DOI:
10.1039/D4CC06087C
(Feature Article)
Chem. Commun., 2025,
61, 4279-4292
Nanoporous high-entropy alloys and metallic glasses: advanced electrocatalytic materials for electrochemical water splitting
Received
15th November 2024
, Accepted 21st January 2025
First published on 23rd January 2025
Abstract
Electrochemical water splitting is a promising approach to convert renewable energy into hydrogen energy and is beneficial for alleviating environmental pollution and energy crises, and is considered a clean method to achieve dual-carbon goals. Electrocatalysts can effectively reduce the reaction energy barrier and improve reaction efficiency. However, designing electrocatalysts with high activity and stability still faces significant challenges, which are closely related to the structure and electronic configuration of catalysts. Nanoporous high-entropy alloys (np-HEAs) and metallic glasses (np-MGs), characterized by long-range chemical disorder intertwined with local chemical order combined with three-dimensional, interconnected nanoporous structure, exhibit distinctive electrocatalytic properties and application potential for electrochemical water splitting. To promote the widespread application of np-HEAs and np-MGs, it is of great significance to rationally design and apply them in the field of electrolytic water splitting. In this review, the basic principles of hydrogen evolution reaction and oxygen evolution reaction as well as the fabrication techniques of np-HEAs and np-MGs are introduced. The recent progress in the efficient application of np-HEAs and np-MGs in electrochemical water splitting, and the current challenges and prospects are summarized. This review will provide theoretical guidance for the development of np-HEAs and np-MGs in electrochemical water splitting applications.
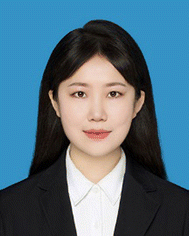
Yu Zhang
| Dr Yu Zhang is an assistant researcher at the Institute for New Energy Materials and Low-Carbon Technologies, Tianjin University of Technology. She received her PhD from Shandong University in 2023, and then took the current position. Her main research focuses on the development of nanoporous metal materials for application in electrocatalytic water splitting. |
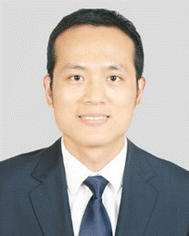
Yangchuan Cai
| Dr Yangchuan Cai is an associate professor of School of Materials Science and Engineering at Tianjin University of Technology. He received his PhD from Tianjin University in 2019 and joined Tianjin University of Technology in the same year. His current research focuses on the design of nanoporous high-entropy alloys and nanoporous metallic glasses for hydrogen evolution reaction and oxygen evolution reaction. |
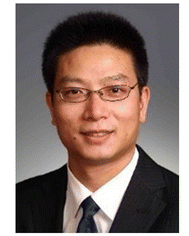
Yi Ding
| Prof. Yi Ding received his PhD in Materials Science and Engineering from Johns Hopkins University. He is currently a distinguished professor at the Institute for New Energy Materials and Low-Carbon Technologies, Tianjin University of Technology. Prof. Ding's research focuses on the design and processing of dealloyed nanoporous metals for green catalysis and advanced energy technologies. |
1. Introduction
Renewable energy technologies, such as solar and wind power, offer promising solutions to meet the growing global energy demand while significantly reducing greenhouse gas emissions.1,2 However, due to regional and seasonal variations, the direct supply of renewable energy can be inconsistent, posing challenges in reliably meeting the needs of modern society.3 Therefore, efficient storage and regeneration of renewable energy are essential to overcome these limitations. Hydrogen energy, with its high energy density and a calorific value two to three times greater than that of traditional fuels, stands out as an ideal candidate for energy storage.4,5 The chemical bonds in hydrogen (H2) molecules store energy without self-discharge, thus avoiding energy loss over time.6,7 As a result, hydrogen energy presents a green and viable option for renewable energy storage and conversion, offering substantial potential for both research advancements and practical applications.
Currently, the primary methods for H2 production are steam methane reforming, coal gasification, and electrochemical water splitting.8 The first two processes account for over 95% of global H2 production, which require significant fossil fuel consumption and produce substantial greenhouse gas emissions, notably carbon dioxide (CO2), thereby contributing to environmental challenges.9 In contrast, electrochemical water splitting relies solely on water (H2O) as feedstock to achieve zero carbon emissions, and is widely considered the cleanest, most sustainable, and efficient approach to H2 production.10 Renewable sources primarily supply the electricity for electrochemical water splitting. However, the intermittent and variable nature of these sources poses challenges to maintaining continuous and stable H2 production through electrolysis. Thus, the development of efficient and stable electrolysis technologies is essential to advancing H2 production through electrochemical water splitting.
The electrochemical water splitting to produce H2 involves the hydrogen evolution reaction (HER) at the cathode and the oxygen evolution reaction (OER) at the anode.11 The reaction efficiency is pivotal to the overall water-splitting process, where the performance largely depends on the catalyst employed. High-quality electrocatalysts are essential for achieving efficient water splitting for H2 generation. Currently, Ru-, Ir-, and Pt-based materials (precious metal oxides, single-atom catalysts, and heterostructured precious metal-based catalysts) stand out as the most effective electrocatalysts for both HER and OER.12–15 However, while precious metal-based electrocatalysts demonstrate excellent electrochemical water splitting performance, they face several significant challenges, including limited availability, high cost, and stability issues.16 Consequently, developing low-cost, non-precious metal-based electrocatalysts for water splitting remains an attractive yet challenging research area.
In conventional binary or ternary alloy systems, catalytic performance is mainly governed by the primary constituent, while the doped elements exert a relatively minor influence,17 which limits the flexibility to tune the intrinsic catalytic performance. High-entropy alloys (HEAs) are composed of five or more elements, whose electrocatalytic performance arises from the collective contributions of all components (a phenomenon referred to as the “cocktail effect”). Furthermore, the “lattice distortion effect” reduces the system's energy, facilitating the activation and transport of active sites throughout the catalytic process. With high mixing entropy in the system, HEAs enhance the diversity of active surface sites, leading to significant adsorption phenomena for catalytic intermediates.18 Metallic glasses (MGs), another type of multi-principal alloy system, contain more than three elements characterized by atomic size differences exceeding 12% and negative mixing enthalpies between constituents.19 Similar to HEAs, MGs permit flexible adjustment of atomic ratios, offering a wide array of catalytic active sites.20,21 Their metastable structures are notable for a high density of coordination-unsaturated sites and elevated surface energy.22 Consequently, both HEAs and MGs have garnered increasing interest in recent years within the field of electrochemical water splitting. At present, these novel materials are primarily supported on conductive substrates (current collectors) such as nanoparticles,23,24 nanowires,25 and nanosheets.26 Researchers are intensively working to optimize the catalytic performance of these advanced electrode materials by exploring various alloy systems,27 macroscopic morphologies,28 microscopic defects,29 and the introduction of non-metal elements (e.g., O,30 N,31 S32). However, the weak adhesion between conductive substrates and catalytic active sites limits active site exposure, and catalysts may detach from the substrate during high-current or long-term electrocatalytic processes.33 This challenge underscores the need for the design and fabrication of efficient, stable self-supporting electrodes to meet the demands of electrochemical water splitting and address the limitations of powder-based catalysts.
Nanoporous metals, as self-supported electrodes, present a range of advantages, including a high specific surface area, numerous exposed active sites, excellent conductivity, efficient electron transport, mechanical stability under high current, and low interfacial resistance due to super-hydrophilic structure.34–38 Additionally, the relatively simple fabrication process renders them well-suited for fulfilling the multifunctional demands of electrode materials.39 By merging the advantages of novel materials such as HEAs and MGs with nanoporous architectures, innovative self-supported nanoporous metal electrodes are anticipated to become cost-effective, highly catalytic, and exceptionally stable materials for a wide range of electrochemical applications. Numerous researchers are currently focused on this field, producing significant and systematic research achievements that advance its development.
2. The principle of electrochemical water splitting
The process of electrochemical water splitting involves two electrode reactions including HER at the cathode and OER at the anode. The HER is a two-electron process and follows the Volmer–Heyrovsky mechanism and the Volmer–Tafel mechanism (Fig. 1).40 In acidic media, the first step is the Volmer step, where a proton reacts with an electron to form an adsorbed hydrogen atom (H*) on the catalyst surface (eqn (1) and (4)). In contrast, in alkaline media, the hydrogen ions originate from the dissociation of water molecules, making the occurrence of HER slower under alkaline conditions than under acidic conditions. Subsequently, hydrogen molecules are formed through two pathways. One is that a proton combines with an adsorbed hydrogen atom to form a hydrogen molecule (eqn (2) and (5)), known as the Heyrovsky step. The other is that two adsorbed hydrogen atoms directly combine to form a hydrogen molecule (eqn (3) and (6)), called the Tafel step. Furthermore, the Tafel slope is a crucial parameter that reflects the electrochemical kinetics involved in HER, in which the Tafel slopes of 118, 39, and 29.5 mV dec−1 correspond to the Volmer, Heyrovsky, and Tafel steps, respectively.41 Typically, a lower Tafel slope signifies a more rapid electron transfer rate.
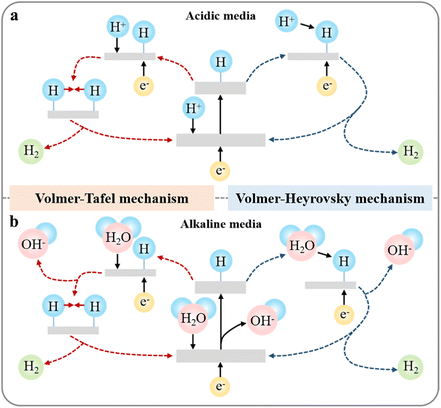 |
| Fig. 1 Mechanism of HER in (a) acidic media and (b) alkaline media. | |
Acidic:
Alkaline:
| H* + H2O + e− → OH− + H2 | (5) |
| 2H2O + 2e− → 2OH− + H2 | (6) |
The OER possesses sluggish kinetics than HER due to involving a four electron proton transfer process. The mechanisms of OER can be mainly divided into the adsorbate evolution mechanism (AEM) and the lattice oxygen oxidation mechanism (LOM) (Fig. 2).42–44 The key distinction is that LOM involves the direct participation of lattice oxygen in the catalyst, which significantly affects the catalytic activity and stability. In an AEM process under acidic solutions, water molecules adsorb onto active sites on the catalyst surface to form OH* intermediates (eqn (7)). Then OH* intermediates undergo deprotonation reaction to further oxidize into O* species, which react with additional water molecules to form OOH* intermediates, ultimately releasing oxygen (eqn (8), (10) and (11)). According to the LOM pathway under acidic conditions, the initial steps are similar to that of AEM involving the formation of OH* and O* species. Subsequently, the O* species couple with the lattice oxygen to directly form oxygen molecules, leaving vacancies in the catalyst crystal structure (eqn (9)), which are filled by water molecules forming new OH* intermediates. Finally, the catalyst returns to its initial state by deprotonation. In alkaline solution, the reaction pathway is similar to that in acidic solution except that water molecules dissociate into OH− (eqn (12)–(15)). Therefore, the LOM mechanism can break off adsorption energy scaling relationship of the AEM pathway, providing a potential low energy barrier pathway for OER by directly utilizing lattice oxygen to participate in O–O coupling, which may explain the high OER activity. However, participation of the lattice oxygen poses challenges to the structural stability of the catalyst.45,46 Therefore, a deep understanding of the OER mechanism is crucial for the design and development of efficient and stable OER catalysts.
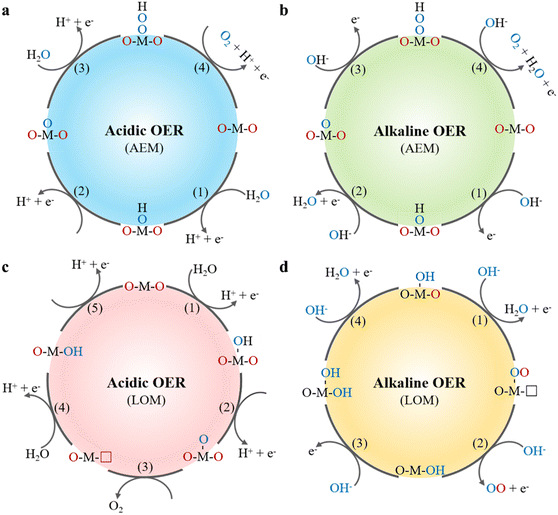 |
| Fig. 2 Acidic and alkaline OER mechanisms: (a), (b) the adsorbate evolution mechanism (AEM) and (c), (d) the lattice oxygen evolution mechanism (LOM). | |
Acidic:
| * + H2O → *OH + H+ + e− | (7) |
| *-O + *O →* + O2 + 2e− | (9) |
| or *O + H2O → *OOH + H+ + e− | (10) |
Alkaline:
| *OH + OH− → *O + H2O + e− | (13) |
| *-O + *O →* + O2 + 2e− or *O + OH− → *OOH + e− | (14) |
| *OOH + OH− → O2 + H2O + e− | (15) |
3. Preparation technologies of nanoporous high-entropy alloys (np-HEAs) and metallic glasses (np-MGs)
3.1 Fabrication methods of precursor alloys
Nanoporous metals, as self-supporting structures, are commonly derived from precursor materials in the form of strips or sheets. For HEAs, the main precursor preparation methods include casting followed by cutting (e.g., wire or sawing)47,48 and melt spinning.49,50 Among these, melt spinning leverages the rapid solidification of liquid metal to achieve refined grain sizes, producing smaller nanoporous structures after alloy dealloying. In contrast, casting typically involves quasi-equilibrium solidification, which aims to explore unique precursor microstructures, such as eutectic phases,51,52 followed by mechanical or wire cutting to produce sheet-like precursors. The formation of MGs requires extremely high temperature gradients or substantial compositional undercooling, making melt spinning the primary method for preparing these types of precursors.53,54
3.2 Selection of dealloying process
The preparation methods of nanoporous metal can be broadly classified into four main types: chemical dealloying,55 electrochemical dealloying, liquid metal dealloying (LMD), and vapor phase dealloying (VPD),56 as illustrated in Fig. 3. Chemical dealloying generally involves immersing a precursor alloy into a corrosive electrolyte (typically acidic or alkaline) and exploiting the electrochemical reactivity differences between metal components. This approach selectively dissolves the more active components, while the inert components diffuse and reorganize to form a nanoporous structure. Electrochemical dealloying, also referred to as constant current or constant potential dealloying, utilizes the differences in electrode potentials among elements within an alloy. By applying an external potential or current, the active components are selectively dissolved, resulting in the formation of a nanoporous structure. LMD involves selecting a molten metal that is miscible with one component of the precursor alloy but immiscible with the other. During the dissolution process, the immiscible component undergoes phase separation and diffuses at the solid–liquid interface. A subsequent chemical dealloying step is then employed to remove the miscible component, leaving behind a nanoporous metallic framework. VPD is a technique wherein the component of the alloy with a lower vapor pressure is selectively evaporated under precisely controlled temperature and vacuum conditions. Concurrently, components with higher vapor pressures undergo diffusion and reorganization, ultimately leading to the formation of a nanoporous structure. Among the four dealloying processes, both LMD and VPD require high-temperature conditions. However, the long-range ordered and short-range disordered characteristics of MGs are stable only at low temperatures, making chemical and electrochemical dealloying processes more suitable for the preparation of np-MGs. In contrast, the excellent thermal stability of HEAs allows for greater flexibility in dealloying process selection, enabling the application of all four processes. Nevertheless, the nanopores formed via the LMD process tend to be relatively large (on the order of hundreds of nanometers) and require significant consumption of active metal elements, primarily Ni. Consequently, LMD is predominantly utilized for the fabrication of nanoporous refractory HEAs,57 and to date, its application in electrochemical water splitting has not been reported.
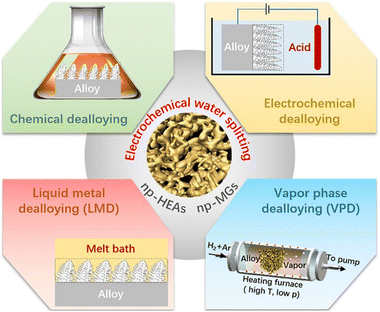 |
| Fig. 3 Dealloying process of np-HEAs and np-MGs. | |
4. Np-HEAs
The concept of entropy reflects the “intrinsic level of disorder” within a system. Yeh et al. categorize alloys based on entropy values as low-entropy alloys (LEAs, ΔSmix < 1.0 R), medium-entropy alloys (MEAs, 1.0 R ⩽ ΔSmix < 1.6 R), and high-entropy alloys (HEAs, ΔSmix
1.6 R).58 HEAs, a novel class of alloys, are composed of five or more elements, with a higher mixing entropy due to the increased number of constituent elements.59 The unique combinations of chemical elements in HEAs lead to complex and diverse structures and properties. Compared to traditional alloys, HEAs exhibit four distinctive effects including the thermodynamic high-entropy effect, the kinetic sluggish diffusion effect, the structural lattice distortion effect, and the performance-enhancing cocktail effect, as illustrated in Fig. 4,60 which significantly enhance the variety and number of active sites on the surface of HEAs. The multi-principal-element nature of HEAs further extends the control over the catalytic activity. The catalytic properties of np-HEAs are enhanced due to the exponentially increased specific surface area, which makes np-HEAs a very promising class of electrode materials.
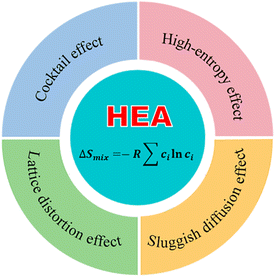 |
| Fig. 4 Fundamental effects of HEAs. | |
4.1 Np-HEAs with a single pore structure
4.1.1 Precious metal based.
Precious metals such as Ir and Ru are excellent electrocatalysts for the OER in acidic environments. Numerous Ir-based catalysts with nanostructures (e.g., alloys, oxides) have been reported in the literature.61–65 However, in these studies, the Ir content typically exceeds 50 wt%. Given the high cost and low abundance of Ir, multi-component Ir-based nanoalloys can reduce Ir content while potentially enhancing catalytic performance. Furthermore, np-HEAs with high surface areas and more active sites typically improve catalytic activity and material utilization efficiency. Qiu et al. reported a quintuple AlNiCoIrMo np-HEA with Ir content reduced to 20 at%. Np-HEAs provide greater flexibility in tuning the electronic properties and optimizing catalytic activity, owing to the infinite combinations of constituent elements. When applied to overall water splitting, the AlNiCoIrMo np-HEA exhibited an overpotential of only 275 mV at a current density of 10 mA cm−2.66 Compositional engineering effectively limits element diffusion through high-entropy effects, simultaneously tuning the electronic structure of active Ir sites to regulate the adsorption of intermediates in both HER and OER, thus mitigating element dissolution. For example, Song et al. designed a ZnNiCoIrX (X: Fe, Mn) np-HEA. The incorporation of the Mn element causes the d-band center of ZnNiCoIrX to shift negatively, with a binding energy of 21.9 eV, which is lower than that of ZnNiCoIr (40.1 eV), thereby enhancing the intrinsic activity of the HEAs, as shown in Fig. 5(a) and (b). The ZnNiCoIrMn np-HEA exhibited a HER overpotential of only 50 mV at a current density of 50 mA cm−2, and an OER overpotential of just 237 mV at a current density of 10 mA cm−2. Furthermore, the ZnNiCoIrMn np-HEA demonstrated excellent stability for both HER and OER with nearly no voltage decay after 100 h.67
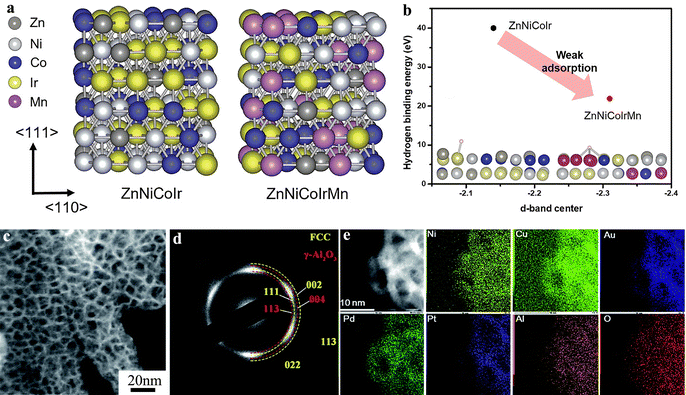 |
| Fig. 5 DFT results of the ZnNiCoIrMn np-HEA: (a) computational modeling of ZnNiCoIr and ZnNiCoIrMn with random atomic arrangement. (b) The linear relationship between the d-band center and hydrogen binding energy.67 TEM characterization results of the AlNiCuPtPdAu np-HEA: (c) dark-field STEM image. (d) The corresponding SAED image. (e) STEM-EDS mapping.68 | |
However, it remains a challenge for traditional bottom-up synthesis methods to controllably incorporate more than five immiscible metal elements into a single nanostructure. For instance, during the dealloying of Al in alkaline solution, active components (redox potential equal to or lower than Ni/Ni2+) tend to oxidize and form mixed oxides, which separate from the precious metals, resulting in the formation of metal/metal oxide composites.69,70 In this context, Qiu et al. synthesized a twelve-element Mn70Ni7.5Cu7.5Co4.2V4.2Fe2Mo2Pd0.5Pt0.5Au0.5Ru0.5Ir0.5 np-HEA for overall water splitting, achieving a current density of 10 mA cm−2 at a voltage of 1.49 V.71 Liu et al. synthesized an AlNiCuPtPdAu np-HEA (Fig. 5(c)), which exhibited mass activity 10 times higher than Pt/C for HER, significantly reducing the Pt content.68 The selected-area electron diffraction (SAED) image and scanning transmission electron microscopy-energy dispersive X-ray spectroscopy (STEM-EDS) mapping of the np-HEA confirmed the formation of oxides during the dealloying process, as illustrated in Fig. 5(d) and (e). Fujita et al. synthesized a nanoporous ultra-high-entropy alloy (np-UHEA) containing up to 14 elements through a single-step dealloying method. In acidic solution, Al89Ag1Au1Co1Cu1Fe1Ir1Ni1Pd1Pt1Rh1Ru1 demonstrated HER and OER activity with small overpotentials of 32 mV and 258 mV at a current density of 10 mA cm−2 respectively. When used for overall water splitting, the np-UHEA required only 1.53 V at 10 mA cm−2, outperforming commercial IrO2||Pt/C (1.66 V).72
4.1.2 Transition metal based.
The catalytic performance of np-HEAs with low precious metal content in electrochemical water splitting has been extensively validated in the literature. However, the potential of np-HEAs composed exclusively of transition metals has also garnered significant attention, as researchers explore their feasibility in industrial requirements. Luo et al. synthesized a CoCrFeNiMo np-HEA via microwave sintering, with a low overpotential of 220 mV at a current density of 10 mA cm−2 in 1.0 M KOH. Notably, stable operation was maintained for 24 h.73 Jiang et al. developed a NiFeCoCuTi np-HEA on a nanoporous Ni scaffold with columnar nanostructures, which exhibited outstanding current activity and stability, requiring an overpotential of only 209 mV to achieve an ultra-high current density of 2 A cm−2, with no degradation in activity even after 240 h of continuous operation in 1 M KOH.74 Hojjati-Najafabadi et al. reported a bifunctional FeCoNiCuTi catalyst, which demonstrated overpotentials of 64.9 mV for HER and 175 mV for OER at a current density of 10 mA cm−2 owing to complex electrochemical components.75 Kang et al. employed a np-NiCoFeMoMn HEA as both the cathode and anode for overall water splitting, achieving a voltage of only 1.47 V at a current density of 10 mA cm−2.76
4.2 Np-HEAs with a hierarchical porous structure
The hierarchical porous structure provides interconnected pores across multiple scales, accessible voids, and a large specific surface area, which significantly enhances mass transfer efficiency and accelerates chemical reaction rates, leading to optimal catalytic performance.77 Furthermore, the gradient porosity, spanning from macroscopic to mesoscopic scales, facilitates efficient gas release and mitigates the intense effects of continuous bubble formation at high current densities, which not only prevents rapid degradation of the catalyst structure but also ensures high stability during prolonged operation. Hierarchical np-HEA electrocatalysts effectively combine distinctive structural features with specific properties of the material, demonstrating superior electrochemical activity and enhanced mass transfer efficiency.78–83 Zhang et al. leveraged the Al–Al3Ni eutectic structure as a driving force to design the Al97.6Ni2Pt0.1Pd0.1Rh0.1Ir0.1 alloy.
They successfully fabricated nanoporous nanowires by a two-step chemical dealloying process, as shown in Fig. 6(a).78 Li et al. employed the Mn75Ni10Cu10Co4.5Pt0.5 alloy precursor and applied a multi-step process comprising chemical vapor deposition (CVD) and two-step dealloying to synthesize graphene-encapsulated nanoporous Pt50Mn8Ni14Cu14Co14, as illustrated in Fig. 6(b).79 This approach facilitated the formation of a hierarchical pore structure while simultaneously enhancing the content of the active element, Pt. Lu et al. developed a quaternary FeCoNiCu HEA with hierarchical porous architecture including a bi-continuous, Cu-enriched dendritic framework at the microscopic scale, accompanied by a secondary ultrafine mesoporous structure, as shown in Fig. 6(c). This catalyst exhibited a remarkably low overpotential of 42.2 mV for HER at a current density of 10 mA cm−2.80 Jiang et al. conducted their research based on the eutectic composition point in the Al–Cu binary phase diagram and partially substituted Cu with elements such as Ni, Mo, and Fe to create the (Cu8/wNix/wMoy/wFez/w)17.7Al82.3 (at%, where w = 8 + x + y + z, and x, y, z = 0 or 1) eutectic alloy and successfully obtained a two-phase porous CuAlNiMoFe HEA by using the single dealloying method, as shown in Fig. 6(d). The surface of the CuAlNiMoFe np-HEA acts as a bifunctional site, promoting water dissociation and facilitating the adsorption/desorption of H*, while the Cu framework serves as a scaffold for efficient electron transfer and ion/molecule transport. The CuAlNiMoFe np-HEA demonstrated excellent HER performance, achieving current densities of 1840 mA cm−2 and 100 mA cm−2 at overpotentials of 240 mV and 183 mV in 1 M KOH and 1 M PBS, respectively.81 Li et al. engineered the multiphase spatial structure of FeCoNiCr MEAs by alloying with Zr through physical metallurgy techniques, as shown in Fig. 6(e). This self-supporting catalyst, characterized by interconnected three-scale gradient porosity (ranging from ≈ 6 μm to ≈2 nm), demonstrated an OER overpotential of 215 mV at 10 mA cm−2 and 370 mV at 1 A cm−2. Moreover, it maintained nearly unchanged activity after 1000 h of operation at an ultra-high current density of 2 A cm−2, outperforming commercial IrO2 and RuO2 catalysts.82
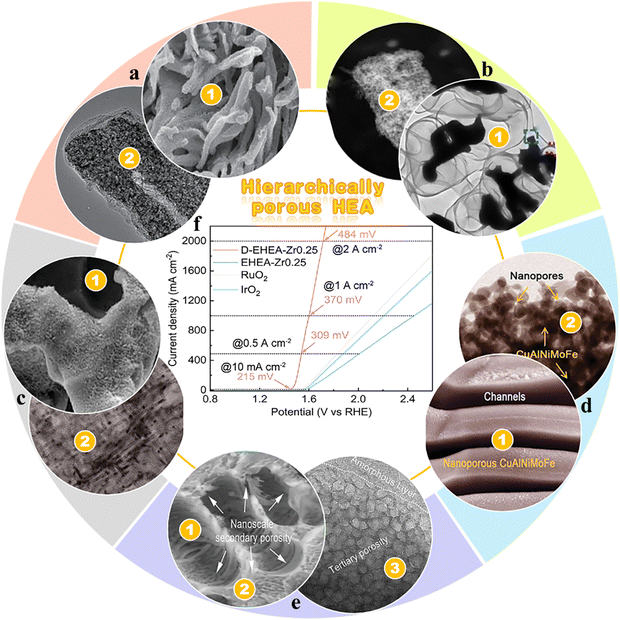 |
| Fig. 6 Hierarchically porous HEAs: (a) NiPtPdRhIrAl nanoporous nanowires.78 (b) CVD assisted two-step dealloying process to fabricate graphene-encapsulated nanoporous Pt50Mn8Ni14Cu14Co14.79 (c) Coexistence of a microscale dendritic-like skeleton and an internal secondary spinodal decomposition-like mesoporous structure formed with multiple metal elements in np-FeCoNiCu.80 (d) Quasi-eutectic CuAlNiMoFe np-HEA.81 (e) Hypo-eutectic hierarchically porous FeCoNiCrZr0.25 HEA.82 (f) Polarization curves of the hierarchically porous FeCoNiCrZr0.25 HEA in 1.0 M KOH. Scan rate: 5 mV s−1.82 | |
5. Np-MGs
MGs are a class of novel multi-component materials, typically formed by rapidly quenching a molten alloy to create a disordered solid structure.84–86 Np-MGs, characterized by nanoscale pores and an amorphous structure, on the one hand possess abundant low-coordination active sites and high Gibbs free energy, and on the other hand the nanoporous structure increases the specific surface area and provides more active sites. As a result, np-MGs show considerable potential for energy conversion and storage applications, particularly in H2 production through electrochemical water splitting.87–89
5.1 Nanoporous low-entropy metallic glasses (np-LEMGs)
Compared to crystalline electrocatalysts, disordered amorphous materials exhibit superior electrocatalytic performance due to their unique atomic structure.90–92 Lin et al. demonstrated that the Fe78Si9B13 np-MG exhibited exceptional OER activity, with an overpotential of only 199 mV at a current density of 10 mA cm−2.93 Similarly, Chang et al. reported that the np-Pd10Fe70P5C15 MGs displayed outstanding HER activity and stability.94 Furthermore, Wang et al. prepared an iron-based np-Fe85B10Si2P3 MG via electrochemical dealloying and impregnation methods, achieving excellent OER performance, requiring an overpotential of only 258 mV and exhibiting fast kinetics, with a Tafel slope of 51.7 mV dec−1 in 1.0 M KOH.95 During the preparation of np-MGs, the development of the nanoporous structure is accompanied by atomic rearrangement, which drives the transformation of certain atoms in the ligands from an amorphous disordered state to a crystalline ordered state,96 as shown in Fig. 7(a). The amorphous–crystalline heterostructure combines the rich unsaturated coordination of the amorphous phase with the high conductivity of the crystalline phase, making it a promising catalyst for the OER. Specifically, the unsaturated coordination sites in the amorphous phase provide abundant catalytic active sites, while the crystalline phase enhances electron transfer. Moreover, the interface between the amorphous and crystalline phases modulates the electron density at the interface sites, optimizing the adsorption and desorption of reaction intermediates, thereby improving catalytic performance.97–99 Zhu et al. employed vacuum annealing and electrochemical dealloying methods to prepare a nanocrystal-enriched, self-supporting np-Fe40Co40B20-800-5min catalyst. This catalyst exhibited exceptional OER performance, attributed to the synergistic effect between the nanocrystals and the amorphous phase, which facilitated electron transfer and enhanced the intrinsic active sites at the phase boundaries.100 Liu et al. enhanced the effective surface area for catalytic reactions by preparing a nanoporous Ni/metallic glass with micrometer-scale slits and nanometer-scale pores, using a one-step dealloying method on Ni40Zr40Ti20 MG wires. This design facilitated the catalytic process, achieving an overpotential of 78 mV at a current density of 10 mA cm−2.101 Tian et al. synthesized a self-supporting Cu60Ti37Mo3 np-MG, achieving a current density of 100 mA cm−2 at an overpotential of 220 mV.102 Zhang et al. synthesized an Fe–Ni–Co-based np-MG, which demonstrated an overpotential of 274 mV at a current density of 10 mA cm−2, as shown in Fig. 7(b) and (c).103
 |
| Fig. 7 (a) Diagram of the transition of the atomic configuration from amorphous to crystalline in the process of dealloying amorphous alloys.96 (b) TEM micrographs and STEM element mapping of Fe–Ni–Co-based np-MGs.103 (c) The HRTEM image of the precipitated phase and the amorphous matrix.103 | |
5.2 Nanoporous high-entropy metallic glasses (np-HEMGs)
HEMGs integrate the unique properties of MGs and HEAs. The high-entropy effect inherent to HEMGs enhances their glass-forming ability, making them superior to conventional MGs.104 HEMG electrocatalysts offer several advantages, including abundant defects (such as free volume regions), high coordination-unsaturated sites, increased potential energy, flexible atomic bonding, and improved corrosion resistance.105–107 Li et al. synthesized the np-Fe29Co27Ni23Si9B12 HEMG using melt spinning combined with electrochemical corrosion etching techniques. The amorphous structure enhances the catalytic performance by reducing the interaction between the surface and oxygen intermediates, thereby optimizing the adsorption Gibbs free energy. As a result, the HEMGs exhibit superior OER catalytic activity compared to crystalline HEAs, requiring overpotentials of only 230 mV and 409 mV at current densities of 10 mA cm−2 and 100 mA cm−2, respectively.108 Wang et al. reported Fe70−xCo10Ni10Zr10Ptx (x = 1, 3, 5) MGs, which exhibited a low HER overpotential of 102 mV at a current density of 1000 mA cm−2 and no activity decay during 250 h at a current density of 500 mA cm−2 due to their high surface area, enhanced chemical stability, and modulation of the electronic structure of Pt active sites.109 Additionally, Shen et al. engineered the (FeCoNiB0.75)97Pt3 np-HEMG through defect engineering. The introduction of lattice distortion (LD) and stacking fault (SF) defects modulated the atomic arrangement and electronic structure, while the nanoporous architecture provided additional active sites, thereby reducing the reaction energy barrier, as shown in Fig. 8(a) and (b). In this study, the influence of element B was excluded. Density functional theory (DFT) calculations revealed that the formation of SF induces significant LD in the face-centered cubic (FCC) matrix, as illustrated in Fig. 8(c). Additionally, 2D electron density difference and free energy calculations indicated that the incorporation of SF enhanced the electronic properties, as shown in Fig. 8(d) and (e). These modifications enabled the reduction of Pt content to just 3 at%, achieving a HER overpotential of 104 mV and an OER overpotential of 301 mV at a current density of 1 A cm−2. The material also demonstrated exceptional long-term stability, maintaining performance for 200 h at a current density of 100 mA cm−2, as shown in Fig. 8(f) and (g).110 Meanwhile, the equiatomic PdPtCuNiP np-HEMG synthesized by Qiao et al. exhibited exceptional HER performance, requiring only 35.4 mV at a current density of 10 mA cm−2, with a Tafel slope of 34.2 mV dec−1.111
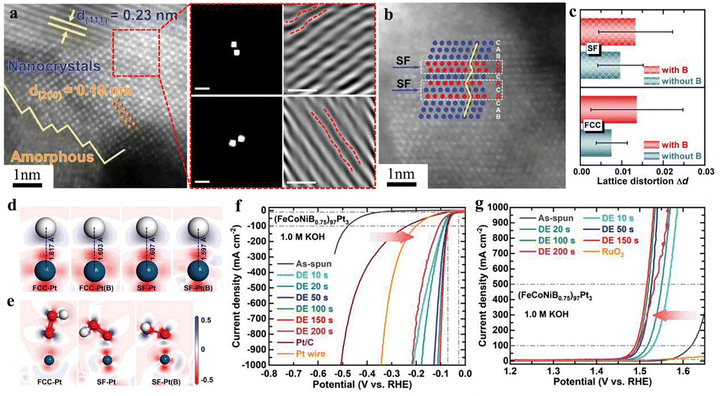 |
| Fig. 8 Defect engineering of np-(FeCoNiB0.75)97Pt3 HEMGs:110 (a) high-resolution HAADF-STEM image, FFT and IFFT images in the Pt-rich nanocrystal region with LD. (b) High-resolution HAADF-STEM image with SFs in the Pt-rich nanocrystal region. (c) The degree of LD (Δd) of FCC and SF models with and without B. (d) 2D electron density differences after adsorption of H* onto FCC-Pt, FCC-Pt(B), SF-Pt, and SF-Pt(B). (e) 2D electron density differences after adsorption of OOH* onto FCC-Pt, SF-Pt, and SF-Pt(B). Polarization curves of HER (f) and OER (g) at a scan rate of 5 mV s−1 in 1.0 M KOH. | |
6. Surface reconstructions of np-HEAs and np-MGs
Most electrocatalysts undergo irreversible and rapid structural transformations during the OER, leading to the formation of metal oxides/hydroxides on the catalyst surface. These structural changes are particularly pronounced under alkaline conditions and at elevated potentials. In fact, the oxidized outer layer of the catalyst is often regarded as the true active electrocatalyst.112–114 Since the electrocatalytic reaction occurs at the electrode/electrolyte interface, the active species on the catalyst surface play a pivotal role in the OER process. Kang et al. in situ transformed np-NiFeCoMn HEAs into np-NiFeCoMnOOH, thereby facilitating lattice oxygen activation. This catalyst exhibited an overpotential of 194 mV at 10 mA cm−2 and demonstrated long-term stability for up to 120 h at 100 mA cm−2.115 Subsequently, the research team introduced Cu into the np-MnFeCoNi HEA using the same method, converting it in situ to np-MnFeCoNiCuOOH, as shown in Fig. 9(a). Raman spectroscopy revealed that during electrochemical activation, the np-MnFeCoNiCuOOH electrode undergoes dynamic surface restructuring, ultimately achieving the lowest overpotential values, as shown in Fig. 9(b) and (c). Due to its optimal adsorption energy with reaction intermediates, the catalyst demonstrated outstanding OER performance under alkaline conditions, with an overpotential of 176 mV at 10 mA cm−2 and stable operation for over 5500 h at a current density of 500 mA cm−2, as illustrated in Fig. 9(d).116 Pan et al. in situ constructed nanoporous structures and active hydroxide/oxide species on the surface of FeVNbTiZrOF. Compared to the non-activated catalyst, the activated catalyst exhibited a 184 mV decrease in overpotential for the OER at a current density of 10 mA cm−2.117 Cui et al. reported that Fe50Ni27Nb3P13C7 forms NiOOH during the OER process, and the overpotential at a current density of 10 mA cm−2 was only 348 mV in 6 M KOH.118 Furthermore, the development of self-healing OER catalysts was aimed at addressing the challenging trade-off between catalyst activity and stability. Lu et al. in situ transformed Fe1.98Co1.22Ni1.00Nb0.62, composed of the FCC phase and Laves phase, into a dual-layer structure comprising of an inner amorphous NbOx layer and an outer amorphous (FeCoNiNb)Ox layer on the surface of (FeCoNi)2Nb. The outer multicomponent amorphous oxide layer endowed the catalyst with remarkable OER activity, while the inner layer provided dynamic replenishment, achieving a balance between activity and stability. This was evidenced by a low overpotential of 235 mV at a current density of 10 mA cm−2 and remarkable stability, maintaining performance for over 1600 h at a current density of 500 mA cm−2.119
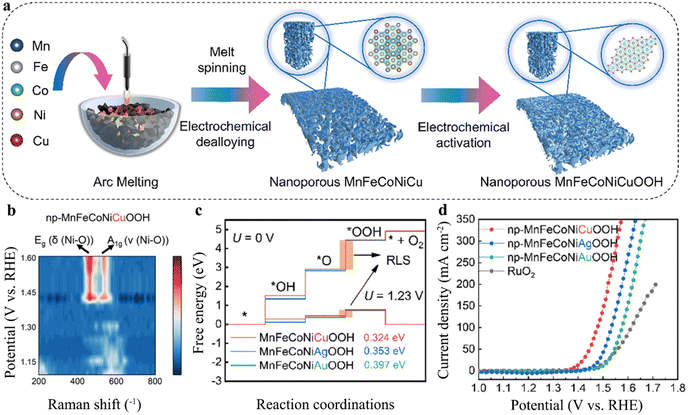 |
| Fig. 9 (a) Schematic route for the synthesis of np-MnFeCoNiCuOOH. (b) Electrochemical in situ Raman spectra of np-MnFeCoNiCuOOH in the range of 200–800 cm−1 at the operated potentials from 1.1 V to 1.6 V vs. RHE. (c) Free energy on the electrocatalyst surface at a potential of 0 V. (d) OER polarization curves of np-MnFeCoNiCuOOH in 1.0 M KOH (electronic grade) with iR-correction. Scan rate: 5 mV s−1.118 | |
7. Conclusions and perspectives
Electrochemical water splitting to produce H2 can convert green energy into hydrogen energy, providing a zero-carbon emission effective way to produce high-purity H2. The efficiency of this technology heavily relies on the performance of electrocatalysts, which is closely related to composition, structure, and electronic configuration. The advent of nanoporous high-entropy alloys (np-HEAs) and metallic glasses (np-MGs) has revolutionized traditional alloy design principles, presenting a plethora of opportunities for the development of water electrolysis due to their tunable compositions, unique structures, and superior performance. This review elucidates the fundamental principles of HER and OER, outlines the fabrication techniques for np-HEAs and np-MGs, and summarizes recent research on np-HEA and np-MG electrocatalysts in electrochemical water splitting, in which a structure–function relationship is established, aiming to foster a profound understanding of catalytic mechanisms and guide the design of superior np-HEA and np-MG electrocatalysts. Despite advancements in the synthesis, characterization, and application np-HEAs and np-MGs in electrochemical water splitting, the underlying design principles, structure–activity relationships, and catalytic mechanisms remain unclear. Furthermore, the performance study of membrane electrode assemblies (MEAs) is still in its infancy, indicating that the development of np-HEAs and np-MGs with high activity and stability for electrochemical water splitting faces numerous challenges (Fig. 10).
 |
| Fig. 10 Summary and perspectives of designing nanoporous HEAs and np-MGs for water electrolyzers. | |
(1) Precision and controllable synthesis of electrocatalysts. Although various np-HEAs and np-MGs have been fabricated, there is often a disconnect between the structure and activity of electrocatalysts, leading to discrepancies between the anticipated and actual performance of the catalysts. Np-HEAs, with their diverse elemental compositions and tunable electronic structures, have been applied in H2 production through electrochemical water splitting. Np-MGs, with their disordered atomic arrangements, provide a rich source of active sites, exhibiting higher intrinsic catalytic activity and stronger activation capabilities compared to crystalline materials. By adjusting the composition, the electronic structure of np-MGs can be optimized to improve the internal diffusion of reactants, enhancing catalytic efficiency. Moreover, machine learning techniques are accelerating the discovery of new materials for np-HEAs and np-MGs and improving the efficiency and accuracy of their design optimization. By analyzing data patterns to predict material properties, these techniques reduce the time and resource consumption associated with trial-and-error methods, aiding scientists in optimizing alloy design.
(2) Understanding the complex structure–activity relationships. Np-HEAs, composed of five or more elements in near-equal atomic ratios, offer tunable active sites that can be optimized through careful selection of elemental configurations and compositions. Np-MGs, with their disordered atomic arrangements, exhibit excellent thermal stability and corrosion resistance, which are crucial for catalysis. Future research should integrate in situ characterization techniques (such as in situ Raman, in situ X-ray spectroscopy, and online differential electrochemical mass spectrometry) to reveal how the unique properties of these alloys contribute to their catalytic capabilities and how their performance can be enhanced through structural regulation and composition optimization. This will not only deepen the understanding of catalytic mechanisms of alloys but also provide a scientific basis for the design of efficient catalysts.
(3) Research of membrane electrode performance for electrochemical water splitting. Despite the increasing recognition of the limitations of traditional electrochemical performance testing systems, the adoption of device-scale reactors and MEAs has not yet become a practice in research. Promoting research on MEAs and the widespread use of device-scale reactors will greatly facilitate the development and progress of this field. Device-scale reactors can better simulate industrial conditions, providing higher reaction efficiency and stability, while MEA optimization can enhance the performance of electrochemical reactions. By combining these two approaches, researchers can achieve more efficient catalyst development and application, thereby advancing electrochemical technology and its industrialization. As the core component of the electrolytic water system, MEAs directly affect the entire system's performance, and their efficient multiphase transport capabilities can significantly improve the efficiency and lifespan of electrolytic water splitting. Therefore, promoting the application of device-scale reactors and optimizing MEA research will lead to significant technological advancements and broaden the application prospects in the field of H2 production through electrochemical water splitting.
Author contributions
Yu Zhang: writing – review & editing. Yangchuan Cai: investigation, writing – review & editing. Yi Ding: supervision, writing – review & editing, funding acquisition.
Data availability
No primary research results, software or code have been included and no new data were generated or analysed as part of this review.
Conflicts of interest
The authors declare that they have no known competing financial interests or personal relationships that could have appeared to influence the work reported in this paper.
Acknowledgements
This work was financially supported by the National Key Research and Development Program of China (2019YFA0705700), the National Natural Science Foundation of China (no. U2102214) and the Scientific and Technological Project of Yunnan Precious Metals Laboratory (YPML-20240502030).
Notes and references
- P. D. Luna, C. Hahn, D. Higgins, S. A. Jaffer, T. F. Jaramillo and E. H. Sargent, Science, 2019, 364, eaav3506 CrossRef PubMed.
- Z. Zhai, Y. Wang, C. Si, P. Liu, W. Yang, G. Cheng and Z. Zhang, Nano Res., 2023, 16, 2026–2034 CrossRef CAS.
- I. Staffell and S. Pfenninger, Energy, 2018, 145, 65–78 CrossRef.
- S. Pandey, Y. Oh, M. Ghimire, J. W. Son, M. Lee and Y. Jun, Chem. Commun., 2024, 60, 8789–8805 RSC.
- L. Zhang, X. Shi, A. J. Xu, W. W. Zhong, J. T. Zhang and S. J. Shen, Nano Res., 2024, 17, 2061–2069 CrossRef.
- M. Chatenet, B. G. Pollet, D. R. Dekel, F. Dionigi, J. Deseure, P. Millet, R. D. Braatz, M. Z. Bazant, M. Eikerling, I. Staffell, P. Balcombe, Y. Shao-Horn and H. Schaefer, Chem. Soc. Rev., 2022, 51, 4583–4762 RSC.
- Z. Y. Yu, Y. Duan, X. Y. Feng, X. Yu, M. R. Gao and S. H. Yu, Adv. Mater., 2021, 33, 2007100 CrossRef CAS PubMed.
- X. Zou and Y. Zhang, Chem. Soc. Rev., 2015, 44, 5148–5180 RSC.
- V. R. Stamenkovic, D. Strmcnik, P. P. Lopes and N. M. Markovic, Nat. Mater., 2017, 16, 57–69 CrossRef CAS PubMed.
- J. Turner, G. Sverdrup, M. K. Mann, P. C. Maness, B. Kroposki, M. Ghirardi, R. J. Evans and D. Blake, Int. J. Energy Res., 2008, 32, 379–407 CrossRef CAS.
- H. J. Xu, X. C. Wang, W. Zhao, R. J. Guo, Z. Y. Xue, T. Zhang, Y. Shao and K. F. Yao, Sci. China Mater., 2023, 66, 3855–3864 CrossRef CAS.
- S. Hao, M. Liu, J. Pan, X. Liu, X. Tan, N. Xu, Y. He, L. Lei and X. Zhang, Nat. Commun., 2020, 11, 5368 CrossRef CAS PubMed.
- B. Lu, L. Guo, F. Wu, Y. Peng, J. E. Lu, T. J. Smart, N. Wang, Y. Z. Finfrock, D. Morris, P. Zhang, N. Li, P. Gao, Y. Ping and S. Chen, Nat. Commun., 2019, 10, 631 CrossRef CAS PubMed.
- J. J. Li, Z. Lian, Q. Li, Z. C. Wang, L. F. Liu, F. L. Deepak, Y. P. Liu, B. Li, J. Y. Xu and Z. X. Chen, Nano Res., 2022, 15, 5933–5939 CrossRef CAS.
- Q. L. Wu, K. Jiang, J. H. Han, D. C. Chen, M. Luo, J. Lan, M. Peng and Y. W. Tan, Sci. China Mater., 2022, 65, 1262–1268 CrossRef CAS.
- Y. Jiao, Y. Zheng, M. Jaroniec and S. Z. Qiao, Chem. Soc. Rev., 2015, 44, 2060–2086 RSC.
- X. Fu, J. Zhang, S. Zhan, F. Xia, C. Wang, D. Ma, Q. Yue, J. Wu and Y. Kang, ACS Catal., 2022, 12, 11955–11959 CrossRef CAS.
- X. Huang, G. Yang, S. Li, H. Wang, Y. Cao, F. Peng and H. Yu, J. Energy Chem., 2022, 68, 721–751 CrossRef CAS.
-
A. Inoue, Bulk Amorphous Alloys, Trans Tech Publications Ltd., Switzerland, 1st edn, 1998 Search PubMed.
- X. Han, G. Wu, J. Du, J. Pi, M. Yan and X. Hong, Chem. Commun., 2021, 58, 223–237 RSC.
- P. Debenedetti and F. Stillinger, Nature, 2001, 410, 259–267 CrossRef CAS PubMed.
- X. Wang, H. Tian, X. Yu, L. Chen, X. Cui and J. Shi, Chin. J. Catal., 2023, 51, 5–48 CrossRef CAS.
- H. Luo, L. Li, F. Lin, Q. Zhang, K. Wang, D. Wang, L. Gu, M. Luo, F. Lv and S. Guo, Adv. Mater., 2024, 36, 2403674 CrossRef CAS PubMed.
- X. Yang, Q. Q. Chen, C. J. Wang, C. C. Hou and Y. Chen, J. Energy Chem., 2019, 35, 197–203 CrossRef.
- J. Xu, C. Zhang, H. Liu, J. Sun, R. Xie, Y. Qiu, F. Lu, Y. Liu, L. Zhuo, X. Liu and J. Luo, Nano Energy, 2020, 70, 104529 CrossRef CAS.
- Y. Shi, J. Fei, H. Li, C. Li, T. Zhan, J. Lai and L. Wang, Appl. Catal., B, 2024, 359, 124465 CrossRef CAS.
- M. Wei, Y. Sun, J. Zhang, F. Ai, S. Xi and J. Wang, Energy Environ. Sci., 2023, 16, 4009–4019 RSC.
- S. Jo, M. C. Kim, K. B. Lee, H. Choi, L. Zhang and J. I. Sohn, Adv. Energy Mater., 2023, 13, 2301420 CrossRef CAS.
- Y. Lu, K. Huang, X. Cao, L. Zhang, T. Wang, D. Peng, B. Zhang, Z. Liu, J. Wu, Y. Zhang, C. Chen and Y. Huang, Adv. Funct. Mater., 2022, 32, 2110645 CrossRef CAS.
- J. Baek, M. D. Hossain, P. Mukherjee, J. Lee, K. T. Winther, J. Leem, Y. Jiang, W. C. Chueh, M. Bajdich and X. Zheng, Nat. Commun., 2023, 14, 5936 CrossRef CAS PubMed.
- X. Zhou, L. Zou, H. Zhu, M. Yan, J. Wang, S. Lan, S. Chen, H. Hahn and T. Feng, Small, 2024, 20, 2310327 CrossRef CAS PubMed.
- L. Lin, Z. Ding, G. Karkera, T. Diemant, M. V. Kante, D. Agrawal, H. Hahn, J. Aghassi-Hagmann, M. Fichtner, B. Breitung and S. Schweidler, Small Struct., 2023, 4, 2300012 CrossRef CAS.
- S. Chandrasekaran, M. Khandelwal, F. Dayong, L. Sui, J. S. Chung, R. D. K. Misra, P. Yin, E. J. Kim, W. Kim, A. Vanchiappan, Y. Liu, S. H. Hur, H. Zhang and C. Bowen, Adv. Energy Mater., 2022, 12, 2200409 CrossRef CAS.
- H. M. Sun, Z. H. Yan, F. M. Liu, W. C. Xu, F. Y. Cheng and J. Chen, Adv. Mater., 2020, 32, 1806326 CrossRef CAS PubMed.
- Q. F. Hu, Z. L. Chen, J. J. Wang, X. R. Zheng, X. P. Han, Y. D. Deng and W. B. Hu, Sci. China Mater., 2022, 65, 1825–1832 CrossRef CAS.
- Y. Wang, W. Huang, C. H. Si, J. Zhang, X. J. Yan, C. H. Jin, Y. Ding and Z. H. Zhang, Nano Res., 2016, 9, 3781–3794 CrossRef CAS.
- Y. J. Shi, Y. Zhang and Z. H. Zhang, Sci. China Mater., 2021, 64, 1521–1533 CrossRef CAS.
- S. Shi, X. L. Wen, Q. Q. Sang, S. Yin, K. L. Wang, J. Zhang, M. Hu, H. M. Yin, J. He and Y. Ding, Nano Res., 2021, 14, 2681–2688 CrossRef CAS.
- H. Yang, M. Driess and P. W. Menezes, Adv. Energy Mater., 2021, 11, 2102074 CrossRef CAS.
- J. Zhu, L. Hu, P. Zhao, L. Y. S. Lee and K. Y. Wong, Chem. Rev., 2020, 120, 851–918 CrossRef CAS PubMed.
- J. Gan, Z. K. Huang, W. Luo, W. Y. Chen, Y. Q. Cao, G. Qian, X. G. Zhou and X. Z. Duan, J. Energy Chem., 2021, 52, 33–40 CrossRef CAS.
- N. T. Suen, S. F. Hung, Q. Quan, N. Zhang, Y. J. Xu and H. M. Chen, Chem. Soc. Rev., 2017, 46, 337–365 RSC.
- Z. W. Lei, T. Y. Wang, B. Zhao, W. B. Cai, Y. Liu, S. H. Jiao, Q. Li, R. G. Cao and M. L. Liu, Adv. Energy Mater., 2020, 2000478 CrossRef CAS.
- J. Yu, Q. J. He, G. M. Yang, W. Zhou, Z. P. Shao and M. Ni, ACS Catal., 2019, 9, 9973–10011 CrossRef CAS.
- T. Binninger, R. Mohamed, K. Waltar, E. Fabbri, P. Levecque, K. Rüdiger and T. J. Schmidt, Sci. Rep., 2015, 5, 12167 CrossRef CAS PubMed.
- F. Y. Chen, Z. Y. Wu, Z. Adler and H. T. Wang, Joule, 2021, 5, 1704–1731 CrossRef CAS.
- Z. Jin, J. Lv, H. Jia, W. Liu, H. Li, Z. Chen, X. Lin, G. Xie, X. Liu, S. Sun and H. J. Qiu, Small, 2019, 15, 1904180 CrossRef CAS PubMed.
- Z. Jin, X. Zhou, Y. Hu, X. Tang, K. Hu, K. M. Reddy, X. Lin and H. J. Qiu, Chem. Sci., 2022, 13, 12056–12064 RSC.
- G. Fang, J. Gao, J. Lv, H. Jia, H. Li, W. Liu, G. Xie, Z. Chen, Y. Huang, Q. Yuan, X. Liu, X. Lin, S. Sun and H. J. Qiu, Appl. Catal., B, 2020, 268, 118431 CrossRef CAS.
- Y. Zhang, J. Kang, H. Xie, H. Yin, Z. Zhang, E. Liu, L. Ma, B. Chen, J. Sha, L. Qian, W. Hu, C. He and N. Zhao, Appl. Catal., B, 2024, 341, 123331 CrossRef CAS.
- R. Q. Yao, Y. T. Zhou, H. Shi, W. B. Wan, Q. H. Zhang, L. Gu, Y. F. Zhu, Z. Wen, X. Y. Lang and Q. Jiang, Adv. Funct. Mater., 2021, 31, 2009613 CrossRef CAS.
- Q. Chen, X. Han, Z. Xu, Q. Chen, Q. Wu, T. Zheng, P. Wang, Z. Wang, J. Wang, H. Li, Z. Xia and J. Hao, Nano Energy, 2023, 110, 108380 CrossRef CAS.
- J. Qin, H. Zhang, W. Lu, J. Zhu, J. Tian and J. Shen, Chem. Eng. J., 2024, 490, 151700 CrossRef CAS.
- X. Zhang, Y. Yang, Y. Liu, Z. Jia, Q. Wang, L. Sun, L. C. Zhang, J. J. Kruzic, J. Lu and B. Shen, Adv. Mater., 2023, 35, 2303439 CrossRef CAS PubMed.
- C. Wang, P. Zou, W. Xu, Y. Zhang, J. Huo, J.-Q. Wang, Y. Liu and C. Qin, J. Alloys Compd., 2024, 995, 174790 CrossRef CAS.
- Q. Sang, S. Hao, J. Han and Y. Ding, Energy Chem., 2022, 4, 100069 CrossRef CAS.
- S. H. Joo, I. Okulov and H. Kato, J. Mater. Res. Technol., 2021, 14, 2945–2953 CrossRef CAS.
- W. L. Hsu, C. W. Tsai, A. C. Yeh and J. W. Yeh, Nat. Rev. Chem., 2024, 8, 471–485 CrossRef PubMed.
- J. W. Yeh, S. K. Chen, S. J. Lin, J. Y. Gan, T. S. Chin, T. T. Shun, C. H. Tsau and S. Y. Chang, Adv. Eng. Mater., 2004, 6, 299–303 CrossRef CAS.
- M. K. Xie, X. Xiao, D. J. Wu, C. Zhen, C. S. Wu, W. J. Wang, H. Nian, F. Y. Li, M. D. Gu and Q. Xu, Nano Res., 2024, 17, 5288–5297 CrossRef CAS.
- X. Xiong, J. Tang, Y. Ji, W. Xue, H. Wang, C. Liu, H. Zeng, Y. Dai, H. J. Peng, T. Zheng, C. Xia, X. Liu and Q. Jiang, Adv. Energy Mater., 2024, 14, 2304479 CrossRef CAS.
- D. Liu, Q. Lv, S. Lu, J. Fang, Y. Zhang, X. Wang, Y. Xue, W. Zhu and Z. Zhuang, Nano Lett., 2021, 21, 2809–2816 CrossRef CAS PubMed.
- H. Guo, Z. Fang, H. Li, D. Fernandez, G. Henkelman, S. M. Humphrey and G. Yu, ACS Nano, 2019, 13, 13225–13234 CrossRef CAS PubMed.
- F. Liao, K. Yin, Y. Ji, W. Zhu, Z. Fan, Y. Li, J. Zhong, M. Shao, Z. Kang and Q. Shao, Nat.
Commun., 2023, 14, 1248 CrossRef CAS PubMed.
- Z. Xie, H. Chen, X. Wang, Y. A. Wu, Z. Wang, S. Jana, Y. Zou, X. Zhao, X. Liang and X. Zou, Angew. Chem., Int. Ed., 2025, 64, e202415032 CrossRef CAS PubMed.
- Z. Jin, J. Lv, H. Jia, W. Liu, H. Li, Z. Chen, X. Lin, G. Xie, X. Liu, S. Sun and H. J. Qiu, Small, 2019, 15, 1904180 CrossRef CAS PubMed.
- J. Kwon, S. Sun, S. Choi, K. Lee, S. Jo, K. Park, Y. K. Kim, H. B. Park, H. Y. Park, J. H. Jang, H. Han, U. Paik and T. Song, Adv. Mater., 2023, 35, 2300091 CrossRef CAS PubMed.
- T. Yu, Y. Zhang, Y. Hu, K. Hu, X. Lin, G. Xie, X. Liu, K. M. Reddy, Y. Ito and H. J. Qiu, ACS Mater. Lett., 2022, 4, 181–189 CrossRef CAS.
- H. J. Qiu, G. Fang, Y. Wen, P. Liu, G. Xie, X. Liu and S. Sun, J. Mater. Chem. A, 2019, 7, 6499–6506 RSC.
- Z. Jin, J. Lyu, Y. L. Zhao, H. Li, Z. Chen, X. Lin, G. Xie, X. Liu, J. J. Kai and H. J. Qiu, Chem. Mater., 2021, 33, 1771–1780 CrossRef CAS.
- P. Du, Y. Wen, F. K. Chiang, A. Yao, J. Q. Wang, J. Kang, L. Chen, G. Xie, X. Liu and H. J. Qiu, ACS Appl. Mater. Interfaces, 2019, 11, 14745–14752 CrossRef CAS PubMed.
- Z. X. Cai, H. Goou, Y. Ito, T. Tokunaga, M. Miyauchi, H. Abe and T. Fujita, Chem. Sci., 2021, 12, 11306–11315 RSC.
- S. Singla, S. Sharma, S. Basu, N. P. Shetti and T. M. Aminabhavi, Int. J. Hydrogen Energy, 2021, 46, 33696–33717 CrossRef CAS.
- H. Shi, X. Y. Sun, S. P. Zeng, Y. Liu, G. F. Han, T. H. Wang, Z. Wen, Q. R. Fang, X. Y. Lang and Q. Jiang, Small Struct., 2023, 4, 2300042 CrossRef CAS.
- Y. He, J. Qin, F. Hu, L. Mao, B. Shen, T. M. Aminabhavi, Y. Vasseghian and A. Hojjati-Najafabadi, Chem. Eng. J., 2024, 492, 152145 CrossRef CAS.
- H. Liu, H. Qin, J. Kang, L. Ma, G. Chen, Q. Huang, Z. Zhang, E. Liu, H. Lu, J. Li and N. Zhao, Chem. Eng. J., 2022, 435, 134898 CrossRef CAS.
- X. Y. Yang, L. H. Chen, Y. Li, J. C. Rooke, C. Sanchez and B. L. Su, Chem. Soc. Rev., 2017, 46, 481 RSC.
- Y. Wang, B. Yu, M. He, Z. Zhai, K. Yin, F. Kong and Z. Zhang, Nano Res., 2022, 15, 4820–4826 CrossRef CAS.
- L. Zhu, Q. Li, Y. Hu, X. Wu, K. Madhav Reddy, K. Li, G. Xie, X. Liu and H. J. Qiu, Nanoscale Horiz., 2024, 9, 1506–1513 RSC.
- R. Li, X. Liu, W. Liu, Z. Li, K. C. Chan and Z. Lu, Adv. Sci., 2022, 9, 2105808 CrossRef CAS PubMed.
- R. Q. Yao, Y. T. Zhou, H. Shi, W. B. Wan, Q. H. Zhang, L. Gu, Y. F. Zhu, Z. Wen, X. Y. Lang and Q. Jiang, Adv. Funct. Mater., 2021, 31, 2009613 CrossRef CAS.
- Q. Zhang, Q. Guo, Y. Zhang, Y. He, W. Gong, W. Liu, X. Liu and R. Li, Adv. Funct. Mater., 2024, 2414446 Search PubMed.
- Q. Chen, X. Han, Z. Xu, Q. Chen, Q. Wu, T. Zheng, P. Wang, Z. Wang, J. Wang, H. Li, Z. Xia and J. Hao, Nano Energy, 2023, 110, 108380 CrossRef CAS.
- W. H. Wang, C. Dong and C. H. Shek, Mater. Sci. Eng., R, 2004, 44, 45–89 CrossRef.
- J. C. Qiao and J. M. Pelletier, J. Mater. Sci. Technol., 2014, 30, 523–545 CrossRef.
- D. V. Louzguine-Luzgin and V. I. Polkin, Russ. J. Non-Ferrous Metals, 2017, 58, 80–92 CrossRef.
- C. Pei, S. Chen, T. Zhao, M. Li, Z. Cui, B. Sun, S. Hu, S. Lan, H. Hahn and T. Feng, Adv. Mater., 2022, 34, 2200850 CrossRef CAS PubMed.
- Y. C. Hu, Y. Z. Wang, R. Su, C. R. Cao, F. Li, C. W. Sun, Y. Yang, P. F. Guan, D. W. Ding, Z. L. Wang and W. H. Wang, Adv. Mater., 2016, 28, 10293–10297 CrossRef CAS PubMed.
- Y. W. Tan, F. Zhu, H. Wang, Y. Tian, A. Hirata, T. Fujita and M. W. Chen, Adv. Mater. Interfaces, 2017, 4, 1601086 CrossRef.
- R. Li, X. Liu, R. Wu, J. Wang, Z. Li, K. Chan, H. Wang, Y. Wu and Z. Lu, Adv. Mater., 2019, 31, 1904989 CrossRef CAS PubMed.
- S. Ju, J. Feng, P. Zou, W. Xu, S. Wang, W. Gao, H. J. Qiu, J. Huo and J. Q. Wang, J. Mater. Chem. A, 2020, 8, 3246–3251 RSC.
- M. W. Glasscott, A. D. Pendergast, S. Goines, A. R. Bishop, A. T. Hoang, C. Renault and J. E. Dick, Nat. Commun., 2019, 10, 2650 CrossRef PubMed.
- F. Chu, K. Y. Wu, Y. Y. Meng, D. Q. You, W. Li and H. J. Lin, J. Non-Cryst. Solids, 2021, 566, 120831 CrossRef CAS.
- R. Jiang, Z. Cui, W. Xu, S. Zhu, Y. Liang, Z. Li, S. Wu, C. Chang and A. Inoue, Electrochim. Acta, 2019, 328, 135082 CrossRef CAS.
- Y. Ye, D. Wang, H. Meng, M. Du, Y. Lin, Z. Dong, A. Wang and Y. Wang, J. Non-Cryst. Solids, 2024, 646, 123208 CrossRef CAS.
- S. Jin, Y. Li, Y. Yang and W. Zhang, Mater. Today Nano, 2024, 26, 100485 CrossRef CAS.
- S. Li, B. Chen, Y. Wang, M. Y. Ye, P. A. van Aken, C. Cheng and A. Thomas, Nat. Mater., 2021, 20, 1240–1247 CrossRef CAS PubMed.
- J. Huang, H. Sheng, R. D. Ross, J. Han, X. Wang, B. Song and S. Jin, Nat. Commun., 2021, 12, 3036 CrossRef CAS PubMed.
- Y. Chen, Z. Lai, X. Zhang, Z. Fan, Q. He, C. Tan and H. Zhang, Nat. Rev. Chem., 2020, 4, 243–256 CrossRef CAS PubMed.
- L. Xiao, J. Gao, X. Yao, X. Dong, F. Yang, J. Wang, Z. Cui, C. Li and S. Zhu, Appl. Surf. Sci., 2023, 640, 158395 CrossRef CAS.
- J. Wang, L. You, Z. Li, X. Liu, R. Li, Q. Du, X. Wang, H. Wang, Y. Wu, S. Jiang and Z. Lu, J. Mater. Sci. Technol., 2021, 73, 145–150 CrossRef CAS.
- K. S. Aneeshkumar, J. Tian and J. Shen, J. Alloys Compd., 2021, 886, 161270 CrossRef CAS.
- Y. Jin, G. Xi, R. Li, Z. A. Li, X. B. Chen and T. Zhang, J. Alloys Compd., 2021, 852, 156876 CrossRef CAS.
- Y. Chen, Z. W. Dai and J. Z. Jiang, J. Alloys Compd., 2021, 866, 158852 CrossRef CAS.
- C. I. Müller, T. Rauscher, A. Schmidt, T. Schubert, T. Weißgärber, B. Kieback and L. Röntzsch, Int. J. Hydrogen Energy, 2014, 39, 8926–8937 CrossRef.
- J. Ye, J. Lu, C. Liu, Q. Wang and Y. Yang, Nat. Mater., 2010, 9, 619–623 CrossRef CAS PubMed.
- Y. Pei, G. Zhou, N. Luan, B. Zong, M. Qiao and F. F. Tao, Chem. Soc. Rev., 2012, 41, 8140–8162 RSC.
- H. Wang, R. Wei, X. Li, X. Ma, X. Hao and G. Guan, J. Mater. Sci. Technol., 2021, 68, 191–198 CrossRef CAS.
- M. Pan, H. Feng, Z. Zhang, M. Gao, L. Lei, D. Wang, G. Li, J. Huo and J.-Q. Wang, J. Mater. Chem. A, 2024, 12, 15334–15342 RSC.
- X. Zhang, Y. Yang, Y. Liu, Z. Jia, Q. Wang, L. Sun, L. C. Zhang, J. J. Kruzic, J. Lu and B. Shen, Adv. Mater., 2023, 35, 2303439 CrossRef CAS PubMed.
- Y. Li, J. Tang, H. Zhang, Y. Wang, B. Lin, J. Qiao, H. Zheng, Z. Yu, Y. Liu, T. Zhou and X. Lei, Chem. Eng. J., 2023, 453, 139905 CrossRef CAS.
- W. Wang, Q. Wen, D. Huang, Y. Lin, N. Zhao, L. Tang, M. Li, Y. Liu and R. He, Angew. Chem., Int. Ed., 2025, 64, e202415132 CrossRef CAS PubMed.
- F. Wu, F. Tian, M. Li, S. Geng, L. Qiu, L. He, L. Li, Z. Chen, Y. Yu, W. Yang and Y. Hou, Angew. Chem., Int. Ed., 2025, 64, e202413250 CrossRef CAS PubMed.
- L. Magnier, G. Cossard, V. Martin, C. Pascal, V. Roche, E. Sibert, I. Shchedrina, R. Bousquet, V. Parry and M. Chatenet, Nat. Mater., 2024, 23, 252–261 CrossRef CAS PubMed.
- Y. Zhang, J. Kang, H. Xie, H. Yin, Z. Zhang, E. Liu, L. Ma, B. Chen, J. Sha, L. Qian, W. Hu, C. He and N. Zhao, Appl. Catal., B, 2024, 341, 123331 CrossRef CAS.
- Y. Zhang, J. Kang, H. Xie, H. Yin, Z. Zhang, Y. Ma, G. Sun, E. Liu, L. Ma, B. Chen, J. Sha, L. Qian, W. Hu, C. He and N. Zhao, J. Mater. Chem. A, 2024, 12, 26909–26919 RSC.
- Y. Zhu, W. Dai, X. Zhong, T. Lu and Y. Pan, J. Colloid Interface Sci., 2021, 602, 55–63 CrossRef CAS PubMed.
- L. Xiao, Y. Liang, Z. Li, S. Wu, S. Luo, H. Sun, S. Zhu and Z. Cui, J. Colloid Interface Sci., 2022, 608, 1973–1982 CrossRef CAS PubMed.
- Z. Li, R. Wu, D. Duan, X. Liu, R. Li, J. Wang, H. Chen, S.-W. Chen, Y. Wu, H. Wang, S. Jiang, X. Zhang and Z. Lu, Joule, 2024, 06, 023 Search PubMed.
|
This journal is © The Royal Society of Chemistry 2025 |
Click here to see how this site uses Cookies. View our privacy policy here.