Mechanochemistry enabled highly efficient solvent-free deoxygenation of phosphine oxides in air†
Received
15th February 2024
, Accepted 15th April 2024
First published on 16th April 2024
Abstract
Deoxygenation of phosphine oxides is an important method for the synthesis of valuable organophosphine compounds and recycling of phosphorus resources. However, existing solution-based deoxygenation protocols usually require long reaction times, significant amounts of potentially harmful organic solvents, and inert gas atmospheres. In addition, reactions of poorly soluble phosphine oxides are challenging and often inefficient. Herein, we demonstrate that a high-temperature mechanochemical protocol enables the highly efficient solvent-free deoxygenation of phosphine oxides with hydrosilanes in the presence of a phosphoric acid additive. These reactions were rapid and completed within 30 min for most substrates. Notably, this is the first practical deoxygenation of phosphine oxides in which all synthetic operations can be carried out in air. A preliminary study on the mechanochemical catalytic Wittig reaction is also described.
Introduction
Tertiary phosphines are an essential class of compounds that are used as stoichiometric synthetic reagents, nucleophilic organocatalysts, and ligands in organometallic catalysts.1 Therefore, the development of efficient methods for the synthesis of tertiary phosphines has attracted significant attention. Given their high chemical stability and ease of handling under atmospheric conditions, phosphine oxides serve as important synthetic intermediates that can be converted into a broad range of organic phosphine compounds through the deoxygenation of the P
O bond.2 In addition, phosphine oxides are generated as stoichiometric chemical waste in numerous fundamental organic transformations, including the Wittig, Mitsunobu, Staudinger, Rauhut–Currier, and Appel reactions.1 Deoxygenation of phosphine oxides to phosphines has been recognized as a prominent strategy for recycling phosphorus resources.2 Despite the importance of organophosphine synthesis and phosphorus recycling, existing deoxygenation methods are harsh owing to the strength of the P
O bond and require long reaction times, potentially harmful organic solvents, and delicate operating conditions, which reduce their practical utility.2–7
Conventional deoxygenation of phosphine oxides involves the use of highly reactive metal hydrides (e.g., LiAlH4)3 and low-valent metal reductants (e.g., SmI2/hexamethylphosphoramide and Cp2TiCl2/Mg).4 Such conditions are affected by functional group tolerance and require special precautions. Recently, hydrosilanes have been used as reductants and many useful deoxygenation protocols that proceed under mild conditions have been developed (Scheme 1).5 However, existing solution-based deoxygenation methods with hydrosilanes usually require significant amounts of reaction solvents and long reaction times (>24 h). Furthermore, these reactions must be performed in an inert -gas atmosphere, which requires special training. Although the solvent-free microwave-assisted deoxygenation of phosphine oxides with hydrosilanes has also been reported,6 an excess amount of hydrosilanes and an inert gas atmosphere are still required. Unfortunately, these requirements present major drawbacks from both environmental and economic perspectives.
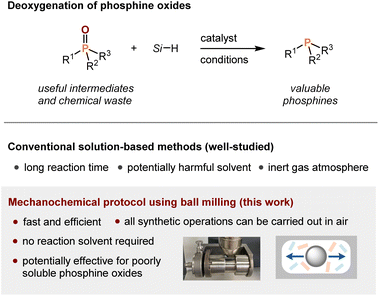 |
| Scheme 1 Development of a mechanochemical protocol for the deoxygenation of phosphine oxides to phosphines. | |
Recently, mechanochemical synthesis via ball milling has attracted considerable attention as an efficient solvent-free synthetic technique.8 Mechanochemical organic reactions often show much faster reaction kinetics than those under conventional solution-based conditions because of their high concentrations; moreover, the experimental operations can be carried out in air. Considering these achievements, including our recent success in solid-state ball-milling synthesis,9 we envisioned that this mechanochemical strategy can be applied to the deoxygenation of phosphine oxides, providing a practical solution to many issues associated with conventional solution-based protocols (Scheme 1).
Results and discussion
All mechanochemical reactions were conducted in a Retsch MM400 mill [stainless steel milling jar (5 mL), 20 Hz; stainless steel ball (10 mm diameter)]. All experiments were performed in air. First, we investigated the deoxygenation of triphenylphosphine oxide (1a) with phenylsilane (2a), which is commonly used as a reductant in various solution-based deoxygenation reactions of phosphine oxides (Table 1).2,5 The mechanochemical reaction at room temperature did not yield the deoxygenation product (4a) (<1%, entry 1). To accelerate the mechanochemical deoxygenation, we carried out the reaction at a higher temperature. We used a commercially available temperature-controllable heat gun placed directly above the ball-milling jar (see the ESI† for details).9g The desired product (4a) was obtained in good yield (80%) with the heat gun preset to 200 °C (entry 2). The internal temperature of the reaction mixture (120 °C) was confirmed by thermography immediately after opening the milling jar (see the ESI† for details). To further improve the efficiency, we added phosphoric acid (3) to the mixture under Beller's solution-based conditions because these additives are solid, inexpensive, and easy to handle under ambient conditions.5c The use of diphenyl phosphate (3a) (10 mol%) did not improve the reactivity (76%, entry 3). The reaction with a nitro-substituted phosphate, which is the best additive for Beller's protocol, lowered the yield of 4a (67%, entry 4). We found that BINOL-derived phosphoric acid (3c), which has never been used for the deoxygenation of phosphine oxides, significantly accelerated the mechanochemical reaction to form 4a in quantitative yield (99%, entry 5). Notably, the reaction was nearly complete within 30 min (94% yield, entry 6). A further increase in the reaction temperature decreased the yield (77%, entry 7). We also attempted the deoxygenation reaction in a test tube with efficient mixing by magnetic stirring under the optimized conditions; however, the reaction gave a much lower yield of 4a (61%, entry 8). This result suggests that strong mechanical agitation in a ball mill is crucial for highly efficient solvent-free deoxygenation. Although further studies are required, we speculate that a strong mechanical impact could crush the solid 1a into smaller particles with increased surface area, thereby facilitating efficient deoxygenation reactions under solvent-free conditions.
Table 1 Optimization studya

|
Entry |
Phosphoric acid (3) |
Internal temp. (°C) |
Time (min) |
Yield of 4a (%)b |
Conditions: 1a (0.3 mmol), 2a (0.75 mmol), 3 (0.03 mmol) in a stainless steel milling jar (5 mL) with a stainless steel ball (10 mm).
Determined by GC analysis of the crude reaction mixture using an internal standard.
Reaction was performed in a test tube under magnetic stirring.
|
1 |
None |
30 |
60 |
<1 |
2 |
None |
120 |
60 |
80 |
3 |
3a
|
120 |
60 |
76 |
4 |
3b
|
120 |
60 |
67 |
5 |
3c
|
120 |
60 |
99 |
6 |
3c
|
120 |
30 |
94 |
7 |
3c
|
145 |
30 |
77 |
8c |
3c
|
120 |
30 |
61 |
|
Next, we investigated mechanochemical deoxygenation reactions using different hydrosilanes (Scheme 2). The use of 1,1,3,3-tetramethyldisiloxane (2b) instead of 2a resulted in a significant decrease in the yield of 4a (39%). Using triethoxysilane (2c) and tris(trimethylsilyl)silane (2d) afforded very low yields of 4a (5% and 4%, respectively). Trichlorosilane (2e), which is widely used in the deoxygenation of phosphine oxides,2 provided 4a in a low yield (28%). The reaction using poly(methylhydrosiloxane) [the number-average molecular weight (Mn): 1700−3200] (2f) was attempted, but the yield of 4a was moderate (35%). These results suggest that 2a is the best reductant for the mechanochemical deoxygenation of 1a.
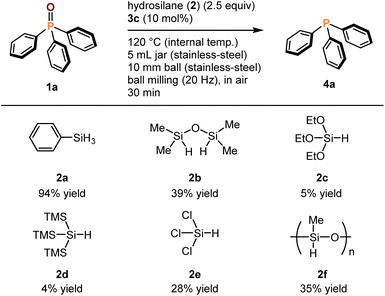 |
| Scheme 2 Mechanochemical deoxygenation of 1a with various silanes. aConditions: 1a (0.3 mmol), 2 (0.75 mmol), 3c (0.03 mmol) in a stainless steel milling jar (5 mL) with a stainless steel ball (10 mm). GC yields are shown. | |
With the optimized conditions in hand, we explored the phosphine oxide substrate scope of mechanochemical deoxygenation. As shown in Table 2, various aromatic, heteroaromatic, and aliphatic substituted phosphine oxides were smoothly reduced to their corresponding phosphines (4) with full conversion for most of the substrates. The products (4) were isolated using flash column chromatography in air. The mechanochemical deoxygenation of aromatic phosphine oxides bearing both electron-donating and -withdrawing groups (1a–f) proceeded smoothy to afford the corresponding phosphines (4a–f) in good-to-high isolated yield (75–99%). To our delight, heteroaromatic substrates (1g and 1h) were also converted into the desired products (4g and 4h) in moderate-to-good yields (46% and 88%, respectively). Furthermore, the reduction of more oxidization sensitive, electron-rich alkyl substituted phosphine oxides (1i–k) gave the corresponding phosphines (4i–k) in good-to-excellent isolated yield (56–94%), despite some oxidation of the products during the purification via silica gel column chromatography.
Table 2 Substrate scope. aConditions: 1 (0.3 mmol), 2a (0.75 mmol), 3c (0.03 mmol) in a stainless steel milling jar (5 mL) with a stainless steel ball (10 mm). The isolated yields are shown
To explore the practical utility of this protocol, we compared the efficiencies of solution-based and mechanochemical reactions (Scheme 3). The solution-based reaction of 1a with 2a in the presence of 3c as the catalyst in toluene (0.125 M) was not complete in 3 h, requiring 24 h to afford a high yield (97%) (Scheme 3a). Such long reaction times are commonly required for the deoxygenation of 1a using solution-based protocols. Notably, the mechanochemical deoxygenation of 1a under the developed conditions was completed within 30 min, and a high yield (94%) was obtained, indicating the outstanding performance of the mechanical approach. The solution-based reaction of a phosphine oxide bearing a large aromatic structure, such as a pyrene moiety (1l), exhibited a slower kinetic profile than 1a, and a low yield (36%) of the product (4l) was obtained after 3 h (Scheme 3b). The observed low reactivity is probably due to the poor solubility of 1l, which has a solubility in toluene at room temperature of 1.2 × 10−2 M, while the solubility of 1a is 0.22 M. In contrast, 1l was quickly converted into 4l within 90 min, and a quantitative yield was obtained (99%) using the newly developed mechanochemical protocol (Scheme 3b). These results demonstrate the synthetic potential of our approach for the efficient deoxygenation of poorly soluble phosphine oxides, which are less reactive in solution.
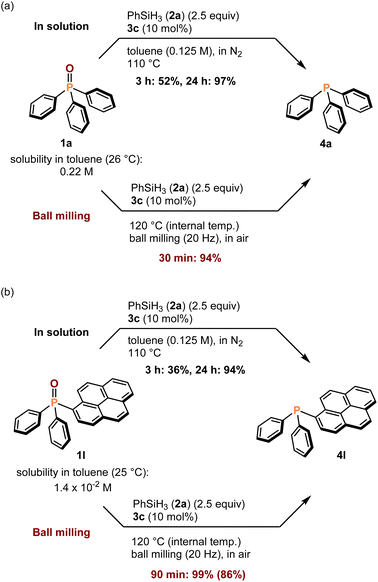 |
| Scheme 3 Comparison to solution-based conditions. aFor details of the reaction conditions, see the ESI.† For (3a), GC yields are shown. In (3b), NMR yields are shown, and the isolated yields are shown in parentheses. | |
To demonstrate the practical utility of this reaction, we investigated the scaled-up reaction (Scheme 4). A 2 mmol-scale reaction was conducted in a 10 mL stainless steel jar with a 10 mm stainless steel ball. The desired product 4a was obtained in 99% yield, which was comparable to the yield obtained in the small-scale reaction. This result emphasizes the practical utility of the protocol.
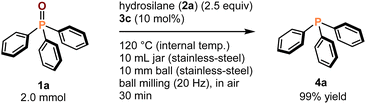 |
| Scheme 4 Scaled-up reaction of 1a. aFor details of the reaction conditions, see the ESI.† The isolated yields are shown. | |
The successful development of a highly efficient mechanochemical deoxygenation reaction for phosphine oxides encouraged us to investigate the catalytic Wittig reactions under mechanochemical conditions. In 2002, Pecharsky et al. reported the first Wittig reaction using stoichiometric amounts of triphenylphosphine (4a) under mechanochemical conditions.10 Recently, Mack et al. developed a mechanochemical Wittig reaction using a polymer-supported triphenylphosphine.11 There are still no reports on the development of a mechanochemical catalytic Wittig reaction in which a generated phosphine oxide is reduced to form the corresponding phosphine in situ; therefore, phosphine can catalyze the Wittig reaction.12 We first examined the mechanochemical deoxygenation of ethyl bromoacetate (5) and benzaldehyde (6) in the presence of 1a (20 mol%), BINOL-derived phosphoric acid (3c) (10 mol%), phenylsilane (2a), and diisopropylethylamine under high-temperature ball-milling conditions (Scheme 5). Unfortunately, the reaction did not proceed to completion. Given that the cyclic phosphine oxide 1m often shows high activity in solution-based catalytic Wittig reactions, we carried out a mechanochemical Wittig reaction with 1m (Scheme 5).12 To our delight, desired product 7 was obtained in a promising yield (64%) even after a short reaction time (60 min). Preliminary investigation of the reaction conditions by varying the mechanochemical parameters, reductants, and bases did not improve the yield of 7 (for details, see the ESI†). Further optimization studies are currently underway.
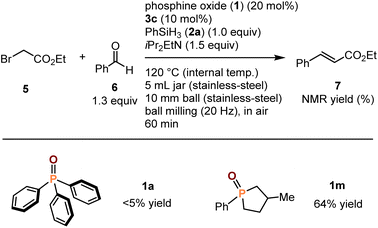 |
| Scheme 5 Preliminary study on the catalytic Wittig reaction using high-temperature mechanichemistry. aFor details of the reaction conditions, see the ESI.† | |
Conclusions
In summary, we demonstrated that a mechanochemical approach at high temperatures enabled the highly efficient solvent-free deoxygenation of phosphine oxides to afford the corresponding phosphines in high yields. The developed conditions enable much faster reaction kinetics than those of solution methods and require only 30 min to complete the reactions for most substrates. Importantly, this is the first practical deoxygenation protocol for phosphine oxides in which all synthetic procedures can be carried out in air; therefore, a complicated reaction setup and special synthetic techniques are not required. The synthetic utility of this protocol was demonstrated by the highly efficient deoxygenation of poorly soluble phosphine oxides, which are less reactive in solution. The advantages of the newly developed deoxygenation protocol suggest that this mechanochemical strategy will inspire the development of efficient synthetic routes to valuable organophosphine compounds and an attractive recycling method for phosphorus resources in a practical and environmentally friendly manner.
Conflicts of interest
There are no conflicts to declare.
Acknowledgements
This work was supported by the Japan Society for the Promotion of Science (JSPS) via KAKENHI grants 22H00318, 21H01926, 22K18333, and 22H05328; by the JST via CREST grant JPMJCR19R1; by FOREST grant JPMJFR201I; as well as by the Institute for Chemical Reaction Design and Discovery (ICReDD), which was established by the World Premier International Research Initiative (WPI), MEXT, Japan. We thank Mr Tetsu Makino for his help in cross-checking experiments.
Notes and references
-
(a)
A Guide to Organophosphorus Chemistry, ed. L. D. Quin, Wiley, New York, 2000 Search PubMed;
(b) W. Tang and X. Zhang, Chem. Rev., 2003, 103, 3029 CrossRef CAS PubMed.
-
(a) D. Hérault, D. H. Nguyen, D. Nuel and G. Buono, Chem. Soc. Rev., 2015, 44, 2508 RSC;
(b) E. Podyacheva, E. Kuchuk and D. Chusov, Tetrahedron Lett., 2019, 60, 575 CrossRef CAS.
- For selected examples of metal hydride reducing agents, see:
(a) P. D. Henson, K. Naumann and K. Mislow, J. Am. Chem. Soc., 1969, 91, 5645 CrossRef CAS;
(b) T. Imamoto, T. Takeyama and T. Kusumoto, Chem. Lett., 1985, 1491 CrossRef CAS;
(c) T. Imamoto, T. Oshiki, T. Onozawa, T. Kusumoto and K. Sato, J. Am. Chem. Soc., 1990, 112, 5244 CrossRef CAS;
(d) T. Imamoto, S. Kikuchi, T. Miura and Y. Wada, Org. Lett., 2001, 3, 87 CrossRef CAS PubMed;
(e) C. A. Busacca, R. Raju, N. Grinberg, N. Haddad, P. James-Jones, H. Lee, J. C. Lorenz, A. Saha and C. H. Senanayake, J. Org. Chem., 2008, 73, 1524 CrossRef CAS PubMed;
(f) R. M. Hiney, L. J. Higham, H. Muller-Bunz and D. G. Gilheany, Angew. Chem., Int. Ed., 2006, 45, 7248 CrossRef CAS PubMed.
- For selected examples of the use of low-valent metal reductants, see:
(a) F. Dallemer, J. Collin and H. B. Kagan, Appl. Organomet. Chem., 1995, 9, 431 CrossRef CAS;
(b) Y. Handa, J. Inanaga and M. Yamaguchi, J. Chem. Soc. Chem. Commun., 1989, 298 RSC;
(c) F. Mathey and R. Maillet, Tetrahedron Lett., 1980, 21, 2525 CrossRef CAS;
(d) M. Kuroboshi, T. Kita, A. Aono, T. Katagiri, S. Kikuchi, S. Yamane, H. Kawakubo and H. Tanaka, Tetrahedron Lett., 2015, 56, 918 CrossRef CAS.
- For selected examples of the use of hydrosilanes, see:
(a) J. A. Buonomo, C. G. Eiden and C. C. Aldrich, Chem.–Eur. J., 2017, 23, 14434 CrossRef CAS PubMed;
(b) O. M. Demchuk, R. Jasiński and K. M. Pietrusiewicz, Heteroat. Chem., 2015, 26, 441 CrossRef CAS;
(c) Y. Li, L.-Q. Lu, S. Das, S. Pisiewicz, K. Junge and M. Beller, J. Am. Chem. Soc., 2012, 134, 18325 CrossRef CAS PubMed;
(d) M. Mehta, I. G. de la Arada, M. Perez, D. Porwal, M. Oestreich and D. W. Stephan, Organometallics, 2016, 35, 1030 CrossRef CAS;
(e) M.-L. Schirmer, S. Jopp, J. Holz, A. Spannenberg and T. Werner, Adv. Synth. Catal., 2016, 358, 26 CrossRef CAS;
(f) A. Chardon, O. Maubert, J. Rouden and J. Blanchet, ChemCatChem, 2017, 9, 4460 CrossRef CAS;
(g) M. Berthod, A. Favre-Réguillon, J. Mohamad, G. Mignani, G. Docherty and M. Lemaire, Synlett, 2007, 10, 1545 Search PubMed.
- G. Keglevich, T. Kovács and F. Csatlós, Heteroat. Chem., 2015, 26, 199 CrossRef CAS.
- Selected examples of the electroreduction of phosphine oxides:
(a) S. Manabe, C. M. Wong and C. S. Sevov, J. Am. Chem. Soc., 2020, 142, 3024 CrossRef CAS PubMed;
(b) J. S. Elia, C. Costentin and D. G. Nocera, J. Am. Chem. Soc., 2018, 140, 13711 CrossRef PubMed.
- For selected reviews on the use of ball-milling for organic synthesis, see:
(a) S. L. James, C. J. Adams, C. Bolm, D. Braga, P. Collier, T. Friščić, F. Grepioni, K. D. M. Harris, G. Hyett, W. Jones, A. Krebs, J. Mack, L. Maini, A. G. Orpen, I. P. Parkin, W. C. Shearouse, J. W. Steed and D. C. Waddell, Chem. Soc. Rev., 2012, 41, 413 RSC;
(b) G.-W. Wang, Chem. Soc. Rev., 2013, 42, 7668 RSC;
(c) J.-L. Do and T. Friščić, ACS Cent. Sci., 2017, 3, 13 CrossRef CAS PubMed;
(d) J. G. Hernández and C. Bolm, J. Org. Chem., 2017, 82, 4007 CrossRef PubMed;
(e) T.-X. Métro, J. Martinez and F. Lamaty, ACS Sustainable Chem. Eng., 2017, 5, 9599 CrossRef;
(f) T. K. Achar, A. Bose and P. Mal, Beilstein J. Org. Chem., 2017, 13, 1907 CrossRef CAS PubMed;
(g) O. Eguaogie, J. S. Vyle, P. F. Conlon, M. A. Gîlea and Y. Liang, Beilstein J. Org. Chem., 2018, 14, 955 CrossRef CAS PubMed;
(h) J. L. Howard, Q. Cao and D. L. Browne, Chem. Sci., 2018, 9, 3080 RSC;
(i) J. Andersen and J. Mack, Green Chem., 2018, 20, 1435 RSC;
(j) C. Bolm and J. G. Hernández, Angew. Chem., Int. Ed., 2019, 58, 3285 CrossRef CAS PubMed;
(k) T. Friščić, C. Mottillo and H. M. Titi, Angew. Chem., Int. Ed., 2020, 59, 1018 CrossRef PubMed;
(l) K. Kubota and H. Ito, Trends Chem., 2020, 2, 1066 CrossRef CAS;
(m) A. Porcheddu, E. Colacino, L. De Luca and F. Delogu, ACS Catal., 2020, 10, 8344 CrossRef CAS;
(n) J. A. Leitch and D. L. Browne, Chem.–Eur. J., 2021, 27, 9721–9726 CrossRef CAS PubMed;
(o) P. Ying, J. Yu and W. Su, Adv. Synth. Catal., 2021, 363, 1246 CrossRef CAS;
(p) K. J. Ardila-Fierro and J. G. Hernández, ChemSusChem, 2021, 14, 2145 CrossRef CAS PubMed;
(q) V. Martinez, T. Stolar, B. Karadeniz, I. Brekalo and K. Užarević, Nat. Rev. Chem, 2023, 7, 51 CrossRef CAS PubMed;
(r) K. Kubota, Bull. Chem. Soc. Jpn., 2023, 96, 913 CrossRef CAS;
(s) N. Fantozzi, J.-N. Volle, A. Porcheddu, D. Virieux, F. García and E. Colacino, Chem. Soc. Rev., 2023, 52, 6680 RSC.
- For selected examples of organic transformations using ball milling from our group, see:
(a) K. Kubota, T. Seo, K. Koide, Y. Hasegawa and H. Ito, Nat. Commun., 2019, 10, 111 CrossRef PubMed;
(b) Y. Pang, T. Ishiyama, K. Kubota and H. Ito, Chem.–Eur. J., 2019, 25, 4654 CrossRef CAS PubMed;
(c) K. Kubota, R. Takahashi and H. Ito, Chem. Sci., 2019, 10, 5837 RSC;
(d) T. Seo, T. Ishiyama, K. Kubota and H. Ito, Chem. Sci., 2019, 10, 8202 RSC;
(e) T. Kubota, Y. Pang, A. Miura and H. Ito, Science, 2019, 366, 1500 CrossRef PubMed;
(f) T. Seo, K. Kubota and H. Ito, J. Am. Chem. Soc., 2020, 142, 9884 CrossRef CAS PubMed;
(g) T. Seo, N. Toyoshima, K. Kubota and H. Ito, J. Am. Chem. Soc., 2021, 143, 6165 CrossRef CAS PubMed;
(h) T. Seo, K. Kubota and H. Ito, Angew. Chem., Int. Ed., 2023, 62, e202311531 CrossRef CAS PubMed;
(i) T. Seo, K. Kubota and H. Ito, J. Am. Chem. Soc., 2023, 145, 6823 CrossRef CAS PubMed.
- V. P. Balema, J. W. Wiench, M. Pruski and V. K. Pecharsky, J. Am. Chem. Soc., 2002, 124, 6244 CrossRef CAS PubMed.
- K. L. Denlinger, L. Ortiz-Trankina, P. Carr, K. Benson, D. C. Waddell and J. Mack, Beilstein J. Org. Chem., 2018, 14, 688 CrossRef CAS PubMed.
-
(a) C. J. O'Brien, J. L. Tellez, Z. S. Nixon, L. J. Kang, a. l. Carter, S. R. Kunkel, K. C. Prezeworski and G. A. Chas, Angew. Chem., Int. Ed., 2009, 48, 6836 CrossRef PubMed;
(b) Z. Lao and P. H. Toy, Beilstein J. Org. Chem., 2016, 12, 2577 CrossRef CAS PubMed;
(c) L. Longwitz, A. Spannenberg and T. Werner, ACS Catal., 2019, 9, 9237 CrossRef CAS;
(d) T. Werner, M. Hoffmann and S. Deshmukh, Eur. J. Org Chem., 2014, 6873 CrossRef CAS.
|
This journal is © The Royal Society of Chemistry 2024 |
Click here to see how this site uses Cookies. View our privacy policy here.