DOI:
10.1039/C8RA06373G
(Paper)
RSC Adv., 2018,
8, 31406-31413
Fabrication of ZnO nanoarchitectured fluorine-free robust superhydrophobic and UV shielding polyester fabrics for umbrella canopies†
Received
28th July 2018
, Accepted 23rd August 2018
First published on 6th September 2018
Abstract
Mechanically robust, durable, fluorine-free superhydrophobic and UV shielding surfaces are fabricated on polyester umbrella canopy fabrics by self-assembly of stearic acid on zinc oxide (ZnO) nanoarchitectures on polyester fabrics. Drawbacks of conventional umbrella canopies including rain water penetration through the canopy during heavy rains, wet canopies taking too long to dry, and limited blockage of harmful UV radiation have been overcome with the surface modified canopy fabrics in the present study. Herein, in the typical synthesis, the polyester fabric is dipped in Zn(NO3)2
:
hexamethylenetetraamine (HMT), at 1
:
1 molar ratio solution and heated at 100 °C for 2 h to grow ZnO nanoarchitectures on the fabric surface. Stearic acid is allowed to self-assemble by dipping the fabric in 1 g dm−3 stearic acid solution. The modified fabrics are characterized using scanning electron microscopy coupled with energy dispersive X-ray spectroscopy, Fourier transform infrared spectroscopy, thermogravimetric analysis and X-ray fluorescence spectroscopic techniques. The modified fabrics show superhydrophobicity characterized by water contact angles over 150° with the optimum analyzed conditions. The superhydrophobic layer formed on the fabric is resistant to acid rain and stayed durable throughout 50 abrasion cycles and under 1.5 h strong surfactant washing. The developed method is useful to fabricate a smart umbrella canopy with acid rain resistant, durable, robust superhydrophobic and UV blocking properties.
Introduction
Superhydrophobic surfaces are extensively used in many products and applications due to their interesting properties including self-cleaning, anti-corrosive, oil water separation, extreme water repellency and so on.1–10 A few of the many applications of superhydrophobic surfaces are anti-bio fouling paints for boats, anti-sticking of snow for antennas and windows, self-cleaning windshields for automobiles, microfluidics, lab-on-a-chip devices, metal refining, stain resistant textiles, anti-soiling architectural coatings, and dust-free coatings on building glasses etc.1–10 There is a plethora of reported methods to prepare superhydrophobic surfaces including electrochemical deposition,11 phase separation method,12 self-assembly layer-by-layer method,13,14 hydrothermal synthesis,15 chemical vapor deposition,16 wet chemical reaction,17 sol gel processing,18 electro-spinning,19,20 dip coating,19,21 and spray coating.22 The two major requirements for a surface to be superhydrophobic are, having appropriate surface roughness and low surface free energy.19,23 The surface roughness can be achieved by fabricating a seed layer, which is a layer of nanoparticles, on the surface. A low surface free energy substance that would enable superhydrophobicity, can be fabricated or allowed to self-assemble on top of the intermediate nanostructured layer.24,25 Furthermore, most of superhydrophobic surfaces are fabricated with fluorine containing compounds which cause harmful effects to the environment due to their bioaccumulation. Therefore, fluorine-free compounds and methods are timely needed to develop superhydrophobic surfaces.
This superhydrophobic property can be applied to an umbrella canopy to prevent the major drawbacks of conventional umbrellas such as failure to withstand heavy showers, time taken to be dried when the umbrella canopy gets wet and limited blockage of harmful radiations like UV and IR. Having a superhydrophobic layer on top of the textile of the umbrella prevents it from wetting in the rain and roll off the moisture from the fabric. Hence the umbrella does not get wet and it is easier for the end-user when handling. Various fabric materials are used as canopy material of umbrella including linen, polyester, cotton, leather, taffeta variety of silk, lace, gloria (especially made only for umbrella), rayon, and acetate. Nowadays most commonly used canopy materials are nylon taffeta and treated polyester. Recently, umbrellas with advanced features have appeared around the world. There are smart umbrellas including “Light Saber Umbrella”, which emits light from the umbrella handle, “Nano nuno umbrella” with superhydrophobic property, “Ambient forecasting umbrella”, which gives out a light according to different weather conditions, solar power generating umbrella, which lights LED for about four hours in dark, and radiation blocking umbrellas.26
Even though there are many publications on superhydrophobic textiles, there are only few reports on fabricated superhydrophobic umbrellas.27,28 Bi Xu and Zaisheng Cai prepared superhydrophobic cotton textile using wet chemical route.29 They have used dip-pad-cure process to coat ZnO nanocrystals on the fabric. Then ZnO nanorod arrays were grown in a sealed stainless steel pot at 90 °C for 3 h and the fabric was then dipped in n-dodecyltrimethoxysilane solution for 24 h to introduce superhydrophobicity. M. Ashraf et al. developed a method to produce a superhydrophobic surface on polyester.30 ZnO seeds were grown by immersing the fabric in seed layer solution and squeezing the fabric between two rollers for five times with in between drying at 120 °C. ZnO nanorods were grown using zinc nitrate hexahydrate and HMT in a Teflon bottle containing the fabric at 90 °C for 4 h. For hydrophobization, the fabric was dipped in octadecyltrimethoxysilane solution for 24 h at 40 °C. Zhao et al. prepared ZnO nanorods on polyethylene terephthalate (PET) fabric using two step hydrothermal growth method. There, ZnO seed precursor was synthesized by a sol-gel-reaction and this precursor was coated onto the PET fabrics by dip-pad-cure process. To grow ZnO nanorods, the seed layer grown fabric was dipped in a solution of zinc nitrate hexahydrate and methenamine for 3 h at 90 °C and oscillated continuously using a dyeing machine.31 Huang et al. prepared superhydrophobic fabric for UV-shielding and oil-water separation using a hydrothermal reaction to fabricate flower-like TiO2 on cotton fabrics. TiO2 layer was grown using potassium titanium oxalate and H2O2 hydrothermal reaction. The superhydrophobicity was achieved by soaking the fabrics in a methanolic solution of hydrolyzed perfluorooctyltriethoxysilane or perfluorodecyltriethoxysilane solution.32 Shouwei Gao et al prepared superhydrophobic cotton fabrics through a one-step hot-pressing process. The fabric was dipped in a n-octyltriethoxysilane to get The hydrophobicity, and micro-nano structure was obtained by coating TiO2 particles.33 Zhu et al. prepared a multi-layered superhydrophobic coating on cotton fabric using the dip coating process. There method, firstly polydimethylsiloxane (PDMS) layer was deposited on cotton fabric and surface roughness was achieved by deposition of ZnO nanoparticle layer. The second PDMS layer was applied on this nanoparticle layer by the dip-coating method.34 Xue et al. prepared UV-durable superhydrophobic PET textile. Firstly ZnO nanostructures were grown on PET surface by a hydrothermal process and then these fibers were coated with silica forming a ZnO/SiO2 core–shell structure. Hydrophobicity was achieved by immersing in an hexadecyltrimethoxysilane solution.35
In this work, for the first time, superhydrophobic and UV shielding fabrics were made by growing various morphologies of ZnO nanostructures on the surface of the commercially available polyester umbrella canopy fabric material followed by self-assembling hydrophobic stearic acid. Compared to previously reported work as mentioned above, this method requires fewer steps to achieve robust hydrophobic property. More importantly, being able to modify umbrella canopy fabric currently in use to make umbrellas, is very attractive as it has a commercial importance. Here, the ZnO structures were formed on fabrics using zinc nitrate hexahydrate and hexamethylenetetramine (HMT) baths followed by heating. Various morphologies of ZnO were obtained by varying temperature and molar ratios and the reaction conditions were optimized to obtain superhydrophobicity in fabrics. Furthermore, the resistance and durability of modified fabrics against pH of the water was studied to get an insight into their stability against acid rain. The fabrics tolerated the acidity very well therefore; it can be used in acid rain conditions. The coatings are durable for over 1.5 h strong surfactant washing cycles and over 50 mechanical abrasion cycles. Superhydrophobic and UV shielding umbrellas reported in this study are very important for exceptional development of umbrella manufacturing industries throughout the globe.
Experimental
Materials
All the chemical reagents used in this study were of analytical grade (Sigma-Aldrich) and were used without further purification: zinc nitrate hexahydrate (Zn(NO3)2·6H2O) (99% purity), hexamethylenetetraamine (HMT) (C6H12N4) (99% purity), stearic acid (CH3(CH2)16COOH) (99% purity) and ethanol (C2H5OH) (95% purity). Polyurethane and polyacrylic coated polyester umbrella manufacturing fabrics were obtained from Rainco (Pvt) Ltd, a leading umbrella manufacturer in Sri Lanka.
Growth of ZnO nanostructures on umbrella fabrics
In a typical growth method of ZnO nanostructures on fabrics, 40 ml of each solution of 0.05 M Zn(NO3)2·6H2O and HMT were mixed together to make a reaction bath. Herein, several baths were prepared by varying HMT concentration as 0.010, 0.025, 0.050, 0.075 and 0.100 M to get the optimum molar ratio for growth of seed layer. Pieces of fabrics (5 cm × 5 cm) were dipped in each bath and the reaction baths were kept in an oven for 1 h at 100 °C. The fabric pieces were taken out from the reaction bath and kept in the oven for 10 min at 60 °C. The fabrics were dipped in the respective zinc nitrate and HMT reaction bath again and kept in the oven for 1 h at 100 °C. Then the fabrics were taken out, oven dried for 20 min at 60 °C.
Optimization of the condition for self-assembly of hydrophobic layer
ZnO seed layer applied fabric samples were dipped in a stearic acid solution (1 g dm−3) for 15 h. Fabric sample prepared using 0.05 M
:
0.05 M, Zn(NO3)2
:
HMT ratio was dipped in stearic acid solutions in different concentrations as 0.1, 0.25, 0.50, 0.75, and 1 g dm−3 for 15 h to optimize the stearic acid concentration. Fabric sample prepared using 0.05 M
:
0.05 M, Zn(NO3)2
:
HMT bath was dipped in concentration 1 g dm−3 of stearic acid solutions with varying dipping time as 1, 3, 5, 7, 9, 11, 13, and 15 h to optimize the dipping time.
Evaluation of superhydrophobicity
Superhydrophobicity was evaluated by varying the pH and dipping time.
Effect of water pH and dipping time
Fabric sample prepared using 0.05 M
:
0.05 M, Zn(NO3)2
:
HMT bath followed by dipping in 1 g dm−3 stearic acid solution for 15 h was used to test the resistance of the superhydrophobicity of modified fabric to pH of the water and contact time. A solution series was prepared by varying the pH as 4.0, 4.5, 5.0, 5.5, 6.0, 6.5, and 7.0. The fabric samples were dipped in each solution with varying the dipping time as 0.5, 1, 1.5, 2, 2.5, and 3 h.
Durability of the fabrics over abrasion and washing
Abrasion durability of fabrics was tested using a crock meter (Infinity RS-8318B). The treated fabrics were placed flat on the base of the crock meter. A 5 cm × 5 cm dry test cloth was mounted over the end of the finger which projects downward from the weighed (9 N) sliding arm. The finger was lowered on to the test specimen and it was crocked back and forth 50 times by making 25 complete turns (AATCC test method 8-2007). After each 5 cycles the water contact angles (WCAs) of fabrics were measured. To test the washing durability of the fabrics, the washing temperature was maintained at 40 °C and the spin speed was 645 rpm. The dry load to detergent ratio was maintained at 400
:
9 ratio and the total washing time was 30 min. The washed fabrics were oven dried at 70 °C for 50 min.
Study of UV blocking property
Fabric sample prepared using 0.05 M
:
0.05 M, Zn(NO3)2
:
HMT bath followed by dipping in 1 g dm−3 stearic acid solution for 15 h and the bare fabric were used for the UV-Vis characterization. Absorption, reflection and transmission spectra of the fabrics were measured using UV-Vis spectrophotometer.
Characterization techniques
Fourier-transform infrared (FTIR) spectra of fabrics were recorded on Bruker vertex-80 with a spectral range of 4000 to 400 cm−1 with 32 scans per measurement with 0.4 cm−1 resolution. Thermogravimetric analysis (TGA) was carried out using a TGA SDT Q600 at a heating rate of 10 °C min−1 to 1000 °C. The morphological features of the fabrics were observed by a scanning electron microscopy (SEM) (HITACHI SU 600) under the operating voltage of 10 kV, the samples were sputtered with gold (nanoparticles) before they were analyzed with SEM. Elemental analysis of the coating was carried out using energy dispersing X-ray spectroscopy (EDS) analysis by OXFORD instruments EDS detector coupled with SEM. X-ray fluorescence (XRF) characterization of the fabric samples was carried out using Horiba XGT-5200. The optical properties of fabrics were analyzed via UV-Vis spectrophotometer (Shimadzu, UV-3600). For WCA measurements, KRUSS drop shape analyzer (DSA25) was used. The fabric samples were placed on the stage and 2 μl water droplets were placed on fabrics. The measurements were taken at three different locations of each fabric. Both treated and non-treated fabrics were tested for their stress and strain properties using Instron 55R1123 tensile testing machine according to the ASTM D5034 standardized method, with loading rate of 300 mm min−1. The length and width of the samples were 70 mm and 20 mm respectively. The thicknesses of the non-treated and treated samples were 0.098 mm and 0.109 mm respectively.
Results and discussion
Morphological analysis
The SEM analysis of the non-treated fabric (Fig. 1a) shows a clean and smooth surface. The used commercial fabric has slight hydrophobicity due to the coating of low surface free energy substances like polyurethane and polyacrylic. Fig. 1b–f shows SEM images of the fabrics with ZnO seed layers prepared with various HMT concentrations. Nanometer scale ZnO particles are observed on all the samples. The reactions taking place in the presence of Zn(NO3)2 and HMT are given below in eqn (1)–(5).36 |
HMT + 6H2O → 4NH3 + 6HCHO
| (1) |
|
NH3 + H2O → NH4+ + OH−
| (2) |
|
4Zn2+ + 4NH3 → [Zn(NH3)]42+
| (3) |
|
Zn2+ + 2OH− → Zn(OH)2
| (4) |
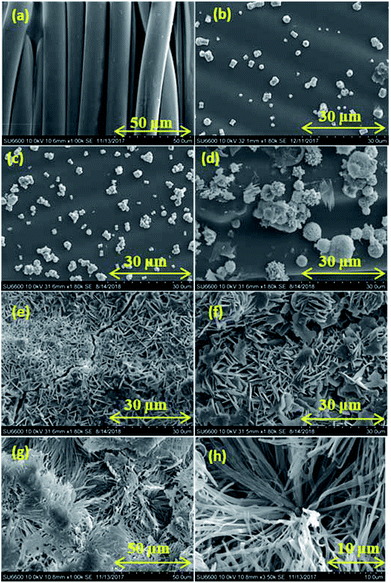 |
| Fig. 1 SEM images of (a) non-treated fabric, treated-fabric with molar ratios of HMT : zinc nitrate (b) 0.01 : 0.05, (c) 0.025 : 0.05, (d) 0.05 : 0.05, (e) 0.075 : 0.05, (f) 0.1 : 0.05, (g) and (h) ZnO seed layer deposited fabric with HMT : Zn(NO3)2 0.05 : 0.05 treated with stearic acid 1 g dm−3 for 15 h. | |
ZnO can be prepared from Zn(NO3)2 in a basic environment. NH3 released from HMT hydrolysis as shown in eqn (1), creates the basic environment by undergoing hydrolysis and releasing hydroxyls (eqn (2)). Slow release of NH3 controls the ZnO particle size in nano range (eqn (3)). Zn2+ ions react with OH− to produce Zn(OH)2 as shown in eqn (4). When Zn(OH)2 is heated to 100 °C ZnO is formed (eqn (5)). Fig. 1b and c show spherical particles. However, the distribution of particles on the surface of fabric is low due to low concentrations of Zinc nitrate and HMT used. Fig. 1d shows spherical ZnO nanoparticles with homogeneous and higher particle distribution. Fig. 1e and f both show higher ZnO distribution with plate-like ZnO nanoparticles. Sample prepared with HMT
:
Zn(NO3)2, 1
:
1 ratio shows better particle size distribution. Hence, HMT
:
Zn(NO3)2 1
:
1 was chosen as the optimum molar ratio for further analyses (Fig. S1 in ESI† for nanoarchitectures). Fig. 1g and h depict SEM images of the fabrics with superhydrophobic stearic acid layer applied on top of the ZnO seed layer with 0.05 M
:
0.05 M Zn(NO3)2
:
HMT ratio. It shows higher stearic acid self-assembled coverage with particle size of 100–500 nm. Stearic acid is an amphiphilic compound. It has a polar head and a non-polar tail groups. ZnO seed layer is polar. Hence, the polar head group of stearic acid is attached to the polar seed layer while the non-polar tail group sticking out of the surface.
Elemental analysis
EDS analysis of ZnO seed layer of fabric sample prepared with 0.05 M
:
0.05 M, Zn(NO3)2
:
HMT bath is shown in the Fig. 2a–f. It clearly shows that ZnO nanoparticles have been formed on the surface of the fabric material. The area of the fabric that is not covered with ZnO is shown as carbon (C) since the fabric is made of carbon. Fig. 3a–f shows the EDS analysis of the stearic acid assembled superhydrophobic fabric. It shows better stearic acid coverage on top of the ZnO seed layer representing more carbon percentage and less Zn and O percentage on the fabric surface. Elemental analysis was further confirmed by XRF (Fig. S2 in ESI†).
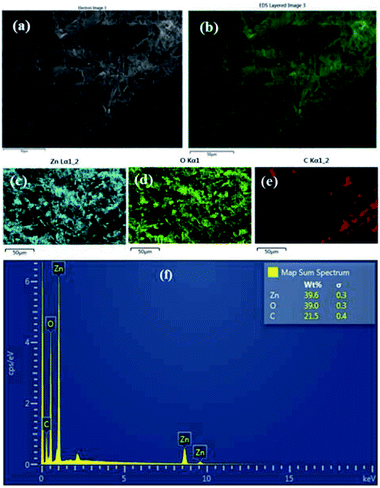 |
| Fig. 2 (a and b) EDS results of ZnO seed layer applied fabric 0.05 M : 0.05 M, Zn(NO3)2 : HMT (c) Zn (d) O (e) C (f) weight percentages with spectrum. | |
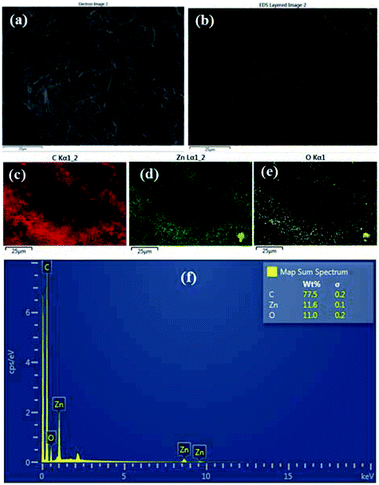 |
| Fig. 3 (a and b) EDS results of stearic acid self-assembled 1 g dm−3 for 15 h fabric (c) C (d) Zn (e) O (f) weight percentages with spectrum. | |
FTIR characterizations
Fig. 4 shows the FTIR spectra of treated and non-treated fabrics. Fig. 4a and b are non-treated and ZnO seed applied fabric with HMT (M)
:
Zn(NO3)2 (M) 0.05
:
0.05 molar ratio respectively. Both spectra show approximately similar kind of characteristic stretching vibrations for the umbrella fabric. Fig. 4c shows stearic acid self-assembled fabric with concentration of 1 g dm−3 with 15 h of dipping time. In stearic acid superhydrophobic layer applied sample there is an additional stretching between 2800–3000 cm−1 and sharp medium bands at 1460 cm−1 and 1530 cm−1. When stearic acid molecules are self-assembled on top of the ZnO seed layer, hydrophobic tail groups remain on the surface of fabric. Hence C–C and C–H bond vibrations have been observed. C–H stretching appears around 3000 cm−1 and C–H bending around 1400–1500 cm−1.37–39
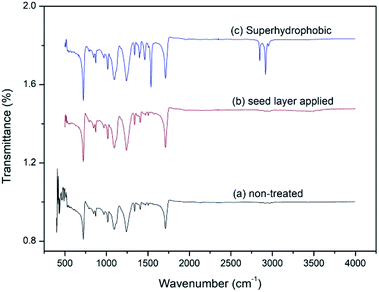 |
| Fig. 4 FTIR spectrum of (a) non-treated fabric (b) ZnO seed layer applied fabric HMT(M) : Zn(NO3)2(M) 0.05 : 0.05 and (c) stearic acid with concentration of 1 g dm−3 dipped for 15 h self-assembled on ZnO seed layer applied fabric. | |
Thermal characteristics
The TGA thermograms of the non-treated fabric and fabric sample prepared using 0.05 M
:
0.05 M Zn(NO3)2
:
HMT bath (dipped in 1 g dm−3 stearic acid solution for 15 h) are shown in Fig. 5a and b respectively. The non-treated fabric shows three types of weight losses and the treated fabric shows two types of weight losses. In both thermograms, the weight loss between 250 °C and 550 °C indicates the loss of OH− and CO32−,which react with O2 to form H2O and CO2.40–42 Polyester decomposes 100% in to volatile gasses and char byproducts. Maximum rate of weight loss is observed at ca. 420 °C in both fabrics. TGA of bare fabric shows weight reduction at about 200 °C which is attributed to the removal of moisture. TGA of the treated fabric does not show significant mass loss due to evaporation of water as there is no water adsorption on this hydrophobic surface.
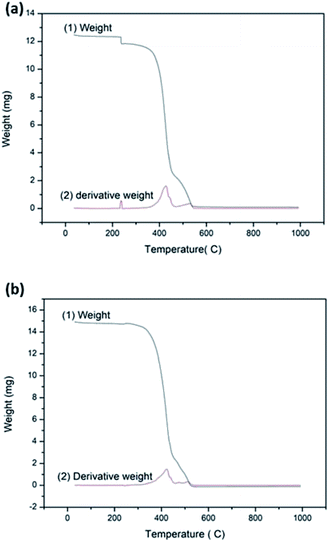 |
| Fig. 5 TGA analysis of (a) the non-treated fabric [(1) weight (2) derivative weight] (b) the treated fabric with stearic acid 1 g dm−3 dipped for 15 h on top of the ZnO seed layer [(1) weight (2) derivative weight]. | |
Evaluation of UV blocking property of fabrics
UV-Vis spectra recorded for untreated and treated fabrics by transmission are shown in Fig. 6. Lowest transmission in the UV region (225–325 nm) is shown by the stearic acid assembled superhydrophobic fabric (2.8%). ZnO seed layer applied fabric also has lower transmission (3.6%) than non-treated fabric (7.8%) in UV region.43,44
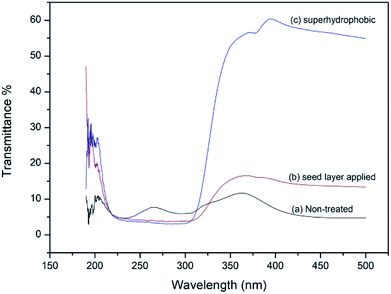 |
| Fig. 6 UV-Vis transmission spectra of (a) normal fabric, (b) seed layer applied fabric Zn(NO3)2 (M) : HMT (M) 0.05 : 0.05 and (c) superhydrophobic fabric (stearic acid 1 g dm−3 dipped for 15 h). | |
Evaluation of superhydrophobicity of umbrella fabric
WCA measurements for fabrics made with varying concentrations of HMT.
The WCA measurements for the HMT concentration varied fabrics dipped in 1 g dm−3 stearic acid solution for 15 h are shown in the Table 1. According to results, 1
:
5 and 1
:
2 HMT and zinc nitrate concentrations do not show better hydrophobicity because of the low ZnO nanoparticle coverage on the fabric. 1
:
1, 3
:
2 and 2
:
1 molar ratios show superhydrophobicity. Hence the optimum molar ratio will be 1
:
1 HMT
:
Zn(NO3)2 concentrations45–47 (ESI Fig. S3†).
Table 1 WCA for fabric made with varying concentrations of HMT
No. |
HMT concentration (M)/40 ml |
Zinc nitrate hexahydrate concentration (mol dm−3)/40 ml |
HMT : Zn(NO3)2 molar ratio |
WCA |
I |
0.010 |
0.050 |
1 : 5 |
136° (±0.11) |
II |
0.025 |
0.050 |
1 : 2 |
140° (±0.22) |
III |
0.050 |
0.050 |
1 : 1 |
158° (±0.05) |
IV |
0.075 |
0.050 |
3 : 2 |
145° (±0.05) |
V |
0.100 |
0.050 |
2 : 1 |
151° (±0.06) |
Effect of stearic acid concentration
WCA measurements of the study on effect of stearic acid concentration are provided in Table 2. According to the results, 0.1 g dm−3 stearic acid concentration shows superhydrophobicity with highest WCA at 150°.48 Therefore the optimum stearic acid concentration is 0.1 g dm−3. Fig. 7 shows the water contact angle of superhydrophobic fabric which was prepared using 0.1 g dm−3 stearic acid with 15 h dipping time (ESI Fig. S4†).
Table 2 WCA of fabrics treated with different stearic acid concentrations dipped for 1 h
Stearic acid concentration (g dm−3) |
0.010 |
0.025 |
0.050 |
0.075 |
0.100 |
WCA |
138° (±0.18) |
138.5° (±0.16) |
144.3° (±0.73) |
144.0° (±0.09) |
158.2° (±0.19) |
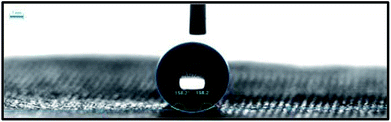 |
| Fig. 7 WCA of stearic acid (1 g dm−3 dipped for 1 h) self-assembled on top of the ZnO seed layer applied fabric Zn(NO3)2 : HMT molar ratio 0.05 : 0.05. | |
Effect of stearic acid dipping time
According to the results (Table 3) dipping of fabric for 1 h in stearic acid is not enough for the self-assembly of stearic acid on top of the ZnO seed layer. Superhydrophobic WCA over 135° has been observed by dipping the fabric more than 3 h. The best superhydrophobicity has been obtained in the fabric dipped for 11 h with WCA 150°. Contact angles are given in ESI Fig. S5.†
Table 3 WCA of fabrics at different dipping time in stearic acid
Stearic acid dipping time (h) |
1 |
3 |
5 |
7 |
9 |
11 |
13 |
15 |
WCA |
150.9 (±0.01) |
151.0° (±0.11) |
156.0° (±0.07) |
154.3° (±0.09) |
155.5° (±0.12) |
161.4° (±0.06) |
153.5° (±0.05) |
158.2° (±0.08) |
Evaluation of the resistance of fabrics to rain water pH
Naturally unpolluted rainwater has slight acidity about pH 5–5.5. This experiment was carried out to test the durability of the superhydrophobic layer of the fabric against various pH levels and varying dipping time in each pH. WCA measurements were taken for each fabric under various pH and various time periods. The measured WCA for every fabric is in between 144–160° which is in the superhydrophobic region and a significant variation is not observed.49 The superhydrophobic layer has not been disrupted due to the pH of the water during the 3 h dipping time. Therefore, it can be concluded that the superhydrophobicity developed in this work is not affected by the pH of rain water (see ESI Fig. S6 and S7† for WCA) (Table 4).
Table 4 WCA for pH and dipping time varied fabrics
Time (h) |
pH |
4.0 |
4.5 |
5.0 |
5.5 |
6.0 |
6.5 |
7.0 |
0.5 |
147.3° (±0.12) |
145.0° (±0.08) |
154.7° (±0.11) |
150.7° (±0.13) |
144.2° (±0.05) |
147.1° (±0.11) |
151.2° (±0.07) |
1.0 |
152.8° (±0.07) |
150.4° (±0.05) |
151.5° (±0.05) |
150.4° (±0.07) |
153.5° (±0.06) |
155.6° (±0.11) |
155.0° (±0.08) |
1.5 |
151.7° (±0.102) |
152.2° (±0.12) |
163.6° (±0.07) |
144.9° (±0.09) |
150.7° (±0.12) |
157.1° (±0.13) |
159.3° (±0.11) |
2.0 |
151.7° (±0.11) |
153.4° (±0.13) |
157.1° (±0.09) |
151.6° (±0.10) |
162.4° (±0.10) |
151.9° (±0.06) |
162.8° (±0.09) |
2.5 |
150.3° (±0.06) |
151.7° (±0.07) |
156.5° (±0.12) |
152.7° (±0.08) |
155.1° (±0.11) |
146.5° (±0.07) |
156.2° (±0.12) |
3.0 |
150.1° (±0.10) |
144.0° (±0.05) |
152.4° (±0.13) |
152.7° (±0.10) |
148.7° (±0.05) |
152.2° (±0.09) |
164.4° (±0.10) |
The water contact angle of the treated fabric is shown in Fig. 8a after 50 cycles of abrasion which shows 157° of WCA with superhydrophobicity. The WCA of fabric after 1.5 h washing time period is 147° [Fig. 8b]. Therefore the superhydrophobic layer has an excellent durability over 50 cycles of abrasion and 1.5 h washing.
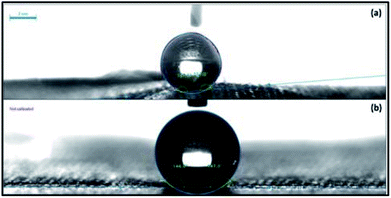 |
| Fig. 8 WCAs of fabrics (a) after 50 cycles of abrasion and (b) after 1.5 h washing. | |
Mechanical properties
Tensile and tear properties of treated fabrics were compared with those of non-treated fabrics (Fig. S8†). Treated fabrics show 77.11 (±7.03) MPa maximum tensile stress while non-treated fabrics show 115.25 (±7.83) MPa maximum tensile stress.
Conclusions
The superhydrophobic umbrella fabrics were successfully realized using a seed layer of ZnO nanostructures as an intermediate. The morphology of the ZnO nanoparticle and particle distribution can be changed by varying the HMT concentration. The seed layer applied using optimized molar ratio of 0.05 M
:
0.05 M Zn(NO3)2
:
HMT. Stearic acid self-assembled through hydrogen and coordination bonds between carboxylate group and Zn in order to give superhydrophobicity. Seed layer applied fabric dipped in 1 g dm−3 for 11 h showed the best superhydrophobicity with more than 150° WCA compared to other conditions. The improved fabrics are resistant to acidity of the water. The treated fabric material limitedly transmitted UV radiation (3.35%) in 225–325 nm region compared to the non-treated fabric (7.78%). Therefore, the method is suitable to prepare modified fabric to manufacture smart umbrellas with robust superhydrophobic and UV blocking properties.
Conflicts of interest
There are no conflicts to declare.
Acknowledgements
Authors are grateful to Mr D. M. S. N. Dissanayake, Mr T. C. Palihawadana, Ms A. Senthilnathan, Ms D. Chandrakumara and Mr D. P. Priyantha for their kind support during this research. We also thank Prof. Metthew Linford at Brigham Young University for his valuable suggestions to improve the manuscript. The authors highly acknowledge Rainco (Pvt) Ltd., Sri Lanka for providing umbrella fabrics and necessary information.
Notes and references
- Y. Zhang, B. Dong, S. Wang, L. Zhao, L. Wan and E. Wang, RSC Adv., 2017, 7, 47357–47365 RSC.
- I. You, Y. Chang Seo and H. Lee, RSC Adv., 2014, 4, 10330–10333 RSC.
- C. Zeng, H. Wang, H. Zhou and T. Lin, RSC Adv., 2015, 5, 61044–61050 RSC.
- C.-H. Xue, X. Li, S.-T. Jia, X.-J. Guo and M. Li, RSC Adv., 2016, 6, 84887–84892 RSC.
- S. Wang, S. Wu, J. Zhang and T. Wang, RSC Adv., 2017, 7, 24374–24381 RSC.
- A. K. Singh and J. K. Singh, RSC Adv., 2016, 6, 103632–103640 RSC.
- A. M. Kansara, S. G. Chaudhri and P. S. Singh, RSC Adv., 2016, 6, 61129–61136 RSC.
- S. Fu, H. Zhou, H. Wang, J. Ding, S. Liu, Y. Zhao, H. Niu, G. C. Rutledge and T. Lin, RSC Adv., 2018, 8, 717–723 RSC.
- H. Yan, H. Zhou, Q. Ye, X. Wang, C. M. Cho, A. Y. X. Tan and J. Xu, RSC Adv., 2016, 6, 66834–66840 RSC.
- H. Wang, H. Zhou, S. Liu, H. Shao, S. Fu, G. C. Rutledge and T. Lin, RSC Adv., 2017, 7, 33986–33993 RSC.
- M. Li, J. Zhai, H. Liu, Y. Song, L. Jiang and D. Zhu, J. Phys. Chem. B, 2003, 107, 9954–9957 CrossRef.
- J. Liu, X. Xiao, Y. Shi and C. Wan, Appl. Surf. Sci., 2014, 297, 33–39 CrossRef.
- S. Li, J. Huang, Z. Chen, G. Chen and Y. Lai, J. Mater. Chem. A, 2017, 5, 31–55 RSC.
- S. Wang and C. Wang, Appl. Surf. Sci., 2012, 261, 561–566 CrossRef.
- J. Wu, J. Chen, J. Xia, W. Lei and B. P. Wang, Adv. Mater. Sci. Eng., 2013, 2013, 232681 Search PubMed.
- S. S. Latthe, A. B. Gurav, C. S. Maruti and R. S. Vhatkar, J. Surf. Eng. Mater. Adv. Technol., 2012, 2012, 76–94 Search PubMed.
- X. Wu, L. Zheng and D. Wu, Langmuir, 2005, 6065–6067 Search PubMed.
- V. Mannari and M. Niknahad, Design, Development and Evaluation of Super Hydrophobic Coatings, 2015, pp. 1–5 Search PubMed.
- E. J. Park, B. R. Kim, D. K. Park, S. W. Han, D. H. Kim, W. S. Yun and Y. D. Kim, RSC Adv., 2015, 5, 40595–40602 RSC.
- M. Zhang, J. Pang, W. Bao, W. Zhang, H. Gao, C. Wang, J. Shi and J. Li, Appl. Surf. Sci., 2017, 419, 16–23 CrossRef.
- J. Du, L. Zhang, J. Dong, Y. Li, C. Xu and W. Gao, J. Eng. Fibers Fabr., 2016, 11, 31–37 Search PubMed.
- V. K. Wimalasiri, H. U. Weerathunga, N. Kottegoda and V. Karunaratne, J. Nanomater., 2017, 2017, 2102467 Search PubMed.
- Y. Yao, C. Li, H. Zhang and R. Yang, Appl. Surf. Sci., 2017, 419, 52–62 CrossRef.
- R. Zhang, W. Wan, L. Qiu, Y. Wang and Y. Zhou, Appl. Surf. Sci., 2017, 419, 342–347 CrossRef.
- E. V Bryuzgin, V. V Klimov, S. A. Repin, A. V Navrotskiy and I. A. Novakov, Appl. Surf. Sci., 2017, 419, 454–459 CrossRef.
- Top 10 High-Tech Umbrellas for Rainy Days|PCMag.com.
- S. Mondal, S. Pal and J. Maity, New J. Chem., 2018, 42, 6831–6838 RSC.
- A. K. Singh and J. K. Singh, New J. Chem., 2017, 41, 4618–4628 RSC.
- B. Xu and Z. Cai, Appl. Surf. Sci., 2008, 254, 5899–5904 CrossRef.
- M. Ashraf, C. Campagne, A. Perwuelz, P. Champagne, A. Leriche and C. Courtois, J. Colloid Interface Sci., 2013, 394, 545–553 CrossRef PubMed.
- Z. Zhou, Y. Zhao and Z. Cai, Appl. Surf. Sci., 2010, 256, 4724–4728 CrossRef.
- J. Y. Huang, S. H. Li, M. Z. Ge, L. N. Wang, T. L. Xing, G. Q. Chen, X. F. Liu, S. S. Al-Deyab, K. Q. Zhang, T. Chen and Y. K. Lai, J. Mater. Chem. A, 2015, 3, 2825–2832 RSC.
- S. Gao, J. Huang, S. Li, H. Liu, F. Li, Y. Li, G. Chen and Y. Lai, Mater. Des., 2017, 128, 1–8 CrossRef.
- T. Zhu, S. Li, J. Huang, M. Mihailiasa and Y. Lai, Mater. Des., 2017, 134, 342–351 CrossRef.
- C. H. Xue, W. Yin, P. Zhang, J. Zhang, P. T. Ji and S. T. Jia, Colloids Surf., A, 2013, 427, 7–12 CrossRef.
- C. Pholnak, C. Sirisathitkul, S. Suwanboon, D. J. Harding, M. Technology, N. S. Thammarat and H. Yai, Mater. Res., 2014, 17, 405–411 CrossRef.
- E. Velayi and R. Norouzbeigi, Appl. Surf. Sci., 2017, 426, 674–687 CrossRef.
- B. Jiang, Z. Chen, Y. Sun, H. Yang, H. Zhang, H. Dou and L. Zhang, Appl. Surf. Sci., 2018, 441, 554–563 CrossRef.
- J. Deyo, P. J. Rivero, C. Berlanga, D. M. Bastidas, J. F. Palacio and R. Rodriguez, Appl. Surf. Sci., 2017, 419, 138–149 CrossRef.
- Y. Qi, B. Xiang, W. Tan and J. Zhang, Appl. Surf. Sci., 2017, 419, 213–223 CrossRef.
- Y. R. Somarathna, M. M. M. G. P. G. Mantilaka, D. G. G. P. Karunaratne, R. M. G. Rajapakse, H. M. T. G. A. Pitawala and K. G. U. Wijayantha, Cryst. Res. Technol., 2016, 51, 207–214 CrossRef.
- M. M. M. G. P. G. Mantilaka, W. P. S. L. Wijesinghe, H. M. T. G. A. Pitawala, R. M. G. Rajapakse and D. G. G. P. Karunaratne, J. Natl. Sci. Found. Sri Lanka, 2014, 42, 221–228 Search PubMed.
- Y. Zhao, Z. Xu, X. Wang and T. Lin, Appl. Surf. Sci., 2013, 286, 364–370 CrossRef.
- M. M. Hassan and S. J. Leighs, Appl. Surf. Sci., 2017, 419, 348–356 CrossRef.
- B. S. Yilbas, M. Khaled, N. Abu-dheir, N. Aqeeli and S. Z. Furquan, Appl. Surf. Sci., 2013, 286, 161–170 CrossRef.
- X. Zhang, J. Mo, Y. Si and Z. Guo, Appl. Surf. Sci., 2018, 441, 491–499 CrossRef.
- E. Velayi and R. Norouzbeigi, Appl. Surf. Sci., 2018, 441, 156–164 CrossRef.
- K. Shen, M. Yu, Q. Li, W. Sun, X. Zhang, M. Quan, Z. Liu, S. Shi and Y. Gong, Appl. Surf. Sci., 2017, 426, 694–703 CrossRef.
- S. Wook, E. Ji, M. Jeong, I. Hee, H. Ook, J. Hwan, K. Kim and Y. Dok, Appl. Surf. Sci., 2017, 400, 405–412 CrossRef.
Footnote |
† Electronic supplementary information (ESI) available. See DOI: 10.1039/c8ra06373g |
|
This journal is © The Royal Society of Chemistry 2018 |
Click here to see how this site uses Cookies. View our privacy policy here.