DOI:
10.1039/D4TC01833H
(Paper)
J. Mater. Chem. C, 2025,
13, 3020-3027
Magnesium vapor-assisted deoxidation of La–Ce alloys through micro-alloying†
Received
5th May 2024
, Accepted 25th November 2024
First published on 23rd December 2024
Abstract
Deep deoxidation of La–Ce alloys using Mg vapor is a crucial process to ensure the quality of the alloy. In this study, we systematically investigated the effects of temperature, time and vacuum on the oxygen content in La–Ce alloys during the deoxidation with Mg vapor. The relationship between surface characteristics and the deoxidation process was also discussed. The results showed that the oxygen concentration of La–Ce alloys decreased to as low as 24 ppm after Mg vapor deoxidation. The Mg/MgO layers and micro-alloyed regions on the surface of La–Ce alloys were confirmed to be the driving force of deep oxidation.
1. Introduction
Rare earth (RE) elements are highly valued strategic metals that find extensive application in advanced technology industries, such as superconductive, electric, and nuclear industries, owing to their unique optical, electrical, and magnetic properties.1–3 Among cerium-based alloys, lanthanum–cerium alloys are the most commonly used due to their low cost, excellent technical specifications, and diverse functions such as hydrogen and oxygen inclusion purification, grain refinement, and micro-alloying. These alloys serve as effective additives to enhance the overall performance of metallic materials, particularly in the steel industry.4,5 The research and development of rare earth elements and rare earth steels have been carried out in the field of metallurgy for many years.6,7 The first introduction of rare-earth materials into steel dates back to the 1920s in the United States.8 Since then, rare-earth steels have been studied globally, and these studies have demonstrated the attractive advantages of rare-earth additions to steel.9–11 However, due to the fluctuating properties of rare earth steels and the clogging of nozzles during the casting process, they have not been widely used in industry.12
In recent years, the Institute of Metals Research of the Chinese Academy of Sciences13 has revealed that inconsistent performance of rare-earth steels and nozzle blockages are caused by the oxygen content. The performance of rare earth steels is affected not only by the oxygen content in the molten steel, but more significantly by the oxygen content in the added rare earth metals. After rare earth additions in a high purity GCr15 bearing steel, it presented a remarkable 40 times increase in fatigue life under ±800 MPa tensile fatigue compared to a bearing steel without rare-earth addition. Additionally, fluctuations pose a potential risk to the fatigue life of rare-earth containing alloys with 270 ppm oxygen content in rare-earth metals in commercial use. Only a few hundred grams of lanthanum and cerium light rare earth alloys need to be added to tons of steel, with no significant increase in cost or change in process conditions. Therefore, improving the purity of lanthanum and cerium alloys, particularly reducing the content of oxygen impurities, is of great significance and advantageous for China's rare earth resources. This will balance the excessive production of light rare earth resources and enhance the quality of special steels as additives.
However, the low melting point and low vapor pressure of La–Ce alloys make it challenging to create suitable deoxidation conditions under high temperature and vacuum conditions.14,15 Moreover, oxygen removal from La–Ce alloys is extremely difficult due to their high affinity for oxygen. To address this, reducing the chemical potential of oxygen in La–Ce alloys is necessary.16–18 A more chemically active metal can act as an external driving force, taking advantage of its stronger binding energy with oxygen,19 by which the thermodynamic prohibition and kinetics of oxygen diffusion may be solved through close contact between the active metal and the sample.20 Materials with higher oxygen affinities, such as Ca, Y, and Mg, are often used for this purpose.
In previous study, our group conducted oxygen reduction on La–Ce alloy ingots through Ca and Y deoxidation.21 The results confirmed that these two external getters participated in the deoxygenation reaction in the molten and solid forms, respectively. However, studies on the removal of oxygen impurities from rare earth metals by active metals in the gaseous form are insignificant. Therefore, we explored the potential of the Mg vapor deoxidation method using the solid–vapor reaction of La–Ce alloys and Mg with several advantages including a short process time, convenient recovery, and excellent deoxidation ability.22 In this study, the changes of the oxygen content and surface characteristics of La–Ce alloys after magnesium vapor deoxidation were investigated systematically, and the deoxidation process was analyzed in detail by establishing a deoxidation model.
2. Thermodynamic calculations
For the deoxidation using a solid phase external getter, the affinity of the getter for oxygen must be greater than that of the metal being refined.14,15 However, there was limited research on the use of the Mg metal for deoxidation of rare earth metals, compared to Ca and Y. To investigate the suitability of magnesium for removing oxygen impurities from La–Ce alloys, the Gibbs free energy of reaction with oxygen was calculated and the results are shown in Fig. 1. The reaction Gibbs free energy between oxygen and La, Ce, gaseous Mg and solid Mg should be critically considered. The affinity order of these elements for oxygen is: Mg(g) > Y(s) > Ca(s) > Ce(s) > La(s) > Mg(s). The use of a solid phase external getter allows deoxidation at lower temperatures (below the melting point of La–Ce alloys at 993 K) and under low vacuum conditions. Additionally, the formation conditions of Mg vapor were determined by calculating the saturation vapor pressure, and the results are shown in Fig. 2. Mg had a higher vapor pressure than Ca and Y, and a large amount of Mg vapor for deoxygenation can be formed in the experimental temperature range.
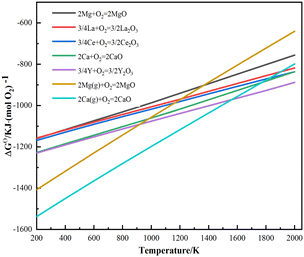 |
| Fig. 1 Gibbs free energy changes with temperature for the reaction of La, Ce, Y, Ca and Mg with O. | |
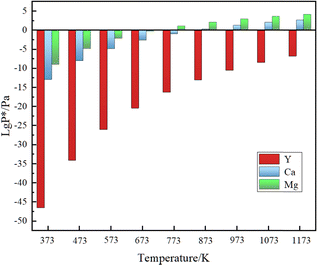 |
| Fig. 2 Saturated vapor pressure of Ca, Mg and Y as a function of temperature. | |
Oxygen atoms were present within the lattice interstices in the solid solution state in the La–Ce alloys, as well as in mixed oxide phases consisting of La2O3, Ce2O3 and CeO2 on the surface.23,24Table 1 shows the Gibbs free energy of the reaction between magnesium vapor and La2O3, Ce2O3 and CeO2. The results indicated that oxidation–reduction reactions can occur between the Mg vapor and the oxygen present on the surface and bulk of La–Ce alloys. This reduced the oxygen concentration on the surface and facilitated the migration of oxygen impurities from the interior to the surface, which were eventually removed by the reaction. Thermodynamic calculations suggested that it was feasible to reduce the oxygen content in La–Ce alloys by the Mg vapor.
Table 1 Free energy changes with temperature for the reactions of Mg with La2O3 and Ce2O3
Temperature (K) |
3Mg(g) + La2O3 → 3MgO + 2La ΔG (KJ mol−1) |
3Mg(g) + Ce2O3 → 3MgO + 2Ce ΔG (KJ mol−1) |
2Mg(g) + CeO2 → 2MgO + 2Ce ΔG (KJ mol−1) |
673 |
−196.451 |
−180.691 |
−248.729 |
773 |
−159.251 |
−143.200 |
−225.700 |
873 |
−122.264 |
−105.839 |
−202.861 |
973 |
−85.502 |
−68.612 |
−180.213 |
1073 |
−48.973 |
−31.976 |
−157.983 |
3. Experimental
3.1. Experimental procedure
Fig. 3 shows the experimental procedure for the deoxidation of La–Ce alloys, in which the content of Ce was 60%. La–Ce alloys were cut into a size of L10 mm × W5 mm × H20 mm, and each sample weighed approximately 6–7 g. The surface of the samples was abraded with a 100 to 1000 mesh sandpaper to remove impurities and then rinsed ultrasonically with ethanol. Then the samples were dried and used for experiments immediately to prevent surface oxidation. Mg particles with 99.95% purity and the La–Ce alloy were mixed directly in a graphite crucible, and the weight ratio of Mg to the sample was 1
:
1.5. The deoxidation was performed at 623–873 K for 0.5–4 h in a vacuum.
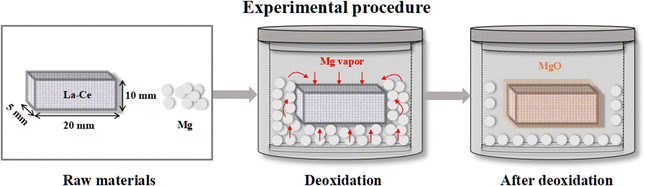 |
| Fig. 3 Schematic diagram of the experimental flow of the external getter. | |
3.2. Characterization
The oxygen concentration in the La–Ce alloy after deoxidation was measured using an oxygen/nitrogen/hydrogen analyzer (ONH-836, America) and the test sample must be internal to the metal, so the alloy was cut open to take samples from the center of the alloy when testing, and tested immediately after removing the test sample, and 3 positional points were selected to test each time to reduce errors. The concentration of Mg in the La–Ce alloy was determined by inductively coupled plasma mass spectrometry (ICP-MS, Agilent 7700s, America), with volume up to 10 ml at a time. The microstructure of the La–Ce alloy before and after the deoxidation was studied using a scanning electron microscope (SEM, TM303Plus, Japan), and the accelerating voltage was 3 kV for morphology shooting and 15 kV for spectral mapping. The structure of the La–Ce alloy after deoxidation was examined using a transmission electron microscope operated at 200 kV(TEM, JEM-F 200, Japan). The phases of the sample were characterized by X-ray diffraction (XRD, X&apos-Pert 3 Powder, England) using Cu Kα (40 kV and 40 mA) radiation. The patterns were scanned by a speed of 2°/min from 10° to 90°. The structure data were employed for phase determination, as shown in Table 2.25,26
Table 2 The main phase structure data of La–Mg and Ce–Mg systems
Phase |
Space group |
a (Å) |
b (Å) |
c (Å) |
Ref. |
CeMg12 |
I4/mmm |
10.33 |
10.33 |
5.96 |
25
|
La2Mg17 |
63/mmc |
10.36 |
10.36 |
10.24 |
26
|
Ce5Mg41 |
I4/m |
14.78 |
14.78 |
10.43 |
25
|
4. Results and discussion
4.1. The dependence of the oxygen concentration on the annealing temperature
Thermodynamic calculations and kinetic analyses21 showed that not only the thermodynamic advantage of magnesium deoxidation decreased at higher temperatures, but also the kinetic limitation of magnesium deoxidation decreased. At the same time, the higher the temperature, the more favorable to the evaporation of the magnesium metal. In order to study the dependence of the oxygen concentration on the annealing temperature, the experimental conditions were set to be a vacuum degree of 5 × 10−2 Pa, a vacuum sealing tube maintained under the condition of a vacuum degree of 0.02 MPa, a holding time for 2 h, and a temperature range of 623–873 K.
As shown in Fig. 4, the oxygen concentration in the La–Ce alloy tended to decrease and then increase with the increase of the annealing temperature during the process of deoxidation. The reason should be that with the increase of temperature, the evaporation rate of magnesium increases, and a large amount of magnesium vapor was generated, which promoted the removal of oxygen impurities in the La–Ce alloys. However, when the temperature was too high, the thermodynamic advantage of magnesium vapor deoxidation decreased, the contact area between the magnesium vapor and the base metal was limited at the same time, and the deoxidation efficiency decreased. The oxygen concentration in the sample was reduced from 550 ppm to 24 ppm at T = 723 K, the removal rate of oxygen impurities reached 95.6%, and the oxygen concentration in samples was also the lowest under the experimental conditions.
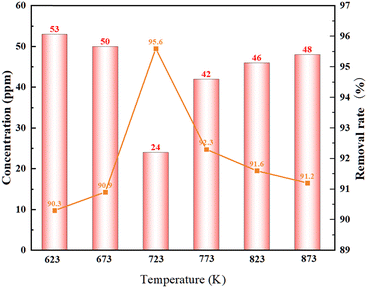 |
| Fig. 4 Variation of the oxygen content with the annealing temperature in the La–Ce alloy after deoxidation by the magnesium vapor. | |
4.2. The influence of the annealing time on oxygen dependence
The annealing time was also an important influence factor during the process of deoxidation, and to further investigate its influence on magnesium deoxidation, the experiment was conducted under the experimental conditions of temperatures of 673 K, 723 K, and 773 K, and a vacuum degree of 5 × 10−2 Pa, and the results are shown in Fig. 5.
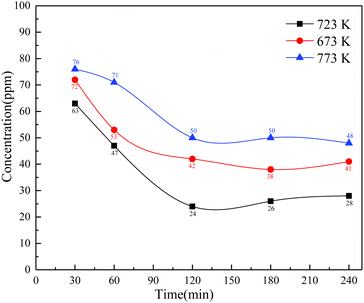 |
| Fig. 5 Variation of the oxygen content in the La–Ce alloy with time after deoxidation of the magnesium vapor. | |
Fig. 5 shows that the oxygen concentration in the La–Ce alloys at different experimental temperatures was decreasing before an annealing time of 3 h, and then stabilizing. Especially at an optimum temperature of 723 K, the oxygen concentration in the La–Ce alloys decreased to 24 ppm in the annealing time up to 2 h. Continuing to prolong the annealing time, the oxygen concentration tended to increase slightly, which indicated that the effect of deoxidation was getting more and more unstable after a long annealing time, and it might be attributed to the formation of deoxidation products and the mutual diffusion of the La–Ce alloy and magnesium after the prolonged deoxidation reaction.
4.3. The influence of vacuum on deoxidation
A higher vacuum was helpful to avoid the influence of the furnace atmosphere on the experiment and reduce the oxidation of the samples, so the whole experiment should be carried out under high vacuum conditions. In order to further determine the influence of vacuum on deoxidation, the variations of the oxygen concentration under two vacuum levels of 5 × 10−2 Pa and 5 Pa were investigated under the conditions of 723 K and 2 h.
As shown in Fig. 6, the lower the vacuum, the lower the oxygen concentration. Meanwhile, the lower vacuum could avoid the sample contamination due to the furnace atmosphere and reduce the kinetic limitations of deoxidation, thus promoting the diffusion of oxygen impurities in the sample and improving the deoxidation efficiency. Considering the improvement of deoxidation efficiency and the shortening of the annealing time, the optimum vacuum level in this experiment is 5 × 10−2 Pa.
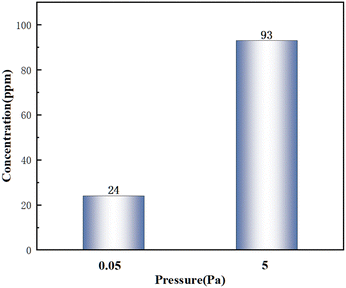 |
| Fig. 6 Variation of the oxygen concentration in the La–Ce alloy with vacuum after magnesium vapor deoxidation. | |
Table 3 shows the oxygen analyses of different materials from references, although a detailed kinetic analysis was not carried out in the work, it could be found that the lower deoxidation temperature and the shorter deoxidation time with a better deoxidation effect were achieved.
Table 3 The deoxidation analyses of some materials
Raw material |
Deoxidizer |
Temperature (K) |
Time (h) |
Oxygen concentration (ppm) |
Ref. |
La–Ce alloy |
Mg |
723 |
2 |
24 |
This work |
La–Ce alloy |
Ca |
873 |
8 |
54 |
21
|
La–Ce alloy |
Y |
873 |
8 |
55 |
21
|
Off-grade Ti |
Mg |
933 |
0.5 |
1200 |
27
|
Ti |
Y/YOCl/YCl |
1173 |
48 |
240 |
28
|
Niobium |
Ca |
1173 |
20 |
110 |
29
|
4.4. Relation between the surface morphology and the deoxidation reaction
The experiments were conducted to investigate the interaction between Mg and the base metal during deoxidation. Fig. 7 displays the elemental distribution of the sample surface after deoxidation. SEM imaging revealed that magnesium was uniformly distributed on the surface of the La–Ce alloys after deoxidation, and a typical region of the Mg layer covering the base metal surface was formed, which showed that magnesium microalloyed at the interface with the base metal by slight diffusion. In order to further investigate the degree of microalloying, EDS line scanning was carried out on the cross-section of the sample, as shown in Fig. 8, from which it can be clearly seen that the thickness of the Mg layer was about 40 μm, the microalloyed area is mainly in the range of 40–80 μm, and the depth of diffusion of Mg was about 80 μm, which was easy to be removed by grinding in the later stage.
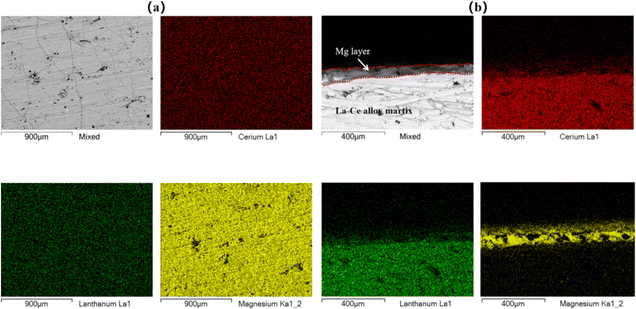 |
| Fig. 7 Surface (a) and cross-sectional morphology (b) of the La–Ce alloy after Mg deoxidation. | |
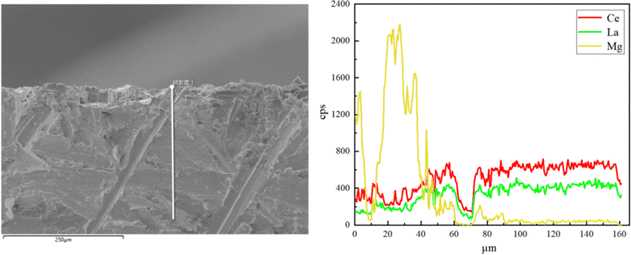 |
| Fig. 8 EDS line scan at the contact interface with the Mg deoxygenated La–Ce alloy and Mg. | |
To further confirm the relationship between Mg and the base metal interior, the area near the Mg layer was thinned, using precision ion milling, and the TEM microstructures and EDS analysis results of the La–Ce alloy after deoxidation are shown in Fig. 9. The low-magnification image and the elemental distribution map of the edge of the Mg layer at the right, as well as the high-magnification micrograph and the elemental distribution map of the corresponding area are also presented in Fig. 9(a); it could be seen that there was no significant variation in the microstructure of the La–Ce alloy in low-magnification and and high-magnification micrographs, and the distribution of La, Ce and a small portion of Mg was essentially overlapped in the base metal interior, but the content of Mg was not detected according to the EDS analysis results shown in Fig. 9(b). In addition, Fig. 9(b) also shows that the content of La and Ce inside the alloy after deoxidation is the same as the initial content of the alloy (La-60%Ce), which indicates that the Mg layer is only formed on the surface of the alloy and Mg was not present within the base metal interior and it will not cause the contamination to interior of the alloy during deoxidation.
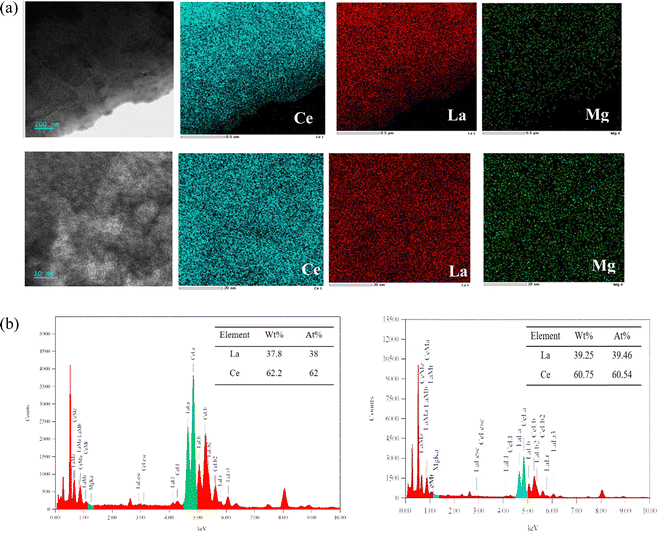 |
| Fig. 9 The TEM micrographs (a) and EDS analysis results (b) of the La–Ce alloy after deoxidation. | |
The XRD results of the deoxygenated sample surface are shown in Fig. 10. The formation of deoxidation product MgO and a microalloyed region consisting of CeMg12 and La2Mg17 was recognized,30,31 which was also confirmed by the phase diagram. Table 4 demonstrates that there were no significant changes in the content of Mg before and after deoxygenation, indicating that the magnesium vapor deoxygenation did not contaminate the base metal interior.
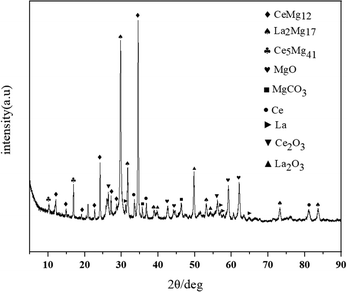 |
| Fig. 10 XRD patterns of the sample surface after Mg is deoxygenated. | |
Table 4 ICP-MS results of Mg in the La–Ce alloy
Element |
Raw material-Mg |
Deoxidation material-Mg |
Content (10−6) |
100 |
92 |
4.5. Deoxidation pathways of Mg vapor as an external getter
Based on the microstructure observation, the mechanism of removal of oxygen impurities by magnesium vapor during the whole deoxidation process is shown in Fig. 11. The deoxidation reaction using Mg vapor takes place according to the following reaction equations: | Mg(g) + [O]La–Ce → MgO(s) | (1) |
| 3Mg(g) + Re2O3(s) → 2Re(s) + 3Mg(s) | (2) |
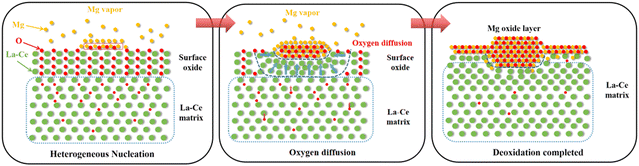 |
| Fig. 11 Process of magnesium vapor removal of oxygen impurities in the La–Ce alloy. | |
As the temperature increases, the Mg metal gradually evaporates and magnesium vapor is produced. Then, the oxide layer on the surface of the La–Ce alloy would react with magnesium vapor, leading to a continuous decrease of the surface oxygen concentration in a redox reaction. The formation of Mg/MgO nuclei during the initial stage of deoxidation attracted oxygen diffusion towards that region, leading to the occurrence of micro-alloying between magnesium and matrix metal atoms. After the deoxidation was completed, a Mg/MgO layer (thickness about 40 μm) and a microalloying area (thickness about 40 μm) were formed on the surface of the lanthanum–cerium alloy sample.
5. Conclusions
In this study, La–Ce alloys with a low concentration of oxygen were prepared using Mg vapor as a solid phase external getter, and the surface characteristics of the La–Ce alloys before and after Mg vapor phase deoxidation were systematically investigated. The following conclusions were drawn from the present work:
(1) As the temperature increased, the oxygen concentration in the La–Ce alloy first decreased and then increased, and the lowest oxygen content decreased to 24 ppm after annealing at an optimum temperature of 723 K for 2h. The lower degree of vacuum increased the deoxidation efficiency.
(2) A Mg/MgO layer of 40 μm thick and a microalloyed area of 40 μm thick mainly composed of CeMg12 and La2Mg17 were formed on the surface of the La–Ce alloy after deoxidation.
(3) The diffusion depth of Mg in the La–Ce alloy is only 80 μm, which does not contaminate the interior of the base metal.
Author contributions
Wenxia Xie: conceptualization, validation, investigation, and writing – original draft. Congli Lu: conceptualization, methodology,validation, and writing – original draft. Xuechen Ren: conceptualization and methodology. Fei Wang: writing – review and editing and supervision. Baoqiang Xu: conceptualization. Bin Yang: conceptualization.
Data availability
All data presented in this article are available in the original references cited. The original XRD results are supplemented in the ESI.†
Conflicts of interest
On behalf of all authors, the corresponding author states that there is no conflict of interest.
Acknowledgements
This research work is financially supported by the National Natural Science Foundation of China (92475108 and 52374414). We also greatly appreciate the Institute of Metal Research, Chinese Academy of Sciences for providing sufficient raw materials. This study was also supported by Mr Zou Lin of Shandong Hengbang Smelting Co., Ltd. in ICP-MS detection.
References
- X. Y. Song, J. X. Zhang, M. Yue, E. D. Li, H. Zeng, N. D. Lu, M. L. Zhou and T. Y. Zuo, Technique for preparing ultrafine nanocrystalline bulk material of pure rare-earth metals, Adv. Mater., 2006, 18, 1210–1215, DOI:10.1002/adma.200502619.
- H. Liu, Y. Zhang and Y. K. Luan, Research Progress in Preparation and Purification of Rare Earth Metals, Metals, 2020, 10, 1–13, DOI:10.3390/met10101376.
- F. X. Qin, N. S. Bingham, H. Wang, H. X. Peng, J. F. Sun, V. Franco, S. C. Yu, H. Srikanth and M. H. Phan, Mechanical and magnetocaloric properties of Gd-based amorphous microwires fabricated by melt-extraction, Acta Mater., 2013, 61, 1284–1293, DOI:10.1016/j.actamat.2012.11.006.
- G. L. Li, H. Guo, L. Li, C. Y. Wang, J. Zheng, W. H. Tian, H. P. Li and X. G. Li, Purification of terbium by means of argon and hydrogen plasma arc melting, J. Alloys Compd., 2016, 659, 1–7, DOI:10.1016/jjallcom.2015.10.180.
- B. H. Wu, X. F. Ding, Q. K. Zhang, L. J. Yang, B. Z. Zheng, F. Q. Hu and Z. L. Song, The dual trend of diffusion of heavy rare earth elements during the grain boundary diffusion process for sintered Nd-Fe-B magnets, Scr. Mater., 2018, 148, 29–32, DOI:10.1016/j.scriptamat.2018.01.021.
- D. Li, P. Wang and X. Q. Chen,
et al., Low-oxygen rare earth steels, Nat. Mater., 2022, 21, 1137–1143, DOI:10.1038/s41563-022-01352-9.
- R. Ganguli and D. R. Cook, Rare earths: A review of the landscape, MRS Energy Sustainability, 2018, 5, E9, DOI:10.1557/mre.2018.7.
- B. C. McLellan, G. D. Corder and A. Golev,
et al., Sustainability of the rare earths industry, Proc. Environ. Sci., 2014, 20, 280–287, DOI:10.1016/j.proenv.2014.03.035.
- L. A. Smirnov, V. A. Rovnushkin, A. S. Oryshchenko, G. Y. Kalinin and V. G. Milyuts, Modification of steel and alloys with rare-earth elements. Part 1, Metallurgist, 2016, 59, 1053–1061, DOI:10.1007/s11015-016-0214-x.
- L. M. Wang, Q. Lin, J. W. Ji and D. N. Lan, New study concerning development of application of rare earth metals in steels, J. Alloy. Compd., 2006, 408–412, 384–386, DOI:10.1016/j.jallcom.2005.04.090.
- G. A. Lillieqvist and C. G. Mickelson, Properties of cast steels improved with rare earth element additions, JOM, 1952, 4, 1024–1031, DOI:10.1007/BF03397760.
- N. Kojola, S. Ekerot, M. Andersson and P. G. Jonsson, Pilot plant study of nozzle clogging mechanisms during casting of REM treated stainless steels, Ironmaking Steelmaking, 2011, 38, 1–11, DOI:10.1179/030192310X12690127076398.
- D. Z. Li, P. Wang, X. Q. Chen, P. X. Fu, Y. K. Luan, X. Q. Hu, H. W. Liu, M. Y. Sun, Y. Chen, Y. F. Cao, L. G. Zheng, J. Z. Gao, Y. T. Zhou, L. Zhang, X. L. Ma, C. L. Dai, C. Y. Yang, Z. H. Jiang, Y. Liu and Y. Y. Li, Low-oxygen rare earth steels, Nat. Mater., 2022, 1476–4660, DOI:10.1038/s41563-022-01352-9.
- F. Tian, G. L. Li, L. Li, Z. Q. Wang, S. H. Yan and X. G. Li, Advance in solid-state purification technology for metals, J. Alloys Compd., 2014, 592, 176–184, DOI:10.1016/j.jallcom.2013.12.260.
- T. H. Okabe, T. N. Deura, T. Oishi, K. Ono and D. R. Sadoway, Electrochemical deoxidation of yttrium-oxygen solid solutions, J. Alloys Compd., 1996, 237, 150–154, DOI:10.1016/0925-8388(95)02129-9.
- T. H. Okabe, K. Hirota, E. Kasai, F. Saito, Y. Waseda and K. T. Jacob, Thermodynamic properties of oxygen in RE-O (RE = Gd, Tb, Dy, Er) solid solutions, J. Alloys Compd., 1998, 279, 184–191, DOI:10.1016/50925-8388(98)00690-2.
- G. L. Li, H. Guo, L. Li, C. Y. Wang, J. Zheng, W. H. Tian, H. P. Li and X. G. Li, Purification of terbium by means of argon and hydrogen plasma arc melting, J. Alloys Compd., 2016, 659, 1–7, DOI:10.1016/j.jallcom.2015.10.180.
- G. L. Li, L. Li and K. Fu,
et al., Hydrogen in-situ refining method for preparing high purity gadolinium, J. Alloys Compd., 2015, 648, 29, DOI:10.1016/j.jallcom.2015.06.222.
- G. L. Li, L. Li, R. Y. Miao, W. H. Tian, S. H. Yan and X. G. Li, Research on the removal of impurity elements during ultra-high purification process of terbium, Vacuum, 2016, 125, 21–25, DOI:10.1016/j.vacuum.2015.12.003.
- J. K. Wang, K. Fu, X. G. Li and G. L. Li, Behavior of impurity elements in pure gadolinium during ultra-high purification, Vacuum, 2019, 162, 67–71, DOI:10.1016/j.vacuum.2019.01.007.
- C. L. Lu, Y. Z. Chen, Y. H. Bai, B. Q. Xu, H. Liu, B. Yang, Y. K. Luan and F. Wang, Deoxidation purification of La-Ce alloy by solid state external gettering, Vacuum, 2023, 213, 112086, DOI:10.1016/j.vacuum.2023.112086.
- T. Kim and J. W. Lim, Surface characterization of Ti and Ti–6Al–4V alloy by Ca vapor deoxidation: Relation between surface morphology and deoxidation reaction, Appl. Surf. Sci., 2022, 590, 153098, DOI:10.1016/j.apsusc.2022.153098.
- Q. B. Ren, P. C. Zhang, M. F. Chu and W. P. Gong, Process of Surface Oxidation of Ce-5%La Alloy, J. Chin. Soc. Rare Earths, 2007, 730–735, DOI:10.3321/j.issn:1000-4343.2007.06.017.
- W. P. Gong, R. Zhang and Z. S. Cheng, Thermodynamic modelling and applications of Ce-La-O phase diagram, Trans. Nonferrous Met. Soc. China, 2011, 21, 2671–2676, DOI:10.1016/S1003-6326(11)61109-6.
- F. Liu, L. Fang and Z. Li,
et al., Diffusion behaviors and mechanical properties of binary Mg–Ce system, Vacuum, 2023, 216, 112409, DOI:10.1016/j.vacuum.2023.112409.
- X. Li, T. Yang and Y. Zhang,
et al., Kinetic properties of La2Mg17–x wt.% Ni (x= 0–200) hydrogen storage alloys prepared by ball milling, Int. J. Hydrogen Energy, 2014, 39, 13557–13563, DOI:10.1016/j.ijhydene.2014.04.123.
- S. H. Park, H. J. Jeoung and T. H. Lee,
et al., Development of deoxidation process for off-grade titanium sponge using magnesium metal with wire mesh strainer type of crucible, Sci. Rep., 2024, 14, 542, DOI:10.1038/s41598-023-50765-2.
- H. Fang, Y. Zhao and L. Kong,
et al., Study on the deep deoxidation mechanism of titanium powder using Y/YOCl/YCl3 and Y/Y2O3 systems, J. Alloy. Compd., 2024, 177132, DOI:10.1016/jjallcom.2024.177132.
- S. Liu, R. O. Suzuki and K. Ono, Solid state deoxidation of niobium by calcium and magnesium, J. Alloy. Compd., 1998, 266, 247–254, DOI:10.1016/s0925-8388(97)00509-4.
- X. Hua, Q. Yang and D. Zhang,
et al., Microstructures and mechanical properties of a newly developed high-pressure die casting Mg-Zn-RE alloy, J. Mater. Sci. Technol., 2020, 53, 174–184, DOI:10.1016/j.jmst.2020.04.030.
- S. Couillaud, E. Gaudin and J. L. Bobet, Rich magnesium ternary compound so-called LaCuMg8 derived from La2Mg17. Structure and hydrogenation behavior, Intermetallics, 2011, 19, 336–341, DOI:10.1016/j.intermet.2010.10.011.
|
This journal is © The Royal Society of Chemistry 2025 |
Click here to see how this site uses Cookies. View our privacy policy here.