Hydrothermal synthesis of a layered-type W–Ti–O mixed metal oxide and its solid acid activity†
Received
18th October 2016
, Accepted 29th November 2016
First published on 29th November 2016
Abstract
A layered-type W–Ti–O mixed oxide was synthesized by hydrothermal synthesis from an aqueous solution of ammonium metatungstate and titanium sulfate. To avoid the formation of titania, oxalic acid was used as a reductant. Optimized synthesis led to rod-like particles comprised of MO6 (M = W, Ti) octahedra connected in a corner-sharing fashion in the c-direction and in the form of micropore-containing {W6O21} units in the a–b plane. The surface area, acidity and acid catalytic activity (alkylation) increased with the amount of the layered-type W–Ti–O phase. Strong Brønsted acid sites formed due to the thermal release of ammonia from the uncalcined precursor. Calcination at 400 °C led to the highest acidity and alkylation activity. Alkylation of benzyl alcohol and toluene led to heavy product formation due to over-alkylation of the product. The selectivity to the mono-alkylated product was improved by the addition of water, which competes with the selectively formed products for adsorption on the acid sites. FT-IR measurements showed that the layered-type W–Ti–O possesses Brønsted acid sites and at least two different Lewis acid sites. The stronger Lewis acid sites can be converted into Brønsted acid sites in the presence of water, and the weaker Lewis acid sites functioned in the presence of water. This water tolerance of Lewis acid sites is an important characteristic of layered-type W–Ti–O, as it allows the bifunctional catalyst to convert 1,3-DHA into lactic acid in water.
Introduction
Mixed metal oxides of transition metals are important inorganic materials which amongst others can serve as catalysts and ceramics. The demand for solid acid catalysts is expected to increase because such catalysts are reusable and can be readily separated from the reaction mixture. Many inorganic oxides including zeolites and metal oxides, which have Lewis acid sites, have been found to be nearly inactive for reactions in water because of the strong coordination of water to Lewis acid sites.1 Therefore, the development of a Lewis acid catalyst that exhibits excellent catalytic activity and selectivity for various organic reactions in the presence of water is desirable.2
An area in which solid acid catalysts operating in water are required is biomass conversion, involving reactions such as the formation of 5-hydroxymethylfurfural from hexoses and lactic acid from trioses. Furfural derivatives are raw materials for polymers. Accordingly, the conversion from sugars to furfural, which is the main component of woody biomass, has been targeted in an effort to make the transition to a sustainable economy.3 Lactic acid is also a bio-based commodity chemical with many applications, including the rapidly expanding use of polylactate as a bio-plastic.4 Lactic acid can be synthesized from glyceraldehyde or 1,3-dihydroxyacetone (DHA) over acid catalysts.5–7 These molecules are readily produced by the oxidation of glycerol, the main by-product in biodiesel production. Therefore, an efficient catalytic system that converts GLA and DHA into lactic acid would be promising for lactic acid production.8
One of the typical solid acid catalysts is niobium oxide, which has Lewis acidity and Brønsted acidity. Niobium oxide (or hydrated niobium oxide) has been used as a water-tolerant solid acid catalyst.1,9–12 Titania is also known for its combined Lewis and Brønsted acid properties. Kasuga et al. reported that nanotube-type titania can be easily obtained by heating titania in a concentrated aqueous alkali solution.13 Titania nanotubes have been shown to function as acid catalysts. The structural distortion of the nanotube structure is thought to give rise to solid acidity, a feature which is absent in the nanosheet structure.14,15 The presence of acid sites was confirmed by 31P MAS NMR and COads IR measurements, demonstrating the enhanced Brønsted acidity of the bridging Ti–OH–Ti groups in the nanotube structure. These catalysts showed already good performance in the Friedel–Crafts alkylation reactions with toluene and benzyl chloride at room temperature.
We have studied the relationship between the crystalline structure of W-based oxide mixed metal oxides (W–M–O (M = Nb, Ta, V)) and their catalytic activity.16–22 These catalysts were found to function as solid acids, and the acidic and structural properties have been discussed from the viewpoint of crystalline metal oxide structures. Tungsten oxides are a class of solid acids that form tungsten bronze based on W-centered oxygen octahedra.23 The formation of mixed oxides between Ti and W or the substitution of W in WO3 by Ti will enhance the acidity and catalytic performance,24 as strong Brønsted acid sites, attributed to bridging hydroxyl groups M–(OH)–M′ (M = Ti, Nb or Ta, M′ = W or Mo) in previous studies25–27 and W–(OH)–Ti in this study, will appear in such materials.
We report herein the synthesis of a W–Ti–O mixed oxide by a hydrothermal process from ammonium metatungstate and titanium(III) sulfate precursors. The W–Ti–O mixed oxide is synthesized by the assembly of MO6 (M = W, Ti) units, which gives rise to octahedra-based layered materials. This layered mixed W–Ti–O contains Brønsted acid and Lewis acid sites at its surface. The promise of the W–Ti–O as a Lewis acid catalyst is demonstrated in a water-mediated reaction.
Experimental
Preparation of W–Ti–O samples
W–Ti–O oxides were synthesized by a hydrothermal method from ammonium metatungstate (AMT, (NH4)6H2W12O40·nH2O, Nippon Inorganic Colour & Chemical) and titanium sulfate (Ti2(SO4)3·nH2O, Mitsuwa Chemical) precursors. Typically, Ti2(SO4)3·nH2O (1.27 mmol based on Ti) was added to 25 mL of water and stirred for about 20 min until it was dissolved. AMT (5 mmol W) was dissolved in 20 mL of deionized water, and then the W precursor solution was added to the Ti-containing solution. Oxalic acid (5 mmol, Wako) was added to the solution, and the mixture was stirred for 5 min. Then, the solution was sealed in a 60 mL Teflon liner stainless-steel autoclave. Hydrothermal reaction was carried out at 175 °C for 24 hours. The obtained solid was filtered, washed thoroughly with deionized water, and dried at 80 °C overnight and then calcined at 400 °C for 2 h.
Catalytic activity measurements
A 50 mL round-bottom three-neck flask equipped with a reflux condenser was used as a stirred bed reactor to evaluate the catalytic performance of the solids. For alkylation, a mixture of benzyl alcohol (10 mmol), anisole or toluene (100 mmol), and an internal standard (decane, 5 mmol) was added to the reactor and the reaction temperature was adjusted to 100 °C. Then, 0.2 g of the catalyst and a Teflon-coated magnetic stir bar were loaded into the reactor. Aliquots (each 0.1 mL) were collected at regular intervals. The concentrations of the reactant and product were measured by gas chromatography using a flame ionization detector (GC-FID, GL science GC390B) with a ZB-1 column. To study hydrolysis, 5 wt% of an ethyl acetate aqueous solution (30 g, 17 mmol ethyl acetate) or 1 wt% o-toryl acetate aqueous solution (60 g, 4.03 mmol methyl phenyl acetate) with acetonitrile as an internal standard was introduced into the reactor. The reaction temperature was 60 °C and 0.8 g of the catalyst was used. The concentrations of the reactant and product were measured by GC-FID with a TC-WAX column. For pyruvaldehyde and 1,3-DHA transformations, an aqueous solution (2 mL) of the substrate (100 mM) and 0.1 g of the catalyst were used at 120 °C for 6 h by using a glass-type pressure tight vial (3 mL). The catalyst was removed after the reaction, and the solution was diluted with aqueous H2SO4. The concentrations of the reactant and product were measured by HPLC (JASCO, LC-2000 plus) equipped with an Aminex HPX-87 H column (diameter: 300 mm × 7.8 mm, eluent: 0.005 M H2SO4 0.5 mL min−1, temperature: 35 °C), with refractive index (RI) and photodiode array (PDA) detectors.
Characterization
The catalysts were characterized by the following techniques. Powder XRD patterns were measured with a diffractometer (RINT Ultima+, Rigaku) using Cu-Kα radiation (tube voltage: 40 kV, tube current: 20 mA). Diffractions were recorded in the range of 4–60° with 5° min−1. The morphology was investigated by using a transmission electron microscope (JEM-2100F, JEOL) at 200 kV. The samples were dispersed in ethanol by an ultrasonic treatment for several minutes, and drops of the suspension were placed on a copper grid for TEM observations. Raman spectra were obtained using a spectrometer (inVia Reflex, Renishaw, with a spectral resolution of 2 cm−1) under the conditions of a wavelength of 532 nm and collection time of 10 s. N2 adsorption isotherms at liquid N2 temperature were measured by using an automatic physisorption apparatus (BELSORP MAX, BEL JAPAN) for the samples. Prior to N2 adsorption, the catalysts were evacuated under vacuum at 300 °C for 2 h. The external surface area was calculated by the Brunauer–Emmett–Teller (BET) method. Temperature-programmed desorption (TPD) of ammonia (NH3-TPD) was used to determine the acidity. These measurements were done in an automated chemisorption apparatus (BEL JAPAN). The experimental procedure was as follows. The catalyst (ca. 50 mg) was placed between two layers of quartz wool in a quartz reactor and pre-heated in a helium flow (50 mL min−1) at 400 °C for 1 h. Then, ammonia was introduced at 100 °C for 30 min. The desorption profile from 100 to 700 °C was recorded with a mass spectrometer in a helium flow (50 mL min−1). Temperature-programmed decomposition mass spectrometry (TPD-MS) measurements were performed from 40 to 700 °C at a heating rate of 10 °C min−1 in a helium flow (50 mL min−1). The decomposed gas molecules were monitored by a mass spectrometer (ANELVA, Quadrupole Mass Spectrometer, M-100QA, BEL Japan), collecting several mass fragments: CO2 (44), O2 (32), CO and N2 (28), H2O (18, 17, 16) and NH3 (17, 16, 15). The acidity of the catalysts was measured by FT-IR spectroscopy (JASCO) of adsorbed pyridine or CO using a furnace cell with CaF2 windows containing a self-supporting disk of a sample. The samples were pretreated in a vacuum at 350 °C. Pyridine was adsorbed onto the samples at 100 °C, and the adsorption spectrum was recorded after evacuation at 250 °C for 1 h. The spectrum of the adsorbed pyridine on the sample in the presence of water vapor (4.6 Torr) was also recorded. CO was adsorbed at −183 °C and the adsorption spectrum was recorded with degassing.
Results and discussion
Synthesis of octahedra-layered W–Ti–O mixed metal oxide
In order to discuss the relationship between the crystalline structure of the W–Ti–O catalyst and its catalytic activity, various types of W–Ti–O mixed metal oxides and WO3 were prepared. The synthesis conditions were optimized in an attempt to obtain as pure as possible samples of a single phase. Fig. 1 shows the XRD patterns of the most important W–Ti–O samples obtained in this study (further XRD patterns are shown in the ESI† (Fig. S1–S4)). The W/Ti ratio in the precursor solution was first investigated (Fig. S1†). The XRD pattern of W–Ti–O mixed oxides showed weak diffraction peaks at 2θ = 23° and 47°, when the atomic W/Ti ratio was between 3/2.84 and 3/1.42 (Fig. S1a–c†). Pure hexagonal WO3 was obtained when there was no Ti in the precursor solution (Fig. S1f†). When Ti was added to the synthesis solution (W/Ti = 3/0.5), hexagonal W–Ti–O mixed oxides were obtained without the formation of anatase TiO2 (Fig. S1e†). When the W/Ti ratio was lower than 3/1.42, anatase TiO2 was formed (Fig. S1c†) and the intensity of the diffraction peaks of the hexagonal phase decreased and broadened. The diffraction peaks at 2θ = 23° and 47° observed in W–Ti–O mixed oxides when the atomic W/Ti ratio was between 3/1.42 and 3/2.84 were different from the peak derived from the (001) crystal plane of hexagonal WO3 (d001 = 3.898 Å) and hexagonal W–Ti–O mixed oxide (d001 = 3.896 Å). The d-spacing corresponding to this value of the new phase W–Ti–O mixed oxides was 3.940 Å, indicative of a new layered-type W–Ti–O mixed oxide based on MO6 (M = W, Ti) octahedra connected in the c-axis direction. This conclusion is based on our earlier report on a similar W-based mixed oxide having a layered-type structure based on MO6 octahedra and pentagonal bipyramidal {M6O21} (M = W or Nb) units.19–22,28
 |
| Fig. 1 XRD patterns of W–Ti–O samples: (a) W/Ti = 5/1.27 mmol (5 mmol oxalic acid), (b) W/Ti = 3/0.711 mmol (5 mmol oxalic acid), (c) W/Ti = 3/0.5 mmol, (d) W/Ti = 3/0 mmol in 45 mL of precursor solution. | |
The oxidation state of Ti in the precursor (Ti2(SO4)3·nH2O) is 3+, which changed to 4+ during the mixed oxide formation as confirmed by XPS analysis. The TiIII species acted as a reductant for the formation of the pentagonal bipyramidal {W6O21} units, which are essential in the formation of the layered-type structure. Hexagonal WO3 consists of WO6 octahedra. The presence of a reductant is essential for the formation of the pentagonal bipyramidal {W6O21} units. Accordingly, the presence of a reductant will suppress the formation of the hexagonal structure of tungsten oxide. The formation of pentagonal bipyramidal {W6O21} units was confirmed by Raman spectroscopy. Fig. S5† shows the Raman spectra of the layered-type W–Ti–O and hexagonal WO3 samples. For hexagonal WO3, Raman bands at 642 cm−1, 688 cm−1, and 817 cm−1 are assigned to the symmetric stretching modes of the W–O–W linkage.29 The Raman band at 781 cm−1 of the layered-type W–Ti–O is assigned to the symmetric stretching mode of the polyhedra, supporting the formation of pentagonal bipyramidal {W6O21} units.
Although the formation of the hexagonal tungsten oxide phase was increased by the addition of more TiIII precursor, it led to the formation of anatase titania when there was too much Ti in the precursor solution. In an attempt to avoid the formation of titania, we added oxalic acid as an additional reducing agent (Fig. S2 and S3†). This greatly suppressed the formation of the crystalline hexagonal structure already by the addition of 5 mmol of oxalic acid (Fig. 1b). TiIV can form a four-coordinate structure with a carboxyl group. The Ti precursor composed of TiIV coordinated with four oxalic acid molecules accelerates the self-assembly of the mixed oxide based on octahedra under hydrothermal conditions. Fig. S4† shows the influence of the concentration of the precursor solution on the phases obtained. The W–Ti–O samples obtained with the higher precursor concentration (W/Ti ratio between 4/0.925 and 15/3.56) showed intense and sharp peaks at 2θ = 23° and 47°, evidencing the formation of the layered W–Ti–O without formation of hexagonal WO3 and titania. The higher precursor concentration increases the rate of nucleation during hydrothermal synthesis and improves phase purity by avoiding the formation of other hexagonal (WO3) and anatase (TiO2) phases.
A representative TEM image of the layered-type W–Ti–O mixed oxide is shown in Fig. S6.† The layered-type W–Ti–O mixed oxide appeared as rod-like crystals with a diameter of 5–10 nm and lengths of 30–50 nm.
By varying the concentrations in the precursor, we were able to obtain a phase-pure layered-type structure based on octahedra MO6 (M = W, Ti), showing two diffraction peaks at 2θ = 23 and 47°, without the formation of hexagonal WO3 and titania (Fig. 1). The crystalline motif of the layered-type W–Ti–O in the a–b plane is due to the interconnection of MO6 (M = W, Ti) octahedra and {M6O21} (M = W) pentagonal units. However, the atomic ordering in the a–b plane is not sufficient to give rise to strong diffraction peaks of the sample, which is in line with the nanosized morphology of the rod-shaped particle visible by TEM.
Characterization of the W–Ti–O sample
We then proceeded to characterize the optimal phase-pure layered-type W–Ti–O sample, which was prepared at an atomic W/Ti ratio of 5/1.27 in the presence of oxalic acid. Fig. S7† shows the nitrogen adsorption–desorption isotherm and the corresponding Barrett–Joyner–Halenda (BJH) plot of the layered-type W–Ti–O mixed oxide. The adsorption isotherms displayed type IV hysteresis, suggesting the presence of mesopores. The BET surface area was 107 m2 g−1. The TEM image suggests that the layered-type W–Ti–O mixed oxide sample seemed to be composed of the aggregates of nanosized crystal particles, and the mesopores are formed by the intraparticle voids. The insert highlights the adsorption at low pressure. Uptake starts at P/P0 = 10−7, showing that the layered-type W–Ti–O sample has micropores.12,30 Thus, by combining results of physisorption, XRD, Raman spectra and TEM, we demonstrate that the layered-type W–Ti–O sample contains nanosized rod-like crystals comprised of a crystalline motif of W–Ti–O in the a–b plane made up of interconnected units of MO6 (M = W, Ti) octahedra and {W6O21} pentagonal units that hold micropore channels (Fig. S8†).
In order to understand the solid acid properties of the layered W–Ti–O sample, we determined the influence of the calcination temperature on the amount of ammonia released during NH3-TPD. The calcined samples were also evaluated in alkylation reactions that require Brønsted acid sites. The results of these experiments are shown in Fig. 2. The highest activity for the alkylation of benzyl alcohol and anisole to benzylanisole was observed for the sample calcined at 400 °C. At lower calcination temperature (300 °C), ammonium cations remained in the sample originating from the precursor. This leads to a higher than expected ammonia release during NH3-TPD. This is supported by the TPD patterns of the uncalcined layered W–Ti–O sample and the sample after calcination at 400 °C shown in Fig. S9.† The desorption peak of the ammonia derived from the ammonium cation precursor was at around 390 °C for the uncalcined sample. We argue that the Brønsted acid sites are formed due to desorption of ammonia from the layered W–Ti–O sample. From the TPD of the sample calcined at 400 °C, which shows no further release of ammonia, we infer that all ammonium cations have decomposed. Thus, the increase in alkylation activity from calcination at 300 °C to 400 °C is due to ammonia release, generating Brønsted acid sites. A possible reason for the decreasing catalytic activity observed for calcination temperatures higher than 400 °C is the phase transition of tungsten oxide to monoclinic WO3. This is clear from the XRD patterns shown in the ESI.† Therefore, the layered W–Ti–O sample was calcined at 400 °C for 2 h.
 |
| Fig. 2 Relationships of calcination temperature of the layered-type W–Ti–O catalyst with alkylation activity (cat., 0.1 g; reaction time, 1 h; anisole, 100 mmol; benzyl alcohol, 10 mmol) and the amount of NH3 desorbed by NH3-TPD. | |
We also compared the performance of the layered W–Ti–O sample to that of hexagonal W–Ti–O and hexagonal WO3. The hexagonal W–Ti–O mixed oxide sample was obtained by using W/Ti = 3/0.5 without oxalic acid. Table 1 shows the results of alkylation reactions of anisole (or toluene) and benzyl alcohol. The alkylation activity of the layered-type W–Ti–O sample was much higher for both alkylation reactions than that of the hexagonal W–Ti–O sample. Fig. S11† shows the IR spectrum of pyridine adsorbed at 100 °C followed by evacuation at 250 °C for 1 h. Clearly, the layered W–Ti–O sample contains Brønsted and Lewis acid sites, whereas these sites are not observed in the hexagonal W–Ti–O sample. These results indicate that the amount of acid sites for hexagonal W–Ti–O was much smaller than that for the layered W–Ti–O sample. Hexagonal WO3 was the least active among the three tested samples.
Table 1 Physical properties of catalysts and results of alkylation
Catalyst |
Crystalline phase |
d(001) |
BET surface area/m2 g−1 |
NH3 desorbed amount/mmol g−1 |
Alkylation of anisolea |
Alkylation of tolueneb |
Conv.c/% |
Yield4/% |
Conv.c/% |
Yieldd/% |
Reaction conditions: benzyl alcohol (10 mmol), anisole (100 mmol), catalyst (0.2 g), 100 °C, 10 min.
Reaction conditions: toluene (10 mmol), anisole (100 mmol), catalyst (0.2 g), 100 °C, 20 min toluene.
Conversion of benzyl alcohol.
Yield of benzyl anisole or benzyl toluene. Parentheses show the yield of dibenzyl ether.
|
W–Ti–O |
Layered-type |
3.940 |
107 |
0.451 |
48 |
43 (5) |
78 |
32 (46) |
h-W–Ti–O |
Hexagonal |
3.896 |
79 |
0.277 |
6 |
5 (1) |
32 |
12 (20) |
h-WO3 |
Hexagonal |
3.898 |
11 |
0.036 |
4 |
2 |
— |
— |
Solid acid reactions in the presence of water
The prospect of using the W–Ti–O mixed metal oxides as catalysts in aqueous phase reactions was investigated. First, alkylation of toluene with benzyl alcohol was investigated for the layered W–Ti–O sample. Fig. 3 shows the influence of water on the time course of the benzyltoluene and dibenzyl ether yields. In spite of the addition of water (5 mmol) into the mixture of reactant solution with the catalyst, the substrate solution was apparently homogeneous because of the bare solubility of benzyl alcohol to water (7.15 g/100 g-H2O at 90 °C) and an adsorptive property of the catalyst (2.35 mmol g−1). For the alkylation of toluene and benzyl alcohol without the addition of water, dibenzyl ether was only obtained directly after the start of the reaction, followed by an increase of the benzyltoluene yield with reaction time. The benzyltoluene and dibenzyl ether yields stabilized after 1 h of reaction when water was not present. On the other hand, in the presence of water (5 or 10 mmol), the yield of dibenzyl ether decreased only after 30 min and the yield of benzyltoluene increased as reaction time proceeded. In another experiment shown in Fig. 3, we added 10 mmol of water after 70 min of reaction. This led to a decrease of the dibenzyl ether yield and an increase of the benzyltoluene yield. We speculate that water promotes desorption of the products from the acid sites on the layered W–Ti–O catalyst. From the TPD spectrum (Fig. S12†) for the layered-type W–Ti–O catalyst used in the absence of water, it is clear that the surface contains heavy products, containing toluene groups. The peak at low temperature is due to toluene, the peak at high temperature is due to decomposition of heavier products, which likely originate from multiple alkylations. From the analysis of the reactant solution by GC-FID and GC-MS (Fig. S13†), heavy alkylation products such as dibenzyltoluene and tribenzyltoluene were observed. The strong Brønsted acid sites of the layered-type W–Ti–O catalyst adsorb the alkylation products on the surface of the catalyst and promote their successive alkylation. On the other hand, the addition of water to the reactant solution leads to competitive adsorption with the reactants and in this way decreases by-product formation. The other function of the addition of water would be shifting the equilibrium between benzyl alcohol and dibenzyl ether (C14H14O + H2O → 2C6H5CH2OH), resulting in a higher alkylation rate.
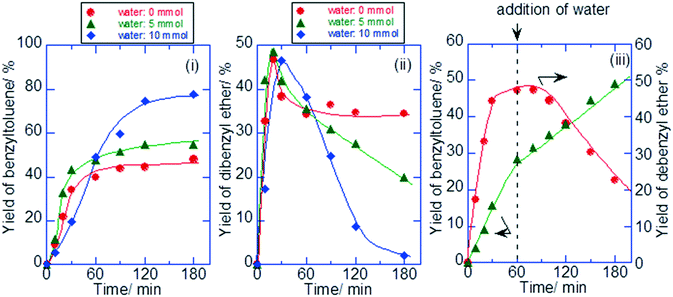 |
| Fig. 3 Influence of the amount of water on the formation of benzyltoluene by alkylation reaction of toluene with benzyl alcohol over the layered-type W–Ti–O sample: (i) yield of benzyltoluene, (ii) yield of dibenzylether, (iii) and the influence of water addition on the alkylation reaction (water added after a reaction time of 70 min). | |
Next, solid acid activity was examined by several catalytic reactions in water by using typical model reactions of hydrolysis of ethyl acetate and o-toryl acetate (Table 2 and Table S1†).31 Hydrolysis of ethyl acetate by using the layered-type W–Ti–O catalyst resulted in the formation of ethanol at a rate of 18.7 μmol g−1 min−1 for 2 h. ZSM-5 and WO3/TiO2 prepared by the impregnation method were tested for comparison in the same reaction conditions. The formation rates of ethanol were 19.8 μmol g−1 min−1 for ZSM-5 and 2.1 μmol g−1 min−1 for WO3/TiO2. For the hydrolysis of the more bulky ester o-toryl acetate, the formation rates of o-cresol were 8.3 μmol g−1 min−1 for the layered-type W–Ti–O catalyst, 3.3 μmol g−1 min−1 for WO3/TiO2 and 0.3 μmol g−1 min−1 for ZSM-5. The catalytic activities based on both catalytic weight and acid site of the layered-type W–Ti–O catalyst were competitive compared to those of the other typical solid acids such as Cs2.5H0.5PW12O40, SO42−/ZrO2 and Nb2O5.31 The bulkiness of the reactant, in this case, prevents diffusion into the small zeolite micropores. Yet, the layered-type W–Ti–O can act as a solid acid in an aqueous solution for the hydrolysis of both large and small esters. The reactant solution was analyzed by ICP-AES to check for possible leaching of the layered-type W–Ti–O catalyst. The results of ICP-AES showed that the amounts of leaching of the layered-type W–Ti–O catalyst were negligible.
Table 2 Catalytic activity over the layered-type W–Ti–O sample in the presence of watera
Reaction |
Catalyst/g |
Reaction temp./°C |
Conv./% |
Yield/% |
Details of reaction conditions are shown in the Experimental section.
Reaction time, 6 h.
Reaction time, 2 h.
Parentheses show the yield of pyruvaldehyde.
|
CH3COOC2H5 + H2O → CH3COOH + C2H5OH |
0.8 |
60 |
(18.7 μmol g−1 min−1) |
|
0.2 |
60 |
(8.3 μmol g−1 min−1) |
|
0.1 |
100b |
18 |
18 |
0.1 |
120c |
70 |
40 |
|
0.1 |
120c |
>99 |
37 (3)d |
Then, the layered-type W–Ti–O catalyst was applied to pyruvaldehyde conversion to lactic acid. The formation rate of lactic acid was slow at 100 °C. The conversion after 2 h was 18%, with nearly 100% lactic acid selectivity. The reaction at 120 °C enhanced the rate of pyruvaldehyde conversion at the expense of lactic acid selectivity. The conversion of pyruvaldehyde was 70% with 40% lactic acid yield for 2 h at 120 °C. The by-products of the reaction were dimers and trimers of the carbonyl compounds formed by the aldol condensation reaction. This performance was much better than that with sulfuric acid, which is a strong Brønsted acid (10% conversion with 6% selectivity to lactic acid at 120 °C for 2 h). Lactic acid synthesis from 1,3-DHA proceeds by dehydration reaction of 1,3-DHA to pyruvaldehyde followed by hydride transfer of pyruvaldehyde. The layered-type W–Ti–O catalyst showed full conversion with 38% selectivity to lactic acid. These values were corresponding to approximately 238 mol (m2 mol-acid−1) h−1 of the conversion rate and 88 mol (m2 mol-acid−1) h−1 of the formation rate based on acid density. This result shows that the layered-type W–Ti–O catalyst contains Brønsted acid sites and Lewis acid sites suitable for the transformation of 1,3-DHA. The Lewis acid sites are effective in water for pyruvaldehyde transformation.32,33 Below, we will show by pyridine IR that this sample contains such sites.
Solid acidity analysed by FT-IR
Fig. 4 shows the IR spectra of CO adsorbed at −183 °C on the layered-type W–Ti–O sample. The negative feature at 3660 cm−1 due to OH groups becomes weaker with increasing CO coverage and is replaced by a shift in the OH stretch band at 3450 cm−1. This OH frequency shift upon interaction with CO, indicates that the OH groups are strongly Brønsted acidic. The absorption at 2170 cm−1 is attributed to the vibration of CO adsorbed on these Brønsted acid sites. The absorption band at 2179–2205 cm−1 is attributed to the vibrations of CO adsorbed on Lewis acid sites. The adsorption at around 2180 cm−1 observed at 4 Torr shifted to a higher wavenumber with the decrease in CO pressure. The presence of various absorption bands shows that the layered-type W–Ti–O sample possesses at least two kinds of Lewis acid sites of different strengths.
 |
| Fig. 4 FT-IR spectra of CO adsorbed (−183 °C) on the layered-type W–Ti–O catalyst. | |
Fig. 5 shows the ratio of Brønsted acid sites and Lewis acid sites calculated by the integral IR absorbance of pyridine adsorbed on the layered-type W–Ti–O sample. The absorption bands at 1450 cm−1 and 1540 cm−1 were calculated as Lewis acid sites and Brønsted acid sites, respectively. After pyridine was adsorbed onto the samples at 100 °C, the parameters of the desorbed temperature of pyridine, the measurement temperature of FT-IR and the measurement atmosphere (in a vacuum or in the presence of water) were controlled and shown as desorbed temperature/°C, measurement temperature/°C, and measurement atmosphere, respectively. A comparison of the conditions (150, 150, vacuum) with the conditions (150, 150, water) shows that the area of the adsorption peak at 1450 cm−1 decreased and that of the peak at 1540 cm−1 increased by the addition of water. This demonstrates that a part of the Lewis acid sites was converted to Brønsted acid sites at 150 °C upon interaction with water. Tentatively, this can be expressed by M(L) + M
O + H2O → 2M–OH(B). The amount of Lewis acid sites that changed to Brønsted acid sites increased with increasing desorption temperature of pyridine. It is interesting to compare the IR spectra for the conditions (400, 400, vacuum), (400, 400, water) and (400, 150, water). These show that the Lewis acid sites changed to Brønsted acid sites in the presence of water and that additional Lewis acid sites were changed to Brønsted acid sites by a decrease of the temperature to 150 °C. These results suggest that weak Lewis acid sites, which were observed in the presence of water at lower temperature, act as a Lewis acid in water and that strong Lewis acid sites, which adsorbed pyridine at a higher temperature, were easily changed to Brønsted acid in the presence of water. The two peaks observed in the FT-IR spectrum of CO adsorbed corresponded to different behaviors of Lewis acid observed by FT-IR of pyridine adsorbed.
 |
| Fig. 5 Ratio of Brønsted acid sites and Lewis acid sites calculated by the peak area of pyridine-adsorbed FT-IR spectra of the layered-type W–Ti–O catalyst. (The numbers and conditions in parentheses show the desorption temperature of pyridine (°C), measurement temperature (°C) and atmosphere, respectively.) | |
Conclusions
Layered-type W–Ti–O mixed oxides were synthesized from ammonium metatungstate and titanium sulfate precursors with oxalic acid by a hydrothermal method. By optimization of the preparation conditions, the formation of a hexagonal structure and anatase TiO2 was suppressed in the hydrothermal synthesis. The addition of oxalic acid as a reducing agent suppressed the formation of hexagonal W–Ti–O mixed oxide. Higher concentration of the precursors is favorable for the formation of the layered-type W–Ti–O catalyst. In general, the surface area, acidity and acid catalytic activity (alkylation) increased with the amount of the layered-type W–Ti–O phase. Strong Brønsted acid sites are obtained due to the thermal release of ammonia from the uncalcined precursor. Optimum acidity and alkylation activity were achieved by calcination at 400 °C. Alkylation of benzyl alcohol and toluene led to heavy product formation due to multiple alkylations of the product due to its strong adsorption on the catalytic surface. The selectivity could be improved by the addition of water, which competes with the products for the acid sites. FT-IR measurements showed that the layered-type W–Ti–O possesses Brønsted acid sites and at least two different Lewis acid sites. The stronger Lewis acid sites can be converted into Brønsted acid sites in the presence of water, and the weaker Lewis acid sites functioned in the presence of water. This water tolerance of Lewis acid sites is an important characteristic of layered-type W–Ti–O, as it allows the conversion of 1,3-DHA into lactic acid in water.
Acknowledgements
This work was financially supported by the European Union FP7 NMP project NOVACAM (Novel cheap and abundant materials for catalytic biomass conversion, FP7-NMP-2013-EUJapan-604319). And this study was supported by the Cooperative Research Program of Institute for Catalysis, Hokkaido University (13A1002) and the Cooperative Research Program of Materials and Structures Laboratory, Tokyo Institute of Technology (2013-53).
References
- K. Nakajima, Y. Baba, R. Noma, M. Kitano, J. N. Kondo, S. Hayashi and M. Hara, J. Am. Chem. Soc., 2011, 133, 4224–4227 CrossRef CAS PubMed.
- S. Kobayashi and K. Manabe, Acc. Chem. Res., 2002, 35, 209–217 CrossRef CAS PubMed.
- M. Hara, K. Nakajima and K. Kamata, Sci. Technol. Adv. Mater., 2015, 16, 34903 CrossRef PubMed.
- C. B. Rasrendra, B. A. Fachri, I. G. B. N. Makertihartha, S. Adisasmito and H. J. Heeres, ChemSusChem, 2011, 4, 768–777 CrossRef CAS PubMed.
- R. M. West, M. S. Holm, S. Saravanamurugan, J. Xiong, Z. Beversdorf, E. Taarning and C. H. Christensen, J. Catal., 2010, 269, 122–130 CrossRef CAS.
- F. De Clippel, M. Dusselier, R. Van Rompaey, P. Vanelderen, J. Dijkmans, E. Makshina, L. Giebeler, S. Oswald, G. V. Baron, J. F. M. Denayer, P. P. Pescarmona, P. A. Jacobs and B. F. Sels, J. Am. Chem. Soc., 2012, 134, 10089–10101 CrossRef CAS PubMed.
- E. Taarning, S. Saravanamurugan, M. S. Holm, J. Xiong, R. M. West and C. H. Christensen, ChemSusChem, 2009, 2, 625–627 CrossRef CAS PubMed.
- Y. Hayashi and Y. Sasaki, Chem. Commun., 2005, 2716–2718 RSC.
- T. Iizuka, K. Ogasawara and K. Tanabe, Bull. Chem. Soc. Jpn., 1983, 56, 2927–2931 CrossRef CAS.
- C. Tagusagawa, A. Takagaki, A. Iguchi, K. Takanabe, J. N. Kondo, K. Ebitani, T. Tatsumi and K. Domen, Chem. Mater., 2010, 22, 3072–3078 CrossRef CAS.
- I. Nowak and M. Ziolek, Chem. Rev., 1999, 99, 3603–3624 CrossRef CAS PubMed.
- T. Murayama, J. Chen, J. Hirata, K. Matsumoto and W. Ueda, Catal. Sci. Technol., 2014, 4, 4250–4257 CAS.
- T. Kasuga, M. Hiramatsu, A. Hoson, T. Sekino and K. Niihara, Langmuir, 1998, 14, 3160–3163 CrossRef CAS.
- M. Kitano, K. Nakajima, J. N. Kondo, S. Hayashi and M. Hara, J. Am. Chem. Soc., 2010, 132, 6622–6623 CrossRef CAS PubMed.
- M. Kitano, E. Wada, K. Nakajima, S. Hayashi, S. Miyazaki, H. Kobayashi and M. Hara, Chem. Mater., 2013, 25, 385–393 CrossRef CAS.
- T. Konya, T. Katou, T. Murayama, S. Ishikawa, M. Sadakane, D. Buttrey and W. Ueda, Catal. Sci. Technol., 2013, 3, 380–387 CAS.
- S. Ishikawa, X. Yi, T. Murayama and W. Ueda, Appl. Catal., A, 2014, 474, 10–17 CrossRef CAS.
- S. Ishikawa, X. Yi, T. Murayama and W. Ueda, Catal. Today, 2014, 8–13 Search PubMed.
- K. Omata, S. Izumi, T. Murayama and W. Ueda, Catal. Today, 2013, 201, 7–11 CrossRef CAS.
- K. Omata, K. Matsumoto, T. Murayama and W. Ueda, Chem. Lett., 2014, 43, 435–437 CrossRef CAS.
- K. Omata, K. Matsumoto, T. Murayama and W. Ueda, Catal. Today, 2015, 259, 205–212 CrossRef.
- T. Murayama, N. Kuramata and W. Ueda, J. Catal., 2016, 339, 143–152 CrossRef CAS.
- C. Yue, X. Zhu, M. Rigutto and E. Hensen, Appl. Catal., B, 2015, 163, 370–381 CrossRef CAS.
- M. Hino, M. Kurashige, H. Matsuhashi and K. Arata, Appl. Catal., A, 2006, 310, 190–193 CrossRef CAS.
- T. Kitano, S. Okazaki, T. Shishido, K. Teramura and T. Tanaka, Catal. Today, 2012, 192, 189–196 CrossRef CAS.
- T. Shishido, T. Kitano, K. Teramura and T. Tanaka, Catal. Lett., 2009, 129, 383–386 CrossRef CAS.
- T. Kitano, T. Hayashi, T. Uesaka, T. Shishido, K. Teramura and T. Tanaka, ChemCatChem, 2014, 6, 2011–2020 CrossRef CAS.
- T. Murayama, N. Kuramata, S. Takatama, K. Nakatani, S. Izumi, X. Yi and W. Ueda, Catal. Today, 2012, 185, 224–229 CrossRef CAS.
- Y. Chen and I. E. Wachs, J. Catal., 2003, 217, 468–477 CrossRef CAS.
- T. Konya, T. Katou, T. Murayama, S. Ishikawa, M. Sadakane, D. Buttrey and W. Ueda, Catal. Sci. Technol., 2013, 3, 380–387 CAS.
- M. Kimura, T. Nakato and T. Okuhara, Appl. Catal., A, 1997, 165, 227–240 CrossRef CAS.
- T. Komanoya, A. Suzuki, K. Nakajima, M. Kitano, K. Kamata and M. Hara, ChemCatChem, 2016, 8, 1094–1099 CrossRef CAS.
- Y. Koito, K. Nakajima, M. Kitano and M. Hara, Chem. Lett., 2013, 42, 873–875 CrossRef CAS.
Footnote |
† Electronic supplementary information (ESI) available. See DOI: 10.1039/c6cy02198k |
|
This journal is © The Royal Society of Chemistry 2017 |
Click here to see how this site uses Cookies. View our privacy policy here.