DOI:
10.1039/D4MH01227E
(Communication)
Mater. Horiz., 2025,
12, 258-266
Electrically switched asymmetric interfaces for liquid manipulation†
Received
6th September 2024
, Accepted 21st October 2024
First published on 29th October 2024
Abstract
External field driven fluid manipulation, in particular electric field, offers the advantages of real-time control and exceptional flexibility, rendering it highly promising for applications in microfluidic devices, liquid separation and energy catalysis. However, it is still challenging for controlled liquid transport and fine control of droplet splitting. Herein, we demonstrate a strategy to achieve direction-controlled liquid transport and fine droplet splitting on an anisotropic groove-microstructured electrode surface via an electrically switched asymmetric interface. The balance of asymmetric capillary force generated by microstructures and electro-capillary force is critical in determining directional liquid transport and fine droplet splitting. Asymmetric bubbles generated by liquid electrolysis form an asymmetric liquid–gas–solid interface and result in gradient liquid wetting behavior on the two neighboring electrode surfaces. The electric field further enhances the asymmetric wetting of a liquid droplet on the electrode surface, exhibiting electric field direction-dependent motion. Moreover, the groove-microstructured electrode surface can strengthen the liquid droplet anisotropic wetting and correspondingly refine the volume range of the splitting sub-droplet. Even unidirectional/bidirectional liquid droplet transport can be controlled in collaboration with the asymmetric groove-microstructure and electric field. Thus, this work provides a new route for liquid transport and droplet splitting, showing great potential in controllable separation, microreaction and microfluidic devices.
New concepts
Electric field driven fluid manipulation offers the advantages of real-time control and exceptional flexibility. Despite great progress in this field, achieving directional liquid transport and fine droplet splitting remains a challenge. Inspired by the directional fluid transport properties of a natural biological surface like rice leaves and desert lizards, herein, we develop a strategy to achieve direction-controlled liquid transport and fine droplet splitting via an electrically switched asymmetric interface on an anisotropic groove-microstructured electrode surface, resulting from electric field induced asymmetric interfaces and asymmetric microstructures of the electrode. Due to electrolysis on the electrode surface, when different volumes of gases are generated it promotes asymmetric interfacial transition from liquid–oil–solid to liquid–gas–solid, leading to asymmetric interfaces and gradient wetting behavior. Moreover, groove microstructures can regulate the gradient liquid wetting to effectively control liquid motion speed, and correspondingly refine the volume range of the splitting sub-droplet at the micro–nano level through reducing adhesion. Even unidirectional and bidirectional liquid droplet transport can be controlled in collaboration with the asymmetric capillary force generated by microstructure and electro-capillary force generated by an electric field. This innovative work has promising applications for designing functional interface materials in the fields of microfluidics, oil–water separation, and biological analysis.
|
1 Introduction
Fluid manipulation, e.g., transport, splitting and merging have critical applications in areas such as mass and heat transfer, fluid collection and separation, microfluidics and energy catalysis.1–8 The key for fluid manipulation is to create unbalanced driving forces toward a fluid on the material surface.9–11 In nature, many biological surfaces possess unique liquid transport properties. For example, liquid can undergo anisotropic wetting and movement on rice leaves due to its groove-like surface mocrostructures.12,13 The interconnected network of capillary channels among the scales on the integument of desert lizards forms a double capillary channel for unidirectional fluid transport.14,15 The results suggest that asymmetric micro-/nanoscale structures and composition play important roles in obtaining gradient wetting and dewetting for liquid transport. Inspired by this, researchers achieve gradient wettability by designing chemical components and micro-/nanoscale structures on the material surface, which are important means to achieve fluid manipulation.16–24 However, these passive directional wetting surfaces depend on the specific structural shape and surface chemistry, resulting in the difficulties in achieving direction-controlled liquid transport and manipulation. Another effective method of modulating a surface to achieve liquid transport and control is utilizing external fields, e.g., light,25–27 electric field,28,29 magnetic field30,31 and temperature.32,33 Among them, an electric field induced interface for fluid control, especially electrowetting, has the advantages of real-time response, high flexibility, in situ control, low power consumption and programmability compared with other methods.34–37 For instance, electrocapillary stripping of the thin film,38 electrically switched capillary adhesion interfaces,39 and electrically controlled liquid valves.33,40,41 Despite great progress in this field, achieving directional liquid transport and fine droplet splitting remains a challenge.
Herein, we develop a strategy to achieve an electrically switched asymmetric interface for liquid manipulation, i.e., direction-controlled liquid transport and fine droplet splitting, resulting from an electric field induced asymmetric interface and asymmetric microstructure of an electrode surface. Due to electrolysis on the electrode surface, different volumes of gases generated on the anode and cathode promote asymmetric interfacial transition from liquid–oil–solid to liquid–gas–solid, leading to an asymmetric interface and gradient wetting behavior of the corresponding electrodes. Moreover, the groove microstructures can enhance the gradient liquid wetting and reduce adhesion on the electrode surface, enabling effective control of liquid motion speed and droplet splitting volume at the micro–nano level. Most importantly, asymmetric groove microstructures can even control unidirectional/bidirectional liquid droplet transport with collaboration of an electric field. This work will contribute to droplet dispensing, chemical reactions and microfluidic chips, which also extends the potential fields of microassays and biochemical diagnosis.
2 Results and discussion
2.1 Electric field induced unidirectional liquid droplet motion
As reported, electric field induced conductive liquid wetting occurs on an electrode surface.28,42,43 When a liquid droplet (10 μL) is firstly placed across two electrodes, arranged in parallel with the interspace (D) on superhydrophobic substrate in oil, directional liquid droplet wetting occurs when a certain voltage is applied (Fig. 1a and Fig. S1, ESI†). Subsequently, the effect of voltage magnitude and direction on liquid droplet wetting was investigated (Fig. 1b and c). The liquid droplet stays stable on the electrode surface when D = 0.5 mm with a contact angle of θ0,oil = ∼140° on both sides at 0 V (the contact angle in air, θ0,air is ∼74°, Fig. S2, ESI†). Electrowetting occurs and the liquid droplet contact angle begins to decrease when the applied voltage reaches the critical electrowetting (EW) voltage of Uc1 = 1.6 V. When the applied voltage is increased to the critical electrolysis voltage of Uc2 = 2.6 V, liquid droplet electrolysis occurs accompanied by bubbles generated on the electrode surface and the liquid droplet contact angle significantly decreases. It is worth noting that the degree of electrolysis on the two sides of the droplet is not consistent, owing to the different volumes of oxygen and hydrogen produced on the anode and cathode, which results in the cathode surface becoming more hydrophilic than that of the anode and creates an asymmetric wetting tendency. When the applied voltage is increased to the critical transfer voltage of Uc3 = 4 V, the liquid droplet can be completely transferred to the negative electrode and the liquid droplet contact angle increases abruptly. However, when the electric field direction is reversed, the liquid droplet moves in the opposite direction.
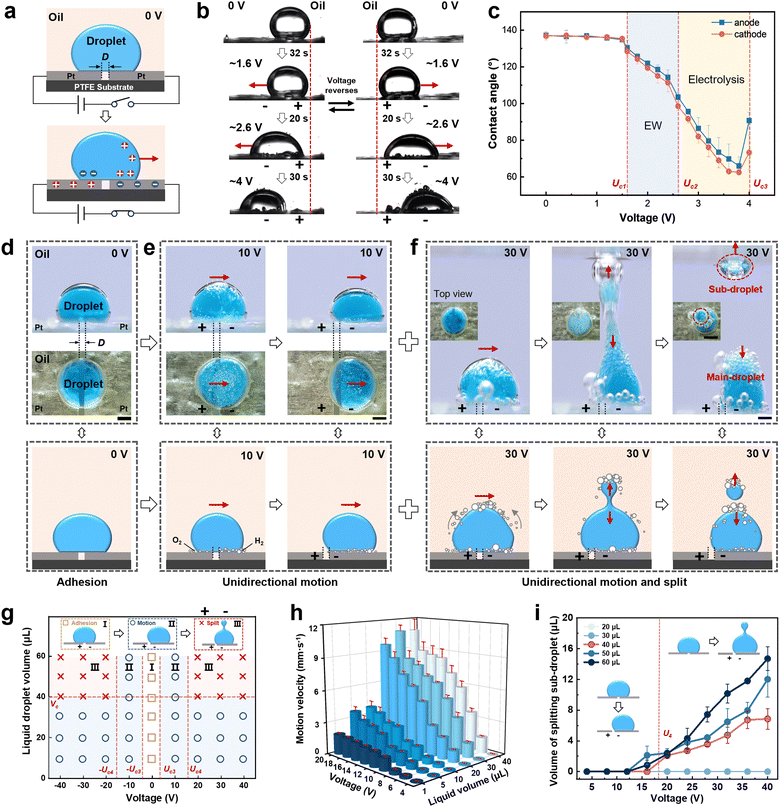 |
| Fig. 1 Electric field induced unidirectional liquid droplet motion. (a) Schematic electrowetting of a liquid droplet on an electrode surface. (b) Liquid droplet (10 μL, 0.1 M DBAE in 0.1 M PBS solution) wetting and motion behavior changes with increasing voltage from 0 V to 4 V. A liquid droplet is firstly placed across two neighbouring Pt electrode surfaces. When the applied voltage increases to the electrowetting threshold voltage of Uc1 = 1.6 V, liquid droplet electrowetting occurs and the contact angle begins to decrease. Liquid droplet electrolysis occurs and the contact angle decreases significantly at an electrolysis threshold voltage of Uc2 = 2.6 V, and liquid droplet is completely transferred to the negative electrode at a transfer threshold voltage of Uc3 = 4 V. The liquid droplet moves in the opposite direction as the electric field direction reverses. (c) Liquid droplet contact angle varies with increasing voltage in oil. (d)–(f) When the applied voltage increases to 10 V, the liquid droplet (40 μL) moves unidirectionally to the negative electrode side, and a splitting sub-droplet is produced at 30 V when the liquid droplet moves unidirectionally towards the negative electrode. Scale bars in (d)–(f) are 1 mm. The red arrows in the figures represent the direction of liquid droplet motion. (g) Three liquid droplet motion states change with applied voltage and liquid volume. (h) The liquid droplet motion velocity changes with voltage and volume. (i) The splitting sub-droplet volume varies with applied voltage and liquid volume. The results indicate that the electric field (direction and voltage) and initial liquid volume determine the movement direction and volume of the splitting sub-droplet. | |
However, a long electrolysis time at low voltage leads to slow movement of the liquid droplet. To solve this problem and achieve directional liquid droplet transport with a fast response, increasing the applied voltage facilitates the enhancement of the electrowetting and electrolysis effect. For example, when the applied voltage is increased to 10 V (Fig. 1d and e and Movie S1, ESI†), gas bubbles are instantaneously generated at the interface between the electrode surface and the liquid droplet to replace the oil phase rapidly. A liquid droplet wets the electrode surface quickly where the bubbles displace the oil and eventually the liquid droplet moves unidirectionally to the cathode side by electro-capillary force. This phenomenon is also certified on the wire electrode surface (Fig. S3, ESI†). Additionally, the wetting and dewetting of the liquid droplet on the electrode surface can be realized by adjusting the electrode shape and direction (Fig. S4, ESI†), which enables the reversible liquid droplet capture and release. Furthermore, upon increasing the voltage to 30 V, the liquid droplet is split along with the unidirectional movement, and a sub-droplet separates from the main droplet and is then produced (Fig. 1f).
In addition, the liquid droplet volume and voltage have a great influence on unidirectional motion and the splitting process, thus liquid droplet motion behavior was further investigated. As shown in Fig. 1g, liquid droplet motion can be divided into three regions according to the applied voltage and droplet volume. In region I, a liquid droplet can be adhered onto the electrode surface at the voltage of −Uc3 < U < Uc3 = 4 V. In region II, a liquid droplet can move in a unidirectional manner at a voltage of U ≤ −Uc3 or U ≥ Uc3. In region III, when the applied voltage is increased to the critical splitting voltage of Uc4 = 16 V or −Uc4 = −16 V and the liquid droplet volume reaches the critical splitting volume of Vc = 40 μL, droplet splitting occurs at the same time of directional movement. During the electric field induced liquid droplet movement, the maximum motion speed is ∼10.84 mm s−1 (Fig. 1h), and the splitting sub-droplet can be precisely controlled within the range of ∼2.0–14.7 μL (Fig. 1i). Accordingly, the direction and strength of electric field induced gradient wettability determine the direction and manner of the liquid droplet motion.
2.2 Groove-microstructure enhanced liquid droplet motion behavior
Gradient wettability of the electrode surface is the key factor affecting liquid droplet motion behavior. To thoroughly investigate the effect of microstructure surface on gradient wetting and further liquid transport and droplet splitting in detail,16 groove microstructured electrodes were designed and prepared by using laser etching (Fig. S5 and S6, ESI†). Taking a Pt electrode with a groove width (w) of 400 μm and a ridge width (d) of 100 μm for example (Fig. 2a), the liquid droplet contact angle on the groove-microstructured electrode surface with a different groove width was tested as shown in Fig. 2b. Liquid droplet wetting on the electrode surface is anisotropic, and varies with the groove width (Fig. 2c and Fig. S7, ESI†). Furthermore, different arrangement directions of the grooves affect liquid droplet transport velocity. Specifically, the transport velocity of the liquid droplet increases as it moves along the groove array (w = 400 μm) on the electrode surface, while the transport velocity decreases when it moves perpendicular to the groove array (Fig. 2d). The groove width on the electrode surface in the X direction further affects the liquid droplet transport velocity. The liquid droplet transport velocity enhances when the groove width of the microstructured electrode surface is in the range of 300–600 μm. In particular, when the groove width is 400 μm, the droplet transport velocity can be enhanced by ∼52.1% when a voltage of 12 V is applied (Fig. 2e), which is beneficial to lower energy consumption. However, the liquid droplet transport velocity is limited when the groove width of the microstructured electrode surface is less than 300 μm due to the reduced contact area. Besides, even though constructing microstructures enables precise liquid droplet manipulation with low losses, a small amount of liquid loss still exists.
 |
| Fig. 2 Groove-microstructure enhanced liquid droplet motion. (a) The prepared groove-microstructured Pt electrode with a groove width (w) of 400 μm, and ridge width (d) of 150 μm. (b) Schematic electric field induced liquid droplet motion on the groove-microstructured electrode surface. (c) The liquid droplet contact angle on the groove-microstructured electrode surface changes with different groove widths along the X and Y directions. (d) Liquid droplet motion velocity along the X and Y direction of the groove-microstructured electrode surface (w = 400 μm) changes with different voltage. (e) Liquid droplet motion velocity changes with groove width and voltage along the X direction. (f) The splitting sub-droplet volume on a flat or groove-microstructured electrode surface varies with different voltage and volume. (g) The maximum and minimum volume of splitting sub-droplet on a groove-microstructured electrode surface changes with different groove widths at the voltage of U > Uc4 (critical splitting voltage) and the droplet volume of V > Vc (critical splitting volume). The results indicate that the groove-microstructures can be used to enhance the liquid motion velocity and control the droplet splitting more finely. | |
Additionally, droplet splitting behavior on the groove-microstructured electrode was further investigated. The volume of a sub-droplet ranging from ∼0.1 to ∼0.9 μL on a groove-microstructured electrode surface is significantly smaller than that of the sub-droplets ranging from ∼2.0 to ∼14.7 μL formed on a flat electrode under identical conditions (Fig. 2f and Movie S2, ESI†). This feature provides the advantage of high-precision, on-demand droplet control and enables droplet segmentation with a large volume range. The maximal and minimal volume of sub-droplet produced by droplet splitting on the groove-microstructured electrode surface with other groove widths were also further investigated (Fig. 2g). The splitting sub-droplet volume can be varied within a small range of ∼0.05–0.80 μL by regulating the groove width. These results strongly demonstrate that the groove-microstructures can accelerate liquid motion and control droplet splitting more finely. From a practical application point of view, effective regulation of liquid droplet motion speed can control the microchemical reaction time and degree, while controlled droplet splitting is expected to be applied to the precise separation and delivery of drugs in the medical field.
2.3 Asymmetric groove-microstructure induced liquid droplet directional motion
In order to further improve the performance of gradient wetting on an electrode surface to facilitate directional liquid droplet transport, in the following we designed and fabricated asymmetric groove-microstructured electrodes to explore the gradient liquid wetting and motion behavior. Taking the combined asymmetric groove-microstructured electrodes with a groove width of 200 μm and 400 μm as an example, a liquid droplet can move on an asymmetric groove-microstructured electrode surface (Fig. 3a and b). When a 10 μL liquid droplet is placed across the asymmetric electrode surface with a groove width of w1 = 400 μm and w2 = 200 μm (Fig. 3c), the liquid droplet moves in the +X direction at −3.8 V, while the liquid droplet adheres when the electric field direction reverses. When the applied voltage is increased to 4 V, the liquid droplet can move regardless of the electric field direction, i.e., the liquid motion changes from unidirectional to bidirectional (Fig. 3d). If decreasing the groove width from w1 = 400 μm to w3 = 100 μm, the liquid droplet can move along the −X direction instead of moving along the +X direction, i.e., unidirectional liquid motion along the −X direction is realized (Fig. 3e). Subsequently, liquid droplet motion states on the asymmetric groove-microstructured electrode surface with different voltage were investigated in detail (Fig. 3f), and can be divided into four regions according to the applied voltage. In region I, a liquid droplet stays stably on an asymmetric electrode surface due to adhesion when the applied voltage is at the voltage of −Uc5 < U < Uc3 (where Uc5 is the critical motion voltage), i.e., −3.7 V < U < 4 V. In region II, a liquid droplet can move at the voltage of −4 to −3.7 V, while it adheres at the voltage of 3.7–4 V, i.e., liquid droplet behavior exhibits unidirectional motion on the groove-microstructured electrode surface. In region III, when the applied voltage increases to the threshold unidirectional/bidirectional motion voltage of Uc6 = 4.2 V, the liquid droplet adhesion/motion state can be controlled by modulating the groove at a voltage of −4.2 to −4 V, i.e., unidirectional and bidirectional liquid transport can be realized, and the critical groove width (wc) for determining liquid droplet motion is 300 μm (Fig. 3g). In region IV, a liquid droplet can move at the voltage of U > 4.2 V and U < −4.2 V, i.e., the liquid droplet behavior shows bidirectional motion. In addition, the maximum and minimum volume of splitting a sub-droplet from a groove-microstructured electrode surface with the groove width of w1 = 400 μm, w2 = 200 μm, and w3 = 100 μm were also calculated (Fig. 3h). Different groove widths have less effect on splitting a sub-droplet. The results indicate that an electric field and asymmetric structure collaboratively determine the direction of liquid motion, i.e., unidirectional/bidirectional liquid droplet transport, which is expected to be applied as a liquid diode.
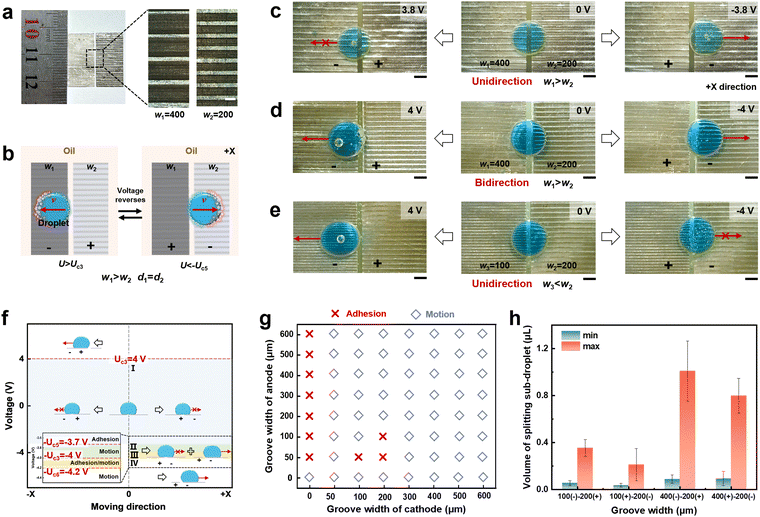 |
| Fig. 3 Asymmetric groove-microstructure induced liquid droplet directional motion. (a) Combined groove-microstructured electrode with different groove widths of w1 = 400 μm and w2 = 200 μm. (b) Schematic electric field induced liquid droplet motion on combined asymmetric groove-microstructured electrode surfaces. (c) When the droplet is placed across on electrode surface of w1 = 400 μm and w2 = 200 μm, the liquid droplet moves in the +X direction at the voltage of −3.8 V, while the droplet does not move when the electric field direction reverses. (d) Based on (c), when the voltage is increased to 4 V, the liquid droplet can move regardless of the electric field direction, i.e., bidirectional droplet motion can be realized. (e) Based on (d), by decreasing the groove width from w1 = 400 μm to w3 = 100 μm, a liquid droplet can move along the −X direction instead of moving along the +X direction, i.e., unidirectional liquid droplet motion along the −X direction is realized. The scale bars in (c)–(e) are 1 mm. (f) The four liquid droplet motion states on the groove-microstructured electrode surface vary with different voltage. In region I, the liquid droplet stays stably on the electrode surface due to adhesion at the voltage of −3.7 to 4 V. In region II, liquid droplet behavior exhibits unidirectional motion at the voltage of 3.7 to 4 V and −4 to −3.7 V. In region III, liquid droplet behavior shows unidirectional and bidirectional motion at the voltage of 4 to 4.2 V and −4.2 to −4 V. In region IV, liquid droplet behavior shows bidirectional motion at the voltage of U > 4.2 V and U < −4.2 V. (g) The groove width of an electrode can regulate the liquid droplet motion states along the +X direction at the voltage of −4.2 to −4 V, i.e., move or stop. (h) The maximum and minimum volume of splitting a sub-droplet on a combined groove-microstructured electrode surface changes with different widths of w1 = 100 μm, w2 = 200 μm and w3 = 400 μm. The results indicate that an electric field and asymmetric structure synergistically determine the direction of liquid droplet motion. Bidirectional liquid droplet motion occurs when the electric field driving force is dominant, while unidirectional liquid droplet motion occurs when the capillary force generated by asymmetric microstructures is dominant. | |
2.4 Mechanism of an electric field induced asymmetric interface for liquid droplet manipulation
To thoroughly understand liquid droplet motion behavior on different electrodes induced by an electric field, the mechanism of electric field induced liquid droplet wetting on an asymmetric electrode surface has been investigated and modeled. The force analysis of liquid droplet motion on a flat electrode surface was elucidated. Electro-capillary force FE1 leads to the directional liquid droplet movement on the electrode surface overcoming the static friction Fs1 (FE1 > Fs1) at the voltage of Uc3 < U < Uc4 (Fig. 4a). During the liquid wetting process, the initial contact angle of a liquid droplet on the anode and cathode electrodes are θ1 and θ2, which decreases to θ+ and θ− with the different volume of gas produced by electrolysis respectively, that is, θ+ < θ1, θ− < θ2, and θ− < θ+ (Fig. 4b1, b2 and Fig. S8, S9, ESI†). Similarly, underwater directional transport of an oil droplet on the electrode surface was also realized (Fig. S10, ESI†). The electric field induced wettability transition is crucial in achieving gradient force and correspondingly determining liquid droplet motion. During droplet splitting, the cohesion force of the sub-droplet conforms to Stefan's equation, which is expressed as follows:44 |  | (1) |
where Fco denotes the cohesive force of the sub-droplet, R0 is the radius of the contact area, C is a constant, η is the viscosity of the sub-droplet, V is the liquid droplet stretching speed and d is the droplet splitting distance.
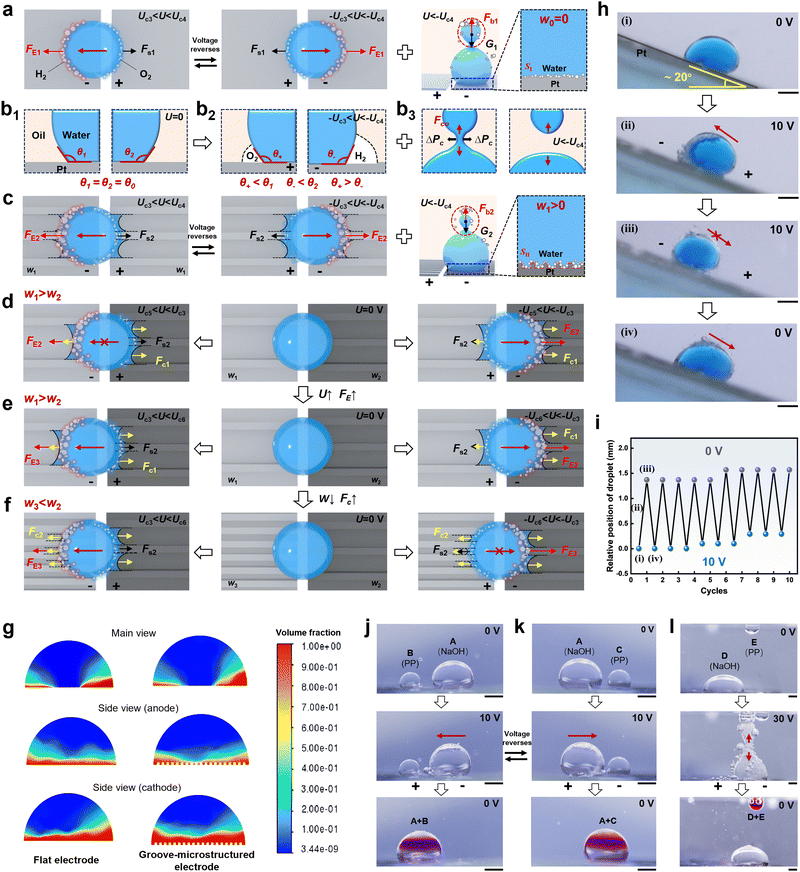 |
| Fig. 4 Mechanism of an electric field induced asymmetric interface for liquid droplet manipulation. (a) Schematic liquid droplet motion, splitting and contact interface on a symmetrical flat electrode surface. (b1)–(b3) Schematic interface transformation during electric field induced liquid droplet motion and splitting. (c) Schematic liquid droplet motion, splitting and contact interface on a symmetrical groove-microstructured electrode surface. (d)–(f) Schematic unidirectional and bidirectional liquid droplet transport on an asymmetric groove-microstructured electrode surface synergistically regulated by an electric field and microstructure. A liquid droplet exhibits adhesion on an asymmetric groove-microstructured electrode surface with Uc5 < U < Uc3 and w1 > w2 since the electro-capillary force FE is less than the resultant force of friction force Fs and capillary force Fc. When the applied voltage increases, FE increases to overcome the resultant force of Fs and Fc, thus the liquid droplet motion behavior changes from unidirectional motion to bidirectional motion. When the groove width decreases, Fc increases, resulting in FE failing to overcome the resultant force of Fs and Fc, and the liquid droplet behavior changes from bidirectional motion to unidirectional motion. (g) Main and side views of the simulated gas distribution on a flat and groove-microstructured electrode surface. (h) Reversible droplet climbs on an electrode surface with an inclination angle of 20°. (i) Cyclic test of reversible droplet climb. (j)–(l) Prototype demonstration of liquid droplet transport and split for chemical reaction. The scale bars are 1 mm. The results indicate the balance of competition between capillary force generated by asymmetric microstructures and asymmetric electro-capillary force generated by an electric field is critical to decide the motion state, i.e., direction and splitting, of the liquid droplet. | |
In the meantime, the connected part of the main droplet and the sub-droplet is subjected to an additional pressure (ΔP), which can be expressed by the Young–Laplace formula:
| 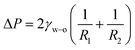 | (2) |
where
γw–o is the surface tension of the water–oil phase and
R1 and
R2 are the curvature radius of the curved liquid surface.
When the external pressure generated by buoyancy is less than the critical additional pressure (ΔPc) of a liquid droplet, i.e., ΔP < ΔPc, sub-droplet detachment occurs and the droplet completes splitting (Fig. 4b3). For a groove-microstructured electrode, the contact area of the liquid droplet with the electrode surface is larger than that of the liquid droplet with the flat electrode surface (SII > SI). The incorporation of groove microstructures creates more solid–gas–liquid interface, and thus generates a larger electro-capillary force (FE2 > FE1). That is, a gradient wetting interface is formed that accelerates the liquid droplet movement (Fig. 3c and Fig. S11–S13, liquid droplet wetting state changes from Cassie state to Wenzel state with increasing groove width, ESI†). The electro-capillary force of a liquid droplet on a flat and groove-microstructured electrode surface at a voltage of Uc3 = 4 V determined by calculation is 3.35 × 10−3 mN and 6.49 × 10−3 mN, suggesting that the incorporation of the microstructures facilitates the actuation of liquid droplet transport (Fig. S14, ESI†). In the process of droplet splitting at the voltage of U > Uc4, the sub-droplet is subjected to the bubble buoyancy force Fb and self-gravity G and tends to split. Once Fb > G, the sub-droplet keeps rising and splits at the neck. The groove-microstructures reduce the adhesion force between the liquid droplet and the electrode surface (Fig. S15, Fs2 < Fs1, ESI†), and guide the liquid droplet to move, thus resulting in a reduction in the volume of the generated sub-droplet. Furthermore, liquid droplet composition has an effect on liquid droplet motion behavior. The reduction in surface tension favors liquid droplet motion and splitting (Table S1, ESI†).
For an asymmetric groove-microstructured electrode surface, the competition between the driving force induced by an electric field and the capillary force generated by microstructures is critical in determining the direction of liquid droplet transport (Fig. 4d–f). When a liquid droplet is located on an asymmetric groove-microstructured electrode surface with Uc5 < U < Uc3 and w1 > w2, the electro-capillary force is less than the friction force and capillary force (Fc1) to drive liquid droplet motion, i.e., FE2 ≤ Fc1 + Fs2 (Fig. 4d). When the electric field is reversed, the electro-capillary force and capillary force act in the same direction and greater than the static friction force, i.e., Fc1 + FE2 > Fs2, resulting in the unidirectional liquid droplet movement. When the voltage is further increased within the range of Uc3 < U < Uc6, the electro-capillary force increases from FE2 to FE3 and overcomes the capillary force and static friction force, namely FE3 > Fc1 + Fs2, allowing the liquid droplet to move bidirectionally (Fig. 4e). If the groove width is decreased from w1 to w3 (w3 < wc) at the voltage of Uc3 < U < Uc6, the capillary force increases from Fc1 to Fc2, i.e., FE3 ≤ Fc2 + Fs2, resulting in unidirectional liquid droplet transport (Fig. 4f), which is consistent with the wetting behavior of liquid droplet in air, and the liquid droplet wets towards the electrode with the smaller groove width (Fig. S16, ESI†). Further computational fluid dynamics simulations were visualized for gas distribution on a flat and groove-microstructured electrode surface. By calculating the relative volume fraction of gas on both sides of the liquid droplet, it is demonstrated that the cathode produces more gas volume than the anode, and the gas distribution on the electrode surface exhibits asymmetric characteristics (Fig. 4g).
Based on electric field direction-dependent liquid droplet manipulation, prototype demonstrations of liquid droplet transport and splitting were designed. For instance, a droplet can climb upwards and slide downwards cyclically on the electrode with an inclined angle of 20° under varying voltage between 0 V and 10 V (Fig. 4h and i). In addition, the mixing and reacting experiments of liquid droplets were designed and conducted. First, liquid droplet A (NaOH solution) and liquid droplet B (phenolphthalein solution) are dropped on the electrode surface. When the electric field is applied to the electrode surface, liquid droplet A moves toward liquid droplet B, and the two droplets combine together, so that the combined droplet reacts and appears purple in color (Fig. 4j). Similarly, liquid droplet A moves towards liquid droplet C (phenolphthalein solution) and reacts by reversing the electric field (Fig. 4k). Moreover, liquid droplet D (NaOH solution) can also be split to combine with liquid droplet E (phenolphthalein solution) and react (Fig. 4l), indicating significant potential for application in the automation of chemical reactions. Therefore, electric field induced directional liquid transport and droplet splitting on an electrode surface underoil can be successfully achieved.
3 Conclusions
In summary, this work presents a novel approach to achieve direction-controlled liquid droplet transport and fine droplet splitting induced by an electrically switched asymmetric interface on an anisotropic groove-microstructured electrode surface. Bubbles with different volumes generated by liquid droplet electrolysis form asymmetric liquid–gas–solid interfaces and result in gradient liquid droplet wetting behavior, exhibiting electric field-dependent liquid droplet motion behavior. Moreover, a groove-microstructured electrode surface can strengthen the liquid droplet anisotropic wetting by enhancing the contact area, and correspondingly refine the volume range of the splitting sub-droplet through reducing adhesion. Finally, even unidirectional/bidirectional liquid droplet transport can be controlled in collaboration with the asymmetric capillary force generated by microstructures and electro-capillary force generated by an electric field. This work provides an effective approach for controllable liquid transport and fine droplet splitting in complex environments, with significant potential applications in microfluidics, oil–water separation, and biological analysis.
4 Experimental section
4.1 Materials
Pt electrodes were purchased from Wuhu Kezhao new materials Co., Ltd. Liquid paraffin was purchased from Xilong Chemical Co., Ltd. PFFE emulsion (60%) was purchased from Dongguan Zhanyang Polymer Materials Co., Ltd. Phosphate-buffered saline (PBS) and 2-(dibutylamino)ethanol (DBAE) were purchased from Macklin. Deionized water, ethanol, and acetone were used for reaction and cleaning.
4.2 Fabrication of superhydrophobic substrates
The glass sheet (40 × 10 × 1 mm) was firstly cleaned with ethanol and deionized water in turn, and dried at 60 °C for 30 min. PTFE emulsion was spin-coated onto the glass sheet at a speed of 1200 rpm, followed by curing at 350 °C for 30 min to obtain a superhydrophobic substrate in oil for use.
4.3 Fabrication of a groove-microstructured Pt electrode
Pt electrodes (20 × 10 × 0.1 mm) were firstly cleaned with ethanol and deionized water in turn, and dried at 60 °C for 30 min, then etched by laser to prepare groove-microstructures on Pt electrodes with different groove widths. The laser beam (30 kHz, 1060 nm) from a highly repetitive femtosecond laser system (Inngu Grace X 355-5) was used for fabrication. The laser power, scan pitch, focal spot size and speed were adjusted to 10 W, 50 μm, 0.05 mm and 500 mm s−1, respectively.
4.4 Instrument and characterization
The liquid droplet motion behavior on a Pt electrode surface was recorded with an SLR camera (Canon EOS 90D). Liquid droplet CAs were measured using a CA measurement instrument (OCA 20, Data-Physics) at ambient temperature. The liquid droplet adhesive forces were measured using a sensitive microelectromechanical balance system (Data-Physics DCAT 11, Germany). The detachment behavior of the liquid droplet on the electrode surface was recorded with a high-speed camera (Revealer 2F01M). The SEM images were characterized using a JEOL JSM-7500F SEM at 5 kV. The surface tension of the liquid droplet was measured by using an automatic surface tensiometer (JK 99M). Using a digital DC power supply (KORAD KA6003D), a voltage of −40 V to 40 V was applied between the electrodes, and the motion of a 0–60 μL liquid droplet containing 0.1 M DBAE in 0.1 M PBS solution was observed at various voltage levels.
Data availability
We confirm that the data supporting the findings of this study are available within the article and its ESI.†
Conflicts of interest
There are no conflicts to declare.
Acknowledgements
The authors are grateful for financial support from the National Natural Science Foundation of China (22272005, 22475011).
References
- H. Ko, J. Lee, Y. Kim, B. Lee, C. H. Jung, J. H. Choi, O. S. Kwon and K. Shin, Adv. Mater., 2014, 26, 2335–2340 CrossRef CAS PubMed.
- C. Dong, Y. Jia, J. Gao, T. Chen, P. I. Mak, M. I. Vai and R. P. Martins, Lab Chip, 2017, 17, 896–904 RSC.
- E. D. Wikramanayake and V. Bahadur, Int. J. Heat Mass Transfer, 2019, 140, 260–268 CrossRef.
- S. Zhang, M. Chi, J. Mo, T. Liu, Y. Liu, Q. Fu, J. Wang, B. Luo, Y. Qin, S. Wang and S. Nie, Nat. Commun., 2022, 13, 4168 CrossRef CAS PubMed.
- W. Li, L. Zhang, X. Ge, B. Xu, W. Zhang, L. Qu, C. Choi, J. Xu, A. Zhang, H. Lee and D. Weitz, Chem. Soc. Rev., 2018, 47, 5646–5683 RSC.
- S. Thakur, A. K. Dasmahapatra and D. Bandyopadhyay, Adv. Colloid Interface Sci., 2021, 294, 102453 CrossRef CAS PubMed.
- C. Zhang, Z. Xu, N. Han, Y. Tian, T. Kallio, C. Yu and L. Jiang, Sci. Adv., 2023, 9, eaddd6978 CrossRef PubMed.
- Z. Long, C. Yu, M. Cao, J. Ma and L. Jiang, Adv. Mater., 2024, 36, e2312179 CrossRef PubMed.
- K. Han and K. Yong, Adv. Funct. Mater., 2021, 31, 2101970 CrossRef CAS.
- L. Wang, K. Yin, Q. Deng, Q. Huang, J. He and J. A. Duan, Adv. Sci., 2022, 9, e2204891 CrossRef PubMed.
- K. Yin, L. Wang, Q. Deng, Q. Huang, J. Jiang, G. Li and J. He, Nano-Micro Lett., 2022, 14, 97 CrossRef CAS.
- D. Wu, J. Wang, S. Wu, Q. Chen, S. Zhao, H. Zhang, H. Sun and L. Jiang, Adv. Funct. Mater., 2011, 21, 2927–2932 CrossRef CAS.
- X. Yang, K. Zhuang, Y. Lu and X. Wang, ACS Nano, 2020, 15, 2589–2599 CrossRef PubMed.
- P. Comanns, G. Buchberger, A. Buchsbaum, R. Baumgartner, A. Kogler, S. Bauer and W. Baumgartner, J. R. Soc., Interface, 2015, 12, 20150415 CrossRef PubMed.
- G. Buchberger, R. Baumgartner, A. Kogler, T. Fritz, S. Bauer and W. Baumgartner, Sens. Actuators, A, 2018, 283, 375–385 CrossRef CAS.
- L. Hou, X. Liu, X. Ge, R. Hu, Z. Cui, N. Wang and Y. Zhao, Innovation, 2023, 4, 100508 CAS.
- D. Xie, Y. Sun, Y. Wu, K. Wang, G. Wang, F. Zang and G. Ding, Adv. Mater., 2023, 35, e2208645 CrossRef PubMed.
- C. Liu, Y. Sun, J. Huanng, Z. Guo and W. Liu, Adv. Colloid Interface Sci., 2021, 295, 102502 CrossRef CAS.
- G. Wang, F. Ma, L. Zhu, P. Zhu, L. Tang, H. Hu, L. Liu, S. Li, Z. Zeng, L. Wang and Q. Xue, Adv. Mater., 2024, e2311489, DOI:10.1002/adma.202311489.
- K. Luan, M. He, B. Xu, P. Wang, J. Zhou, B. Hu, L. Jiang and H. Liu, Adv. Funct. Mater., 2021, 31, 2010634 CrossRef CAS.
- Y. Zhang, M. Cao, Y. Peng, X. Jin, D. Tian, K. Liu and L. Jiang, Adv. Funct. Mater., 2017, 28, 1704220 CrossRef.
- Z. Cui, L. Xiao, Y. Li, Y. Zhang, G. Li, H. Bai, X. Tang, M. Zhou, J. Fang, L. Guo, S. Liu, C. Xiao and M. Cao, J. Mater. Chem. A, 2021, 9, 9719–9728 RSC.
- Y. Du, P. Li, Y. Wen and Z. Guan, Small, 2023, 19, e2207256 CrossRef.
- K. Shao, S. Jiang, Y. Hu, Y. Zhang, C. Li, Y. Zhang, J. Li, D. Wu and J. Chu, Adv. Funct. Mater., 2022, 32, 2205831 CrossRef CAS.
- Y. Yang, R. Chen, X. Zhu, D. Ye, Y. Yang, W. Li, D. Li, H. Li and Q. Liao, Adv. Sci., 2022, 9, 2201431 Search PubMed.
- G. Cheng, C. Kuan, K. Lou and Y. Ho, Adv. Mater., 2024, 2313935, DOI:10.1002/adma.202313935.
- S. Wang, R. Zhou, Y. Hou, M. Wang and X. Hou, Chin. Chem. Lett., 2022, 33, 3650–3656 CrossRef CAS.
- J. Tan, P. Tian, M. Sun, H. Wang, N. Sun, G. Chen, Y. Song, D. Jiang, H. Jiang and M. Xu, Nano Energy, 2022, 92, 106697 CrossRef CAS.
- J. Li, N. S. Ha, T. Liu, R. M. Dam and C. ‘Cj’ Kim, Nature, 2019, 572, 507–510 CrossRef CAS PubMed.
- X. Han, S. Tan, R. Jin, L. Jiang and L. Heng, J. Am. Chem. Soc., 2023, 145, 6420–6427 CrossRef CAS PubMed.
- S. Jiang, B. Li, J. Zhao, D. Wu, Y. Zhang, Z. Zhao, Y. Zhang, H. Yu, K. Shao, C. Zhang, R. Li, C. Chen, Z. Shen, J. Hu, B. Dong, L. Zhu, J. Li, L. Wang, J. Chu and Y. Hu, Nat. Commun., 2023, 14, 5455 CrossRef CAS.
- C. Liu, C. Lu, Z. Yuan, C. Lv and Y. Liu, Nat. Commun., 2022, 13, 3141 CrossRef CAS PubMed.
- A. Li, H. Li, S. Lyu, Z. Zhao, L. Xue, Z. Li, K. Li, M. Li, C. Sun and Y. Song, Nat. Commun., 2023, 14, 2646 CrossRef CAS PubMed.
- R. Tabassian, J. H. Oh, S. Kim, D. Kim, S. Ryu, S. M. Cho, N. Koratkar and I. K. Oh, Nat. Commun., 2016, 7, 13345 CrossRef CAS.
- Y. Jin, X. Liu, W. Xu, P. Sun, S. Huang, S. Yang, X. Yang, Q. Wang, R. H. W. Lam, R. Li and Z. Wang, ACS Nano, 2023, 17, 10713–10720 CrossRef CAS.
- X. Liu, D. Ma, H. Ye, Y. Hou, X. Bai, Y. Xing, X. Cheng, B. Lin and Y. Lu, TrAc, Trends Anal. Chem., 2023, 166, 117153 CrossRef CAS.
- J. Tan, Z. Fan, M. Zhou, T. Liu, S. Sun, G. Chen, Y. Song, Z. Wang and D. Jiang, Adv. Mater., 2024, 36, 2314346 CrossRef CAS PubMed.
- P. Li, X. Huang and Y. P. Zhao, Nat. Commun., 2023, 14, 6150 CrossRef CAS.
- H. Zheng, J. Li, Y. Zhou, C. Zhang, W. Xu, Y. Deng, J. Li, S. Feng, Z. Yi, X. Zhou, X. Ji, P. Shi and Z. Wang, Nat. Commun., 2022, 13, 4584 CrossRef CAS PubMed.
- Y. Yan, Z. Guo, X. Zhang, L. He, Y. Li, K. Liu, J. Cai, D. Tian and L. Jiang, Adv. Funct. Mater., 2018, 28, 1800775 CrossRef.
- A. Ainla, M. Hamedi, F. Guder and G. Whitesides, Adv. Mater., 2017, 29, 1702894 CrossRef PubMed.
- A. Staicu and F. Mugele, Phys. Rev. Lett., 2006, 97, 167801 CrossRef.
- W. Xu, Y. Jin, W. Li, Y. Song, S. Gao, B. Zhang, L. Wang, M. Cui, X. Yan and Z. Wang, Sci. Adv., 2022, 8, eade2085 CrossRef CAS PubMed.
- B. Bao, B. Su, S. Wang, S. Chen, L. Wu, Z. Jia, Y. Song and L. Jiang, Adv. Mater. Interfaces, 2014, 1, 1400080 CrossRef.
|
This journal is © The Royal Society of Chemistry 2025 |
Click here to see how this site uses Cookies. View our privacy policy here.