DOI:
10.1039/D3GC02373G
(Critical Review)
Green Chem., 2023,
25, 9603-9643
Recent developments in polysaccharide and lignin-based (nano)materials for CO2 capture
Received
2nd July 2023
, Accepted 12th October 2023
First published on 27th October 2023
Abstract
Global warming in 2023 shows no signs of slowing down. The situation alarms scientists, including the Intergovernmental Panel on Climate Change, the international body responsible for regularly developing knowledge on climate change. Indeed, some impacts are already threatening the environment. Today, the average global temperature has increased by about 1 °C compared to the pre-industrial era (1850–1900). At the current rate, the increase in global average temperature will reach 1.5 °C between 2030 and 2052. The greenhouse effect is unbalanced by human activities, in particular the use of fossil fuels (oil, gas, and coal), which lead to the release of greenhouse gases. CO2 represents nearly 2/3 of global greenhouse gas emissions caused by human activities and has the tendency to linger in the atmosphere for a long time. This is why the effect of other greenhouse gases is usually measured in CO2 equivalent. Current CO2 emissions will impact atmospheric concentrations and global temperatures for decades. To date, some solutions have been proposed to deal with this (energy transition, regulation of emissions, etc.). However, most of these solutions have not yet been sufficiently developed and/or do not offset the effects of ever-increasing industrialization on anthropogenic CO2 emissions. As a result, carbon capture and sequestration processes appear to be attractive solutions. CO2 capture can take place by absorption (chemical and/or physical) and/or adsorption (chemisorption and/or physisorption). Various compounds can act as sorbents, among which polysaccharides and lignin have special importance due to their many advantages, the most important of which are biodegradability, availability, relatively cheapness, environmental friendliness, etc. In this review, we report recent studies regarding polysaccharides and lignin-based materials for CO2 capture. Such materials can be in different forms such as composites, aerogels, hydrogels, pellets, heteroatom-doped materials, membranes, metal–organic frameworks (MOFs), porous carbons, etc. These materials are used for CO2 capture through the adsorption or absorption processes.
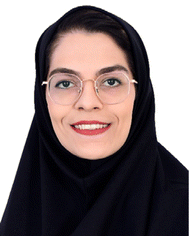 Zahra Nezafat | Zahra Nezafat was born in Iran. She received her MSc in organic chemistry in 2021 from the University of Qom. She is currently pursuing her PhD in organic chemistry at the Iran University of Science and Technology under the supervision of Dr Shahrzad Javanshir and Dr Mahmoud Nasrollahzadeh. Her research interests are mainly focused on the design and the fabrication of biopolymer-based (nano)catalysts and green synthesis of metal nanoparticles applied for the synthesis of organic compounds as well as electrocatalytic applications. |
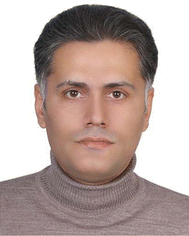 Mahmoud Nasrollahzadeh | Mahmoud Nasrollahzadeh is an Associate Professor at the University of Qom, Iran, and the Director of the Nanobiotechnology Laboratory. Since July 2023, he has been working as a Guest Researcher at TU Dresden, Dresden, Germany. His research program focuses on the application of biowaste and nature-inspired (nano)materials in catalysis, energy conversion, biomass conversion, and the development of novel functional materials; especially chitosan and lignin-based materials. He is the recipient of several research awards including the 2021 Abu Rayhan Prize given by the Iranian Academy of Sciences for the Top Young Chemist of Iran, and the 2020 Distinguished Researcher Award by the Iran Science Elites Federation. He has received research funding from different institutions and corporate entities. |
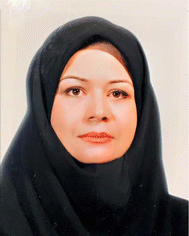 Shahrzad Javanshir | Shahrzad Javanshir (born October 19, 1960) is an Associate Professor in the Department of Chemistry at Iran University of Science and Technology. She received his BS in Chemistry in 1983, and her Master's and M. Phil. in Organic Chemistry in 1984 and 1985, respectively, from Claude Bernard University Lyon I. She received her PhD from Alzahra University in 2007. She has authored over 100 published scientific articles. Her work is focused on synthesizing organic compounds, the development of new bio-based materials, and heterogeneous catalysts. |
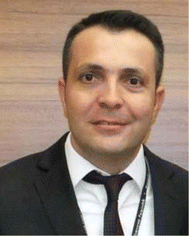 Talat Baran | Talat Baran received his doctoral degree from Aksaray University in 2015. He currently serves as an Associate Professor in the Department of Chemistry at Aksaray University. In his research, he focuses on the synthesis and characterization of various environmentally friendly materials, such as carbohydrate polymers, clay, zeolite, carbon-based materials, etc. He also works on the production of metal and metal oxide nanoparticles supported on these materials, which can function as homogeneous or heterogeneous catalysts. He examines the catalytic activities and reaction mechanisms of these catalysts in various applications, including the treatment of hazardous substances in water/wastewater, different organic transformations, hydrogen production, and microbial fuel cells. Currently, he has 118 publications in international ISI journals and 3 book chapters published by Elsevier. His work has received over 5100 citations, and his h-index is 48. |
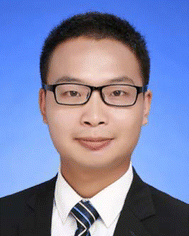 Yahao Dong | Yahao Dong received his Ph.D. from Huazhong University of Science and Technology in 2020. He is currently working at the School of Chemistry and Chemical Engineering, Henan Normal University. His research interest is the synthesis of heterogeneous catalysts for organic reactions and CO2 conversion. |
1. Introduction
Since the end of the industrial revolution (19th century), global warming has been described as being mainly due to human activities leading to the continuous increase in the emission of greenhouse gases including carbon dioxide.1 This translates to a rise in temperatures, which impacts our ecosystem and jeopardizes the living conditions for future generations. In spite of recent awareness regarding global warming, it still remains a major current problem. With the increase in human population, the need for energy also increases. A large part of the world's energy still comes from the combustion of fossil fuels, which leads to the emission of greenhouse gases.2–4 It is commonly accepted that global warming is closely linked to the emission of anthropogenic greenhouse gases, mainly CO2. Increasing the amount of CO2 from 280 to 410 ppm increases the global temperature between 0.6 and 1 °C. There are several sources of CO2 emission, both natural and human, the most important of which are represented in Fig. 1.5–7
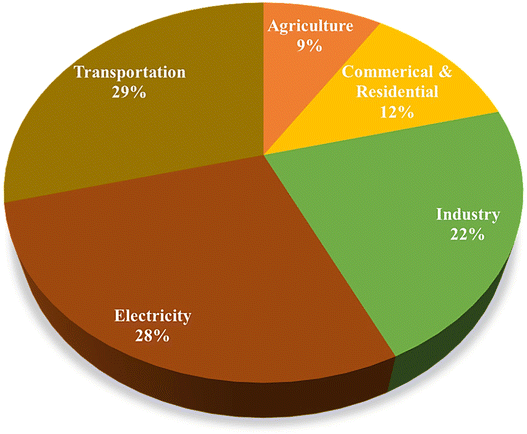 |
| Fig. 1 Schematic representation of different sources and amounts of CO2 emission.5 | |
The increase in the CO2 concentration in the world causes the irregularity of the weather and the rise of the average level of seas and oceans. These factors can endanger life under the seas and the survival of living organisms.2,8 The Intergovernmental Panel on Climate Change has estimated that the concentrations of CO2 in the world will reach 570 ppmv by 2100, which will lead to an increase of 1.9 °C in air temperature and a rise of 3.8 m in average sea and ocean levels.9 To reduce these environmental risks, researchers around the world are studying ways to reduce the amount of CO2. To deal with global warming, in parallel with the efforts undertaken to develop renewable energies and reduce emissions, the capture of anthropogenic CO2 appears to be an essential solution given the still predominant use of fossil fuels. To achieve this, many solutions are being studied, including the use of solid adsorbents.10–16 There are several CO2 capture processes (post-combustion capture, precombustion capture, or oxy-fuel combustion) the main ones being pre-combustion and post-combustion. Although post-combustion is the most restrictive solution in terms of separation due to the low concentration of CO2, it nevertheless remains the most applicable from an industrial point of view since it does not require any modification of the equipment.17 There may be other methods, but they have limitations including expensiveness and excessive energy usage, long processing time, production of side products, etc.18–23 There are some review papers pertaining to the removal of CO2 using different methods.24–30
CO2 capture can take place by absorption (chemical and/or physical) and/or by adsorption (chemisorption and/or physisorption).31–35 Promising materials for CO2 capture include amines as well as porous materials such as MOFs,36,37 metal oxides,38 graphene,39 zeolites,40 synthetic and natural polymers, etc.41–44 Among these, natural polymers or biopolymers are very efficient materials for CO2 capture and polysaccharides have attracted much attention.45–51
Polysaccharides and lignin are important and large groups of biopolymers with many properties such as biodegradability, environmental friendliness, accessibility, low price, etc.52–56 In addition, polysaccharides and lignin have many useful functional groups such as hydroxyl, carboxyl, carbonyl, aldehyde, etc., making them very applicable.57–61 Polysaccharides and lignin-based materials can be obtained in different forms for various purposes such as food-packaging, catalysis, environmental applications, etc.62–68 The properties of polysaccharides and lignin make them very efficient for CO2 capture. Cellulose, alginate, starch, gum, chitosan, and pectin are diverse kinds of polysaccharides, which can be applied for the capture of CO2.69–71 In addition, lignin-based materials can be used for CO2 capture applications.72–76 In fact, the mentioned polysaccharides and lignin have a special chemical structure, which enables them to be used in different forms such as aerogels, composites, N-doped materials, MOFs, membranes, hydrogels, etc. In addition, they can be functionalized with various materials.77–86 These features make polysaccharides and lignin very suitable and effective options for CO2 capture. In this review paper, we report recent studies using alginate, starch, cellulose, chitosan, gum, pectin, and lignin-based materials for CO2 capture. These materials are in different forms such as composites, hydrogels, aerogels, pellets, MOFs, membranes, etc.
2. CO2 capture processes
There are several CO2 capture processes including oxy-combustion, pre-combustion, and post-combustion capture (Fig. 2a). In oxy-combustion process, the combustion is carried out with pure oxygen instead of air, resulting in the production of a CO2/H2O mixture. CO2 is therefore easily captured since it is then sufficient to condense the water to recover CO2. However, the most studied and main processes are pre-combustion and post-combustion. In the pre-combustion, adapted for example to power stations, the coal is first gasified, leading to a high-pressure gas (at a pressure and temperature of about 10 bar and close to 150 °C) composed of H2 (55%), CO2 (38%), N2 (4%), CO (2%), and traces of other species. The hydrogen can then be used to obtain electricity. Afterward, the generated CO2 is separated through chemical and physical absorption processes. The hydrogen-rich fuel can be applied in furnaces, gas turbines, and boilers.13,87 In the post-combustion capture process, the CO2 is captured after combustion in the exhaust gases. The concentration of CO2 in these gases fluctuates between 10 and 30%. CO2 post-combustion capture methods include absorption (amines, ethylene glycol, etc.), adsorption and membranes. Adsorption is a promising technique for CO2 capture owing to its advantages such as simplicity of handling, absence of corrosion difficulties, reduced energy necessity, and cost-effectiveness.9,88 Different adsorbents such as zeolites and carbon-based materials can be used for capturing CO2.89–91 In the absorption process, the capturing of CO2 flue gas occurs by reaction with a chemical solvent, which is usually an amine-based solvent.9 The use of amine-based solvents has some disadvantages such as a low capacity for CO2 capture, high energy price for the recycling of the absorbent owing to the presence of H2O in the solution of amine, thermal degradation, and losses of amines by evaporation.92 Solid amine-based absorbents can be used to overcome the problem caused by soluble amines. The advantage of solid amine-based absorbents over soluble amines is lower energy consumption because the water evaporation step is eliminated. In addition, solid amine-based absorbents have high-capacity performance compared to soluble amines. Nevertheless, these solid sorbents have not been applied on an industrial scale since this knowledge is not yet fully developed.12,93 Another post-combustion capturing technique is membrane separation. A membrane is defined as a permeable and selective barrier, active or passive, separating two media. Under the effect of a driving force, it allows the selective passage of certain compounds in a gaseous and/or liquid mixture. Membrane separation is the ability of materials to control the penetration of different species. One of the advantages of CO2 membrane separation is its continuous mode of operation, unlike absorption and adsorption processes where, once the storage capacity has been reached, the solvent (or solid) must be regenerated. Owing to the exceptional structural properties of CO2, it can reversibly react with Brønsted and Lewis bases such as KOH and amines, respectively.94,95Fig. 2b shows the properties, opportunities, and challenges associated with these techniques.13
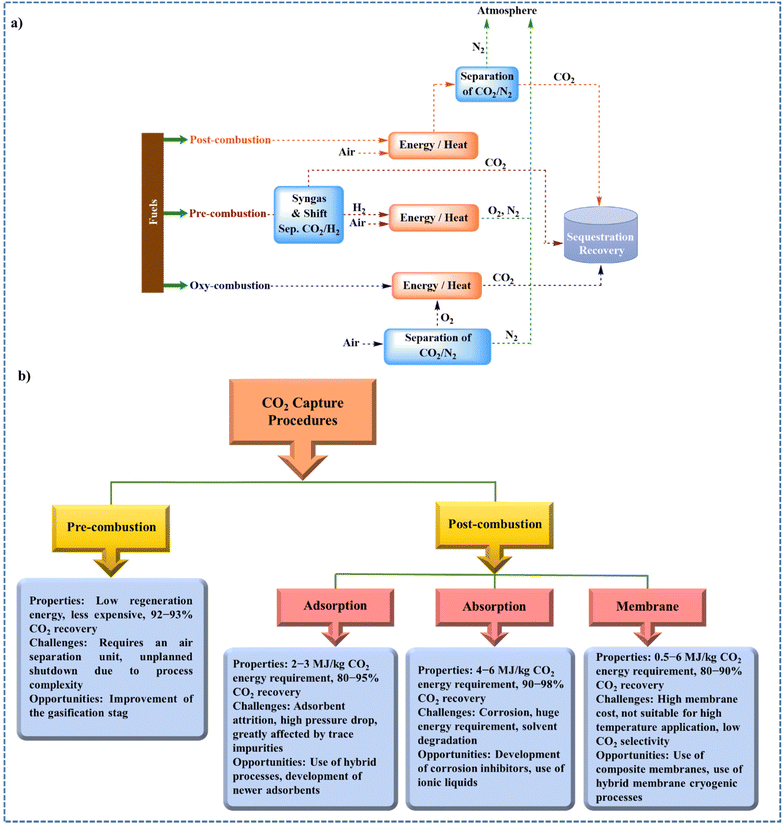 |
| Fig. 2 Schematic representation of (a) CO2 capture processes by post-, pre-, and oxy-combustion and (b) different properties of the two methods for CO2 capture.13 | |
3. Mechanism for CO2 capture
The elimination of acid gases depends on their ability to react with alkanolamines. CO2 reacts with alkanolamines as a Lewis acid at a finite rate, but with variable reaction mechanisms depending on the degree of substitution or steric hindrance of the amine nitrogen. Two main mechanisms have been proposed to explain the reaction between CO2 with primary (R1NH2) and secondary (R1R2NH) alkanolamines; namely, the zwitterion and the Crooks and Donnellan mechanisms.96 In this mechanism, first, the amine reacts with CO2 to form a zwitterion (eqn (1)) intermediate, which then reacts with the base (such as OH−, H2O, or amine) to yield neutral carbamate (eqn (2)).97–102
Unlike the zwitterion mechanism,103 a one-step mechanism has been proposed for the reaction between CO2 with primary or secondary amines simultaneously and the formation of carbamate in a one-step (eqn (3)). In such mechanism, monoethanolamine (MEA) does not function as a proton acceptor.104
Carbamic acid is generated in the other mechanism. In this mechanism, in the first step, MEA reacts with CO2 (eqn (4)). In the second step, the fabricated carbamic acid reacts with another MEA to form the carbamate (eqn (5)).105
| CO2 + RNH2 ⇌ RNH2+COO− | (1) |
| RNH2+COO− + RNH2 ⇌ RNHCOO− + RNH3+ | (2) |
| CO2 + RNH2⋯B ⇌ RNHCOO−⋯BH+ | (3) |
| RNCOOH + RNH2 ⇌ RNHCOO− + RNH3+ | (5) |
Among these mechanisms, the zwitterion mechanism is more considered. In the meantime, it is moreover broadly applied to describe the reaction of CO2 absorption into other solvents, including mixed amines and functionalized ionic liquids.106–108 In a study, Jing and co-workers described the mechanism of CO2 adsorption onto MEA.109 In the first step, the reversible reaction occurs between CO2 (at low loading) and MEA to form the carbamate. Following high CO2 loading, HCO3−/CO32− is formed through the hydration of CO2. In this step, the carbamate is hydrolyzed (Fig. 3a). In addition, the absorption of CO2 can occur in diethanolamine (DEA) and triethanolamine (TEA). CO2 absorption by DEA is similar to that by MEA. However, in the case of TEA, the mechanism is different.110 Tertiary amines do not have the necessary (N–H) bond to form the carbamate ion, and therefore do not react directly with CO2. Thus, Donaldson and Nguyen proposed the mechanism presented in Fig. 3b in 1980, which describes the reaction of CO2 with tertiary amines, followed by the hydrolysis of CO2 to form bicarbonate.111 In a study, Zheng and colleagues investigated the synthesis of SiO2 nanoparticles (NPs) and organic hybrid materials (NOHMs).112 For this purpose, they used SiO2 NPs as core and 3-glycidoxypropyl trime thoxysilane (KH-560) (NOHM-C) or 3-(trihydroxysilyl)-1-propane sulfonic acid (SIT) (NOHM-I) as the corona. Additionally, they used polyetheramine M-1000 (M-1000) as the canopy. The NOHMs applied for CO2 capture and the mechanism are displayed in Fig. 3c. There are three types of active sites for the CO2 capture and storage. In the active site 1, secondary amine groups can react with CO2. In the active site 2, there are other groups, which can react with CO2via Lewis acid–base interactions. In addition, active site 3, which is a potential space between the long organic chains and facilitates the physical adsorption of CO2, can be removed by applying vacuum.
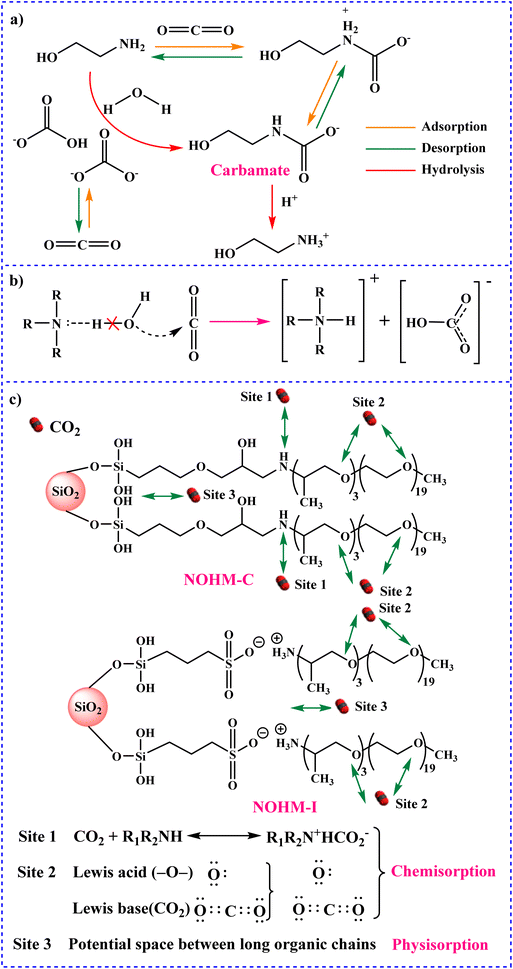 |
| Fig. 3 Schematic representation of the mechanism for CO2 capture using (a) MEA,109 (b) TEA111 and (c) SiO2 NPs functionalized amine.112 | |
4. Current CO2 capture polysaccharides and lignin-based materials
4.1. Polysaccharides-based materials for CO2 capture
4.1.1. Alginate-based materials.
Alginate (another name is alginic acid or align) is a polysaccharide of anionic nature present in the cell walls of brown algae. The two main functional groups are –COO− and –OH. In the acid form, this polysaccharide can be found in different types of salts such as sodium and calcium Alginate. Other properties of alginate include linearity and solubility in water.57,113–115 β-D-Mannuronic and α-L-guluronic acid are two units forming the structure of the alginate. The structure and functional groups of the alginate make this polysaccharide a suitable option for all kinds of applications including drug delivery, tissue engineering, food industry, catalysis, and environmental purposes.116–120 Alginate has advantages such as biodegradability, environmental friendliness, non-toxicity, etc. However, it has disadvantages, including low chemical and thermal stability as well as low mechanical strength.121,122 To overcome these disadvantages and increase its absorption properties, alginate can be modified by different methods and different structures such as composites, hydrogels, aerogels, etc.113,123–125 In this section, we review the CO2 adsorption properties of the different structures of alginate-based materials.
4.1.1.1. Alginate-based composite materials.
One of the most interesting materials for the removal of CO2 is composites. Composites can be synthesized using different materials. For example, Rasoulzadeh and colleagues reported the synthesis of one composite by the functionalization of alginate with amine materials.126 As mentioned earlier, alginate alone has low stability. Therefore, they used biosilica to enhance the thermal stability and mechanical strength of alginate. In addition, for enhancing the adsorption property, they used (3-aminopropyl)triethoxysilane (APTES) to prepare amine-functionalized bio silica/alginate (NH2-SiO2/ALG). The NH2-SiO2/ALG composite was applied for CO2 capture in a fixed-bed reactor. They optimized different parameters such as moisture content (MC), gas flow rate (FR), and temperature. The results displayed that the removal efficiency (RE) of CO2 was 93.08% at optimum conditions including 5%, 40 mL min−1, and 40 °C for MC, FR, and temperature, respectively. In this example, the adsorption capacity and stability of alginate were increased by adding an amine-containing compound. Hosseini and co-workers investigated the preparation of calcined eggshell/sodium alginate (CES/SA) composite.127 They synthesized a gel bead by modification of CES/SA with ammonia and applied it for CO2 adsorption. In the experimental work, they optimized FR, the concentration of CO2, temperature, and pressure. The highest CO2 capture (0.2380 mmol g−1) happened when the temperature, pressure, and concentration of CO2 were 30 °C, 1 bar, and 45%, respectively. In fact, they synthesized eggshell materials using alginate for CO2 capture for the first time.
4.1.1.2 Alginate-based nitrogen-doped materials.
Today, nitrogen-doped materials are one of the most efficient materials for CO2 adsorption. As a result, in a study in 2021, Huang et al. developed a technique for the preparation of N-doped hierarchically porous carbon spheres.128 They synthesized the mentioned materials through co-pyrolyzation of poly(vinylidene chloride) and melamine in an alginate gel bead (Fig. 4a). In this structure, melamine played two roles including a template for the macropore structures and a nitrogen source. The prepared N-doped material was applied for CO2 capture. The innovation of this work is the application of melamine to make gel beads, which also helps adsorb CO2.
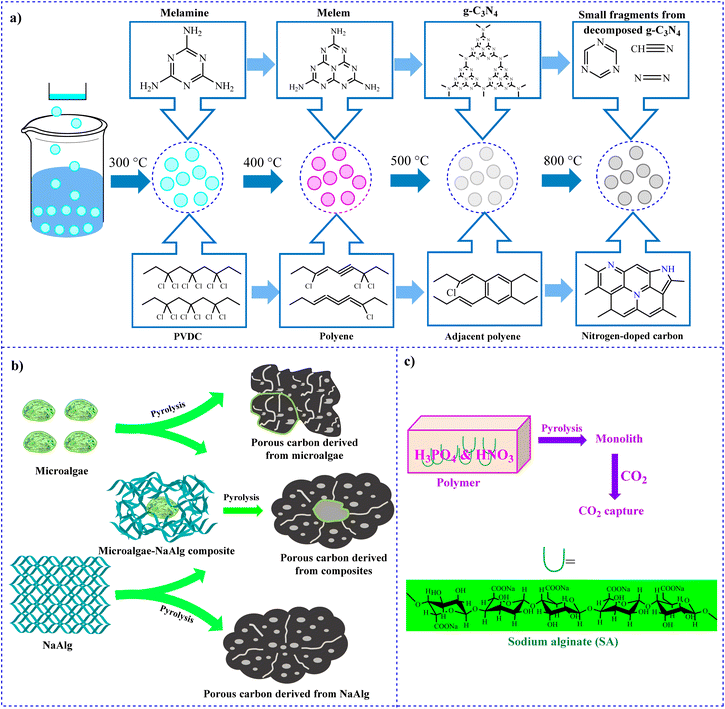 |
| Fig. 4 Experimental procedure for (a) preparation of N-doped materials,128 (b) N-doped-based alginate porous carbon129 and (c) the preparation of the highly porous carbons.130 | |
The preparation of N-doped activated carbon (AC) using microalgae-sodium alginate (NaAlg) was performed by Liu and colleagues in 2018.129 NaAlg has a high nitrogen content and can be applied as an efficient precursor. The N-doped materials showed a high activity for CO2 adsorption owing to high N content and suitable pore size distributions. The adsorption capacity was 3.75 mmol g−1 at the temperature and pressure of 25 °C and 1 bar, respectively. Fig. 4b shows the effect of composition in microalgae-NaAlg. As mentioned, one of the important features of this adsorbent is the large number of nitrogen groups and the proper size of the holes, which helps increase the adsorption of CO2.
Cao and co-workers studied the preparation of N-doped carbon monolith (SA-xN-yP) using binary H3PO4–HNO3 and Na-alginate (SA) as co-activating agents and carbon precursor, respectively (Fig. 4c).130 The x and y in the sample name correspond to the volumes of HNO3 and H3PO4, respectively. The prepared SA-2N-P sample had HSSA (1740 m2 g−1) and CO2 adsorption (8.99 mmol g−1) at 273 K. In addition, at 298 K, the amount of CO2 adsorption was 4.57 mmol g−1. These results indicated that the SA-2N-P sample had high adsorption capacity and selectivity for CO2.
4.1.1.3 Alginate-based MOF materials.
Today, one of the most promising porous materials is MOFs. These materials consist of hybrid materials from organic and inorganic compounds including organic linkers and metals. MOFs have some properties including high specific surface area (HSSA), ease of modification, and suitable pore sizes. Thus, they are widely used today for absorbing and removal of gases. Nevertheless, these compounds may be less effective for CO2 adsorption because the organic rings in the structure of MOF may have a weak affinity with CO2. Therefore, these compounds have been functionalized using nitrogen groups.131–135 For example, in 2021, Xiao and co-workers investigated the synthesis of zirconium-based MOF beads for CO2 capture applications.136 For this purpose, they prepared Zr-based DUT-68 into alginate beads. Gas capture performance was then assessed through CO2 and volatile iodine adsorption. They synthesized DUT-68 beads by cross-linked polymerization of Na-alginate using Ca2+ ions. The prepared composites had HSSA as well as high porosity. The DUT-68@Alginate bead (60% MOF) exhibited a 1.25 mmol g−1 CO2 adsorption capacity at 273 K. In this work, the alginate stability and the adsorption performance were enhanced. In the same year, Salehi and Hosseinifard reported the synthesis of MIL-101-derived nano porous carbon (MDC)/polysaccharides nanocomposite137 using the impregnation of alginate, chitosan, and cellulose on the MDC. They used waste Cr for the synthesis of MIL-101. The prepared nanocomposite was applied for the uptake of CO2 and CH4. In another study, Mondino et al. successfully developed the preparation of MOF and alginate-based sphere, referred to as CPO-27-Ni/alginate spheres, through spray-granulation technique.138 The CPO-27-Ni/alginate spheres were very suitable materials for the moving-bed temp-swing adsorption (MBTSA) process in the post-combustion capture of CO2.
4.1.1.4 Miscellaneous alginate-based materials.
Nanofiber (NF) is one of the types of nano materials, which have HSSA and are broadly applied for the removal of CO2. NF materials can be synthesized through different methods, electrospinning being the most widely applied. Electrospun NFs are used for CO2 adsorption owing to their properties including HSSA, high porosity, suitable pore size, excellent interconnectivity, and mechanical properties.139 In 2022, Suratman and colleagues reported the synthesis of alginate NF using the incorporation of poly(vinyl alcohol) (PVA) in alginate (Alg/PVA NFs) by electrospinning method (Fig. 5a).140 To improve the performance of the alginate NF, they used the impregnation of zeolite (Z) into the solution of polymer (Alg/PVA/Z NFs) (Fig. 5b). The CO2 adsorption capacities of the prepared Alg/PVA NFs and Alg/PVA/Z NFs were 3.286 and 10.710 mmol g−1, respectively. In this example, a combination of zeolite and alginate was used to synthesize a novel composition. In addition, in 2020, Koly and colleagues prepared another type of NF; named alginate/polyethylene oxide/Triton X-100 NFs (Alg/PEO/TX NFs) by electrospinning method.141 They evaluated the CO2 capture capacity of the synthesized NFs. Their results displayed that the optimum adsorption capacity of 12.398 mmol g−1 was achieved using FR and contact time of 10 mL min−1 and 25 min, respectively. The electrospinning method is a novel technique for the preparation of adsorbents.
 |
| Fig. 5 Schematic representation of intermolecular interactions of (a) Alg/PVA NFs, (b) Alg/PVA/Z NFs140 and (c) hydrogen bond between NaAlg and Na-tartrate.149 | |
One of the most efficient biocompounds for CO2 capture is carbonic anhydrase. In fact, using carbonic anhydrase for CO2 capture, the cost and size of the reactor were reduced. A specific form of carbonic anhydrase is the immobilization of it on the reactor, which maintains the suitability of separation and controls the process.142–145 In 2016, Zhu et al. reported the decoration of carbonic anhydrase on the alginate and investigated its effect on the acceleration of CO2 capture in post-combustion.146 The immobilization of carbonic anhydrase on the alginate was carried out using glutaraldehyde cross-linking technique. The batch-scale results exhibited that CO2 adsorption was improved by the addition of immobilized carbonic anhydrase. By immobilization of carbonic anhydrase on the alginate, the operational stability and porosity were increased.
Membranes provide an excellent potential for the capture of CO2 owing to their advantages such as low cost, easy industrialization, small energy necessity, and eco-friendly nature.147,148 In a study, Zhi and colleagues reported a membrane-based CO2 separation procedure.149 For this aim, they used NaAlg and Na-tartrate, which were connected through hydrogen bonds (Fig. 5c). The prepared membranes were applied for the separation of CO2 and N2. In this study, the presence of nitrogen-containing compounds may have increased the efficiency of the adsorbent.
4.1.1.5 Summary of this section.
Alginate has low stability, which necessitates the preparation of alginate-based materials. Regarding the capture of CO2 by alginate, relatively few studies have been carried out and most of them were based on N-doped materials. However, given the capability of alginate to form all kinds of gels; especially hydrogels, novel alginate-based hydrogels can be made for CO2 absorption. Considering that the removal efficiency of composites is higher than that of other structures (93.08% in one case), novel structures can be prepared since alginate has hydroxyl and acid functional groups, which can form composites with various materials. In general, most materials and structures used with alginate for CO2 capture are N-doped and MOF-based materials. In the case of N-doped materials, since there are no amine functional groups in the alginate, which is very important for CO2 capture, these materials are very noteworthy. Furthermore, MOFs are good for CO2 capture owing to their porous structure and the results indicate the considerable effect of the application of alginate on the enhancement of their structure and performance.
4.1.2. Starch-based materials.
One of the most plentiful and low-cost polysaccharides is starch. Starch is fabricated from some plants for the storage of carbohydrates. The natural sources of starch include potato, cassava, rice, maize, wheat, etc. Two types of polysaccharides form the structure of starch including (1,6) α-D-glucan amylopectin and (1,4)-linked α-D-glucan amylose, which are linear and branched, respectively. Starch has different features such as biodegradability, accessibility, and low-price. In the structure of starch, there are many –OH functional groups, making it very useful. Therefore, starch can be applied as a support, stabilizer, template, etc. for different applications.150–153 In this section, we report different studies regarding starch-based materials for CO2 capture.
4.1.2.1 Starch-based nitrogen-doped materials.
In 2022, Lin et al. reported the fabrication of a series of N-doped microporous carbon materials.154 In this research, they used starch as a carbon source, melamine and formaldehyde (MF) as a polymer resin, and KOH as an activator (MF@Cs). The presence of MFs enhances the active site of carbon materials owing to their rich N and O groups. In addition, MFs form 3D networks. At the temperature and pressure of 273 K and 100 kPa, respectively, MF@Cs show great performance for CO2 adsorption with the adsorption capacity of 6.54 mmol g−1. Interestingly enough, they also used resin to make the adsorbent.
In 2021, Park and co-workers prepared two sequences of novel materials including corn starch-derived microporous carbons modified with/without thiourea (Fig. 6).155 For this aim, they used different types of activation materials such as K2CO3, KOH, and K2C2O4. The sample doped with thiourea was more porous than the undoped carbon sample. Thiourea-doped K2C2O4 AC (STO) displayed well-defined micropores. The porous structure of STO considerably improved the performance of STO for CO2 adsorption. The results displayed that the adsorption performance was 269.61 mg g−1 at 0 °C and 1 bar. The innovation of this work was the effect of thiourea on the efficiency of the CO2 adsorbent.
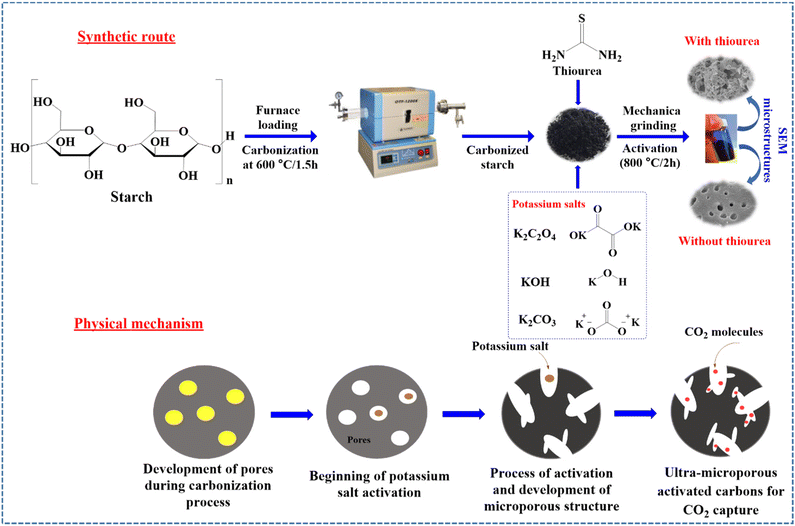 |
| Fig. 6 Schematic representation of the preparation of the undoped/N,S co-doped with different activation salts of potassium starch-derived micro porous carbons and probable activation mechanism. Reproduced from ref. 155 with permission from Elsevier, copyright 2021. | |
Isahak et al. reported the fabrication of an N-doped porous carbon hybrid from starch (SH800).156 In this study, they investigated the CO2 capture capacity of SH800. The results displayed that SH800 had an excellent CO2 capture capacity of 29.8 wt% for biohydrogen gas adsorption.
4.1.2.2 Starch-based pellets materials.
Preparation of sorbent pellets using Ca-based sorbents with a starch pore via the extrusion–spheronization method was performed by Han and colleagues.157 For this aim, they used starch and cement as template and stabilizers, respectively. Their results exhibited that the optimum uptake of CO2 was achieved using 10 and 20% of starch and cement, respectively. The 0.15 g g−1 CO2 capture was achieved after 20 cycles.
In 2021, the synthesis of monolithic porous nanostructures of CaO–MgO composites using a self-sustained combustion reaction of molded pellets was performed by Nethravathi and colleagues.158 For this purpose, they used a mixture of starch, nitrate salts of calcium and magnesium, and urea. The starch was applied as a binder and template and urea was used as fuel. Porous monoliths had high CO2 capture at 650 °C in a 20% CO2 gas stream. However, the adsorption capacity of the CaO–MgO porous nanostructures was 67–51 mass% of the sorbent.
4.1.2.3 Other starch-based materials.
Tan et al. reported the fabrication of AC from carbonized gelatin and starch biomass using the dry chemical activation approach.159 The synthesized samples had gelatin (G) and starch (S), activated by KOH (K), G and S being mixed with different amounts (y) at 700 °C and were referred to as GSKy-700. The results displayed considerably excellent CO2 adsorption (7.49 mmol g−1 at 0 °C and 1 bar) by GSK1-700. In another study, Fuertes and Sevilla prepared porous carbons using the chemical activation of hydrothermally carbonized starch and cellulose as well as sawdust biomass.160 The samples prepared were used as sorbents for the capture of CO2. The samples produced under mild activation conditions (KOH/HC = 2) performed well, showing a high capacity for CO2 uptake. In addition, the samples synthesized at 600 °C had a high capacity (4.8 mmol g−1 at 25 °C and 1 atm) for storage of CO2 at ambient temperature.
4.1.2.4 Summary of this section.
Starch has been mainly used as a carbon source and in most cases, carbonized and used as a source of AC. Starch has been used as a template, but not widely used to make CO2 capture materials. Thus, studies in this area are scarce and there is much to be done including starch-based, N-doped, and pellet materials. As a suggestion for future studies, starch can be used to fabricate composites using the combination of starch and MOF to increase the adsorption capacity of fabricated materials for CO2 capture.
4.1.3 Gum-based materials.
Gum is made up of many hydroxyl groups and is found in a variety of sources such as seeds, trees, and aquatic weeds. Gums are made from trees including Arabic, Kondabolu, karaya, tragacanth, Gum Ghatti, etc.58 Gums are well-known natural polysaccharides made of sugar and are frequently utilized in the industry owing to their biocompatibility, odorlessness, non-toxicity, solubility in water, renewability, cost-effectiveness, and accessibility.81,161 In this part, we review recent studies on gum-based materials for CO2 capture application.
4.1.3.1 Gum-based pellet materials.
In a study, Hussin and co-workers utilized to synthesize high-quality carbon pellets. AC was combined with organic binders such as tapioca starch (TS) and xanthan gum (XG) to produce pellets.162 Both kinds of carbon pellets (TS-AC and XG-AC) continued to yield a high carbon content after the addition of water and the binder. Given their many functional groups, a longer breakthrough time, and a higher CO2 adsorption capacity compared with xanthan gum, carbon pellets made with tapioca starch performed better than those prepared using xanthan gum. In comparison to XG-AC pellets (16.86 mg g−1), TS-AC carbon pellets had remarkably high breakthrough time and CO2 adsorption capacity of 16.2 min and 21.84 mg g−1, respectively, at 25 °C. The innovation of this work is that two types of biopolymers have been used for the synthesis of adsorbents.
4.1.3.2 Other gum-based materials.
In another study, Tasmanian Blue Gum (TBG) tree bark was chosen by Prasankumar et al. as the starting material for producing activated porous carbon utilizing an easy KOH activation and carbonization procedure.163 For CO2 collection from concentrated sources and diluted 4% CO2 simulated flue streams, AC-TBG was used. With a 1.6 mmol g−1 working capacity at 40 °C and 4% of CO2, AC-TBG demonstrated exceptional CO2 absorption (4.5 mmol g−1) at 0 °C and 1 bar for pure CO2.
4.1.3.3 Summary of this section.
There are very few examples of gums-based materials for CO2 capture (only 2 studies are available). In these examples, gum has been used as a source for making AC. In general, the application of gums to make materials capable of capturing CO2 is not very efficient. However, the structure of gum is similar to that of alginate such that it can easily form a gel and hence it can be very effective in making hydrogels. Thus, one of the issues, which should be addressed in the future is the preparation of hydrogels based on different types of suitable and effective gums for CO2 capture. The structure of these hydrogels must be such that amine groups are located on the top so that they can have a high efficiency for CO2 capture.
4.1.4 Pectin-based materials.
Pectin is a complex polysaccharide made up of linear -(1,4) galacturonic acid residues connected throughout the chain by -(1−4) glycosidic links with hydroxyl and carboxyl groups.164,165 Fruit peels and many plant cell walls contain pectin. Considering its capacity to form aqueous gels, it is employed as a stabilizer in the food industry. The biocompatibility, biodegradability, non-toxicity, hydrophilicity, and flexibility of pectin make it suitable for biomedical and cosmetic uses.166
4.1.4.1 Pectin-based other materials.
In 2022, to prepare micro–mesoporous carbon powders, which are both oxygen and nitrogen-loaded, Vafaeinia et al. used pectin and melamine as the corresponding organic precursors.167 Given its unique micro–mesoporous structure and abundance of basic nitrogen-containing functionalities, at 273 K at 1 bar, the ideal porous carbon had CO2 adsorption capacities of up to 3.1 mmol g−1.
Jovellana and Pajarito demonstrated the viability of pectin as the foundation for amine functionalization by coating it on zeolites for CO2 absorption.168 Pectin has been successfully modified using NH3 and triethylenetetramine (TETA) as alternative amine-functionalized coating agents and coated on substrates such as zeolites for CO2 uptake. Adsorbents coated with NH3 and TETA-modified pectins had adsorption capacities of 2.24 and 2.28 mmol g−1 at 5% breakthrough, respectively. In this study, zeolite was used along with pectin for better efficiency. Moreover, in 2016, pectin was used as the primary starting material to synthesize nanoporous AC in a two-step method through hydrothermal carbonization of a pectin water dispersion at 230 °C, followed by chemical activation with KOH at 700 °C. At 1 atm and room temperature, this material had a considerable CO2 capture capability of 13–7 mmol g−1.169
4.1.4.2 Summary of this section.
In the field of CO2 capture, pectin is often used as a functional biopolymer to make porous activated carbon. Nitrogen-enriched pectin, prepared by functionalization with various amine materials, exhibits high efficiency for CO2 capture since the obtained porous sorbent is enriched in both oxygen and nitrogen.
4.1.5 Chitosan-based materials.
The only naturally occurring polysaccharide with an amino group, chitosan (CS), is prepared by deacetylating chitin, which is found in abundance in nature. Over 10 billion tons of chitin are produced by biosynthesis each year, and after cellulose, it is the most frequently occurring biopolymer in nature, which is found in the shells of crabs and shrimp, fungi, and insects.170,171 As a natural biopolymer, CS has several inherent benefits, including affordability, biodegradability, biocompatibility, non-toxicity, and effective sorption capabilities. In particular, the free amino-hydroxyl groups give CS features including antibacterial activity, chelating with heavy metals, protein affinity, solubility in water, and most significantly, the simplicity of processing and modification.166,172,173 CS has a strong adsorption capacity. However, given its low reusability, weak mechanical properties, and ease of solubilization in acids, its applicability is limited.170 Nevertheless, these limitations can be resolved by chemical or physical modifications. In addition to enhancing mechanical strength and adsorption capabilities, physical and chemical modifications can prevent the dissolution of CS in strong acids. Physical modification often involves combining (derivatives) CS with other materials or transforming it into distinct forms, including membranes, microspheres, fibers, gels, and porous particles without altering the inherent features of CS.174 Given the capability of CO2 molecules to hop between the matrix's arbitrary openings, CS is anticipated to allow selective CO2 permeation due to the basic amino groups present in the polymeric chain (Fig. 7).175,176 In this section, we have reviewed the CO2 adsorption features of different CS-based materials such as composites, membranes, hydrogel, etc.
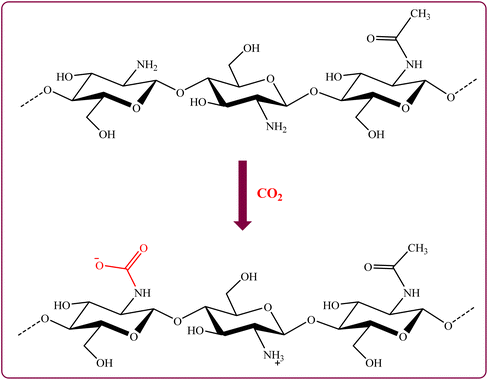 |
| Fig. 7 Adsorption of CO2 molecules by CS. | |
4.1.5.1 Chitosan-based aerogel materials.
To prepare aerogels with high CO2 absorption, much research has been carried out. For example, in 2021, using a phase inversion technique followed by freeze-drying, Luzzi et al. were able to successfully embed zeolite 13X (ZX) powder in the CS framework to prepare composite aerogel beads (Fig. 8).177 This method completely utilized the potential of the constituents, resulting in a sample with 561 m2 g−1 HSSA and 4.23 mmol g of CO2 uptake capacity for the sample containing 90% zeolite. The beads were coherent, mechanically stable, and reusable after regeneration using a gentle pressure swing technique, and had an exceptional ability to adsorb CO2. In this study, the presence of zeolite has increased the efficiency of the adsorbent due to its porous structure.
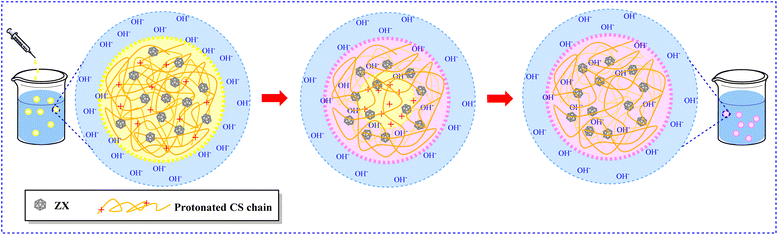 |
| Fig. 8 Production of the hydrogel beads by the phase inversion method.177 | |
Furthermore, in 2021, Liu and colleagues developed a model high-strength hydrogel and aerogel using CS and lithium sulfonate double networks using an electron beam.178 The aerogels had a double network structure with CO2-philic properties, which gave them a porous structure and 67.9 mg g−1 CO2 capture capacity at 0.1 MPa and 298 K, indicating that they had a HSSA of 114.18 m2 g−1. Applications for harvesting CO2 in real-world settings are feasible because of the physical and chemical strength of the aerogel. The innovation of this is the shape of the adsorbent structure, which is in the form of a double network structure.
A unique GO/Laponite® RD/CS was prepared by Du and co-workers.179 Ternary composite produced using the freeze-drying and sol–gel methods was then employed as a CO2 adsorbent. Aerogel-type solid amine adsorbent had a CO2 adsorption capacity of 78.9 mg g−1 and was capable of both physical and chemical adsorptions. This adsorbent had several advantages, including inexpensive starting materials, environmental friendliness, and a comparatively high adsorption capacity.
According to the research by Hsan and co-workers in 2019, CS-grafted GO aerogels have a wide surface area, high porosity, and a significant number of amine groups, which allow CO2 adsorption gas. At 1 bar, CS-grafted GO aerogels had an approximate adsorption capacity of 0.257 mmol g−1.180 To reversibly capture CO2 from the environment through humidity swing, Song et al. employed cost-effective quaternized CS (QCS)/PVA hybrid aerogels containing quaternary ammonium groups and hydroxide ions (Fig. 9a). The capability of QCS/PVA hybrid aerogel to extract CO2 was predicted to be 0.18 mmol g−1 in the temperature range of 10–30 °C (Fig. 9b).181
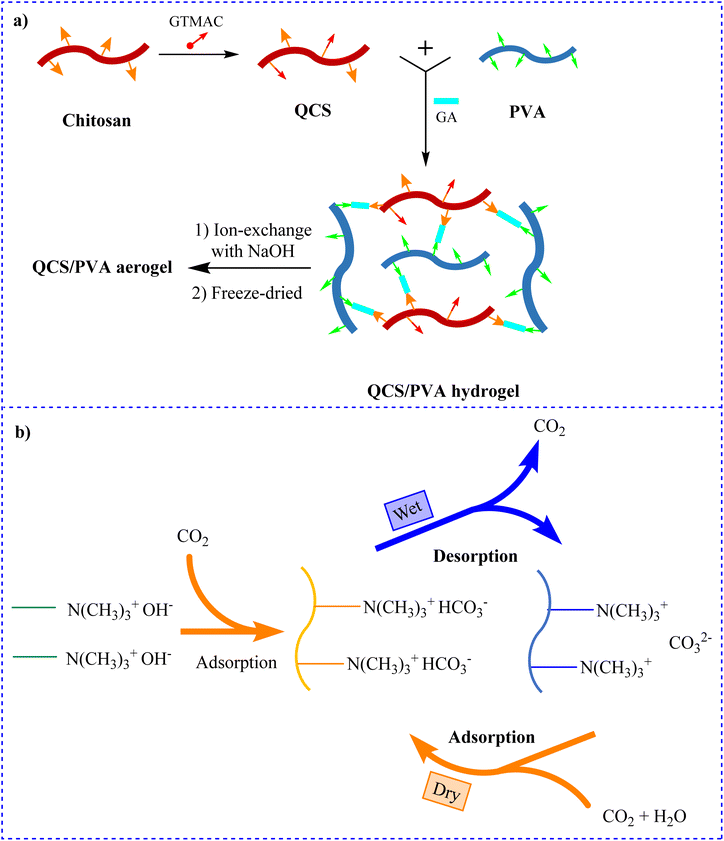 |
| Fig. 9 (a) Preparation of QCS/PVA hydrogel and QCS/PVA aerogel181 and (b) adsorption of CO2 by humidity swing.181 | |
Alhwaige et al. synthesized MMT-CTS-PBZ nanocomposite aerogels using biobased CS-poly benzoxazine (CTSPBZ) as a precursor for high CO2 adsorbing carbon aerogels and montmorillonite (MMT) to reinforce the CTS-PBZ aerogel.182 MMT-CTS-PBZ aerogels were prepared using the freeze-drying method and subsequently cross-linked by the ring-opening polymerization of benzoxazine and carbonization at 800 °C. Even at high pressure, polybenzoxazine enhanced the structural stability for CO2 removal from the environment. The carbon aerogels had strong reversible CO2 adsorption–desorption activity by a maximum of 5.72 mmol g−1 and mesoporous materials with pore sizes in the 2–7 nm range, high BET surface area, and mesoporous materials. The innovation of this work was the application of MMT along with chitosan to make the absorbent. In another study in 2013, CS, an environmentally safe biopolymer was combined with varying concentrations of GO by Alhwaige et al. to develop hybrid monolith aerogels. The adsorption capacities of the aerogels for CO2 collection were investigated. Upon the addition of 20 wt% GO, the quantity of CO2 adsorbed at 25 °C increased from 1.92 to 4.15 mol kg−1.183 In fact, the addition of GO significantly improved the adsorption capacity.
4.1.5.2 Chitosan-based composite materials.
In the conversion of CO2 to valuable products, in 2018, Kumar et al. studied CO2 adsorption and its conversion to cyclic carbonates in the absence of any solvent using an environmentally friendly method based on CS/GO nanocomposite film. At 4.6 bar, a CSGO nanocomposite with an adsorption capacity of 1.0152 mmol g−1 was reported.184 In this study, after adsorbing CO2, it was converted into carbonate products, which is an interesting innovation.
4.1.5.3 Chitosan-based hydrogel materials.
One method for CO2 capture is the use of hydrogels, which are made of a polymeric network. In 2021, Kunalan et al. examined the gas transport properties of hydrogel CS and CS-polyethylene glycol (CS + PEG) polymer mix surface-modified poly-vinyl trimethyl silane (PVTMS) composite membranes for pure CO2, N2, and CH4 gases.185 The transmembrane pressure of 76 cmHg and the reaction temperature of 30 °C, which were the optimal conditions, allowed the CS + PEG-modified PVTMS membranes to achieve an acceptable CO2 permeability of 153 barrer. The innovation of this work is the application of a mixed polymer matrix to make membranes. In another study, Wen and colleagues prepared a unique bimetal-based inorganic–carbonic anhydrase hybrid nanoflower (CANF), which immobilized carbonic anhydrase using bimetal ions (Cu2+ and Zn2+) rather than individual metal ions. These CANF composites were then embedded into PVA/CS hydrogel membranes (PVA/CS@CANF) to produce a new decorated carbonic anhydrase for CO2 capture.186 Exceptional mechanical strength, great catalytic performance, and ease of flow were all characteristics of the PVA/CS@CANF hydrogel membranes. PVA/CS@CANF, in particular, might effectively absorb CO2. CaCO3 production by PVA/CS@CANF was 9 and 2-fold more than those of free carbonic anhydrase and CANF, respectively. Consequently, there may be a lot of potential applications for bimetallic-based protein hybrid hydrogel membranes in CO2 capture.
4.1.5.4 Chitosan-based membrane materials.
Technologies employing membranes to capture CO2 have the following advantages: they use less energy, are easier to design and operate, and have superior thermal and mechanical stability. In 2022, Li et al. fabricated thin-film composite (TFC) membranes with piperazine (PIP) solution and carboxymethyl chitosan (CMC) chains, which have water-swelling properties, using interfacial polymerization (IP) to enhance the performance of CO2 separation (Fig. 10a)187 This research proposed a quick and efficient way to adjust the membrane shape and improve assisted transport. The application of CO2/N2 mixed gas, PIP/TMC, CMC/TMC, and PIP-CMC/TMC membranes was also investigated. For CO2 capture from flue gas, PIP-CMC/TMC membranes with octopus-branched nanostructures exhibited good CO2 permselectivity and offered a wide range of potential applications.
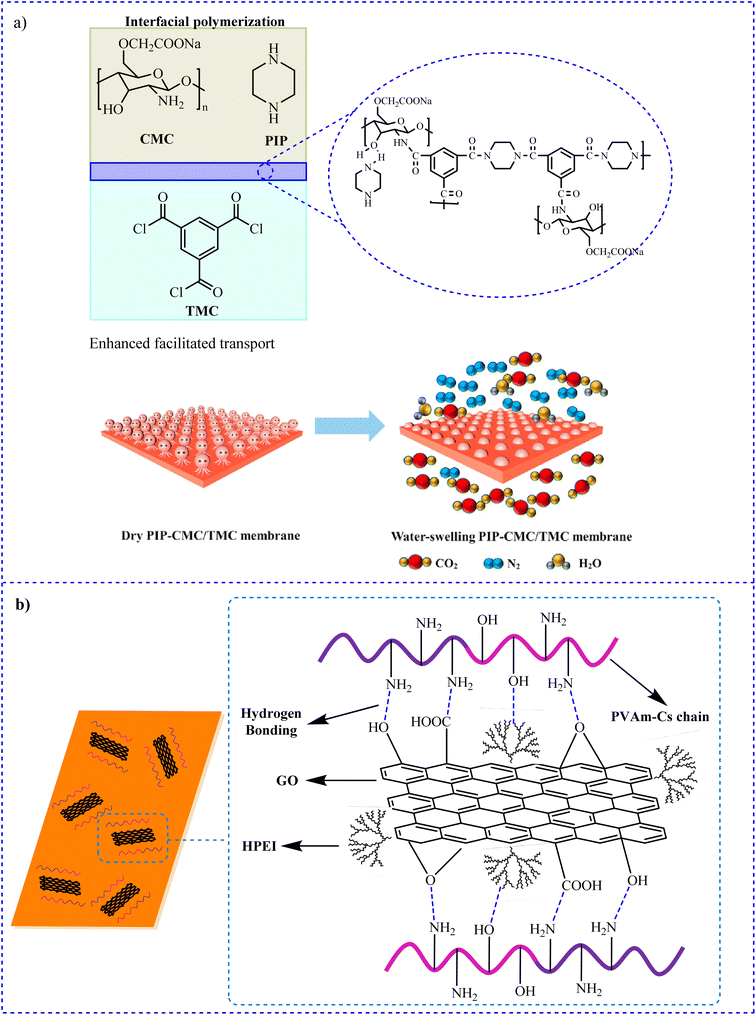 |
| Fig. 10 Preparation of (a) PIP-CMC/TMC membranes. Reproduced from ref. 187 with permission from Elsevier, copyright 2022 and (b) HPEI-GO/CS-PVAm/PS membranes.188 | |
Shen et al. fabricated a transport mixed matrix membranes via the surface coating process by dispersing GO grafted with hyperbranched polyethylenimine (HPEI-GO) nanosheets in CS cross-linked with polyvinyl amine (PVAm) polymer matrix solution for CO2/N2 separation (Fig. 10b).188 The maximum CO2 performance was 36 GPU in a 2 wt% HPEI-GO membrane, while the best CO2/N2 selectivity was 107 in a 3 wt% HPEI-GO membrane.
4.1.5.5 Chitosan-based MOF materials.
Due to their advantages, MOFs, a type of hybrid nanoparticle material, have attracted a lot of attention. Using a packed bed column and a gas mixture containing 15% CO2 and 85% N2, Singo and co-workers impregnated a sodalite zeolite-like MOF (sod-ZMOF) with CS in 2017 and studied its capability of absorbing CO2.189 At a temperature of 25, an FR of 25 ml min−1, and a pressure of 1 bar, Sod-ZMOF-CS showed maximum adsorption capacity of 978 mg g−1. In this study, sodalite, which is a scarce mineral, was used in the preparation of the absorbent.
Using mathematical modeling, Yoro et al. studied the behavior of Sod-MOFs/CSs as an adsorbent for post-combustion CO2 absorption.190 Sod-ZMOF/CS demonstrated a two-stage adsorption process with an initial quick CO2 absorption and a later sluggish CO2 adsorption process under various adsorption temperatures. The tests performed to validate these models were carried out at temperatures of 30, 45, and 60 °C, an operating pressure of 200 kPa, a gas FR of 2.5 mL s−1, and a mass of adsorbent of 0.1 g.
4.1.5.6 Chitosan-based heteroatom-doped materials.
Malini and co-workers prepared N-doped porous AC using CS and hexamethylenetetramine (HMT) (in ratios of 1
:
1 and 1
:
3 wt/wt) as the carbon precursor and an additional nitrogen source, respectively.191 The CS/HMT-derived AC had a larger N-content and enhanced thermal stability, but as the HMT content increased, the surface characteristics decreased. At 25 °C, the CO2 adsorption of AC produced from CS was determined to be 97.98 mg g−1, compared to 72.95 and 55.11 mg g−1 for AC/HMT (1
:
1) and AC/HMT (1
:
3), respectively.
In another study, CS and NaNH2 were used by Yang et al. to synthesize N-doped under solvent-free conditions.192 At 273.15 K and 100 kPa, the adsorption capacity of CO2 reached 6.33 mmol g−1. Using N-doped porous carbon as a promoter, CO2 could be converted into various formamides with good yields in the absence of metals. These CS-based N-doped porous carbons are therefore possible candidates for CO2 capture and conversion due to their good uptake of CO2, great reactivity, the cost-effectiveness of the precursor, and simple production method. The novelty of this work was the preparation of the absorbent in the absence of solvents.
Li et al. prepared N-doped carbon nanosheets using various activators such as KOH, KAc, K2CO3, KHCO3, and CS derived from biomass as a carbon precursor.193 The materials produced by KOH activation (CN6-750-KOH) demonstrated a remarkable CO2 adsorption capacity of 3.91 mmol g−1 at 298 K and 1 bar. Surprisingly, a carbon activated via KAc (CN6-750-Kac), performed comparably to CN6-750-KOH, attaining a CO2 capture capacity of 3.54 mmol g−1. In this study, different types of activators were used.
Preparation of the N,P co-doped porous carbon materials (NPPCs) with phytic acid (PA)-induced self-assembled CS materials was performed by Xiao and colleagues through pyrolysis and activation processes.194 PA works as a P source, an acid regulator, and a structure-directing agent to form more pores with enhanced activation efficiency. A small amount of NaNO3 is concurrently utilized as a template and an activator. The as-prepared NPPCs, which are bifunctional carbon materials, performed well at adsorbing CO2 and storing electrochemical energy. NPPC-0.75-600 showed CO2 adsorption capacities of 5.31 and 3.02 mmol g−1 at pressures of 500 and 100 kPa, respectively.
He and colleagues synthesized AC by carbonizing rice husk, followed by activation with KOH. KOH activation was carried out concurrently with surface modification using CS as a nitrogen source.195 At 273 K and 1 bar, with a CO2 adsorption activity of 5.83 mmol g−1, CAC-5 (modified AC) outperformed AC-5 (generic AC) due to the formation of CO2-philic active sites on the surface of the modified AC by N-species.
To fabricate N,S co-doped carbons (NSCDCs), Shi et al. developed a unique and simple strategy through the chemical blowing process.196 Carbon and nitrogen were provided by CS while sulfur was supplied by hydroquinonesulfonic acid potassium salt (HAPS), which was also utilized as the blowing agent (Fig. 11a). By carbonizing, a combination of CS and HAPS in one step, NSCDC with a hierarchically porous structure was produced. At pressures of 20 and 1 bar and temperature of 25 °C, the best CO2 uptakes were 12.9 and 2.4 mmol g−1, respectively.
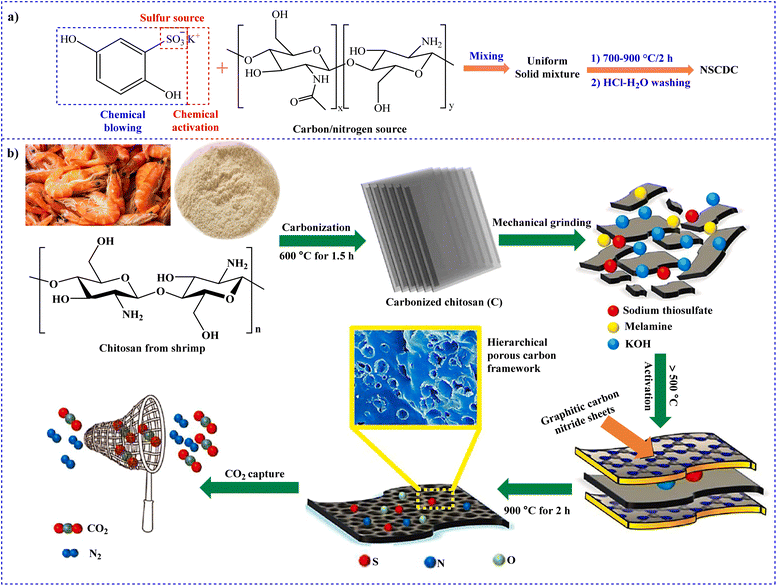 |
| Fig. 11 Synthesis of (a) NSCDC196 and (b) N,S,O doped hierarchical micro porous carbons from CS. Reproduced from ref. 197 with permission from Elsevier, copyright 2021. | |
Nazir et al. designed a sequence of non-doped/heteroatom (N,S,O)-doped porous carbons by a two-step pyrolysis-KOH chemical activation after extracting CS from used shrimp shells by deproteination and deacetylation methods (Fig. 11b).197 At 273 K and 1 bar, the as-prepared material exhibited outstanding CO2 adsorption capacity (236.8 mg g−1).
In 2019, using CS (NCS-T) and glucose (NCSNH3-T) as the starting materials, Wu et al. synthesized two kinds of carbon microspheres with abundant porous N-containing groups utilizing practical and affordable methods.198 Due to the micropores and ultramicro pores formed, the CO2 adsorption capacities of NCS-T and NCSNH3-T were 51–141 and 180–243 mg g−1, respectively. In this study, two types of starting materials were used to synthesize N-containing materials.
Fujiki and Yogo prepared extremely porous N-doped AC (NACs) via chemical CS activation using alkali carbonates.199 1.6 and 4.9 mmol g−1 CO2 capacities were displayed by the NACs at temperatures and pressure of 25, 15 °C and 100 kPa, respectively. At low partial pressures, the addition of N-doped improved CO2 adsorption. Furthermore, Fan and co-workers used CS and K2CO3 as a precursor and activator, respectively, to prepare N-doped porous carbons for CO2 capture.200 These porous carbons exhibited high CO2 adsorption capacity. In particular, the sample prepared using K2CO3/CS = 2 at 635 °C showed a considerably high CO2 capture capacity of 3.86 mmol g−1 at temperature and pressure of 25 °C and 1 atm., respectively. In another study, Thote et al. used CS as the biopolymer template to produce N-doped mesoporous alumina. At 55 °C, the adsorption capacity was 29.4 mg g−1.201 At 55 °C, this value was 4 times higher than that of commercial mesoporous alumina. This increased CO2 adsorption is caused by the basicity of the alumina surface in combination with the nitrogen in the template in the synthesized sample.
Table 1 shows further examples of CO2 capture technologies based on chitosan-based polymers.
Table 1 Chitosan-based materials for CO2 capture
Entry |
CS-based sorbent |
Operating conditions (temperature and pressure (bar)) |
Capacity (mmol g−1) |
Ref. |
Hydrothermal carbonization of CS.
Hierarchical porous nitrogen-containing AC derived from CS.
CS grafted multi-walled carbon nanotube.
Cu-BTC-integrated CS/PVA nanofibrous membranes.
CS-bleaching earth clay composite.
CS based meso-tetrakis(4-sulfonatophenyl)porphyrin.
Polyethylenimine-functionalized porous CS.
Amine-functionalized AC with CS.
AC impregnated CS.
|
1 |
NaOH@CS-Fe3O4 |
25 °C and 9 |
3.21 |
202
|
2 |
CM-Cs in BMI·OAc |
r.t. and 1 atm |
2.32 |
203
|
3 |
Biochar derived CS |
0 °C and 1 |
4.11 |
204
|
4 |
HTC of CSa |
25 °C and 1 |
4-Fold |
205
|
5 |
N-ACs from CSb |
0 °C/25 °C and 1 |
7.9/5.6 |
206
|
6 |
CSMWCNTc |
298 K and 1 |
1.92 ccg−1 |
207
|
7 |
TiO2-grafted CS film |
— |
— |
208
|
8 |
CNFs/Cu/BTC-3d |
298 K and 100 kPa |
9.5 cm3 g−1 |
209
|
9 |
Micro porous carbons from CS |
273 K and 1 |
280 mg g−1 |
210
|
10 |
Micro porous carbons from CS |
0 °C and 0.15 |
17.3–22 |
211
|
11 |
Furfuryl-imine-CS fibers |
295 K and 0.610 |
0.978 |
212
|
12 |
CS-derived mesoporous carbon |
100 °C under atmospheric pressure |
3.72 |
213
|
13 |
Chi-BEe |
38.13 °C |
344.98 mg g−1 |
214
|
14 |
CS/MWCNT |
45 °C and 1.1 |
3 mg g−1 |
215
|
15 |
CS-TPPSf |
— |
0.9 |
216
|
16 |
Triphenyl amine CS derivative |
5 |
0.85 mmol/mmol |
217
|
17 |
CS/mesoporous silica |
25 °C and 1 atm |
0.98 |
218
|
18 |
PEI-CS beadg |
313 K and 15 kPa |
2.3 |
219
|
19 |
AC-CSh |
298 K and 40 |
13.65 |
220
|
20 |
CGACi |
— |
0.25 mol kg−1 |
221
|
21 |
CS modified CMK-3s |
— |
— |
222
|
22 |
Graphitic carbons derived from CS |
0 °C and atmospheric pressure |
5 |
45
|
23 |
Zeolite ZY-chitosan composite |
4.6 |
1.7 |
223
|
24 |
CS/ZIF-8 composite |
275.15 K and 500 kPa |
3.6 |
224
|
4.1.5.7 Summary of this section.
Chitosan is a natural polymer containing an amine functional group. On the other hand, it can form various types of gels. As a result, many studies have been conducted in the field of CO2 capture using chitosan-based materials. In the field of chitosan-based gels for CO2 capture, two studies have been performed using hydrogels and aerogels. Moreover, chitosan is capable of forming Com with other materials. However, there is still much work to be done in the future. Membranes are also effective materials for CO2 capture and chitosan has been used to make membranes. Of course, membranes are mostly used when there is a mixture of several gases. The combination of chitosan and MOFs has also been reported to have a relatively high adsorption capacity. As pointed out at the beginning, chitosan possesses an amino functional group. However, there are relatively many studies on the application of chitosan-based N-doped materials for CO2 capture. This shows that the presence of amine groups is useful and necessary for the capture of CO2. In addition, and the studies in this field show the high adsorption capacity of CO2 in these materials.
4.1.6 Cellulose-based materials.
The most common polymer on earth is cellulose, a linear polysaccharide. Natural cellulose fibers may be found in materials such as cotton, linen, and wood. These materials are reasonably priced, biodegradable, and biocompatible.225–228 Linear homopolysaccharide cellulose, with the chemical formula (C6H10O5)n, is built of β-D-anhydroglucopyranose units and possesses a hydrogen bond because of the electrostatic interactions between hydrogen and oxygen atoms. This hydrogen bond reduces the solubility of cellulose in polar liquids.229,230
As shown in Fig. 12, some examples of nanocelluloses are cellulose nanofibril (CNF), cellulose nanocrystal (CNC), cellulose nanocomposite, and bacterial cellulose (BC).231,232 Low mechanical properties, poor microbiological resistance, and limited porosity are only a few of the challenges associated with the practical application of cellulose. Several conventional methods, including physical adsorption and surface chemical alterations, have been developed over time to provide various functions on cellulose materials.233–236 The CO2 adsorption characteristics of several cellulose-based materials, including hydrogel, composites, membranes, etc., have been reviewed in this part.
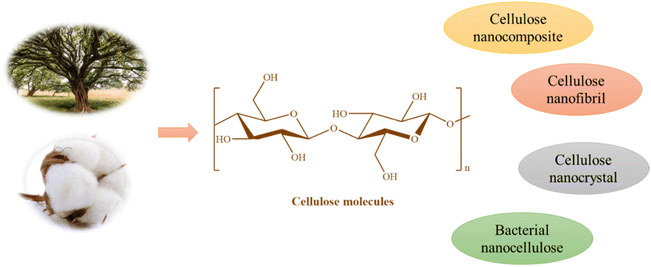 |
| Fig. 12 Types and structure of cellulose. | |
4.1.6.1 Cellulose-based composite materials.
To investigate the impact of packing materials on the efficiency of cryogenic CO2 removal from natural gas, in 2019, Babar and colleagues used three different types of packing materials; namely, spherical glass beads, cellulose acetate (CA) monofilament and hollow fibers, and composite CA/NH2-MIL-101(Al) hollow fibers.237 In addition, it was found that the composite CA/NH2-MIL-101(Al) hollow fibers collected CO2 more effectively than glass beads and pure CA fibers. Additionally, it was found that the CO2 removal efficiencies of composite hollow fibers were 141.9 and 9.5% higher than those of spherical glass beads and pure CA hollow fibers, respectively. In another study in 2016, Gunathilake et al. developed amidoxime-functionalized microcrystalline cellulose (MCC)-mesoporous silica composites using a two-step procedure. At first, in the presence of Pluronic P123 triblock copolymer under acidic conditions, solvent evaporation-induced self-assembly of MCC, tetraethylorthosilicate, and (3-cyanopropyl)triethoxysilane produced MCC-mesoporous silica containing cyanopropyl groups (MCC-CP).238 The material was then treated with hydroxylamine hydrochloride in a further step to convert the cyanopropyl groups into amidoxime functionalities and generate a mesoporous MCC-AO composite. At a high temperature of 120 °C, they achieved the remarkable CO2 adsorption capacities of 2.15–2.41 mmol g−1 (MCC-CP) and 2.84–3.85 mmol g−1 (MCC-AO).
4.1.6.2 Cellulose-based MOF materials.
MOFs have been broadly employed as adsorbents for CO2 adsorption and separation. For example, Jabbar et al. prepared micro and nanocomposites of cellulose@MOF-199 using cotton fabrics and nanobacterial cellulose (NBC) (Fig. 13).239 Under standard conditions of temperature and pressure, NBC@MOF-199 and Cotton@MOF-199 both displayed high adsorption capacities of 2.9 and 1.2 mmol g−1, respectively.
 |
| Fig. 13 Schematic representation of carboxymethylation and MOF-199 growth processes on the surface of nanobacterial cellulose.239 | |
In 2021, by synthesizing Cu Luzzi et al. were able to successfully embed zeolite-1,3,5-tricarboxylate [Cu3(BTC)2], Zn 2-methylimidazolate [Zn(MeIm)2], and AlBTC in situ in a mesoporous cellulose template made of balsa wood, Wang et al. successfully prepared foam-like TO-wood/MOF composites (Fig. 14).240 TO-wood/Cu3(BTC)2 composite had a greater CO2 adsorption capacity than TO-wood/Zn(MeIm)2 and TO-wood/AlBTC composites, at 1.46 mmol g−1 at 25 °C and atmospheric pressure.
 |
| Fig. 14 Synthesis of the TO-wood/MOF composite using Cu3(BTC)2. Reproduced from ref. 240 with permission from American Chemical Society, copyright 2021. | |
To capture CO2, Policicchio and colleagues developed a novel composite containing 2% CNC with a range of surface functional groups (such as carboxylic acids, sulfonic acids, and amines) incorporated into UiO-66.241
Yang et al. used cellulose paper packed with precipitated calcium carbonate (PCC) to produce cellulose paper@MOF-5 composite (Fig. 15).242 According to gas adsorption experiments, the as-prepared paper@MOF-5 composite showed a superior capacity to adsorb nitrogen gas and may have a lot of potentials to adsorb or store other gaseous products such as H2, CO2, CH4, etc.
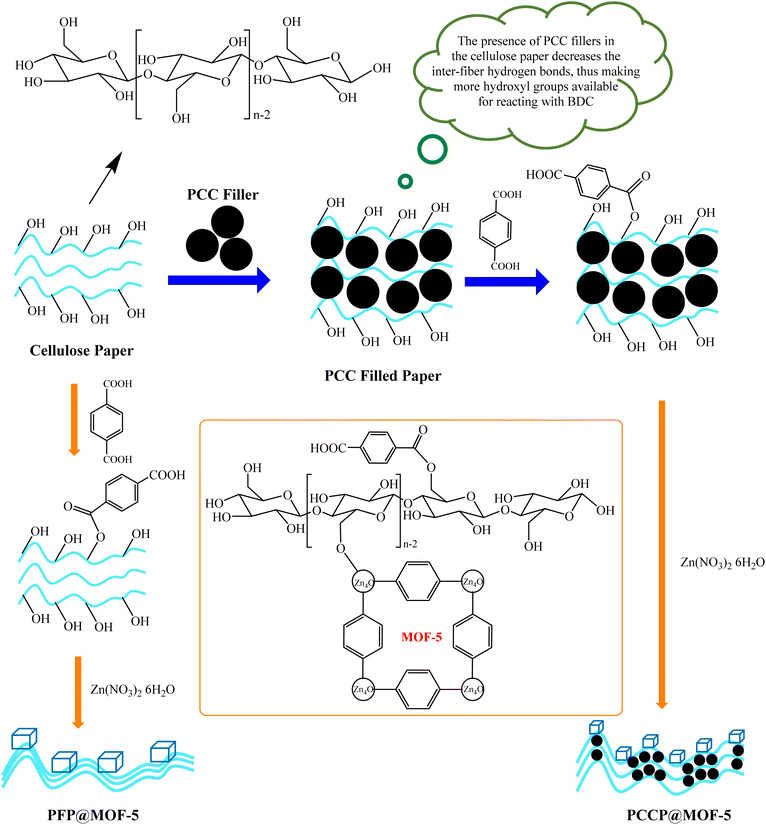 |
| Fig. 15 Preparation of cellulose paper@MOF-5 composite.242 | |
4.1.6.3 Cellulose-based membrane.
In 2022, Brunetti et al. continuously exposed cellulose-based carbon hollow fiber membranes to a gas stream, which also contained H2S and/or water vapor for 183 days while observing the separation performances of the membranes.243 At 298 K and 10 bar, CO2 and CH4 showed adsorption capacities of 2.98 and 2 mmol g−1, respectively. Moreover, in 2022, mixed matrix membranes (MMMs) with better CO2 adsorption capability were prepared by Rehman and colleagues.244 Cu-MOF-GO composite was added to CA polymer matrix as filler at a rate of 1 to 5 wt% to form MMMs (Fig. 16a). At a pressure of 15 bar, the maximal CO2 absorption rate was 1.79 mmol g−1 and 7.98 wt%. According to the adsorption data, Cu-MOF-GO composite and CA-based MMM can both effectively collect CO2.
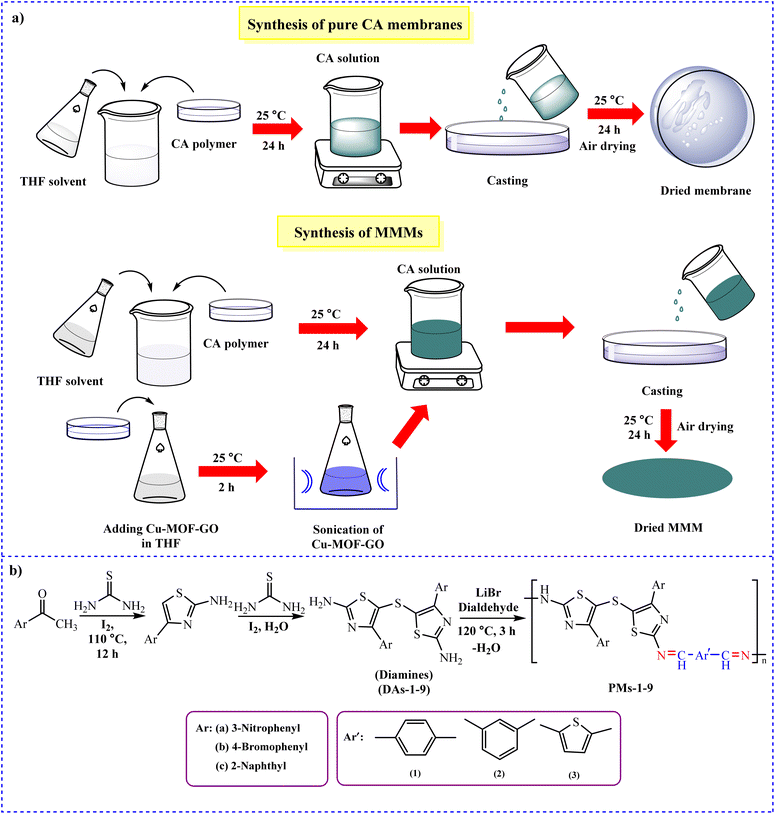 |
| Fig. 16 Synthesis of (a) pristine CA membranes (blank) and MMMs of Cu-MOF-GO loading in CA-matrix244 and (b) thiazole-based PMs-1-9.247 | |
To produce a novel class of MMMs for selective biogas upgrading, Regmi and co-workers combined TiO2 nanotube (TNT) amalgamated GO matrix with cellulose triacetate (CTA) (TNT@GO/CTA).245 The resulting MMMs had a higher affinity for CO2 adsorption. Almost 7 times more CO2 was permeable, reaching 22.54 Barrer. Using materials such as TNT, GO, and CTA, the adsorption performance was considerably enhanced. In a cellulose-based polymer matrix, Ali et al. assessed the possible intercalated effects of metal-induced microporous polymer (MMP) dots.246 Under both dry and humid conditions, the CO2 separation efficiency and plasticization pressure of MMP-intercalated smart membranes were assessed. According to the gas permeation measurements, adding MMP nanodots to cellulose polymer increased CO2 permeability from 14.1 to 108.9 Barrer. HSSA, hydrolytic stability, and effective performance for natural gas-type effluents under humid conditions are only a few of the promising characteristics of ultrathin intercalated membranes developed employing MMP nano-dots.
Green blend membranes were developed by Akbarzadeh et al. using glassy CA combined with ortho-linked thiazole-based polyimine (PM-4) and thioether linkage (Fig. 16b).247 The materials had great resistance to thermal properties. 3.72 mmol g−1 of this polymer may absorb a lot of CO2 at 1 bar and 298 K.
For CO2 separations, Raza and colleagues produced novel blended membranes made of CTA and cellulose diacetate (CDA).248 CTA and CDA blends were selected due to their similar chemical structures, strong separation performance, availability, and environmental friendliness. With a CO2 permeability of 17.32 barrer and a CO2/CH4 selectivity of 18.55, CTA
:
CDA (80
:
20) has moved higher in Robeson's upper bound curve. In 2020, to separate CO2/CH4 and CO2/N2, Jamil et al. prepared MMMs using CA and various bentonite (Bt) clay loadings.249 At a pressure of 2 bar pressure and 1 wt% Bt loading, the highest value of optimum selectivity for CO2/CH4 was attained, which is 79% greater than that of pure CA membranes. The optimal selectivity for CO2/N2 at a pressure of 4 bar was 123% greater than that of the clean membranes.
Nanocellulose fibril surfaces may be effectively modified for improved performance in CO2 separation membranes, as shown by Janakiram and colleagues.250 Using humid gas permeation experiments, thin composite membranes with the modified nanofibers in water-swelling PVA and a combination of sterically hindered polyallylamine (SHPAA) and PVA were formed and evaluated (Fig. 17). Compared to pure PVA membranes, the addition of nanocellulose showed improved CO2 permeance and CO2/N2 selectivity. Using a combination of SHPAA and PVA, CO2 permeance up to 652 GPU and a CO2/N2 selectivity of 41.3 was achieved.
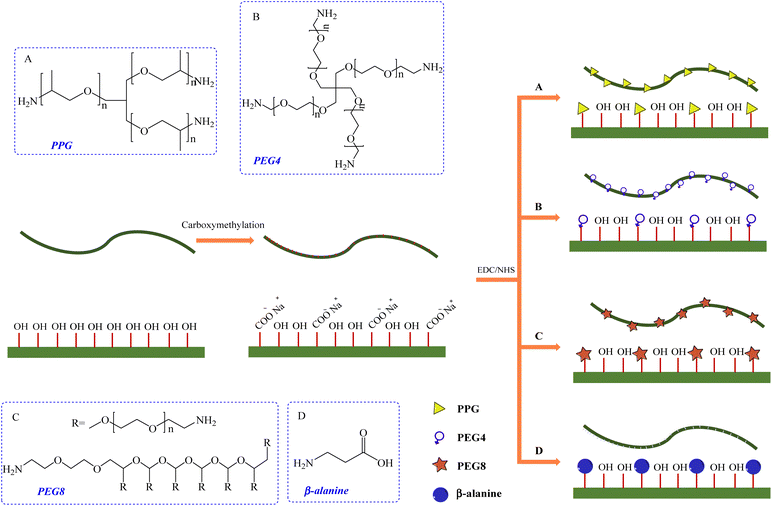 |
| Fig. 17 Surface modification of nanocellulose fibrils.250 | |
In 2015, pure CA and CA-TiO2 composite membranes were produced by Hafeez and co-workers to study the CO2 adsorption behavior.251 The high CO2 adsorption capacity may improve CO2 solubility and diffusion in the CA-TiO2 composite membrane, improving CO2 separation. Nevertheless, compared to pure CA membrane, CO2 adsorption is higher in the CA-TiO2 mixed membranes from 2.5 bars.
4.1.6.4 Cellulose-based aerogel materials.
In 2023, Chen et al. developed an epoxy-functionalized PEI-modified epichlorohydrin-cross-linked cellulose aerogel as an adsorbent for CO2 collection during the freezing-thawing processes (Fig. 18).252 By a maximum adsorption capacity of 6.45 mmol g−1 and freeze-drying, the sample displayed good adsorption performance.
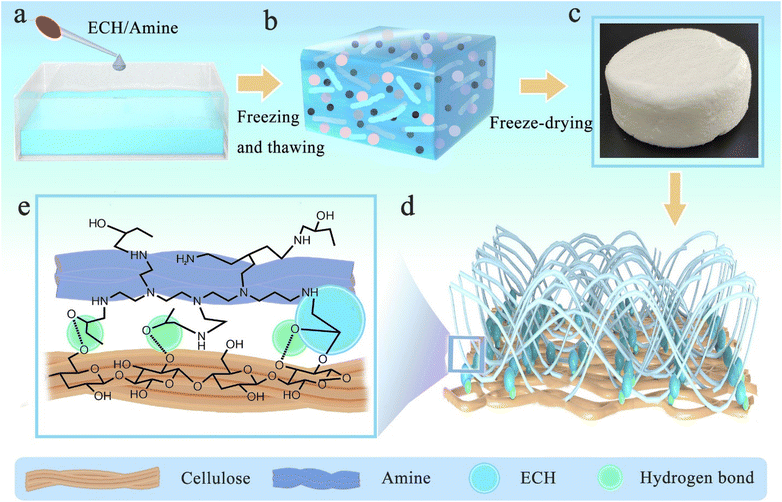 |
| Fig. 18 Synthesis of epoxy-functionalized PEI-modified epichlorohydrin-cross-linked cellulose aerogel. Reproduced from ref. 252 with permission from Elsevier, copyright 2023. | |
Cheng et al. synthesized 3D network-shaped biomass-derived cellulose carbon aerogels from Typha Orientalis (TO).253 The results showed that the material possessed 0.6 wt% hydrogen storage capacity at ambient temperature and adsorption capacities of 16 mmol g−1, 123.31 and 124.57 mg g−1 for o-xylene and o-dichlorobenzene, respectively.
In 2022, by tert-butanol substitution, gradual heating, high-temperature activation, and freeze-drying, Zhang et al. fabricated a cellulose nanofiber (CNF)/PVA/GO aerogel.254 The amount of GO in the material improved its HSSA (392.41 m2 g−1) and CO2 adsorption capacity (432.76 cm3 g−1 at 273 K). In fact, the novelty of this work is the presence of GO, which improves SSA.
Sun and colleagues used a simple vacuum impregnation approach along with a directional freeze-drying procedure to form a novel composite aerogel made of konjac glucomannan (KGM)/TEMPO-oxidized cellulose nanofibers (TOCNF)@HKUST-1 (KTA@HKUST-1) utilizing KGM and TOCNF as starting materials.255 The CO2 adsorption capacity of KTA@HKUST-1-10 (KTA@H10) may be as high as 3.50 mmol g−1 at 1 bar and 298 K and the adsorption capacity retention rate can be as high as 91.43% after 7 cycles, according to the experimental findings.
By employing BC as a template, Gong et al. developed a hydrothermal synthesis method to quickly construct hierarchical pompon-like SAPO-34. To prepare SAPO-34, SiO2-loaded BC aerogel was synthesized and employed as a silicon source.256 Furthermore, the CO2 adsorption capacity of the hierarchical pompon-like SAPO-34 crystals was 2.26 mmol g−1 at 100 kPa and 298 K, and the corresponding CO2/CH4 ideal separation factor was 5.7, which was greater than that of trigonal SAPO-34 crystals. In a study by Othaman et al., they prepared nanocrystalline cellulose (NCC) from oil palm empty fruit bunch fiber (OPEFB) and grafted it with three different aminosilanes; namely, 3-(aminopropyl) trimethoxysilane (APTMS), 3-(2-aminoethylamino) propyl-dimethoxymethylsilane (AEAPDMS), and N-(3-trimethoxysilylpropyl)diethylenetriamine (DET3)).257 According to these findings, APTMS-NCC aerogel has a greater CO2 adsorption (0.20 mmol g−1) than NCC aerogel, which has not been changed (0.010 mmol g−1).
Jiang and colleagues used a phase inversion-induced sol–gel method with supercritical drying to synthesize a cellulose aerogel. 3-Aminopropyltriethoxysilane (APTES) was grafted onto the cellulose gel structure to produce an amine-grafted cellulose aerogel (AGCA).258 AGCA demonstrated remarkable stability within 20 adsorption–desorption cycles, reaching a CO2 adsorption capacity of 1.20 mmol g−1 with dry 1% CO2. In another study, Zhou et al. produced cellulose whiskers/silica by a sol–gel technique. Tetraethyl orthosilicate (TEOs) and an alkaline silica solution were used to form solid aerogels from skim cotton (Fig. 19).259 Achieving a maximum adsorption capacity of 2.25 mmol g−1, the sample CSA-TEPA-70% showed good adsorption capacity.
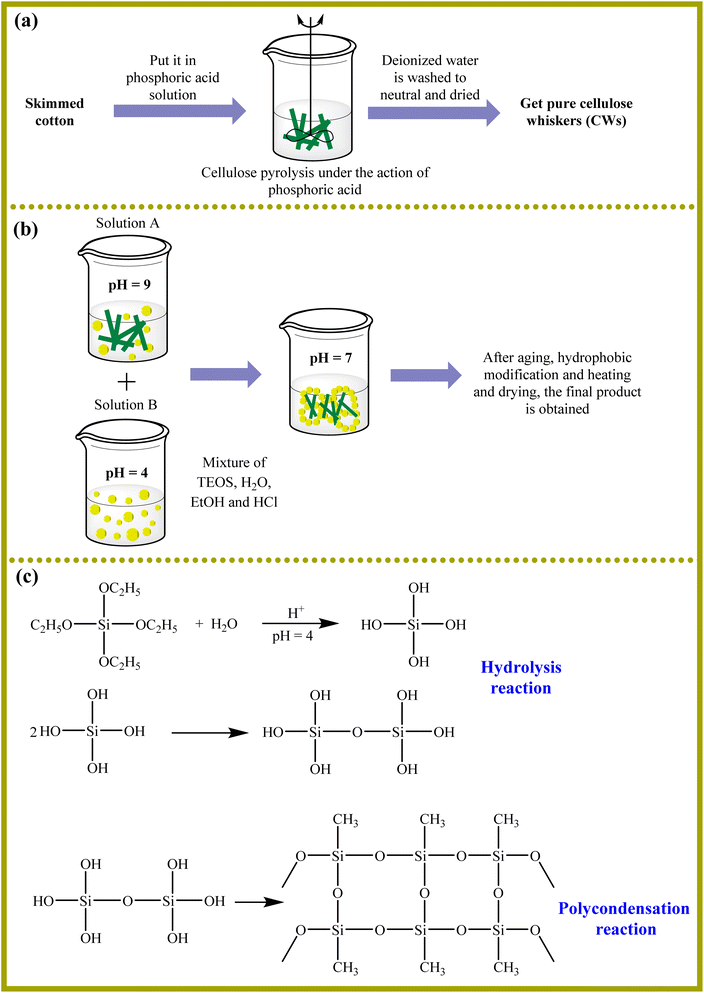 |
| Fig. 19 The preparation of (a) CWs and (b and c) CSA.259 | |
Xu and colleagues were able to functionalize CNC aerogel by employing aminosilane in a vapor-phase process.260 At 25 °C and 101.33 kPa, the adsorption capacity reached 2.57 mmol CO2 and was completely dominated by chemisorption. The adsorption capacity was reduced only 3–4% after six cycles. In addition, Zhu et al. prepared an amino CNC aerogel using 3-(2-aminoethylamino)-propylmethyldimethoxy silane (APS) as the modifier via chemical vapor deposition, which maintained the CO2 adsorption performance while improving the utilization ratio of the modifier.261 The CNC aerogel grafted with APS showed a CO2 adsorption capacity of 1.5034 mmol g−1 at 25 °C, 1 bar, and a pure dry CO2 environment. After 10 cycles, the APS-CNC aerogel demonstrated outstanding CO2 adsorption/desorption recyclability. According to the results obtained in this study, the adsorbent had a high stability up to 10 cycles.
For the in situ preparation of a variety of silica/cellulose aerogels in a NaOH/urea solution, Miao et al. employed fly ash-based fresh wet silica gel and cellulose derived from old corrugated containers.262 With a CO2 adsorption value of 3.68 mmol g−1 at 25 °C and 1 atm, the CA-Si-0 (Si-free aerogel) sample showed the highest adsorption.
In 2020, Zhang and colleagues used a facile amine gas phase modification technique to prepare a biomass-based nano cellulose aerogel with excellent CO2 adsorption capability.263 The modified nano cellulose aerogel adsorption capacity for CO2 improved from 0.19 to 1.59 mmol g−1, a factor of 7.4, compared to the unaltered one. Furthermore, Li and co-workers used N-(2-aminoethyl)-3-aminopropylmethyldimethoxysilane (APMDS) to add amines to CNFs during the functionalization process.264 The uptakes of CO2 by chemical and physical interactions at 15 kPa and 25 °C were 1.01 and 0.35 mmol g−1, respectively. In another study, Tang et al. functionalized cellulose with acrylamide in the 1-butyl-3-methylimidazolium chloride (BMIMCl) ionic liquid system by free radical grafting polymerization.265 At 313.15 K and 190 kPa, aerocellulose had an adsorption capacity of 0.52 mmol g−1. The sorption of AM-g-AC (38.59%), which was 2.06 times higher than that of AC, was 1.07 mmol g−1 under the same conditions.
Miao and colleagues synthesized a series of aerogels with different cellulose concentrations in NaOH/urea solution using old corrugated containers (OCCs) with small recycling potential as the starting material by freeze-drying method (Scheme 1a).266 At room temperature and pressure, the aerogels exhibited excellent CO2 adsorption capacities in the range of 1.96–11.78 mmol g−1.
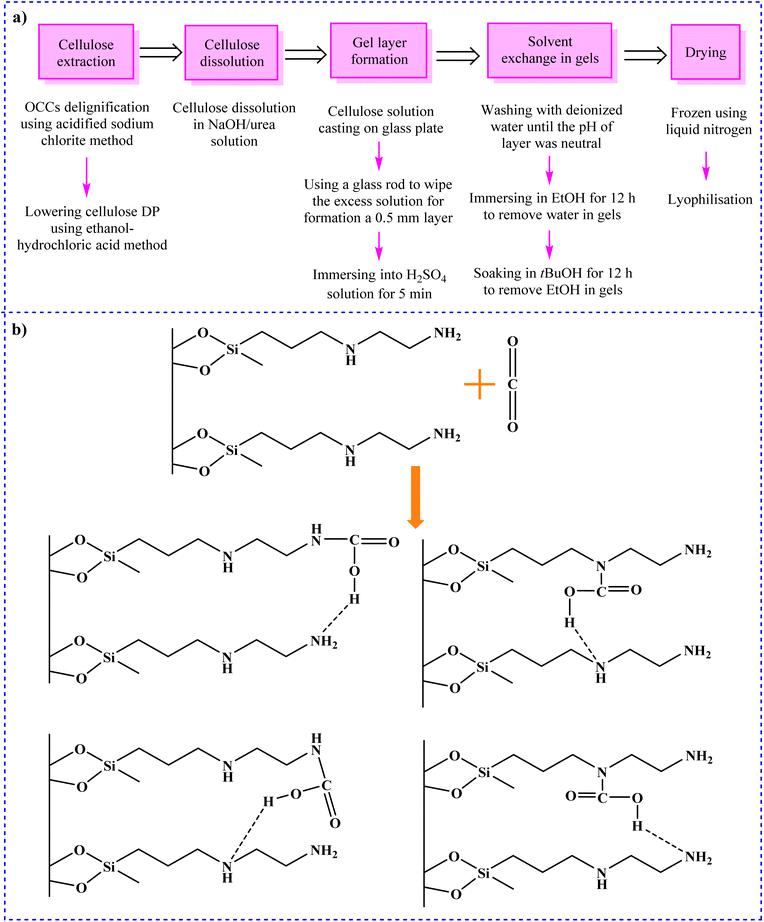 |
| Scheme 1 Synthesis of (a) cellulose aerogel from OCCs266 and (b) the CO2 adsorption mechanism of A-CNC-aerogel.267 | |
Zhang et al. developed a method for the preparation of CNC aerogel spheres modified with N-(2-aminoethyl)-3-amino-propylmethyldimethoxysilane (AEAPMDS) using a water phase heat treatment.267 The amount of CO2 adsorbed at a pressure of 3 bar by the modified aerogel (2.63 mmol g−1) was significantly higher than that of the unmodified aerogel (0.26 mmol g−1). Scheme 1b displayed the CO2 adsorption mechanism of A-CNC-aerogel. According to this Scheme, the in anhydrous conditions, the π bond in the chemical structure of CO2 was broken owing to the attacking of the lone pair electrons of the N in the structure of the A-CNC-aerogel to the C atom on the acid gas CO2 which led to formation of the carbamate.
Wang and Okubayashi used the sol–gel method, hydrolysis, and cross-linking to develop a novel PEI-cross-linked cellulose (PCC) aerogel sorbent. The CO2 adsorption capacity of PCC aerogel was 2.31 mmol g−1 at 25 °C in an environment with only dry, pure CO2.268 After 10 cycles, the PCC aerogel displayed excellent CO2 adsorption–desorption recyclability.
In 2018, unique amine-based aerogels, which may be employed as CO2 adsorbents, were synthesized by Wu and colleagues using CNFs (Scheme 2a).269 A significant CO2 adsorption capacity of 1.91 mmol g−1 at 25 °C and 1 bar was observed in CNF grafted with aminosilane. In addition, heating the aerosol to 80 °C facilitated the regeneration process.
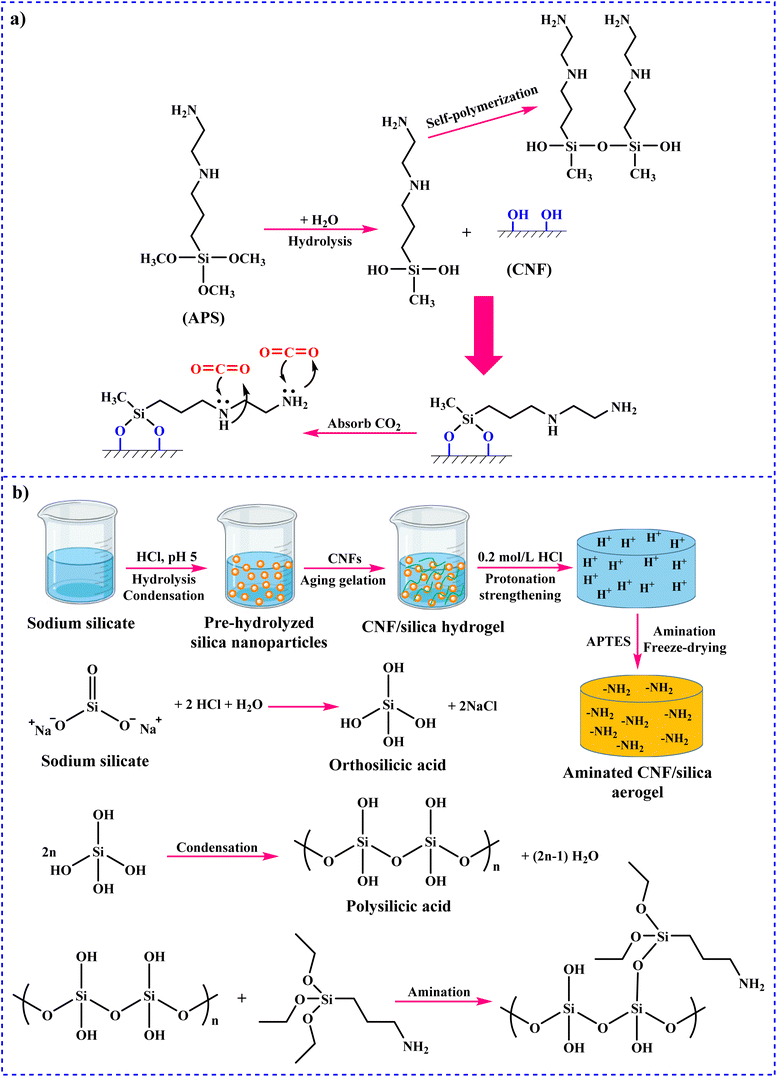 |
| Scheme 2 Synthesis of (a) polymer aerogel269 and (b) aminated CNF/silica aerogel.271 | |
Using eucalyptus pulp as a starting material, Liu et al. produced cellulose nanofibres via a chemical mechanical process. Subsequently, using the suspension titration approach, the spherical CNFs hydrogel was generated.270 Amino-modified bio-spherical CNF aerogels were then produced using the freeze-drying technology and the grafting modification process. The aerogels exhibited good regeneration of more than 10 cycles and their highest CO2 adsorption capacity was 1.78 mmol g−1. Moreover, Jiang et al. developed CNF-silica aerogels using a one-step in situ aqueous sol–gel method, which involved polymerization as well as aging the silica precursor in the presence of CNFs (Scheme 2b).271 CNF aerogels showed great flexibility and dry compressive strength and silica aerogels have had high thermal stability. Organosilane functionalization of CNF-silica aerogels resulted in the introduction of primary amine groups with an adsorption capacity of 1.49 mmol g−1 for CO2.
In 2017, Wu and colleagues grafted N-(2-aminoethyl)-3-aminopropylmethyldimethoxysilane (AEAPMDS) onto CNC derived from hybrid poplar residue.272 High CO2 adsorption capacities of 1.7 and 2.6 mmol g−1 were determined at 1 bar at temperatures of 25 and 0 °C, respectively. By carbonizing and activation with CO2, Dassanayake et al. could prepare AC from monoliths of cellulose-based aerogel (aerocellulose) (Fig. 20a).273 The aerocellulose retained its monolithic structure during the carbonization and activation operations. With CO2 adsorption capacities of 5.8 and 3.7 mmol g−1 at 0 °C, 1 atm and 25 °C, 1.2 atm, respectively, the resultant AC demonstrated outstanding adsorption characteristics toward CO2.
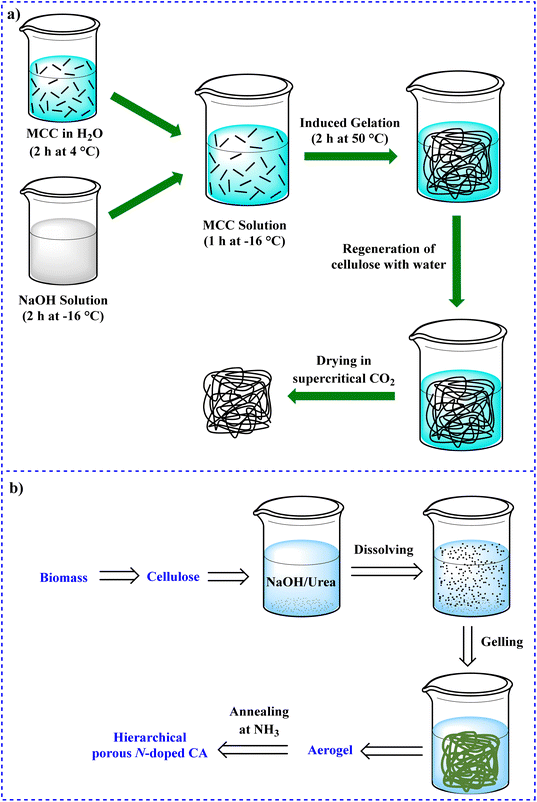 |
| Fig. 20 Synthesis of (a) aerocellulose monoliths273 and (b) hierarchical porous N-doped carbon aerogels.274 | |
In 2016, Hu and colleagues developed a quick and convenient method for producing hierarchical porous N-doped carbons from cellulose to prepare high-performance supercapacitor and CO2 capture applications. According to this procedure, hierarchical porous cellulose aerogels were first synthesized using a dissolving-gelling process, followed by carbonization in an atmosphere of NH3 to produce hierarchical porous N-doped carbon aerogels with more linked mecropores and micropores (Fig. 20b).274 The CO2 adsorption capacity of N-doped carbon aerogels was 4.99 mmol g−1, which is substantially greater than that of other porous carbons. The innovation of this study is that a double compound acting as both a supercapacitor and a CO2 absorber has been designed.
4.1.6.5 Cellulose-based ZIF materials.
A potential method to fabricate hybrid materials, which blend organic and conventional materials, is the crystal development of zeolitic imidazolate frameworks (ZIFs) on cellulose. In 2019, Valencia and Abdelhamid reported the one-pot synthesis of gelatin/nanocellulose leaf-like ZIF-L foams and ZIF-L stands to Zn(mim)2(Hmim)1/2(H2O)3/2, in which Hmim stands for 2-methylimidazole.275 As a model for nanocellulose, TOCNF was employed. Using water as the solvent, the in situ growth of ZIF-L into TOCNF was accomplished at room temperature.
In 2021, Abdelhamid and Mathew used a derivative of cellulose named TOCNF to modulate the crystal growth of ZIF-8 and ZIF-L, called CelloZIF-8 and CelloZIF-L, respectively.276 At room temperature, the synthesis process was carried out in the presence or absence of NaOH in water. CO2, metal ions, and colors were all adsorbed using the resultant CelloZIFs materials.
In the same year, Mubashir et al. synthesized CA-based membranes by interfacial engineering and integration of ZIF-62 glass NPs for CO2 separation.277 The maximum CO2 permeability and CO2/CH4 ideal selectivity were also provided by this set of membranes at 84.8 Barrer and 35.3, an increase of 436.7 and 189.3%, respectively. In another study, BC, a renewable and biodegradable material, was employed by Ma and co-workers as the substrate for ZIF growth. Using an in situ growth technique, amino-functionalized ZIF-8 (ZIF-8-NH2) was generated inside the BC substrate. The chelating action among zinc metal ions and –OH groups gives the composites great interface affinity and compatibility. Cellulose fibers were evenly covered with ZIF crystals.278 The final foams, produced at 25 °C and 1 bar, showed a high CO2 adsorption capacity of 1.63 mmol g−1.
4.1.6.6 Cellulose-based pellet materials.
To capture CO2, Zeng et al. prepared graphite-casted K2CO3-based adsorbent pellets with SiO2, ZrO2 and TiO2 as porous supports.279 The ZrO2-supported, 30 wt% K2CO3-loaded pellets showed the greatest CO2 adsorption capacity, around 0.93 mmol g−1, in contrast to the K2CO3 pellets supported by TiO2 or SiO2. The SiO2-supported K2CO3 adsorbent pellets with a 30 wt% K2CO3 loading and 500 °C calcination showed an adsorption capability of 0.38 mmol g−1. Furthermore, in 2022, Zheng et al. synthesized composite adsorbent pellets containing alkali metal salts (AMS) and MgO using the extrusion-spheronization technique.280 To enhance the porosity, morphologies, and CO2 uptakes of the AMS-MgO pellets, pore-forming templates composed of MCC, urea (UA), ammonium bicarbonate (AB), and citric acid (CA) were used. A fixed-bed reactor was used to study the CO2 uptakes and adsorption kinetics of the adsorbent pellets. At 340 °C and 50% CO2, the ideal AMS-MgO-MC pellets modified with an MC template had a significant CO2 absorption of 7.54 mmol g−1, CO2 absorption being maintained at 5 mmol g−1 throughout the course of 20 cycles. In addition, Sun et al. produced CaO-based pellets using an extrusion–spheronization technique. Although the addition of a cellulose template helped increase the CO2 absorption of CaO-based sorbent pellets above 0.32 g CO2 per g sorbent after 25 cycles, the impact of the cellulose particle size in improving CO2 capture performance was limited.281
In 2018, by using a surfactant-assisted steam explosion technique, Helmlinger et al. developed a unique method for the rapid and economical preparation of amine-functionalized cellulose pellets.282 A new laboratory reactor was used for capacity testing, and the results showed that the CO2 capacity was 1 mmol g−1, which is equivalent to those of other cellulose-based adsorbents reported in the literature. In another study, Hu and colleagues developed a facile gel-casting method to produce highly effective CaO-based sorbent pellets in a single step.283 In comparison to the unmodified pellets, the pellets modified with microcrystalline cellulose (CaOMC) achieved a significant CO2 capture capacity of 0.48 g/g at the 25th cycle under mild calcination conditions and maintained a reasonably exceptional efficiency of 0.41 g/g through 25 medium-cycle tests (CaO-pellets).
Sun et al. synthesized CaO-based pellets from residual carbide slag using a model extrusion-spheronization technique.284 For the first time, the pore architectures of the pellets were altered to improve their CO2 adsorption capacity. These modifications involved the use of two different types of biomass-based pore-forming materials (MCC and rice husk).
Other examples of CO2 collection using cellulose-based materials are shown in Table 2.
Table 2 Cellulose-based materials for CO2 capture
Entry |
Cellulose-based sorbent |
Operating conditions (temperature and pressure (bar)) |
Capacity (mmol g−1) |
Ref. |
Poly(ethyleneimine) (PEI) immobilized on cellulose, cellulose tosylate (CT), and cellulose carbamate (CC).
CNF-based thermoresponsive bionic fiber.
Thermoresponsive cellulose nanofiber (TRCNF)-based PEI.
Cellulose impregnated with urea and KOH.
Cotton pulp as carbon fibers activated with KOH/C.
Jute as carbon fibers activated with KOH/C.
Kenaf as carbon fibers activated with KOH/C.
Ionic liquid 1-butyl-3-methylimidazolium tetrafluoroborate [BMIM][BF4] and monoethanolamine or triethanolamine dropped cellulose fibers.
N-(2-Aminoethyl) (3-amino-propyl) methyldimethoxysilane (AEAPMDS) grafted onto the CNCs.
CNF films modified with diaminosilane N-[3-(trimethoxysilyl)propyl]ethylenediamine (DAMO) from corn husks (CH).
CNF films modified with DAMO from oat hulls (OH).
CNF films modified with DAMO from Kraft pulp (KP).
Nanocrystalline cellulose (NCC) modified with aminosilane, 3-(2-aminoethylamino)propyl-dimethoxymethylsilane (AEAPDMS).
|
1 |
Cellulose@CaCO3 composite |
— |
7.3 |
285
|
2 |
Cellulose gelation in NaOH (aq) |
— |
— |
286
|
3 |
PEI-functionalized cellulose materialsa |
80 °C |
0.026 mgCO2 mgadsorbent−1 |
287
|
4 |
CNF-TBFAb |
— |
6.52 |
288
|
5 |
TRCNF/PEIAc |
60 °C |
6.74 |
289
|
6 |
Biochar derived cellulose |
25 °C and 760 mm Hg |
3.6 |
290
|
7 |
CNC |
25–45 °C |
1.81 |
291
|
8 |
CNC-COOH |
25–45 °C |
3.19 |
291
|
9 |
CNC-NH2 |
25–45 °C |
3.46 |
291
|
10 |
PAMAM functionalized CNC |
25–45 °C |
3.54 |
291
|
11 |
Cell-UKd |
273 K and 1 |
297.1 mg g−1 |
292
|
12 |
CP-ACe |
25 °C and 35 |
14.3 |
293
|
13 |
J-ACf |
25 °C and 35 |
18.4 |
293
|
14 |
K-ACg |
25 °C and 35 |
17.8 |
293
|
15 |
Cellulose fibers/IL/TEA or MEAh |
25 °C and 25 |
141 mg of CO2 per g of fiber |
294
|
16 |
Phthalimide-modified CNF |
— |
— |
295
|
17 |
Quaternized bamboo cellulose |
— |
— |
296
|
18 |
Cellulose-TiO2 |
298.15 K and 30 |
184.1 mg g−1 |
297
|
19 |
Cellulose-Fe3O4 |
298.15 K and 30 |
130.6 mg g−1 |
297
|
20 |
Formaldehyde-free decorative paper coated with AEAPMDS-CNCsi |
25 °C and 1 |
1.806 |
298
|
21 |
75 wt% cellulose-supported [N1888][Ac] |
298 K and 30 |
30 g kg−1 |
299
|
22 |
75 wt% cellulose-supported [N4444][Ac] |
298 K and 30 |
31.6 g kg−1 |
299
|
23 |
70 wt% cellulose-supported [N8888]Br |
298 K and 30 |
19.8 g kg−1 |
299
|
24 |
75 wt% cellulose-supported [Bmim]Br |
298 K and 30 |
28.8 g kg−1 |
299
|
25 |
CH-CNF-DAMOj |
— |
0.89 |
300
|
26 |
OH-CNF-DAMOk |
— |
1.27 |
300
|
27 |
KP-CNF-DAMOl |
— |
2.11 |
300
|
28 |
CaO-based sorbent pellets |
— |
0.1 g CO2 per g of sorbent |
301
|
29 |
Cellulose dissolved in NaOH (aq) |
— |
— |
302
|
30 |
AC-derived Cladophora cellulose |
273 K and 1 |
5.52 |
303
|
31 |
NCC-AO composite |
120 °C and 1 atm |
5.54 |
304
|
32 |
Cross-linked-TBA |
25 °C and 3 MPa |
71 mg g−1 |
305
|
33 |
Organoclay-TOCNF |
— |
— |
306
|
34 |
NCC-AEAPDMSm |
— |
— |
307
|
35 |
Ammonia activation of carbonized cellulose |
— |
2.44 |
308
|
36 |
Cellulose fiber-based porous carbon |
298 K and 1 |
3.776 |
309
|
37 |
Nanofibrillated cellulose-polyethylenimine foams |
— |
2.22 |
310
|
38 |
Amine-functionalized nanofibrillated cellulose |
— |
— |
311
|
39 |
Amine-functionalized nanofibrillated cellulose |
90 °C and 30 mbar |
0.90 |
312
|
40 |
Hollow fibres of deacetylated CA |
— |
— |
313
|
41 |
Microfibrillated cellulose/Lupamin |
— |
— |
314
|
4.1.6.7 Summary of this section.
Various types of cellulose such as carboxymethylcellulose and microcrystalline cellulose have been used to prepare sorbent materials for CO2 capture. The use of cellulose as an edifice material offers new opportunities expanding the prospects of cellulose for CO2 capture. However, in future studies, new composites based on cellulose can be prepared and their efficiency of CO2 absorption can be improved to a great extent. The combination of cellulose and MOF has performed relatively well for carbon dioxide absorption. Cellulose-based membranes used for gas separation have shown good selectivity and CO2 capture efficiency. Studies conducted in the field of making cellulose-based aerogels show that cellulose is a suitable material for making aerogels in addition to possessing a high efficiency in absorbing and CO2 trapping. Studies have also been performed on cellulose-based pellets, but much work remains to be done. In general, cellulose and cellulosic sources are the appropriate and predominant biopolymers for making materials for carbon capture.
4.2 Lignin-based materials for CO2 capture
Lignin is a complex lignocellulosic biomass. After cellulose, lignin is the most abundant aromatic natural polymer. The sources of lignin are plant cell walls as well as a by-product of biorefineries and pulp manufacturing. In the structure of lignin, there are some functional groups such as carboxyl, hydroxyl, aldehyde, phenolic, and methoxy groups, which make this natural polymer very useful. Lignin has various properties such as biodegradability, low price, accessibility, HSSA, and stability, making it an attractive material applied in different industries including food packaging, medicine, catalysis, adsorption, etc. About 85% of the world's annual production of lignin is Kraft lignin although lignosulfonates are the prominent commercially available lignin source with a crop of about ∼1 million tons.315–319 In this section, we review recent studies regarding lignin-based materials for CO2 capture applications.
4.2.1 Lignin-based composite materials.
HKUST-1 is a type of MOF. In 2022, López-Monreal and Loera-Serna investigated the synthesis of a bio-nanocomposite using HKUST-1 and lignin.320 They synthesized HKUST-1-supported lignin (HKUST-1@lignin) for CO2 capture. Since HKUST-1 does not have a HSSA to act as an adsorbent, HKUST-1 was coated on the lignin surface to improve this property.
4.2.2 Lignin-based doped materials.
The preparation of sulfur-doped (S-D) nano porous carbons through one-step synthesis (Fig. 21) was performed by Saha and colleagues.321 For this aim, they used lignin as the precursor for the synthesis of nano porous carbons. Sodium thiosulfate and KOH were applied as sulfurizing and activating agents, respectively. The prepared S-D materials were applied for the CO2 adsorption, N2, and CH4. At 298 K and 760 torr, the experimental results indicated that the equilibrium capture capacity of CO2 was ∼11 mmol g−1.
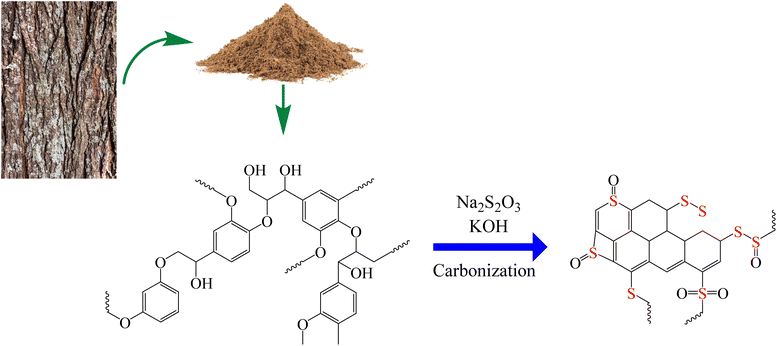 |
| Fig. 21 Schematic of one-step preparation of S-D nano porous carbon from lignin.321 | |
In 2023, Gong and Bao reported the synthesis of the N,O-codoped porous carbon from lignin for CO2 capture application.322 For this work, they used precarbonization, pyrolysis, and chemical activation with KOH. Their results displayed that the CO2 adsorption activity of the materials was considerably improved by the precarbonization of lignin. The adsorption capacity of the materials was 5.82 (at 273 K) and 3.98 mmol g−1 (at 298 K) at 1 bar.
In another study, Demir and co-workers fabricated heteroatom-doped porous carbons (LHPCs) by hydrothermal carbonization following chemical activation.323 The prepared carbons have 2.5–5.6 and 54 wt% nitrogen and oxygen, respectively. The prepared materials possessed micro– and mesoporous structures. LHPCs were applied as CO2 adsorbents and electrodes for supercapacitors. The adsorption capacity of the materials was 4.8 mmol g−1 at 1 bar and 298 K. The innovation of this study is that a double compound functioning as both a capacitor and a CO2 absorber has been designed.
Park et al. reported the synthesis of the N-doped ultra-porous carbon derived from lignin by hydrothermal carbonization and activation using KOH.324 The fabricated materials were applied for CO2 adsorption. The adsorption capacity of the materials was 13.6 mmol g−1 at 25 °C up to 10 atm and they showed high stability through 10 adsorption/desorption cycles. The results displayed that N-doped porous carbon had a high performance compared with non-doped porous carbon, indicating the enhancement of CO2 adsorption by functionalization with N.
In 2017, Saha and colleagues prepared N-doped and hierarchical porous carbons using lignin as the precursor and KOH and NH3 as activation agents.325 They used pyridinic, amino, and pyrrolic/pyridone materials for the functionalization of porous carbon. The materials prepared were applied for CO2 adsorption. The adsorption capacities were 5.48 and 8.6 mmol g−1 at 298 and 273 K and 1 bar, respectively.
4.2.3 Lignin-based aerogel materials.
Geng and colleagues investigated the synthesis of high-performance multi-functional carbon aerogels using Kraft lignin and cellulose nanofibers through ice-templating and carbonization approaches.326 Cellulose and lignin were extracted from renewable resources. The prepared carbon aerogels were used for CO2 capture as well as capacitive energy storage. At 273 K and 100 kPa, the results displayed excellent performance with adsorption capacity of 5.23 mmol g−1.
4.2.4 Lignin-based other materials.
Preparation of several types of porous carbon materials using black liquor lignin by chemical activation following the template technique was performed by Wang and co-workers.327 They used KOH as an activator for the synthesis of porous carbon (C-BLL-KOH), which has a HSSA (1336.5 m2 g−1) as well as high microporosity. These properties make the prepared materials very suitable for CO2 adsorption applications. According to the results, C-BLL-KOH showed high performance in CO2 capture and the maximum adsorption capacities were 5.20, 3.60, and 2.23 mmol g−1 at 0, 25, and 50 °C at 100 kPa pressure, respectively.
Sun et al. studied the synthesis of ordered mesoporous carbons using lignin and siliceous mesostructured cellular foam as precursor and template, respectively, through a solvothermal procedure.328 The synthesized lignin carbon materials showed a 3D large mesopore system as well as thin pore size distribution center. The fabricated mesoporous lignin carbon can be used as a support for CO2 adsorption. The results indicated that 60 wt% polyamines (polyethyleneimine (PEI)) could be loaded on the support and applied for CO2 adsorption. The adsorption capacity was 129.9 mg or 2.95 mmol CO2 per g-adsorbent at 75 °C. The meso porous carbon functionalized with PEI was highly stable and only 6% of the performance decreased after 50 runs.
In 2023, Liu and colleagues reported the preparation of lignin-based absorbents using grafted active amine group on a lignin-derived compound (vanillin and alkali lignin) and applied it for CO2 absorption (Fig. 22a).329 The results displayed that the vanillin-functionalized acrylamide had high adsorption capacity of CO2 (0.114 g CO2 per g of absorbent at 25 °C and 100 kPa). The synthesized absorbent was highly stable even after 6 cycles.
 |
| Fig. 22 (a) The schematic representation of the synthesis of absorbent and CO2 absorption process. Reproduced from ref. 329 with permission from Elsevier, copyright 2023 and (b) representation demonstration for the preparation process of HCP1∼HCP6 over Friedel–Crafts reaction.331 | |
In 2022, Sun and co-workers carried out the synthesis of several types of bio-carbon materials using Kraft lignin precursor through a chemical activation procedure.330 The Kraft lignin-derived carbons were applied for CO2 adsorption. The adsorption capacities of the carbon synthesized at 600 °C were 3.29 and 2.01 mmol g−1 at 0 and 25 °C at 15 kPa, respectively.
In the same year, the synthesis of the 6 aromatic units prepared from the depolymerization of the liquid products of lignin was performed by Chen and co-workers.331 They synthesized O-rich hyper-cross-linked polymers (HCPs) through a one-pot Friedel–Crafts reaction using formaldehyde dimethyl acetal (FDA) as a crosslinker (Fig. 22b). The prepared HCPs exhibited high CO2 uptake and selectivity of 64.1 mg g−1 and 35.2 at 273 K, respectively.
Atta-Obeng and colleagues developed an efficient process for the synthesis of amine-functionalized carbons derived from technical lignin.332 For this purpose, they first synthesized carbonaceous materials (CMs) from lignin using hydrothermal treatment, following activation by KOH. Afterward, they functionalized CMs using PEI, which is appropriate for CO2 capture applications. The optimum amount of PEI for loading was 5% and a further increase in the amount of PEI decreased CO2 absorption.
4.2.5 Summary of this section.
Lignin is a natural polymer possessing many functional groups in its structure, which can be functionalized with various materials. However, there are relatively few studies in the field of making lignin composites for carbon capture. Given the unique capacities and characteristics of lignin, future studies in the field of preparing lignin-based composites are necessary. For example, lignin can be easily aminated through the Mannich reaction and these structures can be very beneficial for CO2 capture. Moreover, in other studies, lignin has been used as a source of carbon and various atoms have been doped on it, yielding relatively effective materials. In general, considering the high potential of lignin as well as its many properties, there is a lot of work to be done in the future.
5. Summary and discussion
Since CO2 is a toxic and dangerous gas for the environment and humans, it is necessary to identify routes to capture or convert it into useful materials.333 The materials used for CO2 capture have been summarized in this review. In other words, in this review, the applications of polysaccharides and lignin-based materials, which are environmentally friendly and biodegradable, for capturing CO2 have been reviewed. Different structures based on polysaccharides and lignin have been prepared and used for this purpose. The results have shown that the more nitrogen groups there are in the structure, the higher the ability to capture CO2. On the other hand, the more porous the structure, the greater the ability to capture it. Polysaccharides and lignin are important for CO2 removal because they are natural materials and do not harm the environment. The results also showed that they have a high absorption capacity and are thus suitable for CO2 capture. There are other materials, which can capture CO2. These materials are not made of natural materials, and in some cases, they may have relatively good absorbency. However, toxic, non-environmentally friendly materials may have been used in the process of making them, making them undesirable materials. In addition, other materials are not cost-effective. Other materials may have complex and expensive methods of preparation and purification, but polysaccharides and lignin are readily available because they are natural, affordable, and economical. A number of different materials, which do not have polysaccharides and lignin-based materials used for CO2 capture, are reported in Table 3. Generally, these materials including graphene, MOF, zeolite, etc., are porous. The absorbability of these materials is not very high compared to polysaccharides and lignin-based materials, and are not very suitable because most of them do not have a natural source.
Table 3 Non-polysaccharide and lignin-based materials for CO2 capture
Entry |
Non-polysaccharide and lignin-based sorbent |
Operating conditions (temperature and pressure (bar)) |
Capacity (mmol g−1) |
Ref. |
Co-grafting of polyethyleneimine (PEI) on mesocellular silica foam (MCF), and (3-glycidyloxypropyl)triethoxysilane (GPTES).
Synthetic silico-metallic mineral particles.
|
1 |
N-doped graphene composite |
298 K and 1 |
2.7 |
334
|
2 |
Borane-modified graphene-based materials |
1 |
1.82 |
335
|
3 |
Zeolite 13X (13X-C) |
25 °C and 1 |
6.2 |
336
|
4 |
Zeolite 13X (13X-B) |
25 °C and 1 |
4.8 |
336
|
5 |
Dispersing CaO on γ-Al2O3 support |
650 °C |
6.4 |
337
|
6 |
Polyethyleneimine-graphene-silica |
75 °C and 7.5 bar |
4.3 |
338
|
7 |
Polyethyleneimine-F-Ce-2.5 nanosheets |
35 °C and 2 bar |
1.32 |
339
|
8 |
MCF@G-PEIa |
50 °C |
2.78 |
340
|
9 |
SSMMPb-Ni 50%-ammonium Br |
25 °C and 1 |
1.91 |
341
|
10 |
SSMMP-Ni 50%-imidazolium Br |
25 °C and 1 |
1.64 |
341
|
6. Conclusion and future prospects
Climate change, largely linked to the emission of greenhouse gases, including CO2, is disrupting our planet, threatening the lives of humans and other living beings. This review highlights interesting points to explore further and gaps to fill. As pointed out, many workers are interested in the separation of CO2via post-combustion processes for CO2 capture. Various classes of materials, which could be used for the capture and removal of CO2 by adsorption (or absorption) have received a great deal of attention in recent years. These materials can be in different forms including composites, aerogels, hydrogels, pellets, heteroatom-doped materials, membranes, MOFs, porous carbons, etc. Among the materials already used or under examination, polysaccharides and lignin, which are classified as biopolymers, are of great interest to researchers because they have many advantages such as biodegradability, environmental friendliness, availability, low cost, and non-toxicity. As a result, making compounds using polysaccharides and lignin to capture CO2 is a very effective method. In this review, recent publications regarding the application of polysaccharide and lignin-based materials for CO2 capture have been reviewed. In other words, in these studies, researchers have used environmentally friendly materials to protect the environment by capturing CO2.
Various polysaccharides such as alginate, starch, pectin, gum, chitosan, and cellulose have been used for CO2 capture. According to the existing studies, starch, pectin and gum have rarely been used for this purpose. However, chitosan and cellulose were more frequently used; especially in the form of aerogel. This highlights the suitability, appropriability, and efficiency of chitosan and cellulose, as well as their aerogels, compared to other polysaccharides for CO2 capture.
Undoubtedly, in gas separation applications, membranes offer the greatest potential. The studies conducted reveal that cellulose-based materials have been among the most studied in this field, and that the newly developed cellulose-based membrane materials have superior performance to most conventional commercial membranes. Studies on lignin have been less numerous and used lignin as a source for porous carbon supra-particle production. Nonetheless, lignin-based CO2 sorbents have been synthesized by functionalization of the functional groups in the structure of lignin (such as hydroxyl, carbonyl, sulfur, aldehyde, etc.). It should be noted that there is still much work to be done in this field.
Although relatively many studies have been conducted in the field of the application of polysaccharides (especially cellulose and chitosan) and lignin to capture CO2, there is still much work to be done in this field, which include:
• The combination of polysaccharides and lignin to increase the surface as well as mechanical and chemical properties.
• More use of pectin polysaccharides and gums for CO2 capture.
• Using polysaccharides and lignin on an industrial scale for CO2 capture
• These materials have been used as absorbents for CO2 capture, but CO2 can be converted into valuable compounds. Thus, these compounds can be made in such a way that after adsorbing (or absorbing) CO2, they can convert it into valuable compounds.
• Using other biopolymers for CO2 capture, such as collagen and gelatin, which are in the category of proteins.
Conflicts of interest
There are no conflicts to declare.
Acknowledgements
The supports from Iranian Nano Council, Iran University of Science and Technology and the University of Qom are appreciated. The authors also acknowledge the financial support from the “Belt and Road” Innovative Talents Exchange Foreign Experts Project of China (Grant No. DL2022026005L).
References
- Z. Sun, T. Wang, R. Zhang, H. Li, Y. Wu, S. Toan and Z. Sun, Bioresour. Technol., 2023, 382, 129197 CrossRef CAS PubMed
.
- A. George, B. Shen, M. Craven, Y. Wang, D. Kang, C. Wu and X. Tu, Renewable Sustainable Energy Rev., 2021, 135, 109702 CrossRef CAS
.
- L. Jeffry, M. Y. Ong, S. Nomanbhay, M. Mofijur, M. Mubashir and P. L. Show, Fuel, 2021, 301, 121017 CrossRef CAS
.
- F. C. Özbuğday and B. C. Erbas, Energy, 2015, 82, 734–745 CrossRef
.
- U. Kamran and S.-J. Park, J. Cleaner Prod., 2021, 290, 125776 CrossRef CAS
.
- L. Li, N. Zhao, W. Wei and Y. Sun, Fuel, 2013, 108, 112–130 CrossRef CAS
.
-
K. Riahi, E. S. Rubin and L. Schrattenholzer, in Greenhouse Gas Control Technologies-6th International Conference, Elsevier, 2003, pp. 1095–1100.
- Y. Qin, G. Niu, X. Wang, D. Luo and Y. Duan, J. CO2 Util., 2018, 28, 283–291 CrossRef CAS
.
- M. K. Mondal, H. K. Balsora and P. Varshney, Energy, 2012, 46, 431–441 CrossRef CAS
.
- X. Shen, H. Du, R. H. Mullins and R. R. Kommalapati, Energy Technol., 2017, 5, 822–833 CrossRef CAS
.
- A. Nosrati, S. Javanshir, F. Feyzi and S. Amirnejat, ACS Omega, 2023, 8, 3981–3991 CrossRef CAS PubMed
.
- B. Dutcher, M. Fan and A. G. Russell, ACS Appl. Mater. Interfaces, 2015, 7, 2137–2148 CrossRef CAS PubMed
.
- I. S. Omodolor, H. O. Otor, J. A. Andonegui, B. J. Allen and A. C. Alba-Rubio, Ind. Eng. Chem. Res., 2020, 59, 17612–17631 CrossRef CAS
.
- P. R. Yaashikaa, P. S. Kumar, S. J. Varjani and A. Saravanan, J. CO2 Util., 2019, 33, 131–147 CrossRef CAS
.
- S. Saeidi, N. A. S. Amin and M. R. Rahimpour, J. CO2 Util., 2014, 5, 66–81 CrossRef CAS
.
- A. Alok, R. Shrestha, S. Ban, S. Devkota, B. Uprety and R. Joshi, J. Environ. Chem. Eng., 2022, 10, 106922 CrossRef CAS
.
- K. Sumida, D. L. Rogow, J. A. Mason, T. M. McDonald, E. D. Bloch, Z. R. Herm, T.-H. Bae and J. R. Long, Chem. Rev., 2012, 112, 724–781 CrossRef CAS PubMed
.
- C. M. White, B. R. Strazisar, E. J. Granite, J. S. Hoffman and H. W. Pennline, J. Air Waste Manage. Assoc., 2003, 53, 645–715 CrossRef CAS PubMed
.
- P. Markewitz, W. Kuckshinrichs, W. Leitner, J. Linssen, P. Zapp, R. Bongartz, A. Schreiber and T. E. Müller, Energy Environ. Sci., 2012, 5, 7281–7305 RSC
.
- N. MacDowell, N. Florin, A. Buchard, J. Hallett, A. Galindo, G. Jackson, C. S. Adjiman, C. K. Williams, N. Shah and P. Fennell, Energy Environ. Sci., 2010, 3, 1645–1669 RSC
.
- E. S. Rubin, H. Mantripragada, A. Marks, P. Versteeg and J. Kitchin, Prog. Energy Combust. Sci., 2012, 38, 630–671 CrossRef CAS
.
- J. C. M. Pires, F. G. Martins, M. C. M. Alvim-Ferraz and M. Simões, Chem. Eng. Res. Des., 2011, 89, 1446–1460 CrossRef CAS
.
- A. A. Olajire, Energy, 2010, 35, 2610–2628 CrossRef CAS
.
- Z. Zhang, T. N. Borhani and A. G. Olabi, Energy, 2020, 205, 118057 CrossRef CAS
.
- N. P. Wickramaratne and M. Jaroniec, ACS Appl. Mater. Interfaces, 2013, 5, 1849–1855 CrossRef CAS PubMed
.
- J. M. Kolle, M. Fayaz and A. Sayari, Chem. Rev., 2021, 121, 7280–7345 CrossRef CAS PubMed
.
- A. Saravanan, D.-V. N. Vo, S. Jeevanantham, V. Bhuvaneswari, V. A. Narayanan, P. R. Yaashikaa, S. Swetha and B. Reshma, Chem. Eng. Sci., 2021, 236, 116515 CrossRef CAS
.
- J. Ma, N. Sun, X. Zhang, N. Zhao, F. Xiao, W. Wei and Y. Sun, Catal. Today, 2009, 148, 221–231 CrossRef CAS
.
- B. Li, Y. Duan, D. Luebke and B. Morreale, Appl. Energy, 2013, 102, 1439–1447 CrossRef CAS
.
- A. A. Chaugule, A. H. Tamboli and H. Kim, Fuel, 2017, 200, 316–332 CrossRef CAS
.
- G. Zhao, Z. Li, B. Cheng, X. Zhuang and T. Lin, Sep. Purif. Technol., 2023, 315, 123754 CrossRef CAS
.
- M. Li, Q. Xia, S. Lv, J. Tong, Z. Wang, Q. Nie and J. Yang, Green Chem., 2022, 24, 7500–7518 RSC
.
- S. Zhang, X. Bai, C. Zhao, Q. Tan, G. Luo, J. Wang, Q. Li, L. Wu, F. Chen and C. Li, Earth’s Future, 2021, 9, e2020EF001938 CrossRef CAS
.
- M. Xi, C. He, H. Yang, X. Fu, L. Fu, X. Cheng and J. Guo, Chin. Chem. Lett., 2022, 33, 2595–2599 CrossRef CAS
.
- C. Zhao, M. Xi, J. Huo, C. He and L. Fu, Chin. Chem. Lett., 2023, 34, 107213 CrossRef CAS
.
- J. H. Choe, H. Kim and C. S. Hong, Mater. Chem. Front., 2021, 5, 5172–5185 RSC
.
- Z. Hu, Y. Wang, B. B. Shah and D. Zhao, Adv. Sustainable Syst., 2019, 3, 1800080 CrossRef
.
- N. H. Khdary, A. S. Alayyar, L. M. Alsarhan, S. Alshihri and M. Mokhtar, Catalysts, 2022, 12, 300 CrossRef CAS
.
- R. Balasubramanian and S. Chowdhury, J. Mater. Chem. A, 2015, 3, 21968–21989 RSC
.
- S. Kumar, R. Srivastava and J. Koh, J. CO2 Util., 2020, 41, 101251 CrossRef CAS
.
- L. Yin, D. Li, S. Li, F. Gai, T. Zhang, Y. Liu and X. Zhao, J. Dispersion Sci. Technol., 2022, 44, 2303–2310 CrossRef
.
- E. Magnanelli, Ø. Wilhelmsen, E. Johannessen and S. Kjelstrup, J. Membr. Sci., 2016, 513, 129–139 CrossRef CAS
.
- Y. Han and W. S. W. Ho, J. Membr. Sci., 2021, 628, 119244 CrossRef CAS
.
- S. Yu, X. Zhao, J. Zhang, S. Liu, Z. Yuan, X. Liu, B. Liu and X. Yi, Cellulose, 2022, 29, 6783–6796 CrossRef CAS
.
- A. Primo, A. Forneli, A. Corma and H. García, ChemSusChem, 2012, 5, 2207–2214 CrossRef CAS PubMed
.
- S. Manzoor, M. Talib, A. V. Arsenin, V. S. Volkov and P. Mishra, ACS Omega, 2023, 8, 893–906 CrossRef CAS PubMed
.
- Q. Yang, D. Teng, J. Qu, P. Li and Y. Cao, Ind. Eng. Chem. Res., 2021, 60, 13023–13030 CrossRef CAS
.
- J. Shen, Y. Yuan and S. Salmon, ACS Sustainable Chem. Eng., 2022, 10, 7772–7785 CrossRef CAS
.
- D. E. F. Oliveira, J. A. O. Chagas, A. L. De Lima and C. J. A. Mota, Ind. Eng. Chem. Res., 2022, 61, 10522–10530 CrossRef CAS
.
- Z. Dai, J. Deng, Y. Ma, H. Guo, J. Wei, B. Wang, X. Jiang and L. Deng, Ind. Eng. Chem. Res., 2022, 61, 9067–9076 CrossRef CAS
.
- X. Qiu, S. Wang and S. Chen, Cellulose, 2022, 29, 5645–5658 CrossRef CAS
.
- J. Ralph, C. Lapierre and W. Boerjan, Curr. Opin. Biotechnol., 2019, 56, 240–249 CrossRef CAS PubMed
.
- S.-J. Sun, P. Deng, C.-E. Peng, H.-Y. Ji, L.-F. Mao and L.-Z. Peng, Polymers, 2022, 14, 2899 CrossRef CAS PubMed
.
- M. Nasrollahzadeh, N. S. S. Bidgoli, N. Shafiei and F. Momenbeik, Int. J. Biol. Macromol., 2021, 182, 59–64 CrossRef CAS PubMed
.
- B. Jaleh, A. Moradi, M. Eslamipanah, S. Khazalpour, H. Tahzibi, S. Azizian and M. B. Gawande, J. Magnesium Alloys, 2023, 11, 2072–2083 CrossRef CAS
.
- A. Nasri, B. Jaleh, S. Khazalpour, M. Nasrollahzadeh and M. Shokouhimehr, Int. J. Biol. Macromol., 2020, 164, 3012–3024 CrossRef CAS PubMed
.
- M. Dohendou, K. Pakzad, Z. Nezafat, M. Nasrollahzadeh and M. G. Dekamin, Int. J. Biol. Macromol., 2021, 192, 771–819 CrossRef CAS PubMed
.
- Y. Orooji, Z. Nezafat, M. Nasrollahzadeh and T. A. Kamali, Int. J. Biol. Macromol., 2021, 188, 950–973 CrossRef CAS PubMed
.
- M. Nasrollahzadeh, N. Shafiei, Z. Nezafat and N. S. S. Bidgoli, Mol. Catal., 2020, 489, 110942 CrossRef CAS
.
- G. A. M. Mersal, H. S. El-Sheshtawy, I. S. Yahia and K. I. Assaf, Comput. Theor. Chem., 2021, 1204, 113413 CrossRef CAS
.
- P. Thiyam, C. Persson, D. F. Parsons, D. Huang, S. Y. Buhmann and M. Boström, Colloids Surf., A, 2015, 470, 316–321 CrossRef CAS
.
- M. Sajjadi, F. Ahmadpoor, M. Nasrollahzadeh and H. Ghafuri, Int. J. Biol. Macromol., 2021, 178, 394–423 CrossRef CAS PubMed
.
- H. Rasoulzadeh, S. Motesaddi Zarandi, M. Massoudinejad, M. M. Amini and A. Sheikhmohammadi, Int. J. Environ. Anal. Chem., 2021 DOI:10.1080/03067319.2021.2004408
.
- D. Bi, X. Yang, L. Yao, Z. Hu, H. Li, X. Xu and J. Lu, Mar. Drugs, 2022, 20, 564 CrossRef CAS PubMed
.
- H. Wang, J. Qian and F. Ding, J. Agric. Food Chem., 2018, 66, 395–413 CrossRef CAS PubMed
.
- X. Qiu, X. Wang and S. Chen, New J. Chem., 2022, 46, 6956–6965 RSC
.
- P. Jia, J. Xu, X. Wang, Z. Chen, Z. Xie and H. Jiang, J. Porous Mater., 2022, 29, 745–758 CrossRef CAS
.
- K. Malini, M. Sasi, R. Meghanath, D. Selvakumar and N. S. Kumar, Int. J. Environ. Anal. Chem., 2021 DOI:10.1080/03067319.2021.1965595
.
- A. Verma, S. Thakur, G. Goel, J. Raj, V. K. Gupta, D. Roberts and V. K. Thakur, Curr. Res. Green Sustainable Chem., 2020, 3, 100027 CrossRef
.
- Y. Chen, Y. Long, J. Sun, S. Bai, Y. Chen, Z. Chen and C. Zhao, Energy Fuels, 2021, 35, 13215–13223 CrossRef CAS
.
- S. Ren, C. Li, Z. Tan, Y. Hou, S. Jia and J. Cui, J. Agric. Food Chem., 2019, 67, 3372–3379 CrossRef CAS PubMed
.
- N. A. Rashidi, S. Yusup and B. H. Hameed, Energy, 2013, 61, 440–446 CrossRef CAS
.
- Q. B. Meng and J. Weber, ChemSusChem, 2014, 7, 3312–3318 CrossRef CAS PubMed
.
- B. Zhao, M. Borghei, T. Zou, L. Wang, L.-S. Johansson, J. Majoinen, M. H. Sipponen, M. österberg, B. D. Mattos and O. J. Rojas, ACS Nano, 2021, 15, 6774–6786 CrossRef CAS PubMed
.
- J. Yi, D.-L. Zhong, J. Yan and Y.-Y. Lu, Energy, 2019, 171, 61–68 CrossRef CAS
.
- B. Zhu, J. Huang, J. Lu, D. Zhao, L. Lu, S. Jin and Q. Zhou, Int. J. Electrochem. Sci., 2017, 12, 11102–11107 CrossRef CAS
.
- W. H. Arnawtee, B. Jaleh, M. Nasrollahzadeh, R. Bakhshali-Dehkordi, A. Nasri and Y. Orooji, Sep. Purif. Technol., 2022, 290, 120793 CrossRef CAS
.
- X. Wang, M. Tarahomi, R. Sheibani, C. Xia and W. Wang, Int. J. Biol. Macromol., 2023, 241, 124472 CrossRef CAS PubMed
.
- Y. Wu, A. Parandoust, R. Sheibani, F. Kargaran, Z. Khorsandi, Y. Liang, C. Xia and Q. Van Le, Carbohydr. Polym., 2023, 318, 121102 CrossRef CAS PubMed
.
- C. Xu, M. Nasrollahzadeh, M. Selva, Z. Issaabadi and R. Luque, Chem. Soc. Rev., 2019, 48, 4791–4822 RSC
.
- B. Jaleh, M. Nasrollahzadeh, A. Nasri, M. Eslamipanah, A. Moradi and Z. Nezafat, Int. J. Biol. Macromol., 2021, 182, 1056–1090 CrossRef CAS PubMed
.
- R. Mohami, A. Shakeri and M. Nasrollahzadeh, Sep. Purif. Technol., 2022, 285, 120373 CrossRef CAS
.
- M. Nasrollahzadeh, N. S. S. Bidgoli and M. M. Karimkhani, Biomass Convers. Biorefin., 2023, 13, 9675–9688 CrossRef CAS
.
- A. Khan, M. Goepel, J. C. Colmenares and R. Gläser, ACS Sustainable Chem. Eng., 2020, 8, 4708–4727 CrossRef CAS
.
- F. Freitas, V. D. Alves, M. A. Reis, J. G. Crespo and I. M. Coelhoso, J. Appl. Polym. Sci., 2014, 131, 40047 CrossRef
.
- Z. Nezafat, B. F. Mohazzab, B. Jaleh, M. Nasrollahzadeh, T. Baran and M. Shokouhimehr, Inorg. Chem. Commun., 2021, 130, 108746 CrossRef CAS
.
- C. Zhao, X. Chen, E. J. Anthony, X. Jiang, L. Duan, Y. Wu, W. Dong and C. Zhao, Prog. Energy Combust. Sci., 2013, 39, 515–534 CrossRef
.
- Q. Wang, J. Luo, Z. Zhong and A. Borgna, Energy Environ. Sci., 2011, 4, 42–55 RSC
.
- A. E. Creamer and B. Gao, Environ. Sci. Technol., 2016, 50, 7276–7289 CrossRef CAS PubMed
.
- C. H. Lee, S. Mun and K. B. Lee, Chem. Eng. J., 2014, 258, 367–373 CrossRef CAS
.
- R. V. Siriwardane, M.-S. Shen, E. P. Fisher and J. Losch, Energy Fuels, 2005, 19, 1153–1159 CrossRef CAS
.
- M. S. Duyar, S. Wang, M. A. Arellano-Trevino and R. J. Farrauto, J. CO2 Util., 2016, 15, 65–71 CrossRef CAS
.
- W. Zhang, H. Liu, Y. Sun, J. Cakstins, C. Sun and C. E. Snape, Appl. Energy, 2016, 168, 394–405 CrossRef CAS
.
- P. Luis, T. Van Gerven and B. Van der Bruggen, Prog. Energy Combust. Sci., 2012, 38, 419–448 CrossRef CAS
.
- Y. Han and W. S. W. Ho, Chin. J. Chem. Eng., 2018, 26, 2238–2254 CrossRef CAS
.
- R. J. Littel, G. F. Versteeg and W. P. M. Van Swaaij, Chem. Eng. Sci., 1992, 47, 2037–2045 CrossRef CAS
.
- M. Caplow, J. Am. Chem. Soc., 1968, 90, 6795–6803 CrossRef CAS
.
- H.-B. Xie, Y. Zhou, Y. Zhang and J. K. Johnson, J. Phys. Chem. A, 2010, 114, 11844–11852 CrossRef CAS PubMed
.
- N. J. M. C. Penders-van Elk, S. Fradette and G. F. Versteeg, Chem. Eng. J., 2015, 259, 682–691 CrossRef CAS
.
- P. Khakharia, L. Brachert, J. Mertens, C. Anderlohr, A. Huizinga, E. S. Fernandez, B. Schallert, K. Schaber, T. J. H. Vlugt and E. Goetheer, Int. J. Greenhouse Gas Control, 2015, 34, 63–74 CrossRef CAS
.
- A. García-Abuín, D. Gomez-Diaz, A. B. López, J. M. Navaza and A. Rumbo, Ind. Eng. Chem. Res., 2013, 52, 13432–13438 CrossRef
.
- L. Zhu, G. W. Schade and C. J. Nielsen, Environ. Sci. Technol., 2013, 47, 14306–14314 CrossRef CAS PubMed
.
- J. E. Crooks and J. P. Donnellan, J. Chem. Soc., Perkin Trans. 2, 1989, 331–333 RSC
.
- E. F. Da Silva and H. F. Svendsen, Ind. Eng. Chem. Res., 2004, 43, 3413–3418 CrossRef CAS
.
- B. Arstad, R. Blom and O. Swang, J. Phys. Chem. A, 2007, 111, 1222–1228 CrossRef CAS PubMed
.
- H. Guo, Z. Zhou and G. Jing, Int. J. Greenhouse Gas Control, 2013, 16, 197–205 CrossRef CAS
.
- S. Kasahara, E. Kamio and H. Matsuyama, J. Membr. Sci., 2014, 454, 155–162 CrossRef CAS
.
- H. Sun, X. Zhou, Z. Xue, Z. Zhou and T. Mu, Int. J. Greenhouse Gas Control, 2014, 20, 43–48 CrossRef CAS
.
- B. Lv, B. Guo, Z. Zhou and G. Jing, Environ. Sci. Technol., 2015, 49, 10728–10735 CrossRef CAS PubMed
.
- S.-J. Han and J.-H. Wee, Environ. Sci. Pollut. Res., 2020, 27, 44951–44968 CrossRef CAS PubMed
.
- T. L. Donaldson and Y. N. Nguyen, Ind. Eng. Chem. Fundam., 1980, 19, 260–266 CrossRef CAS
.
- R. Yang, W. Fan, Y. Zheng, T. Wang, Y. Wang, T. Shi, D. Yao, L. Chen and A. Zhang, J. Mater. Sci., 2018, 53, 5172–5182 CrossRef CAS
.
- J.-S. Yang, Y.-J. Xie and W. He, Carbohydr. Polym., 2011, 84, 33–39 CrossRef CAS
.
- K. Y. Lee and D. J. Mooney, Prog. Polym. Sci., 2012, 37, 106–126 CrossRef CAS PubMed
.
- M. G. Dekamin, S. Ilkhanizadeh, Z. Latifidoost, H. Daemi, Z. Karimi and M. Barikani, RSC Adv., 2014, 4, 56658–56664 RSC
.
- B. Wang, Y. Wan, Y. Zheng, X. Lee, T. Liu, Z. Yu, J. Huang, Y. S. Ok, J. Chen and B. Gao, Crit. Rev. Environ. Sci. Technol., 2019, 49, 318–356 CrossRef CAS PubMed
.
- N. T. T. Uyen, Z. A. A. Hamid, N. X. T. Tram and N. Ahmad, Int. J. Biol. Macromol., 2020, 153, 1035–1046 CrossRef CAS PubMed
.
- J. Venkatesan, I. Bhatnagar, P. Manivasagan, K.-H. Kang and S.-K. Kim, Int. J. Biol. Macromol., 2015, 72, 269–281 CrossRef CAS PubMed
.
- L. Wang, Y. Hou, X. Zhong, J. Hu, F. Shi and H. Mi, Carbohydr. Polym., 2019, 208, 42–49 CrossRef CAS PubMed
.
-
Y. Qin, J. Jiang, L. Zhao, J. Zhang and F. Wang, in Biopolymers for Food Design, Elsevier, 2018, pp. 409–429 Search PubMed
.
- T. Ramdhan, S. H. Ching, S. Prakash and B. Bhandari, Trends Food Sci. Technol., 2020, 106, 150–159 CrossRef CAS
.
- X. Guo, Y. Wang, Y. Qin, P. Shen and Q. Peng, Int. J. Biol. Macromol., 2020, 162, 618–628 CrossRef CAS PubMed
.
- A. Benettayeb, E. Guibal, A. Morsli and R. Kessas, Chem. Eng. J., 2017, 316, 704–714 CrossRef CAS
.
- Z. Belattmania, F. Bentiss, C. Jama, M. Barakate, C. Katif, A. Reani and B. Sabour, Bionanoscience, 2018, 8, 617–623 CrossRef
.
-
J. Venkatesan, S. Anil and S.-K. Kim, Seaweed Polysaccharides: Isolation, biological and biomedical applications, Elsevier, 2017 Search PubMed
.
- H. Rasoulzadeh, S. Motesaddi Zarandi, M. Massoudinejad and M. M. Amini, Int. J. Environ. Anal. Chem., 2021, 103, 3740–3761 CrossRef
.
- S. Hosseini, F. E. Babadi, S. M. Soltani, M. K. Aroua, S. Babamohammadi and A. M. Moghadam, Process Saf. Environ. Prot., 2017, 109, 387–399 CrossRef CAS
.
- Y. Li, J. Wang, S. Fan, F. Wang, Z. Shen, H. Duan, J. Xu and Y. Huang, J. Energy Chem., 2021, 53, 168–174 CrossRef CAS
.
- Y. Wu, Z. Chen, Y. Liu, Y. Xu and Z. Liu, Fuel, 2018, 233, 574–581 CrossRef CAS
.
- X. Ma, Y. Li, M. Cao and C. Hu, J. Mater. Chem. A, 2014, 2, 4819–4826 RSC
.
- Z. Li, W. Sun, C. Chen, Q. Guo, X. Li, M. Gu, N. Feng, J. Ding, H. Wan and G. Guan, Appl. Surf. Sci., 2019, 480, 770–778 CrossRef CAS
.
- J. M. Park, D. K. Yoo and S. H. Jhung, Chem. Eng. J., 2020, 402, 126254 CrossRef CAS
.
- P. Chen, X. He, M. Pang, X. Dong, S. Zhao and W. Zhang, ACS Appl. Mater. Interfaces, 2020, 12, 20429–20439 CrossRef CAS PubMed
.
- K. Wang, Y. Tang, Q. Jiang, Y. Lan, H. Huang, D. Liu and C. Zhong, J. Energy Chem., 2017, 26, 902–908 CrossRef
.
- A. Kidanemariam, J. Lee and J. Park, Polymers, 2019, 11, 2090 CrossRef CAS PubMed
.
- S. Xiao, M. Li, H. Cong, L. Wang, X. Li and W. Zhang, Polymers, 2021, 13, 4075 CrossRef CAS PubMed
.
- S. Salehi and M. Hosseinifard, Chem. Eng. J., 2021, 410, 128315 CrossRef CAS
.
- G. Mondino, A. I. Spjelkavik, T. Didriksen, S. Krishnamurthy, R. E. Stensrød, C. A. Grande, L. O. Nord and R. Blom, Ind. Eng. Chem. Res., 2020, 59, 7198–7211 CrossRef CAS
.
- J. Xue, T. Wu, Y. Dai and Y. Xia, Chem. Rev., 2019, 119, 5298–5415 CrossRef CAS PubMed
.
- A. Suratman, D. N. Astuti, R. Jonathan, A. Kuncaka and Y. Yusuf, Indones. J. Chem., 2022, 22, 317–330 CrossRef CAS
.
- F. V. L. Koly and A. Suratman, Suyanta, Mor. J. Chem., 2020, 8, 053–063 CAS
.
- S. Wanjari, C. Prabhu, R. Yadav, T. Satyanarayana, N. Labhsetwar and S. Rayalu, Process Biochem., 2011, 46, 1010–1018 CrossRef CAS
.
- S. Zhang, Z. Zhang, Y. Lu, M. Rostam-Abadi and A. Jones, Bioresour. Technol., 2011, 102, 10194–10201 CrossRef CAS PubMed
.
- D. Dziedzic, K. B. Gross, R. A. Gorski and J. T. Johnson, J. Air Waste Manage. Assoc., 2006, 56, 1631–1641 CrossRef CAS PubMed
.
- N. Liu, G. M. Bond, A. Abel, B. J. McPherson and J. Stringer, Fuel Process. Technol., 2005, 86, 1615–1625 CrossRef CAS
.
- Y. Zhu, W. Li, G. Sun, Q. Tang and H. Bian, Int. J. Greenhouse Gas Control, 2016, 49, 290–296 CrossRef CAS
.
- A. Hussain and M.-B. Hägg, J. Membr. Sci., 2010, 359, 140–148 CrossRef CAS
.
- Y. Zhang, Z. Wang and S. Wang, Chem. Lett., 2002, 31, 430–431 CrossRef
.
- Z. H. U. Yaqun, W. Zhi, C. Zhang, W. Jixiao and W. Shichang, Chin. J. Chem. Eng., 2013, 21, 1098–1105 CrossRef
.
- P. Mahajan, M. B. Bera, P. S. Panesar and A. Chauhan, Int. J. Biol. Macromol., 2021, 180, 61–79 CrossRef CAS PubMed
.
- B. Dereje, Int. J. Biol. Macromol., 2021, 187, 911–921 CrossRef CAS PubMed
.
- M. Nasrollahzadeh, N. Shafiei, Z. Nezafat, N. S. S. Bidgoli and F. Soleimani, Carbohydr. Polym., 2020, 241, 116353 CrossRef CAS PubMed
.
- F. Xie, E. Pollet, P. J. Halley and L. Averous, Prog. Polym. Sci., 2013, 38, 1590–1628 CrossRef CAS
.
- W. Dang, Q. Lin, H. Pan and D. Zhang, J. Mater. Sci., 2022, 57, 12438–12448 CrossRef CAS
.
- G. Nazir, A. Rehman and S.-J. Park, J. CO2 Util., 2021, 51, 101641 CrossRef CAS
.
-
S. A. Anuar, W. N. R. W. Isahak and M. S. Mastar, in IOP Conference Series: Earth and Environmental Science, IOP Publishing, 2019, vol. 268, p. 12093 Search PubMed
.
- N. Rong, Y. Wu, J. Wang, L. Han and G. Wang, Energy Fuels, 2021, 35, 6056–6067 CrossRef CAS
.
- R. Rajamathi, Bhojaraj and C. Nethravathi, ACS Appl. Nano Mater., 2021, 4, 10969–10975 CrossRef CAS
.
- A. Alabadi, S. Razzaque, Y. Yang, S. Chen and B. Tan, Chem. Eng. J., 2015, 281, 606–612 CrossRef CAS
.
- M. Sevilla and A. B. Fuertes, Energy Environ. Sci., 2011, 4, 1765–1771 RSC
.
- R. Mohammadinejad, A. Kumar, M. Ranjbar-Mohammadi, M. Ashrafizadeh, S. S. Han, G. Khang and Z. Roveimiab, Polymers, 2020, 12, 176 CrossRef CAS PubMed
.
- F. Hussin, N. N. Hazani and M. K. Aroua, Mater. Today: Proc., 2023 DOI:10.1016/j.matpr.2023.01.094
.
- T. Prasankumar, D. Salpekar, S. Bhattacharyya, K. Manoharan, R. M. Yadav, M. A. C. Mata, K. A. Miller, R. Vajtai, S. Jose and S. Roy, Carbon, 2022, 199, 249–257 CrossRef CAS
.
- J. Chen, W. Liu, C.-M. Liu, T. Li, R.-H. Liang and S.-J. Luo, Crit. Rev. Food Sci. Nutr., 2015, 55, 1684–1698 CrossRef CAS PubMed
.
- C. F. de Oliveira, D. Giordani, R. Lutckemier, P. D. Gurak, F. Cladera-Olivera and L. D. F. Marczak, LWT–Food Sci. Technol., 2016, 71, 110–115 CrossRef
.
- M. Nasrollahzadeh, M. Sajjadi, S. Iravani and R. S. Varma, Carbohydr. Polym., 2021, 251, 116986 CrossRef CAS PubMed
.
- M. Vafaeinia, M. S. Khosrowshahi, H. Mashhadimoslem, H. B. M. Emrooz and A. Ghaemi, RSC Adv., 2022, 12, 546–560 RSC
.
- J. A. K. P. Jovellana and B. B. Pajarito, Key Eng. Mater., 2019, 801, 179–184 Search PubMed
.
- A. Lagazzo, E. Finocchio, P. Petrini, C. Ruggiero and L. Pastorino, Mater. Lett., 2016, 171, 212–215 CrossRef CAS
.
- K. V. H. Prashanth and R. N. Tharanathan, Trends Food Sci. Technol., 2007, 18, 117–131 CrossRef CAS
.
- F. Gu, J. Geng, M. Li, J. Chang and Y. Cui, ACS Omega, 2019, 4, 21421–21430 CrossRef CAS PubMed
.
- M. J. Ahmed, B. H. Hameed and E. H. Hummadi, Carbohydr. Polym., 2020, 247, 116690 CrossRef CAS PubMed
.
- K. Kurita, Mar. Biotechnol., 2006, 8, 203–226 CrossRef CAS PubMed
.
- X. Liu, X. Zhao, Y. Liu and T. Zhang, Polym. Bull., 2022, 79, 2633–2665 CrossRef CAS
.
- L. A. El-Azzami and E. A. Grulke, J. Polym. Sci., Part B: Polym. Phys., 2007, 45, 2620–2631 CrossRef CAS
.
- M. H. Al Marzouqi, M. A. Abdulkarim, S. A. Marzouk, M. H. El-Naas and H. M. Hasanain, Ind. Eng. Chem. Res., 2005, 44, 9273–9278 CrossRef
.
- E. Luzzi, P. Aprea, M. Salzano de Luna, D. Caputo and G. Filippone, ACS Appl. Mater. Interfaces, 2021, 13, 20728–20734 CrossRef CAS PubMed
.
- Z. Liu, R. Ma, W. Du, G. Yang and T. Chen, RSC Adv., 2021, 11, 20486–20497 RSC
.
- W. Du, R. Ma, Z. Liu, G. Yang and T. Chen, Materials, 2021, 14, 3224 CrossRef CAS PubMed
.
- N. Hsan, P. K. Dutta, S. Kumar, R. Bera and N. Das, Int. J. Biol. Macromol., 2019, 125, 300–306 CrossRef CAS PubMed
.
- J. Song, J. Liu, W. Zhao, Y. Chen, H. Xiao, X. Shi, Y. Liu and X. Chen, Ind. Eng. Chem. Res., 2018, 57, 4941–4948 CrossRef CAS
.
- A. A. Alhwaige, H. Ishida and S. Qutubuddin, ACS Sustainable Chem. Eng., 2016, 4, 1286–1295 CrossRef CAS
.
- A. A. Alhwaige, T. Agag, H. Ishida and S. Qutubuddin, RSC Adv., 2013, 3, 16011–16020 RSC
.
- S. Kumar, M. Y. Wani, J. Koh, J. M. Gil and A. J. F. N. Sobral, J. Environ. Sci., 2018, 69, 77–84 CrossRef CAS PubMed
.
- S. Kunalan, K. Palanivelu, E. K. Sachin, D. A. Syrtsova and V. V. Teplyakov, J. Appl. Polym. Sci., 2022, 139, 52024 CrossRef CAS
.
- H. Wen, L. Zhang, Y. Du, Z. Wang, Y. Jiang, H. Bian, J. Cui and S. Jia, J. CO2 Util., 2020, 39, 101171 CrossRef CAS
.
- N. Li, Z. Wang and J. Wang, J. Membr. Sci., 2022, 642, 119946 CrossRef CAS
.
- Y. Shen, H. Wang, J. Liu and Y. Zhang, ACS Sustainable Chem. Eng., 2015, 3, 1819–1829 CrossRef CAS
.
- M. C. Singo, X. C. Molepo, O. O. Oluwasina and M. O. Daramola, Energy Procedia, 2017, 114, 2429–2440 CrossRef CAS
.
-
K. O. Yoro, M. Singo, M. O. Daramola and J. L. Mulopo, in Proceedings of the 33rd annual international pittsburgh coal conference. Omnipress, Capetown, South Africa, 2016.
- K. Malini, D. Selvakumar and N. S. Kumar, J. Porous Mater., 2022, 29, 1539–1550 CrossRef CAS
.
- C. Yang, T. Zhao, H. Pan, F. Liu, J. Cao and Q. Lin, Chem. Eng. J., 2022, 432, 134347 CrossRef CAS
.
- J. Li, A. Bao, J. Chen and Y. Bao, J. Environ. Chem. Eng., 2022, 10, 107021 CrossRef CAS
.
- J. Xiao, Y. Wang, T. C. Zhang, L. Ouyang and S. Yuan, J. Power Sources, 2022, 517, 230727 CrossRef CAS
.
- S. He, G. Chen, H. Xiao, G. Shi, C. Ruan, Y. Ma, H. Dai, B. Yuan, X. Chen and X. Yang, J. Colloid Interface Sci., 2021, 582, 90–101 CrossRef CAS PubMed
.
- J. Shi, H. Cui, J. Xu, N. Yan, C. Zhang and S. You, Fuel, 2021, 305, 121505 CrossRef CAS
.
- G. Nazir, A. Rehman and S.-J. Park, J. Environ. Manage., 2021, 299, 113661 CrossRef CAS PubMed
.
- Q. Wu, G. Zhang, M. Gao, L. Huang, L. Li, S. Liu, C. Xie, Y. Zhang and S. Yu, J. Alloys Compd., 2019, 786, 826–838 CrossRef CAS
.
- J. Fujiki and K. Yogo, Chem. Commun., 2016, 52, 186–189 RSC
.
- X. Fan, L. Zhang, G. Zhang, Z. Shu and J. Shi, Carbon, 2013, 61, 423–430 CrossRef CAS
.
- J. A. Thote, R. V. Chatti, K. S. Iyer, V. Kumar, A. N. Valechha, N. K. Labhsetwar, R. B. Biniwale, M. K. N. Yenkie and S. S. Rayalu, J. Environ. Sci., 2012, 24, 1979–1984 CrossRef CAS PubMed
.
- M. Helmi, F. Moazami, A. Ghaemi and A. Hemmati, Fuel, 2023, 338, 127300 CrossRef CAS
.
- M. Lopes, A. Cecílio, M. Zanatta and M. C. Corvo, J. Cleaner Prod., 2022, 367, 132977 CrossRef CAS
.
- I. Barroso-Martín, J. A. Cecilia, E. Vilarrasa-García, D. Ballesteros-Plata, C. P. Jiménez-Gómez, Á. Vílchez-Cózar, A. Infantes-Molina and E. Rodríguez-Castellón, Polymers, 2022, 14, 5240 CrossRef PubMed
.
- J. A. O. Chagas, G. O. Crispim, B. P. Pinto, R. A. S. San Gil and C. J. A. Mota, ACS Omega, 2020, 5, 29520–29529 CrossRef CAS PubMed
.
- P. Wang, G. Zhang, W. Chen, Q. Chen, H. Jiao, L. Liu, X. Wang and X. Deng, ACS Omega, 2020, 5, 23460–23467 CrossRef CAS PubMed
.
- N. Hsan, P. K. Dutta, S. Kumar, N. Das and J. Koh, J. CO2 Util., 2020, 41, 101237 CrossRef CAS
.
- I.-H. Tseng, Z.-C. Liu and P.-Y. Chang, Carbohydr. Polym., 2020, 230, 115584 CrossRef CAS PubMed
.
- P. Jiamjirangkul, T. Inprasit, V. Intasanta and A. Pangon, Chem. Eng. Sci., 2020, 221, 115650 CrossRef CAS
.
- A. Rehman and S.-J. Park, Carbon, 2020, 159, 625–637 CrossRef CAS
.
- G. Singh, S. Tiburcius, S. M. Ruban, D. Shanbhag, C. I. Sathish, K. Ramadass and A. Vinu, Emergent Mater., 2019, 2, 337–349 CrossRef CAS
.
- L. Marin, B. Dragoi, N. Olaru, E. Perju, A. Coroaba, F. Doroftei, G. Scavia, S. Destri, S. Zappia and W. Porzio, Eur. Polym. J., 2019, 120, 109214 CrossRef CAS
.
- H.-L. Peng, J.-B. Zhang, J.-Y. Zhang, F.-Y. Zhong, P.-K. Wu, K. Huang, J.-P. Fan and F. Liu, Chem. Eng. J., 2019, 359, 1159–1165 CrossRef CAS
.
- M. A. Islam, Y. L. Tan, M. A. Islam, M. Romić and B. H. Hameed, Colloids Surf., A, 2018, 554, 9–15 CrossRef
.
- K. Osler, N. Twala, O. O. Oluwasina and M. O. Daramola, Energy Procedia, 2017, 114, 2330–2335 CrossRef CAS
.
- S. Kumar, J. de A. e Silva, M. Y. Wani, J. M. Gil and A. J. F. N. Sobral, Carbohydr. Polym., 2017, 175, 575–583 CrossRef CAS PubMed
.
- S. Kumar, J. de A. e Silva, M. Y. Wani, C. M. F. Dias and A. J. F. N. Sobral, J. Dispersion Sci. Technol., 2016, 37, 155–158 CrossRef CAS
.
- G. Sneddon, A. Y. Ganin and H. H. P. Yiu, Energy Technol., 2015, 3, 249–258 CrossRef CAS
.
- J. Fujiki and K. Yogo, Energy Fuels, 2014, 28, 6467–6474 CrossRef CAS
.
- M. Keramati and A. A. Ghoreyshi, Phys. E, 2014, 57, 161–168 CrossRef CAS
.
- C. Patkool, P. Chawakitchareon and R. Anuwattana, Environ. Eng. Res., 2014, 19, 289–292 CrossRef
.
- C.-C. Huang and S.-C. Shen, J. Taiwan Inst. Chem. Eng., 2013, 44, 89–94 CrossRef CAS
.
- S. Kumar, K. Prasad, J. M. Gil, A. J. F. N. Sobral and J. Koh, Carbohydr. Polym., 2018, 198, 401–406 CrossRef CAS PubMed
.
- C. Li, N. He, X. Zhao, X. Zhang, W. Li, X. Zhao and Y. Qiao, ChemistrySelect, 2022, 7, e202103927 CrossRef CAS
.
- H. P. S. A. Khalil, A. H. Bhat and A. F. I. Yusra, Carbohydr. Polym., 2012, 87, 963–979 CrossRef
.
- A. Gholampour and T. Ozbakkaloglu, J. Mater. Sci., 2020, 55, 829–892 CrossRef CAS
.
- K. A. Adegoke, I. A. Bello, O. S. Bello, M. A. Balogun and N. W. Maxakato, Sci. Afr., 2022, 16, e01138 CAS
.
- B. Zhang, H. Chen, Q. Hu, L. Jiang, Y. Shen, D. Zhao and Z. Zhou, Adv. Funct. Mater., 2021, 31, 2105395 CrossRef CAS
.
- S. Wohlhauser, G. Delepierre, M. Labet, G. Morandi, W. Thielemans, C. Weder and J. O. Zoppe, Macromolecules, 2018, 51, 6157–6189 CrossRef CAS
.
- A. H. Tayeb, E. Amini, S. Ghasemi and M. Tajvidi, Molecules, 2018, 23, 2684 CrossRef PubMed
.
- D. Plackett, K. Letchford, J. Jackson and H. Burt, Nord. Pulp Pap. Res. J., 2014, 29, 105–118 CrossRef CAS
.
- Z. Dai, V. Ottesen, J. Deng, R. M. L. Helberg and L. Deng, Fibers, 2019, 7, 40 CrossRef CAS
.
- Y. Habibi, L. A. Lucia and O. J. Rojas, Chem. Rev., 2010, 110, 3479–3500 CrossRef CAS PubMed
.
- R. J. Moon, A. Martini, J. Nairn, J. Simonsen and J. Youngblood, Chem. Soc. Rev., 2011, 40, 3941–3994 RSC
.
- V. K. Thakur and M. K. Thakur, Carbohydr. Polym., 2014, 109, 102–117 CrossRef CAS PubMed
.
- X.-F. Zhang, Z. Wang, M. Ding, Y. Feng and J. Yao, J. Mater. Chem. A, 2021, 9, 23353–23363 RSC
.
- M. Babar, M. A. Bustam, A. Ali, A. S. Maulud, U. Shafiq, A. M. Shariff and Z. Man, Cryogenics, 2019, 101, 79–88 CrossRef CAS
.
- C. Gunathilake, R. S. Dassanayake, N. Abidi and M. Jaroniec, J. Mater. Chem. A, 2016, 4, 4808–4819 RSC
.
- S. Q. Jabbar, H. Janani and H. Janani, J. Polym. Environ., 2022, 30, 4210–4224 CrossRef CAS
.
- S. Wang, C. Wang and Q. Zhou, ACS Appl. Mater. Interfaces, 2021, 13, 29949–29959 CrossRef CAS PubMed
.
- A. Policicchio, M. Florent, M. F. Attia, D. C. Whitehead, J. Jagiello and T. J. Bandosz, Adv. Mater. Interfaces, 2020, 7, 1902098 CrossRef CAS
.
- Q. Yang, M. Zhang, S. Song and B. Yang, Cellulose, 2017, 24, 3051–3060 CrossRef CAS
.
- A. Brunetti, L. Lei, E. Avruscio, D. S. Karousos, A. Lindbråthen, E. P. Kouvelos, X. He, E. P. Favvas and G. Barbieri, Chem. Eng. J., 2022, 448, 137615 CrossRef CAS
.
- A. Rehman, Z. Jahan, F. Sher, T. Noor, M. B. K. Niazi, M. A. Akram and E. K. Sher, Chemosphere, 2022, 307, 135736 CrossRef CAS PubMed
.
- C. Regmi, S. Ashtiani, F. Průša and K. Friess, Sep. Purif. Technol., 2022, 282, 120128 CrossRef CAS
.
- A. Ali, M. Mubashir, A. Abdulrahman and P. E. Phelan, Chemosphere, 2022, 306, 135482 CrossRef CAS PubMed
.
- E. Akbarzadeh, A. Shockravi and V. Vatanpour, Carbohydr. Polym., 2021, 252, 117215 CrossRef CAS PubMed
.
- A. Raza, S. Farrukh, A. Hussain, I. Khan, M. H. D. Othman and M. Ahsan, Membranes, 2021, 11, 245 CrossRef CAS PubMed
.
- A. Jamil, M. Zulfiqar, U. Arshad, S. Mahmood, T. Iqbal, S. Rafiq and M. Z. Iqbal, Adv. Polym. Technol., 2020, 2020, 8855577 CrossRef
.
- S. Janakiram, X. Yu, L. Ansaloni, Z. Dai and L. Deng, ACS Appl. Mater. Interfaces, 2019, 11, 33302–33313 CrossRef CAS PubMed
.
- S. Hafeez, X. Fan, A. Hussain and C. F. Martín, J. Environ. Sci., 2015, 35, 163–171 CrossRef CAS PubMed
.
- X. Chen, J. Lin, H. Wang, Y. Yang, C. Wang, Q. Sun, X. Shen and Y. Li, Carbohydr. Polym., 2023, 302, 120389 CrossRef CAS PubMed
.
- J. Cheng, X. Cheng, Z. Wang, M. B. Hussain and M. Wang, Energy, 2023, 263, 125984 CrossRef CAS
.
- Q. Zhang, W. Lu, M. Wu, G. Qi, Y. Yuan, J. Li, H. Su and H. Zhang, J. Environ. Manage., 2022, 302, 114044 CrossRef CAS PubMed
.
- J. Sun, M. Shang, M. Zhang, S. Yu, Z. Yuan, X. Yi, S. Filatov and J. Zhang, Carbohydr. Polym., 2022, 293, 119720 CrossRef CAS PubMed
.
- J. Gong, F. Tong, C. Zhang, M. S. Nobandegani, L. Yu and L. Zhang, Microporous Mesoporous Mater., 2022, 331, 111664 CrossRef CAS
.
- N. H. Mohd, H. Kargazadeh, M. Miyamoto, S. Uemiya, N. Sharer, A. Baharum, T. L. Peng, I. Ahmad, M. A. Yarmo and R. Othaman, J. Mater. Res. Technol., 2021, 13, 2287–2296 CrossRef CAS
.
- X. Jiang, Y. Kong, H. Zou, Z. Zhao, Y. Zhong and X. Shen, J. Porous Mater., 2021, 28, 93–97 CrossRef CAS
.
- G. Zhou, K. Wang, R. Liu, Y. Tian, B. Kong and G. Qi, Colloids Surf., A, 2021, 631, 127675 CrossRef CAS
.
- J. Xu, P. Jia, X. Wang, Z. Xie, Z. Chen and H. Jiang, J. Appl. Polym. Sci., 2021, 138, 50891 CrossRef CAS
.
- W. Zhu, Y. Yao, Y. Zhang, H. Jiang, Z. Wang, W. Chen and Y. Xue, Ind. Eng. Chem. Res., 2020, 59, 16660–16668 CrossRef CAS
.
- Y. Miao, M. Pudukudy, Y. Zhi, Y. Miao, S. Shan, Q. Jia and Y. Ni, Carbohydr. Polym., 2020, 236, 116079 CrossRef CAS PubMed
.
- T. Zhang, W. Zhang, Y. Zhang, M. Shen and J. Zhang, Cellulose, 2020, 27, 2953–2958 CrossRef CAS
.
- Y. Li, P. Jia, J. Xu, Y. Wu, H. Jiang and Z. Li, Ind. Eng. Chem. Res., 2020, 59, 2874–2882 CrossRef CAS
.
- Y. Tang, S. Tang and T. Zhang, Cellulose, 2020, 27, 3263–3275 CrossRef CAS
.
- Y. Miao, H. Luo, M. Pudukudy, Y. Zhi, W. Zhao, S. Shan, Q. Jia and Y. Ni, Carbohydr. Polym., 2020, 227, 115380 CrossRef CAS PubMed
.
- T. Zhang, Y. Zhang, H. Jiang and X. Wang, Environ. Sci. Pollut. Res., 2019, 26, 16716–16726 CrossRef CAS PubMed
.
- C. Wang and S. Okubayashi, Carbohydr. Polym., 2019, 225, 115248 CrossRef PubMed
.
- Y. Wu, Y. Zhang, N. Chen, S. Dai, H. Jiang and S. Wang, Carbohydr. Polym., 2018, 194, 252–259 CrossRef CAS PubMed
.
- S. Liu, Y. Zhang, H. Jiang, X. Wang, T. Zhang and Y. Yao, Environ. Chem. Lett., 2018, 16, 605–614 CrossRef CAS
.
- F. Jiang, S. Hu and Y. Hsieh, ACS Appl. Nano Mater., 2018, 1, 6701–6710 CrossRef CAS
.
- Y. Wu, F. Cao, H. Jiang and Y. Zhang, Mater. Res. Express, 2017, 4, 85303 CrossRef
.
- R. S. Dassanayake, C. Gunathilake, T. Jackson, M. Jaroniec and N. Abidi, Cellulose, 2016, 23, 1363–1374 CrossRef CAS
.
- Y. Hu, X. Tong, H. Zhuo, L. Zhong, X. Peng, S. Wang and R. Sun, RSC Adv., 2016, 6, 15788–15795 RSC
.
- L. Valencia and H. N. Abdelhamid, Carbohydr. Polym., 2019, 213, 338–345 CrossRef CAS PubMed
.
- H. N. Abdelhamid and A. P. Mathew, Chem. Eng. J., 2021, 426, 131733 CrossRef
.
- M. Mubashir, L. F. Dumée, Y. Y. Fong, N. Jusoh, J. Lukose, W. S. Chai and P. L. Show, J. Hazard. Mater., 2021, 415, 125639 CrossRef CAS PubMed
.
- H. Ma, Z. Wang, X.-F. Zhang, M. Ding and J. Yao, Carbohydr. Polym., 2021, 270, 118376 CrossRef CAS PubMed
.
- P. Zeng, C. Zhao, C. Liang, P. Li, H. Zhang, R. Wang, Y. Guo, H. Xia and J. Sun, Sep. Purif. Technol., 2023, 306, 122608 CrossRef CAS
.
- Y. Zheng, J. Wu, L. Zhang, Y. Guo, Z. Xu, Y. Huang, P. Huang, J. Zhang and C. Zhao, Chem. Eng. J., 2022, 450, 137944 CrossRef CAS
.
- J. Sun, C. Liang, X. Tong, Y. Guo, W. Li, C. Zhao, J. Zhang and P. Lu, Fuel, 2019, 239, 1046–1054 CrossRef CAS
.
- L. Helmlinger, Y. Zhu, J. Gensel, T. Neumeyer, S. Thäter, F. Strube, C. Bauer, B. Rosemann and V. Altstädt, J. Renewable Mater., 2018, 6, 219 CAS
.
- Y. Hu, W. Liu, Y. Peng, Y. Yang, J. Sun, H. Chen, Z. Zhou and M. Xu, Fuel Process. Technol., 2017, 160, 70–77 CrossRef CAS
.
- J. Sun, W. Liu, Y. Hu, J. Wu, M. Li, X. Yang, W. Wang and M. Xu, Chem. Eng. J., 2016, 285, 293–303 CrossRef CAS
.
- H.-X. Zhao, J.-C. Li, Y. Wang, Y.-R. Guo, S. Li and Q.-J. Pan, Sep. Purif. Technol., 2023, 307, 122774 CrossRef CAS
.
- G. Reyes, R. Ajdary, E. Kankuri, J. J. Kaschuk, H. Kosonen and O. J. Rojas, Carbohydr. Polym., 2023, 302, 120355 CrossRef CAS PubMed
.
- M. P. Vocht, P. Tomasic, R. Beyer, A. Müller, U. Zuberbühler, B. Stürmer, F. Hermanutz and M. R. Buchmeiser, Macromol. Mater. Eng., 2022, 307, 2200093 CrossRef CAS
.
- W. Lu, X. Shi, H. Zhou, W. Luo, L. Wang and H. He, Chem. Eng. J., 2022, 449, 137885 CrossRef CAS
.
- J. Lin, W. Lu, X. Shi, Q. Lu, L. Wang and H. He, ACS Sustainable Chem. Eng., 2021, 9, 10184–10195 CrossRef CAS
.
- N. Chouikhi, J. A. Cecilia, E. Vilarrasa-García, L. Serrano-Cantador, S. Besghaier, M. Chlendi, M. Bagane and E. R. Castellón, Biomass Bioenergy, 2021, 155, 106297 CrossRef CAS
.
- Y. Wang, X. He and Q. Lu, Cellulose, 2021, 28, 4241–4251 CrossRef CAS
.
- A. Rehman, G. Nazir, K. Y. Rhee and S.-J. Park, Chem. Eng. J., 2021, 420, 130421 CrossRef CAS
.
- R. Ahmadi, M. Ardjmand, A. Rashidi and M. Rafizadeh, Energy Sources, Part A, 2020 DOI:10.1080/15567036.2020.1845878
.
- M. F. A. Hernández, M. F. Rojas, F. Bernard, S. Einloft and L. A. C. Diaz, Fibers Polym., 2020, 21, 2861–2872 CrossRef
.
- S. Sepahvand, M. Jonoobi, A. Ashori, F. Gauvin, H. J. H. Brouwers, K. Oksman and Q. Yu, Carbohydr. Polym., 2020, 230, 115571 CrossRef CAS PubMed
.
- C. Hou, Y. Wu, T. Wang, X. Wang and X. Gao, Energy Fuels, 2018, 33, 1745–1752 CrossRef
.
- S. Campbell, F. L. Bernard, D. M. Rodrigues, M. F. Rojas, L. Á. Carreño, V. V. Chaban and S. Einloft, Fuel, 2019, 239, 737–746 CrossRef CAS
.
- W. Zhu, M. Ji, Y. Zhang, Z. Wang, W. Chen and Y. Xue, Polymers, 2019, 11, 2021 CrossRef CAS PubMed
.
- P. García-Gutiérrez, R. M. Cuéllar-Franca, D. Reed, G. Dowson, P. Styring and A. Azapagic, Green Chem., 2019, 21, 4100–4114 RSC
.
- F. Valdebenito, R. García, K. Cruces, G. Ciudad, G. Chinga-Carrasco and Y. Habibi, ACS Sustainable Chem. Eng., 2018, 6, 12603–12612 CrossRef CAS
.
- Y. Zhang, X. Gong, X. Chen, L. Yin, J. Zhang and W. Liu, Fuel, 2018, 232, 205–214 CrossRef CAS
.
- M. Gunnarsson, D. Bernin, Å. Östlund and M. Hasani, Green Chem., 2018, 20, 3279–3286 RSC
.
- C. Xu, C. Ruan, Y. Li, J. Lindh and M. Strømme, Adv. Sustainable Syst., 2018, 2, 1700147 CrossRef
.
- R. S. Dassanayake, C. Gunathilake, A. C. Dassanayake, N. Abidi and M. Jaroniec, J. Mater. Chem. A, 2017, 5, 7462–7473 RSC
.
- F. L. Bernard, D. M. Rodrigues, B. B. Polesso, A. J. Donato, M. Seferin, V. V. Chaban, F. Dalla Vecchia and S. Einloft, Fuel Process. Technol., 2016, 149, 131–138 CrossRef CAS
.
- K. J. Shah and T. Imae, Biomacromolecules, 2016, 17, 1653–1661 CrossRef CAS PubMed
.
- N. H. Mohd, N. F. H. Ismail, J. I. Zahari, W. Fathilah, H. Kargarzadeh, S. Ramli, I. Ahmad, M. A. Yarmo and R. Othaman, J. Nanomater., 2016, 2016, 4804271 Search PubMed
.
- T. Y. Han, S. K. Park and J. S. Lee, Bull. Korean Chem. Soc., 2016, 37, 689–694 CrossRef CAS
.
- Y.-J. Heo and S.-J. Park, Energy, 2015, 91, 142–150 CrossRef CAS
.
- H. Sehaqui, M. E. Gálvez, V. Becatinni, Y. Cheng Ng, A. Steinfeld, T. Zimmermann and P. Tingaut, Environ. Sci. Technol., 2015, 49, 3167–3174 CrossRef CAS PubMed
.
- C. Gebald, J. A. Wurzbacher, A. Borgschulte, T. Zimmermann and A. Steinfeld, Environ. Sci. Technol., 2014, 48, 2497–2504 CrossRef CAS PubMed
.
- C. Gebald, J. A. Wurzbacher, P. Tingaut and A. Steinfeld, Environ. Sci. Technol., 2013, 47, 10063–10070 CrossRef CAS PubMed
.
- X. He, J. A. Lie, E. Sheridan and M.-B. Hägg, Energy Procedia, 2009, 1, 261–268 CrossRef CAS
.
- L. Ansaloni, J. Salas-Gay, S. Ligi and M. G. Baschetti, J. Membr. Sci., 2017, 522, 216–225 CrossRef CAS
.
- S. Kang, X. Li, J. Fan and J. Chang, Renewable Sustainable Energy Rev., 2013, 27, 546–558 CrossRef CAS
.
- M. Nasrollahzadeh, M. Ghasemzadeh, H. Gharoubi and Z. Nezafat, J. Mol. Liq., 2021, 342, 117559 CrossRef CAS
.
- Z. Nezafat, M. M. Karimkhani, M. Nasrollahzadeh, S. Javanshir, A. Jamshidi, Y. Orooji, H. W. Jang and M. Shokouhimehr, Food Chem. Toxicol., 2022, 168, 113310 CrossRef CAS PubMed
.
- M. Nasrollahzadeh, F. Soleimani, Z. Nezafat, Y. Orooji and F. Ahmadpoor, Biomass Convers. Biorefin., 2023, 13, 12451–12465 CrossRef CAS
.
- Y. Zhu, Z. Li and J. Chen, Green Energy Environ., 2019, 4, 210–244 CrossRef
.
- B. A. López-Monreal and S. Loera-Serna, MRS Adv., 2022, 7, 504–507 CrossRef
.
- D. Saha, G. Orkoulas and D. Bates, Materials, 2023, 16, 455 CrossRef CAS PubMed
.
- L. Gong and A. Bao, J. CO2 Util., 2023, 68, 102374 CrossRef CAS
.
- M. Demir, T. Tessema, A. A. Farghaly, E. Nyankson, S. K. Saraswat, B. Aksoy, T. Islamoglu, M. M. Collinson, H. M. El-Kaderi and R. B. Gupta, Int. J. Energy Res., 2018, 42, 2686–2700 CrossRef CAS
.
- S. Park, M. S. Choi and H. S. Park, Carbon Lett., 2019, 29, 289–296 CrossRef
.
- D. Saha, S. E. Van Bramer, G. Orkoulas, H.-C. Ho, J. Chen and D. K. Henley, Carbon, 2017, 121, 257–266 CrossRef CAS
.
- S. Geng, J. Wei, S. Jonasson, J. Hedlund and K. Oksman, ACS Appl. Mater. Interfaces, 2020, 12, 7432–7441 CrossRef CAS PubMed
.
- J. Zhao, W. Zhang, D. Shen, H. Zhang and Z. Wang, J. Energy Inst., 2023, 107, 101179 CrossRef CAS
.
- S. Sani, X. Liu, M. Li, L. Stevens and C. Sun, Microporous Mesoporous Mater., 2023, 347, 112334 CrossRef CAS
.
- Y. Cui, B. He, Y. Lei, Y. Liang, W. Zhao, J. Sun and X. Liu, Chin. J. Chem. Eng., 2023, 54, 89–97 CrossRef
.
- M. Li, X. Liu, C. Sun, L. Stevens and H. Liu, J. Environ. Chem. Eng., 2022, 10, 107471 CrossRef CAS
.
- L. Shao, N. Liu, L. Wang, Y. Sang, P. Zhan, L. Zhang, J. Huang and J. Chen, Chemosphere, 2022, 288, 132499 CrossRef CAS PubMed
.
- E. Atta-Obeng, B. Dawson-Andoh, E. Felton and G. Dahle, Waste Biomass Valorization, 2019, 10, 2725–2731 CrossRef CAS
.
- L. Xu, Y. Xiu, F. Liu, Y. Liang and S. Wang, Molecules, 2020, 25, 3653 CrossRef CAS PubMed
.
- K. C. Kemp, V. Chandra, M. Saleh and K. S. Kim, Nanotechnology, 2013, 24, 235703 CrossRef PubMed
.
- J. Oh, Y.-H. Mo, V.-D. Le, S. Lee, J. Han, G. Park, Y.-H. Kim, S.-E. Park and S. Park, Carbon, 2014, 79, 450–456 CrossRef CAS
.
- C. Chen, D.-W. Park and W.-S. Ahn, Appl. Surf. Sci., 2014, 292, 63–67 CrossRef CAS
.
- P. Gruene, A. G. Belova, T. M. Yegulalp, R. J. Farrauto and M. J. Castaldi, Ind. Eng. Chem. Res., 2011, 50, 4042–4049 CrossRef CAS
.
- S. Yang, L. Zhan, X. Xu, Y. Wang, L. Ling and X. Feng, Adv. Mater., 2013, 25, 2130–2134 CrossRef CAS PubMed
.
- M. Zhao, J. Guo, Q. Xin, Y. Zhang, X. Li, X. Ding, L. Zhang, L. Zhao, H. Ye and H. Li, Sep. Purif. Technol., 2023, 324, 124512 CrossRef CAS
.
- H. Shi, J. Yang, Z. Ahmad, H. Zhang and J. Chen, Sep. Purif. Technol., 2023, 325, 124608 CrossRef CAS
.
- D. Rodrigues, J. Wolf, B. Polesso, P. Micoud, C. Le Roux, F. Bernard, F. Martin and S. Einloft, Fuel, 2023, 346, 128304 CrossRef CAS
.
|
This journal is © The Royal Society of Chemistry 2023 |
Click here to see how this site uses Cookies. View our privacy policy here.