DOI:
10.1039/C2RA21829A
(Paper)
RSC Adv., 2012,
2, 10217-10221
NiO hierarchical structure: template-engaged synthesis and adsorption property†
Received
16th August 2012
, Accepted 16th August 2012
First published on 14th September 2012
Abstract
NiO hierarchical structure was synthesized via a facile template-engaged solvothermal reaction of Mg5(CO3)4(OH)2·4H2O and Ni(NO3)2·6H2O, followed by annealing Ni-base precursor at high temperature in air. The as-prepared samples were characterized by X-ray diffraction (XRD), scanning electron microscopy (SEM), energy dispersive X-ray (EDX) and N2 adsorption-desorption. It has been demonstrated that the NiO hierarchical structure retains the morphology of the template, and possesses a high surface area (over 58 m2 g−1). Moreover, the growth mechanism of Ni-base precursor has been proposed. The porous hierarchical NiO exhibited good adsorption for the removal of organic dye pollutants from water. Thus, the porous hierarchical NiO is expected to find promising applications in catalysis, energy storage and sensors.
1. Introduction
Over the past few years, the synthesis of hierarchical micro/nanostructures has attracted considerable attention owing to their potential in numerous fields, such as medicine, energy storage, catalysis and adsorption.1–5 Within this context, the sacrificial template method has been proven to be a straightforward, versatile, and effective approach to fabricate hierarchical micro/nanostructures.6–10 Such strategy usually requires template materials to have controllable architecture and suitable oxidation-reduction or ion-exchange capacities. Thus, developing non-toxic and economical template materials with designed morphology and appropriate activity is an important topic in the field of hierarchical material synthesis.
On the other hand, as an important transition metal oxide, NiO has attracted special interest due to their broad applications, such as catalysis, lithium-ion batteries, dye-sensitized solar cells, and electrochemical super-capacitors.11–15 And more and more attention has been paid on improving the performances of NiO materials. One effective approach is the formation of hierarchical structures with high specific surface area, which can absorb more reactant and provide more reaction active sites. Although various methods have been employed for the preparation of NiO hierarchical strutucres,16–20 there has been comparatively few research on template-engaged synthesis of NiO materials because of the weaker oxidation-reduction and ion-exchange capacities of Ni2+.
As a part of our continuous studies on magnesium chemistry,21,22 we have recently focused our attention on Mg5(CO3)4(OH)2·4H2O (MCH), which has been found to have a significantly different solubility compared to other insoluble metal carbonates or hydroxides, and can more easily grow into hierarchical structures, including flowerlike and hierarchical hollow structures.23–25 These characteristics of MCH led us to adopt it as a sacrificial template to prepare hierarchical structures. And NiO was chosen as the target to develop this general template route to synthesize hierarchical structured oxides.
Herein, we present a facile template-engaged strategy to synthesize hierarchical NiO with porous network-like structures by using MCH as template. The samples were characterized by X-ray diffraction, scanning electron microscopy, energy dispersive X-ray and N2 adsorption-desorption. The as-prepared NiO exhibits excellent adsorption activities and can be a candidate for practical applications in waste-water treatment.
2. Experimental
2.1 Preparation of MCH template
MCH were synthesized referring to the previous reported methods.24–27 Ethanol (95%, 50 mL) was transferred to a 250 mL three-necked flask. And MgCl2–NH4HCO3 mixed aqueous solution (60 mL, containing 0.4 mol L−1 of Mg(HCO3)2) was added into the vigorously stirred ethanol. Then a white precipitate was collected, filtered off, and washed with water, then dispersed in 120 mL of deionized water in a 250 mL beaker. Subsequently, the suspension was maintained at 80 °C for 2 h. After that, the white powder was collected, filtered off, washed with water and ethanol three times, and dried in a blast drying oven at 60 °C for 4 h.
2.2 Preparation of NiO hierarchical structure
The as-prepared MCH template (0.3 g) was dispersed in 20 mL of ethanol. Ni(NO3)2·6H2O–ethanol solution (0.50 mol L−1, 10 mL) was added to the suspension of MCH with vigorous stirring. The mixture was stirred for 30 min, and transferred into an autoclave (50 mL capacity), then treated at 120 °C for 18 h. Subsequently, the autoclave was cooled down to room temperature naturally. The green precursor was collected, filtered off, washed with ethanol three times, and dried in a blast drying oven at 60 °C for 4 h. Finally, the hierarchical NiO was obtained by heating the precursor in tube furnace at 400 °C for 3 h.
2.3 Characterization
The as-prepared samples were characterized by XRD (Rigaku-DMax 2400) in reflection mode (Cu-Kα radiation) at scanning rate of 0.02 S−1 in the 2θ from 5 to 80°. The shapes and structures of as-prepared samples were observed with scanning electron microscope and field emission scanning electron microscope (SEM, JEOL-6360LV, operated at 20 kV; FE-SEM, NOVA NANOSEM 450, operated at 5–10 kV). Energy Dispersive X-Ray (EDX) analysis was also performed on JEOL-6360LV during SEM.
2.4 Adsorption property of hierarchical NiO
N2 adsorption-desorption data were determined on ASAP 2020 physisorption apparatus at the temperature of liquid nitrogen, in which the sample was degassed at 105 °C for 10 h before measurement. The surface area was calculated by using the Brunauer-Emmett-Teller method.
Simulated waste-water with different concentrations (10, 20, 40 mg L−1) was prepared by solution of acid fuchsine with deionized water. Adsorption experiments were carried out in a beaker (500 mL) containing as-obtained porous hierarchical NiO (0.35 g) and acid fuchsine aqueous solution (350 mL) under stirring. At different intervals, 5.0 mL of the suspensions was collected, filtered, and analyzed by a Hitachi U-4100 UV-visible spectrophotometer immediately.
To recycle hierarchical NiO, the filters containing acid fuchsine and NiO was collected, and heated in tube furnace at 400 °C under air for 2 h. Finally, the reborn NiO was used for adsorption of acid fuchsine from water again. The as-prepared and reborn NiO used for absorption of acid fuchsine at different initial concentrations (20, 40 mg L−1) were labeled as S-20, R-20, S-40 and R-40, respectively.
3. Result and discussion
3.1 Chemical transformation of MCH template in to hierarchical NiO
The NiO hierarchical structure was generated by solvothermal reaction of MCH template with Ni(NO3)2·6H2O, followed by calcining the precursor at 400 °C. Fig. 1 shows the X-ray diffraction (XRD) of template, solvothermal and calcined products. It can be seen from Fig. 1a, all peaks can match well with Mg5(CO3)4(OH)2·4H2O. (JCPDS No. 25-0513), indicating a monoclinic space group P21/c with lattice parameters: a = 1.011 nm, b = 0.894 nm, c = 0.838 nm, and β = 114.58 (Z = 2). It is noteworthy that the solvothermal product is Ni3(OH)4(NO3)2 (as shown in Fig. 1b, JCPDS No. 22-0752, a hexagonal with lattice parameters: a = 0.313 nm, c = 0.6898 nm), rather than nickel carbonate or nickel hydroxide. It can be understood that Ni3(OH)4(NO3)2 is more stable than nickel carbonate or nickel hydroxide under solvothermal conditions.20 After calcining, the XRD data of product shows clear reflections characteristic of NiO (JCPDS No.47-1049, cubic space group Fm3m with lattice parameters: a = 0.417 nm, (Z = 2)). And only Ni and O can be detected by Energy Dispersive X-Ray (EDX) analysis (Fig. S1†) to confirm the complete transformation of MCH into NiO.
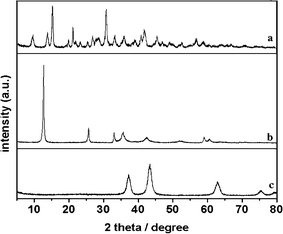 |
| Fig. 1 XRD patterns of the MCH template (a), solvothermal product (b) and calcined product (c). | |
The typical scanning electron microscope (SEM) and field emission scanning electron microscope (FE-SEM) images of template, solvothermal and calcined products are shown in Fig. 2. As shown in Fig. 2a, the MCH template has a uniform flower-like morphology with the size of ranging from 6 to 8 μm. It can also be observed from the high magnification image (inset of Fig. 2a and Fig. 2d), the flower-like particle is built up by a number of microsheets. Fig. 2b shows that Ni3(OH)4(NO3)2 keep the flower-like morphology of MCH template and display rather rougher surface compared with that of template. It can be seen from Fig. 2e, the Ni3(OH)4(NO3)2 has a hierarchical structure consisting of interconnected and primary nanoflakes with the size of 100–200 nm. After calcination, flower-like morphology of the structures still remained with the phase transformation from Ni3(OH)4(NO3)2 to NiO (Fig. 2c). Moreover, it is worth noting that the NiO primary particles have wormlike morphology, and assemble into a porous network-like structure (in Fig. 2f). The TEM image (in Fig. S2†) clearly reveals hierarchical NiO is built up by nanoflake with size of about 100 nm and thickness of 5–10 nm. It also can be seen from TEM images, the nanoflake is hollow. Considering the fact that the Ni3(OH)4(NO3)2 particles are flake-like, porous network-like structure should be formed during thermal decomposition. The SEM and FESEM characterizations clearly indicate that this template-engaged strategy is very successful.
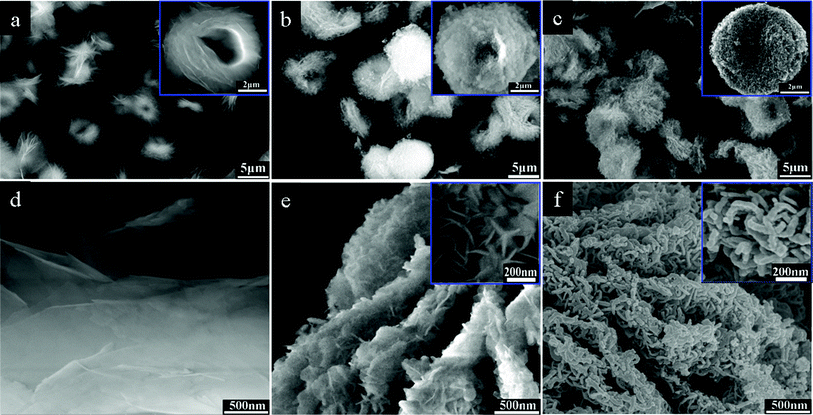 |
| Fig. 2 Overview SEM images of MCH template (a), solvothermal product (b) and calcined product (c); FE-SEM images of MCH template (d), solvothermal product (e) and calcined product (f). | |
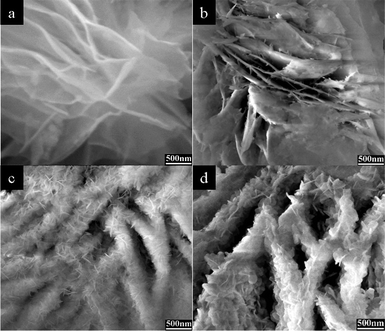 |
| Fig. 3 FE-SEM images of the samples obtained under time-dependent experiments: (a) room temperature, 30 min, (b) 120 °C, 3 h, (c) 120 °C, 9 h, (d) 120 °C, 18 h. | |
3.2 Growth mechanism of hierarchical Ni-base precursor
To investigate the growth mechanism of hierarchical structured Ni-base precursor, time-dependent experiments were carefully carried out. The related FE-SEM characterizations were shown in Fig. 3a–d, and the related XRD data of as-prepared samples at different time were shown in Fig. S3†. When MCH template and Ni(NO3)2·6H2O–ethanol solution were mixed under stirring at room temperature for 30 min, no Ni3(OH)4(NO3)2 was generated (Fig. 3a). While the solvothermal reaction was conducted for 3 h, a small amount of flake-like structures was formed on the surface of MCH microsheets (Fig. 3b). On increasing solvothermal reaction time to 9 h, the amount and size of flake-like structures increased with disappearing of MCH microsheet as shown in Fig. 3c. Finally, the typical hierarchical Ni3(OH)4(NO3)2 microstructure was formed. FE-SEM observation of the typical product obtained for 18 h (Fig. 3d) reveals that the hierarchical structure formation in Ni3(OH)4(NO3)2 goes through template-engaged MCH template and aggregation of Ni3(OH)4(NO3)2 nanoflake.
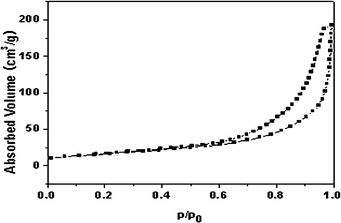 |
| Fig. 4 N2 adsorption/desorption isotherms of porous hierarchical NiO. | |
Based on above experiments, the formation mechanism of hierarchical structured Ni3(OH)4(NO3)2 may be explained as replacement reaction and Kirkendall effect that is similar to the previous reports.6–9 MCH and Ni(NO3)2·6H2O can react with each other and form a diffusion pair. Because CO32−, OH−, Mg2+ and H2O in MCH microsheet diffuse faster than Ni2+ and NO3− ions, replacement reaction relies on the diffusion of atoms around the surface of MCH. Ni2+ and NO3− ions are first adsorbed on the surface of MCH, and CO32−, OH−, Mg2+ and H2O are dissociated from MCH. Then, CO32− is hydrolyzed into OH− under solvothermal conditions. In this time, Ni2+ and NO3− react with OH− resulting in Ni3(OH)4(NO3)2 nanoflakes on the surface of MCH. With the continuous outward atoms flow of MCH from solution to, and inward flow of Ni2+ and NO3− ions through the gaps between Ni3(OH)4(NO3)2 nanoflakes, the reaction interface move towards interior of MCH microsheet that lead to complete conversion of MCH into Ni3(OH)4(NO3)2. Finally, the typical Ni3(OH)4(NO3)2 hierarchical structure was formed.
3.3 Adsorption activity and reducibility of hierarchical NiO
In general, transition metal oxides could be used for catalytic oxidation of reductive organic or inorganic by adsorption and subsequent catalysis at relatively low temperature.28–31 And the specific surface area is the crucial factor to the adsorption and catalysis performance. N2 adsorption-desorption analysis shows that the as-prepared hierarchical NiO have a high Brunauer-Emmett-Teller (BET) surface area of 58.5 m2 g−1, and a high pore volume of 0.30 cm3 g−1 (as shown in Fig. 4). The nitrogen adsorption/desorption curves can be assigned to IV type isotherms defined by IUPAC. At higher relative pressure (P/P0 = 0.6–1.0), well-defined H-3 type hysteresis loops is obtained. This indicates that mesopores exist in the as-prepared hierarchical NiO. Moreover, at higher relative pressure (P/P0 > 0.95), adsorption capacity increase rapidly, indicating the existence of macropores. Therefore, the isotherm curves and analysis reveal that mesopores and macropores co-exist in the hierarchical NiO.
In this paper, as an example of potential applications, the as-prepared hierarchical NiO were used as an adsorbent for waste-water treatment. Acid fuchsine is mainly used for biological staining, tissue staining and identification of free chlorine. It is difficult to degrade acid fuchsine in wastewater through traditional chemical and biological approaches for its stable structure.19 When the initial concentration of acid fuchsine in water is 20 mg L−1, the as-synthesized NiO (1 g L−1) could remove about 98% of the acid fuchsine without any additives at room temperature in 30 min, as shown by the UV/Vis absorption curves and photo within different time (Fig. 5a and its inset). Fig. 5b shows the time profile of acid fuchsine removal with NiO at different initial acid fuchsine concentrations. It can be seen that the adsorption rates within the first 30 s were surprisingly fast under all the concentrations, which may be attributed to the unique structures of porous hierarchical NiO. The adsorption process almost finished within 10 min, and no significant change was observed from 10 to 30 min. The removal efficiencies were found to be 99, 98, and 81% at the initial acid fuchsine concentrations of 10, 20, and 40 mg L−1, respectively. Therefore, the maximum acid fuchsine adsorption capacity of hierarchical NiO was found to be 32.4 mg g−1 when the initial acid fuchsine concentration was 40 mg L−1. Table 1 summarises the comparisons between the adsorption capacity of the as-synthesized hierarchical NiO in this study and those of NiO synthesized previously in the literature. Obviously, the adsorption capacity of our synthesized hierarchical NiO is higher than that of rose-like NiO nanoparticle,19 and similar with that of the NiO hollow structure.
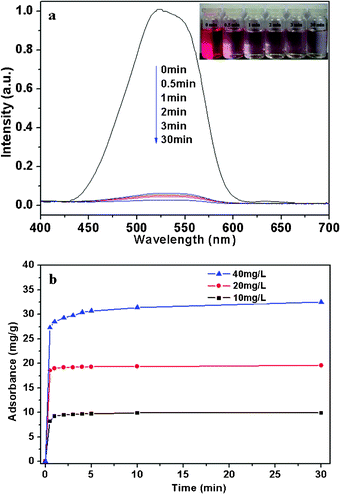 |
| Fig. 5 (a) Absorption spectra and photographs of 350 mL of 20 mg L−1 acid fuchsine aqueous solution in the presence of 350 mg of NHS in different time. (b) Time profile of acid fuchsine removal with NHS; The concentration of NHS adsorbent was 1.0 g L−1; the initial acid fuchsine concentrations ranged from 10 to 40 mg L−1. | |
Table 1 Comparisons of acid fuchsine adsorption capacities of different NiO adsorbentsa
Adsorbent |
Removal capacity (mg g−1) |
References |
NiO microtube was prepared according to our previous report,21 and was used as adsorbent at the initial acid fuchsine concentrations of 40 mg L−1.
|
Hierarchical NiO |
32.4 |
This work |
Rose-like NiO |
14.0 |
19
|
NiO microtube |
34.5 |
This work |
After adsorption, the solid/liquid separation of suspension was very easy by filtration, because the as-prepared NiO were several micrometers in size. After calcining, the reborn sample still remains as a flowerlike hierarchical structure (in Fig. S4†), and have the same absorption activity of acid fuchsine as the initial one (as shown in Fig. S5†). This advantage is very important for practical applications.
4. Conclusions
In summary, a facile template-engaged strategy to synthesize NiO hierarchical structure by using Mg5(CO3)4(OH)2·4H2O as a template has been demonstrated. The as-prepared NiO retains the morphology of the template, and possesses porous network-like structures with a high surface area. The growth mechanism of the Ni-base precursor has been investigated and can be explained by the Kirkendall effect. The results of acid fuchsine removal from water show that the adsorptivity of porous hierarchical NiO is obviously higher than rose-like NiO nanostructures. Meanwhile, the as-prepared NiO exhibited excellent separation and regeneration activity. Thus, the porous hierarchical NiO is expected to find promising applications in catalysis, energy storage and sensors. Further studies on controlling the size and shape of the MCH template and its application in the preparation of other hierarchical structured metal oxides are ongoing in our lab. We expect that this template-engaged method may open a new way to fabricate metal oxide hierarchical structures with good physical and/or chemical properties.
Acknowledgements
This work was supported by National High Technology Research and Development Program of China (2008AA03A325), National Natural Science Foundation of China (21076041 and 21276046), the Fundamental Research Funds for the Central Universities of China (DUT11LK16), the Ministry of Education Science and technology research projects and High-Tech R&D projects in Magnesuim Industry of Liaoning Province in China.
References
- K. Liu, Z. H. Nie, N. N. Zhao, W. Li, M. Rubinstein and E. Kumacheva, Science, 2010, 329, 197 CrossRef CAS.
- F. W. Zhuge, J. J. Qiu, X. M. Li, X. D. Gao, X. Y. Gan and W. D. Yu, Adv. Mater., 2011, 23, 1330 CrossRef CAS.
- X. Y. Zhang, X. Chen, S. M. Dong, Z. H. Liu, X. H. Zhou, J. H. Yao, S. P. Pang, H. X. Xu, Z. Y. Zhang, L. F. Li and G. L. Cui, J. Mater. Chem., 2012, 22, 6067 RSC.
- H. W. Bai, Z. Y. Liu and D. D. Sun, Phys. Chem. Chem. Phys., 2011, 13, 6205 RSC.
- X. M. Wu, H. Q Cao, G. Yin, J. F Yin, Y. X. Lu and B. J. Li, Phys. Chem. Chem. Phys., 2011, 13, 5047 RSC.
- J. B. Fei, Y. Cui, X. H. Yan, W. Qi, Y. Yang, K. W. Wang, Q. He and J. B. Li, Adv. Mater., 2008, 20, 452 CrossRef.
- Z. Y. Wang, D. Y. Luan, C. M. Li, F. B. Su, S. Madhavi, F. Y. C. Boey and X. W. Lou, J. Am. Chem. Soc., 2010, 132, 16271 CrossRef CAS.
- S. Muduli, O. Game, V. Dhas, A. Yengantiwar and S. B. Ogale, Energy Environ. Sci., 2011, 4, 2835 CAS.
- L. N. Ye, C. Z. Wu, W. Guo and Y. Xie, Chem. Commun., 2006, 42, 4738 RSC.
- X. W. Lou, L. A. Archer and Z. C. Yang, Adv. Mater., 2008, 20, 3987 CrossRef CAS.
- G. W. Peng, L. R. Merte, J. Knudsen, R. T. Vang, E. Laegsgaard, F. Besenbacher and M. Mavrikakis, J. Phys. Chem. C, 2010, 114, 21579 CAS.
- B. Zhao, X. K. Ke, J. H. Bao, C. L. Wang, L. Dong, Y. W. Chen and H. L. Chen, J. Phys. Chem. C, 2009, 113, 14440 CAS.
- E. A. Gibson, A. L. Smeigh, L. Le Pleux, J. Fortage, G. Boschloo, E. Blart, Y. Pellegrin, F. Odobel, A. Hagfeldt and L. Hammarstrom, Angew. Chem., Int. Ed., 2009, 48, 4402 CrossRef CAS.
- L. Li, E. A. Gibson, P. Qin, G. Boschloo, M. Gorlov, A. Hagfeldt and L. C. Sun, Adv. Mater., 2010, 22, 1759 CrossRef CAS.
- S. J. Ding, T. Zhu, J. S. Chen, Z. Y. Wang, C. L. Yuan and X. W. Lou, J. Mater. Chem., 2011, 21, 6602 RSC.
- J. W. Lang, L. B. Kong, W. J. Wu, Y. C. Luo and L. Kang, Chem. Commun., 2008, 35, 4213 RSC.
- L. X. Yang, Y. J. Zhu, H. Tong, Z. H. Liang and W. W. Wang, Cryst. Growth Des., 2007, 7, 2716 CAS.
- M. S. Wu, Y. P. Lin, C. H. Lin and J. T. Lee, J. Mater. Chem., 2012, 22, 2442 RSC.
- S. Q. Shang, K. Y. Xue, D. R. Chen and X. L. Jiao, CrystEngComm, 2011, 13, 5094 RSC.
- Z. X. Yang, W. Zhong, C. Au, J. Y. Wang and Y. W. Du, CrystEngComm, 2011, 13, 1831 RSC.
- P. Tian, J. W. Ye, N. Xu, W. T. Gong, Q. S. Zhang, Y. Lin and G. L. Ning, Chem. Commun., 2011, 47, 12008 RSC.
- H. C. Pang, G. L. Ning, W. T. Gong, J. W. Ye and Y. Lin, Chem. Commun., 2011, 47, 6317 RSC.
- C. L. Yan and D. F. Xue, J. Phys. Chem. B, 2006, 110, 1581 CrossRef CAS.
- Z. P. Zhang, Y. J. Zheng, J. X. Zhang, Q. Zhang, J. P. Chen, Z. M. Liu and X. M. Liang, Cryst. Growth Des., 2007, 7, 337 CAS.
- K. Mitsuhashi, N. Tagami, K. Tanabe, T. Ohkubo, H. Sakai, M. Koishi and M. Abe, Langmuir, 2005, 21, 3659 CrossRef CAS.
- Z. P. Zhang, Y. J. Zheng, Y. W. Ni, Z. M. Liu, J. P. Chen and X. M. Liang, J. Phys. Chem. B, 2006, 110, 12969 CrossRef CAS.
- N. Sutradhar, A. Sinhamahapatra, S. K. Pahari, P. Pal, H. C. Bajaj, I. Mukhopadhyay and A. B. Panda, J. Phys. Chem. C, 2011, 115, 12308 CAS.
- H. Zhang, J. L. Cao, G. S. Shao and Z. Y. Yuan, J. Mater. Chem., 2009, 19, 6097 RSC.
- L. S. Zhong, J. S. Hu, H. P. Liang, A. M. Cao, W. G. Song and L. J. Wan, Adv. Mater., 2006, 18, 2426 CrossRef CAS.
- X. Y. Yu, T. Luo, Y. Jia, R. X. Xu, C. Gao, Y. X. Zhang, J. H. Liu and X. J. Huang, Nanoscale, 2012, 4, 3466 RSC.
- J. B. Fei, Y. Cui, J. Zhao, L. Gao, Y. Yang and J. B. Li, J. Mater. Chem., 2011, 21, 11742 RSC.
Footnote |
† Electronic Supplementary Information (ESI) available: EDX, XRD and TEM characterizations of the as-synthesized samples. See DOI: 10.1039/c2ra21829a |
|
This journal is © The Royal Society of Chemistry 2012 |
Click here to see how this site uses Cookies. View our privacy policy here.