DOI:
10.1039/C2RA01175A
(Paper)
RSC Adv., 2012,
2, 1890-1896
Waste paper based activated carbon monolith as electrode materials for high performance electric double-layer capacitors
Received
24th November 2011
, Accepted 24th November 2011
First published on 6th January 2012
Abstract
A surface modified carbon monolith (m-CM) was successfully synthesized by carbonization of a waste paper precursor, followed by a simple surface modification with a HNO3 solution. The morphology, pore structure, and surface functional groups of the as-obtained m-CM are characterized by scanning electron microscopy (SEM), N2 adsorption–desorption measurements, and Fourier transform infrared spectroscopy (FT-IR), respectively. The electrochemical properties are investigated by cyclic voltammetry (CV), galvanostatic charge–discharge, and electrochemical impedance spectroscopy (EIS). After surface modification, the surface hydrophilicity and the electrical conductivity of the m-CM is increased by introducing functional groups and dissolution of the impurities, thus the electrochemical performances of the m-CM are significantly improved. A high gravimetric capacitance (Cm) and volumetric capacitance (Cv) of 232 F g−1 and 36.7 F cm−3 is obtained at a current density of 5 mA cm−2 in 2 M KOH electrolyte, respectively. Based on the above investigation, such a treatment could be a promising method to convert organic waste to high-performance carbon electrode materials for electric double-layer capacitors.
Introduction
In the near future, energy conservation and pollution reduction will become two of the most significant factors in economic development and social circulate. One approach to solve these problems is the development of new clean energy storage devices and another is the recycling of the waste.1 Presently, two types of electrochemical energy storage devices are available: supercapacitors and batteries.2–4 Batteries have a higher specific energy, but have lower specific power and a limited number of charging–discharging cycles than supercapacitors.5 Supercapacitors can be divided into electric double-layer capacitors (EDLCs) and pseudo-capacitors.6 EDLCs store energy through the storage and release of charges along the double layer formed at the electrode–electrolyte interface,7 which are characterized as high-power density, long cycle life, and with a quick charge–discharge capability. They aroused considerable interest in applications in electric vehicles, uninterruptible power sources, digital communications system, and other high-power apparatuses.5
All kinds of electrode materials, including activated carbons (ACs),8,9carbon aerogels,10carbon nanotubes,11 and carbon monoliths (CMs)12,13 have been investigated in EDLCs. Among them, ACs are the main electrode materials due to their relatively low cost and porous structure with high surface area. Presently, activated carbons are prepared from natural products such as seaweed biopolymers14 and wood precursors.15 These kind of carbons exploited from natural organic systems become more and more promising in EDLCs because of their high performance and abundant raw materials. However, in practical applications, the consumption of large amounts of natural resources would result in the damage of the ecological environment. Thus developing CMs from inexpensive, abundant, and sustainable organic waste seems to be the most effective and promising approach to prepare carbon electrode materials for EDLCs.
It is well known that the pore structures play important role in determining the capacitance of carbon materials. It has been demonstrated that not all pores are effective in the charge accumulation due to ion sieving effects of the electrolyte16 and the poor hydrophilicity of the carbon surface. A good matching between the electrode pore size and the dimensions of the ionic species, and excellent surface hydrophilicity of electrodes are critical for an optimal performance of these systems.17–19 Generally speaking, the surface hydrophilicity of the carbons in aqueous electrolytes can be improved further by incorporating heteroatoms such as oxygen, nitrogen, and boron atoms in the carbon framework.20–23 Substantial efforts have been devoted to tailoring the surface properties of porous carbon.24 One way to functionalize them is the treatment in an acidic solution,25 another strategy is to employ a polymer with a functionality as a carbon precursor.26–28
Herein, we present a waste paper based carbon monolith synthesized by carbonization of a waste paper precursor. The as-prepared m-CM, taking advantage of their self-sintering ability, can be widely used as an environment friendly electrode material due to its abundant sources, facile preparation, low cost, lower pollution, and easy to realize large-scale industrialization.29 Since the inorganic impurities which exist in the obtained waste based CM can be dissolved by the HNO3 solution, the CM is treated by a facile modification method using HNO3 as the treatment solution. The electrochemical properties of the m-CM are significantly improved after surface modification due to its improved surface hydrophilicity and electrical conductivity by introduction of functional groups and the dissolving of the impurities. Additionally, the as-prepared m-CM has a higher volumetric capacitance than fine powder carbons such as CMK-3 and AC, suggesting the necessity of surface modification and the potential application in the conversion of organic waste to high-performance carbon electrode materials for EDLCs.
Experimental
Materials
HNO3 and KOH, purchased from Sinopharm Chemical Reagent Co. Ltd, were all of analytical grade and were used as received without any further purification. AC was purchased from ShaoWu Xin Sen Carbon Company, China. CMK-3 was synthesized with the method described by Ryoo et al.30
Synthesis of the m-CM
The typical preparation process of m-CM is illustrated in Fig. 1. Waste paper from a cardboard box was cut into pieces to be used as precursors, then the carbonization process was carried out in an argon atmosphere with a temperature increase rate of 3 °C min−1 to a final temperature of 900 °C and maintained for 6 h. After the samples were cooled to room temperature, surface modification was carried out in a HNO3 solution under different conditions, including different temperatures, different concentrations of HNO3 solution and modification time. Subsequently, m-CM was recovered and washed thoroughly with distilled water until the pH was close to 7, and further dried at 80 °C overnight. The carbons modified through different conditions were denoted as m-CMx-y-z, where x is the HNO3 concentration, y is the modification time, and z indicates the modification temperature. For instance, m-CM6-8-120 means that the carbon was modified with 6 M HNO3 for 8 h, and the modification temperature was 120 °C.
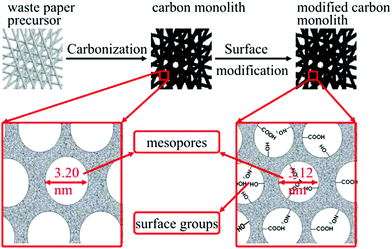 |
| Fig. 1 A schematic diagram of the preparation procedure and the mesoporous structure of the m-CM material. | |
Structure characterization
The structure and morphology of the samples were characterized by a field emission scanning electron microscope (JEOL, JSM-6701F, Japan). The pore structure properties of the m-CMs were characterized by nitrogen adsorption–desorption experiments (Micromeritics, ASAP 2010M, USA). The functional groups on the m-CM surface were measured by a FT-IR technique which were recorded on a Nicolet Nexus 670 Fourier transform infrared spectrometer using a KBr tableting technique.
Electrochemical measurements
The electrochemical measurements of each as-prepared electrode were carried out using an electrochemical working station (CHI660C, Shanghai, China) in a half-cell setup configuration at room temperature and using a 2 M KOH solution as the electrolyte. A platinum plate electrode and a saturated calomel (SCE) electrode served as the counter electrode and the reference electrode, respectively. The prepared m-CM with a surface area of 1 cm2 (1 cm × 1 cm) and a thickness of 0.8 mm directly served as the working electrode. The corresponding gravimetric capacitance and volumetric capacitance were calculated from the following equations: | 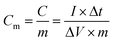 | (1) |
| 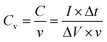 | (2) |
where Cm (F g−1) is the gravimetric capacitance, Cv (F cm−3) is the volumetric capacitance, I (A) is discharge current, Δt (s) is the discharging time, ΔV (V) represents the potential drop during discharge process, m (g) is the mass and v (cm3) is the volume of the carbon electrode.
Results and discussion
Characterization of materials
In the present work, FTIR is employed to analyze the surface groups of the as-obtained carbon materials after surface modification. The FTIR spectra of the obtained carbons before and after surface oxidation are shown in Fig. 2. A broad band at around 3343 cm−1 is observed in both samples. It is mainly caused by the O–H stretching vibration of the adsorbed water molecules and the –OH radical on the surface of m-CM6-8-120 after surface modification, which also has a weak bending vibration mode corresponding to the band recorded at 1618 cm−1. In addition, new bands are discovered from m-CM6-8-120 samples due to the introduced oxygen-containing groups after surface modification and oxidation. The weak band at 1732 cm−1 denote the absorption of the C
O stretching vibration of a –COOH radical. The band that appeared at 1384 cm−1 is assigned to the bending vibration of the –NO2group. The results indicate that oxygen and nitrogen functional groups, such as –OH, –COOH, and –NO2groups, are successfully introduced onto the surface of the carbon materials after surface modification. These surface functional groups play important roles in improving the hydrophilicity of the carbon surface, and are essential for increasing the specific capacitance of m-CM. The reaction equations of the surface modification in a HNO3 solution can be proposed as follows:31
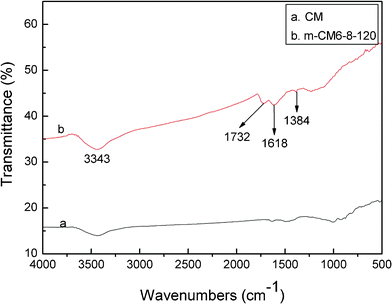 |
| Fig. 2
FT-IR patterns of CM and m-CM6-8-120. | |
All bands of the
FTIR data are relatively weak, which means that the contents of the functional groups on the surface of
m-CM6-8-120 are relatively lower. Although higher contents of surface groups can be obtained from high-acid concentrations and high temperature with a long reaction time, harsh reaction conditions will lead to structure transformation and finally impair their capacitance performance. This is not the desired result. In fact, surface modification of the
carbon electrode materials is to improve surface hydrophilicity on the premise of structure preservation. Lower oxidation temperatures and acid concentrations are favorable in term of maintaining the
m-CM structure.
To further investigate the surface morphology and monitor changes on the surface of the as-prepared m-CM before and after surface modification, SEM measurement was employed. Fig. 3a and b show the SEM images of CM and m-CM6-8-120, respectively. Both of the samples have a loose packed wire-like structure from carbonization of the fibers. The loosely packed structure can store sufficient electrolyte solution and is important for the supercapacitor providing a high power density at a high discharge current. Interestingly, impurities are observed from the SEM images before HNO3 oxidation, but disappear after oxidation. This means that the impurities were dissolved by the HNO3 solution during the oxidation process. After removal of these inorganic impurities, which have a poor electrical conductivity, the electrical conductivity and the purity of m-CM is improved, which are favorable for m-CM to exhibit high-performance supercapacitive behavior.
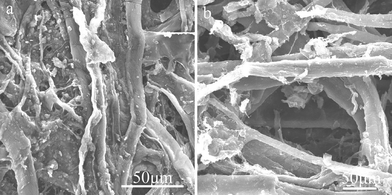 |
| Fig. 3
SEM images of (a) CM, (b) m-CM6-8-120. | |
The specific surface area and pore-size distribution analyses of the CM and m-CM6-8-120 was conducted using N2 adsorption–desorption experiments. Fig. 4a and b show the N2 adsorption–desorption isotherms and the corresponding BJH pore-size distributions, respectively. As seen from Fig. 4a, the existence of the hysteresis loops in both isotherms indicated the adsorption–desorption characteristic of the porous materials. It also can be seen from Fig. 4b that both of the samples exhibited a narrow pore size distribution of around 4 nm, indicating their mesoporous structure. In fact, a pore size between 4 and 10 nm is more adapted for EDLCs with a high power density.32Table 1 summarizes the textural properties of the samples. It is obvious that CM exhibited a higher specific surface area and larger pore volume, as well as a larger average pore size, than m-CM6-8-120. The reason for this is that acid oxidation could cause a partial structural collapse and dissolution of the inorganic impurities due to the harsh oxidation conditions which are adverse for reducing the surface area and dissolving the non-carbons. The pore size decrease after surface modification might be explained by the fixation of the surface oxygen on the walls which, on average, lead to a decrease in pore diameter.33
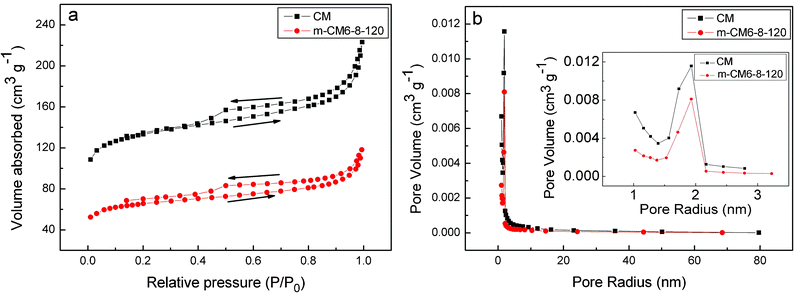 |
| Fig. 4 (a) N2 adsorption–desorption isotherms, (b) pore size distribution curves of CM and m-CM6-8-120. | |
Table 1 Specific surface area, pore volume, and pore size of CM and m-CM6-8-120
Samples |
BET specific surface area (m2 g−1) |
BJH pore volume (cm3 g−1) |
BJH pore size (nm) |
CM
|
463.4 |
0.193 |
3.20 |
m-CM6-8-120
|
223.9 |
0.104 |
3.12 |
Electrochemical test
CV, EIS, and chronopotentiometry are employed to evaluate the electrochemical performance of the as-prepared m-CM. Fig. 5a shows the CV curves of m-CM6-8-120 at different scan rates in a 2 M KOH aqueous electrolyte. It can be seen that the m-CM6-8-120 electrode exhibited an ideal double-layer behavior with quasi-rectangular CV curves. Obviously, the shape of the CV curves is not significantly influenced with the increasing of the sweep rates, suggesting a highly reversible system. The tiny distortion in the CV curves at high scan rate is due to the limited diffusion and migration of electrolyte ions in the bulk of the materials.
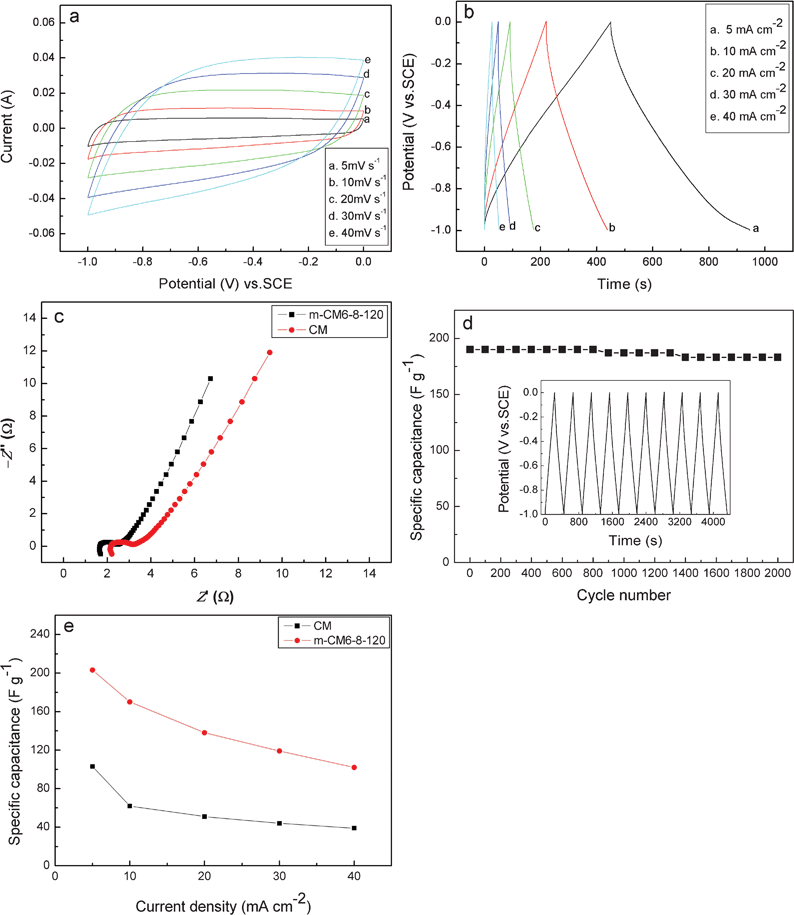 |
| Fig. 5 Electrochemical properties of the m-CM6-8-120 electrode in 2 M KOH solution. (a) CV curves of m-CM6-8-120. (b) Charge–discharge curves of m-CM6-8-120. (c) Complex-plane impedance plots of the CM and m-CM6-8-120 electrodes. (d) Cycling performance of m-CM6-8-120. (e) Specific capacitance of CM and m-CM6-8-120 at different current densities. | |
Fig. 5b shows the charge–discharge curves of m-CM6-8-120 electrode within a potential window of −1 to 0 V at various current densities. It is clearly seen that the shape of the charge–discharge curves are closely linear and show a typical triangle symmetrical distribution, indicating a good double layer capacitive property. The value of the specific capacitance of the as-prepared m-CM electrode were calculated to be 203, 170, 138, 119, and 98 F g−1, corresponding to the current densities of 5, 10, 20, 30, and 40 mA cm−2, respectively. The decrement of the specific capacitance at higher current densities is due to the increment of the voltage (IR) drop and insufficient mass transportation at high current density.
EIS measurements were performed on CM and m-CM6-8-120 electrodes, and the complex plane plots of the AC impedance spectra are shown Fig. 5c. It is seen that both impedance spectra are almost similar, composed of one semicircle component at high-frequency followed by a linear component at the low-frequency. However, it should be mentioned that there are obvious differences existing between the two spectra. One is the internal resistance (Rb), which includes the total resistance of the ionic resistance of the electrolyte and the intrinsic resistance of the carbon electrode. The Rb of CM and m-CM6-8-120 electrodes is 2.1 and 1.6 Ω, respectively. The lower Rb of the m-CM6-8-120 electrode than that of the CM electrode is due to the dissolution of the inorganic impurities during the surface modification process, which improves the electrical conductivity of the m-CM6-8-120. Another difference is that the charge transfer resistance (Rct) which is evaluated by the diameter of the semicircle,34 associated with the surface properties of the porous electrode. The Rct of the m-CM6-8-120 electrode is smaller than that of the CM electrode which indicates an excellent ionic conductivity at the electrode–electrolyte interface due to the improved surface hydrophilicity. At the lower frequencies, a straight sloping line represents diffusive resistance (Warburg impedance) of the electrolyte in pores of the host carbon. Both of the spectra showed higher angles than 45°, indicating the suitability of the CM-based materials as the electrodes for EDLCs due to their effective mesopores which facilitate the transport of electrolyte ions.35,36
The cycle stability of m-CM6-8-120 is demonstrated in Fig. 5d. It can be seen that the specific capacitance gradually decreased with the increase of the cycle number and a 96.5% of the initial specific capacitance remained after 2000 cycles. The results revealed the excellent stability of the waste paper based carbon electrodes for high-performance EDLCs. All the electrochemical tests demonstrate that the as-fabricated waste paper based carbon materials have a superior supercapacitive performance and are promising for use in EDLCs.
For further evaluation of the contribution of the surface modification on the supercapacitive performance of the as-obtained carbon electrode, the electrochemical behavior of CM without surface modification was also studied. The specific capacitance of CM and m-CM6-8-120 at different current densities are showed in Fig. 5e. It is obvious that the specific capacitance was greatly increased after surface modification. The results indicate that the surface modification is essential for carbon materials to improve their specific capacitance. We believe that the improved surface hydrophilicity and electrical conductivity of the m-CM6-8-120 electrode are in favor of the absorption and transportation of electrolyte ions through porous channels within the bulk of the carbon materials. Therefore, the higher specific capacitance of the m-CM6-8-120 electrode is mainly attributed to by the improved surface hydrophilicity and electrical conductivity. Additionally, the introduced chemical groups can also provide pseudo-capacitance to some extent as shown by the following redox reactions:37
However, because of their low contents of functional groups which can be concluded from the FTIR data for their weak bands, no visible redox peaks are observed on the CV curves.
Effects of surface modification conditions on specific capacitance of m-CM
As stated above, surface modification of carbon materials is a chemical reaction to introduce functional groups on the surface, but to preserve the intrinsic structure of the carbon. Harsh reaction conditions will lead to structure transformation and finally impair their capacitance performance.31 Therefore, to further understand the effects of the modification time, oxidation temperature, and the concentration of HNO3 solution on the specific capacitance of m-CM, a orthogonal experiment was performed and the results are shown in Fig. 6. It is clearly seen that the specific capacitance of m-CM corresponding to different current densities is strongly dependent on the oxidation conditions. At 100 °C, relatively mild reaction conditions would not cause surface and structure destruction. Thus the specific capacitance gradually increased with the increase of modification time and HNO3 concentration since more functional groups are introduced on the surface of m-CM, indicating that a higher modification temperature than 100 °C may be needed to achieve optimum surface modification of m-CM. Thus the surface modification is carried out at a relatively higher temperature of 120 °C. Results show that the specific capacitance of m-CM at a lower discharge current, like 5 mA cm−2, is increased with the increase of modification time and HNO3 concentration. But the specific capacitance at high current density becomes decreasing with an increase of modification time and HNO3 concentration as destruction of the structure m-CM appears. Note that m-CM6-8-120 has a high specific capacitance of 203 F g−1 and exhibits an excellent rate capability. But when the conditions become 8 M HNO3 with a 6 h modification time, though the specific capacitance at the current density of 5 mA cm−2 is still high, the decrement of the specific capacitance at high current density becomes more obvious, indicating that harsh conditions begin to introduce surface and structure destruction of the m-CM. The results also suggest that the effect of HNO3 concentration on the specific capacitance of the m-CM is more obvious than that of the modification time. When the temperature is further increased to 140 °C, the specific capacitance and rate capability is strongly impaired with increases of modification time and HNO3 concentration. The main reason is that too harsh oxidation conditions are adverse for carbon materials, reducing the surface area and conductivity of the carbons.31 For instance, the specific capacitance of the m-CM2-6-140 and m-CM8-8-140 electrodes at a current density of 40 mA cm−2 was close to zero, especially for m-CM2-6-140; the specific capacitance decreases more quickly at higher current densities. The results suggest that the surface and structure of the m-CM were completely destroyed and could not serve as electrode materials any more. The results indicate that for the surface modification to introduce functional groups on the carbon surface, relatively mild conditions are more favorable in terms of maintaining the microstructure and electrochemical performance of the carbons. The surface modification conditions including modification temperature, oxidation time, and the concentration of the HNO3 solution combine to determine the extent of the surface modification. An optimum modification should take all of these conditions into consideration. Obviously, the temperature of 120 °C, modification time of 8 h, and 6 M HNO3 concentration is the premium modification conditions for this experiment.
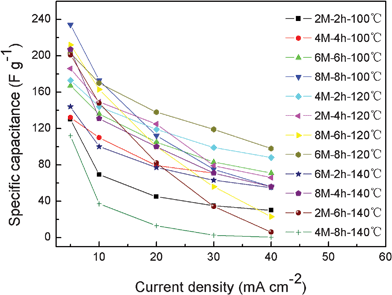 |
| Fig. 6 Specific capacitance of m-CM modified at different conditions. | |
In order to illustrate the application potentials of m-CM, Cm and Cv of AC and CMK-3 are measured as comparative samples, the results are shown in Table 2. It is obvious that m-CM6-8-120 has a higher Cm and Cv than standard samples, suggesting excellent supercapacitive properties. Since monolithic carbon has a much higher bulk density than powder carbons and need no substrates when preparing them to electrodes, the volumetric capacitance of these m-CM like carbon materials is much higher than AC and CMK-3, which is significant for the practical application. Therefore, the as-obtained m-CM could be a promising electrode material for EDLCs.
Table 2 Gravimetric capacitance and volumetric capacitance of m-CM8-8-100, AC, and CMK-3
|
m-CM8-8-100
|
CMK-3
|
AC |
C
m/F g−1 |
232 |
218 |
186 |
C
v/F cm−3 |
36.7 |
26.7 |
24.8 |
Conclusions
In summary, a waste paper based m-CM was successfully synthesized by a facile carbonization method, followed by a simple surface modification process. The as-prepared m-CM acted as a high-performance electrode material of EDLC. As a result of the improved electrical conductivity and surface hydrophilicity of the carbon electrode after surface modification, a much higher specific capacitance of 232 F g−1and 36.7 F cm−3 is reached. The effects of the modification conditions on the supercapacitive performance were systematically investigated. Among them, m-CM6-8-120 shows the highest specific capacitance and exhibits an excellent rate capability. Therefore, based on the above investigation, such a facile method to make activated carbons from organic waste could be a promising method to dispose of organic waste and prepare activated carbon materials. In a word, this kind of m-CM could be a promising candidate for EDLCs.
Acknowledgements
This work was supported by the National Natural Science Foundation of China (No. 21163010).
References
- C. M. B. Holt, S. Murphy, M. R. Gray and D. Mitlin, Catal. Commun., 2010, 12, 314 CrossRef CAS.
- J. Chmiola, G. Yushin, Y. Gogotsi, C. Portet, P. Simon and L. P. Taberna, Science, 2006, 313, 1760 CrossRef CAS.
- P. Simon and Y. Gogotsi, Nat. Mater., 2008, 7, 845 CrossRef CAS.
- J. R. Miller and P. Simon, Science, 2008, 321, 651 CrossRef CAS.
- T. Thomberg, A. Janes and E. Lust, Electrochim. Acta, 2010, 55, 3138 CrossRef CAS.
-
B. E. Conway, Electrochemical Supercapacitors: Scientific Fundamentals and Technological Applications, Kluwer Academic/Plenum Publishers, New York, 1999 Search PubMed.
- C. O. Ania, V. Khomenko, E. Raymundo-Pinero, J. B. Parra and F. Beguin, Adv. Funct. Mater., 2007, 17, 1828 CrossRef CAS.
- H. Shi, Electrochim. Acta, 1996, 41, 1633 CrossRef CAS.
- D. Y. Qu and H. Shi, J. Power Sources, 1998, 74, 99 CrossRef CAS.
- H. Probstle, M. Wiener and J. Fricke, J. Porous Mater., 2003, 10, 213 CrossRef.
- F. Pico, J. M. Rojo, M. L. Sanjuan, A. Anson, A. M. Benito, M. A. Callejas, W. K. Maser and M. T. Martinez, J. Electrochem. Soc., 2004, 151, A831 CrossRef CAS.
- A. Garcia-Gomez, P. Miles, T. A. Centeno and J. M. Rojo, Electrochim. Acta, 2010, 55, 8539 CrossRef CAS.
- V. Ruiz, C. Blanco, R. Santamaria, J. M. Ramos-Fernandez, M. Martinez-Escandell, A. Sepulveda-Escribano and F. Rodriguez-Reinoso, Carbon, 2009, 47, 195 CrossRef CAS.
- E. Raymundo-Pinero, F. Leroux and F. Beguin, Adv. Mater., 2006, 18, 1877 CrossRef CAS.
- K. Laszlo, G. Onyestyak, C. Rochas and E. Geissler, Carbon, 2005, 43, 2397 CrossRef.
- C. O. Ania, J. Pernak, F. Stefaniak, E. Raymundo-Pinero and F. Beguin, Carbon, 2009, 47, 3158 CrossRef CAS.
- C. O. Ania, J. Pernak, F. Stefaniak, E. Raymundo-Pinero and F. Beguin, Carbon, 2006, 44, 3113 CrossRef.
- J. Chmiola, G. Yushin, R. Dash and Y. Gogotsi, J. Power Sources, 2006, 158, 765 CrossRef CAS.
- C. Largeot, C. Portet, J. Chmiola, P. L. Taberna, Y. Gogotsi and P. Simon, J. Am. Chem. Soc., 2008, 130, 2730 CrossRef CAS.
- T. Tomko, R. Rajagopalan, P. Aksoy and H. C. Foley, Electrochim. Acta, 2011, 56, 5369 CrossRef CAS.
- D. W. Wang, F. Li, Z. G. Chen, G. Q. Lu and H. M. Cheng, Chem. Mater., 2008, 20, 7195 CrossRef CAS.
- S. Shiraishi, M. Kibe, T. Yokoyama, H. Kurihara, N. Patel, A. Oya, Y. Kaburagi and Y. Hishiyama, Appl. Phys. A: Mater. Sci. Process., 2006, 82, 585 CrossRef CAS.
- W. Kim, M. Y. Kang, J. B. Joo, N. D. Kim, I. K. Song, P. Kim, J. R. Yoon and J. Yi, J. Power Sources, 2010, 195, 2125 CrossRef CAS.
- W. Kim, J. B. Joo, N. Kim, S. Oh, P. Kim and J. Yi, Carbon, 2009, 47, 1407 CrossRef CAS.
- K. Jiang, A. Eitan, L. S. Schadler, P. M. Ajayan, R. W. Siegel, N. Grobert and M. Mayne, Nano Lett., 2003, 3, 275 CrossRef CAS.
- D. Hulicova, J. Yamashita, Y. Soneda, H. Hatori and M. Kodama, Chem. Mater., 2005, 17, 1241 CrossRef CAS.
- A. Lu, A. Kiefer, W. Schmidt and F. Schuth, Chem. Mater., 2005, 16, 100 CrossRef.
- Y. Xia and R. Mokaya, Chem. Mater., 2004, 16, 1553 CrossRef CAS.
- W. T. Huang, H. Zhang, Y. Q. Huang, W. K. Wang and S. C. Wei, Carbon, 2011, 49, 838 CrossRef CAS.
- J. S. Lee and R. Ryoo, J. Am. Chem. Soc., 2002, 124, 1156 CrossRef CAS.
- H. F. Li, H. A. Xi, S. M. Zhu, Z. Y. Wen and R. D. Wang, Microporous Mesoporous Mater., 2006, 96, 357 CrossRef CAS.
- Y. S. Yang, Battery, 2006, 36, 3 Search PubMed.
- P. A. Bazula, A. H. Lu, J. J. Nitz and F. Schuth, Microporous Mesoporous Mater., 2008, 108, 266 CrossRef CAS.
- Y. K. Zhou, B. L. He, W. J. Zhou and H. L. Li, J. Electrochem. Soc., 2004, 151, A1052 CrossRef CAS.
- M. W. Xu, D. D. Zhao, S. J. Bao and H. L. Li, J. Solid State Electrochem., 2007, 11, 1101 CrossRef CAS.
- J. W. Lang, X. B. Yan and Q. J. Xue, J. Power Sources, 2011, 196, 7841 CrossRef CAS.
- E. Frackowiak and F. Beguin, Carbon, 2001, 39, 937 CrossRef CAS.
|
This journal is © The Royal Society of Chemistry 2012 |
Click here to see how this site uses Cookies. View our privacy policy here.