DOI:
10.1039/D2RA07650K
(Paper)
RSC Adv., 2023,
13, 3255-3264
Strong metal–support interactions between atomically dispersed Ru and CrOx for improved durability of chlorobenzene oxidation†
Received
1st December 2022
, Accepted 8th January 2023
First published on 25th January 2023
Abstract
In this work, two single-atom catalysts (SACs) with atomically dispersed RuO2 supported on CrOx were successfully synthesized with a simple reduction strategy for the efficient catalytic oxidation of chlorobenzene (CB). With characterizations like Cs-corrected STEM, XPS, H2-TPR, and O2-TPD, the structure–activity relationship is addressed. The noble metal precursor Ru3+ was anchored with different oxygen species and exposed facets based on the physicochemical properties of catalyst supports. Based on the analysis results, the Ru3+ precursor could be mainly anchored into the surface lattice oxygen of Cr2O3-M over high-index facets (223) and adsorbed oxygen of Cr2O3-P over low-index facets (104), where the precursor Ru3+ was all oxidized to RuO2 when being anchored with the oxygen species of Cr2O3-M and Cr2O3-P, respectively according to XPS analysis. There is a stronger metal–support interaction (SMSI) between Ru ions and the surface lattice oxygen of Cr2O3-M, according to H2-TPR and O2-TPD characterizations. Further, the catalytic performance for CB combustion at a high space velocity of 120
000 mL (g−1 h−1) was tested, and 1RuCr2O3-M performed better than 1RuCr2O3-P in both durability and activity. This could be attributed to the SMSI between single-atom Ru and the lattice oxygen of the 1RuCr2O3-M catalyst and the abundant active sites from the exposed high-index facets. The study provided a novel synthesis strategy for Ru-based SACs with SMSI effect, and the good durability of the catalyst (1RuCr2O3-M) extended the great potential for practical application.
1 Introduction
Chlorinated volatile organic compounds (CVOCs) are attractive due to their similar molecular structure to polychlorinated dibenzo-p-dioxins (PCDDs) and dibenzofurans (PCDFs).1 Because of their stable chemical and degradation-resistant properties, there are high quantities of CVOCs in the environment, e.g., coming from waste incineration flue gas of metallurgical industries and consumption of fossil energy, and bring about severe environmental issues.2,3 They cause multiple health problems for humans and animals, such as cancer and aberration.4,5 Stringent environmental regulations have been adopted in many countries to prevent or remove the emission of these hazardous compounds.6 In laboratory research, chlorobenzene (CB) is often used as the indicator to evaluate the catalytic activity of catalysts for the oxidation of dioxins.7 Catalytic combustion is one promising technology to oxidize CB to harmless or low toxicity compounds at low temperatures, and a lower concentration of contaminants can be eliminated compared with other technologies.8 The development of catalysts with high activity and stability is a desired factor for the removal of CB by catalytic combustion technology.9
Research has focused on metal oxide and noble metal catalysts.10 Nobel metal catalysts have attracted attention due to their good catalytic activities for heterogeneous catalysis11 at lower temperatures.12 Yet, some intrinsic properties of noble metals inhibit practical application, such as cost, particle agglomeration, and the fact they can be poisoned by organochlorine adsorption.13 To overcome these disadvantages, the preparation of SACs (single atom catalyst) may be useful. In previous studies, the SACs have displayed superiorities in CO oxidation14 photochemical water splitting, sensing,15 etc. The limited examples of oxidation of VOCs have provided the need for the development of SACs in this field.16 It is well known that ruthenium is the cheapest among the precious metal series (including Pt, Pd, Au, and Ru). We used RuCl3 as the noble metal precursor, with the single-atom dispersed Ru maximizing the utilization efficiency of precious metals in the catalytic process, which reduced the cost of catalyst preparation. Cr2O3 was selected as the catalyst supports because of its thermostability and poisoning resistance during organic oxidation reactions.17 It can be deduced from our previous studies that different synthesis strategies often lead to different physicochemical properties of the same catalyst supports.18,19
Atomically dispersed catalyst 1RuCr2O3-P and 1RuCr2O3-M composites with similar amounts of Ru (∼0.9 wt% loading) were successfully prepared through a simple reduction method, where Cr2O3-P was obtained by precipitation and Cr2O3-M was derived from the pyrolysis of a MOF-template as in a previous study.18 The results indicated that 1RuCr2O3-M showed the best catalytic activity and promoted stability. Calcination temperatures, amounts (measured by ICP-OES), and morphology (observed by Cs-corrected STEM) indicate that the better performance of 1RuCr2O3-M on CB oxidation could result from the stable Ru–O structure with a strong metal–support interaction (SMSI) effect. This can effectively restrain the mutual contact of noble metals and inhibit the aggregation and migration of single atoms.
We examined how catalytic activities influenced by the interaction between these two components (Ru and O). With several characterizations, including XPS, H2-TPR, and O2-TPD, we found that Ru3+ were anchored into different crystals of catalyst supports. This resulted in a different catalytic performance of CB oxidation, where Ru3+ could be mainly anchored into the surface lattice oxygen of Cr2O3-M over the high-index (223) facets and adsorbed oxygen of Cr2O3-P over low-index (104) facets. Then atomically dispersed RuO2 was formed on the Cr2O3-M and Cr2O3-P supports after the oxidation of Ru3+. The better durability performance for chlorobenzene oxidation is mainly due to the SMSI effect of Ru ions and lattice oxygen species.
2 Experimental section
2.1 Chemicals and materials
Analytical reagents were used without further purification. NaBH4, HF, NH4OH (25–28%), Cr (NO3)3·9H2O, and chlorobenzene were obtained from Sinopharm Chemical Reagent Co., Ltd (Shanghai, China). RuCl3 was purchased from Shaanxi Kaida Chemical Engineering Co., Ltd (Shanghai, China); 1,4-dicarboxybenzene was obtained from Aladin (Shanghai, China).
2.2 Preparation of Cr2O3-M and 1RuCr2O3-M
The catalyst precursor MIL-101-Cr and its derived product Cr2O3-M were prepared according to a previous study.19 The catalyst 1RuCr2O3-M (Ru = 0.88 wt%, according to the results of ICP-OES) was synthesized via a simple reduction method using NaBH4 for the reduction of Ru3+. Precisely, a gram of Cr2O3-M was homogenously dispersed in DI water by ultrasonic dispersion, then the desired amount of RuCl3 solution with 1 wt% of Ru content was dropwise added into the suspension under vigorous stirring. Then a certain amount of NaBH4 aqueous solution was added to the resulting mixture after stirring for 1 h. The sample was collected by filtration and then dried at 120 °C for several hours, and finally calcined at 500 °C under air for 2 h.
2.3 Preparation of Cr2O3-P and 1RuCr2O3-P
Cr2O3-P was prepared by a precipitation method, where Cr(NO3)3·9H2O and NH4OH were used as the precursor and precipitant, respectively. Typically, 2.0 g of Cr(NO3)3·9H2O was dissolved in 50 mL of DI water as chromium ions sources; 2.3 g of NH4OH was added into 50 mL of DI water to obtain the uniform ammonia solution, and then was added dropwise into the solution of Cr(NO3)3·9H2O. The mixture was stirred overnight on a magnetic stirrer and aged for about 2 h. The solid was isolated by decantation and washed with water several times until the pH value of the supernatant was close to neutral. The obtained product was dried at 120 °C and calcined at 500 °C for 2 h. The synthesis of 1RuCr2O3-P was similar to that of 1RuCr2O3-M. The amount of supported Ru was confirmed by regional energy spectrum analysis (shown in Fig. S1†), which achieved a similar value to that of ICP-OES (Ru = 0.91 wt%).
2.4 Catalytic tests for chlorobenzene oxidation
Catalytic performance was tested in fixed-bed equipment, in which 66 mg of catalysts (40–60 mesh) were packed into a quartz tube with a 6 mm inner diameter. Each end of the catalyst bed was blocked by quartz sands and wool to stabilize the gas flow and to protect the catalysts from being blown away. CB (1000 ppm) with 66 mL min−1 or 132 mL min−1 of airflow passed through the catalyst bed to give the space velocity (SV) of 60
000 mL (g−1 h−1) and 120
000 mL (g−1 h−1). CB gas was produced through continuous gas bubbling of air into a liquid CB saturator, where the concentrations of CB were related to the environment temperature controlled by a cooling circulation system. Reaction temperatures were set in the range of 200–500 °C, which were monitored at the bottom of the catalyst bed using a thermocouple. The gas flow passed through the catalysts from top to bottom. To more accurately reflect the activities of catalysts, each temperature point was extended to as long as 40 min.
The effect of water was achieved by bubbling air (120
000 mL g−1 h−1) through the water at 28 °C to yield a relative humidity of approximately 5%. To ensure the moist air could fully pass through the catalysts rather than condense on the inner walls of pipes, they were highly insulated to keep the temperature at ∼110 °C in reactions. The concentrations of CB and CO2 from the inlet and outlet were analyzed online by a gas chromatograph (GC) with a flame ionization detector and a thermal conductivity detector (TCD), respectively. CB conversion was achieved according to the formula 100% × (Cin − Cout)/Cin, where Cin and Cout indicate the CB concentrations of inlet and outlet gases, respectively. And the mineralization rate in CB combustion was calculated as 100% × M(CO2)/M(CO2)t, where M(CO2) is the concentration of CO2 generated during the reaction at the corresponding temperature and M(CO2)t signifies the calculated concentration of CO2 from the full decomposition of CB in theory.
2.5 Durability measurements
Durability tests were performed on 1RuCr2O3-M and 1RuCr2O3-P under both dry and humid conditions, where 120
000 mL (g−1 h−1) and 305 °C were selected as the space velocity and test temperature.
2.6 Characterizations
The elemental content of Ru was measured using inductively coupled plasma-optical emission spectroscopy (ICP-OES). The phase compositions and chemical bonding states of catalysts were characterized by power X-ray diffraction (XRD, Panalytical X'Pert Pro; Holland) and Raman spectra (HJY, France), respectively. The BET surface areas, structure compositions, pore size distributions, etc. were measured using an automated physical adsorption apparatus (Quantachrome; America). The morphologies, crystal structures, and element distributions of prepared catalysts were observed by transmission electronic microscopy (TEM, JEM 2100F; Japan). Spherical aberration-corrected transmission electron microscopy (JEM ARM 200F) was conducted for the observation of the distribution of noble metals supported. H2 temperature-programmed reduction (H2-TPR) was determined by a chemical sorption instrument (Quantachrome; America), which was also used for oxygen temperature-programmed desorption analysis (O2-TPD) as well. Ammonia temperature-programmed characterization (NH3-TPD) was conducted by the above chemical sorption analyzer connecting a mass spectrum (Quantachrome; America) for the detection of desorbed NH3 signals. X-ray photoelectron spectroscopy (XPS) was performed using a PerkinElmer model PHI 5600 model system equipped with an Al Kα X-ray source (hν = 1486.6 eV). All the peaks corresponding to certain binding energies were calibrated according to the signal of carbon at a binding energy of 284.8 eV, and the curves were fitted carefully. In situ DRIFTS (Thermo Fisher; America) were conducted for mechanistic assessment of CB oxidation under N2 and air atmospheric pressure.
3 Results and discussion
3.1 Structural analysis
As seen in Fig. 1(a), the XRD results indicate that there is little difference in the catalyst peaks with or without Ru loading, where no new peaks corresponding to metallic Ru or oxidation state of Ru (RuOx) can be observed in Ru-based catalysts. The only difference is that the intensity of the XRD pattern for 1RuCr2O3-M is weaker than that of Cr2O3-M whereas it is so close for 1RuCr2O3-P and Cr2O3-P. The slight reduction in the intensity of XRD peaks of 1RuCr2O3-M is due to the incorporation of Ru on the surface of Cr2O3 to cause structural disorder during the reduction of noble metal ions by NaBH4.20 Compared with 1RuCr2O3-P, the interaction between Ru and Cr2O3-M is more intense to make the structure of 1RuCr2O3-M change. A similar phenomenon occurred in Raman spectra of samples, as shown in Fig. 1(b). The peaks centered at 301 (Eg), 340 (Eg), 540 (A1g), and 595 (Eg) cm−1 correspond to Eg symmetry and A1g symmetry of Cr2O3.18,19 Peak intensity decreases after Ru loading on Cr2O3-M. In general, defects and lattice strains can affect the position and intensity of Raman peaks.21 Compared with 1RuCr2O3-P, the stronger intensities of Raman peaks for 1RuCr2O3-M were probably due to the presence of strong interactions between Ru and Cr2O3-M.22
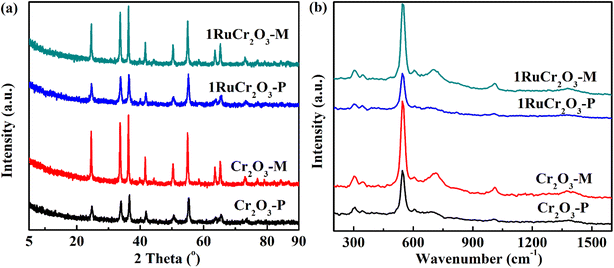 |
| Fig. 1 XRD patterns (a) and Raman spectra (b) of catalysts. | |
Generally, the variation of lattice parameters and lattice distortion often results in a change in XRD and Raman peak intensity.23,24 The peak intensity of Cr2O3-M or 1RuCr2O3-M is stronger than that of Cr2O3-P or 1RuCr2O3-P, indicating more defects and absorbed oxygen on Cr2O3-P and 1RuCr2O3-P compared with Cr2O3-M and 1RuCr2O3-M. The decreased peak intensity of XRD and Raman spectra for 1RuCr2O3-M verified the SMSIs between Ru and surface lattice O, which was considered to be advantageous in VOC oxidation.25,26
The isotherms of nitrogen adsorption–desorption and pore size distribution status are presented in Fig. S2,† where a typical III isotherm with H3 hysteresis indicates irregular mesoporous structure in the as-prepared catalysts (Fig. S2(a)†).19 The pore size distribution was calculated by the BJH method to further observe the pore structure of the materials. As shown in Fig. S2(b),† the pore diameter of the samples all have a dominating structure <40 nm. The difference is that, with a load of Ru species, the pore volume and average pore size of Cr2O3-P both decreased while they remain unchanged for Cr2O3-M under the same treatment (Table 1). The probable reason is that Ru ions were anchored with lattice oxygen of Cr2O3-M in the reduction process of RuCl3 precursors and thus did not destroy the packing state of the Cr2O3 crystal. But for Cr2O3-P, the electrostatic interaction or packing state of the Cr2O3 crystal was broken after Ru was loaded on the surface of Cr2O3. This would lead to the rearrangement of grain crystals to be more tightly integrated. As a result, the pore volume and average pore size decreased accordingly.
Table 1 Nitrogen adsorption–desorption and XPS analysis of samples
Samples |
BET (m2 g−1) |
Pore volume (m3 g−1) |
Average pore size (nm) |
XPS (%) |
Cr2O3/total (%) |
OSur/OLatt (%) |
Cr2O3-P |
34 |
0.4 |
47.9 |
38 |
70 |
Cr2O3-M |
38 |
0.2 |
22.3 |
43 |
19 |
1RuCr2O3-P |
31 |
0.3 |
39.2 |
44 |
18 |
1RuCr2O3-M |
36 |
0.2 |
24.9 |
45 |
17 |
3.2 Morphology characterization
To verify the results obtained by XRD and Raman, HRTEM, element mapping, and Cs-corrected STEM analysis were carried out to visually observe the distribution of noble metals. It can be seen in Fig. 2(a1 and b1) that the micro-morphology of 1RuCr2O3-P and 1RuCr2O3-M is similar to each other, showing irregular oval shapes. They have well-resolved lattice fringes with d-space values ∼0.270 nm, which corresponds with the (104) crystal plane of Cr2O3. No noble metal nanoparticles (metallic Ru0 or RuOx) were observed on the surface with catalysts in HRTEM images of 1RuCr2O3-P (a1) and 1RuCr2O3-M (b1). However, the presence of precious metals was confirmed by the results of ICP-OES, element mapping characterizations (Fig. S3(a and b)†), and energy spectrum analysis (Fig. S1†). Therefore, it can be inferred that the supported Ru is too small to be observed at this scale and amplification.
 |
| Fig. 2 HRTEM and Cs-corrected STEM images of samples: HRTEM (a1), Cs-corrected STEM (a2 and a3) images of 1RuCr2O3-P; HRTEM (b1) and Cs-corrected STEM (b2 and b3) images of 1RuCr2O3-M. | |
To further investigate the interactions between Ru and Cr2O3 supports, a Cs-corrected HAADF-STEM analysis was conducted. It can be seen in Fig. 2(a2 and b2) that the simple reduction method possibly downsizes Ru into single atoms of less than 2 Angstrom (white dots on the surface of supports). There are also a few nanoclusters randomly anchored over the generally exposed low-index (104) facets of 1RuCr2O3-P (Fig. 2(a3)).27,28 By contrast, it can be seen that the single-atom Ru are arranged to anchor over the high index (223) facets of 1RuCr2O3-M (Fig. 2(b3)). Theoretically, high-index faceted metal oxide has more edges, steps, or kinks, which expose a high density of low-coordinated atoms and can provide more active sites to take part in chemical reactions.29 Also, it is recognized that immobilizing single atoms on the high-index facets of supports plays a crucial role in the stability of SACs with metal–support interactions.30 Therefore, the good performance in the activity evaluation (Fig. 6) and durability tests (Fig. 7) under dry and humid conditions is probably due to the atomically dispersed Ru being anchored over the high-index facets, which offers more active sites for oxidation reactions.31
3.3 Surface physicochemical properties
To evaluate the surface element compositions of catalysts, XPS measurements were conducted. As shown in Fig. 3(a), the XPS spectra of O 1s were divided into three sections, where the first peak with binding energies ranging from 529.6 to 530.0 eV is ascribed to lattice oxygen (OLatt);32,33 the second section in the 531.3–531.7 eV range is attributed to oxygen contained in defective sites, which is so-called adsorbed oxygen (OAds);34,35 and the minimum peak of the O 1s spectra centered at 533.0 eV could be identified as surface absorbed O2 or H2O.36,37 The binding energy of lattice oxygen for Cr2O3-P is lower than that of the other three catalysts. That is because the excessive adsorbed oxygen in Cr2O3-P (∼70% for the proportion of OAds/OLatt as shown in Table 1) leads to the increased electron cloud densities of outer electrons in lattice oxygen. From Table 1, it can also be found that the ratio of OAds/OLatt for 1RuCr2O3-P (18%) is much lower than that for Cr2O3-P (70%), which could be attributed to the combination of Ru with absorbed oxygen of Cr2O3-P. And the slight decrease of absorbed oxygen in 1RuCr2O3-M after Ru loading (from 19% to 17%) indicates that most Ru was anchored with lattice oxygen of Cr2O3-M. It could be concluded that the binding energy of oxygen species could be the critical factor for the combination of Ru with CrOx support.
The Cr 2p3/2 XPS spectra were separated into three peaks with binding energies at about 575.4, 576.5, and 578.1 eV (Fig. 3(b)). The former peak can be attributed to Cr(OH)3 species; the second is assigned to Cr2O3; and the peak centered at a high binding energy of 578.1 eV implies the existence of CrO3 species.38–40 Proportions of surface Cr are summarized in Table 1. This shows that the molar ratio of Cr2O3 species in catalyst Cr2O3-P is lower than that of Cr2O3-M, which could be attributed to more adsorbed oxygen and more defects in Cr2O3-P than in Cr2O3-M. The active adsorbed oxygen of Cr2O3-P laid the foundation for Ru to be combined with it. Therefore, the contents of Cr2O3 species in 1RuCr2O3-P increased from 38% to 44% due to the combination of adsorbed oxygen species with Ru. The amounts of Cr2O3 species in 1RuCr2O3-M were relatively unchanged. All the above analyses indicate that Ru is anchored with absorbed oxygen of 1RuCr2O3-P and with lattice oxygen of 1RuCr2O3-M, which could have various impacts on the catalytic efficiency for CB oxidation. The XPS curves of Ru 3p are shown in Fig. 3(c) for both supported catalysts. The binding energies at 486.0 and 463.0 eV are assigned to Ru 3p1/2 and Ru 3p3/2 electron orbit, respectively, which are associated with RuO2 species.41
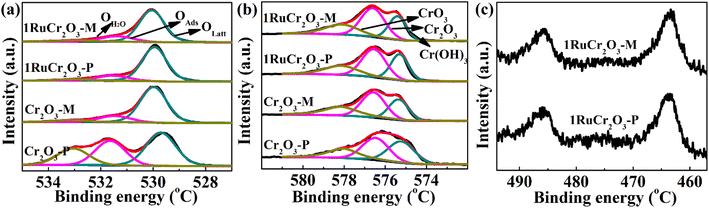 |
| Fig. 3 XPS spectra of catalysts: O 1s (a), Cr 2p3/2 (b), Ru 3p (c). | |
The reduction capacity and active oxygen desorption ability are the most important indicators of catalysts for catalytic oxidation of VOCs,42,43 and are evaluated by characterizations of H2-TPR and O2-TPD, respectively. As shown in Fig. 4(a), the temperatures range from 170 to 370 °C which implies the reduction of Cr6+ to Cr3+.44–46 It can be seen that the initial reduction temperature of Cr2O3-P is a little higher than that of Cr2O3-M, and the reduction temperature range of Cr6+ to Cr3+ for Cr2O3-P is broader than that for Cr2O3-M. This suggests that Cr2O3-M is easier to be reduced and would perform better in CB oxidation. For supported Ru catalysts, the former two peaks at 100–170 °C are assigned to the reduction of RuO2 to metallic Ru (Ru0).47,48 More specifically, the two peaks in the temperature range of 100–170 °C are attributed to the reduction of bulk oxygen of RuO2 with H2.49 For 1RuCr2O3-M, the RuO2 is difficult to reduce compared with that in 1RuCr2O3-P. It could be rationalized that Ru is anchored into lattice oxygen of 1RuCr2O3-M due to a huge lattice matching, which resulted in a strong mental–support interaction (SMSI) of Ru with lattice oxygen. Previous studies indicated that strong interaction between atomically dispersed or other forms of noble metals and catalyst support makes the noble metals harder to reduce.50,51 The reduction peaks of 1RuCr2O3-M for Cr6+ to Cr3+ (170–370 °C) almost vanished after Ru application but were different with Cr2O3-P and 1RuCr2O3-P. This implies that the combination of Ru and oxygen in 1RuCr2O3-P does not have an impact on the reduction of Cr2O3-P support. It is different from the H2-TPR analysis of 1RuCr2O3-M, as there is nearly no reduction peak of Cr6+ to Cr3+. The phenomenon implies the lattice oxygen species of Cr2O3-M is difficult to be moved during this temperature range. Corresponding to Cs-corrected STEM results, the H2-TPR confirmed the different combination forms between single-atom Ru and oxygen species, where adsorbed oxygen and lattice oxygen are the main components to be anchored with Ru for 1RuCr2O3-P and 1RuCr2O3-M.
O2-TPD is shown in Fig. 4(b), and it can be seen that there is much more adsorbed oxygen in Cr2O3-P in comparison with Cr2O3-M. The result is consistent with the analysis of XPS. In the spectrum of 1RuCr2O3-P, a strong peak can be observed at a temperature of 680 °C, which indicates the desorption of bulk lattice oxygen. But for 1RuCr2O3-M, nearly no peak can be observed from 70 to 800 °C, which further indicated the conclusion derived from Raman, XPS, and H2-TPR of the SMSI between Ru and lattice oxygen of 1RuCr2O3-M.
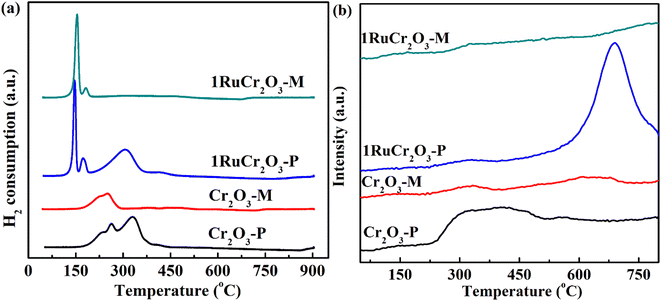 |
| Fig. 4 H2-TPR (a) and O2-TPD (b) analysis of catalysts. | |
Acid site was considered as a crucial factor on catalyst activity and selectivity for heterogeneous catalysis.52,53 NH3-TPD was performed to study the acid sites of catalysts, and the profiles are shown in Fig. 5. The peak area and temperature location correspond to the amounts and varieties of acid sites on the surface of catalysts.54 Brønsted acid sites are weaker than Lewis acids on the surface of Cr2O3, thus it is easier for NH3 adsorbed on Brønsted acid sites to be released at a lower temperature than that on Lewis acid sites. And based on the intensities of acid sites, desorption peaks ranging from 100 to 350 °C could be attributed to the weak and medium acid sites, and desorption peaks at a higher temperature of ∼600 °C imply strong acid sites.55 So, peaks with temperatures below 200 °C (section I) could be ascribed to the desorption of physically adsorbed NH3 and NH4+ on the weak Brønsted acid sites of catalysts. Section II between 230 and 470 °C indicates the desorption of NH3 from strong Brønsted acid sites. Then, the desorption peaks contained in section III denote NH3 is adsorbed on Lewis acid sites on the surface of catalysts. It can be inferred from the NH3-TPD profiles that the contents of Brønsted acid sites on Cr2O3-M and 1RuCr2O3-M are much larger than that on the surface of Cr2O3-P and 1RuCr2O3-P. Based on previous reports,56–58 the presence of Brønsted acid sites can result in nucleophilic substitution among chlorinated organics and acid sites, thereby degrading CB into phenolates and leading to ring cleavage. So, the catalysts with plenty of Brønsted acid sites (Cr2O3-M and 1RuCr2O3-M) were considered beneficial to CB adsorption. Another point worth noting is that after Ru is supported on the catalysts, there is little difference in the Brønsted acid sites between Cr2O3-M and 1RuCr2O3-M but with an obvious increase for 1RuCr2O3-P compared with Cr2O3-P. The results indicate that the contents of Brønsted acid sites can be increased due to the supported Ru on the surface of catalysts (1RuCr2O3-P). If constrained to the lattice of support (Cr2O3-M), it would have little effect on the acid sites.
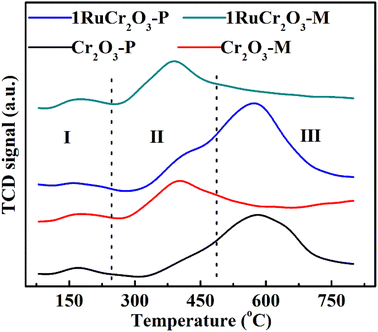 |
| Fig. 5 NH3-TPD profiles of catalysts. | |
3.4 Activity and durability tests
CB conversions and CO2 mineralization rate of as-prepared catalysts with 120
000 mL (g−1 h−1) of SV are shown in Fig. 6. As shown in Fig. 6, both CB conversion and CO2 mineralization rate of Cr2O3-M are higher than that of Cr2O3-P, which is due to the higher BET surface area of Cr2O3-M. When the temperature is less than 260 °C, the conversion and CO2 mineralization rate of 1RuCr2O3-P is close to that of Cr2O3-M. That can be attributed to the better active oxygen desorption ability of Cr2O3-M at low temperatures (shown in Fig. 4(b)), and the surface oxygen of 1RuCr2O3-P could be anchored by the Ru4+ and therefore not vulnerable to migrate at low temperature. When the temperature increases, the oxygen could be released from RuO2 due to the redox reaction between CB and catalysts, which results in the increased activities of 1RuCr2O3-P in high-temperature regions. But for 1RuCr2O3-M, the CO2 mineralization and CB conversion is always higher than that of the other three catalysts with an increase in temperature. The result indicates that the active oxygen of 1RuCr2O3-M works from low temperature to high temperature, unlike 1RuCr2O3-M. From the activity performance above, it is reasonable to infer that the active oxygen of 1RuCr2O3-M could be different with 1RuCr2O3-P.
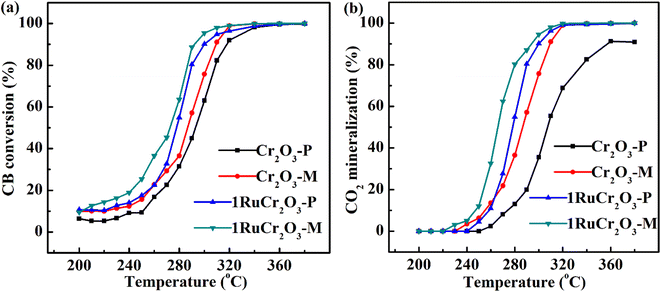 |
| Fig. 6 CB conversion (a) and CO2 mineralization rate (b) of the catalysts with CB concentration = 1000 ppm and SV = 120 000 mL (g−1 h−1). | |
Because the turning points of temperature are located at ∼300 °C for CB conversion and CO2 mineralization rate of 1RuCr2O3-P, the stability measurements were conducted at this temperature to further verify the above conclusion derived from activity tests under both dry and humid conditions. It can be seen from Fig. 7 that CB conversion and CO2 mineralization rate of 1RuCr2O3-P are lower than that of 1RuCr2O3-M under dry conditions. With longer times, the CO2 mineralization rate of 1RuCr2O3-P declines more than that of 1RuCr2O3-M. The phenomenon shown in the on-stream tests corresponds to the activities in Fig. 6. Moreover, it can be seen from the durability test under the humid condition that the conversion and mineralization rate of 1RuCr2O3-M decreased due to the competitive adsorption of water vapor and CB. The CB conversion and CO2 mineralization rate of 1RuCr2O3-M are close to each other under humid conditions but have an obvious difference in dry conditions with a much higher conversion than mineralization rate, indicating the hydroxyl oxygen derived from water promoted the oxidation of CB.59,60 Generally, the state of the noble metals could be crucial for the catalytic property in durability test. To observe the morphology and thoroughly comprehend the stability of 1RuCr2O3-M, the used catalysts in dry and humid conditions were characterized by HRTEM and Cs-corrected STEM shown in Fig. S4.† It is interesting that after careful observation nano-sized or aggregated Ru could not be found using HRTEM. And Cs-corrected STEM confirmed the maintaining of single-atom Ru on the surface of 1RuCr2O3-M. The result indicates that the as-prepared catalyst has the good thermal stability and crystal structure in long time high temperature process.
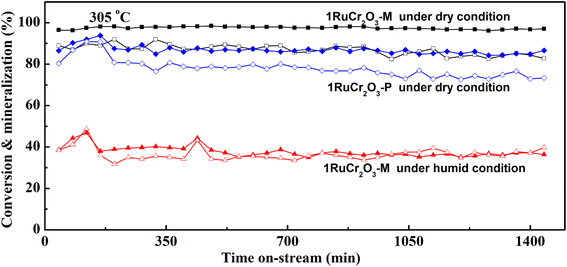 |
| Fig. 7 Durability tests of 1RuCr2O3-M under dry (black lines), humid conditions (relative humidity of 5%, red lines) and 1RuCr2O3-P under dry condition (blue lines) at 305 °C with CB concentration = 1000 ppm and SV = 120 000 mL (g−1 h−1), where the solid symbols represent CB conversion and hollow symbols denote CO2 mineralization rate correspondingly. | |
Based on the performance of catalysts and several characterizations, such as Cs-corrected STEM, O2-TPD, H2-TPR, and XPS, it can be concluded that the binding form of Ru and oxygen species (adsorbed or lattice oxygen) could be the main factor for the durability of CB combustion. With similar Ru content and the same supports, the high tolerance of 1RuCr2O3-M on CB oxidation could be due to the SMSI between single-atom Ru and lattice oxygen (which makes CB deeply oxidized and suppresses the organochlorine adsorptions and coke accumulations).
4 Mechanism analysis
The CB adsorption and reaction pathway over the optimum catalyst (1RuCr2O3-M) were analyzed by in situ FT-IR measurements under different atmospheric pressures where 99.999% of N2 was used to study the effect of lattice oxygen in CB oxidation at different temperatures. The reactions were examined at temperatures from 200 to 400 °C. Fig. 8(a) shows the CB adsorbed on the 1RuCr2O3-M catalyst as a function of temperature under the N2 atmosphere. Several peaks identified at approximate 1582, 1478, and 1448 cm−1 are ascribed to the vibrations of ν(C
C), ν(C–H), and δ(C–H)/ν(C
C),61 respectively, indicating adsorption of CB on the catalyst. The wavebands of 3000–4000 cm−1 are assigned as hydroxyl regions, where the peaks at 3638 and 3658 cm−1 imply the –OH being grafted on the Cr2O3 surface,58 and the peaks at ∼3730 and 2300 cm−1 originate from the produced H2O and CO2 at a temperature of 200 °C. Another peak at about 3420 cm−1 could also be identified as hydroxyl at the metal oxide surface. With increasing temperature, the reverse IR band at 3420 cm−1 indicated the consumption of –OH groups because of adsorption of CB. When the temperature was >200 °C, the produced H2O and CO2 almost disappeared, indicating the reaction was inhibited without air supply. The results indicated that the produced H2O and CO2 at the beginning were derived from the reaction products of surface lattice oxygen and CB. In the region of 1200–1700 cm−1, peaks at ∼1215, 1325 and 1394, 1657 cm−1 can be attributed to C–O stretching of surface phenolate,56 surface carboxylates,61 and C
O vibration of benzoquinone species,58,62 respectively.
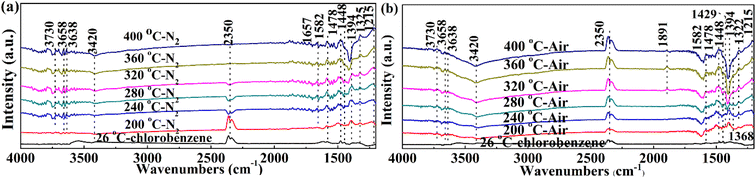 |
| Fig. 8 In situ FT-IR analysis on 1RuCr2O3-M under exposure to chlorobenzene in N2 (a) and high pure air (b). | |
As shown in Fig. 8(b), air was introduced into the system. Some bands are observed at 1368, 1429, and 1891 cm−1 which can be assigned to chlorinated acetates, surface maleate species, and aldehyde-type species,56,58,63 respectively. Another difference is that the bands corresponding to CO2 (2350 cm−1) and H2O (3730 cm−1) were enhanced when the air was introduced into the reaction system. A comparison with Fig. 8(a) indicates that the introduction of air can accelerate intermediate products derived from the reaction between surface lattice oxygen and CB to be deeply degraded into CO2 and H2O.
To sum, it can be concluded that catalyst 1RuCr2O3-M can convert CB into non-toxic products. The possible pathway for combustion oxidation of CB over 1RuCr2O3-M could be that CB was first adsorbed on the surface lattice oxygen of the catalyst to form surface phenolate species, which led to the change of electronic properties of the benzene ring. Then the benzoquinone-type species and some further oxidation products, including chlorinated acetates and surface maleate species, were observed due to the electrophilic substitution between the oxygen-containing group and chlorine substituents at a lower temperature. With the increase in temperature, the chlorinated acetates were transformed into aldehyde-type species and finally formed CO2, H2O, and HCl. The detailed reaction pathway may proceed as the diagram shown in Fig. 9.
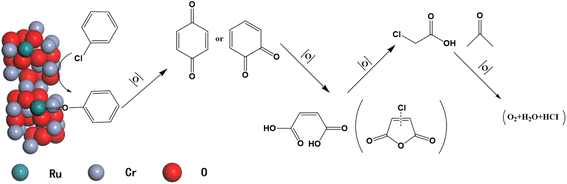 |
| Fig. 9 The pathway of CB degradation over 1RuCr2O3-M. | |
5 Conclusions
The Ru single-atom catalysts (Ru/Cr2O3) were successfully synthesized through a relatively simple reduction method for the efficient oxidation of CB—this is novel research for the preparation of SACs. The same metal oxides (Cr2O3) with different preparation methods resulted in different bonding between the noble metal Ru and supports Cr2O3, with Ru supported on the surface of Cr2O3-P while being confined in the lattice of Cr2O3-M. The results were related to the predominant oxygen species of catalyst supports, indicated by the characterizations of XPS and H2-TPR. Due to the atomically dispersed Ru and its strong interaction (SMSI) with lattice oxygen of high-index facets of Cr2O3-M, the catalyst 1RuCr2O3-M not only led to an excellent catalytic efficiency but also ensured durability and an anti-poisoning effect for CB oxidation. The study provides a simple and reliable way for the preparation of Ru-based SACs with SMSI. The good durability in chlorobenzene oxidation implies its practical potential application in this field, and the synthetic approach could be extended to other noble-metal catalysts.
Conflicts of interest
There are no conflicts to declare.
Acknowledgements
This work was supported by the Fundamental Research Program of Youth of Shanxi Province (No. 20210302124478, 20210302124347) and the Scientific and Technological Project of Shanxi Province (No. 201903D321082).
References
- Y. Su, K. Fu, C. Pang, Y. Zheng, C. Song, N. Ji, D. Ma, X. Lu, C. Liu, R. Han and Q. Liu, Environ. Sci. Technol., 2022, 56, 9854–9871 CrossRef CAS PubMed.
- Y. Kuang and H. Li, Renewable Sustainable Energy Rev., 2021, 151, 111582 CrossRef CAS.
- H. Xu and H. Li, J. Energy Chem., 2022, 73, 133–159 CrossRef CAS.
- Y. Huang, S. Fang, M. Tian, Z. Jiang, Y. Wu and C. He, Processes, 2021, 9, 19 Search PubMed.
- T. K. Nevanpera, S. Pitkaaho, S. Ojala and R. L. Keiski, Molecules, 2020, 25, 4644 CrossRef CAS PubMed.
- G. Gan, S. Fan, X. Li, Z. Zhang and Z. Hao, J. Environ. Sci., 2023, 123, 96–115 CrossRef PubMed.
- X. Lv, S. Cai, J. Chen, D. Yan, M. Jiang, J. Chen and H. Jia, Catal. Sci. Technol., 2021, 11, 4581–4595 RSC.
- C. Li, Y. Zhao, H. Song and H. Li, J. Chem. Technol. Biotechnol., 2020, 95, 2069–2082 CrossRef CAS.
- Y. Su, K. Fu, Y. Zheng, N. Ji, C. Song, D. Ma, X. Lu, R. Han and Q. Liu, Appl. Catal., B, 2021, 288, 119980 CrossRef CAS.
- H. Liu, X. Li, Q. Dai, H. Zhao, G. Chai, Y. Guo, Y. Guo, L. Wang and W. Zhan, Appl. Catal., B, 2021, 282, 119577 CrossRef CAS.
- J. Jiang, W. Ding and H. Li, Renewable Energy, 2021, 179, 1262–1270 CrossRef CAS.
- H. Liu, J. Yang, Y. Jia, Z. Wang, M. Jiang, K. Shen, H. Zhao, Y. Guo, Y. Guo, L. Wang, S. Dai and W. Zhan, Environ. Sci. Technol., 2021, 55, 10734–10743 CrossRef CAS.
- S. Lee, H. Han, W. Yoon and W. B. Kim, Appl. Catal., A, 2021, 611, 117970 CrossRef CAS.
- M. Yoo, Y.-S. Yu, H. Ha, S. Lee, J.-S. Choi, S. Oh, E. Kang, H. Choi, H. An, K.-S. Lee, J. Y. Park, R. Celestre, M. A. Marcus, K. Nowrouzi, D. Taube, D. A. Shapiro, W. Jung, C. Kim and H. Y. Kim, Energy Environ. Sci., 2020, 13, 1231–1239 RSC.
- Q. Kuang, X. Wang, Z. Jiang, Z. Xie and L. Zheng, Acc. Chem. Res., 2014, 47, 308–318 CrossRef CAS PubMed.
- J. Li, Z. Yang, Y. Li and G. Zhang, J. Hazard. Mater., 2022, 429, 128285 CrossRef CAS PubMed.
- Y. Huang, M. Tian, Z. Jiang, M. Ma, C. Chen, H. Xu, J. Zhang, R. Albilali and C. He, Appl. Catal., B, 2022, 304, 121002 CrossRef CAS.
- X. Chen, X. Chen, S. Cai, J. Chen, W. Xu, H. Jia and J. Chen, Chem. Eng. J., 2018, 334, 768–779 CrossRef CAS.
- X. Chen, X. Chen, S. Cai, E. Yu, J. Chen and H. Jia, Appl. Surf. Sci., 2019, 475, 312–324 CrossRef CAS.
- P. S. Murphin Kumar, V. K. Ponnusamy, K. R. Deepthi, G. Kumar, A. Pugazhendhi, H. Abe, S. Thiripuranthagan, U. Pal and S. K. Krishnan, J. Mater. Chem. A, 2018, 6, 23435–23444 RSC.
- K. K. Mandari, J. Y. Do, A. K. R. Police and M. Kang, Appl. Catal., B, 2018, 231, 137–150 CrossRef CAS.
- Z. Xi, D. P. Erdosy, A. Mendoza-Garcia, P. N. Duchesne, J. Li, M. Muzzio, Q. Li, P. Zhang and S. Sun, Nano Lett., 2017, 17, 2727–2731 CrossRef CAS PubMed.
- B. Li, L. Qiu and J. W. Tian, J. Alloys Compd., 2018, 767, 797–802 CrossRef CAS.
- W.-F. Chen, H. Chen, P. Koshy, A. Nakaruk and C. C. Sorrell, Mater. Chem. Phys., 2018, 205, 334–346 CrossRef CAS.
- X. Q. Yang, S. H. Liu, J. W. Li, J. Y. Chen and Z. B. Rui, Chemosphere, 2020, 249, 1–8 Search PubMed.
- S. Akram, L. Chen, Q. Wang, X. R. Zhang, N. Han, G. L. Shen, Z. Wang and G. L. Ge, Catal. Lett., 2017, 147, 128–140 CrossRef CAS.
- W.-C. Huang, L.-M. Lyu, Y.-C. Yang and M. H. Huang, J. Am. Chem. Soc., 2012, 134, 1261–1267 CrossRef CAS PubMed.
- S. T. Hunt and Y. Román-Leshkov, Acc. Chem. Res., 2018, 51, 1054–1062 CrossRef CAS PubMed.
- C. X. Yang, Z. H. Li, H. L. Li, H. Liang, J. H. Liu, Y. C. Zhang, X. C. Wang, X. Y. Jiang, W. Z. Chen, J. Yuan, S. Q. Liu and X. Y. Li, Sens. Actuators, B, 2023, 374, 132753 CrossRef CAS.
- X. Li, X. Yang, Y. Huang, T. Zhang and B. Liu, Adv. Mater., 2019, 31, 1902031 CrossRef CAS PubMed.
- S. Sun, X. Zhang, J. Cui, Q. Yang and S. Liang, Nanoscale, 2019, 11, 15739–15762 RSC.
- H.-J. Chun, Y. Lee, S. Kim, Y. Yoon, Y. Kim and S.-C. Park, Appl. Surf. Sci., 2022, 578, 152018 CrossRef CAS.
- G. Alba, M. P. Villar, R. Alcántara, J. Navas and D. Araujo, Nanomaterials, 2020, 10, 1193 CrossRef CAS PubMed.
- S. Kozhukharov, C. Girginov, A. Tsanev and N. Boshkova, Appl. Surf. Sci., 2022, 602, 154254 CrossRef CAS.
- G. V. Prasath, K. S. Usha, M. Karuppaiah, G. Ravi and P. Krishnan, J. Sol-Gel Sci. Technol., 2022, 104, 198–210 CrossRef.
- M. C. Biesinger, B. P. Payne, A. P. Grosvenor, L. W. M. Lau, A. R. Gerson and R. S. C. Smart, Appl. Surf. Sci., 2011, 257, 2717–2730 CrossRef CAS.
- W. Qin, L. Su, C. Yang, Y. Ma, H. Zhang and X. Chen, J. Agric. Food Chem., 2014, 62, 5827–5834 CrossRef CAS PubMed.
- W.-X. Zhang, Y. Liang, J.-W. Luo, A.-P. Jia, Y.-J. Wang, J.-Q. Lu and M.-F. Luo, J. Mater. Sci., 2016, 51, 6488–6496 CrossRef CAS.
- Y. Lin, W. Cai, X. Tian, X. Liu, G. Wang and C. Liang, J. Mater. Chem., 2011, 21, 991–997 RSC.
- X.-Z. Fu, X.-X. Luo, J.-L. Luo, K. T. Chuang, A. R. Sanger and A. Krzywicki, J. Power Sources, 2011, 196, 1036–1041 CrossRef CAS.
- Z. Mohamed, V. D. B. C. Dasireddy, S. Singh and H. B. Friedrich, Int. J. Hydrogen Energy, 2018, 43, 22291–22302 CrossRef CAS.
- W. Si, Y. Wang, S. Zhao, F. Hu and J. Li, Sci. Technol., 2016, 50, 4572–4578 CrossRef CAS PubMed.
- Y. Wang, H. Arandiyan, J. Scott, M. Akia, H. Dai, J. Deng, K.-F. Aguey-Zinsou and R. Amal, ACS Catal., 2016, 6, 6935–6947 CrossRef CAS.
- J. S. B. Grzybowska, R. Grabowski, K. Wcisło, A. Kozłowska, J. Stoch and J. Zieliński, J. Catal., 1998, 178, 687–700 CrossRef.
- G. Bai, H. Dai, Y. Liu, K. Ji, X. Li and S. Xie, Catal. Commun., 2013, 36, 43–47 CrossRef CAS.
- P. Xia, S. Zuo, F. Liu and C. Qi, Catal. Commun., 2013, 41, 91–95 CrossRef CAS.
- M. A. G. Hevia, A. P. Amrute, T. Schmidt and J. Pérez-Ramírez, J. Catal., 2010, 276, 141–151 CrossRef CAS.
- X. Liu, Q. Han, W. Shi, C. Zhang, E. Li and T. Zhu, J. Catal., 2019, 369, 482–492 CrossRef CAS.
- J. Shi, F. Hui, J. Yuan, Q. Yu, S. Mei, Q. Zhang, J. Li, W. Wang, J. Yang and J. Lu, Catalysts, 2019, 9, 108 CrossRef.
- Q. Zhang, X.-X. Qin, F.-P. Duan-Mu, H.-M. Ji, Z.-R. Shen, X.-P. Han and W.-B. Hu, Angew. Chem., Int. Ed., 2018, 57, 9351–9356 CrossRef CAS PubMed.
- Y. Luo, Q. Qian and Q. Chen, Mater. Res. Bull., 2015, 62, 65–70 CrossRef CAS.
- Y. Geng and H. Li, Chemsuschem, 2022, 15, e202102495 CrossRef CAS PubMed.
- H. Wei, Z. Wang and H. Li, Green Chem., 2022, 24, 1930–1950 RSC.
- M. Guo, Q. Liu, P. Zhao, J. Han, X. Li, Y. Ha, Z. Fu, C. Song, N. Ji, C. Liu, D. Ma and Z. Li, Chem. Eng. J., 2019, 361, 830–838 CrossRef CAS.
- H. Liu, L. Wei, R. Yue and Y. Chen, Catal. Commun., 2010, 11, 829–833 CrossRef CAS.
- J. Lichtenberger and M. D. Amiridis, J. Catal., 2004, 223, 296–308 CrossRef CAS.
- X. Weng, P. Sun, Y. Long, Q. Meng and Z. Wu, Environ. Sci. Technol., 2017, 51, 8057–8066 CrossRef CAS PubMed.
- J. Wang, X. Wang, X. Liu, T. Zhu, Y. Guo and H. Qi, Catal. Today, 2015, 241, 92–99 CrossRef CAS.
- Y. Deng, S. Peng, H. Liu, S. Li and Y. Chen, Front. Environ. Sci. Eng., 2019, 13, 21 CrossRef CAS.
- P. Sun, W. Wang, X. Weng, X. Dai and Z. Wu, Environ. Sci. Technol., 2018, 52, 6438–6447 CrossRef CAS PubMed.
- Y. Liu, W. Wu, Y. Guan, P. Ying and C. Li, Langmuir, 2002, 18, 6229–6232 CrossRef CAS.
- Y. Gu, T. Cai, X. Gao, H. Xia, W. Sun, J. Zhao, Q. Dai and X. Wang, Appl. Catal., B, 2019, 248, 264–276 CrossRef CAS.
- G. Busca, G. Ramis and V. Lorenzelli, J. Mol. Catal., 1989, 50, 231–240 CrossRef CAS.
Footnote |
† Electronic supplementary information (ESI) available: (1) EDS analysis of 1Ru/Cr2O3-P and 1Ru/Cr2O3-M, (2) Nitrogen adsorption–desorption isotherms and pore size distributions of 1Ru/Cr2O3-P and 1Ru/Cr2O3-M, and (3) CB conversion and CO2 mineralization rate of samples with CB concentration = 1000 ppm and SV = 60 000 mL (g−1 h−1). See DOI: https://doi.org/10.1039/d2ra07650k |
|
This journal is © The Royal Society of Chemistry 2023 |
Click here to see how this site uses Cookies. View our privacy policy here.