DOI:
10.1039/D4TA06520D
(Communication)
J. Mater. Chem. A, 2025,
13, 205-213
Efficient anti-icing/deicing via photothermal-wind synergistic effects on femtosecond laser-induced superhydrophobic graphene†
Received
13th September 2024
, Accepted 26th November 2024
First published on 28th November 2024
Abstract
Photothermal superhydrophobic surfaces have been demonstrated for anti-icing/deicing applications. However, preparing these materials using simple and environmentally friendly methods remains a challenge. Herein, a high-efficiency energy utilization strategy based on a photothermal-wind synergistic effect combined with superhydrophobicity has been proposed for anti-icing/deicing. Using one-step femtosecond laser direct writing technology, we modified a polyether ether ketone surface, which resulted in a superhydrophobic surface with photothermal effects. The optimized fabrication condition was laser treatment with velocity of 80 mm s−1 (LT-V80), which gave a surface possessing a high water contact angle (∼160.9°) and a low rolling angle (∼3°), and excellent self-cleaning properties were seen. Furthermore, LT-V80 showed high light absorptivity (∼94.6%), which caused the surface temperature to increase by 44.5 °C under 1.0 sun illumination. The addition of wind to the system resulted in a synergistic effect together with the photothermal and superhydrophobic properties, and caused a 87.1% reduction of the deicing time and a 220.3% increase in the icing time. This strategy also demonstrated good deicing efficiency in a cold outdoor environment. An efficient solar energy utilization strategy as demonstrated by LT-V80 indicates that efficient anti-icing/deicing is possible using simple, environmentally friendly, and low cost fabrication methods.
1. Introduction
Ice accumulation on human infrastructure causes serious safety hazards and economic losses in many areas, such as aircraft wings,1,2 power lines,3 photovoltaic panels4 and wind turbines.5,6 Many anti-icing and deicing strategies have been developed in an attempt to overcome this problem, including chemical methods, mechanical methods and electro-thermal methods.7–10 Nevertheless, these traditional methods are energy-intensive, inefficient and eco-unfriendly. In contrast, superhydrophobic surfaces are seen as a promising solution because of their ability to delay ice formation and promote natural shedding of ice.11–15 Unfortunately at temperatures below the freezing point of water, superhydrophobicity alone is sometimes not enough to remove ice and snow. Therefore, superhydrophobic surfaces are often combined with other active deicing methods for efficient anti-icing/deicing.16–20
The heat generated on surfaces from the photothermal effect can cause any attached ice to melt.21–24 Because superhydrophobic surfaces can remove ice water and delay freezing, photothermal superhydrophobic surfaces have great application potential in anti-icing and deicing.25–29 For example, Lee et al.30 developed an organic superhydrophobic surface with photothermal effects. Under near-infrared laser irradiation (808 nm, 0.3 W), the surface temperature increased from −20 °C to 30 °C. Zhang et al.31 fabricated a robust corrosive-resistant superhydrophobic surface with photothermal effects through solution reaction and spray methods. The durability of the surfaces was tested by soaking in corrosive solutions for 20 days or tape-peeling 90 times, after which the surfaces still showed superhydrophobicity. Li et al.3 prepared a low emissivity photothermal superhydrophobic coating, which achieved effective deicing of cables at −15 °C. These and other examples have shown that these photothermal superhydrophobic materials have great potential in improving anti-icing/deicing capabilities. However, problems remain such as complex material preparation processes, unstable material properties, being environmentally unfriendly.32–34 Polyether ether ketone (PEEK) has been widely used in aerospace, electrical equipment, automotive manufacturing and other fields due to its advantages of high temperature resistance, corrosion resistance, lightweight, and high mechanical strength. However, research on PEEK for anti-icing/deicing is rarely reported. Hence, it is promising to construct a photothermal superhydrophobic surface on PEEK for anti-icing/deicing using a simple and environmentally friendly femtosecond laser direct writing technology.
In this study, we propose an efficient solar energy utilization strategy based on a solar-powered thermal-wind synergistic effect combined with superhydrophobicity for anti-icing/deicing. Laser-induced graphene superhydrophobic micro/nanostructures were constructed on a PEEK surface using a one-step femtosecond laser direct writing technology. The optimal sample was found using laser treatment (LT) with a laser scanning velocity (V) of 80 mm s−1 (LT-V80) that achieved micro/nanostructured and graphitized surface composition of the PEEK surface. The results show that the laser treated sample boasts not merely self-cleaning capabilities and multiple liquid repellent properties, but also exhibits a remarkable average light absorptivity of 94.6%, enabling a substantial temperature rise of approximately 44.5 °C under 1.0 sun illumination. Furthermore, exceptional anti-icing/deicing properties were seen, which were synergistic with wind. The deicing time was reduced by 87.1% and the anti-icing time increased by 220.3% compared to untreated samples lacking wind assistance. Finally, we demonstrated the deicing of the treated sample in a cold outdoor environment.
2. Experimental section
2.1 Preparation
PEEK substrates (∼1.0 mm thick) were purchased from Ningbo Zheneng Precision Plastics Co., Ltd (Ningbo, China). In this experiment, a one-step femtosecond laser direct writing method was used to process PEEK substrates. The laser beam was generated by a commercial femtosecond fiber laser system (HR-Femto-IR-50-40B, Huaray, China) with a pulse width of 350 fs, a central wavelength of 1035 nm, and a repetition frequency of 400 kHz. A dual mirror current scanning system equipped with f-theta lenses (focusing length 125 mm) guided the laser beam to the surface of the PEEK substrate. The scanning spacing and power of the laser were 15 μm and 2.4 W, respectively. In addition, the samples obtained by femtosecond laser treatment at scanning velocities of 50 mm s−1, 80 mm s−1, and 200 mm s−1 were named LT-V50, LT-V80, and LT-V200, respectively. Unless otherwise specified, the sample used in this work was LT-V80, with a treated area of 25 mm × 25 mm.
2.2 Characterization
We characterized the micro/nanostructures of different samples using a field emission scanning electron microscope (MIRA3 LMU, TESCAN, Czech Republic). The elemental mappings and distributions were obtained through an energy-dispersive X-ray spectroscopy (TESCAN, Czech Republic). The 3D surface morphologies and cross-sectional profiles were acquired from an optical profilometer (WYKO NT9100, Veeco Metrology Inc, America). The Raman spectra of LT-V80 were obtained using a confocal Raman spectrometer (inVia, Renishaw, Britain). Infrared absorptivity spectra were collected using a Fourier transform infrared (FTIR) spectroscope (Nicolet iS50, Thermo Scientific, America) with a mercury–cadmium–telluride detector (Pike Technologies) and a gold integrating sphere. The FTIR spectra were acquired using a FTIR spectrometer (Nicolet iS50, Thermo Scientific, America). Furthermore, we studied the wettability and photothermal properties of different samples. The static water contact angles and dynamic rolling angles were measured through a contact angle measurement system (SinDin, China). High frame rate videos were recorded using a high-speed camera. The LT-V80 was heated through a high-temperature drying furnace (101-1BS, Shaoxing Supo Instrument Co., Ltd, China). External sunlight input was simulated by a solar simulator (CEL-HXF300-T3, Beijing Zhongjiao Jinyuan Technology Co., Ltd, China). The intensity of light was measured through an optical power meter (CEL-NP2000, Beijing Zhongjiao Jinyuan Technology Co., Ltd, China). The surface temperatures of different samples were observed using an infrared thermal imager (UTI320E, UNI-T, China).
2.3 Anti-icing/deicing experiment
The anti-icing/deicing performance test system was constructed using a solar simulator, refrigerator, electric fan and 0.3 mm thick glass sheets (Fig. S1†). The refrigerator consists of a power source, a radiator, a thermoelectric cooler, and an aluminum plate (200 × 200 × 4 mm). The light intensity can be controlled by adjusting the distance between the light outlet of the solar simulator and the sample. Similarly, the wind speed is adjusted by changing the distance between the electric fan and the sample and the gear of the electric fan. The light intensity was determined by an optical power meter, and the wind speed was measured by an anemometer. After the refrigerator was turned on for 10 minutes, the surface temperature of aluminum plate stabilized at about −15 °C. The steps of the deicing experiment are as follows. The two ends of the sample were placed on glass sheets, with a 0.3 mm air layer created between the bottom of the sample and the aluminum plate. Subsequently, the solar simulator and refrigerator were activated. After 10 minutes, an ice cube (5 × 5 × 5 mm) was placed on the sample surface while the electric fan was turned on. Immediately, the process of deicing under different conditions was recorded by a digital camera. Finally, the deicing time was recorded when there was no ice on the sample surface. The ambient temperature was 22 ± 2 °C and the relative humidity was 35 ± 5%. The steps of the anti-icing experiment are as follows. First, the sample was placed on the surface of aluminum plate. Then, the solar simulator and refrigerator were activated. After 3 minutes, 10 μL deionized water was dropped onto the sample surface, and the electric fan was turned on. Subsequently, the process of water droplet freezing under different conditions was recorded using a digital camera. Finally, the anti-icing time is recorded when the water droplet on the sample surface is completely frozen. The ambient temperature was 18 ± 2 °C and the relative humidity was 45 ± 5%.
3. Results and discussion
3.1 Preparation and anti-icing/deicing principle of the LT-V80
Femtosecond laser processing is a highly efficient and precise environmentally friendly technology.35–38 Its direct writing capability makes it easily controllable and it is widely used for the construction of micro/nanostructures on various material surfaces.39–43Fig. 1a shows a schematic of preparing laser treated surfaces using variable laser scanning velocities on a PEEK substrate using a one-step femtosecond laser direct writing technology. Femtosecond laser with a wavelength of 1035 nm and a repetition rate of 400 kHz deposits a large amount of photothermal energy on the PEEK surface through line-by-line scanning. Therefore, chemical bonds such as C–H, C–O–C, and C
O were disrupted, ultimately forming laser-induced graphene. The laser-treated PEEK surface exhibited porous micro/nanostructures, which gave it superhydrophobicity and excellent photothermal effect. The optimized velocity for the laser treatment was 80 mm s−1 (LT-V80), and this surface was tested for anti-icing/deicing. The anti-icing/deicing system using the photothermal-wind-superhydrophobicity synergistic effect is illustrated in Fig. 1b. On the one hand, solar energy can heat the surface of LT-V80. On the other hand, it can be converted into electrical energy through solar cells to drive an electric fan to generate wind. The wind accelerates the transfer of heat through thermal convection and promotes the rolling of ice and water off the surface. The superhydrophobic surface (LT-V80) facilitates the rolling of ice and water, and reduces the contact area between water and surface, thereby delaying nucleation and reducing heat loss.44,45 This efficient energy utilization strategy benefits from the photothermal-wind-superhydrophobicity synergistic effect, thus achieving efficient anti-icing/deicing.
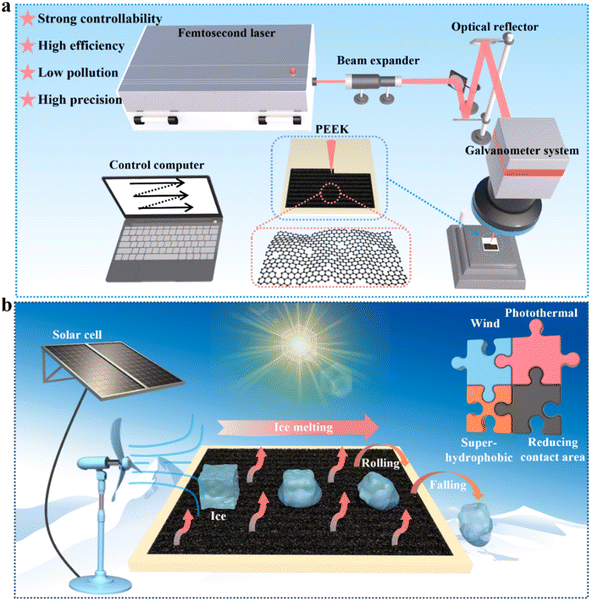 |
| Fig. 1 (a) Schematic of preparing LT-V80 using a one-step femtosecond laser direct writing technology. (b) Schematic diagram of anti-icing/deicing under the synergy of photothermal-wind-superhydrophobicity. | |
3.2 Surface topographies and chemical compositions
The surface structure and chemical properties of LT-V80 were characterized. SEM images of the LT-V80 surface at different magnifications are shown in Fig. 2a–c. Compared with the flat PEEK surface (Fig. S2a†), the LT-V80 possessed a periodic groove structure extending along the x-axis (Fig. 2a). By further magnification, the porous structure on the LT-V80 surface was observed, and the width of the grooves was approximately 16 μm (Fig. 2b). The LT-V80 surface exhibited nano pores and particles at high magnification (Fig. 2c). The sample surfaces obtained at different laser scanning velocities displayed different micro/nanostructures (Fig. S2b and c†). By observing Fig. 2d and S3,† it can be further demonstrated that samples at different laser scanning velocities have different 3D shapes and cross-sectional profiles, with the LT-V80 surface being the roughest. The Raman spectrum of LT-V80 showed three characteristic peaks (Fig. 2e), with the D peak, G peak, and 2D peak located at 1350 cm−1, 1588 cm−1, and 2700 cm−1, respectively. The D peak indicated the disordered graphene and graphene edge structures of LT-V80. The G peak was caused by the vibration of sp2 hybridized carbon atoms in the aromatic ring. The 2D peak indicated the existence of multi-layer graphene structure. These characteristic peaks demonstrated the generation of multilayer graphene structures with certain degrees of defects. In addition, the LT-V80 surface was composed of a large amount of carbon (98.65%) and a small amount of oxygen (1.35%) (Fig. 2f), and had a higher carbon content compared to LT-V50 and LT-V200 (Fig. S4†). Fig. 2g indicates that LT-V80 had a high infrared absorptivity of about 90%. As shown in Fig. 2h, the FTIR spectra of PEEK and LT-V80 surfaces were analyzed. A spectrum typically representing PEEK was seen including peaks at 767 cm−1 and 834 cm−1 from the Ar–C–H bending vibration and the peak located at 1217 cm−1 from C–O–C stretching vibrations. The peaks of 1486 cm−1 and 1594 cm−1 were caused by vibrations in the benzene plane, and the characteristic peak of 1647 cm−1 represented the aromatic C
O stretching vibration. However, after laser processing, all characteristic peaks of PEEK disappeared, indicating the complete graphitization of the surface.
 |
| Fig. 2 (a–c) SEM images of LT-V80 surface at different magnifications. (d) 3D surface morphology and cross-sectional profile images of LT-V80 surface. (e) Raman spectra of LT-V80 surface. (f) EDS spectrum and elemental mappings of LT-V80 surface. (g) Infrared absorptivity spectrum of PEEK and LT-V80 surfaces. (h) FTIR spectra of PEEK and LT-V80 surfaces. | |
3.3 Wettability characterization
Samples obtained under different laser processing parameters showed different surface structures and chemical compositions, resulting in varying wettability (Fig. 3a).46–49 The water droplet on the PEEK surface exhibited a hemispherical shape. LT-V50 surface shows superhydrophilicity, allowing the water droplet to fully spread out. In contrast, the water droplets on the surfaces of LT-V80 and LT-V200 exhibited ellipsoidal shapes, indicating that these surfaces have strong water repellency. Furthermore, the average water contact angles on the surfaces of PEEK, LT-V50, LT-V80, and LT-V200 were 80.7°, 4.6°, 160.9°, and 153.5°, respectively (Fig. 3b). Fig. S5† shows the dynamic wetting behavior of water droplets in contact with PEEK, LT-V50, LT-V80, and LT-V200 surfaces, with no residual water on the LT-V80 and LT-V200 surfaces. The LT-V80 surface was selected with the strongest water repellency for further wettability testing. The average contact angles of different droplets (tea, coffee, milk, seawater, rainwater) on the LT-V80 surface was greater than 150°, proving that LT-V80 possesses liquid repellency over a broad range of liquids (Fig. 3c). The process of a water droplet colliding with LT-V80 was captured by a high-speed camera (Video S1†), very similar to the bouncing behavior of a water droplet on a superhydrophobic surface simulated by COMSOL. This further demonstrated that the LT-V80 surface had excellent superhydrophobicity (Fig. 3d). Furthermore, Fig. 3e indicates the easy rolling (∼3°) of water droplets on the LT-V80 surface. Therefore, LT-V80 possessed good self-cleaning performance (Video S2†), in which water droplets could remove dust on the surface (Fig. 3f). Due to the crucial importance of durability in practical applications of superhydrophobic surfaces, we conducted a series of durability tests on the LT-V80 surface. After 180 minutes of high-temperature (150 °C) treatment, the LT-V80 surface still exhibited superhydrophobicity (Fig. 3g). The durability test of washing in water is shown in Fig. 3h. During the 60 washing tests, the average water contact angle of LT-V80 remained almost unchanged. As shown in Fig. 3i, LT-V80 surface displays good storage durability in atmospheric environments.
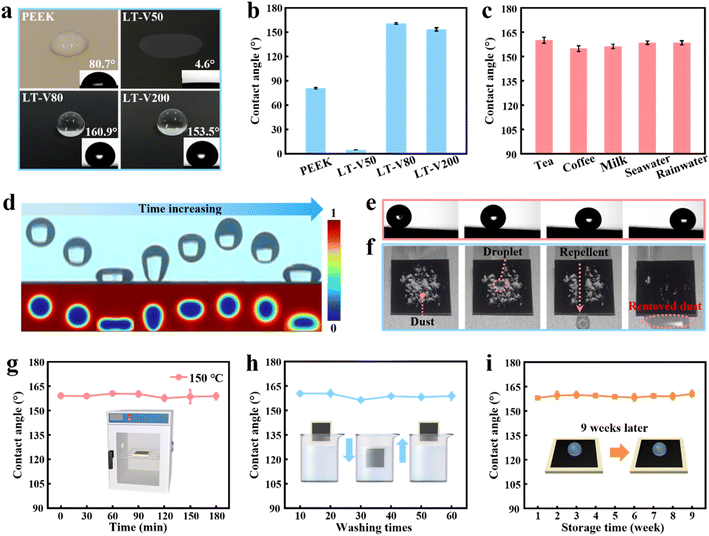 |
| Fig. 3 (a) Optical photos of water droplets placed on PEEK, LT-V50, LT-V80, and LT-V200, respectively. (b) The average water contact angle of PEEK, LT-V50, LT-V80, and LT-V200, respectively. (c) The average contact angle of tea, coffee, milk, seawater, and rainwater placed on LT-V80, respectively. (d) Photos of a water droplet (60 μL) impact on the LT-V80 surface and corresponding COMSOL simulation. (e) Pictures of a water droplet rolling (∼3°) on the LT-V80 surface. (f) The self-cleaning process of LT-V80 surface. (g) Thermal durability experiment of LT-V80. (h) Durability test of washing LT-V80 in water. (i) The average water contact angles of LT-V80 surface after being placed in air for 9 weeks. | |
3.4 Photothermal performance of the LT-V80 surface
The surface color of PEEK after laser processing changed from beige to black. PEEK and LT-V80 surfaces were irradiated by a red laser (Fig. 4a), and we observed reflection on the smooth PEEK surface and significant absorption on the rough LT-V80 surface. Fig. 4b exhibits the absorptivity of different samples in the range of 400 nm to 1700 nm. The average absorptivity of PEEK, LT-V50, LT-V80, and LT-V200 were 49.9%, 94.0%, 94.6%, and 93.1%, respectively. Compared with previously reported work, LT-V80 had a high light absorptivity (Fig. 4c).50–57 This might be because the unique micro/nanostructured surface allows light to undergo multiple reflections and absorptions on the LT-V80 surface (Fig. 4d). Light is converted into thermal energy through molecular thermal vibrations during this process. In order to further investigate the influence of surface structure on light absorptivity, we used COMSOL to calculate the absorptivity of plane and groove structures in the range of 400–1600 nm. The results indicated that the groove structure had an average light absorptivity of 94.8%, 28.7% higher than the light absorptivity of the plane structure (Fig. 4e). In addition, the photothermal conversion ability of LT-V80 was quantitatively studied by observing the surface temperature of the samples under different conditions (Fig. 4f). And for LT-V80, an excellent photothermal performance was readily seen. After one minute of illumination (1.0 sun), the surface temperature of LT-V80 was 26.1 °C higher than that of the PEEK surface (Fig. 4g). The surface temperatures of LT-V80 and PEEK were increased by 44.5 °C and 26.3 °C, respectively, within 240 s, because LT-V80 possessed a higher light absorptivity (Fig. 4h). Furthermore, the rapid temperature changes of LT-V80 were observed during xenon lamp on and off cycles and shows an efficient photothermal response. Fig. 4i shows the temperature is changed on the LT-V80 surface under different optical power densities. As the light intensity increases from 1.0 to 2.0 sun, the stable temperature of LT-V80 surface was increased from 66.0 °C to 103.3 °C. Stable photothermal performance is crucial for photothermal materials. Therefore, cyclic stability testing and long-term stability testing of the photothermal properties were conducted. The results showed that LT-V80 maintained a stable surface temperature after 20 cycles of light exposure (Fig. 4j) and 40 minutes of light exposure (Fig. S6†). Subsequently, the influence of wind speed on surface temperature was studied, as shown in Fig. 4k. The surface temperature of the refrigerator was −15 °C, and the ambient temperature was 20 °C, under 1.0 sun illumination. As the wind speed increased, the surface temperature of LT-V80 rose, reaching 17 °C at a wind speed of 1.8 m s−1 (Fig. 4l). However, when the refrigeration table was replaced with polyethylene foam, the sample surface temperature was decreased with the increase of wind speed (Fig. S7†). This was caused by the difference between the surface temperature of the sample and the ambient temperature.
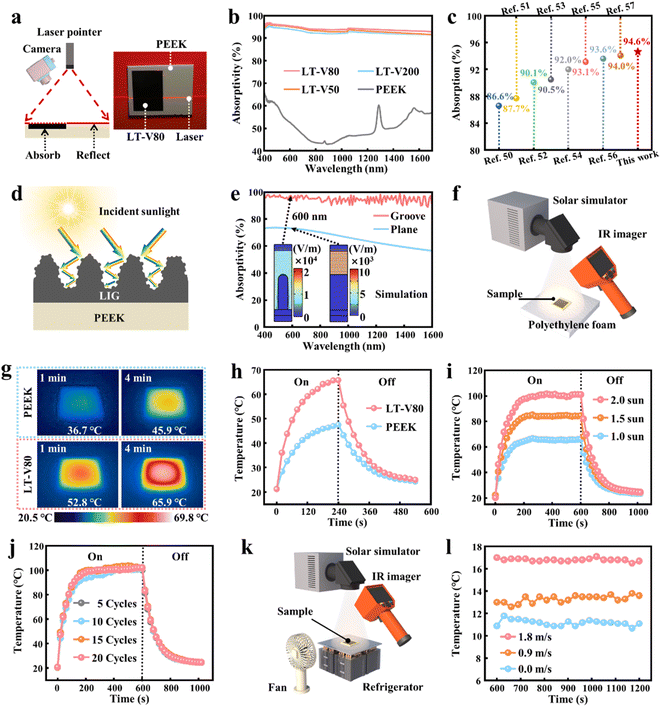 |
| Fig. 4 (a) Strong light irradiation on the surface of PEEK and LT-V80. (b) Light absorptivity of different samples. (c) Comparison of absorptivity between LT-V80 and previously reported photothermal conversion materials. (d) Schematic of light absorption on the LT-V80 surface. (e) COMSOL simulation of absorptivity and electric field distribution of groove and plane structures. (f) Schematic for testing the photothermal performance of PEEK and LT-V80 surfaces. (g) Infrared temperature images of PEEK and LT-V80 surfaces. (h) Surface temperature variation curves of PEEK and LT-V80 under 1.0 sun. (i) Temperature variation curves of LT-V80 surface. (j) Photothermal cycling durability test of LT-V80 under 2.0 sun. (k) Schematic of surface temperature testing for LT-V80 under the thermal-wind synergistic effect. (l) Surface temperature of LT-V80 at different wind speeds. | |
3.5 Anti-icing/deicing performance of the LT-V80 surface
As shown in Fig. 5a, an experimental scenario was constructed to investigate the anti-icing/deicing capabilities of the LT-V80 surface under the photothermal-wind synergistic effect.58Fig. 5d shows the deicing process under different conditions (Video S3†). The ice on the PEEK surface melted within 1729 s, compared to 1024 s on the LT-V80 due to the photothermal and superhydrophobic effects. On this basis, the ice water mixture on LT-V80 rolled off within 221 s, by adding wind (1.8 m s−1). The wind not only accelerated the ice melting, but also promoted the rolling of ice water mixtures. The results indicated that LT-V80 had the highest deicing efficiency under the photothermal-wind synergistic effect, and the LT-V80 surface remained dry. The deicing times of LT-V80 under different wind speeds and light intensities are shown in Fig. 5b. The LT-V80 surface had no residual water when the light intensity was greater than 1.0 sun and the wind speed was over 1.8 m s−1. In addition, the LT-V80 surface exhibited good deicing stability after 20 deicing cycles or 4 weeks in air (Fig. S8†). In comparison to selected previously published works, the deicing strategy of LT-V80 surface under the photothermal-wind synergistic effect had the following advantages: high deicing efficiency, no water residue, environmentally friendly, and efficient sample preparation (Fig. 5c).32–34 Subsequently, the freezing process of water droplets under different conditions was studied. From Fig. 5e, it can be concluded that LT-V80 has stronger anti-icing ability under the photothermal-wind synergistic effect (Video S4†). Possible reasons include the following: (1) the high surface temperature of LT-V80; (2) the small heat transfer area between the LT-V80 surface and water droplets (Fig. S9†); (3) wind slows down the freezing of water droplets through thermal convection. Further simulations were conducted using COMSOL to investigate the water freezing process at different substrate temperatures and water contact angles. After the same amount of time, the water droplet on the surface with a temperature of −8 °C and a water contact angle of 110° have the lowest degree of freezing, indicating that high substrate temperature and large substrate water contact angle are beneficial for delaying freezing of water droplets (Fig. 5g). In addition, deicing experiments were conducted in a cold outdoor environment (Fig. 5f) with an ambient temperature of −1 °C, a solar intensity of approximately 0.9 sun, and a fan speed of approximately 0.9 m s−1. Fig. 5h shows the process of outdoor deicing experiment (Video S5†). The LT-V80 surface achieved deicing within 933 s under the solar-powered thermal-wind synergistic effect. The PEEK surface achieved deicing within 1146 s, but there was still water residue.
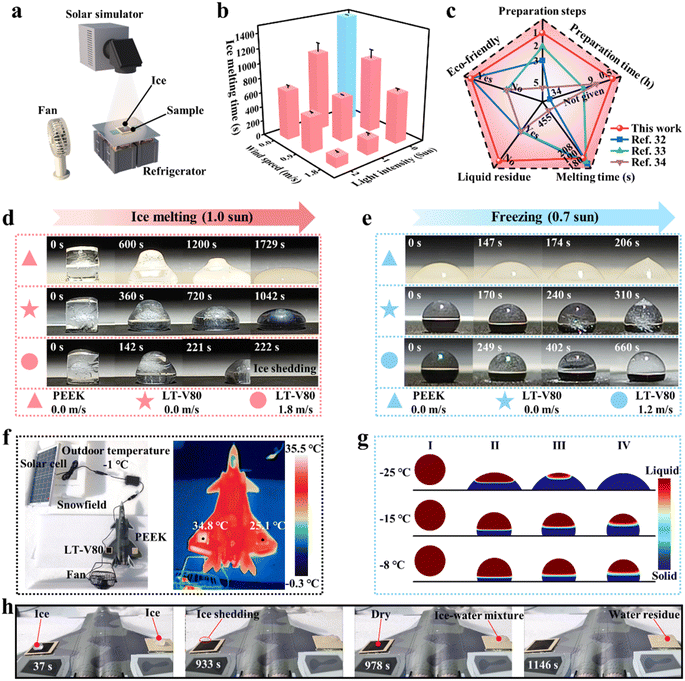 |
| Fig. 5 (a) Schematic diagram of anti-icing/deicing experiment. (b) The deicing times of LT-V80 surface under different conditions. (c) Comparison of comprehensive deicing ability between LT-V80 and previously reported photothermal deicing materials. (d) Optical images of the ice melting process. (e) Optical images of the icing process. (f) Optical photo and infrared temperature image of outdoor deicing experimental scene. (g) COMSOL simulation of icing process under different conditions. (h) Optical images of outdoor ice melting process. | |
4. Conclusion
In summary, we have prepared porous micro/nanostructured laser-induced graphene in one-step using femtosecond laser direct writing technology. A high-efficiency energy utilization strategy based on a photothermal-wind synergistic effect combined with superhydrophobicity has been proposed for anti-icing/deicing. The as-prepared sample has a high light absorptivity of 94.6%, and the surface possesses the water contact angle of 160.9°. In addition, wind accelerates ice melting and delays water freezing through thermal convection, and also the wind can cause water or ice water mixtures to roll off the surface. Compared to pristine PEEK without wind, the deicing time decreased by 87.1% and the anti-icing time increased by 220.3%. Benefiting from the above factors, the optimized sample, LT-V80, also exhibited efficient deicing capability in a cold outdoor environment. In general, the efficient photothermal-wind synergistic strategy based on photothermal superhydrophobic materials proposed in this study provides a new solution for the anti-icing/deicing.
Data availability
The data that support the findings of this study are available from the corresponding author upon reasonable request.
Author contributions
Xinghao Song: investigation, data curation, formal analysis, visualization, writing – original draft, editing. Kai Yin: resources, supervision, review, project administration, funding acquisition. Xun Li: review. Lingxiao Wang: data curation, formal analysis. Pengyu Yang: data curation, formal analysis. Jiaqing Pei: data curation, formal analysis. Yin Huang: review. Christopher J. Arnusch: review. Guoqiang Li: review, project administration, funding acquisition.
Conflicts of interest
The authors have no conflicts to disclose.
Acknowledgements
This research was supported by the National Key R&D Program of China (No. 2023YFB4604200), National Natural Science Foundation of China (grant no. 52475499, 52222513 and 52075557), Science and Technology Innovation Program of Hunan Province (grant no. 2021RC3011), Natural Science Foundation of Hunan Province (grant no. 2024JJ5426). The Central South University Innovation-Driven Research Programme (grant no. 2023CXQD019), the State Key Laboratory of Precision Manufacturing for Extreme Service Performance, Central South University (No. ZZYJKT2023-12), the State Key Laboratory of Intelligent Manufacturing Equipment and Technology, Huazhong University of Science and Technology (No. IMETKF2024018), Fundamental Research Funds for the Central Universities of Central South University (grant no. 2024ZZTS0736).
References
- M. J. Kreder, J. Alvarenga, P. Kim and J. Aizenberg, Nat. Rev. Mater., 2016, 1, 1–15 CrossRef.
- Y. Cao, W. Tan and Z. Wu, Aerosp. Sci. Technol., 2018, 75, 353–385 CrossRef.
- Y. Li, W. Ma, Y. S. Kwon, W. Li, S. Yao and B. Huang, Adv. Funct. Mater., 2022, 32, 2113297 CrossRef CAS.
- W. Tong, M. Han, C. Ma, Z. Wu, N. Wang, N. Du, T. Xiang and J. Zhu, ACS Appl. Mater. Interfaces, 2024, 16, 30611–31874 CrossRef PubMed.
- L. Gao and H. Hu, Proc. Natl. Acad. Sci. U. S. A., 2021, 118, e2111461118 CrossRef CAS PubMed.
- Z. Wang, Z. Zhao, G. Wen, Y. Zhu, J. Chen, X. Jing, S. Sun, L. Zhang, X. Liu and H. Chen, ACS Nano, 2023, 17, 13724–13733 CrossRef CAS PubMed.
- H. U. Sajid, A. Jalal, R. Kiran and A. Al-Rahim, Constr. Build. Mater., 2022, 319, 126062 CrossRef CAS.
- W. Huang, J. Huang, Z. Guo and W. Liu, Adv. Colloid Interface Sci., 2022, 304, 102658 CrossRef CAS PubMed.
- L. Pan, Z. Liu, O. kızıltaş, L. Zhong, X. Pang, F. Wang, Y. Zhu, W. Ma and Y. Lv, Compos. Sci. Technol., 2020, 192, 108117 CrossRef CAS.
- H. Ba, L. Truong-Phuoc, T. Romero, C. Sutter, J. Nhut, G. Schlatter, G. Giambastiani and C. Pham-Huu, Carbon, 2021, 182, 655–668 CrossRef CAS.
- L. Wang, Q. Gong, S. Zhan, L. Jiang and Y. Zheng, Adv. Mater., 2016, 28, 7729–7735 CrossRef CAS PubMed.
- J. Wei, B. Li, N. Tian, J. Zhang, W. Liang and J. Zhang, Adv. Funct. Mater., 2022, 32, 2206014 CrossRef CAS.
- S. Xuan, H. Yin, G. Li, Z. Zhang, Y. Jiao, Z. Liao, J. Li, S. Liu, Y. Wang, C. Tang, W. Wu, G. Li and K. Yin, ACS Nano, 2023, 17, 21749–21760 CrossRef PubMed.
- L. Wang, D. Li, G. Jiang, X. Hu, R. Peng, Z. Song, H. Zhang, P. Fan and M. Zhong, ACS Nano, 2024, 18, 12489–12502 CrossRef CAS PubMed.
- L. Li, J. Wei, J. Zhang, B. Li, Y. Yang and J. Zhang, Sci. Adv., 2023, 9, eadj1554 CrossRef PubMed.
- F. Chu, Z. Hu, Y. Feng, N. Lai, X. Wu and R. Wang, Adv. Mater., 2024, 36, 2402897 CrossRef CAS PubMed.
- Z. Zhao, Y. Wang, Z. Wang, X. Cui, G. Liu, Y. Zhang, Y. Zhu, J. Chen, S. Sun, K. Zhang, X. Liu and H. Chen, Small, 2024, 20, 2311435 CrossRef CAS PubMed.
- Y. Guo, H. Zhao, C. Zhang and G. Zhao, Chem. Eng. J., 2024, 497, 154383 CrossRef CAS.
- J. Liu, C. He, B. Liu, Z. Wang, S. Zhao, Z. Lu, Y. Zhang, Z. Tang, X. Gao and X. Aday, Chem. Eng. J., 2024, 489, 151338 CrossRef CAS.
- X. Su, H. Li, X. Lai, Z. Yang, Z. Chen, W. Wu and X. Zeng, J. Mater. Chem. A, 2018, 6, 16910–16919 RSC.
- L. Zhang, B. Luo, K. Fu, C. Gao, X. Han, M. Zhou, T. Zhang, L. Zhong, Y. Hou and Y. Zheng, Adv. Sci., 2023, 10, 2304187 CrossRef CAS PubMed.
- L. Wang, K. Yin, Q. Deng, Q. Huang and C. J. Arnusch, Carbon, 2024, 219, 118824 CrossRef CAS.
- Y. Wu, J. Ma, S. Zang, W. Zhou, Z. Wang, M. Han, S. M. Osman, C. Wang, Y. Yamauchi, J. You, M. An, L. Wang and Z. Yuan, Chem. Eng. J., 2023, 472, 144600 CrossRef CAS.
- J. Yu, J. Yun, S. Zang, M. Han, X. Sun, Z. Wang, Y. Zhou, A. Khan, M. An, J. Li, S. Chen, Y. Yamauchi and Z. Yuan, Nano Energy, 2023, 117, 108847 CrossRef CAS.
- M. Hou, Z. Jiang, W. Sun, Z. Chen, F. Chu and N. Lai, Adv. Mater., 2024, 36, 2310312 CrossRef CAS PubMed.
- S. Wu, Y. Du, Y. Alsaid, D. Wu, M. Hua, Y. Yan, B. Yao, Y. Ma, X. Zhu and X. He, Proc. Natl. Acad. Sci. U. S. A., 2020, 117, 11240–11246 CrossRef CAS PubMed.
- Y. Zhao, C. Yan, T. Hou, H. Dou and H. Shen, ACS Appl. Mater. Interfaces, 2022, 14, 26077–26087 CrossRef CAS PubMed.
- Y. Wu, L. Dong, X. Shu, Y. Yang, P. Feng and Q. Ran, Chem. Eng. J., 2023, 469, 143924 CrossRef CAS.
- F. Zhang, H. Yan and M. Chen, Small, 2024, 20, 2312226 CrossRef CAS PubMed.
- S. Lee, M. J. Bae, E. J. Seo, J. Lyu, S. Lee, Y. Jung, H. Jung, Y. I. Park, J. C. Kim and J. Jeong, Prog. Org. Coat., 2024, 189, 108298 CrossRef CAS.
- L. Zhang, C. Gao, L. Zhong, L. Zhu, H. Chen, Y. Hou and Y. Zheng, Chem. Eng. J., 2022, 446, 137461 CrossRef CAS.
- H. Xie, J. Wei, S. Duan, Q. Zhu, Y. Yang, K. Chen, J. Zhang, L. Li and J. Zhang, Chem. Eng. J., 2022, 428, 132585 CrossRef CAS.
- N. Li, Y. Zhang, H. Zhi, J. Tang, Y. Shao, L. Yang, T. Sun, H. Liu and G. Xue, Chem. Eng. J., 2022, 429, 132183 CrossRef CAS.
- S. Zhang, F. Zhang, Z. Zhang, G. Li, H. Fu, J. Huang, Y. Wang, Z. Lei, X. Qian and Y. Lai, Chem. Eng. J., 2022, 450, 138328 CrossRef CAS.
- Y. Liu, K. Yin, P. Yang, D. Yan and C. J. Arnusch, Appl. Phys. Lett., 2024, 125, 071602 CrossRef CAS.
- P. Pou, J. d. Val, A. Riveiro, R. Comesaña, F. Arias-González, F. Lusquiños, M. Bountinguiza, F. Quintero and J. Pou, Appl. Surf. Sci., 2019, 475, 896–905 CrossRef CAS.
- P. Yang, K. Yin, X. Li, X. Song, L. Wang, J. Pei, T. Wu, Y. Huang, S. U. Awan and A. S. G. Khalil, Appl. Phys. Lett., 2024, 125, 051602 CrossRef CAS.
- Q. Huang, Y. He, K. Yin, H. Zhang, P. Yang, G. Li, S. U. Awan and A. S. G. Khalil, Appl. Phys. Lett., 2024, 125, 031601 CrossRef CAS.
- T. Wu, K. Yin, J. Pei, Y. He, Ji-An. Duan and C. J. Arnusch, Appl. Phys. Lett., 2024, 124, 161602 CrossRef CAS.
- P. Yang, K. Yin, X. Song, L. Wang, Q. Deng, J. Pei, Y. He and C. J. Arnusch, Nano Lett., 2024, 24, 3133–3141 CrossRef CAS PubMed.
- Y. He, L. Wang, T. Wu, Z. Wu, Y. Chen and K. Yin, Nanoscale, 2022, 14, 9392–9400 RSC.
- L. Wang, K. Yin, Q. Deng, Q. Huang, J. He and Ji-An. Duan, Adv. Sci., 2022, 9, 2204891 CrossRef CAS PubMed.
- Y. He, K. Yin, L. Wang, T. Wu, Y. Chen and C. J. Arnusch, Appl. Phys. Lett., 2024, 124, 171601 CrossRef CAS.
- S. Zhang, J. Huang, Y. Cheng, H. Yang, Z. Chen and Y. Lai, Small, 2017, 13, 1701867 CrossRef PubMed.
- Q. Li and Z. Guo, J. Mater. Chem. A, 2018, 6, 13549–13581 RSC.
- H. Zhong, Z. Zhu, J. Lin, C. F. Cheung, V. L. Lu, F. Yan, C. Chan and G. Li, ACS Nano, 2020, 14, 6213–6221 CrossRef CAS PubMed.
- T. Darmanin and F. Guittard, Prog. Polym. Sci., 2014, 39, 656–682 CrossRef CAS.
- Z. Jiao, H. Zhou, X. Han, D. Han and Y. Zhang, J. Colloid Interface Sci., 2023, 629, 582–592 CrossRef CAS PubMed.
- D. Yan, K. Yin, Y. He, Y. Liu, L. Wang, Q. Deng, J. He, S. U. Awan and A. S. G. Khalil, Nanoscale, 2024, 16, 7341–7362 RSC.
- J. Dong, Y. Feng, K. Lin, B. Zhou, F. Su and C. Liu, Adv. Funct. Mater., 2024, 34, 2310774 CrossRef CAS.
- S. Lu, F. Liu, P. Qiu, M. Qiao, Y. Li, Z. Cheng, N. Xue, X. Hou, C. Xu, Y. Xiang, F. Peng and Z. Guo, Chem. Eng. J., 2020, 379, 122382 CrossRef CAS.
- Z. Zheng, H. Liu and X. Wang, Desalination, 2024, 574, 117276 CrossRef CAS.
- D. Han, Z. Chen, J. Li, J. Mao, Z. Jiao, W. Wang, W. Zhang, Y. Zhang and H. Sun, ACS Appl. Mater. Interfaces, 2020, 12, 25435–25443 CrossRef CAS PubMed.
- X. Xiao, L. Pan, T. Chen, M. Wang, L. Ren, B. Chen, Y. Wang, Q. Zhang and W. Xu, Engineering, 2023, 30, 153–160 CrossRef CAS.
- Z. Yao, K. Yu, M. Pan, H. Xu, T. Zhao and Z. Jiang, Green Energy Environ., 2022, 7, 492–499 CrossRef CAS.
- B. Zhang, P. W. Wong, J. Guo, Y. Zhou, Y. Wang, J. Sun, M. Jiang, Z. Wang and A. K. An, Nat. Commun., 2022, 13, 3315 CrossRef CAS PubMed.
- L. Yu, M. Wang, H. Hou, X. Zhang, S. Lei, J. Liu, G. Liu and G. Qiao, Ceram. Int., 2023, 49, 11696–11704 CrossRef CAS.
- Q. Deng, T. Wu, K. Yin, X. Li, L. Wang, Q. Huang, Y. Huang, C. J. Arnusch and J. Duan, Appl. Phys. Lett., 2024, 125, 121602 CrossRef CAS.
|
This journal is © The Royal Society of Chemistry 2025 |
Click here to see how this site uses Cookies. View our privacy policy here.