DOI:
10.1039/D4SU00267A
(Critical Review)
RSC Sustain., 2024,
2, 3704-3729
Progress in waterborne polymer dispersions for coating applications: commercialized systems and new trends
Received
27th May 2024
, Accepted 24th October 2024
First published on 25th October 2024
Abstract
The environmental impact and safety of products have become increasingly prominent in recent years, with stringent legislation expected to persist. Polymeric coatings are pervasive in modern life, serving to impart desirable properties and protection to a wide range of surfaces. Traditionally dispersed in volatile organic solvents harmful to the environment and workers, modern coatings are shifting towards waterborne, minimizing harmful environmental emissions. Waterborne coatings have seen substantial commercial uptake in large sectors such as architectural and automotive coatings. Nevertheless, their performance still lags behind conventional systems, and, currently, some products lack commercially viable waterborne alternatives. This review focuses on the current state of commercialized waterborne polymer systems, scrutinizing their performance, composition, and market penetration. Additionally, it explores future trends aimed at addressing existing challenges and pioneering novel coating technologies, with an emphasis on achieving fully sustainable systems.
Sustainability spotlight
Existing waterborne polymeric coatings are essential to modern lifestyle but their manufacture frequently results in harmful emissions to workers and the environment. A shift from more harmful chemicals to safe and environmentally friendly water is necessary for fully sustainable coatings. In this review, progress on waterborne coating systems is reported with currently commercialized products highlighted and scrutinized. The future for waterborne coating systems is analyzed, with a focus on current impediments to wider adoption, as well as making fully sustainable systems using biobased and biodegradable polymers. Waterborne coating systems advance each of the following important UN sustainable development goals: good health and well being (SDG 3), industry, innovation, and infrastructure (SDG 9), responsible consumption and production (SDG 12), and climate action (SDG 13).
|
1. Introduction
Polymerically coated surfaces have become ubiquitous in modern life. From house paint to food packaging, kitchenware to synthetic leathers, a myriad of products leverage the properties imparted by the polymeric coating in tandem with the substrate to provide improved material appearance, functionality, or performance.1–5 At the same time, these coatings must remain competitive with alternative options in terms of cost, availability, environmental impact, and other pertinent indicators.1,6
Even as a thin surface coating, polymers offer substantial advantages over non-polymeric materials. A broad range of tunable materials enables the selection of a polymer system that fulfills a wide range of color ranges, textures, and appearances, ranging from metallic luster to imitation leather, matte finish and more.7–9 Moreover, these surfaces can be tailored to exhibit high performance in areas, such as water and vapor barrier properties (high barrier or selectively porous membranes), UV and corrosion resistance, electrical conductivity, flexibility, and impact strength, thereby enhancing the properties of or safeguarding the underlying substrate.1 Furthermore, polymer coatings facilitate the generation of smart surfaces, providing functionalities, such as antimicrobial surfaces, actuators, and active packaging.10–13
There are multiple methods available for coating polymers onto surfaces, including extrusion, powder coating, and liquid carriers. Drawbacks associated with extrusion and other hot melt methods include high processing temperatures and handling costs due to the highly viscous polymer melt.14,15 For some materials, like poly(hydroxybutyrate-valerate) (PHBV) and polylactic acid (PLA), extrusion methods can yield brittle films,16,17 while liquid-borne coating method allows for flexible film formation.6 Powder coating enables the application of thin, uniform coatings without requiring an evaporation step, although it necessitates an initial melting stage for powder formation and encounters challenges such as powder agglomeration and moisture control.18 Other liquid-free coating methods, such as press, supercritical fluid, and cold spray coating are also used in specialized applications.19,20
When using a liquid carrier, the polymer is either dissolved in or dispersed within a suitable solvent, which is subsequently evaporated after surface coating.21 Liquid carriers are chosen to enable evaporation at lower processing temperatures compared to other film preparation methods involving polymer melting.21 Coating polymers from within a liquid medium offers a broad range of application methods, such as spraying, dipping, rod coating, and more.3 Liquid coating is also preferred when functionality or multicomponent systems are involved, as it allows for self-stratification of different components.22
Waterborne systems are preferred over organic solvents whenever possible due to their superior environmental friendliness and enhanced safety features, including reduced fire, explosion, and worker physiological risks.23,24 It is important to note that within this review work, ‘solvent’ or ‘solventborne’ refer to organic liquids that can act as hazardous pollutants. Initially, waterborne systems gained popularity because of their ability to achieve sufficiently high solid weight percentages (wt%) while substantially reducing targeted emissions.23 Higher solids percentage results in smaller equipment sizes, faster drying time, and reduced storage and transportation costs.25 Achieving higher solids percentages in dispersions is possible because the system is no longer constrained by the amount of polymer that can dissolve in the solvent or form via reaction, as the viscosity remains relatively low as desired.26,27 Rather than viscosity being dictated by the hydrodynamic interactions between the dissolved polymer and the solvent, the viscosity is largely dictated by particle size, and any added rheological modifiers.6,26,28,29 While waterborne and high solids content were initially synonymous with one another,23 some applications of waterborne polymer systems now do not necessarily require high solids content to be industrially practical.4,30
However, designing waterborne systems is still limited by several drawbacks. Chiefly, many polymer systems do not dissolve or disperse well in water and instead prefer organic solvents.31 Additionally, water-phase polymerization of monomer to obtain waterborne polymers is not possible for many preformed polymers, including biopolymers, many of which are of interest for sustainable coatings.21 As a result, substantial resources must be allocated to create a suitable dispersion. Additionally, while higher wt% means lower storage and shipment costs than organic solvent systems, dry systems offer even better cost-effectiveness in this regard. Storage and shipment can also be complicated by the poor stability arising in many waterborne systems.32 Organic solvents are also still frequently required as part of the overall process.6,23 Lastly, the evaporation temperature for water is often higher than its organic solvent counterparts.26 A summary of these benefits and remaining drawbacks is provided in Fig. 1.
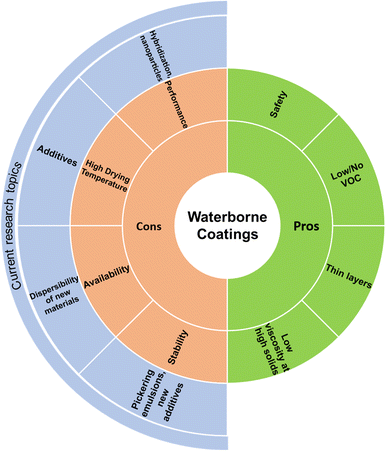 |
| Fig. 1 Benefits and drawbacks to waterborne coating systems compared to existing alternatives. | |
While there are multiple methods available, the predominant approach for obtaining waterborne polymer dispersions of preformed polymers (not emulsion polymerizable) is through phase inversion.21 In this process, the preformed polymer is dissolved in a suitable organic solvent, which is immiscible in water. Subsequently, water and a surfactant are added to the solution alongside an energy input. The organic solvent is then evaporated, leaving the polymer dispersed in water.6 Although an organic solvent is still used in this process, the quantity required can be significantly reduced compared to non-waterborne processes. Moreover, it can be better controlled and recovered during the preparation process, and in some cases, it may be eliminated entirely with alternative preparation methods.23,33
The waterborne dispersion is subsequently cast onto a substrate, and as water evaporates, the polymer particles undergo merging to form a homogeneous coated surface.21 Initially, as water evaporates, the dispersed polymer spheres pack closely together due to the decreasing volume and start to deform to fill in void spaces. With sufficient temperature (above the minimum film forming temperature, or MFFT), the spheres coalesce, with the polymer chains interpenetrating and forming a continuous film.21,26,34,35 It is important to note that this process is specific to dispersed polymer systems, which require spherical particle deformation and coalescence, rather than dissolved polymer systems.26 These steps are illustrated in Fig. 2. While the process involved for dispersed systems is more complex, it can be beneficial in tuning film morphology.36 Different dispersed particles exhibit greatly varying coalescence behavior, as opposed to dissolved systems, where behavior is nearly uniform.36
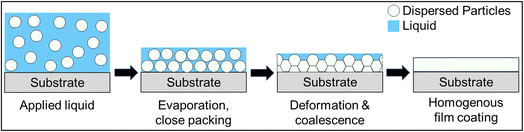 |
| Fig. 2 Process of film formation from liquid polymer dispersions. | |
Currently, waterborne dispersions are used in place of solventborne in some of the largest use case coatings industries, including the biggest, architectural applications.23,37 Advances in waterborne technology have also allowed their use for wood coatings, automotive, and more.38,39 As the technology continues to advance, replacement of conventional coatings for applications, such as paper packaging,21 availability of water-insoluble polymers like polyhydroxyalkanoates,35 novel applications including smart packaging,40 and stabilization methods such as Pickering emulsions41 will all continue the expansion of the waterborne coatings industry.
This review paper sets out to showcase the most recent challenges and developments in waterborne polymer coatings. The latest progress in improvements to stability, breadth of materials, and industrial viability is critically reviewed. As well, current industrial uptake and the future of waterborne system advancement and adoption is thoroughly discussed.
2. Established waterborne polymer systems
Waterborne coatings have gained significant traction across various commercial applications, offering a multitude of benefits. They provide grease/moisture barrier properties in packaging products, mitigate moisture and microbial attack in wood finishes, and enhance corrosion resistance in metal substrates. Notably, waterborne coatings constitute the largest global class of coatings,42 and they substantially reduce the volatile organic compounds (VOC) content compared to solventborne coatings, thereby benefiting both workers and the environment.23,24 Additionally, dispersion coatings can utilize less solid material than dry coating methods like extrusion.35 Although formulating waterborne coatings to match the stability and performance as conventional coatings presents challenges,32 ongoing advancements are steadily enhancing their efficacy. Consequently, the market adoption of waterborne coatings is projected to continue rising in the foreseeable future.43
2.1. Wood coatings
Uncoated wood, whether indoors or outdoors, is highly vulnerable to environmental damage and degradation. Factors, such as moisture, radiation, microorganisms, temperature variations, mechanical stresses, and chemical exposure can easily compromise its integrity.44,45 The frequency and intensity of these stressors in a given environment dictate the degree of protection which must be imparted by the selected coating.44 The biopolymers constituting wood (polysaccharides, lignin, phenolics) are particularly susceptible to degradation caused by ultraviolet (UV) and biological attack.45 Due to the high incidence of fungal growth, moisture control is of utmost importance.45,46 While some wood treatments involve chemical modification of the wood or the addition of fillers, wood coatings remain the standard for providing protection.47,48
In addition to imparting protection, wood coatings are commonly used to enhance the visual appearance of the product, and must meet consumer expectations in terms of aesthetics.44,49 This can pose challenges, especially for applications requiring extensive protection, such as exterior products, and even more so when a clearcoat finish is desired to preserve the natural beauty of the wood.49 Clearcoats typically allow UV transmittance through the coating to the wood substrate, leading to photodegradation and coating delamination.49 In such cases, the coating alone may not suffice, necessitating the combination with pretreatments or other measures to stabilize the wood.49 Extensive research has been conducted to develop successful clearcoats that do not require additional treatments, such as using silicone coatings with metal additives. However, the protective and longevity performance of these clearcoats has yet to match that of opaque alternatives.38,49
In general, waterborne wood coatings for exterior applications are based on polyurethane, acrylic, or alkyd based polymers.38 Polyurethane coatings exhibit strong weathering and mechanical degradation resistance.38 Since polyurethane is incompatible with water, various waterborne dispersing methods are employed to generate waterborne systems.50 As well, the fundamental polyurethane formation reaction of a polyol with a polyisocyanate should not be performed in the presence of water as the water and isocyanate reaction will react as shown in Scheme 1.51 Common industrial methods include forming a hydrophilic pre-polymer that is then polymerized in water or conducting the formation in acetone and then transferring to water when removing the acetone.50 Less commonly, hot-melting or using a ketimine–ketazine process are reported.50 Other waterborne polyurethane (WPU) polymerization methods under development include homogenous solution (HSP), reversible addition–fragmentation chain transfer (RAFT), miniemulsion (MEPP), and atom transfer radical (ATRP).52 While the pre-polymer and acetone methods remain the most widely used, advantages of the other processes include benefits such as being a single-step procedure in the case of the miniemulsion process and the hot-melt process being solvent-free.50,52
 |
| Scheme 1 Undesired reaction between polyisocyanates and water. | |
Acrylic solutions offer strong UV resistance, dry quickly, and possess good adhesion to wood.38 However, they may contain micropores, which allow fungal penetration and degradation of the wood, and often require additional measures to prevent fungal growth.38,53 Acrylic coatings are typically produced through emulsion co-polymerization to form a stable colloidal dispersion in water.44 Alternatively, solution, bulk, and suspension polymerization are used to a limited degree industrially, with miniemulsions also being employed for some waterborne acrylic hybrids.54,55 Waterborne self-emulsifying hybrid acrylics are under development which are solvent-free, but do not appear to be industrially employed.56 Lastly, alkyd resins for wood coatings offer distinct benefits, including a glossy appearance and potential for auto-oxidative curing.38 Alkyd dispersions in water can be formed either via direct emulsification or through phase inversion methods.57
Alkyd and acrylic resins are often combined to mitigate individual disadvantages, typically utilizing water-soluble alkyds for wood coating applications.38,44 For example, the acrylic backbone generally provides superior physical toughness and durability to the resulting coating, while the alkyd resin promotes chemical resistance and visual appeal.56 For interior applications, where the degradative stresses on wood are much lower, protective performance is of reduced concern.30,58 The same polymers serve as the basis of interior wood waterborne coatings, albeit with simpler formulations required.59 Multi-coat systems are prevalent, including combinations like acrylic primers and polyurethane top-coating, or hybridized versions thereof.60 Coating additives encompass components acting as colorants, fillers, thickeners, dispersants, UV absorbers, and more depending on the desired properties.45 Biopolymers, such as lignin, chitin, and zein all have potential to displace some current conventional wood coatings with biodegradable alternatives.45 However, material availability, costs, and more complex formulations act as barriers to commercial adoption.61
Wood coatings are typically applied via spraying, brushing, or dipping methods.46 Subsequently, the coating undergoes curing, which can involve applying heat to facilitate surface coalescence, using UV light or another reaction initiator when the system is not yet fully polymerized such as some polyurethanes, or drying at ambient conditions.44,50,62 In addition to these conventional surface coating methods, there are alternative pressurized and non-pressurized methods available for achieving deeper penetration, such as the Bethell process and Gedrian's Bath.46 However, these methods tend to be costly, and are generally reserved for chemical treatment and nanoparticle impregnation rather than combined with surface coating applications.46
Unfortunately, waterborne wood coatings still exhibit numerous drawbacks. In exterior applications, water barrier properties are of utmost concern to avoid fungal growth, yet waterborne coatings tend to have higher hydrophilicity than conventional coatings.63 Conversely, for interior applications, mechanical resistance is the most desired property, and waterborne coatings often fall short.61 These challenges are further complicated by wood's inherent properties, such as its porosity, which leads to dimensional changes as moisture levels fluctuate. Consequently, coatings must be flexible and possess strong surface adhesion to prevent deterioration and decay over time.46 Nevertheless, significant strides, including nanoparticle incorporation and other modifications to existing coatings or the development of novel waterborne formulations, have enabled the mitigation of these issues, offering a promising future for the continued utilization of improved waterborne wood coatings.46,61
2.2. Paints
Paints encompass a vast category, characterized by diverse purposes, polymers, substrates, and coating methods. However, their primary function is always to enhance appearance and, in commercial contexts, to provide some level of protection to the underlying substrate.64,65 Consequently, paints typically contain colorants alongside polymeric resin and other additives.65–67 Architectural paints dominate market segment size, comprising over 50% of worldwide volume, and include both indoor and outdoor paints with ∼75% of the coatings being waterborne.39,42,68 Other significant applications include automotive, coil, and marine coatings, all of which are discussed in this work. Although numerous additional paint applications exist, such as toys and home appliances, they occupy smaller market shares and research interests, often exhibiting substantial technological overlap with the aforementioned segments.69 For many years, the paint industry raised environmental and occupational concerns due to high VOC emissions. However, a combination of innovation and legislation has significantly reduced emissions, favoring lower VOC options like waterborne paints.23,39,70
2.2.1. Automotive paints.
Automotive paints represent some of the most complex coatings, with multiple distinct layers required to meet the stringent appearance, lifespan, and environmental resistance requirements which are demanded by consumers.66,71 Automotive coatings are highly competitive among companies with consumers holding high expectations, and having been subject to substantial environmental and worker safety regulations.42,72–74 These factors have contributed to automotive coatings having substantial significance to the overall coatings industry (outsized beyond market share) as it has been involved in many industry innovations, from formulations to application methods.71,73 Relevant to this work, waterborne exterior automotive paints began to be introduced in the 1980s for basecoats, with waterborne primer and clearcoats following in the 1990s.39
Broadly, automotive coatings can be divided into exterior and interior applications, with exterior coatings necessarily undergoing much greater environmental stress.66 Exterior metal automotive parts involve multiple layers of coating, including an initial corrosion resistant layer known as the electrodeposition coat (E-coat), followed by a primer, basecoat, and a clearcoat, applied in this order, as shown in Fig. 3.42,75
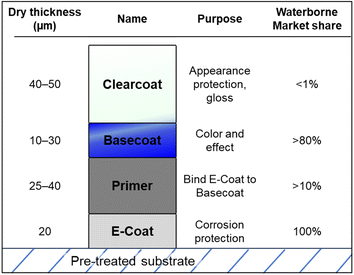 |
| Fig. 3 Layers of a typical automotive exterior paint stack, with estimates of global waterborne market share within each standard automotive exterior coating layer.39,72,75–78 | |
Additional coating layers are also applied to areas for specific purposes, such as anti-chip coatings on the hood and lower body between the e-coat and primer layers, and additional rustproofing and sound deadening of the underbody.71 Exterior plastic parts, such as bumpers and mirror shells, are frequently coated to match the appearance of their metallic counterparts, and can be coated independently of the metal components (offline), or mounted and then metal and plastic parts coated all at once (inline/online depending on at which layer the plastic and metal components are combined).79 In either case, the basecoat and clearcoat products are identical, as is the application equipment, such that the components appear identical.79 Rather, the primary difference between components is in the primer layers and initial treatment steps. For electrostatic basecoats (uncommon) only, an offline or inline (mounted after E-coating) plastic component must be coated with an electrically conductive primer or have electrical conductivity integrated into the substrate.79 Online coated systems (mounted prior to pretreatment) must be capable of withstanding temperatures of 160–190 °C used for E-coat drying, limiting some plastics from being mounted early in the process.79,80 While not itself a layer, there is also an initial pretreatment step. Pretreatment ensures that the surface is smooth and free of contaminants and dust, and possesses desired surface energy and tension, allowing for better coating adhesion and smooth film formation.79,81 Pretreatment requirements are even more stringent when waterborne coatings are involved, with the current industry standard being a multi-zone water power wash and dry to avoid the introduction of organic solvents.71,79,82 For plastic components, the pre-treatment stage may also include the use of an adhesion promoting layer, as coating adhesion is frequently the most challenging part of using coated plastic components.80
2.2.1.1. Electrodeposition coat (E-coat).
Following pretreatment, the first coating layer applied is designed to provide corrosion resistance and is known as the electrodeposition coat or E-coat.71 Modern E-coats overwhelmingly provide protection via barrier properties (as opposed to sacrificial or inhibitor coatings) whereby the coating blocks water, salt, and oxygen from reaching the underlying metal surface.83 This layer also serves to enhance chip-resistance and contributes to the overall durability of the coating stack, often working in conjunction with the primer.72,83 Initially, anodic electrodeposition was used for coating application, but modern processes overwhelmingly use cathodic electrodeposition whereby the metal is negatively charged and the paint is positively charged.71 The coating is applied via a dip tank, for which the car body passes through a tank (∼90 °F) containing majority deionized water (80–90%), paint solids (10–20%), and some solvent.71 The car body then enters a bake oven at 160–190 °C for 10 minutes to allow evaporation, crosslinking, and uniform film formation.71,79,80 Solvent content is very low, below 0.5%, thus this layer is typically considered environmentally friendly from an emissions perspective.71,83 Final coated thicknesses are around 20 μm, with the process standardized and highly reliable to the point where many manufacturers have only a single electrocoating tank/line feeding all further downstream coating lines.83 A further benefit of the dip tank method is that internal surfaces which would otherwise be difficult to reach are also coated.71,84 These tanks are very large, with a material turnover rate (theoretical rate of tank contents by feed material) of two weeks to six months.83
The paint solids makeup is typical of a waterborne paint, being majority (70%) comprised of a waterborne resin and a cross-linker, with the remainder being pigment grinding and stabilizing resin, pigments, and extenders and additives, such as dispersants, stabilizers, and cross-linking catalysts.83 The resin composition is typically an epoxy blend (such as bis-phenol) which further incorporates polyesters, polyacrylates, and polyurethanes, with rubber also occasionally included to further improve energy absorption and thus chip resistance.83,85–89 While any crosslinking functional group could be used, for best solubility and consistent film formation, primary amine substitution is highly preferential.83,85 Similarly, many crosslinking agents are available, however modified polyisocyanates are currently heavily favored by industry due to their high reactivity and capability to fine-tune final film properties.85,90 Waterborne epoxy dispersions are principally prepared commercially using either chemical modification or phase inversion techniques.91–93 Phase inversion waterborne epoxy is more widely applied due to being more easily performed, but yields products with worse size distributions and stability than more carefully controllable modification reactions.91 Automotive Original Equipment Manufacturer (OEM) coating is oligopolistic, with BASF, PPG, and Axalta (Dupont pre-2013 (ref. 94–96)) providing nearly all exterior coatings, and with these products highly engineered specifically for automotive applications.39
For E-coating, their respective products are CathoGuard® (BASF), ENVIRO-PRIME® & POWERCRON® (PPG), and AquaEC™ (Axalta).97–99 The chemical reactions at the electrodes produce oxygen and hydrogen, which can present as bubbles in the film if the bath and/or drying temperatures are insufficient to allow for their release.83 Other common defects include craters, pinholes, boil outs, hash marks, and “water spots”, which can be removed by sanding.71,83 Overall, drawbacks to the waterborne approach currently employed are relatively few. Among these, the primary issues are preventing bacterial growth in the large open water tanks used for coating, the necessity and intensity of the pretreatment steps, and the high energy associated with baking the E-coat layer.72,83,85 As the percentage of metal components replaced with polymer composites as the substrate for exterior automotive applications continues to grow, the demand for and purpose of this layer may change significantly.71,80
2.2.1.2. Primer.
A primer (or primer surfacer) is the next layer applied, and primarily serves to ensure a high-quality bond between the E-coat and the topcoat (basecoat + clearcoat).100 Secondarily, the primer acts as another layer of chip resistance, and enhances the overall paint appearance by providing a smooth coating surface for finishing.71 Lastly, the primer acts to block UV from reaching and delaminating the E-coat, as the topcoat thicknesses and compositions are usually insufficient for this purpose due to the focus being on final appearance.100
Solventborne, waterborne, and powder primers are available, with solventborne still dominant worldwide but with waterborne standard in Europe and powders heavily used in the United States, due to stricter environmental and safety regulations in these markets phasing out solventborne options.89,100 Regardless of format, the polymer content is usually acrylic, polyurethane, or polyester crosslinked with alkyoxylated melamine.84 Powders have the advantages over waterborne of having near zero volatile content, as well as waste from overspray being able to be recycled.74 On the other hand, waterborne systems are more easily retrofitted into existing manufacturing plants,101 as well as having thinner films and lower material usage.74 Color of the primer is chosen to roughly match the color of the basecoat, such that a chip which penetrates to the primer is less visible.84,102 Depending on the type of primer and application method, typical thicknesses range from 25–40 μm.72,84
Recently, there have been successful efforts to remove the primer layer entirely by shifting its responsibilities to other layers. Beyond material savings and emission reductions from the coating layer itself, this has the further benefit of reducing the number of “bakes” or curing steps which occurs from the current standard of 3 bakes down to 2. Note that despite 4 layers, there are only 3 bakes since with the standard process the topcoat consisting of base and clearcoats is always applied wet-on-wet then cured with a single bake.103 The standard 4-coat-3-bake (4C3B) process as well as primerless deviations is shown in Fig. 4. There would be substantial environmental benefit from development of widely applicable waterborne systems requiring fewer coating and baking steps.103
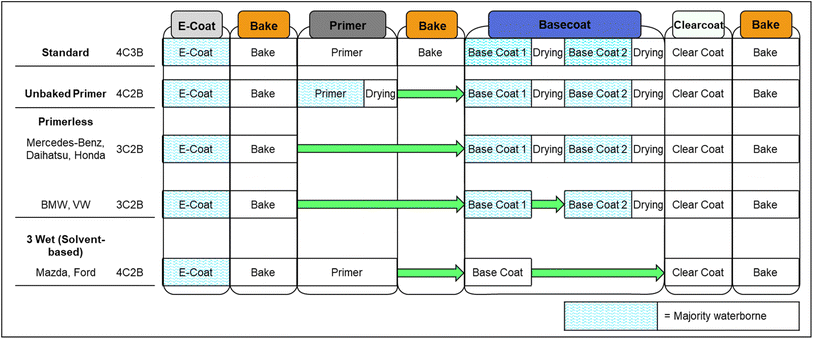 |
| Fig. 4 Standard automotive coating process and variations thereof. Steps where waterborne coatings are the dominant choice are highlighted. | |
A primerless system incorporating isocyanate into the basecoat to impart better chip and UV resistance has been used by Volkswagen (VW) and BMW at various plants in Mexico, Spain, the United States, the United Kingdom, and more.66,104 Daihatsu and Mercedes-Benz have also used a 3-coat-2-bake (3C2B) which retains dying between layers, while Mazda and Ford have employed a 4C2B solventborne system retaining the primer where each layer is applied wet-on-wet.74 However, these methods described have not gained worldwide adoption as they generally sacrifice the majority of the chip and UV resistance aspects imparted by the conventional primer and are thus ill-suited for high corrosion risk geographic areas, as well as having a lower lifespan before UV-caused delamination will occur.89 As such, while as much as 50% of vehicles in economically developing regions are made without the primer layer for cost purposes,66 the focus here is on waterborne primerless systems which can compete with conventional systems in terms of performance. More recently, Honda has introduced a 3C2B system to a plant in Brazil, in which two waterborne basecoats and clearcoat are all applied and then cured in a single bake.89,103 This method retains the increased durability and quality imparted by the primer layer, but shifts the responsibility to the first basecoat layer.89 Defect control also becomes more difficult as the three successive waterborne layers compounds the risks of popping and sagging occurring.89 In the standard process depicted in Fig. 4, basecoat 1 and basecoat 2 are the same coating just applied multiple times (e.g. 2× with bell applicators or bell followed by pneumatic spray).66 As a result, the Honda process does have four formulaically distinct coatings similar to the standard process.89 Further, the responsibilities of the standard primer have been shifted nearly exclusively to the new basecoat 1 layer, while conventional basecoat responsibility for color development is now solely provided by basecoat 2.103 Therefore, the distinction between the primer in the standard process and basecoat 1 employed in the Honda process is not clear, and the author feels the Honda process could fairly be regarded as a 4C2B system with a single-application basecoat replacing the conventionally double-applied basecoat. Regardless, it should be recognized that the Honda technology depicted in Fig. 4 is distinct from that of Mercedes-Benz and Daihatsu, as while the process steps are the same the more recent Honda technology incorporates greater vehicle protection measures.103 Similarly, the BMW process listed works similarly to that of Honda, shifting the responsibilities of the primer to a new basecoat 1 distinct from basecoat 2, making it also effectively a 4C2B system.104 Also, the numbering conventions differ between publications and manufacturers, likely in part due to it being beneficial to claim any reduction in the number of coats or bakes. There are also references to 3C1B systems which ignore the 1C1B aspect of the initial E-coat, however in this paper that is always counted as a discrete step.105
Toyota has also published research into applying the primer, basecoat, and clearcoat followed by a single bake for the three layers.105 Toyota notes that the appearance of the single bake systems is conventionally inferior to that of the traditional 4C3B system, and so has been confined largely to economy-class vehicles.105 To improve surface smoothness of the basecoat (and thus the basecoat/clearcoat interface) as well as the final coating appearance and quality, the glass transition temperature (Tg) of the acrylic resin should be reduced, and melamine substituted with an isocyanate hardener.105
2.2.1.3. Basecoat.
The main purpose of the basecoat is to provide the desired color and visual appearance effects to the vehicle.72,106 Because of the high quantity of pigments and additives, basecoats are the most expensive layer in the vehicle paint stack.84 Basecoats typically have a thickness of 10–20 μm.72,84 However, the thickness is dependent on the colour and incorporated effects, and how well they exhibit black-white hiding.66 Silver and white tend to be thinner, while chromatics such as red may be as high as 30 μm.66 Monocoat systems (single topcoat layer rather than separate basecoat and clearcoat) were the standard until 1970, and remain available in limited capacity.66,107,108 However, they have been phased out in North America and other markets where the improved durability and appearance of the 2C1B topcoat outweighs the increase in cost.66,109
White is by far the most popular color worldwide as it was utilized for 35% of new vehicles in 2021, the locally leading color in nine out of 10 identified major market regions, and the global lead for the past eleven years.110,111 Despite this, white's share has been slowly declining as chromatic (non-white, black, gray, or silver) colors have increased in popularity, albeit still representing <20% of the market.110,111 Black and gray tie for 2nd place with 19% each, with the only market where white is not in 1st place being Europe, where it is in 2nd place behind gray; at 27% for gray and 23% for white.110 It should be noted that the large coating companies, BASF and Axalta, both classify silver as a separate category from gray; at nearly 10% of new global vehicles the combination of silver and gray would be solidly above black for 2nd place, although black retains an outsized share in the luxury vehicle segment.110,111 While white leads in nearly all regions, its largest lead is also home to the highest automotive production volume, with just under 50% of vehicles in Asian regions having white coatings.110,111 TiO2 (titanium white) is overwhelmingly used as the white pigment, both for automotive and other applications, and in fact nearly 95% of global titanium production is for titanium white.66,112,113 However, due to photocatalytic degradation caused by unmodified TiO2, the TiO2 particles are coated with layers of both SiO2 and AlO3 to prevent photooxidation of the coating matrix.66,114 There are over 40
000 distinct automotive base coatings which have appeared on the market, with over 1000 released annually.66 The color and desired visual effect largely impacts the selection of pigments and additives rather than the resin, with insoluble pigments as opposed to soluble dyes being overwhelmingly chosen for automotive applications due to their superior lightfastness.66
Waterborne basecoats use an acrylic and/or polyester as the main binder, as a partially cross-linked core–shell emulsified polymer.66,84 Co-binders are additional polyesters or polyurethanes, while melamine provides more cross-linking upon baking.66,84 Shear-thinning behavior is critical (as with most paints), and for waterborne basecoats this is generally achieved by incorporating silicates.66,115 Thixotropic behavior not only prevents defects, such as sagging, but is also necessary for proper flake orientation during drying (also aided by high volume shrinkage caused by the evaporation), and preventing settling in supply tanks.66,84,116 However, the low-shear viscosity cannot be too high or else proper levelling of the film will not occur, so the choice and quantity of additives must be done with great care.116 Solid basecoats can be applied as a single coat while more complex paint effects, such as metallic paints, require two coats to properly achieve the desired visual effect.74 In the past 10 years, waterborne basecoats have overtaken solventborne options within major markets, driven by environmental regulations.117–119
Waterborne basecoats remain a significant source of emissions, as VOC content is typically still 10–15%.66,72,120 While the shift to waterborne paints (and other improvements) has cut automotive VOC emissions to less than 10% of the level seen in the 1970's, development of waterborne basecoats without the need for an appreciable VOC content is critical to eliminating remaining emissions.72
2.2.1.4. Clearcoat.
Clearcoats are the final layer applied, and act to both protect the appearance of the vehicle and impart a glossy visual effect.84,106 Typical thicknesses are 40–50 μm, applied via spraying.72,84 The clearcoat is applied directly onto the basecoat, without an intermediary baking step.84 However, there is a brief drying/flashing stage which dries the basecoat to be as high as 90% solids content.72,78
The clearcoat must be durable against multiple adverse conditions, including temperature, UV, abrasion, impacts, airborne pollutants, and acid rain.84,121 As a result, durable resins must be chosen, and all formulations include ultraviolet light absorbers (UVAs) and hindered amine light stabilizers (HALS) to assist with longevity.84 Waterborne clearcoats generally use polyester-acrylate resin which is crosslinked with melamine and/or blocked isocyanate.66,122 Since the late 1990s, top clearcoats have employed nanosilica to improve scratch resistance and gloss retention.75
While waterborne clearcoats were first available in 1990, as of 2008 they constituted <1% of the global clearcoat market, and remain similarly low today.66 Instead, solventborne clearcoating remains dominant, with powder coating capturing a small (<5%) portion, but edging out waterborne coatings as the environmentally friendly clearcoat option chosen by industry.66,78 Isocyanate is difficult to incorporate into waterborne systems without incurring unwanted reactions or extremely short pot life, and has been among the key limitations on waterborne clearcoat development.123,124 The high thickness of the clearcoat layer has been noted as another key issue, as a waterborne clearcoat will then require substantial energy and time for evaporation, as well as increased risk of improper curing.125,126 Despite this, waterborne clearcoats are available on the market, and see moderate adoption in the refinishing segment.125,127 However, regardless of whether waterborne or powder clearcoats are chosen, widespread OEM adoption will only occur if forcibly imposed via stricter emission regulations.119,125
2.2.1.5. Automotive interiors.
Interior automotive surfaces employ a variety of coatings to bestow specific appearances and textures, as well as improve durability.42 Waterborne polyurethane (WPU) is the most employed, being used for synthetic leather surfaces, nonwoven fiber protection, and as a clear coating.5,128 WPU is also extensively employed throughout other parts of automobiles, for example as adhesives and foams.129 As a coating, WPU is known to provide excellent mechanical properties, as well as vital resistance to UV and weatherability.128 Coated fibers such as those constituting floor mats are dip coated, while synthetic leathers are coated then dried (and surface coagulated) via a variety of proprietary methods such as applying acids or heat depending on the formulation and desired appearance.5,130 The microsphere structure of the resulting surface plays a strong role in the resulting appearance, with a smoother surface appearing glossier while a rougher surface appears matte (approximately linear relationship).5,131–133 Control of the surface morphology can be performed through control of crosslinking, such as through additives, as crosslinking increases roughness and thus decreases gloss, and vice versa.5,9 Surface heterogeneity also plays a large role in gloss determination.134 For automotive leathers, the WPU chosen is generally based on an aliphatic diisocyanate for superior long-term durability.135 The selection of polyol (WPU's are obtained by reaction of polyol and diisocyanate) is more varied depending on the specific desired effects, with polyester, acrylic, polyether, and polycarbonate-based polyols all seeing use.135,136 The surface coating will also incorporate acrylic emulsions, as well as typical additives such as pigments and rheological modifiers.135 These WPU synthetic leather surfaces are also used for other products, such as furniture, clothing, and accessories, however the high weatherability and durability requirements for automotive applications makes the application of particular interest, as successful coatings can then generally be applied to other products with lesser requirements.5
2.2.1.6. Other waterborne automotive coatings.
There is interest in converting the remaining solventborne coatings still in use to waterborne counterparts, such as for engine coatings.137 As well, there is continued innovative improvement of systems such as waterborne flaky aluminum pigments in order to suppress existing issues with corrosion (novel double-layered surface decoration),138 addition of nanoparticles to existing dispersions for improved performance,139,140 improvement of WPU self-healing properties,141 and invention of smart coatings which can react to varied environmental stimuli.71 Lastly, it should be noted as well that the information presented is specifically for OEM coatings rather than refinish coatings unless otherwise specified. Refinish coatings must cure at temperatures between ambient and 60 °C, and do not have access to intensive coating processes, making waterborne applications inconsistent and expensive.119,123,142,143 As a result, while the polymer composition of the coatings remains very similar, resin with a lower glass transition temperature may be used in order to achieve better curing.142 Waterborne refinishing coatings are therefore much tougher to formulate as faster-drying coatings and therefore lower boiling point solvents are more desirable.142 With that in mind, automotive refinishing shops are aware of the benefits to worker health in using waterborne coatings over solventborne, and have been seen to voluntarily switch to waterborne as they have been made more readily available.144 As painting currently consumes 30–50% of the total energy input to the automotive manufacturing process, development of waterborne coatings which can be cured at lower temperatures would result in enormous energy savings, compounding their environmental returns.72,103
2.2.2. Coil coatings.
Coil coatings have the primary purpose of imparting corrosion protection to metal, particularly aluminum and steel.42 The metal comes uncoated as coils, is unrolled and coated, then rerolled or immediately formed into the final product.42,68 Since the coating is applied to flat metal sheets and then formed, the coating must be highly flexible such that tight bends can be achieved without cracking or delamination.68 As well, as mentioned, the coating must be highly corrosion resistant, have weatherability resistance for outdoor applications, and be durable.68
Unlike architectural coatings where waterborne coatings are the majority, for coil coatings waterborne adoption is still extremely limited (<1% of market) due to relatively poor performance and higher costs, as well as operational difficulties.42,68,145,146 The few industrial systems which do exist employ acrylic or acrylate–epoxy hybrid dispersions.42,147 Solventborne coil coatings are conventionally polyesters (frequently siliconized), polyvinylidene fluoride (PVDF), polyvinyl chloride (PVC), and polyurethanes.42,68,146 Each of these polymers with the exception of PVC has seen successful waterborne formulations for coil coating at lab-scale.42,145,146 It is important to note as well that the coating performed while the sheet is flattened involves multiple stages and coatings, along with pretreatment. There is frequently a primer/basecoat as well as the topcoat, so ideally the entire system must be changed to be waterborne, increasing complexity.42 The waterborne coatings are applied in the same manner as solventborne coil coatings, primarily via continuous rollers.42,68 However, solventborne coil coatings are also occasionally coated using electrostatic high-speed discs.68
2.2.3. Architectural.
Architectural coatings are by far the largest coatings market segment, by both revenue and product volume.23,37 Architectural coatings encompass both indoor and outdoor coatings (especially paints) which improve the appearance of our buildings, while also providing environmental protection to the underlying substrate.65,148,149 Waterborne coatings make up over 70% of the global architectural coatings market, driven by being the standard for interiors (the largest subsegment).42 Current interior architectural coatings have very low of zero VOC content.34 While waterborne interior coatings have been available for over 60 years,42 waterborne products meeting the more strenuous performance demands of exterior environments has only been met in the past few decades.150 The higher demands for exterior coatings include resistance to chalking, water absorbance, yellowing, acidity, abrasion, extreme temperatures, and more.54,148–150
Currently, waterborne architectural coatings most commonly employ acrylic, styrene–acrylic, alkyd (hybridized, often with styrene/acrylic), polyvinyl acetate, or polyurethane polymer dispersions, with silicones occasionally added.54,150–154 5–35% of the waterborne paint is the resin by volume.65 Pigment, extenders, surfactants, and rheology modifiers are also nearly always present in the formulation while UV absorbers, dispersants, biocides, defoamers, adhesion promoters, slip agents, and more are added as desired for the specific application.65,148 Rheological behavior of architectural coatings is critical, as they are generally applied relatively thickly (brush/roller as opposed to spray etc.) to vertical surfaces and then dried at ambient conditions.42,65 A general guide to the desired magnitude of shear thinning is provided in Fig. 5.65 As waterborne formulations are typically known for having low viscosity, without addition of a thickener the paint will be prone to issues, such as runs, drips, and sags.65 Associative and cellulosic thickeners are the most common thickeners for waterborne architectural coatings.42 Due to the number of components in the formulation, the rheological characteristics are quite complex and thus formulations cannot be made via modelling alone.65 Alongside the rheological modifier additive, the polymer particle size (smaller = more viscous),28 the surfactant, and polymer volumetric concentrations majorly influence the resultant behavior, while factors such as the pigment have a much smaller effect.65
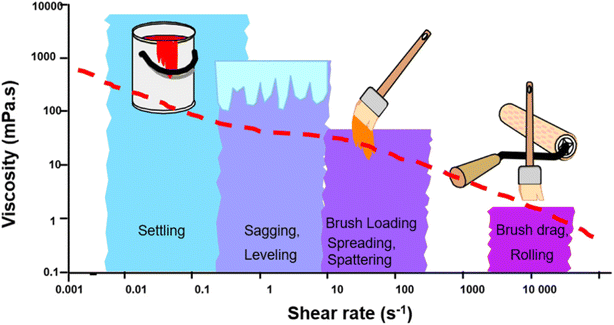 |
| Fig. 5 Desired relationship between viscosity, shear rate, and paint properties. Reproduced from ref. 65 with permission of Elsevier © 2022. | |
Continued innovation in waterborne architectural coatings includes complementation of a broader range of substrates (wood, stone, etc.),148,149 better waterproofing lifespan for high demand applications such as roof sealing,151 and nanoparticle additives for improved properties, such as dirt resistance and antibacterial activity.155–157 As the architectural coating market continues to expand and with waterborne architectural coatings continuing to be the dominant option, further research and sustainability regulations may allow further advances, such as bio-renewable and biodegradable resins to become economically viable.34,70 In the meantime, the very low VOC content of current architectural coatings acts as a goal for other industries still primarily using solventborne coatings.70
2.2.4. Marine.
For marine coatings, the most important aspects are corrosion resistance and anti-biofouling properties.42,158 Biofouling of large ships can lead to fuel cost increases of over 40%, as well as other issues such as introduction of invasive species.159,160 For anti-biofouling, there are two classes of coating in this space: self-polishing antifouling coatings and foul-release coatings.42,159 Self-polishing marine coatings employ a biocide which is soluble or reactive with the water, and thus is gradually stripped off over time maintaining a relatively smooth surface.42,159 The vast majority of these paints were acrylics incorporating tributyltin (TBT) until TBT was banned worldwide in 2008 due to its harmful environmental effects.159,160 Now, other organometal biocides, primarily copper pyrithione (CuPT), are used, despite persisting environmental concerns.159
Foul-release coatings are the primary alternative, using an ultra-smooth surface to stop adhesion of microorganisms to the surface.42 Fluoropolymers and siloxanes, such as polydimethylsiloxane (PDMS), are incorporated into polymeric materials including waterborne polyurethane (WPU).42,161 While the PDMS provides the smooth surface, the WPU promotes substrate adhesion, has low cost, and during drying allows for migration of siloxane groups to the surface.42 Ideally, foul-release coatings would be so smooth that initial adhesion to the surface is halted. However, there is still some adhesion to foul-release coatings in practice.161 Nevertheless, these adhered fouling organisms can be removed easily during cleaning.161 As a result, this has not been a significant barrier to adoption, and adoption of foul release coatings increased from less than 1% of the market in 2009 to over 10% in 2014.159 The largest barrier to further increase is the high cost and requirement for frequent re-application, which can be over 100 USD/L for material alone. While such cost can be justifiable for large commercial boats spending millions on fuel per year, it is exorbitant for the recreational vessels constituting 20% of the market.159 The other key issue with foul-release coatings is that they usually require a high amount of ship movement to effectively prevent adhesion; as a result, they are ineffective for many vessels and temporary underwater structures which remain stationary for extended periods of time.159,161 In fact, some shipping companies that committed to adopting foul-release coatings after the 2008 ban on TBT later switched back to biocidal copper paints, such as Maersk in 2012, due to poor foul-release coating performance.159
Some coatings newer to the market look to combine the benefits of both antifouling and foul release coatings, or otherwise improve upon the performance of siloxane-based foul release coatings. Sol–gel coatings are available which allow for extremely smooth surface finishes further hindering initial adhesion of fouling agents, allowing effective fouling prevention even for vessels at rest.159 Other coatings employ microencapsulated biocides, which are slow-released leading to over 95% lower biocide emitted than with the traditionally water-soluble biocides.162
Beyond the antifouling topcoat for components directly submerged in water, the primer and various fillers provide critical corrosion resistance to all marine components. The intensity of required resistance varies greatly depending on multiple factors, such as location on the interior or exterior of the vessel, fresh or salt water, or presence of the marine component in the water splash zone.163,164 Waterborne primers and top coats based on acrylics, epoxy, and urethanes are employed, mostly for low-corrosion stress applications.163 High-stress applications, such as ocean-submerged pipelines do not use waterborne coatings as they cannot compete in terms of resistance, durability, or cost.163 Waterborne styrene–acrylic copolymers are also widely used commercially as metallic substrate primers, and additives such as zinc phosphate are used to promote anticorrosive properties.42,164 In addition to ship hulls, other immersed metal components, such as pipelines and offshore platforms, require coating for anti-corrosion and biofouling resistance.161,164 Anti-corrosion coatings are further required for any components exposed atmospherically or periodically to the marine environment, such as shipyards, metallic bridge structures, holds, and other interior areas.158,163,164
The application and drying process of waterborne marine coatings also causes difficulties. Most shipyard components are coated and dried in the open-air to the detriment of waterborne coatings, which are highly moisture and temperature sensitive for drying.158 This issue is compounded by the fact that shipyards are by nature generally located in areas of high atmospheric moisture, leading to slow and inconsistent drying.158 Marine coatings are generally applied via spray, rollers, or brushes.159
2.3. Packaging
Rather than just protecting the substrate, packaging coatings must additionally protect the package contents.165,166 For food packaging, barrier property performance is critical, protecting contents from moisture and oxygen to preserve freshness.167 Other products, such as disposable drinking cups, must add a coating to overcome the weak wet strength of paper, which would otherwise tear and fall apart.168 Packages are frequently comprised of multiple distinct layers and/or use petrochemical-based polymers, making them destined for the landfill, even despite the otherwise biodegradable substrate in the case of paper.3,167 While extrusion coating and lamination are most common, waterborne dispersion coatings allow for other methods, such as curtain, dip, bar, and roll coatings which have lower film thickness and thus lower dry material usage.3,169 Packaging comprises a very high percentage of our overall plastic usage, as well as our solid waste.3,170 As a result, biobased and biodegradable packaging options are heavily researched and factor into consumer decisions and sustainability initiatives.70,171–173
Unfortunately, existing commercial paper packaging coatings do not extensively employ waterborne technology.169 There are however a few in limited use, such as acrylic dispersions from BASF (e.g. Joncryl®) and Aquaspersions.174,175 The implementation of waterborne dispersion coatings for paper packaging is a very promising area of research and is discussed in Section 3.3. For now, commercial waterborne packaging coatings are largely confined to the areas of aluminum coatings.
Metal drink can coatings must also protect the drink from obtaining a metallic flavour or losing its carbonation (if applicable), while also protecting the can from corroding due to the drink acidity.69 These coatings have been predominantly waterborne now for decades, with epoxy–acrylic copolymers with phenolic or amino crosslinkers being the common basis.69,176 Originally, toxic bisphenol A (BPA) was used, but is now largely replaced by other bisphenols with lower or unproven toxicity.69,177 Polyester-based, as well as a bio-based phenol coating derived from cashew shell waste have also been investigated, although the cashew option is not currently waterborne.177,178 Waterborne varnishes for exterior coating of the metal drink cans has a much lower rate of adoption, but has grown substantially in recent years.179
2.4. Other commercialized coating systems
There remain numerous other commercialized waterborne coatings, which represent smaller markets and may often be considered subsets of the discussed systems due to similarity of the technology.70 For example, other transportation coatings such as for buses and trains have similar substrate protection and environmental exposure resistance requirements, but with differing cosmetic requirements.180 As a result, the overall coating system is quite similar, but simplified in terms of layers and additives.180 Aircraft and automotive refinish paints are also similar to the automotive paints discussed, with different environmental exposure requirements for aircraft and economic considerations for refinish paints.181–183
Similarly, as touched on earlier there are countless applications for waterborne paints. Toys, agricultural equipment, appliances, helmets, cookware, gym equipment, and road markings are a few examples which employ waterborne paints in some capacity.23,67,184,185 Waterborne printing ink has also begun to see market uptake, mainly with waterborne polyurethanes for currently commercialized systems but with some interest in acrylic systems.55,186–189 Waterborne polyurethanes are also used in adhesives,50,170 soft-touch materials such as synthetic leather,5 nail enamel,190 textile coatings,191 and more.192 Waterborne polyurethane/acrylic hybrid systems are often used in these and similar applications where the less expensive acrylic cannot meet performance requirements on its own.55,193
Other commercialized waterborne coating systems using a variety of polymeric systems include seed coatings,194 drug pellet coatings,195 and anti-smudge coatings.196 Paper coatings for non-packaging purposes comprises applications, such as paperback books,67 playing cards,197 and thermal paper.198 Emulsified asphalt, especially for the waterproofing layer of pavement structure, commonly employs styrene–butadiene latex but has also been shown to perform well using polyvinyl acetate and waterborne epoxy resin.199,200 Lastly, polytetrafluoroethylene (PTFE) is used for a myriad of non-stick and non-reactive surfaces and is commonly coated as a waterborne dispersion.201–203 As stated, this section is not meant to comprise an exhaustive list. Other commercial waterborne coatings exist, and as time passes and new systems are developed or become economically viable this list will continue to grow. The shift to waterborne coatings is already in full swing as solventborne coatings are continually phased out for their more environmentally friendly counterparts.43,70,204
2.5. Overview of commercialized systems
A summary of currently commercialized waterborne polymers is given in Table 1, below. Note that this table is not exhaustive, and only considers the main polymer resins rather than polymeric additives such as bactericides and associative thickeners.205
Table 1 Commercialized waterborne polymer resins for dispersion coatings
Waterborne polymer |
General unit structure |
Commercialized applications |
References |
Acrylic |
Polyacrylate |
|
Wood coating, paint, adhesive, marine |
31, 38, 54, 60, 84, 163 and 206 |
Alkyd |
|
|
Wood coating, paint |
38, 152 and 207 |
Epoxy |
Polyepoxide |
|
Anticorrosion (automotive, marine, aluminum can) |
83, 89, 163 and 176 |
Polyester |
|
|
Paint |
84 and 208 |
PTFE |
Polytetrafluoroethylene |
|
Non-stick |
201 and 206 |
PU |
Polyurethane |
|
Wood coating, paint, synthetic leather, adhesives, marine, ink, nail enamel, textile |
5, 38, 42, 50, 60, 84, 129, 151, 189–191 and 209 |
While waterborne polymer coatings overall are on the rise,43,70 they are not without drawbacks hindering their full adoption. Suitable waterborne systems are not currently commercially available for all coating applications, such as paper packaging169 and some wood products.30,210 Also, their performance, high drying temperatures, and pot stability makes them inadequate for some applications in their current technological state.26,32 Lastly, most of the systems do not fully address sustainability concerns. High drying temperatures means high energy usage, there is often still a small amount of organic solvent, and the polymers are often not biobased nor biodegradable.6,23,26,72 Despite all of this, waterborne systems have demonstrated success for many applications, while improving safety and environmental characteristics.23,24,192 As the shortcomings continue to be addressed through advancing research (as discussed in Section 3), waterborne polymeric coatings will continue to see increased commercial adoption and success in the foreseeable future.
3. The future for waterborne polymer systems
In this section, new developments and trends in waterborne systems are highlighted. A focus is given on progress towards new commercialized systems and improvements to existing systems. New methods of waterborne system formation, materials and additives, and applications are discussed.
3.1. New methods of formation and stabilization
As a precursor to new materials being made into stable waterborne dispersions, new methods of formation are necessary to overcome innate hydrophobicity and instability.31,32 For existing waterborne systems the pot life remains a challenge to overcome, often retaining some level of VOC presence to provide stability and expected functionality.32,42,211
Perhaps the most exciting trend for formation and stabilization is Pickering emulsions. Aqueous Pickering emulsions use small solid amphiphilic particles bound irreversibly to the interface between the water and immiscible phases in order to provide stability.212 Compared to systems stabilized using conventional surfactants, Pickering emulsions can boast reduced toxicity and cost, while greatly increasing stability.212 Pickering emulsions have seen an immense increase in research interest over the past 20 years. In 2000, less than 10 papers on the topic were published, in 2010 more than 100, to now over 800 papers published in 2021.213,214 Some successful oil-in-water Pickering systems researched for coatings include beeswax stabilized using cellulose nanoparticles for fruit coating,41,215 paraffin stabilized using cellulose nanoparticles for textile thermal regulation,216 and glycidyl methacrylate stabilized with graphene oxide for a self-healing coating.217 Kalashnikova et al. have produced excellent images showing the Pickering particle coverage of cellulosic nanorods stabilizing the oil/water interface, as shown in Fig. 6 below.218
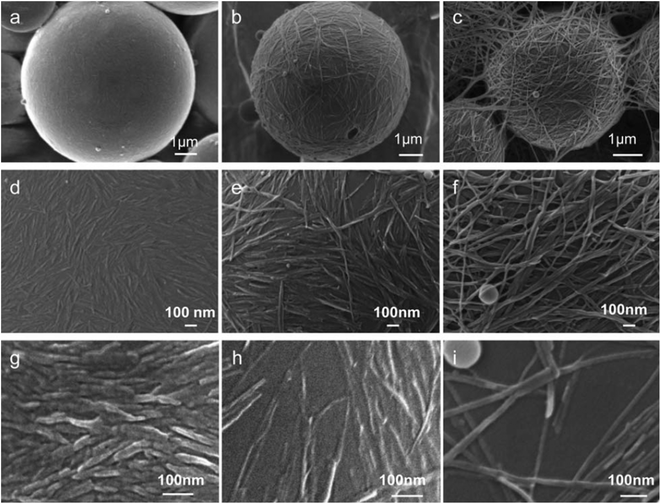 |
| Fig. 6 Scanning electron microscopy (SEM) images of polymerised styrene–water Pickering emulsions stabilized by cotton cellulose nanorods (a, d and g), bacterial cellulose nanorods (b, e and h), and Cladophora cellulose nanorods (c, f and i) at two different nanocrystal concentrations: 5 g L−1 (d–f), and 1 g L−1 (g and h) – revealing the coverage variation as a function of nanocrystal concentration and length. Reproduced from ref. 218 with permission of The Royal Society of Chemistry © 2013. | |
New methods of formation are continually investigated for reasons. Aims of this research include reduced energy requirements, improved product, allowing new materials, and solvent quantity reduction.31,50,219–221 For waterborne polyurethanes, hot-melt processing and solvent-free condensation polymerization are promising methods of formation, which emit no organic solvent.50,219 Other methods, such as radical ring-opening polymerization methods are expanding the ability to synthesize degradable polymers.222 Emulsion polymerization-induced self-assembly mediated by reversible addition–fragmentation chain transfer was recently performed using dibenzo[c,e]oxepane-5-thione to obtain block copolymer nanoparticles directly in water.222 Lastly, other stabilization methods seeing interest are thickeners65,223 and the use of copolymers.224
3.2. New trends in waterborne materials and additives
Of particular interest for improving current systems are the utilization of hybrid dispersions and the addition of nanoparticles to bring waterborne dispersion performance closer to that of solventborne.46,50,153 As well, for new systems, development of waterborne dispersions of biobased and biodegradable polymers is greatly appealing to further reduce the environmental impact of polymer coatings.21
Hybrid dispersions combine two or more polymers chemically bound together to form an improved product.152,153 This synergy can lead to superior performance compared to individual polymers alone,56,153,225,226 or it can maintain performance levels while decreasing the quantity needed of the costlier polymer.55 Many hybrid systems already see commercial use, such as the alkyd–acrylic architectural paint and acrylic–polyurethane wood coatings discussed earlier.60,152,153 New hybridized systems include many new acrylic–polyurethane hybrids due to the flexibility of the underlying polymer formulation.55,193 Current research on hybrid coatings includes the development of a novel one-package (1 K) waterborne non-isocyanate polyurethane–epoxy hybrid,227 improvements to the performance of polyacrylate–polyurethane hybrids,228 and numerous other projects.229–233
Nanoparticles and other additives are of great interest to improve existing capabilities and introduce new possibilities.46,50,149,160,234–236 Nanoparticles offer advantages, such as greater effective surface area, high stability in dispersions, and can impart unique properties not possible with conventional particles.46,237 The possibilities are immense as both organic and inorganic nanomaterials with varying compositions, different morphologies, and more, lead to inexhaustible combinations.4,148,237 Recently, Vijayan et al. embedded ceria–zirconia nanoparticles in waterborne epoxy for marine anti-biofouling, with the antibacterial success shown in Fig. 7f.160 Another interesting finding is by Koyuncu et al., incorporating bismuth oxide nanoparticles into waterborne polyurethane textile coatings to provide protection against ionizing radiation, for example as a lightweight X-ray shielding apron.238 Incorporation of nanoparticles in waterborne epoxy for a bonded solid lubricating coating239 and in waterborne polyurethane to improve textile puncture resistance240 are two additional projects within this immense research space. Novel additives to enhance existing waterborne systems are similarly rife, for example adding engineered polysaccharides to natural rubber latex241,242 and kaolin to styrene–butadiene latex,243 both to improve barrier property performance. Other additives can be critical to incorporate, such as those discussed earlier including thickeners, pigments, plasticizers, and more.39,45,65 Of particular interest to the topics discussed in this publication are additives to reduce the drying energy requirements (directly or indirectly, such as initiators to allow photopolymerization) in order to mitigate that key drawback to waterborne systems.244–250
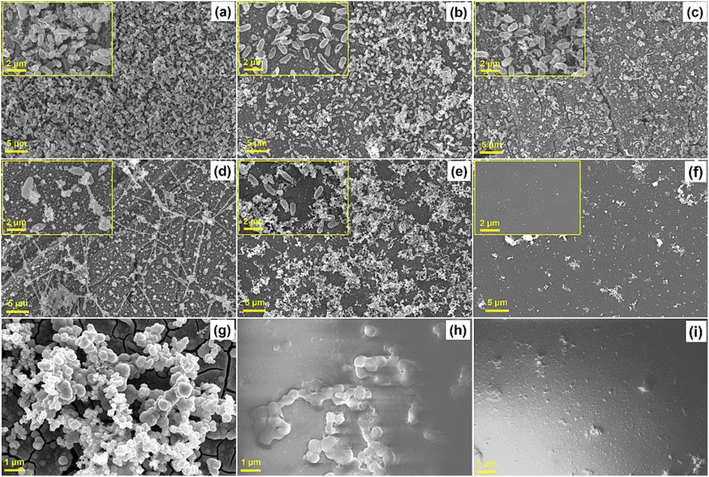 |
| Fig. 7 (a–f) SEM images of uncoated control, epoxy coated, and composites coated mild steel surface after treating with bacteria ((a) control, (b) epoxy, (c) epoxy and ceria, (d) epoxy with 80 : 20 polydopamine (PDA) : ceria, (e) epoxy with 60 : 40 ceria : zirconium and (f) epoxy with 48 : 32 : 20 ceria : zirconium : PDA (EPCZ)). (g–i) SEM images of uncoated control, epoxy coated and EPCZ coated mild steel surface after treating with sea water consortium ((g) control, (h) pure epoxy and (i) EPCZ). Reproduced from ref. 160 with permission of Elsevier © 2024. | |
Regarding development of waterborne dispersions using new polymer resins, there is particular focus on biobased and biodegradable materials to further improve the environmental benefits.6 Pieters and Mekonnen6 successfully dispersed the biobased and biodegradable polymer poly(3-hydroxybutyrate-co-3-hydroxyvalerate) (PHBV) in water. Likewise, Bramhall35 has dispersed polyhydroxyalkanoates (PHA) in water using a similar approach. Waterborne dispersions of both poly(lactic acid) (PLA)21 and poly(butylene succinate) (PBS)251 have also been reported in the literature. The waterborne PLA development may be of particular interest for practical applicability, as PLA is a mature biopolymer, and the extrusion-coated commercial paperboard products are already widely available.252,253 Each of these works demonstrated the applicability of waterborne polymer systems on paper substrates for barrier coating purposes, a highly desirable application for waterborne biodegradable coatings as discussed further in Section 3.3. Additional newly developed waterborne dispersions include biodegradable polybutylene succinate251 and biobased carnauba wax.254 The latter, by Lozhechnikova et al.,254 demonstrated applicability as a wood coating for UV exposure as shown in Fig. 8, as well as other protective properties. Lastly, there has also been substantial work involved in bringing the performance standard of bio-based versions of the existing coatings, for example bio-based waterborne polyurethanes, up to the level of their conventional counterparts.139,192,255,256
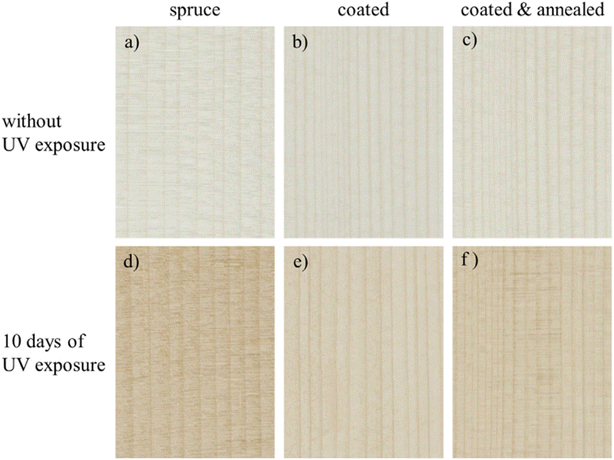 |
| Fig. 8 Photographs of original spruce (a), spruce coated with 8 bilayers ZnO/carnauba wax at 10 g L−1 without (b) and with annealing at 110 °C (c). Spruce (d), spruce coated (e) as well as spruce coated and annealed (f) after UV exposure for 10 days. All photographs were taken with identical camera settings and illumination. Reproduced from ref. 254 with permission of Elsevier © 2017. | |
3.3. New applications for waterborne coatings
Research into new applications for waterborne coatings can be categorized into either replacing an existing coating with more environmentally friendly alternatives or formulating new coating products. For existing applications, packaging is a key target due to the astronomical amount of waste currently produced.3 For new applications there is a push towards smart and active materials (including within packaging) which can adapt to and alter the surrounding environment, respectively.12,13 Also, novel waterborne products such as chip-board coatings and hairspray are undergoing significant developments.
Paper is a very common packaging material due to being printable, biodegradable, biobased, recyclable, low cost, light weight, versatility, and more.3,251,257 In fact, 30% of global packaging material is paper, behind only plastics (40%), and ahead of aluminum (20%).3 Paper's market share for packaging applications is expected to further grow as bans on single-use plastic are implemented.251 Unfortunately, paper is porous and hydrophilic, resulting in poor barrier properties (gases, water, grease) and inferior wet strength.3,251 Surface coatings are used to overcome these challenges.3,251 Current barrier paper coatings use petrochemical derived coatings, which severely limits recycling and inhibits biodegradation167 Cost reductions play an essential role for packaging, as they are largely single-use and secondary to the main product contained within.167,258,259 Dispersion coatings can allow for reduced material usage, reducing cost.169 Lastly, consumer decisions and government regulations have also promoted shifts to more sustainable packaging options.70,171–173 As mentioned earlier, there has been experimental success in creating paper packaging with biobased and/or biodegradable waterborne coatings of PLA, PHBV, other PHA's, and PBS, making the introduction of commercialized systems in this area very likely to occur in the near-future.6,21,35,251
Other packaging products being developed include direct food coatings, smart packaging, and active packaging. Direct food coatings such as waxes can be biobased and edible, while reducing food spoilage through limiting water and gas transfer.41 The remarkable effectiveness of these systems can be seen in Fig. 9, in which Trinh et al. used an edible Pickering emulsion of beeswax to limit spoilage of strawberries and sliced apples (as shown), as well as bananas.41 Active packaging employs a multicomponent system, such as encapsulation and embedment in the coating matrix.260 As an example, Ma et al. embedded anti-corrosive agents within a smart pH-responsive capsule in waterborne epoxy for metal coating, with the success shown in Fig. 10.261 Importantly, smart packaging improves quality through the incorporation of sensors and indicators.12 Smart packaging coatings will be similar to active packaging from the perspective of the coating, with the functionality imparted as an addition to or separate component from the primary waterborne coating itself.12,262 Similarly, functional paints possess additional properties alongside providing protection and improved appearance to the substrate.263 Self-cleaning, self-healing, antigraffiti, antifouling, and more are possible property additions,263 as is a specific focus on biocidal behavior.264–268 Some of these are already commercialized for some applications, such as antifouling marine coatings as discussed earlier in this work. However, as these systems are more complex than simple barrier coatings they are currently not in widespread use and will likely see a longer timeframe for market adoption.167
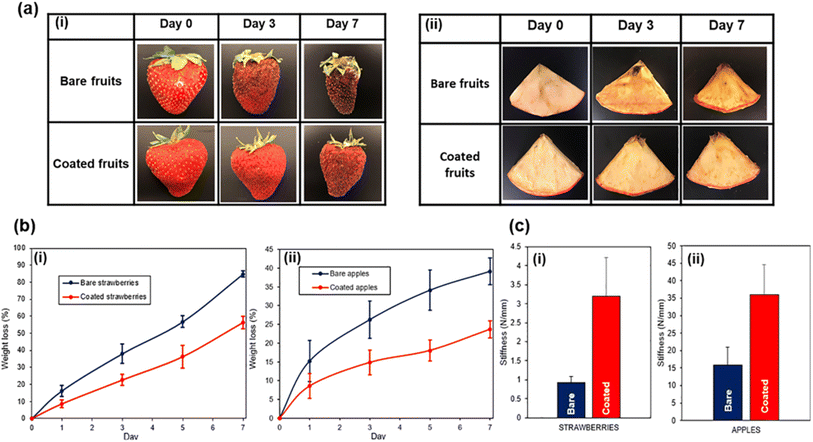 |
| Fig. 9 Effect of edible emulsion coatings on strawberries and apples. (a) Time-lapse photographs of bare and coated (i) strawberries and (ii) flesh-cut apples over 7 days. (b) Water weight loss of (i) strawberries and (ii) flesh-cut apples over 7 days, and (c) comparison between stiffness of bare and coated (i) strawberries and (ii) flesh-cut apples. Reproduced from ref. 41 with permission of Elsevier © 2022. | |
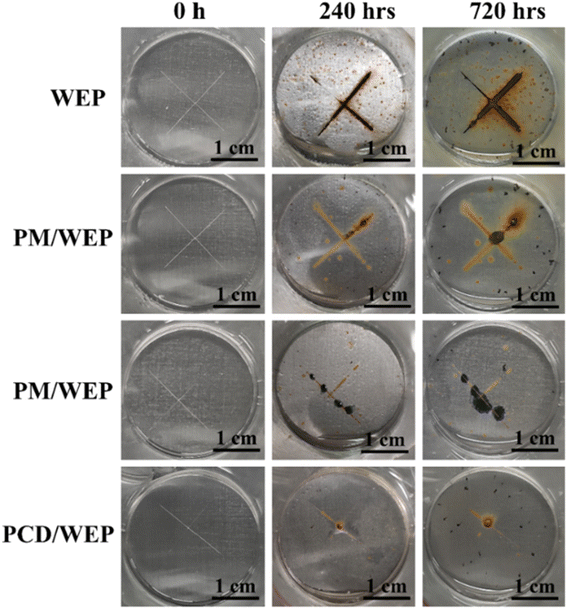 |
| Fig. 10 Visual images of blank waterborne epoxy (WEP), melamine phytate/WEP, melamine phytate with Ce(III)/WEP, and melamine phytate with Ce(III) and polydopamine/WEP of the scratch zone at 0, 240 h, and 720 h immersion stage. The area of the coating exposed to the 3.5 wt% NaCl solution is 7.07 cm2. Reproduced from ref. 261 with permission of Elsevier © 2022. | |
Many innovative waterborne applications are under ongoing investigation across dissimilar industries. For example, a waterborne acrylic photoresist layer for printed circuit boards has recently been produced.269 With the rapidly rising rate of manufacturing printed circuit boards, waterborne coatings to replace the VOC-intensive processes will be an important step to reducing the environmental and safety impacts.269 Antistatic textile coatings,270 hair-styling products using bio-based waterborne polyurethanes prepared from castor oil,271 and slow release fertilizer coatings272 are just a few more of the various products currently in development.
4. Conclusions
The recent adoption of waterborne systems for commercial coatings marks a promising start to the future of sustainable coatings. These systems have demonstrated broad applicability while enhancing environmental and safety characteristics through a reduction in organic solvent emissions. While hybrid systems employing multiple polymers have been used for years, their recent expanded use presents a promising avenue for potential cost-savings and addressing remaining performance issues. Furthermore, the incorporation of nanoparticles and the use of other novel additives are broadening the scope of possibilities regarding the capability and applicability of waterborne coatings.
Despite the various progresses, challenges persist. Certain systems still lack waterborne counterparts that meet acceptable standards for commercialization, notably clearcoats for outdoor applications. Additionally, issues such as pot-life, energy requirements, and the available range of systems still lags behind solventborne alternatives for many applications. Research endeavors aimed at addressing these challenges are ongoing, with emerging stabilization techniques like Pickering emulsions seeing widespread interest. Furthermore, continuous investigation and incorporation of other additives are underway to further enhance waterborne coating performance and applicability.
Lastly, the predominant resins in use are still primarily derived from petrochemical sources. Consequently, the coatings are largely non-biobased and non-biodegradable. Moving beyond the environmental improvements achieved with waterborne systems to achieve fully sustainable coatings will be the next step, and a key challenge in the coming decades. Progress toward this transition is already underway, with the widespread adoption of bio-based waterborne polyurethanes and successful experimental applications of fully biobased and biodegradable polymers in water-dispersive formulations.
Nevertheless, these upcoming endeavors should not overshadow the significant strides made by the coatings industry toward environmental sustainability. Commercialized products must adhere to performance standards, and achieving full sustainability requires considerable time and collective effort. Waterborne systems have emerged as the standard for architectural coatings, the largest commercial coatings sector, as well as automotives, one of the sectors with the highest visibility for coatings innovation. Waterborne coatings will persist in leading environmentally conscious coating options and pioneering new coatings applications.
Data availability
No raw data was used to prepare this review manuscript.
Author contributions
Kyle Pieters: conceptualization (equal), methodology (equal), validation, formal analysis, investigation, resources (equal), data curation, writing (lead), visualization, funding acquisition (supporting). Tizazu H. Mekonnen: conceptualization (equal), methodology (equal), resources (equal), writing (supporting), supervision, project administration, funding acquisition (lead).
Conflicts of interest
The authors declare no competing financial interest.
Acknowledgements
The financial support of Agriculture and Agri Food Canada (AAFC) through the Bioindustrial Innovation Canada (BIC) to carry out the research is greatly appreciated. Kyle Pieters appreciates the financial support of the Faculty of Engineering of the University of Waterloo through the Engineering Excellence Master's Fellowship and Deans Entrance Scholarship.
References
-
Polymer-based Nanoscale Materials for Surface Coatings, ed. S. Thomas and J. S. George, Elsevier, Amsterdam, Kidlington, Oxford, Cambridge, MA, 2023 Search PubMed.
- A. Kausar, Polymer coating technology for high performance applications: Fundamentals and advances, J. Macromol. Sci., Part A: Pure Appl.Chem., 2018, 55, 440–448 CrossRef CAS.
- A. Adibi, B. M. Trinh and T. H. Mekonnen, Recent progress in sustainable barrier paper coating for food packaging applications, Prog. Org. Coat., 2023, 181, 107566 CrossRef CAS.
- V. Rastogi and P. Samyn, Bio-Based Coatings for Paper Applications, Coatings, 2015, 5, 887–930 CrossRef CAS.
- Z. Sun, S. Ren, T. Wu, J. Wen, J. Fang and H. Fan, A Self-Matting Waterborne Polyurethane Coating for PVC Artificial Leather, Polymers, 2022, 15, 127 CrossRef PubMed.
- K. Pieters and T. H. Mekonnen, Stable aqueous dispersions of poly(3-hydroxybutyrate-co-3-hydroxyvalerate) (PHBV) polymer for barrier paper coating, Prog. Org. Coat., 2024, 187, 108101 CrossRef CAS.
- M. Barletta, G. Rubino, L. Lusvarghi and F. Pighetti Mantini, Surface appearance and mechanical strength of multi-layer polymeric films, Prog. Org. Coat., 2008, 61, 249–261 CrossRef CAS.
- X. Zhu, Q. Li, L. Wang, W. Wang, S. Liu, C. Wang, Z. Xu, L. Liu and X. Qian, Current advances of Polyurethane/Graphene composites and its prospects in synthetic leather: A review, Eur. Polym. J., 2021, 161, 110837 CrossRef CAS.
- Q. Yong, D. Xu, Q. Liu, Y. Xiao and D. Wei, Advances in polymer-based matte coatings: A review, Polym. Adv. Technol., 2022, 33, 5–19 CrossRef CAS.
- U. Mahanta, M. Khandelwal and A. S. Deshpande, Antimicrobial surfaces: a review of synthetic approaches, applicability and outlook, J. Mater. Sci., 2021, 56, 17915–17941 CrossRef CAS PubMed.
-
K. Umar, A. A. Yaqoob, M. N. M. Ibrahim, T. Parveen and M. T. Safian, in Smart Polymer Nanocomposites, Elsevier, 2021, pp. 295–312 Search PubMed.
- M. Soltani Firouz, K. Mohi-Alden and M. Omid, A critical review on intelligent and active packaging in the food industry: Research and development, Food Res. Int., 2021, 141, 110113 CrossRef CAS PubMed.
- K. Wieszczycka, K. Staszak, M. J. Woźniak-Budych, J. Litowczenko, B. M. Maciejewska and S. Jurga, Surface functionalization – The way for advanced applications of smart materials, Coord. Chem. Rev., 2021, 436, 213846 CrossRef CAS.
- A. S. Achanta, P. S. Adusumilli, K. W. James and C. T. Rhodes, Development of Hot Melt Coating Methods, Drug Dev. Ind. Pharm., 1997, 23, 441–449 CrossRef CAS.
- K.-S. Seo, R. Bajracharya, S. H. Lee and H.-K. Han, Pharmaceutical Application of Tablet Film Coating, Pharmaceutics, 2020, 12, 853 CrossRef CAS PubMed.
- V. Jost and H.-C. Langowski, Effect of different plasticisers on the mechanical and barrier properties of extruded cast PHBV films, Eur. Polym. J., 2015, 68, 302–312 CrossRef CAS.
- C. Zengwen, H. Pan, Y. Chen, J. Bian, L. Han, H. Zhang, L. Dong and Y. Yang, Transform poly(lactic acid) packaging film from brittleness to toughness using traditional industrial equipments, Polymer, 2019, 180, 121728 CrossRef CAS.
- R. Sharma and G. Setia, Mechanical dry particle coating on cohesive pharmaceutical powders for improving flowability – A review, Powder Technol., 2019, 356, 458–479 CrossRef CAS.
- S. Bose and R. H. Bogner, Solventless Pharmaceutical Coating Processes: A Review, Pharm. Dev. Technol., 2007, 12, 115–131 CrossRef CAS PubMed.
- B. Fotovvati, N. Namdari and A. Dehghanghadikolaei, On Coating Techniques for Surface Protection: A Review, J. Manuf. Mater. Process., 2019, 3, 28 CAS.
- G. Belletti, S. Buoso, L. Ricci, A. Guillem-Ortiz, A. Aragón-Gutiérrez, O. Bortolini and M. Bertoldo, Preparations of Poly(lactic acid) Dispersions in Water for Coating Applications, Polymers, 2021, 13, 2767 CrossRef CAS PubMed.
- P. K. Singh, M. L. Pacholski, J. Gu, Y. K. Go, G. Singhal, C. Leal, P. V. Braun, K. A. Patankar, R. Drumright, S. A. Rogers and C. M. Schroeder, Designing Multicomponent Polymer Colloids for Self-Stratifying Films, Langmuir, 2022, 38, 11160–11170 CrossRef CAS PubMed.
- K. D. Weiss, Paint and coatings: A mature industry in transition, Prog. Polym. Sci., 1997, 22, 203–245 CrossRef CAS.
- V. Duecoffre, W. Diener, C. Flosbach and W. Schubert, Emulsifiers with high chemical resistance: a key to high performance waterborne coatings, Prog. Org. Coat., 1998, 34, 200–205 CrossRef CAS.
- Z. Aguirreurreta, J. C. De La Cal and J. R. Leiza, Preparation of high solids content waterborne acrylic coatings using polymerizable surfactants to improve water sensitivity, Prog. Org. Coat., 2017, 112, 200–209 CrossRef CAS.
- L. A. Felton, Mechanisms of polymeric film formation, Int. J. Pharm., 2013, 457, 423–427 CrossRef CAS PubMed.
- D. Lee, M. Shayan, J. Gwon, D. H. Picha and Q. Wu, Effectiveness of cellulose and chitosan nanomaterial coatings with essential oil on postharvest strawberry quality, Carbohydr. Polym., 2022, 298, 120101 CrossRef CAS PubMed.
- R. Pal, Effect of droplet size on the rheology of emulsions, AIChE J., 1996, 42, 3181–3190 CrossRef CAS.
- S. Kinra and R. Pal, Rheology of Pickering Emulsions Stabilized and Thickened by Cellulose Nanocrystals over Broad Ranges of Oil and Nanocrystal Concentrations, Colloids Interfaces, 2023, 7, 36 CrossRef CAS.
- Z. Zhao, Y. Niu and F. Chen, Development and finishing technology of waterborne UV lacquer-coated wooden flooring, BioResources, 2020, 16, 1101–1114 Search PubMed.
- O. Llorente, A. Barquero, M. Paulis and J. R. Leiza, Challenges to incorporate high contents of bio-based isobornyl methacrylate (IBOMA) into waterborne coatings, Prog. Org. Coat., 2022, 172, 107137 CrossRef CAS.
- A. Wegmann, Chemical resistance of waterborne epoxy/amine coatings, Prog. Org. Coat., 1997, 32, 231–239 CrossRef CAS.
- M. J. Gonzalez-Alvarez, J. Paternoga, K. Breul, H. Cho, M. Z. Roshandel, M. Soleimani and M. A. Winnik, Understanding particle formation in surfactant-free waterborne coatings prepared by emulsification of pre-formed polymers, Polym. Chem., 2017, 8, 2931–2941 RSC.
- S. Jiang, A. Van Dyk, A. Maurice, J. Bohling, D. Fasano and S. Brownell, Design colloidal particle morphology and self-assembly for coating applications, Chem. Soc. Rev., 2017, 46, 3792–3807 RSC.
-
J. A. Bramhall, Ph.D. thesis, University of Georgia, 2020.
- A. Overbeek, Polymer heterogeneity in waterborne coatings, J. Coat. Technol. Res., 2010, 7, 1–21 CrossRef CAS.
-
MarketLine, MarketLine Industry Profile: Global Paints & Coatings, 2020 Search PubMed.
- A. Cogulet, P. Blanchet and V. Landry, The Multifactorial Aspect of Wood Weathering: A Review Based on a Holistic Approach of wood Degradation Protected by Clear Coating, BioResources, 2017, 13, 2116–2138 CrossRef.
-
H.-J. Streitberger and K.-F. Dössel, Automotive Paints and Coatings, Wiley-VCH, Weinheim, 2nd, completely revised and extended edn, 2008 Search PubMed.
- J. Guo, H. Zhang, L. Chen, L. Ding, F. Hu, L. Pei, S. Liang, Q. Yang and J. Wang, A visual detection films based on waterborne polyurethane for real-time monitoring of yogurt freshness, Dyes Pigm., 2023, 210, 110995 CrossRef CAS.
- B. M. Trinh, M. Smith and T. H. Mekonnen, A nanomaterial-stabilized starch-beeswax Pickering emulsion coating to extend produce shelf-life, Chem. Eng. J., 2022, 431, 133905 CrossRef CAS.
-
A. Javadi, A. Cobaj and M. D. Soucek, in Handbook of Waterborne Coatings, Elsevier, 2020, pp. 303–344 Search PubMed.
- V. L. Mucci, M. E. V. Hormaiztegui, J. I. Amalvy and M. I. Aranguren, Formulation, structure and properties of waterborne polyurethane coatings: a brief review, J. Adhes. Sci. Technol., 2024, 38, 489–516 CrossRef CAS.
- M. De Meijer, Review on the durability of exterior wood coatings with reduced VOC-content, Prog. Org. Coat., 2001, 43, 217–225 CrossRef CAS.
- C.-A. Teacă, D. Roşu, F. Mustaţă, T. Rusu, L. Roşu, I. Roşca and C.-D. Varganici, Natural bio-based products for wood coating and protection against degradation: A Review, BioResources, 2019, 14, 4873–4901 Search PubMed.
- T.-J. Teng, M. N. Mat Arip, K. Sudesh, A. Nemoikina, Z. Jalaludin, E.-P. Ng and H.-L. Lee, Conventional Technology and Nanotechnology in Wood Preservation: A Review, BioResources, 2018, 13, 9220–9252 CrossRef.
- M. Nikolic, J. M. Lawther and A. R. Sanadi, Use of nanofillers in wood coatings: a scientific review, J. Coat. Technol. Res., 2015, 12, 445–461 CrossRef CAS.
- A. N. Papadopoulos, D. N. Bikiaris, A. C. Mitropoulos and G. Z. Kyzas, Nanomaterials and Chemical Modifications for Enhanced Key Wood Properties: A Review, Nanomaterials, 2019, 9, 607 CrossRef CAS PubMed.
- P. Evans, J. Haase, A. Seman and M. Kiguchi, The Search for Durable Exterior Clear Coatings for Wood, Coatings, 2015, 5, 830–864 CrossRef CAS.
- H. Honarkar, Waterborne polyurethanes: A review, J. Dispersion Sci. Technol., 2018, 39, 507–516 CrossRef CAS.
- A. Noomen, The chemistry and physics of low-emission coatings: Part 2. Waterborne two-pack coatings, Prog. Org. Coat., 1989, 17, 27–39 CrossRef CAS.
- X. Zhou, Y. Li, C. Fang, S. Li, Y. Cheng, W. Lei and X. Meng, Recent Advances in Synthesis of Waterborne Polyurethane and Their Application in Water-based Ink: A Review, J. Mater. Sci. Technol., 2015, 31, 708–722 CrossRef.
- S. Tamantini, S. Bergamasco, F. Zikeli, M. Humar, M. Cavalera and M. Romagnoli, Cellulose Nano Crystals (CNC) as Additive for a Bio-Based Waterborne Acrylic Wood Coating: Decay, Artificial Weathering, Physical and Chemical Tests, Nanomaterials, 2023, 13, 442 CrossRef CAS PubMed.
- C. Jiao, L. Sun, Q. Shao, J. Song, Q. Hu, N. Naik and Z. Guo, Advances in Waterborne Acrylic Resins: Synthesis Principle, Modification Strategies, and Their Applications, ACS Omega, 2021, 6, 2443–2449 CrossRef CAS PubMed.
- S. Mehravar, N. Ballard, R. Tomovska and J. M. Asua, Polyurethane/Acrylic Hybrid Waterborne Dispersions: Synthesis, Properties and Applications, Ind. Eng. Chem. Res., 2019, 58, 20902–20922 CrossRef CAS.
- M. Elrebii, A. Ben Mabrouk and S. Boufi, Synthesis and properties of hybrid alkyd–acrylic dispersions and their use in VOC-free waterborne coatings, Prog. Org. Coat., 2014, 77, 757–764 CrossRef CAS.
- D. J. Watson and M. R. Mackley, The rheology of aqueous emulsions prepared by direct emulsification and phase inversion from a high viscosity alkyd resin, Colloids Surf., A, 2002, 196, 121–134 CrossRef CAS.
- M. Pánek, O. Dvořák, E. Oberhofnerová, K. Šimůnková and A. Zeidler, Effectiveness of Two Different Hydrophobic Topcoats for Increasing of Durability of Exterior Coating Systems on Oak Wood, Coatings, 2019, 9, 280 CrossRef.
-
M. Nejad and P. Cooper, in Wood in Civil Engineering, ed. G. Concu, InTech, 2017 Search PubMed.
- M. Pavlič, M. Petrič and J. Žigon, Interactions of Coating and Wood Flooring Surface System Properties, Coatings, 2021, 11, 91 CrossRef.
- P. Hochmańska-Kaniewska, D. Janiszewska and T. Oleszek, Enhancement of the properties of acrylic wood coatings with the use of biopolymers, Prog. Org. Coat., 2022, 162, 106522 CrossRef.
- E. Scrinzi, S. Rossi, F. Deflorian and C. Zanella, Evaluation of aesthetic durability of waterborne polyurethane coatings applied on wood for interior applications, Prog. Org. Coat., 2011, 72, 81–87 CrossRef CAS.
- C.-W. Chang and K.-T. Lu, Natural castor oil based 2-package waterborne polyurethane wood coatings, Prog. Org. Coat., 2012, 75, 435–443 CrossRef CAS.
- P. Pandey and U. V. Kiran, Degradation of paints and its microbial effect on health and environment, J. Crit. Rev., 2020, 7, 4879–4884 Search PubMed.
- R. G. Larson, A. K. Van Dyk, T. Chatterjee and V. V. Ginzburg, Associative thickeners for waterborne paints: Structure, characterization, rheology, and modeling, Prog. Polym. Sci., 2022, 129, 101546 CrossRef CAS.
-
K.-F. Dössel, in Automotive Paints and Coatings, Wiley-VCH, Weinheim, 2nd, completely revised and extended edn, 2008 Search PubMed.
-
R. Lambourne and T. A. Strivens, Paint and Surface Coatings, Woodhead Publishing Limited, 1999 Search PubMed.
- G. R. Pilcher, Market analysis preview – Coil and extrusion coatings, CoatingsTech, 2012, 1, 1–8 Search PubMed.
-
G. P. A. Turner, in Paint and Surface Coatings, Woodhead Publishing Limited, 1999 Search PubMed.
- M. F. Cunningham, J. D. Campbell, Z. Fu, J. Bohling, J. G. Leroux, W. Mabee and T. Robert, Future green chemistry and sustainability needs in polymeric coatings, Green Chem., 2019, 21, 4919–4926 RSC.
- N. Akafuah, S. Poozesh, A. Salaimeh, G. Patrick, K. Lawler and K. Saito, Evolution of the Automotive Body Coating Process—A Review, Coatings, 2016, 6, 24 CrossRef.
- A. Giampieri, J. Ling-Chin, Z. Ma, A. Smallbone and A. P. Roskilly, A review of the current automotive manufacturing practice from an energy perspective, Appl. Energy, 2020, 261, 114074 CrossRef.
-
H.-J. Streitberger and K.-F. Dössel, in Automotive Paints and Coatings, Wiley-VCH, Weinheim, 2nd, completely revised and extended edn, 2008 Search PubMed.
-
P. Svejda, in Automotive Paints and Coatings, Wiley-VCH, Weinheim, 2nd, completely revised and extended edn, 2008 Search PubMed.
- M. Groenewolt, Polyurethane coatings: a perfect product class for the design of modern automotive clearcoats, Polym. Int., 2019, 68, 843–847 CrossRef CAS.
- M. Bock and T. H. Engbert, Waterborne Polyurethane Based Paint Materials for the Automotive Industry—Present Situation and Future Possibilities, J. Manuf. Mater. Process., 1995, 707–714 Search PubMed.
- W. Kreis and P. Smith, 10 Years of Waterborne Coatings for OEM, J. Jpn. Soc. Colour Mater., 1998, 71, 777–783 CrossRef CAS.
- L. Prendi, P. Henshaw and E. K. L. Tam, Automotive coatings with improved environmental performance, Int. J. Environ. Stud., 2006, 63, 463–471 CrossRef CAS.
-
G. Wilke, in Automotive Paints and Coatings, Wiley-VCH, Weinheim, 2nd, completely revised and extended edn, 2008 Search PubMed.
- J. Thomas, R. S. Patil, J. John and M. Patil, A Comprehensive Outlook of Scope within Exterior Automotive Plastic Substrates and Its Coatings, Coatings, 2023, 13, 1569 CrossRef CAS.
-
H. Gehmecker, in Automotive Paints and Coatings, Wiley-VCH, Weinheim, 2nd, completely revised and extended edn, 2008 Search PubMed.
- N. C. Debnath, Importance of Surface Preparation for Corrosion Protection of Automobiles, J. Surf. Eng. Mater. Adv. Technol., 2013, 03, 94–105 Search PubMed.
-
H.-J. Streitberger, in Automotive Paints and Coatings, Wiley-VCH, Weinheim, 2nd, completely revised and extended edn, 2008 Search PubMed.
-
M. Nichols and J. Tardiff, in Active Protective Coatings, ed. A. E. Hughes, J. M. C. Mol, M. L. Zheludkevich and R. G. Buchheit, Springer Netherlands, Dordrecht, 2016, vol. 233, pp. 373–384 Search PubMed.
-
R. Kollah, M. Scott, G. Mccollum and J. Bethoski, Electrodepositable coating composition containing bismuth and amino acid materials and electrodeposition method, US Pat., US9920205B2, 2018 Search PubMed.
- M. Liu, Y. Guo, J. Wang and M. Yergin, Corrosion avoidance in lightweight materials for automotive applications, npj Mater. Degrad., 2018, 2, 24 CrossRef.
- H. S. Aljibori, A. Alamiery and A. A. H. Kadhum, Advances in corrosion protection coatings: A comprehensive review, Int. J. Corros. Scale Inhib., 2023, 12, 1476–1520 CAS.
- M. Bakhtiary-Noodeh, S. Moradian and Z. Ranjbar, Improvement of the edge protection of an automotive electrocoating in presence of a prepared epoxy-amine microgel, Prog. Org. Coat., 2017, 103, 111–125 CrossRef CAS.
-
K. Kojima and T. Ogawa, The Development of Primer Process-less Paint System (4WET Paint System by Using Waterborne Chipping Primer), SAE International, 2014 Search PubMed.
- M. Melchiors, M. Sonntag, C. Kobusch and E. Jürgens, Recent developments in aqueous two-component polyurethane (2K-PUR) coatings, Prog. Org. Coat., 2000, 40, 99–109 CrossRef CAS.
- D. Ai, R. Mo, H. Wang, Y. Lai, X. Jiang and X. Zhang, Preparation of waterborne epoxy dispersion and its application in 2K waterborne epoxy coatings, Prog. Org. Coat., 2019, 136, 105258 CrossRef CAS.
- Z. Z. Yang, D. L. Zhao, Y. Z. Xu and M. Xu, Preparation of waterborne dispersions of epoxy resin by the phase-inversion emulsification technique. 1. Experimental study on the phase-inversion process, Colloid Polym. Sci., 2000, 279, 1164–1171 CrossRef.
- M. Yao, E. Tang, C. Guo, S. Liu, H. Tian and H. Gao, Synthesis of waterborne epoxy/polyacrylate composites via miniemulsion polymerization and corrosion resistance of coatings, Prog. Org. Coat., 2017, 113, 143–150 CrossRef CAS.
-
H. Enocson and L. Wretenfeldt, Master Degree Project, University of Gothenburg, 2016 Search PubMed.
-
D. C. Webster and R. A. Ryntz, in Handbook of Industrial Chemistry and Biotechnology, ed. J. A. Kent, T. V. Bommaraju and S. D. Barnicki, Springer International Publishing, Cham, 2017, pp. 805–822 Search PubMed.
-
J. Lerner and A. Leamon, Venture Capital, Private Equity, and the Financing of Entrepreneurship, Wiley, Hoboken, NJ, 2nd edn, 2024 Search PubMed.
-
Axalta, AquaEC Electrocoats, https://www.axalta.com/corporate/en_US/products-and-customers/liquid-coatings/aquaec-electocoats.html, accessed 26 March 2024 Search PubMed.
-
BASF, Corrosion Protection, https://www.basf-coatings.com/global/en/products-and-solutions/automotive_oem_coatings/exterior_solutions/e-coat.html, accessed 26 March 2024 Search PubMed.
-
PPG, Electrocoat, https://www.ppg.com/autocoatings/en-US/products/electrocoat, accessed 26 March 2024 Search PubMed.
-
H. Wonnemann, in Automotive Paints and Coatings, Wiley-VCH, Weinheim, 2nd, completely revised and extended edn, 2008 Search PubMed.
-
M. Howard and A. Graves, Developing a New Approach to Automotive Coatings and Lean Manufacture, SAE Technical Paper, 2001, pp. 1–8 Search PubMed.
- C. K. Schoff and S. Associates, Automotive Coatings Defects Part 1: In-Plant and Field Defects, JCT CoatingsTech, 2004, 34–39 CAS.
-
E. Sigolo, E. Y. Honda, R. Trevisoli, V. A. Pereira and F. Barbosa, Application of Honda 3-Wet Primer-less Technology in Body Painting for Emission Reduction (CO2 and VOC), Brazilian Society of Automotive Engineering–SIMEA 2023, Sao Paulo, Brasil, 2023, pp. 1–6 Search PubMed.
- T. Pennington, Waterborne painting process is a first at South Carolina BMW plant, Plast. Technol., 2013 Search PubMed , (accessed March 12, 2024).
- S. Yomo, K. Tachi and T. Narita, Improving the appearance of 3-coat-1-bake multilayer films on automotive bodies, Prog. Org. Coat., 2018, 123, 299–305 CrossRef CAS.
- C. Wang, X. Lin, C. G. Schäfer, S. Hirsemann and J. Ge, Spray Synthesis of Photonic Crystal Based Automotive Coatings with Bright and Angular-Dependent Structural Colors, Adv. Funct. Mater., 2021, 31, 2008601 CrossRef CAS.
- E. M. Suzuki, Infrared spectra of North American automobile original finishes. XI: In situ identification of perylene pigments—Analysis of Perylene Maroon (C.I. Pigment Red 179) and alumina-based red pearlescent pigments, Forensic Chem., 2021, 25, 100351 CrossRef CAS.
- S. C. Prajapati and P. K. Kamani, Preparation and characterisation of acrylic resin for electro-deposited mono-coat coatings, Indian Chem. Eng., 2021, 63, 349–362 CrossRef CAS.
-
C. Harris and PPG Industries, Inc., Coatings and Process Development for Reduced Energy Automotive OEM Manufacturing Final Technical Report, North Dakota State University (NDSU) DURR Systems USA Inc., 2019 Search PubMed.
- Axalta Coating Systems Germany GmbH & Co. KG, The Most Popular Car Colors in the World, IST Int. Surf. Technol., 2022, 15, 6–7 Search PubMed.
- BASF Coatings GmbH, Chromatic Colors Were in Vogue in 2020, IST Int. Surf. Technol., 2021, 14, 10–11 CrossRef.
- M. J. Gázquez, M. Contreras, S. M. Pérez-Moreno, J. L. Guerrero, M. Casas-Ruiz and J. P. Bolívar, A Review of the Commercial Uses of Sulphate Minerals from the Titanium Dioxide Pigment Industry: The Case of Huelva (Spain), Minerals, 2021, 11, 575 CrossRef.
- M. N. B. Razali, A. A. Alkaf and M. K. N. B. M. Zuhan, Formulation of water-based white colour paint from waste titanium dioxide, Mater. Today: Proc., 2022, 48, 1905–1909 CAS.
- H. A. Kiwaan, T. M. Atwee, E. A. Azab and A. A. El-Bindary, Photocatalytic degradation of organic dyes in the presence of nanostructured titanium dioxide, J. Mol. Struct., 2020, 1200, 127115 CrossRef CAS.
- X. Lin, D. Schmelter and H. Hintze-Bruening, High solid waterborne automotive base coat: Beyond shear thinning, Prog. Org. Coat., 2021, 160, 106530 CrossRef CAS.
- D. Bhattacharya, K. Seo, L. T. Germinario, M. D. Clark, K. W. McCreight and C. Williams, Novel techniques to investigate the impact of cellulose esters on the rheological properties and appearance in automotive basecoat systems, J. Coat. Technol. Res., 2007, 4, 139–150 CrossRef CAS.
-
J. Huetter, PPG: Environmental, Productivity Gains to Spur Greater Waterborne Paint Adoption, https://www.repairerdrivennews.com/2015/10/08/ppg-environmental-productivity-gains-to-spur-greater-waterborne-paint-adoption/ Search PubMed.
-
A. Wang, Waterborne Refinish Coatings Market Shows Quick Growth in China, 2018, https://www.coatingsworld.com/issues/2018-06-01/view_china-reports/waterborne-refinish-coatings-market-shows-quick-growth-in-china/ Search PubMed.
-
J. Woodstock, A Practical Guide to Vehicle Refinishing, Taylor & Francis, Boca Raton, 2020 Search PubMed.
-
S. Whittaker and L. Brown, Waterborne vs. Solventborne Automotive Basecoats: An Alternatives Assessment, 2019, https://kingcountyhazwastewa.gov/-/media/hazwaste/lhwmp-documents/technical-reports/automotive-paint/rsh-waterborne--vs-solvent-borne-automotive-basecoats-alternative-assessment.pdf Search PubMed.
- S. M. Noh, J. W. Lee, J. H. Nam, K. H. Byun, J. M. Park and H. W. Jung, Dual-curing behavior and scratch characteristics of hydroxyl functionalized urethane methacrylate oligomer for automotive clearcoats, Prog. Org. Coat., 2012, 74, 257–269 CrossRef CAS.
- H. Moon, S. M. Noh and H. W. Jung, Thermal crosslinking characteristics of dual-curable isocyanate blocked with methacrylate-functionalized amine derivatives for eco-friendly automotive clearcoats, Appl. Surf. Sci., 2023, 607, 155058 CrossRef CAS.
- H. Petit, N. Henry, A. Krebs, G. Uytterhoeven and F. D. Jong, Ambient cure high solids acrylic resins for automotive refinish clear coat applications, Prog. Org. Coat., 2001, 43, 41–49 CrossRef CAS.
- W. Collong, A. Göbel, B. Kleuser, W. Lenhard and M. Sonntag, 2K waterborne clearcoat—a competition between crosslinking and side reactions, Prog. Org. Coat., 2002, 45, 205–209 CrossRef CAS.
-
M. Clark, Waterborne Paint FAQs, 2011, https://www.bodyshopbusiness.com/waterborne-paint-faqs/, accessed Oct 28, 2024 Search PubMed.
- K. I. Jung, J. U. Hong, S. M. Noh and H. W. Jung, Crosslinking characteristics of dual-curable blocked isocyanate with thermal radical initiator for lowering curing temperature of automotive clearcoats, Prog. Org. Coat., 2022, 163, 106611 CrossRef CAS.
-
PPG Industries, Inc., Envirobase® High Performance, 2024, https://www.ppg.com/refinish/en-US/products/envirobase-high-performance/, accessed Oct 28, 2024 Search PubMed.
- O. Azmami, L. Sajid, A. Boukhriss, S. Majid, Z. El Ahmadi, A. Benayada and S. Gmouh, Mechanical and aging performances of Palm/Wool and Palm/Polyester nonwovens coated by waterborne polyurethane for automotive interiors, Ind. Crops Prod., 2021, 170, 113681 CrossRef CAS.
-
A. Kausar, in Eco-Friendly Waterborne Polyurethanes: Synthesis, Properties, and Applications, CRC Press, Boca Raton, 1st edn, 2021 Search PubMed.
-
L. Mobley, R. Subramanian, K. Skaggs, W. Zhou, D. Bhattacharjee and R. Moore, Process to make synthetic leather and synthetic leather made therefrom, US Pat., US7306825B2, 2007 Search PubMed.
- J. Järnström, P. Ihalainen, K. Backfolk and J. Peltonen, Roughness of pigment coatings and its influence on gloss, Appl. Surf. Sci., 2008, 254, 5741–5749 CrossRef.
- Q. Yong, J. Chang, Q. Liu, F. Jiang, D. Wei and H. Li, Matt Polyurethane Coating: Correlation of Surface Roughness on Measurement Length and Gloss, Polymers, 2020, 12, 326 CrossRef CAS PubMed.
- A. Larena, F. Millan, M. Verdu and G. Pinto, Surface roughness characterisation of multilayer polymer films for graphic arts applications, Appl. Surf. Sci., 2002, 187, 339–346 CrossRef CAS.
- T. A. Trezza and J. M. Krochta, Specular reflection, gloss, roughness and surface heterogeneity of biopolymer coatings, J. Appl. Polym. Sci., 2001, 79, 2221–2229 CrossRef CAS.
-
S. D. Vecchi, J. Christner, A. Rama, S. Summa and D. Rinaldi, Automotive leathers – Evaluating the performance limits (part II), IULTCS Congress, Dresden, 2019 Search PubMed.
- V. V. Gite, P. P. Mahulikar and D. G. Hundiwale, Preparation and properties of polyurethane coatings based on acrylic polyols and trimer of isophorone diisocyanate, Prog. Org. Coat., 2010, 68, 307–312 CrossRef CAS.
-
Y. Li and Z. Wang, in Proceedings of China SAE Congress 2019: Selected Papers, ed. China Society of Automotive Engineers, Springer Singapore, Singapore, 2021, vol. 646, pp. 805–813 Search PubMed.
- W. Li, L. Shi, J. Zhang, J. Cheng and X. Wang, Double-layered surface decoration of flaky aluminum pigments with zinc aluminum phosphate and phytic acid–aluminum complexes for high-performance waterborne coatings, Powder Technol., 2020, 362, 462–473 CrossRef CAS.
-
R. K. Gupta, Eco-Friendly Waterborne Polyurethanes: Synthesis, Properties, and Applications, CRC Press, Boca Raton, 1st edn, 2021 Search PubMed.
- M. L. Nobel, S. J. Picken and E. Mendes, Waterborne nanocomposite resins for automotive coating applications, Prog. Org. Coat., 2007, 58, 96–104 CrossRef CAS.
- A. Zhang, J. Li, H. Fan, J. Xiang, L. Wang and J. Yan, Effect of mechanical properties on the self-healing behavior of waterborne polyurethane coatings, J. Appl. Polym. Sci., 2022, 139, 52364 CrossRef CAS.
-
J. Lin, J. Shen and M. E. Zimmer, in Protective Coatings, ed. M. Wen and K. Dušek, Springer International Publishing, Cham, 2017, pp. 377–402 Search PubMed.
- J.-B. Lee, C.-H. Lee, S.-J. Ryu, B. Gong, O.-S. Kwon, M.-D. Kim, N. Y. Kim and Ki J. Paeng, Analysis of Waterborne Automotive Refinish Paint for Investigating Insurance Fraud, Appl. Chem. Eng., 2017, 28, 490–494 CAS.
- L. A. Brown, G. Fisk, M. A. Cohen, A. Crollard and S. G. Whittaker, Using an alternatives assessment framework to evaluate waterborne versus solventborne basecoats used in automotive refinishing, Integr. Environ. Assess. Manage., 2022, 18, 1101–1113 CrossRef CAS PubMed.
- F. Zhang, G. B. Zhang, Z. Chen and Z. Z. Long, Preparation and film formation mechanism of an environmental-friendly polyester/epoxy ester coil coating primer, Materialwiss. Werkstofftech., 2020, 51, 469–479 CrossRef CAS.
- I. M. Dehcheshmeh, P. N. Moghadam, A. P. Marjani and M. Frediani, Synthesis and Characterization of Eco-Friendly Waterborne Polyester-Urethane-Phosphorus Resin for Industrial Coil Coatings, Polym. Sci., Ser. A, 2021, 63, 690–704 CrossRef CAS.
- L. Fedrizzi, F. Deflorian, G. Boni, P. L. Bonora and E. Pasini, EIS study of environmentally friendly coil coating performances, Prog. Org. Coat., 1996, 29, 89–96 CrossRef CAS.
- M. Vlad Cristea, B. Riedl and P. Blanchet, Enhancing the performance of exterior waterborne coatings for wood by inorganic nanosized UV absorbers, Prog. Org. Coat., 2010, 69, 432–441 CrossRef CAS.
- F. Sbardella, M. P. Bracciale, M. L. Santarelli and J. M. Asua, Waterborne modified-silica/acrylates hybrid nanocomposites as surface protective coatings for stone monuments, Prog. Org. Coat., 2020, 149, 105897 CrossRef CAS.
-
K. Khaletskaya, V. Khaletski, S. Ediene and A. Maikiene, in The 9th International Conference ‘Environmental Engineering 2014’, Vilnius Gediminas Technical University Press “Technika” 2014, Vilnius, Lithuania, 2014 Search PubMed.
- Y.-T. Hsu, W.-H. Wang and W.-H. Hung, Architectural Sustainability and Efficiency of Enhanced Waterproof Coating from Utilization of Waterborne Poly(Siloxane-Imide-Urethane) Copolymers on Roof Surfaces, Sustainability, 2020, 12, 4411 CrossRef CAS.
- A. Hofland, Alkyd resins: From down and out to alive and kicking, Prog. Org. Coat., 2012, 73, 274–282 CrossRef CAS.
- N. Kartaloğlu, S. E. Akçin, M. Eren and A. Delibaş, Waterborne hybrid (alkyd/styrene acrylic) emulsion polymers and exterior paint applications, J. Coat. Technol. Res., 2023, 20, 1621–1637 CrossRef.
- A.-C. Hellgren, P. Weissenborn and K. Holmberg, Surfactants in water-borne paints, Prog. Org. Coat., 1999, 35, 79–87 CrossRef CAS.
- X. Wang and D. Jiang, Modification of nanometer calcium carbonate for water-borne architectural coatings, J. China Univ. Min. Technol., 2008, 18, 76–81 CrossRef CAS.
- C. Dominguez-Wong, G. M. Loredo-Becerra, C. C. Quintero-González, M. E. Noriega-Treviño, M. E. Compeán-Jasso, N. Niño-Martínez, I. DeAlba-Montero and F. Ruiz, Evaluation of the antibacterial activity of an indoor waterborne architectural coating containing Ag/TiO2 under different relative humidity environments, Mater. Lett., 2014, 134, 103–106 CrossRef CAS.
-
A. A. M. Al Qattan, Towards Sustainable Architectural Facade Applications of Nano technology in Coatings and Paints, 10th International Confernece on Nanotechnology in Construction, Egypt, 2018 Search PubMed.
-
F. Rideout, C. Ray, L. Henton and J. Peart, Waterborne Coatings for Marine Applications, Georgia Institute of Technology Report, 1981 Search PubMed.
- R. Ciriminna, F. V. Bright and M. Pagliaro, Ecofriendly Antifouling Marine Coatings, ACS Sustainable Chem. Eng., 2015, 3, 559–565 CrossRef CAS.
- A. S. Vijayan, A. Joseph, A. Joseph, T. S. Abhijith, B. G. Nair and V. Sajith, Polydopamine functionalised ceria-zirconia nanoparticles embedded water-borne epoxy nanocomposite for anti-biofouling coatings, Prog. Org. Coat., 2024, 187, 108094 CrossRef CAS.
- M. M. Rahman, H.-H. Chun and H. Park, Waterborne polysiloxane–urethane–urea for potential marine coatings, J. Coat. Technol. Res., 2011, 8, 389–399 CrossRef CAS.
-
World Intellectual Property Organization, WO 2011/076856 A1, 2011.
- M. Faccini, L. Bautista, L. Soldi, A. M. Escobar, M. Altavilla, M. Calvet, A. Domènech and E. Domínguez, Environmentally Friendly Anticorrosive Polymeric Coatings, Appl. Sci., 2021, 11, 3446 CrossRef CAS.
- K. Pélissier and D. Thierry, Powder and High-Solid Coatings as Anticorrosive Solutions for Marine and Offshore Applications? A Review, Coatings, 2020, 10, 916 CrossRef.
- I. D. Ibrahim, Y. Hamam, E. R. Sadiku, J. M. Ndambuki, W. K. Kupolati, T. Jamiru, A. A. Eze and J. Snyman, Need for Sustainable Packaging: An Overview, Polymers, 2022, 14, 4430 CrossRef CAS PubMed.
- B. Wohner, E. Pauer, V. Heinrich and M. Tacker, Packaging-Related Food Losses and Waste: An Overview of Drivers and Issues, Sustainability, 2019, 11, 264 CrossRef.
- B. M. Trinh, B. P. Chang and T. H. Mekonnen, The barrier properties of sustainable multiphase and multicomponent packaging materials: A review, Prog. Mater. Sci., 2023, 133, 101071 CrossRef CAS.
- S. Buxoo and P. Jeetah, Feasibility of producing biodegradable disposable paper cup from pineapple peels, orange peels and Mauritian hemp leaves with beeswax coating, SN Appl. Sci., 2020, 2, 1359 CrossRef CAS.
- A. Marinelli, J. Lyytikäinen, P. Tanninen, B. Del Curto and V. Leminen, Barrier, converting, and tray-forming properties of paperboard packaging materials coated with waterborne dispersions, Packag. Technol. Sci., 2024, 37, 149–165 CrossRef CAS.
- R. Mort, E. Olson, H. Thurber, S. Jiang, K. Vorst and G. Curtzwiler, Waterborne Polyurethane/Acrylic Adhesive Blends from Physaria fendleri Oil for Food Packaging Applications, Sustainability, 2022, 14, 8657 CrossRef CAS.
- Y. Zhong, T. Zhang, W. Zhang, G. Wang, Z. Zhang, P. Zhao, X. Liu and H. Li, Antibacterial castor oil-based waterborne polyurethane/gelatin films for packaging of strawberries, Food Packag. Shelf Life, 2023, 36, 101055 CrossRef CAS.
- G. Orzan, A. Cruceru, C. Bălăceanu and R.-G. Chivu, Consumers' Behavior Concerning Sustainable Packaging: An Exploratory Study on Romanian Consumers, Sustainability, 2018, 10, 1787 CrossRef.
- Z. Boz, V. Korhonen and C. Koelsch Sand, Consumer Considerations for the Implementation of Sustainable Packaging: A Review, Sustainability, 2020, 12, 2192 CrossRef.
-
BASF, JONCRYL® HPB 4010, https://dispersions-resins-products.basf.us/products/joncryl-hpb-4010, accessed 17 March 2024 Search PubMed.
-
Aquaspersions, Aquarez EAA, https://aquaspersions.com/products/?_industries=packaging, accessed 17 March 2024 Search PubMed.
- C. G. Demmer and N. S. Moss, A new development in water-based can coatings, J. Oil Colour Chem. Assoc., 1982, 65, 249–257 CAS.
- N. Zhang, J. B. Scarsella and T. G. Hartman, Identification and Quantitation Studies of Migrants from BPA Alternative Food-Contact Metal Can Coatings, Polymers, 2020, 12, 2846 CrossRef CAS PubMed.
- L. R. R. Da Silva, F. Avelino, O. B. F. Diogenes, V. D. O. F. Sales, K. T. Da Silva, W. S. Araujo, S. E. Mazzetto and D. Lomonaco, Development of BPA-free anticorrosive epoxy coatings from agroindustrial waste, Prog. Org. Coat., 2020, 139, 105449 CrossRef.
-
T. Parker, Waterborne: The future of coating in the can industry?, https://www.nspackaging.com/news/waterborne-solvent-borne-coating-varnishing-cans/, accessed 17 March 2024 Search PubMed.
- F. Deflorian, S. Rossi and S. Prosseda, Improvement of corrosion protection system for aluminium body bus used in public transportation, Mater. Des., 2006, 27, 758–769 CrossRef CAS.
-
J. V. Koleske, C. R. Hegedus, S. J. Spadafora, A. T. Eng, D. F. Pulley and D. J. Hirst, in Paint and Coating Testing Manual: 15th Edition of the Gardner-Sward Handbook, ed. J. V. Koleske, ASTM International, 100 Barr Harbor Drive, PO Box C700, West Conshohocken, PA 19428-2959, 2012, p. 739 Search PubMed.
- F. Moupfouma, Aircraft Structure Paint Thickness and
Lightning Swept Stroke Damages, SAE Int. J. Aerosp., 2013, 6, 392–398 CrossRef.
- H.-P. Rink and B. Mayer, Water-based coatings for automotive refinishing, Prog. Org. Coat., 1998, 34, 175–180 CrossRef CAS.
- D. Babić, T. E. Burghardt and D. Babić, Application and characteristics of waterborne road marking paint, Int. J. Traffic Transport. Eng., 2015, 5, 150–169 CrossRef PubMed.
-
H. J. Bremmer and M. P. Van Veen, Children's Toys Fact Sheet, National Institute for Public Health and the Environment (RIVM), Netherlands, 2002 Search PubMed.
- R. Sang and F. Yang, Effect of TiO2@CaCO3 Waterborne Primer on the Coloring Performance of Inkjet-Printed Wood Product Coatings, Coatings, 2023, 13, 2071 CrossRef CAS.
- L. Zhao, C. Hong, C. Wang, J. Li, H. Ren and C. Zhou, Enhancement of the adhesion strength of water-based ink binder based on waterborne polyurethane, Prog. Org. Coat., 2023, 183, 107765 CrossRef CAS.
- B. Sharma, S. Singh, B. Prakash, H. Sharma, P. K. Maji, D. Dutt and A. Kulshreshtha, Effect of cellulose nanocrystal incorporated acrylic copolymer resin on printing properties of waterborne inks, Prog. Org. Coat., 2022, 167, 106842 CrossRef CAS.
-
World Intellectual Property Organization (WIPO), WO 2018/182568 A1, 2018, pp. 1–46.
- X. Peng, Y. Liu, B. Xin, H. Guo and Y. Yu, Preparation and characterization of waterborne polyurethane nail enamel modified by silane coupling agent, J. Coat. Technol. Res., 2020, 17, 1377–1387 CrossRef CAS.
- D. De Smet, M. Wéry, W. Uyttendaele and M. Vanneste, Bio-Based Waterborne PU for Durable Textile Coatings, Polymers, 2021, 13, 4229 CrossRef CAS PubMed.
- G. Li, Y. Tan, Z. Li, G. Zhou, X. Yu, Q. Nie, J. Chen, Q. Yong and Z. Xie, Advances in waterborne polyurethane matting resins: A review, Appl. Surf. Sci. Adv., 2024, 19, 100557 CrossRef.
- N. Sukhawipat, W. Raksanak, E. Kalkornsurapranee, A. Saetung and N. Saetung, A new hybrid waterborne polyurethane coating synthesized from natural rubber and rubber seed oil with grafted acrylate, Prog. Org. Coat., 2020, 141, 105554 CrossRef CAS.
- S. Pedrini, D. J. Merritt, J. Stevens and K. Dixon, Seed Coating: Science or Marketing Spin?, Trends Plant Sci., 2017, 22, 106–116 CrossRef CAS PubMed.
- F. Lecomte, J. Siepmann, M. Walther, R. J. MacRae and R. Bodmeier, Polymer Blends Used for the Coating of Multiparticulates: Comparison of Aqueous and Organic Coating Techniques, Pharm. Res., 2004, 21, 882–890 CrossRef CAS PubMed.
- J. Wen, Z. Sun, F. Zhu and H. Fan, Construction of a fluorine-free anti-smudge waterborne polyurethane coating, Prog. Org. Coat., 2023, 174, 107254 CrossRef CAS.
-
Actega, Playing Card Coatings, https://www.actega.com/fr/en/Brands_PlayingCards_Coatings, accessed 19 March 2024 Search PubMed.
-
Spring Coating Systems, TH+ Ink for Thermal and Microwave Printing, https://spring-coating.com/inks/water-based-inks/th-ink/, accessed 19 March 2024 Search PubMed.
- S. Shi, D. Zang, X. Chen, T. Ma, L. Gu, D. Xu and J. Liu, Preparation and properties of a novel waterborne epoxy resin modified emulsified asphalt, Constr. Build. Mater., 2023, 371, 130767 CrossRef CAS.
- Y. Li, X. Yang and B. Lu, Preparation and curing properties of waterborne epoxy emulsified asphalt/DMP-30 composites, Case Stud. Constr. Mater., 2023, 18, e01869 Search PubMed.
- G. Guerrero-Vacas, F. Comino and O. Rodríguez-Alabanda, Evaluation of the effectiveness and durability of commercial non-stick coatings, J. Food Eng., 2024, 370, 111959 CrossRef CAS.
- H. Zhou, H. Wang, H. Niu, Y. Zhao, Z. Xu and T. Lin, A Waterborne Coating System for Preparing Robust, Self-healing, Superamphiphobic Surfaces, Adv. Funct. Mater., 2017, 27, 1604261 CrossRef.
-
Chemours, Teflon™ PTFE Coatings, https://www.teflon.com/en/products/coatings/ptfe-coatings, accessed 19 March 2024 Search PubMed.
- M. Argaiz, F. Ruipérez, M. Aguirre and R. Tomovska, Ionic Inter-Particle Complexation Effect on the Performance of Waterborne Coatings, Polymers, 2021, 13, 3098 CrossRef CAS PubMed.
- J. V. Koleske, R. Springate and D. Brezinski, Paint Coat. Ind., 2011, 1–64 Search PubMed.
-
G. Wypych, Handbook of Polymers, ChemTec Publishing, Toronto, 2nd edn, 2016 Search PubMed.
- M. Praw, Alkyd Resins, Part Two, Paint Coat. Ind., 2023 Search PubMed , https://www.pcimag.com/articles/111334-alkyd-resins-part-two, (accessed March 26, 2024).
-
S. Turner and Y. Liu, in Polymers for Advanced Functional Materials, ed. K. Matyjaszewski, M. Möller, K. Müllen and C. K. Ober, Elsevier, Amsterdam, 2012 Search PubMed.
- A. Patti, F. Costa, M. Perrotti, D. Barbarino and D. Acierno, Polyurethane Impregnation for Improving the Mechanical and the Water Resistance of Polypropylene-Based Textiles, Materials, 2021, 14, 1951 CrossRef CAS PubMed.
- C. Challener, CoatingsTech, 2021, 18 Search PubMed.
- S. Yomo, Effects of Organic Solvent on Curing Behavior and Storage Stability for Waterborne Paint Containing Catalyst Encapsulated in Micelles, Coatings, 2021, 11, 722 CrossRef CAS.
- L. E. Low, S. P. Siva, Y. K. Ho, E. S. Chan and B. T. Tey, Recent advances of characterization techniques for the formation, physical properties and stability of Pickering emulsion, Adv. Colloid Interface Sci., 2020, 277, 102117 CrossRef CAS PubMed.
- L. Ming, H. Wu, A. Liu, A. Naeem, Z. Dong, Q. Fan, G. Zhang, H. Liu and Z. Li, Evolution and critical roles of particle properties in Pickering emulsion: A review, J. Mol. Liq., 2023, 388, 122775 CrossRef CAS.
- D. Gonzalez Ortiz, C. Pochat-Bohatier, J. Cambedouzou, M. Bechelany and P. Miele, Current Trends in Pickering Emulsions: Particle Morphology and Applications, Engineering, 2020, 6, 468–482 CrossRef.
- B. Xie, X. Zhang, X. Luo, Y. Wang, Y. Li, B. Li and S. Liu, Edible coating based on beeswax-in-water Pickering emulsion stabilized by cellulose nanofibrils and carboxymethyl chitosan, Food Chem., 2020, 331, 127108 CrossRef CAS PubMed.
- Y. Zheng, H. Oguzlu, A. Baldelli, Y. Zhu, M. Song, A. Pratap-Singh and F. Jiang, Sprayable cellulose nanofibrils stabilized phase change material Pickering emulsion for spray coating application, Carbohydr. Polym., 2022, 291, 119583 CrossRef CAS PubMed.
- F. Yu, H. Feng, L. Xiao and Y. Liu, Fabrication of graphene oxide microcapsules based on Pickering emulsions for self-healing water-borne epoxy resin coatings, Prog. Org. Coat., 2021, 155, 106221 CrossRef CAS.
- I. Kalashnikova, H. Bizot, P. Bertoncini, B. Cathala and I. Capron, Cellulosic nanorods of various aspect ratios for oil in water Pickering emulsions, Soft Matter, 2013, 9, 952–959 RSC.
- Y. Lei, Z. Liu, B. Wu, L. Jiang and J. Lei, Preparation and properties of cross-linked waterborne polyurethane based on solvent-free route, Polym. Bull., 2020, 77, 3263–3275 CrossRef CAS.
- R. Dubey, T. C. Shami and K. U. B. Rao, Microencapsulation Technology and Applications, Def. Sci. J., 2009, 59, 82–95 CAS.
- V. Klug, J.-P. Schöggl, D. Dallinger, K. Hiebler, C. Stueckler, A. Steiner, A. Arzt, C. O. Kappe and R. J. Baumgartner, Comparative Life Cycle Assessment of Different Production Processes for Waterborne Polyurethane Dispersions, ACS Sustainable Chem. Eng., 2021, 9, 8980–8989 CrossRef CAS.
- P. Galanopoulo, N. Gil, D. Gigmes, C. Lefay, Y. Guillaneuf, M. Lages, J. Nicolas, F. D'Agosto and M. Lansalot, RAFT-Mediated Emulsion Polymerization-Induced Self-Assembly for the Synthesis of Core-Degradable Waterborne Particles, Angew. Chem., Int. Ed., 2023, 62, e202302093 CrossRef CAS PubMed.
- A. Patti and D. Acierno, Structure-property relationships of waterborne polyurethane (WPU) in aqueous formulations, J. Vinyl Addit. Technol., 2023, 29, 589–606 CrossRef CAS.
- Y.-C. Chen, Y.-C. Huang, C.-H. Wu, H.-W. Lin, W.-Y. Chiu, R.-J. Jeng and S.-H. Tung, Waterborne Epoxy/Acrylic Resins Stabilized through the Neutralization of Basic Amine-Modified Epoxy and Acidic Acrylic Copolymers, ACS Appl. Polym. Mater., 2024, 6, 828–836 CrossRef CAS.
- G. Clamen, T. Ferrari, Z. Fu, A. Hejl, G. Larson, L. Procopio, W. Rosano, A. Sheppard and A. Swartz, Protection of metal with a novel waterborne acrylic/urethane hybrid technology, Prog. Org. Coat., 2011, 72, 144–151 CrossRef CAS.
- T. Nabuurs, R. A. Baijards and A. L. German, Alkyd-acrylic hybrid systems for use as binders in waterborne paints, Prog. Org. Coat., 1996, 27, 163–172 CrossRef CAS.
- Z. Ling, C. Zhang and Q. Zhou, Synthesis and characterization of 1 K waterborne non-isocyanate polyurethane epoxy hybrid coating, Prog. Org. Coat., 2022, 169, 106915 CrossRef CAS.
- Y. Meng, J. Liu, J. Li, Y. Gao and Z. Zhang, Preparation and Characterization of the Cross-Linked Fluoro-Silicon Polyacrylate–Polyurethane Hybrid Emulsions for Superior Performance of Waterborne Coatings, ACS Appl. Polym. Mater., 2023, 5, 7854–7866 CrossRef CAS.
- Y. Meng, Y. Gao, J. Li, J. Liu, X. Wang, F. Yu, T. Wang, K. Gao and Z. Zhang, Preparation and characterization of cross-linked waterborne acrylic/PTFE composite coating with good hydrophobicity and anticorrosion properties, Colloids Surf., A, 2022, 653, 129872 CrossRef CAS.
- Y. Wang, J. Deng, J. Zhao and H. Shi, Comparative study on flame retardancy of phosphates modified waterborne styrene-acrylate emulsion-based coatings: Experiment and DFT calculation, Prog. Org. Coat., 2021, 158, 106346 CrossRef CAS.
- N. Kartaloğlu and A. Delibaş, Investigation of the effect of fluorine and silane-containing monomers on waterborne hybrid (alkyd/styrene acrylic) latexes, J. Coat. Technol. Res., 2024, 1067–1087 CrossRef.
- Y. Bao, R. Fu, Y. Liu, R. Guo and Y. Ding, Polyacrylate modified alkyd hybrid latex with high anti-corrosion performance synthesized via solvent-free and emulsifier-free method, Sustainable Chem. Pharm., 2024, 39, 101535 CrossRef CAS.
- O. M. Shafey, M. M. El-Sayed, F. A. Ahmed and W. S. Abdel-Wakil, Preparation, characterization, and evaluation of new alkyd-vinyl acetate grafted copolymer for water-based coating, Al-Azhar Bull. Sci., 2024, 35, 85–97 Search PubMed.
- A. Hooda, M. S. Goyat, J. K. Pandey, A. Kumar and R. Gupta, A review on fundamentals, constraints and fabrication techniques of superhydrophobic coatings, Prog. Org. Coat., 2020, 142, 105557 CrossRef CAS.
- X. Yan, L. Wang and X. Qian, Preparation and Characterization of Low Infrared Emissive Aluminum/Waterborne Acrylic Coatings, Coatings, 2020, 10, 35 CrossRef CAS.
- F. Zhong, Y. He, P. Wang, C. Chen, Y. Lin, Y. Wu and J. Chen, Self-assembled graphene oxide-graphene hybrids for enhancing the corrosion resistance of waterborne epoxy coating, Appl. Surf. Sci., 2019, 488, 801–812 CrossRef CAS.
- I. Khan, K. Saeed and I. Khan, Nanoparticles: Properties, applications and
toxicities, Arabian J. Chem., 2019, 12, 908–931 CrossRef CAS.
- B. Koyuncu, N. Aral, C. Candan and B. Nergis, Bismuth oxide nanoparticles/waterborne polyurethane-coated fabrics for ionizing radiation protection, J. Coat. Technol. Res., 2024, 21, 969–978 CrossRef CAS.
- H. He, Y. Liu, Y. Xu, S. Yu, W. Wang and F. Liang, Self-lubrication waterborne epoxy composite coating with amphiphilic Janus nanoparticles, Prog. Org. Coat., 2024, 189, 108303 CrossRef CAS.
- D. Acierno, L. Graziosi and A. Patti, Puncture Resistance and UV aging of Nanoparticle-Loaded Waterborne Polyurethane-Coated Polyester Textiles, Materials, 2023, 16, 6844 CrossRef CAS PubMed.
- A. Adibi, D. Valdesueiro, L. Simon, C. P. Lenges and T. H. Mekonnen, High Barrier Sustainable Paper Coating Based on Engineered Polysaccharides and Natural Rubber, ACS Sustainable Chem. Eng., 2022, 10, 10718–10732 CrossRef CAS.
- A. Adibi, D. Valdesueiro, J. Mok, N. Behabtu, C. Lenges, L. Simon and T. H. Mekonnen, Sustainable barrier paper coating based on alpha-1,3 glucan and natural rubber latex, Carbohydr. Polym., 2022, 282, 119121 CrossRef CAS PubMed.
- A. Marinelli, M. V. Diamanti, M. Pedeferri and B. Del Curto, Kaolin-Filled Styrene-Butadiene-Based Dispersion Coatings for Paper-Based Packaging: Effect on Water, Moisture, and Grease Barrier Properties, Coatings, 2023, 13, 195 CrossRef CAS.
- J. Xu, Y. Jiang, T. Zhang, Y. Dai, D. Yang, F. Qiu, Z. Yu and P. Yang, Synthesis of UV-curing waterborne polyurethane-acrylate coating and its photopolymerization kinetics using FT-IR and photo-DSC methods, Prog. Org. Coat., 2018, 122, 10–18 CrossRef CAS.
- X. Guo, S. Ge, J. Wang, X. Zhang, T. Zhang, J. Lin, C. X. Zhao, B. Wang, G. Zhu and Z. Guo, Waterborne acrylic resin modified with glycidyl methacrylate (GMA): Formula optimization and property analysis, Polymer, 2018, 143, 155–163 CrossRef CAS.
- S. Ahuja, Comparison of the performances of different drying enhancers for waterborne polyvinyl alcohol films, J. Appl. Polym. Sci., 2023, 140, e53876 CrossRef CAS.
- P. Berce, S. Skale, T. Razboršek and M. Slemnik, Influence of coalescing aids on the latex properties and film formation of waterborne coatings, J. Appl. Polym. Sci., 2017, 134, 45142 CrossRef.
- D. Sharma, J. Sharma, R. K. Arya, S. Ahuja and S. Agnihotri, Surfactant enhanced drying of waterbased poly(vinyl alcohol) coatings, Prog. Org. Coat., 2018, 125, 443–452 CrossRef CAS.
- M. Rawat, A. Chalotra and D. Tiwari, Design of waterborne coatings using crosslinking agent for enhancing drying, Mater. Today: Proc., 2022, S2214785322068602 Search PubMed.
- L. Boton, J. M. Puguan, M. Latif and H. Kim, Synthesis and properties of quick-drying UV-curable hyperbranched waterborne polyurethane coating, Prog. Org. Coat., 2018, 125, 201–206 CrossRef CAS.
- S. S. Hamdani, H. Emch, J. Isherwood, A. Khan, V. Kumar, A. Alford, I. Wyman, R. Sharma, P. Mayekar, A. Bher, R. Auras and M. Rabnawaz, Waterborne Poly(butylene succinate)-Coated Paper for Sustainable Packaging Applications, ACS Appl. Polym. Mater., 2023, 5, 7705–7717 CrossRef CAS.
-
Greenmunch, Greenmunch Take-Out Containers, https://www.greenmunch.ca/take-out-containers/, accessed 17 March 2024 Search PubMed.
-
GreenCentury, PLA Lined Kraft Deli Paper Container, https://greencentury.ca/product-category/bowls/compostable-bowls/pla-lined-kraft-deli-paper-bowl/, accessed 17 March 2024 Search PubMed.
- A. Lozhechnikova, H. Bellanger, B. Michen, I. Burgert and M. Österberg, Surfactant-free carnauba
wax dispersion and its use for layer-by-layer assembled protective surface coatings on wood, Appl. Surf. Sci., 2017, 396, 1273–1281 CrossRef CAS.
- M. Salzano De Luna, Recent Trends in Waterborne and Bio-Based Polyurethane Coatings for Corrosion Protection, Adv. Mater. Interfaces, 2022, 9, 2101775 CrossRef CAS.
- M. E. V. Hormaiztegui, B. Daga, M. I. Aranguren and V. Mucci, Bio-based waterborne polyurethanes reinforced with cellulose nanocrystals as coating films, Prog. Org. Coat., 2020, 144, 105649 CrossRef CAS.
- S. Bakker, J. Aarts, A. C. C. Esteves, G. A. Metselaar and A. P. H. J. Schenning, Water Barrier Properties of Resin-Stabilized Waterborne Coatings for Paperboard, Macromol. Mater. Eng., 2022, 307, 2100829 CrossRef CAS.
-
L. Yueyi, Z. Xiaodong and W. Pei, in Proceedings of the 2019 Annual Meeting on Management Engineering, ACM, Kuala Lumpur Malaysia, 2019, pp. 35–41 Search PubMed.
- S. J. Eilert, New packaging technologies for the 21st century, Meat Sci., 2005, 71, 122–127 CrossRef CAS PubMed.
- A. Zaitoon, X. Luo and L. Lim, Triggered and controlled release of active gaseous/volatile compounds for active packaging applications of agri-food products: A review, Compr. Rev. Food Sci. Food Saf., 2022, 21, 541–579 CrossRef CAS PubMed.
- Y. Ma, H. Wang, S. Li, Y. Chen, L. Zhang and X. Sheng, An eco-friendly and pH response cerium-based melamine phytate (PM) nanosheets with active and passive anticorrosion ability in water-borne epoxy coating, Appl. Surf. Sci., 2022, 597, 153726 CrossRef CAS.
- X. Luo, A. Zaitoon and L. Lim, A review on colorimetric indicators for monitoring product freshness in intelligent food packaging: Indicator dyes, preparation methods, and applications, Compr. Rev. Food Sci. Food Saf., 2022, 21, 2489–2519 CrossRef PubMed.
-
N. Bellotti and D. Cecilia, in Handbook of Waterborne Coatings, Elsevier, Amsterdam, 2020 Search PubMed.
- L. E. Mardones, M. S. Legnoverde, J. D. Monzón, N. Bellotti and E. I. Basaldella, Increasing the effectiveness of a liquid biocide component used in antifungal waterborne paints by its encapsulation in mesoporous silicas, Prog. Org. Coat., 2019, 134, 145–152 CrossRef CAS.
- M. V. Revuelta, S. Bogdan, E. Gámez-Espinosa, M. C. Deyá and R. Romagnoli, Green antifungal waterborne coating based on essential oil microcapsules, Prog. Org. Coat., 2021, 151, 106101 CrossRef CAS.
- N. Bellotti, L. Salvatore, C. Deyá, M. T. Del Panno, B. Del Amo and R. Romagnoli, The application of bioactive compounds from the food industry to control mold growth in indoor waterborne coatings, Colloids Surf., B, 2013, 104, 140–144 CrossRef CAS PubMed.
- A. M. Pereyra, M. R. Gonzalez, V. G. Rosato and E. I. Basaldella, A-type zeolite containing Ag+/Zn2+ as inorganic antifungal for waterborne coating formulations, Prog. Org. Coat., 2014, 77, 213–218 CrossRef CAS.
- P. Zhao, F. Mecozzi, S. Wessel, B. Fieten, M. Driesse, W. Woudstra, H. J. Busscher, H. C. Van Der Mei and T. J. A. Loontjens, Preparation and Evaluation of Antimicrobial Hyperbranched Emulsifiers for Waterborne Coatings, Langmuir, 2019, 35, 5779–5786 CrossRef CAS PubMed.
- H. Xu, W. Li, X. Wang, Y. Chen, J. Qian and Y. Li, Assisted Preparation of Waterborne Anti-etching Coating for Printed Circuit Board Photoresist Using Dibenzoyl Peroxide/Copper(II)-Phthalocyanine at Room Temperature, ACS Appl. Polym. Mater., 2024, 6, 232–243 CrossRef CAS.
- A. Lacruz, M. Salvador, M. Blanco, K. Vidal, A. M. Goitandia, L. Martinková, M. Kyselka and A. M. De Ilarduya, Biobased Waterborne Polyurethane-Urea/SWCNT Nanocomposites for Hydrophobic and Electrically Conductive Textile Coatings, Polymers, 2021, 13, 1624 CrossRef CAS PubMed.
- Y. Zhang, W. Zhang, X. Wang, Q. Dong, X. Zeng, R. L. Quirino, Q. Lu, Q. Wang and C. Zhang, Waterborne polyurethanes from castor oil-based polyols for next generation of environmentally-friendly hair-styling agents, Prog. Org. Coat., 2020, 142, 105588 CrossRef CAS.
- A. Sofyane, E. Ben Ayed, M. Lahcini, M. Khouloud, H. Kaddami, B. Ameduri, S. Boufi and M. Raihane, Waterborne butyl methacrylate (co)polymers prepared by Pickering emulsion polymerization: Insight of their use as coating materials for slow release-fertilizers, Eur. Polym. J., 2021, 156, 110598 CrossRef CAS.
|
This journal is © The Royal Society of Chemistry 2024 |
Click here to see how this site uses Cookies. View our privacy policy here.