DOI:
10.1039/C5RA15186D
(Paper)
RSC Adv., 2016,
6, 9261-9269
Castor leaf mediated synthesis of iron nanoparticles for evaluating catalytic effects in transesterification of castor oil†
Received
30th July 2015
, Accepted 7th January 2016
First published on 12th January 2016
Abstract
A castor (Ricinus communis) leaf extract mediated process was developed for the synthesis of iron nanoparticles. The resultant iron nanoparticles were used as a catalyst in the transesterification of castor oil. The iron nanoparticles were characterized using UV-visible absorption spectrophotometry (UV-visible), Fourier-transform infrared spectroscopy (FTIR), X-ray diffraction (XRD), X-ray photoelectron spectroscopy (XPS), scanning electron microscopy (SEM), energy dispersive X-ray (EDX) and transmission electron microscopy (TEM). The TEM images confirm that the size of the iron nanocatalyst was in the range of 10 to 35 nm. The optimum conditions for obtaining the high yield of biodiesel were a 65 °C temperature, a 1
:
9 molar ratio of castor oil and methanol, 1 wt% catalyst loading, 150 min of reaction time and a 400 rpm stirring speed. The iron nanocatalyzed transesterification of castor oil yielded 85 ± 1% of biodiesel. The distributions of the saturated, monounsaturated and polyunsaturated fatty acid methyl esters (FAMEs) were identified as 4.11, 89.63 and 6.26%, respectively, using gas chromatography-mass spectrometry (GC-MS). The physico-chemical properties of the produced biodiesel agreed well with the ASTM standards.
1. Introduction
The world’s fuel demands are met by non-renewable energy resources like coals and crude oils. The rapid exhaustion of fossil fuels and environmental concerns lead to the search for an alternate fuel. Nowadays, biodiesel is considered as one of the substitutes for petroleum derived diesel (petrodiesel), since it has many advantages such as being renewable, biodegradable and non-toxic and having reduced emissions.1 Biodiesel (fatty acid methyl esters, FAMEs) is obtained from the transesterification of various vegetable oils. However, biodiesel production is expensive due to the high price of raw materials, catalyst selection, energy intensive purification and the separation of products. Recent research has focused on the use of low cost non-edible vegetable oils such as Azadirachta indica oil,2 Pongamia pinnata oil,3,4 Jatropha curcas oil,4,5 Ricinus communis oil6 and Calophyllum inophyllum oil7 for biodiesel production. These plants can produce a high yield of oils and they can be largely grown in wastelands and uncropped marginal lands. Thus, castor oil was chosen in the present study as the feed stock for the production of biodiesel.
Homogeneous and heterogeneous catalysts are employed for the commercial production of biodiesel. Homogeneous catalysts have various drawbacks such as catalyst separation, catalyst recyclability, corrosiveness and their influence on soap formation.8 Heterogeneous catalysts exhibit many disadvantages such as complicated preparation, they are expensive in nature and have low yields of biodiesel.8 Therefore, it is necessary to develop cost effective and potential catalysts to produce high yields of biodiesel. Recently, metal nanoparticles have played a vital role in the transesterification process as catalysts to produce high yields of biodiesel, owing to their more active surface area, improved resistance to the saponification reaction, good rigidity and high catalytic activity.9 On the contrary, metal nanoparticles are unstable in nature and they have a tendency to form aggregates.10 Xie and Ma11 developed biodiesel which was obtained from soyabean oil using immobilized lipase dispersed on magnetic Fe3O4 nanoparticles. However, the immobilization of enzymes requires additional time and cost. According to the literature, phytogenic metal nanoparticles are stable for a longer period of time.12 Thus, the present research focuses on the catalytic efficiency of phytogenic metal nanoparticles without the encapsulation of enzymes in the transesterification of castor oil.
Biological methods are gaining importance in recent years for the synthesis of nanoparticles, due to their non-toxicity, low cost and environmentally friendly nature. The biological synthesis of nanoparticles using microorganisms13 is time consuming and it is difficult to scale up the process whereas, the plant mediated synthesis of nanoparticles consumes less time.14 Recently, a few studies have reported the plant based biosynthesis of iron nanoparticles using aqueous Sorghum bran extract,14 green tea extract15 and Murraya koenigii leaf extract.16 To the best of our knowledge, there is no literature available for the synthesis of iron nanoparticles using castor leaf extract and to investigate their catalytic activity in the transesterification of castor oil.
The objectives of the study were to develop a castor leaf extract mediated process for the synthesis of iron nanoparticles and their catalytic efficiency in the transesterification of castor oil for the production of biodiesel. The phytosynthesized iron nanocatalyst was characterized using spectroscopic and electron microscopic analysis. The important physical and chemical properties of the biodiesel were also analyzed as per the American Society for Testing and Materials (ASTM) and the obtained values were compared with the biodiesel specification of ASTM D6751.
2. Materials and methods
2.1. Materials
Castor (Ricinus communis) oil was obtained from the local market in Tiruchirappalli, Tamil Nadu, India. Ferric chloride (FeCl3) and methanol (CH3OH) were procured from Merck specialities private Ltd, India. The castor oil and other chemicals were used without further purification. Fresh castor leaves were collected from dry land in Tiruchirappalli, Tamil Nadu, India.
2.2. Preparation of castor leaf extract
Castor leaves were thoroughly washed with tap water several times and finally washed with double distilled water. The washed leaves were cut into small pieces. Ten grams of the chopped leaves was taken in a glass beaker; 100 mL of double distilled water was added and boiled for 10 min at 100 °C. The obtained extract of the castor leaves was cooled, filtered and used as a reducing agent.
2.3. Green synthesis of iron nanoparticles
Ninety milliliters of 2.5 mM ferric chloride aqueous solution was prepared using sterile double distilled water in a 250 mL beaker under stirring conditions. Ten milliliters of prepared castor leaf extract was slowly added at 37 °C. To investigate the effect of leaf extract on iron nanoparticle formation, the ratio of ferric chloride solution to leaf extract was varied as 9
:
1, 8
:
2 and 7
:
3. To find out the optimum concentration of ferric chloride for the synthesis of the iron nanoparticles, the study was carried out by varying the concentration of ferric chloride as 0.25, 0.5, 1.0, 1.5, 2.0, 2.5 and 3.0 mM at 9
:
1. The appearance of a black colour indicated the formation of the iron nanoparticles. At the end of the reaction, the reaction mixture was centrifuged to separate the iron nanoparticles at 11
000 rpm for a period of 15 min. The obtained iron nanoparticles were washed with distilled water, dried and stored for further use.
2.4. Characterization of phytosynthesized iron nanocatalysts
UV-visible absorption spectrophotometry (Shimadzu Model no. UV-2450) at a resolution of 1 nm in the range of 200 to 800 nm was used to analyze the effect of FeCl3 on the formation of the iron nanoparticles. Fourier-transform infrared spectroscopy (FTIR) was recorded for the leaf extract and dried powder of the iron nanoparticles using a spectrum instrument (Perkin Elmer, Spectrum RX I) with the diffuse reflectance mode at a resolution of 2 cm−1 in the range of 400 to 4000 cm−1. The dried iron nanoparticles were examined using an X-ray diffractometer (XRD; PANalytical, Model no. XPERTPRO) for their crystallinity, X-ray photoelectron spectroscopy (XPS) using K-Alpha instruments supplied by Thermo Scientific for the chemistry at the surface of the nanoparticles and a scanning electron microscope (SEM) equipped with an energy dispersive X-ray (EDX) detector (JEOL, Model no. JSM – 6390LV). Also, the resultant iron nanoparticles were subjected to analysis of their size and shape using a transmission electron microscope (TEM) made by Philips (Model: Tecnai 10).
2.5. Production of biodiesel from castor oil
The transesterification reaction was conducted in a 250 mL three necked round bottom glass reactor assisted with stirring, heating and condensing facilities. The significant parameters including reaction temperature (45 to 65 °C), molar ratio of oil and alcohol (1
:
3 to 1
:
12), amount of iron nanocatalyst (0.5 to 1.5 wt%), reaction time (60 to 180 min) and stirring rate (100 to 500 rpm) were optimized to obtain the high yield of biodiesel. The optimized conditions were 1 wt% of the phytosynthesized iron nanocatalyst (Bio-FeNPs), 1
:
9 molar ratio of oil and methanol, 65 °C reaction temperature and 150 min reaction time at 400 rpm. The nanocatalysed transesterification of castor oil was performed using the above mentioned optimized conditions for the production of biodiesel. After completion of the reaction, the products were cooled to room temperature and allowed to stand for phase separation. The excess methanol was removed from the separated top layer of the crude biodiesel using a rotary vacuum evaporator (IKV, Model no. RV-10).
2.6. Characterization of biodiesel
The produced biodiesel was also analyzed using FTIR to identify the functional groups and the conditions were similar to those mentioned in Section 2.4. The various fatty acid methyl esters (FAMEs) present in the produced castor biodiesel were analyzed using gas chromatography-mass spectrometry (GC-MS; GC MS 5975C Agilent). The GC-MS was operated under the following conditions: DB-5 ms of an Agilent quartz capillary column (30 m × 0.25 mm × 0.25 μm) was used; the capillary column temperature of biodiesel was raised by 10 °C min−1 from 70 to 300 °C; the interface temperature of the biodiesel was 250 °C, the injector temperature was 250 °C; the gas flow rate of the high purity helium carrier was 1.51 mL min−1 and the injection volume was 1.0 μL. The interpretation of the mass spectrum was done using the MS library database of NIST. The fuel properties of the biodiesel were examined by performing the following experiments including cloud point, specific gravity, flash point, kinematic viscosity, refractive index, pour point, ash content, water content, calorific value and copper strip corrosion. The American Society for Testing and Materials (ASTM) procedures were adopted for analyzing the fuel properties. The obtained values of the biodiesel were compared with the ASTM D6751 standards. The reported values are within the repeatability range.
3. Results and discussion
3.1. UV-visible analysis of iron nanoparticles
The different ratios of ferric chloride solution and Ricinus communis leaf extract (9
:
1, 8
:
2 and 7
:
3) were evaluated to find out the optimum ratio for the formation of iron nanoparticles. The addition of one part castor leaf extract to nine parts of 2.5 mM aqueous FeCl3 solution instantly turned the solution to a black colour from its original pale yellow colour. The change in colour indicated the formation of iron nanoparticles (ESI Fig. S1† – inset). Similar results on the formation of iron nanoparticles using tea extract17 and grape leaf extract18 were reported. At the ratios of 8
:
2 and 7
:
3, the reaction mixture immediately turned to a precipitate. Hence, the optimum ratio of ferric chloride solution to leaf extract was 9
:
1. Further, the UV-visible spectra of the reaction mixture at different concentrations of ferric chloride solution (0.25, 0.5, 1.0, 1.5, 2.0, 2.5 and 3.0 mM) were recorded to find out the optimum concentration for the formation of iron nanoparticles (ESI Fig. S1†). The UV-visible spectra of the reaction mixture at 0.25 and 0.5 mM FeCl3 did not show any distinct peak. A precipitate was formed at a concentration of 3.0 mM ferric chloride and hence, the reactant mixture was not measured using UV-visible spectroscopy. The appearance of peaks was noticed at 270 and 305 nm, when the concentration of FeCl3 varied from 1.0 to 2.5 mM. These peaks indicate the formation of the iron oxide nanoparticles. Similar observations were reported by Cornell and Schwertmann.19 The maximum absorption was observed at 2.5 mM. Therefore, the 2.5 mM concentration of ferric chloride was considered as the optimum value. The results revealed the presence of two peaks showing the formation of the anisotropic iron oxide nanoparticles, as observed by Mohanraj et al.16
3.2. FTIR analysis of iron nanoparticles
Fig. 1 shows the FTIR spectra of the phytosynthesized iron nanoparticles and castor leaf extract to identify the responsible biomolecules for the formation of the Bio-FeNPs. The FTIR spectrum of the leaf extract shows bands at 3426, 2073, 1637 and 697 cm−1. The intense broad absorption at 3426 cm−1 is ascribed to the –OH stretching vibration of the hydroxyl group present in polyphenols. The characteristic peak at 2073 cm−1 may be attributed to the primary amines (–C–N) of amino acids present in the leaf extract. The characteristic peak at 1637 cm−1 is assigned to the amide-I (–N–H) group of the proteins. The characteristic band at 697 cm−1 may be attributed to the
C–H bending vibrations of polyphenols. The FTIR spectrum of the iron nanoparticles exhibits peaks at 3430, 2282, 1638, 1353, 1214, 1063, 763 and 549 cm−1. The band at 3430 cm−1 is assigned to the hydroxyl group of polyphenols. The characteristic peaks at 2282 and 1638 cm−1 are attributed to the nitrile group (–C
N) and carbonyl group (–C
O) of the amide in proteins, respectively. The peaks at 1353 and 1214 cm−1 may be assigned to the –N
O bending and inplane (–C–H) bending, respectively. The absorption band at 1063 cm−1 is attributed to the –C–N stretching vibration of aliphatic amines. The characteristic peak at 763 cm−1 is ascribed to the –C–C–C– deformations of the phenyl ring. The strong absorption peak at 549 cm−1 is assigned to the Fe–O stretching of the iron nanoparticles. A similar result was reported in earlier literature.20 The appearance of absorption bands at 3430, 2282, 1638, 1353, 1214 and 1063 cm−1 indicate that the synthesized iron nanoparticles may be surrounded by polyphenols and proteins. These findings reveal that biomolecules like polyphenols and proteins present in the castor leaf extract were identified as being responsible for the reduction of the Fe3+ ions and stabilization of the iron nanoparticles, as reported by Mohanraj et al.16 and Luo et al.18
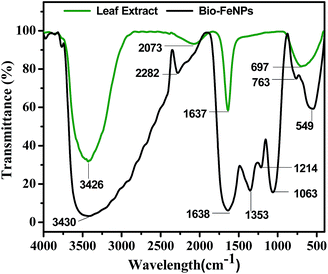 |
| Fig. 1 FTIR spectra of castor leaf extract and phytosynthesized iron nanoparticles. | |
3.3. XRD analysis of iron nanoparticles
Fig. 2 shows the XRD pattern of the phytosynthesized iron nanoparticles. The XRD pattern shows a dominant peak at 2θ = 44.27° which corresponds to the index (110) plane of a face-centred cubic lattice. The results indicate that the formed iron nanoparticles were predominantly crystalline in nature and in the zerovalent state (Fe0). The data obtained from the XRD analysis was in accordance with the file no. 85-1410 of the Joint Committee on Powder Diffraction Standards (JCPDS). A similar result was reported by Lee et al.21
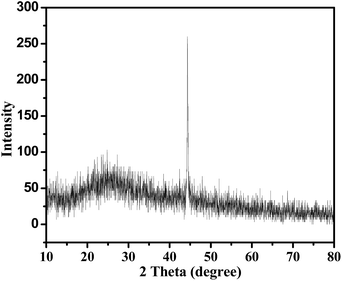 |
| Fig. 2 XRD pattern of the iron nanoparticles. | |
3.4. XPS analysis of iron nanoparticles
The overview XPS spectrum of the phytosynthesized iron nanoparticles is given in Fig. 3a. The XPS results clearly show that the photoelectron peaks at 710.31, 530.21, 399.01 and 284.6 eV represent the binding energies of iron, oxygen, nitrogen and carbon, respectively. The XPS spectrum for the narrow scan of the iron 2p-electrons of the iron nanoparticles is shown in Fig. 3b. In the XPS spectrum of the iron 2p-electrons, the two distinct states of the iron atoms for Fe 2p3/2 and Fe 2p1/2 are observed at the binding energies of 710.7 and 724.9 eV, respectively. The results of the study demonstrate that the presence of iron oxide is evident on the surface of the synthesized nanoparticles. A similar result was obtained by Yamashita and Hayes22 for the fractured surface of a Fe2O3 standard sample. The formation of iron oxide on the surface of the iron nanoparticles may be due to the presence of biomolecules. A similar observation was suggested for the formation of silver oxide nanoparticles.23 The other possibility of forming iron oxide may be due to the surface oxidation of the iron core shell nanoparticles through the Fe0–Fe(OH)2–Fe3O4–(Fe2O3) process, as predicted by Kumar et al.24 However, further studies are required to predict the precise mechanism in the phytosynthesis of iron oxide nanoparticles. The presence of carbon indicated that the biomolecules acted as a capping agent for the iron nanoparticles. The obtained results agreed well with the FTIR and EDX results.
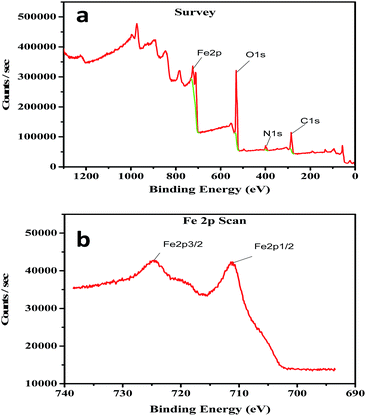 |
| Fig. 3 XPS spectra of the iron nanoparticles (a) overview XPS spectrum of the phytosynthesized iron nanoparticles. (b) XPS spectrum of the iron 2p-electrons of the iron nanoparticles. | |
3.5. SEM-EDX and TEM analysis of iron nanoparticles
The SEM images of the formed iron nanoparticles by castor leaf extract are shown in Fig. 4a and b. The iron nanoparticles were varied in shape and size due to agglomeration. The reason for the agglomeration of the iron nanoparticles may be due to the presence of biomolecules, as reported by Markova et al.25 EDX analysis was carried out to find out the elemental composition of the formed iron nanoparticles (Fig. 4c). The EDX spectrum of the iron nanoparticles at 6.398, 0.525 and 0.277 keV showed they were primarily composed of iron, oxygen and carbon atoms, respectively. The presence of carbon and oxygen may possibly arise from the biomolecules of the castor leaf extract which act as capping agents. Similar observations were also made by Wang et al.26 for the synthesis of iron nanoparticles using eucalyptus leaf extracts. The presence of chlorine may be from the precursor of FeCl3. The silica in the EDX spectrum may occur from the Si(Li) detector or from the castor leaf extract, as reported by Wang et al.27 This result is in good agreement with the XRD, XPS and FTIR results. The TEM image of the biosynthesised iron nanoparticles is shown in Fig. 5a–c and ESI Fig. S2.† The micrograph clearly indicates that the synthesized iron nanoparticles are irregular shapes and agglomerate, with the size range of 10 to 35 nm. Agglomeration may be due to the biomolecules present on the surface of the iron nanoparticles. A similar result was reported by Sangeetha et al.28 The average size of the iron nanoparticles was measured using Image J software and found to be 28 nm (Fig. 5d).
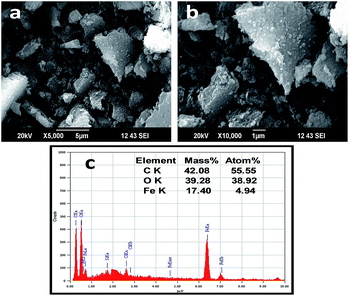 |
| Fig. 4 SEM images of the phytosynthesized iron nanoparticles at different magnifications and the EDX analysis: (a) 5000×, (b) 10 000× and (c) EDX spectrum. | |
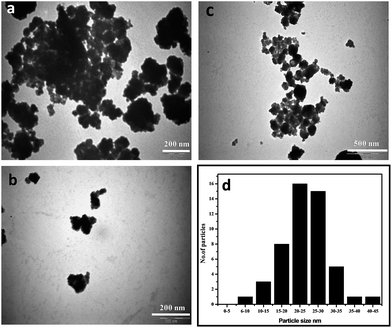 |
| Fig. 5 TEM images of the phytosynthesized iron nanoparticles at different scales and the size distribution: (a) & (b) 200 nm, (c) 500 nm and (d) particle size distribution. | |
3.6. Process optimization of transesterification reaction
3.6.1 Effect of temperature on castor biodiesel yield. In order to find the effect of temperature on biodiesel yield, the reaction was conducted at 45, 50, 55, 60 and 65 °C. The reaction temperature at above the boiling point of methanol was not considered, so as to minimize the loss of methanol. Each reaction was carried out under the following operating conditions including a 1
:
9 molar ratio of oil to methanol, 1 wt% of the Bio-FeNPs catalyst (relative to castor oil), 400 rpm stirring speed and duration of 150 min. The effect of the reaction temperature on the biodiesel yield is shown in Fig. 6a. It was observed that the conversion of castor oil into biodiesel was found to be increased with varying temperature from 45 to 65 °C. At 45 °C, only 30.6% of the biodiesel yield was obtained. Similarly, the yield of biodiesel at 50, 55 and 60 °C was about 51.4, 62.1 and 70.6%, respectively. At the reaction temperature of 65 °C, the yield of biodiesel was 85.2%. The results indicated that the increasing yield may be due to the increase in the rate of reaction. Based on the above results, the reaction temperature at 65 °C was chosen as the optimum temperature for the transesterification of castor oil. A similar trend was noticed by Dias et al.,6 for castor biodiesel using KOH as a catalyst by varying the temperature from 55 to 65 °C.
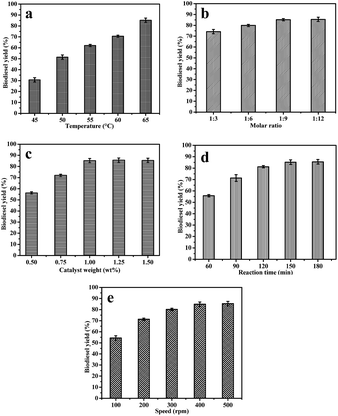 |
| Fig. 6 Optimization of castor biodiesel: effect of (a) temperature, (b) molar ratio, (c) catalyst load, (d) reaction time and (e) rate of stirring. | |
3.6.2 Effect of castor oil–methanol molar ratio on biodiesel yield. The effect of the castor oil–methanol ratio on the biodiesel yield was investigated at different molar ratios of 1
:
3, 1
:
6, 1
:
9 and 1
:
12. Each reaction was carried out with 1 wt% of the Bio-FeNPs catalyst at 65 °C and a stirring speed of 400 rpm for 150 min. The experimental results are given in Fig. 6b. It was noticed that the biodiesel yield increased on varying the castor oil to methanol ratio from 1
:
3 to 1
:
9 and there was no enhancement at 1
:
12. The yields of biodiesel at the molar ratios of 1
:
3, 1
:
6, 1
:
9 and 1
:
12 were 74.2, 79.9, 85.2 and 85.5%, respectively. Based on the results, the optimum molar ratio of castor oil to methanol for the transesterification reaction was considered to be 1
:
9. Further increasing the amount of methanol may induce the formation of methoxide (with the –OH group of ricinoleic acid) which affects the quality of biodiesel, as reported by Serra et al.29 Also, Encinar et al.,30 obtained similar results for castor biodiesel using a KOH catalyst.
3.6.3 Effect of iron nanocatalyst on castor biodiesel yield. In order to investigate the efficiency of the iron nanocatalyst, the reaction was conducted by varying the catalyst amount to 0.5, 0.75, 1.0, 1.25 and 1.50 wt% with respect to the castor oil weight. The castor oil to methanol molar ratio was 1
:
9, and a stirring speed of 400 rpm at 65 °C for 150 min was maintained. The obtained results are illustrated in Fig. 6c. The biodiesel yield from 56.2 to 85.2% was varied on changing the amount of the iron nanocatalyst from 0.5 to 1.0 wt%. There was no significant improvement in the biodiesel yield with above 1 wt% catalyst loading. From these results, 1 wt% of the Bio-FeNPs catalyst load was considered as the optimum concentration for the maximum production of castor biodiesel. Similarly, Encinar et al.,30 investigated the effect of a KOH catalyst on biodiesel conversion by varying the catalyst amount from 0.3 to 1 wt% and the highest yield was observed at 1 wt% catalyst loading. In the present study, the effect of the spent iron nanocatalysts on the production of castor biodiesel was also analyzed by recycling the catalysts three times. At the end of each cycle, the same catalyst was separated using a centrifuge and washed with methanol for further use. The yields of biodiesel obtained from the spent catalyst in the first, second and third recycles were 84.3, 83.5 and 81.8%, respectively. The obtained yields are comparable with the yield of the fresh catalyst (85.2%). Based on the results, it was concluded that the synthesized nanoparticles were considered as an efficient catalyst.
3.6.4 Effect of reaction time on castor biodiesel yield. The reaction time was varied as 60, 90, 120, 150 and 180 min at 65 °C and 400 rpm to determine the optimum reaction time for biodiesel production. The effect of the reaction time on biodiesel yield is shown in Fig. 6d. It was demonstrated that, more than 50% yield was obtained at the reaction time of 60 min. Moreover, the yield of biodiesel was gradually increased with varying of the reaction time from 60 to 150 min. Further increase in the reaction time did not show any significant changes in the biodiesel yield. The highest yield of biodiesel was 85.2% at 150 min. The results of the study conclude that, the optimum reaction time for the production of castor biodiesel was 150 min. According to the literature, Meneghetti et al.31 found that the highest yields for CH3O−K+, CH3O−Na+ and H2SO4 catalysts were obtained at 60, 120 and 480 min, respectively.
3.6.5 Effect of stirring rate on castor biodiesel yield. In order to find out the optimum stirring rate for biodiesel production, the stirring speed was varied as 100, 200, 300, 400 and 500 rpm at 65 °C. The optimum values for castor oil to methanol molar ratio (1
:
9), catalyst load (1 wt%) and reaction time (150 min) were also maintained. An incomplete transesterification reaction was noticed at 100 rpm and only 50–60% yield of biodiesel was obtained. The low stirring speed affected biodiesel formation. The increase in mixing intensity resulted in high conversion, as shown in Fig. 6e. The yield of biodiesel was increased by changing the stirring rate from 100 to 400 rpm. There were no significant improvements in the biodiesel yield when the stirring rate was varied from 400 to 500 rpm. The highest yield of biodiesel at 400 rpm was 85.2%. It was concluded that, the optimum stirring rate for the production of castor biodiesel was 400 rpm.
3.7. FTIR and GC-MS analysis of biodiesel
According to our previous report,32 the observed absorption peaks for castor oil were 3397, 1573, 1400 and 1126 cm−1. The FTIR spectrum of castor oil biodiesel is shown in Fig. 7a. In the FTIR spectrum of the produced biodiesel, the absorption bands appeared at 3396, 2928, 2858, 1737, 1570, 1403, 1173 and 721 cm−1. The peak at 3396 cm−1 is attributed to the –OH group present in ricinoleic acid of the castor oil. The sharp peaks at 2858 and 2928 cm−1 may be attributed to the –C–H stretching of the produced biodiesel. The characteristic peak at 1737 cm−1 is ascribed to the existence of the –C
O stretching of the ester group. The –C–C– stretching of the biodiesel was noticed by the characteristic peaks at 1570 and 1403 cm−1. The presence of the ester group (–C–O–) at 1173 cm−1 confirms the formation of biodiesel. A similar result was also observed by Siatis et al.,33 for the transesterification of palm oil. The characteristic absorption band at 721 cm−1 is assigned to the –CH2– rocking of FAMEs. Further, GC-MS was used to confirm the various fatty acid methyl esters present in the produced biodiesel (Fig. 7b). The obtained results of various FAMEs present in castor biodiesel are presented in Table 1. The GC-MS results confirmed the presence of ricinoleic acid methyl ester (9-octadecnoic acid, 12-hydroxy-methyl ester), linoleic acid methyl ester and oleic acid methyl ester in the castor biodiesel. The distributions of the saturated, monounsaturated and polyunsaturated FAMEs of castor biodiesel were 4.11, 89.63 and 6.26% respectively. Further, it was observed that, methoxide formation with the –OH group of ricinoleic acid did not occur during transesterification. Hence, the quality of the produced biodiesel was not affected.
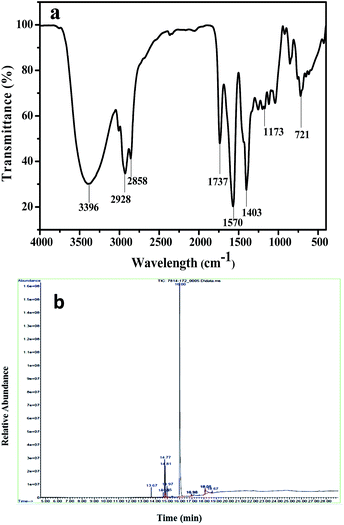 |
| Fig. 7 (a) FTIR spectrum of the produced biodiesel and (b) GC-MS analysis of the resultant biodiesel. | |
Table 1 GC-MS results for the fatty acid methyl ester composition of castor biodiesel
Fatty acid |
FAMEa |
Formula |
Structure |
Composition of biodiesel (%) |
Transesterification reaction at 65 °C for a period of 150 min at 400 rpm. |
Palmitic |
Hexadecanoic methyl ester |
C16H32O2 |
16:0 |
1.59 |
Stearic |
Methyl stearate |
C18H36O2 |
18:0 |
1.62 |
Oleic |
cis-9-Octadecenoic methyl ester |
C18H34O2 |
18:1 |
4.74 |
Linoleic |
cis-9,12-Octadecenoic methyl ester |
C18H32O2 |
18:2 |
5.66 |
Ricinoleic |
9-Octadecnoic acid, 12-hydroxy methyl ester |
C18H33O2 |
18:1 (OH) |
76.3 |
Arachidic |
Eicosanoic acid, methyl ester |
C20H40O2 |
20:0 |
0.51 |
3.8. Reaction mechanism of the bionano-catalysed transesterification reaction
The proposed reaction for the transesterification of castor oil using the phytosynthesized iron nanocatalyst is shown in Scheme 1. The transesterification of castor oil with methanol was performed at 65 °C to obtain the fatty acid methyl esters (FAMEs) and glycerol. The phytosynthesized iron nanoparticles acted as a catalyst in the transesterification of castor oil for biodiesel production. From the reaction in Scheme 1, it was observed that, one mole of castor oil with three moles of methanol in a transesterification reaction produced three moles of FAMEs and one mole of glycerol. In general, the transesterification reaction is reversible in nature. In order to induce the reaction in the forward direction, excess methanol (castor oil–methanol ratio of 1
:
9) was used in the presence of the iron nanoparticles, as suggested by Murugesan et al.34
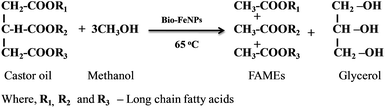 |
| Scheme 1 Transesterification of castor oil using the phytosynthesized iron nanocatalyst. | |
The proposed reaction mechanism for the production of biodiesel using the iron oxide nanocatalyst is presented in Scheme 2. In the first step, the proton was transferred from methanol to form a methoxide anion by means of the iron oxide nanocatalyst. In the second step, the carbonyl carbon present in the triglycerides of the castor oil was attracted by the methoxide anion for the formation of one mole of biodiesel and one mole of diglyceride through a methoxycarbonyl intermediate. The same procedure was followed in step 3 and step 4 for the production of biodiesel. In step 3, another mole of biodiesel was formed with monoglyceride. Finally, three moles of biodiesel, one mole of glycerol and the spent catalyst were obtained.
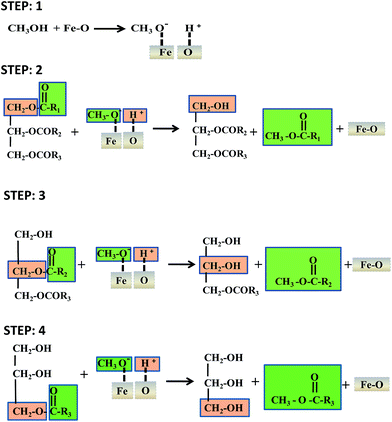 |
| Scheme 2 Reaction mechanism of the transesterification of castor oil using the iron nanocatalyst. | |
3.9. Physical and chemical properties of biodiesel
The important fuel properties of the resultant biodiesel are given in Table 2. The experimental results were compared with the ASTM D6751 standard. The physico-chemical properties of the produced biodiesel agreed well with the ASTM standard except for the specific gravity and kinematic viscosity. The specific gravity of the produced biodiesel from castor oil was 0.907 at 15 °C. Similarly, Encinar et al.,30 and Madankar et al.,35 reported 0.909 and 0.927 of specific gravity for the castor oil methyl ester at 40 °C, respectively. The kinematic viscosity of the resultant castor biodiesel was measured as 7.4 mm2 s−1 at 40 °C. The standard value for kinematic viscosity as per ASTM D6751 ranges from 1.9 to 6.0 mm2 s−1. According to the literature, Madankar et al.35 found that the viscosity of biodiesel was about 15.94 mm2 s−1. The high value of viscosity may be due to the incomplete transesterification reaction or impurities present in the biodiesel. This may lead to poor atomization and poor ignition, as reported by Murugesan et al.34 The –OH group present in ricinoleic acid of the castor oil may be responsible for the higher value of specific gravity and kinematic viscosity than the ASTM standard, as reported by Meneghetti et al.31 This can be easily rectified by suitable blending of biodiesel with petrodiesel or by adding suitable additives.36
Table 2 Fuel properties of the produced biodiesel and ASTM specifications
Physico-chemical parameters |
ASTM methods |
ASTM 6751 specification |
Properties of biodiesela |
Produced biodiesel from castor oil. Temperature at 15 °C. Value in mm2 s−1 at 40 °C. |
Specific gravityb |
D 4052 |
0.81–0.90 |
0.907 |
Kinematic viscosityc |
D 445 |
1.9–6.0 |
7.4 |
Flash point (°C) |
D 93 |
≥130 |
179 |
Cloud point (°C) |
D 97 |
−3 to 12 |
1.0 |
Water content (% vol) |
D 2709 |
≤0.05 |
0.015 |
Carbon residue (% mass) |
D 524 |
≤0.05 |
0.04 |
Refractive index |
— |
— |
1.469 |
Copper strip corrosion |
D 130 |
No. 3 max |
1b |
Calorific value (cal g−1) |
— |
— |
8477 |
The water content of castor methyl esters was found to be 0.015% which is below the specification limits. The low value water content of the resultant biodiesel favours the combustion performance and corrosion resistance of a diesel engine. The resultant biodiesel showed a value of 179 °C as its flash point. As per the ASTM D6751 standard, the minimum requirement of the flash point for biodiesel is 130 °C. It was suggested that the resultant biodiesel can be handled in a safe manner during transport and storage. The cloud point of the FAMEs was found to be 1 °C. This result indicates that the synthesized biodiesel has good flow properties and that it can also be used under cold weather conditions. The carbon residue of the formed biodiesel was reported as 0.04% which favours the low carbon deposition tendencies in a diesel engine. The copper strip corrosion of the biodiesel was identified as Class 1b (slightly tarnish). The results revealed that the biodiesel was superior in quality and it has good resistance to copper corrosion. The refractive index and calorific value of the castor biodiesel were 1.469 and 8477 cal g−1, respectively.
4. Conclusions
An economic, efficient and instant route for the green synthesis of iron nanoparticles was developed using castor leaf extract as a reducing agent as well as stabilizing agents. The TEM observations confirmed the nano-sized iron particles. The phytogenic nanocatalyzed transesterification of castor oil was successfully developed for the production of biodiesel. The phytosynthesized iron nanoparticles were believed to be an efficient catalyst in the transesterification of castor oil. The properties of the castor biodiesel were almost similar to conventional petrodiesel. Hence, the produced biodiesel can be considered as a substitute for petrodiesel. The results of the findings conclude that, the castor leaf extract can be used to synthesize other metal nanocatalysts and the iron nanoparticles obtained in this study can be used as a catalyst for the transesterification of other vegetable oils.
Notes and references
- M. Balat and H. Balat, Appl. Energy, 2010, 87, 1815–1835 CrossRef CAS
. - M. H. Ali, M. Mashud, M. R. Rubel and R. H. Ahmad, Procedia Eng., 2013, 56, 625–630 CrossRef CAS
. - Y. C. Sharma, B. Singh and J. Korstad, J. Agric. Food Chem., 2010, 58, 242–247 CrossRef PubMed
. - V. Mutreja, S. Singh, T. K. Minhas and A. Ali, RSC Adv., 2015, 5, 46890–46896 RSC
. - M. F. R. Nizah, Y. H. Taufiq-Yap, U. Rashid, S. H. Teo, Z. A. ShajaratunNur and A. Islam, Energy Convers. Manage., 2014, 88, 1257–1262 CrossRef
. - J. M. Dias, J. M. Araujo, J. F. Costa, M. C. M. Alvim-Ferraz and M. F. Almeida, Energy, 2013, 53, 58–66 CrossRef CAS
. - I. M. R. Fattah, M. A. Kalam, H. H. Masjuki and M. A. Wakil, RSC Adv., 2014, 4, 17787–17796 RSC
. - M. K. Lam, K. T. Lee and A. R. Mohamed, Biotechnol. Adv., 2010, 28, 500–518 CrossRef CAS PubMed
. - S. Hu, Y. Guan, Y. Wang and H. Han, Appl. Energy, 2011, 88, 2685–2690 CrossRef CAS
. - J. Xu, J. Sun, Y. Wang, J. Sheng, F. Wang and M. Sun, Molecules, 2014, 19, 11465–11486 CrossRef PubMed
. - W. Xie and N. Ma, Energy Fuels, 2009, 23, 1347–1353 CrossRef CAS
. - S. Iravani, Green Chem., 2011, 13, 2638–2650 RSC
. - A. K. Jha, K. Prasad and A. R. Kulkarnic, Colloids Surf., B, 2009, 71, 226–229 CrossRef CAS PubMed
. - E. C. Njagi, H. Huang, L. Stafford, H. Genuino, H. M. Galindo, J. B. Collins, G. E. Hoag and S. L. Suib, Langmuir, 2011, 27(1), 264–271 CrossRef CAS PubMed
. - V. Smuleac, R. Varma, S. Sikdar and D. Bhattacharyya, J. Membr. Sci., 2011, 379, 131–137 CrossRef CAS PubMed
. - S. Mohanraj, S. Kodhaiyolii, M. Rengasamy and V. Pugalenthi, Appl. Biochem. Biotechnol., 2014, 173(1), 318–331 CrossRef CAS PubMed
. - G. E. Hoag, J. B. Collins, J. L. Holcomb, J. R. Hoag, M. N. Nadagouda and R. S. Varma, J. Mater. Chem., 2009, 19, 8671–8677 RSC
. - F. Luo, Z. Chen, M. Megharaj and R. Naidu, RSC Adv., 2014, 4, 53467–53474 RSC
. - R. M. Cornell and U. Schwertmann, The iron oxides: Structure, Properties, Reactions, Occurrences and uses, Wiley-VCH, Weinheim, 2003, pp. 150–151 Search PubMed
. - B. Bhushan, A. Basumallick, N. Y. Vasanthacharya, S. Kumar and D. Das, Solid State Sci., 2010, 12, 1063–1069 CrossRef CAS
. - Y. C. Lee, C. W. Kim, J. Y. Lee, H. J. Shin and J. W. Yang, Desalin. Water Treat., 2009, 10, 33–38 CrossRef CAS
. - T. Yamashita and P. Hayes, Appl. Surf. Sci., 2008, 254, 2441–2449 CrossRef CAS
. - P. Ghorbani, M. Soltani, M. Homayouni-Tabrizi, F. Namvar, S. Azizi, R. Mohammad and A. B. Moghaddam, Molecules, 2015, 20, 12946–12958 CrossRef CAS PubMed
. - N. Kumar, M. Auffan, J. Gattacceca, J. Rose, L. Olivi, D. Borschneck, P. Kvapil, M. Jublot, D. Kaifas, L. Malleret, P. Doumenq and J. Y. Bottero, Environ. Sci. Technol., 2014, 48, 13888–13894 CrossRef CAS PubMed
. - Z. Markova, P. Novak, J. Kaslik, P. Plachtova, M. Brazdova, D. Jancula, K. M. Siskova, L. Machala, B. Marsalek, R. Zboril and R. Varma, ACS Sustainable Chem. Eng., 2014, 2, 1674–1680 CrossRef CAS
. - T. Wang, J. Lin, Z. Chen, M. Megharaj and R. Naidu, J. Cleaner Prod., 2014, 83, 413–419 CrossRef CAS
. - Y. Wang, X. He, K. Wang, X. Zhang and W. Tan, Colloids Surf., B, 2009, 73, 75–79 CrossRef CAS PubMed
. - G. Sangeetha, S. Rajeshwari and R. Venckatesh, Mater. Res. Bull., 2011, 46, 2560–2566 CrossRef CAS
. - T. M. Serra, D. R. de Mendonca, J. P. V. da Silva, M. R. Meneghetti and S. M. Plentz Meneghetti, Fuel, 2011, 90, 2203–2206 CrossRef CAS
. - J. M. Encinar, J. F. Gonzalez and A. Pardal, Fuel Process. Technol., 2012, 103, 9–15 CrossRef CAS
. - S. M. P. Meneghetti, M. R. Meneghetti, C. R. Wolf, E. C. Silva, G. E. S. Lima, L. L. Silva, T. M. Serra, F. Cauduro and L. G. Oliveira, Energy Fuels, 2006, 20, 2262–2265 CrossRef
. - M. Rengasamy, S. Mohanraj, S. Harshavardhan, R. Balaji and V. Pugalenthi, J. Chem. Pharm. Sci., 2014, 2, 108–112 Search PubMed
. - N. G. Siatis, A. C. Kimbaris, C. S. Pappas, P. A. Tarantilis and M. G. Polissiou, J. Am. Oil Chem. Soc., 2006, 83(1), 53–57 CrossRef CAS
. - A. Murugesan, C. Umarani, T. R. Chinnusamy, M. Krishnan, R. Subramanian and N. Neduzchezhain, Renewable Sustainable Energy Rev., 2009, 13, 825–834 CrossRef CAS
. - C. S. Madankar, S. Pradhan and S. S. Naik, Ind. Crops Prod., 2013, 43, 283–290 CrossRef CAS
. - T. P. Thomas, D. M. Birney and D. L. Auld, Ind. Crops Prod., 2012, 36, 267–270 CrossRef
.
Footnote |
† Electronic supplementary information (ESI) available. See DOI: 10.1039/c5ra15186d |
|
This journal is © The Royal Society of Chemistry 2016 |
Click here to see how this site uses Cookies. View our privacy policy here.