Engineering g-C3N4 composited Fe-UIO-66 to in situ generate robust single-atom Fe sites for high-performance PEMFC and Zn–air battery†
Received
12th October 2022
, Accepted 17th November 2022
First published on 18th November 2022
Abstract
Developing an efficient and robust electrocatalyst for the sluggish oxygen reduction reaction (ORR) in PEMFC is imperatively desirable and challenging. This study presents a feasible route of co-carbonization of the Fe-loaded UIO-66/g-C3N4 hybrid to access an efficient mesoporous carbon (MC) encapsulated Fe–N ensemble (denoted as Fe–N/MC catalyst). The co-presence of g-C3N4 served as a significant binary functionality during the synthesized route. One way is affording the N species covalency with Fe atoms to generate the Fe–N active sites and the other way is by offering carbon precursors to yield mesoporosity within the carbon matrix. Beneficial to these enriched Fe–N species, improved conductivity, hierarchical porosity, etc.; this novel Fe–N/MC catalyst presents significantly improved ORR activity and stability as the cathode in the membrane electrode assembly (MEA). Specifically, a high and stable peak power density of 1.15 W cm−2 with a minor decay (ca. 21.8%) of power density after a long period of discharge is achieved. This work may offer a facile strategy to develop non-precious metal-based catalysts assembled in a cathode for both PEMFC and metal–air batteries with high performance and improved stability.
1. Introduction
In the pursuit of highly efficient devices and techniques for energy storage and conversion, proton exchange membrane fuel cells (PEMFC) show appealing merits (e.g., high energy conversion efficiency, environmentally benign) and evoke great interest among scientists and technicians.1–3 The oxygen reduction reaction (ORR) that occurs in the cathode of PEMFC has significantly limited the overall cell performance due to its inherent sluggish kinetics relative to the anode reaction. A widely used and compromised strategy to improve the ORR performance is the high loading of Pt-based catalysts in the cathode.4–8 Unfortunately, the high cost of Pt owing to its scarcity seriously hinders its large-scale production for commercialization.9–11 Alternatively, scientists have turned to developing platinum group metal-free (PGM-free) catalysts with reasonable catalytic activity and durability to realize PEMFC commercialization.
The recently emerged transition metal and nitrogen co-doped porous carbon catalysts (M–NX/C, M = Fe, Co, Mn, etc.) have shown their promising potential in replacing the conventional noble metal cathode catalysts.12–22 Several research groups have also achieved several exciting breakthroughs. For example, Sun et al.23 reported a Fe/N/C ORR catalyst prepared by pyrolysis under NH3 that exhibited a half-wave potential of 0.78 V in 0.1 M HClO4. The Wu group developed an efficient CVD method to prepare atomically dispersed and N, S co-ligated single Fe active site catalysts that exhibited a half-wave potential of 0.81 V in acidic environments.24 Although progress has been achieved, the cell performance, especially for stability, is still unsatisfactory when the catalysts are applied in the cathode of PEMFC.
Tuning the electron density and local coordination structure of the metal center could modulate the adsorption energies of O2 and ORR intermediates and thus facilitate the intrinsic activity.25–28 Apart from increasing the intrinsic activity, adequate exposure to metal sites is also a prerequisite for designing highly efficient catalysts. Previous studies reported that few Fe–NX moieties could be referred to as the actual active sites toward ORR catalysis,29–35 especially in the solid-state cathode catalyst layers of membrane electrode assemblies (MEAs) for fuel cells. However, to match the anode, a large amount of catalysts must be assembled in the cathode of the MEA. This is apt to render active sites inaccessible due to the thick catalyst layer. Generally, the external Fe–NX moieties dispersed at the triple-phase boundaries (TPBs) of catalysts are accessible and possess better ORR activity than the usually inaccessible bulk Fe–NX species, leading to a tremendous waste of metal moieties in Fe–N/C catalysts.36–38 Thus, developing atomically dispersed Fe–N/C catalysts with high intrinsic activity and more exposed Fe–NX moieties at TPBs is particularly critical to enhancing the practical performance of Fe–N/C catalysts in PEMFCs.
In addition, the insufficient durability of atomically dispersed Fe–N/C catalysts remained another bottleneck. From the analysis of the progress of the study, the main reasons for the performance decay of the Fe–N/C catalyst are:39–44 (i) leaching of active metal components, (ii) attack by H2O2 and free radicals, (iii) corrosion of the carbon surface, (iv) active site covered by carbon layers or water generated at the cathode. Although there are now some literature reports on the mechanism of attenuation of Fe/N/C catalysts, some remaining doubts still need to be explored and studied.
Herein, we developed an efficient strategy of co-carbonization of Fe-doped UIO-66 and g-C3N4 to access a novel mesoporous carbon encapsulated Fe–NX ensemble electrocatalyst, Fe–NX/MC. The co-presence of g-C3N4 serves a crucial binary functionality that affords both nitrogen and carbon sources to in situ generate the Fe–NX active sites and mesoporosity, respectively. The enriched Fe–NX active sites, smoothed charge-transfer and mass-transport efficacy contribute concurrently to the enhanced peak power density at H2–O2 PEMFC.29 The optimized catalyst has a half-wave potential of 0.86 V (vs. RHE) in 0.1 M KOH and 0.76 V (vs. RHE) in 0.1 M HClO4. More importantly, a high-power density of 1.15 W cm−2 was generated in the H2–O2 PEMFC. Its cell performance can be recovered to close to its initial performance after 24 h of discharging, with its power density only decaying by 21.8%. Meanwhile, by observing the causes of the Fe/N/C catalyst decay mentioned above, it was found that the leaching of Fe from the catalyst was the main reason for the poor stability of the Fe–N/C catalysts, and the encapsulation of the active center in the N-doped carbon matrix effectively prevented the leaching of Fe from the active center.
2. Experimental
Zirconium tetrachloride, 2-aminoterephthalic acid, ferrocene, N,N-dimethylamine, glacial acetic acid, methanol, and melamine were purchased from Shanghai Chemical Reagent Factory, China. Deionized water with a specific resistance of 18.25 MΩ was used. All reagents were of analytical grade and were used as received without further purification.
2.1 Synthesis of UIO-66 and g-C3N4 nanoparticles
The UIO-66 and g-C3N4 nanoparticles were each synthesized using a previously reported method.44–47 For the UIO-66, 2-aminoterephthalic acid (NH2-BDC) (8.1 mg), ZrCl4 (10.7 mg), and 1.2 mL acetic acid (HAc) were placed in a 15 mL glass vial and dissolved together by 10 mL N,N-dimethylformamide (DMF). Then, the glass vial was capped and heated to 120 °C in a thermostatic drying oven for 24 h. After that, the mixture was washed with DMF and methanol three times each, and then dried under vacuum for 12 h at 80 °C for further use. For the g-C3N4, a calculated amount of melamine was put into a crucible with a lid, and kept in static air in a muffle furnace at 550 °C for 4 h at a heating rate of 6 °C min−1.
2.2 Preparation of Fe–NX ensemble encapsulated in mesoporous carbon (Fe–N/MC) composite catalysts
The fabrication of the Fe–N/MC catalysts follows three successive steps, as shown in Fig. 1, including the loading of ferrocene (FeCp) molecules on UIO-66, mixing of g-C3N4 nanoparticles, and thermal carbonization. Firstly, FeCp molecules, as the Fe precursor, were vaporized and captured by the as-obtained UIO-66 via chemical vapor deposition in a tubular oven. Then, the pre-formed g-C3N4 nanoparticles were loaded on the resulting FeCp@UIO-66 by physical mixing. Next, the hybrid mixture was pyrolyzed at an optimal temperature of 950 °C for 1 h in an argon atmosphere. After cooling down to room temperature, the black composite was etched by hydrofluoric acid to remove the weak-anchored Fe and Zr ions, and secondary carbonization was conducted. Finally, a Fe–NX ensemble encapsulated in mesoporous carbon, denoted as Fe–N/MC, was collected. Precursor-derived Fe–N/MCs were prepared in FeCp and UIO-66 at different mass ratios of 1
:
1, 1.5
:
1, 2
:
1, and 4
:
1 and named Fe–N/MC-1, Fe–N/MC, Fe–N/MC-2, and Fe–N/MC-4, respectively. For comparison, a reference sample (Fe–N/C-ref) was prepared with the same process, but without the presence of g-C3N4.
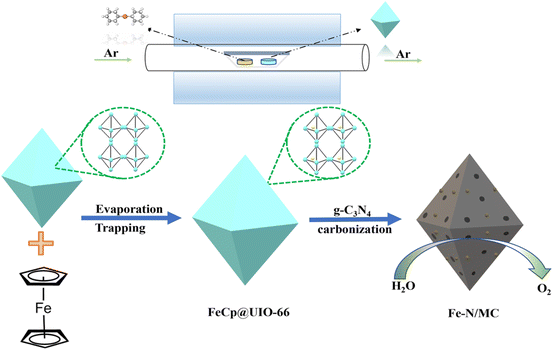 |
| Fig. 1 Schematic diagram for the synthesized route to the Fe–N/MC catalyst. | |
2.3 Characterizations
Fourier transform infrared (FT-IR) spectroscopy was used to analyze the bonding states and compositions of the FeCp@UIO-66 precursors in the range of 4000 to 400 cm−1 on a Nicolet-5700 spectrometer. Raman spectra were obtained from 200 to 2300 cm−1 on a Raman spectrometer (Labram HR, Horiba). X-ray diffraction (XRD) patterns were obtained at the 2θ angle of 5 to 80° at a scan rate of 5° min−1 by using Cu Kα radiation sources. X-ray photoelectron spectroscopy (XPS) was conducted on a VG ESCALAB MK2 X-ray photoelectron spectrometer (VG Corporation, U.K.) using an Al-Kα X-ray source. Low-pressure N2 adsorption–desorption isotherms for the Brunauer–Emmett–Teller (BET) specific surface area were recorded on an Autosorb-iQ (Quantachrome) analyzer at 77 K. The samples' morphologies were investigated using a scanning electron microscope and transmission electron microscopy. (SEM, FEI Nova™ NanoSEM230. TEM, Hitachi HT7700). Inductively coupled plasma optical emission spectrometry (ICP-OES, Optima 5300DV) was used to determine the Fe content in the samples.
2.4 Electrocatalytic measurements
All electrochemical measurements were conducted using an Ivium electrochemical workstation (Ivium, Netherlands) in a standard three-electrode system, with an Ag/AgCl reference electrode for the acidic medium and a Hg/HgO reference electrode for the alkaline medium. A graphite rod was used as the counter electrode and a glassy carbon (GC) electrode as the working electrode substrate (0.196 cm2). All carbon catalyst-loaded electrodes were prepared by the following procedure: 5 mg catalyst was ultrasonically dispersed in 1 mL Nafion/ethanol solution (0.25 wt% Nafion), yielding a catalyst ink. Then, 20 μL of the catalyst ink was pipetted onto a GC substrate electrode and dried under infrared radiation. The catalyst loading was about 0.5 mg cm−2.
Linear sweep voltammetry (LSV) and cyclic voltammetry (CV) were carried out in O2 or N2-saturated 0.1 M KOH and 0.1 M HClO4 electrolytes at a scan rate of 10 mV s−1. The electron transfer number during ORR testing was calculated by employing the Koutecky–Levich (K–L) equation:
J−1 = Jk−1 + (0.62nFCD2/3γ−1/6ω1/2)−1 |
where
J is the measured current density,
Jk is the kinetic current density,
n is the electron transfer number,
ω is the electrode rotation rate,
F is the Faraday constant,
C is the O
2 saturation concentration in the electrolyte,
D is the O
2 diffusion coefficient in the electrolyte, and
γ is the kinetic viscosity of the electrolyte. Durability testing was conducted at 0.6 V for 12 h at a rotation rate of 1600 rpm in an O
2-saturated 0.1 M KOH solution and an O
2-saturated 0.1 M HClO
4 solution using the chronoamperometric technique.
The catalyst charge transfer number and hydrogen peroxide (H2O2) yield were obtained from the results of the rotating ring-disk electrode (RRDE) test. The RRDE was also recorded using linear scanning voltammetry (LSV) in an O2-saturated 0.1 M HClO4 solution. The test was performed in the scanning voltage range of 0.8 V to −0.2 V (vs. Ag/AgCl) with a scanning rate of 10 mV S−1 and a speed of 1600 rpm, while the ring electrode voltage was kept at 1.31 V vs. RHE. The H2O2 yield was calculated from the following equation:
H2O2 (%) = (200Iring/N)/(Idisk + (Iring/N)) |
I
ring and Idisk are the absolute values of the ring current and disk current obtained during the test, respectively, and N is the collection rate on the Pt ring electrode, generally N = 0.37.
In the oxygen evolution reaction (OER) test, the working electrode is a glassy carbon electrode. The counter electrode is a graphite rod, and the reference electrode is a saturated Hg/HgO electrode. The LSV is tested in 1 M KOH (scan rate of 5 mV s−1).
2.5 MEA preparation and fuel cell test
The single fuel cell performance of the cathode catalysts was evaluated in PEMFCs. Before the fuel cell test, the membrane electrode assembly (MEA) was prepared using the following method. First, the calculated Fe–N/MC catalyst, isopropanol, and 5 wt% Nafion ionomer solution (DuPont, USA) were ultrasonically mixed for 1 h. Then, the resulting ink-like slurry was sprayed on one side of a pretreated sulfonic acid resin membrane (Dongyue, DF260) as the cathode using the method of catalyst sprayed membrane. The anode catalyst ink was prepared by the same method using commercial Pt/C (57.7 wt% Pt, TKK) and sprayed on the other side of the membrane. The final weight ratios of dry Nafion to cathode and anode catalyst were 1
:
2 and 1
:
2.5, respectively. The catalyst loadings at the cathode were 4 mg cm−2, and the Pt loading at the anode was 0.1 mg cm−2. A single fuel cell with an area of 4.0 cm2 was assembled by the as-prepared MEAs and gas diffusion layers (GDL) on both sides (SGL, 29BC). Fuel cell polarization plots were recorded using fuel cell test stations (Type, Nanjing). The fuel cell backpressure on both sides was 30 psi, and the cell temperature was fixed at 70 °C. The inlet H2 and O2 were humidified at 70 °C, and kept at flow rates of 400 mL min−1 and 600 mL min−1, respectively.
2.6 Zn–air battery performance test
All Zn–air battery tests were performed at room temperature on the Ivium Station workstation. LSV was performed to record the charge and discharge polarization curve, and the scan rate was fixed at 10 mV s−1.
Preparation of the air cathode: 4 mg of the catalyst was dissolved in 1 mL of ethanol, then dropped into 11 μL of PTFE solution (6 wt%), and sonicated for 30 minutes to form a uniform suspension. The catalyst suspension was then spread uniformly on the side of the carbon paper without the microporous layer, with a loading of approximately 1 mg cm−2. After the catalyst solvent evaporated, the obtained electrode could be prepared for the Zn–air battery assembly and further testing.
3. Results and discussion
As depicted in Fig. 1, the UIO-66 was first doped with ferrocene. Thus, we first performed FT-IR and XRD characterizations to assess the structure alteration upon the ferrocene loading. Fig. 2a compares the FT-IR spectra between different synthesized samples. The ferrocene holds a featured peak at 1650 cm−1, characteristic of the metal and benzene ring C
C skeleton vibration,48,49 at which the UIO-66 has a relatively weak shoulder peak. Upon the loading of FeCp, the FeCp@UIO-66 presents an enhanced peak at the same position, indicating the successful loading of ferrocene on UIO-66. The corresponding XRD (Fig. 2b) shows a group of similar peaks assigned to the typical pattern of UIO-66 crystallite between the two samples, suggesting little change in the crystallite structure upon the FeCp loading.
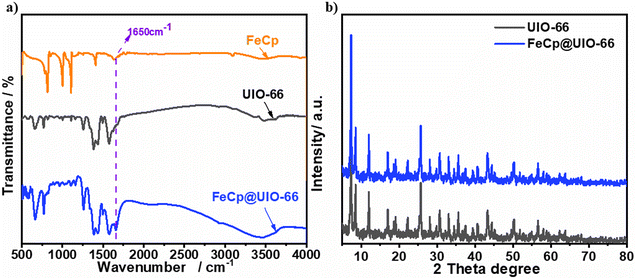 |
| Fig. 2 (a) FTIR spectra and (b) XRD patterns of various samples. | |
After undergoing carbonization at 950 °C, these UIO-66-based compounds were transformed into carbon-based composites. Without acid leaching, all three samples exhibit characteristic diffraction peaks of ZrO2 after the first pyrolysis, as shown in Fig. 3a of the XRD pattern. This is because the UIO-66 belongs to the typical MOF that includes zirconium nod ions and organic linker. At the same time, a couple of peaks assigned to the metallic Fe and Fe3C species appear on both the Fe–N/C-ref and Fe–N/MC catalysts. In contrast, the intensity of the Fe species becomes weaker on Fe–N/MC than that on Fe–N/C-ref, indicating that the introduction of g-C3N4 could prevent the agglomeration of iron and promote the anchoring of Fe to form the Fe–NC species. Eliminating the residual Zr compounds that are inactive for catalysis can improve the accessibility of the Fe–N real active sites, so the catalysts were treated by acid leaching and followed the second pyrolysis. As shown in Fig. 3b, the UIO-66, Fe–N/C-ref, and Fe–N/MC have a broad peak at around 26°, assigned to the (002) plane of graphitic carbon,50,51 where the Fe–N/MC has the highest graphitic degree of all. In the corresponding Raman spectra, the defects in the sample can be assessed by the intensity ratio between the D and G bands.52,53 The ID/IG (Fig. 3c) of Fe–N/MC is 1.09, which is lower than that of Fe–N/C-ref (1.19) and UIO (1.16). These results suggested the highest graphitization of Fe–N/MC, which was consistent with the XRD results. It has been reported that enhancing the graphitization degree of the catalysts in the appropriate range can effectively improve the durability of the catalysts.54,55
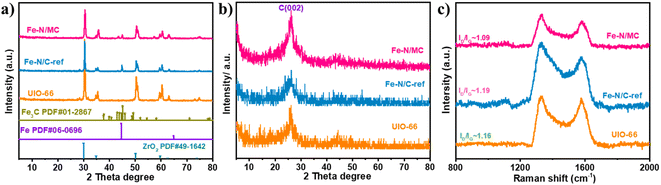 |
| Fig. 3 (a) XRD patterns of UIO, Fe–N/C-ref, Fe–N/MC without acid leaching after the first pyrolysis; (b) and (c) XRD patterns and Raman spectra of UIO, Fe–N/C-ref, Fe–N/MC. | |
Fig. 4a shows the N2 isothermal adsorption/desorption plots to characterize the samples' specific surface areas and pore structures. UIO-66 presents two steep adsorption regions; one is at p/p0 < 0.1, raised by the micropores. The other occurred at p/p0 > 0.9, which is attributable to the meso–macropores caused by inter-particles. Moreover, FeCp@UIO-66 has adsorption characteristics similar to those of UIO-66 except for some decrease in micropores, which can be related to the filling of the micropores by the FeCp molecules. For the Fe–N/MC, besides the micropores and inter-particle porosity, the Fe–N/MC fascinatingly observed a prominent increase in mesopore (2–10 nm) volume, as shown in Fig. 4b and c. This demonstrates that, while preserving its parent porosity of UIO-66, the Fe–N/MC remarkably also improves mesoporosity. As a result, the Fe–N/MC catalysts have a comparable high surface area (625 m2 g−1). The rising mesoporosity induced by the introduction of g-C3N4 can predicate the enhanced accessibility of the three-phase active site that promotes its electrochemical activity in PEMFC.26
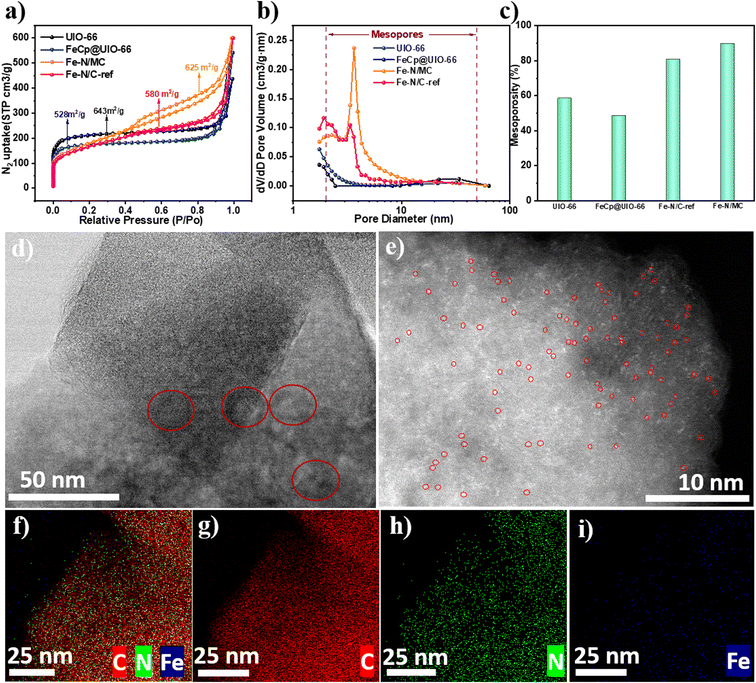 |
| Fig. 4 (a) N2 adsorption–desorption isotherms of UIO-66, FeCp@UIO-66, Fe–N/MC, and Fe–N/C-ref, (b) and their corresponding pore size distribution curves and (c) mesoporosity histograms. (d) TEM images of Fe–N/MC; (e and f) HAADF-STEM image of Fe–N/MC, and its corresponding EDS elemental mapping analysis images of (g) carbon (red), (h) nitrogen (green), and (i) iron (blue). | |
Fig. S1† shows the scanning electron microscopy (SEM) of the samples. Fe–N/MC catalysts maintain their octahedra morphology with a uniform particle size of 300 nm.46 Nevertheless, the reference catalysts prepared in the absence of g-C3N4 cannot maintain the octahedral structure after pyrolysis, which suggests that g-C3N4 effectively prevents organic skeleton contraction and metal agglomeration during pyrolysis, allowing the octahedral structure to be maintained.27,45 To further investigate the micro-structure of the catalysts, we performed TEM analysis for Fe–N/MC, as shown in Fig. 4d. The wormhole-like mesoporosity (circled in red) can be seen in these carbonized samples, which would be beneficial for oxygen and electrolyte diffusion.56 Not only that, but we also cannot observe Fe nanoparticles in the TEM and HADD-STEM images, and found the distribution of monoatomic Fe in Fig. 4d and e. This indicated that the high dispersion of Fe–NX active sites after g-C3N4 doping could be precisely controlled by the gas-phase adsorption strategy.44 In addition, TEM mapping (Fig. 4f–i) showed that Fe and N were uniformly dispersed in the doped carbon framework.
Fig. 5a–c and S2† show the XPS spectra of the UIO-66, Fe–N/C-ref, and Fe–N/MC samples. The N spectra can be fitted into various species by deconvoluting the XPS spectra. It is clear that the Fe–N/MC has a high nitrogen content of 2.12 at%, overwhelming the other two samples (Table S1†). This proves that the added g-C3N4 can promote the N enrichment. Furthermore, Fe–N/MC gives rise to more pyridinic nitrogen,28 with an increase of the pyridine-N content from 11.44 at% on Fe–N/C-ref to 26.06 at% on Fe–N/MC (Fig. 5d and Table S2†). This is beneficial to the ORR.16–18,53 Numerous studies have recognized that the nitrogen in the Fe–NX moieties originates from pyridinic N during high-temperature of pyrolysis.57,58 Thus, the g-C3N4-induced enrichment of pyridine-N promotes the generation of Fe–NX ensembles, enhancing the oxygen adsorption and promoting catalytic ORR.59
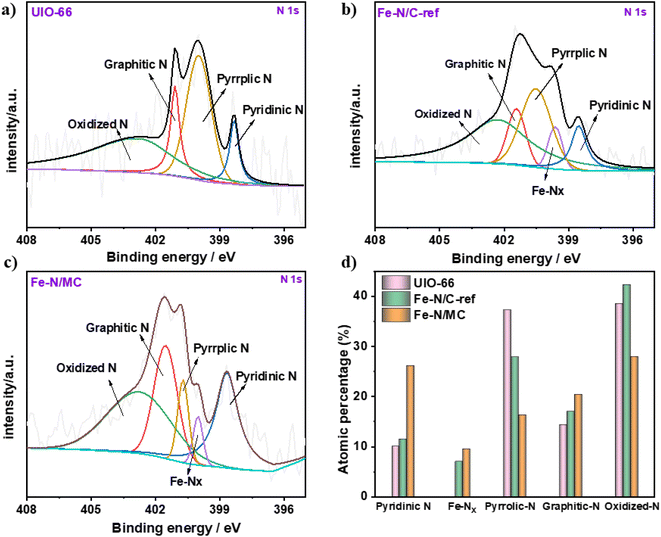 |
| Fig. 5 (a) N 1s XPS spectra of UIO-66; (b) N 1s XPS spectra of Fe–N/C-ref; (c) N 1s XPS spectra of Fe–N/MC; (d) fraction of the different N species present in UIO, Fe–N/C-ref, and Fe–N/MC. | |
The ORR activity of Fe–N/MC was evaluated in alkaline and acidic solutions by linear sweep voltammetry in the rotating ring disk electrode. In an O2-saturated solution, the CV curves for Fe–N/MC showed a well-defined cathodic peak at 0.79 V in 0.1 M HClO4 (Fig. S3a†) and 0.89 V in 0.1 M KOH (Fig. S3b†), revealing the excellent electrocatalytic activity of Fe–N/MC in both electrolytes. Fig. 6a and c show the ORR polarization curves of the catalysts in O2-saturated 0.1 M HClO4 and 0.1 M KOH solutions. Unsurprisingly, the introduction of g-C3N4 in the Fe–N/MC catalyst could greatly improve the ORR performance in both alkaline and acidic media. In contrast, the UIO-66 and Fe–N/C-ref catalysts exhibited relatively poor electrocatalytic activity compared to that of the Fe–N/MC catalysts, with lower half-wave potentials of 0.7 V and 0.8 V in acidic and basic environments, respectively. The ORR activity enhancement of Fe–N/MC may be due to the increase of three-phase active sites after the introduction of g-C3N4 and the improvement of the electron transfer (Tables S3 and S4†). Fig. S4† shows the ORR LSVs of FeCp and g-C3N4-derived Fe-NCNTs, with half-wave potentials of 0.79 and 0.67 V in 0.1 M KOH and 0.1 M HClO4 solutions, respectively, much lower than Fe–N/MC. This further proves that the enhanced intrinsic activity of Fe–N/MC is attributed to the increase of the three-phase active sites and their hierarchical structure. We also investigated the different doping amounts of FeCp on the catalyst activity in Fig. S5.† From Fig. S5,† it revealed that the catalyst attained the best ORR activity when the ratio of FeCp to UIO-66 is 1.5
:
1. On the one hand, the high loading of FeCp will further etch the UIO-66-derived mesoporous carbon. On the other hand, it will lead to a more severe agglomeration of the active sites. Fig. S6† shows the result of the Kentucky–Levich analysis. It can be seen that the electron transfer number of Fe–N/MC in acidic and alkaline electrolytes was 3.89 (Fig. S6b†) and 3.97 (Fig. S6d†), respectively, indicating that Fe–N/MC dominated a four-electron pathway during the ORR process.
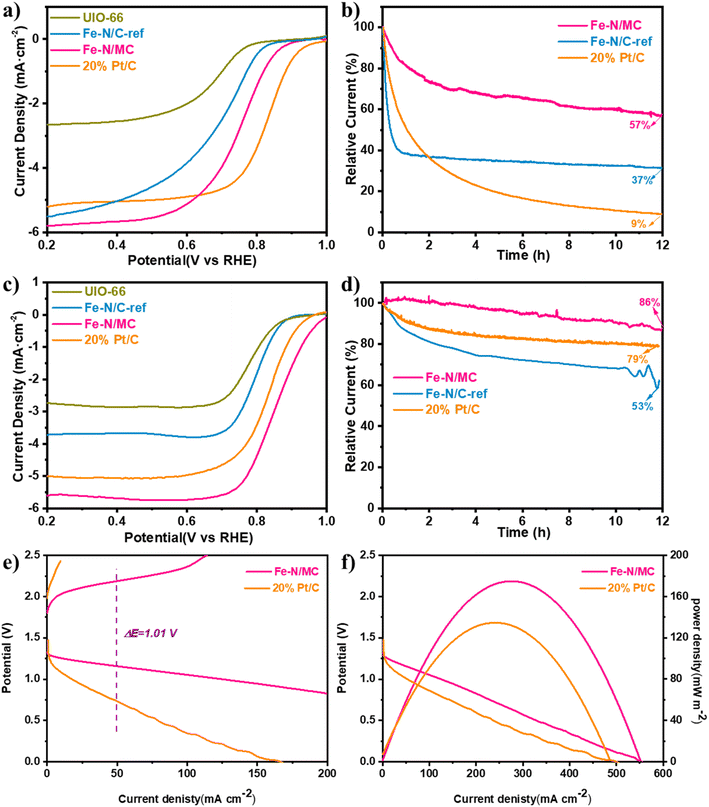 |
| Fig. 6 LSV curves of UIO, Fe–N/C-ref, Fe–N/MC, Pt/C at O2-saturation (a) 0.1 M HClO4 and (c) 0.1 M KOH (rpm: 1600 rpm); durability test results of the catalysts at O2-saturation (b) 0.1 M HClO4 and (d) 0.1 M KOH; (e) the corresponding power density curves are displaced polarization curves of Fe–N/MC and 20% Pt/C; (f) charge and discharge polarizations of Fe–N/MC and 20% Pt/C. | |
In addition, Fe–N/MC exhibited excellent stability in both electrolytes (Fig. 6b and d), which was evaluated via elongated chronopotentiometry measurement. After 12 h long discharge, the current density of Fe–N/MC in 0.1 M KOH solution decayed by only 14%, while Fe–N/C-ref without g-C3N4 doping in the catalyst showed a 44% drop in current density compared to the initial performance. In 0.1 M HClO4 solution, the current density of Fe–N/MC was attenuated by 43% after 12 h testing, which was less decay compared with that of Fe–N/C-ref (63%). The stability enhancement of Fe–N/MC may be due to the anchoring of the Fe atoms caused by introducing g-C3N4, which is favorable to prevent the oxidation of the Fe active sites, and the higher graphitization degree of catalyst can enhance the corrosion resistance of carbon. The above view was confirmed by comparing the CV curves of Fe–N/MC before and after durability (Fig. S7†). We found that the forward reduction peak potential (Ered) of the as-prepared catalysts did not change in both acid and alkaline electrolytes, indicating that the material was not oxidized to other intermediate valence states during the process of oxygen reduction. The OER performance was measured in a 1.0 M KOH solution. As shown in Fig. S8a and b,† Fe–N/MC catalysts have a low overpotential (η = 320 mV) at 10 mA cm−2 and a small Tafel slope (160 mV dec−1), indicating that the Fe–N/MC catalysts possess faster oxygen release reaction kinetics.
Due to its outstanding ORR and OER performance in alkaline conditions, we constructed assembled ZAB equipped with Fe–N/MC as an air cathode catalyst to expand its potential applications. In Fig. S9,† the open-circuit voltage of the ZAB constructed with Fe–N/MC was 1.44 V, which was higher than that of 20% Pt/C (1.42 V). Additionally, the battery has no remarkable decay after 15
000 s of standing, indicating that the Fe–N/MC catalysts show significant catalytic activity and better stability. Fig. 6e shows the charging and discharging polarization curves. Compared to 20% Pt/C, the charge/discharge voltage gap of the ZAB composed of Fe–N/MC was smaller (ΔE = 1.01 V), indicating the superior charge/discharge performance of Fe–N/MC. Meanwhile, Fig. 6f shows the discharge and power density curves of the ZAB. The peak power density of Fe–N/MC was 175.94 mW cm−2, which was substantially higher than that of 20% Pt/C (134.95 mW cm−2).
In order to evaluate the actual performance of the Fe–N/MC catalyst, we applied the catalysts in the cathode of H2–O2 PEMFC (Fig. 7a). Because of the excellent ORR activity of Fe–N/MC, the open-circuit voltage of MEA was as high as 0.94 V, the current density was 615 mA cm−2 at 0.7 V, and the peak power density could reach 1.15 W cm−2. More importantly, we found that its performance at low current density is comparable to that of commercial Pt/C catalysts, but better than Fe–N/C-ref catalysts. This is mainly due to the increase of the Fe–NX active site in the catalyst after N doping. So far, Fe–N/MC was one of the best non-precious metal catalysts applied in H2–O2 PEMFC (Table S5†). Notably, the maximum power density of the Fe–N/C-ref catalyst without g-C3N4 doping in MEA was only 715 mW cm−2, which was lower than that of the Fe–N/MC catalyst. The distinct performance between Fe–N/MC MEA and Fe–N/C-ref MEA highlights the key role of g-C3N4 in promoting the selective formation of the Fe-NX moieties.44 We also investigated the durability of the catalyst in PEMFC by 24 h discharging. The current density loss of Fe–N/MC was 42.3% (Fig. 7b) at 0.7 V. The retention rate of 57.6% was greater than that of the catalyst prepared without g-C3N4 doping. We speculate that the stability improvement is due to the addition of g-C3N4 as follows: (1) the introduction of g-C3N4 enhances the graphitization of the catalyst; (2) g-C3N4 could promote the anchoring of the Fe atoms to slow down the loss of active sites; (3) the active sites in the three-phase boundary are increased by g-C3N4 doping, and the ORR activity of the catalyst is enhanced, which could also reduce the production of H2O2.
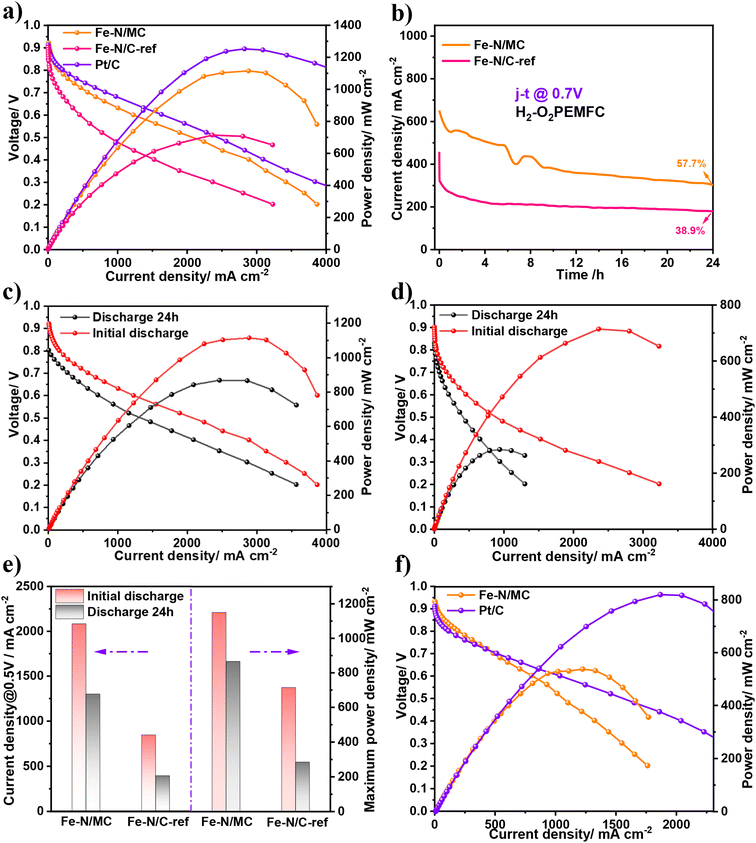 |
| Fig. 7 (a) Polarization curves and power density plots of H2–O2 PEMFC; (b) durability test of Fe–N/MC and Fe–N/C-ref in an H2–O2 fuel cell. Polarization curve before and after endurance test of (c) Fe–N/MC, (d) Fe–N/C-ref; (e) current density at 0.5 V and maximum power density histogram of Fe–N/MC and Fe–N/C-ref as cathode catalysts (initial and after 24 h discharge); (f) polarization curves and power density plots of H2–air PEMFC. | |
Based on the above speculation, we measured the accurate total Fe loading and the solubility of the iron active species with the two catalysts separately by ICP-OES (Table S6†). It was found that the dissolution of Fe is up to 28.3% after dispersing the Fe–N/C-ref sample in 0.5 M H2SO4 solution for 24 h, which was much higher than that of Fe–N/MC (12.7%). So, the dissolution of Fe ions may be one of the essential reasons for the decay of the catalysts' performance. On the other hand, the presence of hydrogen peroxide has a tremendous negative impact on the stability of catalysts. The H2O2 produced by the carbon-based catalyst during the ORR process will attack not only the Nafion binder, but also the active sites of the catalyst, accelerating the oxidation of carbon and leading to severe carbon corrosion.60 In order to analyze the amount of hydrogen peroxide produced during the ORR process, the H2O2 yield of the catalyst was effectively characterized by the rotating disk ring electrode (RRDE) test (Fig. S10†). The results clearly show that the H2O2 yield of the Fe–N/MC catalyst was nearly 1.9%, which was slightly higher than that of Pt/C (0.8%). However, the H2O2 yield of the Fe–N/C-ref catalyst was up to 9.6%. The results indicated that the substantial reduction of active sites and the intensification of side reaction rates during ORR for Fe–N/C-ref catalysts, leading to relatively high H2O2 production, might be one of the reasons affecting its stability.
Finally, to evaluate the performance recoverability of Fe–N/MC MEA, the polarization test with several cycles of MEA was measured strictly after long-period discharge (Fig. S11†). We found that after ten cycles of repeated discharge from open circuit voltage to 0.2 V, the Fe–N/MC MEA performance could be gradually recovered to nearly 80% compared with its performance at the beginning of life (Fig. 7c). This phenomenon may be associated with catalyst flooding, which originated from the thicker and hydrophilic catalysts layer after long discharge at high current density and causes a gas diffusion obstacle in the cathode.61 Meanwhile, we surprisingly found that the OCV for Fe–N/MC MEA and Fe–N/C-ref MEA dropped to 0.82 V and 0.8 V, respectively. Such a decrease in OCV can be assigned to active site loss or destruction. After 10 cycles of repeated IV curves, the peak power density could still be maintained at 0.866 W cm−2 for Fe–N/MC, much better than that of Fe–N/C-ref (Fig. 7d). We assume that the in situ introduction of g-C3N4 could anchor more Fe atoms and resist the loss of the Fe active species effectively. The comparative Fe loading from the ICP results verifies this stabilized Fe species.
The performance of H2–air PEMFC with Fe–N/MC as a cathode catalyst is meaningful for the real application. From the result in Fig. 7e, we can see that the current density was 418 mA cm−2 at the voltage of 0.7 V, and the peak power density was 0.53 W cm−2. The MEA with Fe–N/MC catalysts exhibited comparable performance to MEA with Pt/C in the electrochemical reaction region. However, in the region of ohmic polarization area, the performance of MEA with the Fe–N/MC catalyst is lower than that of MEA with the Pt/C catalyst. This is mainly due to the high ohmic resistance caused by the thick catalysts layer, which slowed down the ORR catalytic reaction efficiency. In the concentration region, the performance gap between Fe–N/MC and Pt/C is caused by the thicker and more hydrophilic catalyst layer, which will hinder the mass transfer process.
4. Conclusion
In summary, our work has demonstrated a feasible strategy of co-carbonization of Fe-loaded UIO-66/g-C3N4 hybrid to attain an efficient mesoporous carbon (MC) encapsulated Fe–N ensemble, Fe–N/MC catalyst for cathode catalyst in PEMFC. The introduction of g-C3N4 served as a binary functionality during the synthesis route. One affords the N species that is covalent with Fe to generate the Fe–N active sites, and the other offers carbon precursors to yield mesoporosity within the carbon matrix. While the optimized catalyst applied in the cathode of H2–O2 PEMFC, the current density can reach up to 615 mA cm−2 at 0.7 V. Furthermore, the peak power density is up to 1.15 W cm−2, and its power density is only decayed by 21.8% after 24 h of discharge. Moreover, a high-power density of 0.53 W cm−2 can be achieved in the condition of H2–air. Meanwhile, by observing the causes of the Fe/N/C catalyst decay mentioned above, it was found that the leaching of Fe from the catalyst was the main reason for the poor stability of Fe–N/C catalysts. Furthermore, the encapsulation of the active center in the N-doped carbon matrix effectively prevented the leaching of Fe from the active center. This work may provide a new path to synthesize non-precious metal catalysts with high performance and good stability for PEMFC and metal–air batteries.
Conflicts of interest
There are no conflicts to declare.
Acknowledgements
We gratefully acknowledge the financial support from the National Natural Science Foundation of China (21905055) and Guangzhou Key Laboratory of Clean Transportation Energy and Chemistry.
References
- M. H. Shao, Q. W. Chang, J. P. Dodelet and R. Chenitz, Recent Advances in Electrocatalysts for Oxygen Reduction Reaction, Chem. Rev., 2016, 116, 3594–3657 CrossRef CAS.
- C. Z. Zhu, H. Li, S. F. Fu, D. Du and Y. H. Lin, Highly efficient non-precious metal catalysts towards oxygen reduction reaction based on three-dimensional porous carbon nanostructures, Chem. Soc. Rev., 2016, 45, 517–531 RSC.
- S. M. Zhang, M. H. Chen, X. Zhao, J. L. Cai, W. Yan, J. C. Yen, S. L. Chen, Y. Yu and J. J. Zhang, Advanced Non carbon Materials as Catalyst Supports and Non-noble Electrocatalysts for Fuel Cells and Metal–Air Batteries, Electrochem. Energy Rev., 2021, 4, 336–381 CrossRef CAS.
- C. Chen, X. Deng, Y. Deng, L. An, Y. Deng, Y. Zheng, D. Dang and X. Yang, A bi-functional Co–Ni layered double hydroxide three-dimensional porous array electrode derived from ZIF-L(Co)@ZIF-L(Co, Ni) for oxygen evolution reaction and supercapacitors, Int. J. Hydrogen Energy, 2022, 47, 14896–14905 CrossRef CAS.
- H. Wang, S. Hua, R. Lin, S. Liu, X. Cai, W. Ji and J. Tian, Ionomer distribution control by self-assembled monolayers for high-power and low Pt-loaded proton exchange membrane fuel cells, J. Power Sources, 2022, 542, 231793 CrossRef CAS.
- Z.-H. Zhu, B. Yu, W. Sun, S. Chen, Y. Wang, X. Li and L.-P. Lv, Triazine organic framework derived Fe single-atom bifunctional electrocatalyst for high performance zinc air batteries, J. Power Sources, 2022, 542, 231583 CrossRef CAS.
- J. B. Zhang, C. F. Zhang, W. Li, Q. Guo, H. C. Gao, Y. You, Y. T. Li, Z. M. Cui, K. C. Jiang, H. J. Long, D. W. Zhang and S. Xin, Nitrogen-Doped Perovskite as a Bifunctional Cathode Catalyst for Rechargeable Lithium Oxygen Batteries, ACS Appl. Mater. Interfaces, 2018, 10, 5543–5550 CrossRef CAS PubMed.
- F. Dong, M. Wu, Z. Chen, X. Liu, G. Zhang, J. Qiao and S. Sun, Atomically Dispersed Transition Metal–Nitrogen–Carbon Bifunctional Oxygen Electrocatalysts for Zinc–Air Batteries: Recent Advances and Future Perspectives, Nano-Micro Lett., 2021, 14, 36 CrossRef.
- V. R. Stamenkovic, B. Fowler, B. S. Mun, G. F. Wang, P. N. Ross, C. A. Lucas and N. M. Markovic, Improved oxygen reduction activity on Pt3Ni(111) via increased surface site availability, Science, 2007, 315, 493–497 CrossRef CAS PubMed.
- X. G. Fu, N. Li, B. H. Ren, G. P. Jiang, Y. R. Liu, F. M. Hassan, D. Su, J. B. Zhu, L. Yang, Z. Y. Bai, Z. P. Cano, A. P. Yu and Z. W. Chen, Tailoring FeN4 Sites with Edge Enrichment for Boosted Oxygen Reduction Performance in Proton Exchange Membrane Fuel Cell, Adv. Energy Mater., 2019, 9, 1803737 CrossRef.
- W. H. Deng, T. J. Wu, Y. F. Wu, H. T. Zheng, G. Li, M. X. Yang, X. Q. Zou, Y. S. Bai, Y. C. Yang, M. J. Jing and X. Y. Wang, Single atomic Fe-pyridine N catalyst with dense active sites improve bifunctional electrocatalyst activity for rechargeable and flexible Zn–air batteries, J. Mater. Chem. A, 2022, 10, 20993–21003 RSC.
- Z. W. Chen, D. Higgins, A. P. Yu, L. Zhang and J. J. Zhang, A review on non-precious metal electrocatalysts for PEM fuel cells, Energy Environ. Sci., 2011, 4, 3167–3192 RSC.
- L. Liu, X. F. Yang, N. Ma, H. T. Liu, Y. Z. Xia, C. M. Chen, D. J. Yang and X. D. Yao, Scalable and Cost-Effective Synthesis of Highly Efficient Fe2N-Based Oxygen Reduction Catalyst Derived from Seaweed Biomass, Small, 2016, 12, 1295–1301 CrossRef CAS PubMed.
- X. G. Fu, G. P. Jiang, G. B. Wen, R. Gao, S. Li, M. Li, J. B. Zhu, Y. Zheng, Z. Q. Li, Y. F. Hu, L. Yang, Z. Y. Bai, A. P. Yu and Z. W. Chen, Densely accessible Fe–NX active sites decorated mesoporous-carbon-spheres for oxygen reduction towards high performance aluminum–air flow batteries, Appl. Catal., B, 2021, 293, 120176 CrossRef CAS.
- Q. Y. Zhou, Z. Zhang, J. J. Cai, B. Liu, Y. L. Zhang, X. F. Gong, X. L. Sui, A. P. Yu, L. Zhao, Z. B. Wang and Z. W. Chen, Template-guided synthesis of Co nanoparticles embedded in hollow nitrogen doped carbon tubes as a highly efficient catalyst for rechargeable Zn–air batteries, Nano Energy, 2020, 71, 104592 CrossRef CAS.
- F. Jaouen, E. Proietti, M. Lefevre, R. Chenitz, J. P. Dodelet, G. Wu, H. T. Chung, C. M. Johnston and P. Zelenay, Recent advances in non-precious metal catalysis for oxygen–reduction reaction in polymer electrolyte fuel cells, Energy Environ. Sci., 2011, 4, 114–130 RSC.
- J. Li, Y. J. Song, G. X. Zhang, H. Y. Liu, Y. R. Wang, S. H. Sun and X. W. Guo, Pyrolysis of Self-Assembled Iron Porphyrin on Carbon Black as Core/Shell Structured Electrocatalysts for Highly Efficient Oxygen Reduction in Both Alkaline and Acidic Medium, Adv. Funct. Mater., 2017, 27, 1604356 CrossRef.
- L. Lin, Z. K. Yang, Y. F. Jiang and A. W. Xu, Nonprecious Bimetallic (Fe,Mo)-N/C Catalyst for Efficient Oxygen Reduction Reaction, ACS Catal., 2016, 6, 4449–4454 CrossRef CAS.
- M. Liu, L. Wang, L. Zhang, Y. Zhao, K. Chen, Y. Li, X. Yang, L. Zhao, S. Sun and J. Zhang,
In Situ Silica Xerogel Assisted Facile Synthesis of Fe–N–C Catalysts with Dense Fe–NX Active Sites for Efficient Oxygen Reduction, Small, 2022, 18, e2104934 CrossRef PubMed.
- W. Z. Cheng, J. L. Liang, H. B. Yin, Y. J. Wang, W. F. Yan and J. N. Zhang, Bifunctional iron-phthalocyanine metal–organic framework catalyst for ORR, OER and rechargeable zinc–air battery, Rare Met., 2020, 39, 815–823 CrossRef CAS.
- M. Wu, G. Zhang, Y. Hu, J. Wang, T. Sun, T. Regier, J. Qiao and S. Sun, Graphitic-shell encapsulated FeNi alloy/nitride nanocrystals on biomass-derived N-doped carbon as an efficient electrocatalyst for rechargeable Zn–air battery, Carbon Energy, 2020, 3, 176–187 CrossRef.
- X. Deng, X. Gu, Y. Deng, Z. Jiang, W. Chen, D. Dang, W. Lin and B. Chi, Boosting the activity and stability via Co nanoparticles and MoC synergistic catalysis to construct a bifunctional electrocatalyst for high-performance and long-life rechargeable zinc–air batteries, Nanoscale, 2022, 13192–13203 RSC.
- Q. L. Wei, G. X. Zhang, X. H. Yang, R. Chenitz, D. Barham, L. J. Yang, S. Y. Ye, S. Knights and S. H. Sun, 3D Porous Fe/N/C Spherical Nanostructures as High-Performance Electrocatalysts for Oxygen Reduction in Both Alkaline and Acidic Media, ACS Appl. Mater. Interfaces, 2017, 9, 36944–36954 CrossRef CAS PubMed.
- X. Li, X. Yang, L. Liu, H. Zhao, Y. Li, H. Zhu, Y. Chen, S. Guo, Y. Liu, Q. Tan and G. Wu, Chemical Vapor Deposition for N/S-Doped Single Fe Site Catalysts for the Oxygen Reduction in Direct Methanol Fuel Cells, ACS Catal., 2021, 11, 7450–7459 CrossRef CAS.
- X. G. Fu, J. Y. Choi, P. Zamani, G. P. Jiang, M. A. Hoque, F. M. Hassan and Z. W. Chen, Co–N Decorated Hierarchically Porous Graphene Aerogel for Efficient Oxygen Reduction Reaction in Acid, ACS Appl. Mater. Interfaces, 2016, 8, 6488–6495 CrossRef CAS PubMed.
- Y. He, H. Guo, S. Hwang, X. Yang, Z. He, J. Braaten, S. Karakalos, W. Shan, M. Wang, H. Zhou, Z. Feng, K. L. More, G. Wang, D. Su, D. A. Cullen, L. Fei, S. Litster and G. Wu, Single Cobalt Sites Dispersed in Hierarchically Porous Nanofiber Networks for Durable and High-Power PGM-Free Cathodes in Fuel Cells, Adv. Mater., 2020, 32, 2003577 CrossRef CAS PubMed.
- Y. J. Deng, B. Chi, X. L. Tian, Z. M. Cui, E. S. Liu, Q. Y. Jia, W. J. Fan, G. H. Wang, D. Dang, M. S. Li, K. T. Zang, J. Luo, Y. F. Hu, S. J. Liao, X. L. Sun and S. Mukerjee, g-C3N4 promoted MOF derived hollow carbon nanopolyhedra doped with high density/fraction of single Fe atoms as an ultra-high performance non-precious catalyst towards acidic ORR and PEM fuel cells, J. Mater. Chem. A, 2019, 7, 5020–5030 RSC.
- Y. Y. Li, P. Y. Zhang, L. Y. Wan, Y. P. Zheng, X. M. Qu, H. K. Zhang, Y. S. Wang, K. Zaghib, J. Y. Yuan, S. H. Sun, Y. C. Wang, Z. Y. Zhou and S. G. Sun, A General Carboxylate-Assisted Approach to Boost the ORR Performance of ZIF-Derived Fe/N/C Catalysts for Proton Exchange Membrane Fuel Cells, Adv. Funct. Mater., 2021, 31, 2009645 CrossRef CAS.
- N. Yang, L. L. Peng, L. Li, J. Li, Q. Liao, M. H. Shao and Z. D. Wei, Theoretically probing the possible degradation mechanisms of an FeNC catalyst during the oxygen reduction reaction, Chem. Sci., 2021, 12, 12476–12484 RSC.
- R. Chenitz, U. I. Kramm, M. Lefevre, V. Glibin, G. X. Zhang, S. H. Sun and J. P. Dodelet, A specific demetalation of Fe–N4 catalytic sites in the micropores of NC_Ar + NH3 is at the origin of the initial activity loss of the highly active Fe/N/C catalyst used for the reduction of oxygen in PEM fuel cells, Energy Environ. Sci., 2018, 11, 365–382 RSC.
- D. H. Deng, L. Yu, X. Q. Chen, G. X. Wang, L. Jin, X. L. Pan, J. Deng, G. Q. Sun and X. H. Bao, Iron Encapsulated within Pod-like Carbon Nanotubes for Oxygen Reduction Reaction, Angew. Chem., Int. Ed., 2013, 52, 371–375 CrossRef CAS PubMed.
- L. Shi, X. Lin, F. Liu, Y. Long, R. Cheng, C. Tan, L. Yang, C. Hu, S. Zhao and D. Liu, Geometrically Deformed Iron-Based Single-Atom Catalysts for High-Performance Acidic Proton Exchange Membrane Fuel Cells, ACS Catal., 2022, 12, 5397–5406 CrossRef CAS.
- X. Xie, L. Peng, H. Yang, G. I. N. Waterhouse, L. Shang and T. Zhang, MIL-101-Derived Mesoporous Carbon Supporting Highly Exposed Fe Single-Atom Sites as Efficient Oxygen Reduction Reaction Catalysts, Adv. Mater., 2021, 33, e2101038 CrossRef PubMed.
- H. L. Zhang, H. Z. Guang, R. P. Li, X. Y. Lu, H. Xu, D. Wang, L. H. Xiao, J. Q. Zhang, M. Z. An and P. X. Yang, Doping engineering: modulating the intrinsic activity of bifunctional carbon-based oxygen electrocatalysts for high-performance zinc–air batteries, J. Mater. Chem. A, 2022, 10, 21797–21815 RSC.
- Y. Mu, T. T. Wang, J. Zhang, C. G. Meng, Y. F. Zhang and Z. K. Kou, Single-Atom Catalysts: Advances and Challenges in Metal–Support Interactions for Enhanced Electrocatalysis, Electrochem. Energy Rev., 2022, 5, 145–186 CrossRef CAS.
- R. X. Wang, X. D. Yang, L. Y. Wan, B. A. Lu, L. F. Shen, Y. Y. Li, S. G. Sun and Z. Y. Zhou, Graphene-covered FePc as a model of the encapsulated type of catalyst for the oxygen reduction reaction, Electrochem. Commun., 2020, 112, 106670 CrossRef CAS.
- G. A. Ferrero, K. Preuss, A. Marinovic, A. B. Jorge, N. Mansor, D. J. L. Brett, A. B. Fuertes, M. Sevilla and M. M. Titirici, Fe–N-Doped Carbon Capsules with Outstanding Electrochemical Performance and Stability for the Oxygen Reduction Reaction in Both Acid and Alkaline Conditions, ACS Nano, 2016, 10, 5922–5932 CrossRef CAS PubMed.
- C. H. Choi, C. Baldizzone, G. Polymeros, E. Pizzutilo, O. Kasian, A. K. Schuppert, N. Ranjbar Sahraie, M.-T. Sougrati, K. J. Mayrhofer and F. Jaouen, Minimizing operando demetallation of Fe–NC electrocatalysts in acidic medium, ACS Catal., 2016, 6, 3136–3146 CrossRef CAS.
- C. X. Zhao, J. N. Liu, J. Wang, D. Ren, B. Q. Li and Q. Zhang, Recent advances of noble-metal-free bifunctional oxygen reduction and evolution electrocatalysts, Chem. Soc. Rev., 2021, 50, 7745–7778 RSC.
- Q. Wang, Y. Yang, F. Sun, G. Chen, J. Wang, L. Peng, W. T. Chen, L. Shang, J. Zhao, D. Sun-Waterhouse, T. Zhang and G. I. N. Waterhouse, Molten NaCl-Assisted Synthesis of Porous Fe–N–C Electrocatalysts with a High Density of Catalytically Accessible FeN4 Active Sites and Outstanding Oxygen Reduction Reaction Performance, Adv. Energy Mater., 2021, 11, 2100219 CrossRef CAS.
- L. Shen, M. Ma, F. Tu, Z. Zhao, Y. Xia, K. Goh, L. Zhao, Z. Wang and G. Shao, Recent advances in high-loading catalysts for low-temperature fuel cells: from nanoparticle to single atom, SusMat, 2021, 1, 569–592 CrossRef.
- J.-P. Dodelet, V. Glibin, G. Zhang, U. I. Kramm, R. Chenitz, F. Vidal, S. Sun and M. Dubois, Reply to the ‘Comment on “Non-PGM electrocatalysts for PEM fuel cells: effect of fluorination on the activity and stability of a highly active NC_Ar + NH3 catalyst”’ by Xi Yin, Edward F. Holby and Piotr Zelenay, Energy Environ. Sci., 2021, 14, 1034–1041 RSC.
- M. Shao, Q. Chang, J.-P. Dodelet and R. Chenitz, Recent advances in electrocatalysts for oxygen reduction reaction, Chem. Rev., 2016, 116, 3594–3657 CrossRef CAS PubMed.
- L. Zheng, Y. Y. Dong, B. Chi, Z. M. Cui, Y. J. Deng, X. D. Shi, L. Du and S. J. Liao, UIO-66-NH2-Derived Mesoporous Carbon Catalyst Co-Doped with Fe/N/S as Highly Efficient Cathode Catalyst for PEMFCs, Small, 2019, 15, 1803520 CrossRef PubMed.
- Z. Y. Wu, X. X. Xu, B. C. Hu, H. W. Liang, Y. Lin, L. F. Chen and S. H. Yu, Iron Carbide Nanoparticles Encapsulated in Mesoporous Fe–N-Doped Carbon Nanofibers for Efficient Electrocatalysis, Angew. Chem., Int. Ed., 2015, 54, 8179–8183 CrossRef CAS PubMed.
- A. C. Ferrari, S. E. Rodil and J. Robertson, Interpretation of infrared and Raman spectra of amorphous carbon nitrides, Phys. Rev. B, 2003, 67, 155306 CrossRef.
- J. Yang, H. Y. Sun, H. Y. Liang, H. X. Ji, L. Song, C. Gao and H. X. Xu, A Highly Efficient Metal-Free Oxygen Reduction Electrocatalyst Assembled from Carbon Nanotubes and Graphene, Adv. Mater., 2016, 28, 4606–4613 CrossRef CAS.
- Z. Guo, Y. Ma, Y. Zhao, Y. Song, S. Tang, Q. Wang and W. Li, Trimetallic ZIFs-derived porous carbon as bifunctional electrocatalyst for rechargeable Zn–air battery, J. Power Sources, 2022, 542, 231723 CrossRef CAS.
- G. Y. Ye, Q. He, S. Q. Liu, K. M. Zhao, Y. K. Su, W. W. Zhu, R. J. Huang and Z. He, Cage-confinement of gas-phase ferrocene in zeolitic imidazolate frameworks to synthesize high-loading and atomically dispersed Fe–N co-doped carbon for efficient oxygen reduction reaction, J. Mater. Chem. A, 2019, 7, 16508–16515 RSC.
- J. L. Shui, C. Chen, L. Grabstanowicz, D. Zhao and D. J. Liu, Highly efficient non-precious metal catalyst prepared with metal–organic framework in a continuous carbon nanofibrous network, Proc. Natl. Acad. Sci. U. S. A., 2015, 112, 10629–10634 CrossRef CAS.
- X. Deng, Z. Jiang, Y. Chen, D. Dang, Q. Liu, X. Wang and X. Yang, Renewable wood-derived hierarchical porous, N-doped carbon sheet as a robust self-supporting cathodic electrode for zinc–air batteries, Chin. Chem. Lett., 2022, 107389 Search PubMed.
- Q. Jia, N. Ramaswamy, U. Tylus, K. Strickland, J. Li, A. Serov, K. Artyushkova, P. Atanassov, J. Anibal, C. Gumeci, S. C. Barton, M.-T. Sougrati, F. Jaouen, B. Halevi and S. Mukerjee, Spectroscopic insights into the nature of active sites in iron–nitrogen–carbon electrocatalysts for oxygen reduction in acid, Nano Energy, 2016, 29, 65–82 CrossRef CAS.
- Y. J. Deng, Y. Y. Dong, G. H. Wang, K. L. Sun, X. D. Shi, L. Zheng, X. H. Li and S. J. Liao, Well-Defined ZIF-Derived Fe–N Codoped Carbon Nanoframes as Efficient Oxygen Reduction Catalysts, ACS Appl. Mater. Interfaces, 2017, 9, 9699–9709 CrossRef CAS PubMed.
- V. Prabhakaran, G. X. Wang, J. Parrondo and V. Ramani, Contribution of Electrocatalyst Support to PEM Oxidative Degradation in an Operating PEFC, J. Electrochem. Soc., 2016, 163, F1611–F1617 CrossRef CAS.
- A. A. Eissa, N. H. Kim and J. H. Lee, Rational design of a highly mesoporous Fe–N–C/Fe3C/C–S–C nanohybrid with dense active sites for superb electrocatalysis of oxygen reduction, J. Mater. Chem. A, 2020, 8, 23436–23454 RSC.
- J. Yang, F. J. Zhang, X. Wang, D. S. He, G. Wu, Q. H. Yang, X. Hong, Y. Wu and Y. D. Li, Porous Molybdenum Phosphide Nano-Octahedrons Derived from Confined Phosphorization in UIO-66 for Efficient Hydrogen Evolution, Angew. Chem., Int. Ed., 2016, 55, 12854–12858 CrossRef CAS PubMed.
- L. Lin, Q. Zhu and A. W. Xu, Noble-Metal-Free Fe–N/C Catalyst for Highly Efficient Oxygen Reduction Reaction under Both Alkaline and Acidic Conditions, J. Am. Chem. Soc., 2014, 136, 11027–11033 CrossRef CAS PubMed.
- V. Yarlagadda, N. Ramaswamy, R. S. Kukreja and S. Kumaraguru, Ordered mesoporous carbon supported fuel cell cathode catalyst for improved oxygen transport, J. Power Sources, 2022, 532, 231349 CrossRef CAS.
- Z. H. Li, M. F. Shao, L. Zhou, R. K. Zhang, C. Zhang, M. Wei, D. G. Evans and X. Duan, Directed Growth of Metal–Organic Frameworks and Their Derived Carbon-Based Network for Efficient Electrocatalytic Oxygen Reduction, Adv. Mater., 2016, 28, 2337–2344 CrossRef CAS PubMed.
- H. L. Jiang, Y. F. Yao, Y. H. Zhu, Y. Y. Liu, Y. H. Su, X. L. Yang and C. Z. Li, Iron Carbide Nanoparticles Encapsulated in Mesoporous Fe–N-Doped Graphene-Like Carbon Hybrids as Efficient Bifunctional Oxygen Electrocatalysts, ACS Appl. Mater. Interfaces, 2015, 7, 21511–21520 CrossRef CAS.
- Y. Kim, H. E. Bae, D. Lee, J. Kim, E. Lee, S. Oh, J.-H. Jang, Y.-H. Cho, M. Karuppannan and Y.-E. Sung, High-performance long-term driving proton exchange membrane fuel cell implemented with chemically ordered Pt-based alloy catalyst at ultra-low Pt loading, J. Power Sources, 2022, 533, 231378 CrossRef CAS.
|
This journal is © The Royal Society of Chemistry 2023 |
Click here to see how this site uses Cookies. View our privacy policy here.