DOI:
10.1039/D3GC04332K
(Critical Review)
Green Chem., 2024,
26, 10687-10717
Recent progress in energy conversion and storage of agricultural waste-derived (carbon/nano)materials: a review†
Received
8th November 2023
, Accepted 19th August 2024
First published on 16th September 2024
Abstract
Nowadays, with the mechanization of human societies, the demand for energy production and storage has also increased. Fossil fuels are running out, and thus, clean energy production using non-toxic and accessible sources is desirable. The valorization of waste materials into useful compounds is among the most important research subjects. Increasing interest in cost-effective raw materials and environmentally friendly precursors has brought agricultural residues up as promising, widespread biowaste all around the world. Rice husks (RHs), corn husks, wheat straws, sugarcane bagasse, fruit nut residues, and many other agricultural wastes have been broadly applied for designing novel materials, which can be applicable for energy conversion and storage. Agricultural waste contains useful chemical compounds, which may act as reducing, stabilizing, or capping agents, templates, precursors, etc., to produce various compounds viz. carbonaceous and (nano)materials. This review paper discusses the compounds that can be applicable for electrocatalytic applications for energy conversion in addition to energy storage. In fact, in this review, reports concerning agricultural waste-derived (carbon/nano)materials for energy conversion as well as energy storage devices such as different types of batteries, supercapacitors, and solar cell systems have been reviewed. The application of agricultural waste for energy conversion and storage is a very important issue due to the increase in the human population in the future, resulting in energy shortage problems. Therefore, suitable solutions must be developed for energy conversion and storage. On the other hand, the application of natural and environmentally friendly agricultural waste is very important for energy production and storage in addition to preventing the accumulation of this waste in the environment.
1. Introduction
Ongoing developments in numerous industries involve constant improvements to increase their revenues. Furthermore, considering green and environmentally benign resources for different activities and the preparation of new materials could solve the rising problem of environmental pollution.1,2 Many recent studies have attempted to design and establish environmentally benign methods and products to control pollution discharge into the environment.3–7 Extensive agricultural biowaste has always been of interest due to its safety for the environment, high availability, and extensive resources worldwide.8–15 Agricultural products are nutritionally valuable, yet their by-products, often referred to as waste, are frequently discarded without being utilized. In other words, the application of waste materials for the synthesis of various catalysts makes use of inexpensive and environmentally friendly materials.16–18 A huge number of agricultural residues are annually disposed of as waste.19–24 The USA, China, and India are the countries with the highest number of surveys, the main focus of which has been the application and exploitation of agricultural waste, obtained from cereal crops, principally corn and wheat, as they are the main producers of this sort of crop.25 Agricultural waste refers to compounds formed as a result of various agricultural processes and activities. Agricultural waste has advantages such as low price, recyclability, availability, an environmentally friendly nature, and being economical. In addition, agricultural waste is an important source for the production of different products, such as biofuel, biogas, antioxidants, enzymes, mushrooms, vitamins, antibiotics, and animal feed in addition to activated and porous carbons (PCs), because it is a rich source of bioactive compounds and carbon materials.20,26–32
Modern agriculture has many benefits. However, one major problem is the production of organic agricultural waste.33 This waste includes the peels of fruits and vegetables, waste fruits and vegetables, and plant debris such as stems, roots, husks, pods, and leaves. The agglomeration of this unusable waste causes environmental problems. For example, in some cases, people burn organic agricultural waste in the open air, which produces CO2 gas and creates environmental pollutants. Therefore, this waste must be reused for other applications such as the production of energy (biofuel and biogas), fertilizers, and animal feed. One of the most important applications of this agricultural waste is for catalytic purposes. In other words, this agricultural waste can play different roles, such as efficient supports, reducing or stabilizing agents, templates, or sources of carbon compounds, in the preparation of different types of catalysts.16,34–39
Several experimental studies over many years have made it plain that there are valuable chemicals in agricultural products and their residues, which can be used for the design and preparation of eco-friendly systems for various applications. They can be a source of carbon40,41 and be used as a source of energy, which burns cleaner than fossil fuels in addition to pharmaceuticals and food additives.10,42–47 The valorization of biowaste for energy production minimizes waste production as well as the emission of greenhouse gases.48–50 Furthermore, the functional groups present in agricultural waste such as carbonyl, alcoholic, acetamido, phenolic, amino, and amido groups have an affinity for heavy metal ions, which are capable of forming metal complexes or chelates.51,52 They are also promising for the adsorption of dyes and organic contaminants.53,54 Furthermore, these resources are renewable, biodegradable, cheap, and beneficial for the manufacture of biohydrogen55 and ethanol,56 and are good precursors for the production of activated carbon (AC) with a high surface area and pore volume.57,58
Lately, clean and renewable energy resources have become vital topics for researchers owing to environmental deterioration and energy shortages as a result of the overconsumption of fossil fuels.59–61 Moreover, in industrial applications, the tendency toward renewable energy has been growing significantly due to demands from the world's population, which has been predicted to grow more by 2030. The energy outlook in the USA is represented in Fig. 1. For instance, biomass energy sources were used to generate 26.7 billion kilowatt hours (k W h) of electricity in 2022.62 In the last few years, many attempts have been made to improve green and sustainable materials for energy conversion and storage.63,64 To this end, many electrode/electrocatalytic materials have been developed.63,64 Advanced energy conversion approaches include the application of fuel cells (FCs), the oxygen reduction reaction (ORR),64–66 the methanol and ethanol oxidation reactions (MOR and EOR),67,68 the oxygen evolution reaction (OER), the hydrogen evolution reaction (HER)69–71 and other electrochemical reactions such as the CO2 reduction reaction (CO2RR)72 and the nitrogen reduction reaction (NRR).73 In addition, a large number of green-energy storage devices such as lithium-ion batteries (LIBs)74,75 and supercapacitors76,77 have been widely studied and utilized. Moreover, considering the present global energy and environmental scenarios, hydrogen is assumed to be a key solution. Thus, water electrolysis is regarded as a vital source of hydrogen for the future.78,79 Furthermore, microbial fuel cells (MFCs) have attracted significant attention for the direct conversion of chemical energy from fuels into electrical energy.80,81 For single-chamber MFCs (SC-MFCs), O2 infused through the air-cathode is considered to be an efficient electron acceptor owing to its availability.82 However, the slow kinetics of the ORR, which causes poor energy conversion efficiency, low output power density, unsatisfactory stability, and difficulties in scaling up the preparation of the MFC device, have inevitably restricted the widespread application of MFCs and should be improved.83,84
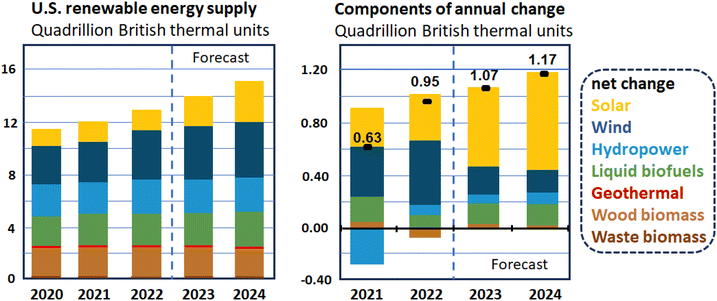 |
| Fig. 1 The short-term energy outlook released by the U.S. Energy Information Administration.62 | |
Today, a large number of electrodes used in various applications, such as energy production or storage, are made of carbon-based materials.63 Some of these carbon materials are derived from different compounds such as biomass or organic polymers,85–88 and their greatest disadvantage is their relatively low capacity in non-aqueous electrolytes. Conversely, some researchers have developed electrodes using carbon derived from polymers,89,90 which can be either expensive or involve costly carbon production processes. Therefore, finding compounds that are carbon-rich and cheap is a very important issue. In this field, agricultural waste has been widely used in recent years (Fig. 2). Agricultural waste is a rich source of carbon, from which carbon can be extracted through relatively inexpensive processes and used to fabricate electrodes for various applications.91–93 Another characteristic of agricultural waste is that it is a cost-effective, biodegradable, environmentally friendly, readily available, and renewable natural resource. All residues and by-products from the agriculture, forestry, farm animal, and agriculture-based industries are called agro-industrial wastes.94 Duhan et al. and Bajić et al. reported that agro-industrial wastes could be categorized as agricultural residues, and this could be further divided into field residues (such as corn stalks, sunflower stalks, wheat straw, rice straw (RS), oat straw, leaves, etc., remaining in the field after crop harvesting), process residues (such as corncobs, wheat chaff, rye chaff, rice chaff, coffee husk, groundnut husk, etc., obtained after crop processing) (Fig. 3a), industrial residues (such as cassava peel, potato peel, orange peel (OP), apple peel, tomato pomace, grape pomace, frying oil, etc., produced by the food industry after the primary processing of raw material) and industrial by-products (whey, crude glycerol, oil cakes, bagasse, etc., generated by the food industry at the end of processing).20,94 These agricultural wastes can serve as efficient electrode materials for different energy conversion and storage purposes. Fig. 3b displays the general procedure for the preparation of electrode materials from agricultural wastes.14,95–102 Different methods are employed for producing carbon from biowaste, each path resulting in diverse properties based on end-user requests. Porosity and surface area are the two critical aspects with significant effects on the energy storage capabilities of the carbon nanostructures generated, the high surface area of which prevents supercapacitive performance due to low porosity. Therefore, studies dealing with the tuning of the porosity in these carbons for improving the performance of energy storage devices (supercapacitors) are valuable.103
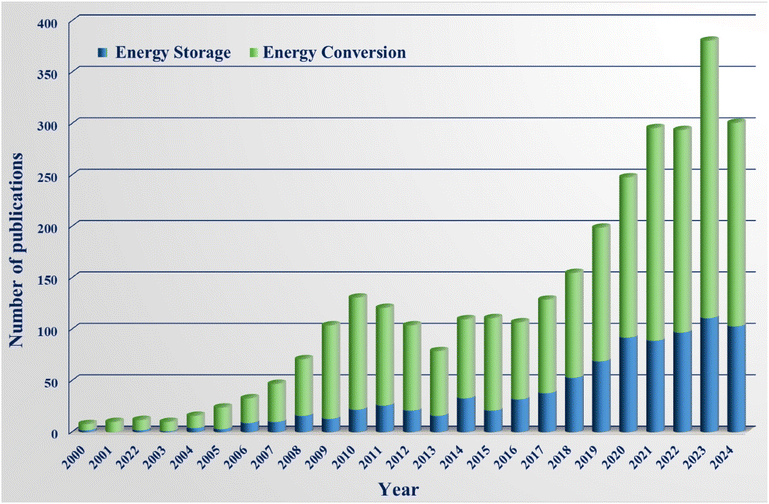 |
| Fig. 2 Progress in interest for the application of agricultural waste in energy conversion and energy storage in the period 2000–2024 (source: Scopus; date: 24 Aug 2024). | |
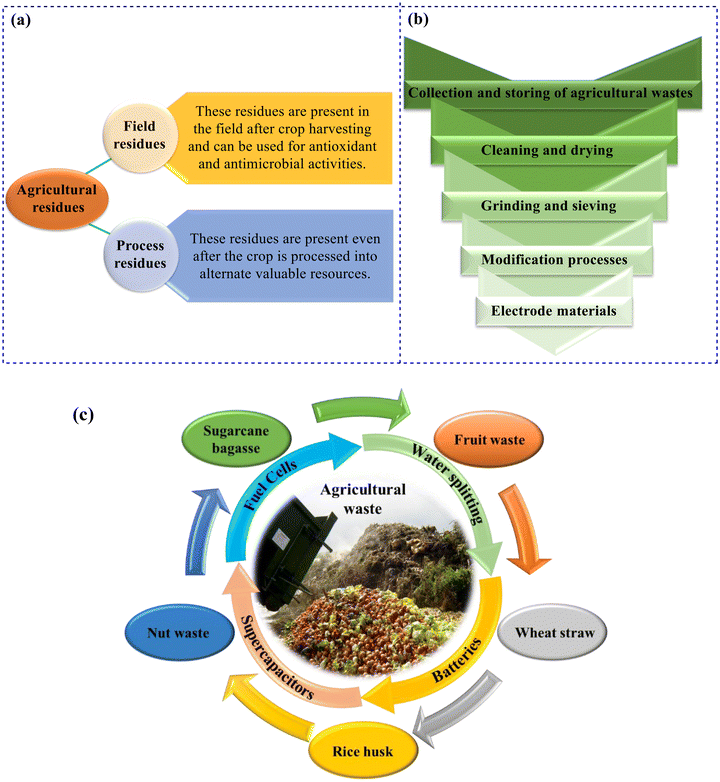 |
| Fig. 3 (a) Categorization of agricultural waste, (b) common preparation techniques for converting agricultural waste into electrode materials, and (c) diverse types of agricultural waste for energy conversion and storage. | |
In this review, recent developments in the preparation of agricultural waste-derived (carbon/nano)materials for advanced energy conversion and storage are investigated. The applications of agricultural residues including RH, RS, wheat straw, fruit, and nut residues such as shell, pomace, stone, bagasse, etc. for energy conversion and storage are also reviewed (Fig. 3c).
2. Various types of agricultural waste
2.1 Rice husk
One of the primary agricultural wastes is RH, which is produced in rice-growing countries. RH is one of the side products of rice grain formed in the rice production process.104,105 The results of various analyses have shown that RH contains carbon (9.55–18.74%), oxygen (30.90–35.51%), silica (58.19–43.17%), and potassium (1.36–1.66%).106,107 Internationally, approximately 545 million tons of RH are produced yearly, which is one-fifth of the gross production of rice every year.108 RH is usually burned by farmers, which causes pollutants and the emission of greenhouse gases, while it can be a useful resource for various applications.109,110 RH is a rich source of carbon and silica.111–115 Carbon derived from RH can be converted into PC or AC.115,116 RH has various uses including catalysts for chemical transformations, pollutant absorbents, and energy production and storage.116–120 According to reports, RH is mostly used in the energy field to make all kinds of lithium batteries, which could be related to the high amount of carbon in its structure.121,122
2.2 Fruit peels
Every year, large amounts of fruit peels are produced by the food-processing industry.123,124 Fruit peels are natural compounds and are biodegradable. However, large amounts of them accumulate in nature and can cause environmental pollution. Fruit peels contain useful compounds such as carbon, flavonoids, vitamins, etc., which can be converted into high-value-added materials by various methods.123,125,126 One of the most important applications of fruit peels is the production of biogas and bioethanol.127,128 Some fruit peel extracts have antimicrobial properties.129,130 In addition, as previously pointed out, fruit peels have flavonoids in their chemical structures and can thus be applied for the synthesis of different nanoparticles (NPs).43,131 Fruit peels include pomelo, pomegranate, banana, citrus, etc. Moreover, fruit peels are a rich source of carbon. The most important application of the carbons extracted from fruit peels is to make all kinds of electrodes. These electrodes are used for energy storage applications and are very effective because they have a natural source and are made from environmentally friendly and readily available compounds.132,133
2.3 Bagasse
Bagasse is produced by crushing and extraction of sugarcane juice. Bagasse is one of the most important agricultural residues in the world.134,135 Different analyses indicate that sugarcane bagasse has different portions of materials including lignin, cellulose, hemicellulose, wax, and ash.136,137 The materials present in the sugarcane bagasse indicate that this agricultural waste has many applications in different fields such as catalysis, fiber reinforcement in composites, adsorption of pollutants, biodegradation of crude oil polluted systems, electrodes, production of bioethanol, etc.138–143 Bagasse is mostly applied for the production of electricity for cogeneration boilers in sugar manufacture, and the surplus electricity is exported to the grid.144 As mentioned, bagasse is a rich source of cellulose and lignin. One of the ways to use this agricultural waste is to extract cellulose and lignin from it, which can then be used for various applications.145–148 It is also possible to prepare carbon from bagasse and use it in different forms such as PC, AC, etc. to make electrodes.149–153 Bagasse has mostly been used to make LIBs and supercapacitors.149,150,152,153 Moreover, there are also examples of energy conversion using bagasse.134,154
3. Agricultural waste-derived (carbon/nano)materials for energy conversion and storage
In recent years, owing to the rapid consumption of fossil fuels and as a result, the lack of energy, as well as environmental pollution and greenhouse effects, the production of clean energy and sustainable energy conversion technologies have gradually become common and popular topics among researchers. To store and use clean energy at any time, different electrochemical energy storage devices were developed. These devices include supercapacitors, solar cells, and various types of batteries. Theoretically, the energy storage activity of the devices mentioned mostly depends on the electrode materials. Agricultural waste-derived (carbon/nano)materials are excellent choices for these purposes because these materials have many advantages such as accessibility, non-toxicity, low price, and some useful functional groups. In this section, recent studies focusing on the conversion of energy using agricultural waste-derived (carbon/nano)materials are summarized. In addition, recent progress in the application of agricultural waste-derived (carbon/nano)materials in supercapacitors, solar cells, and different types of batteries is reported.
3.1 Fuel cell electrode reactions
FCs are energy conversion systems, which transform chemical energy into electrical energy through fuel oxidation. These conversion systems have many advantages such as cost-effectiveness, excellent efficiency, high energy density, etc. An FC contains different parts, namely, electrolytes, a cathode, an anode and an external circuit called the load. The fuel and oxidant reach the anode and cathode, respectively. Fuels can be pure hydrogen (H2) and gaseous hydrogenated compounds (such as MeOH and EtOH) as well as oxidants including pure O2 and oxygenated gaseous compounds (such as air and halogens). FC reactions are categorized into different groups including ORR, MOR, EOR, glycerol oxidation reaction, etc.155,156 In this context, two types of FC reactions, namely, ORR and MOR, which use agricultural waste-derived (carbon/nano)materials, are summarized.
3.1.1 Oxygen reduction reaction (ORR).
The ORR is a significant limiting factor to affect FCs. Therefore, various ORR electrocatalysts have been under investigation in recent years.65,156–158 Furthermore, conventional compounds for the synthesis of electrode materials, such as polypyrrole, porphyrin-based materials, and metal–organic frameworks (MOFs) have some disadvantages, making their large-scale production difficult due to the relatively cumbersome and expensive preparation process.159–161 Recently, there have been some studies using agriculture-based materials for ORR applications.162–164 In a study in 2019, Lu and his group used soybean straw (SS) biomass as a carbon source to design cobalt and nitrogen-doped (N-D) porous biocarbon electrocatalysts (CoNASS) with a high N content (1.92%) and embedded cobalt NPs with a specific surface area of 1185 m2 g−1 and sponge-like structure (Fig. 4a).165 The half-wave potential of commercial Pt/C (CPC) is 0.827 V (vs. RHE (reversible hydrogen electrode)) whereas the corresponding value for CoNASS is 0.786 V (vs. RHE), which shows the better efficiency of the manufactured electrode. The HRTEM and elemental mapping results for CoNASS are displayed in Fig. 4a.
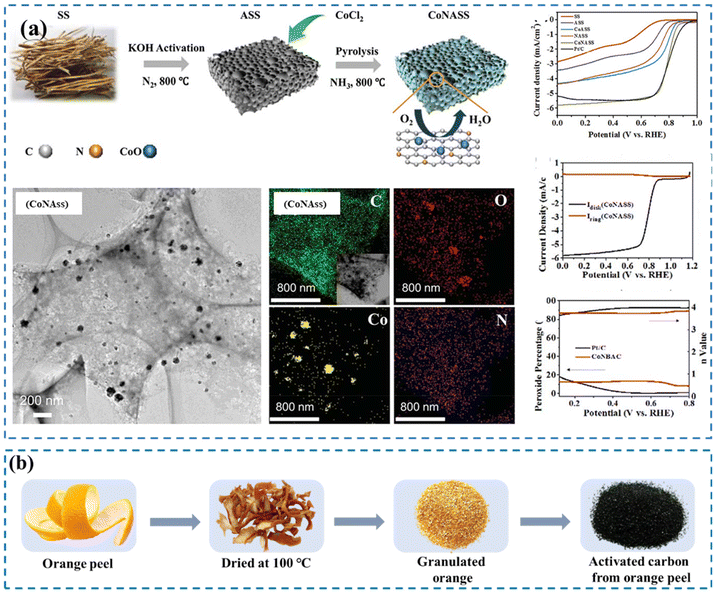 |
| Fig. 4 (a) Schematic representation of the formation of N and Co co-doped CoNASS, HRTEM image and elemental mapping of CoNASS, ORR performance, linear scan voltammetry (LSV) curves of SS, ASS, NASS, CoASS, CoNASS, and Pt/C in O2-saturated 0.1 M KOH solution at 1600 rpm (top), LSV curve of CoNASS in 0.1 M KOH solution at 1600 rpm obtained from rotating ring-disk electrode measurements (center), H2O2 yield and n value of CoNASS and Pt/C (bottom). Reproduced from ref. 165 with permission from Royal Society of Chemistry, copyright 2019. (b) Steps in the preparation of AC from OP. Reproduced from ref. 166 with permission from Elsevier, copyright 2017. | |
The preparation of Pt-supported AC electrodes from orange peel (Pt/OP-AC) was reported by Kalpana and co-workers. The Pt/OP-AC electrode was applied for supercapacitor and ORR applications.166 Their results revealed that the AC-derived OP had a high specific capacitance of 275 F g−1. This feature has made OP an excellent source for the preparation of AC. Fig. 4b shows the steps for the preparation of AC from OP.
MOFs are compounds with porous structures, which are assembled from metallic nodes and organic linkers with high specific surface areas, tunable pore structures, simplicity of functionalization, and several compositions.167,168 In 2017, Yin et al. prepared N-D pomelo peel-derived carbon (NPC) using melamine and pomelo peel (PP) waste.169 The prepared NPC showed good porosity with a high nitrogen content. It afforded a good catalytic performance toward the ORR in alkaline electrolytes. Furthermore, NPC was combined with ZIF-67 to prepare ZIF-67@NPC hybrids (Fig. 5a). The designed hybrid catalysts displayed markedly greater activities in comparison with 20 wt% CPC.
 |
| Fig. 5 (a) Schematic representation of ZIF-67@NPC for ORR and OER.169 (b) Schematic representation and images showing the preparation of BCMs and a-BCMs, SEM images, and illustration of carbocatalysis of the ORR over a-BCMs: (i) fast adsorption of O2 and (ii) interfacial carbocatalysis of the ORR over the catalytically active sites via the 4e− reduction pathway, with the assistance of the conductive carbon framework. Reproduced from ref. 176 with permission from Royal Society of Chemistry, copyright 2020. (c) Synthesis route to HP-SN-PGC. Reproduced from ref. 178 with permission from Elsevier, copyright 2019. | |
Valuable metallic ORR catalysts have been broadly applied as cathodes, owing to their high electrocatalytic potential.170 However, scarcity, high cost, methanol intolerance, and a lack of stability have limited the application of ORR catalysts in MFCs.171–173 In 2020, Zhou et al. reported the preparation of a PC cathode from RHs through hydrolysis, activation, and rolling.174 This study afforded a BET surface area of 1809 m2 g−1 with a maximum powder density of 317.7 ± 0.4 mW m−2. In addition, Lin and co-workers prepared N-D PC from RH, which had a similar electrocatalytic performance, better stability, and MeOH toxicity resistance in comparison with the CPC catalyst.175
In another study in 2020, Deng and co-workers explored metal-free FCs based on renewable, naturally abundant PP.176 They developed two kinds of N-D carbon catalysts from PP viz. biochar microspheres (BCMs) and their activated porous counterparts (a-BCMs) (Fig. 5b). The designed a-BCMs were employed for the cathodic ORR in MFCs. These a-BCMs showed a high porosity and great specific surface area with an appropriate amount of graphitic N and pyridinic N doping in the strong conductive carbonaceous background. The utilization of a-BCMs as the cathodic catalyst resulted in a power density of 907.2 mW m−2. The SEM images of PP, BCMs, and a-BCMs are displayed in Fig. 5b.
Lignin-based mesoporous carbonaceous compounds have been the center of wide consideration in recent studies owing to their high carbon content. In 2019, Peng and co-workers reported the preparation of sulfur and nitrogen co-doped carbon nanosheets using bagasse lignin-derived carbon (LC).177 The LC-4-1000 sample afforded a large pore volume of 1.40 cm3 g−1 with a high surface area of 1208 m2 g−1. LC-4-1000 had a higher positive half-wave potential and current density in comparison with those of CPC for the ORR in an alkaline medium.
In another study in 2019, Dai et al. used silica nanospheres as templates to organize highly-porous metal-free nitrogen/sulfur co-doped partially-graphitized carbon (HP-SN-PGC) in which pectin extracted from PP was a source of carbon (Fig. 5c).178 HP-SN-PGC was employed as a cathode for the ORR. SC-MFC employing the HP-SN-PGC-0.5 cathode with 0.5 g silica represented the shortest start-up period (45 h) and a power density of 1161.34 mW m−2, which was higher than that of Pt/C (1116.90 mW m−2).
Biomass, including SS,165 OP,166 PP,169 RHs,174 and bagasse lignin,177 is used as a carbon source to design porous biocarbon electrocatalysts for the ORR. The catalytic activities and efficiency of these electrocatalysts were compared with those of a conventional electrode such as Pt/C. In addition to economic and environmental superiority, they exhibited better performance in spite of the multi-stage and long preparation process in some cases.179–183 The higher activities of electrocatalysts may be related to the porosity and active sites of carbon-based catalysts derived from biomass.
3.1.2 Methanol oxidation reaction (MOR).
The MOR is a serious subject in studies on the direct methanol fuel cell (DMFC) as a power source for electric/electronic vehicles and devices.184,185 In the past years, there have been some studies in this field in which agriculture-based materials were used for the MOR.154,186 One of the most common types of agricultural waste is sugarcane.154 After extracting sugarcane juice, its residue, which is called bagasse, is widely available in nature and has produced certain environmental difficulties. Bagasse can be used for some applications. For example, in 2017, Zou and colleagues investigated the synthesis of porous MoS2/N-D carbon (MoS2/CNX), which was applied as a support for Pt (Fig. 6a).187 They used bagasse waste as an efficient source of carbon materials in the MOR, due to its high surface activity and good mass performance. The prepared Pt/MoS2/CNX material was applied for the MOR (Fig. 6b). CNX has rich binding sites for the growth and dispersion of MoS2 particles. According to the experimental results, Pt/MoS2/CNX showed a higher mass performance than CPC (1030.2 vs. 405.4 mA mgpt−1). However, CNX has plentiful attachment sites for anchoring Pt. In addition, MoS2/CNX has many oxygen-containing functional groups, which lead to the oxidation of intermediates (CO-species) on the active sites of Pt.
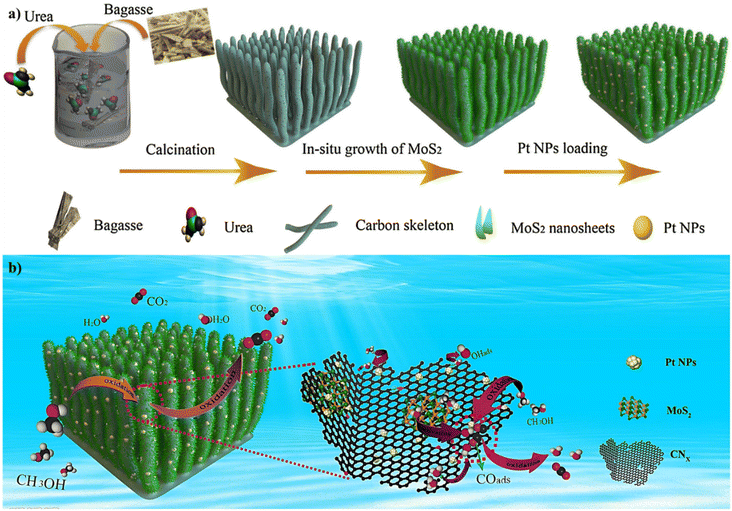 |
| Fig. 6 Schematic representation of (a) the preparation of Pt/MoS2/CNX nanocomposites and (b) MOR using the Pt/MoS2/CNX catalyst. Reproduced from ref. 187 with permission from Elsevier, copyright 2017. | |
In another example in 2021, Ishak and co-workers developed an efficient technique for the manufacture of Pt NPs through a bioreduction process.188 They used sugarcane (Saccharum officinarum L.) bagasse extract as a bio-based reducing agent for the preparation of biogenic Pt NPs. The biogenic Pt NPs prepared have an electrochemical performance for the MOR. The biogenic Pt NPs displayed a high performance for the MOR with a high mass activity (about 382.80 mA mg−1). In addition, the green synthesis of Pt NPs based on OP extract, which is used as a green, inexpensive, and bio-based reducing agent, was developed by Karim and co-workers.189 The Pt NPs prepared were then immobilized on carbon black for the MOR. Their experimental results revealed that the Pt NPs had a high performance for the MOR in a DMFC.
3.2 Electrochemical water splitting reactions
For many years, the application of a green source of energy has been one of the most important issues for researchers. Hydrogen, which is a green and environmentally friendly source of energy, can be produced by the electrolysis of water as well as electrochemical water splitting.190 In this electrochemical reaction, water is split into its elemental components, namely, H2 and O2. In fact, the electrochemical water splitting reaction involves two half-reactions, referred to as oxidation and reduction, which occur in the anode and cathode, respectively. The half-reactions of water oxidation and reduction are often referred to as the OER and HER, respectively. The OER and HER half reactions are displayed in eqn (1) and (2).191–193 In this section, some reports on agriculture-based materials for the OER and HER are investigated. | H2O → 2H+ + 2e− + 1/2 O2 OER | (1) |
3.2.1 Oxygen evolution reaction (OER).
The OER is an important electrochemical reaction in electrolytic water-splitting and metal–air batteries to achieve clean energy production and efficient energy storage.194–197 Today, the application of carbon derived from biowaste has attracted much consideration for the OER.198,199 Among these, waste onion (Allium cepa) skins are important owing to their exclusive chemical composition including S, N, and polyphenols. In a study in 2022, Kim and co-workers developed an effective technique for the synthesis of an electrocatalyst based on waste onion skins.200 In fact, they developed a process for transforming waste onion skins into an efficient and very stable electrocatalyst. They prepared a core–shell material in which Fe–Fe3C particles and N-D carbon (FO800) were the core and shell, respectively. The FO800 material prepared displayed a high OER performance. Due to the presence of a protective carbon shell, FO800 showed high stability for 24 h. The FO800 sample displayed current densities of 10 and 50 mA cm−2 at low overpotentials (Ov) of 330 and 380 mV, respectively, with a Tafel slope of 52 mV dec−1.
Some of the most important materials for OER catalysts are transition metal phosphates and phosphide.201–204 In fact, the partially positive charge of the metals is applied as an acceptor of hydroxyl, which becomes the active center for the OER. For example, in 2022, Zhang and colleagues investigated the synthesis of an efficient bifunctional catalyst for the ORR/OER.204 For this aim, they used crude wheat straw, which contained a large amount of cellulose and was a green source of carbonaceous compounds. They synthesized novel Fe/Co bimetallic phosphide NPs embedded in N, P dual-doped carbon matrix (FeCoP2-NPWC) (Fig. 7) for catalyzing the ORR and OER. The FeCoP2-NPWC catalyst exhibited an excellent ORR performance with a half-wave potential of 0.85 V (vs. RHE) and a limiting current density of 6 mA cm−2, which surpassed that of the Pt/C catalyst. It also exhibited an excellent OER performance and achieved an overpotential of 339 mV at a current density of 10 mA cm−2. Subsequently, the prepared catalyst was used in a rechargeable zinc–air battery. The rechargeable liquid and solid zinc–air batteries achieved 122.5 and 55.6 mW cm−2 and were stable upon cycling for 110 and 35 h, respectively.
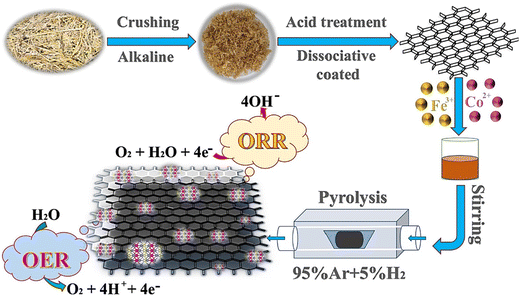 |
| Fig. 7 Schematic representation of the synthesis of FeCoP2-NPWC. Reproduced from ref. 204 with permission from Elsevier, copyright 2022. | |
In another study, the preparation of an efficient and inexpensive bifunctional (OER and ORR applications) catalyst for Zn–air batteries was performed by Sumboja.205 In fact, they used a heterostructure of carbon-containing graphitic and amorphous carbon, which was derived from red bean pods as agricultural waste. The heterostructured carbon had a high surface area (625.5 m2 g−1), showing an ORR onset potential of 0.89 V vs. RHE and an OER Ov of 470 mV at 5 mA cm−2. To enhance the bifunctional performance of the catalyst, the prepared compounds were modified with nitrogen dopant and hollow FeCo NPs, to reach an ORR onset potential of 0.93 V vs. RHE and an OER Ov of 360 mV.
In the OER and ORR, waste onion,200 crude wheat straw,204 and red bean pods205 were applied as green and low-cost precursors for the preparation of carbonous compounds to achieve heterogeneous catalysts. In some cases, more modification and functionalization are needed to reach acceptable efficiency despite the tedious preparation process.
3.2.2 Hydrogen evolution reaction (HER).
Although non-noble metal-based carbon composites are widely utilized,206 the application of biomass and agriculture waste-derived electrocatalysts is a significant consideration today.199,207 Zhou and co-workers used watermelon peel to fabricate Mo2C/C electrocatalysts through a two-step approach and pyrolysis process for HER applications.208 The sample, denoted as Mo2C/C-800 °C, showed a geometrical Ov of 133 mV to deliver a current density of 10 mA cm−2 in 1 M KOH solution with long-term durability for 300 h. This excellent HER performance is due to the large surface area, unique pore sizes of the Mo2C/C electrocatalysts, and rich mass transfer of electrons.
Electrocatalyst powders based on transition metals have been broadly studied for the HER.209,210 In 2020, Min and co-workers developed a self-supported H2 evolution cathode based on a PC membrane derived from PP (PPDC) with entrenched Co NPs (Co@PPDC), which showed a high electrocatalytic performance for the HER in 1 M KOH solution with Ov values of 154 and 264 mV at current densities of 10 and 100 mA cm−2, respectively.211 Furthermore, the good structural integrity of Co@PPDC results in high cycling stability for 2000 cycles and a stable current density of ∼100 mA cm−2 at a constant Ov of 265 mV over 12 h with a faradaic efficiency and H2 production rate of almost 100% and 1.56 mmol h−1, respectively.
A study by Yun et al. involved the successful preparation of a sequence of nano-sized bimetals (Al, Cr, and Fe) and niobium oxide NPs anchored on aloe peel (AP)-derived PC skeleton hybrids (AN/APPC, CN/APPC, and FN/APPC) through co-precipitation.212 The prepared samples were used as electrocatalysts for the alkaline HER and in photovoltaic applications. The synergy between the highly conductive PC skeleton and nano-sized metal niobium oxides caused these robust poly-component hybrid electrocatalysts to display outstanding catalytic performance and accelerated triiodide reduction and the HER. A solar cell with an AN/APPC electrocatalyst afforded a high device efficiency of 7.31%, which was higher than that of Pt (6.84%), and the AN/APPC electrocatalyst showed an Ov of 131.6 mV with a current density and Tafel slope of 10 mA cm−2 and 54 mV dec−1, respectively, in 1 M KOH for the HER. In addition, in 2020, Yoo and co-workers used golden shower pod biomass to synthesize PC or N-D porous carbon (N-PC). For the HER and OER, N-PC@Ni displayed Ov values of 179 and 314 mV at 10 mA cm−2 and Tafel slopes of 98 and 132 mV dec−1.213
PCs derived from watermelon peel,208 PP,211 and AP213 were used to generate heterogenous catalysts for the HER. The catalysts prepared using waste materials exhibited good performance and stability, as indicated by essential performance data. Table S1† presents some other reports on the energy application of agricultural waste-derived materials. According to Table S1,† if PC is prepared from agricultural waste (in this table, most of the waste includes peels of various fruits such as bananas, grapefruit, pomelo, etc.), its specific surface area is relatively high, and as a result, it performs better. It is also possible to prepare metal-free N-D porous carbons with high specific surface areas (entry 12). In addition, this table shows that the carbon derivatives obtained from PP have higher specific surface areas than other waste and are very suitable for the ORR and OER.
3.3 Supercapacitors
Recently, there has been increasing interest in high power and high energy density storage systems.214 Supercapacitor technology has made significant progress in recent years.215–217 Supercapacitors consist of thin dielectric layers and high surface area electrodes. One noticeable advantage of supercapacitors in comparison with batteries is their higher power density. Furthermore, supercapacitors are more brilliant than traditional capacitors (Fig. 8a).218–220 They have a robust thermal operating range, high power capability, many charging–discharging cycles, and a bridging function for the power/energy gap among traditional dielectric capacitors. Furthermore, agricultural waste can act as an important source for energy applications.221–224 Since agricultural waste is renewable, abundant, and low-cost, its derivatives can be employed for several applications including energy storage systems.225–230 It can be converted into carbon-based compounds including carbon nanotubes (CNTs), AC, porous (nano)carbon, etc., which are used as electrodes (Fig. 8b).231–236
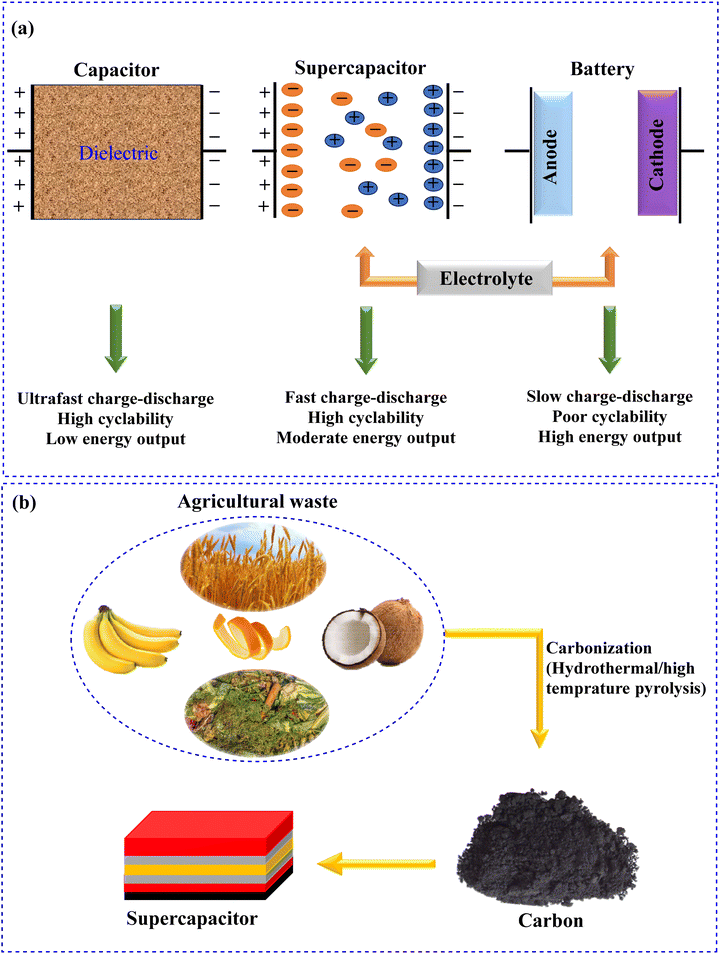 |
| Fig. 8 (a) Comparison of batteries, conventional capacitors, and supercapacitors and (b) carbonization of agricultural waste and its applications in supercapacitors. | |
Carbon-based supercapacitors have several advantages including a fast charge–discharge rate, high power density, and long service life. Several types of biomass have been employed as precursors for carbonaceous compounds, including shaddock peel,237 nuts and fruit peel,238–244 RH,245,246 RS,247,248 wheat straw,249,250 corn husk,251,252 corn straw,253,254etc.
Table S2† presents the carbonaceous compounds from agricultural waste resources and some of their properties, which make them promising for supercapacitor applications. According to Table S2,† RH has a large specific surface area compared to other waste and its specific capacity is high, which makes it suitable for making electrodes for supercapacitor applications (entries 9, 12, 16, 17, 19, 21, 22 and 23). Carbon derivatives are prepared from them. Moreover, this table shows that most of the carbon derivatives prepared from waste are porous carbons, which are used with relatively high capacities to make supercapacitors.
Biomass-derived PC materials show good conductivity, large specific surface areas and provide a framework for doping; especially N, O, P and S.255–258 In addition, according to studies, the peels of citrus fruits constitute a high percentage of the total fruit and are usually considered waste. Citrus fruit peels are known as good precursors of carbon since they are largely made of cellulose, hemicellulose, pectin, and lignin.259–261 Mehare et al. developed a route to synthesize PC materials from lemon peel for supercapacitor applications.262 The synthesized compounds exhibited a high specific capacitance of 121 F g−1 at 1 A g−1 in a system consisting of three electrodes and 106 F g−1 at a current density of 0.2 A g−1 in a symmetric device with a specific energy and power of 11.84 W h kg−1 and 361.8 W kg−1, respectively, as well as cycling stability of 100% over 1000 cycles.
In another recent study by Li et al. in 2022, N, P doped PC nanosheets (NPCNs) were synthesized as high-performance supercapacitors using PP as a spongy structure to surround NH4H2PO4 particles as an activator and co-dopant.263 Accordingly, the optimal sample obtained at a pyrolysis temperature of 750 °C (denoted as NPCNs-750) showed a high specific capacitance of 314 ± 2.6 F g−1 and good rate capability (retention of 82% of capacitance at 20 A g−1). Furthermore, NPCNs-750//NPCNs-750 SSC, the optimal sample, was employed as a symmetrical supercapacitor (SSC) in Li2SO4 as an electrolyte and showed a high energy density of 36 ± 1.5 W h kg−1 at a power density of 1000 W kg−1 with excellent cycling stability after 10
000 cycles with 99% retention.
In 2020, a research group synthesized and compared a sequence of carbon compounds from RH and bean dregs with diverse mass ratios.264 The ratio of 1
:
1 presented a greater capacitive performance of 319 F g−1 at 0.2 A g−1 in a two-electrode system with a capacitance retention of 92.6% after 10
000 cycles. These results show that the synergistic effects of hierarchical porous structures and nitrogen content afford a promising suggestion for the production of high-performance supercapacitors. In other research, Shin et al. prepared AC papers as supercapacitor electrodes.265 According to their results, the porosity and electrochemical efficacy of the compound depended strongly on the activation temperature. For example, the specific surface area of 202.92 at 500 °C increased to 2158.48 m2 g−1 at 1100 °C.
Moreover, the proximate analysis of onion peels shows the presence of ∼80% carbohydrates, which can be a good source of carbon.266 Dhoble et al. effectively prepared hierarchical PC from onion peel through a double crucible system with a high specific capacitance of 127 F g−1 at a current density of 0.75 A g−1 with a capacitance retention of 109% after 2000 cycles in a three-electrode system in addition to an energy density of 13.61 W h kg−1 at a power density of 200.8 W kg−1 with noteworthy electrochemical stability and capacitance retention up to 100% over 14
000 cycles.267
In 2020, Musyoka et al. used hydrochar derived from waste onion peels to prepare AC.268 The best sample showed a specific surface area of 3150 m2 g−1, a pore volume of 1.64 cm3 g−1, and hydrogen take up of above 3 wt%. It also showed a specific capacitance of 169 F g−1 at a specific current of 0.5 A g−1. Furthermore, the compound displayed a high coulombic efficiency of 99.85% at 5 A g−1 after 10
000 cycles. In addition, Chaudhary et al. prepared ternary-doped layered graphene nanosheets from onion peel via a green pyrolysis synthesis method. The synthesized nanosheets were used for energy storage applications with a capacitance of 450 A g−1 at a current density of 1 A g−1 in 2 M H2SO4 solution.269
As mentioned, biowaste is composed of carbon-rich compounds, which can be promising feedstocks for the preparation of AC as a potential electrode material in supercapacitors.270–272 In 2021, Ajay and co-workers used OP as the precursor of AC (OPAC) and polyaniline to prepare polyaniline–OPAC nanocomposites as electrode materials for supercapacitors.273 OPAC has a high surface area of 904 m2 g−1 and an average pore volume of 0.5543 cm3 g−1. The polyaniline–OPAC electrode showed a specific capacitance of 427 F g−1 and a capacitance retention of 75% after 5000 cycles, which was better than that of pure OPAC.
In another study in 2021, Sathish et al. reported the preparation of S-doped graphitic carbon nitride/cobalt disulfide (S-gC3N4/CoS2) and OP-derived AC as positive and negative electrodes, respectively, to prepare a high-performance hybrid asymmetric supercapacitor with a very high current density of 30 A g−1 and high electrochemical stability of 89% over 100
000 cycles with a coulombic efficiency of 99.6%.274
Furthermore, bimetallic sulfides are an innovative type of electrode for supercapacitors because of their rich redox active sites, high conductivity, and wide operating potential window. In 2021, Xu and co-workers used Ni–Co sulfide hollow nanoboxes and RH AC as the anode and cathode, respectively, which afforded a remarkable energy density of 46.7 W h kg−1 at a power density of 400 W kg−1 and high cycling stability of 82.7% at 5 A g−1 after 10
000 cycles.275
Furthermore, Wang et al. prepared N-D PC from RHs in 2020.276 The prepared nitrogen-containing PC (4NPC-800) showed a good volumetric capacitance of 306 F cm−3 at 0.5 A g−1 in 1 M H2SO4 electrolyte and a superior volumetric energy density of 15.24 W h L−1 at 594 W L−1 as well as excellent cycling stability.
Moreover, wheat husk contains a high percentage of carbon, which makes it an essential precursor for AC production.277 In 2021, Gul and Baig carbonized wheat husk to prepare AC (WHAC).278 The NiCo2S4/WHAC/Ni electrode was synthesized through a hydrothermal process with a capacitance of 1962 F g−1 at a current density of 1 A g−1.
In the same year, Niu et al. reported the preparation of capacitive carbons with high surface areas, uniform porous structures, and near-perfect graphitization structures employing corncob residues as the carbon source.279 The material showed high specific capacities of up to 394.9 F g−1 at a current density of 1 A g−1, a high energy density of 8.9 W h kg−1 at a current density of 0.5 A g−1, and outstanding cycling stability (99% lifetime retention after 10
000 cycles).
Carbon dots (CDs) are well-known NPs with exceptional properties including nanometer size, various functional groups, high surface area, surface HA, and structural tunability. They can be equipped with available cheap precursors. CDs are rich in surface N and O-containing functional groups, which are known to improve electron transfer, ion adsorption, charge transport, hydrophilicity, surface wettability, and electrochemical conductivity and they can act as electron reservoirs. Moreover, they can introduce pseudo-capacitive behavior and promising contact between electrolytes and electrodes and thus have been employed as additives in supercapacitor electrodes.280 In 2019, Gomes and Hoang synthesized zucchini-derived CDs using zucchini waste with a porous nature and carbon and oxygen in the structure.281 The prepared CDs were treated with graphene oxide to afford three-dimensional (3D) porous reduced graphene oxide/CD composites with a surface area and total pore volume of 185 m2 g−1 and 0.58 cc g−1, respectively. The specific capacitance of the composite was 374 F g−1 at 2 mV s−1 with a high capacitance retention of 93.8% over 10
000 cycles at 10 A g−1.
Moreover, biochar is known as a significant sort of carbon-based compound for preparing supercapacitor electrodes.282 In 2018, Zhou et al. prepared PC from corn straw biochar and employed it as the electrode for electric double-layer capacitors in which the hierarchical micro-meso-macro-porosity meaningfully enhanced the activity of biochar-based carbons.283 As observed, the surface area, pore volume, and maximum specific capacitance were 2790.4 m2 g−1, 2.04 cm3 g−1, and 327 F g−1, respectively. The prepared electric double-layer capacitors presented excellent cycling stability for 120
000 cycles at 5 A g−1 in alkaline electrolytes.
Furthermore, biomass-derived cellulose is a renewable, sustainable, low-cost, and biodegradable biopolymer with good thermal and electrochemical stability.284,285 In 2021, Zhang et al. prepared an N-D PC derived from cellulose microfibers of RS.286 The organized carbon material had a moderate nitrogen doping of 1.65 at% and an ultrahigh specific surface area of ∼2800 m2 g−1. In addition, the compound showed an outstanding specific capacitance of 380.1 F g−1 at 0.5 A g−1 and capacitance retention of 61.8% at 50 A g−1. The capacitance loss of this compound was only 4.6% after 10
000 charge–discharge cycles, indicating its good cycling stability.
Furthermore, in 2017, Song and co-workers used residual pre-cross-linked lignin from wheat straw to synthesize meso-structured carbon using Pluronic F127 and nano-sized MgO as templates with a specific surface area, total pore volume, and mesopore content of 712 m2 g−1, 0.90 cm3 g−1, and 83%, respectively, which proved to be promising for supercapacitor applications.287
Different types of biomass including lemon peel,262 PP,263 RH and bean dregs,264 onion peel,267,268 OP,273,274 RH,275,276 banana peel,288 Jackfruit,289etc. are employed alone or in combination with other compounds to generate PC as an active and porous component of supercapacitors. High stability, good specific capacitance, and improved specific surface area are the advantages and multi-step synthesis processes, unintelligible final structure, and the need for more modifications are the disadvantages of biowaste-based supercapacitors. However, the high demand for new sources of energy justifies research on this topic.
More studies are focusing on the preparation of supercapacitors from agricultural waste. Table S3† briefly summarizes these studies. According to Table S3,† the electrodes prepared from different agricultural wastes and metals placed on them during electrode preparation have high specific capacities. Of course, this table shows that nitrogen or sulfur-doped carbon metal-free electrodes can also have a relatively high specific capacity (entries 2 and 4). In addition, AC and PC derived from some wastes alone are suitable options for making electrodes because they have relatively high capacitances (entries 9, 10, and 12). This shows that this waste, which includes corn husk, garlic peel, and mung bean husk, is very suitable for making electrodes.
3.4 Batteries
Today, with the industrialization of human societies, the pursuit of sustainable development for the entire human race faces significant challenges. Burning different fuels causes global warming and air pollution. Thus, today, the production of energy from renewable sources is a very important and necessary matter. One of the most promising devices for energy storage is rechargeable batteries, which are broadly applied in electric vehicles. These batteries have many advantages, the most important of which are their simple technology and environmentally friendly nature.290–292
3.4.1 Li-ion batteries.
Among various kinds of rechargeable batteries, LIBs are the most important owing to their great energy density, the absence of any memory results, and only a gradual loss of capability when not in use.293 In other words, LIBs play an important role in today's modern world.294,295 Some researchers have used natural and biowaste sources for the preparation of these LIBs.296,297 In this section, the applications of different agricultural wastes for the synthesis of LIBs are reported.
One of the most commercial anodes applied for the preparation of LIBs is graphite. However, graphite cannot meet the future demands of people because of its small theoretical capacity. Thus, researchers have investigated novel promising anode materials.298,299 RH is an abundantly accessible agricultural waste, which is a rich source of silica and carbon. In a study in 2021, Dawei and colleagues reported the synthesis of the RH-based SiO2/C composite and applied it as a promising anode material for the preparation of LIBs.300 On the other hand, they prepared SiO2/C by adjusting the ash content of pyrolyzed RH with NaOH solution and studied the effect of ash amount variations on the Li storage efficiency of SiO2/C. Their experimental results revealed that 19.2 wt% ash had a greater reversible capacity of 886 mA h g−1 at 200 mA g−1. In another study performed by Sun and colleagues, the construction of S/N dual-doped porous C/SiOx composites (SN@C/SiOx) was investigated (Fig. 9a).301 For this aim, they used RH as a source of Si and C and applied thiourea as a source of N and C. The SN@C/SiOx material synthesized, as a high-performance LIB anode, provided a remarkable particular capacity (1150 mA h g−1). EDX mapping results for SN@C/SiOx and the charge/discharge curves are displayed in Fig. 9a.
 |
| Fig. 9 (a) Schematic representation of the green route to synthesize SN@C/SiOx composite and its structure, galvanostatic discharge–charge profiles at 0.1 A g−1, and long cycling property at 1 A g−1. Reproduced from ref. 301 with permission from Elsevier, copyright 2021. (b) Schematic representation of the preparation procedure for RH cellulose-based PC material, charge and discharge characteristics and cycle curves. Reproduced from ref. 304 with permission from Elsevier, copyright 2021. (c) Graphical drawing of the self-assembly procedure for the Si@CA@RH composite, the cross-linking process between CMC and CA, and a schematic of the chemical connections of RH, CA, Si and CMC. Reproduced from ref. 308 with permission from American Chemical Society, copyright 2020. | |
Today, the use of carbon materials to build new anodes is of great interest to researchers because these compounds have different advantages such as abundant pores, high specific surface areas, and stable features. Carbon-based anode materials have different pore sizes, corresponding to microporous < 2 nm, 2 nm < mesoporous < 50 nm and 50 nm < macroporous.302,303 For example, in a study in 2021, Liang and colleagues investigated the synthesis of RH-derived porous carbon materials (RH-PC and RH-HPC-x (x = 12, 24, 36)) as anodes for LIBs.304 For this aim, they used SiO2-derived RH as an eco-friendly source and applied it as a template for the preparation of porous hard carbon (HPC) compounds (Fig. 9b). Their results revealed that the synthesized material had an exclusive PC structure containing micropores, mesopores, and macropores. The porous carbon material hydrothermally treated for 24 h showed an excellent electrochemical performance. The discharging specific capacity of biomass hard carbon can reach 679.9 mA h g−1 after 100 cycles at a current density of 0.2 C. The charge and discharge characteristics and cycle curves are displayed in Fig. 9b. In another study, the preparation of N-enriched PC/SiO2 (SiO2/NC) composite derived from RH using ball milling was performed by Wang et al.305 They used the SiO2/NC composite as an anode for LIBs. In addition, they prepared optimum SiO2/NC composites using different N precursors, such as melamine and urea, and different N-D techniques, including dry and wet ball milling. The results showed that the optimum SiO2/NC composite was prepared using urea as the N precursor and the dry ball milling technique, which delivered a stable reversible capacity of 581 mA h g−1 at a high current loading of 1 A g−1 in the 1000th cycle.
Recently researchers developed the application of citric acid (CA) as a coating layer for the Si surface to avoid the uncontrollable growth of the solid electrolyte interface during cycling.306,307 Xu and co-workers developed a method for the preparation of a stable silicon/carbon anode composite.308 They enhanced the cycling performance and stability of the composite using CA. On the other hand, Si NPs encapsulated using CA could maintain the bond with the carbon structure through ester bonds (Fig. 9c). According to Fig. 9c, CA-coated Si particles were cross-linked with sodium carboxymethyl cellulose (CMC). In addition, the RH-derived carbon network was used for the structural stability of the electrode and facilitated the electronic conduction network. The Si@CA@RH electrode showed a stable capacity and high coulombic efficiency of 2126 mA h g−1 and 99.5% after 250 cycles, respectively; these values are very appropriate for high-performance LIBs.
Today, metal oxides can be applied as anode replacements for conventional carbon compounds due to some advantages such as a great theoretical capacity, cost-effectiveness, and exceptional Li storage mechanisms.309,310 One of the most promising metal oxides is zinc oxide, which is very appropriate for anode materials.311,312 In 2020, Liang and colleagues successfully carried out the preparation of efficient anode materials using flower-like ZnO, which was combined with hollow carbon derived from RH (RHC).313 The prepared ZnO/RHC composite was used as the anode for LIBs, which displayed exceptional electrochemical activity and cycling stability. The ZnO/RHC composite had a sheet structure containing ZnO, which was coated on the biomass carbon layer to make many conductive networks. The abovementioned structure improved the electrochemical performance of the ZnO/RHC composite. The ZnO/RHC composite had the highest specific capacity of 1002.5 mA h g−1 after 160 cycles at 0.2 C, which was much higher than the specific capacity of ZnO.
Graphene quantum dots (GQDs) are a member of the graphene family and their most important feature is their nanoscale dimensions.314 GQDs can be applied as modified compounds to improve the properties of raw materials. In 2020, Li et al. reported the synthesis of AC derived from RH, which was modified by GQDs.315 The prepared composite was applied as an electrode for LIBs and displayed a high electrochemical performance.
One of the most promising compounds for application in LIBs is tin oxide (SnO2). SnO2 has some advantages such as abundant accessibility and environmental friendliness. However, it has some problems such as vast volume changes and little conductivity.316–318 To solve these problems, Liang and colleagues investigated the preparation of an efficient SnO2@RH cellulose composite using SnO2 NPs and RH cellulose through a hydrothermal technique.319 For this aim, they encapsulated SnO2 NPs with RH cellulose, which promoted the conductivity of the SnO2 anodes. The synthesized composite was used as a promising anode for LIBs with an initial discharge capacity of 2090 mA h g−1 and high capacities of 930 and 587 mA h g−1 after 100 cycles at 0.2 C and 1 C, respectively.
One of the most abundant agricultural wastes is bagasse. Usually, it is burned, which is a waste of resources, and it produces air and environmental pollutants. Bagasse is a rich source of cellulose, lignin, and hemicellulose, which makes it an appropriate carbon source to prepare carbon electrodes that are applied for energy storage systems such as LIBs.320 In 2021, Qin and co-workers developed an efficient and cost-effective technique for the preparation of anode materials for LIBs using carbon derived from bagasse.320 They prepared N, P co-doped, bagasse-based, sheet-like mesoporous carbon (NP-BC) using NH4H2PO4 and bagasse as raw materials. Their results revealed that the NP-BC composite had a high electrochemical performance. In another study in the same year, Ramesha and colleagues investigated the preparation of low-cost and high-performance anodes for LIBs using multi-heteroatom co-doped carbon derived from bagasse [N, S, and O co-doped carbon (NSOC-10)] (Fig. 10).321 In addition, they reported the effect of HA doping on the carbon matrix and electrochemical features when applied in both Li-ion and Li–S batteries. The experimental results revealed that NSOC-10 had a capacity of 574 mA h g−1 even after 1000 cycles (Fig. 10), while the undoped carbon showed only 26.6% capacitance retention within 250 cycles.
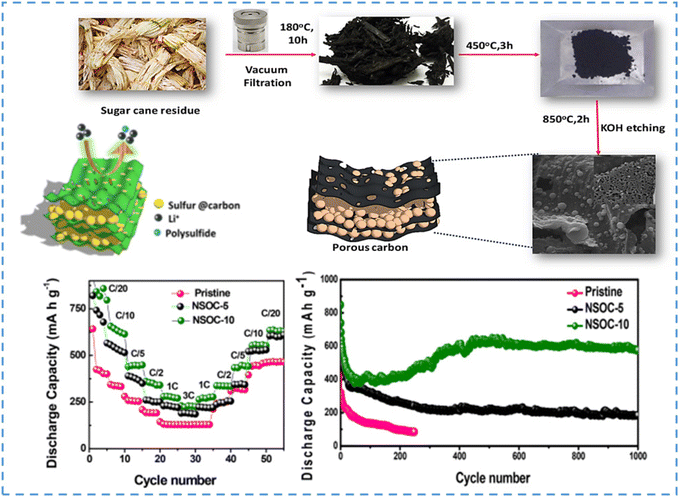 |
| Fig. 10 Schematic representation of the synthesis process for N, S, and O co-doped PC, discharge capacities at different rates, and cycling performance tests of pristine material, NSOC-5, and NSOC-10. Reproduced from ref. 321 with permission from American Chemical Society, copyright 2021. | |
In other work in 2019, Wan and Hu investigated the synthesis of N-D biomass-derived porous carbon (N/C) as an efficient anode for LIBs.322 For this aim, they used bagasse and melamine as C and N sources, respectively. The prepared N/C material had a 3D framework with a high specific surface area. The obtained N/C anode displayed a reversible special capacity of 530 mA h g−1 at 0.1 A g−1 after 100 cycles. In the same year, Zhu and co-workers reported the synthesis of carbon materials with a hierarchical porous structure derived from bagasse by a procedure comprised of a hydrothermal treatment with thiourea (for doping N and S atoms) and carbonization (Fig. 11).323 They showed that the structure of the prepared composite contained nanopores, supermicropores, and ultra-micropores and a large specific surface area (2419 m2 g−1). In addition, the application of thiourea led to the production of various papillae of a few hundred nanometers in diameter on the tubular wall. The composite can be applied as an electrode and anode in supercapacitors and LIBs, respectively. As a LIB anode, it showed a capacity of 621 mA h g−1 at 100 mA g−1.
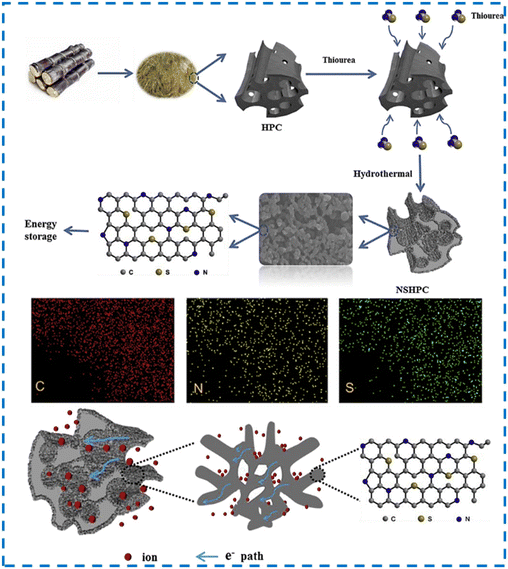 |
| Fig. 11 Schematic representation of the preparation process for the N–S doped hierarchical PC inherited from bagasse, EDS elemental mapping of doped hierarchical PC, and a schematic representation of transport paths for ions and electrons in the N–S doped hierarchical PC derived from bagasse. Reproduced from ref. 323 with permission from Elsevier, copyright 2019. | |
One of the agricultural wastes produced in large amounts is wheat straw, which is a cost-effective compound with many applications. One of the main constituents of wheat straw is cellulose.324 In a study in 2021, Liang and colleagues developed a method for the synthesis of efficient anode materials for LIBs using cellulose derived from wheat straw and nano-sized SnO2.324 For this purpose, they separated cellulose from wheat straw by chemical treatment and used it as a coating material for nano-sized SnO2 through a hydrothermal technique. Finally, they applied thiourea for doping N and S atoms (Fig. 12a). SnO2@wheat straw carbon (SnO2@WSC) was applied as an anode for LIBs with a specific discharge capacity (DC) of 1750 mA h g−1 in the first cycle. In another study in 2019, Yan et al. reported the fabrication of hierarchical PC from low-cost, novel, and abundant wheat straw (Fig. 12b).325 They used KOH as an activator and the prepared biomass carbon activated using KOH (KWSC) had a microstructure and was applied as the anode material of LIBs.
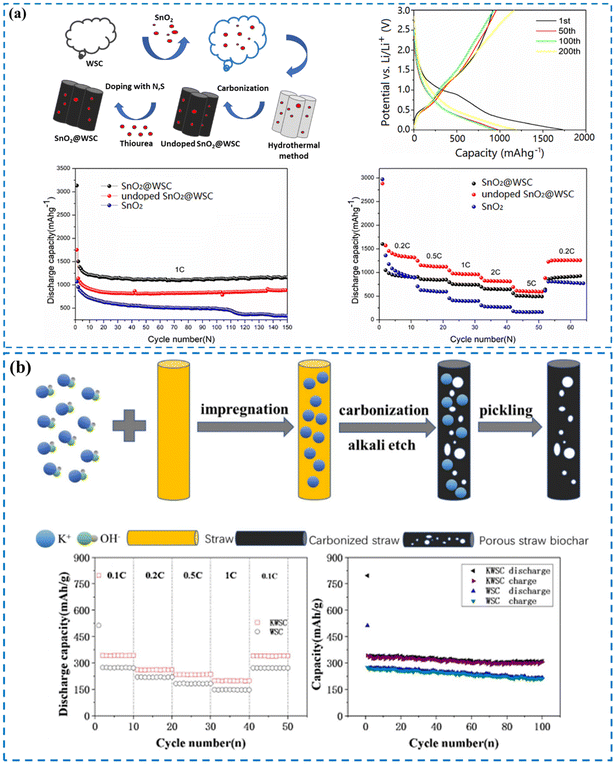 |
| Fig. 12 (a) Schematic representation of the method for the preparation of SnO2@WSC, charge/discharge profiles of SnO2@WSC, cycling performance, and rate performance of SnO2 and its composite material. Reproduced from ref. 324 with permission from Elsevier, copyright 2021. (b) Schematic representation of the method for the preparation of porous biomass carbon derived from wheat straw, charge–discharge cycling performances, and cycling capability of KWSC and WSC. Reproduced from ref. 325 with permission from Springer Nature, copyright 2019. | |
One of the most useful types of biomass is PP. It is applied as an exceptional compound for the preparation of hard carbon sheets, which have been broadly used as anodes for electrochemical applications, through carbonization. In addition, PP-derived carbon can be used as a substrate for the deposition of active compounds owing to its cost-effectiveness and good conductivity.326 In 2020, Zhang and colleagues reported the preparation of nanostructured NiCo2O4 supported on carbon sheets using a hydrothermal method following thermal treatment.327 Carbon materials are derived from the carbonization of PP. The prepared composite had some advantages such as a mesoporous structure and a large specific surface area. The composite could be applied as the anode of LIBs with a high reversible capacity of 473.7 mA h g−1 after 210 cycles at 500 mA g−1.
In 2020, Wang et al. investigated the application of AC derived from waste buttonwoods, pineapple peels, and lettuce leaves as anodes for LIBs.328 For this aim, they used KOH as an activator and then carbonized it through a high-temperature process. Their results indicated that the first discharge capacities of activated pineapple peels, buttonwoods, and lettuce leaves were 296.6, 313.9, and 674.5 mA h g−1 while the corresponding charging capacities were 129, 162.2, and 357.2 mA h g−1, respectively. In another example, the preparation of orange peel-derived hard carbon (OPDHC-A) was carried out by Xiang and co-workers.329 For this work, they prepared a microporous structure through the pyrolyzation of OP at 800 °C and activation by KOH. The synthesized compound, which showed an initial capacity of 878 mA h g−1 at 1 A g−1 and 497 mA h g−1 at 0.5 A g−1 when applied as anodes for LIBs and Na ion batteries (NIBs), respectively. The experimental results showed that 3000 and 1000 cycling stabilities were achieved at 2 and 1 A g−1 for LIBs and NIBs, respectively.
The most employed biowaste in LIB applications is RH due to the abundance of C and Si, which leads to good capacity in LIBs.300,301 Some research efforts have been made regarding the influence of preparation techniques on the performance of the final composite.305 Moreover, it was discovered that the modification of RH-derived carbon compounds with organic moieties,308 metal oxides,313,319 and GQDs315 led to improved stability, better capacity, and higher electrochemical performance. From a critical perspective, it seems that reaching sufficient activity, stability, and efficiency of biowaste-based LIBs needs further investigation.
Furthermore, there are many more examples of the utilization of carbon-derived agricultural wastes for LIB applications, which are summarized in Table S4.† According to Table S4,† the most widely used agricultural waste for battery applications is RH (entries 1–61). Most compounds prepared from RH are various carbon derivatives (activated and porous carbons) and silica since it is a rich source of carbon and silica. In addition, RH has been used as a reducing agent for making nanoparticles. Other waste used in large amounts in this table is bagasse (entries 62–76), from which carbon derivatives are prepared and used for batteries. Smaller amounts of different fruit peels are also used for LIB applications. This shows that the best agricultural wastes for battery applications are RH and bagasse, which are both rich sources of carbon, and RH is additionally the source of large quantities of silica. Moreover, this table shows that the main electrolyte used for battery applications is LiPF6 solution.
3.4.2 Li–O2 batteries.
Lithium–oxygen (Li–O2) batteries are a new generation of secondary batteries that have garnered significant attention due to their exceptionally high theoretical energy density.330,331 In the cathode of these batteries, the electrochemical reaction between Li+, O2−, and electrons occurs in addition to the deposition of discharge products.332 It is a very important issue to prepare an efficient cathode with an efficient electron transfer rate, Li+ transfer, and oxygen transmission. In 2019, Tsiakaras and co-workers developed an efficient and cost-effective method for the fabrication of 3D self-standing electrodes for Li–O2 batteries.332 For this aim, they prepared a 3D composite (NiFe@NC/PPC) based on NiFe@NC core–shell NPs highly dispersed on the self-standing N-doped carbon (NC) microtubule network (NiFe@NC/PPC), which was derived from NiFe-Prussian blue analogues/PP (NiFe-PBA/PP). In other words, they used PP and modified its surface using in situ-grown NiFe-PBA (Fig. 13a). The prepared NiFe@NC/PPC cathode combined the benefits of PPC (carbonized pomelo peel) and NiFe@NC (nickel-iron composite embedded in a nitrogen-doped carbon matrix) and exhibited a high specific capacitance of 13.79 mA h cm−2 over 290 cycles at a current density of 0.1 mA cm−2. Zhang and colleagues reported the application of citrus maxima peel (CMP) as a precursor for the synthesis of activated carbon (CMPACs) and Fe-loaded AC (CMPACs-Fe) (Fig. 13b).333 For this purpose, they used a pyrolysis method under an N2 atmosphere using KOH as an activator. The prepared CMPAC-based Li–O2 battery had a high cycling performance and specific capacitance of 466 cycles and 7800 mA h g−1, respectively. The two types of electrodes prepared showed high specific surface areas, porous structures, and many active sites.
 |
| Fig. 13 (a) Schematic representation of the preparation of NiFe@NC/PPC. Reproduced from ref. 332 with permission from Elsevier, copyright 2019. (b) Structures of the two kinds of electrodes (CMPACs and CMPACs-Fe). Reproduced from ref. 333 with permission from American Chemical Society, copyright 2018. | |
3.4.3 Li–S batteries.
Recently, rechargeable lithium–sulfur batteries (Li–SBs) have attracted much attention owing to their high theoretical specific capacity (1675 mA h g−1) and energy density (2600 W h kg−1).334,335 Additionally, the cathode materials of these batteries (elemental sulfur) are abundant in nature, inexpensive, and eco-friendly. Diverse kinds of compounds are used for the preparation of Li–SBs.336–338 Among them, agricultural wastes have been broadly reported.288,339,340 AC derived from agricultural waste is a suitable choice for electrochemical applications due to its electrochemical capacitive ability and high microporous volume.223,341,342 Tao and colleagues developed a type of multi-functional carbon-derived RH for optimizing the Li anode and sulfur cathode of Li–SBs.343 The carbon-derived RH had a large specific surface area and SiO2 NPs were useful for confining sulfur and sulfides. The experimental results revealed that the discharge capacity of the battery was improved when the Li metal anode was modified with a carbon/sulfur composite. In addition, the cycling stability and rate capability were improved. Yan et al. carried out the synthesis of banana peel-derived PC (BPPC) by pyrolysis carbonization using various amounts of KOH as an activator.344 In the next step, they loaded S and the synthesized S/C composite, which was used as a cathode for Li–SBs. They showed that when the KOH activation was increased, the specific surface area, as well as the pore volume of the BPPC and the electrochemical performance of composite cathode in Li–SBs, improved. In addition, the fabrication of porous nitrogen and boron dual-doped carbon aerogels derived from PP (NB-PPCA) was reported by Zhu and co-workers,345 who used a green and inexpensive approach for the preparation of a valuable and low-cost compound. The NB-PPCA material synthesized, which could reduce the interface resistance between the cathode and separator and thus improve the reaction kinetics of Li–SB, was applied as a coating on a pristine separator in Li–SBs. The cell configuration of the Li–S cell with PPCA or NB-PPCA modified separators is displayed in Fig. 14. The cell had a specific capacitance of 586.6 mA h g−1 after 500 cycles at 1 C and showed a good rate performance and cycling stability.
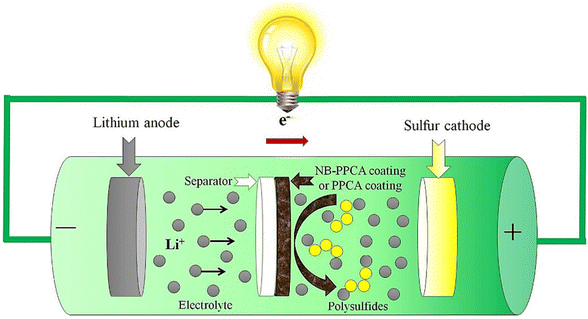 |
| Fig. 14 Schematic representation of the configuration of the Li–S cell for the PPCA or NB-PPCA modified separator. Reproduced from ref. 345 with permission from Elsevier, copyright 2019. | |
The preparation of highly porous AC compounds with micro- and mesoporosity through the carbonization of RH following treatment with K2CO3 was performed by Le and colleagues.346 In the next step, they loaded elemental S in the micropores via a solution infiltration technique to prepare RHAC@S composites. The prepared RHAC@S was used as the cathode for Li–SBs. With 0.25 mg cm−2 of S loading, the composite displayed an initial discharge capacity of 1080 mA h g−1 at a rate of 0.1 C. In another study, Tsiakaras and co-workers developed an efficient method for the preparation of porous biochar-coated metal NPs (CoFe@NC/PPC) through loading PBA on the PP as a carbon source, followed by calcination at a high temperature.347 In the next step, the immersion melting method was applied for the injection of S to prepare S/CoFe@NC/PPC. The prepared material was applied as an efficient sulfur cathode for Li–SBs and exhibited an initial specific capacity of 915.6 mA h g−1 at 1 C and remained at 447.4 mA h g−1 after 500 cycles with a coulombic efficiency of 97.3%.
Other examples in this field are summarized in Table S5.† According to the literature, the results indicate that bagasse and RH, two types of agricultural waste, are very important for LIBs, Li–SBs, and NIBs applications.97,153,348–355 Furthermore, it is important to note that in recent years, fruit peels have been used several times for LIB, Li–SB and NIB applications.356–362
3.5 Dye-sensitized solar cells
Dye-sensitized solar cells (DSSCs) are p–n junction photovoltaic devices.363–367 For the first time, it was found that electricity could be produced by illuminating organic dyes in electrochemical cells. The photoanode is organized by adsorbing a dye in a porous TiO2 layer. Therefore, the dye enables the production of electricity from visible light, extending the performance of the semiconductor to collect photons at lower energies.368–370 DSSCs contain a counter electrode, a metal oxide semiconductor, an electrolyte, and a dye sensitizer. There are some photosensitizers, such as ruthenium polypyridyl complex, with various limitations such as difficult synthesis processes, the presence of heavy metals, high costs, etc. There are some natural and green dyes in various wastes. These pigments include betanins, anthocyanins, chlorophyll, tannins, carotenoids, etc.371–378 For example, the extraction of natural dye from the husks, cobs, and silk of purple corn as efficient photosensitizers was performed by Swatsitang and co-workers.379 These natural dye sensitizers were used for the preparation of DSSCs. The results displayed maximal efficiency (1.06%) with purple corn husk extract. In another study, Yuliarto et al. used Citrus reticulata and Musa acuminata fruit peels as green and efficient photosensitizers for the preparation of DSSCs.380Fig. 15 demonstrates the photosensitization process of both hesperidin and gallocatechin dyes (which are flavonoids in Citrus reticulata and Musa acuminata pigment, respectively) under illumination. Their experimental results led to the longest diffusion length, the fastest electron transit, and the longest electron lifetime of 32.2 μm, 0.22 ms, and 4.29 ms, respectively. In addition, some studies used agro or fruit waste peels as natural dyes for DSSCs.381–385
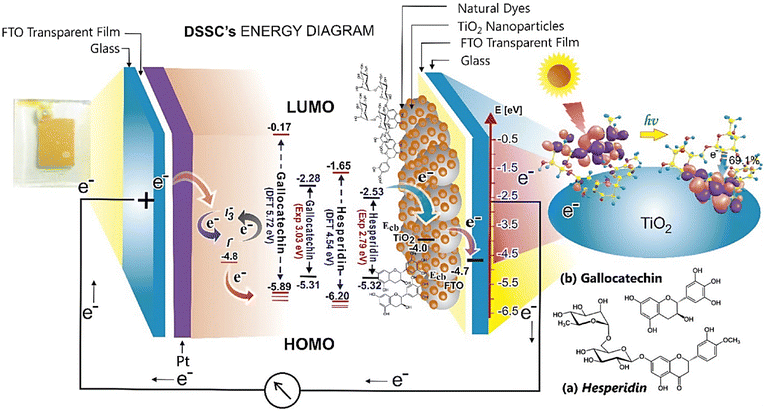 |
| Fig. 15 The natural DSSC structure and a representation of its reaction. Reproduced from ref. 380 with permission from Elsevier, copyright 2017. | |
In 2017, Xiang and colleagues developed a method for the synthesis of N-D bagasse-derived carbon/Pt composite (NBC/Pt) through an environmentally friendly hydrothermal process.386 They used bagasse as a carbon source and considered it as the counter electrode of DSSCs. The size of Pt NPs was reduced by N doping, which additionally resulted in better dispersion of Pt NPs on the carbon support. According to their results, under simulated AM 1.5 G solar illumination at 100 mW cm−2, the DSSCs with the NBC/Pt composite counter electrode displayed a power conversion efficiency of 6.98%. In 2022, Kathiravan and co-workers reported DSSCs containing peels of red banana and aloe vera leaf as dye sensitizers.387 They used acetone and ethanol solvents for the extraction of dyes from these peels. Indeed, they prepared DSSCs using extracted dyes and commercial TiO2 as a sensitizer and semiconductor oxide, respectively. A high efficiency of 0.679% was obtained using aloe vera peel extract and ethanol solvent.
Generally, according to the literature, most of the agricultural wastes applied for DSSCs are fruit peels.388–390 Some studies in which agricultural wastes have been used for DSSC preparation are summarized in Table S6.†
4. Conclusion and prospects
Recently, due to the deteriorating environment and the depletion of fossil energy, it has been promising to develop clean energy production and storage systems that utilize non-toxic and accessible sources. Numerous biowastes from agricultural resources are lost to landfill or disposal. The food industry uses fruits and discards peels and stones, or farmers consider rice the main crop and husk the side product. However, these second-class or side products can have extensive applications in various fields. The conversion of these biowastes into valuable chemicals could offer approaches for constructing sustainable energy conversion and storage systems.
Depending on outstanding properties such as low cost, accessibility, and natural abundance for agricultural waste-derived (carbon/nano)materials, these could be applied in energy conversion and storage. Therefore, this review mainly focuses on the performance of agricultural waste-derived (carbon/nano)materials for energy conversion and storage. Energy conversion involves FC electrodes and electrolytic water-splitting reactions, namely ORR, MOR, OER, and HER, and several applications and progress in this field were reviewed. Then, the application of agricultural wastes for energy storage has also been investigated. Energy storage devices include different types of batteries like LIBs, Li–O2, and Li–SBs, as well as supercapacitors and solar cell systems. Although graphite is used to make batteries, it does not fulfill human needs. Therefore, researchers utilized new combinations of agricultural wastes to prepare anodes for all kinds of batteries. Furthermore, the application of carbonaceous compounds to construct novel anodes is of great interest to researchers because these compounds possess different advantages such as abundant pores, high specific surface areas, and stable features. Carbons derived from agricultural waste could be applied as anodes for diverse types of batteries. Despite significant research in energy generation and storage from agricultural waste, several issues warrant further investigation:
• Using agricultural waste on an industrial scale for energy production and storage.
• Using agricultural waste in other electrocatalytic reactions such as EOR, CO2RR, NRR, etc.
• More use of this agricultural waste as substrates for the preparation of heterogeneous catalysts for electrocatalytic reactions or as anodes or cathodes for energy production devices.
• Controlling the size of pores in carbon compounds derived from agricultural waste.
• In the LIB application, most of the applied agricultural wastes are RH and bagasse. As a result, an area of further research for the future is the application of other waste, such as that from the peels of fruits and nuts, for battery applications.
Abbreviations
AC | Activated carbon |
AP | Aloe peel |
APPC | Aloe peel-derived porous carbon |
BCMs | Biochar microspheres |
BPPC | Banana peel-derived porous carbon |
CA | Citric acid |
CDs | Carbon dots |
CMC | Carboxymethyl cellulose |
CMP | Citrus maxima peel |
CNTs | Carbon nanotubes |
CO2RR | CO2 reduction reaction |
CPC | Commercial Pt/C |
3D | Three-dimensional |
DEC | Diethyl carbonate |
DMC | Dimethyl carbonate |
DMFC | Direct methanol fuel cell |
DSSCs | Dye-sensitized solar cells |
EC | Ethylene carbonate |
EMC | Ethyl methyl carbonate |
EOR | Ethanol oxidation reaction |
FCs | Fuel cells |
GQDs | Graphene quantum dots |
HER | Hydrogen evolution reaction |
HP-SN-PGC | Highly-porous metal-free nitrogen/sulfur co-doped partially-graphitized carbon |
LC | Lignin-derived carbon |
Li–O2 | Lithium–oxygen |
Li–SBs | Lithium–sulfur batteries |
LIBs | Lithium-ion batteries |
LSV | Linear scan voltammetry |
MFCs | Microbial fuel cells |
MOFs | Metal–organic frameworks |
MOR | Methanol oxidation reaction |
NB-PPCA | Nitrogen and boron dual-doped carbon aerogel derived from pomelo peel |
NBC/Pt | N-D bagasse-derived carbon/Pt composite |
N/C | N-D biomass-derived porous carbon |
N-PC | N-D porous carbon |
NC | N-Doped carbon |
NC/PPC | N-Doped carbon/carbonized pomelo peel |
NIBs | Na ion batteries |
NP-BC | N, P co-doped bagasse-based sheet-like mesoporous carbon |
NPC | N-D pomelo peel-derived carbon |
NPCNs | N, P doped PC nanosheets |
NPs | Nanoparticles |
NSOC | N, S, and O co-doped carbon |
NRR | Nitrogen reduction reaction |
OER | Oxygen evolution reaction |
OP | Orange peel |
ORR | Oxygen reduction reaction |
Ov | Overpotential |
PBA | Prussian blue analogues |
PC | Porous carbon |
PP | Pomelo peel |
PPC | Carbonized pomelo peel |
PPCA | Carbon aerogel derived from pomelo peel |
PPDC | Pomelo peel-derived porous carbon |
RHC | Rice husk-derived carbon |
RHE | Reversible hydrogen electrode |
RHs | Rice husks |
RS | Rice straw |
SC-MFCs | Single-chamber microbial fuel cells |
SiO2/NC | N-enriched PC/SiO2 |
SnO2 | Tin oxide |
SS | Soybean straw |
SSC | Symmetrical supercapacitor |
WHAC | Wheat husk-derived activated carbon |
WSC | Wheat straw carbon |
Data availability
No primary research results, software, or code have been included and no new data were generated or analysed as part of this review.
Conflicts of interest
There are no conflicts to declare.
Acknowledgements
Support from the Iranian Nano Council and the University of Qom are appreciated. The authors also acknowledge financial support from the “Belt and Road” Innovative Talents Exchange Foreign Experts Project of China (Grant No. DL2022026005L).
References
-
P. Prediger, T. de Figueiredo Neves, N. G. Camparotto and E. A. Rodrigues, Green Nanomaterials for Environmental Remediation, in Handbook of Green and Sustainable Nanotechnology, ed. U. Shanker, C. M. Hussain and M. Rani, Springer, Cham. 2023, pp. 1031–1064 Search PubMed.
-
S. Bano, S. Sultana, S. Sabir and M. Z. Khan, Advanced application of green materials in environmental remediation, in Applications of Advanced Green Materials, ed. S. Ahmed, Elsevier, 2021, pp. 481–502 Search PubMed.
- C. Xu, M. Nasrollahzadeh, M. Selva, Z. Issaabadi and R. Luque, Chem. Soc. Rev., 2019, 48(18), 4791–4822 RSC.
- K. Kumar, R. Kumar, S. Kaushal, N. Thakur, A. Umar, S. Akbar, A. A. Ibrahim and S. Baskoutas, Chemosphere, 2023, 345, 140419 CrossRef CAS PubMed.
- H. N. Hamad and S. Idrus, Polymers, 2022, 14(4), 783 CrossRef CAS PubMed.
- R. Chakraborty, K. Vilya, M. Pradhan and A. K. Nayak, J. Mater. Chem. A, 2022, 10, 6965–7005 RSC.
- L. Lu, W. Yu, Y. Wang, K. Zhang, X. Zhu, Y. Zhang, Y. Wu, H. Ullah, X. Xiao and B. Chen, Biochar, 2020, 2, 1–31 CrossRef.
- L. Ren, X. Kong, J. Su, D. Zhao, W. Dong, C. Liu, C. Liu, L. Luo and B. Yan, Bioresour. Technol., 2022, 346, 126578 CrossRef CAS PubMed.
- M. A. Yahya, Z. Al-Qodah and C. W. Zanariah Ngah, Renewable Sustainable Energy Rev., 2015, 46, 218–235 CrossRef CAS.
- E. Capanoglu, E. Nemli and F. Tomas-Barberan, J. Agric. Food Chem., 2022, 70(23), 6787–6804 CrossRef CAS PubMed.
-
F. A. Khan, A. Tomar, Y. K. Agarwal and H. O. Shukla, Agricultural Solid Waste Management: An Approach to Protect the Environment and Increase Agricultural Productivity. in Handbook of Solid Waste Management, ed. C. Baskar, S. Ramakrishna, S. Baskar, R. Sharma, A. Chinnappan and R. Sehrawat, Springer, Singapore, 2022, pp. 545–570 Search PubMed.
-
A. Barik, G. Rajhans, S. K. Sen and S. Raut, Agricultural Bio-wastes: A Potent Sustainable Adsorbent for Contaminant Removal, in Handbook of Solid Waste Management, ed. C. Baskar, S. Ramakrishna, S. Baskar, R. Sharma, A. Chinnappan and R. Sehrawat, Springer, Singapore, 2022, pp. 571–591 Search PubMed.
- X. Nqoro, R. Taziwa and P. Popoola, Biomass Convers. Biorefin., 2023 DOI:10.1007/s13399-023-05044-5.
- Y. W. Yap, N. Mahmed, M. N. Norizan, S. Z. Abd Rahim, M. N. A. Salimi, K. A. Razak, I. S. Mohamad, M. M. Al-Bakri Abdullah and M. Y. M. Yunus, Materials, 2023, 16(9), 3601 CrossRef CAS PubMed.
-
K. Senthilkumar, M. Naveen Kumar, V. Chitra Devi, K. Saravanan and S. Easwaramoorthi, Agro-Industrial Waste Valorization to Energy and Value Added Products for Environmental Sustainability. in Biomass Valorization to Bioenergy. Energy, Environment, and Sustainability, ed. R. Praveen Kumar, B. Bharathiraja, R. Kataki and V. Moholkar, Springer, Singapore, 2020, pp. 1–9 Search PubMed.
- H. Mahmood Khan, T. Iqbal, S. Yasin, C. Haider Ali, M. Mujtaba Abbas, M. Asif Jamil, A. Hussain, M. E. M. Soudagar and M. Muhitur Rahman, Catalysts, 2021, 11(10), 1215 CrossRef.
- J. A. Bennett, K. Wilson and A. F. Lee, J. Mater. Chem. A, 2016, 4, 3617–3637 RSC.
- H. M. Khan, T. Iqbal, S. Yasin, C. H. Ali, M. M. Abbas, M. A. Jamil, A. Hussain, M. E. M. Soudagar and M. M. Rahman, Catalysts, 2021, 11(10), 1215 CrossRef CAS.
- C. Maraveas, Polymers, 2020, 12(5), 1127 CrossRef CAS PubMed.
- P. K. Sadh, S. Duhan and J. S. Duhan, Bioresour. Bioprocess., 2018, 5, 1 CrossRef.
- V. Vaibhav, U. Vijayalakshmi and S. M. Roopan, Spectrochim. Acta, Part A, 2015, 139, 515–520 CrossRef CAS PubMed.
- K. S. Ukanwa, K. Patchigolla, R. Sakrabani, E. Anthony and S. Mandavgane, Sustainability, 2019, 11(22), 6204 CrossRef CAS.
- T. A. H. Nguyen, H. H. Ngo, W. S. Guo, J. Zhang, S. Liang, Q. Y. Yue, Q. Li and T. V. Nguyen, Bioresour. Technol., 2013, 148, 574–585 CrossRef CAS PubMed.
- A. Shahbaz, M. Ayaz, U. B. Khalid and L. Liaqat, Energy Sources, Part A, 2023, 45(1), 1464–1484 CrossRef CAS.
- M. Duque-Acevedo, L. J. Belmonte-Urena, F. J. Cortés-García and F. Camacho-Ferre, Glob. Ecol. Conserv., 2020, 22, e00902 Search PubMed.
- T. N.-D. Cao, H. Mukhtar, C.-P. Yu, X.-T. Bui and S.-Y. Pan, Renewable Sustainable Energy Rev., 2022, 170, 112965 CrossRef.
- O. Awogbemi and D. V. Von Kallon, Heliyon, 2022, 8(10), e11117 CrossRef CAS PubMed.
- A. P. Khedulkar, B. Pandit, V. D. Dang and R. Doong, Sci. Total Environ., 2023, 869, 161441 CrossRef CAS PubMed.
- H.-Y. Wu, S. S. Chen, W. Liao, W. Wang, M.-F. Jang, W.-H. Chen, T. Ahamad, S. M. Alshehri, C.-H. Hou, K.-S. Lin, T. Charinpanitkul and K. C.-W. Wu, Environ. Res., 2020, 191, 110176 CrossRef CAS PubMed.
- M. Radenković, J. Petrović, S. Pap, A. Kalijadis, M. Momčilović, N. Krstulović and S. Živković, Chemosphere, 2024, 347, 140684 CrossRef PubMed.
- M. M. Bade, A. A. Dubale, D. F. Bebizuh and M. Atlabachew, ACS Omega, 2022, 7(22), 18770–18779 CrossRef CAS PubMed.
- L. M. Reguengo, M. K. Salgaço, K. Sivieri and M. R. M. Júnior, Food Res. Int., 2022, 152, 110871 CrossRef CAS PubMed.
- E. Lizundia, F. Luzi and D. Puglia, Green Chem., 2022, 24, 5429–5459 RSC.
-
S. K. Malpani and D. Goyal, Green agricultural waste-derived silica nanoparticles as catalyst support materials. in Advances in Green and Sustainable Nanomaterials, ed. M. R. Goyal and S. Kulkarni, Taylor & Francis, 2023 Search PubMed.
- M. Kumar, S. Ambika, A. Hassani and P. V. Nidheesh, Sci. Total Environ., 2023, 858(Part 1), 159762 CrossRef CAS PubMed.
- E. A. Flores-Contreras, R. B. González-González, J. J. Pablo Pizaña-Aranda, L. Parra-Arroyo, A. A. Rodríguez-Aguayo, M. Iñiguez-Moreno, G. M. González-Meza, R. G. Araújo, D. Ramírez-Gamboa, R. Parra-Saldívar and E. M. Melchor-Martínez, Frontal Nanotechnol., 2024, 6, 1346069 CrossRef.
- P. C. Nath, A. Ojha, S. Debnath, M. Sharma, K. Sridhar, P. K. Nayak and B. S. Inbaraj, Agronomy, 2023, 13(2), 561 CrossRef CAS.
- S. Asaei and R. Norouzbeigi, Ceram. Int., 2021, 47(8), 11756–11768 CrossRef CAS.
- N. A. I. M. Ishak, S. K. Kamarudin, S. N. Timmiati, N. A. Karim and S. Basri, J. Adv. Res., 2021, 28, 63–75 CrossRef CAS PubMed.
- B. H. Thippeswamy, A. S. Maligi and G. Hegde, Catalysts, 2021, 11(12), 1485 CrossRef CAS.
- P. Manasa, S. Sambasivam and F. Ran, J. Energy Storage, 2022, 54, 105290 CrossRef.
- C. Briens, J. Piskorz and F. Berruti, Int. J. Chem. React. Eng., 2008, 6(1) DOI:10.2202/1542-6580.1674.
- M. Nasrollahzadeh, N. Shafiei, Z. Nezafat, N. S. Soheili Bidgoli, F. Soleimani and R. S. Varma, Chem. Rec., 2020, 20, 1338–1393 CrossRef CAS PubMed.
- S. Bala, D. Garg, K. Sridhar, B. S. Inbaraj, R. Singh, S. Kamma, M. Tripathi and M. Sharma, Bioengineering, 2023, 10(2), 152 CrossRef CAS PubMed.
- Z. Liu, T. S. P. de Souza, B. Holland, F. Dunshea, C. Barrow and H. A. R. Suleria, Processes, 2023, 11(3), 840 CrossRef CAS.
- I. Mármol, J. Quero, R. Ibarz, P. Ferreira-Santos, J. A. Teixeira, C. M. R. Rocha, M. Pérez-Fernández, S. García-Juiz, J. Osada, O. Martín-Belloso and M. J. Rodríguez-Yoldi, Food Bioprod. Process., 2021, 128, 247–258 CrossRef.
- K. Kumar, A. N. Yadav, V. Kumar, P. Vyas and H. S. Dhaliwal, Bioresour. Bioprocess., 2017, 4, 18 CrossRef.
- R. Kapoor, P. Ghosh, M. Kumar, S. Sengupta, A. Gupta, S. S. Kumar, V. Vijay, V. Kumar, V. K. Vijay and D. Pant, Bioresour. Technol., 2020, 304, 123036 CrossRef CAS PubMed.
- A. Pragati, S. Smriti, A. C. Kharkwal and V. Ajit, Int. J. Curr. Microbiol. Appl. Sci., 2015, 4(1), 470–477 Search PubMed.
- P. K. Swain, Mater. Today: Proc., 2017, 4(11 Part 3), 11959–11967 Search PubMed.
- D. Sud, G. Mahajan and M. P. Kaur, Bioresour. Technol., 2008, 99(14), 6017–6027 CrossRef CAS PubMed.
- M. A. Mohammed, A. Shitu, M. A. Tadda and M. Ngabura, Int. Res. J. Environ. Sci., 2014, 3(3), 62–71 CAS.
- K. S. Bharathi and S. T. Ramesh, Appl. Water Sci., 2013, 3, 773–790 CrossRef.
- Y. Dai, Q. Sun, W. Wang, L. Lu, M. Liu, J. Li, S. Yang, Y. Sun, K. Zhang, J. Xu, W. Zheng, Z. Hu, Y. Yang, Y. Gao, Y. Chen, X. Zhang, F. Gao and Y. Zhang, Chemosphere, 2018, 211, 235–253 CrossRef CAS PubMed.
- X. M. Guo, E. Trably, E. Latrille, H. Carrère and J.-P. Steyer, Int. J. Hydrogen Energy, 2010, 35(19), 10660–10673 CrossRef CAS.
- S. J. Kulkarni, N. L. Shinde and A. K. Goswami, Int. J. Sci. Res. Sci. Eng. Technol., 2015, 1(4), 231–233 Search PubMed.
- R. H. Hesas, W. M. A. W. Daud, J. N. Sahu and A. Arami-Niya, J. Anal. Appl. Pyrolysis, 2013, 100, 1–11 CrossRef.
- A. Demirbas, J. Hazard. Mater., 2009, 167(1–3), 1–9 CrossRef CAS PubMed.
- Z. Li, J.-Y. Fu, Y. Feng, C.-K. Dong, H. Liu and X.-W. Du, Nat. Catal., 2019, 2, 1107–1114 CrossRef CAS.
- S. Yun, N. Vlachopoulos, A. Qurashi, S. Ahmad and A. Hagfeldt, Chem. Soc. Rev., 2019, 48, 3705–3722 RSC.
- S. Yun, Y. Zhang, Q. Xu, J. Liu and Y. Qin, Nano Energy, 2019, 60, 600–619 CrossRef CAS.
-
E. Voegele
, EIA Updates 2023, 2024 Bioenergy Forecasts, Available online: https://biomassmagazine.com/articles/eia-updates-2023-2024-bioenergy-forecasts-19815 (accessed on 7 March 2023).
- Q. Wu, L. Yang, X. Wang and Z. Hu, Adv. Mater., 2020, 32(27), 1904177 CrossRef CAS PubMed.
- B. Jaleh, A. Nasri, M. Eslamipanah, M. Nasrollahzadeh, J. H. Advani, P. Fornasiero and M. B. Gawande, J. Mater. Chem. A, 2023, 11, 9333–9382 RSC.
- X. Wang, Z. Li, Y. Qu, T. Yuan, W. Wang, Y. Wu and Y. Li, Chem, 2019, 5(6), 1486–1511 CAS.
- A. Kulkarni, S. Siahrostami, A. Patel and J. K. Nørskov, Chem. Rev., 2018, 118(5), 2302–2312 CrossRef CAS PubMed.
- K. L. Hohn and Y. Lin, ChemSusChem, 2009, 2(10), 927–940 CrossRef CAS PubMed.
- S. G. Peera, C. Liu, J. Shim, A. K. Sahu, T. G. Lee, M. Selvaraj and R. Koutavarapu, Ceram. Int., 2021, 47(20), 28106–28121 CrossRef CAS.
- H.-F. Wang, L. Chen, H. Pang, S. Kaskel and Q. Xu, Chem. Soc. Rev., 2020, 49, 1414–1448 RSC.
- S. Sultan, J. N. Tiwari, A. N. Singh, S. Zhumagali, M. Ha, C. W. Myung, P. Thangavel and K. S. Kim, Adv. Energy Mater., 2019, 9(22), 1900624 CrossRef.
- S. Chandrasekaran, D. Ma, Y. Ge, L. Deng, C. Bowen, J. Roscow, Y. Zhang, Z. Lin, R. D. K. Misra, J. Li, P. Zhang and H. Zhang, Nano Energy, 2020, 77, 105080 CrossRef CAS.
- M.-Y. Lee, K. T. Park, W. Lee, H. Lim, Y. Kwon and S. Kang, Crit. Rev. Environ. Sci. Technol., 2020, 50(8), 769–815 CrossRef CAS.
- X. Zhao, G. Hu, G.-F. Chen, H. Zhang, S. Zhang and H. Wang, Adv. Mater., 2021, 33(33), 2007650 CrossRef CAS PubMed.
- H. Yuan, M. Wu, J. Zheng, Z.-G. Chen, W. Zhang, J. Luo, C. Jin, O. Sheng, C. Liang, Y. Gan, Y. Xia, J. Zhang, H. Huang, Y. Liu, J. Nai and X. Tao, Adv. Funct. Mater., 2019, 29(17), 1809051 CrossRef.
- H. Yang, H.-H. Wu, M. Ge, L. Li, Y. Yuan, Q. Yao, J. Chen, L. Xia, J. Zheng, Z. Chen, J. Duan, K. Kisslinger, X. C. Zeng, W.-K. Lee, Q. Zhang and J. Lu, Adv. Funct. Mater., 2019, 29(13), 1808825 CrossRef.
- X. Wang, S. Yun, W. Fang, C. Zhang, X. Liang, Z. Lei and Z. Liu, ACS Sustainable Chem. Eng., 2018, 6, 11397–11407 CrossRef CAS.
- Y. Deng, Y. Ji, H. Wu and F. Chen, Chem. Commun., 2019, 55, 1486–1489 RSC.
- A. González, E. McKeogh and B.Ó. Gallachóir, Renewable Energy, 2004, 29(4), 471–489 CrossRef.
- P. Kruger, Int. J. Hydrogen Energy, 2005, 30, 1515–1522 CrossRef CAS.
- M. Li, S. Ci, Y. Ding and Z. Wen, Sustainable Energy Fuels, 2019, 3, 3415–3421 RSC.
- X. Wu, Y. Qiao, Z. Shi and C. M. Li, Sustainable Energy Fuels, 2018, 2, 655–662 RSC.
- H. Tang, Y. Zeng, Y. Zeng, R. Wang, S. Cai, C. Liao, H. Cai, X. Lu and P. Tsiakaras, Appl. Catal., B, 2017, 202, 550–556 CrossRef CAS.
- Y. Hindatu, M. S. M. Annuar and A. M. Gumel, Renewable Sustainable Energy Rev., 2017, 73, 236–248 CrossRef CAS.
- J. R. Trapero, L. Horcajada, J. J. Linares and J. Lobato, Appl. Energy, 2017, 185(Part 1), 698–707 CrossRef CAS.
- Y. Zhang, H. Pan, Q. Zhou, K. Liu, W. Ma and S. Fan, Inorg. Chem. Commun., 2023, 153, 110768 CrossRef CAS.
- S. Zang, J. Jiang, Y. An, Z. Li, H. Guo, Y. Sun, H. Dou and X. Zhang, J. Electroanal. Chem., 2020, 876, 114723 CrossRef CAS.
- F. Yu, S. Li, W. Chen, T. Wu and C. Peng, Energy Environ. Mater., 2019, 2(1), 55–67 CrossRef CAS.
- Y.-L. Bai, C.-C. Zhang, F. Rong, Z.-X. Guo and K.-X. Wang, Chem. – Eur. J., 2024, 30(23), e202304157 CrossRef CAS PubMed.
- R. Vinodh, C. V. V. Muralee Gopi, V. G. R. Kummara, R. Atchudan, T. Ahamad, S. Sambasivam, M. Yi, I. M. Obaidat and H.-J. Kim, J. Energy Storage, 2020, 32, 101831 CrossRef.
- S. Wang, J. Dou, R. Holze, T. Zhang, L. Ye, L. Duan, J. Xue, S. Li and X. Chen, ChemElectroChem, 2023, 10(20), e202300223 CrossRef CAS.
- R. L. Shrestha, T. Shrestha, B. M. Tamrakar, R. G. Shrestha, S. Maji, K. Ariga and L. K. Shrestha, Materials, 2020, 13(10), 2371 CrossRef CAS PubMed.
- J. Yang, J. Peng, Y. Lei, Y. Tang, P. Liu, J. Zeng, C. Yi, Y. Shen, L. Zheng and X. Wang, ACS Appl. Energy Mater., 2024, 7(2), 469–478 CrossRef CAS.
- B. Li, H. Zhang and C. Zhang, RSC Adv., 2019, 9(50), 29190–29194 RSC.
- D. Vučurović, B. Bajić, Z. Trivunović, J. Dodić, M. Zeljko, R. Jevtić-Mučibabić and S. Dodić, Foods, 2024, 13(5), 711 CrossRef PubMed.
- B. Li, H. Zhang, D. Wang, H. Lv and C. Zhang, RSC Adv., 2017, 7, 37923–37928 RSC.
- H. Krishnamoorthy, R. Ramyea, A. Maruthu, K. Kandasamy, M. Michalska and S. K. Kandasamy, Bioresour. Technol. Rep., 2022, 19, 101187 CrossRef CAS.
- Mohit and S. A. Hashmi, J. Energy Storage, 2024, 83, 110694 CrossRef.
- N. P. Rumjit, P. Thomas, C. W. Lai, Y. H. Wong, V. George, P. Basilraj and M. R. B. Johan, Encycl. Energy Storage, 2022, 4, 382–397 CrossRef.
- S. E. Kayode and F. J. González, J. Compos. Sci., 2023, 7(3), 127 CrossRef CAS.
- I. S. Ismail, M. F. H. Othman, N. A. Rashidi and S. Yusup, Biomass Convers. Biorefin., 2023, 13, 14341–14357 CrossRef CAS PubMed.
- Sonu, G. M. Rani, D. Pathania, Abhimanyu, R. Umapathi, S. Rustagi, Y. S. Huh, V. K. Gupta, A. Kaushik and V. Chaudhary, Sci. Total Environ., 2023, 875, 162667 CrossRef CAS PubMed.
- C. Yan, X. Jiang, J. Yu, Z. Ding, L. Ma, T. Su, Y. Wang, C. Wang, G. Huang and S. Xu, Green Chem., 2023, 25, 3816–3846 RSC.
- S. G. Krishnan, A. Arulraj, P. Jagadish, M. Khalid, M. Nasrollahzadeh, R. Fen, C. C. Yang and G. Hegde, Crit. Rev. Solid State Mater. Sci., 2023, 48(1), 1–56 CrossRef CAS.
- X. Liu, X. Chen, L. Yang, H. Chen, Y. Tian and Z. Wang, Res. Chem. Intermed., 2016, 42, 893–913 CrossRef CAS.
- M. Amran, R. Fediuk, G. Murali, N. Vatin, M. Karelina, T. Ozbakkaloglu, R. S. Krishna, A. K. Sahoo, S. K. Das and J. Mishra, Crystals, 2021, 11(2), 168 CrossRef CAS.
- M. Kordi, N. Farrokhi, M. I. Pech-Canul and A. Ahmadikhah, Ric. Sci., 2023, 31(1), 14–32 CrossRef.
- J. R. Fu, L. X. Zhu, X. T. Sun, D. H. Zhou, L. J. Ouyang, J. M. Bian, H. H. He and J. Xu, Genet. Mol. Res., 2015, 14(4), 17739–17748 CrossRef CAS PubMed.
- Q. Feng, Q. Lin, F. Gong, S. Sugita and M. Shoya, J. Colloid Interface Sci., 2004, 278(1), 1–8 CrossRef CAS PubMed.
-
Y. Zou and T. Yang, Chapter 9 - Rice husk, rice husk ash and their applications, Rice Bran and Rice Bran Oil, Elsevier, 2019, pp. 207–246 Search PubMed.
-
S. H. Ali, M. Y. Emran and H. Gomaa, Rice Husk-Derived Nanomaterials for Potential Applications, in Waste Recycling Technologies for Nanomaterials Manufacturing. Topics in Mining, Metallurgy and Materials Engineering, ed. A. S. H. Makhlouf and G. A. M. Ali, Springer, Cham, 2021, pp. 541–588 Search PubMed.
- Y. Shen, P. Zhao and Q. Shao, Microporous Mesoporous Mater., 2014, 188, 46–76 CrossRef CAS.
- P. U. Nzereogu, A. D. Omah, F. I. Ezema, E. I. Iwuoha and A. C. Nwanya, Hybrid Adv., 2023, 4, 100111 CrossRef.
- A. Rodriguez-Otero, V. Vargas, A. Galarneau, J. Castillo, J. H. Christensen and B. Bouyssiere, Processes, 2023, 11(12), 3373 CrossRef CAS.
- S. Steven, E. Restiawaty and Y. Bindar, Renewable Sustainable Energy Rev., 2021, 149, 111329 CrossRef CAS.
- Z. Wu, Z. Meng, C. Yao, Y. Deng, G. Zhang and Y. Wang, Mater. Chem. Phys., 2022, 275, 125246 CrossRef CAS.
- Z. Shamsollahi and A. Partovinia, J. Environ. Manage., 2019, 246, 314–323 CrossRef CAS PubMed.
- F. Adam, J. N. Appaturi and A. Iqbal, Catal. Today, 2012, 190(1), 2–14 CrossRef CAS.
- L. A. Silva, I. F. S. dos Santos, G. de Oliveira Machado, G. L. Tiago Filho and R. M. Barros, J. Cleaner Prod., 2021, 290, 125188 CrossRef.
- K.-T. Chen, J.-X. Wang, Y.-M. Dai, P.-H. Wang, C.-Y. Liou, C.-W. Nien, J.-S. Wu and C.-C. Chen, J. Taiwan Inst. Chem. Eng., 2013, 44(4), 622–629 CrossRef CAS.
- M. S. Yerdauletov, K. Nazarov, B. Mukhametuly, M. A. Yeleuov, C. Daulbayev, R. Abdulkarimova, A. Yskakov, F. Napolskiy and V. Krivchenko, Molecules, 2023, 28(15), 5818 CrossRef CAS PubMed.
- O. F. Abraham, V. S. Aigbodion, E. C. Ejiogu and U. C. Ogbuefi, Diamond Relat. Mater., 2022, 123, 108885 CrossRef CAS.
- S.-S. Huang, M. T. Tung, C. D. Huynh, B.-J. Hwang, P. M. Bieker and C.-C. Fang, ACS Sustainable Chem. Eng., 2019, 7(8), 7851–7861 CrossRef CAS.
- H. Kumar, K. Bhardwaj, R. Sharma, E. Nepovimova, K. Kuča, D. S. Dhanjal, R. Verma, P. Bhardwaj, S. Sharma and D. Kumar, Molecules, 2020, 25(12), 2812 CrossRef CAS PubMed.
- S. N. Joglekar, P. D. Pathak, S. A. Mandavgane and B. D. Kulkarni, Environ. Sci. Pollut. Res., 2019, 26, 34713–34722 CrossRef PubMed.
- M. Lucarini, A. Durazzo, R. Bernini, M. Campo, C. Vita, E. B. Souto, G. Lombardi-Boccia, M. F. Ramadan, A. Santini and A. Romani, Molecules, 2021, 26(21), 6338 CrossRef CAS PubMed.
- A. J. Antonisamy, S. Marimuthu, S. Malayandi, K. Rajendran, Y.-C. Lin, G. Andaluri, S. L. Lee and V. K. Ponnusamy, Environ. Res., 2023, 217, 114758 CrossRef PubMed.
- S. O. Dahunsi, S. Oranusi and V. E. Efeovbokhan, J. Cleaner Prod., 2017, 156, 19–29 CrossRef CAS.
- J. T. Casabar, Y. Unpaprom and R. Ramaraj, Biomass Convers. Biorefin., 2019, 9, 761–765 CrossRef CAS.
- B. Singh, J. P. Singh, A. Kaur and N. Singh, Int. J. Food Sci. Technol., 2019, 54(4), 959–965 CrossRef CAS.
- M. Saleem and M. T. Saeed, J. King Saud Univ. Sci., 2020, 32(1), 805–810 CrossRef.
- R. Suhag, R. Kumar, A. Dhiman, A. Sharma, P. K. Prabhakar, K. Gopalakrishnan, R. Kumar and A. Singh, Crit. Rev. Food Sci. Nutr., 2023, 63(24), 6757–6776 CrossRef CAS PubMed.
- R. Taslim, I. B. Pasaribu, N. Yanti, A. Apriwandi and E. Taer, Mater. Today: Proc., 2023, 87(Part 2), 18–24 CAS.
- J. R. Rajabathar, S. Manoharan, J. Vijaya J, H. A. Al-Lohedan and P. Arunachalam, J. Energy Storage, 2020, 32, 101735 CrossRef.
- S. Fu, M. Li, S. Asperti, W. de Jong and R. Kortlever, ChemSusChem, 2023, 16(9), e202202188 CrossRef CAS PubMed.
- L. A. September, N. Kheswa, N. S. Seroka and L. Khotseng, RSC Adv., 2023, 13, 1370–1380 RSC.
- A. M. Shabbirahmed, D. Haldar, P. Dey, A. K. Patel, R. R. Singhania, C.-D. Dong and M. K. Purkait, Environ. Sci. Pollut. Res., 2022, 29, 62785–62806 CrossRef CAS PubMed.
- Y. R. Loh, D. Sujan, M. E. Rahman and C. A. Das, Resour., Conserv. Recycl., 2023, 75, 14–22 CrossRef.
- W.-Y. Lou, Q. Guo, W.-J. Chen, M.-H. Zong, H. Wu and T. J. Smith, ChemSusChem, 2012, 5(8), 1533–1541 CrossRef CAS PubMed.
- C. T. Hiranobe, A. S. Gomes, F. F. G. Paiva, G. R. Tolosa, L. L. Paim, G. Dognani, G. P. Cardim, H. P. Cardim, R. J. dos Santos and F. C. Cabrera, Clean Technol., 2024, 6(2), 662–699 CrossRef.
- M. R. Trejo-Hernandez, A. Ortiz, A. I. Okoh, D. Morales and R. Quintero, Chemosphere, 2007, 68(5), 848–855 CrossRef CAS PubMed.
- P. Barciela, A. Perez-Vazquez, M. Fraga-Corral and M. A. Prieto, Processes, 2023, 11(11), 3116 CrossRef CAS.
- S. Sarkar, A. Arya, U. K. Gaur and A. Gaur, Biomass Bioenergy, 2020, 142, 105730 CrossRef CAS.
- L. Wannasen, N. Chanlek, S. Siriroj, S. Maensiri, E. Swatsitang and S. Pinitsoontorn, Nanomaterials, 2022, 12(20), 3555 CrossRef CAS PubMed.
- K. O. Iwuozor, E. C. Emenike, J. O. Ighalo, F. O. Omoarukhe, P. E. Omuku and A. G. Adeniyi, Cleaner Mater., 2022, 100162 CrossRef CAS.
- M. A. Mahmuda and F. R. Anannya, Heliyon, 2021, 7(8), e07771 CrossRef PubMed.
- F. Antunes, I. F. Mota, J. da Silva Burgal, M. Pintado and P. S. Costa, Biomass Bioenergy, 2022, 166, 106603 CrossRef CAS.
- S. Al Arni, Ind. Crops Prod., 2018, 115, 330–339 CrossRef.
- N. Y. Nguyen-Thi, C. Q. Nguyen, Q. L. Dang, Q. D. Tran, T. N. Do-Thia and L. H. Vu Thanh, RSC Adv., 2024, 14, 4533–4542 RSC.
- W. Somyanonthanakun, A. Greszta, A. J. Roberts and S. Thongmee, Sustainability, 2023, 15(6), 5566 CrossRef CAS.
- Mohit, N. Yadav and S. A. Hashmi, J. Energy Storage, 2022, 55(Part A), 105421 CrossRef.
- S. Sutthasupa, W. Koo-amornpattana, N. Worasuwannarak, P. Prachakittikul, P. Teachawachirasiri, W. Wanthong, T. Thungthong, P. Inthapat, W. Chanamarn, C. Thawonbundit, A. Srifa, S. Ratchahat and W. Chaiwat, Int. J. Biol. Macromol., 2023, 253(Part 7), 127464 CrossRef CAS PubMed.
- B. Du, L. Chai, H. Zhu, J. Cheng, X. Wang, X. Chen, J. Zhou and R.-C. Sun, Int. J. Biol. Macromol., 2021, 184, 604–617 CrossRef CAS PubMed.
- K. Pongpanyanate, S. Roddecha, C. Piyanirund, T. Phraewphiphatd and P. Hasin, RSC Adv., 2024, 14, 2354–2368 RSC.
- N. A. I. Md Ishak, S. K. Kamarudin, S. N. Timmiati, S. M. Sauid, N. A. Karim and S. Basri, J. Cleaner Prod., 2023, 382, 135111 CrossRef CAS.
- N. Sazali, W. N. W. Salleh, A. S. Jamaludin and M. N. M. Razali, Membranes, 2020, 10(5), 99 CrossRef CAS PubMed.
- B. Jaleh, M. Nasrollahzadeh, M. Eslamipanah, A. Nasri, E. Shabanlou, N. R. Manwar, R. Zboril, P. Fornasiero and M. B. Gawande, Carbon, 2022, 198, 301–352 CrossRef CAS.
- W. Zhang, S. Yi, Y. Yu, H. Liu, A. Kucernak, J. Wu and S. Li, J. Mater. Chem. A, 2024, 12, 87–112 RSC.
- Y. Zhao, D. P. A. Saseendran, C. Huang, C. A. Triana, W. R. Marks, H. Chen, H. Zhao and G. R. Patzke, Chem. Rev., 2023, 123(9), 6257–6358 CrossRef CAS PubMed.
- Z. Xiao, Y. Wu, S. Cao, W. Yan, B. Chen, T. Xing, Z. Li, X. Lu, Y. Chen, K. Wang and J. Jiang, Chem. Eng. J., 2021, 413, 127395 CrossRef CAS.
- Z. Liang, H.-Y. Wang, H. Zheng, W. Zhang and R. Cao, Chem. Soc. Rev., 2021, 50, 2540–2581 RSC.
- R. Hao, J. Chen, Z. Wang, Y. Huang, P. Liu, J. Yan, K. Liu, C. Liu and Z. Lu, J. Colloid Interface Sci., 2021, 586, 621–629 CrossRef CAS PubMed.
- F. Wang, Q. Li, Z. Xiao, B. Jiang, J. Ren, Z. Jin, X. Tang, Y. Chen and X. Li, J. Colloid Interface Sci., 2022, 606(Part 2), 1014–1023 CrossRef CAS PubMed.
- Y. Zhou, L. Yan and J. Hou, Molecules, 2022, 27(1), 328 CrossRef CAS PubMed.
- S. Li, S.-H. Ho, T. Hua, Q. Zhou, F. Li and J. Tang, Green Energy Environ., 2021, 6(5), 644–659 CrossRef CAS.
- G. Lu, Z. Li, W. Fan, M. Wang, S. Yang, J. Li, Z. Chang, H. Sun, S. Liang and Z. Liu, RSC Adv., 2019, 9, 4843–4848 RSC.
- M. Dhelipan, A. Arunchander, A. K. Sahu and D. Kalpana, J. Saudi Chem. Soc., 2017, 21(4), 487–494 CrossRef CAS.
- Z. A. Sandhu, M. A. Raza, N. S. Awwad, H. A. Ibrahium, U. Farwa, S. Ashraf, A. Dildar, E. Fatima, S. Ashraf and F. Ali, Mater. Adv., 2024, 5, 30–50 RSC.
- V. F. Yusuf, N. I. Malek and S. Kumar Kailasa, ACS Omega, 2022, 7(49), 44507–44531 CrossRef CAS PubMed.
- H. Wang, F.-X. Yin, B.-H. Chen, X.-B. He, P.-L. Lv, C.-Y. Ye and D.-J. Liu, Appl. Catal., B, 2017, 205, 55–67 CrossRef CAS.
- B.-A. Lu, N. Tian and S.-G. Sun, Curr. Opin. Electrochem., 2017, 4(1), 76–82 CrossRef CAS.
- A. Dessalle, J. Quílez-Bermejo, V. Fierro, F. Xu and A. Celzard, Carbon, 2023, 203, 237–260 CrossRef CAS.
- A. Liu, M. Ma, X. Zhang, J. Ming, L. Jiang, Y. Li, Y. Zhang and S. Liu, J. Electroanal. Chem., 2018, 824, 60–66 CrossRef CAS.
- S. Y. Sawant, T. H. Han and M. H. Cho, Int. J. Mol. Sci., 2017, 18(1), 25 CrossRef PubMed.
- Y. Jiao, Y. Hu, L. Han and M. Zhou, Electroanalysis, 2020, 32(12), 2969–2975 CrossRef CAS.
- J. Shi, N. Lin, H.-B. Lin, J. Yang and W.-L. Zhang, New Carbon Mater., 2020, 35(4), 401–409 CrossRef CAS.
- Y. Zhang, L. Deng, H. Hu, Y. Qiao, H. Yuan, D. Chen, M. Chang and H. Wei, Sustainable Energy Fuels, 2020, 4, 1642–1653 RSC.
- Y. Shen, F. Peng, Y. Cao, J. Zuo, H. Wang and H. Yu, J. Energy Chem., 2019, 34, 33–42 CrossRef.
- Y. Ma, S. You, B. Jing, Z. Xing, H. Chen, Y. Dai, C. Zhang, N. Ren and J. Zou, Int. J. Hydrogen Energy, 2019, 44(31), 16624–16638 CrossRef CAS.
- W.-Y. Xie, C. Ling, Z.-Y. Huang, W.-C. Chen, S.-F. He, L.-P. Si and H.-Y. Liu, Int. J. Hydrogen Energy, 2024, 51(Part A), 857–868 CrossRef CAS.
- H. Jin, L. Zhou, G. Zha, P. Huang, F. Wang, S. Li, M. Jianga and C. Liu, Sustainable Energy Fuels, 2023, 7, 4525–4532 RSC.
- L. Zhang, Z. Shen, X. Lu, X. Jiao and G. He, Mater. Lett., 2023, 341, 134237 CrossRef CAS.
- M. N. Ansari, S. Sarrouf, M. F. Ehsan, S. Manzoor, M. N. Ashiq and A. N. Alshawabkeh, Electrochim. Acta, 2023, 453, 142351 CrossRef CAS PubMed.
- G. Wang, W. Wang, Y. Chen, C. Yan and Z. Gao, Appl. Surf. Sci., 2023, 610, 155456 CrossRef CAS.
- F. Achmad, S. K. Kamarudin, W. R. W. Daud and E. H. Majlan, Appl. Energy, 2011, 88(5), 1681–1689 CrossRef.
- S. S. Mahapatra, A. Dutta and J. Datta, Int. J. Hydrogen Energy, 2011, 36(22), 14873–14883 CrossRef CAS.
- N. A. I. M. Ishak, S. K. Kamarudin, S. N. Timmiati, N. Karim and S. Basri, Int. J. Energy Res., 2021, 45(5), 7380–7403 CrossRef.
- B. Tang, Y. Lin, Z. Xing, Y. Duan, S. Pan, Y. Dai, J. Yu and J. Zou, Electrochim. Acta, 2017, 246, 517–527 CrossRef CAS.
- N. A. I. M. Ishak, S. K. Kamarudin, S. N. Timmiati, S. Basri and N. A. Karim, Mater. Today: Proc., 2021, 42(Part 1), 138–147 CAS.
- N. A. Karim, N. J. Rubinsin, M. A. A. Burukan and S. K. Kamarudin, Int. J. Green Energy, 2019, 16(15), 1518–1526 CrossRef CAS.
- N. S. Hassan, A. A. Jalil, S. Rajendran, N. F. Khusnun, M. B. Bahari, A. Johari, M. J. Kamaruddin and M. Ismail, Int. J. Hydrogen Energy, 2024, 52(Part B), 420–441 CrossRef CAS.
- Z. P. Ifkovits, J. M. Evans, M. C. Meier, K. M. Papadantonakis and N. S. Lewis, Energy Environ. Sci., 2021, 14, 4740–4759 RSC.
- B. You and Y. Sun, Acc. Chem. Res., 2018, 51(7), 1571–1580 CrossRef CAS PubMed.
- J. Wang, L. Ji, X. Teng, Y. Liu, L. Guo and Z. Chen, J. Mater. Chem. A, 2019, 7, 13149–13153 RSC.
- J. Corbin, M. Jones, C. Lyu, A. Loh, Z. Zhang, Y. Zhu and X. Li, RSC Adv., 2024, 14, 6416–6442 RSC.
- Z.-L. Wang, D. Xu, J.-J. Xu and X.-B. Zhang, Chem. Soc. Rev., 2014, 43, 7746–7786 RSC.
- J. Mohammed-Ibrahim, J. Power Sources, 2020, 448, 227375 CrossRef CAS.
- Z. Feng, C. Dai, Z. Zhang, X. Lei, W. Mu, R. Guo, X. Liu and J. You, J. Energy Chem., 2024, 93, 322–344 CrossRef CAS.
- S. K. Guchhait, D. Sutradhar, R. Nandi and A. K. Sarma, Energy Sources, Part A, 2023, 45(2), 5957–5969 CrossRef CAS.
- S. Park, J. Kim and K. Kwon, Chem. Eng. J., 2022, 446(Part 1), 137116 CrossRef CAS.
- H. A. Bandal, A. A. Pawar and H. Kim, Electrochim. Acta, 2022, 422, 140545 CrossRef CAS.
- Y. Meng, G. Ni, X. Jin, J. Peng and Q. Y. Yan, Mater. Today Nano, 2020, 12, 100095 CrossRef.
- Y. Zhang, J. Wu, B. Guo, H. Huo, S. Niu, S. Li and P. Xu, Carbon Energy, 2023, 5(12), e375 CrossRef CAS.
- G. Givirovskiy, V. Ruuskanen, T. Väkiparta and J. Ahola, Mater. Today Energy, 2020, 17, 100426 CrossRef.
- W. Chen, H. Yu, S. Chang, W. Li, R. Liu, Y. Wang, H. Zhang and Z. Zhang, Appl. Surf. Sci., 2022, 573, 151486 CrossRef CAS.
- M. A. A. Mahbub, C. G. Adios, M. Xu, B. Prakoso, J. M. LeBeau and A. Sumboja, Chem. – Asian J., 2021, 16(17), 2559–2567 CrossRef CAS PubMed.
- J. Wang, F. Xu, H. Jin, Y. Chen and Y. Wang, Adv. Mater., 2017, 29(14), 1605838 CrossRef PubMed.
- Q. Wang, R. Guo, Z. Wang, D. Shen, R. Yu, K. Luo, C. Wu and S. Gu, Fuel, 2021, 293, 120440 CrossRef CAS.
- O. A. Fakayode, B. A. Yusuf, C. Zhou, Y. Xu, Q. Ji, J. Xie and H. Ma, Energy Convers. Manage., 2021, 227, 113628 CrossRef.
- H. Xiang, Q. Dong, M. Yangc and S. Liu, Mater. Chem. Front., 2024, 8, 1888–1926 RSC.
- S. J. Yoon, S. J. Lee, M. H. Kim, H. A. Park, H. S. Kang, S.-Y. Bae and I.-Y. Jeon, Nanomaterials, 2023, 13(18), 2613 CrossRef CAS PubMed.
- S. Min, Y. Duan, Y. Li and F. Wang, Renewable Energy, 2020, 155, 447–455 CrossRef CAS.
- S. Yun, J. Shi, Y. Si, M. Sun, Y. Zhang, A. Arshad and C. Yang, J. Colloid Interface Sci., 2021, 601, 12–29 CrossRef CAS PubMed.
- C. Sathiskumar, S. Ramakrishnan, M. Vinothkannan, A. Rhan Kim, S. Karthikeyan and D. J. Yoo, Nanomaterials, 2020, 10(1), 76 CrossRef CAS PubMed.
- Y. Li, J. Zhang, Q. Chen, X. Xia and M. Chen, Adv. Mater., 2021, 33(27), 2100855 CrossRef CAS PubMed.
- Y. Liu, G. Li, L. Huan and S. Cao, Nanoscale, 2024, 16, 504–526 RSC.
- J. Zhang, M. Gu and X. Chen, Micro Nano Eng., 2023, 21, 100229 CrossRef.
- E. S. Greenhalgh, S. Nguyen, M. Valkova, N. Shirshova, M. S. P. Shaffer and A. R. J. Kucernak, Compos. Sci. Technol., 2023, 235, 109968 CrossRef CAS.
- B. Ren, M. Fan, X. Yang, L. Wang and H. Yu, ChemistrySelect, 2019, 4(19), 5641–5650 CrossRef CAS.
- H. Gou, J. He, G. Zhao, L. Zhang, C. Yang and H. Rao, Ionics, 2019, 25, 4371–4380 CrossRef CAS.
- X. He, P. Ling, J. Qiu, M. Yu, X. Zhang, C. Yu and M. Zheng, J. Power Sources, 2013, 240, 109–113 CrossRef CAS.
- F. Chen, Y. Ji, Y. Deng, F. Ren, S. Tan and Z. Wang, J. Mater. Sci., 2020, 55(25), 11512–11523 CrossRef CAS.
- L. Peng, Y. Liang, J. Huang, L. Xing, H. Hu, Y. Xiao, H. Dong, Y. Liu and M. Zheng, ACS Sustainable Chem. Eng., 2019, 7(12), 10393–10402 CrossRef CAS.
- K. Chen and D. Xue, Chin. J. Chem., 2017, 35(6), 861–866 CrossRef CAS.
- C. Ramirez-Castro, C. Schütter, S. Passerini and A. Balducci, Electrochim. Acta, 2016, 206, 452–457 CrossRef CAS.
- H. Wei, H. Wang, A. Li, H. Li, D. Cui, M. Dong, J. Lin, J. Fan, J. Zhang, H. Hou, Y. Shi, D. Zhou and Z. Guo, J. Alloys Compd., 2020, 820, 153111 CrossRef CAS.
- H. Yang, H. Lin, C. Yang, H. Hu, H. Dong, Y. Liu, X. Liu, J. Cui and Y. Xiao, J. Energy Storage, 2024, 83, 110688 CrossRef.
- A. P. Khedulkar, V. D. Dang, A. Thamilselvan, R.-A. Doong and B. Pandit, J. Energy Storage, 2024, 77, 109723 CrossRef.
- Q. Yang, J. Guo, S. Zhang, W. Wang, X. Zhang, J. He and Y. Xu, Ind. Crops Prod., 2024, 209, 118060 CrossRef CAS.
- Y. Wang, L. Wang and X. Lu, Materials, 2023, 16(13), 4577 CrossRef CAS PubMed.
- T. Subramaniam, S. G. Krishnan, M. N. M. Ansari, N. A. Hamid and M. Khalid, Crit. Rev. Solid State Mater. Sci., 2023, 48(2), 289–331 CrossRef CAS.
- H. Lin, Y. Liu, Z. Chang, S. Yan, S. Liu and S. Han, Microporous Mesoporous Mater., 2020, 292, 109707 CrossRef CAS.
- V. S. Bhat, P. Kanagavalli, G. Sriram, R. Prabhu B, N. S. John, M. Veerapandian, M. Kurkuri and G. Hegde, J. Energy Storage, 2020, 32, 101829 CrossRef.
- H. S. AlSalem, K. M. S. Katubi, M. S. Binkadem, S. T. Al-Goul and A. M. Wahba, ACS Omega, 2023, 8(43), 40808–40816 CrossRef CAS PubMed.
- Y.-P. Zhao, R.-X. Xu, J.-P. Cao, X.-Y. Zhang, J.-S. Zhu and X.-Y. Wei, J. Electroanal. Chem., 2020, 871, 114288 CrossRef CAS.
- A. Zekenova, M. Nazhipkyzy, W. Li, A. Kalybayeva, G. Zhumanova and O. Zubova, Inorganics, 2022, 10(10), 160 CrossRef CAS.
- H. Jin, S. Wu, T. Li, Y. Bai, X. Wang, H. Zhang, H. Xu, C. Kong and H. Wang, Appl. Surf. Sci., 2019, 488, 593–599 CrossRef CAS.
- J. Chen, Y. Lin, J. Liu, D. Wu, X. Bai, D. Chen and H. Li, J. Energy Storage, 2021, 39, 102640 CrossRef.
- D. Chinnadurai, H.-J. Kim, S. Karupannan and K. Prabakar, New J. Chem., 2019, 43, 3486–3492 RSC.
- H. Xu, L. Wang, Y. Zhang, Y. Chen and S. Gao, Nanoscale, 2021, 13, 10051–10060 RSC.
- Z. Yang, W. Xu, M. Zhao, W. Yang, J. Xia, Z. Zhou, J. Song, L. Sheng and B. Wei, Chem. Commun., 2020, 56, 15561–15564 RSC.
- E. Elanthamilan, B. C. Meena, N. Renuka, M. Santhiya, J. George, E. P. Kanimozhi, J. C. Ezhilarasi and J. Princy Merlin, J. Electroanal. Chem., 2021, 901, 115762 CrossRef CAS.
- T.-M. Chou and J.-L. Hong, Ionics, 2020, 26, 1419–1429 CrossRef CAS.
- M. Pulikkottil, H. Antony, M. N. Muralidharan, E. V. Gopalan and S. Ansari, ChemistrySelect, 2022, 7(23), e202200984 CrossRef CAS.
- V. Yang, R. A. Senthil, J. Pan, T. R. Kumar, Y. Sun and X. Liu, J. Colloid Interface Sci., 2020, 579, 347–356 CrossRef CAS PubMed.
- Z. Chen, X. Wang, B. Xue, W. Li, Z. Ding, X. Yang, J. Qiu and Z. Wang, Carbon, 2020, 161, 432–444 CrossRef CAS.
- S. Xiao, J. Huang, C. Lin, A. Xie, B. Lin, L. He and D. Sun, Microporous Mesoporous Mater., 2020, 291, 109709 CrossRef CAS.
- H. Jin, J. Hu, S. Wu, X. Wang, H. Zhang, H. Xu and K. Lian, J. Power Sources, 2018, 384, 270–277 CrossRef CAS.
- L. Zhu, F. Shen, R. L. Smith Jr, L. Yan, L. Li and X. Qi, Chem. Eng. J., 2017, 316, 770–777 CrossRef CAS.
- W. Du, Z. Zhang, L. Du, X. Fan, Z. Shen, X. Ren, Y. Zhao, C. Wei and S. Wei, J. Alloys Compd., 2019, 797, 1031–1040 CrossRef CAS.
- W. Liu, J. Mei, G. Liu, Q. Kou, T. Yi and S. Xiao, ACS Sustainable Chem. Eng., 2018, 6(9), 11595–11605 CrossRef CAS.
- M. U. Rani, K. Nanaji, T. N. Rao and A. S. Deshpande, J. Power Sources, 2020, 471, 228387 CrossRef.
- S. Song, F. Ma, G. Wu, D. Ma, W. Geng and J. Wan, J. Mater. Chem. A, 2015, 3, 18154–18162 RSC.
- D. Liu, Y. Wang, B. Jia, J. Wei, C. Liu, J. Zhu, S. Tang, Z. Wu and G. Chen, ACS Omega, 2020, 5(40), 26084–26093 CrossRef CAS PubMed.
- H. Ma, Z. Chen, X. Wang, Z. Liu and X. Liu, J. Renewable Sustainable Energy, 2019, 11(2), 24102 CrossRef.
- T. Liu, H. Zhou, Y. Lan, C. Qiu, G. Du and X. Su, Diamond Relat. Mater., 2021, 116, 108375 CrossRef CAS.
- Y.-N. Li, D. Xu, M. Zhang, Q. Qin, M. Song, J. Zhou, Z. Chen, C. Teng and G. Ren, J. Electroanal. Chem., 2021, 901, 115781 CrossRef CAS.
- B. Wang, L. Ji, Y. Yu, N. Wang, J. Wang and J. Zhao, Electrochim. Acta, 2019, 309, 34–43 CrossRef CAS.
- J. Qu, C. Geng, S. Lv, G. Shao, S. Ma and M. Wu, Electrochim. Acta, 2015, 176, 982–988 CrossRef CAS.
- K. S. Lee, I. Phiri, C. W. Park, S. Kim and J. M. Ko, J. Colloid Interface Sci., 2021, 592, 42–50 CrossRef CAS PubMed.
- N. R. Kim, Y. S. Yun, M. Y. Song, S. J. Hong, M. Kang, C. Leal, Y. W. Park and H.-J. Jin, ACS Appl. Mater. Interfaces, 2016, 8(5), 3175–3181 CrossRef CAS PubMed.
- Z. Liu, Q. Yang, L. Cao, S. Li, X. Zeng, W. Zhou and C. Zhang, Molecules, 2023, 28(11), 4429 CrossRef CAS PubMed.
- M. D. Mehare, A. D. Deshmukh and S. J. Dhoble, J. Mater. Sci.: Mater. Electron., 2021, 32, 14057–14071 CrossRef CAS.
- G. Li, Y. Li, X. Chen, X. Hou, H. Lin and L. Jia, J. Colloid Interface Sci., 2022, 605, 71–81 CrossRef CAS PubMed.
- D. Xu, Y. Su, S. Zhang and Y. Xiong, Energy Sources, Part A, 2020, 42(14), 1797–1807 CrossRef CAS.
- H. G. Kim, Y.-S. Kim, L. K. Kwac and H. K. Shin, Molecules, 2020, 25(17), 3951 CrossRef CAS PubMed.
- G. A. M. Ali, S. Supriya, K. F. Chong, E. R. Shaaban, H. Algarni, T. Maiyalagan and G. Hegde, Biomass Convers. Biorefin., 2021, 11, 1311–1323 CrossRef CAS.
- M. D. Mehare, A. D. Deshmukh and S. J. Dhoble, J. Mater. Sci., 2020, 55, 4213–4224 CrossRef CAS.
- N. M. Musyoka, B. K. Mutuma and N. Manyala, RSC Adv., 2020, 10, 26928–26936 RSC.
- S. Chaudhary, R. Mohan and O. P. Sinha, Appl. Phys. A, 2020, 126, 806 CrossRef CAS.
- S. Sundriyal, V. Shrivastav, H. D. Pham, S. Mishra, A. Deep and D. P. Dubal, Resour., Conserv. Recycl., 2021, 169, 105548 CrossRef CAS.
- K. Subramani, N. Sudhan, M. Karnan and M. Sathish, ChemistrySelect, 2017, 2(35), 11384–11392 CrossRef CAS.
- A. M. Abioye and F. N. Ani, Renewable Sustainable Energy Rev., 2015, 52, 1282–1293 CrossRef CAS.
- K. M. Ajay, M. N. Dinesh, G. Byatarayappa, M. G. Radhika, N. Kathyayini and H. Vijeth, Inorg. Chem. Commun., 2021, 127, 108523 CrossRef CAS.
- S. Vinoth, K. Subramani, W.-J. Ong, M. Sathish and A. Pandikumar, J. Colloid Interface Sci., 2021, 584, 204–215 CrossRef CAS PubMed.
- H. Wu, Z. Wei, J. Yin, S. Jiang, J. Wu, S. Zheng, J. He, X. Xu and Y. Gao, Electrochim. Acta, 2021, 386, 138445 CrossRef CAS.
- B. Xue, X. Wang, Y. Feng, Z. Chen and X. Liu, J. Energy Storage, 2020, 30, 101405 CrossRef.
- M. M. Baig and I. H. Gul, Biomass Bioenergy, 2021, 144, 105909 CrossRef CAS.
- M. M. Baig and I. H. Gul, J. Energy Storage, 2021, 37, 102477 CrossRef.
- M. Xu, Q. Huang, J. Lu and J. Niu, Ind. Crops Prod., 2021, 161, 113215 CrossRef CAS.
- T. Jorn-Am, J. Praneerad, R. Attajak, N. Sirisit, J. Manyam and P. Paoprasert, Colloids Surf., A, 2021, 628, 127239 CrossRef CAS.
- V. C. Hoang and V. G. Gomes, Mater. Today Energy, 2019, 12, 198–207 CrossRef.
- Y. Li, L. Zhu, J. Shi, Y. Dou, S. Li, R. You, S. Zhang, X. Miao, S. Shi, H. Ji and G. Yang, Appl. Surf. Sci., 2021, 561, 150076 CrossRef CAS.
- Z. Qiu, Y. Wang, X. Bi, T. Zhou, J. Zhou, J. Zhao, Z. Miao, W. Yi, P. Fu and S. Zhuo, J. Power Sources, 2018, 376, 82–90 CrossRef CAS.
- M. A. Islam, H. L. Ong, A. R. Villagracia, K. A. A. Halim, A. B. Ganganboina and R.-A. Doong, Ind. Crops Prod., 2021, 170, 113694 CrossRef CAS.
- X. Zheng, M. Chen, Y. Ma, X. Dong, F. Xi and J. Liu, J. Solid State Electrochem., 2017, 21(12), 3449–3458 CrossRef CAS.
- H. Liu, F. Zhang, Z. Wu, E. Cui, L. Yue, G. Hou and L. Wang, Energy Fuels, 2021, 35(12), 10190–10198 CrossRef CAS.
- Y. Song, J. Liu, K. Sun and W. Xu, RSC Adv., 2017, 7, 48324–48332 RSC.
- Y. Zhang, Z. Gao, N. Song and X. Li, Electrochim. Acta, 2016, 222, 1257–1266 CrossRef CAS.
- P. Sennu, V. Aravindan and Y.-S. Lee, J. Power Sources, 2016, 306, 248–257 CrossRef CAS.
- W. Guo, T. Hua, C. Qiao, Y. Zou, Y. Wang and J. Sun, Energy Storage Mater., 2024, 66, 103244 CrossRef.
- P. Molaiyan, G. Simões, D. Reis, D. Karuppiah, C. M. Subramaniyam, F. García-Alvarado and U. Lassi, Batteries, 2023, 9(2), 116 CrossRef CAS.
- X. Hu, W. Zhang, X. Liu, Y. Mei and Y. Huang, Chem. Soc. Rev., 2015, 44, 2376–2404 RSC.
- T. L. Kulova, Russ. J. Electrochem., 2013, 49, 1–25 CrossRef CAS.
- C. Zhang, S. Chou, Z. Guo and S.-X. Dou, Adv. Funct. Mater., 2024, 34(5), 2308001 CrossRef CAS.
- A. Zanoletti, E. Carena, C. Ferrara and E. Bontempi, Batteries, 2024, 10(1), 38 CrossRef CAS.
- M. Nanthagopal, D. Mouraliraman, Y.-R. Han, C. W. Ho, J. Obregon, J.-Y. Jung and C. W. Lee, Nanomaterials, 2023, 13(22), 2963 CrossRef CAS PubMed.
- N. Tran, Q. T. H. Ta and V. V. Tran, Int. J. Energy Res., 2022, 46(10), 13251–13275 CrossRef CAS.
- S. Wang, N. Zhao, C. Shi, E. Liu, C. He, F. He and L. Ma, Appl. Surf. Sci., 2018, 433, 428–436 CrossRef CAS.
- T. Kesavan and M. Sasidharan, ACS Sustainable Chem. Eng., 2019, 7(14), 12160–12169 CAS.
- L. Dawei, Z. Xiaoxiao, W. Yu, Z. Peijie, Z. Li, Z. Zongbo, G. Xin, Q. Yingyun, L. Guixia and T. Yuanyu, J. Alloys Compd., 2021, 854, 156986 CrossRef.
- J. Cui, Y. Qiu, H. Zhang, Z. Yao, W. Zhao, Y. Liu and J. Sun, Solid State Ionics, 2021, 361, 115548 CrossRef CAS.
- M. E. Davis, Nature, 2002, 417, 813–821 CrossRef CAS PubMed.
- J. Lee, J. Kim and T. Hyeon, Adv. Mater., 2006, 18(16), 2073–2094 CrossRef CAS.
- J. Hou, X. Mao, J. Wang, C. Liang and J. Liang, Chem. Phys., 2021, 551, 111352 CrossRef CAS.
- Y. Feng, L. Liu, X. Liu, Y. Li, Y. Wu, Y. Zhu and X. Wang, Chem. – Eur. J., 2021, 27(41), 10749–10757 CrossRef CAS PubMed.
- C. C. Nguyen, D. M. Seo, K. W. D. K. Chandrasiri and B. L. Lucht, Langmuir, 2017, 33(37), 9254–9261 CrossRef CAS PubMed.
- K. W. D. K. Chandrasiri, C. C. Nguyen, B. S. Parimalam, S. Jurng and B. L. Lucht, J. Electrochem. Soc., 2018, 165(10), A1991–A1996 CrossRef CAS.
- Y. Wang, X. Wang, H. Jin, Y. Bai and H. Xu, Sustainable Energy Fuels, 2020, 4, 2583–2592 RSC.
- J. Du, Q. Li, J. Chai, L. Jiang, Q. Zhang, N. Han, W. Zhang and B. Tang, Dalton Trans., 2022, 51, 9584–9590 RSC.
- K. Ullah, N. Shah, R. Wadood, B. M. Khan and W. C. Oh, NanoTrends, 2023, 1, 100004 Search PubMed.
- H. Köse, Ş. Karaal, A. O. Aydın and H. Akbulut, J. Power Sources, 2015, 295, 235–245 CrossRef.
- C. Xiao, S. Zhang, S. Wang, Y. Xing, R. Lin, X. Wei and W. Wang, Electrochim. Acta, 2016, 189, 245–251 CrossRef CAS.
- Y. Li, Y. Huang, X. Wang, W. Liu, K. Yu and C. Liang, J. Phys. Chem. Solids, 2020, 145, 109540 CrossRef CAS.
- P. He, J. Sun, S. Tian, S. Yang, S. Ding, G. Ding, X. Xie and M. Jiang, Chem. Mater., 2015, 27(1), 218–226 CrossRef CAS.
- Y. Li, F. Wu, X. Jin, H. Xu, X. Liu and G. Shi, Inorg. Chem. Commun., 2020, 112, 107718 CrossRef CAS.
- C. Gu, H. Zhang, X. Wang and J. Tu, Mater. Res. Bull., 2013, 48(10), 4112–4117 CrossRef CAS.
- F. Li, J. Du, H. Yang, W. Shi and P. Cheng, RSC Adv., 2017, 7, 20062–20067 RSC.
- X. W. Lou, Y. Wang, C. Yuan, J. Y. Lee and L. A. Archer, Adv. Mater., 2006, 18(17), 2325–2329 CrossRef CAS.
- Z. Hu, X. Xu, X. Wang, K. Yu, J. Hou and C. Liang, New J. Chem., 2019, 43, 8755–8760 RSC.
- S. Zheng, Y. Luo, K. Zhang, H. Liu, G. Hu and A. Qin, Mater. Lett., 2021, 290, 129459 CrossRef CAS.
- D. Bosubabu, R. Sampathkumar, G. Karkera and K. Ramesha, Energy Fuels, 2021, 35(9), 8286–8294 CrossRef CAS.
- H. Wan and X. Hu, Solid State Ionics, 2019, 341, 115030 CrossRef CAS.
- R. Luan, D. Xu, H. Pan, C. Zhu, D. Wang, X. Meng, Y. Li, M. Imtiaz, S. Zhu and J. Ma, J. Energy Storage, 2019, 22, 60–67 CrossRef.
- J. Liang, P. Bai, K. Yu and C. Liang, Diamond Relat. Mater., 2021, 112, 108231 CrossRef CAS.
- P. Yan, F. Ai, C. Cao and Z. Luo, J. Mater. Sci.: Mater. Electron., 2019, 30, 14120–14129 CrossRef CAS.
- Z. Wang, Y. Tan, Y. Yang, X. Zhao, Y. Liu, L. Niu, B. Tichnell, L. Kong, L. Kang, Z. Liu and F. Ran, J. Power Sources, 2018, 378, 499–510 CrossRef CAS.
- C. Zhang, Z. Xie, W. Yang, Y. Liang, D. Meng, X. He, P. Liang and Z. Zhang, J. Power Sources, 2020, 451, 227761 CrossRef CAS.
- J. Miao, C. Zhang, Q. Wang, H. Tian, Y. Zhang, Z. Zhang, Y. Guo and M. Ma, J. Mater. Sci.: Mater. Electron., 2020, 31(10), 7766–7775 CrossRef CAS.
- J. Xiang, W. Lv, C. Mu, J. Zhao and B. Wang, J. Alloys Compd., 2017, 701, 870–874 CrossRef CAS.
- W.-J. Kwak, Rosy, D. Sharon, C. Xia, H. Kim, L. R. Johnson, P. G. Bruce, L. F. Nazar, Y.-K. Sun, A. A. Frimer, M. Noked, S. A. Freunberger and D. Aurbach, Chem. Rev., 2020, 120(14), 6626–6683 CrossRef CAS PubMed.
- S. Pakseresht, M. Celik, A. Guler, A. W. M. Al-Ogaili and T. Kallio, Batteries, 2023, 9(7), 380 CrossRef CAS.
- S. Jing, Y. Zhang, F. Chen, H. Liang, S. Yin and P. Tsiakaras, Appl. Catal., B, 2019, 245, 721–732 CrossRef CAS.
- D. Li, Q. Wang, Y. Yao, F. Wu, Y. Yu and C. Zhang, ACS Appl. Mater. Interfaces, 2018, 10(38), 32058–32066 CrossRef CAS PubMed.
- X. Zhao, C. Wang, Z. Li, X. Hu, A. A. Razzaqab and Z. Deng, J. Mater. Chem. A, 2021, 9, 19282–19297 RSC.
- R. Fang, K. Chen, Z. Sun, G. Hu, D.-W. Wang and F. Li, Interdiscip. Mater., 2023, 2(5), 761–770 Search PubMed.
- Y. Guo, Q. Niu, F. Pei, Q. Wang, Y. Zhang, L. Du, Y. Zhang, Y. Zhang, Y. Zhang, L. Fan, Q. Zhang, L. Yuan and Y. Huang, Energy Environ. Sci., 2024, 17, 1330–1367 RSC.
- R. Mori, J. Solid State Electrochem., 2023, 27, 813–839 CrossRef CAS.
- H. Pan, Z. Cheng, P. He and H. Zhou, Energy Fuels, 2020, 34(10), 11942–11961 CrossRef CAS.
- Y. Cheng, S. Ji, X. Xu and J. Liu, RSC Adv., 2015, 5, 100089–100096 RSC.
- M. K. Rybarczyk, H.-J. Peng, C. Tang, M. Lieder, Q. Zhang and M.-M. Titirici, Green Chem., 2016, 18, 5169–5179 RSC.
- D.-L. Vu, J.-S. Seo, H.-Y. Lee and J.-W. Lee, RSC Adv., 2017, 7, 4144–4151 RSC.
- M. Xue, C. Chen, Z. Ren, Y. Tan, B. Li and C. Zhang, Mater. Lett., 2017, 209, 594–597 CrossRef CAS.
- C. Jin, O. Sheng, W. Zhang, J. Luo, H. Yuan, T. Yang, H. Huang, Y. Gan, Y. Xia, C. Liang, J. Zhang and X. Tao, Energy Storage Mater., 2018, 15, 218–225 CrossRef.
- Y. Yan, Y. Wei, Q. Li, M. Shi, C. Zhao, L. Chen, C. Fan, R. Yang and Y. Xu, J. Mater. Sci.: Mater. Electron., 2018, 29, 11325–11335 CrossRef CAS.
- L. Zhu, H. Jiang, W. Ran, L. You, S. Yao, X. Shen and F. Tu, Appl. Surf. Sci., 2019, 489, 154–164 CrossRef CAS.
- T.-T. Mai, D.-L. Vu, D.-C. Huynh, N.-L. Wu and A.-T. Le, J. Sci.: Adv. Mater. Devices, 2019, 4(2), 223–229 Search PubMed.
- S. Jing, P. Ding, Y. Zhang, H. Liang, S. Yin and P. Tsiakaras, Ionics, 2019, 25(11), 5297–5304 CrossRef CAS.
- L. E. Arvizu-Rodríguez, M. Olvera-Sosa, J. A. Arcibar-Orozco, L. F. Chazaro-Ruiz, R. Rangel-Mendez and M. Avalos-Borja, Energy Technol., 2024, 12(1), 2300743 CrossRef.
- B. Verma, H. Raj, H. Rajput and A. Sil, Ionics, 2023, 29, 5205–5216 CrossRef CAS.
- H. Lin, J. Yang, P. Feng, G. Liu, J. Cui, X. Liu and Y. Xiao, Energy Fuels, 2023, 37(15), 11342–11354 CrossRef CAS.
- Z. Hu, G. Su, S. Long, X. Zhang, L. Zhang, Y. Chen, C. Zhang and G. Liu, Environ. Res., 2024, 245, 118078 CrossRef CAS PubMed.
- N. Ratsameetammajak, T. Autthawong, K. Khunpakdee, M. Haruta, T. Chairuangsri and T. Sarakonsri, Polymers, 2023, 15(24), 4638 CrossRef CAS PubMed.
- Z. Zhao, M. Cai, Y. Zhao, H. Xie, Y. X. Zhuang and H. Yin, ACS Appl. Nano Mater., 2023, 6(1), 502–511 CrossRef CAS.
- F. Ahmed, G. Almutairi, P. M. Z. Hasan, S. Rehman, S. Kumar, N. M. Shaalan, A. Aljaafari, A. Alshoaibi, B. AlOtaibi and K. Khan, Micromachines, 2023, 14(1), 192 CrossRef PubMed.
- P. C. Rath, J. Patra, H.-T. Huang, D. Bresser, T.-Y. Wu and J.-K. Chang, ChemSusChem, 2019, 12(10), 2302–2309 CrossRef CAS PubMed.
- Y. Wei, Q. Wang, Q. Liu, R. Wang, Y. Wang, S. Luo, Y. Zhang, P. Hou, S. Yan, X. Liu and J. Guo, Appl. Surf. Sci., 2024, 648, 159017 CrossRef CAS.
- A. Pundir and A. Sil, Biomass Bioenergy, 2024, 180, 106999 CrossRef CAS.
- M. Ndour, J.-P. Bonnet, S. Cavalaglio, T. Lombard, J. Safran, C. Pau-Roblotc and V. Bonnet, New J. Chem., 2023, 47, 17499–17507 RSC.
- N. Nieto, O. Noya, A. Iturrondobeitia, P. Sanchez-Fontecoba, U. Pérez-López, V. Palomares, A. Lopez-Urionabarrenechea and T. Rojo, Batteries, 2022, 8(4), 28 CrossRef CAS.
- L. Shang, R. Yuan, H. Liu, X. Li, B. Zhao, X. Liu, A. Li, X. Chen and H. Song, Carbon, 2024, 223, 119038 CrossRef CAS.
- R. Muruganantham, F.-M. Wang and W.-R. Liu, Electrochim. Acta, 2022, 424, 140573 CrossRef CAS.
- F. Luna-Lama, J. Morales and A. Caballero, Materials, 2021, 14(20), 5995 CrossRef CAS PubMed.
- S. Wrede, B. Cai, F. Cheng, M. B. Johansson, T. Kubart, C. Hägglundc and H. Tian, Sustainable Energy Fuels, 2024, 8, 1004–1011 RSC.
- M. K. Nazeeruddin, E. Baranoff and M. Grätzel, Sol. Energy, 2011, 85(6), 1172–1178 CrossRef CAS.
- A. Sen, M. Hamidi Putra, A. K. Biswas, A. K. Behera and A. Groβ, Dyes Pigm., 2023, 213, 111087 CrossRef CAS.
- H. Alessa and K. G. U. Wijayantha, J. Umm Al-Qura Univ. Appll. Sci., 2024 DOI:10.1007/s43994-024-00136-y.
- J. Barichello, P. Mariani, L. Vesce, D. Spadaro, I. Citro, F. Matteocci, A. Bartolotta, A. D. Carlo and G. Calogero, J. Mater. Chem. C, 2024, 12, 2317–2349 RSC.
- G. Calogero and G. Di Marco, Sol. Energy Mater. Sol. Cells, 2008, 92(11), 1341–1346 CrossRef CAS.
- K. Sharma, V. Sharma and S. S. Sharma, Nanoscale Res. Lett., 2018, 13, 381 CrossRef PubMed.
- G. Wang, D. Wang, S. Kuang, W. Xing and S. Zhuo, Renewable Energy, 2014, 63, 708–714 CrossRef CAS.
- L. Csoka, D. Dudić, I. Petronijević, C. Rozsa, K. Halasz and V. Djoković, Cellulose, 2015, 22, 779–788 CrossRef CAS.
- G. Richhariya, A. Kumar, P. Tekasakul and B. Gupta, Renewable Sustainable Energy Rev., 2017, 69, 705–718 CrossRef CAS.
- S. Ananth, T. Arumanayagam, P. Vivek and P. Murugakoothan, J. Mater. Sci.: Mater. Electron., 2016, 27(1), 146–153 CrossRef CAS.
- M. A. M. Escobar and F. Jaramillo, J. Renewable Mater., 2015, 3(4), 281–291 CrossRef CAS.
- N. I. A. Shukor, K.-Y. Chan, G. S. H. Thien, M.-E. Yeoh, P.-L. Low, N. K. Devaraj, Z.-N. Ng and B. K. Yap, Sensors, 2023, 23(20), 8412 CrossRef CAS PubMed.
- S. Rahman, A. Haleem, M. Siddiq, M. K. Hussain, S. Qamar, S. Hameedd and M. Waris, RSC Adv., 2023, 13, 19508–19529 RSC.
- F. Kabir, S. Manir, M. M. H. Bhuiyan, S. Aftab, H. Ghanbari, A. Hasani, M. Fawzy, G. L. Thushani De Silva, M. R. Mohammadzadeh, R. Ahmadi, A. Abnavi, A. M. Askar and M. M. Adachi, Sustainable Energy Technol. Assess., 2022, 52(Part C), 102196 CrossRef.
- N. I. Abdul Shukor, K.-Y. Chan, G. S. H. Thien, M.-E. Yeoh, P.-L. Low, N. Kumari Devaraj, Z.-N. Ng and B. K. Yap, Sensors, 2023, 23(20), 8412 CrossRef PubMed.
- K. Phinjaturus, W. Maiaugree, B. Suriharn, S. Pimanpaeng, V. Amornkitbamrung and E. Swatsitang, Appl. Surf. Sci., 2016, 380, 101–107 CrossRef CAS.
- E. C. Prima, N. N. Hidayat, B. Yuliarto, Suyatman and H. K. Dipojono, Spectrochim. Acta, Part A, 2017, 171, 112–125 CrossRef CAS PubMed.
- O. Adedokun, Y. K. Sanusi and A. O. Awodugba, Optik, 2018, 174, 497–507 CrossRef CAS.
- H. Jing, D. Wu, S. Liang, X. Song, Y. An, C. Hao and Y. Shi, J. Energy Chem., 2019, 31, 89–94 CrossRef.
- A. Pervez, K. Javed, Z. Iqbal, M. Shahzad, U. Khan, H. Latif, S. A. Shah and N. Ahmad, Optik, 2019, 182, 175–180 CrossRef CAS.
- Y. Kusumawati, A. S. Hutama, D. V. Wellia and R. Subagyo, Heliyon, 2021, 7(12), e08436 CrossRef CAS PubMed.
- M. Hosseinnezhad, S. Rouhani and K. Gharanjig, Opto-Electron. Rev., 2018, 26(2), 165–171 Search PubMed.
- C. Xiang, T. Lv, C. A. Okonkwo, M. Zhang, L. Jia and W. Xia, J. Electrochem. Soc., 2017, 164(4), H203–H210 CrossRef CAS.
- I. Kathiravan, S. Sankaranarayanan, J. Balasundaram and B. Subramaniam, Environ. Sci. Pollut. Res., 2022, 29, 83897–83906 CrossRef CAS PubMed.
- X. Qin, J. Liu, G. Teng, B. Liu, Y. Xie, L. Ma and D. Hu, RSC Adv., 2023, 13, 7267–7279 Search PubMed.
- W. Ghann, H. Kang, T. Sheikh, S. Yadav, T. Chavez-Gil, F. Nesbitt and J. Uddin, Sci. Rep., 2017, 7, 41470 CrossRef CAS PubMed.
- J. A. Castillo-Robles, E. Rocha-Rangel, J. A. Ramírez-de-León, F. C. Caballero-Rico and E. N. Armendáriz-Mireles, J. Compos. Sci., 2021, 5(11), 288 CrossRef CAS.
|
This journal is © The Royal Society of Chemistry 2024 |
Click here to see how this site uses Cookies. View our privacy policy here.