DOI:
10.1039/C9RA08640D
(Paper)
RSC Adv., 2019,
9, 36658-36663
Low-temperature selective catalytic reduction of NOx with NH3 over an activated carbon-carbon nanotube composite material prepared by in situ method†
Received
22nd October 2019
, Accepted 6th November 2019
First published on 11th November 2019
Abstract
Ce-supported activated carbon–carbon nanotube composite (Ce/AC-CNTs) catalyst was prepared by in situ formation of CNTs on AC and then modified by Ce. This Ce/AC-CNTs catalyst was subsequently used for low-temperature selective catalytic reduction of NOx with NH3 (NH3-SCR). The NO conversion of Ce/AC-CNTs was 1.41 times higher than that of Ce/AC at 150 °C with good SO2 tolerance. The catalysts were analyzed by N2 physisorption, SEM, XRD, NH3-TPD, XPS, and Raman technologies. The results showed that the introduction of CNTs could form new mesopores and increase the amount of surface chemisorbed oxygen and acid sites, which all contribute to the high NH3-SCR activity.
1. Introduction
Nitrogen oxides (NOx) originating from fossil fuel combustion have caused serious environmental pollution problems, such as photochemical smog, acid rain, ozone layer depletion, and even global warming.1,2 Among various denitrification technologies the selective catalytic reduction of NOx with NH3 (NH3-SCR) is the most successful and widely applied technology.3,4 The V2O5–WO3(MoO3)/TiO2 catalyst is used as a typical commercial NH3-SCR catalyst which works at relatively high temperatures (300–400 °C).5,6 However, some inevitable disadvantages of the commercial catalysts, such as the narrow operation temperature window and the poor low-temperature catalytic activity, are still observed.7,8 Therefore, developing an efficient catalyst for low temperature NH3-SCR reaction is highly desirable.
Activated carbon (AC) have been widely used as the support for NH3-SCR catalysts due to its low price and developed porous structure.9 Wang et al. found that the CeMn/AC catalyst showed 44% NO removal efficiency at 160 °C.10 Jing et al. reported that the V2O5/AC exhibited 60% NO conversion at 150 °C.11 However, the AC-catalysts were easily deactivation in the presence of SO2.12 Therefore, further efforts should be carried out to improve SO2 resistance of SCR catalysts.
Carbon nanotubes (CNTs) were used as support for NH3–SCR reaction in recent years due to their high adsorbability for NOx and NH3.13 Besides, NO could even be decomposed directly over CNTs,14 and importantly, the CNTs-catalyst presented good SO2 and water resistance.15 Luo et al. found that NO can be 100% decomposed at 600 °C on CNTs.16 Bai et al. reported that the NO conversion of V2O5/CNTs (50%) was higher than that on V2O5/AC (38%) at 250 °C, and V2O5/CNTs also had a better SO2 resistance compared with V2O5/AC.17 Cai et al. found that the catalytic activity of Fe@Mn@CNTs is barely affected by the SO2 and exhibits an over 85% NO conversion temperature window from 150 to 270 °C.18 Santillan-Jimenez et al. investigated the existence of H2O and noted slight inhibitory effects on the catalytic activity of the SCR catalyst when CNTs were used as the support.19 Thus, considering of the cost and catalytic performance, an activated carbon-carbon nanotubes composite (AC-CNTs) was used for NH3-SCR reaction.
Due to the low dispersion and self-aggregation property of carbon nanotubes, it is difficult to get carbon nanotubes into AC by mechanical mixing method.20 Su et al. successfully prepared AC-CNT (CNF) composite by treating the Fe/AC catalyst in flowing C2H4/H2.21 Chen et al. also found that the CNTs were successfully grew on Fe-deposited Si substrate via the chemical vapor deposition method using a CH4–CO2 gas mixture.22 However, the use of AC-CNTs composites in the NH3-SCR reaction has not been reported.
In this work, an AC-CNTs composite was prepared via CH4 decomposition on AC. Then the Ce/AC-CNTs catalysts were obtained by an impregnation method. This work aims to combine the advantages of CNTs and AC and used the Ce/AC-CNTs catalyst for NH3-SCR reaction at low temperature. The physicochemical properties of catalysts were also comprehensively discussed in the present work.
2. Materials and methods
2.1 Materials
The AC (C 78.68%, N 0.27%, O 18.59%, and H 2.46%) was used as the precursor to prepare activated carbon-CNTs (AC-CNTs) bought from Xinhua Activated Carbon Co., Ltd. The agents used in this study, such as Ni(NO3)2·6H2O and Ce(NO3)3·6H2O, were of analytical reagent grade (AR) and purchased from Chengdu Chron Chemicals Co., Ltd.
2.2 Preparation of catalysts
The AC-CNTs were prepared via in situ formation of CNTs (by methane decomposition) on AC. First, AC was impregnated with a certain amount of Ni(NO3)2 solution for 24 h at 25 °C and then dried at 80 °C for 12 h to obtain the Ni/AC precursor, which was the catalyst of methane decomposition. Subsequently, the obtained sample was pretreated at 750 °C under N2 flow for 2 h, and then, cooled to 650 °C (with switching to CH4 atmosphere) for 30 min to produce CNTs on AC (AC-CNTs). The obtained sample was named AC-CNTs. The AC and AC-CNTs impregnated with the Ce(NO3)3 solution and calcined at 450 °C for 6 h under N2 atmosphere were donated as Ce/AC and Ce/AC-CNTs, respectively.
2.3 Denitrification test
NH3-SCR experiments of the prepared samples were performed in a fixed-bed quartz tube reactor with an internal diameter of 10 mm. The reaction temperature and space velocity (GHSV) was 150 °C and 50
000 h−1, respectively. The total flow rate of gas was 500 mL min−1, and the typical reactant gas contained 500 ppm of NO, 550 ppm of NH3, 5 vol% of O2, 50 ppm (142.8 mg m−3) of SO2 (when used), 10 vol% of H2O (when used), and balance of N2. A flue gas analyzer (Gasboard-3000, Wuhan Cubic Optoelectronics Co., Ltd., CN) was used to determine the inlet and outlet NO concentrations online. The NO reduction with NH3 of all samples was beginning (was started) at the NO saturated sample under the same denitrification condition to eliminate the adsorption effect of NO.
2.4 Characterization of adsorbents
N2 adsorption–desorption experiments of the prepared samples were measured at 77 K using the ASAP 2460 instrument (Micromeritics Instrument Co., Ltd., USA). The specific surface area (SBET), total pore volume (Vtot), mesopore volume (Vmes), micropore volume (Vmic), and pore size distribution were obtained from the N2 adsorption–desorption isotherms by using the Brunauer–Emmett–Teller (BET) equation, N2 adsorption amount at the maximum relative pressure, Barrett–Joyner–Halenda method, t-plot method, and density functional theory method, respectively. The surface morphology of samples was observed microscopically via scanning electron microscopy (SEM, JSM-7500F, Jeol Co., Ltd., Japan).
The crystal structure of AC was analyzed by X-ray diffraction using an X'Pert PRO MPD diffractometer (Panalytical Co., Ltd., Netherlands). The crystalline phases were identified by comparison with the reference data from the International Center for Diffraction Data (JCPDs).
The NH3-temperature-programming desorption (NH3-TPD) was conducted on a TP-5076 chemisorption analyzer (Tianjin First Industry and Trade Development Co. Ltd., CN). The samples were pretreated at 400 °C in a He flow for 1 h. Subsequently, the samples were cooled down to 30 °C and saturated with NH3 until adsorption equilibrium was reached, followed by blowing with He at the same temperature to avoid NH3 physisorption. The saturated samples were then heated from 30 °C to 800 °C at a rate of 10 °C min−1 in He.
The surface chemistry was determined by X-ray photoelectron spectroscopy using an XSAM-800 spectrometer (Kratos Co., Ltd., UK) with light as the mono Al Kα (1486.6 eV). Raman spectra were collected by a Raman spectrometer (LabRAM-HR, Horiba Co., Ltd., Japan). The wavelength and power were 532 nm and 5 mW, respectively, while the spectral resolution was ±1 cm−1.
3. Results and discussion
3.1 Catalyst characterization
3.1.1 Textural properties. Fig. 1 shows loose and porous structures of the AC surface. After the introduction of CNTs, distinct CNTs were observed on the surface of AC-CNTs with a length distribution of approximately 100–300 nm and diameter of 10–30 nm.
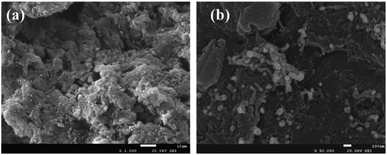 |
| Fig. 1 SEM images of (a) AC and (b) AC-CNTs. | |
N2 adsorption–desorption isotherms and textural properties of the prepared samples are shown in Fig. S1 (seen in ESI†) and Table 1, respectively. The BET surface area of the catalysts varied as follows: AC (803 m2 g−1) > AC-CNTs (774 m2 g−1) > Ce/AC (700 m2 g−1) > Ce/AC-CNTs (599 m2 g−1). Notably, the Vmic evidently decreased after the introduction of CNTs. The Vmic of AC and Ce/AC was 0.28 and 0.24 cm3 g−1 while that of AC-CNTs and Ce/AC-CNTs decreased to 0.24 and 0.17 cm3 g−1, respectively, after CNTs introduction. However, the Vmes of the catalyst displayed an opposite trend to that of Vmic. The Vmes of AC and Ce/AC was 0.24 and 0.19 cm3 g−1 while that of AC-CNTs and Ce/AC-CNTs increased to 0.31 and 0.22 cm3 g−1, respectively, after CNTs introduction. Furthermore, the Vmic/Vtot and average pore size decreased, while the Vmes/Vtot increased after CNTs introduction. These results suggested that pore blockage occurred to a considerable extent upon the loading of Ce species and formation of CNTs due to the obvious decrease of the SBET and Vmic after the introduction of Ce and CNTs.
Table 1 Textural structure parameters of prepared samplesa
Catalyst |
SBET (m2 g−1) |
Vtot (cm3 g−1) |
Vmic (cm3 g−1) |
Vmes (cm3 g−1) |
Vmic/Vtot (%) |
Vmes/Vtot (%) |
Dmean (nm) |
SBET, BET surface area; Vtot, total pore volume; Vmic, micropore volume; Vmes, mesopore volume; Dmean, average pore diameter. |
AC |
803 |
0.57 |
0.28 |
0.24 |
48.2 |
41.4 |
6.42 |
AC-CNTs |
774 |
0.58 |
0.24 |
0.31 |
41.5 |
53.6 |
3.00 |
Ce/AC |
700 |
0.48 |
0.24 |
0.19 |
50.6 |
39.8 |
6.32 |
Ce/AC-CNTs |
599 |
0.43 |
0.17 |
0.22 |
39.5 |
51.1 |
5.22 |
Interestingly, the Vmes of AC increased from 0.28 cm3 g−1 to 0.31 cm3 g−1 for AC after CNT introduction and decreased to 0.22 cm3 g−1 after the further introduction of Ce. This result inferred that the in situ formation of CNTs on AC may form some new mesopores on AC-CNTs. Meanwhile, a certain extent of pore blockage occurred on Ce/AC-CNTs after Ce introduction.
Raman spectra were performed to further study the structure of Ce/AC and Ce/AC-CNTs catalysts, and the results are shown in Fig. 2. The two main peaks were at approximately 1323 cm−1 (D-band) and 1590 cm−1 (G-band).23 The D-band of the catalyst was mainly derived from the disordered carbon or amorphous carbon, whereas the G-band was assigned to the well-ordered carbon. The intensity ratio (ID/IG) of D-band to G-band is an index of the integrity of catalysts.24 As shown in Fig. 2, the ID/IG of Ce/AC (1.2) was lower than that of Ce/AC-CNTs (1.3). The increased ID/IG of Ce/AC-CNTs was attributed to the generation of new defects and surface functional groups during the CNTs formation (methane decomposition on AC). This result suggested that the introduction of CNTs favored the formation of disordered or defected carbon.
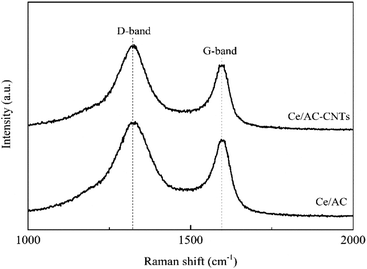 |
| Fig. 2 Comparison of the Raman spectra of Ce/AC and Ce/AC-CNTs. | |
3.1.2 Surface acidity. The surface acidity of catalysts is generally one of the key factors for their denitrification performance in the NH3-SCR reaction. The adsorption and activation of NH3 species over the catalysts were highly dependent on the surface acidity properties of the catalysts. The NH3-TPD experiments were conducted to measure the number of acid sites and strength of acid on the surface of Ce/AC and Ce/AC-CNTs catalysts. The NH3 desorption temperature and integral area of desorption peaks in NH3-TPD profiles could represent the acid strength and the number of acid sites, respectively. As shown in Fig. S3 (seen in ESI†), the Ce/AC and Ce/AC-CNTs catalysts exhibited three desorption peaks during 50 °C-650 °C with the increase in desorption temperature and are denoted as I, II, and III. In the NH3-TPD curves of Ce/AC, the low-temperature desorption peak I centered at approximately 124 °C was attributed to NH3 species desorbed from the weak acid sites. Peak II centered at 179 °C was assigned to desorption of NH3 species from medium to strong acid sites. Peak III centred at 377 °C was related to strong acid sites.25 As reported, the NH4+ ions adsorbed on the Lewis acid sites were more thermally stable than those of Brønsted acid sites. Thus, the desorption peak at low temperature of catalysts was ascribed to the NH4+ ions adsorbed on the Brønsted acid sites, while the desorption peak at high temperature was due to NH3 molecules originating from the Lewis acid sites.26Ce/AC and Ce/AC-CNTs presented three strong NH3 desorption peaks (Fig. S3 in ESI†). As shown in Table 2, the quantitative data (from the area of the desorption peak) of NH3-TPD suggested that the relative amount of acid sites on Ce/AC-CNTs (19.14 mmol g−1) was higher than that of Ce/AC (15.80 mmol g−1). This result implied that the Ce/AC-CNTs catalyst possessed more acid sites than that of Ce/AC. Moreover, the curve of NH3 desorption peaks for Ce/AC-CNTs shifted toward the high temperature region (from 377 °C to 470 °C). This result demonstrated that the strength of acid sites on Ce/AC-CNTs was stronger than that of Ce/AC. Thus, Lewis acidity was strengthened on Ce/AC-CNTs. As reported, the CNTs could supply strong acid sites, and CeO2 supported on CNTs could significantly increase the acidity of CNTs and in favor of the NH3-SCR reaction.27
Table 2 Deconvolution of the NH3-TPD profiles of Ce/AC and Ce/AC-CNTs catalysts
Catalyst |
Peak temp. (°C) |
Relative amount of acid sites (%) |
Total desorption amount (mmol g−1) |
Peak I |
Peak II |
Peak III |
S I |
S II |
S III |
Ce/AC |
124 |
179 |
377 |
24.9 |
36.1 |
39.0 |
15.80 |
Ce/AC-CNTs |
123 |
179 |
470 |
25.4 |
36.1 |
38.5 |
19.14 |
3.1.3 XPS. The binding energy and surface atomic composition of Ce/AC and Ce/AC-CNTs were estimated by XPS analysis. Table 3 shows that the relative content of total oxygen of Ce/AC-CNTs was 14.3%, which was higher than that of Ce/AC (11.6%). The ratios of O/C for Ce/AC-CNTs and Ce/AC were 0.17 and 0.13, respectively. Thus, CNTs introduction could promote the formation of surface total oxygen, which could contribute to the high catalytic activity of Ce/AC-CNTs for NH3-SCR reaction; this outcome was in good agreement with the results of Wang.24
Table 3 XPS results of the catalysts
Sample |
Ce/AC |
Ce/AC-CNTs |
C (%) |
87 |
84.2 |
O (%) |
11.6 |
14.3 |
O/C |
0.13 |
0.17 |
Ce (%) |
1.5 |
1.5 |
(Oβ)/(Oα + Oβ + Oγ) (%) |
38.6 |
42.1 |
The O 1s spectra of Ce/AC and Ce/AC-CNTs are exhibited in Fig. S4 (seen in ESI†). Three distinct peaks were observed for Ce/AC and Ce/AC-CNTs. One major peak that appearing at approximately 529.6 eV is assigned to lattice oxygen (O2−) (denoted as Oα). Meanwhile, two peaks that appeared at relatively high binding energy located at approximately 532.3 and 533.8 eV could be assigned to chemisorbed oxygen (denoted as Oβ) and –O– oxygen (denoted as Oγ).28 The Oβ, which was the most active oxygen, generally had a strong migration capability, and usually adsorbed on the defective sites of catalysts.29
In this study, the relative content of chemisorbed oxygen of Ce/AC-CNTs calculated by Oβ/(Oα + Oβ + Oγ) was 42.1%, which was higher than that of Ce/AC (38.6%). As reported, metal oxides, such as CeO2 and MnO2, could increase the electrochemical active surface area of the catalyst.30 Thus, the introduction of CNTs increased the chemisorbed oxygen and promotion of the electron transfer on the surface of catalyst, these conditions were beneficial to the catalytic activity of Ce/AC-CNTs for the NH3-SCR reaction.31–34
3.2 Catalytic activity
Fig. 3 shows the NO conversions of NH3-SCR reaction over different catalysts. The results showed that the NO conversion (9.4%) over the AC was quite low at 150 °C, whereas the NO conversion over AC-CNTs (<1%) was even lower than that of AC. Moreover, the nickel species on AC-CNTs and Ce/AC-CNTs are mainly in bulk, instead of surface (Table S1 in ESI†), which indicated that the Ni species on catalyst has no obvious effect on denitrification performance. For the Ce-added AC (Ce/AC catalyst), the NO conversion (29.4%) was much higher than that on non-promoted AC (9.4%) due to the presence of the active ceria species. Interesting, compared with Ce/AC, NO conversion evidently improved over Ce/AC-CNTs (41.4%), which was 1.41 times as that of Ce/AC. The effluent gases from stationary sources always contain trace amounts of SO2 and water vapor, which could have inhibitory effects on the NOx removal, especially at low temperature.35 Thus, SO2 and water vapor deactivation experiments were performed to clarify the impacts of SO2 and water vapor on the Ce/AC-CNTs (Fig. 3b). As shown in Fig. 3b, with the absence of SO2, the catalyst maintained NO conversion at approximately 41.4%. When 50 ppm of SO2 was added into the inlet gas, only a slight inhibition effect on NO conversion (decreased by 4.8%) was observed on Ce/AC-CNTs, whereas that of Ce/AC exhibited serious decrease (16.3%) in its NO conversion (Fig. S6 and S7 in ESI†). After the removal of the SO2 gas, the catalytic activity of Ce/AC-CNTs catalyst was restored to approximately 41.4% as before. Moreover, when H2O was added into the inlet gas, the NO conversion of Ce/AC-CNTs decreased by 21.7%, while the NO conversion of Ce/AC decreased by 30.6%.
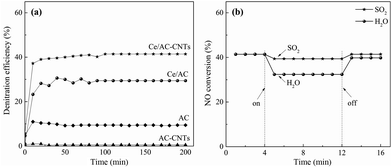 |
| Fig. 3 Variation of (a) NO conversion of AC, AC-CNTs, Ce/AC and Ce/AC-CNTs, and (b) SO2 tolerance and water-resistance of Ce/AC-CNTs over time. Reaction conditions: [NO] = 500 ppm, [NH3/NO] = 1.1, [O2%] = 5 vol%, [SO2] = 50 ppm (when used), [H2O%] = 10 vol% (when used), N2 balance, reaction temperature = 150 °C and GHSV = 50 000 h−1. | |
Furthermore, the NO conversion was rapidly restored to 39.4% when the water vapor supply was turned off. The results indicated the reversible inhibitory effect of water of Ce/AC-CNTs catalyst. The high NO conversion and good SO2 tolerance of Ce/AC-CNTs suggested that a significant synergistic effect between CeO2 and CNTs contribute to the NH3-SCR reaction.
The comparison of NO removal efficiency with those of literatures have been studied. As it was shown in Table 4, at 150 °C, NO removal efficiency Ce/AC-CNTs (the present work) was 41%, which was higher than reported M/AC (M = metal) catalysts, and even higher than many M/CNTs catalysts. This indicated that the Ce/AC-CNTs catalyst in the present work is competitive for NH3-SCR reaction.
Table 4 Comparison of NO removal efficiency of various catalysts
Sample |
Temperature (°C) |
NO removal efficiency (%) |
Reference |
Ce/AC-CNTs |
150 |
41 |
This work |
Mn-CeOx/AC |
220 |
35 |
3 |
V2O5/AC |
150 |
30 |
36 |
V–Zr/AC |
150 |
40 |
16 |
Mn@CNTs |
150 |
59 |
37 |
Fe@Mn@CNTs |
90 |
40 |
37 |
Fe-Cu-O/CNTs-TiO2 |
250 |
12 |
38 |
V2O5/CNT |
270 |
38 |
32 |
4. Further discussion
A CNT-promoted-Ce/AC-CNTs catalyst (Ce/AC-CNTs) was prepared by in situ formation of CNTs on AC (via decomposition of methane) and used for NH3-SCR reaction. The catalytic activity of Ce/AC-CNTs catalyst (41.4%) was much higher than that of Ce/AC (29.4%). Although pore blockage occurred to a large extent upon the introduction of CNTs with the decrease in SBET and Vmic, the Vmes of AC-CNTs and Ce/AC-CNTs increased to 0.07 cm3 g−1 and 0.03 cm3 g−1 compared with that of AC and Ce/AC, respectively, after the introduction of CNTs. Thus, the in situ formation of CNTs on AC formed some new mesopores on AC-CNTs and Ce/AC-CNTs.
CNTs introduction could facilitate the formation of surface total oxygen amount (increasing from 11.6% of Ce/AC to 14.3% of Ce/AC-CNTs) and chemisorbed oxygen (increasing from 38.6% of Ce/AC to 42.1% of Ce/AC-CNTs). The increased amount of chemisorbed oxygen contributes to the high catalytic activity.
CNTs introduction increased the number of acid sites and strengthened the acidity of Ce/AC-CNTs, which enhanced the NH3 adsorption on catalysts and then improved the SCR catalytic activity. The cost of the AC-CNTs in this work was about 369 Chinese Yuan per kilogram (in laboratory). However, the commercial CNTs (Chengdu Branch Chinese Academy of Science) was 30
000 Chinese Yuan per kilogram, which indicated that the AC-CNTs prepared in this work greatly reduced the cost of catalyst compared to CNTs.
5. Conclusions
Ce/AC-CNTs catalyst was prepared by in situ formation of CNTs on AC and then modified by Ce, and used for NH3-SCR reaction. The NO conversion of Ce/AC-CNTs was 1.41 times higher than that of Ce/AC at 150 °C with good SO2 tolerance. CNTs introduction could form new mesopores and provide several acid sites, high surface total oxygen, and high surface chemisorption oxygen concentration on Ce/AC-CNTs, resulting in an enhancement of NH3-SCR.
Conflicts of interest
There are no conflicts to declare.
Acknowledgements
This work was supported by the China Postdoctoral Science Foundation (2018M643482), and Fundamental Research Funds for the Central Universities (2019SCU12055, the Postdoctoral Foundation of Sichuan University).
Notes and references
- H. Jiang, Y. Niu, Q. Wang, Y. Chen and M. Zhang, Catal. Commun., 2018, 113, 46–50 CrossRef CAS.
- Z. Song, X. Wu, Q. Zhang, P. Ning, J. Fan, X. Liu, Q. Liu and Z. Huang, RSC Adv., 2016, 6, 69431–69441 RSC.
- B. Shen, J. Chen, S. Yue and G. Li, Fuel, 2015, 156, 47–53 CrossRef CAS.
- B. Samojeden and T. Grzybek, Energy, 2016, 116, 1484–1491 CrossRef CAS.
- G. Ramis, G. Busca, F. Bregani and P. Forzatti, Appl. Catal., 1990, 64, 259–278 CrossRef CAS.
- H. Xu, Q. Lin, Y. Wang, L. Lan, S. Liu, C. Lin, Q. Wang, J. Wang and Y. Chen, RSC Adv., 2017, 7, 47570–47582 RSC.
- S. Zhan, Q. Shi, Y. Zhang, Y. Li and Y. Tian, RSC Adv., 2016, 6, 59185–59194 RSC.
- B. Huang, R. Huang, D. Jin and D. Ye, Catal. Today, 2007, 126, 279–283 CrossRef CAS.
- Y. Fu, Y. Zhang, G. Li, J. Zhang and F. Tian, RSC Adv., 2016, 6, 8539–8548 RSC.
- Y. Wang, X. Li, L. Zhan, C. Li, W. Qiao and L. Ling, Ind. Eng. Chem. Res., 2015, 54, 2274–2278 CrossRef CAS.
- W. Jing, Q. Guo, Y. Hou, G. Ma, X. Han and Z. Huang, Catal. Commun., 2014, 56, 23–26 CrossRef CAS.
- W. Tian, H. Yang, X. Fan and X. Zhang, J. Hazard. Mater., 2011, 188, 105–109 CrossRef CAS.
- M. Zheng, P. Li, G. Fu, Y. Chen, Y. Zhou, Y. Tang and T. Lu, Appl. Catal., B, 2013, 129, 394–402 CrossRef CAS.
- S. J. Wang, W. X. Zhu, D. W. Liao, C. F. Ng and C. T. Au, Catal. Today, 2004, 93–95, 711–714 CrossRef CAS.
- J. Lilong, Y. Wang, L. Xian, Y. Cao and K. Wei, Chin. J. Catal., 2013, 34, 2271–2276 CrossRef.
- J. Z. Luo, L. Z. Gao, Y. L. Leung and C. T. Au, Catal. Lett., 2000, 66, 91–97 CrossRef CAS.
- S. Bai, S. Jiang, H. Li and Y. Guan, Chin. J. Chem. Eng., 2015, 23, 516–519 CrossRef CAS.
- S. Cai, H. Hu, H. Li, L. Shi and D. Zhang, Nanoscale, 2016, 8, 3588–3598 RSC.
- E. Santillan-Jimenez, V. Miljković-Kocić, M. Crocker and K. Wilson, Appl. Catal., B, 2011, 102, 1–8 CrossRef CAS.
- K. Lota, V. Khomenko and E. Frackowiak, J. Phys. Chem. Solids, 2004, 65, 295–301 CrossRef CAS.
- D. Su, X. Chen, G. Weinberg, A. Klein-Hofmann, O. Timpe, S. B. Abd Hamid and R. Schlogl, Angew. Chem., 2005, 44, 5488–5492 CrossRef CAS PubMed.
- M. Chen, C.-M. Chen, S.-C. Shi and C.-F. Chen, Jpn. J. Appl. Phys., 2003, 42, 614–619 CrossRef CAS.
- J. Wei, B. Jiang, X. Zhang, H. Zhu and D. Wu, Chem. Phys. Lett., 2003, 376, 753–757 CrossRef CAS.
- L. Wang, B. Huang, S. U. Yanxia, G. Zhou, K. Wang, H. Luo and Y. E. Daiqi, Chem. Eng. J., 2012, 192, 232–241 CrossRef CAS.
- X. Yao, L. Zhang, L. Li, L. Liu, Y. Cao, X. Dong, F. Gao, Y. Deng, C. Tang, Z. Chen, L. Dong and Y. Chen, Appl. Catal., B, 2014, 150, 315–329 CrossRef.
- F. Cheng, Z. Dengsong, C. Sixiang, Z. Lei, H. Lei, L. Hongrui, M. Phornphimon, S. Liyi, G. Ruihua and Z. Jianping, Nanoscale, 2013, 5, 9199–9207 RSC.
- N. Zhu, Z. Lian, Y. Zhang, W. Shan and H. He, Chin. Chem. Lett., 2019, 30, 867–870 CrossRef CAS.
- J. Guo, J. Liang, Y. Chu, M. Sun, H. Yin and J. Li, Appl. Catal., A, 2012, 421–422, 142–147 CrossRef CAS.
- Z. Wu, R. Jin, Y. Liu and H. Wang, Catal. Commun., 2008, 9, 2217–2220 CrossRef CAS.
- C. Zhou, H. Wang, F. Peng, J. Liang, H. Yu and J. Yang, Langmuir, 2009, 25, 7711–7717 CrossRef CAS.
- X. Chen, P. Wang, P. Fang, T. Ren, Y. Liu, C. Cen, H. Wang and Z. Wu, Fuel Process. Technol., 2017, 167, 221–228 CrossRef CAS.
- B. Huang, R. Huang, D. Jin and D. Ye, Catal. Today, 2007, 126, 279–283 CrossRef CAS.
- Z. Liu, Y. Yi, J. Li, S. I. Woo, B. Wang, X. Cao and Z. Li, Chem. Commun., 2013, 49, 7726–7728 RSC.
- T. Gu, Y. Liu, X. Weng, H. Wang and Z. Wu, Catal. Commun., 2010, 12, 310–313 CrossRef CAS.
- F. Cheng, D. Zhang, L. Shi, R. Gao, H. Li, L. Ye and J. Zhang, Catal. Sci. Technol., 2013, 3, 803–811 RSC.
- A. Boyano, M. J. Lázaro, C. Cristiani, F. J. Maldonado-Hodar, P. Forzatti and R. Moliner, Chem. Eng. J., 2009, 149, 173–182 CrossRef CAS.
- S. Cai, H. Hu, H. Li, L. Shi and D. Zhang, Nanoscale, 2016, 8, 3588 RSC.
- Z. Ma, H. Yang, Q. Li, J. Zheng and X. Zhang, Appl. Catal., A, 2012, 427–428, 43–48 CrossRef CAS.
Footnote |
† Electronic supplementary information (ESI) available. See DOI: 10.1039/c9ra08640d |
|
This journal is © The Royal Society of Chemistry 2019 |
Click here to see how this site uses Cookies. View our privacy policy here.