DOI:
10.1039/B807094F
(Perspective)
Energy Environ. Sci., 2008,
1, 542-564
Biofuels: a technological perspective
Received
28th April 2008
, Accepted 1st August 2008
First published on
5th September 2008
Abstract
Environmental issues, the growing demand for energy, political concerns and the medium-term depletion of petroleum has created the need for development of sustainable technologies based on renewable raw materials. Biofuels might help to meet the future energy supply demands as well as contributing to a reduction of green house gas emissions. Although this topic is highly controversial and many investigations are currently ongoing, this review is intended to give a brief overview about certain aspects of the complex biofuel issue, providing the latest update of the production and potential of biofuels in the transport sector including types of biofuel, feedstocks and technologies and some of the possible socio-economic, environmental and political implications of the widespread use of biofuels in our society.
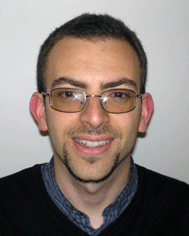 Rafael Luque | Rafael Luque has been a post-doctoral researcher working in the Green Chemistry Centre of Excellence over the last three years. His PhD is from Universidad de Cordoba in Spain under Prof. Campelo's supervision. His interests are materials science, catalysis and more recently biofuels. He is (co-)author of over 35 manuscripts and 2 patents. He will return to Prof. Campelo's group in late September. |
| Juan M. Campelo is the head of the Departamento de Quimica Organica at the Universidad de Cordoba in Spain. For three decades he has been involved in acid–base heterogeneous catalysis research applied to organic chemistry. He has recently joined the interest in biofuels, starting a new research line in Cordoba around 2nd generation biodiesel. He is (co-)author of over 140 peer-reviewed publications and 6 patents. |
| James H. Clark holds a Chair in Chemistry at the University of York. James has been at the forefront of green and sustainable chemistry for over 10 years, being founding scientific editor of the journal Green Chemistry and founding Director of the Green Chemistry Network. He currently runs the Green Chemistry Centre of Excellence at York bringing together research and industrial collaboration on renewable resources and clean synthesis. |
Introduction
There is now a general scientific consensus that observed trends in global warming are been caused by fossil fuel combustion and anthropogenic emissions of greenhouse gases (GHG) including nitrous oxide (N2O) and especially carbon dioxide (CO2) and methane (CH4).1 Initial concerns about the impact of GHG in our society led to the development of the United Nations Framework Convention on Climate Change (1992), which in turn resulted in the 1997 Kyoto Protocol as a way to tackle the problem. In 2002 the European Union ratified the Kyoto Protocol and emphasised the potential for scientific innovation as a means of countering GHG emissions. Neither these targets nor the Kyoto targets have so far been met. The reality is that the situation is likely to become more complicated in the next few years. Transport has shown the highest rates of growth in GHG emissions in any sector over the last ten years (20% global CO2 emissions, 25% UK emissions), with a predictable 80% higher energy use and carbon emissions than now by 2030.2
Oil is the world's primary source of energy and chemicals with a current demand of about 12 million tonnes per day (84 million barrels a day)3 with a projection to increase to 16 million tonnes per day (116 million barrels a day) by 2030. While 30% of the global oil consumption accounts for transport, a striking 60% of the rising demand expected for 2030 corresponds to transport.4 With the transport sector expanding in the US and Europe and especially developing in the newly industrialised and emerging economies of China and India, these values can easily be underestimated. The availability of conventional oil is again becoming geographically restricted and a general agreement now is that the era of cheap and secure oil (cheap energy) is over.5 Several alternatives are currently being explored, including a range of carbon free and renewable sources (photovoltaics, wind and nuclear power, hydrogen), in an attempt to replace natural gas, coal and oil in the electricity generation sector. However, there is no such equivalent in transportation yet, since fuel cells, electric/hybrids and natural gas based cars are still a long way from becoming mainstream vehicles.
A short and medium term alternative is needed. Crop-based fuels denoted as biofuels including biodiesel and bioethanol, emerged as a real alternative to the use of gasoline and conventional diesel in transportation. An exponential increase in the consumption of such biofuels has taken place in the last few years (Fig. 1).
 |
| Fig. 1 Biofuels consumption (1991–2006) in the EU27. Source: REFUEL, IEA, Eurovserv' ER. Reproduced with permission of Marc Londo. | |
Ideally, such oil alternatives should reduce (or even remove) the dependence of oil as well as contributing as much as possible to meet the GHG emissions target. However, it is also widely accepted that joint efforts from politicians, regulators, scientists and consumers will be needed to support an independent oil/GHG controlled scenario in the future.
In view of the predictions, the need for a secure energy supply for transportation make it essential to explore biofuels as alternatives to mineral oil based fuels addressing and evaluating socio-economic and environmental consequences originated in their implementation.
From a wider context, there are three main drivers for the promotion, development and implementation of biofuels in our society. In principle, these are energy independence, climate change and rural development.3 The political motivation to support biofuels arises from each individual driver or combinations of them. The main theoretical reasons for the promotion of biofuels can be summarised as follows:
1. Biofuels can improve independence and energy security
Local, national or global production of energy can avoid the reliance on politically and/or socially unstable energy suppliers.6 In addition, the global oil demand is increasing exponentially and there is a need to find alternatives to fossil fuels derived from petroleum.
2. Biofuels may contribute to a reduction in carbon emissions (aka climate change mitigation)
They have been often considered a solution to climate change. In fact, net emissions from biofuels have been reported to be remarkably lower than those generated from the combustion of fossil fuels.7 Nevertheless, the GHG emissions from the production of biofuels are a key issue that needs careful attention as they arise from every single stage in the supply chain from feedstock production and transport to conversion, biofuels distribution and end use (Fig. 2). Recently, some studies point out the CO2 reduction may be far less than originally thought due to the inclusion of crop production costs including fertilisers, machinery, etc. as well as harvesting, transformations and distribution.3
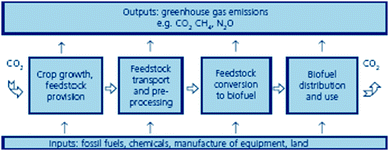 |
| Fig. 2 Greenhouse gas emissions from production and utilisation of biofuels (source: Sustainable biofuels: prospects and challenges, The Royal Society. Policy document 01/08, ISBN 978 0 85403 662 2. Reproduced with permission of the Royal Society). | |
3. Biofuels can help to increase farm income and contribute to rural development
With a growing biofuels market, many countries will be able to grow more types of crops to cover national or foreign demands on energy crops. The increasing demand for agriculture due to the labour-intensive plant derived technologies8 is expected to improve farm income, which in countries with oversupply can also help to reduce the need for subsidies. Traditionally deprived rural areas could experience a renaissance through the implementation of biofuels and biorefineries. In addition, there is also a lot of controversy over food vs. fuel and the growth of specific crops to be transformed into biofuels. The resolution of this process will necessarily take place on the basis of very different variables over time.9
With a wide array of potentially renewable energy resources, the concept and proposed benefits evolving from the use of biofuels are inspiring; therefore they need to be taken into account in order to contribute to a sustainable and energy secure future.
In this review, we aim to provide a general (not exhaustive) overview of the state of the art in the production and potential of biofuels for transport as well as their socio-economic, environmental and technological implications of their widespread implementation on our society.
What are biofuels?
Biofuels (also denoted sometimes as agrofuels to make reference to biofuels from agriculture and forestry) can be broadly defined as any sort of fuel that is made from organic matter (aka biomass). The most common biofuels are biodiesel and bioalcohols, including bioethanol and biobutanol (also called biogasoline).
The past of biofuels: an overview of the history of biofuels
Biofuels are not a recent discovery. The transesterification of vegetable oils has been widely known and employed since the 19th century. In fact, the process currently in use for making biofuels from biomass is the same inherited from the past. The feedstocks utilised for their preparation were also very similar. Peanut, hemp and corn oil and animal tallow were conventionally used and have been partially replaced by soybean, rapeseed, recycled oil, forest wastes and trees and sugar cane. But the history of biofuels is more political and economical than technological.
Liquid biofuels for transport have been used since the early days of the automobile industry. Nikolaus August Otto, the German inventor of the internal combustion engine (Fig. 3), conceived his invention to run on ethanol. In 1898, Rudolph Diesel (Fig. 4) used peanut oil (the “original” biodiesel) in the first demonstration of his compression ignition engine at the World's Exhibition in Paris. Vegetable oils were used in diesel engines until the 1920's when an alteration was made to the engine, enabling it to use a residue of petroleum (currently known as No. 2 diesel fuel).
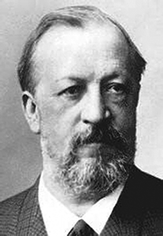 |
| Fig. 3 Nikolaus August Otto, inventor of the internal combustion engine. | |
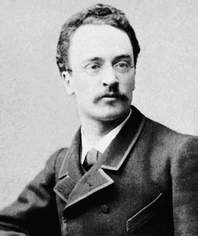 |
| Fig. 4 Rudolf Diesel, inventor of the diesel engine. | |
Nevertheless, Diesel was not the only person to believe that biofuels could be the way forward of the transportation industry. Henry Ford (Fig. 5) was so convinced that renewable resources were the key to the success of his automobiles that he designed them (from the 1908 Model T) to be run with ethanol. He also built an ethanol plant in the Midwest and established a partnership with Standard Oil to sell it in their distributing stations.
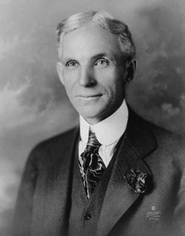 |
| Fig. 5 Henry Ford, founder of the Ford company. | |
At the beginning of World War II, both the Allies and Germany utilized biomass fuels in their machines. Wartime Germany experienced extreme oil shortages. The vehicles were then powered with blends including Reichskraftsprit that was a blend of gasoline with alcohol fermented from potatoes. In Britain, grain alcohol was blended with petrol by the Distillers Company Ltd. Under the name Discol and marketed through Esso's affiliate Cleveland. Despite their use during World War II, biofuels remained in obscurity to which they had been forced from fossil fuels (petroleum). Until the 70s, the solid petrol-based industry establishment made us very dependent on foreign oil. However, the supply of crude oil, as are all supplies of fossil fuels, is limited and some issues were about to take place. In 1973 we experienced the first of two oil crises. The Organisation of the Petroleum Exporting Countries (OPEC) that controls the majority of the global oil reduced supplies and increased prices. The second one came five years later in 1978.
Then, the potential of biofuels reappeared in the public consciousness, brought back by various bio-energy programs including the Programa Nacional do Alcool (Proálcool) established in Brazil in 1975 (which was critical in the development of ethanol fuel) and international organisations such as the International Energy Agency (IEA) Bioenergy, established in 1978 by the Organisation for Economic Co-operation and Development (OECD), that aimed to improve cooperation and information exchange between countries that have national programs in bioenergy research, development and implementation.
On a worldwide scale, the United Nations (UN) International Biofuels Forum is formed by Brazil, China, India, South Africa, the United States and the European Commission, the United States, Brazil, France, Sweden and Germany being the world leaders in biofuel development and use.
As examples, some interesting available data are given. France was the second largest biofuel consumer among the EU States in 2006 (increasing by 62.7%). Biodiesel represents the largest share of this (78%, far ahead of bioethanol with 22%).10 Germany itself remained the largest European biofuel consumer, with a consumption estimate of 2.8 million tons of biodiesel (equivalent to 2
408
000 toe), 0.71 million ton of vegetable oil (628
492 toe) and 0.48 million ton of bioethanol (307
200 toe), being ADM Ölmühle Hamburg AG (a subsidiary of the American group Archer Daniels Midland Company) the largest biodiesel producer.10 In Brazil, the government hopes to build on the success of the Proálcool ethanol program by expanding the production of biodiesel which must contain 2% biodiesel by 2008, increasing to 5% by 2013.
More interesting and entertaining examples that illustrate the effects of biofuels in our current society can be found in journals, press and the internet. Biodiesel produced today can be used in unmodified diesel engines. Over 200 major fleets in the United States now run on biodiesel with entities including the United States Post Office, the US Military, metropolitan transit systems, agricultural concerns, and school districts being major users. In Europe, biodiesel is readily available to purchase in many gas stations (well over 1000 stations in Europe). Journey to Forever, a non-government organization, traveled from Hong Kong to Southern Africa producing their own biodiesel along the way and teaching people from small villages how to make their own biofuels to employ in heaters, tractors, buses, automobiles, and other machines they might have. Josh Tickell traveled on The Veggie Van (Fig. 6) 25
000 miles around the United States on new and recycled fryer oil. Nowadays, The Veggie Van Organization is a non profit educational service that promotes biofuels through hands-on demonstrations, school presentations and road tours.11 David Ramey also drove his unmodified 1992 Buick across America in the summer of 2005 using 100% butanol as fuel.12
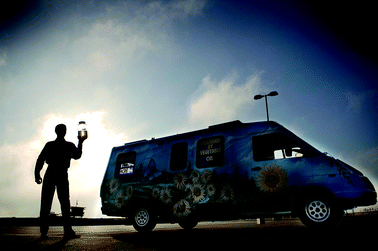 |
| Fig. 6 The Veggie Van project. Reproduced with permission of Barry J. Holmes. | |
For a more detailed study about various industrial uses and biofuels programmes worldwide, we refer the readers to recently reported documents3,10,13 and the discussion around biofuels.
Present of biofuels: the biofuels ladder
In this changing environment, many opportunities are arising for bioenergy. There has been a relatively high acceptance from general public, governments, producers and part of the agricultural sectors in promoting the expansion of biofuels in our society in an attempt to switch from the petrol-based industry we have been relying on for the last 50+ years to a biobased industry and society that can guarantee a more secure energy supply. In this regard, much of the work carried out in the last few years has been focused on the development of various methodologies for the production of biofuels for transport. There are several important factors that we have to take into account for a successful implementation of biofuels in our society and we will deal with them in the discussion around biofuels. However, since we started to climb the biofuels ladder, we have already achieved a certain level of development (2nd generation of biofuels with a potential 3rd generation in sight) that is already contributing to prove the real potential of biofuels in our lives. We will briefly go through the different types of biofuels that have been developed until now. It is generally accepted that there are two different generations of biofuels that have been classified starting from the conventional technologies and feedstocks (1st generation) to the latest advances in the field (2nd and potential 3rd generation).
Scheme 1 summarises a very simplified classification of biofuels we propose for a better understanding of the subject. The latest results reported by Howard et al.14 right before the submission of this manuscript might lead to a third generation of biofuels as we will highlight in future perspectives.
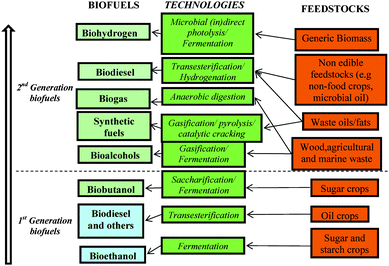 |
| Scheme 1 The biofuels ladder. Road map of biofuels production from feedstocks and technologies. | |
First generation biofuels
The first generation biofuels referred to biofuels manufactured from readily available energy crops including sugar, starch and oil crops (edible feedstocks) using conventional technologies. The most common first generation biofuels are biodiesel and bioethanol. Some other biofuels in this category including biofuels integrating glycerol, biofuels from catalytic cracking, biobutanol and 2,5-dimethylfuran (DMF) will also be briefly discussed. The various biofuels will be grouped according to the technology employed for their preparation. These are chemical, thermo-chemical and biological conversion.
Biofuels produced by chemical conversion
Biodiesel
First generation biodiesel is currently the most common biofuel in Europe. It remains in the political and economic arena and is playing a part in the biofuels expanding process as the awareness alternative fuel spreads through the consciousness of the general public. Only in 2007, 19 biodiesel plants in the new EU member states were starting operations, or were under construction/planning. Relatively large plants can be found in Lithuania, Poland and Romania, with capacities of 100
000 tonnes y−1. The conventional methodology for the production of biodiesel involves the transesterification of triglycerides (TG) from vegetable oils (palm, corn, soybean, rapeseed, sunflower, etc.) with short chain alcohols including methanol and ethanol to yield fatty acid (m)ethyl esters (FAM/EE) and glycerol as a by product (Scheme 2).
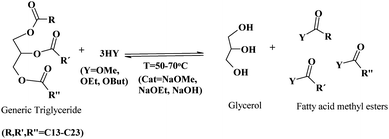 |
| Scheme 2 Conventional transesterification of TG for the production of biodiesel. | |
Several reviews on the preparation of biodiesel from different feedstocks can be found in the literature.15,16 A very good overview of such technologies has been recently published by Al-Zuhair.17
The methods of preparation of biodiesel can be classified in: chemical catalytic (base- or acid catalysis), biocatalytic (enzyme catalysis) and non-catalytic processes.
Biodiesel produced by chemical catalytic methods.
Homogeneous catalysis.
The conventional and traditional methodology for the production of biodiesel primarily involved the transesterification of the vegetable oils using NaOH and KOH18–20 or mineral Brønsted acids (sulfuric, phosphoric or hydrochloric acids)21–23 as homogeneous catalysts and vegetable oils or waste oils and fats as feedstock at relatively mild temperatures (50–80 °C).
Few reports on the production of biodiesel using a variety of homogeneous catalysts including guanidines24 and different amines as catalysts (yielding conversions higher than 98% in a one-step reaction, minimizing the production of waste water)25 can also be found.
Regardless of the limitations of the methodology, the process is also far from being environmentally friendly. The final mixture needs to be separated, neutralised and thoroughly washed, generating a great amount of salt, soaps, and waste water which need to be further purified or treated. The catalyst cannot also be recycled. These several additional steps certainly put the total overall biodiesel production costs up, at the same time reducing the quality of its main by-product (glycerol). This phase needs to be separated from the biodiesel for further washing/drying to remove the traces of glycerol and from the fuel to comply with EU quality standard regulations (EN 14214). The standard prescribes 0.02% or lower glycerol content must be present in the biodiesel.
The acid catalysed homogeneous transesterification has not been widely investigated compared to the alkali-catalysed process due to its slower reaction rates, the need of harsher conditions (higher temperatures, methanol to oil molar ratios and quantities of catalysts) and the formation of unwanted secondary products such as dialkyl or glycerol ethers.16b These drawbacks make impractical its successful implementation with hardly any examples of commercial processes available.26
Heterogeneous catalysis.
Several reports can be recently found on the production of biodiesel involving other chemically catalysed protocols as greener alternatives using vegetable oils using solid bases27–30 and solid acids.23b, 27,31–33 Di Serio et al. have recently reviewed the use of heterogeneous catalysts for biodiesel production.27
The advantages of the heterogeneously catalysed protocols from the green chemistry standpoint are that the catalyst may be recycled and subsequently employed in the reaction. The biodiesel prepared has improved properties compared to the homogeneously catalysed process. The elimination of the pre-treatment steps and the minimisation of waste, avoiding the production of waste salts, also improves the green credentials of the reaction. Excellent yields of FAME/FAEE can be obtained under relatively mild conditions with many of these heterogeneous catalysts. However, the separation, disposal or use of the glycerol generated in the process as well as the washing of the crude biodiesel obtained to remove the traces of glycerol to meet the EEC regulations are often a problem associated to the chemical production of biodiesel.
Biodiesel produced by biochemical catalytic methods.
The increasing environmental concerns have led to a growing interest in the use of enzyme catalysis as it usually produces a cleaner biodiesel under milder conditions. It also generates less waste than the conventional chemical process. Many authors have reported a wide range of efficient and low energy intensive protocols obtaining very promising results with lipases (in both free and immobilised form)34,35 and combining lipases with alkali catalysts.36
The limitations of the industrial use of enzymatic methodology is mainly due to their high production costs, which may be overcome by molecular technologies to enable the production of the enzymes in higher quantities as well as in a virtually purified form.37
Biodiesel produced by non-catalysed processes.
The most common and simple non-catalysed biodiesel production process has been performed using supercritical methanol via simultaneous transesterification of triglycerides and esterification of fatty acids.38 The alcohol supercritical conditions are essential because a very low reaction rate is obtained under subcritical conditions.
The procedure has been claimed to be very effective yielding high FAME contents in a very short time of reaction (typically less than 30 min). The presence of water also facilitated the formation of the methyl esters. Nevertheless, the supercritical methodology is still very expensive and the implementation of such costly technology in industry is currently a challenge.
Properties and advantages/disadvantages of first generation biodiesel.
Biodiesel is non toxic, sulfur-free and biodegradable being used in unmodified diesel engines pure or as a blend. It has a significant added value compared to petrol-diesel because of its higher lubricity, flash point and lower aromatic content which extend engine life and reduces maintenance costs. Biodiesel has also lower combustion emissions [except for nitrogen oxides (NOx)], particulate matter and unburned hydrocarbons compared to petrol-based diesel.15
However, biodiesel suffers from low mileage (higher fuel consumption compared to No. 2 diesel fuel) and oxidative instability as well as being corrosive.17 It also produces slightly lower power and torque.
Biofuels integrating glycerol
Novel methodologies for the preparation of esters from TG which directly afford alternative biofuels are currently under development.39
The transesterification reaction of triglycerides with dimethyl carbonate (DMC),40 methyl acetate41 or ethyl acetate42 produced a mixture of three molecules of FAME or FAEE and one of glycerol carbonate (GC) or glycerol triacetate (triacetin). Such a mixture (FAME + GC) has suitable physical properties to be employed as fuel, constituting a novel biofuel denoted as DMC-BioD.20b,20c
Gliperol is another patented novel biofuel.41a Gliperol is composed of a mixture of three molecules of FAMEs and one molecule of triacetin. It can be obtained after the transesterification of one mole of TG with three moles of methyl acetate employing a lipase as a catalyst.41,42
Similarly, we have patented a novel biofuel denoted as Ecodiesel-100 obtained via 1,3-selective partial ethanolysis of the triglycerides with pig pancreatic lipase (PPL).43 The biofuel is a mixture of two parts of FAEE and one part of MG, with minor quantities of DG.
Properties and advantages/disadvantages of biofuels integrating glycerol.
DMC-BioD, Gliperol and Ecodiesel-100 incorporate glycerol in their monophasic homogeneous mixtures, avoiding the generation of residues or by-products in their preparation processes. The main difference with respect to the conventional biodiesel (FAME) production is that no additional separation steps are needed. GC and/or triacetin can be perfectly burnt together with the FAME in the blend. In terms of green chemistry, the incorporation of glycerol into the biofuel improves the efficiency of the process (from current 90% to 100%), without substantial modifications of its physico-chemical properties. The atom efficiency is also improved as the total number of atoms involved in the reaction is part of the final mixture. Recent studies have also demonstrated that the presence of MG adds value to the biofuel by improving the lubricity on the engine.44 However, the implementation of such interesting biofuels in the transport sector can be greatly conditioned by the performance of the biofuels in actual diesel engines due to their high content in “additives” including MG, triacetin and GC. These compounds may also have higher melting points (e.g. MG) and potentially form carbonaceous deposits when burnt. Furthermore, the current legislation on biodiesel does not restrict the presence of MG and glycerol so that a special legislation promoting these biofuels might be necessary.
DMF has attracted a great deal of attention as a potential biofuel. Advances in the production of DMF from fructose and glucose using catalytic biomass-to-liquid (BTL) processing have been recently reported.45 The process involves, in the first step, an acid-catalysed dehydration of fructose to produce 5-hydroxymethyl furfural (HMF). HMF is then extracted from the organic phase and subsequently converted to DMF by the hydrogenolysis of C–O bonds using a carbon supported copper-ruthenium catalyst.45 The potential of DMF is currently under investigation. A DMF joint venture is currently under development involving the University of Wisconsin (Madison, US) and Virent Energy Systems.
Properties and advantages/disadvantages of DMF.
DMF has interesting physico-chemical properties. Its energy density is 40% greater than ethanol, making it comparable to gasoline. It is also chemically stable, insoluble in water (does not absorb moisture from the atmosphere) and has a higher boiling point (92 °C) than ethanol. However, the toxicological properties of DMF have not been thoroughly tested. The limited information available suggests that DMF is no more toxic than current fuel components.45 The scaling up of the technology, in terms of costs and production, might be another issue to take into account.
Biofuels from catalytic cracking
Catalytic cracking of vegetable oils has also been reported as a promising alternative to the preparation of biofuels. Several vegetable oils (e.g. palm, canola, soybean) have been employed in the process that involves conversion of the oils into biofuels suitable for gasoline engines using acid catalysts such as transition metal catalysts (that yield biofuels enriched in diesel fraction—over 50% by weight)46 and zeolites and mesoporous materials that give biofuels with higher gasoline fractions—over 40%—with higher aromatic content.47 The reaction is normally performed at moderate to high temperatures (300–500 °C) using different oils to catalyst ratios depending on the oil and the catalyst.47
Properties and advantages/disadvantages of biofuels from catalytic cracking.
The technology is relatively simple and efficient and it has the advantage that industrially similar processes using micro- and mesoporous materials to produce fuels and chemicals are well developed. The main shortcoming of the successful implementation of such biofuels lies on the economics of the process with the use of expensive vegetable oils as raw materials
Biofuels produced by biological conversion
Bioalcohols
Bioethanol.
Bioethanol is the other common first generation biofuel that is generally used as a blend that can go up to 85% content (E85).48 It is the most employed biofuel on a world level with the US currently being the world's largest producer and Brazil the largest exporter, accounting together for 70% of the world's production and 90% of ethanol used for fuel.48 In Sweden and the US, a high-proportion bioethanol blend E85 (85% ethanol and 15% petrol) is being used in Flexible Fuel Vehicles (FFVs) with modified engines that are able to run on either E85 or petrol, or any mixture of the two. The E85 can nowadays also be purchased in several petrol stations in the UK (Fig. 7). Neat ethanol (E100) has also been employed in large scale in Brazil in specially modified engines.
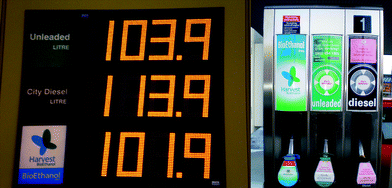 |
| Fig. 7 E85 bioethanol blend can be found at cost-competitive prices in many petrol stations all over the UK (April 2008). | |
The common feedstocks employed for the production of first generation bioethanol are energy crops including sugar cane, corn, wheat, maize and sugar beet (aka ‘food’ crops) although a great potential of grain or sweet sorghums in replacing maize and sugar cane, respectively, has been reported.49
First generation bioethanol is generally obtained by biological conversion involving two key steps: hydrolysis and fermentation, followed by a distillation and dehydration of the bioethanol produced to obtain a higher concentration of alcohol to make it suitable for its use as automotive fuel.
Hydrolysis (saccharification).
The digestion of the feedstock is normally performed via enzymatic hydrolysis using mixtures of amylases enzymes to convert the starch into sugars. Sugar cane and beet directly produce sugars that can be directly fed into the bioreactor.
Fermentation.
The released sugars are subsequently fermentated to ethanol using yeast (e.g.Saccharomyces cerevisiae) using a similar process to that used in beer and wine-making.50,51 The invertase enzymes present in the yeast catalyse the conversion of sucrose into glucose and fructose that are subsequently transformed into ethanol and carbon dioxide by the zymases enzymes (Scheme 3).
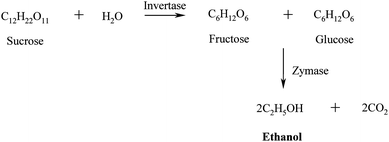 |
| Scheme 3 Production of bioethanol via fermentation of hydrolysed sugars from energy crops. | |
Bacteria strains such as Zymmomonas mobilis have been demonstrated as an alternative to yeasts offering several advantages in the fermentation including higher specific productivity, ethanol yield and alcohol tolerance.3
Properties and advantages/disadvantages of first generation bioethanol.
First generation bioethanol offers a very convenient blend with gasolines for engines due to its higher octane number (over 100), lower cetane number (less than 10) and a higher heat of vaporisation compared to gasoline. Such properties allow a higher compression ratio, shorter burn time and leaner burn engine, which lead to theoretical efficiency advantages over gasoline in an internal combustion engine.52 Bioethanol is also believed to give a 70% carbon dioxide reduction compared to petrol, reducing also the particulate and NOx emissions.50
However, bioethanol has various disadvantages. Firstly, it is hygroscopic and this is possibly the main disadvantage of the use of such biofuel as transport fuel. The blend of bioethanol with gasoline has to take place right before its use. Therefore, storage and distribution issues of the biofuels will arise, putting up the costs of the final product. Secondly, bioethanol has several problems, in terms of physical properties, entailing the automobile engines needing to be modified to be run on a blend containing more than 5 (E5, Europe) to 10% (E10, North America) bioethanol according to the respective EN228 and ASTM D5798 regulations. Bioethanol also has low energy density (over 30% less energy than gasoline, although it can be partly compensated by its better efficiency, reducing it to about 10–12%),50 low flame luminosity and lower vapor pressure than gasoline (making cold starts difficult). It is also corrosive, miscible with water and relatively toxic to ecosystems.50
Biobutanol.
Biobutanol (also denoted as biogasoline) is another interesting candidate that recently entered the battle of the alcohols and has the potential to become one of the key biofuels of the future due to its interesting properties.53–55
The biobutanol is produced via fermentation in which the sugars from the source (so far from edible feedstocks) are firstly converted to butyrate and hydrogen, then turned into butanol via fermentation using various bacteria strains.53 The process has been reported to work with a wide range of bacteria and biomass.53–56 Four main species have been in use, namely C. acetobutylicum, C. beijerinckii, C. saccharoperbutylacetonicum and C. saccharobutylicum. Most data are available from C. acetobutylicum that has been widely employed in the fermentation of starchy raw materials.53
Dupont and BP announced a partnership in 2006 to develop the next generation of biofuels, with biobutanol as first product.55,57 A biobutanol demonstration plant has recently started to be built at an existing BP site in the UK that is expected to start test production of biobutanol by 2009 using sugar beet as feedstock.57 Similar biobutanol pilot plant projects are also ongoing in the US.58
Properties and advantages/disadvantages of biobutanol.
Biobutanol offers a number of potentially significant advantages. It is believed to have around 85 percent of the energy content of gasoline (compared a less than 70% of bioethanol) and the existing engines can run on it without modification (compared to the maximum 85% for bioethanol), one of the reasons why biobutanol is also known as biogasoline. Biobutanol has low vapor pressure therefore it is safe to handle and it would not affect RVP.55 It is also less corrosive and hygroscopic compared to ethanol and therefore less prone to water contamination allowing the possibility of blending within the biorefinery, allowing its implementation in the current infrastructure (tanks, pipes, filling stations). Another key feature of biobutanol is that one of its derivatives, dibutyl ether, may have the potential to be employed as biofuel.53 However, butanol also has some disadvantages. It has low RVP and a low flash point, therefore it is not very safe.54
Biofuel produced by thermo-chemical conversion
Biofuels from fast pyrolysis
Vegetable oils can be employed as fuels for diesel engines, but their viscosities need to be reduced in order to allow their use in such engines without substantial modifications. Different methodologies have been developed to reduce such viscosities including dilution, microemulsification and pyrolysis as well as the already discussed transesterification and catalytic cracking.
Fast pyrolysis involves the breaking down of high molecular weight compounds to smaller molecules by heating at moderate to high temperatures (300–500 °C).59 The vapors generated in the pyrolysis of the oil are condensed and normally two liquid fractions (aqueous and organic) are obtained. The fractions are separated and the organic fraction, containing a wide range of hydrocarbons, is usually analysed and sometimes catalytically upgraded59,60 prior to its use as biofuel. A variety of vegetable oils (e.g. sunflower, castor, soybean, palm) have been employed in the process.59,60
Properties and advantages/disadvantages of biofuels from fast pyrolysis.
Fast pyrolysis of vegetable oils for the production of biofuels is a simple, efficient and inexpensive technology to produce biofuels. Compared to transesterification, pyrolysis has many advantages as the liquid fuel produced in this process has similar chemical components to conventional petroleum diesel fuel and can be used without major modifications as alternative engine fuels. The production costs (due to the expensive raw materials employed, the biofuels obtained are 50 to 100% more expensive than conventional fuel!61), the corrosive nature of the fuels obtained and the variety of product compositions that is highly dependent on temperature and/or catalyst content (for the particular case of biofuel upgrading) are important issues related to the potential commercialisation of such biofuels.
Prospects for 1st generation biofuels
Various interesting conclusions can be drawn from the use of first generation biofuels. Biodiesel, bioethanol and specially biobutanol have many advantages as petrol-fuel replacements but also important disadvantages.
Despite the discussed drawbacks associated to each methodology, the main concern related to the production of first generation biofuels comes from the fact that the conventional biofuel production process generally involves the use of ‘food’ crops. This issue has generated much controversy in a world where the limited area of arable land and grain reserves will contribute to skyrocket the food prices if we carry on using such food crops extensively for biofuel production. That and other issues that arise related to deforestation, global warming and threats to biodiversity, in particular in developing countries (e.g. Malaysia as a consequence of the demand of edible oils [e.g. palm oil]) encouraged the search for alternative technologies and feedstocks for biofuels production.
Second generation biofuels
Alternative feedstocks, generally non-edible feedstocks including waste vegetable oils and fats, non-food crops and biomass sources, and/or technologies are starting to be developed in an attempt to overcome the major shortcomings of the production of first generation biofuels. The biofuels obtained from such technologies have been denoted as second generation biofuels.62 In theory, these can solve these problems and can supply a larger proportion of fuel supply in a more sustainable and reasonably priced way with greater environmental benefits (Fig. 8).
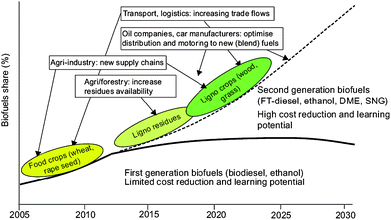 |
| Fig. 8 Road map of potential development pathways for first and second generation biofuels, including implications for different markets. Source: REFUEL. http://www.refuel.eu/fileadmin/refuel/user/docs/REFUEL_final_road_map.pdf. Reproduced with permission of Marc Londo. | |
Several advances have been made in the last few years/months. The majority of the second generation biofuels processing technologies are not yet available on a fully commercial scale so the biofuels are expected to enter the market within a few years. Moreover, the development of many other approaches are currently ongoing and many more are to be reported, so the list included below, far from being exhaustive, provides the most interesting technologies reported until very recently. Second generation biofuels will be classified in various groups depending on the technologies employed for their preparation. In a similar way to those of the first generation biofuels, these are prepared by chemical, biological, and thermo-chemical conversion.
Biofuels prepared by chemical conversion
Biodiesel from non-edible feedstocks (via transesterification)
Biodiesel from non-food crops.
A second type of feedstock becoming relevant for the production of biodiesel is the so-called non-edible raw materials including non-food crops and waste oils and fats. Non-food crops, generally not suitable for human consumption or animal feed, have comparable or even higher oil yields (27–40% w/w) and lower resource consumption (i.e. cultivation inputs) than conventional ‘food’ crops,63 making then specially suitable for a more sustainable biodiesel production, in terms of a more efficient use of resources, minimal interaction with food crops and expected lower environmental impact.64
Examples of these crops including Brassica carinata65,66 and Jatropha curcas64,66,67 for the preparation of biodiesel have recently been reported. Jatropha is a particularly good example of a non-food crop for biofuel production since it thrives on poor soil and land unsuitable for food crops, actually creating topsoil, and gives a high oil yield.
The preparation of biodiesel from non-food crops is very similar to the chemical transformations (transesterifications) previously described for the use of traditional vegetable oils from food crops.
In the summer of 2007, Brazil opened its first commercial Jatropha biodiesel facility (Compahnhia Productora de Biodiesel de Tocantins) with an estimated production of 40
000 tonnes biodiesel y−1 by 2008.67c Some other Brassica and Jatropha projects including pilot plants in India, Africa and South America are also ongoing.
Biodiesel from used vegetable oils (UVO) and fats.
UVO and animal fats are also being considered as very attractive feedstocks for the production of biodiesel due to their lower market value compared to virgin oils and their fact of being recycled materials from other industrial sectors.68 The processing of the oil often requires a reduction of the high FFA content via acid catalysed esterification before the actual raw material can be transesterified to biodiesel.67b
Kulkarni et al. have recently reported the use of a heterogeneous solid acid catalyst that is able to carry out a simultaneous esterification of the free fatty acids and transesterification of the triglycerides, giving high FAME yields.69 Efficient and low energy intentive protocols of the production of biodiesel from waste oils and animal fats combining lipases with alkali catalysts have also been reported.70
Biodiesel from microbial oil (via transesterification).
Biodiesel from algae oil.
Research is currently ongoing into the production of biodiesel from microalgae, which are believe to afford greater oil yields than any known feedstock as has been recently reported.71
Microalgae are sunlight-driven cell organisms that convert atmospheric CO2 (via photosynthesis) into a plethora of chemicals including methane, hydrogen, polysaccharides and oil.71,72 The production of microalgal oil is remarkably more efficient compared to conventional oil crops, providing higher oil yields (up to a 75% dry weight) and lower land area utilisation (Tables 1 and 2).
Table 1 Microbial oil content (% dry weight) of various algae species71
Microalgae |
Oil content (% dry wt) |
Botryococcus braunii
|
25–75 |
Chlorella sp. |
28–32 |
Cylindrotheca sp. |
16–37 |
Nannochloropsis
|
31–68 |
Nitzschia sp. |
45–47 |
Schizochytrium sp. |
50–77 |
Table 2 Comparison of oil yield vs. required land for different biodiesel feedstocks in the US71
Crop |
Oil yield/L ha−1 |
Required land/M ha−1a |
To meet 50% of all US current transport consumption.
70% (w/w) oil yield in biomass.
30% (w/w) oil yield in biomass.
|
Microalgaeb |
136 900 |
2 |
Microalgaec |
58 700 |
4.5 |
Oil palm |
5950 |
45 |
Jatropha
|
1892 |
140 |
Canola |
1190 |
223 |
Soybean |
446 |
594 |
Corn |
172 |
1540 |
The process involves the extraction of the oil from microalgae and subsequent transesterification with alcohols using homogeneous or heterogeneous catalysts (in a similar way to that of biodiesel obtained from (non) edible feedstocks) to give biodiesel.
Significant advances in the field have recently been reported with biodiesel from microbial oil. Cellana, a joint venture of Shell and HR Biopetroleum started the construction of a pilot facility in the Kona coast of Hawaii Island to grow algae as biofuel feedstock.73
Biodiesel from other microbial oils.
Many reports can be found on the subject using different microbes including various yeasts and bacteria.74 A summary of the main reported microorganisms and their respective oil yields has been included in Table 3.
Table 3 Oil production (oil content and yield) of different microorganisms grown on various carbon sources74
Microorganism |
Carbon source |
Biomass/g L−1 |
Oil content (%) |
Oil yield/g L−1 |
Ref. |
Trichosporon fermentans
|
Molasses |
36.4 |
35.3 |
12.8 |
74a
|
Lipomyces starkeyi
|
Sewage sludge |
9.4 |
68.0 |
6.4 |
74b
|
Mortierella isabellina
|
Starch |
10.4 |
36.0 |
3.7 |
74c
|
Pectin |
8.4 |
24.0 |
2.0 |
74c
|
Cunningamella echinilata
|
Starch |
13.5 |
28.0 |
3.8 |
74c
|
Pectin |
4.1 |
10.0 |
0.4 |
74c
|
In general, the cultivation of such microorganisms is not dependent on seasons or climate. They can also be easily grown on a variety of inexpensive substrates including waste residues from agriculture and industry,74b providing they have the nutrients needed for the microorganisms.
Properties and advantages/disadvantages of biodiesel from non-edible feedstocks.
Second generation biodiesel has very similar properties to those of first generation biodiesel, without significant differences between edible and non-edible feedstocks. A reduction in the NOx emissions of the biodiesel obtained from used oil has also been reported,75 although some authors highlight the larger fumes production with the use of UVO as feedstock.76 Most importantly, the use of cheap feedstocks (e.g. waste oils and fats) and the potential commercialisation of glycerol (and glycerol derived products) considerably reduces the biodiesel production costs, especially taking into account that 70–90% of the biodiesel cost arises from the cost of the oil.77 However, the use of high temperatures in the transesterification, incomplete conversion and variability of the incoming feedstock (with marked differences in water content and FFA depending on the source, location and usage) are problems related to such feedstocks for biodiesel production.
The production of methyl esters from algal oil has recently attracted a great deal of attention. The enormous diversity of species of algae with high oil content that require tiny land utilisation compared to oil crops offers an interesting possibility of industrial exploitation of such organisms in the production of biodiesel.
However, there are major limitations in their successful implementation, the economic feasibility of the technology being the most important. Firstly, the recovery of such bio-oil from algae is a very challenging task. The algal broth produced in the biomass production generally needs to be further processed to recover the biomass78 and then the concentrated biomass paste is extracted with an organic solvent (e.g. hexane) to recover the algal oil that can be transesterified into biodiesel.
Secondly, microalgal oil is rich in long-chain polyunsaturated acids including eicosapentaenoic (20:5 n-3, EPA) and docosahexaenoic acids (22:6 ω-3, DHA) which are generally undesirable in conventional biodiesel due to the negative impact of the polyunsaturations on oxidation stability. The presence of EPA and DHA is not contemplated in the EU (EN 14214 and EN 14213, biodiesel for transport and heating) and US (ASTM D6751) quality biodiesel standards that specify a limit of 130 g (EN 14213) and 120 g (EN 14214) iodiene per 100 g biodiesel (iodine value). The storage issues arising from the oxidation instability may either be overcome through chemical transformations (e.g. hydrogenations) of the polyunsaturated compounds.79 It is yet unclear how the presence of much more saturated FAME will affect cold performance (CFPP) of the biodiesel
These main drawbacks will undoubtedly put up the costs of an already costly process in which problems related to capital infrastructure costs, contamination through open pond systems and costs associated with harvesting, drying and valorisation of the rest of the algae may also have a major contribution. A full and precise estimation of the economics of the process, that have been argued to be far too good from what Chisti et al.71 originally reported, is needed in order to demonstrate its feasibility.72,78
Biofuels from catalytic cracking
Several feedstocks and catalysts have been employed for the preparation of biofuels46,80–83 in the so-called biomass-to-liquid (BTL) process. Corma et al. and Dumesic et al. have recently reviewed the technologies and feedstocks for the catalytic cracking of biomass to produce fuels and chemicals.80
Transition metal catalysts, common materials in the hydroprocessing industry, under high hydrogen partial pressures yield diesel-type biofuels46 while molecular sieves (e.g. zeolites and mesoporous materials from the M41S family including MCM-41 and MCM-48 patented by Mobil) afford gasoline-like fuel with higher aromatic content.80,83 Feedstocks including TG, waste oils and fats, cellulosic feedstocks, urban and municipal waste have been reported.46,80,84
Properties and advantages/disadvantages of biofuels for catalytic cracking.
As mentioned for the first generation biofuels from catalytic cracking, the technologies are relatively simple and inexpensive. An important advantage is that the raw materials used are also inexpensive (e.g. waste oils, cellulosic biomass) as compared to first generation feedstocks. However, the efficiency of the process using crude feedstocks (with variable compositions) and biomass needs to be addressed.
Biofuels produced by biological conversion
Bioalcohols
Bioethanol.
Second generation bioethanol is usually produced from a range of alternative readily abundant and inexpensive, cellulosic biomass feedstocks including woody biomass, grasses, forestry and agricultural waste.85 Very interesting reviews about the progress in bioethanol and lignocellulosic processing have been recently reported.50,86
An overview of the production routes of second generation bioethanol is included in Fig. 9.
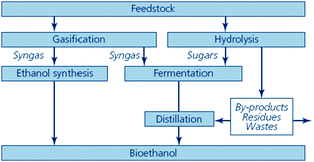 |
| Fig. 9 Thermochemical and biological routes to second generation bioethanol (source: Sustainable biofuels: prospects and challenges, RS Policy document 01/08, ISBN 978 0 85403 662 2. Reproduced with permission of The Royal Society). | |
The process (Fig. 9, right hand side) is identical to that described in the production of first generation bioethanol: decomposition of the material into fermentable sugars (hydrolysis) and transformation of the sugars into bioethanol (fermentation).
The main changes are the processing technologies and the feedstocks that usually account for the majority of the plant cost. Cellulosic biomass comprises of two main components; cellulose and hemicellulose (complex carbohydrate polymers), accounting roughly for about a 70–75 wt% of the lignocellulose. A mixture of enzymes (cellulases and hemicellases) different from those of the first generation bioethanol production are employed in the hydrolysis step. In the particular case of lignocellulosic (woody) materials, lignin is obtained as a by-product of the process. Lignin can be burned to produce heat and power for the processing plant and potentially for surrounding homes and businesses and it is hoped that it can become a future source of aromatic chemicals and materials. Alternative organisms also need to be employed due to the impossibility of the traditional yeast and bacteria to process the pentose (C5) sugars derived from hemicellulose.87
Branched alcohol mixtures.
The preparation of a branched-longer chain alcohol mixture with a potential use as biofuel has been recently reported by Liao et al..88 Such an alcohol mixture with high isobutanol content is produced via synthetic non-fermentative pathways employing metabolic engineered bacteria (e.g.E. coli) and glucose as carbon source. This strategy diverts the 2-ketoacid intermediates in the aminoacid biosynthetic pathway of E. coli for alcohol synthesis, converting them into aldehydes (by 2-ketoacid decarboxylases) and then to alcohols (by alcohol dehydrogenases).88 The process has already been licensed to Gevo (spin-off company from Pasadena, US) that hopes to begin commercial scale production within a few years.89
Properties and advantages/disadvantages of bioalcohols.
Second generation bioethanol offers several improvements with respect to first generation bioethanol. It can reduce GHG emissions in around 90% compared with fossil fuels,50 providing greater savings than those obtained with first generation bioethanol (over 60% reduction). However, the development of an efficient pre-treatment process in order to break up the fibre structure of the biomass is needed because the methodologies investigated (mechanical, thermal, chemical, enzymatic-cellulase and various combinations) have been proven to be unsuitable due their high costs, low yields, produced waste or undesired by-products. Secondly, an efficient microorganism for the fermentation of pentoses, present in hemicellulose, needs to be developed. Therefore, there is a need for a joint effort from chemists, microbiologists and chemical and biochemical engineers in order to demonstrate the potential of the second generation bioethanol.
Branched-mixed alcohols have interesting properties as biofuel due to their higher energy density and lower hygroscopicity as well as higher octane numbers compared to their linear chain counterparts (e.g. bioethanol). The reported strategy also opens up many interesting possibilities for biofuels production as more user-friendly microorganisms (e.g.Saccharomyces cerevisiae) are readily applicable.88 Furthermore, it enables the exploration of biofuels beyond those naturally produced in microbial fermentation (e.g. in the production of bioethanol).
Biogas
Biogas is an environmentally friendly, clean, cheap and versatile fuel, composed of a mixture of CH4 and CO2 that is usually generated from bacterial digestion of biomass in the absence of air between 10–72 °C.90,91 Almost any type of organic matter (e.g. sewage sludge, animal wastes, industrial effluents) is suitable for the production of biogas, which can be directly utilised in cooking and heating systems.92 The process is carried out in anaerobic digesters that can vary in size from 1 m3 (small household unit) to as large as 2000 m3,93 involving a step-wise series of reactions that require the cooperative action of several microorganisms. Initially, a group of microorganisms (acidogens) break down the organic matter into a digestible form (usually simpler fatty acids) that can be utilised by methane-generating anaerobic bacteria (methanogens) that produce biogas as a metabolic by-product.94
The use of biogas as transport fuel has been explored in its application in explosion engines. Biogas has shown a great potential for its uses in Brazil,95 and in places such as Sweden it has been used in urban buses since 2004.96 Also in Sweden, some studies have evaluated the economic and environmental feasibility of biogas as a renewable source of energy in large scale showing positive results in its applicability CHP (centralised heat and power).97
Properties and advantages/disadvantages of biogas.
Biogas might be of relevance in renewable energy markets both for transport and for generation of electricity. It is also a realistic alternative to the accumulation of waste in landfills as new sites can be specially configured to optimise gas output (as high as 1000 m3 h−1 biogas). However, LCA studies have identified an impact to GHG in its production, associated to the generation and emission of CO2 and N2O in the process.97
Biohydrogen
Various authors have recently reviewed the prospects and potential in the production of biohydrogen.98–100 Biohydrogen can be produced by three different biological pathways: fermentation and direct or indirect (bio)photolysis.
Fermentation.
Dark and photo fermentation are technologies under development (currently at lab scale) to produce biohydrogen from wet biomass (e.g. molasses, organic wastes, sewage sludge) using (an)aerobic hydrogen fermenting bacteria.100,101 The advantage of dark fermentation is that the biohydrogen is produced directly without formation of methane.98c,100 During dark fermentation, various organic acids are also produced. These compounds can subsequently be converted to hydrogen by a process denoted as photo fermentation.
Direct photolysis.
In this approach, the process takes advantage of the photosynthetic capability of algae and cyanobacteria to split water into O2 and H2via direct absorption of light and transfer of electrons to two groups of enzymes that participate in biological hydrogen metabolism: hydrogenases and nitrogenases.99
Indirect photolysis.
Alternatively, biohydrogen can be prepared through the use of some microorganisms (algae) that can directly produce hydrogen under certain conditions.98,99 Most specifically, sealed cultures of green algae become anaerobic in the light under deprivation of sulfur nutrients and spontaneously induce the “hydrogenase pathway” to photosynthetically produce hydrogen.98c Substantial rates of hydrogen production were obtained over 60 h in the light although the hydrogen production leveled off reaching a point (after 100 h) in which the algae go back to the normal photosynthetic pathway in order to restore the consumption of internal starch and proteins that takes place in the course of the hydrogen production.102
Properties and advantages/disadvantages of biohydrogen.
Biohydrogen is believed to be one of the biofuels for the future, combining its ability to potentially reduce the dependence of foreign oil and contribute to lower the GHG emissions from the transportation sector. However, storage (biohydrogen has to be compressed, liquefied, or stored in metal hydrides), transportation and use (fuel cell vehicles are not commercially available yet and a distribution infrastructure for hydrogen cannot be realised in the short term) as well as the technological advances needed for its successful implementation limit biohydrogen only as a longer-term option for the transport sector.
Biofuels produced by thermo-(chemical) conversion
Biofuels included under this headline are also prepared from various non-edible biomass feedstocks. Thermo-chemical conversion pathways include processes such as gasification and pyrolysis (Fig. 10).80,90
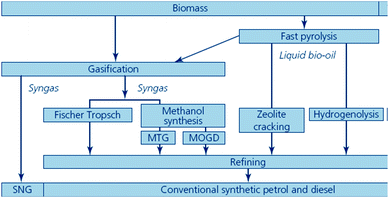 |
| Fig. 10 Biomass gasification and pyrolysis routes to synthetic biofuels (source: Sustainable biofuels: prospects and challenges, RS Policy document 01/08, ISBN 978 0 85403 662 2. Reproduced with permission of The Royal Society). | |
The process involves the partial combustion of the feedstock to produce syngas (a mixture of carbon monoxide (CO) and hydrogen (H2) denoted as bio-synthetic natural gas, bio-SNG) via conventional or alternative gasification processes. Then, bio-SNG is subsequently transformed into liquid hydrocarbons (mostly diesel and kerosene-type fuels) and/or gases via different processes, leading to a variety of biofuels that will be outlined. Such prospective liquid/gas biofuels for transport (Fig. 10) include bioalcohols (methanol, ethanol and linear higher chain alcohol mixtures) and synthetic biofuels.
At this point, it is worth mentioning that although bio-SNG could be classified as synthetic biofuel, it comes first since all the reported biofuels from gasification are obtained from it and thus the technologies (up to the preparation of the syngas) are very similar.
Bio-SNG.
Bio-SNG can be produced by a conventional gasification process (methanation) at high temperatures (800–1000 °C) aiming at producing large quantities of methane. The current technology employed allows the use of a wide range of biomass feedstocks including wood chips and waste wood.103,104 The conventional gasification process involves various steps (Scheme 4).104b Firstly, the biomass undergoes endothermal steam gasification (reaction 1) to give a mixture of CO and H2, which is subsequently converted into methane, CO2 and hydrogen (reactions 2 and 3). The net overall reaction from biomass to methane and CO2 (reaction 4) is slightly exothermic. However, the main drawback of the conventional gasification technology is the formation of tars and char.61
 |
| Scheme 4 Reactions involved in the conventional gasification of biomass. | |
Interestingly, the gasification of biomass can be performed at lower temperatures (250–400 °C) in supercritical water. It has currently been reported at lab scale, employing different Ni and Co based catalysts.104 In this process, the biomass disintegrates in supercritical water forming a mixture of carbon dioxide, carbon monoxide and methane (SNG). The technology is expected to be especially suitable for wet (polluted) biomass and has higher efficiency than the conventional gasification process at a lower temperature.104b Bio-SNG can also be produced from biogas.
Various projects in the Netherlands, including the largest existing bio-SNG plant located in Buggenum, currently produce bio-SNG from the co-gasification of biomass with coal at different proportions.105
Properties and advantages/disadvantages of bio-SNG.
Bio-SNG has various advantages and disadvantages. Its octane number is very high, but the cetane number is very low, which means that bio-SNG has to be used in spark ignition engines, which have to be adapted for the use of bio-SNG. Storage is also an issue for bio-SNG as it is also a gas at room temperature so it needs to be compressed or liquefied to be used as an automotive fuel. Furthermore, larger storage and fuel tanks are needed due to the lower volumetric energy content of the fuel.
The supercritical water low-temperature gasification technology may overcome the main technological barriers in the process. Still, gas cleaning (especially tar removal) and catalyst development are important technological issues, although if active and selective catalysts are used (e.g. Ru/C), no significant quantities of tars or char are formed.104b However, the cost of the supercritical water production of bio-SNG is several times higher than that of the conventional gasification process.106
Bioalcohols.
Biomethanol.
Biomethanol can be produced from synthesis gas106via conventional gasification of biomass (partial oxidation) at high temperatures (800–1000 °C) and subsequent catalytic synthesis of the CO + H2—in a 1 : 2 ratio—under high pressures (4–10 MPa).106,107
The biofuel can be blended with petrol up to 10–20% without the need of any engine modifications.107 Several feedstocks including bark, woodchips, bamboo, waste wood and pulp106,107 and even glycerol108 have been reported to be used in the process.
There are a few biomethanol pilot plants under development, mainly in the US (e.g. North Shore Energy Technologies, 40 MMgy plant) and Japan (e.g. Norin Green no1, MAFF and Mitsubishi heavy industries).107a
Bioethanol.
Bioethanol can also be obtained via conventional thermal gasification of biomass to syngas combined with catalytic processes in a similar way to those for the production of biomethanol (Fig. 9, left side).3
Alternatively, following biomass gasification, the syngas can be directly fermented to ethanol using anaerobic bacteria (Fig. 9).109 This eliminates the need of the hydrolysis step to break up the cellulose and hemicellulose fractions of the biomass. The lignin fraction can also be converted into ethanol. The process has been reported at lab scale and is still under development.3,109 However, the efficient delivery of the syngas to the microorganisms still remains a challenge.3
There are some examples of ongoing industrial processes. An operating lignocellulosic bioethanol production plant is located in Ottawa (Canada), run by the IOGEN Corporation.110 The demonstration plant produces up to 3 million litres of bioethanol per year. The feedstocks employed are wheat, oat and barley straw. A bioethanol plant in Ulmea (Sweden) is running using waste stream of cellulose-based materials and another pilot plant production for the preparation of bioethanol from lignocellulosic materials (e.g. Norway Spruce) has recently started production.111
Linear bioalcohol mixtures.
Mixed linear alcohols (i.e., mixtures of mostly ethanol, propanol and butanol, with some pentanol, hexanol, heptanol and octanol) can also be produced from syngas in a similar way to that described for methanol and ethanol.112 One of these linear alcohol mixtures denoted as Ecalene™ is currently registered with the US Environmental Protection Agency per 40 CFR 79.23 as a fuel blending additive.112
Properties and advantages/disadvantages of bioalcohols.
Biomethanol is considerably easier to recover than bioethanol as it does not form an azeotrope with water like ethanol. The technology to prepare biomethanol from syngas has been reported to be in place, requiring efficiency improvements and scale up to make methanol an economically viable transportation fuel.113 However, biomethanol suffers from severe shortcomings including a low vapour pressure, low volumetric energy density (about half of that of petrol), toxicity (methanol is highly poisonous), high flammability and the incompatibility with engines except at relatively low biomethanol content.
In terms of properties, bioethanol obtained from gasification of biomass does not have significant differences compared to that obtained by biological conversion. However, the processes are remarkably dissimilar. The conventional gasification step is a costly process compared to the relatively inexpensive biological conversion. Nevertheless, the biomass feedstock can effectively be turned into syngas (without the need of any microorganisms) and subsequently into bioethanol in a simple catalytic reaction similar to that of biomethanol.3 Compared to bioethanol produced by biological conversion, this protocol avoids issues such as the inefficient degradation of biomass to fermentable sugars as well as dealing with the processing of the pentoses (C5) generated in the hydrolysis of biomass.
The mixture of linear alcohols has superior energy content compared to biomethanol or bioethanol, lower heat of vaporisation (essential for cold starts) and increasing compatibility of the ethanol-gasoline in a blend due to an improved water tolerance and a decrease in gas emissions. The main problems are the costly gasification technology as well as the lack of standards for producers and users.
Synthetic biofuels.
Synthetic biofuels can be defined as fuels prepared from syngas via different processes. Bridgwater and Demirbas have recently reported comprehensive overviews of the development of these technologies for the preparation of biofuels.61,106
Under this headline we can include a selection of some interesting options such as bio-dimethylether (bio-DME), biofuels obtained by steam reforming, biofuels obtained via HydroThermal Upgrading (HTU) and biofuels produced via Fischer–Tropsch Synthesis (FTS).
Bio-DME.
DME derived from fossil fuels was mainly employed in the past as a substitute propellant for chlorofluorocarbons (CFCs) in spray cans.114 DME is a liquefied gas that can be produced from a variety of feedstocks including residual oils, organic waste and biomass.114
Bio-DME can be directly produced from syngas in a process that is very similar to that of biomethanol.3 Alternatively, it can be produced from biomethanol via catalytic dehydration using slightly acidic catalysts including γ-Al2O3115 and ion exchange resins116 at temperatures ranging from 100–400 °C depending on the methodology employed.3,115,116
Biofuels obtained by steam reforming.
Steam reforming can be applied to various solid waste materials including organic waste, sewage sludge, waste oils, black liquor and agricultural waste to produce biofuels.106 Steam reforming of natural gas (often referred as steam CH4 reforming) is the most common method to produce commercial H2.106
Biohydrogen can therefore be produced from a biomass feedstock via conventional gasification at high temperatures to syngas to obtain methane (reaction 4, Scheme 4) and subsequent steam CH4 reforming at high temperatures (700–1100 °C) using Ni supported catalysts (e.g. Ni/Al2O3, Ni/MgO) at 3–25 bar pressure (Scheme 5, reaction 1).106,117 For the production of high purity H2, the reforming of the biofuel that includes multiple catalytic steps is followed by two water gas-shift (WGS) reaction steps (Scheme 5, reaction 2), a final CO purification and removal of the remaining CO2 by pressure swing adsorption or ceramic membrane separation.106,117
 |
| Scheme 5 Steam CH4 reforming (1) and WGS (2) reactions for the preparation of biohydrogen. | |
Alternatively, the gasification step of biohydrogen can also be performed in supercritical water (in a similar way to that of the bio-SNG) with the advantages of the direct use of wet biomass without drying and a high gasification efficiency at lower temperature.106,118 However, the cost of H2 production using this technology is several times higher than the current price of H2 obtained from steam reforming.106
Biofuels obtained via HydroThermal Upgrading (HTU).
HTU-diesel can be produced from various feedstocks including dry (wood and lignocellulose)119 and wet (beet pulp, sludge or bagasse) biomass.120,121 This methodology involves the hydrothermal treatment of biomass that is converted into a mixture of hydrocarbons at relatively low temperatures (250–350 °C) and moderate (autogenous pressure)119 to high (120–180 bar) pressures.120
The biocrude obtained is a heavy organic liquid immiscible with water that contains a wide range of hydrocarbons including acids (e.g. acetic acid), alcohols (e.g. isopropyl alcohol) and phenolic derivatives (in the particular case of lignocellulosic materials).119–121 Often, the obtained hydrocarbon mixture needs further processing (via catalytic hydro-de-oxygenation [HDO]) to yield a liquid biofuel similar to fossil diesel that can be blended with fossil diesel in any proportion without the necessity of engine or infrastructure modifications.121 HTU research has been mainly performed in The Netherlands, with an HTU demonstration plan in Amsterdam that is able to generate over 12
000 tonnes of biocrude (including ash) per year.120
Biofuels obtained via Fischer–Tropsch Synthesis (FTS).
The Fischer–Tropsch (FT) process is one of the advanced biofuels conversion technologies. It has been known since 1923 when German scientists Franz Fisher and Hans Tropsch aimed to synthesize long-chain hydrocarbons from a CO and H2 gas mixture, but it was mainly used in the past for the production of liquid fuels from coal or natural gas.122
Prior to the FTS, the gasification of biomass feedstocks takes place in a similar way as that described for the production of bio-SNG, to obtain syngas (Scheme 4). Then, a cleaning and conditioning step of the produced syngas is normally performed to remove all the impurities present prior to the catalytic reaction to minimise the poisoning of the catalyst.123
The FTS process is then carried out. It comprises of various steps described by the set of equations in Scheme 6, where x is the average length of the hydrocarbon chain and y is the number of H2 atoms per carbon.
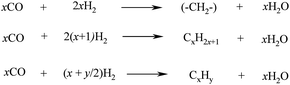 |
| Scheme 6 FTS reactions for the production of linear long-chain hydrocarbons. | |
The first step involves the reaction of CO with H2 in the presence of a Co or Fe catalyst (Scheme 5, top reaction) to afford a hydrocarbon chain extension (–CH2–) that is a building block for the formation of longer hydrocarbons. Typical operation conditions are temperatures between 200–400 °C and 15–40 bar pressures, depending on the process.106,122
All reactions are exothermic and the product is a sulfur free mixture of different predominantly linear hydrocarbons (primarily alkanes and alkenes) that frequently undergoes upgrade and refining steps to be turned into automotive fuels, namely FT-diesel (main product) and gasoline-like biofuels (by-products).106 The FT catalysts are mainly based on iron and cobalt.106,122,124 Cobalt catalysts have the advantage of a higher conversion rate and they are also more reactive in hydrogenation, producing less unsaturated hydrocarbons and alcohols compared to iron catalysts that produce higher alkenes and oxygenates content.106,122
The process using biomass as feedstock is currently under development. In theory, there are no restrictions in the type of biomass that can be used as feedstock. Woody and grassy materials and agricultural and forestry residues have been investigated in the process.123,125
Pilot production facilities for Fischer–Tropsch liquids from biomass are currently in operation in Germany and the Netherlands.105
Properties and advantages/disadvantages of synthetic biofuels.
Synthetic biofuels have several advantages as they can be used in unmodified diesel engines (with the exception of bio-DME)105,106 and they are cleaner that traditional fuels due to the removal of all contaminants to avoid the poisoning of the catalysts used in the processing steps.3,123
Synthetic biofuels can have excellent autoignition characteristics (except bio-DME that has a low-self-ignition temperature and lower volumetric energy content) as they have similar energy content, density and viscosity than of fossil diesel as well as a higher cetane number and lower aromatic content (which results in lower particle emissions). They are also S-, N-free and less corrosive than other biofuels (e.g. bioethanol and biodiesel) therefore being more environmentally friendly than fuels produced from crude oil. Some of them (e.g. FT-diesel) have been proved to reduce the CO, NOx and particulate matter compared to diesel fuel.105,124
However, the production of synthetic biofuels faces a similar technological barrier to that of the listed gasification-derived biofuels (i.e. bioalcohols and other synthetic biofuels): the production of the synthesis gas has to be adapted to the higher reactivity and different properties of biomass with respect to coal. This includes two key steps in the process that need thorough improvements: biomass pre-treatment (via torrefaction and/or pyrolysis) to avoid the aggregation of the biomass particles that can plug the feeding lines and economically viable inferior temperatures of gasification (e.g.via supercritical water gasification) that have been reported to provide higher efficiencies.
For instance, the FTS biofuel production can be more cost effective reducing both the capital and the operating costs of the plant,126 being the purification of the syngas the most expensive section to take into account for costs in an FT plant. The development of active and selective catalysts and the utilisation of by-products including electricity, heat and steam are some other inputs that need to be addressed.
Biofuels from fast pyrolysis
Fast pyrolysis is an attractive alternative to gasification to convert biomass into more valuable chemicals and fuels (Fig. 10). This process involves the thermal decomposition of biomass in extremely short periods of time to obtain a solid residue (char) and hydrocarbon-like mixtures (bio-oils) of higher value-added chemicals (e.g. carboxylic acids, ketones, aldehydes and aromatics). Fast pyrolysis usually is a pre-treatment step to increase the energy density of biomass in further combustion or gasification processing as the dark viscous liquid obtained after cooling and condensation has a heating value about half of that other conventional fuels.61,94a
A fast pyrolysis process involves several steps including feedstock drying (ideally leaving less than 10% water content to minimise the water in the bio-oil) and grinding (to provide sufficiently small particles to ensure a rapid reaction), thermal decomposition, separation of char and collection of the final product (bio-oil).
Almost any form of biomass can be considered for fast pyrolysis. Wood forestry and agricultural waste have been largely explored.61,94a Lignocelluloses, hemicellulose and other types of biomass break down through thermal treatment in absence of air. The conversion takes place at temperatures between 450–550 °C at high heating rates, (103–104 K s−1), followed by rapid condensation of the vapours, being solid char and bio-oil (up to 80% yield) the final products of the process, with a considerable water content.46,61 The heating rate, much higher than in conventional pyrolysis, is essential in order to optimise the process to the desired products, where lower values of heating rate will generate a larger amount of tar than volatiles, as it does in conventional pyrolysis.127
Alternatively, microwaves might be a realistic option for optimised compositions of bio-oil, attempting to minimise downstream upgrading processes. Other feedstocks have also been studied, vegetable (waste) oils and algal biomass being the most significant. The use of TG yields a bio-oil with relatively similar properties to that of the feedstock at temperatures between 300–500 °C with portions of such liquids having similar properties to that of diesel fuel.46,128 The bio-oil obtained is either normally gasified or refined in conventional petrol refineries.
Algae have also a great potential. The bio-oil yields obtained from algae are lower than those of terrestrial crops and a higher tar yield is produced. The proportion of aromatic compounds is also lower to that of wood and straw due to the absence of lignin in algae.129 The studies made in microalgae showed a lower oxygen content and a higher heating value than wood.130
Properties and advantages/disadvantages of biofuels from fast pyrolysis.
Fast pyrolysis for the production of biofuels has some advantages. In general, it is a simple and inexpensive technology. It also has the potential to build up an infrastructure of multiple biomass pre-treatment plants where the bio-oil could supply feedstock for gasification and combustion processes.131 In this way, transport costs could be reduced up to 87%.3,131
Some of its limitations are the mentioned corrosive nature of bio-oil due to its acidity, the presence of impurities such as salts and solids (especially in marine biomass) plus the generation of aromatic toxins. The high acidity, water content and variable viscosity of the mixture is a limitation for its stability, complicating its processing and direct use.81 The high oxygen content of the mixtures considerably decreases density energy, which is 40% less compared to fuel oil.46 In this regard, further downstream processing is usually required to lower the oxygen content to optimise and stabilise the composition of the bio-oil for higher aptitudes as fuel. Processes such as hydro-treatment (to reduce water and oxygen content)132 hydro-cracking133 (analogous to the conventional refinery), emulsification with mineral diesel for direct use134 and steam reforming135 (to produce hydrogen as in natural gas) are some of the key technologies employed.
Economically, the cost of bio-oil is 10 to 100% more expensive than fossil fuel61 and therefore the scaling-up of the technology needs to reduce costs to turn the process economically viable. An improvement of the product quality ensuring norms and standards for producers and users (due to its current lack of standards for use and distribution) is also required.
Prospects for 2nd generation biofuels
Production of biofuels from second generation biofuels from non-edible feedstocks have interesting features. Non-food crops can be cultivated in alternative lands including the so-called “wastelands”, tropical zones or even arid regions as they are more likely to proliferate at relatively extreme conditions (e.g. plagues and dry environments) with a low fertiliser input. Many of the biomass feedstocks are also self-seeding crops (they do not need to be planted and re-seeded after being harvested) and require little or virtually no fertilizer input. These approaches can therefore be applied to “marginal lands” where the soil cannot/should not support food crops.136 In this way, they will not interfere with the land dedicated to food crops.
They can also provide a solution for the production of quality biofuels in developing countries (e.g. India) where, for example, a blend of biodiesel obtained from jatropha and palm has been reported to have the right balance of physical properties conferring the product with an adequate cold low performance and oxidation stability,63 also falling within the acceptable limits by the American and European biodiesel standards.67b
However, the switch to these non-edible feedstocks poses various concerns. The cultivation patterns of the crops are still under investigation and early studies have shown relative differences depending on the approach taken to crop cultivation and oil production management.137 The crops have only been employed by local communities for different uses (e.g. soap production and natural crop protection for the inedible nature of the oil and toxicity of the seeds, respectively).138 Therefore, the evaluation of the sustainability index needs more data to estimate the real global impact of these crops. Another important issue in the production of biofuels from non-food crops deals with their cultivation in poor soils which imply lower productivities and hence higher costs of production.
Furthermore, the technologies available for the majority of the second generation biofuels are still in their infancy and need major developments to be able to sustain a scaled-up production of biofuels for transport. The economics of the processes may play a key role in the successful implementation of many of these technologies as we will discuss in the next chapter.
Discussion around biofuels
The biofuels field is expanding and evolving on a daily basis. We are aware that some of the trends and areas of this perspective may have changed by the time the readers are able to go through it due to changing government policies, financial incentives, technological breakthroughs, market prices as well as socio-economic and environmental issues. However, we can say that the future of biofuels is far from clear and involves complex and dynamic social, economic and environmental issues. Rather than giving a full technical study about biofuels issues, we aim to focus on ongoing discussions around biofuels and their impact in all aspects of our society.
Use of fossil fuel and raw materials to produce biofuels
The whole life-cycle of the production of biofuels involves the use of fossil fuel and raw materials to some extent. Whether the net gain balance out of the fossil input obtained in terms of low emissions is positive or not remains under discussion. Few comparative studies can be found for the production of ethanol (from various crops including corn, sugarcane and cassava139,140) and biodiesel (from oilseeds141) in different locations. For instance, the production of bioethanol from corn was reported to have half of the net value of energy recovered from the fossil input compared to that of the ethanol obtained from sugarcane and cassava. Sheehan et al. also found that the replacement of petroleum diesel for neat biodiesel (B100) in buses reduced the consumption of oil in the whole life cycle by 95%.141 Janulis found a reduction of around 80–86% fossil usage and net GHG emissions using biodiesel from rapeseed with respect to petrol-diesel.142 However, these promising figures have been taken from a limited number of studies in very specific locations and they cannot be generalised.
Availability of land for fuel. The food vs. fuel issue.
The available land to produce virgin crops is a major limitation for first generation biofuels. For instance, based on the DEFRA estimations,140,143 the 1.73 Mha easily available land in the UK for biofuel production (around 10% from total agriculture land) will struggle to meet the 5.75% bioethanol/biodiesel blend EU target (estimated in 1.75 Mha) set for 2010.144 This is also the case for many countries worldwide.
Current biofuel producers do not always have a secure access to raw materials due to limited grain reserves and the fact that the current costs of crude vegetable oil from ‘food crops’ are variable. This has a major impact on the production of first generation biofuel since the price of the feedstock is the major input cost (70–90% of the total operating cost).77 Biobased energy industries are also currently in competition with food producers and we perceive them as being a primary cause of the increase in food prices.
In order to make biofuel production profitable and more sustainable, avoiding as much as possible competition with the food market, companies have to focus on second generation biofuels made from alternative cheap feedstocks (e.g. (waste)biomass, waste oils and fats, residues, etc.). (Ligno)cellulosic ethanol and biodiesel from either waste oils, non-food crops or algae emerge as real alternatives to tackle this problem (Fig. 11).
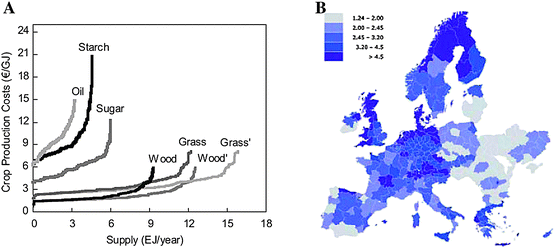 |
| Fig. 11 (A) First vs. second generation energy crop production cost/supply. Wood and grass refer to the potential on arable land. Wood' and grass' refer to potential of both arable and pasture land. (B) Distribution of biofuel production costs from lignocellulosic materials (€/GJ). Source: REFUEL. http://www.refuel.eu/fileadmin/refuel/user/docs/REFUEL_final_road_map.pdf. Reproduced with permission of Marc Londo. | |
The implementation of such alternatives might considerably improve the figures. Extensive second generation biofuels production can also intensify and change land use and consequently have environmental, economic and social impacts which are not easy to predict.
However, the food vs. fuel issue is far more complex than has generally been presented since agricultural and export policies and the politics of food availability are factors of far greater importance and biofuels are only “part of the problem” but not “the problem” itself. The argument should be analysed against the background of the world's (or an individual country's or region's) real food situation of food supply and demand (ever-increasing food surpluses in most industrialized and a number of developing countries), the use of food as animal feed, the under-utilized agricultural production potential, the increased potential for agricultural productivity, and the advantages and disadvantages of producing biofuels.145
Environmental impact.
Despite the fact that some studies carried out to date show first generation biofuels may offer a low carbon balance, fossil fuel usage and GHG balance, further outputs and environmental indicators must be addressed. Water usage (in the growth of the crops), eutrophication (run off of lawn fertilisers into natural waters) and soil erosion are some of them. Moreover, intensive monoculture farming may have an impact on ecosystems and biodiversity,146 to a higher extent if genetically modified crops are widely spread.136 Deforestation as a consequence of the replacement of the tropical rainforest for fuel-crops (e.g. the Malaysian case) will also have a major impact in biodiversity and climate change (Fig. 12).147 Nevertheless, it is difficult to predict the overall environmental impact of biofuels consumption in the future at this stage of development of the various biofuels technologies.
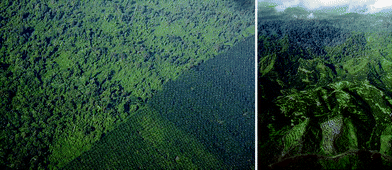 |
| Fig. 12 Aerial photographs of oil palm plantations (left photo, bottom) encroaching on natural rainforest (left, right photos, top) and deforestation in Malaysia. Source: Rhett Butler, http://www.mongabay.com/. | |
Second and potential third generation biofuels are more attractive in terms of crop economy. The Green Chemistry Centre of Excellence at the University of York (UK) has recently started to coordinate a new project (SUSTOIL) funded by the European Commission through Framework 7 aiming to develop advanced biorefinery schemes to convert whole EU oil-rich crops into energy (biofuels, power and heat), food and bio-products including speciality and commodity chemicals (http://www.sustoil.org).
However, the need to control the extensive usage of organisms to hydrolyse cellulose might be essential because the potential release of such organisms to the environment could have catastrophic consequences.
Socio-economic impact.
Some sectors of the industry estimated that a robust global biofuel market will be fully established around 2012. Despite the great emphasis on the environmental aspects for the promotion of biofuels, many authors agree on the key role of socio-economic motivations in the rise of biofuel markets,148 mainly from the OECD countries. However, the impacts that biofuels could have on economies, especially in those of developing countries, have not been properly evaluated. Undoubtedly, their implementation in developing nations will promote their development to some extent. Many issues might arise from an inadequate implementation of the global market. A generalised conception is that developing countries are likely to be the main producers while higher industrialised countries (e.g. OECD) will be the major consumers. This conception is based on studies based on land availability, production costs, environmental conditions and levels of consumption in developing countries.
The developing/developed countries approach has many particularities. Asia is generally linked to the palm oil issue, with major deforestation and threats to biodiversity. However, jatropha cultivation shows a great potential for the whole region, as well as cassava (production of bioethanol) in China and Thailand.139,149 Several studies for the EU identify the potential of Eastern European countries (the Czech Republic being one of the best examples) for biofuels production based on the extensive agricultural land available and the acquisition of a system of incentives (Fig. 13).150 In contrast, Africa, despite its potential for the production of biofuels, still has serious difficulties in developing a robust market due to a lack of enough political, legal and economical infrastructure nationally promoted biofuels programs to succeed as well as unskilled labour and cultural constraints.151
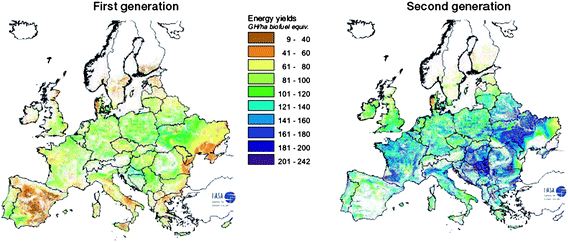 |
| Fig. 13 Potential energy yields for 1st and 2nd generation feedstocks (best feedstock for both generation production chains). Source: REFUEL http://www.refuel.eu/fileadmin/refuel/user/docs/REFUEL_final_road_map.pdf. Reproduced with permission from Marc Londo. | |
Some authors welcome in this situation the opportunity for big bioenergy players to use large available cultivable land.152 The situation seems to be promising in places like Colombia, where in 2001 the government approved the E10 program based on better economics of sugarcane in this country.153
The implementation of biofuels will also be highly dependent on the feasibility of the technologies employed for their production and the economics of the processes play a fundamental role in this regard. The price of crude oil is presently increasing to about $140 per barrel (June 2008). At this price, microalgal biomass with an oil content of 55% will need to be produced at approximately $400 ton−1 to make it competitive with petroleum diesel. However, literature estimated data pointed out that microalgal biodiesel can currently be produced at $3000 ton−1.71
The implementation of biofuels into economies131,154 will be conditioned by several factors including local, global and national issues, types of feedstocks or level of development of the market.
As examples, a number of studies have evaluated economic implications of the implementation of large scale biofuel production in developing countries.154,155 In the case of Tanzania, the assumption estimated an initial production cost of biofuels (e.g. biodiesel) of 2.23–2.29 $US L−1 at a small scale plant(local) compared to the 0.47 $US L−1 price for conventional fuel.154 These figures could potentially drop to 0.7–0.8 $US L−1 at a large scale batch production in a very optimistic scenario.154 However, a national biodiesel plan would be constrained by the economical burden generated in the African country in terms of taxes not collected from substitution of conventional diesel plus need for subsidies to the emerging market in order to make it fully competitive. These facts summarise some of the main issues for Africa in the production of biofuels.
Furthermore, each biofuel has several particularities to consider. Some useful examples are given.
Biodiesel economics in large continuous processes are suitable for high volume productions where high capital plan cost is offset by lower operational costs and large competitive volumes of fuel produced.156 On the other hand, proportionally higher running costs from smaller scale batch production would suit locally produced and distributed fuel.151,156 However, full costs evaluation will be conditioned by the type of feedstock employed and the possibility of economic premium through adding value to its main by-product (glycerol). Low value feedstocks such as soapstocks, UVO, and free fatty acids from oil refining are generally more accessible and economical than even high yield oil content oilseeds (approx. 600–800 $US t−1 to 1700–2000 $US t−1, for a product sold at 1200–1400 $US t−1).157 Haas reported a 25% saving in the use of biodiesel from waste soapstock with respect to the use of pure virgin soyabean oil.158 Nonetheless, low value feedstocks might have a negative cost implication for more industrious downstream processing,159 sometimes compensated by glycerine sales (6.5% saving in operational cost).157,160
Ethanol economics are largely dependant on the type of feedstock employed.161 The use of sugar cane and cellulose ethanol involves generally higher capital cost than corn production; however there are larger returns in production cost in terms of a more effective use of by-products (such as bagasses and molasses for sugar cane) or the possibility to use virtually free feestocks (wood chips, forestry). For corn, it has been reported that a larger number of inputs might be needed for the same ethanol volumes produced than for cane under the same agricultural conditions.161 Here is where local factors (e.g. availability of land and water, climate, etc.) would play a fundamental role.153
Biobutanol preparation requires improvements at three levels of production: preteatment (preferable from cellulosic materials where appropriate), optimisation of the bacterial strain for fermentation and purification of the biofuel from the broth.53
Synthetic biofuels production also finds a number of technical and non technical limitations that might make them less economic than fossil equivalents. Bridgwater et al. have largely studied pyrolysis and gasification processes finding that a modest 10 MW facility operating at 35% would require approximately 40
000 t y−1 (40 km2).127,131,134 Despite the high capital investment and cost needed, a good deal of the operational cost (attributed to collection of biomass and distribution) should be taken into account when assessing the plant size.131
Apart from the impact of biofuels on the economies of developing/developed countries or the practicalities and economics of the processes, there is also an increasing concern in society regarding the subsidies in the promotion of biofuels. Supporting a future scenario without subsidies is under debate. A good example of that is the closure of certain biodiesel companies in Germany conditioned by the removal of incentives in taxation of B100 fuel.162 However, we must not forget or ignore the huge subsidies (mostly hidden) given to the oil industry that will have to be taken into consideration for a fair comparison.
In summary, a careful consideration of the many factors described above (together with the policies that promote the development and implementation of such petrol-fuel replacements) will determine the implementation of one or another technology, based in certain types of feedstocks and orientated to certain markets.
Sustainability.
A set of procedures, standards, metrics and evaluations of management systems need to be implemented, at technological, social, environmental and policy making levels, adapting to the whole diversity of levels and scenarios in the complex and politically sensitive energy/bioenergy markets.
One of these powerful tools is life cycle assessment (LCA). This technique has its origin in engineering or process design aiming to indicate factors of concern in a system (i.e. an industrial process, and ecosystem or the potential effect of an energy crop in a certain set of land).163 LCA also establishes a balance of inputs/outputs plus precise boundaries for their assessment, and most importantly a system of reference.163 In the particular case of biofuels, the relevant factors will mainly be emissions, erosion and the run off of fertilisers. The boundaries might vary from specific steps in the production of the fuel (gate to gate) to a full life cycle (cradle to grave), from cultivation to end-of-use. The system of reference will usually be fossil fuel.
Some of the useful metrics to evaluate the impacts of biofuels (from a carbon/energy efficiency point of view) have been detailed by Rajagopal and Zilberman90 and Farrell et al.164
These authors attempted to unify and give meaningful information to previously reported LCA studies of ethanol from corn,9,165 developing a set of comparative methodologies where the metrics were net energy values [MJ L−1-biofuel (e.g. ethanol)] and GHG emissions (gCO2 per MJ-ethanol) as follows:
• Net energy value (NEV): Its simple definition is “energy contained in a litre of ethanol minus fossil energy used to produce it” (MJ L−1). This metric relates to the used fossil energy only (fossil energy to produce ethanol in; agriculture, conversion technology, transportation of crops and eventually final fuel).
• Net petroleum offset: Relates to the net petroleum saving made by the use of biofuels (e.g. the number of gallons of gasoline displaced by one gallon of bioethanol). This metric might be useful to evaluate the impact of the use of biofuels in oil depletion, taxation and imports.
• Net carbon reduction: Net carbon emissions reduction resulting from the consumption of a unit of biofuel. This value is expected to result in lower net addition to the atmosphere than fossil fuels, because the carbon emitted through combustion is sequestered during recultivation.
However, LCA has intrinsic limitations as a simplified LCA-GHG/energy approach may lead to misleading conclusions. These limitations are mainly difficulties in delimiting the boundaries of the system and the need to consider a broader set of indicators for a much more complete analysis of metrics (e.g. water consumption of the crop, carbon sequestration in soil, erosion, acidification, eutrophication and biodiversity impact).90,164
A potential complementary tool with a primarily dynamic approach is the so-called Strategic Niche Management (SNM).166 This useful dynamic methodology is based on the continuous and interacting process of learning from simulated experiments that are created in order to evaluate the success of a new and complex technology (e.g. biofuels).167
SNM has already been applied to different aspects of biofuels. Various case-studies have been reported (i.e. introduction of Jatropha cultivation in Tanzania, and the creation of experimental markets for biofuels in the UK and Germany-B100 diesel.168
The main limitation of this methodology is similar to that of the LCA, that is, the delimitation of boundaries to be set. It is also relatively new and it needs some improvements. However, we believe SNM could have a positive influence in the expansion of the use of more sustainable technologies.
Future perspectives and prospects
Several potential scenarios for biofuels can be foreseen in the future. The big hopes for the transport sector are second and future third generation biofuels, including biodiesel from microbial oil, the production of biobutanol (from non-edible feedstocks) as a more petrol-like fuel and the preparation of biofuels from cellulosic and biomass non-edible feedstocks. The production of 60 billion gallons of biofuels by 2030 by the US, assuming commercially available cellulosic ethanol by 2012, has been estimated by de la Torre Ugarte et al.169 Some other sources reflect a similar increase in the volume of biofuels produced in the next few decades (Fig. 14). According to the predictions from REFUEL, the 1st generation bioethanol would disappear by 2015, while biodiesel might peak by 2025, the same time at which FT-diesel may start to take off.
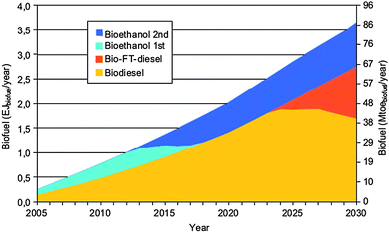 |
| Fig. 14 Expected production of various biofuels in the EU27. Source: REFUEL http://www.refuel.eu/fileadmin/refuel/user/docs/REFUEL_final_road_map.pdf. Reproduced with permission from Marc Londo. | |
The reality is that biofuels have started to have a negative public perception in some countries at the time of writing this review; this is supported by members of the scientific community claiming adverse social5a and environmental effects9,170 in first generation biofuels.
One of the critical factors that will influence the future prospects of biofuels is diversification. The future of biofuels as a sustainable (economic, social and environmental definitions) technology is directly linked to the maximum use of by-products that will make its production more cost effective (e.g. glycerol obtained as a by-product from biodiesel production can be converted into a wide range of high-added value chemicals;171 by-products from forestry could generate commercially relevant bioplastics from biological transformation;172 CO2 from ethanol production might find uses after sequestration for highly efficient carbon absorbent plants such as algae71).
Biology and synthetic biology would have the opportunity to design plants with special properties through genetic engineering. In this regard, a variety of genetically modified corn (Spartan Corn III) has recently been developed by scientists at Michigan State University to be specifically used as a biofuel feedstock.172 The crop has a specific enzyme that allows the leaves and stalk to be processed into biofuels. However, little is known about potential environmental concerns and effects on soil and land use this might create.
A few weeks before the submission of this manuscript, Howard et al. have reported the fixation of CO2 from plants can be modulated depending on changes in the availability of light.14 Such a discovery can significantly change the future of biofuels, as a major contribution to the GHG reduction can be done through the regulation of the CO2 fixed by plants in crops utilised for the production of biofuels. Many interesting advances in the field are currently ongoing.
Conclusions
The potential for biofuels has been recognised throughout the 20th century but the new century has brought with it a widespread realisation that the petroleum age is coming to an end. Rather than starting to introduce sustainable fuels in a steady, planned way over the last 30 years (since the oil crisis of the 70s), there is now a degree of panic in the need for alternatives to conventional fuels with a not very well studied plan, poorly judged policies and badly controlled practices. The use of petrol-fuel replacements has generated a lot of controversy; ideally they should contribute to global sustainability, ensuring the energy supply and meeting the GHG targets (as well as being profitable and cost competitive as much as possible) without compromising the economies, culture, societies and the environment of our future. More thoughtful analysis is now showing that many of these so-called first generation biofuels are little better and, possibly much worse, than traditional fuels, at least in terms of overall carbon footprint and environmental damage. These important issues should however, not let us be distracted from the potential benefits of biofuels and more widely, biomass exploitation. It should rather encourage us to redouble our efforts to produce later generation biofuels based on low value and waste biomass, using the greenest and efficient technologies and with properly measured and reported environmental impacts. A joint effort from politicians, economists, environmentalists and scientists is needed now, more than ever, to address the issues of the progressive incorporation of biofuels in our society and to come up with alternatives, policies and choices to advance the key technologies for a more sustainable future. The debate of biofuels has just begun. Hail to the winners!
Acknowledgements
LHD would like to acknowledge the Knowledge Transfer Partnership (KTP) and Double Green Ltd. for their support and fruitful discussion. The authors would like to thank colleagues at the Green Chemistry Centre of Excellence and Departamento de Quimica Organica from Universidad de Cordoba for their help and support. The authors wish to thank Barry J. Holmes, Marc Londo, Ron Cascone and Rhett Butler (http://www.mongabay.com/) for their kind help and permission to partially reproduce diverse material throughout the manuscript.
References
-
IPCC ( 2007a), Climate change 2007: the physical science basis, Contribution of working group 1 to the fourth assessment report of the Intergovernmental Panel on Climate Change, ed. S. Solomon, D. Qin, M. Manning, Z. Chen, M. Marquis, K. B. Averyt , M. Tignor and H. L. Miller , Cambridge University Press, Cambridge, United Kingdom and New York, NY, USA Search PubMed
.
-
IPCC ( 2007b), Climate change 2007: mitigation, Contribution of working group 3 to the Fourth Assessment Report of the Intergovernmental Panel on Climate Change, B. Metz, O. R. Davidson, P. R. Bosch , R. Dave and L. A. Meyer , Cambridge University Press, Cambridge, United Kingdom and New York, USA Search PubMed
.
- Sustainable biofuels: prospects and challenges, The Royal Society, 2008, ISBN 978 0 85403 662 2.
-
IEA ( 2007), World energy outlook 2007, International Energy Agency, Paris Search PubMed
.
-
(a) C. Ford Runge and B. Senauer, Foreign Affairs, 2007, 86(3) Search PubMed
(http://www.foreignaffairs.org/20070501faessay86305-p10/c-ford-runge-benjamin-senauer/how-biofuels-could-starve-the-poor.html);
(b)
Bioenergy and Agriculture: promises and challenges, International Food Policy Research Institute 2020 Focus No14, ed. P. Hazell and R. K. Pachauri, 2006 Search PubMed
.
- A. Demirbas, Energy Sources B, Economics, Planning Policy, 2008, 3, 177–185 Search PubMed
.
-
(a)
G. Rothenberg, Catalysis; Concepts and Green Applications, Willey-VCH, ISBN: 978-3-527-31824-7, 2008 Search PubMed
;
(b) A. Demirbas, Prog. Energy Combust. Sci., 2005, 31, 466–487 CrossRef CAS
.
-
D. M. Kammen, K. Kapadia, M. Fripp, “Putting Renewables to Work: How Many Jobs Can the Clean Energy Industry Generate?”, Report of the Renewable and appropriate Energy Laboratory, University of California Berkeley, 2004 Search PubMed
.
- D. Pimentel and T. W. Patzek, Nat. Resour. Res., 2005, 14, 65–76 Search PubMed
.
-
http://en.wikipedia.org/wiki/Biofuel
.
-
http://www.veggievan.org/index.html
.
-
http://www.autobloggreen.com/2006/12/30/biobutanol-the-other-white-meat/
.
- A. D. Sagar and S. Kartha, Ann. Rev. Environ. Resour., 2007, 32, 131–167 Search PubMed
.
- T. P. Howard, M. Metodiev, J. C. Lloyd and C. A. Raines, Proc. Natl. Acad. Sci. U. S. A., 2008, 105, 4056–4061 CrossRef CAS
.
-
(a) J. M. Marchetti, V. U. Miguel and A. F. Errazu, Renewable Sustainable Energy Rev., 2007, 11, 1300–1311 CrossRef CAS
;
(b) G. Vicente, M. Martinez and J. Aracil, Energy Fuels, 2006, 20, 394–398 CrossRef CAS
.
-
(a) A. C. Pinto, L. L. N. Guarieiro, M. J. C. Rezende, N. M. Ribeiro, E. A. Torres, W. A. Lopes, P. A. P. Pereira and J. B. de Andrade, J. Braz. Chem. Soc., 2005, 16, 1313–1330 CAS
;
(b)
M. Mittelbach, C. Remschmidt, Biodiesel, the comprehensive handbook, 2nd edn, 2005 Search PubMed.
- S. Al-Zuhair, Biofuels Bioprod. Biorefin., 2007, 1, 57–66 Search PubMed
.
-
(a) M. Mittelbach, M. Wörgetter, J. Pernkopf and H. Junek, Energy Agric., 1983, 2, 369–384 Search PubMed
;
(b) G. Vicente, M. Martinez and J. Aracil, Bioresour. Technol., 2004, 92, 297–305 CrossRef CAS
.
-
(a) H. Noureddini and D. Zhu, J. Am. Oil Chem. Soc., 1997, 74, 1457–1463 CrossRef CAS
;
(b) G. Antolin, F. V. Tinaut, Y. Briceno, V. Castano, C. Perez and A. I. Ramirez, Bioresour. Technol., 2002, 83, 111–114 CrossRef CAS
.
- M. V. Ruiz-Méndez, S. Marmesat, A. Liotta and M. C. Dobarganes, Grasas y Aceites, 2008, 59, 45–50 Search PubMed
.
-
(a) B. Freedman, R. O. Butterfield and E. H. Pryde, J. Am. Oil Chem. Soc., 1986, 63, 1375–1380 CrossRef CAS
.
- S. Zheng, M. Kates, M. A. Dubé and D. D. McLean, Biomass Bioenergy, 2006, 30, 267–272 CrossRef CAS
.
-
(a) M. Canakci and J. Van Gerpen, Trans. ASAE, 2001, 44, 1429–1436 Search PubMed
;
(b) E. Lotero, Y. Liu, D. E. Lopez, K. Suwannakarn, D. A. Bruce and J. G. Goodwin Jr., Ind. Eng. Chem. Res., 2005, 44, 5353–5363 CrossRef CAS
.
- U. Schuchardt, R. Sercheli and R. M. Vargas, J. Braz. Chem. Soc., 1998, 9, 199–210 CAS
.
- T. Cerce, S. Peter and E. Weidner, Ind. Eng. Chem. Res., 2005, 44, 9535–9541 CrossRef CAS
.
-
T. Ono, K. Yoshibaru, US Pat. , 4
164
506, 1979
.
- M. Di Serio, R. Tesser, L. Pengmei and E. Santacesaria, Energy Fuels, 2008, 22, 207–217 CrossRef CAS
.
-
(a) M. Verziu, B. Cojocaru, J. Hu, R. Richards, C. Ciuculescu, P. Filip and V. I. Parvulescu, Green Chem., 2008, 10, 373–381 RSC
;
(b) D. G. Cantrell, L. J. Gillie, A. F. Lee and K. Wilson, Appl. Catal., A, 2005, 287, 183–190 CrossRef CAS
;
(c) H. Chen and J. F. Wang, Stud. Surf. Sci. Catal., 2006, 159, 153–156 CAS
.
- G. J. Suppes, K. Buchwinkel, S. Lucas, J. B. Botts, M. H. Mason and J. A. Heppert, J. Am. Oil Chem. Soc., 2001, 78, 139–145 CrossRef CAS
.
- G. Vicente, A. Coteron, M. Martinez and J. Aracil, Ind. Crops Prod., 1998, 8, 29–35 CrossRef CAS
.
-
(a) H. J. Kim, B. S. Kang, M. J. Kim, Y. M. Park, D. K. Kim, J. S. Lee and K. Y. Lee, Catal. Today, 2004, 93–95, 315–320 CrossRef CAS
;
(b) H. Ma, S. Li, B. Wang, R. Wang and S. Tian, J. Am. Oil Chem. Soc., 2008, 85, 263–270 CrossRef CAS
.
-
(a) E. Leclercq, A. Finiels and C. Moreau, J. Am. Oil Chem. Soc., 2001, 78, 1161–1165 CrossRef CAS
;
(b) M. Toda, A. Takagaki, M. Okamura, J. N. Kondo, S. Hayashi, K. Domen and M. Hara, Nature, 2005, 438, 178 CrossRef CAS
.
-
(a) C. S. MacLeod, A. P. Harvey, A. Lee and K. Wilson, Chem. Eng. J., 2008, 135, 63–70 CrossRef CAS
.
-
(a) Y. Shimada, Y. Watanabe, T. Samukawa, A. Sugihara and Y. Tominaga, J. Mol. Catal. B: Enzym., 2002, 17, 133–142 CrossRef CAS
;
(b) A. F. Hsu, K. Jones, T. A. Foglia and W. N. Marmer, Biotechnol. Appl. Biochem., 2002, 36, 181–186 CrossRef CAS
;
(c) T. Tan and C. Yin, Biochem. Eng. J., 2005, 25, 39–45 CrossRef CAS
;
(d) A. Macario, G. Giordano, L. Setti, A. Parise, J. M. Campelo, J. M. Marinas and D. Luna, Biocatal. Biotrans., 2007, 25, 328–335 CrossRef CAS
.
-
(a) F. Sanchez and P. T. Vasudevan, Appl. Biochem. Biotechnol., 2006, 135, 1–14 CrossRef CAS
;
(b) F. Yagiz, D. Kazan and N. A. Akin, Chem. Eng. J., 2007, 134, 262–267 CrossRef CAS
.
- Y. Watanabe, P. Pinsirodom, T. Nagaoa, A Yamauchi, T. Kobayashi, Y. Nishida, Y. Takagi and Y. Shimada, J. Mol. Catal. B: Enzym., 2007, 44, 99–105 CrossRef CAS
.
-
(a) A. Houde, A. Kademi and D. Leblanc, Appl. Biochem. Biotechnol., 2004, 118, 155–170 CrossRef CAS
;
(b) R. Sharma, Y. Chisti and U. C. Banerjee, Biotechnol. Adv., 2001, 19, 627–662 CrossRef CAS
;
(c) U. T. Bornscheuer, Enzyme Microb. Technol., 1995, 17, 578–586 CrossRef CAS
.
-
(a) A. Demirbas, Energy Conv. Manage., 2002, 43, 2349–2356 CrossRef CAS
;
(b) R. Sawangkeaw, K. Bunyakiat and S. Ngamprasertsith, Green Chem., 2007, 9, 679–685 RSC
;
(c) H. He, T. Wang and S. Zhu, Fuel, 2006, 86, 442–447
.
- K. S. Tyson, Fuel Proc. Technol., 2005, 86, 1127–1136 Search PubMed
.
-
(a)
M. Notari, F. Rivetti, PCT Int. Pat., WO 2004/052874, 2004
;
(b) D. Fabbri, V. Bevoni, M. Notari and F. Rivetti, Fuel, 2007, 86, 690–697 CrossRef CAS
.
-
(a)
J. Kijenski, A. W. Lipkowski, W. Walisiewicz-Niedbalska, H. Gwardiak, K. Rozycki, I. Pawlak, EPC Appl. Pat., 04007404.9, 2004
;
(b) Y. Xu, W. Du and D. Liu, J. Mol. Catal. B: Enzym., 2005, 32, 241–245 CrossRef CAS
.
- M. K. Modi, J. R. C. Reddy, B. V. S. K. Rao and R. B. N. Prasad, Bioresour. Technol., 2007, 98, 1260–1264 CrossRef CAS
.
-
D. Luna, F. M. Bautista, V. Caballero, J. M. Campelo, J. M. Marinas and A. A. Romero, PCT Pat. 2007, No. PCT/ES 2007/000450
.
-
(a) J. Hu, Z. Du, C. Li and E. Min, Fuel, 2005, 84, 1601–1606 CAS
;
(b) G. Knöthe and K. R. Steidley, Fuel, 2007, 86, 2560–2567 CrossRef CAS
;
(c)
The biodiesel handbook, G. Knöthe, J. Van Gerpen, J. Krahl, Eds. AOCS Press, 2005
.
-
(a) Y. R. Leshkov, C. J. Barrett, Z. Y. Liu and J. A. Dumesic, Nature, 2007, 447, 982–986 CrossRef CAS
.
- K. D. Maher and D. C. Bressler, Bioresour. Technol., 2007, 98, 2351–2368 CrossRef CAS
.
-
(a) G. J. Dykstra, A. W. Schwab, E. Selke, S. C. Sorenson and E. H. Pryde, J. Am. Oil Chem. Soc., 1995, 73, 484–497
;
(b) S. Bhatia, F. A. Twaiq and N. A. M. Zabidi, Ind. Eng. Chem. Res., 1999, 38, 3230–3237 CrossRef
.
-
http://siteresources.worldbank.org/INTWDR2008/Resources/, The World Bank 2008.
- X. Draye, Y. R. Lin, X. Y. Qian, J. E. Bowers, G. B. Burow, P. L. Morrell, D. G. Peterson, G. G. Presting, S. X. Ren, R. A. Wing and A. H. Patterson, Plant Physiol., 2001, 125, 1325–1341 CrossRef CAS
.
- M. Balat, H. Balat and C. Oz, Prog. Energy Combust. Sci., 2008, 34, 551–573 CrossRef CAS
.
- K. A. Gray, L. Zhao and M. Emptage, Curr. Opin. Chem. Biol., 2006, 10, 141–146 CrossRef CAS
.
- M. Balat, Energy Explor. Exploit., 2007, 25, 195–218 Search PubMed
.
-
(a) P. Dürre, Biotechnol. J., 2007, 2, 1525–1534 Search PubMed
;
(b) P. Dürre, Ann. N. Y. Acad. Sci., 2008, 1125, 353–362
.
- T. T. Ezeji, Q. Chukwuemeka, B. Nasib and P. Hans, Curr. Opin. Biotechnol., 2007, 18, 220–227 CrossRef CAS
.
- R. Cascone, Hydrocarbon Process., 2007, 86, 95–109 CAS
.
- D. Antoni, V. V. Zverlov and W. H. Schwarz, Appl. Microbiol. Biotechnol., 2007, 77, 23–35 CrossRef CAS
.
-
(a)
http://www2.dupont.com/Biofuels/en_US/
;
(b)
http://www.biofuelsmedia.com/news_link.php?new = 55
.
-
http://www.butanol.com/index.html
.
- D. G. Lima, V. C. D. Soares, E. B. Ribeiro, D. A. Carvalho, E. C. V. Cardoso, F. C. Rassi, K. C. Mundim, J. C. Rubim and P. A. Z. Suarez, J. Anal. Appl. Pyrolysis, 2004, 71, 987–996 CrossRef CAS
.
- L. Dandik and H. A. Aksoy, Fuel Process. Technol., 1998, 57, 81–92 CrossRef CAS
.
- A. V. Bridgwater, Chem. Eng. J., 2003, 91, 87–102 CrossRef CAS
.
- L. Plass and S. Reimelt, Hydrocarbon Eng., 2007, 12, 71–74 Search PubMed
.
- R. Sarin, M. Sharma, S. Sinharay and R. K. Malhotra, Fuel, 2007, 86, 1365–1371 CrossRef CAS
.
- W. M. J. Achten, E. Mathijs, L. Verchot, V. P. Singh, R. Aerts and B. Muys, Biofuels, Bioprod. Biorefin., 2007, 1, 283–291 Search PubMed
.
-
(a) M. P. Dorado, E. Ballesteros, F. J. Lopez and M. Mittelbach, Energy Fuels, 2004, 18, 77–83 CrossRef CAS
;
(b) A. Bouaid, Y. Diaz, M. Martinez and J. Aracil, Catal. Today, 2005, 106, 193–196 CrossRef CAS
.
-
(a) P. Dittrick, Oil Gas J., 2007, 105, 20–26 Search PubMed
;
(b) M. Simpson-Holley and G. Evans, Outlook Pest Manage., 2007, 18, 109–113 Search PubMed
.
-
(a) A. L. Tiwari, A. Kumar and H. Raheman, Biomass Bioenergy, 2007, 31, 569–575 CrossRef
;
(b) H. J. Berchmans and S. Hirata, Bioresour. Technol., 2008, 99, 1716–1721 CrossRef CAS
;
(c)
http://www.renewableenergyworld.com/rea/news/story?id = 49611
.
-
(a) K. Narashimharao, A. Lee and K. Wilson, J. Biobased Mater. Bioenergy, 2007, 1, 19–30 Search PubMed
;
(b) Y. Wang, S. Ou, P. Liu, F. Xue and S. Tang, J. Mol. Catal. A, 2006, 252, 107–112 CrossRef CAS
;
(c) M. Fangrui and A. H. Milford, Bioresour. Technol., 1999, 70, 1–15 CrossRef CAS
;
(d) M. Zong, Z. Q. Duan, W. Y. Lou, T. J. Smith and H. Wu, Green Chem., 2007, 9, 434–437 RSC
.
- M. G. Kulkarni, R. Gopinath, L. C. Meher and A. K. Dalai, Green Chem., 2006, 8, 1056–1062 RSC
.
- G. M. Tashtoush, M. I. Al-Wydian and M. M. Al-Jarrah, Energy Conv. Manage., 2004, 45, 2697–2711 CrossRef CAS
.
-
(a) Y. Chisti, Trend Biotechnol., 2008, 26, 126–131 Search PubMed
;
(b) Y. Chisti, Biotechnol. Adv., 2007, 25, 294–306 CrossRef CAS
.
-
A. S. Carlsson, J. B. Van Bilein, R. Möller, D. Clayton, D. Bowles, Outputs from EPOBIO Project, Micro-and Macroalgae utility for industrial application, CPL Press, York, UK, Sept. 2007 Search PubMed
.
-
http://www.shell.com/home/content/media-en/news_and_library/press_releases/2007/biofuels_cellana_11122007.html
.
-
(a) L. Y. Zhu, M. H. Zong and H. Wu, Bioresour. Technol., 2008, 99, 7881–7885 CrossRef CAS
;
(b) C. Angerbauer, M. Siebenhofer, M. Mittelbach and G. M. Guebitz, Bioresour. Technol., 2008, 99, 3051–3056 CrossRef CAS
;
(c) S. Papanikolau, M. Galiotou-Panayotou, S. Fakas, M. Komaitis and G. Aggelis, Eur. J. Lipid Sci. Technol., 2007, 109, 1060–1070 CrossRef
.
- M. P. Dorado, E. Ballesteros, J. M. Arnal, J. Gómez and F. J. López, Fuel, 2003, 82, 1311–1315 CrossRef CAS
.
- Z. Utlu and M. S. Koçak, Renewable Energy, 2008, 33, 1936–1941 CrossRef CAS
.
- C. C. Lai, S. Zullaikah, S. R. Vali and Y. H. Ju, J. Chem. Technol. Biotechnol., 2005, 80, 331–337 CrossRef CAS
.
- E. Molina Grima, E. H. Belarbi, F. G. Acien Fernandez, A. Robles Medina and Y. Chisti, Biotechnol. Adv., 2003, 20, 491–515 CrossRef CAS
.
- A. J. Dijkstra, Eur. J. Lipid Sci. Technol., 2006, 108, 249–264 CrossRef CAS
.
-
(a) G. W. Huber and A. Corma, Angew. Chem., Int. Ed., 2007, 46, 7184–7201 CrossRef CAS
;
(b) J. N. Chheda, G. W. Huber and J. A. Dumesic, Angew. Chem., Int. Ed., 2007, 46, 7164–7183 CrossRef CAS
.
- Z. Qi, C. Jie, W. Tiejun and X. Ying, Energy Conv. Manage., 2007, 48, 87–92 CrossRef
.
- D. Mohan, C. U. Pittman Jr and P. H. Steele, Energy Fuels, 2006, 20, 848–889 CrossRef CAS
.
- A. A. Lappas, M. Papapetrou and I. A. Vasalos, Stud. Surf. Sci. Catal., 2007, 166, 213–225 CAS
.
- Y. S. Ooi and S. Bhatia, Microporous Mesoporous Mater., 2007, 102, 310–317 CrossRef CAS
.
-
(a) G. Russo, Nature, 2006, 444, 648–649 CrossRef CAS
;
(b) D. Tilman, J. Hill and C. Lehman, Science, 2006, 314, 1598–1600 CrossRef CAS
.
-
(a) J. P. Lange, Biofuels Bioprod. Biorefin., 2007, 1, 39–48 Search PubMed
;
(b) Y. Pu, D. Zhang, M. P. Singh and A. J. Ragauskas, Biofuels Bioprod. Biorefin., 2008, 2, 58–73 Search PubMed
.
- L. R. Lynd, W. H. Van Zyl, J. E. McBride and M. Laser, Curr. Opin. Biotechnol., 2005, 16, 577–583 CrossRef CAS
.
- S. Atsumi, T. Hanai and J. C. Liao, Nature, 2008, 451, 86–90 CrossRef CAS
.
-
(a) J. Tollefson, Nature, 2008, 451, 880–883 CrossRef CAS
;
(b) J. Tollefson, Chem. World, 2008, 5(2), 21 Search PubMed
.
-
D. Rajagopal. D. Zilberman, Policy Research Working paper 4341 (WPS4341), The World Bank, Sept. 2007 Search PubMed
.
- J. Mata-Alvarez, S. Macé and P. Llabrés, Bioresour. Technol., 2000, 74, 3–16 CrossRef CAS
.
- A. Derbimas, Energy Conv. Manage., 2001, 42, 1375–1378
.
-
J. Ramage, J. Scurlock, Biomass. Renewable energy-power for a sustainable future, ed. G. Boyle, Oxford University Press, Oxford, 1996 Search PubMed
.
-
(a) A. Demirbas, Energy Conv. Manage., 2008, 49, 2106–2116 CrossRef CAS
;
(b) S. S. Kapdi, V. K. Vijai, S. K. Rajesh and R. Prasad, Renewable Energy, 2005, 30, 1195–1202 CrossRef CAS
.
- N. Kuwahara, M. D. Berni and S. V. Bajay, Renewable Energy, 1999, 16, 1000–1003 CrossRef CAS
.
-
http://www.trendsetter-europe.org/index.php?ID = 2842
.
-
(a) M. Lantz, M. Svensson, L. Björnsson and P. Börjesson, Energy Policy, 2007, 35, 1830–1843 CrossRef
;
(b) P. Börjesson and M. Berglund, Biomass Bioenergy, 2006, 30, 469–485 CrossRef
;
(c) P. Börjesson and M. Berglund, Biomass Bioenergy, 2006, 31, 326–344
.
-
(a) S. M. Kotay and D. Das, Int. J. Hydrogen Energy, 2008, 33, 258–263 CrossRef
;
(b) D. J. Murphy, Chimica Oggi, 2008, 26, 14–19 Search PubMed
;
(c) A. Melis, Int. J. Hydrogen Energy, 2002, 27, 1217–1228 CrossRef CAS
.
- S. Manis and R. Banerjee, Int. J. Hydrogen Energy, 2008, 33, 279–286 CrossRef
.
- G. Davila-Vazquez, S. Arriaga, F. Alatriste-Mondragon, A. De Leon-Rodriguez, L. M. Rosales-Colunga and E. Razo-Flores, Rev. Environ. Sci. Biotechnol., 2008, 7, 27–45 Search PubMed
.
-
(a) Z. Qin, N. Q. Ren, J. Z. Li and X. F. Yan, J. Inst. Technol., 2003, 35, 1105–1108 Search PubMed
;
(b) N. Ren, J. Li, B. Li, Y. Wang and S. Liu, Int. J. Hydrogen Energy, 2006, 31, 2147–2157 CrossRef CAS
.
- L. Zhang, T. Happe and A. Melis, Planta, 2002, 214, 552–561 CrossRef CAS
.
-
(a)
http://iv2s.rastaf.net/errichtung-und-demonstrationsbetrieb-einer-biosngtankstelle/_/prog1/subprog26/project350?MyDic_action = set_langid;langid = 2
;
(b)
www.bio-sng.com
.
-
(a) T. Yoshida, Y. Oshima and Y. Matsumura, Biomass Bioenergy, 2004, 26, 71–78 CrossRef CAS
;
(b) F. Vogel, M. H. Waldner, A. A. Rouff and S. Rabe, Green Chem., 2007, 9, 616–619 RSC
.
-
http://www.iec.tu-freiberg.de/conference/conf07/pdf/7.1.pdf
.
- A. Demirbas, Prog. Energy Combust. Sci., 2007, 33, 1–18 CrossRef CAS
.
-
(a) H. Nakagawa, T. Harada, T. Ichinose, K. Takeno, S. Matsumoto, M. Kobayashi and M. Sakai, JARQ, 2007, 41, 173–180 Search PubMed
;
(b)
http://www.refuel.eu/biofuels/biomethanol/
.
-
http://www.solarix.eu/en/news/33 (accessed April 2008).
- J. M. N. van Kasteren, D. Dizdarevic, W. R. van der Waall, J. Guom and R. Verbernem, Bioethanol from syngas, 2005 Search PubMed
, Project number 0456.472.
-
http://www.iogen.ca/
.
-
http://www.processum.se/eng/press/filer/FOLDER_eng.pdf
.
-
http://powerecalene.com/
.
- A. Demirbas, Energy Conv. Manage., 2000, 41, 633–646 CrossRef CAS
.
-
(a) T. A. Semelsberger, R. L. Borup and H. L. Greene, J. Power Sources, 2006, 156, 497–511 CrossRef CAS
;
(b) C. Arcoumanis, C. Bae, R. Crookes and E. Kinoshita, Fuel, 2008, 87, 1014–1030 CrossRef CAS
.
-
(a) A. Eliassi, L. Savadkoohi and A. Kargari, Chem. Eng. Commun., 2007, 194, 1495–1502 CrossRef CAS
;
(b) Y. Yaripour, F. Baghaei, I. Schmidt and J. Perregaard, Catal. Commun., 2005, 6, 147–152 CrossRef
.
- W. An, K. T. Chuang and A. R. Sanger, Can. J. Chem. Eng., 2004, 82, 948–955 CAS
.
- A. Demirbas, Energy Sources, Part A: Recovery, Utilization, Environ. Effects, 2008, 30, 475–482 Search PubMed
.
- A. Demirbas, Int. J. Hydrogen Energy, 2004, 29, 1237–1243 CrossRef CAS
.
- T. Bhaskar, A. Sera, A. Muto and Y. Sakata, Fuel, 2008, 87, 2236–2242 CrossRef CAS
.
-
(a)
L. Steinmann, PCT Int. Pat. 1999, WO 9915605 A1 19990401
;
(b)
www.cpi.umist.ac.uk/eminent/Confidential/meeting/RigaMeeting/Riga%20Workshop/March%2008%20HTU%20case.ppt
.
-
http://www.refuel.eu/biofuels/htu-diesel/
.
-
(a) M. E. Dry, Appl. Catal. A, 1996, 118, 319–344 CrossRef
;
(b) M. E. Dry, J. Chem. Technol. Biotechnol., 2001, 77, 43–50
.
- S. Li, S. Krishnamoorthy, A. Li, G. D. Meitzner and E. Iglesia, J. Catal., 2002, 206, 202–217 CrossRef CAS
; H. Schulz, Appl. Catal A, 1999, 186, 1–16 CrossRef CAS
.
-
(a)
T. L. Alleman, R. L. McCormick, SAE Technical Paper No. 2003-01-0763, 2003 Search PubMed
;
(b) A. Demirbas, Energy Sources B: Economics, Planning, Policy, 2007, 2, 343–351 Search PubMed
.
- M. J. A. Tijmensen, A. P. C. Faaij, C. N. Hamelinck and M. R. M. van Hardeveld, Biomass Bioenergy, 2002, 23, 129–152 CrossRef CAS
.
- A. C. Vosloo, Fuel Process. Technol., 2001, 71, 149–155 CrossRef CAS
.
- A. V. Bridgwater, Appl. Catal., A, 1994, 116, 5–47 CrossRef CAS
.
- D. G. Lima, V. C. D. Soares, E. B. Ribeiro, D. A. Carvalho, E. C. V. Cardoso, F. C. Rassi, K. C. Mundim, J. C. Rubim and P. A. Z. Suarez, J. Anal. Appl. Pyrolysis, 2004, 71, 987–996 CrossRef CAS
.
- A. B. Ross, J. M. Jones, M. L. Kubacki and T. Bridgeman, Bioresour. Technol., 2008, 99, 6494–6504 CrossRef CAS
.
-
(a) X. Miao, Q. Wu and C. J. Yang, J. Anal. Appl. Pyrolysis, 2004, 71, 855–863 CrossRef CAS
;
(b) X. Miao and Q. Wu, J. Anal. Appl. Pyrolysis, 2004, 110, 85–93 CAS
.
- A. V. Bridgwater, Int. J. Global Energy Issues, 2007, 27, 160–203 CrossRef
.
-
(a) R. V. Pindoria, J. Y. Lim, J. E. Hawkes, M. J. Lazaro, A. A. Herod and R. Kandiyoti, Fuel, 1997, 76, 1013–1023 CrossRef CAS
;
(b) R. V. Pindoria, A. Megaritis, A. A. Herod and R. Kandiyoti, Fuel, 1998, 77, 1715–1726 CrossRef CAS
.
- M. I. Nokkosmaki, E. T. Kuoppala, E. A. Leppamaki and A. O. I. Krause, J Anal. Appl. Pyrolysis, 2000, 55, 119–131 CrossRef CAS
.
-
(a) D. Chiaramonti, D. Bonini, E. Fratini, G. Tondi, K. Gartner, A. V. Bridgwater, H. P. Grimm, I. Soldaini, A. Webster and P. Baglioni, Biomass Bioenergy, 2003, 25, 85–99 CrossRef CAS
;
(b) D. Chiaramonti, D. Bonini, E. Fratini, G. Tondi, K. Gartner, A. V. Bridgwater, H. P. Grimm, I. Soldaini, A. Webster and P. Baglioni, Biomass Bioenergy, 2003, 25, 101–111 CrossRef CAS
.
- S. Czernik, R. French, C. Feik and E. Chornet, Ind. Eng. Chem. Res., 2002, 41, 4209–4215 CrossRef CAS
.
- J. Gressel, Plant Sci., 2008, 174, 246–263 CrossRef CAS
.
- J. Van Eijcka and H. Romijnk, Energy Policy, 2008, 36, 311–325 CrossRef
.
-
(a) G. Francis, R. Edinger and K. Becker, Nat. Resour. Forum, 2005, 29, 12–24 Search PubMed
;
(b) G. M. Gubitz, M. Mittelbach and M. L. Trabi, Bioresour. Technol, 1999, 7, 73–82 CrossRef
.
-
I. C. Macedo, M. R. L. V. Leal and J. E. A. R. Silva, Assessment of Greenhouse Gas Emissions in the Production and Use of Ethanol Fuel in Brazil, report to the Governement of State of Sao Paulo , 2004 Search PubMed
.
- G. P. Hammond, S. Kallu and M. C. Mc Manus, Appl. Energy, 2008, 85, 506–515 CrossRef CAS
.
-
J. Sheehan, V. Camobreco, J. Duffield, M. Graboski and H. Shapouri, An Overview of Biodiesel and Petroleum Diesel Life Cycles, Report No. NREL/TP-580–24772, National Renewable Energy Laboratory, Golden, Colorado, 2000 Search PubMed
.
- P. Janulis, Renewable Energy, 2004, 29, 861–871 CrossRef CAS
.
-
http://statistics.defra.gov.uk/esg/publications/auk/default.asp
.
-
(a)
D. Hart, A. Bauen, A. Chase and J. Howes, Liquid biofuels and hydrogen from renewable resources in the UK to 2050: a technical analysis, E4tech (UK) Ltd, Study carried out for the UK Department for Transport, 2003 Search PubMed
;
(b)
http://www.senternovem.nl accessed 3 Apr. 2008.
-
http://journeytoforever.org/biofuel_food.html
.
- A. D. Watt et al., Issues Environ. Sci. Technol., 2007, 25, 135–160 Search PubMed
.
-
(a) J. C. Lovett, Afr. J. Ecol., 2007, 45, 117–119 CrossRef
;
(b)
http://travel.mongabay.com/malaysia/Deforestation.html/
.
- M. B. Charles, R. Ryan, N. Ryan and R. Oloruntoba, Energy Policy, 2007, 35, 5737–5746 CrossRef
.
-
(a)
M. Zhang, X. Dong, H. Lu, C. Liu, Abstracts of Papers, 235th ACS National Meeting, New Orleans, LA, United States, April 6–10, 2008, FUEL-061 Search PubMed
;
(b) T. L. T. Nguyen, S. H. Gheewala and S. Garivait, Environ. Sci. Technol., 2007, 41, 4135–4142 CrossRef CAS
;
(c)
http://www.biofuelsmedia.com/news_link.php?new = 89
;
(d) D. Daia, Z. Hu, G. Pu, H. Li and Ch. Wang, Energy Conv. Manage., 2006, 47, 1686–1699 CrossRef
.
-
(a) E. M. Kondili and J. K. Kaldellis, Renewable Sustainable Energy
Rev., 2007, 11, 2137–2151 CrossRef
;
(b)
www.refuel.eu
.
- B. Amigun, R. Sigamoney and H. von Blottnitz, Renewable Sustainable Energy Rev., 2008, 12, 690–711 CrossRef
.
- J. A. Mathews, Energy Policy, 2007, 35, 3550–3570 CrossRef
.
- J. A. Quintero, M. I. Montoya, O. J. Sanchez, O. H. Giraldo and C. A. Cardona, Energy, 2008, 33, 385–399 CrossRef CAS
.
-
www.re-focus.net, Refocus, March 2003, 42, pp. 26–28, accessed on the 4th of July 2008 Search PubMed.
- J. Peters and S. Thielmann, Energy Policy, 2008, 36, 1538–1544 CrossRef
.
- M. J. Haas, A. J. McAloon, W. C. Yee and T. A. Foglia, Bioresour. Technol., 2006, 97, 671–678 CrossRef CAS
.
- M. P. Dorado, F. Cruz, J. M. Palomar and F. J. Lopez, Renewable Energy, 2006, 31, 1231–1237 CrossRef CAS
.
- M. J. Haas, Fuel Process. Technol., 2005, 86, 1087–1096 CrossRef CAS
.
- Y. Wang, S. Ou, P. Liu, F. Xue and S. Tang, J. Mol. Catal. A: Chem., 2006, 252, 107–112 CrossRef CAS
.
- Y. Zang, M. A. Dube, D. D. McLean and M. Kates, Bioresour. Technol., 2003, 90, 229–240 CrossRef CAS
.
- B. D. Solomon, J. R. Barnes and K. E. Holversen, Biomass Bioenergy, 2007, 31, 416–425 CrossRef
.
- F. O. Licht's and World Ethanol and Biofuels Report, Dark clouds on the Horizon for German Biodiesel sector, F.O. Licht GmbHF, 2007,(8), 6 Search PubMed
.
- M. Weiss and M. Patel, Renewable Resour. Renewable Energy, 2007, 137–154 Search PubMed
.
- A. E. Farrell, R. J. Plevin, B. T. Turner, A. D. Jones, M. O'Hare and D. M. Kammen, Science, 2006, 311, 506–508 CrossRef CAS
.
-
(a) H. Shapouri, J. Duffield and M.S. Graboski, Estimating the Net Energy Balance from Corn Ethanol, US Department of Agriculture, Economic Research Service, Office of Energy, Agricultural Economic Report No. 721 Search PubMed;
(b) T. Patzek, Crit. Rev. Plant Sci., 2004, 23, 519–567 CrossRef CAS
;
(c)
H. Shapouri, A. McAloon, The 2001 net energy balance of corn ethanol, US Department of Agriculture, Washington, DC, 2004. Also available at http://www.usda.gov/oce/index.htm Search PubMed
;
(d)
M. Graboski, Fossil energy use in the manufacture of corn ethanol, National Corn Growers Association, Washington, DC, 2002. Also available at http://www.ncga.com/ethanol/main Search PubMed
;
(e)
M. Wang, Development and use of GREET 1.6 fuel-cycle model for transportation fuels and vehicle technologies, Tech. Rep. ANL/ESD/TM-163, Argonne National Laboratory, Argonne, IL, 2001. Also available at http://www.transportation.anl.gov/pdfs/TA/153.pdf Search PubMed
.
-
(a)
R. Hoogma, R. Kemp, J. Schot, B. Truffer, Experimenting for sustainable transport: the approach of strategic niche management, Spon Press, London and New York, 2002 Search PubMed
;
(b) R. Kemp, J. W. Schot and R. Hoogma, Technol. Anal. Strategic Manage., 1998, 10, 175–196 Search PubMed
;
(c)
M. C. J. Caniëls, H. A. Romijn, Strategic Niche Management as and Operational Tool for Sustainable Innovation: Guidelines for Practice, paper for the Schumpeter Conference, Nice, France, 21–24 June, 2006 Search PubMed
.
- W. W. M. van der Laak, R. P. J. M. Raven and G. P. J. Verbong, Energy Policy, 2007, 35, 3213–3225 CrossRef
.
- C. Bomb, K. McCormick, E. Deurwaarder and T. Kabarger, Energy Policy, 2007, 35, 2256–2267 CrossRef
.
- D. de la Torre Ugarte, B. C. English and K. Jensen, Am. J. Agric. Econ., 2007, 89, 1290–1295 CrossRef
.
-
http://www.rsc.org/AboutUs/News/PressReleases/2008/biofuelsfuture.asp
.
-
(a) C. H. Zhou, J. N. Beltramini, Y. X. Fan and G. Q. Lu, Chem. Soc. Rev., 2008, 37, 527–549 RSC
;
(b) A. Behr, J. Eilting, K. Irawadi, J. Leschinski and F. Lindner, Green Chem., 2008, 10, 13–30 RSC
.
- M. Koller, R. Bona, G. Braunegg, C. Hermann, P. Horvat, M. Kroutil, J. Martinz, J. Neto, L. Pereira and P. Varilam, Biomacromolecules, 2005, 6, 561–565 CrossRef CAS
.
|
This journal is © The Royal Society of Chemistry 2008 |
Click here to see how this site uses Cookies. View our privacy policy here.