DOI:
10.1039/D0RA07859J
(Paper)
RSC Adv., 2020,
10, 42564-42569
Reaction induced robust PdxBiy/SiC catalyst for the gas phase oxidation of monopolistic alcohols†
Received
14th September 2020
, Accepted 13th November 2020
First published on 24th November 2020
Abstract
Reaction induced PdxBiy/SiC catalysts exhibit excellent catalytic activity (92% conversion of benzyl alcohol and 98% selectivity of benzyl aldehyde) and stability (time on stream of 200 h) in the gas phase oxidation of alcohols at a low temperature of 240 °C due to the formation of Pd0–Bi2O3 species. TEM indicates that the agglomeration of the 5.8 nm nanoparticles is inhibited under the reaction conditions. The transformation from inactive PdO–Bi2O3 to active Pd0–Bi2O3 under the reaction conditions is confirmed elaborately by XRD and XPS.
1. Introduction
Alcohol oxidation reaction is widely investigated in both laboratories and industrial applications due to the importance of its valuable products such as aldehydes and ketones, which are widely used in dyestuffs, polymer precursors, and pharmaceutical and agrochemical industries.1–3 Traditionally, stoichiometric oxidants such as dichromate or permanganate are used in the liquid phase oxidation but are toxic and expensive, which could not meet the development of green chemistry. Hence, there is a need of shifting from methods based on the toxic and inorganic oxidants to greener and more atom efficient methods which adopt molecular oxygen as oxidant.4–6
Considering that lots of noble metal catalysts have been used in the oxidation of alcohols using O2 as oxidant, Pd based catalysts have attracted much attention for its simple preparation method and excellent catalytic activity.4 However, some problems still impede its industrial applications. For example, the formation process of active phase is investigated elaborately for Pd/SBA-15, but the agglomeration of the nanoparticles and low efficiency are inevitable.7 Pd/Al2O3 is reported by Li et al., however, the reduction of active PdO to inactive Pd0 in the reaction conditions contributes to the deactivation of the catalyst.8,9 Sulfur doped SBA-15 supported Pd exhibits excellent catalytic activity, however, the unstability of the amphorous Pd is adverse in industrial applications.2 Novel highly stable and anti-sintered large size Pd/TiO2 for the oxidation of benzyl alcohol has been reported, but the conversion of benzyl alcohol is lower than 50%.3
To improve the catalytic activity of Pd catalyst, bimetal Pd based catalysts in alcohol oxidation reaction have attracted increasing interest in recent decades because they can finely tune the catalytic properties of metals. However, there are a lot of problems that still need to be solved. Reaction induced inactive CuPd alloy inhibits the reduction of highly active Cu2O for CuPd–Cu2O/Ti powder, but the conversion is lower than 90% at the temperature of 280 °C.4 The synergistic effect between Au and Pd species in AuPd/TiO2 is prominent in the oxidation of alcohols compared with Au/TiO2 or Pd/TiO2, but the tedious preparation process and the low efficiency impede its applications.10,11
Based on the problems mentioned above, the major challenge is to develop an effective catalyst endowed with high activity at low temperature coupled with high thermal conductivity to enhance the catalyst stability.6 SiC powder is chosen as support because of its excellent heat conductivity, low price and high oxidation/corrosion resistance behavior.5 The synergistic effect between Pd and oxides such as Cu2O has been reported,4 but the reaction temperature is still high and the reaction induced process (the alcohol could convert inactive fresh catalyst into active catalyst) has not been discussed. As a continuation of our previous research, in situ reaction-induced Pd3Bi5/SiC catalyst is prepared by a simple impregnation and calcination method. The transformation from PdO–Bi2O3 to Pd0–Bi2O3 is confirmed, which is testified by XRD and XPS. The synergism between Pd and Bi2O3 is prominent due to excellent catalytic activity of PdBi/SiC and the inferior catalytic activities of Pd/SiC or Bi/SiC.
2. Experimental section
2.1 Materials and methods
SiC powder (200–300 mesh with surface area of 0.15 m2 g−1), Pd(NO3)2·2H2O and Bi(NO3)3·5H2O were purchased from Sinopharm Chemical Reagent Co Ltd. SBA-15 and MCM-41 were supplied by Nankai University Catalyst Co Ltd. Other substrates were supplied by Aladdin Reagent Co. Ltd.
All catalysts were characterized by inductively coupled plasma atomic emission spectrometry (ICP-AES, ICP Thermo IRIS Intrepid II XSP; USA), X-ray photoelectron spectroscopy (XPS, Escalab 250xi spectrometer, Al Kα, adventitious C 1s line (284.8 eV) as the reference), X-ray diffraction (XRD, Rigaku Uitima IV diffractometer with Cu Kα radiation (35 kV and 25 mA); Japan), scanning electron microscopy (SEM, Hitachi S-4800; Japan) equipped with an energy dispersive X-ray fluorescence spectrometer (EDX, Oxford; UK), O2-temperature programmed desorption (O2-TPD) measurements were performed on a Quanta chrome ChemBET 3000 (USA) chemisorption apparatus with a thermal conductivity detector (TCD), and transmission electron microscopy (TEM, FEI-Tecnai G2 F30; USA). 1H NMR spectra were recorded on a Bruker 400 or a Agilent 400 (100 MHz).
2.2 Preparation of the catalysts
Pd3Bi5/SiC fresh (weight loading of Pd and Bi was 3 wt% and 5 wt% respectively) was prepared by impregnation of 1 g SiC powder, 65 mg Pd(NO3)2·2H2O, 116 mg Bi(NO3)3·5H2O and 2 mL H2O followed by being dried at 100 °C overnight and calcinated at 300 °C in air for 2 h, which was denoted as Pd3Bi5/SiC fresh. Additionally, other catalysts such as PdxBiy/SiC fresh, Pdx/SiC fresh and Biy/SiC fresh (x and y indicate the weight content of Pd and Bi respectively) were prepared following the same procedure by simply tuning the weight of Pd(NO3)2·2H2O or Bi(NO3)3·5H2O. The fresh catalysts (PdxBiy/SiC fresh, Pdx/SiC fresh and Biy/SiC fresh) after 1 h running (Time on steam (TOS) of 1 h) in the reaction conditions (see Section 2.3, catalytic tests)were denoted as PdxBiy/SiC, Pdx/SiC and Biy/SiC for short.
2.3 Catalytic tests
The gas phase selective oxidation process was carried out on a fixed-bed reactor (inner diameter of 10 mm) under atmospheric pressure made up by ourselves (Scheme S1†). Catalyst used in each experiment was 0.3 g (200–300 mesh) and alcohols are fed continuously by a peristaltic pump, in parallel with O2 (oxidant) and N2 (dilute gas) feeding using the calibrated mass flow controllers, into the reactor heated to 240 °C. WHSV (weight hourly space velocity) of alcohol was 20 h−1 and the molecular ratio of alcohol/O2/N2 is 1/0.6/2.4. The products were analysed by Gas Chromatography (SP-7820 with TCD detector). The calculation method of benzyl alcohol conversion and benzaldehyde selectivity were listed in the ESI.† All the catalytic tests were repeated for 3 times to improve accuracy.
In order to prevent the oxidation of our catalysts after reaction, the spent catalysts are collected until cooling down to room temperature under the protection of N2.
3. Results and discussion
3.1 Catalytic activity
The catalytic activities of the catalysts are shown in Table 1. Given the strong exothermic effect in the gas phase oxidation of alcohol, the chemically inert SiC powder with excellent thermal conductivity and high oxidation resistance behaviour other than oxides (such as Al2O3 and TiO2) or zeolites (such as SBA-15) is selected as supports (Table 1, entry 1). The catalytic behaviour of pure Pdx/SiC catalysts is very low (Table 1, entries 2 and 3), which is in accordance with previously reported Pd/Ti powder catalyst.4 It is noted that Biy/SiC catalyst is nearly inactive in alcohol oxidation even with Bi content increasing to 5% (Table 1, entries 4 and 5). At 280 °C, the conversion of benzyl alcohol increases from 90% to 95% with Pd loading increasing from 1% to 2% (Table 1, entries 6 and 8) for PdxBi5/SiC catalyst, which is nearly unchanged with Pd loading further increasing to 3% (Table 1, entry 10). As for PdxBi5/SiC catalysts, further increasing the Pd content to 4% or 5% does not yield better performance (Table 1, entries 16 and 17), indicating that there may be sufficient Pd0–Bi2O3 interface in the reaction. So Pd3Bi5/SiC is selected as the optimal catalyst given to its excellent catalytic activity and thermal conductivity, which exhibits remarkable performance compared with previously reported Pd based catalysts. However, the catalytic activity of Pd3Bi5/SiC is much higher than that of Pd1Bi5/SiC and Pd2Bi5/SiC at the lower temperature of 240 °C (Table 1, entries 7, 9 and 11).
Table 1 Catalytic activity of the catalystsa
Entry |
Catalyst |
Content of Pdd (wt%) |
Content of Bid (wt%) |
Conversione (%) |
Selectivityf (%) |
Reaction conditions: catalyst 300 mg, temperature 280 °C, O2/alcohol/N2 = 0.6/1/2.4 and WHSV 20 h−1. Temperature 240 °C. Pd3/SiC and Bi5/SiC are physically mixed. The content is confirmed by ICP. Conversion of benzyl alcohol. Selectivity of benzaldehyde. |
1 |
SiC |
0 |
0 |
3 |
97 |
2 |
Pd1/SiC |
0.96 |
0 |
11 |
98 |
3 |
Pd5/SiC |
4.68 |
0 |
31 |
99 |
4 |
Bi1/SiC |
0 |
0.88 |
2 |
98 |
5 |
Bi5/SiC |
0 |
4.70 |
6 |
97 |
6 |
Pd1Bi5/SiC |
0.90 |
4.68 |
90 |
97 |
7b |
Pd1Bi5/SiC |
0.90 |
4.68 |
78 |
98 |
8 |
Pd2Bi5/SiC |
1.82 |
4.81 |
95 |
98 |
9b |
Pd2Bi5/SiC |
1.82 |
4.81 |
88 |
98 |
10 |
Pd3Bi5/SiC |
2.90 |
4.52 |
98 |
97 |
11b |
Pd3Bi5/SiC |
2.90 |
4.52 |
93 |
98 |
12c |
Pd3/SiC&Bi5/SiC |
2.71 |
4.83 |
25 |
97 |
13b |
CuPd–Cu2O/Ti |
3.10 |
0 |
65 |
99 |
14 |
Pd/TiO2 |
0.7 |
0 |
50 |
98 |
15 |
Pd/SBA-15 |
1.0 |
0 |
99 |
99 |
16 |
Pd4Bi5/SiC |
3.8 |
4.89 |
97 |
95 |
17 |
Pd5Bi5/SiC |
4.9 |
4.92 |
97 |
96 |
Interestingly, the conversion of benzyl alcohol is just 25% when Pd3/SiC and Bi5/SiC are physically mixed (Table 1, entry 12), which is similar to the previously reported Ag2.5Cu5/SiC catalyst.6 So Pd3Bi5/SiC exhibits excellent heat conductivity in the low temperature gas phase oxidation of alcohols. Furthermore, the influence of support in this reaction could be neglected (Table 2). Thus Pd3Bi5/SiC is selected as the optimal catalyst given its excellent catalytic activity and thermal conductivity, which exhibits remarkable performance compared with previously reported Pd based catalysts. Anti-sintered large size Pd particles show inferior catalytic activity compared with aforementioned catalysts (Table 1, entry 14).3 For benzyl alcohol oxidation at 240 °C, Pd3Bi5/SiC delivers a single run life time of 200 hours with excellent activity and selectivity (Fig. 1). For aromatic alcohols, such as 1-phenylethanol and 2-phenylethanol, the conversion is 75% and 55% respectively and the selectivity of phenylacetaldehyde and acetophenone is 98% and 97% respectively. For methanol and ethanol, the conversion is 91% and 88% respectively (Table S1†).
Table 2 Influence of supportsa
Catalyst |
ΔTb (°C) |
Conversionc (%) |
Conversiond (%) |
Reaction conditions: catalyst 300 mg, temperature 240 °C, O2/alcohol/N2 = 0.6/1/2.4 and WHSV 20 h−1. ΔT is the temperature difference between catalyst bed and reactor external wall. Conversion of benzyl alcohol after 2 h running. Conversion of benzyl alcohol after 20 h running. |
Pd3Bi5/SiC |
6 |
98 |
90 |
Pd3Bi5/Al2O3 |
32 |
93 |
68 |
Pd3Bi5/TiO2 |
25 |
96 |
75 |
Pd3Bi5/SiO2 |
36 |
93 |
65 |
Pd3Bi5/SBA-15 |
30 |
95 |
72 |
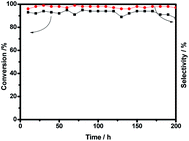 |
| Fig. 1 Long-term test for the Pd3Bi5/SiC catalyst. | |
3.2 Physicochemical characterization of fresh Pd3Bi5/SiC catalyst
In order to further identify the active site in the reaction, Pd3Bi5/SiC fresh is characterized elaborately by XRD and XPS because valance effect other than particle size or surface area plays an important role in the gas phase oxidation of alcohols.12,13 XRD and XPS indicate that PdO and Bi2O3 are formed after calcination of nitrate salts with SiC powder. Given the weak characteristic diffraction peaks of PdO centered at 2θ = 31.5° (Fig. 2A), we conclude that the particle size is very small, which is in accordance with the previous report.7 Just like PdO nanoparticles, the small size Bi2O3 nanoparticles are formed given the weak characteristic diffraction peak centered at 2θ = 27.4° (Fig. 2A). Pd 2p spectrum indicates that the binding energy peak at 336.6 eV is assigned to PdO2,3,8 (Fig. 2B). The binding energy of Bi is centered at 160.0 eV, which is much higher than that of metallic Bi (Fig. 2C).14,15 Hence, the electron transfer from Bi to O is prominent and Bi2O3 is formed in the pre-treatment conditions. Just like Pd3Bi5/SiC fresh, PdO and Bi2O3 are formed for Pd3/SiC fresh and Bi5/SiC fresh respectively (Fig. 2A).
 |
| Fig. 2 (A) XRD patterns of the Pd3/SiC fresh, Bi5/SiC fresh and Pd3Bi5/SiC fresh; (B) Pd 2p spectrums of Pd3/SiC fresh and Pd3Bi5/SiC fresh; (C) Bi 2p spectrums of Bi5/SiC fresh and Pd3Bi5/SiC fresh. | |
3.3 Formation of active site and the influence of supports
Compared with Pd3/SiC and Bi5/SiC, reaction induced Pd0–Bi2O3 species from PdO–Bi2O3 in the reaction conditions plays an important role in the catalytic activity (Table 1, entries 3, 5 and 11), which is verified by XRD, TEM and XPS. XRD pattern indicates that the diffraction peak of Bi2O3 remains unchanged while the diffraction peak of PdO disappears and the new diffraction peaks of Pd form compared with Pd3Bi5/SiC fresh (Fig. 3A). Pd 2p spectrum indicates that the strong binding energy peak at 335.3 eV is prominent, so Pd0 is formed in the reaction conditions (Fig. 3B).3,4 The binding energy of Bi 2p is close to that of the fresh catalyst, so XRD and XPS indicate that Bi2O3 remains unchanged in the reaction conditions (Fig. 3C). TEM indicates that the ensembles consist of the small size 5.8 nm Pd0 or Bi2O3 nanoparticles (Fig. 3D). The lattice fringes of Pd nanoparticle and Bi2O3 nanoparticle are 0.225 nm and 0.326 nm respectively, which is in accordance with XRD results and the previous reports (Fig. 3E and F).4,14,15 The mapping images indicate that Pd, Bi and O distribute on the support randomly and the agglomeration of the nanoparticles is inhibited after the reaction conditions (Fig. 3G–I). Furthermore, TEM images show that the particle sizes of used Pd3/SiC and Bi5/SiC catalysts are 5.5 and 6.5 nm respectively, so the influence of particle size effect on the catalytic activity could be excluded (Fig. S1†). Moreover, TG curve shows that the carbon content is lower than 2 wt%, showing the excellent thermal conductivity of SiC powder (Fig. S1†). In order to further testify the active phase in the oxidation of benzyl alcohol, other supports such as Al2O3, TiO2, SBA-15, SiO2 and MCM-41 are used to prepare the catalysts. Interestingly, Pd3Bi5/Al2O3, Pd3Bi5/TiO2, Pd3Bi5/SiO2, Pd3Bi5/SBA-15 and Pd3Bi5/MCM-41 all exhibit excellent catalytic activities in the first 2 h running (Table 2). However, the conversion of benzyl alcohol decreases rapidly after 20 h running in the reaction conditions. The catalyst bed packed with Pd3Bi5/SiC delivers a low ΔT (the temperature difference between catalyst bed and reactor external wall) of 6 °C at 240 °C, which is much lower than that of other catalysts (Table 2). So Pd3Bi5/SiC exhibits excellent heat conductivity in the low temperature gas phase oxidation of alcohols, which helps in rapidly dissipating the great quantity of reaction heat liberated from such strongly exothermic process and the influence of supports is ruled out for the oxidation of alcohols.13
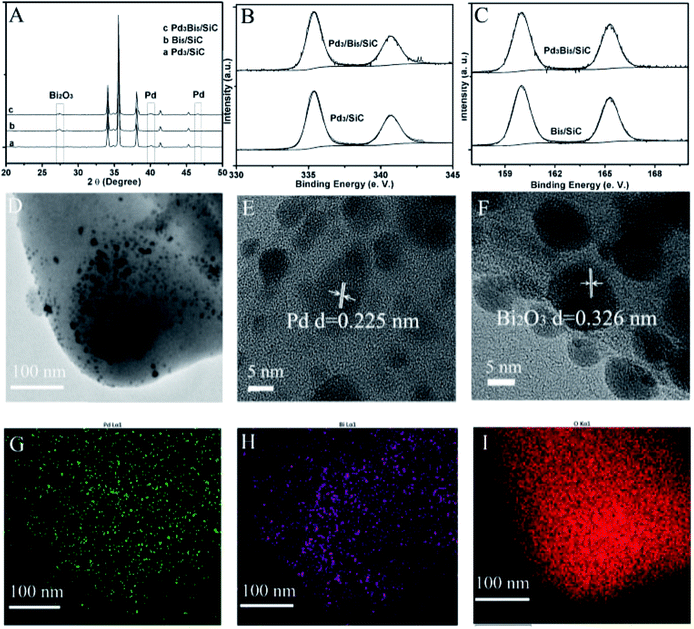 |
| Fig. 3 (A) XRD patterns of the Pd3/SiC, Bi5/SiC and Pd3Bi5/SiC; (B) Pd 2p spectrums of Pd3/SiC and Pd3Bi5/SiC; (C) Bi 2p spectrums of Bi5/SiC and Pd3Bi5/SiC; (D) TEM image of Pd3Bi5/SiC; (E) lattice fringe of Pd in Pd3Bi5/SiC; (F) lattice fringe of Bi2O3 in Pd3Bi5/SiC; (E–G) distributions of Pd, Bi and O in Pd3Bi5/SiC. | |
3.4 Further discussions of active Pd0–Bi2O3 and inactive PdO–Bi2O3 phase
For the fresh and used Pd3Bi5/SiC catalyst, XRD and XPS results indicate that PdO–Bi2O3 and Pd0–Bi2O3 ensembles are the main phase in the catalyst (Section 3.2 and 3.3). Hence, reductive alcohol reduces inactive PdO–Bi2O3 to active Pd0–Bi2O3. To further compare between the catalytic efficiency of PdO–Bi2O3 and Pd0–Bi2O3, we compare the catalytic activities of the catalysts in the reaction conditions after different time on steam (TOS).16 XPS results shows that the binding energy peaks at 335.0 and 336.4 eV are attributed to Pd0 and PdO respectively (Fig. 4A). After calcinations at 300 °C, Pd species for Pd3Bi5/SiC exists in the form of PdO phase (Fig. 2A). The conversion of alcohol increases and the ratio of Pd0/PdO increases with the prolongation of TOS. For example, after 10 minutes running in the reaction conditions, Pd0/PdO ratio is 52% and the conversion of alcohol is 63% (Fig. 4A).4 Similarly, Pd0/PdO ratio is 73% and the conversion of alcohol is 78% after 20 minutes running in the reaction conditions (Fig. 4A).
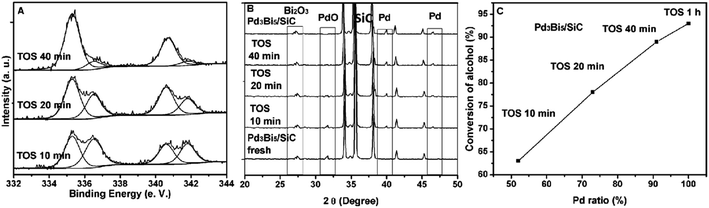 |
| Fig. 4 (A) Pd 2p spectrums of Pd3Bi5/SiC (TOS of 10, 20 and 40 minutes); (B) XRD patterns of Pd3Bi5/SiC (TOS of 10, 20 and 40 minutes); (C) catalytic activity of Pd3Bi5/SiC (TOS of 10, 20 and 40 minutes). | |
Interestingly, PdO disappears and Pd is dominant for Pd3Bi5/SiC (TOS of 1 h) (Fig. 3A). XRD results show that the diffraction peak of PdO decreases and the diffraction peaks of Pd0 increase with the prolongation of reaction time, which is corresponding with XPS results (Fig. 4B). Interestingly, it can been seen that the conversion of benzyl alcohol increases linearly with the Pd0/PdO ratio (Fig. 4C). The diffraction peaks of support and Bi2O3 remain unchanged (Fig. 4B). However, given the low catalytic activity of Pd3/SiC and Bi5/SiC, Pd0 or Bi2O3 is inactive in alcohol oxidation (Table 1, entries 3 and 5, Fig. 3A). Hence, XRD and XPS indicate that benzyl alcohol reduces the inactive PdO–Bi2O3 to active Pd0–Bi2O3, which plays an important role in the low temperature gas phase oxidation of alcohols.
3.5 Synergistic effect between Pd and Bi2O3
Lots of techniques should be adopted to investigate the synergistic effect between Pd and Bi2O3. Reportedly, for the gas phase alcohol oxidation reaction, catalytic and oxidative dehydration are the main routes. For the catalytic dehydrogenation mechanism, the H atom in the alcohol will be captured by the oxides, which will be moved by oxygen with the aid of metals. However, for the oxidative dehydrogenation mechanism, active oxygen species will be participated into the Mars Krevelen mechanism.17,18
The chemical absorbed oxygen couldn't be detected by O2-TPD and the conversion of alcohol will be about 5–10% in the absence of O2 for the catalytic dehydrogenation system. However, the chemical absorbed oxygen could be detected by O2-TPD and the conversion of alcohol will be about 1–2% in the absence of O2 for the oxidative dehydrogenation system. Hence, absorbed oxygen species plays an important role in the oxidative dehydrogenation other than catalytic dehydrogenation.17,18
To differentiate the two mechanisms over Pd3Bi5/SiC catalyst, the control experiments in the absence of O2 are conducted firstly. The conversions of benzyl alcohol are about 7–9% at 240 °C for Bi5/SiC and Pd3Bi5/SiC. Secondly, O2-TPD shows there are no O2 desorption peaks on the two catalysts (Fig. S2†). So the catalytic oxidation cycle is tentatively proposed.
Just like Cu-based catalysts, to further confirm the catalytic oxidation cycle, solid state 1H NMR is used to characterize the Bi2O3–H species. Four catalysts, Pd3Bi5/SiC (a), Pd3Bi5/SiC reacted with benzyl alcohol in the absence of O2 at 240 °C for 2 h (b), Bi5/SiC (c), Bi5/SiC reacted with benzyl alcohol in the absence of O2 at 240 °C for 2 h (d) are used to probe the Bi2O3–H species. The 1H NMR signal at 1.3 and 4.9 pm are corresponding with Bi2O3–H and H2O (Fig. 5). For the catalysts (b) and (d), the similar strong hydride HNMR peaks are obtained, showing their similar catalytic dehydrogenation activity. However, the Bi2O3–H signal decreases obviously on Pd3Bi5/SiC (Aa/Ab = 0.30), while decreases slightly over Bi5/SiC (Aa/Ab = 0.82).
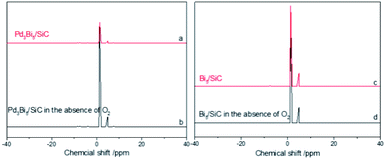 |
| Fig. 5 H NMR spectrums of the catalysts. | |
In the end, the TOF values of Pd3Bi5/SiC and Pd3/SiC are calculated (Table S2†). In the experiments, the WHSVs are optimized to obtain the low benzyl alcohol conversion. The TOF values of Pd3Bi5/SiC is 8842 and 2210 h−1 at 260 and 240 °C respectively, which are about 43 and 34 times of that of Pd3/SiC. So the results mentioned above testify that Pd0–Bi2O3 is beneficial to eliminating the Bi2O3–H intermediates.
4. Conclusions
Pd3Bi5/SiC was successfully prepared in a simple impregnation method, which shows excellent activity and stability in alcohol oxidation reaction. In the reaction conditions, benzyl alcohol reduces the inactive PdO–Bi2O3 to active Pd0–Bi2O3, which plays an important role in the low temperature gas phase oxidation of alcohols. XRD, XPS and control experiments indicate that Pd0/PdO ratio was vital for this reaction. Control experiments, O2-TPD and 1H NMR testify that Pd0–Bi2O3 is beneficial to eliminating the Bi2O3–H intermediates.
Conflicts of interest
There are no conflicts to declare.
Acknowledgements
This work is supported by the National Science Foundation of China (Grant No. 21902100 and 51776116) and the Youth Foundation of Shanghai Polytechnic University (Grant No. EGD19XQD18). We are also grateful for the financial support from the Gaoyuan Discipline of Shanghai – Environmental Science and Engineering (Resource Recycling Science and Engineering).
References
- P. Wu, Y. Cao, L. Zhao, Y. Wang, Z. He, W. Xing, P. Bai, S. Minova and Z. Yan, J. Catal., 2019, 375, 32 CrossRef CAS.
- N. N. Opmbe, C. Guild, C. Kingondu, N. C. Nelson, I. I. Slowing and S. L. Suib, Int. J. Chem. Eng. Res., 2014, 53, 19044 CrossRef.
- K. Liu, X. J. Yan and L. Y. Dai, Catal. Commun., 2015, 58, 132 CrossRef CAS.
- K. Mori, T. Hara, T. Mizugaki, K. Ebitani and K. Kaneda, J. Am. Chem. Soc., 2004, 126, 10657–10666 CrossRef CAS.
- K. Liu, H. K. Long and J. Dong, RSC Adv., 2017, 7, 54861 RSC.
- L. Zhao, L. P. Kong and L. Y. Dai, Catal. Commun., 2017, 10, 1 CrossRef.
- C. H. Liu, C. Y. Lin and J. M. Chen, J. Catal., 2017, 350, 21 CrossRef CAS.
- X. M. Wang, G. J. Wu and L. D. Li, Appl. Catal., B, 2012, 115–116, 7 CrossRef CAS.
- G. J. Wu, X. M. Wang and L. D. Li, Appl. Catal., B, 2013, 136–137, 177–185 CrossRef CAS.
- G. W. Wu, G. L. Brett and G. J. Hutchings, Catal. Sci. Technol., 2016, 6, 4749 RSC.
- N. A. Rifai, F. Galvanin and G. J. Hutchings, Chem. Eng. Sci., 2016, 149, 129 CrossRef.
- G. F. Zhao, M. M. Deng and Y. Lu, J. Catal., 2013, 301, 46 CrossRef CAS.
- G. F. Zhao, Y. K. Li and Y. Lu, AIChE J., 2014, 60, 1045 CrossRef CAS.
- H. B. Liao, J. H Zhu and Y. L. Hou, Nanoscale, 2014, 6, 1049 RSC.
- H. Xu, K. Zhang and P. Yang, J. Power Sources, 2017, 356, 27 CrossRef CAS.
- P. W. Wang, G. F. Zhao and Y. Lu, Sci. Adv., 2017, 3, 1 Search PubMed.
- G. F. Zhao, H. Y. Hu, M. M. Deng, M. Ling and Y. Lu, ChemCatChem, 2011, 3, 1629 CrossRef CAS.
- K. Liu, C. Hou, Y. B. Sun and X. Q. Cao, Catal. Commun., 2020, 135, 105892 CrossRef CAS.
Footnote |
† Electronic supplementary information (ESI) available. See DOI: 10.1039/d0ra07859j |
|
This journal is © The Royal Society of Chemistry 2020 |
Click here to see how this site uses Cookies. View our privacy policy here.