DOI:
10.1039/D4MA00403E
(Paper)
Mater. Adv., 2024,
5, 5896-5902
Highly-robust nanoplate-shaped V2O5 as an efficient cathode material for aqueous zinc ion batteries
Received
18th April 2024
, Accepted 30th May 2024
First published on 31st May 2024
Abstract
The efficiency and performances of energy storage and conversion systems are highly dependent on the electrode performances, which have a direct impact on their functioning. The fabrication of electrode materials with novel nanostructures has a substantial positive impact on their electrochemical performances. Recently, two-dimensional nanomaterials have drawn a lot of attention due to their significant features, such as distinctive 2D-layered structure and infinite planar lengths as well as providing short routes for ion and electron transportation including large surface areas for additional adsorption sites. Herein, we have proposed a simple solvothermal synthesis for the fabrication of 2D nanoplates of a V2O5 cathode for rechargeable aqueous zinc-ion batteries. The obtained high electrochemical results confirmed the potency of the V2O5 nanoplate cathode for zinc ion batteries. Furthermore, the Zn2+ ion storage mechanism within the V2O5 crystal lattice is also discussed, which is based on the phase transition from pristine V2O5 to zinc pyrovanadate (ZnxV2O5·nH2O) during reversible Zn2+ (de)-intercalation in the open-structured hosts.
Introduction
In today's modern civilization, the concerns related to energy storage, conversion, and distribution are crucial. An energy-storage device is considered to be ideal if it possesses the vital features of high safety, environmental friendliness, low cost, high specific capacity, fast charge/discharge capability, and high gravimetric and volumetric energy densities.1–4 Lithium-ion batteries (LIBs) have garnered a lot of attention in recent years due to their numerous applications from small mobile gadgets to hybrid and electric cars. Despite the high energy and power density of LIBs, their wide-scale implementation is constrained by the safety risks caused by flammable organic electrolytes. In addition, the limited Li resources are also a major concern, which may restrict the further use of LIBs.5–8 Recently, the rechargeable aqueous zinc-ion batteries have shown potential to be used as an alternative due to the low cost and high abundance of metallic zinc in the earth's crust (∼2 USD per kg and ∼75 ppm), excellent safety characteristics and low equilibrium redox potential (−0.76 V vs. SCE) of the Zn electrode, and easy assembling procedures.9–14 Similar to LIBs, the chemistry of aqueous zinc-ion batteries involves the movement of Zn2+ ions between the cathode and anode. The theoretical capacity of metallic zinc is ∼820 mA h g−1 and it has a high kinetic overpotential for hydrogen evolution, which makes it stable with an aqueous electrolyte.9–12 Despite many advantages of the zinc metal as an anode, a suitable cathode material is highly required, which is currently restricting the advancement of rechargeable Zn-ion batteries. Various cathode materials for aqueous Zn-ion batteries are currently under investigation, such as Prussian blue analogues,15 polyanion metal phosphates,16 quinone analogues,17 manganese dioxide,18 vanadium-based compounds, etc.19 However, the undesirable phase transitions, co-insertion of H+ along with Zn2+, structural failure and material disintegration were found to be major drawbacks associated with cathode materials.15–21 Thus, to select a novel cathode material with high reversible capacity and a long cycle life is still a challenge for aqueous zinc ion batteries.
Recently, the V2O5 electrode material was identified as a promising cathode due to its high specific capacity (∼589 mA h g−1), rich resources, layered structure with a stable open-framework, steady cycling performance and outstanding rate capability. However, the structural instability during long-term cycling and the low electrical conductivity are still unresolved issues of the V2O5 cathode.19–23 Among all the approaches to optimize these issues, the priority is given to the fabrication of novel nanostructures, which in fact offers numerous intriguing properties such as more active sites for redox reactions, short diffusion paths for Zn2+ ions, high surface area and large electrode/electrolyte contact area, as well as suppresses the structural breakdown to a certain extent induced by volume changes, resulting in excellent electrochemical performances.
Thus, we have fabricated here a two-dimensional (2D) nanoplate-shaped V2O5 cathode material using a facile solvothermal synthesis method and tested its suitability for aqueous zinc ion batteries. Recently, 2D nanomaterials have been significantly used as electrode materials for energy storage applications due to their high mechanical integrity as they are stacked by van der Waals forces and made up by the substantial overlapping of the layers. In addition, the major advantages regarding atomic arrangement, coordination number, bond lengths, atomic or molecular thickness and infinite planar lengths of 2D nanomaterials make them superior to their bulk counterparts.24,25 The obtained results demonstrate that the electrochemical performances of a nanoplate-shaped V2O5 cathode at high current rate are still stable. This research is expected to provide a feasible strategy for designing and creating promising vanadium-based cathode materials for rechargeable aqueous zinc-ion batteries.
Experimental
Material synthesis
Initially, 6 mmol of vanadium acetylacetonate (Sigma Aldrich, India, 97%) was dissolved in 30 mL each of anhydrous carbinol and ethylene glycol under continuous stirring. Thereafter, liquid ammonia (NH4OH) was added dropwise to maintain pH ∼ 9 in the above precursor solution under vigorous stirring. Then, after continuous stirring for 45 min, the obtained solution was further transferred to a Teflon-lined stainless-steel autoclave and heated up to 180 °C for 12 h. The as-prepared product was collected after natural cooling followed by centrifugation and washing with distilled water and ethanol several times to remove the organic impurities. After overnight drying of the as-prepared sample at 80 °C, the calcination was performed in an air atmosphere at 450 °C for 1 h with the heating rate of 1° min−1.
Material characterisation
The crystallinity and purity of the calcined sample was determined by X-ray diffraction analysis (XRD, Shimadzu X-ray diffractometer with Cu Kα radiation, λ = 1.5406 Å). The surface morphology, particle size, and shape of the calcined sample were analyzed by field-emission scanning electron microscopy (FE-SEM, S-4700 Hitachi) and field emission transmission electron microscopy (FE-TEM, Philips TecnaiF20 at 200 kV). Furthermore, the elemental mapping and surface chemical compositions of the calcined sample were characterized by energy dispersive spectroscopy (EDS) and X-ray photoelectron spectroscopy (XPS; M/s Thermo Fischer Scientific Instrument UK with a monochromatic Al Kα X-ray source), respectively. Raman analysis was carried out using a Renishaw Raman Microscope, with a 514 nm laser to analyse the chemical bonding states of the product. The surface area including pore size distribution was investigated by the Brunauer–Emmett–Teller method using N2 adsorption/desorption isotherms (BET, Micromeritics Instrument Corp. Gemini-V).
Electrode fabrication
A CR-2032 coin-type half-cell of the V2O5 cathode was assembled using zinc metal foil as a reference electrode, glass fibre as a separator and 2 M ZnSO4 as an electrolyte. Initially, to fabricate a working electrode, the active materials (70 wt%), acetylene black (15 wt%) and polyacrylic acid (PAA) (15 wt%) were pressed onto a stainless-steel mesh, which was then dried under vacuum at 120 °C for 12 h. The cells were assembled in an open air environment and they were ideally kept for 12 h for aging before the electrochemical measurements. The electrochemical measurements were performed using a WBCS 3000 (WonATech) battery tester between the potential range of 0.2–1.6 V. Cyclic voltammetry (CV) was also carried out using an AUTOLAB PGSTAT302N potentiostat for the initial five cycles at the constant scan rate of 0.2 mV s−1 under the same potential range.
Results and discussion
Physiochemical properties
Fig. 1(a) shows the XRD pattern of the calcined sample, which clearly demonstrates sharp peaks with high intensity, indicating high crystallinity of the sample. All the diffraction peaks of the sample are well consistent with the standard diffraction pattern of the orthorhombic phase of V2O5 with Pmmn space group (JCPDS no: 00-041-1426). In addition, there were no other impurity peaks visible in the diffraction pattern, which implies that the calcined sample is highly pure. The morphological analysis of the calcined sample was then further investigated and the obtained results are shown in Fig. 1(b)–(d). Fig. 1(b) and (c) represent the FE-SEM images taken at different magnifications, which clearly shows 2D nanoplate-type morphology. As can be seen from the figure, the nanoplates are highly aggregated with smooth surfaces. As shown in Fig. 1(d), TEM analysis was also performed for detailed microstructural analysis. The obtained TEM image is in accordance with the FE-SEM results. The nanoplate sizes are in the range of ∼50–200 nm. The high-resolution TEM (HR-TEM) image displayed in Fig. 1(e) indicates the high-crystallinity of the calcined sample. The HR-TEM image demonstrates clear lattice fringes with interplanar spacing of ∼0.571 nm and 0.288 nm, corresponding to the (200) and (301) planes respectively, which is matched with the XRD pattern of the V2O5 sample. The elemental-mapping images displayed in Fig. 1(f) and (g) confirmed the uniform dispersion of vanadium (V-K; yellow) and oxygen (O-K; red) elements without the existence of any other impurities throughout the sample, which indicates that the nanoplates are mainly composed of V2O5.
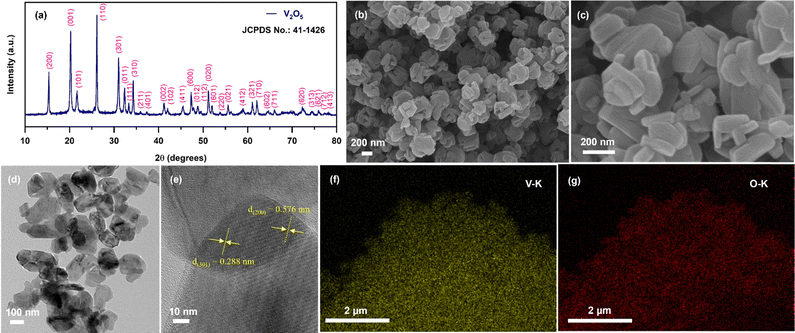 |
| Fig. 1 (a) XRD pattern; (b, c) FE-SEM images at different magnifications; (d) FE-TEM image; (e) HR-TEM image; and (f, g) representative EDX mapping images of the V2O5 sample. | |
In order to investigate the oxidation states of the elements, XPS analysis was carried out and the obtained results are displayed in Fig. 2(a) and (b). Fig. 2(a) shows the survey spectrum of the calcined V2O5 sample, which clearly shows the presence of vanadium (V) and oxygen (O) elements. More precisely, Fig. 2(b) represents the combined de-convoluted XPS spectra of V-2p and O-1s. As can be seen, the characteristic peaks obtained at binding energies of 517.2 and 524.6 eV correspond to V5+ 2p3/2 and 2p1/2, respectively. Since the binding energy difference between the core levels is found to be 7.4 eV, it is in good agreement with the electronic states of V2O5. The peaks located at binding energies of 530 eV and 531.9 eV of the O-1s spectrum belong to the V–O and V–OH bonds of the V2O5 sample.26,27 Raman analysis is also employed to investigate the bonding configurations using a variety of molecular vibrational modes, as shown in Fig. 2(c). The Raman spectrum was measured in the Raman shift range of 50–1100 cm−1, which exhibits various high and intense peaks located at ∼105, ∼146, ∼197, ∼284, ∼304, ∼405, ∼483, ∼526, ∼704 and ∼995 cm−1. The peaks present at 146 and 197 cm−1 are related to the B3g mode of V–O–V chains, which indicates the relative motion of V2O5 layers with regard to one another, indicating high crystallinity of the sample. However, the other two peaks present at 284 and 405 cm−1 show the bending vibration of V
O type bonding. On the other hand, the shoulder peaks obtained at 483 and 304 cm−1 belong to bending vibrations of V–O–V (doubly coordinated oxygen) and V3–O (triply coordinated oxygen) type, respectively.28,29 The peaks positioned at 526 and 704 cm−1 correspond to the stretching vibrations of triply co-ordinated oxygen (V3–O) and doubly co-ordinated oxygen (V2–O), respectively. Finally, the Raman shift present at 995 cm−1 is due to the terminal oxygen (V5+
O) stretching mode.29,30 In addition, BET analysis was also conducted to evaluate the specific surface area and porosity of the material. As depicted in Fig. 2(d), the N2 adsorption–desorption isotherms show a type IV isotherm, indicating mesoporosity in the sample. The BET surface area was found to be 15.94 m2 g−1. Moreover, the Barrett–Joyner–Halenda (BJH) pore size distribution plot, as shown in the inset of the figure, demonstrates an average pore diameter of ∼16.8 nm and total pore volume of ∼0.032 cm3 g−1, which also suggests that the material possesses mesopores. It is well known that a porous nanostructure and large surface area offers a short diffusion length, better electrolyte impregnation, numerous active sites for Zn-ion adsorption, etc., and thereby excellent electrochemical performances.30
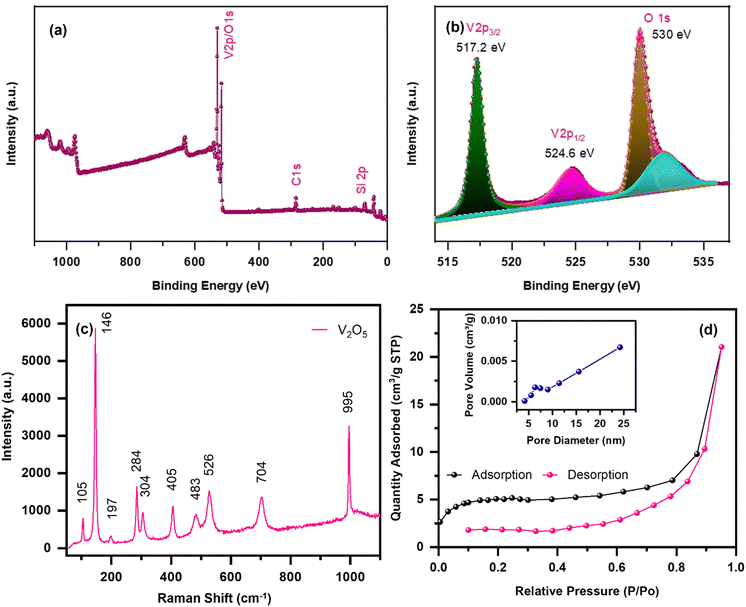 |
| Fig. 2 XPS: (a) survey spectrum; (b) V-2p and O-1s spectrum; (c) Raman spectrum; (d) BET analysis with pore size distribution (inset) of the nanoplate-shaped V2O5 sample. | |
Electrochemical investigation
Fig. 3 displays CV curves for the initial 5 cycles at a constant scan rate of 0.2 mV s−1. As can be seen, the first cycle shows two reduction peaks located at ∼0.57 V and ∼0.9 V, which is due to the insertion processes of Zn-ions in the V2O5 nanoplate electrode. During the anodic scan, the oxidation peaks observed at ∼1.08 and ∼1.35 V can be attributed to the de-insertion of Zn2+ ions.31 However, compared to the first cycle, the peak positions and peak current from the second cycle onwards are different, which may be due to the incomplete extraction of inserted Zn2+ ions from the V2O5 nanostructure.19 In addition, the cathodic peak observed at ∼0.9 V in the first cycle splits into two peaks during the second cycle and appeared to be ∼0.91 V and ∼1.1 V, which could be described by the multiple insertion reactions of Zn2+ ions because of the chemical defects of vanadium oxide.32 The peak located at ∼0.91 V and ∼0.57 V corresponds to the redox reaction of V5+/V4+ and V4+/V3+, respectively.33
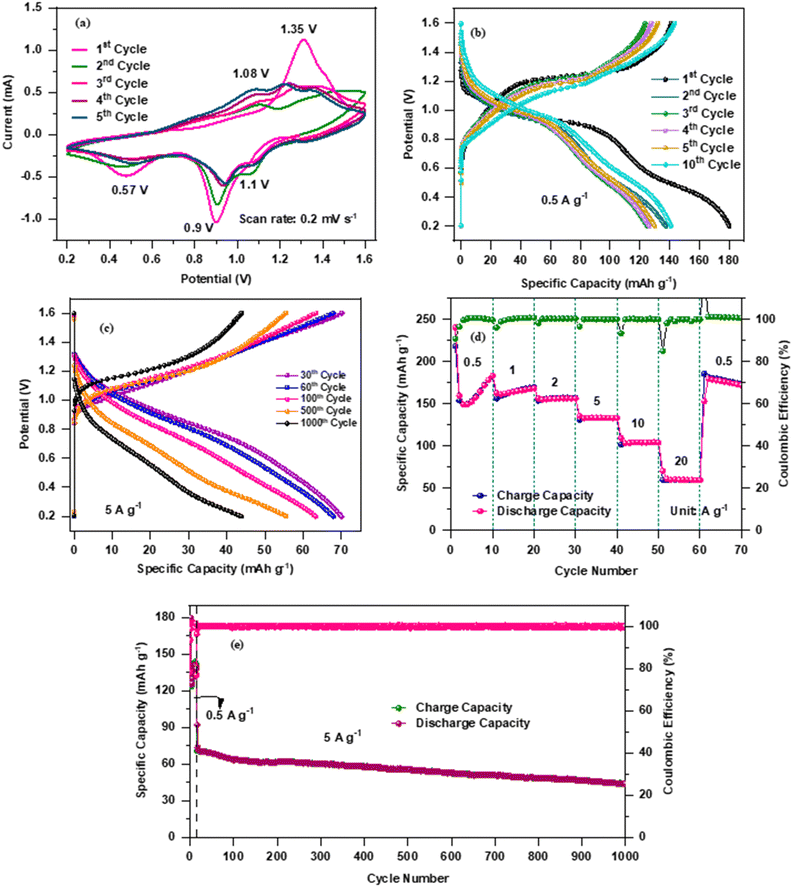 |
| Fig. 3 (a) Cyclic voltammetry curves at a constant scan rate of 0.2 mV s−1; (b) discharge/charge curves at a current density of 0.5 A g−1 for the initial five cycles; (c) discharge/charge curves at a current density of 5 A g−1 for 1000 cycles; (d) C-rate performance at different current densities and (e) cycling performance at a constant current density of 5 A g−1 until 1000 cycles of the nanoplate-shaped V2O5 electrode. | |
Furthermore, the charge/discharge data of the V2O5 electrode was recorded at a constant current density of 0.5 A g−1 for the initial 15 cycles. And out of 15 cycles, Fig. 3(b) shows the charge/discharge curves of the 1st, 2nd, 3rd, 4th, 5th and 10th cycles. Though the voltage profiles are similar, the high reversibility and stability can be easily seen in all the cycles except for the first discharge cycle of the electrode material. The significant irreversible capacity loss observed in the initial discharge cycle can be attributed to the formation of the SEI layer, which causes the kinetic limitations by consuming more number of Zn2+ ions during discharge, but does not allow extraction of the same number of Zn2+ ions during charge.19,34 It is clear from the figure that from the second cycle onwards, the voltage profile shows high reversibility, which indicates a decrease in charge transfer resistance at the electrode/electrolyte contact, resulting in low polarization. The small polarization demonstrates fast Zn2+ transfer kinetics within the electrode. The electrode is able to deliver the charge/discharge capacities of ∼141.2/170.06, ∼132.2/137.38, ∼123.7/124.26, ∼127.8/126.26, ∼132.2/132.03 and ∼141.06/143.46 mA h g−1 for the 1st, 2nd, 3rd, 4th, 5th and 10th cycles, respectively, which clearly indicates ∼100% coulombic efficiency of the electrode. On the other hand, Fig. 3(c) represents the galvanostatic charge/discharge cycles of the V2O5 electrode for the 30th, 60th, 100th, 500th and 1000th cycles at a constant current density of 5 A g−1. It can be observed that the capacity decreases with increase of the cycle numbers. However, the coulombic efficiency was still ∼100% throughout the cycling and the charge/discharge capacity was found to be ∼69/69.8 mA h g−1, ∼67.8/68.8 mA h g−1, ∼63.40/61.34 mA h g−1, 56.34/56.34 mA h g−1 and ∼43.81/43.81 mA h g−1, respectively for the above-mentioned cycle numbers. In addition, it is also believed that the high surface area along with the electrode may also tolerate the absolute volume changes of the electrode during the insertion/de-insertion of Zn2+ ions. In order to investigate the stability of the nanoplate-shaped V2O5 electrode, C-rate was performed at various current densities of 0.5 A g−1 to 20 A g−1 and the obtained results are displayed in Fig. 3(d). The V2O5 cathode delivers the specific capacities of ∼183, ∼168, ∼156, ∼133, ∼104 and ∼59 mA h g−1 at current densities of 0.5, 1, 2, 5, 10 and 20 A g−1, respectively. Impressively, when the current rate returns back to the initial current rate of 0.5 A g−1 after 60 cycles, the electrode is still able to regain the original capacity of ∼180 mA h g−1 with ∼100% coulombic efficiency, which clearly indicates the high stability of the electrode material. In addition, the continuous capacity loss with increase of the current density during cycling is a common phenomenon as Zn2+ ions do not get sufficient time to (de)-intercalate at high current rates.35,36 More importantly, it can be seen that the electrode exhibits 32% of the initial capacity at such a high current density of 20
000 mA g−1 (20 A g−1), which also suggests that the nanoplate morphology maintains the integrity of the electrode during volume expansion/contraction resulting from Zn2+ (de)-insertion. Fig. 3(e) shows the specific capacity versus cycle number graph including the corresponding coulombic efficiency data of the 2D nanoplate-shaped V2O5 electrode at the current density of 0.5 A g−1 for the first 15 cycles followed by 5 A g−1 fo a further 1000 cycles. Since the electrode delivers the initial discharge/charge capacity of ∼180/141 mA h g−1, the capacity was maintained at ∼44 mA h g−1 after 1000 cycles. Significant capacity loss can be noticed after 15 cycles and the capacity reaches ∼75 mA h g−1, which can be ascribed to the fact that the inserted Zn2+ ions could not be completely extracted from the V2O5 lattice. These unextracted Zn2+ ions locate at the “dead Zn2+ sites” making the layered crystalline structure stable with promising stable capacity until 1000 cycles.2,23 The layered V2O5 cathode permits a high extent of reversibility for hydrated Zn2+ (de)-intercalation. It is believed that the co-insertion of H2O along with Zn2+ ions causes structural evolution and changes the layered V2O5 into a layered ZnxV2O5·nH2O. On the other hand, the subsequent charging process enables the reversal of the structural evolution followed by the extraction of hydrated Zn2+ ions that have occurred during discharge. The co-intercalated H2O molecules act as a buffer against the high charge density of Zn2+, which facilitates quick cation transfer and high-rate capability. The reversible reaction of the Zn–V2O5 battery is schematically illustrated in Fig. 4 with the corresponding equation.37
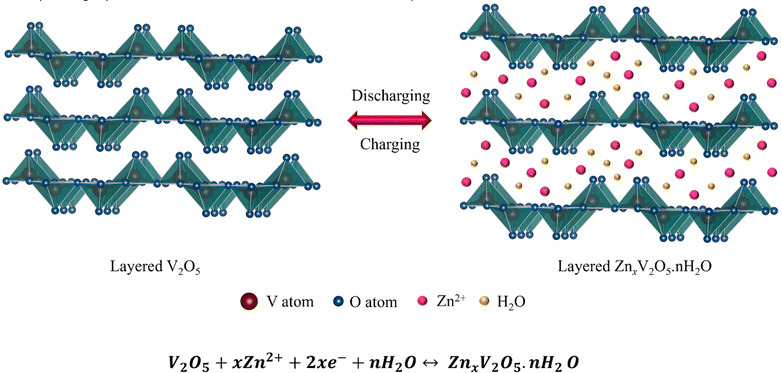 |
| Fig. 4 Schematic illustration of the Zn-ion storage mechanism in the layered V2O5 crystal system. | |
Conclusions
Herein, we have fabricated a 2D nanoplate-shaped V2O5 cathode material through a facile solvothermal method. The electrochemical investigation results clearly demonstrate that the V2O5 electrode exhibits high specific capacity and better rate capability even at a high current density of 20 A g−1. The excellent performance of the V2O5 electrode can be attributed to the unique features of the nanoplates i.e., larger specific surface area and high mechanical stability, which increases the conductivity by shortening the diffusion paths for ions. The cathode delivers an initial charge capacity of ∼141 mA h g−1 at a current density of 0.5 A g−1 and retains a capacity of ∼44 mA h g−1 after 1000 cycles at a current density of 5 A g−1. The obtained results conclude that the high performance of the V2O5 nanoplates provides potential feasibility as a cathode material for ZIBs.
Conflicts of interest
There are no conflicts to declare.
Acknowledgements
One of the authors (Priya Yadav) would like to thank CSIR, New Delhi, for the award of a senior research fellowship (09/0045(11332)/2021-EMR-I). Dr Alok Kumar Rai is grateful to the University Grants Commission (UGC), India for the funding support under the UGC-FRP scheme (FRP ID: 57304). This work was mainly funded by the Council of Scientific and Industrial Research (CSIR) Research Grant (File No. 01(3015)/21/EMR-II) and partially supported by the National Research Foundation of Korea (NRF) grant funded by the Korea government (MSIT) (NRF-2018R1A5A1025224).
References
- J. M. Tarascon and M. Armand, Nature, 2008, 451, 652–657 CrossRef PubMed.
- J. M. Tarascon and M. Armand, Nature, 2001, 414, 359–367 CrossRef CAS PubMed.
- Y. K. Sun, ACS Energy Lett., 2017, 2, 2694–2695 CrossRef CAS.
- J. Hassoun, K. S. Lee, Y. K. Sun and B. Scrosati, J. Am. Chem. Soc., 2011, 133, 3139–3143 CrossRef CAS PubMed.
- H. Kim, J. Hong, K. Y. Park, H. Kim, S. W. Kim and K. Kang, Chem. Rev., 2014, 114, 11788–11827 CrossRef CAS PubMed.
- H. Nishide and K. Oyaiz, Science, 2008, 319, 737 CrossRef CAS PubMed.
- P. Yadav, N. Kumari and A. K. Rai, J. Power Sources, 2023, 555, 232385 CrossRef CAS.
- J. Singh, S. Lee, Zulkifli, J. Kim and A. K. Rai, J. Alloys Compd., 2022, 920, 165925 CrossRef CAS.
- W. Liu, J. Hao, C. Xu, J. Mou, L. Dong, F. Jiang, Z. Kang, J. Wu, B. Jiang and F. Kang, Chem. Commun., 2017, 53, 6872–6874 RSC.
- G. Z. Fang, J. Zhou, A. Q. Pan and S. Q. Liang, ACS Energy Lett., 2018, 3, 2480–2501 CrossRef CAS.
- A. R. Mainar, L. C. Colmenares, J. A. Blazquez and I. Urdampilleta, Int. J. Energy Res., 2018, 42, 903–918 CrossRef.
- F. Wang, O. Borodin, T. Gao, X. Fan, W. Sun, F. Han, A. Faraone, J. A. Dura, K. Xu and C. Wang, Nat. Mater., 2018, 17, 543–549 CrossRef CAS PubMed.
- Y. Bai, L. Luo, W. Song, S. Man, H. Zhang and C. Ming Li, Adv. Sci., 2024, 2308668 CrossRef CAS PubMed.
- Y. Bai, Y. Qin, J. Hao, H. Zhang and C. M. Li, Adv. Funct. Mater., 2024, 34, 2310393 CrossRef CAS.
- L. Y. Zhang, L. Chen, X. F. Zhou and Z. P. Liu, Adv. Energy Mater., 2015, 5, 1400930 CrossRef.
- W. Li, K. Wang, S. Cheng and K. Jiang, Energy Storage Mater., 2018, 15, 14–21 CrossRef.
- Y. Liang, Y. Jing, S. Gheytani, K. Y. Lee, P. Liu, A. Facchetti and Y. Yao, Nat. Mater., 2017, 16, 841–848 CrossRef CAS PubMed.
- H. Pan, Y. Shao, P. Yan, Y. Cheng, K. S. Han, Z. Nie, C. Wang, J. Yang, X. Li, P. Bhattacharya, K. T. Mueller and J. Liu, Nat. Energy, 2016, 1, 16039 CrossRef CAS.
- J. Zhou, L. Shan, Z. Wu, X. Guo, G. Fang and S. Liang, Chem. Commun., 2018, 54, 4457–4460 RSC.
- Y. Bai, H. Zhang, H. Song, C. Zhu, L. Yan, Q. Hu and C. M. Li, Nano Energy, 2024, 120, 109090 CrossRef CAS.
- Y. Bai, H. Zhang, W. Liang, C. Zhu, L. Yan and C. Li, Small, 2023, 2306111 Search PubMed.
- P. Hu, M. Yan, T. Zhu, X. Wang, X. Wei, J. Li, L. Zhou, Z. Li, L. Chen and L. Mai, ACS Appl. Mater. Interfaces, 2017, 9, 42717–42722 CrossRef CAS PubMed.
- F. Liu, Z. Chen, G. Fang, Z. Wang, Y. Cai, B. Tang, J. Zhou and S. Liang, Nano-Micro Lett., 2019, 11, 25 CrossRef CAS PubMed.
- C. L. Tan, X. H. Cao, X. J. Wu, Q. Y. He, J. Yang, X. Zhang, J. Z. Chen, W. Zhao, S. K. Han, G. H. Nam, M. Sindoro and H. Zhang, Chem. Rev., 2017, 117, 6225–6331 CrossRef CAS PubMed.
- L. Shi and T. Zhao, J. Mater. Chem., 2017, 5, 3735–3758 RSC.
- X. Zhang, X. Liu, C. Yang, N. Li, T. Ji, K. Yan, B. Zhu, J. Yin, J. Zhao and Y. Li, Surf. Coat. Technol., 2019, 358, 661–666 CrossRef CAS.
- X. Wang, Y. Huang, D. Jia, W. Pang, Z. Guo, Y. Du, X. Tang and Y. Cao, Inorg. Chem., 2015, 54, 11799–11806 CrossRef CAS PubMed.
- S. H. Lee, H. M. Cheong, M. J. Seong, P. Liu, C. E. Tracy, A. Mascarenhas, J. R. Pitts and S. K. Deb, Solid State Ion., 2003, 165, 111–116 CrossRef CAS.
- N. M. Abd-Alghafour, G. A. Naeem and S. M. Mohammad, J. Phys.: Conf. Ser., 2020, 1535, 012046 CrossRef CAS.
- H. Yin, C. Song, Y. Wang, S. Li, M. Zeng, Z. Zhang, Z. Zhu and K. Yu, Electrochim. Acta, 2013, 111, 762–770 CrossRef CAS.
- Z. Chen, J. Hu, S. Liu, H. Hou, G. Zou, W. Deng and X. Ji, Chem. Eng. J., 2021, 404, 126536 CrossRef CAS.
- L. Shan, J. Zhou, W. Zhang, C. Xia, S. Guo, X. Ma, G. Fang, X. Wu and S. Liang, Energy Technol., 2019, 7, 1900022 CrossRef.
- C. Liu, M. Tian, M. Wang, J. Zheng, S. Wang, M. Yan, Z. Wang, Z. Yin, J. Yang and G. Cao, J. Mater. Chem. A, 2020, 8, 7713–7723 RSC.
- Y. Li, Z. Huang, P. K. Kalambate, Y. Zhong, Z. Huang, M. Xie, Y. Shen and Y. Huang, Nano Energy, 2019, 60, 752–759 CrossRef CAS.
- P. Yadav, D. Putro, J. Kim and A. K. Rai, Batteries, 2023, 9, 133 CrossRef CAS.
- P. Yadav, D. Putro, N. Kumari, J. Kim and A. K. Rai, Phys. Chem. Chem. Phys., 2023, 25, 21082–21088 RSC.
- N. Zhang, Y. Dong, M. Jia, X. Bian, Y. Wang, M. Qiu, J. Xu, Y. Liu, L. Jiao and F. Cheng, ACS Energy Lett., 2018, 3, 1366–1372 CrossRef CAS.
Footnote |
† These authors contributed equally to this manuscript. |
|
This journal is © The Royal Society of Chemistry 2024 |
Click here to see how this site uses Cookies. View our privacy policy here.