Co nanoparticles encapsulated in N-doped carbon nanotube materials derived from new metal–organic frameworks for oxygen electrocatalysis†
Received
9th October 2024
, Accepted 26th November 2024
First published on 27th November 2024
Abstract
Bifunctional electrocatalysts used for oxygen reduction and evolution reactions (ORR/OER) are of great significance for metal–air batteries. Metal–organic frameworks (MOFs), after undergoing a high-temperature calcination process, emerge as promising precursors for preparing efficient metal–nitrogen–carbon (M-N-C) composites tailored specifically for electrocatalytic ORR/OER. Herein, we have successfully synthesized a novel rod-shaped MOF utilizing hydrazine hydrate and cobalt acetylacetonate as the building blocks, named Co-MOF. The Co-MOF has a tetrahedral Co–N4 coordination structure and has a high Co content. Upon undergoing the pyrolysis process, the corresponding M–N–C materials, featuring Co nanoparticles encapsulated within nitrogen-doped carbon nanotubes (Co@N-CNT), were obtained. These Co@N-CNT materials exhibit remarkable bifunctional ORR and OER performance with a half-wave potential of 0.88 V (versus reversible hydrogen electrode, vs. RHE) in 0.1 M KOH and an overpotential of 320 mV at 10 mA cm−2 in 1.0 M KOH, respectively. Moreover, when integrated into a Zn–air battery, the Co@N-CNT catalyst demonstrates unparalleled activities, boasting a peak power density of 235 mW cm−2 and a long-term cycling stability that extends beyond 160 hours. Theoretical calculations further revealed that active Co atoms within Co@N-CNT possess a high density of states (DOS) proximate to the Fermi level, coupled with a favorably low d-band center, both of which synergistically contribute to the enhanced ORR activity. This work offers profound insights into the fabrication of metal-encapsulated CNT materials based on novel frameworks enriched with Co, thereby creating a new path for the development of high-performance energy storage and conversion systems.
1 Introduction
Metal–air batteries have gained great attention owing to their environmental friendliness, absence of emissions, and impressive power densities, making them a promising energy storage solution.1–9 Their operation relies on redox reactions between the Zn anode and air cathode, facilitating energy storage and conversion.10–14 Nevertheless, the critical oxygen reduction reaction (ORR) and oxygen evolution reaction (OER) are hindered by sluggish kinetics.15–26 Consequently, the development of highly efficient ORR and OER electrocatalysts is of great importance for enhancing the performance of metal–air batteries.27–40 Among the catalysts explored, metal–nitrogen–carbon (M–N–C) materials have emerged as a superior class of electrocatalysts. M–N–C materials are used to assemble highly active electrocatalysts by modulating the coordination structure around the metal center, increasing the active site loading and constructing porous structures to improve active site utilization.41–43 Particularly Co–N–C materials featuring Co nanoparticles encapsulated within carbon nanotubes (CNTs), which demonstrate remarkable potential.44–53
In general, the fabrication of Co–N–C materials with encapsulated Co nanoparticles within CNTs typically involves two strategies. The first approach involves direct pyrolysis of a mixture of Co-based precursor materials and melamine, or introducing melamine upstream during the high-temperature calcination process.54–61 Here, the melamine serves as both a nitrogen and carbon source. The Co-based precursor transfers to Co nanoparticles that subsequently catalyze the growth of CNTs in situ.62–64 Alternatively, the second strategy involves the direct or distributed pyrolysis of Co-based metal–organic frameworks (MOFs) under controlled time and temperature conditions to achieve the in situ growth of CNTs.65,66 This latter approach has garnered considerable interest due to the pre-engineered Co coordination sites within the MOFs, which offer precise control over catalytic activity. During pyrolysis, the reducing gas generated transfers Co ions into nanoparticles, which then act as catalysts for the conversion of organic MOF components into CNTs.66 Therefore, there is an urgent need for the design and synthesis of novel MOFs enriched with high Co content to further advance this promising methodology.
Herein, we successfully synthesized a unique purple one-dimensional (1D) nanorod precursor utilizing Co acetylacetonate and hydrazine hydrate. Comprehensive experimental characterizations confirmed the presence of a Co–N4 coordination structure within the nanorods. Upon high-temperature pyrolysis, the internal Co ions underwent reduction to form Co nanoparticles, while the hydrazine hydrate and acetylacetonate served as nitrogen and carbon sources, respectively, facilitating the formation of Co nanoparticles encapsulated within N-doped carbon nanotubes (Co@N-CNT). Notably, the abundant nitrogen content of hydrazine hydrate enabled the autocatalytic growth of CNTs at high temperatures, eliminating the need for external nitrogen sources such as melamine or dicyandiamide. The resulting Co@N-CNT material exhibited a hierarchical structure grown on the 1D precursor. We further evaluated the electrocatalytic performance of the Co@N-CNT material for ORR and OER, as well as its application in Zn–air batteries. Based on the constructed models of Co cluster, Co@CNT, and Co@N-CNT, we were able to study the beneficial effect of this novel structure in facilitating electrocatalytic activity. This work offers fresh perspectives on the synthesis of Co–N–C materials featuring Co nanoparticles encapsulated in N-doped CNTs, contributing to the advancement of metal–air battery technology.
2 Experimental section
2.1 Material synthetic procedures
Synthesis of Co@N-CNT. Initially, Co acetylacetonate (5 mmol, 1.296 g) and N2H4·H2O (80%, 20 mmol, 1.213 mL) were dissolved in water (25 mL) and vigorously stirred for about 2 hours to ensure complete dissolution. Subsequently, this homogeneous solution was transferred into a Teflon-lined stainless-steel autoclave, where it underwent hydrothermal treatment at 120 °C for 12 hours. Upon cooling to room temperature, the resulting purple powders, designed as Co-MOF, were collected via centrifugation at 10
000 rpm, washed with water three times, and dried in a drying oven at 60 °C. Subsequently, the precursor Co-MOF was subjected to pyrolysis at 900 °C for 2 hours under an inert atmosphere of argon, yielding the Co–N–C material.
Synthesis of ZIF-67. Initially, Co(NO3)2·6H2O (4 mmol, 1.164 g) was dissolved in methanol (40 mL) and stirred vigorously for about 0.5 h. Subsequently, 2-methylimidazole (16 mmol, 1.32 g) was dissolved in an additional methanol (40 mL). The solution containing 2-methylimidazole was then cautiously added to the stirring solution of Co(NO3)2·6H2O. This combined solution was left to stand undisturbed for approximately 12 hours, allowing for the gradual formation of the desired product. Upon completion of the aging process, purple powders, referred to as ZIF-67, were obtained.
2.2 Characterization
Powder X-ray diffraction (PXRD) patterns of as-prepared materials were measured with an X-ray diffractometer (Bruker, D8 Advance, Cu Kα, λ = 1.5406 Å, 40 kV/40 mA). The morphologies of as-prepared materials were observed with scanning electron microscopy (SEM, Hitachi, SU8020) and transmission electron microscopy (TEM, JEOL, JEM-2100). Co K-edge X-ray absorption spectra (XAS) were collected by easyXAFS300+. The X-ray photoelectron spectroscopy (XPS) measurements of as-prepared materials were performed with a Kratos AXIS ULTRA XPS. Brunauer–Emmett–Teller (BET) surface areas of as-prepared materials were obtained by a specific surface area analyzer (ASAP 2020, Micromeritics). The weight loss data of as-prepared materials were obtained by a thermoanalyzer system (Q1000DSC + LNCS + FACS Q600SDT, TA Instruments).
2.3 Electrochemical measurement
The electrochemical ORR measurements were carried out using a CHI 760E Electrochemical Analyzer and a Pine Modulated Rotameter. In particular, the rotating disk electrode (RDE) was selected as the working electrode, the carbon rod as the auxiliary electrode, and the saturated Ag/AgCl as the reference electrode. Typically, 4 mg of catalysts and 40 μL of Nafion solution (5 wt%, DuPont) were added into 1 mL of deionized water/isopropanol solution (Vdeionized water
:
Visopropanol = 2
:
1) and then ultrasonicated for ∼1 h to prepare a homogeneous slurry. Subsequently, 15 μL of the slurry was coated onto the RDE electrode using a pipette (catalyst loading: ∼0.2 mg cm−2) and allowed to dried naturally. Cyclic voltammetry (CV) measurements were carried out in an O2/Ar-saturated 0.1 M KOH solution at ∼25 °C with a scan rate of 5 mV s−1. Linear sweep voltammetry (LSV) measurements were performed in an O2-saturated 0.1 M KOH solution at different rotating speeds ranging from 400 to 1600 rpm. Tafel slopes were obtained by measuring LSV with a scan rate of 2 mV s−1 at 1600 rpm. The stability test was carried out by conducting controlled potential electrolysis at 0.56 V (vs. RHE) in an O2-saturated 0.1 M KOH solution at 1600 rpm. The methanol resistance test was performed during the electrolysis at 0.56 V (vs. RHE) by adding 5 v% methanol into the O2-saturated 0.1 M KOH solution at 1600 rpm.
The number of electrons transferred (n) of ORR was calculated based on LSV data measured with the rotating ring-disk electrode (RRDE) in an O2-saturated 0.1 M KOH solution at ∼25 °C with a scan rate of 5 mV s−1. The diameter of the disk is 5.61 mm (0.247 cm2) and the area of the ring is 0.186 cm2. The n was calculated with the following eqn (1):
|  | (1) |
where
id is the disk current,
ir is the ring current, and
N is the ring current collection efficiency, which was determined to be ∼0.39 with the LSV data in K
3Fe[CN]
6 solution. The hydrogen peroxide percentage (%H
2O
2) was calculated with the following
eqn (2):
| 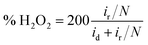 | (2) |
The n can also be calculated based on the Koutecky–Levich (K–L) eqn (3).
|  | (3) |
where
j is the current density,
jk and
jd are the kinetic and diffusion-limited current densities, respectively,
n is the number of electron transferred,
F is the Faraday constant (96
![[thin space (1/6-em)]](https://www.rsc.org/images/entities/char_2009.gif)
485 C mol
−1),
k is the rate constant of ORR,
CO2 is the bulk concentration of O
2 (1.26 × 10
−6 mol cm
−3),
DO2 is the diffusion coefficient of O
2 (1.90 × 10
−5 cm
2 s
−1),
ν is the kinematic viscosity of the electrolyte (0.01 cm
2 s
−1),
ω is the electrode rotation rate. The constant 0.2 is adopted when the rotation speed is expressed in rpm.
The turnover frequency (TOF) could be calculated with the eqn (4):
| 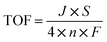 | (4) |
where
J is the current density at a given potential,
S is the surface area of RRDE (0.247 cm
2),
F is the Faraday constant (96
![[thin space (1/6-em)]](https://www.rsc.org/images/entities/char_2009.gif)
485.3 s A mol
−1), and
n is the number of active sites. Herein, metal Co atoms are the active site of Co@N-CNT. Therefore, the
n for Co of Co@N-CNT is 3.7 × 10
−4 mmol calculated with the following
eqn (5).
|  | (5) |
The J of Co@N-CNT is 5.78 mA cm−2.
In addition, the OER performance was evaluated with a CHI 660E Electrochemical Analyzer. LSV data of as-prepared catalysts were measured in a 1.0 M KOH solution with a three-electrode system. The glassy carbon (GC) electrode with a diameter of 3 mm (0.07 cm2) was selected as the working electrode, the carbon rod as the auxiliary electrode, and the saturated Ag/AgCl as the reference electrode. Then, 5 μL of as-prepared catalyst ink was coated onto the GC electrode using a pipette. The long-term stability of Co@N-CNT for OER was carried out at 1.57 V (vs. RHE). The overpotential (η) was calculated based on the following eqn (6):
| η = EAg/AgCl + (0.197 + 0.059 pH) − 1.23 | (6) |
2.4 Zn–air battery evaluation
A typical Zn–air battery consists of three parts: the anode, electrolyte, and cathode. The new polished Zn foil with a thickness of 0.25 mm was selected as the anode. The electrolyte was prepared by dissolving KOH (6.0 M) and Zn(OAc)2 (0.20 M) in deionized water. The catalyst ink was prepared by dispersing catalysts (5 mg) in 950 μL of ethanol and 50 μL of Nafion solution (5 wt% DuPont). The above mixture was sonicated for ∼0.5 h. For the catalyst ink of Pt/C + RuO2, Pt/C (2.5 mg) and RuO2 (2.5 mg) catalysts were weighed and dispersed in the solution using a similar preparation method. A certain amount of the mixed droplets of as-prepared catalyst ink (400 μL) were coated on the carbon cloth/gas diffusion layer (CC/GDL) as the air cathode of Zn–air battery. The corresponding electrochemical test was measured with a CHI 660E Electrochemical Analyzer.
2.5 Theoretical calculations
The spin-unrestricted density functional theory (DFT) methods were all implemented via the CASTEP module of Materials Studio software. The generalized gradient approximation (GGA) and Perdew–Burke–Ernzerhof (PBE) functional were used to describe the electron exchange correlation effects. In addition, the Brillouin zone was sampled using a 2 × 2 × 1 k-point grid based on the Monkhorst Pack grid with a cut-off energy of 280 eV.
3 Results and discussion
3.1 Characterization of Co-MOF and Co@N-CNT
Fig. 1a outlines the systematic synthesis process of the Co-based precursor. Initially, Co acetylacetonate was employed as the metal precursor, with hydrazine hydrate subsequently added and thoroughly mixed for 2 hours at approximately 25 °C. This mixture was then subjected to a hydrothermal reaction at 120 °C for 12 hours, resulting in the formation of a purple powder. Scanning electron microscopy (SEM) images of the Co precursor reveal a uniform distribution of nanorods (Fig. 1b and c). The partial helical structure of Co-MOF, as depicted in Fig. 1d, may be attributed to the small ligand molecules. The average diameter of these nanorods is measured to be 120 nm (Fig. 1d). Additionally, the transmission electron microscope (TEM) image provides further confirmation of the morphology and dimensions of nanorods (Fig. S1†).
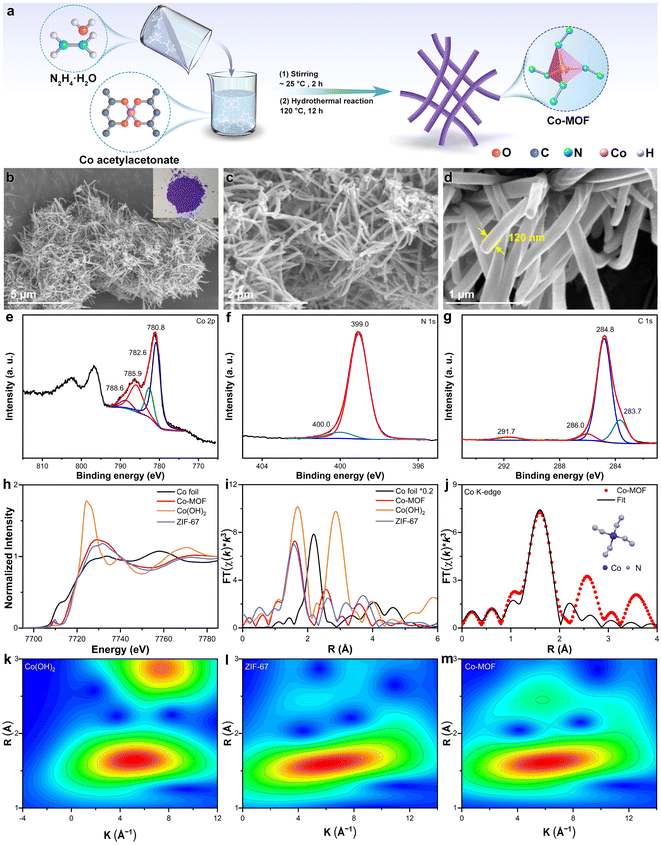 |
| Fig. 1 (a) Schematic illustration of preparation procedure, (b–d) SEM images, high-resolution XPS spectra of (e) Co 2p, (f) N 1s, and (g) C 1s for Co-MOF. (h) Normalized Co K-edge XANES and (i) k3-weighted FT-EXAFS spectra of Co-MOF, Co foil, Co(OH)2, and ZIF-67. (j) The fitting curve of Co-MOF at R space. Co K-edge WT-EXAFS contour plots of Co(OH)2 (k), ZIF-67 (l), and Co-MOF (m). | |
X-ray photoelectron spectroscopy (XPS) and X-ray absorption fine structure (XAFS) measurements were conducted to study the coordination structure and valent state of Co in the synthesized precursor. The XPS full spectrum distinctly reveals the presence of Co, N, C, and O peaks, indicating the successful incorporation of these elements (Fig. S2†). The high-resolution XPS spectrum of Co 2p displays prominent peaks at 780.8 eV and 782.6 eV, corresponding to the Co2+ species of Co 2p3/2 (Fig. 1e). Additionally, satellite peaks of Co were observed at 785.9 eV and 788.6 eV. The N 1s XPS spectrum exhibits two distinct peaks: one at 399.0 eV (92.3%), attributed to metal-N bonds, and another at 400.0 eV (7.7%), assigned to oxidized N species (Fig. 1f). The C 1s XPS spectrum comprises four peaks, corresponding to sp2 C (283.7 eV), C–C (284.8 eV), C–N (286.0 eV), and C
O (291.7 eV), respectively (Fig. 1g). The atomic proportions of the Co-MOF precursor, as determined by XPS, are shown in Table S1,† revealing a Co content of 6.19%, N content of 21.59%, and C content of 66.36%. For comparison, a typical Co-based MOF precursor, zeolitic imidazolate framework-67 (ZIF-67), was also prepared using Co2+ and 2-methylimidazole as starting materials. The successful synthesis of ZIF-67 was verified through SEM imaging and X-ray diffraction (XRD) patterns (Fig. S3 and S4†). Notably, the atomic proportions of Co, N, and C in ZIF-67 were found to be 2.13%, 19.97%, and 69.53%, respectively (Fig. S5†). These findings emphasize the advantage of the Co-MOF precursor in terms of its higher Co and N content, which is anticipated to facilitate the formation of metal nanoparticles encapsulated within CNTs during the subsequent high-temperature pyrolysis process.
Fig. 1h displays the normalized Co K-edge X-ray absorption near-edge structure (XANES) spectra of Co-MOF, benchmarked against Co foil, Co(OH)2, and ZIF-67. The proximity of the absorbing edge position of Co-MOF to those of ZIF-67 and Co(OH)2 suggests a shared valence state (CoII), corroborating the XPS findings. The presence of pre-edge peaks indicates a tetrahedral coordination geometry for the CoII ions in the Co-MOF.67 The Fourier-transform (FT) of the k3-weighted extended X-ray absorption fine structure (EXAFS) spectra at the Co K-edge, without phase correction, reveals a scattering path centered at approximately 1.60 Å for Co-MOF, closely mirroring the main peak of ZIF-67 at 1.59 Å (Fig. 1i). This observation demonstrates the structural similarity between Co-MOF and ZIF-67. To further understand the coordination details, the FT-EXAFS fitting of the Co-MOF precursor was performed (Fig. 1j and S6†). The R-space (R magnitude and R imaginary) fitting curves for the first shell layer of the experimental data provide compelling evidence of the Co–N scattering path. The wavelet transforms (WT) contour plots of the Co-MOF precursor exclusively exhibit a Co–N scattering path (Fig. 2k–m and S7†), mirroring the behavior of ZIF-67. The fitted coordination number for the Co atom in the first shell is 3.432, indicating a Co–N4 configuration as depicted in the inset of Fig. 1j.
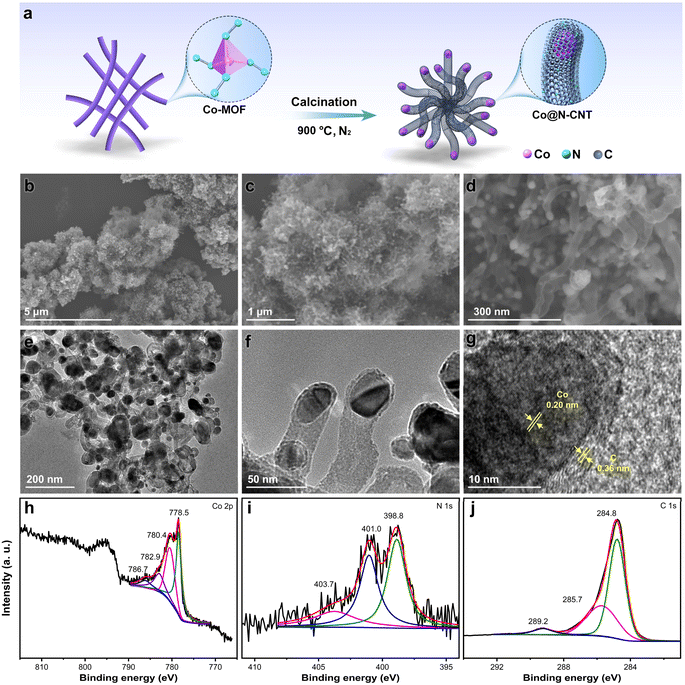 |
| Fig. 2 (a) Schematic illustration of preparation procedure, (b–d) SEM images, (e and f) TEM images, (g) HRTEM image, and high-resolution XPS spectra of Co 2p (h), N 1s (i), and C 1s (j) for Co@N-CNT. | |
The Co-MOF precursor has a purple color, which is also consistent with the ZIF-67 (Fig. 1b and S8†), further demonstrating the shared Co–N4 coordination structure. The XRD pattern of Co-MOF features a diffraction peak at 10° (Fig. S9†). Additionally, the Brunauer–Emmett–Teller (BET) surface area analysis reveals a relatively smaller surface area, which may be attributed to the occlusion of acetylacetone functional groups within the framework (Fig. S10†). Thermogravimetric analysis (TGA) data of Co-MOF indicates stability up to 300 °C, with subsequent weight loss attributed to the high oxygen content of acetylacetone (Fig. S11†). In conclusion, the Co precursor represents a novel MOF featuring a Co–N4 coordination structure. The Co-MOF precursor underwent pyrolysis at 900 °C, yielding a Co–N–C material. Notably, the product featured Co nanoparticles encapsulated within N-doped CNTs, named Co@N-CNT (Fig. 2a). SEM and TEM images confirm the uniform distribution of Co@N-CNT (Fig. 2b–f). High-resolution TEM (HRTEM) image demonstrates the presence of Co nanoparticles and CNTs, with lattice spacings of 0.20 nm and 0.36 nm corresponding to the (111) plane of Co nanoparticles and the (002) plane of graphitic carbon, respectively (Fig. 2g). In addition, high-angle annular dark-field scanning transmission electron microscopy (HAADF-STEM) image and elemental mappings demonstrate the uniform distribution of C, N, and Co within Co@N-CNT (Fig. S12†). The formation of metallic Co was confirmed by the XRD pattern of Co@N-CNT (JCPDS # 15-0806, Fig. S13†). The N2 adsorption/desorption isotherm demonstrates that Co@N-CNT has a BET specific surface area of 91.7 m2 g−1 (Fig. S14†). The XPS spectrum of Co@N-CNT exhibits distinct peaks associated with Co, N, and C (Fig. S15†). Specifically, the Co 2p XPS spectrum of Co@N-CNT shows two prominent peaks at 778.5 eV and 780.4 eV, attributed to metallic Co and Co-NxCy species, respectively (Fig. 2h). The N 1s XPS spectrum of Co@N-CNT reveals three peaks, corresponding to pyridinic N (398.8 eV, 47.8%), graphitic N (401.0 eV, 41.1%), and oxidized N (403.7 eV, 11.1%) (Fig. 2i). Meanwhile, the C 1s XPS spectrum displays three peaks indexing to C–C (284.8 eV), C–N (285.7 eV), and C
O (289.2 eV) bonds (Fig. 2j). The normalized Co K-edge XANES spectra of Co@N-CNT and Co foil exhibit similar absorption edges, indicating that the Co in Co@N-CNT primarily exists in the metallic Co0 state (Fig. S16a†). This finding is consistent with the TEM images and XRD patterns. Additionally, the k3-weighted FT-EXAFS spectra (without phase correction) at the Co K-edge for Co@N-CNT exhibit a predominant peak, which is comparable to Co foil (Fig. S16b†). Only one Co–Co scattering path was observed in the WT contour plots of Co@N-CNT (Fig. S17†). These morphological and structural insights confirm the successful encapsulation of Co nanoparticles with-in N-doped CNTs, forming the Co–N–C material.
3.2 Electrocatalytic ORR and OER studies
The performance of both the Co-MOF precursor and Co@N-CNT in terms of ORR and OER was thoroughly evaluated (Fig. 3). Specifically, cyclic voltammetry (CV) data of Co@N-CNT shows a strong O2 reduction peak at 0.85 V (versus reversible hydrogen electrode, vs. RHE) measured in an O2-saturated 0.1 M KOH solution compared to that measured under Ar condition, which indicates that the catalyst has the ability to reduce oxygen (Fig. S18†). The linear sweep voltammetry (LSV) measurements conducted using a rotating ring disk electrode (RRDE) at 1600 rpm, demonstrate that Co@N-CNT exhibits a superior half-wave potential (E1/2) of 0.88 V (vs. RHE) surpassing both commercial Pt/C (20 wt%) at 0.87 V (vs. RHE) and Co-MOF at 0.70 V (vs. RHE) (Fig. 3a). The optimum performance was demonstrated by testing materials at different synthesis temperatures (800 °C and 1000 °C, Fig. S19–S21†) and using different catalyst loadings (5 μL and 10 μL, Fig. S22†). Additionally, the Co@N-CNT shows the most favourable Tafel slope (89.9 mV dec−1) among the tested materials, including Co-MOF (133.1 mV dec−1) and Pt/C (98.9 mV dec−1), indicating its superior kinetics (Fig. 3b). If all Co atoms on the electrode are assumed to be available, the calculated turnover frequency (TOF) of Co@N-CNT at 0.2 V (vs. RHE) is 0.01 e site−1 s−1. The electron transfer number n and the yield of H2O2 (%) were calculated based on the current measured on the ring electrode (Fig. S23†). The Co@N-CNT has an n value of 3.96 at 0.7 V (vs. RHE), while that value for Pt/C is 3.90. Therefore, both Co@N-CNT and Pt/C have a dominant four-electron (4e) ORR process. Notably, the H2O2 yield for both materials remained low (<5% for Co@N-CNT and <7% for Pt/C) within the potential range of 0.2 to 0.7 V (vs. RHE), confirming their high 4e ORR selectivity (Fig. 3c). LSV data of Co@N-CNT were further tested at different rotation speeds (Fig. 3d). The n value based on the Koutecky–Levich (K–L) equation and plots of j−1versus ω−1/2 for Co@N-CNT is 3.91 (Fig. 3e). Therefore, the Co@N-CNT exhibits excellent catalytic ORR activity and high 4e ORR selectivity. The stability of Co@N-CNT and Pt/C was further measured at 1600 rpm under controlled potential electrolysis at 0.56 V (vs. RHE). The Co@N-CNT shows only a slight current decrease (∼9%) after running a 10 h stability test (Fig. 3f), which is more stable than Pt/C (∼17%). Moreover, the Co@N-CNT shows better methanol resistance compared to Pt/C in the presence of methanol in the electrolyte (Fig. S24†). After the stability test, the morphology and structure of Co@N-CNT are still maintained, further demonstrating the stability of Co@N-CNT (Fig. S25–S27†). The electrocatalytic OER performance of Co-MOF, Co@N-CNT, and commercial RuO2 was evaluated in a 1.0 M KOH solution using a glassy carbon (GC) electrode. The Co@N-CNT exhibits the lowest overpotential η of 320 mV at 10 mA cm−2 and a Tafel slope of 93.9 mV dec−1 compared to Co-MOF (400 mV and 120.5 mV dec−1) and RuO2 (350 mV and 106.6 mV dec−1) (Fig. 3g and h). To gain insights into their electrochemical active surface areas (ECSA), the electrochemical double layer capacitance (Cdl) was measured. The Cdl values, which are directly proportional to ECSA, were derived from CV data acquired in the non-Faraday region at varying scan rates (Fig. S28†). The Co@N-CNT has a Cdl of 0.11 mF, which is larger than Co-MOF (0.05 mF) (Fig. 3i), suggesting a larger ECSA and a higher density of exposed active sites. Furthermore, electrochemical impedance spectroscopy (EIS) analysis reveals that the Co@N-CNT possesses superior electron conductivity compared to Co-MOF (Fig. S29†). When assessing OER stability at a controlled potential of 1.57 V (vs. RHE), the Co@N-CNT demonstrates exceptional durability, with only a slight current decline of ∼10% after 10 hours of operation (Fig. S30†). Furthermore, Co@N-CNT demonstrates excellent structural stability after OER testing (Fig. S31–S33†). Therefore, the Co@N-CNT exhibits excellent OER performance. The voltage gap ΔE(ORR–OER) between the ORR (E1/2) and OER (E10) is only 670 mV, demonstrating the excellent bifunctional electrocatalytic ORR/OER activity of Co@N-CNT (Fig. S34†). The ORR and OER properties of Co@N-CNT have also been compared with those of Co-based catalysts reported, demonstrating excellent bifunctional catalytic activities (Table S2†).
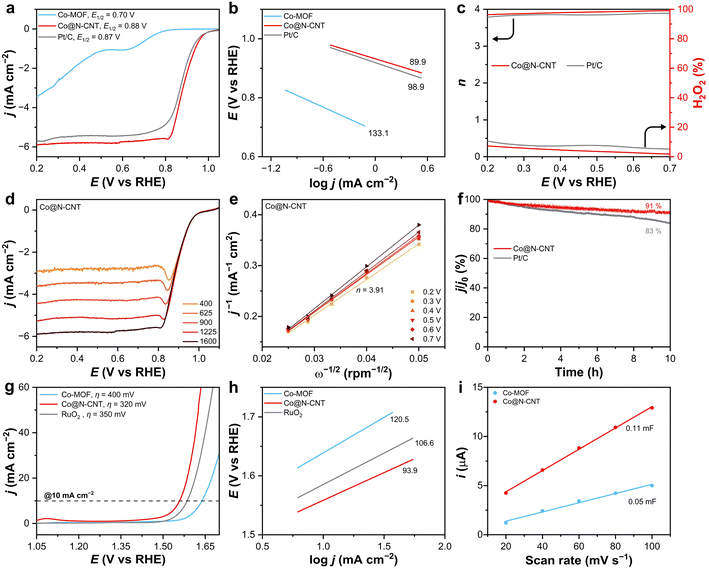 |
| Fig. 3 (a) ORR LSV curves, and (b) Tafel slopes of Co-MOF, Co@N-CNT and Pt/C (20 wt%). (c) Electron transfer number n and H2O2 production (%) of Co@N-CNT and Pt/C. (d) ORR LSV data at different rotation speeds and (e) K–L plots of Co@N-CNT. (f) The stability test of Co@N-CNT and Pt/C was measured at 1600 rpm in an O2-saturated 0.1 M KOH solution. (g) OER LSV data, (h) Tafel slopes of Co-MOF, Co@N-CNT, and RuO2, and (i) plots of current i versus scan rate of Co-MOF and Co@N-CNT measured in 1.0 M KOH solution. | |
3.3 Zn–air battery studies of Co@N-CNT
Given the excellent bifunctional ORR and OER performance, the practical application of the Co@N-CNT catalyst was thoroughly evaluated in a Zn–air battery. A standard rechargeable Zn–air battery was fabricated, utilizing Co@N-CNT as the cathode material and metallic Zn as the anode, with an electrolyte comprising 6.0 M KOH and 0.2 M Zn(OAc)2 (Fig. 4a). Notably, the open voltage of the Co@N-CNT based battery is 1.47 V, which is higher than that of Pt/C + RuO2 (1.42 V, Fig. 4b). The Zn–air battery assembled with Co@N-CNT catalysts shows a large discharge power density with a value of 235 mW cm−2, significantly outperforming Pt/C + RuO2 (82 mW cm−2, Fig. 4c) and other reported electrocatalysts (Table S3†). In addition, the Co@N-CNT also displays a high specific capacity of 803.0 mA h g−1 at j = 20 mA cm−2 (Fig. 4d). The charge–discharge performance was equally impressive. The Zn–air battery assembled with Co@N-CNT catalysts exhibits a discharge potential of 1.20 V and a charge potential of 2.02 V, resulting in a narrower charge–discharge voltage gap of 0.82 V compared to 0.90 V of Pt/C + RuO2 (Fig. 4e). Furthermore, the battery assembled with Co@N-CNT catalysts demonstrates superior rate capability across various current densities ranging from 2 to 50 mA cm−2, showing better reversibility and efficiency than Pt/C + RuO2 (Fig. 4f). Long-term stability was also evaluated through discharge–charge cycling tests. The Zn–air battery assembled with Co@N-CNT shows remarkable durability for over 160 hours (Fig. 4g). Long-term charge/discharge curves at high current densities have also been tested. The Zn–air batteries assembled with Co@N-CNT at j = 5 and 10 mA cm−2 are stable after running for over 50 hours (Fig. S35 and S36†). To demonstrate the practical potential of this catalyst, a Zn–air battery incorporating Co@N-CNT catalysts successfully powered LED panels, toy fans, and toy cars (Fig. 4h, S37 and S38†).
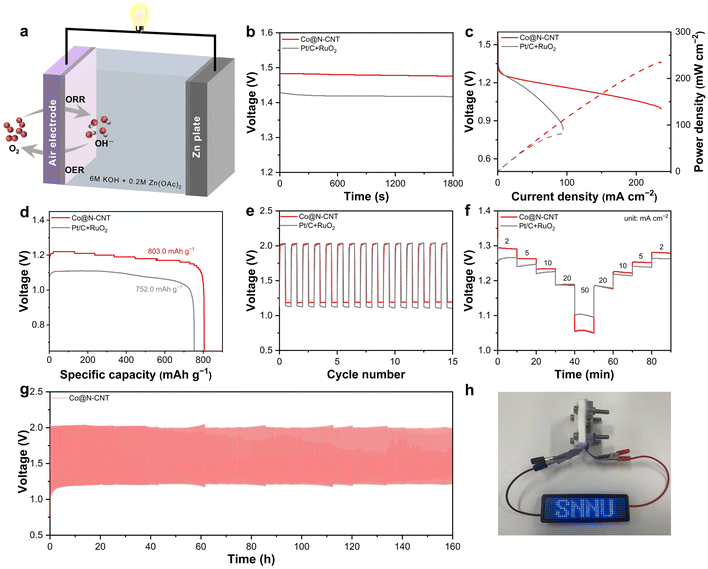 |
| Fig. 4 (a) Schematic diagram of a rechargeable Zn–air battery. (b) The open circuit voltage, (c) discharge data and power densities, (d) discharge data measured at j = 20 mA cm−2, and (e) charge–discharge cycling data measured at j = 2 mA cm−2 of Zn–air batteries constructed with Co@N-CNT and Pt/C + RuO2. (f) Rate capabilities of Co@N-CNT and Pt/C + RuO2 cathodes for various current densities from 2 to 50 mA cm−2. (g) Stability test at j = 2 mA cm−2 and (h) lighted LED panel by a Zn–air battery assembled with Co@N-CNT. | |
3.4 Theoretical studies of Co@N-CNT
Density functional theory (DFT) calculations were used to further investigate the effect of multiple active sites in enhancing the ORR. Three distinct structural models were constructed: a pure Co cluster (Fig. 5a), a Co cluster loaded within CNT tips (Co@CNT, Fig. 5d), and N-doped CNTs loaded with Co clusters at the tip (Co@N-CNT, Fig. 5g). Notably, in Co@CNT, Co atoms are bonded to C atoms through three bonds, whereas in Co@N-CNT, the incorporation of N atoms fosters the formation of additional Co–N bonds, suggesting a greater electron loss from the metal Co nanoparticles. This high valence state of active species is known to improve ORR performance.68 Therefore, from a theoretical standpoint, the models were analyzed based on the Miller index (001). The density of states (DOS) analysis reveals that the active metal atoms in Co@N-CNT exhibit a higher DOS near the Fermi level compared to both Co cluster and Co@CNT (Fig. 5b, e and h). This enhanced DOS significantly improves electron transfer efficiency, thereby further enhancing the electrocatalytic performance.69 Additionally, the d-band center analysis of Co atoms across these catalysts indicates that Co@N-CNT possesses the lowest d-band center at −1.51 eV, compared to −0.96 eV for Co cluster and −1.46 eV for Co@CNT (Fig. 4i). This lower d-band center weakens the adsorption strength of oxygen-containing intermediates during the ORR process, leading to superior catalytic ORR activity.70
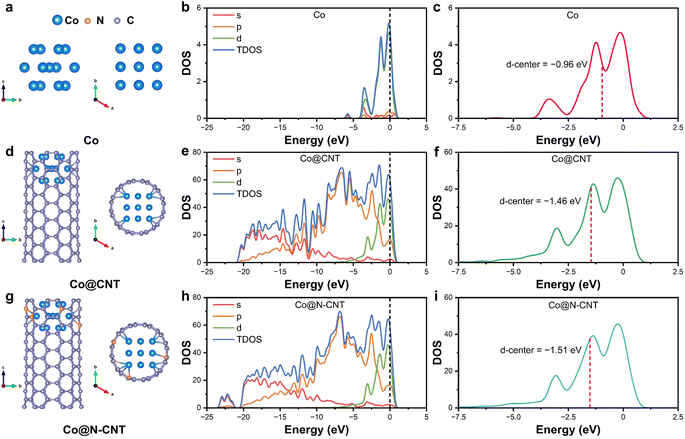 |
| Fig. 5 Structural models (a, d, and g), DOS (b, e, and h), DOS of Co 3d (c, f, and i) for Co cluster (a–c), Co@CNT (d–f) and Co@N-CNT (g-i). | |
4 Conclusions
In summary, we have successfully synthesized a novel 1D MOF, achieved through the reaction of Co acetylacetonate and hydrazine hydrate under stirring and hydrothermal conditions. Notably, this Co-MOF has a tetrahedral structure featuring a Co–N4 coordination geometry. Upon pyrolysis, we obtained Co–N–C materials, characterized by Co nanoparticles intricately encapsulated within N-doped carbon nanotubes (Co@N-CNT). These Co@N-CNT exhibited remarkable bifunctional performance in both ORR and OER, with an E1/2 of 0.88 V (vs. RHE) in 0.1 M KOH for ORR and a low overpotential of 320 mV at j = 10 mA cm−2 in 1.0 M KOH for OER. Furthermore, a Zn–air battery incorporating Co@N-CNT as a catalyst exhibits an impressive discharge power density of 235 mW cm−2 and cycle stability exceeding 160 hours. Theoretical calculations show that the lower d-center of Co@N-CNT weakens the adsorption strength of catalytic intermediates, thereby enhancing catalytic activity. This work not only introduces innovative strategies for the synthesis of high-performance M–N–C materials with metal encapsulation in CNTs but also opens up new avenues for the development of advanced energy conversion and storage devices.
Data availability
The data supporting this article have been included as part of the ESI.† The code for Materials Studio can be found at https://www.3ds.com/products/biovia/materials-studio. The version of the code employed for this study is version 8.0.
Author contributions
Jieling Zhang: writing – original draft, formal analysis, data curation. Weiran Suo: software. Yu Han: investigation, formal analysis. Yiwen Cao: investigation, data curation. Yuhan Xu: investigation, data curation. Mengying Wang: software. Zuozhong Liang: writing – review & editing. Yuan Wang: data curation, funding acquisition. Haoquan Zheng: data curation. Rui Cao: resources, funding acquisition.
Conflicts of interest
There are no conflicts to declare.
Acknowledgements
We are grateful for support from National Natural Science Foundation of China (22178213 and 22478237), Innovation Capability Support Program of Shaanxi Province (2023KJXX-018), Key Research and Development Program of Shaanxi Province (2022GY-201), Fundamental Research Funds for the Central Universities (GK202309002, GK202306007, and GK 202207007), International Joint Research Center on Advanced Characterizations of Xi'an City, and Research Funds of Shaanxi Normal University.
References
- W. Sun, F. Wang, B. Zhang, M. Zhang, V. Küpers, X. Ji, C. Theile, P. Bieker, K. Xu, C. Wang and M. Winter, Science, 2021, 371, 46–51 CrossRef CAS PubMed.
- Z. Liang, H.-Y. Wang, H. Zheng, W. Zhang and R. Cao, Chem. Soc. Rev., 2021, 50, 2540–2581 RSC.
- C.-X. Zhao, J.-N. Liu, J. Wang, D. Ren, B.-Q. Li and Q. Zhang, Chem. Soc. Rev., 2021, 50, 7745–7778 RSC.
- J. Li, K. Zhang, B. Wang and H. Peng, Angew. Chem., Int. Ed., 2022, 61, e202213026 CrossRef CAS PubMed.
- Q. Wang, Q. Feng, Y. Lei, S. Tang, L. Xu, Y. Xiong, G. Fang, Y. Wang, P. Yang, J. Liu, W. Liu and X. Xiong, Nat. Commun., 2022, 13, 3689 CrossRef CAS PubMed.
- G. Nazir, A. Rehman, J.-H. Lee, C.-H. Kim, J. Gautam, K. Heo, S. Hussain, M. Ikram, A. A. AlObaid, S.-Y. Lee and S.-J. Park, Nano-Micro Lett., 2024, 16, 138 CrossRef PubMed.
- D. Deng, J. Wu, Q. Feng, X. Zhao, M. Liu, Y. Bai, J. Wang, X. Zheng, J. Jiang, Z. Zhuang, X. Xiong, D. Wang and Y. Lei, Adv. Funct. Mater., 2024, 34, 2308762 CrossRef CAS.
- S. Gao, X. Wang, X. Liu, C. Guo, Q. Liu and G. Hu, Mater. Chem. Front., 2024, 8, 485–506 RSC.
- M. Chen, J. Ma, C. Chen, J. Ding, Y. Liu, H. He, Q. Liu, G. Hu, Y. Wu and X. Liu, Chem. Eng. J., 2024, 498, 155302 CrossRef CAS.
- W. Zhang, W. Lai and R. Cao, Chem. Rev., 2017, 117, 3717–3797 CrossRef CAS PubMed.
- K. Sun, J. Dong, H. Sun, X. Wang, J. Fang, Z. Zhuang, S. Tian and X. Sun, Nat. Catal., 2023, 6, 1164–1173 CrossRef CAS.
- G. Chen, R. Lu, C. Li, J. Yu, X. Li, L. Ni, Q. Zhang, G. Zhu, S. Liu, J. Zhang, U. I. Kramm, Y. Zhao, G. Wu, J. Xie and X. Feng, Adv. Mater., 2023, 35, 2300907 CrossRef CAS PubMed.
- N. Shang, K. Wang, M. Wei, Y. Zuo, P. Zhang, H. Wang, Z. Chen and P. Pei, J. Mater. Chem. A, 2022, 10, 16369–16389 RSC.
- Y. Li, H. Sun, L. Ren, K. Sun, L. Gao, X. Jin, Q. Xu, W. Liu and X. Sun, Angew. Chem., Int. Ed., 2024, 63, e202405334 CrossRef CAS PubMed.
- Z. Liang, N. Kong, C. Yang, W. Zhang, H. Zheng, H. Lin and R. Cao, Angew. Chem., Int. Ed., 2021, 60, 12759–12764 CrossRef CAS PubMed.
- T.-W. Song, C. Xu, Z.-T. Sheng, H.-K. Yan, L. Tong, J. Liu, W.-J. Zeng, L.-J. Zuo, P. Yin, M. Zuo, S.-Q. Chu, P. Chen and H.-W. Liang, Nat. Commun., 2022, 13, 6521 CrossRef CAS PubMed.
- L. Huang, S. Zaman, X. Tian, Z. Wang, W. Fang and B. Y. Xia, Acc. Chem. Res., 2021, 54, 311–322 CrossRef CAS PubMed.
- Z. Liang, G. Zhou, H. Tan, Y. Mou, J. Zhang, H. Guo, S. Yang, H. Lei, H. Zheng, W. Zhang, H. Lin and R. Cao, Adv. Mater., 2024, 36, 2408094 CrossRef CAS PubMed.
- L. Yan, P. Li, Q. Zhu, A. Kumar, K. Sun, S. Tian and X. Sun, Chem, 2023, 9, 280–342 CAS.
- L. Lyu, X. Hu, S. Lee, W. Fan, G. Kim, J. Zhang, Z. Zhou and Y.-M. Kang, J. Am. Chem. Soc., 2024, 146, 4803–4813 CrossRef CAS PubMed.
- L. Han, H. Yu and Z. Xiang, Small, 2023, 19, 2304108 CrossRef CAS PubMed.
- J. Liang, Y. Wan, H. Lv, X. Liu, F. Lv, S. Li, J. Xu, Z. Deng, J. Liu, S. Zhang, Y. Sun, M. Luo, G. Lu, J. Han, G. Wang, Y. Huang, S. Guo and Q. Li, Nat. Mater., 2024, 23, 1259–1267 CrossRef CAS PubMed.
- B. Xu, T. Liu, X. Liang, W. Dou, H. Geng, Z. Yu, Y. Li, Y. Zhang, Q. Shao, J. Fan and X. Huang, Adv. Mater., 2022, 34, 2206528 CrossRef CAS PubMed.
- H. Zhang, W. Xia, H. Shen, W. Guo, Z. Liang, K. Zhang, Y. Wu, B. Zhu and R. Zou, Angew. Chem., Int. Ed., 2020, 59, 1871–1877 CrossRef CAS PubMed.
- J. T. Mefford, A. R. Akbashev, M. Kang, C. L. Bentley, W. E. Gent, H. D. Deng, D. H. Alsem, Y.-S. Yu, N. J. Salmon, D. A. Shapiro, P. R. Unwin and W. C. Chueh, Nature, 2021, 593, 67–73 CrossRef CAS PubMed.
- C. Qin, S. Chen, H. Gomaa, M. A. Shenashen, S. A. El-Safty, Q. Liu, C. An, X. Liu, Q. Deng and N. Hu, Acta Phys.-Chim. Sin., 2024, 40, 2307059 Search PubMed.
- L. Lin, Y. Ni, L. Shang, H. Sun, Q. Zhang, W. Zhang, Z. Yan, Q. Zhao and J. Chen, ACS Catal., 2022, 12, 7531–7540 CrossRef CAS.
- Z. Liu, Z. Zhao, B. Peng, X. Duan and Y. Huang, J. Am. Chem. Soc., 2020, 142, 17812–17827 CrossRef CAS PubMed.
- S. Mondal, D. Bagchi, M. Riyaz, S. Sarkar, A. K. Singh, C. P. Vinod and S. C. Peter, J. Am. Chem. Soc., 2022, 144, 11859–11869 CrossRef CAS PubMed.
- S. Yang, X. Liu, S. Li, W. Yuan, L. Yang, T. Wang, H. Zheng, R. Cao and W. Zhang, Chem. Soc. Rev., 2024, 53, 5593–5625 RSC.
- L. Tao, K. Wang, F. Lv, H. Mi, F. Lin, H. Luo, H. Guo, Q. Zhang, L. Gu, M. Luo and S. Guo, Nat. Commun., 2023, 14, 6893 CrossRef CAS PubMed.
- H. Chang, X. Liu, S. Zhao, Z. Liu, R. Lv, Q. Zhang and T.-F. Yi, Adv. Funct. Mater., 2024, 34, 2313491 CrossRef CAS.
- Q. Huang, L. Hu, X. Chen, W. Cai, L. Wang and B. Wang, Adv. Funct. Mater., 2023, 33, 2302582 CrossRef CAS.
- Y. Zhao, D. P. Adiyeri Saseendran, C. Huang, C. A. Triana, W. R. Marks, H. Chen, H. Zhao and G. R. Patzke, Chem. Rev., 2023, 123, 6257–6358 CrossRef CAS PubMed.
- Z. Liang, H. Guo, G. Zhou, K. Guo, B. Wang, H. Lei, W. Zhang, H. Zheng, U.-P. Apfel and R. Cao, Angew. Chem., Int. Ed., 2021, 60, 8472–8476 CrossRef CAS PubMed.
- X. Yi, H. Yang, X. Yang, X. Li, C. Yan, J. Zhang, L. Chen, J. Dong, J. Qin, G. Zhang, J. Wang, W. Li, Z. Zhou, G. Wu and X. Li, Adv. Funct. Mater., 2024, 34, 2309728 CrossRef CAS.
- C. Mi, H. Yu, L. Han, L. Zhang, L. Zhai, X. Li, Y. Liu and Z. Xiang, Adv. Funct. Mater., 2023, 33, 2303235 CrossRef CAS.
- J.-N. Liu, C.-X. Zhao, D. Ren, J. Wang, R. Zhang, S.-H. Wang, C. Zhao, B.-Q. Li and Q. Zhang, Adv. Mater., 2022, 34, 2109407 CrossRef CAS PubMed.
- M. Xie, X. Xiao, D. Wu, C. Zhen, C. Wu, W. Wang, H. Nian, F. Li, M. D. Gu and Q. Xu, Nano Res., 2024, 17, 5288–5297 CrossRef CAS.
- P. Liu, Y. Liu, K. Wang, S. Shi, M. Jin, J. Liu, T. Qin, Q. Liu, X. Liu and J. He, Nano Res., 2024, 17, 7957–7966 CrossRef CAS.
- J. Liu, J. Liao, K. Huang, J. Dong, G. He, Z. Gong and H. Fei, Adv. Mater., 2023, 35, 2211398 CrossRef CAS PubMed.
- W. Guan, H. Shao, C. Zhang, X. Qiu, J. Zhao, Y. Wang, L. Zhang, M. Shao and J. Hu, Nano Energy, 2024, 120, 109149 CrossRef CAS.
- Y. Liu, M. Wang, Z. Liang and H. Zheng, Sci. China:Chem., 2024, 67, 3209–3222 CrossRef CAS.
- B. Wu, T. Sun, Y. You, H. Meng, D. M. Morales, M. Lounasvuori, A. Beheshti Askari, L. Jiang, F. Zeng, B. Hu, X. Zhang, R. Tai, Z. J. Xu, T. Petit and L. Mai, Angew. Chem., Int. Ed., 2023, 62, e202219188 CrossRef CAS PubMed.
- X. Lu, P. Yang, Y. Wan, H. Zhang, H. Xu, L. Xiao, R. Li, Y. Li, J. Zhang and M. An, Coord. Chem. Rev., 2023, 495, 215400 CrossRef CAS.
- Y. Wang, T. Yang, X. Fan, Z. Bao, A. Tayal, H. Tan, M. Shi, Z. Liang, W. Zhang, H. Lin, R. Cao, Z. Huang and H. Zheng, Angew. Chem., Int. Ed., 2024, 63, e202313034 CrossRef CAS PubMed.
- W. Xu, R. Zeng, M. Rebarchik, A. Posada-Borbón, H. Li, C. J. Pollock, M. Mavrikakis and H. D. Abruña, J. Am. Chem. Soc., 2024, 146, 2593–2603 CrossRef CAS PubMed.
- Z. Liang, J. Zhang, H. Zheng and R. Cao, Chem. Commun., 2024, 60, 2216–2219 RSC.
- D. Geng, Y. Huang, S. Yuan, Y. Jiang, H. Ren, S. Zhang, Z. Liu, J. Feng, T. Wei and Z. Fan, Small, 2023, 19, 2207227 CrossRef CAS PubMed.
- X. Qu, Y. Yan, Z. Zhang, B. Tian, S. Yin, X. Cheng, R. Huang, Y. Jiang and S. Sun, Chem.–Eur. J., 2024, 30, e202304003 CrossRef CAS PubMed.
- C. Ye, L. Zhang and Y. Shen, ACS Mater. Lett., 2024, 6, 2858–2887 CrossRef CAS.
- P. Li, Y. Jiao, Y. Ruan, H. Fei, Y. Men, C. Guo, Y. Wu and S. Chen, Nat. Commun., 2023, 14, 6936 CrossRef CAS PubMed.
- C.-X. Zhao, J.-N. Liu, J. Wang, C. Wang, X. Guo, X.-Y. Li, X. Chen, L. Song, B.-Q. Li and Q. Zhang, Sci. Adv., 2022, 8, eabn5091 CrossRef CAS PubMed.
- W. Hou, K. Peng, S. Li, F. Huang, B. Wang, X. Yu, H. Yang and H. Zhang, J. Colloid Interface Sci., 2023, 646, 265–274 CrossRef CAS PubMed.
- L. Zou, C.-C. Hou, Z. Liu, H. Pang and Q. Xu, J. Am. Chem. Soc., 2018, 140, 15393–15401 CrossRef CAS PubMed.
- X. Wang, Z. Qin, J. Qian, L. Chen and K. Shen, ACS Catal., 2023, 13, 10672–10682 CrossRef CAS.
- K. Zhang, H. Wang, X. Zhang, L. Liu, B. Feng, Y. Wang and J. Liu, ACS Sustain. Chem. Eng., 2024, 12, 7318–7328 CrossRef CAS.
- L. Yan, Z. Xu, W. Hu, J. Ning, Y. Zhong and Y. Hu, Nano Energy, 2021, 82, 105710 CrossRef CAS.
- N. Cai, S. Xia, X. Zhang, Z. Meng, P. Bartocci, F. Fantozzi, Y. Chen, H. Chen, P. T. Williams and H. Yang, ChemSusChem, 2020, 13, 938–944 CrossRef CAS PubMed.
- W. Ren, X. Tan, C. Jia, A. Krammer, Q. Sun, J. Qu, S. C. Smith, A. Schueler, X. Hu and C. Zhao, Angew. Chem., Int. Ed., 2022, 61, e202203335 CrossRef CAS PubMed.
- Z. Yang, C. Zhao, Y. Qu, H. Zhou, F. Zhou, J. Wang, Y. Wu and Y. Li, Adv. Mater., 2019, 31, 1808043 CrossRef PubMed.
- Y.-L. Wang, P.-Y. Zhao, B.-L. Liang, K. Chen and G.-S. Wang, Carbon, 2023, 202, 66–75 CrossRef CAS.
- Y. Ma, W. Chen, Z. Jiang, X. Tian, X. WangGuo, G. Chen and Z.-J. Jiang, J. Mater. Chem. A, 2022, 10, 12616–12631 RSC.
- X. Xu, D. Li, Q. Mu, X. Yang, R. Su, Q. Yang, Z. Lei and Z. Yang, ACS Appl. Nano Mater., 2024, 7, 13611–13624 CrossRef CAS.
- H. Chang, Y.-F. Guo, X. Liu, P.-F. Wang, Y. Xie and T.-F. Yi, Appl. Catal., B, 2023, 327, 122469 CrossRef CAS.
- J. Meng, C. Niu, L. Xu, J. Li, X. Liu, X. Wang, Y. Wu, X. Xu, W. Chen, Q. Li, Z. Zhu, D. Zhao and L. Mai, J. Am. Chem. Soc., 2017, 139, 8212–8221 CrossRef CAS PubMed.
- T. Yamamoto, X-Ray Spectrom., 2008, 37, 572–584 CrossRef CAS.
- M. Liu, J. Zhang, H. Su, Y. Jiang, W. Zhou, C. Yang, S. Bo, J. Pan and Q. Liu, Nat. Commun., 2024, 15, 1675 CrossRef CAS PubMed.
- S. Zaman, Y.-Q. Su, C.-L. Dong, R. Qi, L. Huang, Y. Qin, Y.-C. Huang, F.-M. Li, B. You, W. Guo, Q. Li, S. Ding and B. Y. Xia, Angew. Chem., Int. Ed., 2022, 61, e202115835 CrossRef CAS PubMed.
- Z. Luo, X. Li, T. Zhou, Y. Guan, J. Luo, L. Zhang, X. Sun, C. He, Q. Zhang, Y. Li and X. Ren, Small, 2023, 19, 2205283 CrossRef CAS PubMed.
|
This journal is © The Royal Society of Chemistry 2025 |
Click here to see how this site uses Cookies. View our privacy policy here.