DOI:
10.1039/C2RA01207C
(Paper)
RSC Adv., 2012,
2, 4189-4197
Rapid desulfurization of CWS via ultrasonic enhanced metal boron hydrides reduction under ambient conditions
Received
30th November 2011
, Accepted 23rd February 2012
First published on 22nd March 2012
Abstract
The present work investigated a rapid desulfurization method for industrial coal water slurry (CWS) using ultrasound-assisted metal boron hydrides (NaBH4, KBH4) reduction. Under ambient pressure and temperature conditions of ultrasonic time (10 min), ultrasonic frequency (20 KHz), deoxidizer concentration (10 mM), CWS concentration (60 g L−1) and coal particle size (≤ 120 mesh), the desulfurization efficiency of CWS can reach about 42% (NaBH4) and 45% (KBH4), respectively. On addition of Ni2+ catalyst (1 mM), the desulfurization efficiency, up to a maximum value of 57%, was significantly improved. Meanwhile, the nitrogen reduction (N) of CWS was reduced by 11.5%. The decrease of S and N greatly cut down SOx and NOx emissions from CWS combustion. After the processing, the ash content and volatile matter were decreased contributing to the slight improvement of combustion characteristics.
1. Introduction
Sulfur oxide (SOx) and nitrogen oxide (NOx) emissions from coal-fired power plants and refinery operations have been implicated as a cause of acid rain and other air pollution related problems.1 Significantly, the acid rain caused by coal combustion brings about irreparable economic losses. Clean coal technology is being applied and popularized at an unprecedented rate in China.2 Coal water slurry (CWS) is a clean liquid fuel, made of low sulfur and low ash coals. But with more restricted environmental legislation and more complex coals being used to make the slurry, the release of sulfur is larger, sometimes beyond the requirements of environmental protection. Furthermore, deep desulfurization prior to combustion can save amounts of flue gas desulfurization (FGD). Therefore, desulfurization of CWS plays an important and practical role in air pollution control in modern times.3
There are several methods of controlling SOx emissions from coal combustion. Some of them apply prior to combustion, some during and some after combustion.4 Desulfurization prior to combustion is more convenient, economical and environmentally friendly than FGD. So many researchers have drawn attention to seek efficient, economical and clean methods of coal desulfurization. The desulfurization processes of coal prior to combustion can be subdivided into physical and chemical methods, etc. Of these, chemical methods can remove almost all of the pyritic sulfur and at least a portion of the organic sulfur.5 A number of chemical methods5–33 and ultrasonic methods of desulfurization34–36 have been researched. Table 1 lists the chemical reagents whose use has been reported in literature and their effects on coal desulfurization. Compared with oxidative desulfurization (OD), reductive desulfurization (RD) has more incomparable advantages such as mild conditions and short processing times:3,37 however, it can not avoid incomplete reactions and lower desulfurization efficiency. Meanwhile, it is difficult to find excellent deoxidizers for RD, except for H2.
Table 1 Various reagents used to remove sulfur from coal
Author |
Reagent |
Time |
Sulfur removal |
Mukherjee5 |
H2O2 + H2SO4 |
4 h |
Using 15% (vol.) H2O2 and 0.1N H2SO4: 45% of total sulfur removed (complete removal of inorganic sulfur and 31% removal of organic sulfur) |
Ozdemmir6 |
Chlorine in CCl4 + H2O |
6 h |
Using 0.033 l min−1 chlorine flow rate at ambient temperature and pressure: All pyritic and sulphate sulfur removed and 30% organic sulfur removed |
Ahnonkitpanit and Prasassarakich7 |
Aqueous H2O2 + H2SO4 |
2 h |
Using 15% H2O2 and 0.1N H2SO4 at 40 °C: 48.7% total sulfur removed (97% pyritic, 89% sulphate and 7.1% organic sulfur removed) |
Krzymien8 |
Aqueous CuCl2 |
48 h |
Using 10 ml of 10% (vol.) CuCl2 at 200 °C, 100% sulfur removed |
Sonmez and Giray9 |
Peroxy acetic acid |
72 h |
45% sulfur removed from Gediz lignite; 85% sulfur removed from Cayirhan lignite |
Chandra10 |
Atmospheric oxidation |
106 days |
44% sulfur removed (36% organic sulfur removal) |
Steinberg11 |
O3 + O2 |
1 h |
Using a flow rate of 200 ml min−1, 1% O3 at 25 °C, 20% sulfur removed. |
Chaung12 |
Combination of dissolved oxygen and alkalis:NaHCO3, Na2CO3 and Li2CO3 |
1 h |
0.2M alkali solution with 3.4 atm O2 partial pressure at 150 °C: Na2CO3:72% of sulfur removed; Li2CO3: 73.1% of sulfur removed; At 0.4M NaHCO3: 77% of sulfur removed. |
Liu13 |
Aeration + NaOH, HCl |
5 h |
Using 0.25M NaOH at 90 °C with aeration rate of 0.136 m3/h and 0.1N HCl solution: 73% organic sulfur removed; 83% sulfide sulfur removed; 84% pyritic sulfur removed. |
Zaidi14 |
NaOH |
3 h |
Using 0.2N NaOH at 70 °C, 36.2% sulfur removed |
Aarya15 |
NaOH |
8 h |
Using 100 g dm−3 NaOH at 80 °C, 30% sulfur removed |
Rodriguez16 |
HNO3 |
2 h |
Using 20% HNO3 at 90 °C, 90% inorganic and 15% organic sulfur removed |
Prasassarakich and Thaweesri17 |
Sodium benzoxide |
90 min |
Using 600 ml sodium benzoxide at 205 °C, 45.9% sulfur removed (83.7% sulphate, 68.6% pyritic, 33.3% organic sulfur removed) |
Yang18 |
NaOH |
60 min |
Using 10 wt% NaOH at 250 °C: 55% sulfur removed (95% pyritic and 33% organic sulfur removed) |
Kara and Ceylan19 |
Molten NaOH at different temperatures |
30 min |
Using 20 wt% NaOH at 450 °C: 83.5% sulfur removed |
Ratanakandilok20 |
Methanol/water and methanol/KOH |
90 min |
Using 2% methanol and 0.025 g KOH/g coal at 150 °C: 58% total sulfur removed (77% sulphate, 47% pyritic and 42% organic sulfur removed) |
Aacharya21 |
Thio-bacillas, ferro-oxidants |
30 days |
91.81% sulfur removed from lignite, 63.17% sulfur removed from polish bituminous coal, 9.41% sulfur removed from Assam coal |
Aacharya22 |
Aspergillus |
10 days |
78% sulfur removed with 2% pulp density |
Ali23 |
H2O2, NH4OH, K2Cr2O7 and CH3COOH |
30 min |
50–90% of sulfur removed, depending on concentration and solvent. |
Baruah24 |
Water |
120 h |
77.59% pyritic sulfur removed with aqueous leaching at 45 °C. |
Hamamci25 |
Fe(NO3)3·9H2O |
12 h |
Using 50 ml of 1M solvent at 70 °C, 72.2% total sulfur (96.6% pyritic sulfur) removal |
Li and Cho33 |
NaClO |
2 h |
Pittsburgh No.8 coal: More than 70% of pyritic sulfur removal was achieved at the optimum conditions of 0.4 M hypochlorite, 0.4 M NaOH, and 90 °C. |
Li37 |
NaBH4 |
1 min |
Using 1.6 mM of NaBH4 concentration, −109 μm of particle size, neutral pH of initial media, 1 min of treated time, 100 rpm of shaking rate, 30 °C of temperature: 23.8% and 59.0% reduction in the pyritic sulfur, 70.4% and 100% reduction in the sulfate sulfur, 11.0% and 15.0% reduction in the organic sulfur, and 31.3% and 40.8% reduction in the total sulfur for the YZ coal and the YS coal, respectively. |
Shen3 |
NaBH4 |
10 min |
43% sulfur reduction of coal water slurry (CWS, 50 g L−1). |
The use of ultrasound can significantly improve the reaction efficiency under phase transfer conditions.38–40 Most phase transfer agents (PTA) are surface-active species that lower surface tension and permit easy formation of microbubbles under ultrasound. Ultrasound helps improve the liquid–liquid interfacial area through emulsification, which is important for viscous films containing gas-filled bubbles and cavitation bubbles. Gas-filled bubbles within the films, oscillating because of ultrasound and mobilized by acoustic streaming, entrain some of the film. Simultaneously, cavitational bubbles spray solvent on the film that covers the pulsing gas bubble. The pulsing action of the gas bubble is therefore disrupted and the liquid is scattered on its surface, leading to highly dispersed emulsions.40 Very fine ultrasonic emulsions, which are much smaller in size and more stable than those obtained conventionally, greatly improve the interfacial area available for reaction, increase the effective local concentration of reactive species, and enhance the mass transfer in the interfacial region. Therefore it leads to a remarkable increase in reaction rate under phase transfer conditions.41 Furthermore, cavitation during sonication produces extreme local conditions and a microenvironment with high temperature and high pressure, which may also create active intermediates that permit the reaction to proceed instantaneously.42 The ultrasound assisted chemical reaction has been applied in liquid fuel desulfurization.34–36,42,43
In this work, we investigated an innovative RD method for CWS under phase transfer conditions and ultrasonication, termed as ultrasound assisted reductive desulfurization (UARD) using relatively mild conditions and avoiding the loss of calorific value. The desulfurization method of sodium borohydride (NaBH4) reduction shows incomparable advantages: mild conditions, short time, and high efficiency of the desulfurization process.3,37,44,45 Metal boron hydrides (MBHs) (KBH4, NaBH4) were chosen as deoxidizers for UARD. The parameters, ultrasonic frequency and time, deoxidizer concentration, CWS concentration and coal particle size, were investigated in the experiments. Then, desulfurization efficiency was further improved with NiCl2 catalysis. At last, the optimized conditions of UARD were obtained by experimental and theoretical analysis.
2. Experimental section
2.1. Materials
A CWS sample was collected from Dongli Fuel Co. Ltd. (Shanghai, China). After being dried at 110 °C in an oven, the solid residue of CWS was ground and passed through different sizes of sieves. The ultimate and proximate analyses of solid CWS samples are given in Table 2. Sodium borohydride (NaBH4·4H2O, > 96%), potassium borohydride (KBH4, > 95%), NiCl2·6H2O (> 98%) and hydrogen peroxide (H2O2, > 30%) were purchased from Sinopharm Chemical Reagent Co. Ltd. (Shanghai, China).
Table 2 Characterization of the coal samplesa
Parameters |
Original coal |
Treated coal (NaBH4 reduction) |
Treated coal (KBH4 reduction) |
Process conditions: 10 min ultrasonic time, 25 KHz ultrasonic frequency, 10 mM deoxidizer (NaBH4, KBH4), 60 g L−1 CWS, ≤ 120 mesh of coal particle size, 100 rpm stirring rate, and 1 mM NiCl2.
Atmospheric conditions, dry basis.
|
Ultimate analysis (wt%, db) |
C |
73.66 |
69.84 (−5%) |
70.40 (−4.4%) |
H |
9.48 |
10.52 |
9.98 |
N |
1.56 |
1.38 (−11.5%) |
1.50 |
S |
1.30 |
0.56 (−56.9%) |
0.62 (−52.3%) |
Odiff. |
14.00 |
17.70 |
17.50 |
Sulfur content of different forms (wt%, daf) |
PS |
0.48 |
0.22 (−54.2%) |
0.18 (−62.5%) |
SS |
0.30 |
0.14 (−53.3%) |
0.16 (−46.7%) |
OSdiff.![[thin space (1/6-em)]](https://www.rsc.org/images/entities/char_2009.gif) |
0.52 |
0.20 (−61.5%) |
0.28 (−46.2%) |
Combustion characteristic |
Calorific value (J g−1) |
32 190 |
32 580 (+ 1.2%) |
32 840 (+ 2.0%) |
Ignition T/°C |
348 |
343 |
342 |
Proximate analysis (wt%, db) |
Ash |
12.6 |
10.2 (−19%) |
8.8 (−30.2%) |
Volatile matterdiff. |
23.9 |
19.6 |
20.4 |
Moistureb |
3.2 |
3.8 |
3.0 |
Fixed carbon |
63.5 |
66.4 (+ 4.4%) |
67.8 (+ 6.8%) |
2.2. Installation and general procedure
A schematic of the UARD apparatus was shown in Fig. 1(a), mainly including four parts: ultrasonic generator, reactor, electronic blender and adsorption bottle (H2O2, aq.) of tail gas. General Procedure: firstly, the quantitative mixed solution of CWS powder and water (100 ml) was added into the reactor. Then, a chemical reagent (NaBH4 or KBH4) was added in as well. After that, the ultrasonic generator was started and the reaction began. The electric stirrer (100 rpm) was not stopped until the reaction was complete. Ultimately, the clean solid CWS collected by filtering, leaching and drying, was used for further analysis and measurement. The schematic of experimental procedure and evaluated parameters is shown in Fig. 1(b). Fig. 1(c) presents the possible mechanism of reductive desulfurization.
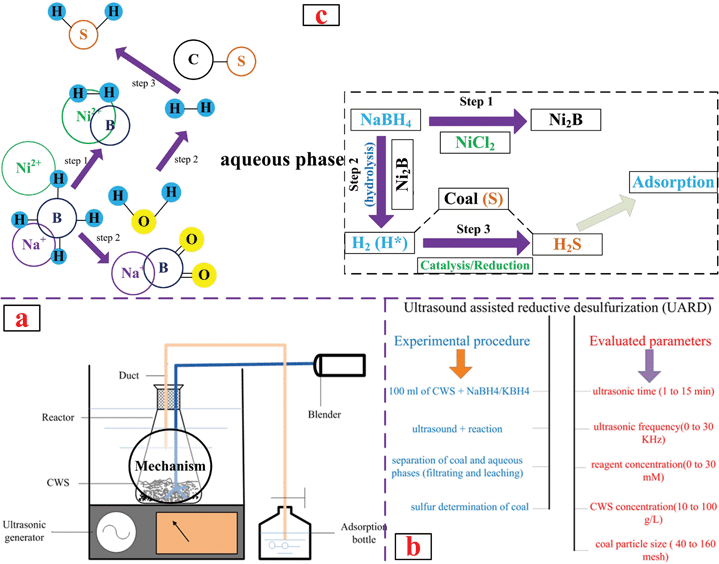 |
| Fig. 1 Schematic of apparatus, procedure and mechanism of UARD. | |
2.3. Analysis methods
The proximate analysis of the CWS sample followed the Chinese standard method (GB/T 212-2001). Total sulfur (TS) and total nitrogen (TN) were determined using an elemental analyzer (Elementar Vario EL III). The sulfate sulfur (SS) was determined gravimetrically using the Eschka method. Pyritic sulfur (PS) was determined by measuring the amount of iron contained in the pyritic state (GB/T 215-2003). Organic sulfur (OS) was estimated by the difference. Analyses of coal calorific value and ignition temperature accorded to the Chinese standard methods of GB/T 213-2003 and GB/T 18511-2001, respectively. Elements in the filtrate were detected by ICP (Iris Advantage 1000, Thermo king-cord Co., USA). Coal samples (dry basis) were analyzed by FTIR (EQUINOX 55, Bruker). The data (error ≤ 5%) are presented as the average of two replicates in each treatment.
3. Results and discussion
3.1. Univariate analysis
Ultrasonic time.
Ultrasonication is a very useful tool for increasing reaction rates in clearing, drilling and chemical processes and the production of emulsions.46–48 The cavitation process is well established as the origin of this sonochemical effect. The cavitation force is greatest at the center of the collapsing bubble where a high instantaneous pressure and temperature are created. The ambient conditions of reaction system are greatly influenced by the intensity of cavitation, which directly affects the reaction rate or yield. In the UARD process, ultrasonic emulsions were much smaller in size and more stable than those obtained conventionally, greatly improving the interfacial area available for reaction. The fine emulsions increased the effective local concentration of reactive species and enhanced mass transfer in the interfacial region, leading to a sizeable increase in the sulfur reduction reaction rate.49 Meanwhile, the main purpose of using ultrasonic methods is to alter the reaction pathways and to shorten the reaction time and enhance the desulfurization efficiency. As shown in Fig. 2(a), desulfurization efficiency increased with the increase of ultrasonic time. The reduction efficiency or rate via NaBH4 reduction was initially superior to KBH4 reduction, while desulfurization efficiency of NaBH4 reduction was less than KBH4 reduction after 8 min. The possible reason is that NaBH4 is unstable in the solution compared with KBH4 resulting in the incomplete desulfurization.
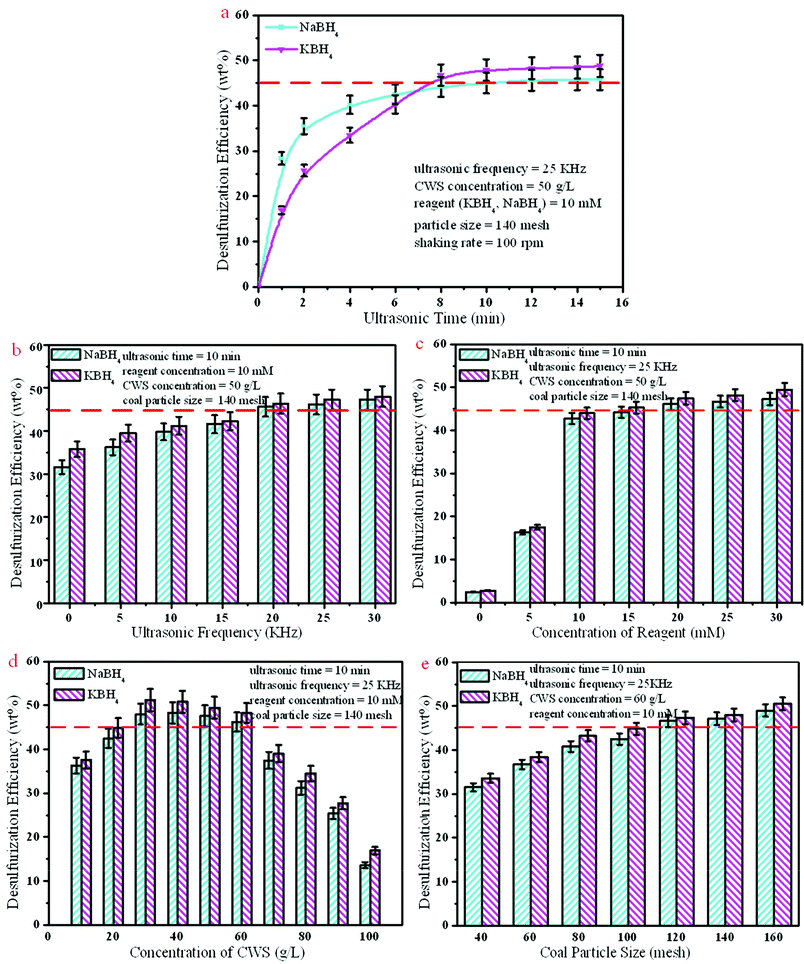 |
| Fig. 2 Effect of ultrasonic time (a), ultrasonic frequency (b), reagent concentration (c), CWS concentration (d) and coal particle size (e) on desulfurization efficiency. | |
Ultrasonic frequency (UF).
Coal structure becomes fluffy because of the swelling effect of the ultrasonication. Ultrasonic cavitation decreases coal particle size and bore diameter is increased. Thus, deoxidizers can easy get access into the macromolecular structures of coal, increasing the contact area of coal particles and deoxidizer. As Sonmez and Giray9 found, ultrasonic enhancement during the coal desulfurization process was closely related to the coal chemical structure characterization and operating parameters. As shown in Fig. 2(b), the desulfurization efficiency increased with the increase of UF. The growth tendency gradually decreased when UF exceeded 20 KHz. When UF ≤ 15 KHz, the desulfurization efficiency of NaBH4 reduction was slightly higher than for KBH4 reduction. It can be concluded that hydrolysis rate of KBH4 was slower than NaBH4 in normal conditions. When UF exceeded 20 KHz, the desulfurization efficiency of KBH4 reduction was higher than for NaBH4 reduction.
Deoxidizer concentration.
NaBH4 has a high hydrogen content, 10.8 wt%, while KBH4 contains 8.9 wt% of hydrogen, when the weight of water is taken into account.50 The deoxidizer concentration of MBHs (KBH4, NaBH4) directly determines the hydrogen generation and desulfurization efficiency. As shown in Fig. 2(c), the desulfurization efficiency increased with the increase of MBH concentration (only 3% reduction w/o MBHs). Using 10 mM MBHs, the desulfurization efficiency can increase up to 45%. However, the growth tendency decreased with MBH concentrations exceeding 10 mM.
CWS concentration.
Higher CWS concentration can decrease the contact frequency of deoxidizers and coal particles to some extent, resulting in the reduction of chemical reaction efficiency, accordingly with the decrease of desulfurization efficiency. As shown in Fig. 2(d), the desulfurization efficiency increased with the increase of CWS concentration from 10 to 30 g L−1, and then greatly decreased with the increase of CWS concentration from 30 to 100 g L−1. A suitable CWS concentration is 30∼60 g L−1.
Coal particle size.
The UARD is a typical two phase (solid and liquid) chemical reaction, according to the mechanism of the solid–liquid chemical reaction. For increasing the reaction rate, the most effective method is decreasing the coal particle size, with the aim of increasing the two phase mass transfer area. Fig. 2(e) shows that the desulfurization efficiency increased with the decrease of coal particle size, with ultrasound-assistance, big particle sizes of coal reached higher desulfurization efficiency as well. Consideration of energy conservation and economical efficiency, ≤ 120 meshes can be employed as the optimized coal particle size.
3.2. NiCl2 catalysis
It is well known that nickel chloride (NiCl2), as a catalyst, can enhance the reducibility of metal boron hydrides.51,52 Deoxygenation of sulfoxide was observed and competed strongly with desulfurization (Scheme 1).53 Under the optimized conditions, the desulfurization efficiencies up to 52% (KBH4) and 56% (NaBH4), respectively, were significantly improved by adding NiCl2 (1 mM). As shown in Fig. 3, the catalytic effect was more significant than the ultrasonic effect, so it was an effective of combination catalysis with ultrasound. Obviously, the reducibility of NaBH4 was fully exhibited, improving the desulfurization efficiency or rate due to Ni2+ catalysis. It is possible that S in coal contains lone pair electrons, and Ni2+ has an empty “d” orbital, so S was easy to react with Ni2+. In the reaction, the activated hydrogen (H*) adsorbed on the surface of nickel boride (Ni2B), forming a kind of Ni-MH intermediate product.54–57 Then H* attacked S bonded with α−C, resulting in C–S, C–N and C–C bond cleavage. Meanwhile, Ni2B produced by the reaction of NiCl2 and MBH has a higher Ni2B/Ni rate, so it is beneficial for the activated adsorption of in situ hydrogen and organic sulfides (OS), which possessing higher desulfurization activity to aromatic OS. Ni2B is a fine black solid that is easily prepared by the reduction of Ni2+ salts with NaBH4, usually in protic solvents as shown in the following equation (4 NaBH4 + 2 NiCl2 + 9 H2O → Ni2B + 3 H3BO3 + 4 NaCl + 12.5 H2 ↑).55
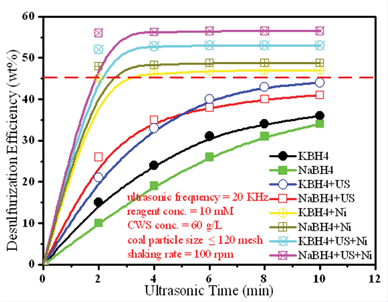 |
| Fig. 3 Desulfurization efficiency with/without ultrasound (US) and Ni catalysis. | |
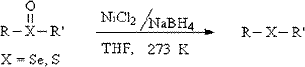 |
| Scheme 1 | |
3.3. Coal characterization
Calorific value and ignition temperature are two important combustion characteristics of coal, commonly improved by deashing or demineralization. As in the previous work, oxidative desulfurization usually tended to decrease the calorific value due to carbon loss,58 while the calorific value slightly increased by 1.2% (NaBH4) and 2.0% (KBH4), respectively. (Table 1) After treatment, coal properties were improved (i.e. increase of calorific value and fixed carbon, decrease of ash content and ignition temperature). It was suggested that the UARD process described here was a relative mild desulfurization method as well.
3.4. Mass balance
The removed S released from coal mainly remained in the filtrate or adsorbed in the adsorption liquid, TS = S1 (filtrate) + S2 (adsorption liquid). The experimental values of TS reduction were 57% (444.6 mg L−1, NaBH4) and 52% (405.6 mg L−1, KBH4) in Table 2, while the estimated values of TS reduction were 439.8 mg L−1 (NaBH4) and 399.0 mg L−1 (KBH4) in Table 3, respectively. Obviously, the experimental value of TS reduction was nearly identical with the estimated value, which suggests that most of the removed S was released from coal in volatile forms (i.e. H2S). After treatment, Ni and B in the filtrates reduced from 58.7 to 55.6 mg L−1 (by 5%), and 108 to 106.2 mg L−1 (by 1.7%), respectively. Thus, a large proportion of Ni and B could be recycled and reused.
Table 3 ICP analytical results of the filtratea
Process |
Reactor (mg L−1) |
Adsorption bottle S2 (mg L−1) |
Ni |
S1 |
B |
Fe |
Process conditions: 10 min ultrasonic time, 25 KHz ultrasonic frequency, 10 mM NaBH4/KBH4, 60 g L−1 CWS, ≤ 120 mesh coal particle size, 100 rpm stirring rate, and 1 mM NiCl2.
Theoretical value.
|
CWS (raw) |
0.02 |
0.20 |
0 |
0.03 |
0 |
CWS + NaBH4 |
55.6 (58.7b) |
125.8 |
106.2 (108b) |
29.16 |
314.0 |
CWS + KBH4 |
53.8 |
110.6 |
105.8 |
26.30 |
288.4 |
3.5. FT-IR analysis
The FT-IR spectrum of common OS are listed as follows: S–O bond (900–700 cm−1, strong), S–H bond (2600–2550 cm−1, very weak), S–C bond (700–590 cm−1, very weak and position variable), sulfoxide of S
O bond (1060–1040 cm−1, strong), sulfone of –SO2– bond (1340–1290 cm−1, asymmetric telescopic vibration) and (1160–1135 cm−1, symmetric telescopic vibration), respectively. Boron hydrides usually are used for organic compounds reductive reaction. The UARD showed effective and rapid OS reduction, 61.5% (NaBH4) and 46.2% (KBH4), respectively. (Table 1) Meanwhile, oxidative states of OS, such as sulfone (–SO2–) and sulfoxide (S
O), which widely exists in coal, can be easily be reduced by MBH reduction. Since reductive reaction was used for coal desulfurization, functional groups of OS should be investigated. Fig. 4 shows that the FT-IR spectrum of sulfone (–SO2–) and sulfoxide (S
O) evidently disappear after processing, whether with or without ultrasonic (US). And the C–S bond was difficult to break without ultrasound-assistance. It can be estimated that NaBH4 first reduced the oxygen functional groups of OS (S
O, –SO2–, etc.) into non-oxygen functional groups (C–S, etc.) by catalytic hydrogenation and hydrolysis. After that, the activated hydrogen (H*) produced by NaBH4 hydrolysis attacked the C–S bond, so S was converted into H2S released from coal (i.e. schematic of sulfoxide removal in Fig. 4). The reductive reaction is so rapid that it is hard to capture the intermediates for the further accurate mechanism analysis. It can infer a S removal mechanism from OS structure changes and NaBH4 reductive reaction. Nitrogen (N) in coals mainly exists in the form of organic N (amidogen, imidogen, nitrile, etc.).59 The N removal may be caused by boron hydride reduction as well. As Fig. 4 shows, the transmittance of amidogen (–NH–, 3402 cm−1) became weak after the UARD process. Without ultrasound the transmittance of amidogen became strong after treatment. It may be suggested that other nitrogen species (
NH,
N, etc.) were reduced into amidogen (–NH–), and its mechanism was similar to OS reduction. C–N was cleaved due to ultrasonic enhancement, and N was released from the coal particles. Compared with OS, the valence bonds of organic N are stable and hard to fracture conducing to lower removal efficiency.
3.6. XRD analysis
Minerals in coal can be qualitatively and quantitatively analysed by X-ray diffraction (XRD). According to the PDF card of standard diffraction data and previous research results,60–62 the content of coal samples mainly contain minerals of kaolinite, quartz, illite, pyrite and others, which are common minerals found in the coals of China.63 The diffraction characteristic peaks (DCPs) of the minerals became weak or disappeared after ultrasonic treatment (Fig. 5, C), while without ultrasound, there were various DCPs from the minerals (Fig. 5, B). It is suggested that ultrasonic enhancement makes the coal particles break into small pieces, so deoxidizers can easily access the macromolecular structures of coal, increasing the contact area of coal particles and deoxidizer. Herein it proves that ultrasonic enhancement can improve the reaction probability, increasing the desulfurization efficiency.
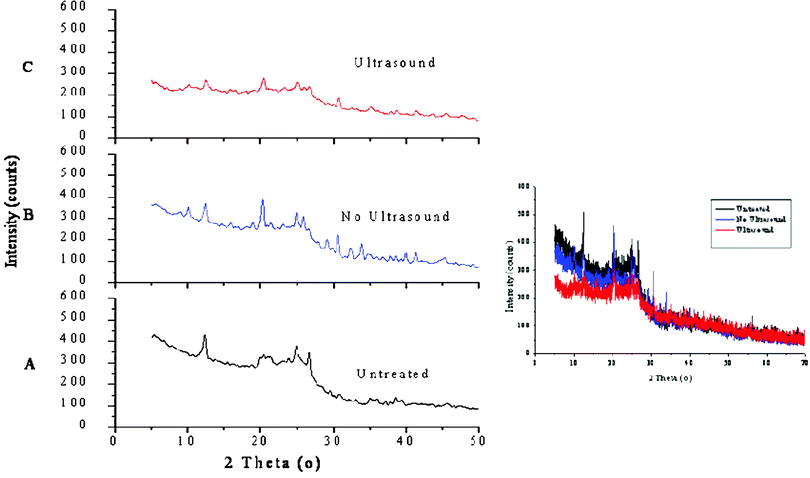 |
| Fig. 5 XRD spectrum of the solid CWS samples (original, treated with/without ultrasound). | |
4. Conclusions
In summary, the UARD process described here is effective for the desulfurization of CWS, and may be an alternative for other liquid fuel desulfurization as well. Under ambient pressure and temperature conditions of ultrasonic time (10 min), ultrasonic frequency (25 KHz), NaBH4 (10 mM), CWS (60 g L−1), coal particle size (≤ 120 mesh), stirring rate (100 rpm), and NiCl2 (1 mM), desulfurization efficiency of CWS was about 57%. Significantly, OS reduction could reach 60∼70%, and denitrification efficiency was up to 11.5%. After treatment, ash content and ignition temperature were decreased, and additionally, the increase of calorific value contributed to the slight improvement of coal properties.
Acknowledgements
We would like to acknowledge the financial supports from the Chinese High Technology Research & Development Program (Grant No. 2009AA062603). We are also thankful to Dr L. Zhang for the assisted measurement works in the Instrumental Analysis Center of Shanghai Jiaotong University (SJTU). And the thoughtful comments provided by anonymous editor and reviewers are greatly appreciated.
References
- C. Huang, C. A. Linkous, O. Adebiyi and A. T. Raissi, Hydrogen production via photolytic oxidation of aqueous sodium sulfite solutions., Environ. Sci. Technol., 2010, 44, 5283–5288 CrossRef CAS.
- W. Chen and R. Xu, Clean coal technology development in China., Energy Policy, 2010, 38(5), 2123–2130 CrossRef.
- Y. Shen, T. Sun and J. Jia, Novel desulfurization method of sodium borohydride reduction for coal water slurry., Energy Fuels, 2011, 25, 2963–2967 CrossRef CAS.
-
S. K. Kawatra and T. C. Eisel, Coal desulfurization: High-efficiency preparation methods. Taylor & Francis, New York 2001: 1–5 Search PubMed.
- S. Mukherjee and S. Mahiuddin, Borthakur PC. Demineralization and desulfurization of sub bituminous coal using hydrogen peroxide., Energy Fuels, 2001, 15, 1418–1424 CrossRef CAS.
- M. Ozdemmir, S. Bayrakceken, A. Gurses and S. Gulaboglu, Desulfurization of two Turkish lignites by chlorinolysis., Fuel Process. Technol., 1990, 26, 15–23 CrossRef.
- E. Ahnonkitpanit and P. Prasassarakich, Coal desulfurization in aqueous hydrogen peroxide., Fuel, 1989, 68, 819–824 CrossRef CAS.
- L. Krzymien, Complete removal of sulfur from coal using solutions containing cupric ions., Fuel, 1982, 61, 871–873 CrossRef.
- O. Sonmez and E. S. Giray, The influence of process parameters on desulfurization of two Turkish lignites by selective oxidation., Fuel Process. Technol., 2001, 70, 159–169 CrossRef CAS.
- D. Chandra, J. N. Chakrabarti and Y. V. Swamy, Auto-desulfurization of coal., Fuel, 1982, 61, 204–205 CrossRef CAS.
- M. Steinberg, R. T. Yang, T. K. Horn and A. L. Berlad, Desulfurization of coal with ozone: an attempt., Fuel, 1977, 56, 227–228 CrossRef CAS.
- K. C. Chaung, R. Markuszewesky and T. D. Wheelock, Desulfurization of coal by oxidation in alkaline solutions., Fuel Process. Technol., 1983, 7, 43–57 CrossRef.
- K. Liu, J. Yang, J. Jia and Y. Wang, Desulfurization of coal via low temperature atmospheric alkaline oxidation., Chemosphere, 2008, 71, 183–188 CrossRef CAS.
- S. A. H. Zaidi, Ultrasonically enhanced coal desulfurization., Fuel Process. Technol., 1993, 33, 95–100 CrossRef CAS.
- P. E. Araya, R. B. Ohlbaum and S. E. Droguett, Study of the treatment of sub bituminous coals by NaOH solutions., Fuel, 1981, 60, 1127–1130 CrossRef CAS.
- R. A. Rodriguez, C. C. Jul and D. G. Limon, The influence of process parameters on coal desulfurization by nitric leaching., Fuel, 1996, 75, 606–612 CrossRef CAS.
- P. Prasassarakich and T. Thaweesri, Kinetics of coal desulfurization with sodium benzoxide., Fuel, 1996, 75, 816–820 CrossRef.
- R. T. Yang, S. K. Das and B. M. C. Tsai, Coal demineralization using sodium hydroxide and acid solutions., Fuel, 1985, 65, 735–742 CrossRef.
- H. Kara and R. Ceylan, Removal of sulfur from four central Anatolian lignites by NaOH., Fuel, 1988, 67, 170–172 CrossRef CAS.
- S. Ratanakandilok, S. Ngamprasertsith and P. Prasassarakich, Coal desulfurization with methanol/water and methanol/KOH., Fuel, 2001, 80, 1937–1942 CrossRef CAS.
- C. Aacharya, R. N. Kar and L. B. Sukla, Bacterial removal of sulfur from three different coals., Fuel, 2001, 80, 2207–2216 CrossRef.
- C. Aacharya, L. B. Sukla and V. N. Misra, Biological elimination of sulfur from high sulfur coal by Aspergillus-like fungi., Fuel, 2005, 84, 1597–1600 Search PubMed.
- A. Ali, S. K. Srivatsava and R. Haque, Chemical desulfurization of high sulfur coals., Fuel, 1992, 71, 835–839 CrossRef CAS.
- B. P. Baruah, B. K. Saikia, P. Kotoky and P. G. Rao, Aqueous leaching on high sulfur sub-bituminous coals, in Assam, India., Energy Fuels, 2006, 20, 1550–1555 CrossRef CAS.
- C. Hamamci, F. Kahraman and M. Z. Diiz, Desulfurization of southeastern Anatolian asphaltites by the Meyers method., Fuel Process. Technol., 1997, 50, 171–177 CrossRef CAS.
- S. Mukherjee and P. C. Borthakur, Chemical demineralization/desulfurization of high sulfur coal using sodium hydroxide and acid solutions., Fuel, 2001, 80, 2037–2040 CrossRef CAS.
- H. G. Alam, A. G. Mogaddam and M. R. Omidkhah, The influence of process parameters on desulfurization of Mezino coal by HNO3/HCl leaching. Fuel Process., Technol., 2009, 90, 1–7 CAS.
- S. Mukherjee and P. C. Borthakur, Demineralization of sub bituminous high sulfur coal using mineral acids., Fuel Process. Technol., 2004, 85, 157–164 CrossRef CAS.
- S. Mukherjee and P. C. Borthakur, Effect of leaching high sulfur sub bituminous coal by potassium hydroxide and acid on removal of mineral matter and sulfur., Fuel, 2003, 82, 783–788 CrossRef CAS.
- W. Li and S. Guo, Supercritical desulfurization of high rank coal with alcohol/water and alcohol/KOH. Fuel Process., Technol., 1996, 46(2), 143–155 CAS.
- K. Charutawai, S. Ngamprasertsisith and P. Prasassarakich, Supercritical desulfurization of low rank coal with ethanol/KOH. Fuel Process., Technol., 2003, 84, 207–216 CAS.
- Y. Yuda and T. Ayse, Supercritical extraction and desulfurization of Beypazari lignite by ethyl alcohol/NaOH treatment. 1. Effect of ethyl alcohol/coal ratio and NaOH., Petroleum Science and Technology, 1990, 8, 87–105 Search PubMed.
- W. D. Li and E. H. Cho, Coal desulfurization with sodium hypochlorite., Energy Fuels, 2005, 19, 499–507 CrossRef CAS.
- P. A. Mello, F. A. Duarte, M. A. G. Nunes, M. S. Alencar, E. M. Moreira and M. Korn, Ultrasound-assisted oxidative process for sulfur removal from petroleum product feedstock., Ultrason. Sonochem., 2009, 16, 732–736 CrossRef CAS.
- Y. Wang and R. Yang, Desulfurization of liquid fuels by adsorption on carbon-based sorbents and ultrasound-assisted sorbent regeneration., Langmuir, 2007, 23, 3825–3831 CrossRef CAS.
- J. Grobas, C. Bolivar and C. E. Scott, Hydro-desulfurization of benzothiophene and hydrogenation of cyclohexene, biphenyl, and quinoline, assisted by ultrasound using formic acid as hydrogen precursor., Energy Fuels, 2007, 21, 19–22 CrossRef CAS.
- Z. Li, T. Sun and J. Jia, An extremely rapid, convenient and mild coal desulfurization new process: Sodium borohydride reduction. Fuel Process., Technol., 2010, 91, 1162–1167 CAS.
- L. H. Thompson and L. K. Doraiswamy, Sonochemistry: science and engineering., Ind. Eng. Chem. Res., 1999, 38, 1215–1249 CrossRef CAS.
-
J. L. Luche, Synthetic organic sonochemistry. New York: Plenum Press, 1998 Search PubMed.
-
Y. T. Shah, A. B. Pandit and V. S. Moholkar, Cavitation reaction engineering. New York: Kluwer/Plenum, 1999 Search PubMed.
-
T. F. Yen, R. D. Gilbert and J. H. Fendler, Membrane mimetic chemistry and its applications.New York: Plenum Press, 1994 Search PubMed.
- S. P. Tu and T. F. Yen, The feasibility studies for radical induced decomposition and demetalization of metalloporphyrins by ultrasonication., Energy Fuels, 2000, 14, 1168–1175 CrossRef CAS.
- H. Mei, B. W. Mei and T. F. Yen, A new method for obtaining ultra-low sulfur diesel fuel via ultrasound assisted oxidative desulfurization., Fuel, 2003, 82, 405–414 CrossRef CAS.
- X. Guo, S. Li, C. Yue and X. Ni, New reduction methods for removing benzothiophene organic sulfur., Journal of Applied Chemistry (Chinese), 2006, 23(9), 852–987 Search PubMed.
- Z. Wang, S. Wang, G. Liu and W. Wang, Electrochemical method preparing sodium borohydride for gasoline desulfurization, Journal of Oil Refining and Chemical Engineering, 2007, 38(11), 6–9 CAS.
- X. Liu, B. Wang, S. Liu and B. Cui, Application of ultrasound technologies in diesel fuels oxidative desulfurization., Applied Chemical Industry, 2011, 40(1), 146–149 CAS.
- M. W. Wan and T. F. Yen, Enhance efficiency of tetraoctylammonium fluoride applied to ultrasound-assisted oxidative desulfurization (UAOD) process., Appl. Catal., A, 2007, 319, 237–245 CrossRef CAS.
- V. Sivakumar, F. Chandrasekaran, G. Swaminathan and P. G. Rao, Towards cleaner degreasing method in industries: ultrasound-assisted aqueous degreasing process in leather making., J. Clean. Prod., 2009, 17, 101–104 CrossRef CAS.
- T. Chen, Y. Shen, W. Lee, C. Lin and M. Wan, The study of ultrasound-assisted oxidative desulfurization process applied to the utilization of pyrolysis oil from waste tires., J. Clean. Prod., 2010, 18, 1850–1858 CrossRef CAS.
- L. Damjanovi'c, S. Bennici and A. Auroux, A direct measurement of the heat evolved during the sodium and potassium borohydride catalytic hydrolysis., J. Power Sources, 2010, 195, 3284–3292 CrossRef CAS.
- J. G. Handique, A. Purkayashtha and J. B. Baruah, Reduction of α, β unsaturated carbonyl compounds by Ni2+–BH4−., J. Organomet. Chem., 2001, 620, 90–93 CrossRef CAS.
- M. V. N. Souza and T. R. A. Vasconcelos, Recent methodologies mediated by sodium borohydride in the reduction of different classes of compounds., Appl. Organomet. Chem., 2006, 17(8), 798–810 CrossRef.
- J. M. Khurana, A. Ray and S. Singh, Deoxygenation of sulfoxides and selenoxides with nickel boride., Tetrahedron Lett., 1998, 39, 3829–3832 CrossRef CAS.
- S. Schouten, D. Pavlović, J. S. Sinninghe Damsté and J. W. de Leeuw, Nickel boride: an improved desulphurizing agent for sulphur-rich geomacromolecules in polar and asphaltene fractions., Org. Geochem., 1993, 20, 901–909 CrossRef CAS.
- T. G. Back, J. K. Yang and H. R. Krouse, Desulfurization of benzo- and dibenzothiophenes with nickel boride., J. Org. Chem., 1992, 57, 1986–1990 CrossRef CAS.
- J. C. Walter, A. Zurawski, D. Montgomery, M. Thornburg and S. Revankar, Sodium borohydride hydrolysis kinetics comparison for nickel, cobalt, and ruthenium boride catalysts., J. Power Sources, 2008, 179, 335–339 CrossRef CAS.
- X. Guo, S. Li, C. Yue and X. Ni, Desulfurization of benzothiophene with new reduction method., Journal of Applied Chemistry (Chinese), 2006, 23, 982–987 CAS.
- B. P. Baruah and P. Khare, Desulfurization of oxidized Indian coals with solvent extraction and alkali treatment., Energy Fuels, 2007, 21, 2156–2164 CrossRef CAS.
- Z. Qiang, Study on occurrence mode of sulfur and nitrogen in coal in China., Clean Coal Technology (Chinese), 2008, 01, 73–75 Search PubMed.
- W. Wang, Y. Qin, D. Song and K. Wang, Column leaching of coal and its combustion residues, Shizuishan, China., Int. J. Coal Geol., 2008, 75(2), 81–87 CrossRef CAS.
- Y. Zhu, H. Zhu, X. Lv and K. Sun, Study of electrolytic reduction desulfurization of high sulfur coal by XRD., Journal of China University of Mining and Technology, 2001, 30(6), 630–633 CAS.
- D. Zhang, M. Zhang and Q. Chen, Research on SEM/TEM and XRD of germ oxidizing pyrite surface in coal., Journal of China University of Mining and Technology, 2005, 34(6), 761–765 CAS.
- X. Liu, Study of some minerals of coals in China., Journal of China University of Mining and Technology, 1994, 23(4), 109–114 Search PubMed.
|
This journal is © The Royal Society of Chemistry 2012 |
Click here to see how this site uses Cookies. View our privacy policy here.