DOI:
10.1039/C2RA20965A
(Paper)
RSC Adv., 2012,
2, 10316-10323
Evidence for in situ graft copolymer formation and compatibilization of PC and PMMA during reactive extrusion processing in the presence of the novel organometallic transesterification catalyst tin(II) 2-ethylhexanoate†
Received
17th May 2012
, Accepted 20th August 2012
First published on 23rd August 2012
Abstract
In this work, we have investigated the role of an organometallic catalyst, tin(II) 2-ethylhexanoate, for the first time for developing compatibilized PC/PMMA blends by a reactive extrusion process. This catalyst is found to be very efficient, as even 0.5% (w/w) of the catalyst is sufficient to develop blends with a single Tg in the second run DSC and a single degradation step in TGA thermograms up to 40% PMMA content. We have shown that the carbonyl peak of PMMA is present in the FTIR spectra of the acetone insoluble portion of the blends, after the extraction of acetone soluble (free/unreacted) PMMA, if there is any, suggesting the development of strong chemical bonding between the PC and PMMA chains during the reactive extrusion process. Furthermore, 1H NMR studies show that the methyl ester proton peak of PMMA is shifted from 3.547 to 3.624 ppm in the blends, revealing a change in the proton environment. We have proposed that the exchange reaction between the carbonate and ester groups of PC and PMMA leads to PC-g-PMMA graft copolymer formation, which is responsible for the observed chemical shift of the methyl ester proton. This graft copolymer, formed in situ during the reactive extrusion process, compatibilizes the PC and PMMA phases. A significant improvement in optical transparency over the otherwise opaque nature of the uncompatibilized blends confirms the compatibilization of PC and PMMA in the blends.
1. Introduction
Compatibilized polymer blends of immiscible components have received enormous interest in recent years because they offer potential for developing controlled morphologies of the dispersed phase, leading to the enhancement of properties of technological significance.1–5 The compatibilized blends are known for their long term stability, as the compatibilizers improve the interfacial adhesion between the immiscible components, thereby preventing the coalescence of the dispersed phase. Since the compatibilized blends are useful for practical applications,6–8 the search for new compatibilizers for developing industrial polymer blends continues to attract considerable attention.8–11 Among the various polymer blends, the mixture of bisphenol A polycarbonate (PC) with poly(methyl methacrylate) (PMMA) is one of the most technologically important polymer blend systems12–32 because of its potential for several applications, such as in compact discs, optical lenses, gas membranes and optical fibers.6,7 PMMA has excellent optical transparency and high surface hardness, and can be synthesized at low cost among the commercial plastics, but lacks adequate toughness because of its brittle/semi-brittle behaviour. PC, on the other hand, not only exhibits excellent optical transparency but also possesses exceptional toughness, dimensional stability, better ductility and a higher glass transition temperature, but its surface hardness is low and its production cost is rather high.7 In addition, it is reported to release the hazardous chemical bisphenol A33,34 as a result of hydrolysis, whereas PMMA is more environmentally benign. Optically transparent PC/PMMA blends offer tremendous possibilities as a cheaper and less hazardous alternative to the tough but expensive PC, with better surface hardness as compared to PC. However, the development of optically transparent homogeneous PC/PMMA blends remains challenging because of the thermodynamic immiscibility of the two phases, as revealed by the positive value of the Flory–Huggins (polymer–polymer interaction) parameter.16
Although the positive value of the Flory–Huggins parameter rules out thermodynamic miscibility of the two phases in the PC/PMMA blend system,16 theoretical molecular modeling studies reveal the presence of specific interactions between PC and PMMA due to the van der Waals forces between the phenyl rings of PC and the carbonyl group of PMMA.13 Recently, our group has found evidence for an interaction between the PC and PMMA phases in solution cast blends.29 Based on light scattering and FTIR studies on samples heated at 250 °C or above, it has been proposed that an exchange reaction takes place between the carbonate and ester groups of PC and PMMA, leading to the formation of PC-g-PMMA graft copolymer, which compatibilizes the PC and PMMA components.18 However, in a later work using NMR, mass spectroscopy and size exclusion chromatography, it was shown that no such exchange reaction occurs between PC and PMMA at 250 °C unless a transesterification catalyst is used.27,28 Thus, although there are some specific interactions between the PC and PMMA phases in PC/PMMA blends, they are not strong enough to make these blends miscible or compatibilized to prevent phase separation upon heat treatment.
To develop homogeneous PC/PMMA blends that do not undergo phase separation, different workers have therefore used compatibilizers using a reactive extrusion technique.23–28 Penco et al.25 and Lee et al.26 used tetrabutylammonium tetraphenylborate (TBATPB) and titanium(IV) butoxide (TiOBu4) as transesterification catalysts for the compatibilization of the PC/PMMA blends during melt extrusion. Based on FTIR studies, they proposed an ester–ester exchange reaction between PC and PMMA, leading to PC-g-PMMA graft copolymer formation in the presence of 1% (w/w) TBATPB and 0.5% (w/w) TiOBu4 transesterification catalysts. In contrast, Montaudo et al.27 showed that in the presence of another transesterification catalyst, SnOBu2, the exchange reaction can take place, but it does not lead to the formation of PC-g-PMMA graft copolymers suggested in ref. 18,25,26. Based on 1H NMR studies, these workers proposed evidence for an exchange reaction occurring between the methyl methacrylate (MMA) monomers, generated by the unzipping of PMMA chains, and the carbonate groups of PC.27 Thus, there is a controversy regarding the actual mechanism of compatibilization, especially the PC-g-PMMA graft copolymer formation, in the presence of organometallic transesterification catalysts in the melt extruded PC/PMMA blends. Recently, our group investigated the role of an inorganic transesterification catalyst, dihydrated stannous chloride (SnCl2·2H2O), for developing compatibilized PC/PMMA blends.28 We found unambiguous evidence for PC-g-PMMA graft copolymer formation in the presence of SnCl2·2H2O transesterification catalyst in the melt extruded PC/PMMA blends, on the basis of 1H NMR studies.28 The fact that the Sn based inorganic transesterification catalyst promotes PC-g-PMMA graft copolymer formation28 but the same Sn based organometallic compound SnOBu227 does not is quite intriguing and deserves further investigation.
The objective of the present investigation is to settle the existing controversies about PC-g-PMMA graft copolymer formation in the presence of organometallic transesterification catalysts. For this we have used tin(II) 2-ethylhexanoate as a catalyst, which has not been used earlier in the context of PC/PMMA blend formation. We show that the use of as low a quantity as 0.5% (w/w) of this catalyst is sufficient to develop compatibilized PC/PMMA blends containing up to 40% PMMA, as corroborated by DSC, TGA, optical transparency and FTIR studies. We present here the 1H NMR and FTIR results, which suggests PC-g-PMMA graft copolymer formation during reactive extrusion processing of the PC/PMMA blends in the presence of this catalyst. We believe that this graft copolymer acts a compatibilizer for the immiscible PC and PMMA phases. Our results may have a bearing on attempts to reduce the PC content in its applications as an engineering thermoplast, because of its high cost and potential for releasing the hazardous bisphenol A compound.33,34
2. Experimental
2.1 Materials
PMMA (IG 840, Mn 52
000, LG MMA), PC (Makrolon 2015, Mn 15
000, Bayer), SnCl2·2H2O (Thomas Baker) and tin(II) 2-ethylhexanoate (Aldrich), were used for preparing PC/PMMA blends. The density, melt flow indices of PC and PMMA and the structure of the tin(II) 2-ethylhexanoate catalyst are given in the ESI.†
2.2 Preparation of PC/PMMA blends
Initially, the PC and PMMA beads were converted into powder form (∼500 μm average size) using a grinder. The requisite amounts of the PC and PMMA powders and the transesterification catalyst (in the case of compatibilized blends) were thoroughly mixed in a beaker with spatula, followed by mixing in a high-speed mixer before putting into the extruder. In order to remove adsorbed moisture, if any, the mixed powder was dried in a vacuum oven for 24 h at 80 °C. The melt extrusion was carried out in a co-rotating twin screw extruder (Thermo Scientific Haake Minilab II) using a typical batch size of 50 gm. Mixing was done for 2 min at an optimized temperature of 230 °C under an optimized shear rate of 50 rpm for the blend formation.
2.3 Characterization methods
The glass transition temperature (Tg) of the PC/PMMA blends was measured using DSC (Mettler-Toledo, 823) at a heating rate of 20 °C min−1 under a nitrogen atmosphere. For measuring Tg, first we heat the pristine blend from 30 to 300 °C at a heating rate of 20 °C min−1, and then cool the sample at the maximum possible cooling rate of 45 °C min−1 available with the DSC. This constitutes the first DSC run. After this, we reheat the sample from 30 to 300 °C at a heating rate of 20 °C min−1 for recording the DSC data for the determination of Tg in the second run. The DSC was calibrated with indium and zinc before use.
Thermal degradation of blends was studied using TGA (Mettler-Toledo, TGA/DSC-1) at a heating rate of 20 °C min−1 under a nitrogen atmosphere. The degradation temperature of the blends was measured, corresponding to a 5% weight loss of the sample.
FT-IR spectroscopic analyses of the film samples were conducted in transmission mode in a Thermo Scientific FTIR spectrometer (model: NICOLET 6700) from 650 to 4000 cm−1 with a resolution of 2 cm−1.
1H NMR spectra were recorded on a Bruker 500 MHz spectrometer (Avance AV 500WB) at ambient temperature in a CDCl3 solvent. The chemical shifts are reported in parts per million relative to tetramethylsilane.
Optical transmittance spectra of PC/PMMA blends were measured by UV/Vis spectrophotometer (Lambda 25, Perkin Elmer, Germany) in the range 400–800 nm. The sample thickness was 2 mm.
3. Results
3.1 Optimization of tin(II) 2-ethylhexanoate content for getting a PC/10PMMA blend with a single Tg
Due to the weakness of the specific interactions between PC and PMMA and the positive value of the Flory–Huggins parameter, PC/PMMA blends prepared by solution casting17,21,22,29 as well as melt extrusion16,30 techniques undergo macro-phase separation at elevated temperatures. For any useful application of PC/PMMA blends, macro-phase separation needs to be prevented using a suitable compatibilization strategy. To study the efficacy of the organometallic transesterification catalyst tin(II) 2-ethylhexanoate for obtaining compatibilized PC/PMMA blends with a single Tg, we first concentrated on the PC/10PMMA blend composition, which was prepared using the tin(II) 2-ethylhexanoate catalyst in different concentrations. Fig. 1(a) shows the second run DSC thermograms of pure PC, pure PMMA and melt extruded PC/10PMMA blends with and without transesterification catalyst tin(II) 2-ethylhexanoate. The PC/10PMMA blend without the catalyst shows two distinct glass transition temperatures, which can be more clearly seen in the first derivative plot of the DSC thermogram shown in Fig. 1(b). The lower Tg is attributable to the PMMA-rich phase, while the higher Tg is for the PC-rich phase. The fact that the lower Tg corresponding to PMMA is slightly shifted towards the higher temperature side, whereas the Tg of PC is nearly unaffected, suggests the presence of specific interactions between the PC and PMMA phases at the PMMA rich end. Marin and Favis30 have also reported that PC is more soluble in PMMA than PMMA is in PC. The PC/10PMMA blend containing 0.3% (w/w) tin(II) 2-ethylhexanoate transesterification catalyst also shows two distinguishable glass transition temperatures, as can be seen from Fig. 1(a) and more clearly from Fig. 1(b). However, the two Tgs are shifted away from the respective Tgs for PC and PMMA, much more than in the uncompatibilized PC/10PMMA blend. This suggests better interaction in the presence of the 0.3% tin(II) 2-ethylhexanoate transesterification catalyst. As the catalyst content in PC/10PMMA is increased from 0.3 to 0.5%, a single Tg is observed, which is ∼15 °C lower than the Tg of pure PC, suggesting that 0.5% (w/w) tin(II) 2-ethylhexanoate is optimal for obtaining compatibilized PC/10PMMA blends.
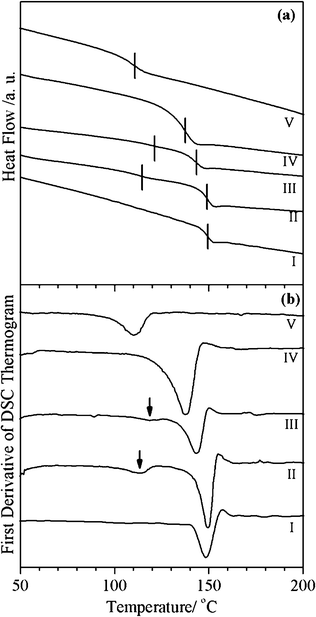 |
| Fig. 1 Second run DSC thermograms (a) and the first derivative (b) of PC, PMMA and PC/PMMA blends prepared using the melt extrusion technique: (I) pure PC, (II) PC/10PMMA, (III) PC/10PMMA + 0.3% tin(II) 2-ethylhexanoate, (IV) PC/10PMMA + 0.5% tin(II) 2-ethylhexanoate, and (V) pure PMMA. | |
3.2 Effect of PMMA content on the Tg of the compatibilized blends
Fig. 2(a) and (b) depict the second run DSC thermograms and their first derivatives, respectively, of extruded PC, PC/PMMA blends containing up to 50% PMMA and PMMA in the presence of tin(II) 2-ethylhexanoate. For comparison, we have also included the data on extruded PC and PMMA without the catalyst. The Tg values of the pure PC and PMMA phases are found to be 149 °C and 111 °C, respectively. However, the Tg of pure PC is slightly lowered in the presence of the catalyst, while the Tg of PMMA is nearly unaffected by the catalyst, as can be seen from Fig. 2(a) and (b). This is because Sn-based catalysts tend to degrade the PC a little,27,28,31 leading to lowering of the molecular weight and hence lowering of the Tg. PMMA, on the other hand, is not degraded and therefore its Tg is nearly unaffected. It is evident from Fig. 2 that the PC/PMMA blends show a single Tg up to 40% PMMA content. For blends containing PMMA content higher than 40%, two Tgs are observed when the 0.5% catalyst is used, which can be seen more clearly in the first derivative of the DSC thermogram shown in Fig. 2(b) for the PC/50PMMA blend composition. Increasing the catalyst content beyond 0.5% gives compatibilized blends with a single Tg, even for a PMMA content of 50% and more; but in this work we have concentrated on the minimum catalyst content required for getting compatibilized blends with a single Tg, since the catalyst also has the tendency to degrade PC when used in larger quantities,31 as discussed in a later section.
What is most significant is that in the compatibilized PC/PMMA blends, the Tg gradually decreases with respect to the Tg of PC with increasing PMMA content. The glass transition of a miscible blend is usually described in terms of the Fox law32 or the additive law. The variation of Tg as a function of the PMMA content in the compatibilized blends is compared with the values expected on the basis of the Fox and additive laws in Fig. 3. The Tg of the compatibilized blends shows significant negative deviation with respect to the Tg predicted by the additive or Fox laws. This suggests a strong interaction developing between the PC and PMMA phases during extrusion in the presence of the catalyst. A similar deviation in the measured Tg from the additive and Fox laws was observed for the compatibilized PC/PMMA blends prepared in the presence of TBATPB,25 organoclays,24 diglycidyl ether of bisphenol A35 and SnCl2·2H2O28 as compatibilizers.
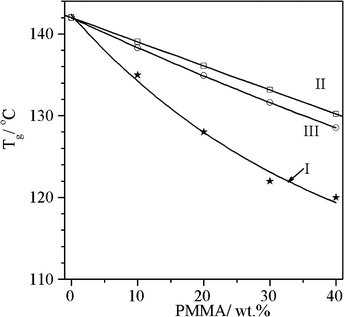 |
| Fig. 3 Variation of Tg as a function of PMMA content: (I) Tg of PC/PMMA + 0.5% tin(II) 2-ethylhexanoate catalyst (II) Tg of miscible PC/PMMA blends, as predicted by additive law, and (III) Tg of miscible PC/PMMA blends, as predicted by Fox law. | |
3.3 Thermal degradation behaviour of the blends
Fig. 4(a) shows the TGA thermograms of extruded PC/PMMA blends in the presence of 0.5% tin(II) 2-ethylhexanoate. For comparison, TGA thermograms of extruded PC and PMMA in the absence and presence of 0.5% tin(II) 2-ethylhexanoate are also presented in the same figure. The PC/10PMMA blend without any transesterification catalyst shows two distinct thermal degradation steps corresponding to PC and PMMA, which can be seen more clearly in the first derivative of TGA thermograms shown in Fig. 4(b), suggesting that the interactions between the two phases, if any, are quite weak. In contrast, we observe single step thermal degradation of all the PC/PMMA blends prepared in the presence of 0.5% tin(II) 2-ethylhexanoate as a catalyst, suggesting the presence of a strong interaction between the PC and PMMA phases in the compatibilized blends. The degradation temperature of the compatibilized PC/PMMA blends has been plotted in the inset of Fig. 4 as a function of PMMA content. It is evident from the figure that as the PMMA content increases the degradation temperature decreases, as expected on the basis of the lower degradation temperature of PMMA. The slight decrease in the degradation temperature of PC/PMMA blends prepared using the transesterification catalyst, with respect to the PC/PMMA blends without the catalyst, may be due to the degradation of PC caused by the catalyst, as is well known for transesterification catalysts.31
3.4 FTIR evidence for the interaction between the PC and PMMA phases
Fig. 5(a) compares the FTIR spectra of the PC/PMMA blends prepared using a 0.5% catalyst with those for pure PC and PMMA in the wave-number range 675–2000 cm−1. The singlet stretching vibration peak of the carbonyl group occurs at 1775 cm−1 and 1733 cm−1 in pure PC and PMMA, respectively.25 In the blends, this peak is a doublet, due to the presence of the carbonyl groups of both PC and PMMA. The variation in the carbonyl peak positions of PC and PMMA in the blends as a function of the PMMA content is depicted in Fig. 5(b). It is evident from Fig. 5(b) that as the PMMA content increases, the carbonyl peak of PC in the compatibilized blends shows a blue shift (towards higher wave number) whereas for the uncompatibilized blends, this peak does not show any significant shift. This blue shift indicates a stronger interaction between the PC and PMMA phases in the compatibilized blends. The carbonyl peak of PMMA does not show any significant shift outside the instrumental resolution for both the compatibilized and uncompatibilized blends.
3.5 Evidence for PC-g-PMMA graft copolymer formation
3.5.1
1H NMR studies.
To understand the mechanism of compatibilization between PC and PMMA in the presence of the tin(II) 2-ethylhexanoate catalyst, we recorded the 1H-NMR spectra of pure PC, pure PMMA and the PC/20PMMA + 0.5% tin(II) 2-ethylhexanoate blends. These spectra are shown in Fig. 6. PC is known to have two different proton environments corresponding to the aromatic ring and the methyl group protons leading to 1H NMR peaks in the range 7.1–7.3 ppm (this is a multiplet) and at 1.685 ppm (singlet), respectively, as can be seen from Fig. 6(I). On the other hand, pure PMMA has three different proton environments corresponding to methyl ester (–OCH3–), methyl (–CH3) and methylene (–CH2–) giving rise to 1H NMR peaks at 3.547 (singlet), 0.791 (multiplet) and 1.761 (multiplet) ppm, as can be seen from Fig. 6(II). It is interesting to note that in the 1H NMR spectrum of the PC/20PMMA blend prepared using 0.5% (w/w) tin(II) 2-ethylhexanoate shown in Fig. 6(III), the methyl ester proton peak appears at 3.624 ppm, which is significantly shifted with respect to that of PMMA occurring at 3.547 ppm. One does not expect any change in the 1H NMR spectrum after compatibilization, because all the proton environments, except that of the methyl ester proton of PMMA, are unaffected by the exchange reaction. The methyl ester proton peak can, however, change due to the exchange reaction, because this reaction occurs between the carbonate and ester groups of PC and PMMA in the presence of the catalyst. The mechanism for such an exchange reaction is shown in Fig. 7 and has also been discussed earlier in our previous work.28 The fact that the methyl ester proton peak of PMMA is significantly shifted with respect to that in pure PMMA clearly suggests that such an exchange reaction takes place. The exchange reaction leads to the formation of the PC-g-PMMA graft copolymer, as explained in the figure.
3.5.2 FTIR studies.
In order to confirm the grafting of PMMA on PC, uncompatibilized and compatibilized PC/20PMMA blends prepared using 0.5% tin(II) 2-ethylhexanoate catalyst were dipped into AR grade acetone (∼1% dilution) for 48 h in two separate closed conical flasks. Acetone was chosen, because it is a good solvent for PMMA and a non-solvent for PC. After two days, acetone was extracted from the mixture and this protocol was repeated thrice for the possible dissolution of PMMA from the blends. Thus, by repeating the extraction process, the PMMA homopolymer (free PMMA) was removed from the uncompatibilized and compatibilized PC/20PMMA blends. The acetone insoluble portion was analyzed by FTIR to check for the presence of the PMMA peak near the 1732 cm−1 wavenumber. It is expected that the acetone insoluble portion will not contain the PMMA peak, unless and until there is a chemical reaction between the PC and PMMA chains leading to PC-g-PMMA graft copolymer formation. Fig. 8 depicts the FTIR spectra of the uncompatibilized and compatibilized blends with and without acetone treatment. It is evident that the PMMA peak disappears after acetone treatment in the uncompatibilized blends. On the other hand, the PMMA peak in the compatibilized blend survives even after acetone treatment, although the intensity of this peak decreases slightly. We believe that the PMMA homopolymers not involved in grafting are responsible for this reduction in intensity. Thus our FTIR studies provide additional confirmation of the PC-g-PMMA graft copolymer formation in the presence of 0.5% tin(II) 2-ethylhexanoate catalyst. We believe that this graft copolymer acts as a compatibilizer between the PC and PMMA phases, giving rise to homogeneous and compatibilized PC/PMMA blends with a single Tg and a single degradation temperature.
3.6 Comparison of the optical transmittance of the uncompatibilized and compatibilized PC/PMMA blends
On account of the immiscible nature of PC and PMMA, the uncompatibilized PC/PMMA blends are heterogeneous, containing macro-phase separated regions of PC and PMMA. These regions scatter light and make the blends opaque. Fig. 9 compares the transmittance of injection molded sheets (∼2 mm thick) of pure PC, pure PMMA, and PC/20PMMA blends with and without 0.5% tin(II) 2-ethylhexanoate catalyst (measured by UV/Vis spectrophotometry over the 400 to 800 nm wavelength region). PMMA and PC exhibit a high transmittance of ∼76% and 75%, respectively, at a wavelength of 700 nm, whereas the optical transmittance of the uncompatibilized PC/20PMMA blends is only 0.4%, revealing its opaqueness. In the case of PC/20PMMA blends with 0.5% (w/w) tin(II) 2-ethylhexanoate transesterification catalyst, we observe ∼53% optical transmittance at a wavelength of 700 nm. This shows that in the presence of the transesterification catalyst, the optical transmittance of the PC/PMMA blends is improved significantly, which may be attributed to the reduction in the relative size of the dispersed phases, which reduces the scattering losses in the visible region. This improvement in the optical transmittance provides indirect proof of the effective compatibilization of the PC and PMMA phases, which prevents macro-phase separation during injection molding. It may, however, be added that the compatibilized blends acquire a light yellow tinge.
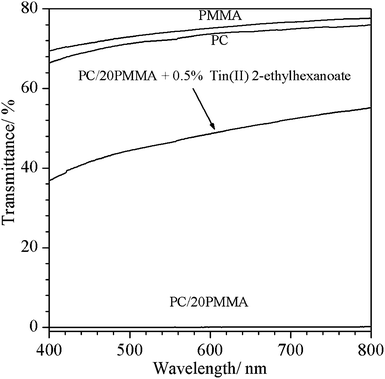 |
| Fig. 9 Optical transmittance of pure PC, pure PMMA, uncompatibilized PC/20PMMA and compatibilized PC/20PMMA blend prepared using 0.5% tin(II) 2-ethylhexanaoate catalyst. | |
4. Discussions
As pointed out in section 1, Montaudo et al.27 used a SnOBu2 catalyst and did not find any evidence for PC-g-PMMA graft copolymer formation. They instead proposed an exchange reaction between the monomer methyl methacrylate (MMA), generated by the unzipping of the PMMA chains, and the carbonate group of PC. Their claim was basically based on the 1H NMR findings. Therefore, it is worth comparing the 1H NMR spectra of the PC/PMMA blends prepared using tin(II) 2-ethylhexanoate in the present work with those prepared using SnOBu2 as the catalyst.27 Montaudo et al.27 reported peaks at 3.8, 5.5 and 6.1 ppm corresponding to the MMA monomer. However, the 1H NMR spectra of our blends do not show any such peaks. This suggests that in the presence of a tin(II) 2-ethylhexanoate organometallic transesterification catalyst, the PMMA phase of the PC/PMMA blends did not depolymerize. Our findings thus differ from those of Montaudo et al.27
It is worth mentioning here that Sn compounds are known to degrade PC by polymer chain scission, when used in sufficient quantity and for sufficient heating duration,31 as can be seen from a comparison of the thermal degradation behaviour of pristine PC and PC with a tin(II) 2-ethylhexanoate catalyst also shown in Fig. 4. On the other hand, we do not find any evidence for a similar degradation of PMMA in the presence of tin(II) 2-ethylhexanoate, as can be seen from its comparison with the degradation behaviour of pristine PMMA shown in the same figure. This suggests that the depolymerization of PMMA reported by Montaudo et al.27 may not have been induced by the organometallic catalyst. We believe that the difference in the findings of Montaudo et al.27 and our work regarding the depolymerization of PMMA is due to the difference in the PMMA used. This is corroborated by the fact that the thermogravimetric analysis of the PMMA used by Montaudo et al.27 shows onset of degradation from 200 °C, whereas the PMMA used in the present and the previous reports28 starts degrading after 300 °C. Furthermore, they have reported 20% weight loss in PMMA after isothermal heating at 230 °C for 60 min, whereas the PMMA used by us under an identical heating protocol shows negligible weight loss at 230 °C (as shown in Fig S1, ESI†).
5. Conclusions
The results presented in this report demonstrate the transesterification catalytic action of the organometallic compound tin(II) 2-ethylhexanoate in the formation of compatibilized PC/PMMA blends. This catalyst has not been used previously for the compatibilization of immiscible PC and PMMA phases. We have shown that as small a quantity as 0.5% (w/w) of tin(II) 2-ethylhexanoate is sufficient to develop compatibilized PC/PMMA blends containing up to 40% PMMA. The 1H NMR and FTIR studies provide unambiguous evidence for PC-g-PMMA graft copolymer formation in the presence of the new transesterification catalyst during the reactive extrusion process. This graft copolymer compatibilizes the PC and PMMA phases. All these blends show a single Tg and a single degradation temperature, while the FTIR spectra reveal a strong interaction between the PC and PMMA phases in the blends. There is a significant improvement in the optical transmittance of the compatibilized blends as compared to that of the uncompatibilized blends, which are simply opaque.
Acknowledgements
Financial support from Department of Information Technology and Moser Baer India Limited (MBIL), India is gratefully acknowledged. Mr. A. K. Singh acknowledges CSIR, India for the award of a Senior Research Fellowship. We thank Prof. B. M. Mandal, for helpful discussions. Thanks are also due to TIFR, India for providing 1H NMR data.
References
- Y. Cao, J. Zhang, J. Feng and P. Wu, ACS Nano, 2011, 5, 5920 CrossRef CAS.
- B. J. Busche, A. E. Tonelli and C. M. Balik, Polymer, 2010, 51, 454 CrossRef CAS.
- R. Malik, C. K. Hall and J. Genzer, Macromolecules, 2011, 44, 8284 CrossRef CAS.
- C. Sailer and U. A. Handge, Macromolecules, 2008, 41, 4258 CrossRef CAS.
- M. L. Xue, Y. L. Yu, H. H. Chuah, J. M. Rhee, N. H. Kim and J. H. Lee, Eur. Polym. J., 2007, 43, 3826 CrossRef CAS.
-
D. R. Paul and C. B. Bucknall, Polymer Blends, John & Sons. Inc, New York, 2000 Search PubMed.
-
L. A. Utracki, Polymer Alloys and blends, Hanser, Munich, 1989 Search PubMed.
- W. S. Chow, Z. A. M. Ishak, J. Karger-Kocsis, A. A. Apostolov and U. S. Ishiaku, Polymer, 2003, 44, 7427 CrossRef CAS.
- L. Cui and D. R. Paul, Polymer, 2007, 48, 1632 CrossRef CAS.
- S. C. Jana, N. Patel and D. Dharaiya, Polymer, 2001, 42, 8681 CrossRef CAS.
- B. G. Soares, F. F. Alves, M. G. Oliveira, A.C.F. Moreira, F. G. Garcia and M. F. S. Lopes, Eur. Polym. J., 2001, 37, 1577 CrossRef CAS.
- Y. Agari, A. Ueda, Y. Omura and S. Nagai, Polymer, 1997, 38, 801 CrossRef CAS.
- G. D. Butzbach and J. H. Wendorff, Polymer, 1991, 32, 1155 CrossRef CAS.
- J. M. Saldanha and T. Kyu, Macromolecules, 1987, 20, 2840 CrossRef CAS.
- T. Kyu and J. M. Saldanha, Macromolecules, 1988, 21, 1021 CrossRef CAS.
- W. N. Kim and C. M. Burns, Macromolecules, 1987, 20, 1876 CrossRef CAS.
- E. M. Woo and C. C. Su, Polymer, 1996, 37, 5186 Search PubMed.
- M. Rabeony, D. T. Heeih, R. T. Garner and D. G. Peiffer, J. Chem. Phys., 1992, 97, 4505 CrossRef CAS.
- N. An, Y. Yang and L. Dong, Macromolecules, 2007, 40, 306 CrossRef CAS.
- T. Kyu and J. M. Saldanha, J. Polym. Sci., Polym. Lett. Ed., 1988, 26, 33 CrossRef CAS.
- M. Nishimoto, H. Keshkkula and D. R. Paul, Polymer, 1991, 32, 272 CrossRef CAS.
- E. M. Woo and C. C. Su, Polymer, 1996, 37, 4111 CrossRef CAS.
- S. R. Ray and M. Bousmina, Macromol. Rapid Commun., 2005, 26, 1639 CrossRef CAS.
- S. R. Ray, M. Bousmina and A. Maazouz, Polym. Eng. and Sci, 2006, 1121 CAS.
- M. Penco, L. Sartore, S. D. Sciucca, L. D. Landro and A. D'Amore, Macromol. Symp., 2007, 247, 252 CrossRef CAS.
- M. S. Lee, M. K. Ha, H. S. Lee and W. H. Jo, J. Kore. Fiber Soc., 2001, 38, 101 Search PubMed.
- G. Montaudo, C. Puglisi and F. J. Damperi, J. Polym. Sci., Part A: Polym. Chem., 1998, 36, 1873 CrossRef CAS.
- A. K. Singh, R. Prakash and D. Pandey, J. Phys. Chem. B, 2011, 115, 1601 CrossRef CAS.
- A. K. Singh, R. K. Mishra, R. Prakash, P. Maiti, A. K Singh and D. Pandey, Chem. Phys. Lett., 2010, 486, 32 CrossRef CAS.
- N. Marin and B. D. Favis, Polymer, 2002, 43, 4723 CrossRef CAS.
- S. J. Chiu, S. H. Chen and C. T. Tsai, Waste Manage., 2006, 26, 252 CrossRef CAS.
- J. G. Fox, Bull. Am. Phys. Soc., 1956, 1, 123 Search PubMed.
- K. L Howdeshell, P. H. Peterman, B. M. Judy, J. A. Taylor, C. E Orazio, R. L Ruhlen, F. S. Vom Saal and W. V. Welshons, Environ. Health Perspect., 2003, 111, 1180 CrossRef.
- A. V. Krishnan, P. Stathis, S. F. Permuth, L. Tokes and D. Feldman, Endocrinology, 1993, 132, 2279 CrossRef CAS.
- E. M. Woo and M. N. Wu, Polymer, 1996, 37, 1907 CrossRef CAS.
|
This journal is © The Royal Society of Chemistry 2012 |
Click here to see how this site uses Cookies. View our privacy policy here.