DOI:
10.1039/C6RA28744A
(Paper)
RSC Adv., 2017,
7, 11233-11243
Carboxylation of styrenes with CBr4 and DMSO via cooperative photoredox and cobalt catalysis†
Received
27th December 2016
, Accepted 7th February 2017
First published on 13th February 2017
Abstract
Cooperative photoredox and cobalt catalyzed carboxylation of styrenes with CBr4 to afford the corresponding α,β-unsaturated carboxylic acids has been realized through radical addition and Kornblum (DMSO) oxidation. DMSO serves as the oxidant, oxygen source and solvent under these photocatalytic conditions.
Introduction
The direct carboxylation of alkenes1,2 is a formidable challenge despite its high potential as a practical method for the preparation of unsaturated carboxylic acid derivatives. A well-known process for carboxylation of alkenes is the transition-metal-catalyzed C–C bond formation with CO2, which has become a fundamental synthetic transformation in recent years.2 Most of those methodologies require the use of rare and expensive metals.3 More recently, Tanaka's group reported that alkenes underwent carboxylation with CO2 in the presence of EtAlCl2 and 2,6-dibromopyridine to afford the corresponding α,β- or β,γ-unsaturated carboxylic acids, but the substrate scope was limited to α-arylalkenes and trialkyl-substituted alkenes (Scheme 1).4 The radical-mediated approach can be a complementary route to the carboxylation of alkenes because radicals have high activity and efficiency.5 By virtue of this radical carboxylation strategy, several terminal alkenes, which are difficult to carboxylation with CO2, have been successfully transformed into the corresponding α,β-unsaturated carboxylic acids.
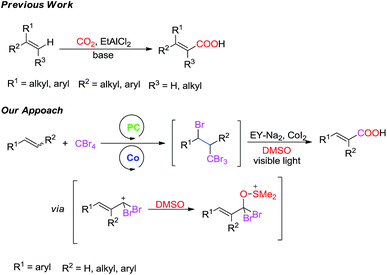 |
| Scheme 1 Carboxylation of styrenes. | |
In the last decade, visible-light driven photoredox catalysis has developed into a versatile tool for organic synthesis that is especially attractive as a sustainable chemical process.6 This is because solar energy (visible light) is clean and renewable. However, most of the reported such reactions often employ ruthenium or iridium polypyridyl complexes which are expensive and potentially toxic. Therefore, the organic dyes, eosin Y,7 would be an appropriate alternative to transition metal photocatalysts.8
Traditionally, carboxylation of styrenes1a–c was though addition of CX4 and acid-catalyzedhydrolysis reaction for two steps. In contrast to traditional methods we design a new method for the synthesis of α,β-unsaturated carboxylic acids directly. We herein report the successful development of a carboxylation of styrenes employing CBr4 and DMSO via cooperative photoredox and cobalt catalysis (CoI2)9 (Scheme 1).
Results and discussion
At first, the carboxylation of alkene was performed using styrene 1a and CBr4 with eosin Y disodium (10 mol%) as a photocatalyst under irradiation from a fluorescent bulb (18 W) and under a nitrogen atmosphere for 15 h in DMSO at 50 °C as the model reaction (Table 1).10 In contrast, Xia group reported the bromination of styrene in the similar photoredox conditions but for 120 hours.11 Subsequently, several catalysts were evaluated to give rise to target compound 2a (entries 1–4), of which eosin Y disodium provided the highest yield of the target product 2a and the intermediate 3 (entry 1). Atom-transfer radical additions of organic halides to alkenes giving the intermediate 3 were previously reported by groups of Stephenson,11a–c Reiser11d and Melchiorre11e. Different concentrations of eosin Y disodium were tested. Unfortunately, the yield of 2a could not be improved (entries 5 and 6). We also investigated BrCCl3 (ref. 11a and b) but the yield did not increase (entry 7). No conversion could be observed when CCl4 was used (entry 8).12 This phenomenon may be attributed to the carbon–chlorine bond more stable (relative to a carbon–bromine bond). Furthermore, we examined different solvent types, such as the protic solvent MeOH; non-polar solvent THF; dipolar solvents CH3CN, CH3NO3 and DMF. However, 2a was not observed in any of the cases (not shown). Cobalt catalysts in various oxidation states have recently attracted particular attention in the development of applicable transformations due to its economy and low toxicity.9 Subsequently, different cobalt catalysts were tested, including Co(acac)2, Co(OAc)2·4H2O, CoCO3, CoF2, CoCI2, CoBr2 and CoI2 (entries 9–15). These investigations identified CoI2 as the most efficient catalyst, which provided the desired product 2a in 70% isolated yield. We also explored the effect of iodide and observed that the addition of I2 resulted in a low yield (entry 16). However, lower or higher reaction temperature led to lower yields (entries 17–18). Next, we varied the amount of the CoI2 from 0.50 equiv. to 2.00 equiv. (entries 19–20). These experiments revealed that 1.0 equiv. of CoI2 gave the best yield (entry 15). In addition, a study of the reaction concentration indicated that increased concentration (i.e., 0.25 mol L−1 vs. 0.50 mol L−1) slightly improved the yield (entries 15 vs. 21). The use of green LEDs (entry 22) was almost effective as white LEDs.
Table 1 Optimization of visible light driven carboxylation of styrene

|
Entrya |
Halide |
Catalyst |
Additive |
2ab (%) |
3b (%) |
Reaction conditions: all reactions were carried out with 1a (0.50 mmol), halide (1.00 mmol), 10 mol% catalyst and additive (0.50 mmol) in solvent (2.00 mL) at 50 °C for 15 h irradiation by 18 W fluorescent lamp under nitrogen atmosphere unless otherwise stated. Isolated yield; n.r. = no reaction; n.d. = no detected. 5 mol% eosin Y disodium was used. 20 mol% eosin Y disodium was used. The reaction was conducted at rt. The reaction was conducted at 80 °C. CoI2 (0.50 equiv.) was used. CoI2 (2.00 equiv.) was used. The reaction was conducted using 1.00 mL DMSO. Green LEDs was used for irradiation. 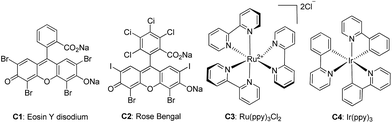 |
1 |
CBr4 |
C1 |
None |
15 |
28 |
2 |
CBr4 |
C3 |
None |
7 |
19 |
3 |
CBr4 |
C4 |
None |
11 |
23 |
4 |
CBr4 |
C2 |
None |
10 |
26 |
5c |
CBr4 |
C1 |
None |
13 |
17 |
6d |
CBr4 |
C1 |
None |
8 |
27 |
7 |
BrCCl3 |
C1 |
None |
13 |
25 |
8 |
CCl4 |
C1 |
None |
n.r. |
n.r. |
9 |
CBr4 |
C1 |
Co(acac)2 |
n.r. |
n.r. |
10 |
CBr4 |
C1 |
Co(OAc)2·4H2O |
Trace |
n.d. |
11 |
CBr4 |
C1 |
CoCO3 |
n.r. |
n.r. |
12 |
CBr4 |
C1 |
CoF2 |
28 |
12 |
13 |
CBr4 |
C1 |
CoCI2 |
19 |
8 |
14 |
CBr4 |
C1 |
CoBr2 |
Trace |
n.d. |
15 |
CBr4 |
C1 |
CoI2 |
70 |
19 |
16 |
CBr4 |
C1 |
I2 |
Trace |
34 |
17e |
CBr4 |
C1 |
CoI2 |
42 |
19 |
18f |
CBr4 |
C1 |
CoI2 |
65 |
15 |
19g |
CBr4 |
C1 |
CoI2 |
42 |
24 |
20h |
CBr4 |
C1 |
CoI2 |
51 |
39 |
21i |
CBr4 |
C1 |
CoI2 |
72 |
9 |
22j |
CBr4 |
C1 |
CoI2 |
70 |
12 |
After determining the optimized conditions for the synthesis of 2a, we examined a diverse range of styrenes (Table 2). Initially, we evaluated the electronic effect of substrates with substituents on the aryl ring. Arylalkenes with methyl substituents at the m and p positions on the aryl ring furnished the target products in good yields (Table 2, 2c and 2d), while the o-methyl substituted arylalkene had a low yield of 45% due to the steric effect (Table 2, 2b). The styrenes bearing the electron-withdrawing groups (F, Cl, and Br) were tolerated and provided moderate yields (Table 2, 2e–2g). For comparison, the yields were well tolerated when the styrenes contained electron-donating substituents such as methoxy and tert-butyl (Table 2, 2h, 2i and 2k). However, when dimethoxy and phenyl groups were introduced to the phenyl ring, the corresponding α,β-unsaturated acid products (Table 2, 2j and 2l) were isolated in 53% and 40% yields, respectively. It is noteworthy that 4-(trifluoromethyl)styrene gave the target product in good yield (Table 2, 2m). Nevertheless, the styrenes bearing the nitro and nitrile groups failed to provide the target products (Table 2, 2n and 2o). These result indicated strong electron withdrawing groups impaired the reactivity to give the target products. Moreover, we were delighted to find that 1-naphthylalkene could also afford the corresponding α,β-unsaturated acid 2p in yield of 62%.
Table 2 Carboxylation of styrenesa,b
Alkene (1a–1p 0.50 mmol), 10 mol% eosin Y disodium, CBr4 (1.00 mmol), CoI2 (0.50 mmol), DMSO (1.00 mL), 50 °C, N2. Isolated yield. Afforded the intermediate 1-nitro-4-(1,3,3,3-tetrabromopropyl)benzene (3n) and 4-(1,3,3,3-tetrabromopropyl)benzonitrile (3o) in 25% and 35% yields, respectively. |
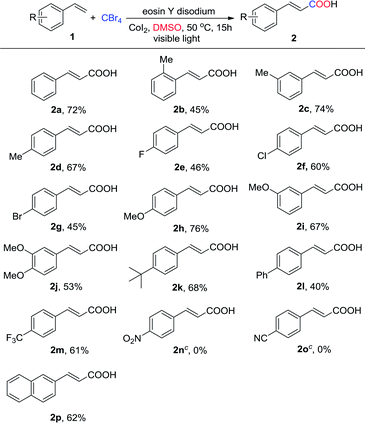 |
Next, we turned our attention to exam the scope of arylalkenes with various substituents on the α- or β-positions under the optimized conditions (Table 3). Unfortunately, the desired product was not obtained when (E)-1,2-diphenylethene was conducted under the optimized reaction conditions. Then we increased the reaction temperature to 100 °C and obtained the target product. In addition, both (Z)-and (E)-1,2-diphenylethene produced product 5a in 15% and 36% yields. The reaction of stilbenes 4b and 4c bearing substituents such as trifluoromethyl and nitro groups furnished the regioselective products 5b and 5c, respectively, in 22% and 32% yields. Moreover, arylalkene with the methyl group on the β-position (4d) furnished the corresponding α,β-unsaturated acid product in a low yield (Table 3, 5d). These results indicated that arylalkenes with various substituents on the β-positions gave low yields which may be because of the steric effect. It is worth mentioning that 1,1-diphenylethylene and indene also proceeded efficiently with yields of 68% and 63% (Table 3, 5e and 5f). Notably, 2-vinylthiophene was also a suitable substrate for the reaction, affording the product 5 g in 58% yield. However, no desired products were observed when other vinyl-substituted heterocycles such as 2-vinylpyrrole, 2-vinylpyridine and 3-vinylindole were used.
Table 3 Carboxylation of arylvinylsa,b
Alkene (4a–4f 0.50 mmol), 10 mol% eosin Y disodium, CBr4 (1.00 mmol), CoI2 (0.50 mmol), DMSO (1.00 mL), 100 °C, N2, 18 W white LED. Isolated yield. Using (Z)-1,2-diphenylethene. Using (E)-1,2-diphenylethene. Reaction run at 50 °C. |
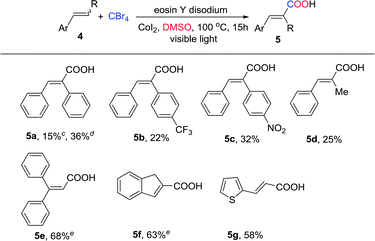 |
Several control experiments were designed to elucidate the plausible reaction mechanism for this carboxylation of styrenes (Scheme 2a). Firstly, the reaction of 1a and CBr4 in the absence of eosin Y disodium, visible light or CoI2 under the standard reaction conditions was investigated. 3a and 2a were obtained in moderate yields respectively (Scheme 2a, entries 1 and 2). These results indicated that eosin Y disodium, visible light and CoI2 were all very important to achieve this reaction. In comparison, 30% yield of 3a with trace amount of 2a were detected without eosin Y disodium, which was essential factor in the second step reaction (Scheme 2a, entries 2 vs. 3). Moreover, TEMPO (2.00 equiv.), a well-known radical scavenger, was found to inhibit this reaction process (Scheme 2a, entry 4), which suggested that the first step of the reaction may occur through a radical mechanism.
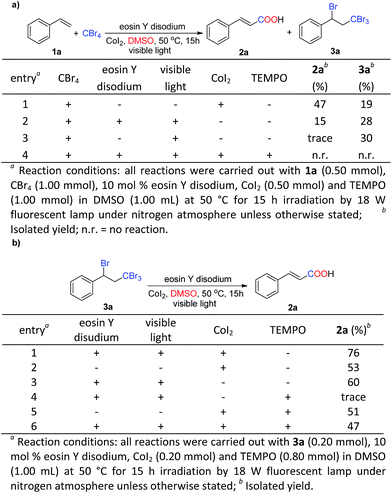 |
| Scheme 2 Mechanistic studies of cascade reactions. | |
To gain insight into mechanism of the second step reaction, a proposed intermediate 3a was tested under the standard conditions resulting in target product 2a in a yield of 76% (Scheme 2b, entry 1), which indicated that 3a was a possible intermediate for this reaction. Besides, in the absence of eosin Y disodium and light or CoI2, the reaction generated 2a in the yields of 53% and 60% respectively (Scheme 2b, entries 2 and 3), showing that eosin Y disodium and CoI2 all play important roles in this step of the reaction mechanism. 3a failed to be transformed into 2a in the presence of eosin Y disodium, visible light and TEMPO. These results suggested that the mechanism may contain a radical process (Scheme 2b, entries 3 vs. 4). In comparison, almost the similar yield of 2a was generated (Scheme 2a, entries 2, 5 and 6). Addition of TEMPO had no obvious effect on the reaction which suggested that this mechanism may contain a CoI2-catalyzed hydrolysis process (Scheme 2b, entries 5 and 6). The above results strongly suggested that this transformation may be achieved via cooperative photoredox and CoI2.
To further understand the mechanism, 18O-labeled H2O and DMSO experiments were performed between styrene 1a and CBr4 under optimized conditions (Scheme 3). When the reaction of 1a was conducted in the presence of 10.00 equiv. of H218O under the standard conditions, only 2a and 18O-2a were obtained in 51% yield with the ratio of 26.67
:
1.00 based on MS analysis. And no 18O2-2a was observed (Scheme 3a). In contrast, when the reaction was performed with 18O-labeled DMSO, the three products could also be obtained with the ratio 1.00
:
10.19
:
31.54 (Scheme 3b). These experimental results indicated that DMSO served as the source of oxygen in this transformation.
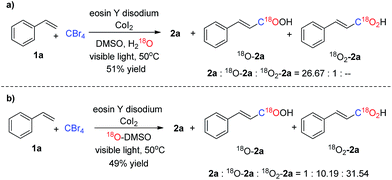 |
| Scheme 3 Labeling studies. | |
Based on the above results and previous reports, a plausible mechanism for the carboxylation is shown (Scheme 4). The excited [eosin Y disodium]* or Co(II) transfers an electron to the halide, generating a radical13,14 that adds to the alkene under electronic and steric control. The resulting radical combines with the halide with concurrent electron transfer back to [eosin Y disodium]+ or Co(III), thus, regenerating the catalyst or Co(II).15 Then, the intermediate 3a is eliminated, giving compound C, which undergoes SET (single electron transfer) reduction to generate the alkyl radical.16 Oxidation of the alkyl radical by [eosin Y disodium]+ generates carbocation E, accompanied by formation of the catalyst. Nucleophilic attack of DMSO to carbocation E affords alkoxysulfonium F,17 which also may be obtained from 3a by CoI2-catalyzed hydrolysis reaction. Then, a reaction similar to Kornblum (DMSO) oxidation proceeds to give compound G. Finally, nucleophilic attack by DMSO leads to the desired product 2a.
 |
| Scheme 4 Proposed reaction mechanism. | |
Conclusions
In summary, we have developed a methodology that combines the photoredox/cabolt-catalyzed radical addition of halides onto alkenes and Kornblum (DMSO) oxidation of the dibromo-substituted carbocation, which enabled the transformation of alkenes with a variety of functional groups into the corresponding α,β-unsaturated carboxylic acids. The preliminary mechanistic studies suggested that DMSO as the oxidant, oxygen source and solvent plays a key roles in this reaction.
Experimental
General information
All reactions were carried out under nitrogen and stirred magnetically. DMSO was distilled prior to use. 1H and 13C NMR spectra were recorded on 500 MHz or 600 MHz spectrometers using CDCl3 with TMS or residual solvent as standard unless otherwise noted. Melting points were determined using a Laboratory Device WRS-3 and are uncorrected/calibrated. TLC analysis was performed using Kangbino glass-backed plates (60 Å, 250 μm) and visualized using UV and phosphomolybdic acid stains. High-resolution mass spectra were obtained using an Agilent 1290 Infinity II-6530B in the ESI mode. Low-resolution mass spectra were obtained using an Agilent 1290 Infinity II-6460 in the ESI mode.
Preparation of substrates (derivatives of styrene)
2-Methylstyrene (1b)18. 2-Methylbenzaldehyde (1.00 g, 8.30 mmol, 1.00 equiv.) was added to a solution of methyltriphenylphosphonium bromide (3.5 g, 10.00 mmol, 1.20 equiv.) and K2CO3 (1.80 g, 13.00 mmol, 1.5 equiv.) in dioxane (7.00 mL). The mixture was refluxed at 110 °C over 10 h. After being cooled to room temperature, excess solvent was removed by rotary evaporation. The residue was diluted with petroleum ether and filtered through celite and concentrated under vacuum. The crude product was purified by flash column chromatography (petroleum ether) to obtain the corresponding product as a colorless oil; 0.50 g, 4.23 mmol; 51% yield. 1H NMR (500 MHz, CDCl3), δ 7.51–7.47 (m, 1H), 7.21–7.14 (m, 3H), 6.96 (dd, J = 17.4, 11.0 Hz, 1H), 5.65 (dd, J = 17.4, 1.4 Hz, 1H), 5.30 (dd, J = 11.0, 1.4 Hz, 1H), 2.37 (s, 3H); 13C NMR (125 MHz, CDCl3), δ 136.8, 135.4, 134.8, 130.2, 127.6, 126.1, 125.3, 115.1, 19.7.
3-Methylstyrene (1c)18. m-Tolualdehyde (1.00 g, 8.30 mmol, 1.00 equiv.) was added to a solution of methyltriphenylphosphonium bromide (3.57 g, 10.00 mmol, 1.20 equiv.) and K2CO3 (1.70 g, 13.00 mmol, 1.5 equiv.) in dioxane (7.00 mL). The mixture was refluxed at 110 °C over 10 h. After being cooled to room temperature, excess solvent was removed by rotary evaporation. The residue was diluted with petroleum ether and filtered through celite and concentrated under vacuum. The crude product was purified by flash column chromatography (petroleum ether) to obtain the corresponding product as a colorless oil; 0.80 g, 6.80 mmol; 82% yield. 1H NMR (500 MHz, CDCl3) δ 7.27–7.23 (m, 3H), 7.12–7.10 (m, 1H), 6.73 (dd, J = 17.6, 10.9 Hz, 1H), 5.78 (d, J = 17.6 Hz, 1H), 5.25 (d, J = 10.9 Hz, 1H), 2.38 (s, 3H); 13C NMR (125 MHz, CDCl3) δ 138.1, 137.5, 137.0, 128.6, 128.4, 126.9, 123.4, 113.6, 21.4.
3-Methoxystyrene (1i)19. 3-Methoxybenzaldehyde (1.00 g, 7.40 mmol, 1.00 equiv.) was added to a solution of methyltriphenylphosphonium bromide (3.20 g, 8.90 mmol, 1.20 equiv.) and K2CO3 (1.60 g, 11.80 mmol, 1.60 equiv.) in THF (10.00 mL). The mixture was refluxed at 75 °C over 10 h. After being cooled to room temperature, excess solvent was removed by rotary evaporation. The residue was diluted with petroleum ether and filtered through celite and concentrated under vacuum. The crude product was purified by flash column chromatography (petroleum ether) to obtain the corresponding product as a colorless oil; 0.79 g, 6.00 mmol; 81% yield. 1H NMR (500 MHz, CDCl3), δ 7.27 (t, J = 7.9 Hz, 1H), 7.03 (m, 1H), 6.98 (s, 1H), 6.86–6.83 (m, 1H), 6.72 (dd, J = 17.6, 10.9 Hz, 1H), 5.77 (d, J = 17.6 Hz, 1H), 5.28 (d, J = 10.9 Hz, 1H), 3.84 (s, 3H); 13C NMR (125 MHz, CDCl3), δ 159.8, 139.0, 136.8, 129.5, 118.9, 114.1, 113.4, 111.5, 55.2.
3,4-(Dimethoxy)styrene (1j)19. 3,4-Dimethoxybenzaldehyde (1.00 g, 6.00 mmol, 1.00 equiv.) was added to a solution of methyltriphenylphosphonium bromide (2.60 g, 7.20 mmol, 1.20 equiv.) and K2CO3 (1.20 g, 9.00 mmol, 1.50 equiv.) in THF (10.00 mL). The mixture was refluxed at 75 °C over 10 h. After being cooled to room temperature, excess solvent was removed by rotary evaporation. The residue was diluted with petroleum ether and filtered through celite and concentrated under vacuum. The crude product was purified by flash column chromatography (petroleum ether) to obtain the corresponding product as a colorless oil; 0.83 g, 4.98 mmol; 83% yield. 1H NMR (500 MHz, CDCl3), δ 6.99–6.94 (m, 2H), 6.83 (d, J = 8.2 Hz, 1H), 6.66 (dd, J = 17.5, 10.9 Hz, 1H), 5.62 (d, J = 17.5 Hz, 1H), 5.16 (d, J = 10.9 Hz, 1H), 3.91 (s, 3H), 3.89 (s, 3H); 13C NMR (125 MHz, CDCl3), δ 149.0, 149.0, 136.5, 130.7, 119.4, 1118, 111.0, 108.5, 55.9, 55.8.
4-Phenylstyrene (1l)18. 4-Biphenylcarboxaldehyde (1.00 g, 5.49 mmol, 1.00 equiv.) was added to a solution of methyltriphenylphosphonium bromide (2.40 g, 6.70 mmol, 1.20 equiv.) and K2CO3 (1.20 g, 8.77 mmol, 1.50 equiv.) in THF (7.00 mL). The mixture was refluxed at 75 °C over 10 h. After being cooled to room temperature, excess solvent was removed by rotary evaporation. The residue was diluted with petroleum ether and filtered through celite and concentrated under vacuum. The crude product was purified by flash column chromatography (petroleum ether) to obtain the corresponding product as a white solid; 0.60 g, 3.34 mmol; 61% yield; mp 119–120 °C (Lit. 120–122 °C), 1H NMR (500 MHz, CDCl3), δ 7.63–7.57 (m, 4H), 7.50 (d, J = 8.2 Hz, 2H), 7.45 (t, J = 7.5 Hz, 2H), 7.36 (t, J = 7.5 Hz, 1H), 6.78 (dd, J = 17.6, 10.9 Hz, 1H), 5.81 (d, J = 17.6 Hz, 1H), 5.29 (d, J = 11.0 Hz, 1H); 13C NMR (125 MHz, CDCl3), δ 140.7, 140.6, 136.6, 136.4, 128.8, 127.3, 127.2, 127.0, 126.6, 113.9.
4-(Trifluoromethyl)styrene (1m)18. 4-(Trifluoromethyl)benzaldehyde (1.00 g, 5.70 mmol, 1.00 equiv.) was added to a solution of methyltriphenylphosphonium bromide (2.40 g, 6.84 mmol, 1.20 equiv.) and K2CO3 (1.18 g, 8.55 mmol, 1.50 equiv.) in THF (8.00 mL). The mixture was refluxed at 75 °C over 10 h. After being cooled to room temperature, excess solvent was removed by rotary evaporation. The residue was diluted with petroleum ether and filtered through celite and concentrated under vacuum. The crude product was purified by flash column chromatography (petroleum ether) to obtain the corresponding product as a colorless oil; 0.66 g, 3.88 mmol; 67% yield. 1H NMR (500 MHz, CDCl3), δ 7.59 (d, J = 8.2 Hz, 2H), 7.51 (d, J = 8.1 Hz, 2H), 6.76 (dd, J = 17.6, 10.9 Hz, 1H), 5.86 (d, J = 17.6 Hz, 1H), 5.40 (d, J = 10.9 Hz, 1H); 13C NMR (125 MHz, CDCl3), δ 140.9, 135.6, 129.8 (q, J = 32.3 Hz), 126.4, 125.5 (q, J = 3.8 Hz), 123.1, 116.4; 19F NMR (470 MHz, CDCl3) δ − 62.5 (s, 3F)
4-Nitrostyrene (1o)18. 4-Nitrobenzaldehyde (1.00 g, 6.60 mmol, 1.00 equiv.) was added to a solution of methyltriphenylphosphonium bromide (2.80 g, 7.90 mmol, 1.20 equiv.) and K2CO3 (1.40 g, 9.90 mmol, 1.50 equiv.) in THF (10.00 mL). The mixture was refluxed at 75 °C over 10 h. After being cooled to room temperature, excess solvent was removed by rotary evaporation. The residue was diluted with petroleum ether and filtered through celite and concentrated under vacuum. The crude product was purified by flash column chromatography (petroleum ether) to obtain the corresponding product as a yellow oil; 0.65 g, 4.36 mmol; 66% yield. 1H NMR (500 MHz, CDCl3), δ 8.16 (d, J = 8.5 Hz, 2H), 7.52 (d, J = 8.7 Hz, 2H), 6.77 (dd, J = 17.6, 10.9 Hz, 1H), 5.92 (d, J = 17.6 Hz, 1H), 5.49 (d, J = 10.9 Hz, 1H); 13C NMR (125 MHz, CDCl3), δ 147.1, 143.8, 134.9, 126.8, 123.9, 118.6.
4-Cyanostyrene (1p)18. 4-Cyanobenzaldehyde (0.50 g, 3.82 mmol, 1.00 equiv.) was added to a solution of methyltriphenylphosphonium bromide (1.60 g, 4.58 mmol, 1.20 equiv.) and K2CO3 (0.83 g, 6.04 mmol, 1.50 equiv.) in dioxane (4.00 mL). The mixture was refluxed at 110 °C over 10 h. After being cooled to room temperature, excess solvent was removed by rotary evaporation. The residue was diluted with petroleum ether and filtered through celite and concentrated under vacuum. The crude product was purified by flash column chromatography (petroleum ether) to obtain the corresponding product as a colorless oil; 0.48 g, 3.70 mmol; 98% yield. 1H NMR (500 MHz, CDCl3), δ 7.62 (d, J = 8.2 Hz, 2H), 7.49 (d, J = 8.2 Hz, 2H), 6.73 (dd, J = 17.6, 10.9 Hz, 1H), 5.88 (d, J = 17.3 Hz, 1H), 5.45 (d, J = 10.9 Hz, 1H); 13C NMR (125 MHz, CDCl3), δ 141.9, 135.4, 132.4, 126.7, 118.9, 117.7, 111.1.
2-Vinylnaphthalene (1p)20. 2-Naphthaldehyde (1.00 g, 6.40 mmol, 1.00 equiv.) was added to a solution of methyltriphenylphosphonium bromide (2.70 g, 7.69 mmol, 1.20 equiv.) and K2CO3 (1.30 g, 9.60 mmol, 1.50 equiv.) in THF (12.00 mL). The mixture was refluxed at 75 °C over 10 h. After being cooled to room temperature, excess solvent was removed by rotary evaporation. The residue was diluted with petroleum ether and filtered through celite and concentrated under vacuum. The crude product was purified by flash column chromatography (petroleum ether) to obtain the corresponding product as a white solid; 0.96 g, 6.20 mmol; 97% yield; mp 63–64 °C (Lit. 62–66 °C), 1H NMR (500 MHz, CDCl3), δ 7.85–7.80 (m, 3H), 7.77 (s, 1H), 7.69–7.64 (m, 1H), 7.51–7.44 (m, 2H), 6.91 (ddd, J = 17.6, 10.9, 2.0 Hz, 1H), 5.90 (dd, J = 17.6, 2.0 Hz, 1H), 5.36 (dd, J = 10.8, 2.0 Hz, 1H); 13C NMR (125 MHz, CDCl3), δ 136.9, 135.0, 133.6, 133.2, 128.2, 128.0, 127.7, 126.4, 126.2, 125.2, 123.2, 114.2.
(E/Z)-1-Styryl-4-(trifluoromethyl)benzene (4b/4b′)18. A solution of benzyltriphenylphosphonium bromide (1.52 g, 3.50 mmol, 1.20 equiv.) and LiOH·H2O (0.36 g, 8.60 mmol, 3.00 equiv.) in isopropanol (10.00 mL) was stirred at room temperature for 30 min, and then 4-(trifluoromethyl)benzaldehyde (0.50 g, 2.87 mmol, 1.00 equiv.) was added. The reaction mixture was stirred at 75 °C for 6 h. After being cooled to room temperature, excess solvent was removed by rotary evaporation. The residue was quenched with water and extracted with ethyl acetate and the combined organic layers were dried over Na2SO4, filtered and concentrated under reduced pressure. The crude product was purified by flash column chromatography (petroleum ether) to obtain the corresponding product (E/Z = 38/62) as a white solid; 0.64 g, 2.58 mmol; 90% yield. 1H NMR (600 MHz, CDCl3, signals corresponding to (E)-isomer) δ 7.60 (s, 4H), 7.46 (d, J = 8.1 Hz, 1H), 7.38 (t, J = 7.6 Hz, 2H), 7.30 (t, J = 7.4 Hz, 1H), 7.19 (d, J = 16.2 Hz, 1H), 7.12 (d, J = 16.3 Hz, 1H); 13C NMR (150 MHz, CDCl3, signals corresponding to (E)-isomer), δ 140.8, 136.6, 131.2, 129.4, 128.3, 128.8, 127.1, 126.8, 126.6, 125.7 (q, J = 3.8 Hz), 123.3; 1H NMR (600 MHz, CDCl3, representative signals corresponding to (Z)-isomer), δ 7.46 (d, J = 8.1 Hz, 2H), 7.33 (d, J = 8.1 Hz, 2H), 7.25–7.21 (m, 5H), 6.72 (d, J = 12.2 Hz, 1H), 6.59 (d, J = 12.2 Hz, 1H); 13C NMR (150 MHz, CDCl3, representative signals corresponding to (Z)-isomer) δ 140.9, 136.7, 132.3, 129.2, 128.8, 128.8, 128.4, 127.6, 125.2 (q, J = 3.7 Hz), 123.3, 121.5.
(E)-1-Nitro-4-styrylbenzene (4c)18. A solution of benzyltriphenylphosphonium bromide (5.20 g, 12.01 mmol, 1.20 equiv.) and LiOH·H2O (1.24 g, 29.76 mmol, 3.00 equiv.) in 2-propanol (40.00 mL) was stirred at room temperature for 30 min, and then 4-nitrobenzaldehyde (1.50 g, 9.93 mmol, 1.00 equiv.) was added. The reaction mixture was stirred at 75 °C for 6 h. After being cooled to room temperature, excess solvent was removed by rotary evaporation. The residue was quenched with water and extracted with ethyl acetate and the combined organic layers were dried over Na2SO4, filtered and concentrated under reduced pressure. The crude product was purified by flash column chromatography (petroleum ether) to obtain the corresponding product: (E)-isomer; yellow solid; 1.16 g, 5.10 mmol; 52% yield; mp 154–155 °C (Lit. 155–158 °C), 1H NMR (600 MHz, CDCl3), δ 8.22 (d, J = 8.6 Hz, 2H), 7.64 (d, J = 8.6 Hz, 2H), 7.55 (d, J = 7.6 Hz, 2H), 7.40 (t, J = 7.6 Hz, 2H), 7.34 (t, J = 7.3 Hz, 1H), 7.27 (d, J = 16.5 Hz, 1H), 7.15 (d, J = 16.3 Hz, 1H), 13C NMR (150 MHz, CDCl3), 146.8, 143.9, 136.2, 133.3, 128.9, 128.9, 127.0, 126.9, 126.3, 124.2.
(Z/E)-β-Methylstyrene (4d/4d′)18. Benzaldehyde (0.50 g, 4.72 mmol, 1.00 equiv.) was added to a solution of ethyltriphenylphosphonium bromide (2.00 g, 5.39 mmol, 1.14 equiv.) and K2CO3 (1.00 g, 7.25 mmol, 1.50 equiv.) in dioxane (4.00 mL). The mixture was refluxed at 110 °C over 10 h. After being cooled to room temperature, excess solvent was removed by rotary evaporation. The residue was diluted with petroleum ether and filtered through celite and concentrated under vacuum. The crude product was purified by flash column chromatography (petroleum ether) to obtain the corresponding product (E/Z = 44/56) as a colorless oil; 0.33 g, 3.00 mmol; 65% yield. 1H NMR (500 MHz, CDCl3, signals corresponding to (Z)-isomer) δ 7.41–7.27 (m, 4H), 7.27–7.20 (m, 1H), 6.51–6.43 (m, 1H), 5.88–5.81 (m, 1H), 1.95 (dd, J = 7.2, 1.8 Hz, 3H); 13C NMR (125 MHz, CDCl3, signals corresponding to (Z)-isomer) δ 137.7, 129.9, 128.9, 128.1, 126.8, 126.4, 14.6; 1H NMR (500 MHz, CDCl3, representative signals corresponding to (E)-isomer) δ 7.41–7.27 (m, 4H), 7.27–7.20 (m, 1H), 6.51–6.43 (m, 1H), 6.32–6.25 (m, 1H), 1.93 (dd, J = 6.6, 1.6 Hz, 3H); 13C NMR (125 MHz, CDCl3, representative signals corresponding to (E)-isomer) δ 138.0, 131.1, 128.5, 123.8, 125.9, 125.7, 18.5.
2-Vinylthiophene (4g)21. Thiophene-2-carbaldehyde (1.00 g, 8.92 mmol, 1.00 equiv.) was added to a solution of ethyltriphenylphosphonium bromide (3.80 g, 10.70 mmol, 1.20 equiv.) and K2CO3 (1.85 g, 13.38 mmol, 1.50 equiv.) in dioxane (10.00 mL). The mixture was refluxed at 110 °C over 10 h. After being cooled to room temperature, excess solvent was removed by rotary evaporation. The residue was diluted with petroleum ether and filtered through celite and concentrated under vacuum. The crude product was purified by flash column chromatography (petroleum ether) to obtain the corresponding product as a colorless oil; 0.59 g, 5.35 mmol; 60% yield. 1H NMR (500 MHz, CDCl3), δ 7.19 (d, J = 5.0 Hz, 1H), 7.00 (m, 2H), 6.85 (dd, J = 17.5, 11.0 Hz, 1H), 5.60 (d, J = 12.5 Hz, 1H), 5.17 (d, J = 10.5 Hz, 1H), 13C NMR (125 MHz, CDCl3), δ 143.1, 129.9, 127.3, 125.8, 124.3, 113.2.
2-Vinylpyrrole (4h)21. Pyrrole-2-carbaldehyde (1.00 g, 10.52 mmol, 1.00 equiv.) was added to a solution of ethyltriphenylphosphonium bromide (4.51 g, 12.63 mmol, 1.20 equiv.) and K2CO3 (2.18 g, 15.78 mmol, 1.50 equiv.) in dioxane (10.00 mL). The mixture was refluxed at 110 °C over 10 h. After being cooled to room temperature, excess solvent was removed by rotary evaporation. The residue was diluted with 9
:
1 petroleum ether/ethyl acetate and filtered through celite and concentrated under vacuum. The crude product was purified by flash column chromatography (19
:
1 petroleum ether/EtOAc) to obtain the corresponding product as a colorless oil; 0.55 g, 5.79 mmol; 55% yield. 1H NMR (500 MHz, CDCl3), δ 8.24 (s, 1H), 6.78 (s, 1H), 6.61 (dd, J = 18.0, 11.0 Hz, 1H), 6.32–6.23 (m, 2H), 5.31 (d, J = 17.5 Hz, 1H), 5.05 (d, J = 11.5 Hz, 1H), 13C NMR (125 MHz, CDCl3), δ 130.9, 127.2, 118.8, 109.5, 108.5, 108.0.
3-Vinylindole (4j)22. To a stirred suspension of methyltriphenylphosphonium bromide (2.96 g, 8.30 mmol, 1.2 equiv.) in THF (20 mL), cooled to −50 °C, n-BuLi (2.90 mL, 2.4 M in hexanes, 6.90 mmol, 1.00 equiv.) was slowly added. The resulting yellow suspension was stirred and allowed to warm to 0 °C in approximately 45 minutes. After cooling to −30 °C, a pre-mixed solution of an indole 3-carboxaldehyde (6.90 mmol, 1 equiv.) and LiHMDS (6.90 mL, 1.0 M in THF, 6.90 mmol, 1.00 equiv.), in THF (8.00 mL) was added. The resulting suspension was then stirred at room temperature for 1 h, then poured onto H2O and extracted with EtOAc (2×). The combined organic phases were dried (Na2SO4), filtered and evaporated. The crude residue was then purified by a short chromatography on silica gel (petroleum ether/ethyl acetate 9
:
1) to obtain the corresponding product as a white solid; 0.90 g, 6.28 mmol; 91% yield; mp 84–86 °C (Lit. 80–81 °C), 1H NMR (500 MHz, DMSO-d6), δ 11.19 (s, 1H), 7.80 (d, J = 8.5 Hz, 1H), 7.48 (s, 1H), 7.38 (d, J = 8.1 Hz, 1H), 7.12 (t, J = 7.0 Hz, 1H), 7.05 (t, J = 8.0 Hz, 1H), 6.86 (dd, J = 18.0, 11.5 Hz, 1H), 5.61 (d, J = 17.5 Hz, 1H), 5.04 (d, J = 11.5 Hz, 1H). 13C NMR (126 MHz, DMSO-d6), δ 137.3, 130.7, 125.9, 125.6, 120.0, 119.97, 119.95, 114.3, 112.2, 109.4.
Carboxylation of alkenes
Procedures for the carboxylation of arylvinyls. Styrene (52 mg, 0.50 mmol, 1.00 equiv.), CBr4 (331 mg, 1.00 mmol, 2.00 equiv.), 10 mol% eosin Y disodium (31 mg, 0.05 mmol) and CoI2 (156 mg, 0.50 mmol, 1.00 equiv.) and 1 mL DMSO were combined in dried flask. The solution was stirred at 50 °C for 15 h on the condition of visible light (18 W fluorescent lamp) under nitrogen. After cooling to room temperature, the reaction mixture was extracted with ethylacetate (20.00 mL × 3) and then washed with brine (20.00 mL). The organic layer was dried over anhydrous Na2SO4 followed by filtration and then condensation. The residue was purified by silica gel column chromatography to afford corresponding product 2a and intermediate 3a.
Cinnamic acid (2a)23. Following the general procedure: white solid; 53 mg, 0.36 mmol; 72% yield; mp 134–136 °C (Lit. 133–135 °C); Rf = 0.51 (hexane
:
ethyl acetate
:
acetic acid = 2
:
2
:
0.01); 1H NMR (500 MHz, DMSO-d6), δ 12.39 (brs, 1H), 7.67–7.64 (m, 2H), 7.59 (d, J = 16.0 Hz, 1H), 7.42–7.37 (m, 3H), 6.52 (d, J = 16.0 Hz, 1H); 13C NMR (125 MHz, DMSO-d6), δ 168.1, 144.4, 134.7, 130.7, 129.4, 128.7, 119.7; MS (ESI): m/z (% relative intensity) = 147.0 (100) (M − H)−.
(E)-3-(o-Tolyl)acrylic acid (2b)24. Following the general procedure using 2-methylstyrene in place of styrene: white solid; 62 mg, 0.23 mmol; 45% yield; mp 184–185 °C (Lit. 175–176 °C); Rf = 0.46 (hexane
:
ethyl acetate
:
acetic acid = 2
:
2
:
0.01); 1H NMR (600 MHz, CDCl3) δ 8.10 (d, J = 15.6 Hz, 1H), 7.59 (d, J = 7.8 Hz, 1H), 7.31 (t, J = 7.8 Hz, 1H), 7.26–7.22 (m, 2H), 6.39 (d, J = 16.2 Hz, 1H), 2.46 (s, 3H); 13C NMR (150 MHz, CDCl3) δ 172.3, 144.7, 138.0, 133.0, 130.9, 130.5, 126.65, 126.5, 118.2, 19.8; MS (ESI): m/z (% relative intensity) = 161.1 (100) (M − H)−.
(E)-3-(m-Tolyl)acrylic acid (2c)25. Following the general procedure using 3-methylstyrene in place of styrene: white solid; 102 mg, 0.37 mmol; 74% yield; mp 115–117 °C (Lit. 116–118 °C); Rf = 0.42 (hexane
:
ethyl acetate
:
acetic acid = 2
:
2
:
0.01); 1H NMR (600 MHz, CDCl3), δ 7.77 (d, J = 15.6 Hz, 1H), 7.36 (d, J = 7.2 Hz, 2H), 7.30 (t, J = 7.8 Hz, 1H), 7.23 (d, J = 7.2 Hz, 1H), 6.45 (d, J = 16.2 Hz, 1H), 2.38 (s, 3H); 13C NMR (150 MHz, CDCl3), δ 172.6, 147.3, 138.7, 134.0, 131.6, 129.0, 128.9, 125.6, 117.1, 21.3; MS (ESI): m/z (% relative intensity) = 161.0 (100) (M − H)−.
(E)-3-(p-Tolyl)acrylic acid (2d)24. Following the general procedure using 4-methylstyrene in place of styrene: white solid; 92 mg, 0.34 mmol; 67% yield; mp 190–192 °C (Lit. 199–200 °C); Rf = 0.45 (hexane
:
ethyl acetate
:
acetic acid = 2
:
2
:
0.01); 1H NMR (500 MHz, DMSO-d6), δ 7.56–7.52 (m, 3H), 7.20 (d, J = 8.0 Hz, 2H), 6.44 (d, J = 16.0 Hz, 1H), 2.30 (s, 3H); 13C NMR (125 MHz, DMSO-d6), δ 168.1, 144.4, 140.6, 131.9, 129.9, 128.6, 118.5, 21.4; MS (ESI): m/z (% relative intensity) = 161.1 (100) (M − H)−.
(E)-3-(4-Fluorophenyl)acrylic acid (2e)24. Following the general procedure using 4-fluorostyrene in place of styrene: white solid; 38 mg, 0.23 mmol; 46% yield; mp 198–200 °C (Lit. 205–207 °C); Rf = 0.41 (hexane
:
ethyl acetate
:
acetic acid = 2
:
2
:
0.01); 1H NMR (500 MHz, DMSO-d6) δ 12.38 (brs, 1H), 7.78–7.73 (m, 2H), 7.58 (d, J = 16.0 Hz, 1H), 7.24 (t, J = 9.0 Hz, 2H), 6.49 (d, J = 16.0 Hz, 1H); 13C NMR (125 MHz, DMSO-d6), δ 168.0, 163.6 (d, 2JCF = 246.3 Hz), 143.1, 131.3 (d, J = 3.1 Hz), 131.0 (d, J = 8.5 Hz), 119.6 (d, J = 2.4 Hz), 116.3 (d, J = 21.2 Hz); 19F NMR (470 MHz, DMSO-d6), δ − 110.44 (m, 1F); MS (ESI): m/z (% relative intensity) = 165.0 (100) (M − H)−.
(E)-3-(4-Chlorophenyl)acrylic acid (2f)25. Following the general procedure using 1-chlorostyrene in place of styrene: white solid; 56 mg, 0.30 mmol; 60% yield; mp 241–243 °C (Lit. 247–249 °C); Rf = 0.38 (hexane
:
ethyl acetate
:
acetic acid = 2
:
2
:
0.01); 1H NMR (500 MHz, DMSO-d6), δ 12.50 (brs, 1H), 7.76 (d, J = 8.5 Hz, 2H), 7.62 (d, J = 16.0 Hz, 1H), 7.51 (d, J = 8.5 Hz, 2H), 6.59 (d, J = 16.0 Hz, 1H); 13C NMR (125 MHz, DMSO-d6), δ 167.8, 143.0, 135.1, 133.7, 130.4, 129.4, 120.5; MS (ESI): m/z (% relative intensity) = 181.0 (100) (M − H)−.
(E)-3-(4-Bromophenyl)acrylic acid (2g)26. Following the general procedure using 4-bromostyrene in place of styrene: white solid; 56 mg, 0.30 mmol; 60% yield; mp 255–256 °C (Lit. 264–265 °C); Rf = 0.43 (hexane
:
ethyl acetate
:
acetic acid = 2
:
2
:
0.01); 1H NMR (500 MHz, DMSO-d6), δ 7.65 (d, J = 8.5 Hz, 2H), 7.60 (d, J = 8.5 Hz, 2H), 7.55 (d, J = 16.0 Hz, 1H), 6.55 (d, J = 16.0 Hz, 1H); 13C NMR (125 MHz, DMSO-d6), δ 167.8, 143.1, 134.0, 132.3, 130.6, 124.0, 120.6; MS (ESI): m/z (% relative intensity) = 226.9 (100) (M − H)−
(E)-3-(4-Methoxyphenyl)acrylic acid (2h)24. Following the general procedure using 4-methoxy styrene in place of styrene: white solid; 68 mg, 0.38 mmol; 76% yield; mp 170–171 °C (Lit. 175–176 °C); Rf = 0.40 (hexane
:
ethyl acetate
:
acetic acid = 2
:
2
:
0.01), 1H NMR (600 MHz, DMSO-d6) δ 12.23 (brs, 1H), 7.64 (d, J = 9.0 Hz, 2H), 7.55 (d, J = 16.2 Hz, 1H), 6.97 (d, J = 8.4 Hz, 2H), 6.38 (d, J = 16.2 Hz, 1H), 3.80 (s, 3H); 13C NMR (150 MHz, DMSO-d6), δ 167.8, 160.9, 143.7, 129.9, 126.8, 116.5, 114.3, 55.3; MS (ESI): m/z (% relative intensity) = 177.0 (100) (M − H)−.
(E)-3-(3-Methoxyphenyl)acrylic acid (2i)25. Following the general procedure using 3-methoxystyrene in place of styrene: white solid; 60 mg, 0.34 mmol; 67% yield; mp 110–112 °C (Lit. 117–119 °C); Rf = 0.43 (hexane
:
ethyl acetate
:
acetic acid = 2
:
2
:
0.01); 1H NMR (600 MHz, CDCl3), δ 7.77 (d, J = 16.2 Hz, 1H), 7.32 (t, J = 7.8 Hz, 1H), 7.15 (d, J = 7.2 Hz, 1H), 7.07 (s, 1H), 6.97 (dd, J = 7.8, 1.8 Hz, 1H), 6.45 (d, J = 15.6 Hz, 1H), 3.84 (s, 3H); 13C NMR (150 MHz, CDCl3), δ 172.3, 159.9, 147.1, 135.4, 130.0, 121.1, 117.6, 116.7, 113.2, 55.4; MS (ESI): m/z (% relative intensity) = 177.0 (100) (M − H)−.
(E)-3-(3,4-Dimethoxyphenyl)acrylic acid (2j)27. Following the general procedure using 3,4-dimethoxytyrene in place of styrene: white solid; 55 mg, 0.27 mmol; 53% yield; mp 189–191 °C (Lit. 191 °C); Rf = 0.34 (hexane
:
ethyl acetate
:
acetic acid = 2
:
2
:
0.01); 1H NMR (500 MHz, CDCl3), δ 7.73 (d, J = 16.0 Hz, 1H), 7.15 (dd, J = 8.0, 1.5 Hz, 1H), 7.08 (d, J = 1.5 Hz, 1H), 6.89 (d, J = 8.5 Hz, 1H), 6.33 (d, J = 16.0 Hz, 1H), 3.93 (s, 6H); 13C NMR (125 MHz, CDCl3), δ 172.2, 151.5, 149.3, 147.0, 127.0, 123.1, 114.8, 111.0, 109.8, 56.0, 55.9; MS (ESI): m/z (% relative intensity) = 206.9 (100) (M − H)−.
(E)-3-(4-(tert-Butyl)phenyl)acrylic acid (2k)26. Following the general procedure using 4-(tert-butyl)styrene in place of styrene: white solid; 83 mg, 0.34 mmol; 68% yield; mp 202–203 °C (Lit. 202–204 °C); Rf = 0.46 (hexane
:
ethyl acetate
:
acetic acid = 2
:
2
:
0.01); 1H NMR (600 MHz, CDCl3), δ 7.79 (d, J = 15.9 Hz, 1H), 7.50 (d, J = 8.2 Hz, 2H), 7.43 (d, J = 8.2 Hz, 2H), 6.43 (d, J = 15.9 Hz, 1H), 1.33 (s, 9H); 13C NMR (150 MHz, CDCl3), δ 172.7, 154.4, 147.0, 131.3, 128.3, 126.0, 116.4, 35.0, 31.2; MS (ESI): m/z (% relative intensity) = 203.0 (100) (M − H)−.
(E)-3-([1,1′-Biphenyl]-4-yl)acrylic acid (2l). Following the general procedure using 4-phenylstyrene in place of styrene: white solid; 50 mg, 0.20 mmol; 40% yield; mp 215–217 °C; Rf = 0.39 (hexane
:
ethyl acetate
:
acetic acid = 2
:
2
:
0.01); 1H NMR (500 MHz, DMSO-d6), δ 7.77 (d, J = 8.0 Hz, 2H), 7.73–7.69 (m, 4H), 7.63 (d, J = 16.0 Hz, 1H), 7.47 (t, J = 7.5 Hz, 2H), 7.38 (t, J = 8.0 Hz, 1H), 6.57 (d, J = 16.0 Hz, 1H); 13C NMR (125 MHz, DMSO-d6), δ 168.0, 143.9, 142.2, 139.7, 133.8, 129.5, 129.3, 128.4, 127.5, 127.1, 119.6; MS (ESI): m/z (% relative intensity) = 223.0 (100) (M − H)−, HRMS (ESI): m/z calcd for C15H12O2 (M − H)− 223.0765, found 223.0764.
(E)-3-(4-(Trifluoromethyl)phenyl)acrylic acid (2m)28. Following the general procedure using 4-trifluoromethylstyrene in place of styrene: white solid; 66 mg, 0.31 mmol; 61% yield; mp 206–208 °C; Rf = 0.43 (hexane
:
ethyl acetate
:
acetic acid = 2
:
2
:
0.01); 1H NMR (500 MHz, DMSO-d6), δ 12.59 (brs, 1H), 7.91 (d, J = 8.0 Hz, 2H), 7.75 (d, J = 8.5 Hz, 2H), 7.65 (d, J = 16.0 Hz, 1H), 6.67 (d, J = 16.0 Hz, 1H); 13C NMR (125 MHz, DMSO-d6), δ 167.6, 142.5, 138.7, 130.3 (q, J = 31.7), 129.3, 126.1 (q, J = 3.7 Hz), 124.5 (d, J = 271.3 Hz), 122.6; 19F NMR (470 MHz, DMSO-d6), δ − 61.28 (s, 3F); MS (ESI): m/z (% relative intensity) = 215.0 (100) (M − H)−.
(E)-3-(Naphthalen-2-yl)acrylic acid (2p). Following the general procedure using 2-vinylnaphthalene in place of styrene: white solid; 61 mg, 0.31 mmol; 62% yield; mp 203–204 °C; Rf = 0.41 (hexane
:
ethyl acetate
:
acetic acid = 2
:
2
:
0.01); 1H NMR (500 MHz, DMSO-d6), δ 12.44 (brs, 1H), 8.17 (s, 1H), 7.96–7.91 (m, 3H), 7.88–7.84 (m, 1H), 7.74 (d, J = 16.0 Hz, 1H), 7.58–7.53 (m, 2H), 6.65 (d, J = 15.5 Hz, 1H); 13C NMR (125 MHz, DMSO-d6), δ 168.1, 144.4, 134.1, 133.3, 132.3, 130.1, 129.0, 128.9, 128.1, 127.7, 127.2, 124.4, 120.0; MS (ESI): m/z (% relative intensity) = 197.0 (100) (M − H)−; HRMS (ESI): m/z calcd for C13H10O2 (M − H)− 197.0608, found 197.0605.
(1,3,3,3-Tetrabromopropyl)benzene (3a)29. Following the general procedure: white solid; 19 mg, 0.05 mmol; 9% yield; mp 55–57 °C; Rf = 0.63 (hexane); 1H NMR (500 MHz, CDCl3), δ 7.53 (d, J = 7.3 Hz, 2H), 7.40 (t, J = 7.4 Hz, 2H), 7.34 (t, J = 7.3 Hz, 1H), 5.38 (dd, J = 7.8, 4.0 Hz, 1H), 4.19–4.07 (m, 2H), 13C NMR (125 MHz, CDCl3), δ 140.8, 129.0, 128.9, 128.2, 66.5, 50.2, 35.3. MS (ESI): m/z (% relative intensity) = 437.0 (100) (M + H)+.
1-Nitro-4-(1,3,3,3-tetrabromopropyl)benzene (3n). Following the general procedure: yellow oil; 60 mg, 0.13 mmol; 25% yield; Rf = 0.59 (petroleum ether
:
ethyl acetate = 9
:
1); 1H NMR (500 MHz, CDCl3), δ 8.24 (d, J = 8.5 Hz, 2H), 7.69 (d, J = 8.5 Hz, 2H), 5.38 (dd, J = 8.5, 3.5 Hz, 1H), 4.18–4.02 (m, 2H), 13C NMR (125 MHz, CDCl3) δ 147.9, 147.5, 129.3, 124.1, 66.0, 47.4, 34.0. MS (ESI): m/z (% relative intensity) = 477.7 (100) (M + H)+; HRMS (ESI): m/z calcd for C13H10O2 (M + H)+ 477.7283, found 477.7282.
4-(1,3,3,3-Tetrabromopropyl)benzonitrile (3o). Following the general procedure: yellow oil; 80 mg, 0.13 mmol; 35% yield; Rf = 0.55 (petroleum ether
:
ethyl acetate = 9
:
1); 1H NMR (500 MHz, CDCl3), δ 7.67 (d, J = 8.0 Hz, 2H), 7.61 (d, J = 8.5 Hz, 2H), 5.32 (dd, J = 8.5, 3.5 Hz, 1H), 4.14–3.99 (m, 2H), 13C NMR (126 MHz, CDCl3), δ 145.6, 132.7, 129.0, 118.2, 112.8, 65.9, 47.9, 34.1. MS (ESI): m/z (% relative intensity) = 457.7 (100) (M + H)+; HRMS (ESI): m/z calcd for C13H10O2 (M + H)+ 457.7283, found 457.7385.
Carboxylation of substituted arylvinyls
(E)-2,3-Diphenylacrylic acid (5a)30. Following the general procedure using (E)-1,2-diphenylethene in place of styrene. The reaction was stirred at 100 °C for 6 h: white solid; 40 mg, 0.18 mmol; 36% yield; mp 170–171 °C (Lit. 171–172 °C); Rf = 0.41 (hexane
:
ethyl acetate
:
acetic acid = 2
:
2
:
0.01); 1H NMR (500 MHz, DMSO-d6) δ 12.72 (brs, 1H), 7.76 (s, 1H), 7.39–7.34 (m, 3H), 7.24–7.13 (m, 5H), 7.04 (d, J = 7.5 Hz, 2H); 13C NMR (125 MHz, DMSO-d6) δ 168.8, 139.4, 136.8, 134.9, 133.8, 130.6, 129.9, 129.5, 128.9, 128.7, 128.0; MS (ESI): m/z (% relative intensity) = 223.0 (100) (M − H)−.
(E)-2,3-Diphenylacrylic acid (5a′). Following the general procedure using (Z)-1,2-diphenylethene in place of styrene. The reaction was stirred at 100 °C for 6 h: white solid; 17 mg, 0.08 mmol; 15% yield; mp 170–171 °C (Lit. 171–172 °C); Rf = 0.41 (hexane
:
ethyl acetate
:
acetic acid = 2
:
2
:
0.01); 1H NMR (500 MHz, DMSO-d6) δ 12.71 (brs, 1H), 7.75 (s, 1H), 7.40–7.34 (m, 3H), 7.24–7.14 (m, 5H), 7.04 (d, J = 7.5 Hz, 2H); 13C NMR (125 MHz, DMSO-d6) δ 168.8, 139.4, 136.8, 134.9, 133.8, 130.6, 129.9, 129.5, 128.9, 128.7, 128.0; MS (ESI): m/z (% relative intensity) = 223.0 (100) (M − H)−.
(E)-3-Phenyl-2-(4-(trifluoromethyl)phenyl)acrylic acid (5b). Following the general procedure using (Z/E)-1-styryl-4-(trifluoromethyl)benzene in place of styrene. The reaction was stirred at 100 °C for 6 h: white solid; 32 mg, 0.11 mmol; 22% yield; mp 192–194 °C; Rf = 0.45 (hexane
:
ethyl acetate
:
acetic acid = 2
:
2
:
0.01); 1H NMR (500 MHz, CDCl3) δ 8.04 (s, 1H), 7.65 (d, J = 8.5 Hz, 2H), 7.39 (d, J = 8.0 Hz, 2H), 7.29 (t, J = 7.5 Hz, 1H), 7.21 (t, J = 8.0 Hz, 2H), 7.06 (d, J = 8.0 Hz, 2H); 13C NMR (125 MHz, CDCl3) δ 171.9, 143.6, 139.1, 133.7, 130.7, 130.4, 130.1, 129.9, 128.5, 125.6 (d, J = 3.4 Hz). 19F NMR (470 MHz, CDCl3) δ − 62.61 (s, 3F); MS (ESI): m/z (% relative intensity) = 291.0 (100) (M − H)−; HRMS (ESI): m/z calcd for C16H11F3O2 (M − H)− 291.0638, found 291.0638.
(E)-2-(4-Nitrophenyl)-3-phenylacrylic acid (5c). Following the general procedure using (E)-1-nitro-4-styrylbenzene in place of styrene. The reaction was stirred at 100 °C for 6 h: white solid; 32 mg, 0.11 mmol; 22% yield; mp 220–223 °C; Rf = 0.34 (hexane
:
ethyl acetate
:
acetic acid = 2
:
2
:
0.01); 1H NMR (500 MHz, CDCl3) δ 8.25 (d, J = 8.5 Hz, 2H), 8.08 (s, 1H), 7.45 (d, J = 8.5 Hz, 2H), 7.30 (t, J = 7.5 Hz, 1H), 7.22 (t, J = 8.0 Hz, 2H), 7.06 (d, J = 7.5 Hz, 2H); 13C NMR (125 MHz, CDCl3) δ 171.3, 147.6, 144.4, 142.3, 133.3, 131.2, 130.7, 130.3, 129.4, 128.6, 123.9; MS (ESI): m/z (% relative intensity) = 268.0 (100); HRMS (ESI): m/z calcd for C15H11NO4 (M − H)− 268.0615, found 268.0614.
(E)-2-Methyl-3-phenylacrylic acid (5d). Following the general procedure using (Z/E)-prop-1-en-1-ylbenzene in place of styrene. The reaction was stirred at 100 °C for 6 h: white solid; 20 mg, 0.13 mmol; 25% yield; mp 59–61 °C; Rf = 0.41 (hexane
:
ethyl acetate
:
acetic acid = 2
:
2
:
0.01); 1H NMR (600 MHz, DMSO-d6) δ 12.52 (brs, 1H), 7.60 (s, 1H), 7.48–7.42 (m, 4H), 7.36 (t, J = 5.5 Hz, 1H), 2.03 (s, 3H); 13C NMR (150 MHz, DMSO-d6) δ 169.3, 137.6, 135.5, 129.6, 128.7, 128.5, 128.4, 13.9; MS (ESI): m/z (% relative intensity) = 161.0 (100) (M − H)−; HRMS (ESI): m/z calcd for C10H10O2 (M − H)− 161.0680, found 161.0680.
3,3-Diphenylacrylic acid (5e)31. Following the general procedure using (Z/E)-prop-1-en-1-ylbenzene in place of styrene: white solid; 68 mg, 0.38 mmol; 76% yield; mp 146–148 °C (Lit. 158 °C); Rf = 0.44 (hexane
:
ethyl acetate
:
acetic acid = 2
:
2
:
0.01). 1H NMR (500 MHz, DMSO-d6) δ 12.15 (brs, 1H), 7.40–7.33 (m, 6H), 7.27–7.22 (m, 2H), 7.15–7.12 (m, 2H), 6.35 (s, 1H); 13C NMR (125 MHz, DMSO-d6) δ 167.2, 154.1, 141.0, 139.3, 129.7, 129.4, 129.0, 128.3, 119.3; MS (ESI): m/z (% relative intensity) = 223.0 (100) (M − H)−.
1H-Indene-2-carboxylic acid (5f)32. Following the general procedure using (Z/E)-prop-1-en-1-ylbenzene in place of styrene: white solid; 50 mg, 0.32 mmol; 63% yield; mp 233–235 °C; Rf = 0.46 (hexane
:
ethyl acetate
:
acetic acid = 2
:
2
:
0.01). 1H NMR (500 MHz, DMSO-d6) 7.68 (s, 1H), 7.61–7.56 (m, 1H), 7.55–7.52 (m, 1H), 7.35–7.31 (m, 2H), 3.62 (s, 2H); 13C NMR (125 MHz, DMSO-d6) δ 166.1, 145.1, 143.0, 140.6, 138.9, 127.7, 127.2, 124.8, 123.8, 38.6; MS (ESI): m/z (% relative intensity) = 159.0 (100) (M − H)−.
(E)-3-(Thiophen-2-yl)acrylic acid (5g)33. Following the general procedure using 2-vinylthiophene in place of styrene: white solid; 45 mg, 0.29 mmol; 58% yield; mp 143–147 °C (Lit. 140–142 °C); Rf = 0.44 (hexane
:
ethyl acetate
:
acetic acid = 2
:
2
:
0.01). 1H NMR (500 MHz, DMSO-d6) δ 12.43 (brs, 1H), 7.73 (d, J = 16.0 Hz, 1H), 7.68 (d, J = 10.0 Hz, 1H), 7.49 (d, J = 3.0 Hz, 1H), 7.14–7.11 (m, 1H), 6.17 (d, J = 16.0 Hz, 1H). 13C NMR (125 MHz, DMSO-d6) δ 167.98, 139.18, 137.35, 132.19, 129.96, 129.03, 117.66. MS (ESI): m/z (% relative intensity) = 153.0 (100) (M − H)−.
18O Labeling experiment
18O Labeled H2O experiment. Styrene (26 mg, 0.25 mmol, 1.00 equiv.), CBr4 (166 mg, 0.50 mmol, 2.00 equiv.), 10 mol% eosin Y disodium (15 mg, 0.03 mmol), CoI2 (78 mg, 0.25 mmol, 2.00 equiv.), 18O–H2O (45 mg, 5.00 mmol, 10.00 equiv.) and 0.50 mL DMSO were combined in dried flask. The solution was stirred at 50 °C for 15 h on the condition of visible light (18 W fluorescent lamp) under nitrogen. After cooling to room temperature, the reaction mixture was extracted with ethyl acetate (10.00 mL × 3) and then washed with brine (10.00 mL). The organic layer was dried over anhydrous Na2SO4 followed by filtration and then condensation. The residue was purified by silica gel column chromatography to afford the corresponding product. ESI-ms analysis of this product clearly assigned the presence of both compounds 2a (M− at 147.0) and 18O-2a (M− at 149.0) in noticeable amount.
Method for preparation of 18O labeled DMSO34. Solid dimethylsulfur dibromide (5.00 g, 22.50 mmol, 1.00 equiv.) prepared as per known procedure35 was added portion wise over 15 min to a vigorously stirred solution of triethylamine (6.30 mL, 45.00 mmol, 2.00 equiv.) freshly distilled from calcium hydride and 18O-labeled water (97 atom% 18O) (0.20 mL, 11.00 mmol, 0.50 equiv.) in 15.00 mL of tetrahydrofuran (freshly distilled from sodium metal). The temperature of the reaction was maintained below 50 °C. The precipitate of triethylamine hydrobromide was removed by centrifugation and washed twice with ether. The combined yellow supernatant and washings were dried on high vacuum pressure pump at room temperature (15 mm) to remove the solvent and was given 0.50 g of a brownish black liquid. Without further purification the reaction was performed styrene (26 mg, 0.25 mmol, 1.00 equiv.), CBr4 (166 mg, 0.50 mmol, 2.00 equiv.), 10 mol% eosin Y disodium (15 mg, 0.03 mmol), CoI2 (78 mg, 0.25 mmol, 2.00 equiv.) following the general procedure giving the corresponding product 2a. ESI-ms analysis of this product clearly assigned the presence of both compounds 2a (M− at 147.0), 18O-2a (M− at 149.0) and 18O2-2a (M− at 151.0) in noticeable amount.
Acknowledgements
Y. T. thanks National Natural Science Foundation of China for generous founding [21172169, 21572154] and the Fundamental Research Funds for the Central Universities [201612013] for financial support.
Notes and references
-
(a) M. S. Kharasch, E. V. Jensen and W. H. Urry, J. Am. Chem. Soc., 1947, 69, 1100 CrossRef CAS
;
(b) T. Nguyen, J. Leroy and C. Wakselman, J. Org. Chem., 1993, 58, 3772 CrossRef CAS
;
(c) M. Aslam, W. F. Stansbury, R. J. Reiter and D. R. Larkin, J. Org. Chem., 1997, 62, 1550 CrossRef CAS
;
(d) J. N. Moorthy and K. N. Parida, J. Org. Chem., 2014, 79, 11431 CrossRef CAS PubMed
;
(e) C. Wuensch, S. M. Glueck, J. Gross, D. Koszelewski, M. Schober and K. Faber, Org. Lett., 2012, 14, 8 CrossRef PubMed
;
(f) C. Wuensch, T. Pavkov-Keller, G. Steinkellner, J. Gross, M. Fuchs, A. Hromic, A. Lyskowski, K. Fauland, K. Gruber, S. M. Glueck and K. Faber, Adv. Synth. Catal., 2015, 357, 1909 CrossRef CAS PubMed
;
(g) S. Beaumont, E. A. Ilardi, L. R. Monroe and A. Zakarian, J. Am. Chem. Soc., 2010, 132, 1482 CrossRef CAS PubMed
;
(h) Z. H. Gu, A. T. Herrmann and A. Zakarian, Angew. Chem., Int. Ed., 2011, 50, 7136 CrossRef CAS PubMed
;
(i) A. T. Herrmann, L. L. Smith and A. Zakarian, J. Am. Chem. Soc., 2012, 134, 6976 CrossRef CAS PubMed
;
(j) E. A. Ilardi and A. Zakarian, Chem. – Asian J., 2011, 6, 2260 CrossRef CAS PubMed
. -
(a) K. Huang, C. L. Sun and Z. J. Shi, Chem. Soc. Rev., 2011, 40, 2435 RSC
;
(b) M. Cokoja, C. Bruckmeier, B. Rieger, W. A. Herrmann and F. E. Kühn, Angew. Chem., Int. Ed., 2011, 50, 8510 CrossRef CAS PubMed
;
(c) Q. Liu, L. Wu, R. Jackstell and M. Beller, Nat. Commun., 2015, 6, 5933 CrossRef PubMed
;
(d) Y. Tsuji and T. Fujihara, Chem. Commun., 2012, 48, 9956 RSC
;
(e) M. D. Greenhalgh and S. P. Thomas, J. Am. Chem. Soc., 2012, 134, 11900 CrossRef CAS PubMed
;
(f) T. G. Ostapowicz, M. Schmitz, M. Krystof, J. Klankermayer and W. Leitner, Angew. Chem., Int. Ed., 2013, 52, 12119 CrossRef CAS PubMed
;
(g) C. M. Williams, J. B. Johnson and T. Rovis, J. Am. Chem. Soc., 2008, 130, 14936 CrossRef CAS PubMed
;
(h) L. Wu, Q. Liu, I. Fleischer, R. Jackstell and M. Beller, Nat. Commun., 2014, 5, 3091 Search PubMed
. -
(a) L. Zhang, J. Cheng, T. Ohishi and Z. Hou, Angew. Chem., Int. Ed., 2010, 49, 8670 CrossRef CAS PubMed
;
(b) I. I. F. Boogaerts, G. C. Fortman, M. R. L. Furst, C. S. J. Cazin and S. P. Nolan, Angew. Chem., Int. Ed., 2010, 49, 8674 CrossRef CAS PubMed
;
(c) I. I. F. Boogaerts and S. P. Nolan, J. Am. Chem. Soc., 2010, 132, 8858 CrossRef CAS PubMed
;
(d) H. Mizuno, J. Takaya and N. Iwasawa, J. Am. Chem. Soc., 2011, 133, 1251 CrossRef CAS PubMed
;
(e) H. Inomata, K. Ogata, S. I. Fukuzawa and Z. Hou, Org. Lett., 2012, 14, 3986 CrossRef CAS PubMed
. - S. Tanaka, K. Watanabe, Y. Tanaka and T. Hattori, Org. Lett., 2016, 18, 2576 CrossRef CAS PubMed
. - H. Togo, Advanced Free Radical Reactions for Organic Synthesis, Elsevier, Amsterdam, 2004 Search PubMed
. -
(a) D. M. Schultz and T. P. Yoon, Science, 2014, 343, 985 CrossRef CAS PubMed
;
(b) J. M. R. Narayanam and C. R. J. Stephenson, Chem. Soc. Rev., 2011, 40, 102 RSC
;
(c) Y. Xi, H. Yi and A. W. Lei, Org. Biomol. Chem., 2013, 11, 2387 RSC
;
(d) C. K. Prier, D. A. Rankic and D. W. C. MacMillan, Chem. Rev., 2013, 113, 5322 CrossRef CAS PubMed
;
(e) M. N. Hopkinson, B. Sahoo, J. L. Li and F. Glorius, Chem.–Eur. J., 2014, 20, 3874 CrossRef CAS PubMed
;
(f) L. Shi and W. J. Xia, Chem. Soc. Rev., 2012, 41, 7687 RSC
;
(g) T. P. Yoon, M. A. Ischay and J. Du, Nat. Chem., 2010, 2, 527 CrossRef CAS PubMed
. - M. Majek, F. Filace and A. J. von Wangelin, Beilstein J. Org. Chem., 2014, 10, 981 CrossRef CAS PubMed
. -
(a) A. K. Yadav, V. P. Srivastava and L. D. S. Yadav, New J. Chem., 2013, 37, 4119 RSC
;
(b) V. P. Srivastava, A. K. Yadav and L. D. S. Yadav, Synlett, 2013, 24, 465 CrossRef CAS
;
(c) J. Zhang, L. Wang, Q. Liu, Z. Yang and Y. Huang, Chem. Commun., 2013, 49, 11662 RSC
;
(d) M. Majek and A. J. von Wanglin, Chem. Commun., 2013, 49, 5507 RSC
;
(e) D. P. Hari, P. Schroll and B. König, J. Am. Chem. Soc., 2012, 134, 2958 CrossRef CAS PubMed
;
(f) D. P. Hari, T. Hering and B. König, Org. Lett., 2012, 14, 5334 CrossRef CAS PubMed
;
(g) Y. Q. Zou, J. R. Chen, X. P. Liu, L. Q. Lu, R. L. Davis, K. A. Jørgensen and W. J. Xiao, Angew. Chem., Int. Ed., 2012, 51, 784 CrossRef CAS PubMed
;
(h) K. Fidaly, C. Ceballos, A. Falguières, M. S. I. Veitia, A. Guy and C. Ferroud, Green Chem., 2012, 14, 1293 RSC
;
(i) M. Neumann, S. Füldner, B. König and K. Zeitler, Angew. Chem., Int. Ed., 2011, 50, 951 CrossRef CAS PubMed
;
(j) D. P. Hari and B. König, Org. Lett., 2011, 13, 3852 CrossRef CAS PubMed
. - For recent reviews of cobalt-catalyzed C–H bond functionalization, see:
(a) M. Moselage, J. Li and L. Ackermann, ACS Catal., 2016, 6, 498 CrossRef CAS
;
(b) D. Wei, X. Zhu, J. L. Niu and M. P. Song, ChemCatChem, 2016, 8, 1242 CrossRef CAS
;
(c) T. K. Hyster, Catal. Lett., 2015, 145, 458 CrossRef CAS
;
(d) O. Daugulis, J. Roane and L. D. Tran, Acc. Chem. Res., 2015, 48, 1053 CrossRef CAS PubMed
. - M. Majek and A. J. von Wangelin, Chem. Commun., 2013, 49, 5507 RSC
. -
(a) J. D. Nguyen, J. W. Tucker, M. D. Konieczynska and C. R. J. Stephenson, J. Am. Chem. Soc., 2011, 133, 4160 CrossRef CAS PubMed
;
(b) C. J. Wallentin, J. D. Nguyen, P. Finkbeiner and C. R. J. Stephenson, J. Am. Chem. Soc., 2012, 134, 8875 CrossRef CAS PubMed
;
(c) C. Dai, J. M. R. Narayanam and C. R. J. Stephenson, Nat. Chem., 2011, 3, 140 CrossRef CAS PubMed
;
(d) M. Pirtsch, S. Paria, T. Matsuno, H. Isobe and O. Reiser, Chem.–Eur. J., 2012, 18, 7336 CrossRef CAS PubMed
;
(e) E. Arceo, E. Montroni and P. Melchiorre, Angew. Chem., Int. Ed., 2014, 53, 12064 (Angew. Chem., Int. Ed., 2014, 126, 12260) CrossRef CAS PubMed
. - Q. Q. Yang, M. Marchini, W. J. Xiao, P. Ceroni and M. Bandini, Chem.–Eur. J., 2015, 21, 18052 CrossRef CAS PubMed
. - Q. Kong, M. Wulff, J. H. Lee, S. Bratos and H. Ihee, J. Am. Chem. Soc., 2007, 129, 13584 CrossRef CAS PubMed
. -
(a) N. Assaf-Anld, K. F. Hayes and T. M. Vogel, Environ. Sci. Technol., 1994, 28, 246 CrossRef PubMed
;
(b) P. Chunchiu and M. Reinhard, Environ. Sci. Technol., 1996, 30, 1882 CrossRef
. - H. Yi, L. B. Niu, C. l. Song, Y. Y. Li, B. Dou, A. K. Singh and A. W. Lei, Angew. Chem., Int. Ed., 2016, 56, 1120 CrossRef PubMed
. -
(a) H. Shimakoshi and Y. Hisaeda, Angew. Chem., Int. Ed., 2015, 54, 15439 CrossRef CAS PubMed
;
(b) H. Shimakoshi, Z. Luo, T. Inaba and Y. Hisaeda, Dalton Trans., 2016, 45, 10173 RSC
. -
(a) R. Tomita, Y. Yasu, T. Koike and M. Akita, Angew. Chem., Int. Ed., 2014, 53, 7144 CrossRef CAS PubMed
;
(b) N. Kornblum, J. W. Powers, G. J. Anderson, W. J. Jones, H. O. Larson, O. Levand and W. M. Weaver, J. Am. Chem. Soc., 1957, 79, 6562 CrossRef CAS
;
(c) M. A. Khuddus and D. Swern, J. Am. Chem. Soc., 1973, 95, 8393 CrossRef CAS
;
(d) A. J. Mancuso and D. Swern, Synthesis, 1981, 165 CrossRef CAS
;
(e) Y. Ashikari, T. Nokami and J.-I. Yoshida, J. Am. Chem. Soc., 2011, 133, 11840 CrossRef CAS PubMed
;
(f) Y. Ashikari, A. Shimizu, T. Nokami and J. I. Yoshida, J. Am. Chem. Soc., 2013, 135, 16070 CrossRef CAS PubMed
. - J. Z. Zhang and Y. Tang, Adv. Synth. Catal., 2016, 358, 752 CrossRef CAS
. - D. F. Taber and C. G. Nelson, J. Org. Chem., 2006, 71, 8973 CrossRef CAS PubMed
. - R. Kumar, A. Sharma, N. Sharma, V. Kumar and A. K. Sinha, Eur. J. Org. Chem., 2008, 2008, 5577 CrossRef
. - J. Waser, B. Gaspar, H. Nambu and E. M. Carreira, J. Am. Chem. Soc., 2006, 128, 11693 CrossRef CAS PubMed
. - C. Gioia, A. Hauville, L. Bernardi, F. Fini and A. Ricci, Angew. Chem., Int. Ed., 2008, 120, 9376 CrossRef
. - M. L. Salum, C. J. Robles and R. Erra-Balsells, Org. Lett., 2010, 12, 4808 CrossRef CAS PubMed
. - T. Fukuyama, M. Arai, H. Matsubara and I. Ryu, J. Org. Chem., 2004, 69, 8105 CrossRef CAS PubMed
. - C. Pardin, J. N. Pelletier, W. D. Lubell and J. W. Keillor, J. Org. Chem., 2008, 73, 5766 CrossRef CAS PubMed
. - W. Szymanski, B. Wu, B. Weiner, S. de Wildeman, B. L. Feringa and D. B. Janssen, J. Org. Chem., 2009, 74, 9152 CrossRef CAS PubMed
. - T. Thiemann, M. W. Elshorbagy, M. H. F. A. Salem, S. A. N. Ahmadani, Y. Al-Jasem, M. A. Azani, M. A. M. Al-Sulaibi and B. Al-Hindawi, Int. J. Org. Chem., 2016, 6, 126 CrossRef CAS
. - J. Takaya, S. Tadami, K. Ukai and N. Iwasawa, Org. Lett., 2008, 10, 2697 CrossRef CAS PubMed
. - M. S. Kharasch, E. V. Jensen and W. H. Urry, J. Am. Chem. Soc., 1946, 68, 154 CrossRef CAS
. - S. Li, W. Yuan and S. Ma, Angew. Chem., Int. Ed., 2011, 50, 2578 CrossRef CAS PubMed
. - M. Bellassoued, S. Mouelhi, P. Fromentin and A. Gonzalez, J. Org. Chem., 2005, 690, 2172 CrossRef CAS
. - T. Mita, K. Suga, K. Sato and Y. Sato, Org. Lett., 2015, 17, 5276 CrossRef CAS PubMed
. - G. F. Xua, X. L. Yang, B. B. Jiang, P. Lei, X. L. Liu, Q. M. Wang, X. B. Zhang and Y. Ling, Bioorg. Med. Chem. Lett., 2016, 26, 1849 CrossRef PubMed
. - N. Mupparapu, S. Khan, S. Battula, M. Kushwaha, A. P. Gupta, Q. N. Ahmed and R. A. Vishwakarma, Org. Lett., 2014, 16, 1152 CrossRef CAS PubMed
. - A. H. Fenselau and J. G. Moffatt, J. Am. Chem. Soc., 1966, 88, 1762 CrossRef CAS
.
Footnote |
† Electronic supplementary information (ESI) available. See DOI: 10.1039/c6ra28744a |
|
This journal is © The Royal Society of Chemistry 2017 |
Click here to see how this site uses Cookies. View our privacy policy here.