DOI:
10.1039/C9RA02678A
(Paper)
RSC Adv., 2019,
9, 24386-24393
Evaluation of Fe(III)EDTA reduction with ascorbic acid in a wet denitrification system†
Received
10th April 2019
, Accepted 4th July 2019
First published on 6th August 2019
Abstract
The reduction of Fe(III)EDTA to Fe(II)EDTA is the core process in a wet flue gas system with simultaneous desulfurization and denitrification. Herein, at first, the reductant ascorbic acid (VC) was used for reducing Fe(III)EDTA. The feasibility of Fe(III)EDTA reduction with ascorbic acid was investigated at different Fe(III)EDTA concentrations, various pH values, diverse temperatures, and different molar ratios of VC to Fe(III)EDTA. The results showed that the Fe(II)EDTA concentration increased with an increase in the initial Fe(III)EDTA concentration. Furthermore, the reduction efficiency increased as the mole ratio of VC to Fe(III)EDTA was increased, and all the Fe(III)EDTA reduction efficiencies were close to 100% when the mole ratio was more than 0.5. On the other hand, an alkaline environment did not favor the conversion of Fe(III)EDTA by VC. The Fe(III)EDTA conversion slightly increased as the temperature was increased. Moreover, compared with other reduction systems, ascorbic acid (VC) was found to be more powerful in reducing Fe(III)EDTA, especially in air. In addition, VC only exhibited powerful ability in the conversion of Fe(III)EDTA to Fe(II)EDTA and hardly reduced Fe(II)EDTA–NO. Finally, the stoichiometry of Fe(III)EDTA reduction by ascorbic acid was derived. Thus, our study would offer a bridge between foundational research and industrial denitration using the combination of Fe(II)EDTA and VC.
1. Introduction
The extensive utilization of fossil fuels has caused a series of serious environmental problems including acidification, photochemical smog, eutrophication, and ozone depletion.1 It is generally considered that nitrogen oxide (NOx) and sulfur dioxide (SO2) are the main pollutants that originate abundantly from fuel gases.2 Therefore, the emissions of NOx and SO2 are strictly controlled by governments all over the world. To date, SO2 can be easily removed by wet flue gas desulfurization (WFGD) because of its high solubility in water.3 However, it is difficult to remove NO (accounting for 95% in total NOx) via wet flue gas desulfurization (WFGD) due to low solubility of NO in water. For this reason, several approaches, including the addition of an oxidizing agent, such as KMnO4,4 NaClO2,5 and H2O2,6 to oxidize NO to the more soluble NO2 and the use of a chelating agent to unite NO to form nitrosyl complexes,7 have been refined to improve NO absorption.
Fe(II)EDTA as an absorbent of nitric oxide (NO) from the flue gas has been widely investigated since the 1970s by many research groups because of the high complexing ability of NO; Fe(II)EDTA can rapidly capture NO to produce the ferrous–nitrosyl complexes Fe(II)EDTA–NO, whose equilibrium constant is about 107 M−1. However, a notable shortcoming of Fe(II)EDTA is that it can be readily oxidized with dissolved oxygen to produce inanimate Fe(III)EDTA.8 The reactions are shown as follows:
|
Fe(II)EDTA2− + NO(L) → Fe(II)EDTA–NO2−
| (2) |
|
4Fe(II)EDTA2− + O2 + 4H+ → 4Fe(III)EDTA− + 2H2O
| (3) |
Therefore, to maintain outstanding NO removal, it is necessary to transform Fe(III)EDTA to Fe(II)EDTA via a reduction reaction.
Sulfur-bearing derivatives (sulfite, bisulfite, dithionite, Na2S2O8, etc.) have been extensively associated with Fe(II)EDTA to improve NO absorption.9–12 Specifically, SO32−, HSO3−, and S2O4− have been used as reducing agents in the transformation of Fe(III)EDTA to Fe(II)EDTA, among which the reducibility of sulfite and bisulfite is relatively weak, and the dithionite ion is easily deteriorated in air, losing the strong reducing power. Therefore, they can hardly maintain high removal efficiency of NO for a long time. An enhanced absorption of NO using Na2S2O8 has been accomplished via a synergistic reaction. Under the catalytic action of Fe(II)EDTA, Na2S2O8 was decomposed to the sulfate radical and hydroxyl radical for enhancing the oxidation and absorption of NO; moreover, the derived ions HSO4− were produced, which could reduce Fe(III)EDTA to Fe(II)EDTA. However, the synergistic reaction between Na2S2O8 and Fe(II)EDTA was limited. Moreover, different bacteria, such as Escherichia coli FR-2 and Klebsiella sp. strain FD-3, have been employed to regenerate Fe(II)EDTA.13,14 However, low Fe(III)EDTA reduction efficiency and the isolation and culture of bacteria, whose requirements are complicated, would result in high operating costs. In addition, activated carbon,15 selenium,16 hydrazine (N2H4),17 metal powders (Zn, Fe, and Al),18 polyphenolic compounds,19 and other reducing agents have been found to be efficient for the reduction of Fe(III)EDTA at ambient temperature. However, due to the complicated process, environmental pollution, and high cost, the commercialization of the abovementioned methods does not appear to be very successful.
Ascorbic acid (vitamin C) is an important biological reductant that is ubiquitous in humans and animals and non-toxic.20 In addition, it shows significant reducibility in the reduction of methylene blue,21 hexavalent chromium,22 and preparation of nanomaterials. Inspired by this, herein, we proposed a strategy of applying ascorbic acid as a reducing agent to enhance the regeneration of Fe(II)EDTA.
2. Materials and methods
2.1. Chemicals
Ascorbic acid (VC) was supplied by Tianjin Kermel Chemical Reagent Co., LVC., China, and used without additional purification. Na2EDTA (99.0%), FeSO4·7H2O (99.0%), NH4Fe(SO4)2·12H2O (99.0%), Zn (99.0%), and Na2S2O4 (99.0%) were purchased from Tianjin Kermel Chemical Reagent Co., LVC., China. N2 (99.999%) and NO (99.99%) were obtained from Guangzhou Yuejia Gas Co., China. All chemicals were analytical grade reagents.
2.2. Fe(III)EDTA reduction by VC under anoxic conditions with different parameters
A 250 mL flask with a pH electrode was set on a heat collection-constant temperature-type magnetic stirrer (Fig. 1). Then, 250 mL aqueous Fe(III)EDTA solution was obtained by blending Na2EDTA and NH4Fe(SO4)2·12H2O in the flask. Then, the solution was separated from atmospheric oxygen using a 3 L min−1 continuous N2 (99.999%) stream. Then, the pH value was adjusted using the H2SO4 and NaOH solution. The Fe(III)EDTA reduction was initiated after the addition of VC to the Fe(III)EDTA solution at the stirring speed of 2500 rpm. Finally, the Fe(II)EDTA concentration of the solution was measured at specific time intervals. The effects of the initial Fe(III)EDTA concentration, the mole ratio of VC to Fe(III)EDTA, pH value, and temperature on the Fe(III)EDTA reduction with VC were systematically investigated (the experimental conditions can be seen in Table 1).
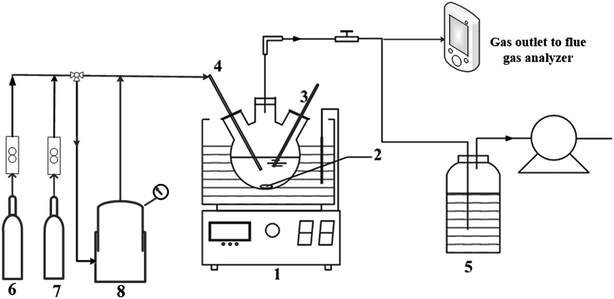 |
| Fig. 1 Experimental apparatus for Fe(III)EDTA reduction by ascorbic acid ((1) heat collection-constant temperature type magnetic stirrer; (2) magnetic stirrer; (3) the pH electrode; (4) inlet for nitrogen or a mixture of NO and N2; (5) buffer tank; (6) N2 cylinder; (7) NO cylinder; and (8) cylinder containing a mixture of NO and N2). | |
Table 1 Initial experimental conditions employed for Fe(III)EDTA reduction by VC
Serial no. |
Parameter |
[Fe(III)EDTA]0 |
[VC]/[Fe(III)]0 |
pH |
Temperature |
1 |
[Fe(III)EDTA]0 |
0.002 M |
0.5 |
6.0 |
60 °C |
0.004 M |
0.008 M |
0.01 M |
2 |
[VC]/[Fe(III)]0 |
0.002 M |
0.25 |
6.0 |
60 °C |
0.5 |
0.75 |
1 |
3 |
pH |
0.002 M |
0.5 |
4.3 |
60 °C |
6 |
7 |
9.3 |
4 |
Temperature |
0.002 M |
0.5 |
6.0 |
30 °C |
40 °C |
50 °C |
60 °C |
2.3. Fe(III)EDTA reduction by VC in air
To investigate the Fe(III)EDTA reduction by VC in air, the reactions were conducted in air at [Fe(III)EDTA]0 = 0.002 mol L−1, T = 30 °C, and pH = 6.0 using VC at the initial concentrations of 0.002, 0.004, 0.008, and 0.016 M. The reduction operation was similar to that performed under anaerobic conditions except that the flask was not stoppered and the solution was directly exposed to air. Finally, the Fe(II)EDTA concentration was measured at specific time intervals. In addition, to highlight the advantages of VC in the Fe(III)EDTA reduction, Zn and Na2S2O4 were used to reduce Fe(III)EDTA in air at [Fe(III)EDTA]0 = 0.002 mol L−1, T = 30 °C, and pH = 6.0.
2.4. Relevance for Fe(II)EDTA–NO reduction
According to a method reported in literature,23 in this study, 250 mL 0.01 mol L−1 Fe(III)EDTA was prepared in a 250 mL flask and maintained under N2 positive pressure. Then, 0.005 M VC was added to the flask to reduce Fe(III)EDTA to Fe(II)EDTA at 30 °C and pH = 6.0. After the reduction reaction was completed, the Fe(II)EDTA–NO complex solution was prepared by bubbling a known mixture of NO and N2 through the produced Fe(II)EDTA solution until the NO concentration (determined using a NO analyzer, KM950) in the outlet was equal to that in the inlet. Then, 0.005 M VC was again added to reduce Fe(II)EDTA–NO. Moreover, the changes in the concentrations of Fe(III)EDTA and Fe(II)EDTA–NO were measured at specific time intervals, and color change during the reduction process was analyzed.
2.5. Analytical methods
The Fe(II)EDTA concentration was determined by o-phenanthroline colorimetric method at the absorbance of 510 nm9. On the other hand, the concentration of Fe(II)EDTA–NO was detected using a UV/vis spectrophotometer at the absorbance of 434 nm.24 The Fe(III) concentration could be calculated from the difference between the total concentration of Fe and the concentration of Fe(II).25 The dehydroascorbic acid concentration was measured by the 2,4-dinitrophenylhydrazine method.26 The experimental data are the mean values of triplicate experiments along with the standard deviation.
The concentration of NO was analyzed by a flue gas analyzer (KM950, KANE International Ltd) after the gas stream passed through the drying tube filled with anhydrous calcium chloride.
The NO removal efficiency was calculated using the following equation:
|
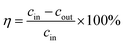 | (4) |
where
η is the NO removal efficiency with the unit of %;
cin is the inlet concentration of NO in ppm; and
cout is the outlet concentration of NO in ppm.
3. Results and discussion
3.1. Effect of the initial concentration of Fe(III)EDTA on the Fe(III)EDTA reduction
Experiments were carried out to investigate the effect of Fe(III)EDTA concentration on the Fe(III)EDTA reduction at pH 6.0, temperature = 60 °C, and [VC]/[Fe(III)] = 0.5. The experimental results are shown in Fig. 2. It was observed that the Fe(II)EDTA concentration increased with an increase in the initial Fe(III)EDTA concentration. For example, the produced Fe(II) concentrations were 0.00197, 0.00405, 0.00763, and 0.00948 M, corresponding to the initial Fe(III)EDTA concentrations of 0.002, 0.004, 0.008, and 0.01 M. The explanation is that the mass transfer impetus between the surface of VC and the liquid bulk gets enhanced as the Fe(III)EDTA concentration increases. The increase in the Fe(III)EDTA concentration on the surface of VC is favorable for the Fe(II)EDTA reduction. In addition, the reduction efficiencies in all the cases exceeded 95%, showing that VC had powerful Fe(III)EDTA reduction ability.
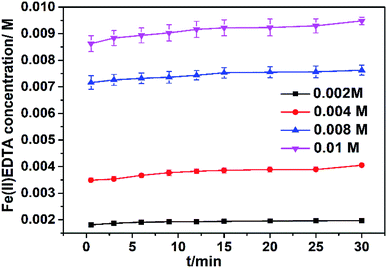 |
| Fig. 2 Fe(II)EDTA concentration change with time at different Fe(III)EDTA concentrations. Conditions: temperature = 60 °C, original mole ratio of VC to Fe(III)EDTA = 0.5; and original pH value = 6.0. | |
3.2. Effect of the mole ratio of VC to Fe(III)EDTA on the Fe(III)EDTA reduction
The percentage of Fe(III) converted to Fe(II) significantly depends on the initial mole ratio of VC to Fe(III)EDTA. The effect of this mole ratio on the Fe(III)EDTA conversion was investigated in a 250 mL solution by varying the ratio of VC to Fe(III)EDTA from 0.25 to 1 at pH 6, [Fe(III)EDTA] = 0.002 M, and temperature = 60 °C. Fig. 3 indicates that the reduction rate increases as the molar ratio increases. For example, the produced Fe(II)EDTA concentrations were 0.00106, 0.00197, 0.00198, and 0.00198 M, corresponding to the mole ratio of 0.25, 0.5, 0.75, and 1. The reason is that more active sites can be obtained at higher initial molar ratios that will lead to higher Fe(II)EDTA regeneration rates. Note that the reduction efficiency at the mole ratio of 0.25 was about 50%; however, all the Fe(III)EDTA reduction efficiencies were close to 100% at the mole ratio of 0.5, 0.75, and 1.
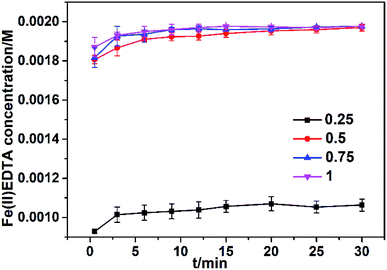 |
| Fig. 3 Fe(II)EDTA concentration change at different original molar ratios of VC to Fe(III)EDTA. Conditions: temperature = 60 °C, Fe(III)EDTA concentration = 0.002 M; and original pH value = 6.0. | |
3.3. Effect of pH on the Fe(III)EDTA reduction
The effect of pH on the Fe(III)EDTA conversion by VC was studied in the pH range of 4.3–9.3 while keeping the other parameters unchanged. The Fe(III)EDTA conversion within 30 min is presented in Fig. 4. In Fig. 4, it was observed that initial pH had a significant impact on the Fe(III)EDTA reduction, and the reduction rate increased as the pH value decreased. Furthermore, lower Fe(III)EDTA conversion was found in an alkaline solution (pH 9.3), whereas the Fe(III)EDTA conversion increased rapidly to 0.00191 M when the initial pH of the solution was 4.3. Thus, an alkaline environment is unfavorable for the Fe(III)EDTA conversion by VC; the reason is that VC itself is acidic and becomes unstable in an alkaline solution.
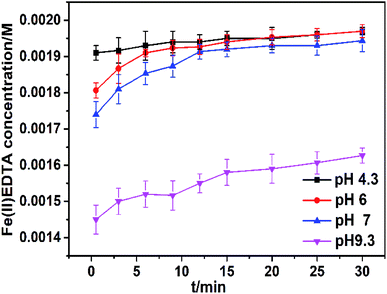 |
| Fig. 4 Fe(II)EDTA concentration variation at different pH values in the range of 4.3–9.3. The reaction parameters: temperature = 60 °C; 0.001 M VC; and [Fe(III)EDTA]0 = 0.002 M. | |
3.4. Effect of temperature on the Fe(III)EDTA reduction
The effect of temperature on the Fe(III)EDTA conversion was explored at pH 6.0. The experimental results depicted in Fig. 5 demonstrate that the Fe(III)EDTA conversion slightly increases as the temperature increases. However, 30 min after the start of the reaction, all the Fe(III)EDTA conversion efficiencies obtained were up to about 98%. On the one hand, high temperatures can accelerate the molecule movement and increase the chemical rate. On the other hand, high temperatures can also promote the decomposition of VC. Therefore, the slight increase in the Fe(III)EDTA conversion with the increasing temperature was the result of the interaction between the abovementioned two effects.
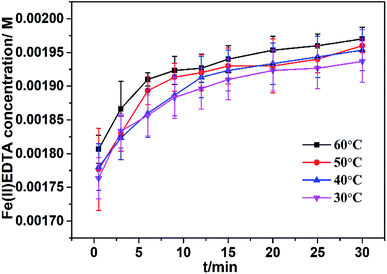 |
| Fig. 5 Fe(II)EDTA concentration variation at different temperatures. The reaction parameters: pH = 6; original VC concentration = 0.001 M; and [Fe(III)EDTA]0 = 0.002 M. | |
3.5. Fe(III)EDTA reduction by VC in air
Industrial flue gases in China generally contain 3–9% (v/v) oxygen, which imposes a significant effect on the Fe(III)EDTA reduction. Therefore, it is necessary to investigate the Fe(III)EDTA reduction by VC in air. In Fig. 6, the results show that VC also exhibits excellent Fe(III)EDTA reduction ability in air, and the Fe(III)EDTA reduction is improved at higher VC concentrations; for example, more than 95% Fe(III)EDTA reduction efficiency can be maintained for 25 min at 0.002 M VC; moreover, more than 90% Fe(III)EDTA reduction efficiency can be maintained for 240 min at 0.016 M VC.
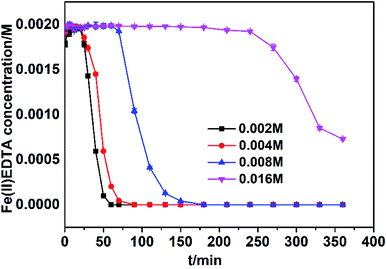 |
| Fig. 6 Fe(II)EDTA concentration variation at different VC concentrations in air. Other reaction parameters: pH = 6; temperature = 30 °C; and [Fe(III)EDTA]0 = 0.002 M. | |
3.6. Comparison between the Fe(III)EDTA reduction efficiency obtained herein and those obtained in some previously reported studies
Via our related experiments, it has been found that ascorbic acid (VC) possesses high Fe(III)EDTA reduction efficiency. However, it is still uncertain whether VC has an advantage over other systems in the Fe(III)EDTA reduction. For this reason, the results of Fe(III)EDTA reduction by VC obtained in our study were compared with those of some other systems reported in the literature; however, comparisons between efficiencies of Fe(III)EDTA reduction achieved by various systems were difficult to make due to dissimilarities in the reaction conditions used by different research teams. The comparisons of the Fe(III)EDTA reduction efficiency obtained herein with those obtained using different systems are presented in Table 2; the selected data in Table 2 show the best performance in terms of Fe(III)EDTA reduction reported in the respective references. Further, from Table 2, it can be observed that only Zn and Na2S2O4 are close to VC in terms of the Fe(III)EDTA reduction efficiency in an anaerobic environment. All three showed very high reduction rates. However, the mole ratio of VC to Fe(III)EDTA was much lower than that of Zn to Fe(III)EDTA. Thus, the amount of VC required to obtain similar reduction efficiency was much less than that of Zn. In addition, Zn and Na2S2O4 get easily oxidized in air; thus, to date, it is unknown whether Zn and Na2S2O4 show a remarkable effect on the Fe(III)EDTA reduction in air. To further explore the advantage of VC, the Fe(III)EDTA reduction in air was conducted using 0.062 M Zn, 0.070 M Na2S2O4, and 0.016 M VC, having the same price, to achieve economic performances, and the reduction efficiencies were compared; it was observed that the times for which more than 90% reduction efficiency was maintained were 3 min, 15 min, and 240 min in an aerobic environment, corresponding to 0.062 M Zn, 0.070 M Na2S2O4, and 0.016 M VC (Table 3). In other words, with the same cost, the Fe(III)EDTA reduction efficiency of VC was best. Therefore, VC is a better reducing agent for Fe(III)EDTA reduction in terms of economy and efficiency.
Table 2 Comparisons between the simultaneous Fe(III)EDTA reduction in different systems (the details of the experimental conditions could be obtained from respective references)
Reference |
Reduction material |
Reduction efficiency (initial concentration) |
Mole ratio of reducing agent to Fe(III)EDTA |
Required time |
14 |
Escherichia coli FR-2 |
87% (6 mM) |
— |
9 h |
13 |
Klebsiella sp. strain FD-3 |
52.4% (10 mM) |
— |
12 h |
18 |
Zn |
100% (50 mM) |
10 |
Instantaneous |
|
Al |
60% (100 mM) |
10 |
40 min |
|
Sn |
<20% (50 mM) |
10 |
60 min |
27 |
Fe |
100% (10 mM) |
10 |
∼40 min |
28 |
Na2S2O4 |
99.5% (50 mM) |
0.7 |
3 min |
29 |
Na2SO3 |
About 65% (10 mM) |
10 |
120 min |
30 |
Na2SO3/Na2SeSO3 mixture |
69.4% (10 mM) |
100 |
— |
31 |
Activated carbon/Na2SO3 |
About 70% (10 mM) |
20 |
200 min |
32 |
Thiourea dioxide |
100% (2 mM) |
5 |
30 min |
This work |
VC |
100% |
0.5 |
0.5 min |
Table 3 Economic analysis of Zn, Na2S2O4 and VC
Reduction material |
Zn |
Na2S2O4 |
VC |
Obtained by the Alibaba internet website. |
Approximate pricea |
$2857 per ton |
$928 per ton |
$4142 per ton |
Unit-price by mole |
$186 per kmol |
$163 per kmol |
$726 per kmol |
Concentration corresponding to the same price |
0.062 M |
0.070 M |
0.016 M |
Time of maintaining 90% efficiency in air |
3 min |
15 min |
240 min |
3.7. Relevance for Fe(II)EDTA–NO reduction
Via the abovementioned analysis and discussions, VC was found to be a powerful reducing agent for the Fe(III)EDTA reduction. In addition, color change can indicate this conclusion. It was found from Fig. 7, (A → B → C) that the solution varied from light yellow Fe(III)EDTA to colorless Fe(II)EDTA; however, when the nitric oxide and nitrogen mixture was bubbled into the colorless Fe(II)EDTA solution, black-brown Fe(II)EDTA–NO appeared, revealing that the product of Fe(III)EDTA reduction with VC could effectively capture NO. These color changes were in accordance with the results reported in relevant literature.16,33 It was further confirmed that VC could transform Fe(III)EDTA into Fe(II)EDTA.
 |
| Fig. 7 Color change during the Fe(III)EDTA reduction by VC ((A) color of 0.01 mol L−1 Fe(III)EDTA with pH 6.0; (B) color of the Fe(III)EDTA solution after reduction by 0.005 mol L−1 VC at 30 °C for 30 min; (C) color of the solution after a known mixed gas of NO and N2 was bubbled into (B); and (D) color of the Fe(II)EDTA–NO solution after reduction by 0.005 mol L−1 VC at 30 °C for 30 min). | |
Fe(II)EDTA–NO is a by-product of flue gas denitrification, which uses Fe(II)EDTA. Thus, the conversion of Fe(II)EDTA–NO to Fe(II)EDTA was also very significant for the NO removal process. However, it is unknown whether VC can transform Fe(II)EDTA–NO to Fe(II)EDTA. Therefore, the color change of the Fe(II)EDTA–NO solution during the reduction process was investigated (Fig. 7, C → D). It was found that the black-brown solution remain unchanged after VC was added to Fe(II)EDTA–NO, and the Fe(II)EDTA–NO concentration was almost unchanged. The color variation illustrates that VC only exhibits powerful conversion efficiency for reducing Fe(III)EDTA to Fe(II)EDTA.
3.8. Reaction mechanism
According to a previous study,34 VC as a reducing agent can be oxidized to dehydroascorbic acid. Consequently, during the Fe(III)EDTA reduction by VC, dehydroascorbic acid is speculated as the main product of VC oxidation.
For verifying our conjecture, the changes occurring in dehydroascorbic acid during the reduction process were investigated. It was found that dehydroascorbic acid was produced during the process, and its concentration increased with an increase in Fe(III)EDTA concentration (Fig. 8). Specifically, the dehydroascorbic acid concentrations were increased by 0.00091, 0.00186, 0.00361, and 0.00457 M during 30 min corresponding to 0.002, 0.004, 0.008, and 0.01 M initial Fe(III)EDTA concentration. Moreover, it was found that the ratio of produced Fe(II)EDTA to generated dehydroascorbic acid was close to 2
:
1 at four different initial concentrations of Fe(III)EDTA. Thus, via the abovementioned observations, it is proved that dehydroascorbic acid can be considered as the main product of VC oxidation.
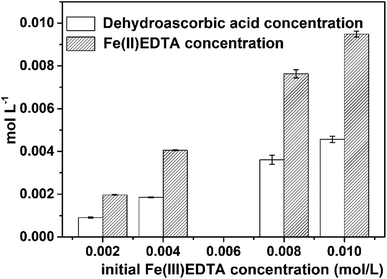 |
| Fig. 8 The concentrations of the produced dehydroascorbic acid and Fe(II)EDTA during 30 min. Conditions: original mole ratio of VC to Fe(III)EDTA = 0.5; initial pH = 6.0; and T = 60 °C. | |
Furthermore, the pH value variation is closely connected to Fe(III)EDTA reduction by VC. We found that the pH values of the Fe(III)EDTA solution after its reduction by VC dropped; this revealed that the H+ was produced when Fe(III)EDTA was reduced by VC.
Based on the charge and element conservation principle, a credible stoichiometry of Fe(III)EDTA reduction with VC was achieved:
|
C6H8O6 + 2Fe(III)EDTA− → 2Fe(II)EDTA2− + C6H6O6 + 2H+
| (5) |
In addition, in Fig. 3, we found that when the mole ratio of VC to Fe(III)EDTA was 0.5
:
2, about 50% of Fe(III)EDTA was reduced to Fe(II)EDTA; however, about 100% Fe(III)EDTA was reduced to Fe(II)EDTA when the molar ratios of VC to Fe(III)EDTA were 1
:
2, 1.5
:
2, and 2
:
2. Thus, the reduction efficiency at different molar ratios of VC to Fe(III)EDTA further confirmed that the stoichiometric ratio of VC to Fe(III)EDTA was 1
:
2, and the chemical reaction equation of the Fe(III)EDTA reduction by VC was determined as eqn (5).
3.9. NO removal
The denitrification experiment using the Fe(II)EDTA solution with VC was conducted in a lab-scale bubbling reactor, as shown in Fig. S1.† The absorption liquid was 500 mL aqueous solution with the initial Fe(II)EDTA concentration of 0.002 M. The inlet NO concentration was 500 ppm. The oxygen concentration in the simulated flue gas was 7% (volume). The gas flow rate was 0.4 L min−1. The experimental results are shown in Fig. 9. We can observe that the NO removal efficiency decreases sharply from 90% to 59.36% in the first 35 min, during which the absorption liquid only contains Fe(II)EDTA. The decrease observed in the NO removal efficiency was mainly due to the oxidation of Fe(II)EDTA by dissolved oxygen present in the flue gas. Then, 0.1761 g VC (equivalent to 0.002 mol L−1 of VC in 500 mL absorbent solution) was added to the absorption liquid at the 35th min. The NO removal efficiency increased to 87.67% and could remain above 76% for 35 min. Thus, the experimental results illustrate that NO removal with Fe(II)EDTA can be improved by the addition of VC.
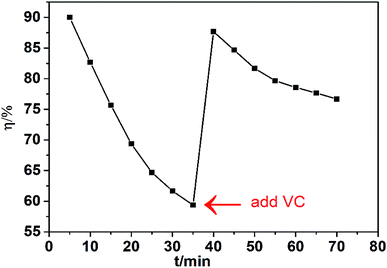 |
| Fig. 9 The NO removal efficiency with time. | |
4. Conclusion
The specific conclusions are as follows:
(1) Ascorbic acid (VC) was found to be a powerful reducing agent for the Fe(III)EDTA reduction. In addition, the stoichiometry of Fe(III)EDTA reduction with ascorbic acid was derived as follows:
C6H8O6 + 2Fe(III)EDTA− → 2Fe(II)EDTA2− + C6H6O6 + 2H+ |
(2) Fe(II)EDTA concentration increased as the initial Fe(III)EDTA concentration increased. Furthermore, the reduction efficiency increased with an increase in the mole ratio of VC to Fe(III)EDTA, and all the Fe(III)EDTA reduction efficiencies were close to 100% when the mole ratio was more than 0.5. Thus, an alkaline environment was unfavorable for Fe(III)EDTA conversion by VC. Moreover, the Fe(III)EDTA conversion slightly increased as the temperature increased.
(3) Upon comparing the present reduction system with other reduction systems, it was established that ascorbic acid (VC) was more powerful in reducing Fe(III)EDTA, especially in air.
(4) VC exhibited powerful ability only in the conversion of Fe(III)EDTA to Fe(II)EDTA and hardly reduced Fe(II)EDTA–NO.
(5) Thus, these findings could provide constructive information for the removal of NO in industrial applications using a mixed Fe(II)EDTA and ascorbic acid system.
Conflicts of interest
There are no conflicts to declare.
Acknowledgements
The project was supported by National Natural Science Foundation of China (No. 21808031).
References
- F. He, X. Deng and J. Ding, RSC Adv., 2018, 8, 32138–32145 RSC.
- K. Liu, Q. Yu, J. Liu, K. Wang, Z. Han, Y. Xuan and Q. Qin, New J. Chem., 2017, 41, 13993–13999 RSC.
- M. Chen, B. Xie, F. He and X. Deng, Energy Fuels, 2019, 33, 1383–1391 CrossRef CAS.
- H. Chu, T.-W. Chien and S. Li, Sci. Total Environ., 2001, 275, 127–135 CrossRef CAS PubMed.
- Y. Zhao, T.-x. Guo, Z.-y. Chen and Y.-r. Du, Chem. Eng. J., 2010, 160, 42–47 CrossRef CAS.
- Y. Liu, J. Zhang, C. Sheng, Y. Zhang and L. Zhao, Chem. Eng. J., 2010, 162, 1006–1011 CrossRef CAS.
- F. He, X. Deng and M. Chen, Chemosphere, 2017, 168, 623–629 CrossRef CAS PubMed.
- S. Wang, Z. Qi, Z. Gu, Z. Wang and Z. Ping, J. Energy Inst., 2016, 90, 522–527 CrossRef.
- T. T. Suchecki, B. Mathews and H. Kumazawa, Ind. Eng. Chem. Res., 2005, 44, 4249–4253 CrossRef CAS.
- E. Sada, H. Kumazawa, I. Kudo and T. Kondo, Ind. Eng. Chem. Process Des. Dev., 1980, 19, 377–382 CrossRef CAS.
- E. Sada, H. Kumazawa and Y. Takada, Ind. Eng. Chem. Fundam., 1984, 23, 60–64 CrossRef CAS.
- Y. G. Adewuyi and M. A. Khan, Chem. Eng. J., 2015, 281, 575–587 CrossRef CAS.
- Z. Zhou, G. Jing and X. Zheng, Bioresour. Technol., 2013, 132, 210–216 CrossRef CAS PubMed.
- W. Li, C.-Z. Wu, S.-H. Zhang, K. Shao and Y. Shi, Environ. Sci. Technol., 2007, 41, 639–644 CrossRef CAS PubMed.
- X. Yang, L. Yang, L. Dong, X. Long and W. Yuan, Energy Fuels, 2015, 25, 4248–4255 CrossRef.
- K. Xiang, H. Liu, B. Yang, C. Zhang, S. Yang, Z. Liu, C. Liu, X. Xie, L. Chai and X. Min, Environ. Sci. Pollut. Res., 2016, 23, 8113–8119 CrossRef CAS PubMed.
- T. T. Suchecki and H. Kumazawa, Org. Lett., 1998, 14, 1206–1209 Search PubMed.
- T. T. Suchecki, B. Mathews, A. W. Augustyniak and H. Kumazawa, Ind. Eng. Chem. Res., 2014, 53, 14234–14240 CrossRef CAS.
- M. H. Mendelsohn and J. B. L. Harkness, Energy Fuels, 1991, 5, 244–248 CrossRef CAS.
- J. Hou, R. Lu, M. Sun, S. A. Baig, T. Tang, L. Cheng and X. Xu, J. Hazard. Mater., 2012, 217–218, 224–230 CrossRef CAS PubMed.
- S. Mowry and P. J. Ogren, J. Chem. Educ., 1999, 76, 970–974 CrossRef CAS.
- X. Xiang-Rong, L. Hua-Bin, L. Xiao-Yan and G. Ji-Dong, Chemosphere, 2004, 57, 609–613 CrossRef PubMed.
- X. Dong, Z. Yu, J. Zhou, H. Li, X. Wang and M. Chen, J. Chem. Technol. Biotechnol., 2013, 89, 111–116 CrossRef.
- V. Zang and R. Van Eldik, Inorg. Chem., 1990, 29, 4462–4468 CrossRef CAS.
- A. E. Harvey, J. A. Smart and E. S. Amis, Anal. Chem., 1955, 27, 26–29 CrossRef CAS.
- J. H. Roe and M. J. Oesterling, J. Biol. Chem., 1944, 152, 511–517 CAS.
- F. He, X. Deng and M. Chen, Fuel, 2016, 186, 605–612 CrossRef CAS.
- T. T. Suchecki, A. Barbara Mathews and H. Kumazawa, Ind. Eng. Chem. Res., 2005, 44, 4249–4253 CrossRef CAS.
- T. T. Suchecki, E. Sada and H. Kumazawa, Ind. Eng. Chem. Res., 1991, 30, 2201–2204 CrossRef CAS.
- K. Xiang, L. Hui, B. Yang, Z. Cong, Y. Shu, Z. Liu, L. Cao, X. Xie, L. Chai and X. Min, Environ. Sci. Pollut. Res., 2016, 23, 8113–8119 CrossRef CAS PubMed.
- X. J. Yang, Y. Lin, D. Li, X. L. Long and W. K. Yuan, Energy Fuels, 2011, 25, 4248–4255 CrossRef CAS.
- F. He, Y. Qian and J. Xu, Energy Fuels, 2019, 33(4), 3331–3338 CrossRef CAS.
- S.-H. Zhang, W. Li, C.-Z. Wu, H. Chen and Y. Shi, Appl. Microbiol. Biotechnol., 2007, 76, 1181–1187 CrossRef CAS PubMed.
- X. R. Xu, H. B. Li, X. Y. Li and J. D. Gu, Chemosphere, 2004, 57, 609–613 CrossRef CAS PubMed.
Footnote |
† Electronic supplementary information (ESI) available. See DOI: 10.1039/c9ra02678a |
|
This journal is © The Royal Society of Chemistry 2019 |
Click here to see how this site uses Cookies. View our privacy policy here.