DOI:
10.1039/C8RA02214C
(Paper)
RSC Adv., 2018,
8, 17176-17182
Reusable magnetic PdxCoy nanoalloys confined in mesoporous carbons for green Suzuki–Miyaura reactions†
Received
13th March 2018
, Accepted 26th April 2018
First published on 10th May 2018
Abstract
We report herein PdxCoy nanoalloys confined in mesoporous carbons (Pdx–Coy@MC) prepared by an eco-friendly one-pot approach consisting in the co-assembly of readily available and non-toxic carbon precursors (phloroglucinol, glyoxal) with a porogen template (pluronic F-127) and metallic salts (H2PdCl4 and Co(NO3)2·6H2O) followed by thermal annealing. Three PdxCoy@MC materials with different alloy compositions were prepared (C1: x/y = 90/10; C2: x/y = 75/25; C3 and C4: x/y = 50/50). The nanoalloys were uniformly distributed in the carbon framework and the particle sizes depended on the alloy composition. These composites were then used for Suzuki–Miyaura reactions using either H2O or a 1
:
1 H2O/EtOH mixture as solvent. The Pd50Co50@MC catalyst C3 proved to be the most efficient catalyst (in terms of efficiency and magnetic recovery) affording the coupling products in good to excellent yields. After reaction, C3 was recovered quantitatively by simple magnetic separation and reused up to six times without loss of efficiency. The amount of palladium lost in the reaction mixture after magnetic separation was very low (ca. 0.1 % wt of the amount initially used).
A Introduction
The syntheses at an industrial scale of numerous compounds possessing important therapeutical (valsartan),1 fungicidal (boscalid)2 or physical (semiconductor materials for OLEDs)3 properties require often as a crucial step the creation of a carbon–carbon bond at the core of the molecule. The formation of new carbon–carbon bonds, and in particular aryl–aryl bonds, is traditionally performed using a Suzuki–Miyaura cross-coupling.4 This reaction is to date the most powerful and the most widely used for this purpose. It is generally performed in high yields and mild conditions by reacting an aryl bromide (sometimes an aryl chloride) with an areneboronic acid in the presence of a base and of a homogeneous palladium catalyst (ca. 10–50 mequiv.) containing in most cases a ligand.4a The major drawback of this cross-coupling lies in the use of palladium and of expensive ligands. It is noteworthy that no economically workable palladium ores exist: this precious metal is generally extracted as a byproduct from nickel, copper, chromium or other platinoids ores. Since palladium is a scarce natural resource with growing uses, its price has considerably increased: it was multiplied by 7 during the last 20 years to reach in late 2017 ca. 27 k€/kg (for comparison ca. 25 k€/kg for platinum and ca. 35 k€/kg for gold). For these reasons it is of crucial importance to preserve the palladium natural resources. In addition, residual amounts of palladium are often present in the coupling products. Therefore tedious and costly purification steps are often necessary to get the almost palladium-free product which is often required.5 For this purpose, during the last decade, numerous groups have developed heterogeneous reusable palladium catalysts.6 In most cases the precious metal is encapsulated in a polymeric shell,7 adsorbed on various inorganic supports or grafted to an organic or inorganic support bearing ligands.6 For example we have reported several polymer-supported reusable palladium catalysts for versatile carbon–carbon bond forming reactions.8 More recently magnetic palladium catalysts have emerged as a promising class of reusable catalysts since they can be recovered from any reaction mixture by simple application of an external magnetic field and reused.9 Most of them are obtained by grafting the palladium catalyst on a magnetic iron oxide (magnetite or maghemite) core surrounded by a polymer or a silica shell bearing ligands.10 Other reusable magnetic palladium catalysts are obtained by using a NiFe2O4
11 or cobalt core recovered by a carbon shell.12 However some drawbacks are still present: one of them is the multi-step preparation of these catalysts which can be tedious and/or requiring toxic and sensitive compounds; a second is the use of traditional organic solvents (DMF, toluene…) for reactions such as Suzuki–Miyaura. Consequently, in order to fulfil the criteria of Green Chemistry, the development of efficient eco-friendly and ligand-free reusable catalysts prepared in one pot from easily accessible starting materials and at least as efficient as their homogeneous analogues suscites huge interest. For example the group of Grison has recently reported Suzuki–Miyaura couplings in the presence of a heterogeneous palladium-containing carbon “ecocatalyst” obtained from plants able to bioconcentrate the precious metal.13 We have also recently reported a green one-pot synthesis of a mesoporous carbon (MC) containing palladium nanoparticles (Pd@MC) starting from a biosourced tannin precursor. This catalyst was successfully used for ligand-free Suzuki–Miyaura reactions in an environment-friendly and non-toxic solvent (propane-1,2-diol) but at high temperature (140 °C).14
In the last years bimetallic catalysts have emerged as a promising class of heterogeneous catalysts since the presence of two metals could bring new properties. It is important to note that the use of such catalysts for carbon–carbon bond forming reactions has only been very sparsely studied. For example, the group of Li has reported a reusable carbon-supported Fe–Pd core–shell catalyst for Suzuki–Miyaura reactions in DMF.15 Later Kutubi et al. have reported poly(N-vinyl-2-pyrrolidone)-stabilized Pd–Ru solid solutions and their use for Suzuki–Miyaura reactions in a 1
:
1 DMA/H2O mixture.16,17 In 2014 the group of Zhang has described a delicate preparation of Pd–Rh nanocrystals of tunable compositions and morphologies (via a hydrothermal approach) for Suzuki–Miyaura reactions.18 Inspired by our previous work on Pd@MC, we have developed a magnetic mesoporous carbon containing Pd–Fe alloys for Suzuki–Miyaura reactions in a green solvent (propane-1,2-diol)19 and, more recently, easy “one-pot synthesis” pathways to obtain metallic alloys (NiCo, PdNi, PdRh, PdAu, PdCo) confined in mesoporous carbons.20 From a practical point of view, the advantages of our MC preparation lie in the use of environment-friendly carbon precursors, in the simultaneous preparation of carbon and metallic alloys without using external chemical reduction agents and in its simplicity. It is noteworthy that the confinement of metal nanoparticles in mesoporous carbons with high surface area and controlled pore size suscites huge attention since it allows to obtain small and well dispersed metal nanoparticles, avoids particle coalescence by Ostwald maturation during the preparation and by chemical processes during use. Therefore this confinement has numerous applications.21,22 In addition, metal nanoparticles possessing magnetic properties are very interesting since they allow the recovery of the catalyst from almost any reaction medium by applying an external magnetic field. The PdCo alloys supported on carbons have already attracted attention as efficient electrocatalyst for formic acid oxidation, as catalyst in oxygen reduction reactions in fuel cells, hydrogen absorbent and as biosensor material.23 Herein we would like to report the use of mesoporous carbons containing confined PdxCoy nanoalloys as magnetic catalysts for Suzuki–Miyaura couplings under environment-friendly conditions.
B Results and discussion
Preparation and characterization of catalysts C1–C4
PdxCoy alloys confined in mesoporous carbons were obtained by a one-pot soft-template approach consisting in the co-assembly of phloroglucinol-glyoxal phenolic resin with an amphiphilic triblock co-polymer template (pluronic F-127) and Pd and Co salts. A thermal annealing step allowed the decomposition of the phenolic resin and template with formation of a porous carbon network containing PdCo nanoparticles (Fig. 1). The XRD patterns showed the presence of several peaks (Fig. 2) which could be indexed to a face-centered-cubic (fcc) crystalline structure of Pd. The position of the peaks was shifted towards higher 2θ angles compared to the reported values for single phase Pd, demonstrating the formation of PdCo alloys. The textural characteristics of the obtained materials were previously evaluated by nitrogen adsorption. The materials are micro/mesoporous and exhibit a specific surface area of 800–850 m2 g−1 and a mesopore average size of ca. 3.5 nm, almost independently of the alloy composition or annealing temperature as shown in more detail elsewhere.24
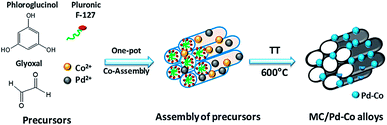 |
| Fig. 1 Schematic representation of the one-pot synthesis of mesoporous carbons containing confined particles. | |
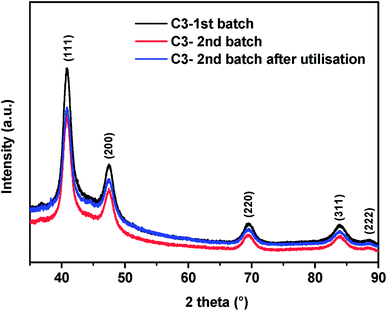 |
| Fig. 2 XRD patterns of two different batches of catalyst C3 before and after one use for Suzuki–Miyaura coupling. | |
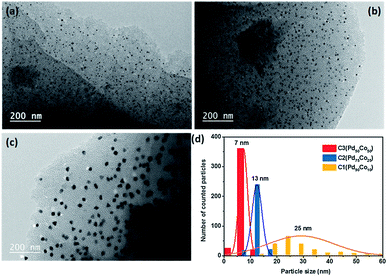 |
| Fig. 3 TEM images of catalysts C1–C3 (a–c) along with their particle size distribution (d). | |
The morphology of the materials was then studied by transmission electron microscopy (TEM) the images of the PdxCoy@MC materials (C1–C3) and their particle size distribution histograms are presented in Fig. 3. The catalysts exhibit homogenously distributed Pd–Co nanoparticles in the carbon network. A narrow particle size distribution is observed for Pd50Co50 C3 with an average particle size of ca. 7 nm. The particle size increased with the percentage of Pd in the alloy and reached 13 nm for Pd75Co25 (C2) while for a higher Pd content, a more important increase of both particle size (25 nm) and width of distribution was observed for Pd90Co10 (C1). Performing the thermal annealing at higher temperatures (800 °C) on Pd50Co50 (C4) increased the particle size from 7 nm for C3 to ∼11 nm for C4.
Optimization of the conditions for the Suzuki–Miyaura reaction
The reaction conditions were optimized (Table 1) using 4-bromoacetophenone and benzeneboronic acid as model substrates, K2CO3 as base and catalyst C3 (Pd50Co50). No reaction was observed by performing the cross-coupling in toluene, 1,4-dioxane or acetonitrile (entries 1–3). We then turned our attention to the use of green solvents. Gratifyingly the coupling product was obtained in respectively 92% and 98% yields by performing the reaction in 95
:
5 or 50
:
50 EtOH/H2O mixtures (entries 4 and 5) and even in 99% using water (entry 6). Reducing the amount of supported palladium from 10 to 5 and then 1 mequiv. resulted in a decrease of the yields from 99% to 75% and <10% (entries 7–8). Noteworthily after only 2 h, 6 h and 8 h of reaction the desired biaryl was respectively obtained in 8%, 81% and 90% yields (in the conditions of entry 6). Finally, the cross-coupling between 4-chloroacetophenone and benzeneboronic acid was unsuccessful and the aryl chloride was recovered in the conditions of entry 6.
Table 1 Optimization of the reaction conditions
Catalyst C3 was then replaced by C2 (Pd75Co25) or C1 (Pd90Co10) in order to evaluate the influence of PdCo alloy composition and particle size on the catalytic efficiency. The desired biaryl was obtained in almost quantitative yields (Table 1, entries 9 and 10). As expected it turned out that during the magnetic separation the catalysts C1 and C2 were more difficult to recover than C3, this being probably related to the lower amount of magnetic Co present in C2 and C1 alloys. This interpretation is sustained by our recent results on magnetic PdNi alloys confined in mesoporous carbon where we have shown that the magnetization value is closely related to the Ni content of the alloys.20c Finally the Suzuki–Miyaura coupling was performed in the presence of catalyst C4 (Pd50Co50 but obtained by calcination at 800 °C instead of 600 °C for C1–C3) affording almost quantitatively 1a (entry 11) which was somehow expected. We decided to pursue our study using catalyst C3 which possesses both good catalyst efficiency and good magnetic properties and is easier to prepare than C4.
Under the best reaction conditions we determined the possibility to reuse C3. For this purpose, at the end of the reaction C3 was almost quantitatively recovered by application of an external neodymium magnet (Fig. 4), washed with water, EtOH and dried. In addition, we found that C3 can be used successfully at least six times with no loss of efficiency (Table 2). The XRD analyses performed on the pristine C3 catalyst and after one catalytic utilisation (Fig. 2) showed almost perfect superposition of XRD peaks with no changes of either their position or their FWHM (full width at half maximum). This suggests that the alloy crystalline phase was conserved as well as the crystallite size which was found to be the same, ca. 6.0 nm, before and after use (Fig. 2). These results are in accordance with the good reusability of catalyst C3. We also measured the amount of palladium lost in the reaction product after magnetic recovery of C3. It turned out that only ca. 0.12% of the initial amount of supported palladium was present in the reaction medium (for further details on the determination of the residual amount of palladium see ESI†). This corresponds to ca. 12 μequiv. Besides, we checked if soluble palladium entities play a significant role in this Suzuki–Miyaura reaction. For this purpose a cross-coupling was performed between 4-bromoacetophenone and benzeneboronic acid in conditions of Table 1, entry 6. After 2 h 30 of reaction in refluxing water the catalyst was removed magnetically (yield at that point: 11%) and the rest of the reaction mixture was refluxed for another 12 h which brought the yield to 19%. This result showed that, in accordance with literature results,25 soluble palladium entities seem to play only a minor role in this reaction. We have also shown that the preparation of catalyst C3 is reproducible since various batches of this catalyst (all prepared according to the general procedure given in the Experimental part) present the same crystallite size (6.0 ± 0.5 nm) and catalytic activity. Finally catalyst C3 is air- and moisture-stable since it could be stored for months without particular precautions and showed no decrease of efficiency.
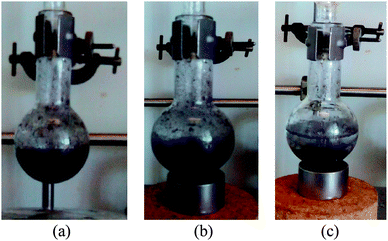 |
| Fig. 4 Magnetic separation of catalyst C3: (a) reaction mixture after reaction, (b) reaction mixture 10 s after placement of the magnet; (c) reaction mixture 2 min after placement of the magnet. | |
Table 2 Reuse of catalyst C3
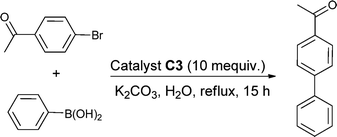
|
Reactions performed using 4-bromoacetophenone (0.5 mmol, 1 equiv.), benzeneboronic acid (0.55 mmol, 1.1 equiv.), K2CO3 (0.6 mmol, 1.2 equiv.) and catalyst C3 (25 mg, 10 mequiv.) in H2O (3 mL). Calculated yields by 1H-NMR of the crude reaction mixture. |
Runa |
1 |
2 |
3 |
4 |
5 |
6 |
Yieldb |
99 |
97 |
97 |
98 |
96 |
97 |
The scope of use of this catalyst for the Suzuki–Miyaura reaction was then determined under the previously optimized conditions (Table 3, entries 1–6). Reacting 4-bromoacetophenone with various areneboronic acids bearing electrodonating groups gave the expected biaryls in 99–86% yields (entries 1–4). The cross-coupling between 4-bromoacetophenone and 4-chlorobenzeneboronic acid afforded also successfully the corresponding biaryl in almost quantitative yield (entry 5). However the cross-couplings between 4-bromoacetophenone and 2-methyl- or 4-nitrobenzeneboronic acid or 3-thiopheneboronic acid were unsuccessful and in each case the aryl bromide was recovered unchanged. We also replaced 4-bromoacetophenone by other aryl bromides. To our surprise, under the conditions described in Table 3 entries 1–6, the yields were reproducible but extremely dependent on the nature of the aryl bromide: the cross-coupling between 4-bromopropiophenone and benzeneboronic acid (entry 6) afforded the corresponding biaryl in <40% yield whereas no reaction products were obtained by performing the cross-couplings with 4-bromobenzophenone, 4-bromobenzaldehyde, 4-bromobenzonitrile, 4-bromonitrobenzene, or 4-bromotoluene. It is noteworthy that these couplings have been performed several times with different batches of C3 and in each case the aryl bromide was recovered quantitatively. Gratifyingly we found that performing the reaction between 4-bromopropiophenone and benzeneboronic acid in a 50
:
50 H2O/EtOH mixture (method B) instead of pure H2O (method A) afforded the desired product in 98% yield (entry 7). These conditions were also successfully used for the cross-couplings between benzeneboronic acid and 4-bromobenzophenone, 4-bromobenzaldehyde, 4-bromobenzonitrile (entries 8–10). But, regretfully, no reactions were observed using either benzeneboronic acid and 4-bromonitrobenzene, 4-bromotoluene, 2- or 3-bromoacetophenone. On the bases of our results it was impossible for us to explain the outcome of the reaction.
Table 3 Syntheses of biaryls
Finally we compared the efficiency of catalyst C3 with other catalysts described in the literature (Table 4). It is noteworthy that most catalysts shown in this table are prepared via multi-step syntheses requiring toxic and sensitive starting materials whereas C3 is prepared in one-pot from “green” reagents. In addition our reaction was run using only water as solvent, albeit only in certain cases.
Table 4 TON and TOF of Suzuki–Miyaura reactions catalyzed by some representative magnetic Pd catalysts
Entry |
Catalyst |
Solvent, T °C |
Pd mequiv. |
TON |
TOF (h−1) |
1 |
C3 |
H2O, 100 °C |
10 |
100 |
7 |
2 26 |
Pd–Co/graphene |
EtOH, 80 °C |
40 |
24 |
12 |
3 27 |
Pd@(CoFe2O4) |
EtOH, 80 °C |
16 |
58 |
12 |
4 12a |
Pd@(Co/C-PPh2) |
EtOH, 80 °C |
0.05 |
19 600 |
980 |
5 12b |
Pd@(Co/C-polymer-PPh2) |
THF/H2O 1 : 2, 65 °C |
11 |
91 |
46 |
6 28 |
Pd@(Co/C–pyrene-PPh2) |
THF/H2O 2 : 5, 60 °C |
5 |
200 |
14 |
6 29 |
Ironoxide-Pd |
DMF, 50 °C |
73 |
14 |
1.1 |
7 30 |
Mag-IL-Pd |
H2O, 60 °C |
0.25–1 |
4000 |
667 |
8 31 |
Pd@(Fe2O3/SiO2-dendrimer) |
EtOH/H20 1 : 1, 80 °C |
0.2 |
4950 |
206 |
9 32 |
Pd@(Fe3O4/SiO2-iminophosphine) |
Toluene, 65 °C |
5 |
186 |
93 |
10 33 |
SPIONs-bis(NHC)-Pd |
DMF/H2O 1 : 2, 90 °C |
0.02 |
40 600 |
5800 |
C Experimental
Materials and methods
All reagents and solvents were obtained from commercial sources (Acros Organics, Sigma-Aldrich and Alfa Aesar) and were used without further purifications. Pluronic F-127 (Sigma-Aldrich) is a triblock copolymer of average formula (PEO)106(PPO)70(PEO)106. The silica gel was purchased from Merck and had a 0.063–0.2 mm granulometry (70–230 mesh ASTM). The external magnet used for magnetic separation was a S-25-07-N (Supermagnete, Uster, Switzerland).
Synthetic procedures
Preparation of catalyst C1–C424. PdxCoy@MC catalysts were prepared via a one-pot evaporation induced self-assembly (EISA) approach as described previously.24 Briefly, the carbon precursors, i.e., phloroglucinol and glyoxal, the porogen agent (pluronic F-127) and the metallic salts H2PdCl4 and Co(NO3)2·6H2O were dissolved in ethanol. The solution was placed in Petri dishes, evaporated and the obtained polymer film containing the metal salts was dried at 80 °C and pyrolysed at 600 °C under Ar. Different amounts of Pd and Co metallic salts were used in order to obtain different PdxCoy compositions, i.e., Pd90Co10 (C1), Pd75Co25 (C2), Pd50Co50 (C3). A supplementary sample having the composition of C3 (Pd50Co50) was in addition prepared but the thermal annealing was done at 800 °C, thus yielding C4. The total amount of metals in the catalyst was kept at ca. 5wt% of the carbon.
Suzuki–Miyaura reactions. Catalyst C3 (ca. 25 mg, 10 mequiv. of supported Pd) was added to a solution of aryl bromide (0.5 mmol, 1 equiv), areneboronic acid (0.55 mmol, 1.1 equiv.), K2CO3 (0.6 mmol, 1.2 equiv) in H2O (3 mL) or in a 1
:
1 H2O/EtOH mixture (3 mL). The reaction mixture was refluxed for 15 h. After cooling to 20 °C, C3 was magnetically recovered and then washed successively with EtOH (2 × 5 mL) and H2O (2 × 5 mL). Ethyl acetate (40 mL) was then added and the combined organic phases were washed with H2O (20 mL), dried with MgSO4, filtered and concentrated under vacuum. When necessary the residue was purified by flash-chromatography on silica gel using AcOEt/cyclohexane as eluant. After drying under vacuum (0.1 mbar) pure biaryls were obtained as shown by their 1H-NMR spectra (CDCl3, 300 MHz) which were in accordance with the literature (see ESI†).
Characterization of catalyst C1–C4. X-ray powder diffraction (XRD) data were collected with a Philips X'Pert MPD diffractometer equipped with Cu Kα1,2 doublet and a flat-plate Bragg–Brentano theta–theta geometry. The pristine catalyst materials as well as the recovered C3 catalyst were analysed. In the latter case, the catalyst was successively washed with water (3 × 30 mL) and diethyl ether (2 × 20 mL) and finally dried. The crystallite size was calculated with Scherrer formula34 using the (111) diffraction peak.The metallic particle morphology and distribution in the carbon framework were evaluated by transmission electron microscopy (TEM) with a Jeol ARM-200F instrument working at 200 kV. The particle size distribution was further determined based on TEM images and ImageJ software. About 250 particles were counted using several TEM images in order to ensure a good representation of the material.
D Conclusions
Mesoporous carbons containing PdxCoy alloys were prepared by a fast, efficient and eco-friendly route and used for Suzuki–Miyaura coupling reactions. They possessed small particles of narrowly distributed size trapped in the carbon network. The particle size was influenced by the alloy composition but only marginally by the annealing temperature. Several catalysts were evaluated and all demonstrated a good catalytic activity. Therefore, Co-rich C3 (Pd50Co50) was chosen and successfully used as a reusable magnetic catalyst for Suzuki–Miyaura couplings in green solvents (H2O or 1
:
1 H2O/EtOH mixture). In addition, we have shown that the catalytic activity was very dependent on the nature of the coupling partners. Studies are currently underway in our group to better understand this dependence and to extend the use of catalyst C3 to other important palladium-catalyzed reactions (Mizoroki–Heck, Sonogashira, Buchwald reactions and “green” carbonylations). Finally other mesoporous carbons containing various Pd-metal alloys have already been prepared and their applications in fine chemistry are in progress.
Conflicts of interest
There are no conflicts to declare.
Acknowledgements
Financial support of this work by the French National Research Agency (ANR) via Genesis project (ANR-13-BS08-0004-02) is acknowledged. We are also grateful to J. Demichel, S. Garnier, B. Dupré for helpful technical assistance, to Dr L. Vidal for TEM, to Dr J.-M. Le Meins for the XRD analyses and to the Fondation pour l'Ecole Nationale Supérieure de Chimie de Mulhouse for generous financial support.
Notes and references
-
(a) P. Lloyd-Williams and E. Giralt, Chem. Soc. Rev., 2001, 30, 145–157 RSC;
(b) M. M. Heravi and E. Hashemi, Tetrahedron, 2012, 68, 9145–9178 CrossRef CAS;
(c) V. Pandarus, D. Desplantier-Giscard, G. Gingras, F. Béland, R. Ciriminna and M. Pagliaro, Org. Process Res. Dev., 2013, 17, 1492–1497 CrossRef CAS.
- I. Volovych, M. Neumann, M. Schmidt, G. Buchner, J.-Y. Yang, J. Wolk, T. Sottmann, R. Strey, R. Schomacker and M. Schwarze, RSC Adv., 2016, 6, 58279–58287 RSC.
- J. N. Moorthy, P. Venkatakrishnan, D.-F. Huang and T. J. Chow, Chem. Commun., 2008, 2146–2148 RSC.
-
(a) J. Hassan, M. Sévignon, C. Gozzi, E. Schulz and M. Lemaire, Chem. Rev., 2002, 102, 1359–1469 CrossRef CAS PubMed;
(b) A. Suzuki, Angew. Chem., Int. Ed., 2011, 50, 6722–6737 (Angew. Chem., 2011, 123, 6854–6869) CrossRef CAS PubMed.
- H. Ren, C. A. Strulson, G. Humphrey, R. Xiang, G. Li, D. R. Gauthier and K. M. Maloney, Green Chem., 2017, 19, 4002–4006 RSC.
-
(a) L. Yin and J. Liebscher, Chem. Rev., 2007, 107, 133–173 CrossRef CAS PubMed;
(b) N. E. Leadbeater and M. Marco, Chem. Rev., 2002, 102, 3217–3274 CrossRef CAS PubMed.
-
(a) S. V. Ley, C. Ramarao, R. S. Gordon, A. B. Holmes, A. J. Morrison, I. F. McConvey, I. M. Shirley, S. C. Smith and M. D. Smith, Chem. Commun., 2002, 1134–1135 RSC;
(b) R. Akiyama and S. Kobayashi, J. Am. Chem. Soc., 2003, 125, 3412–3413 CrossRef CAS PubMed.
-
(a) S. Schweizer, J.-M. Becht and C. Le Drian, Adv. Synth. Catal., 2007, 349, 1150–1158 CrossRef CAS;
(b) S. Schweizer, J.-M. Becht and C. Le Drian, Tetrahedron, 2010, 66, 765–772 CrossRef CAS;
(c) C. Diebold, J.-M. Becht, J. Lu, P. H. Toy and C. Le Drian, Eur. J. Org. Chem., 2012, 893–896 CrossRef CAS;
(d) C. Diebold, S. Schweizer, J.-M. Becht and C. Le Drian, Org. Biomol. Chem., 2010, 8, 4834–4836 RSC;
(e) C. Diebold, A. Derible, J.-M. Becht and C. Le Drian, Tetrahedron, 2013, 69, 264–267 CrossRef CAS.
-
(a) V. Polshettiwar, R. Luque, A. Fihri, H. Zhu, M. Bouhrara and J.-M. Basset, Chem. Rev., 2011, 111, 3036–3075 CrossRef CAS PubMed;
(b) Q. M. Kainz and O. Reiser, Acc. Chem. Res., 2014, 47, 667–677 CrossRef CAS PubMed.
-
(a) D. Rosario-Amorin, M. Gaboyard, R. Clérac, L. Vellutini, S. Nlate and K. Heuzé, Chem.–Eur. J., 2012, 18, 3305–3315 CrossRef CAS PubMed;
(b) P. D. Stevens, J. Fan, H. M. R. Gardimalla, M. Yen and Y. Gao, Org. Lett., 2005, 7, 2085–2088 CrossRef CAS PubMed.
-
(a) B. Baruwati, D. Guin and S. V. Manorama, Org. Lett., 2007, 9, 5377–5380 CrossRef CAS PubMed;
(b) Z. Gao, Y. Feng, F. Cui, Z. Hua, J. Zhou, Y. Zhu and J. Shi, J. Mol. Catal. A: Chem., 2011, 336, 51–57 CrossRef CAS.
-
(a) A. Derible, C. Diebold, J. Dentzer, R. Gadiou, J.-M. Becht and C. Le Drian, Eur. J. Org. Chem., 2014, 7699–7706 CrossRef CAS;
(b) A. Schätz, T. R. Long, R. N. Grass, W. J. Stark, P. R. Hanson and O. Reiser, Adv. Funct. Mater., 2010, 20, 4323–4328 CrossRef PubMed;
(c) M. Zeltner, A. Schätz, M. L. Hefti and W. J. Stark, J. Mater. Chem., 2011, 21, 2991–2996 RSC.
- G. Clave, F. Pellissier, S. Campidelli and C. Grison, Green Chem., 2017, 19, 4093–4103 RSC.
- C. Peter, A. Derible, J.-M. Becht, J. Kiener, C. Le Drian, J. Parmentier, V. Fierro, M. Girleanu and O. Ersen, J. Mater. Chem. A, 2015, 3, 12297–12306 CAS.
- W. Tang, J. Li, X. Jin, J. Sun, J. Huang and R. Li, Catal. Commun., 2014, 43, 75–78 CrossRef CAS.
- M. S. Kutubi, K. Sato, K. Wada, T. Yamamoto, S. Matsumura, K. Kusada, H. Kobayashi, H. Kitagawa and K. Nagaoka, ChemCatChem, 2015, 7, 3887–3894 CrossRef CAS.
-
(a) For Sonogashira reactions in the presence of a Ni-Pd core-shell nanoparticles see: S. U. Son, Y. Jang, J. Park, H. B. Na, H. M. Park, H. J. Yun, J. Lee and T. Hyeon, J. Am. Chem. Soc., 2004, 126, 5026–5027 CrossRef CAS PubMed;
(b) For hydrogenation reaction of nitroarenes in the presence of a Ni-Sb bimetallic catalyst see: V. S. Marakatti and S. C. Peter, New J. Chem., 2016, 40, 5448–5457 RSC.
- S.-B. Wang, W. Zhu, J. Ke, M. Lin and Y.-W. Zhang, ACS Catal., 2014, 4, 2298–2306 CrossRef CAS.
- C. Peter, A. Derible, J. Parmentier, C. Le Drian and J.-M. Becht, New J. Chem., 2017, 41, 4931–4936 RSC.
-
(a) C. Matei Ghimbeu, J.-M. Le Meins, C. Zlotea, L. Vidal, G. Schrodj, M. Latroche and C. Vix-Guterl, Carbon, 2014, 67, 260–272 CrossRef CAS;
(b) C. Matei Ghimbeu, A. Puscasu, A. Martinez, C. Zlotea, Y. Oumellal, M. Latroche and C. Vix-Guterl, Microporous Mesoporous Mater., 2016, 223, 79–88 CrossRef CAS;
(c) A. Martínez de Yuso, J.-M. Le Meins, Y. Oumellal, V. Paul-Boncour, C. Zlotea and C. Matei Ghimbeu, J. Nanopart. Res., 2016, 18, 380 CrossRef;
(d) Y. Oumellal, K. Provost, C. Matei Ghimbeu, A. Martinez de Yuso and C. Zlotea, Nanotechnology, 2016, 27, 465401 CrossRef PubMed;
(e) A. Martinez de Yuso, A. Maetz, Y. Oumellal, C. Zlotea, J.-M. Le Meins and C. Matei Ghimbeu, J. Colloid Interface Sci., 2017, 505, 410–420 CrossRef CAS PubMed.
-
(a) A. Jahel, C. Matei Ghimbeu, L. Monconduit and C. Vix-Guterl, Adv. Energy Mater., 2014, 4, 1400025 CrossRef;
(b) C. Zlotea, Y. Oumellal, S.-J. Hwang, C. Matei Ghimbeu, P. de Jongh and M. Latroche, J. Phys. Chem. C, 2015, 119, 18091–18098 CrossRef CAS.
- A. Martínez de Yuso, Y. Oumellal, C. Zlotea, L. Vidal and C. Matei Ghimbeu, Nano-Struct. Nano-Objects, 2017, 9, 1–12 CrossRef.
-
(a) H. Hosseini, M. Mahyari, A. Bagheri and A. Shaabani, J. Power Sources, 2017, 247, 70–77 CrossRef;
(b) X. Wang and Y. Xia, Electrochem. Commun., 2008, 10, 1644–1646 CrossRef CAS;
(c) K. R. Lee and S. I. Woo, Catal. Today, 2014, 232, 171–174 CrossRef CAS;
(d) C. Zlotea, C. Matei Ghimbeu, Y. Oumellal, J.-C. Crivello, C. Vix-Guterl and M. Latroche, Nanoscale, 2015, 7, 15469–15476 RSC;
(e) D. Liu, Q. Guo, X. Zhang, H. Hou and T. You, J. Colloid Interface Sci., 2015, 450, 168–173 CrossRef CAS PubMed.
- C. Matei Ghimbeu, A. Puscasu, A. Martinez de Yuso, C. Zlotea, Y. Oumellal, M. Latroche and C. Vix-Guterl, Microporous Mesoporous Mater., 2016, 223, 79–88 CrossRef CAS.
- A. F. Schmidt and A. A. Kurokhtina, Kinet. Catal., 2012, 53, 714–730 CrossRef CAS.
- Y.-S. Feng, X.-Y. Lin, J. Hao and H.-J. Xu, Tetrahedron, 2014, 70, 5249–5253 CrossRef CAS.
- K. K. Senapati, S. Roy, C. Borgohain and P. Phukan, J. Mol. Catal. A: Chem., 2012, 352, 128–134 CrossRef CAS.
- M. Keller, V. Collière, O. Reiser, A.-M. Caminade, J.-P. Majoral and A. Ouali, Angew. Chem., Int. Ed., 2013, 52, 3626–3629 CrossRef CAS PubMed.
- P. D. Stevens, G. Li, J. Fan, M. Yen and Y. Gao, Chem. Commun., 2005, 4435–4437 RSC.
- B. Karimi, F. Mansouri and H. Vali, Green Chem., 2014, 16, 2587–2596 RSC.
- C. Deraedt, D. Wang, L. Salmon, L. Etienne, C. Labrugère, J. Ruiz and D. Astruc, ChemCatChem, 2015, 7, 303–308 CrossRef CAS.
- N. J. S. Costa, P. K. Kiyohara, A. L. Monteiro, Y. Coppel, K. Philippot and L. M. Rossi, J. Catal., 2010, 276, 382–389 CrossRef CAS.
- M. Ghotbinejad, A. R. Khosropour, I. Mohammadpoor-Baltork, M. Moghadam, S. Tangestaninejad and V. Mirkhani, J. Mol. Catal. A: Chem., 2014, 385, 78–84 CrossRef CAS.
- A. Patterson, Phys. Rev., 1939, 56, 978–982 CrossRef CAS.
Footnote |
† Electronic supplementary information (ESI) available: Experimental procedures and 1H and 13C-NMR Spectra of Compounds 1a–i. See DOI: 10.1039/c8ra02214c |
|
This journal is © The Royal Society of Chemistry 2018 |
Click here to see how this site uses Cookies. View our privacy policy here.