DOI:
10.1039/C7RA08900G
(Paper)
RSC Adv., 2017,
7, 48208-48213
Ultra-deep oxidative desulfurization of fuel with H2O2 catalyzed by molybdenum oxide supported on alumina modified by Ca2+†
Received
11th August 2017
, Accepted 9th October 2017
First published on 13th October 2017
Abstract
A highly active catalyst of molybdenum oxide supported on mesoporous alumina modified by Ca2+ was synthesized by an in situ method and applied in the catalytic oxidative desulfurization (CODS) system. This catalyst was characterized by FT-IR, XRD, BET and XPS. The influences of m(catalyst)/m(model oil), V(H2O2)/V(model oil), reaction temperature and reaction time on oxidative desulfurization of 4,6-dimethyldibenzothiophene (4,6-DMDBT), dibenzothiophene (DBT) and benzothiophene (BT) were investigated. This catalyst has high desulfurization activity in the removal of organic sulfides under mild conditions. The catalytic oxidation reactivity of sulfur-containing compounds is in the order of DBT > 4,6-DMDBT > BT. The kinetic studies reveal that the oxidative desulfurization of the organic sulfides can present a pseudo first-order kinetic process, and the apparent activation energies of 4,6-DMDBT, DBT and BT are 34.67 kJ mol−1, 33.01 kJ mol−1 and 40.16 kJ mol−1, respectively. The recycling experiments indicate that 4,6-DMDBT, DBT and BT removal can still reach 90.0%, 89.9% and 87.3% after eight cycles.
1. Introduction
Nowadays, manufacturing of ultra-low sulfur fuels has caused worldwide research general concern.1,2 Sulfur oxides and sulfate particulates are produced in the combustion process of the sulfur organic compounds in fuel oil, which comes amid fears, creating environmental pollution such as acid rain.3 Explosion engines are also etched because of these sulfur organic compounds in fuel oil.4 Furthermore, these hazardous substances produced from the sulfur organic compounds in fuel oil also play an important role in contaminating the catalysts for tail gas treatment in catalytic converters.5 Thus, the oil refinery industry is facing more stringent environmental regulations and laws all over the world. In order to meet the requirements of environmental protection, various of desulfurization methods were developed.
Conventionally, hydrodesulfurization (HDS) is the most important technology for removal of the sulfur compounds from fuel oil in the oil refinery industry. However, HDS process usually needs harsh reaction conditions including high temperatures, high pressures and huge amounts of hydrogen. HDS is high efficiency in removing of thiols, sulfides, disulfides, and some thiophenic compounds, but it is hard to remove the refractory sulfur compounds such as 4,6-dimethyldibenzothiophene (4,6-DMDBT), dibenzothiophene (DBT) and benzothiophene (BT).6–9 In order to solve these problems in hydrodesulfurization process, some other supplementary desulfurization methods were researched extensively, such as oxidative desulfurization (ODS),10 adsorption desulfurization,11 alkylation desulfurization,12 biodesulfurization13 and so on. ODS is considered to be a promising method for ultra-deep desulfurization under mild conditions because it is efficient and economical.14 In ODS, non-polar organic sulfides are oxidized by oxidizing agent to their homologous sulfones under catalysts and then remove it by rectification, extraction, adsorption or other separation operation.15
In recent years, various oxidizing agents such as oxygen,16 ozone,17 hydrogen peroxide,18 cumene hydroperoxide (CHP),19 tertiary butyl hydroperoxide (t-BuOOH)20 have been used for the oxidative desulfurization. However, hydrogen peroxide is more popular than the other oxidants due to the environmental friendliness, safety, high oxidation capacity and high selectivity. A number of homogenous and heterogeneous catalysts are developed in diverse ODS systems in order to increase the oxidation activity of the oxidizing agent, for example, sodium bicarbonate,21 organic acids,22 polyoxometalates,23 molecular sieve,24 molybdenum oxide25 and so on. Among these, molybdenum oxide have been extensively researched and employed because of its good performance in the CODS system. Such as, Jia and coworkers26 reported an efficient oxidative desulfurization with MoO3 as the active phase and H2O2 as oxidant under mild and solvent free conditions. García-Gutiérrez and coworkers1 reported that Mo/γAl2O3 as the catalyst and H2O2 as oxidant in the CODS. The sulfur level of diesel fuel can be reduced from about 320 to less than 10 ppmw at 60 °C under atmospheric pressure. Meanwhile, the catalyst support also shows great effects on catalytic oxidative desulfurization. Silica,27 titanium dioxide,28 active carbon29 and alumina (Al2O3)30 as the catalyst supports have been widely investigated. From the perspective of application, Al2O3 has received much attention in both academia and industry community because of its good mechanical properties, adjustable pore structure and high resistance to attrition. Such as, Wang et al.31 used t-BuOOH as oxidant in DBT ODS in a flow-type fixed-bed reactor. They found that Al2O3 as catalyst supports showed higher catalytic activity than those supported on TiO2 and SiO2. Al2O3 is also easy to synthesize and a cheap material compared to other supports. The study found that the introduction of different kinds of promoters can adjust surface acidity and pore structure in a wide range and increase the activity and selectivity of the catalysts. Lanthanides and transition metal elements are the common promoters of catalysts in the oxidation desulfurization system. There are many reports about them. For instance, Zhang and coworkers32 synthesized the catalyst MoO3/SiO2 with the modification of La3+ and applied it in the catalytic oxidative desulfurization system. Yan and coworkers33 reported that mesoporous HPW/SiO2 modified with Ag species was used as the catalyst for the oxidative desulfurization of both model and real diesel oils. However, there are few studies about alkali-earth metal elements as the promoters of catalysts in the oxidation desulfurization system.
In this work, molybdenum oxide was loaded on the mesoporous alumina by in situ synthesis method using the alkali-earth metal Ca2+ as the promoter. The catalytic reaction conditions m(catalyst)/m(model oil), V(H2O2)/V(model oil), reaction temperature and reaction time, kinetic studies of the catalytic oxidation and reuse of the catalyst were investigated in the oxidative desulfurization of the model fuel oil. The results indicated that the mesoporous alumina loaded MoO3 materials of Ca2+ modified exhibited a high catalytic activity in the oxidation desulfurization system of 4,6-DMDBT, DBT and BT model fuel oil.
2. Experimental
2.1. Materials
All chemicals including ammonium molybdate, aluminium chloride, polyethylene oxide–polypropylene oxide–polyethylene oxide (F127), methanol, ethanol, ammonia, calcium nitrate, 4,6-dimethyldibenzothiophene (4,6-DMDBT), dibenzothiophene (DBT), benzothiophene (BT), n-octane, hydrogen peroxide (H2O2, 30% wt), were purchased from Sinopharm Chemical Reagent Co., Ltd.
2.2. Catalyst preparation
For the preparation of the catalysts, 3.17 g AlCl3, 0.67 g ammonium molybdate and 0.056 g calcium nitrate were firstly dissolved respectively in 5.0 ml deionized water to spare. Then 0.38 g F127 was added into a 62.0 ml mixed solution of deionized water, ethanol and ammonia (V(deionized water)
:
V(ethanol)
:
V(ammonia) = 20
:
10
:
1) in a 100 ml three-neck flask. After that, AlCl3, ammonium molybdate, and calcium nitrate were dropwise added in turn every 10 minutes and stirred at 1000 rpm. Next the mixture was continuously stirred for 1 h before aging for 4 h at room temperature, subsequently separated by filtration, thoroughly washed with deionized water and dried in a vacuum oven at 105 °C. Finally, the dried samples were calcined at 540 °C for 12 h and labeled as Ca/MoO3/Al2O3 (n(Mo)/n(Al) = 16.7%, n(Ca)/n(Mo) = 6.1%). The control group catalyst was prepared without calcium nitrate according to the above method and labeled as MoO3/Al2O3.
2.3. Characterization of the samples
FT-IR spectra (4000–500 cm−1) were recorded at room temperature on a Bruker VERTEX 70 FT-IR spectrometer using KBr in the ratio of 1
:
200. The X-ray diffraction (XRD) patterns were recorded on a Phillips Xpert Pro powder diffraction system using Cu Kα radiation with a Ni filter over the range 10° ≤ 2θ ≤ 90°. The pore structure of the catalysts were obtained from N2 adsorption isotherms which were obtained at −195.8 °C in the relative pressure range of 0.001–1 with a Quantachrome instrument for Quadrasorb SI. The X-ray photoelectron spectrum (XPS) measurements were performed with a Multilab 2000 X-ray photoelectron spectrometer (VG, UK) (see ESI†).
2.4. Catalytic oxidative desulfurization
The model fuel was prepared by dissolving a certain amount of 4,6-DMDBT, DBT and BT in n-octane to get the solution with a sulfur content of 400 μg g−1 respectively. The catalytic oxidation reaction was performed in a three necked glass flask with a condenser, stirrer and thermometer. In these experiments, 10.0 ml of the model fuel oil and a certain amount of catalyst were put into the reactor, which were placed in a water bath at a constant temperature. When the reaction mixture was heated to the set temperature, a certain amount of hydrogen peroxide was added into the mixture, and the reaction was kept at the set temperature under stirring at 1000 rpm for a certain time. Then the mixture was rapidly cooled down to room temperature and separated by centrifugation. The reaction products were analyzed by GC-FID equipped with a HP-5 capillary column.
3. Results and discussion
3.1. Oxidative desulfurization of the model fuel oil
In order to verify the CODS activity, the catalytic oxidative desulfurization of the 4,6-DMDBT, DBT and BT model fuel oil was performed with the catalyst Ca/MoO3/Al2O3. The effect of mass ratio of catalyst/model oil on 4,6-DMDBT, DBT and BT removal rate of the 10 ml model oil was shown in Fig. 1. Clearly, with the increase of catalyst amount, the oxidative removals of 4,6-DMDBT, DBT and BT increased gradually and then reached a plateau. When m(catalyst)/m(model oil) reached 0.56% for 4,6-DMDBT or DBT (and 0.70% for BT), the removal rate of the sulfur compound was close to 100.0%. The conversion of 4,6-DMDBT or DBT was higher than that of BT with the same amount of catalyst.
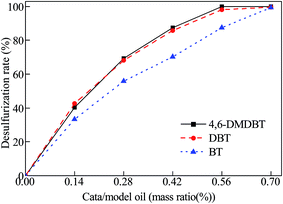 |
| Fig. 1 Effect of catalyst/model oil on 4,6-DMDBT, DBT and BT removal. Reaction conditions for 4,6-DMDBT removal: V(H2O2)/V(model oil) = 0.20%, 55 °C, 10 min; reaction conditions for DBT removal: V(H2O2)/V(model oil) = 0.20%, 55 °C, 8 min; reaction conditions for BT removal: V(H2O2)/V(model oil) = 0.20%, 55 °C, 16 min. | |
The effect of volume ratio of H2O2/model oil on 4,6-DMDBT, DBT and BT removal rate of the 10 ml model oil is shown in Fig. 2. When V(H2O2)/V(model oil) reached 0.2% (n(O/S) = 2.3), the removal rate of 4,6-DMDBT, DBT and BT was close to 100.0%. However, when V(H2O2)/V(model oil) got up to more than 0.2%, the removal rate of 4,6-DMDBT, DBT and BT decreased significantly. It is probably because excess H2O2 caused a side reaction catalyzed by Mo and produced excess H2O. On the one hand, the side reaction occupied the active center and increased the consumption of H2O2.34 On the other hand, a percentage of the hydrophilic catalyst was transferred to the water phase, thus reducing the catalyst dispersed in the oil phase.34 This resulted the reduction of the desulfurization rate.
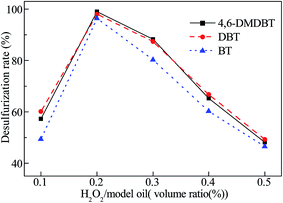 |
| Fig. 2 Effect of H2O2/model oil on 4,6-DMDBT, DBT and BT removal. Reaction conditions for 4,6-DMDBT removal: m(catalyst)/m(model oil) = 0.56%, 55 °C, 10 min; reaction conditions for DBT removal: m(catalyst)/m(model oil) = 0.56%, 55 °C, 8 min; reaction conditions for BT removal: m(catalyst)/m(model oil) = 0.70%, 55 °C, 16 min. | |
The effect of reaction temperature and reaction time on 4,6-DMDBT, DBT and BT removal rate of the 10 ml model oil is shown in Fig. 3. The experimental results show that both enhancing reaction temperature and prolonging reaction time are advantageous to the removal rate of model fuel oil. The higher reaction temperature improved the performance of catalyst greatly, because the higher temperature aggravated the molecules thermal motion, meanwhile the formation quantity of the metallic peroxide species which were produced by the hydrogen peroxide and molybdenum oxide in the catalyst in a unit time increased with increasing of reaction temperature.35 At 55 °C, the oxidative removal rate of 4,6-DMDBT, DBT and BT were close to 100.0% only in 10 min, 8 min and 16 min, respectively. Meanwhile, under the same reaction conditions, the oxidative removal rate of 4,6-DMDBT, DBT and BT catalyzed with MoO3/Al2O3 were 64.4%, 68.3%, 53.9%, respectively. This showed that the desulfurization rate of 4,6-DMDBT, DBT and BT catalyzed with Ca/MoO3/Al2O3 was higher than with MoO3/Al2O3 under the same conditions. The results indicated that oxidation reactivities of these sulfur compounds decreased in the order of DBT > 4,6-DMDBT > BT under the same reaction conditions. This was because of the lower electron density of the sulfur atom on BT (5.739). As calculated by Otsuki et al.36 The electron densities on sulfur atoms are 5.760 for 4,6-DMDBT and 5.758 for DBT. Therefore, it was clearly demonstrated that 4,6-DMDBT and DBT can be oxidized more easily than that of BT. The electron density of the sulfur atom on 4,6-DMDBT is higher than that of DBT, however, 4,6-DMDBT has two methyl groups, as well as the higher steric hindrance. As a result, the reactivity of DBT was higher than that of 4,6-DMDBT. When catalyzed by Ca/MoO3/Al2O3, the oxidative removal rate of DBT was close to 100.0% under 55 °C after 8 min. Chang and coworkers37 reported that oxidation of dibenzothiophene with CHP on MoO3/SiO2 modified with alkaline earth metals. The DBT conversions on MoO3/Ca–SiO2 catalysts was the highest (95%) at 60 °C, 4 h and O/S molar ratio 3.0. It shows that the catalyst Ca/MoO3/Al2O3 prepared in this research has higher activity than other catalysts in ODS.
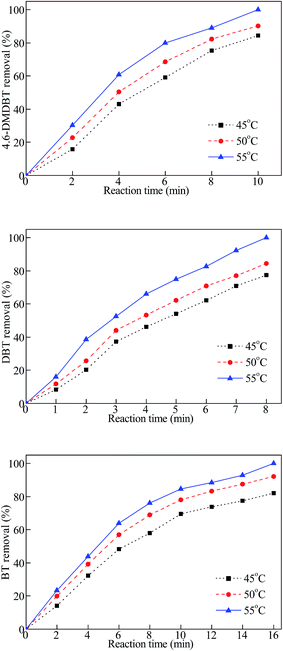 |
| Fig. 3 Effect of reaction time on 4,6-DMDBT, DBT and BT removal. Reaction conditions for 4,6-DMDBT removal: m(catalyst)/m(model oil) = 0.56%, V(H2O2)/V(model oil) = 0.20%; reaction conditions for DBT removal: m(catalyst)/m(model oil) = 0.56%, V(H2O2)/V(model oil) = 0.20%; reaction conditions for BT removal: m(catalyst)/m(model oil) = 0.70%, V(H2O2)/V(model oil) = 0.20%. | |
3.2. Apparent activation energy and reaction rate constant
The reaction rates determined at different temperatures were summarized in Table 1. The apparent activation energies for the CODS reactions (Fig. 4) were calculated by the Arrhenius equation. The results indicated that the CODS reactions fitted pseudo first order reaction kinetics. As can be seen from Fig. 4, the activation energies of 4,6-DMDBT, DBT and BT oxidation reactions were 34.67 kJ mol−1, 33.01 kJ mol−1 and 40.16 kJ mol−1, respectively. The activation energies of DBT and 4,6-DMDBT are lower than that of BT, which proves the easier oxidation of DBT and 4,6-DMDBT. M. A. Safa and coworkers4 reported that the apparent activation energy of DBT in the MoO3/Al2O3–CHP catalytic system was 67.5 kJ mol−1. The experiment and comparison results indicate that the mesoporous Ca/MoO3/Al2O3–H2O2 catalytic system in the present work displays the higher catalytic activity.
Table 1 Reaction rate constant (k) and correlation coefficient (R2) for oxidation reaction of 4,6-DMDBT, DBT and BT at different temperatures
Sample |
t (°C) |
k (min−1) |
R2 |
DBT |
45 |
0.201 |
0.981 |
DBT |
50 |
0.247 |
0.985 |
DBT |
55 |
0.294 |
0.992 |
BT |
45 |
0.119 |
0.989 |
BT |
50 |
0.154 |
0.993 |
BT |
55 |
0.190 |
0.989 |
4,6-DMDBT |
45 |
0.189 |
0.977 |
4,6-DMDBT |
50 |
0.235 |
0.981 |
4,6-DMDBT |
55 |
0.283 |
0.987 |
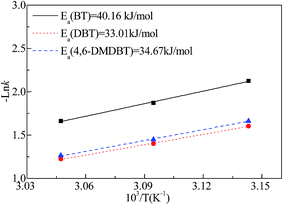 |
| Fig. 4 Arrhenius activation energies for 4,6-DMDBT, DBT and BT oxidation. | |
3.3. Analysis of oxidation product
For analysis the oxidation product, GC-MS was used to research the 4,6-DMDBT, DBT and BT oxidation reaction process catalyzed by Ca/MoO3/Al2O3. After the oxidation reaction, the oil phase and the solid catalyst were separated by centrifugation. After that the catalyst was extracted by methanol. In the end, the methanol phase were analyzed by GC-MS. Fig. 5 shows that MS spectra of oxidized product of 4,6-DMDBT, DBT and BT. The peak observed in the MS spectra at m/z = 244.2, 216.0 and 166.1 were belonged to the molecular ion peak of 4,6-dimethyldibenzothiophene sulfone (4,6-DMDBTO2), dibenzothiophene sulfone (DBTO2) and benzothiophene sulfone (BTO2). By comparison with standard NIST data, 4,6-DMDBT, DBT and BT were oxidized to corresponding sulfone 4,6-DMDBTO2, DBTO2 and BTO2 can be authenticated. Meanwhile, no sulfur and sulfone compounds were detected in oil phase by GC-MS. The experimental result indicated that the oxidation product of 4,6-DMDBT, DBT and BT were 4,6-DMDBTO2, DBTO2 and BTO2, which were adsorbed by the solid catalyst because of its highly polar nature.
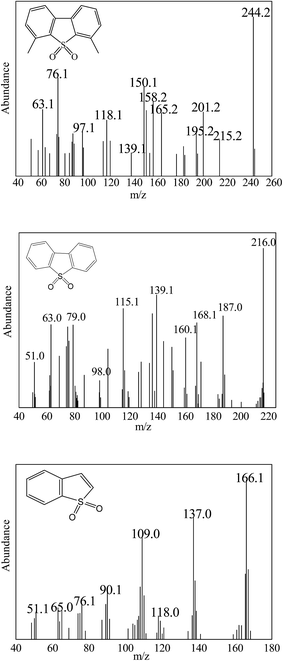 |
| Fig. 5 MS spectra of oxidized product of 4,6-DMDBT, DBT and BT. | |
3.4. Reuse cycles of the catalysts
After each CODS run, the catalyst Ca/MoO3/Al2O3 could be separated by centrifugation. The filter was washed with methanol and then dried at 105 °C in a vacuum drying oven for 12 h. Then the catalyst was charged again with the same volumes of fresh H2O2 solution and model oil for the next cycle. The stability of catalytic system after regeneration was shown in Fig. 6, indicating that Ca/MoO3/Al2O3 has a good recycling performance in the CODS process. After eight recycling, the conversion rates of 4,6-DMDBT, DBT and BT decreased to 90.0%, 89.9% and 87.3%. At the same time, the Mo content in the catalysts before and after the oxidation reaction decreased from 29.4% to 28.3% by ICP-AES. Such a result indicated that weak leaching of MoO3 occurs throughout the CODS process, which resulted in a slight decrease in the desulphurization activity after reused eight times of the catalyst.
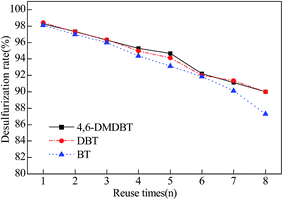 |
| Fig. 6 Effect of reuse times on the oxidative desulfurization rate of 4,6-DMDBT, DBT and BT. | |
4. Conclusion
An amorphous Ca/MoO3/Al2O3 has been prepared and utilized with H2O2 in the CODS system. The advantages of the mesoporous material are low produce cost and simple operation process. The Ca/MoO3/Al2O3 catalyst exhibited higher desulfurization activity for the oxidation of 4,6-DMDBT, DBT and BT under mild conditions. And the catalytic oxidation activity of the sulfur-containing compounds occurred in the following order: DBT > 4,6-DMDBT > BT. The kinetic studies indicated that the oxidative desulfurization of 4,6-DMDBT, DBT and BT was pseudo-first-order reaction. The activation energies of 4,6-DMDBT, DBT and BT were 34.67 kJ mol−1, 33.01 kJ mol−1 and 40.16 kJ mol−1, respectively. GC-MS analysis demonstrated that 4,6-DMDBTO2, DBTO2 and BTO2 were the only products of 4,6-DMDBT, DBT and BT oxidation, which were adsorbed by the catalyst. The recycling experiments of Ca/MoO3/Al2O3 indicated that 4,6-DMDBT, DBT and BT removal still reached 90.0%, 89.9% and 87.3% after 8 cycles.
Conflicts of interest
There are no conflicts to declare.
Acknowledgements
This work was financially supported by the National Natural Science Foundation (No. 21473126).
References
- J. L. García-Gutiérrez, G. A. Fuentes and M. E. Hernández-Terán, et al., Appl. Catal., A, 2008, 334(1–2), 366–373 CrossRef.
- C. Zou, P. Zhao and J. Ge, et al., Fuel, 2013, 104, 635–640 CrossRef CAS.
- J. M. Campos-Martin, M. C. Capel-Sanchez and P. Perez-Presas, et al., J. Chem. Technol. Biotechnol., 2010, 85(7), 879–890 CrossRef CAS.
- M. A. Safa and X. Ma, Fuel, 2016, 171, 238–246 CrossRef CAS.
- A. Stanislaus, A. Marafi and M. S. Rana, Catal. Today, 2010, 153(1–2), 1–68 CrossRef CAS.
- R. M. Casagrande, W. K. Meerbott and A. F. Sartor, et al., Ind. Eng. Chem., 1955, 47(4), 744–749 CrossRef CAS.
- W. Lai, Z. Chen and J. Zhu, et al., Nanoscale, 2016, 8(6), 3823 RSC.
- L. Wang, Y. Wang and Y. Liu, et al., Microporous Mesoporous Mater., 2008, 113(1–3), 435–444 CrossRef CAS.
- L. Yang, X. Li and A. Wang, et al., J. Catal., 2015, 330, 330–343 CrossRef CAS.
- S. Otsuki, T. Nonaka and N. Takashima, et al., Energy Fuels, 2015, 14(6), 750–753 Search PubMed.
- K. S. Triantafyllidis and E. A. Deliyanni, Chem. Eng. J., 2014, 236(2), 406–414 CrossRef CAS.
- W. Rong, J. Wan and Y. Li, et al., Fuel, 2015, 143, 504–511 CrossRef.
- M. Agarwal, P. K. Dikshit and J. B. Bhasarkar, et al., Chem. Eng. J., 2016, 295, 254–267 CrossRef CAS.
- A. W. Bhutto, R. Abro and S. Gao, et al., J. Taiwan Inst. Chem. Eng., 2016, 62, 84–97 CrossRef CAS.
- I. V. Babich and J. A. Moulijn, Fuel, 2003, 82(6), 607–631 CrossRef CAS.
- S. Murata, K. Murata and A. Koh Kidena, et al., Energy Fuels, 2004, 18(1), 116–121 CrossRef CAS.
- J. Wang, D. Zhao and K. Li, Energy Fuels, 2010, 24(4), 2527–2529 CrossRef CAS.
- G. Yu, S. Lu and H. Chen, et al., Energy Fuels, 2005, 19(2), 447–452 CrossRef CAS.
- X. Han, A. Wang and X. Wang, et al., Catal. Commun., 2013, 42(23), 6–9 CrossRef CAS.
- N. A. W. M. Wan, A. W. A. B. Wan and R. Ali, et al., Clean Technol. Environ. Policy, 2015, 17(6), 1487–1497 CrossRef.
- A. D. Bokare and W. Choi, J. Hazard. Mater., 2016, 304, 313–319 CrossRef CAS PubMed.
- D. Bunthid, P. Prasassarakich and N. Hinchiranan, Fuel, 2010, 89(9), 2617–2622 CrossRef CAS.
- W. Trakarnpruk and K. Rujiraworawut, Fuel Process. Technol., 2009, 90(3), 411–414 CrossRef CAS.
- Q. Du, Y. Guo and H. Duan, et al., Fuel, 2017, 188, 232–238 CrossRef CAS.
- J. L. García-Gutiérrez, G. A. Fuentes and M. E. Hernández-Terán, et al., Appl. Catal., A, 2006, 305(1), 15–20 CrossRef.
- Y. Jia, G. Li and G. Ning, Fuel Process. Technol., 2011, 92(1), 106–111 CrossRef CAS.
- P. Yang, S. Zhou and Y. Du, et al., RSC Adv., 2016, 6(59), 53860–53866 RSC.
- X. Wang, F. Li and J. Liu, et al., Energy Fuels, 2012, 26(11), 6777–6782 CAS.
- K. G. Haw, A. W. A. B. Wan and R. Ali, et al., Fuel Process. Technol., 2010, 91(9), 1105–1112 CrossRef CAS.
- Y. Tian, Y. Yao and Y. Zhi, et al., Energy Fuels, 2015, 29(2), 150126070926009 CrossRef.
- D. Wang, E. W. Qian and H. Amano, et al., Appl. Catal., A, 2003, 253(1), 91–99 CrossRef CAS.
- Y. Zhang, J. Qiu and G. Wang, et al., Mater. Rev., 2013, 27, 75–79 CrossRef.
- X. M. Yan, S. U. Gao-Shen and L. Xiong, J. Fuel Chem. Technol., 2009, 37(3), 318–323 CrossRef CAS.
- Y. Tian, G. Wang and J. Long, et al., Chin. J. Catal., 2016, 37(12), 2098–2105 CrossRef CAS.
- J. Qiu, G. Wang and Y. Zhang, et al., Fuel, 2015, 147, 195–202 CrossRef CAS.
- S. Otsuki, T. Nonaka and N. Takashima, et al., Energy Fuels, 2000, 14(6), 750–753 CrossRef.
- J. Chang, A. Wang and J. Liu, et al., Catal. Today, 2010, 149(1), 122–126 CrossRef CAS.
Footnote |
† Electronic supplementary information (ESI) available: Additional experimental details. See DOI: 10.1039/c7ra08900g |
|
This journal is © The Royal Society of Chemistry 2017 |
Click here to see how this site uses Cookies. View our privacy policy here.