2020, 10(23), 2000478 CrossRef CAS.
- P. Shirvanian and F. van Berkel, Novel components in Proton Exchange Membrane (PEM) Water Electrolyzers (PEMWE): status, challenges and future needs. A mini review, Electrochem. Commun., 2020, 114, 106704 CrossRef CAS.
- M. Bernt, A. Siebel and H. A. Gasteiger, Analysis of Voltage Losses in PEM Water Electrolyzers with Low Platinum Group Metal Loadings, J. Electrochem. Soc., 2018, 165(5), F305 CrossRef CAS.
- Z. Shi, J. Li, Y. Wang, S. Liu, J. Zhu, J. Yang, X. Wang, J. Ni, Z. Jiang, L. Zhang, Y. Wang, C. Liu, W. Xing and J. Ge, Customized reaction route for ruthenium oxide towards stabilized water oxidation in high-performance PEM electrolyzers, Nat. Commun., 2023, 14(1), 843 CrossRef CAS PubMed.
- Z. Lin, T. Wang and Q. Li, Designing active and stable Ir-based catalysts for the acidic oxygen evolution reaction, Ind. Chem. Mater., 2023, 1(3), 299–311 RSC.
- Y. Wang, R. Ma, Z. Shi, H. Wu, S. Hou, Y. Wang, C. Liu, J. Ge and W. Xing, Inverse doping IrOx/Ti with weakened Ir–O interaction toward stable and efficient acidic oxygen evolution, Chem, 2023, 9(10), 2931–2942 CAS.
- J. Kwon, S. Sun, S. Choi, K. Lee, S. Jo, K. Park, Y. K. Kim, H. B. Park, H. Y. Park, J. H. Jang, H. Han, U. Paik and T. Song, Tailored Electronic Structure of Ir in High Entropy Alloy for Highly Active and Durable Bifunctional Electrocatalyst for Water Splitting under an Acidic Environment, Adv. Mater., 2023, 35(26), 2300091 CrossRef CAS.
- A. Grimaud, W. T. Hong, Y. Shao-Horn and J. M. Tarascon, Anionic redox processes for electrochemical devices, Nat. Mater., 2016, 15(2), 121–126 CrossRef CAS.
- J. Shan, C. Ye, S. Chen, T. Sun, Y. Jiao, L. Liu, C. Zhu, L. Song, Y. Han, M. Jaroniec, Y. Zhu, Y. Zheng and S.-Z. Qiao, Short-Range Ordered Iridium Single Atoms Integrated into Cobalt Oxide Spinel Structure for Highly Efficient Electrocatalytic Water Oxidation, J. Am. Chem. Soc., 2021, 143(13), 5201–5211 CrossRef CAS.
- Z. Xia and S. Guo, Strain engineering of metal-based nanomaterials for energy electrocatalysis, Chem. Soc. Rev., 2019, 48(12), 3265–3278 RSC.
- S. Hao, H. Sheng, M. Liu, J. Huang, G. Zheng, F. Zhang, X. Liu, Z. Su, J. Hu, Y. Qian, L. Zhou, Y. He, B. Song, L. Lei, X. Zhang and S. Jin, Torsion strained iridium oxide for efficient acidic water oxidation in proton exchange membrane electrolyzers, Nat. Nanotechnol., 2021, 16(12), 1371–1377 CrossRef CAS PubMed.
- J. Shan, C. Guo, Y. Zhu, S. Chen, L. Song, M. Jaroniec, Y. Zheng and S.-Z. Qiao, Charge-Redistribution-Enhanced Nanocrystalline Ru@IrOx Electrocatalysts for Oxygen Evolution in Acidic Media, Chem, 2019, 5(2), 445–459 CAS.
- L. Wang, V. A. Saveleva, S. Zafeiratos, E. R. Savinova, P. Lettenmeier, P. Gazdzicki, A. S. Gago and K. A. Friedrich, Highly active anode electrocatalysts derived from electrochemical leaching of Ru from metallic Ir0.7Ru0.3 for proton exchange membrane electrolyzers, Nano Energy, 2017, 34, 385–391 CrossRef CAS.
- S. Siracusano, N. Hodnik, P. Jovanovic, F. Ruiz-Zepeda, M. Šala, V. Baglio and A. S. Aricò, New insights into the stability of a high performance nanostructured catalyst for sustainable water electrolysis, Nano Energy, 2017, 40, 618–632 CrossRef CAS.
- L. Zhang, Q. Fan, K. Li, S. Zhang and X. Ma, First-row transition metal oxide oxygen evolution electrocatalysts: regulation strategies and mechanistic understandings, Sustainable Energy Fuels, 2020, 4(11), 5417–5432 RSC.
- J. Feng, F. Lv, W. Zhang, P. Li, K. Wang, C. Yang, B. Wang, Y. Yang, J. Zhou, F. Lin, G.-C. Wang and S. Guo, Iridium-Based Multimetallic Porous Hollow Nanocrystals for Efficient Overall-Water-Splitting Catalysis, Adv. Mater., 2017, 29(47), 1703798 CrossRef.
- H. N. Nong, L. Gan, E. Willinger, D. Teschner and P. Strasser, IrOx core–shell nanocatalysts for cost- and energy-efficient electrochemical water splitting, Chem. Sci., 2014, 5(8), 2955–2963 RSC.
- H. N. Nong, T. Reier, H.-S. Oh, M. Gliech, P. Paciok, T. H. T. Vu, D. Teschner, M. Heggen, V. Petkov, R. Schlögl, T. Jones and P. Strasser, A unique oxygen ligand environment facilitates water oxidation in hole-doped IrNiOx core–shell electrocatalysts, Nat. Catal., 2018, 1(11), 841–851 CrossRef CAS.
- S. M. Alia, S. Shulda, C. Ngo, S. Pylypenko and B. S. Pivovar, Iridium-Based Nanowires as Highly Active, Oxygen Evolution Reaction Electrocatalysts, ACS Catal., 2018, 8(3), 2111–2120 CrossRef CAS.
- K.-R. Yeo, K.-S. Lee, H. Kim, J. Lee and S.-K. Kim, A highly active and stable 3D dandelion spore-structured self-supporting Ir-based electrocatalyst for proton exchange membrane water electrolysis fabricated using structural reconstruction, Energy Environ. Sci., 2022, 15(8), 3449–3461 RSC.
- Y. Li and S. Guo, Noble metal-based 1D and 2D electrocatalytic nanomaterials: recent progress, challenges and perspectives, Nano Today, 2019, 28, 100774 CrossRef CAS.
- H. Kim, T. Y. Yoo, M. S. Bootharaju, J. H. Kim, D. Y. Chung and T. Hyeon, Noble Metal-Based Multimetallic Nanoparticles for Electrocatalytic Applications, Adv. Sci., 2022, 9(1), 2104054 CrossRef CAS PubMed.
- J. Zhang, S. Liu, H. Wang, Q. Xia and X. Huang, Polypyrrole assisted synthesis of nanosized iridium oxide for oxygen evolution reaction in acidic medium, Int. J. Hydrogen Energy, 2020, 45(58), 33491–33499 CrossRef CAS.
- S. Park, M. Shviro, H. Hartmann, J. Mayer, M. Carmo and D. Stolten, Cation-Exchange Method Enables Uniform Iridium Oxide Nanospheres for Oxygen Evolution Reaction, ACS Appl. Nano Mater., 2022, 5(3), 4062–4071 CrossRef CAS.
- J. Lim, D. Park, S. S. Jeon, C.-W. Roh, J. Choi, D. Yoon, M. Park, H. Jung and H. Lee, Ultrathin IrO2 Nanoneedles for Electrochemical Water Oxidation, Adv. Funct. Mater., 2018, 28(4), 1704796 CrossRef.
- L. Zu, X. Qian, S. Zhao, Q. Liang, Y. E. Chen, M. Liu, B.-J. Su, K.-H. Wu, L. Qu, L. Duan, H. Zhan, J.-Y. Zhang, C. Li, W. Li, J. Y. Juang, J. Zhu, D. Li, A. Yu and D. Zhao, Self-Assembly of Ir-Based Nanosheets with Ordered Interlayer Space for Enhanced Electrocatalytic Water Oxidation, J. Am. Chem. Soc., 2022, 144(5), 2208–2217 CrossRef CAS.
- Z. Liu, J. Qi, H. Zeng, Y. Zeng, J. Wang, L. Gu, E. Hong, M. Yang, Q. Fu, J. Chen and C. Yang, Electrochemical Preparation of Iridium Hydroxide Nanosheets with Ordered Honeycomb Structures for the Oxygen Evolution Reaction in Acid, ACS Appl. Energy Mater., 2022, 5(6), 6869–6877 CrossRef CAS.
- J. Ahmed and Y. Mao, Ultrafine Iridium Oxide Nanorods Synthesized by Molten Salt Method toward Electrocatalytic Oxygen and Hydrogen Evolution Reactions, Electrochim. Acta, 2016, 212, 686–693 CrossRef CAS.
- S. Chatterjee, X. Peng, S. Intikhab, G. Zeng, N. N. Kariuki, D. J. Myers, N. Danilovic and J. Snyder, Nanoporous Iridium Nanosheets for Polymer Electrolyte Membrane Electrolysis, Adv. Energy Mater., 2021, 11(34), 2101438 CrossRef CAS.
- Y. J. Kim, A. Lim, J. M. Kim, D. Lim, K. H. Chae, E. N. Cho, H. J. Han, K. U. Jeon, M. Kim, G. H. Lee, G. R. Lee, H. S. Ahn, H. S. Park, H. Kim, J. Y. Kim and Y. S. Jung, Highly efficient oxygen evolution reaction via facile bubble transport realized by three-dimensionally stack-printed catalysts, Nat. Commun., 2020, 11(1), 4921 CrossRef CAS.
- M. Elmaalouf, M. Odziomek, S. Duran, M. Gayrard, M. Bahri, C. Tard, A. Zitolo, B. Lassalle-Kaiser, J.-Y. Piquemal, O. Ersen, C. Boissière, C. Sanchez, M. Giraud, M. Faustini and J. Peron, The origin of the high electrochemical activity of pseudo-amorphous iridium oxides, Nat. Commun., 2021, 12(1), 3935 CrossRef CAS.
- M. Faustini, M. Giraud, D. Jones, J. Rozière, M. Dupont, T. R. Porter, S. Nowak, M. Bahri, O. Ersen, C. Sanchez, C. Boissière, C. Tard and J. Peron, Hierarchically Structured Ultraporous Iridium-Based Materials: A Novel Catalyst
Architecture for Proton Exchange Membrane Water Electrolyzers, Adv. Energy Mater., 2019, 9(4), 1802136 CrossRef.
- S. Duran, A. Grimaud, M. Faustini and J. Peron, Porosity as a Morphology Marker to Probe the Degradation of IrO2 Anode Catalyst Layers in Proton Exchange Membrane Water Electrolyzers, Chem. Mater., 2023, 35(20), 8590–8598 CrossRef CAS.
- C. V. Pham, M. Bühler, J. Knöppel, M. Bierling, D. Seeberger, D. Escalera-López, K. J. J. Mayrhofer, S. Cherevko and S. Thiele, IrO2 coated TiO2 core–shell microparticles advance performance of low loading proton exchange membrane water electrolyzers, Appl. Catal., B, 2020, 269, 118762 CrossRef CAS.
- H. Lv, S. Wang, C. Hao, W. Zhou, J. Li, M. Xue and C. Zhang, Oxygen-Deficient Ti0.9Nb0.1O2−x as an Efficient Anodic Catalyst Support for PEM Water Electrolyzer, ChemCatChem, 2019, 11(10), 2511–2519 CrossRef CAS.
- Z. Shi, J. Li, J. Jiang, Y. Wang, X. Wang, Y. Li, L. Yang, Y. Chu, J. Bai, J. Yang, J. Ni, Y. Wang, L. Zhang, Z. Jiang, C. Liu, J. Ge and W. Xing, Enhanced Acidic Water Oxidation by Dynamic Migration of Oxygen Species at the Ir/Nb2O5−x Catalyst/Support Interfaces, Angew. Chem., Int. Ed., 2022, 61(52), e202212341 CrossRef CAS PubMed.
- T. Audichon, E. Mayousse, T. W. Napporn, C. Morais, C. Comminges and K. B. Kokoh, Elaboration and characterization of ruthenium nano-oxides for the oxygen evolution reaction in a Proton Exchange Membrane Water Electrolyzer supplied by a solar profile, Electrochim. Acta, 2014, 132, 284–291 CrossRef CAS.
- L. Chong, G. Gao, J. Wen, H. Li, H. Xu, Z. Green, J. D. Sugar, A. J. Kropf, W. Xu, X.-M. Lin, H. Xu, L.-W. Wang and D.-J. Liu, La- and Mn-doped cobalt spinel oxygen evolution catalyst for proton exchange membrane electrolysis, Science, 2023, 380(6645), 609–616 CrossRef CAS.
- M. Ledendecker, S. Geiger, K. Hengge, J. Lim, S. Cherevko, A. M. Mingers, D. Göhl, G. V. Fortunato, D. Jalalpoor, F. Schüth, C. Scheu and K. J. J. Mayrhofer, Towards maximized utilization of iridium for the acidic oxygen evolution reaction, Nano Res., 2019, 12(9), 2275–2280 CrossRef CAS.
- A. Rabis, P. Rodriguez and T. J. Schmidt, Electrocatalysis for Polymer Electrolyte Fuel Cells: Recent Achievements and Future Challenges, ACS Catal., 2012, 2(5), 864–890 CrossRef CAS.
- C. Hao, H. Lv, C. Mi, Y. Song and J. Ma, Investigation of Mesoporous Niobium-Doped TiO2 as an Oxygen Evolution Catalyst Support in an SPE Water Electrolyzer, ACS Sustainable Chem. Eng., 2016, 4(3), 746–756 CrossRef CAS.
- H. Lv, G. Zhang, C. Hao, C. Mi, W. Zhou, D. Yang, B. Li and C. Zhang, Activity of IrO2 supported on tantalum-doped TiO2 electrocatalyst for solid polymer electrolyte water electrolyzer, RSC Adv., 2017, 7(64), 40427–40436 RSC.
- G. Mohammadnezhad, M. M. Momeni and F. Nasiriani, Enhanced photoelectrochemical performance of tin oxide decorated tungsten oxide doped TiO2 nanotube by electrodeposition for water splitting, J. Electroanal. Chem., 2020, 876, 114505 CrossRef CAS.
-
L. J. Nuttall, A. P. Fickett and W. A. Titterington, Hydrogen Generation by Solid Polymer Electrolyte Water Electrolysis, in Hydrogen Energy: Part A, ed. T. N. Veziroğlu, Springer US, Boston, MA, 1975, pp. 441–455 Search PubMed.
- Z. Chen, L. Guo, L. Pan, T. Yan, Z. He, Y. Li, C. Shi, Z.-F. Huang, X. Zhang and J.-J. Zou, Advances in Oxygen Evolution Electrocatalysts for Proton Exchange Membrane Water Electrolyzers, Adv. Energy Mater., 2022, 12(14), 2103670 CrossRef CAS.
- M. Bühler, P. Holzapfel, D. McLaughlin and S. Thiele, From Catalyst Coated Membranes to Porous Transport Electrode Based Configurations in PEM Water Electrolyzers, J. Electrochem. Soc., 2019, 166(14), F1070 CrossRef.
- K. A. Mauritz and R. B. Moore, State of Understanding of Nafion, Chem. Rev., 2004, 104(10), 4535–4586 CrossRef CAS PubMed.
- A. Kusoglu and A. Z. Weber, New Insights into Perfluorinated Sulfonic-Acid Ionomers, Chem. Rev., 2017, 117(3), 987–1104 CrossRef CAS PubMed.
- J. Park, Z. Kang, G. Bender, M. Ulsh and S. A. Mauger, Roll-to-roll production of catalyst coated membranes for low-temperature electrolyzers, J. Power Sources, 2020, 479, 228819 CrossRef CAS.
- R. Maric, J. Roller and R. Neagu, Flame-Based Technologies and Reactive Spray Deposition Technology for Low-Temperature Solid Oxide Fuel Cells: Technical and Economic Aspects, J. Therm. Spray Technol., 2011, 20(4), 696–718 CrossRef.
- P. Holzapfel, M. Bühler, C. Van Pham, F. Hegge, T. Böhm, D. McLaughlin, M. Breitwieser and S. Thiele, Directly coated membrane electrode assemblies for proton exchange membrane water electrolysis, Electrochem. Commun., 2020, 110, 106640 CrossRef CAS.
- Y. Shi, Z. Lu, L. Guo and C. Yan, Fabrication of membrane electrode assemblies by direct spray catalyst on water swollen Nafion membrane for PEM water electrolysis, Int. J. Hydrogen Energy, 2017, 42(42), 26183–26191 CrossRef CAS.
- L. Sun, R. Ran, G. Wang and Z. Shao, Fabrication and performance test of a catalyst-coated membrane from direct spray deposition, Solid State Ionics, 2008, 179(21), 960–965 CrossRef CAS.
- A. Burdzik, M. Stähler, I. Friedrich, M. Carmo and D. Stolten, Homogeneity analysis of square meter-sized electrodes for PEM electrolysis and PEM fuel cells, J. Coat. Technol. Res., 2018, 15(6), 1423–1432 CrossRef CAS.
- S. Shahgaldi, I. Alaefour, G. Unsworth and X. Li, Development of a low temperature decal transfer method for the fabrication of proton exchange membrane fuel cells, Int. J. Hydrogen Energy, 2017, 42(16), 11813–11822 CrossRef CAS.
- J. E. Park, S. Kim, O.-H. Kim, C.-Y. Ahn, M.-J. Kim, S. Y. Kang, T. I. Jeon, J.-G. Shim, D. W. Lee, J. H. Lee, Y.-H. Cho and Y.-E. Sung, Ultra-low loading of IrO2 with an inverse-opal structure in a polymer-exchange membrane water electrolysis, Nano Energy, 2019, 58, 158–166 CrossRef CAS.
- P. Liu, D. Yang, B. Li, C. Zhang and P. Ming, Recent progress of catalyst ink for roll-to-roll manufacturing paired with slot die coating for proton exchange membrane fuel cells, Int. J. Hydrogen Energy, 2023, 48(51), 19666–19685 CrossRef CAS.
- T. Hrbek, P. Kúš, Y. Kosto, M. G. Rodríguez and I. Matolínová, Magnetron-sputtered thin-film catalyst with low-Ir–Ru content for water electrolysis: long-term stability and degradation analysis, J. Power Sources, 2023, 556, 232375 CrossRef CAS.
- R. Neagu, X. Zhang, R. Maric and J. M. Roller, Characterisation and Performance of SOFC Components made by Reactive Spray Deposition Technology, ECS Trans., 2009, 25(2), 2481 CrossRef CAS.
- H. Yu, N. Danilovic, Y. Wang, W. Willis, A. Poozhikunnath, L. Bonville, C. Capuano, K. Ayers and R. Maric, Nano-size IrOx catalyst of high activity and stability in PEM water electrolyzer with ultra-low iridium loading, Appl.
Catal., B, 2018, 239, 133–146 CrossRef CAS.
- C. Qiu, Z. Xu, F.-Y. Chen and H. Wang, Anode Engineering for Proton Exchange Membrane Water Electrolyzers, ACS Catal., 2024, 14(2), 921–954 CrossRef CAS.
- Z. Kang, G. Yang, J. Mo, Y. Li, S. Yu, D. A. Cullen, S. T. Retterer, T. J. Toops, G. Bender, B. S. Pivovar, J. B. Green and F.-Y. Zhang, Novel thin/tunable gas diffusion electrodes with ultra-low catalyst loading for hydrogen evolution reactions in proton exchange membrane electrolyzer cells, Nano Energy, 2018, 47, 434–441 CrossRef CAS.
- S. Choe, B.-S. Lee, M. K. Cho, H.-J. Kim, D. Henkensmeier, S. J. Yoo, J. Y. Kim, S. Y. Lee, H. S. Park and J. H. Jang, Electrodeposited IrO2/Ti electrodes as durable and cost-effective anodes in high-temperature polymer-membrane-electrolyte water electrolyzers, Appl. Catal., B, 2018, 226, 289–294 CrossRef CAS.
- M. Stähler, A. Stähler, F. Scheepers, M. Carmo and D. Stolten, A completely slot die coated membrane electrode assembly, Int. J. Hydrogen Energy, 2019, 44(14), 7053–7058 CrossRef.
- O. Kasian, J.-P. Grote, S. Geiger, S. Cherevko and K. J. J. Mayrhofer, The Common Intermediates of Oxygen Evolution and Dissolution Reactions during Water Electrolysis on Iridium, Angew. Chem., Int. Ed., 2018, 57(9), 2488–2491 CrossRef CAS PubMed.
- H. Yu, L. Bonville, J. Jankovic and R. Maric, Microscopic insights on the degradation of a PEM water electrolyzer with ultra-low catalyst loading, Appl. Catal., B, 2020, 260, 118194 CrossRef CAS.
- M. Milosevic, T. Böhm, A. Körner, M. Bierling, L. Winkelmann, K. Ehelebe, A. Hutzler, M. Suermann, S. Thiele and S. Cherevko, In Search of Lost Iridium: Quantification of Anode Catalyst Layer Dissolution in Proton Exchange Membrane Water Electrolyzers, ACS Energy Lett., 2023, 8(6), 2682–2688 CrossRef CAS.
- Z. Zeng, R. Ouimet, L. Bonville, A. Niedzwiecki, C. Capuano, K. Ayers, A. P. Soleymani, J. Jankovic, H. Yu, G. Mirshekari, R. Maric and S. Bliznakov, Degradation Mechanisms in Advanced MEAs for PEM Water Electrolyzers Fabricated by Reactive Spray Deposition Technology, J. Electrochem. Soc., 2022, 169(5), 054536 CrossRef CAS.
- C. Spöri, J. T. H. Kwan, A. Bonakdarpour, D. P. Wilkinson and P. Strasser, The Stability Challenges of Oxygen Evolving Catalysts: Towards a Common Fundamental Understanding and Mitigation of Catalyst Degradation, Angew. Chem., Int. Ed., 2017, 56(22), 5994–6021 CrossRef.
- N. Li, S. S. Araya, X. Cui and S. K. Kær, The effects of cationic impurities on the performance of proton exchange membrane water electrolyzer, J. Power Sources, 2020, 473, 228617 CrossRef CAS.
- S. Sun, Z. Shao, H. Yu, G. Li and B. Yi, Investigations on degradation of the long-term proton exchange membrane water electrolysis stack, J. Power Sources, 2014, 267, 515–520 CrossRef CAS.
- M. Zatoń, J. Rozière and D. J. Jones, Current understanding of chemical degradation mechanisms of perfluorosulfonic acid membranes and their mitigation strategies: a review, Sustainable Energy Fuels, 2017, 1(3), 409–438 RSC.
- L. Moriau, M. Smiljanić, A. Lončar and N. Hodnik, Supported Iridium-based Oxygen Evolution Reaction Electrocatalysts - Recent Developments, ChemCatChem, 2022, 14(20), e202200586 CrossRef CAS PubMed.
- Z. B. Wang, H. X. Hu, C. B. Liu and Y. G. Zheng, The effect of fluoride ions on the corrosion behavior of pure titanium in 0.05M sulfuric acid, Electrochim. Acta, 2014, 135, 526–535 CrossRef CAS.
- K. A. Lewinski, D. van der Vliet and S. M. Luopa, NSTF Advances for PEM Electrolysis - the Effect of Alloying on Activity of NSTF Electrolyzer Catalysts and Performance of NSTF Based PEM Electrolyzers, ECS Trans., 2015, 69(17), 893 CrossRef CAS.
- M. K. Debe, Tutorial on the Fundamental Characteristics and Practical Properties of Nanostructured Thin Film (NSTF) Catalysts, J. Electrochem. Soc., 2013, 160(6), F522 CrossRef CAS.
- A. Z. Tomić, I. Pivac and F. Barbir, A review of testing procedures for proton exchange membrane electrolyzer degradation, J. Power Sources, 2023, 557, 232569 CrossRef.
- P. Millet, A. Ranjbari, F. de Guglielmo, S. A. Grigoriev and F. Auprêtre, Cell failure mechanisms in PEM water electrolyzers, Int. J. Hydrogen Energy, 2012, 37(22), 17478–17487 CrossRef CAS.
- M. Chandesris, V. Médeau, N. Guillet, S. Chelghoum, D. Thoby and F. Fouda-Onana, Membrane degradation in PEM water electrolyzer: numerical modeling and experimental evidence of the influence of temperature and current density, Int. J. Hydrogen Energy, 2015, 40(3), 1353–1366 CrossRef CAS.
- V. Prabhakaran, C. G. Arges and V. Ramani, Investigation of polymer electrolyte membrane chemical degradation and degradation mitigation using in situ fluorescence spectroscopy, Proc. Natl. Acad. Sci. U. S. A., 2012, 109(4), 1029–1034 CrossRef CAS PubMed.
- S. H. Frensch, G. Serre, F. Fouda-Onana, H. C. Jensen, M. L. Christensen, S. S. Araya and S. K. Kær, Impact of iron and hydrogen peroxide on membrane degradation for polymer electrolyte membrane water electrolysis: computational and experimental investigation on fluoride emission, J. Power Sources, 2019, 420, 54–62 CrossRef CAS.
- F. Fouda-Onana, M. Chandesris, V. Médeau, S. Chelghoum, D. Thoby and N. Guillet, Investigation on the degradation of MEAs for PEM water electrolysers part I: effects of testing conditions on MEA performances and membrane properties, Int. J. Hydrogen Energy, 2016, 41(38), 16627–16636 CrossRef CAS.
- N. Li, S. S. Araya and S. K. Kær, Long-term contamination effect of iron ions on cell performance degradation of proton exchange membrane water electrolyser, J. Power Sources, 2019, 434, 226755 CrossRef CAS.
- X. Wang, L. Zhang, G. Li, G. Zhang, Z.-G. Shao and B. Yi, The influence of Ferric ion contamination on the solid polymer electrolyte water electrolysis performance, Electrochim. Acta, 2015, 158, 253–257 CrossRef CAS.
- J. P. Masson, R. Molina, E. Roth, G. Gaussens and F. Lemaire, Obtention and evaluation of polyethylene-based solid polymer electrolyte membranes for hydrogen production, Int. J. Hydrogen Energy, 1982, 7(2), 167–171 CrossRef CAS.
- S. Siracusano, S. Trocino, N. Briguglio, F. Pantò and A. S. Aricò, Analysis of performance degradation during steady-state and load-thermal cycles of proton exchange membrane water electrolysis cells, J. Power Sources, 2020, 468, 228390 CrossRef CAS.
- M. Danilczuk, A. J. Perkowski and S. Schlick, Ranking the Stability of Perfluorinated Membranes Used in Fuel Cells to Attack by Hydroxyl Radicals and the Effect of Ce(III): A Competitive Kinetics Approach Based on Spin Trapping ESR, Macromolecules, 2010, 43(7), 3352–3358 CrossRef CAS.
- C. Klose, P. Trinke, T. Böhm, B. Bensmann, S. Vierrath, R. Hanke-Rauschenbach and S. Thiele, Membrane Interlayer with Pt Recombination Particles for Reduction of the Anodic Hydrogen Content in PEM Water Electrolysis, J. Electrochem. Soc., 2018, 165(16), F1271 CrossRef CAS.
- C. L. Briant, Z. F. Wang and N. Chollocoop, Hydrogen embrittlement of commercial purity titanium, Corros. Sci., 2002, 44(8), 1875–1888 CrossRef CAS.
- J.-T. Wang, W.-W. Wang, C. Wang and Z.-Q. Mao, Corrosion behavior of three bipolar plate materials in simulated SPE water electrolysis environment, Int. J. Hydrogen Energy, 2012, 37(17), 12069–12073 CrossRef CAS.
- A. S. Gago, S. A. Ansar, B. Saruhan, U. Schulz, P. Lettenmeier, N. A. Cañas, P. Gazdzicki, T. Morawietz, R. Hiesgen, J. Arnold and K. A. Friedrich, Protective coatings on stainless steel bipolar plates for proton exchange membrane (PEM) electrolysers, J. Power Sources, 2016, 307, 815–825 CrossRef CAS.
- T. J. Toops, M. P. Brady, F.-Y. Zhang, H. M. Meyer, K. Ayers, A. Roemer and L. Dalton, Evaluation of nitrided titanium separator plates for proton exchange membrane electrolyzer cells, J. Power Sources, 2014, 272, 954–960 CrossRef CAS.
-
T. Bystron, M. Paidar, T. Klicpera, M. Schuster and K. Bouzek, Proton Exchange Membrane Water Electrolysers: Materials, Construction and Performance. in Electrochemical Methods for Hydrogen Production, ed. K. Scott, The Royal Society of Chemistry, 2019 Search PubMed.
- R.-T. Liu, Z.-L. Xu, F.-M. Li, F.-Y. Chen, J.-Y. Yu, Y. Yan, Y. Chen and B. Y. Xia, Recent advances in proton exchange membrane water electrolysis, Chem. Soc. Rev., 2023, 52(16), 5652–5683 RSC.
- X. Li, Y. Yao, Y. Tian, J. Jia, W. Ma, X. Yan and J. Liang, Recent advances in key components of proton exchange membrane water electrolysers, Mater. Chem. Front., 2024, 8(13), 2493–2510 RSC.
- T. T. Phan, S.-K. Kim, J. Islam, M.-J. Kim and J.-H. Lee, Degradation analysis of polymer electrolyte membrane water electrolyzer with different membrane thicknesses, Int. J. Hydrogen Energy, 2024, 49, 875–885 CrossRef CAS.
- S. Fahr, F. K. Engel, S. Rehfeldt, A. Peschel and H. Klein, Overview and evaluation of crossover phenomena and mitigation measures in proton exchange membrane (PEM) electrolysis, Int. J. Hydrogen Energy, 2024, 68, 705–721 CrossRef CAS.
- X.-Z. Yuan, S. Zhang, H. Wang, J. Wu, J. C. Sun, R. Hiesgen, K. A. Friedrich, M. Schulze and A. Haug, Degradation of a polymer exchange membrane fuel cell stack with Nafion® membranes of different thicknesses: Part I. In situ diagnosis, J. Power Sources, 2010, 195(22), 7594–7599 CrossRef CAS.
- J. Kink, M. Ise, B. Bensmann and R. Hanke-Rauschenbach, Modeling Mechanical Behavior of Membranes in Proton Exchange Membrane Water Electrolyzers, J. Electrochem. Soc., 2023, 170(5), 054507 CrossRef CAS.
- J. Dang, J. Zhang, X. Deng, S. Yang, B. Liu, X. Zhu, Y. Li, F. Yang and M. Ouyang, Hydrogen crossover measurement and durability assessment of high-pressure proton exchange membrane electrolyzer, J. Power Sources, 2023, 563, 232776 CrossRef CAS.
- Y. Li, H. Li, W. Liu and Q. Zhu, Optimization of membrane thickness for proton exchange membrane electrolyzer considering hydrogen production efficiency and hydrogen permeation phenomenon, Appl. Energy, 2024, 355, 122233 CrossRef CAS.
- H. Chen, Z. Liu, H. Zhou, X. Yang and W. Lin, Screening potential anodic chemistry in lieu of the oxygen evolution reaction in electrolysis systems: the road to practical application, Energy Environ. Sci., 2023, 16(12), 5771–5791 RSC.
- M. Maier, K. Smith, J. Dodwell, G. Hinds, P. R. Shearing and D. J. L. Brett, Mass transport in PEM water electrolysers: a review, Int. J. Hydrogen Energy, 2022, 47, 30–56 CrossRef CAS.
- T. Lickert, M. L. Kiermaier, K. Bromberger, J. Ghinaiya, S. Metz, A. Fallisch and T. Smolinka, On the influence of the anodic porous transport layer on PEM electrolysis performance at high current densities, Int. J. Hydrogen Energy, 2020, 45(11), 6047–6058 CrossRef CAS.
- X. Chen, Z. Yu, C. Yang, Y. Chen, C. Jin, Y. Ding, W. Li and Z. Wan, Performance investigation on a novel 3D wave flow channel design for PEMFC, Int. J. Hydrogen Energy, 2021, 46(19), 11127–11139 CrossRef CAS.
- J. Garcia-Navarro, M. Schulze and K. A. Friedrich, Understanding the Role of Water Flow and the Porous Transport Layer on the Performance of Proton Exchange Membrane Water Electrolyzers, ACS Sustainable Chem. Eng., 2019, 7(1), 1600–1610 CrossRef CAS.
-
T. Wu, B. Liu, F. Yuan and Q. Yang, Coalescence induced late departure of bubbles improves water electrolysis efficiency. arXiv, preprint, 2024, arXiv.2403.12064. 10.48550/arXiv.2403.12064.
- T. Krenz, O. Weiland, P. Trinke, L. Helmers, C. Eckert, B. Bensmann and R. Hanke-Rauschenbach, Temperature and Performance Inhomogeneities in PEM Electrolysis Stacks with Industrial Scale Cells, J. Electrochem. Soc., 2023, 170(4), 044508 CrossRef CAS.
- K. Wang, Y. Feng, F. Xiao, T. Zhang, Z. Wang, F. Ye and C. Xu, Operando analysis of through-plane interlayer temperatures in the PEM electrolyzer cell under various operating conditions, Appl. Energy, 2023, 348, 121588 CrossRef CAS.
- X. G. Li and M. Sabir, Review of bipolar plates in PEM fuel cells: flow-field designs, Int. J. Hydrogen Energy, 2005, 30(4), 359–371 CrossRef CAS.
- Q. S. Liu, F. C. Lan, C. J. Zeng, J. Q. Chen and J. F. Wang, A review of proton exchange membrane fuel cell’s bipolar plate design and fabrication process, J. Power Sources, 2022, 538, 231543 CrossRef CAS.
- Y. L. Wang, X. L. Liao, G. K. Liu, H. K. Xu, C. Guan, H. X. Wang, H. Li, W. He and Y. Z. Qin, Review of Flow Field Designs for Polymer Electrolyte Membrane Fuel Cells, Energies, 2023, 16(10), 4207 CrossRef CAS.
- H. Sun, X. Xu, H. Kim, W. Jung, W. Zhou and Z. Shao, Electrochemical Water Splitting: Bridging the Gaps Between Fundamental Research and Industrial Applications, Energy Environ. Mater., 2023, 6(5), e12441 CrossRef CAS.
- F. Zeng, C. Mebrahtu, L. Liao, A. K. Beine and R. Palkovits, Stability and deactivation of OER electrocatalysts: a review, J. Energy Chem., 2022, 69, 301–329 CrossRef CAS.
- X. Ping, Y. Liu, L. Zheng, Y. Song, L. Guo, S. Chen and Z. Wei, Locking the lattice oxygen in RuO2 to stabilize highly active Ru sites in acidic water oxidation, Nat. Commun., 2024, 15(1), 2501 CrossRef CAS PubMed.
- H. Teuku, I. Alshami, J. Goh, M. S. Masdar and K. S. Loh, Review on bipolar plates for low-temperature polymer electrolyte membrane water electrolyzer, Int. J. Energy Res., 2021, 45(15), 20583–20600 CrossRef CAS.
- N. Govindarajan, J. M. García-Lastra, E. J. Meijer and F. Calle-Vallejo, Does the breaking of adsorption-energy scaling relations guarantee enhanced electrocatalysis?, Curr. Opin. Electrochem., 2018, 8, 110–117 CrossRef CAS.
- Y.-T. Kim, P. P. Lopes, S.-A. Park, A. Y. Lee, J. Lim, H. Lee, S. Back, Y. Jung, N. Danilovic, V. Stamenkovic, J. Erlebacher, J. Snyder and N. M. Markovic, Balancing activity, stability and conductivity of nanoporous core-shell iridium/iridium oxide oxygen evolution catalysts, Nat. Commun., 2017, 8(1), 1449 CrossRef PubMed.
- K. Ayers, High efficiency PEM water electrolysis: enabled by advanced catalysts, membranes, and processes, Curr. Opin. Chem. Eng., 2021, 33, 100719 CrossRef.
- M. Möckl, M. F. Ernst, M. Kornherr, F. Allebrod, M. Bernt, J. Byrknes, C. Eickes, C. Gebauer, A. Moskovtseva and H. A. Gasteiger, Durability Testing of Low-Iridium PEM Water Electrolysis Membrane Electrode Assemblies, J. Electrochem. Soc., 2022, 169(6), 064505 CrossRef.
- N. D. Jaramillo-Rodríguez, A. Luxa and L. Jürgensen, Adaptation and application of a polarisation curve test protocol for a commercial pem electrolyser on cell and stack level, Acta Mech. Autom., 2023, 17(3), 395–404 Search PubMed.
- A. Weiß, A. Siebel, M. Bernt, T. H. Shen, V. Tileli and H. A. Gasteiger, Impact of Intermittent Operation on Lifetime and Performance of a PEM Water Electrolyzer, J. Electrochem. Soc., 2019, 166(8), F487 CrossRef.
- H. Kojima, K. Nagasawa, N. Todoroki, Y. Ito, T. Matsui and R. Nakajima, Influence of renewable energy power fluctuations on water electrolysis for green hydrogen production, Int. J. Hydrogen Energy, 2023, 48(12), 4572–4593 CrossRef CAS.
Footnote |
† These authors contributed equally. |
|
This journal is © The Royal Society of Chemistry 2025 |
Click here to see how this site uses Cookies. View our privacy policy here.