DOI:
10.1039/C2RA01022D
(Paper)
RSC Adv., 2012,
2, 4164-4168
Urchin-like ZnO microspheres synthesized by thermal decomposition of hydrozincite as a copper catalyst promoter for the Rochow reaction†
Received
3rd November 2011
, Accepted 20th February 2012
First published on 22nd March 2012
Abstract
Urchin-like ZnO microspheres were successfully prepared by thermal decomposition of hydrozincite synthesized via homogeneous precipitation of zinc nitrate and urea in the presence of a nonionic surfactant polyethylene glycol. The synthesis conditions, such as reaction temperature and time, precursor concentration, and the amount of surfactant added, as well as the catalytic properties of urchin-like ZnO microspheres as promoters for a commercial copper catalyst in dimethyldichlorosilane synthesis were investigated. In addition, the formation mechanism of urchin-like microspheres from hydrozincite to ZnO was proposed. The ZnO samples were characterized by X-ray diffraction, scanning electron microscopy, transmission electron microscopy, thermogravimetric analysis, and N2 adsorption. It was found that zinc nitrate concentration and the amount of surfactant are the key factors that lead to the formation of urchin-like ZnO microspheres. These ZnO samples had BET surface areas of 16–30 m2 g−1 and an average diameter of 3–8 μm. Compared with commercial Zn microspheres and ZnO nanoparticles, urchin-like ZnO microspheres showed a better performance in dimethyldichlorosilane synthesis via the Rochow reaction due to their larger surface area, which created more interfacial contacts with the copper catalyst and active Cu3Si species. The work is helpful for developing novel catalyst promoters and understanding the role of the promoter in the Rochow reaction.
1. Introduction
The Rochow reaction, which was discovered by Eugene Rochow in the 1940s,1 has been widely employed in the organosilane industry as it is still the most economical route to produce methylchlorosilanes (MCSs). In this reaction, solid silicon reacts with chloromethane (MeCl) gas over copper catalysts, which primarily yields methyltrichlorosilane (CH3SiCl3, M1), dimethyldichlorosilane ((CH3)2SiCl2, M2), and trimethylchlorosilane ((CH3)3SiCl, M3). High selectivity for M2 is most desired due to it being the main monomer for the synthesis of organosilicon products commercially.2 Previous work has demonstrated that Zn compounds, such as Zn and ZnCl2 are effective promoters to assist the copper catalyst in increasing the M2 selectivity.2–6 In addition, a recent US patent showed that ZnO powder as a promoter can be used for promoting the copper catalyst.7 However, to the best of our knowledge, so far no report about the effects of particle morphology and the crystal structure of Zn compound promoters on their activity in the Rochow reaction has been published. Thus, it would be very interesting to explore the influence of different structured Zn promoters on the Rochow reaction and the role of Zn compound in promoting copper catalysts as it is not been fully understood yet.8,9
ZnO, an important multifunctional semiconductor with a wide direct energy band gap of 3.37 eV and large exciton binding energy about 60 meV,10 has been used in optoelectronics,11,12 gas sensing,13 sensors,14,15 microarrays,16 catalysis,17,18 and solar cells.19 ZnO micro/nanostructures such as nanorods,11 hexagonal disks,20 nanowires,21 nanobelts,22 polyhedral cages,23 nanospheres,24 pyramid-shaped cystals,25 nanocups26, and hollow microspheres27,28 have been synthesized by various methods, such as electrodeposition,29,30 sol–gel method,31 chemical template method,32 and hydrothermal method.33,34
In our previous work, we explored the structure–catalysis relationship of copper-based catalysts with mesoporous Cu2O and flower-like CuO microspheres as model catalysts for M2 synthesis via the Rochow reaction.35,36 Herein, we report the preparation and characterization of urchin-like ZnO microspheres as copper catalyst promoters in Rochow reaction. Urchin-like ZnO was prepared by thermal decomposition of hydrozincite which was synthesized by homogeneous precipitation of zinc nitrate and urea in the presence of a nonionic surfactant polyethylene glycol (PEG). The synthesis conditions for the urchin-like ZnO microspheres were systematically investigated and their performance as a copper catalyst promoter in the Rochow reaction was examined. Compared with commercial promoters, Zn microspheres and ZnO nanoparticles, urchin-like ZnO microspheres exhibit higher M2 selectivity and Si conversion under a given reaction condition. The work reveals the effect of the catalyst promoter structure on the Rochow reaction and would be beneficial to the design of good catalyst promoters.
2. Experimental
2.1. Material synthesis
All chemicals (Sinopharm Chemical Reagent Co.Ltd., Shanghai, China) used in the experiments were of analytical grade without further purification. To optimize the synthesis conditions and investigate the product formation mechanism, the parameters such as the reactant concentration, reaction temperature and time, and the amount of added PEG were varied as listed in Table 1. In our experiments, the molar ratio of zinc nitrate hexahydrate (Zn(NO3)2·6H2O, AR, 99%) and urea (CO(NH2)2, AR, 99%) was controlled to be 0.5.27 In a typical synthesis (see sample S3 in Table 1), 0.03 mol zinc nitrate, 0.06 mol urea, and 6 g polyethylene glycol (PEG, MW 20
000) were dissolved in 200 mL of deionized water. The solution was then transferred to a round-bottom flask with a mounted water cooled condenser and heated up to 90 °C in oil bath for 30 min. The resulting precipitate was filtrated, washed with deionized water, and dried at 80 °C, followed by calcination in air at 450 °C for 3.0 h to obtain ZnO samples.
Table 1 The synthesis conditions used in the preparation of ZnO samples
Sample |
Zinc nitrate (mol) |
Zinc nitrate (M) |
Urea (mol) |
PEG (g) |
Time (h) |
T/°C |
S1 |
0.005 |
0.025 |
0.01 |
6 |
0.50 |
90 |
S2 |
0.020 |
0.100 |
0.04 |
6 |
0.50 |
90 |
S3 |
0.030 |
0.150 |
0.06 |
6 |
0.50 |
90 |
S4 |
0.050 |
0.250 |
0.10 |
6 |
0.50 |
90 |
S5 |
0.030 |
0.150 |
0.06 |
0 |
0.50 |
90 |
S6 |
0.030 |
0.150 |
0.06 |
3 |
0.50 |
90 |
S7 |
0.030 |
0.150 |
0.06 |
12 |
0.50 |
90 |
S8 |
0.030 |
0.150 |
0.06 |
6 |
0.25 |
90 |
S9 |
0.030 |
0.150 |
0.06 |
6 |
1.00 |
90 |
S10 |
0.030 |
0.150 |
0.06 |
6 |
3.00 |
90 |
S11 |
0.030 |
0.150 |
0.06 |
6 |
0.50 |
80 |
S12 |
0.030 |
0.150 |
0.06 |
6 |
0.50 |
100 |
2.2. Characterization
The samples were characterized by X-ray diffraction (XRD) patterns using a Bruker D8 diffractometer with Cu-Kα radiation of wavelength λ = 0.1541 nm. Transmission electron microscopy (TEM) images were taken on a Hitachi H-800 transmission electron microscope. Scanning electron microscopy (SEM) images were taken with a JSM-6700F scanning electron microscope. Adsorption–desorption isotherms of N2 at 77 K were measured using a surface area & pore size analyzer (NOVA 3200e, Quantachrome). Prior to the measurement, the sample was degassed at 200 °C for 4 h under vacuum. The specific surface area was determined according to the Brunauer–Emmett–Teller (BET) method in the relative pressure range 0.05–0.2. The pore size distribution was calculated by the Barrett–Joyner–Halenda (BJH) method using the adsorption isotherm branch. Thermogravimetric analysis (TGA) was measured on a Seiko Instruments EXSTAR TG/DTA 6300 with a heating rate of 10 °C min−1 in air stream.
2.3. Catalytic test
The evaluation of catalyst performance was carried out with a typical MCS lab fixed-bed reactor.3 0.10 g of urchin-like ZnO microspheres was homogeneously mixed with 1.00 g of commercial copper catalysts containing Cu, Cu2O, and CuO components (provided by Jiangsu Hongda New Material Co., Ltd), and further mixed with 10.00 g silicon (20–50 mesh, 98.5%, provided by Jiangsu Hongda New Material Co., Ltd) to form a contact mass, which was then loaded into the glass tube reactor in the fixed-bed reactor. The same amount of commercial Zn microspheres and ZnO particles was also tested for a comparison. The reactor system was initially purged with purified N2 for 0.5 h followed by heating to 325 °C within 1 h under N2 flow rate of 25 mL min−1. Subsequently, N2 was turned off and chloromethane (MeCl) gas with a flow rate of 25 mL min−1 was introduced into the reactor to react with Si at 325 °C. After a given period of 24 h, the reaction was terminated. The gas product was cooled down to liquid phase with a water circulating bath controlled at 5 °C by a programmable thermal circulator (GDH series, Ningbo xinzhi biological technology Co., LTD). The spent contact mass (residual solid after reaction) containing unreacted Si powder, Cu compounds, and promoters was weighed to calculate Si conversion, while the collected liquid was analyzed with an Agilent Technologies 7890A GC System. The MCS products are mainly comprised of M1, M2, and M3, which account for about 95 wt % of total reaction products.37 For simplifying the calculation, other trace products and the change of catalyst are not taken into account, hence, the Mi (i = 1, 2, 3) selectivity and Si conversion are calculated according to the following formulas: |  | (1) |
|  | (2) |
3. Results and discussion
As ZnO was obtained by calcination of hydrozincite (Zn5(CO3)2(OH)6), which was initially synthesized from zinc nitrate. The morphology and structure of ZnO should have resembled those of hydrozincite, of which the results will be discussed shortly. For clarity purpose, sample S3 (Table 1) was selected for the following discussion as it was synthesized under the optimized synthesis conditions. Fig. 1a shows the typical XRD patterns of the hydrozincite and the resulting ZnO sample, of which diffraction peaks can be indexed to the pure phase of hydrozincite (JCPDS 54-0047) and pure hexagonal ZnO (JCPDS 70-2551) as there is not any diffraction pattern attributed to the impurities. The average hydrozincite crystal size is 21 nm, calculated using the Debye–Scherrer formula, based on the its diffraction peak at 33.2° while that of the ZnO sample is 23 nm based on the diffraction peak at 36.3°. The thermogravimetric (TG) curves of hydrozincite and PEG are presented in Fig. 1b. Complete combustion of PEG is achieved at about 300 °C and there is no more weight loss observed for hydrozincite above 450 °C, suggesting complete removal of PEG and total conversion of hydrozincite to ZnO. Fig. 1c and 1d clearly show that the urchin-like morphology of the initially prepared hydrozincite was maintained after calcination at 450 °C, which results in the generation of ZnO with the same morphology. The overall microsphere diameters are in the range 3–8 μm.
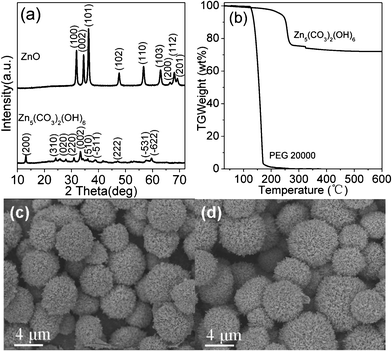 |
| Fig. 1 (a) XRD patterns of hydrozincite and ZnO samples, (b) TG curves of hydrozincite and PEG in air, (c) SEM images of hydrozincite and (d) ZnO microspheres (sample S3). | |
The SEM image taken at higher magnification (Fig. 2a) shows the detailed surface morphology of a single ZnO microsphere, which is assembled with nanoneedles. The TEM image in Fig. 2b displays dense internal structure of urchin-like ZnO microspheres. The high resolution TEM image as shown in Fig. 2c indicates lattice spacings of about 0.25 nm and 0.28 nm, which are attributed to (101) and (100) planes of the ZnO crystal, respectively. The two direction lattice fringes observed in the high resolution image hence confirm the polycrystalline of the building units. The profile of nitrogen adsorption–desorption isotherm is presented in Fig. 2d. The BET surface area of ZnO microspheres is 30.7 m2 g−1 and the shape of the isotherm with a capillary condensation step in the adsorption branch corresponds to a type IV isotherm according to the IUPAC classification.38 Pore size distribution curve (inset of Fig. 2d) indicates that the pore size is larger than 50 nm, beyond the mesoporous level.
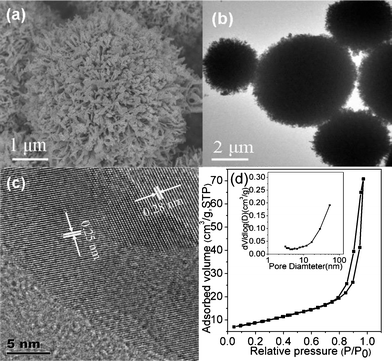 |
| Fig. 2 SEM image (a), TEM images (b and c), and N2 adsorption–desorption isotherm and pore size distribution curve (inset) (d) of urchin-like ZnO microspheres (sample S3). | |
The following are the reactions involved during the synthesis of hydrozincite and ZnO microspheres:
| CO(NH2)2 + H2O → CO2 + 2NH3 | (3) |
| NH3 + H2O → NH4+ + OH− | (4) |
| 5Zn2+ + 2CO2 + 6OH− + 2H2O → Zn5(CO3)2(OH)6↓ + 4H+ | (5) |
| Zn5(CO3)2(OH)6 → 5ZnO + 2CO2 + 3H2O | (6) |
As indicated by reactions 3 and 4, the dissociation of urea generates hydroxide and carbon dioxide, which react with zinc ions to form hydrozincite (reaction 5). After calcination in air at 450 °C (reaction 6) for 3.0 h, ZnO microspheres were obtained. A schematic illustration of the evolution process of the obtained urchin-like microspheres based on the systematic investigation on synthesis parameters such as zinc nitrate concentrations (see Fig. S1†), PEG amount (see Fig. S2†), and reaction time (see Fig. S3†), is depicted in Fig. 3. In the early stage, hydrozincite nuclei were formed from the reaction of Zn2+, OH−, and CO32− ions, which further grow to form hydrozincite nanoneedles (Fig. 3b). The individual units of nanoneedles then self-assembled radically, forming flower-like hydrozincite (Fig. 3c), and eventually urchin-like microspheres directed by PEG linear chains (Fig. 3d). As PEG polymeric chains are known to easily adsorb on the surface of colloids,39 the addition of PEG will modify the growth kinetics of the growing colloids, which finally leads to the anisotropic growth of the crystals.40,41 Long chain PEG or a large dosage of PEG can confine more than one direction of the growing colloid and eventually formed spherical colloids.42,43 Thus, urchin-like hydrozincite microspheres could be successfully synthesized by adding PEG. Lee et al.44 reported that four parameters such as kinetic, temperature, reaction time, and capping agents can affect the growth pattern of nanocrystals under non-equilibrium kinetic growth conditions in the solution-based approach. In addition, in the precipitation process, the kinetics of nucleation and the particle growth in the homogeneous solution can be effectively adjusted by controlling precursors concentration.27 In our experiments, the growth rate of hydrozincite nuclei as well as the urchin-like hydrozincite microspheres are considered to be controlled by the concentrations of Zn2+ and OH−, CO2 released by urea. As the reaction proceeds, the concentration of Zn2+ cations and urea in the solution continuously decreases, resulting in the slower growth of urchin-like hydrozincite microspheres.
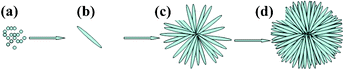 |
| Fig. 3 Schematic illustration of the evolution process of the obtained urchin-like microspheres: (a) nuclei formation from the precipitation of the precursor ions, (b) hydrozincite nanoneedle, (c) flower-like hydrozincite, and (d) urchin-like hydrozincite microsphere. | |
Table 2 presents the catalytic performance of the urchin-like ZnO microspheres (sample S3) together with commercial Zn microspheres and ZnO particles (see Fig. S4†) as copper catalyst promoters, and unpromoted for the Rochow reaction. It is found that urchin-like ZnO microspheres exhibited higher M2 selectivity (SM2) of 85.5% than that of unpromoted (69.5%), commercial Zn (81.5%), and ZnO (83.9%), as well as slightly higher Si conversion (CSi) (34.5%) than that of commercial Zn (32.9%) and ZnO (33.2%). Other ZnO samples show a comparable performance to S3, not shown here. M2 is highly valued commercially, an increase as little as 1% of selectivity for an annual production output of 105 ton MCS could lead to a net gain of more than 1 million US Dollars. The results hence indicate that urchin-like ZnO microspheres are effective as a copper catalyst promoter in the Rochow reaction.
Table 2 The catalytic performance of urchin-like ZnO microspheres compared with that of unprompted, commercial Zn, and ZnO
Promoters |
SM2 (%) |
SM1 (%) |
SM3 (%) |
CSi (%) |
Unpromoted |
69.5% |
26.1% |
4.4% |
15.9% |
Commercial Zn |
81.5% |
15.7% |
2.8% |
32.9% |
Commercial ZnO |
83.9% |
14.5% |
1.6% |
33.2% |
Urchin-like ZnO microspheres (S3) |
85.5% |
12.8% |
1.7% |
34.5% |
Fig. 4A and B show XRD patterns of the spent contact masses after reaction at 325 °C. While Si, Cu, and Cu3Si species appeared in the four reacted contact masses, no Cu2O and CuO species were detected, as shown in Fig. 4A although the copper catalyst used here is composed of Cu, Cu2O, and CuO. The disappearance of Cu2O and CuO species was instead replaced by a strong intensity of Cu diffraction peaks. This could be due to the removal of oxygen from Cu2O and CuO by chlorosilane, and all of the oxygen from the copper oxide (Cu2O and CuO) catalyst ends up as siloxane.45 A more detailed observation of the XRD patterns (Fig. 4B) reveals a much higher intensity of Cu3Si for urchin-like ZnO microspheres’ contact mass suggesting that the prepared ZnO microspheres are more active in assisting the formation of Cu3Si on the Si surface than unpromoted, commercial Zn, and ZnO at 325 °C. In the Rochow reaction, Cu3Si is normally considered as the key catalytic active species, on which M2 is created.46,47 Cu and Si were combined by diffusion to form Cu3Si, which is always formed between the copper catalyst and Si interface, thus, an indication of activity for a copper catalyst.48 As the Rochow reaction proceeds, the active Si species in Cu3Si is consumed, followed with the diffusion of Cu into the bulk Si matrix to form new Cu3Si active centers.48,49 The addition of a Zn promoter helps increase the diffusion rate of Si through copper, which could expedite the formation of Cu3Si, making it readily available for M2 formation.9,50,51 Thus, we can conclude that the urchin-like ZnO microspheres can act as an effective promoter due to their high surface area (see Table S1, ESI†), which facilitates the alloying of Cu and Si, and promotes the formation of active Cu3Si phases, which is the key species to enhance the catalytic activity for M2 production. In addition, during the reaction the copper catalyst and zinc oxide are in intimate contact and form agglomerated particles that allow for increasing the selectively of M2.7 Urchin-like ZnO microspheres, due to their high specific surface area, can increase the contact surface between zinc oxide and copper catalyst, which is helpful for the formation of agglomerated particles and lead to higher selectivity of M2.
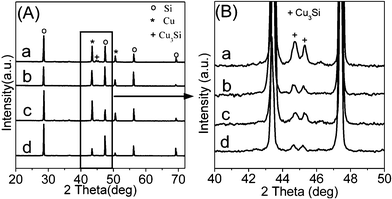 |
| Fig. 4 XRD patterns of contact masses after reaction containing (a) Si, copper catalyst, and urchin-like ZnO microspheres, (b) Si, copper catalyst, and commercial ZnO, and (c) Si, copper catalyst, and commercial Zn, (d) Si and copper catalyst. B is the enlarged view of A. | |
4. Conclusions
In conclusion, we have demonstrated the effect of urchin-like ZnO microspheres as a catalyst promoter in the Rochow reaction. ZnO samples are obtained by thermal decomposition of hydrozincite synthesized by homogeneous precipitation, and have surface areas of 16–30 m2 g−1 and an average diameter of 3–8 μm. As a catalyst promoter for copper catalysts, the urchin-like ZnO microspheres are superior to the commercial Zn microspheres and ZnO particles, because the high surface area urchin-like ZnO microspheres can create a larger contact interface with the copper catalyst, leading to the formation of more active Cu3Si species, and to the further increase of the diffusion rate of Si through copper. Our work is helpful for developing novel catalyst promoters and understanding the catalytic mechanism of the Rochow reaction.
Acknowledgements
The authors gratefully acknowledge the financial support from the Hundred Talents Program of the Chinese Academy of Sciences (CAS), the CAS-Locality Cooperation Program (No. DBNJ-2011-058), National Natural Science Foundation of China (No. 21031005), and State Key Laboratory of Multiphase Complex Systems (No. MPCS-2011-D-14).
References
- E. G. Rochow, J. Am. Chem. Soc., 1945, 67, 963 CrossRef CAS.
- D. Seyferth, Organometallics, 2001, 20, 4978 CrossRef CAS.
- L. N. Lewis and W. J. Ward, Ind. Eng. Chem. Res., 2002, 41, 397 CrossRef CAS.
- A. D. Gordon, B. J. Hinch and D. R. Strongin, J. Catal., 2009, 266, 291 CrossRef CAS.
- J. M. Bablin, A. C. Crawford, D. C. DeMoulpied and L. N. Lewis, Ind. Eng. Chem. Res., 2003, 42, 3555 CrossRef CAS.
- N. P. Lobusevich, SUP-237892-A, 1969 Search PubMed.
- M. K. Barr, T. M. Murphy and M. G. Willams, USP-7205258B2, 2007 Search PubMed.
- L. D. Gasper-Galvin, D. M. Sevenich, H. B. Fpiedrlch and D. G. Rethwlsch, J. Catal., 1991, 128, 468 CrossRef CAS.
- A. D. Gordon, B. J. Hinch and D. R. Strongin, Catal. Lett., 2009, 133, 14 CrossRef CAS.
- T. Zhang, W. Dong, M. Keeter-Brewer, S. Konar, R. N. Njabon and Z. R. Tian, J. Am. Chem. Soc., 2006, 128, 10960 CrossRef CAS.
- M. Bitenc, P. Podbrscek, Z. C. Orel, M. A. Cleveland, J. A. Paramo, R. M. Peters and Y. M. Strzhemechny, Cryst. Growth Des., 2009, 9, 997 CAS.
- R. Zhang, L. Fan, Y. Fang and S. Yang, J. Mater. Chem., 2008, 18, 4964 RSC.
- J. Kim and K. Yong, J. Phys. Chem. C, 2011, 115, 7218 CAS.
- J. F. Zang, C. M. Li, X. Q. Cui, J. X. Wang, X. W. Sun, H. Dong and C. Q. Sun, Electroanalysis, 2007, 19, 1008 CrossRef CAS.
- J. P. Liu, C. X. Guo, C. M. Li, Y. Y. Li, Q. B. Chi, X. T. Huang, L. Liao and T. Yu, Electrochem. Commun., 2009, 11, 202 CrossRef CAS.
- W. H. Hu, Y. S. Liu, Z. H. Zhu, H. B. Yang and C. M. Li, ACS Appl. Mater. Interfaces, 2010, 2, 1569 CAS.
- M. Behrens, S. Kißner, F. Girsgdies, I. Kasatkin, F. Hermerschmidt, K. Mette, H. Ruland, M. Muhler and R. Schlogl, Chem. Commun., 2011, 47, 1701 RSC.
- C. C. Li, R. J. Lin, H. P. Lin, Y. K. Lin, Y. G. Lin, C. C. Chang, L. C. Chen and K. H. Chen, Chem. Commun., 2011, 47, 1473 RSC.
- C. Xu, P. Shin, L. Cao and D. Gao, J. Phys. Chem. C, 2010, 114, 125 CAS.
- B. Reeja-Jayan, E. D. Rosa, S. Sepulveda-Guzman, R. A. Rodriguez and M. J. Yacaman, J. Phys. Chem. C, 2008, 112, 240 CAS.
- S. H. Ko, I. Park, H. Pan, N. Misra, M. S. Rogers, C. P. Grigoropoulos and A. P. Pisano, Appl. Phys. Lett., 2008, 92, 154102 CrossRef.
- Y. Yang, J. Qi, Q. Liao, Y. Zhang, L. Tang and Z. Qin, J. Phys. Chem. C, 2008, 112, 17916 CAS.
- P. X. Gao and Z. L. Wang, J. Am. Chem. Soc., 2003, 125, 11299 CrossRef CAS.
- G. Zhang, X. Shen and Y. Yang, J. Phys. Chem. C, 2011, 115, 7145 CAS.
- Z. Dai, K. Liu, Y. Tang, X. Yang, J. Bao and J. Shen, J. Mater. Chem., 2008, 18, 1919 RSC.
- S. H. Jung, E. Oh, K. H. Lee, Y. Yang, C. G. Park, W. Park and S. H. Jeong, Cryst. Growth Des., 2008, 8, 265 CAS.
- C. Yan and D. Xue, J. Phys. Chem. B, 2006, 110, 11076 CrossRef CAS.
- M. C. Neves, T. Trindade, M. B. Timmons and D. Jesus, Mater. Res. Bull., 2001, 36, 1099 CrossRef CAS.
- T. F. Jaramillo, S. H. Baeck, A. Kleiman-Shwarsctein and E. W. McFarland, Macromol. Rapid Commun., 2004, 25, 297 CrossRef CAS.
- T. Pauporte and J. Rathousky, J. Phys. Chem. C, 2007, 111, 7639 CAS.
- X. Wu, K. Li and H. Wang, J. Hazard. Mater., 2010, 174, 573 CrossRef CAS.
- Z. Liu, Z. Jin, W. Li and J. Qiu, Mater. Res. Bull., 2006, 41, 119 CrossRef CAS.
- L. Dinga, Z. Yinminb and W. Yurena, Appl. Surf. Sci., 2008, 254, 5849 CrossRef.
- H. Wang, G. Li, L. Jia, G. Wang and C. Tang, J. Phys. Chem. C, 2008, 112, 11738 CAS.
- Z. L. Zhang, H. W. Che, Y. L. Wang, J. J. Gao, L. R. Zhao, X. L. She, J. Su, P. Gunawan, Z. Y. Zhong and F. B. Su, Ind. Eng. Chem. Res., 2012, 51, 1264 CrossRef CAS.
- Z. L. Zhang, H. W. Che, Y. L. Wang, J. J. Gao, X. L. She, J. Su, Z. Y. Zhong and F. B. Su, RSC Adv., 2012, 2, 2254 RSC.
- C. P. Homme and G. Simon, USP-4661613, 1987 Search PubMed.
- K. S. W. Sing, D. H. Everett, R. A. W. Haul, L. Moscou, R. A. Pierotti, J. Rouquerol and T. Siernieniewska, Pure Appl. Chem., 1985, 57, 603 CrossRef CAS.
- S. Liufu, H. Xiao and Y. Li, Powder Technol., 2004, 145, 20 CrossRef CAS.
- X. Hou, F. Zhou, B. Yua and W. Liu, Mater. Lett., 2007, 61, 2551 CrossRef CAS.
- X. Zhou, D. Zhang, Y. Zhu, Y. Shen, X. Guo, W. Ding and Y. Chen, J. Phys. Chem. B, 2006, 110, 25734 CrossRef CAS.
- X. Zhou, S. Chen, D. Zhang, X. Guo, W. Ding and Y. Chen, Langmuir, 2006, 22, 1383 CrossRef CAS.
- Z. Li, Y. Xiong and Y. Xie, Inorg. Chem., 2003, 42, 8105 CrossRef CAS.
- S. M. Lee, S. N. Cho and J. Cheon, Adv. Mater., 2003, 15, 441 CrossRef CAS.
- L. N. Lewis, W. V. Ligon and J. C. Carnahan, Silicon Chem., 2002, 1, 23 CrossRef CAS.
- B. F. Banholzer and M. C. Burrell, J. Catal., 1988, 114, 259 CrossRef.
- T. C. Frank, K. B. Kester and J. L. Falconer, J. Catal., 1985, 91, 44 CrossRef CAS.
- W. F. Banholzer, N. Lewis and W. Ward, J. Catal., 1986, 101, 405 CrossRef CAS.
- W. Luo, G. Wang and J. Wang, Ind. Eng. Chem. Res., 2006, 45, 129 CrossRef CAS.
- N. Floquet, S. Yilmaz and J. L. Falconer, J. Catal., 1994, 148, 348 CrossRef CAS.
- J. M. Bablin, L. N. Lewis, P. Bui and M. Gardner, Ind. Eng. Chem. Res., 2003, 42, 3532 CrossRef CAS.
Footnote |
† Electronic Supplementary Information (ESI) available: SEM images and XRD patterns of the products. See DOI: 10.1039/c2ra01022d/ |
|
This journal is © The Royal Society of Chemistry 2012 |
Click here to see how this site uses Cookies. View our privacy policy here.