DOI:
10.1039/C1RA00218J
(Paper)
RSC Adv., 2011,
1, 1579-1584
Efficient extraction of direct coal liquefaction residue with the [bmim]Cl/NMP mixed solvent
Received
25th May 2011
, Accepted 24th August 2011
First published on 25th October 2011
Abstract
A novel solvent mainly consisting of ionic liquid 1-butyl-3-methylimidazolium chloride ([bmim]Cl) and N-methyl pyrrolidinone (NMP), was used to treat Direct Coal Liquefaction Residue (DCLR). The aim was to extract an important organic precursor compound from the DCLR as the raw material of carbon fibers. The performance of extraction and properties of the extract with the mixed solvent were analyzed and characterized by FT-IR, solid state 13C-NMR, DTA, micrograph and elemental analysis. The results showed that the mixed solvent was efficient to extract organic components from DCLR, but inert to inorganic substances. Adding NMP into [bmim]Cl not only accelerated the solid–liquid separation after the dissolution of DCLR, but also increased the extract yield. The possible synergistic mechanism was proposed based on the characteristic results. NMP in the mixture plays an important role to swell the fixed carbons contained in DCLR, and the ionic liquid [bmim]Cl contributes to destroying hydrogen bond forces in DCLR.
1. Introduction
Increased demand for liquid transportation fuels coupled with the gradual depletion of oil reserves have recently renewed interest in coal-to-liquid technologies.1 China has a coal-rich but oil-poor energy structure, so the technologies for conversion of coal to liquid fuel and desired chemicals have been developed in the past decade. China currently has established the first and the largest Direct Coal Liquefaction (DCL) plant (a total capacity of 3 Mt (oil)/y) since World War II.2 However, Direct Coal Liquefaction Residue is inevitably generated as a by-product which usually accounts for as much as 20–30 wt% of coal consumed in the liquefaction process.3,4 Therefore, the effective utilization of DCLR is of importance not only for better economic benefits of a DCL process, but also for the environmental protection.2
Up to now, DCLR has been frequently used as a raw material for gasification,5 asphalt-type modifier6 and further hydrogenation for more liquid fuels;7–10 nevertheless, all of these are of low market value. DCLR should be used effectively as a value-added carbon resource from the viewpoints of environmental protection and economic profit. Recently, DCLR was used to prepare value-added Carbon Fibers (CFs) by Xiao and coworkers.11,12 The possible formation mechanism of CFs is attributed to the transformation of the organic components in DCLR, which are un-reacted organic species from raw coal and/or from aromatic heavy components formed in the liquefaction process due to the condensation and hydrogenation reactions. Thus, the extraction of organic components from DCLR is necessary for increasing the purity and properties of CFs.
Ionic liquids (ILs) with special physico-chemical characteristics such as low melting point, non-flammability and negligible volatility, have been used widely as novel solvents.13–18 In our previous study, we found that some certain imidazolium-based ionic liquids can extract DCLR.19 Amongst these ILs we studied, the performance of [bmim]Cl was best for it can dissolve DCLR to a remarkable degree and moreover dissolved matter can be easily back-extracted by water, but the solid–liquid separation is difficult since the mixtures are very viscous after dissolving DCLR with [bmim]Cl. So for further exploration, several dispersants were selected to form a mixed solvent with [bmim]Cl, and tried to promote separation; moreover, the extractive effects of DCLR with these mixed solvents have been comprehensively examined and we report our initial results here.
2. Experimental details
2.1. Materials
DCLR in this study was sampled from Shenhua direct coal liquefaction pilot plant of China. The DCL reactor was operated at 455 °C and 19 MPa in the presence of Fe-based catalyst. After reaction, the liquids were separated and collected through high-temperature and low-temperature separators, followed by atmospheric and vacuum distillations, and DCLR was discharged and collected from the bottom of a vacuum distillation column.
DCLR was a solid block at room temperature, and was pretreated to sizes smaller than 0.5 mm with a high speed disintegrator, and then conserved without any more treatments. The true density of the sample was 1.59 g cm−3 and the softening point was 147.5 °C; more detailed properties of DCLR are shown in Table 1. The ionic liquid [bmim]Cl used in this study was made in our laboratory, and its purity was tested to be at ≥99%. [bmim]Cl was stored in a vacuum chamber to avoid any possible absorption of water, because [bmim]Cl is very hygroscopic and the presence of water might change its properties. Ethanol, quinoline, ethylene glycol, N-methyl pyrrolidinone and pyridine are analytically pure and were purchased from Guangdong Xilong Chemical Co. Ltd. China.
Table 1 Properties for DCLR in this study. Mad: the content of moisture calculated on the air dry basis; Aad: the content of ash; Vad: the content of the volatile components; FC: the content of fixed carbon
Component |
M
ad
|
A
ad
|
V
ad
|
FC
|
Value (w, %) |
0.26 |
24.0 |
33.9 |
41.8 |
2.2.
Extraction process of DCLR
The “dissolution and back-extraction” method was used to extract DCLR, and the extraction procedure was as followed: firstly, 1 g of DCLR was added into 10.0 g of [bmim]Cl in flasks, and a certain volume of ethanol, ethylene glycol, N-methyl pyrrolidinone or pyridine which was used as a dispersant was poured into the flasks to reduce the viscosity of the mixture, then the mixture in the vessels was agitated by magnetic stirring. The temperature inside the vessels was increased from room temperature to 105 °C, and dissolving time was kept within the range of 2 min to 120 min. Secondly, after the mixture was cooled down to room temperature, the mixture was separated by an air filtration pump. Thirdly, the filtrate was back-extracted with nearly 4 times the volume of water to precipitate soluble matter, and then the precipitate was separated from the aqueous solution by an air filtration pump. Finally, the extract was dried at 70 °C for 12 h, and afterwards stored in capped polyethylene bottles for analysis. Other special experiment processes will be presented hereinafter in the Results and discussion section.
2.3. Analysis methods
In order to characterize functional groups of DCLR, the extract and insoluble matter, Fourier Transform InfraRed spectroscopy (FT-IR) (Nicolet Nexus380, USA) was used in the wavenumber range 3500–500 cm−1. Aromaticity was determined by solid state 13C nuclear magnetic resonance spectroscopy (NMR) (AVANCE III 400, Bruker, Switzerland). C, H, N, and S analyses were made on a Vario analyzer (MICRO CUBE, Elementar, Germany) at least twice for each sample, meanwhile, the oxygen content was measured based on the differential analysis. A microscope (Olympus BX51) was used to investigate the dispersion of the mixture after adding the dispersants. The ash contents of the raw material and the extract were determined using a Differential Thermal Analysis (DTA) system with high purity nitrogen (DTG-60 A, Shimadzu, Japan) referring to other literature.20
3. Results and discussion
3.1. Separation of insoluble DCLR from the IL mixture
3.1.1 Performance of extraction without dispersants.
Ionic liquid [bmim]Cl was a solid at room temperature, and its melting point was nearly 75 °C. When DCRL came into direct contact with [bmim]Cl at above 75 °C, the mixture became a black solution/dispersion just like a gel, which showed that the soluble components in DCLR dissolved into [bmim]Cl. When the mixture was cooled to room temperature (about 25 °C), the mixture still remained like that at the high temperature and no [bmim]Cl crystallized or became solid. Meanwhile, there was no evidence of insoluble DCLR deposited on the bottom of flasks, testifying that the mixture was very viscous and the solid–liquid separation might be difficult. For example, the mixture, like a gel, could not be separated by centrifugation at room temperature, even though the speed of centrifugation was as high as 6000 rpm; it was also inefficient to separate the mixture using membrane separation. Although an air pump was used and the retention size of the filter membrane was improved to 2.5 μm, the membrane filtration stopped very early in the separation process, because “the gel” became more concentrated and the filter membrane clogged too easily.
3.1.2 Performance of extraction with dispersants.
For realizing the separation of the soluble components from the mixture, other traditional organic solvents: ethanol, ethylene glycol, NMP and pyridine, which can be dissolved into [bmim]Cl, were selected as dispersants to be added into [bmim]Cl to reduce the viscosity of the mixture. With the aid of dispersants the solid–liquid separation was easy after dissolution of DCLR in [bmim]Cl, and both centrifugation and membrane filtration can satisfy the requirement of separation. In the following study, membrane filtration using an air pump was applied and the pore diameter of the membrane was 1.2 μm in the process of separation.
3.1.3 The effect of dispersion on separation performance.
The micrographs of the systems with different NMP/ILs were examined in order to explore the performance of the dispersants. Experiments were carried out for 120 min at the DCLR/[bmim]Cl ratio of 1/10 and the temperature of 90 °C. After dissolutions, the mixture was cooled down to room temperature, and the upper layer of the solid–liquid mixture was sampled to be analyzed by a microscope.
The profiles of scattering effects with different NMP/[bmim]Cl ratios are shown in Fig. 1. Without the dispersant NMP, [bmim]Cl solution becomes yellow from transparency in the micrograph after treating DCLR, showing some soluble components of DCLR are transferred into the ionic liquid, meanwhile, some insoluble large particles which are above 100 μm are still suspended in the upper solution, testifying [bmim]Cl is so viscous that the separation of the mixture after contacting with DCLR is difficult (as mentioned above).
![Optical micrographs of the mixtures after mixed solvents with different NMP/IL ratios dissolve DCLR. Conditions: [bmim]Cl/DCLR = 1/10 (w/w), T = 90 °C, time = 120 min, NMP/IL = for A: 0; B: 0.5; C: 1.5; D: 2.0.](/image/article/2011/RA/c1ra00218j/c1ra00218j-f1.gif) |
| Fig. 1
Optical micrographs of the mixtures after mixed solvents with different NMP/IL ratios dissolve DCLR. Conditions: [bmim]Cl/DCLR = 1/10 (w/w), T = 90 °C, time = 120 min, NMP/IL = for A: 0; B: 0.5; C: 1.5; D: 2.0. | |
When the dispersant NMP is added into the mixture, the color of the liquid phase becomes light (Fig. 1B), meanwhile, the yellow micelles containing insoluble particles are still dispersed in the mixture, However, many insoluble particles with diameters above 50 μm disappear in the picture, implying that the larger particles (above 50 μm) deposit due to the decrease of viscosity. The more dispersant is added into mixture, the more insoluble particles deposit. When the ratio of NMP to [bmim]Cl is 2.0, all of the particles deposit by virtue of gravity, indicating that NMP is an efficient dispersant for [bmim]Cl and a NMP/IL ratio of 2.0 is sufficient to facilitate the separation.
Although all the other organic solvents (ethanol, ethylene glycol, and pyridine) can accelerate the separation of mixtures just like NMP, the extraction yields are different. The extraction yields of DCLR with the aid of ethanol, ethylene glycol, NMP and pyridine are 8.50, 18.4, 58.2 and 48.3%, respectively (Fig. 2), and the difference of extraction yields among dispersants might be ascribed to the various polarities of the dispersants. Since NMP exhibits the best performance for the extraction of DCLR amongst these dispersants, we selected NMP as a preferred dispersant to promote solid–liquid separation in the following experiments.
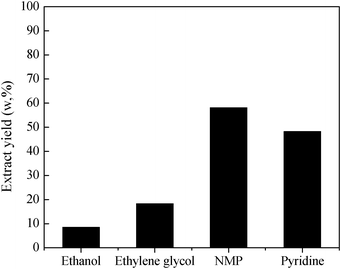 |
| Fig. 2
Extraction yields of DCLR for different dispersants. | |
3.2. Effect of [bmim]Cl mixed with NMP on extraction yields
3.2.1 Influence of NMP/IL ratio on extraction yields.
It was reported that NMP has been used to swell coal particles and it has an ability to dissolve some certain portion of coal.21 As DCLR was derived from coal liquefaction, undoubtedly, NMP alone might dissolve DCLR. In order to understand whether NMP would contribute significantly to the dissolution of DCLR, the extraction yield of DCLR was measured in a series of experiments with different NMP/IL ratios and the extraction yields are shown in Fig. 3(a). Meanwhile, for comparison, the separation experiment without adding NMP was realized according to the following procedures: after dissolving DCLR in [bmim]Cl alone at a given time and temperature, the mixture was rinsed with NMP at once to disperse the slurry and reduce the viscosity of the mixture, then filtered with an air pump simultaneously in order to avoid any further contact between NMP and DCLR.
![Extraction yields of DCLR as a function of (a) NMP/IL ratio, (b) temperature and (c) time. Conditions for (a): DCLR:[bmim]Cl (w/w) = 1 : 5, T = 90 °C, time = 2 h; for (b): DCLR:[bmim]Cl:NMP (w/w) = 1 : 5 : 10, time = 10 min; for (c): DCLR:[bmim]Cl:NMP (w/w) = 1 : 5 : 10, T = 90 °C.](/image/article/2011/RA/c1ra00218j/c1ra00218j-f3.gif) |
| Fig. 3
Extraction yields of DCLR as a function of (a) NMP/IL ratio, (b) temperature and (c) time. Conditions for (a): DCLR:[bmim]Cl (w/w) = 1 : 5, T = 90 °C, time = 2 h; for (b): DCLR:[bmim]Cl:NMP (w/w) = 1 : 5 : 10, time = 10 min; for (c): DCLR:[bmim]Cl:NMP (w/w) = 1 : 5 : 10, T = 90 °C. | |
The extraction yield without adding NMP is found to be 36.7%, and when NMP/IL ratios are 0.25, 0.5, 0.8 and 1.0, the extraction yields are 46.1%, 51.5%, 58.6% and 61.0%, respectively, which indicates an increase of the extraction yield when increasing the NMP/IL ratio in the mixed solvents; namely, NMP can not only facilitate the solid–liquid separation, but also improve the extract efficiency, just as NMP/CS2 mixtures improve the solubility of coal.22 Recently, this effect has also been observed by other researchers when they dissolved and dispersed coal using NMP/[bmim]Cl mixtures as solvents.17
However, the yield is kept stable at about 61.0% even though NMP/IL increases from 1.0 to 4.0, showing that the soluble components in DCLR dissolved fully into the mixed solvent in the NMP/IL range of 1.0–4.0. In our following work, a NMP/IL ratio of 2.0 is selected to dissolve DCLR due to a compromise between solubilizing power and rheological properties. For comparison, the yield of DCLR using NMP alone as the solvent under the same conditions was also examined and the maximum yield was 53.1%; undoubtedly, the mixed solvent consisting of NMP and [bmim]Cl can promote the yield of the extract.
The ash content (namely, the inorganic components) of DCLR is 24.0% (Table 1) and the content of the organic components can be calculated through the difference analysis and the value is 76.0%. If we think of all the organic components as soluble matter, the extraction ratio is as high as 80.3%, showing that the mixed solvent at a NMP/IL ratio of 2.0 is an efficient solvent to extract DCLR.
Although the dissolving mechanism of DCLR with the mixed solvent is not clear, and it is difficult to determine precisely what portion of DCLR has been dissolved by NMP and how NMP promotes the dissolution of DCLR in the presence of [bmim]Cl, undoubtedly, addition of NMP in [bmim]Cl will decrease the viscosity of the mixture, and increase the mixing degree of IL with DCLR, and consequently promote the dissolution of DCLR. Presumably, a portion of DCLR (especially, the Fixed Carbon (FC) which accounts for 41.8% of DCLR (Table 1)), whose structure might be similar to that of the initial coal since it is derived from nonanthracitic coals, should still keep cross-linked networks connected by relatively strong hydrogen bonds to some extent;23 if the cross-linked density of the network is high and the chains are relatively stiff, some portion of the soluble fraction within networks might be trapped and inaccessible to [bmim]Cl even though [bmim]Cl is a strong “fracturer” of hydrogen bonds,14 just as it is “locked” in the cross-linked networks. When NMP is added into [bmim]Cl, NMP is thought to swell FC to a degree as it does to coal,22 thus, just as NMP opens the lock of cross-linked networks, and makes [bmim]Cl much easier to contact the hydrogen bonds “locked” in the cross-linked networks of FC, thus the extraction yield is enhanced by the synergistic effect induced by [bmim]Cl and NMP.
3.2.2 Influence of temperature on extraction yields.
As mentioned above, [bmim]Cl is a solid at room temperature, thus the operational temperature for dissolving DCLR in [bmim]Cl alone should be enhanced to above 75 °C. But the mixed solvent at the NMP/[bmim]Cl ratio of 2.0 is a liquid at room temperature. So the mixed solvent can be used at the lower temperatures (e.g. room temperature).
The effect of temperature in the range from room temperature to 105 °C on extraction is shown in Fig. 3(b). The extraction yield is 45.0% at room temperature (about 25 °C). With increasing temperature, the extract yield improves, and the largest value is 55.9% at about 90 °C. Enhancement of the extraction yield should be ascribed to reduction of the viscosity in the system as the dissolving temperature increases, thus the mixed solvent can easily attack DCLR particles. Moreover, enhancement of the temperature also will promote the fracture of hydrogen bonds and increase the extraction yields.24
3.2.3 Influence of time on extraction yields.
For examining the extraction rate of DCLR in the mixed solvent, the influence of time on the extraction yield of DCLR by the mixed solvent was tested. For ensuring the dissolution of DCLR fully, a dissolving time of 120 min was firstly chosen to test the extraction yield, and the corresponding extraction yield was 60.9% (Fig. 3(c)). When the dissolving time was continuously reduced to 2 min from120 min, the yields fluctuated between 51.5% and 64.5%, and no evident decreases were seen. Here, fluctuation of data should be attributed to the heterogeneity of DCLR. Particularly, the extraction yield still is as high as 56.6% at 2 min, indicating the dissolution of DCLR in the mixed solvent is very quick, and 2 min is enough to extract DCLR, which is desired: on the one hand, it nearly realizes instant solution of the soluble components in DCLR; on the other hand, it can considerably reduce the time of extraction, thus surely decreasing the cost of the operation and saving energy.
3.3. FT-IR analysis
In order to determine the properties of the extract, the original DCLR, the extract and the dissolution-derived residue (insoluble substance in DCLR) were examined using FT-IR. The extracted matter was prepared under the following conditions: DCLR:IL:NMP was 1
:
2
:
4 and the dissolving temperature and time were 50 °C and 10 min, respectively. Insoluble substance was obtained by the following procedure: after DCLR was dissolved into the mixed solvent (mentioned above), the insoluble components were separated by air pump filtration, then washed three times with 20 ml of NMP and distilled water in turn, to remove any possible remaining [bmim]Cl and/or NMP on the surface of the insoluble powder, and finally dried at 70 °C for 12 h.
The FT-IR transmittance spectra of the raw DCLR, the residue after extraction and the extract are illustrated in Fig. 4. In contrast with DCLR, the transmittance at 2919 cm−1 assigned to the vibration of the CH2 stretch vibration (mostly methylene linking aromatic),25,26 and the peaks at 1602 cm−1 and 1438 cm−1, both of which are typical aromatic ring vibrations or condensed ring aromatic series,7 become faint or disappear in the residue after extraction, but strengthen drastically in the extract, showing that a great portion of the organic components containing aromatic hydrocarbons are transferred into the extract from DCLR though dissolution in mixed solvent and back-extraction with water. Moreover, the new peaks at 3039 cm−1 (stretching vibration of C–H in aromatic ring) and 2853 cm−1 (stretching vibration of C–H in methylene), and typical peaks in the range of 875–751 cm−1 (out-of-plane bending vibration of aromatic rings) become more obvious in the extract, which could be ascribed to the enrichment of organic components in the extract.
 |
| Fig. 4
FT-IR spectra of DCLR, the extract and insoluble matter (residue). | |
Furthermore, in order to evaluate the purity of the extracted organic components, the quinoline insoluble (QI) and ash content of the extract were examined and were 0.25% and undetected (Table 2), respectively. It is also testified that the extraction of DCLR by mixed solvents is hydrocarbon and no inorganic minerals are transferred into the final products even though the ash content of raw DCLR is as high as 24.0% (Table 1), which is desired since the purity of the extract is greatly related to high-value utilization of DCLR.
Table 2 Physico-chemical characteristics of the raw material and the extract
Sample |
C (%) |
H (%) |
N (%) |
S (%) |
O (%) |
H/C |
f
a
|
Ash (%) |
QI (%) |
Density (g cm−3) |
Softening point (°C) |
DCLR
|
84.1 |
6.40 |
0.91 |
4.97 |
3.07 |
0.913 |
0.781 |
33.9 |
— |
1.59 |
148 |
The extract |
77.5 |
4.95 |
1.52 |
0.42 |
15.7 |
0.766 |
0.760 |
undetected |
0.25 |
1.32 |
86 |
A new peak at 1020 cm−1 is evident in the extract and the peak should be ascribed to carbonyl or phenolic esters, both of which contains oxygen atoms.19 Correspondingly, the content of oxygen in the extract increases to 15.7% from 3.07% in raw DCLR (Table 2). Interestingly, the intensity and position of this band containing oxygen atoms vary as the NMP/IL ratio and dissolving temperature change (FT-IR spectra are not shown here). The formation or enrichment of this peak is uncertain and might result from the selective extraction caused by the mixed solvents.
3.4. Solid state 13C NMR analysis
The solid state 13C NMR spectra of DCLR and the extract are shown in Fig. 5. Both of them are similar, and there are mainly two resonance areas. One area (in the chemical shift δ range 110–160 ppm) is assigned to aromatic carbons and the other (about 60–22 ppm) is aliphatic carbons. It is clear that the aromatic area of the extract shrinks in contrast with that of DCLR, while the carbon aromaticity (fa)27 is calculated and the fa values of the extract and DCLR are 0.760 and 0.781 (Table 2), respectively, also testifying the reduction of aromatic carbons in the extract.
In addition, it is noticeable that a new resonance area in the range 182 to 162 ppm in the spectrum of the extract emerges, which indicates carbonyl carbon in the aromatic structure, increases or enriches;25 this observation is consistent with the analysis of FT-IR (mentioned above), showing the oxygen content in the extract increases (Table 2).
3.5. Recycling efficiency of the mixed solvent
The recycling efficiency of the mixed solvent was tested by recycling the solvent for extracting DCLR, and the mixed solvent was regenerated by rotary evaporation to remove water. The recycling efficiency of the mixed solvent was examined according to the following procedure: firstly, 60 g of the mixed solvent with a NMP/IL ratio of 2.0 was prepared, and then 6 g of the mixed solvent was used to dissolve 1 g of DCLR for 10 min and the remaining solution was used to rinse the insoluble portion of DCLR during the process of solid–liquid separation. Finally, the liquid was back-extracted with about 240 ml of water to precipitate dissolved matter. For reuse, the resulting liquid after precipitation was evaporated to remove water. Then, fresh DCLR was placed in the reactor with the equivalent amount of mixed solvent after regeneration to examine the recycling efficiency. Since the mixed solvent can be used at room temperature (as mentioned above), the dissolving temperature was chosen firstly at room temperature. The recycling efficiency is shown in Fig. 6.
![Extract of six recycling runs. Experimental conditions: DCLR:[bmim]Cl:NMP (w/w) = 1 : 2 : 4, time = 10 min.](/image/article/2011/RA/c1ra00218j/c1ra00218j-f6.gif) |
| Fig. 6 Extract of six recycling runs. Experimental conditions: DCLR:[bmim]Cl:NMP (w/w) = 1 : 2 : 4, time = 10 min. | |
In the first run, the extraction yield is 47.8%, which is similar to the value of 45.0% in Fig. 3(b), but in the second and third runs, the yields reduce dramatically, which might be attribute to the possible presence of trace water after rotary evaporation. For improving the yields, the dissolving temperature was increased to 90 °C in the following recycling runs, and the extraction yield restores to about 47.0%, indicating that the regenerated mixed solvent should be reused at a higher temperature. This observation shows that the dissolving temperature is one of the important parameters after the recovery of the mixed solvent and when the dissolving temperature is 90 °C in the recycling process, the extraction yields are kept about 47.0%.
4. Conclusions
Using the [bmim]Cl/NMP mixed solvent to dissolve DCLR along with the back-extraction of water, organic components in DCLR can be successfully extracted. NMP not only acts as a dispersant to facilitate the solid/liquid separation, but also works as an assistance solvent to increase the extraction yields. The mechanism of extraction is attributed to the swelling of the fixed carbon in DCLR induced by NMP and strong fracture force of [bmim]Cl to the hydrogen bonding network in DCLR. Moreover, dissolution of DCLR in mixed solvents is instant and 2 min of contact time is enough to dissolve 56.6% of DCLR when DCLR:IL:NMP is 1
:
5
:
10 (w/w) at 90 °C. The mixed solvent is inert to inorganic components in DCLR, and the QI value and ash content of the extract are 0.25% and undetermined, respectively. So the extracted substance can be used as potential precursors for preparing advanced carbon materials.
Acknowledgements
This work is financially supported by the National Natural Science Foundation of China (No. 21036007 and 21106168) and the Major Project of Chinese National Programs for Fundamental Research and Development (973 Program, No. 2009CB219901). The authors are also grateful to the National Institute of Clean and low Carbon Energy (NICE), Beijing, China for financial support.
References
- S. Vasireddy, B. Morreale, A. Cugini, C. Song and J. J. Spivey, Energy Environ. Sci., 2011, 4, 311 Search PubMed.
- Z. Liu, S. Shi and Y. Li, Chem. Eng. Sci., 2010, 65, 12 CrossRef CAS.
- M. Sugano, R. Ikemizu and K. Mashimo, Fuel Process. Technol., 2002, 77–78, 67 CrossRef CAS.
- K. Hirano, Fuel Process. Technol., 2002, 62, 109 CrossRef.
- X. Chu, W. Li, B. Li and H. Chen, Fuel, 2008, 87, 211 CrossRef CAS.
- J. Yang, Z. Wang, Z. Liu and Y. Zhang, Energy Fuels, 2009, 23, 4717 CrossRef CAS.
- J. Li, J. Yang and Z. Liu, Fuel Process. Technol., 2009, 90, 490 CrossRef CAS.
- D. B. Dadyburjor, T. E. Fout and J. W. Zondlo, Catal. Today, 2000, 63, 33 CrossRef CAS.
- M. S. Rana, V. Sámano, J. Ancheyta and J. A. I. Diaz, Fuel, 2007, 86, 1216 CrossRef CAS.
- T.-X. Wang, Z.-M. Zong, J.-W. Zhang, Y.-B. Wei, W. Zhao, B.-M. Li and X.-Y. Wei, Fuel, 2008, 87, 498 CrossRef CAS.
- Y. Zhou, N. Xiao, J. Qiu, Y. Sun, T. Sun, Z. Zhao and Y. Zhang, Fuel, 2008, 87, 3474 CrossRef CAS.
- N. Xiao, Y. Zhou, J. Qiu and Z. Wang, Fuel, 2010, 89, 1169 CrossRef CAS.
- K. Dong, G. Zhou, X. Liu, X. Yao, S. Zhang and A. Lyubartsev, J. Phys. Chem. C, 2009, 113, 10013 CAS.
- R. P. Swatloski, S.K. Spear, J. D. Holbrey and R. D. Rogers, J. Am. Chem. Soc., 2002, 124, 4974 CrossRef CAS.
- Y. Shim and H. J. Kim, ACS Nano, 2009, 3, 1693 CrossRef CAS.
- T. G. A. Youngs, C. Hardacre and J. D. Holbrey, J. Phys. Chem. B, 2007, 111, 13765 CrossRef CAS.
- P. Painter, N. Pulati, R. Cetiner, M. Sobkowiak, G. Mitchell and J. Mathews, Energy Fuels, 2010, 24, 1848 CrossRef CAS.
- A. E. Visser, R. P. Swatloski, W. M. Reichert, S. T. Griffin and R. D. Rogers, Ind. Eng. Chem. Res., 2000, 39, 640 CrossRef.
-
Y. Li, X. Zhang, S. Lai, H. Dong, X. Chen, X. Wang, Y. Nie, Y. Sheng and S. Zhang, Ionic Liquids to Extract Valuable Components from Direct Coal Liquefaction Residues Fuel., unpublished work Search PubMed.
- H. Cui, J. Yang, Z. Liu and J. Bi, Fuel, 2003, 82, 1549 CrossRef CAS.
- H. Shui, Fuel, 2005, 84, 939 CrossRef CAS.
- H. Shui, Z. Wang and J. Gao, Fuel Process. Technol., 2006, 87, 185 CrossRef CAS.
- A. M. Mastral, M.T. Izquierdo and B. Rubio, Fuel, 1991, 70, 139 CrossRef.
- J. D. Smith, C. D. Cappa, K. R. Wilson, R. C. Cohen, P. L. Geissler and R. J. Saykally, Proc. Natl. Acad. Sci. U. S. A., 2005, 102, 14171 CrossRef CAS.
- H. A. Akrami, M. F. Yardim, A. Akar and E. Ekinci, Fuel, 1997, 79, 1389 CrossRef.
- H. Shui, J. Liu, Z. Wang, M. Cao and X. Wei, Fuel Process. Technol., 2009, 90, 1047 CrossRef CAS.
- M. S. Solum, R. J. Pugmire and D. M. Grant, Energy Fuels, 1989, 3, 187 CrossRef CAS.
|
This journal is © The Royal Society of Chemistry 2011 |
Click here to see how this site uses Cookies. View our privacy policy here.