DOI:
10.1039/D4RA04942J
(Paper)
RSC Adv., 2024,
14, 34457-34470
Facile synthesis of a 3D magnetic graphene oxide/Fe3O4/banana peel-derived cellulose composite aerogel for the efficient removal of tetracycline
Received
8th July 2024
, Accepted 21st October 2024
First published on 28th October 2024
Abstract
Many initiatives have incorporated graphene oxide (GO) and biomass into aerogels for wastewater treatment. We report on the facile fabrication of a magnetic GO/Fe3O4/banana peel-derived cellulose (bio-cellulose) aerogel using an ultrasound-assisted mechanical mixing method and freeze-drying technique for the removal of tetracycline (TC). The component materials and composite aerogel were characterized using Fourier-transform infrared spectroscopy (FTIR), X-ray powder diffraction (XRD), Raman spectroscopy, field-emission scanning electron microscopy (FE-SEM), energy-dispersive X-ray spectroscopy (EDX), nitrogen adsorption–desorption analysis, and vibrating sample magnetometry (VSM). The effects of solution pH and adsorbent dose on the adsorption performance of the synthesized adsorbents were investigated. The adsorption behavior at the equilibrium of the GO/Fe3O4/bio-cellulose aerogel was studied and analyzed using four well-known non-linear models: Langmuir, Freundlich, Sips, and Temkin. The results showed that the experimental data fitted well with the Freundlich and Sips isotherm models. The maximum adsorption capacity achieved from the Sips model was 238.7 mg g−1. The adsorption kinetics were studied and proved to follow the Elovich kinetic model with an initial rate of 0.89 g g−1 min−1. These results confirm the favorable adsorption of TC on the heterogeneous surface that exhibits a wide range distribution of adsorption energies of the desired GO/Fe3O4/bio-cellulose aerogel. The experimental findings demonstrate that the aerogel possesses the notable features of environmental friendliness, cost-effectiveness, and comparatively high TC adsorption capacity. Therefore, utilizing biomass to develop the structure of the magnetic GO-based composite aerogel is significantly promising for antibiotic-containing wastewater treatments.
1 Introduction
In recent years, water contamination with inorganic and organic pollutants derived from diverse industrial activities, agricultural practices, and domestic waste has become a severe global concern, jeopardizing aquatic biota and posing a direct threat to human health, such as through waterborne diseases.1–5 Noticeably, antibiotics have been overused in human medicine, animal husbandry, and aquaculture since the introduction of penicillin in 1928.6–8 The massive annual consumption of antibiotics worldwide results in the constant release into aquatic media, escalating water contamination.7,9 Tetracycline (TC) is one of the most commonly prescribed antibiotics owing to its potent antimicrobial properties.10–12 However, TC is only partially metabolized in the bodies of humans and animals, and its residue is mainly excreted into the environment through urine and feces.12–15 The tough degradation and eco-toxicity of this residue remaining in agricultural runoff and municipal sewage can cause accumulation and pollution in soil and water.11,16 Hence, removing TC from aqueous media is an imperative task for protecting and enhancing ecosystem and public health.9 There are numerous approaches to eliminate TC, such as membrane filtration, sludge treatment, adsorption, electrochemical routes, and advanced oxidation methods.7,9,10,17 In particular, adsorption is considered one of the simple, affordable, and manageable measures to separate contaminants from wastewater.9,18 Accordingly, a wide range of adsorbents, including carbonaceous materials,19–24 zeolites,25–27 magnetite nanoparticles,28–30 clay minerals,31–33 and polymeric resins34,35 have been investigated for the removal of TC. Among these materials, GO-based composite aerogel has been emerging as a promising adsorbent for the removal of various pollutants.36–38
The use of GO-based composites can do wonders for a wide range of benefits in wastewater treatments. GO is a commonly used derivative of graphene with the advantage of low-cost production compared to pristine graphene.5 Graphene is a single layer of carbon atoms bonded in a two-dimensional (2D) honeycomb lattice structure.39 GO has a similar structure to graphene with the presence of oxygen-containing functional groups, such as epoxy, hydroxyl, carbonyl, and carboxyl groups.40 GO has aroused widespread attention in pollution mitigation and environmental remediation due to its unique physicochemical properties, such as high mechanical and chemical stabilities, excellent electrical and thermal conductivity, large specific surface area, high optical transparency, low density, and flexibility to incorporate various materials.41 The presence of ample oxygen-containing functional groups in GO and its hydrophilic property allows an easy dispersion of this material in aqueous solutions and effective interactions with various water-soluble compounds, enabling GO to become a valuable material for adsorption applications.4,5,16,41 This characteristic, however, complicates the complete recovery of the material from aqueous media due to the formation of colloidal suspension.38,42 Moreover, using GO in various applications has faced difficulties arising from the phenomena of restacking and aggregation of 2D sheets, thereby reducing their activity and reusability.7,43,44 Thus, the development of three-dimensional (3D) materials such as foams or aerogels based on the 2D structure of GO has been designed to address these issues.7,45,46 The 2D sheets of GO are immobilized into 3D structures by forming interconnected networks, resulting in more stable, bulky, and porous materials.47,48 Therefore, this eases the handling and the regeneration of the materials while the hydrophilic feature is still retained for functionalities or other chemical interactions.49 Furthermore, the combination of magnetite and GO to produce magnetic GO-based composites is beneficial for a rapid separation from the matrix using an external magnetic field.50,51
To date, the aerogel forms of magnetic GO-based composites have been universally prioritized for the elimination of contaminants among 3D GO-based composite existences for a variety of reasons.42,43,52 Specifically, aerogel is an ultra-light 3D porous material with exceptional properties, such as an extremely low density, a huge porosity, and a vast specific surface area.53,54 These features facilitate the adsorption of diverse pollutants while flexibly incorporating various components to create purpose-driven multifunctional materials.2,55 GO is one of the most appropriate precursor materials to satisfy such features, based on its possession of rich hydrophilic functionalities.4 These functional groups can interact with various other hydrophilic agents through hydrogen bonding, π–π bonding, or electrostatic interactions to immobilize 2D sheets of GO and create 3D structured aerogel.5,41,55 The skeletons for building 3D aerogel can be sodium alginate,56 cellulose,2 and ethylene diamine.57 Among them, cellulose is usually employed by virtue of its abundance and rich functionalities.58
Cellulose can be harnessed from various natural resources, such as plants, bacteria, algae, and tunicates.59 Recently, biomass waste-derived cellulose has garnered significant interest in the development of eco-friendly and biocompatible fibers supporting 3D aerogel.60,61 This aligns with the principles of green chemistry and sustainable development in wastewater treatment practices.60 Repurposing these materials for adsorbent production contributes to sustainability by utilizing abundant resources instead of throwing them away, alleviating the environmental impact associated with waste disposal.62,63 Agro-waste materials such as banana peels are readily available in large quantities. Not only are banana peels one of the most abundant agro-waste worldwide, but they are also composed of hemicellulose, cellulose, and lignin, helping them become an ideal selection of inexpensive and bio-based adsorbents for wastewater treatment.61,64,65 The plentiful oxygen-containing functional groups in bio-cellulose provide extraordinary structure for developing 3D aerogel while expectedly upgrading the adsorption capacity.66
This study aims to integrate GO, magnetic Fe3O4, and bio-cellulose into an ultralight 3D composite aerogel using an ultrasound-assisted mechanical mixing method and freeze-drying technique for the removal of TC. This approach was expected to fully utilize the strengths of each component in the composite aerogel, including the magnetic property of Fe3O4 for easy separation of the aerogel after use, the skeletal property of bio-cellulose, and the potential adsorption sites of both GO and bio-cellulose.
2 Experimental
2.1 Chemicals and materials
Graphite powder (Gi, particle size < 20 μm) was procured from Sigma-Aldrich Co. Ltd in Germany. Potassium permanganate (KMnO4, 99%), sulfuric acid (H2SO4, 98%), phosphoric acid (H3PO4, 85%), iron(II) sulfate heptahydrate (FeSO4·7H2O), 99%), iron(III) chloride hexahydrate (FeCl3·6H2O, 99%), ammonia solution (NH4OH, 30%), hydrogen peroxide (H2O2, 30%), sodium hypochlorite (NaOCl, 30%), and ethanol (C2H5OH, 99%) were obtained from Xilong Scientific Co. Ltd in China and employed without additional purification. Cavendish banana peels were collected from the local markets in District 12, Ho Chi Minh City, Vietnam. Distilled water was used in the experiment.
2.2 Synthesis of GO suspension
GO was produced using the modified Hummers' method.67 In brief, 3 g of Gi was incrementally added to an acid mixture comprising 360 mL of 98% H2SO4 and 40 mL of 85% H3PO4 while being continuously stirred at a temperature below 20 °C. Next, 18.0 g of KMnO4 was slowly supplemented to the mixture, heated to 50 °C, and stirred continuously for 12 h. Subsequently, 500 mL distilled water and 15 mL H2O2 were gently added to the solution to cease the oxidation reactions. Centrifugation and washing with distilled water were carried out alternately until the neutral pH of the decanted water was obtained. The centrifugation was carried out at 6000 rpm on the Hettich EBA 21 centrifuge with a 6-place angle rotor. The resulting residue was subjected to drying at 60 °C for 24 h, yielding solid graphite oxide. This solid was then dissolved in distilled water at a concentration of 2 mg mL−1, followed by sonication at 360 W until obtaining the GO colloidal suspension.
2.3 Synthesis of magnetic Fe3O4
Fe3O4 particles were synthesized following the method detailed by Hoang et al.68 Briefly, 25 mL of 1.38 M Fe2+ solution and 25 mL of 2.76 M Fe3+ solution were combined to achieve the Fe2+
:
Fe3+ molar ratio of 1
:
2. Subsequently, ammonia solution 30% was added to the mixture until the pH reached 10.0. After stirring for 1 h, the resulting black precipitates were separated using an external magnet and rinsed thrice with distilled water. The synthesized Fe3O4 particles were then dried at 60 °C for 12 hours.
2.4 Isolation of cellulose from banana peels
The bio-cellulose was isolated from banana peels via alkali treatment and then acid hydrolysis.2,69 Banana peels were cut into small pieces and washed with distilled water. These small pieces were immersed into a 3 M NaOH solution and heated at 70 °C for 4 h to remove lignin and hemicellulose. Afterward, the pieces were filtered and washed with distilled water until they had a neutral pH. The remaining solid was bleached using 2% NaClO at 80 °C for 2 h. Subsequently, the bleached product was washed with distilled water and hydrolyzed with H2SO4 40% at 80 °C for 2 h, then rinsed with distilled water until reaching the neutral pH of the decanted water. The bio-cellulose was separated by centrifugation at 6000 rpm on the Hettich EBA 21 centrifuge with the 6-place angle rotor and stored in a refrigerator for further use.
2.5 Preparation of magnetic GO/Fe3O4/bio-cellulose aerogel
Magnetic Fe3O4 particles were dispersed in the GO colloidal suspension (2 mg mL−1) in an ultrasound bath for 30 min, in which the mass ratio of Fe3O4 to GO was 1
:
1.3 Subsequently, the bio-cellulose was added to the mixture with a double amount of GO mass under the sonication at 360 W for 30 min.2 The resulting mixture was then placed in a water bath at 90 °C for 6 h to yield GO/Fe3O4/bio-cellulose hydrogel and freeze-dried at −40 °C for 48 h to obtain the magnetic GO/Fe3O4/bio-cellulose aerogel.
2.6 Characterization
The functional groups of materials were identified through FTIR spectra analysis using Jasco FT/IR-6X spectrometer (Jasco, Tokyo, Japan) with ATR-FTIR mode, within the wavenumber range of 500–4000 cm−1. Raman spectroscopy was recorded at an excitation wavelength of 532 nm by Labram, Horiba spectroscopy. The crystalline structure of materials was examined using X-ray powder diffraction (D8 Advance X-ray diffractometer) with CuKα irradiation (λX = 0.154 nm) in the 2θ range of 5–80° (0.02° per second). The surface morphology of the materials and elemental mapping were monitored by FE-SEM (TESCAN MIRA3, Czech Republic) equipped with EDX (EDAX, AMETEK) at an accelerating electron voltage of 15.0–20.0 kV, capturing both top view and cross-section view. The specific surface area of materials was measured using the Brunauer–Emmett–Teller method (BET) with Micromeritics MicroActive for TriStar II Plus 2.03 surface area analyzer through N2 adsorption at 77.3 K, pretreated at 120 °C before measurement. The magnetic hysteresis loops were plotted by an in-house developed VSM system under ambient conditions.
2.7 Point of zero charge (pHpzc) determination
To determine the pHpzc of the magnetic GO/Fe3O4/bio-cellulose aerogel, the solid addition method was deployed based on the method of Hoang et al.70,71 Initially, a set of flasks containing 30 mL of 0.1 M KNO3 solution was prepared, with the initial pH (pHi) ranging from 3.0 to 9.0. The pH was adjusted using 0.1 M HCl and 0.1 M NaOH. Subsequently, 50 mg of the as-prepared aerogels was added and shaken at 150 rpm for 24 h until reaching equilibrium. The equilibrium pH (pHe) was recorded to determine the deviation compared to pHi, denoted as ΔpH = pHi – pHe. Finally, a plot of ΔpH as a function of pHi was constructed, and the pHpzc was measured at the intersection point between the axis (at ΔpH = 0) and the resulting curve.
2.8 Adsorption studies
Batch adsorption investigations were conducted to assess the efficiency of the magnetic GO/Fe3O4/bio-cellulose aerogel in removing TC from aqueous solutions. The experimental design involved a one-factor system in which the effect of one factor was investigated at different values while keeping constant for other factors. Specifically, 15 mg of each aerogel was prepared for immersing into Erlenmeyer flasks containing 30 mL TC solutions, meaning the solid-to-liquid ratio of 1
:
2. The solutions were then shaken at 160 rpm and at ambient temperature. After continuous shaking for a specific duration, the aerogels were collected by the external magnet, and the equilibrium TC concentration was determined via the analysis of UV-Vis spectra at 357 nm. The investigated factors and corresponding experimental conditions are outlined in Table 1. The adsorption capacity (qe, mg g−1) of the aerogels was calculated using eqn (1): |
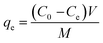 | (1) |
where C0 and Ce are the initial and equilibrium concentrations of TC (mg L−1), respectively; M is the aerogel mass (g); and V is the volume of TC solution (L).
Table 1 Experimental conditions in batch adsorption studies for TC removal
Factors |
Studied values |
Experimental conditions |
Adjusted by 0.1 M HCl and 0.1 M NaOH. |
pH |
3.0, 4.0, 5.0, 6.0, 7.0, 8.0, 9.0, 10.0 a |
Adsorbent dose: 0.5 g L−1 |
Initial TC concentration: 70 mg L−1 |
Adsorption time: 16 h |
Adsorbent dose (g L−1) |
0.50, 0.67, 0.83, 1.0, 1.17, 1.33 |
Solution pH: 5.0 |
Initial TC concentration: 70 mg L−1 |
Adsorption time: 16 h |
Adsorption kinetics |
Adsorption time (min) 5, 10, 20, 40, 120, 240, 360, 960 |
Solution pH: 5.0 |
Adsorbent dose: 0.5 g L−1 |
Initial TC concentration: 70 mg L−1 |
Adsorption isotherms |
Initial TC concentration (C0, mg L−1) 30, 50, 70, 110, 150, 200, 300, 350, 400 |
Solution pH: 5.0 |
Adsorbent dose: 0.5 g L−1 |
Adsorption time: 16 h |
Each experiment included a blank control and three replicates, with the final equilibrium concentration determined as the average of the three replicates.
3 Results and discussion
3.1 Characterization
Fig. 1 illustrates the FTIR spectra of Gi, GO, Fe3O4, bio-cellulose, GO/Fe3O4/bio-cellulose aerogel before and after the TC adsorption, and TC in the wavenumber range of 500–4000 cm−1. In comparison to the FTIR spectrum of Gi, that of GO displayed a number of vibrational features at around 3200, 1730, 1630, 1380, 1220, and 1050 cm−1, representing the plentiful functional groups of O–H (hydroxyl) stretching, C
O (carbonyl) stretching, and C
C stretching in aromatic structure, C–O–H bending, C–O–C (epoxy) stretching, and C–O stretching vibrations, respectively.43,72–74 The presence of the numerous oxygen-containing functionalities firmly proved that Gi was oxidized via the modified Hummers' method to produce GO. It is noticeable that both Gi and GO absorbed CO2 at the vibrational peak of 2350 cm−1,75–77 which also appeared in the FTIR spectra of the other samples. With respect to the FTIR spectrum of Fe3O4, a sharp and strong adsorption peak at 550 cm−1 was assigned to Fe–O stretching vibration of Fe3O4.3,78 This peak was also seen in the FTIR spectra of GO/Fe3O4/bio-cellulose aerogel, demonstrating the successful synthesis of Fe3O4 and its integration in the composite aerogel. For the FTIR spectra of bio-cellulose, vibrational modes at the adsorption band around 3340 cm−1 (O–H stretching) and the multiple intense peaks of 1160, 1107, and 1030 cm−1 were attributed to C–O–C and C–O bonds in the structural skeleton of cellulose, confirming the fruitful preparation of cellulose from banana peels.2,69 Additionally, the adsorption peak at approximately 2910 cm−1 was associated with C–H stretching vibration in the –CH2 group of cellulose.76,79 It is noteworthy that these vibrations in the FTIR spectrum of bio-cellulose were also observed on the FTIR spectrum of the GO/Fe3O4/bio-cellulose aerogel but with less intensity owing to its lower content in comparison to the pristine bio-cellulose. Thus, all observations were combined to conclude the successful preparation of GO/Fe3O4/bio-cellulose aerogel.
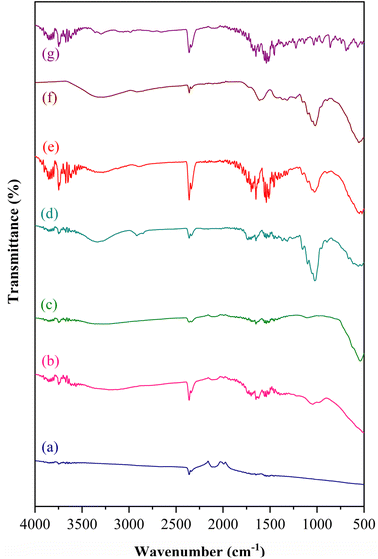 |
| Fig. 1 FTIR spectra of (a) Gi, (b) GO, (c) Fe3O4, (d) bio-cellulose, (e) GO/Fe3O4/bio-cellulose aerogel before the TC adsorption, (f) GO/Fe3O4/bio-cellulose aerogel after the TC adsorption, and (g) TC. | |
Fig. 2a demonstrates the Raman spectra of Gi, GO, and GO/Fe3O4/bio-cellulose aerogel, while those of Fe3O4 and bio-cellulose are displayed in Fig. 2b. Regarding carbonaceous materials in Fig. 2a, the G band at the Raman shift of 1592 cm−1 represented the in-plane vibration of the sp2-hybridized carbon atoms in the aromatic structure, while the D band at the Raman shift of 1342 cm−1 was assigned to the sp3-hybridized counterparts in disordered behaviors.80,81 The degree of defects could be determined via the intensity ratio of D band to G band (ID/IG), meaning that more structural disorders were stated when seeing an increment in the ratio.55,82 The ID/IG ratios of Gi and GO increased from 0.1 to 1.02, confirming that GO was obtained from Gi by the oxidation reactions. This ratio of GO/Fe3O4/bio-cellulose aerogel was 1.12, indicating that the GO in the composite aerogel had become more disordered.82 From Fig. 2b, the Raman spectrum of Fe3O4 was characterized at 683 cm−1, corresponding to the A1g mode of vibration, while the other peaks at 349 and 515 cm−1 were assigned to the T2g mode of vibration.83–85 With regard to the Raman spectrum of bio-cellulose, the peaks at the Raman shifts of 898, 1098, 1256, 1359, and 1570 cm−1 were ascribed to the conformation of cellulose.86,87 Consequently, the Raman spectra analysis emphasized the formation of GO, Fe3O4, bio-cellulose, and GO/Fe3O4/bio-cellulose, as aforementioned in the results of FTIR spectra.
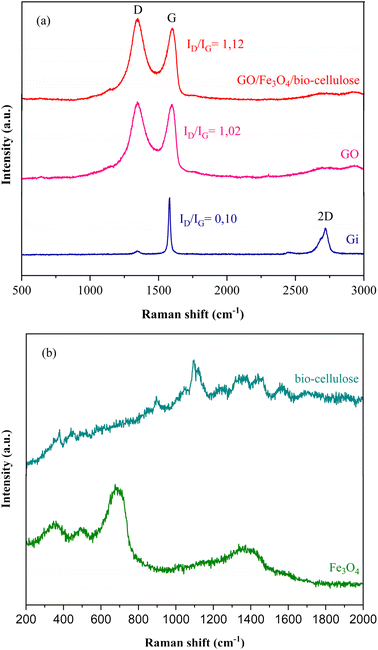 |
| Fig. 2 Raman spectra of (a) Gi, GO, GO/Fe3O4/bio-cellulose aerogel and (b) Fe3O4, bio-cellulose. | |
The crystal structure of the synthesized materials was determined using XRD. Fig. 3 depicts the XRD patterns of Gi, GO, Fe3O4, bio-cellulose, GO/Fe3O4/bio-cellulose aerogel before the TC adsorption, and GO/Fe3O4/bio-cellulose aerogel after the TC adsorption in the diffraction angle 2θ range of 5–80°. As can be seen, there was a translation from the characteristic diffraction peak of Gi at 2θ of 26.65° to that of GO at 2θ of 11.57°, corresponding to the change of (002) crystal plane into (001) crystal plane, respectively. This signified the formation of GO was obtained by the oxidation of Gi.80,88 The XRD analysis of Fe3O4 confirmed that diffraction peaks characterized at 2θ of 30.42°, 35.78°, 43.60°, 57.37°, and 62.96° were ascribed to (220), (311), (400), (511), and (440) crystal planes of Fe3O4 nanoparticles,89–91 which was in agreement with the literature of JCPDS no. 19-0629 for the standard XRD patterns of magnetite.85 These peaks were also identified in the XRD pattern of the magnetic GO/Fe3O4/bio-cellulose aerogel, proving the incorporation of Fe3O4 in the composite aerogel.3 Regarding the XRD pattern of bio-cellulose, diffraction peaks anchored at 2θ of 15.34° and 21.93°, corresponding to (110) and (200) crystal planes, respectively, were characteristic peaks of cellulose.69,79 These diffraction peaks of cellulose were found in the XRD pattern of the GO/Fe3O4/bio-cellulose aerogel but appeared more broadened compared to that of bio-cellulose, possibly signifying the its interaction with GO in the composite aerogel.2,92 The XRD results were consistent with the FTIR and Raman analyses to confirm the successful syntheses of GO, Fe3O4, bio-cellulose, and GO/Fe3O4/bio-cellulose aerogel.
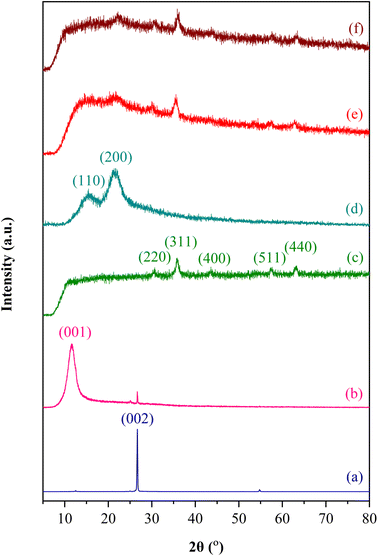 |
| Fig. 3 XRD patterns of (a) Gi, (b) GO, (c) Fe3O4, (d) bio-cellulose, (e) GO/Fe3O4/bio-cellulose aerogel before the TC adsorption, and (f) GO/Fe3O4/bio-cellulose aerogel after the TC adsorption. | |
The surface morphology of GO, Fe3O4, bio-cellulose, and GO/Fe3O4/bio-cellulose aerogel was monitored using FE-SEM (Fig. 4). The FE-SEM images of GO consisted of homogeneous thin layers with many wrinkles on the surface at both top view (Fig. 4b and h) and cross-section view (Fig. 4e), which is assumed to enlarge the surface area of GO sheets.55,93,94 This also confirmed that graphite oxide was exfoliated by the sonication to produce the layers of GO.73,95 For the FE-SEM images of bio-cellulose, it was witnessed as a stratified laminar structure of film-like layers on the top view (Fig. 4c) image or fiber-shaped bundles on the cross-section view counterpart (Fig. 4f), which could be due to the integration of cellulose nanofibers during preparation processes.96–98 Fig. 4g showed the spherical shape of Fe3O4 particles aggregated together because of their magnetic interactions.99 For the FE-SEM images of GO/Fe3O4/bio-cellulose aerogel, the well-assembled and interconnected structure could be observed on the top view image (Fig. 4a), and especially on the cross-section view image (Fig. 4d). The blending of GO sheets with the skeletal structure of cellulose might strengthen the structure of the magnetic GO/Fe3O4/bio-cellulose composite aerogel.
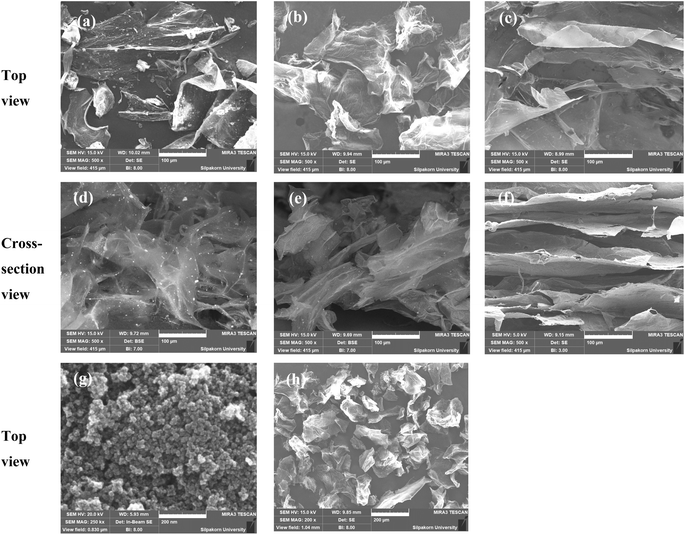 |
| Fig. 4 FE-SEM top view images of (a) GO/Fe3O4/bio-cellulose aerogel, (b) and (h) GO, (c) bio-cellulose, (g) Fe3O4, and FE-SEM cross-section view images of (d) GO/Fe3O4/bio-cellulose aerogel, (e) GO, (f) bio-cellulose at different magnifications. | |
EDX elemental mapping was employed to track the scattering of elements in the composite (Fig. 5). The intensities associated with C, O, Fe, and Cl elements in the EDX spectrum were identified. Accordingly, C and O elements were anchored densely and uniformly throughout the surface of GO/Fe3O4/bio-cellulose aerogel, proving the abundance of the oxygen-containing functional groups. The existence of a negligible amount of Cl could be observed in the EDX spectrum, which was attributable to the use of NaClO during the bleaching treatment of bio-cellulose.100 The EDX mapping of Fe revealed the highly dispersed Fe3O4 attached to the aerogel, allowing the convenient separation of solid materials from aqueous media.
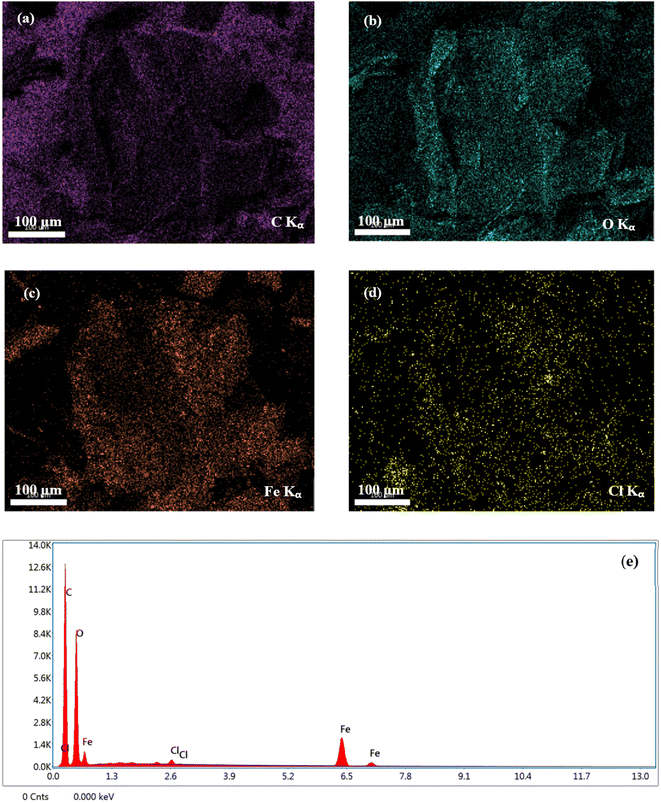 |
| Fig. 5 Elemental mapping images of (a) C, (b) O, (c) Fe, and (d) Cl; (e) EDX spectrum of GO/Fe3O4/bio-cellulose aerogel. | |
The specific surface areas of the GO, bio-cellulose, and GO/Fe3O4/bio-cellulose aerogel were determined using the BET method, yielding values of 40.1, 24.4, and 36.8 m2 g−1, respectively. The obtained surface area of the composite aerogel in this study is similar to those of the hybrid GO/microcrystalline cellulose aerogel reported by Wei X. et al.101 The intermediate value of the specific surface area of the composite aerogel compared to the components indicated the incorporation of bio-cellulose and GO sheets in the final product.
The magnetic property of GO/Fe3O4/bio-cellulose aerogel was compared with that of pristine Fe3O4. As shown in Fig. 6, the nearly zero values of magnetic remanence and coercivity of both hysteresis curves demonstrated their superparamagnetic property.102 The saturation magnetization parameter (Ms) of Fe3O4 was 61.8 emu g−1, while that of the composite was 16.2 emu g−1. This lower saturation magnetization of the composite aerogel could be attributed to the non-magnetic phases of GO or bio-cellulose, yet that value was strong enough to separate the aerogel after use.
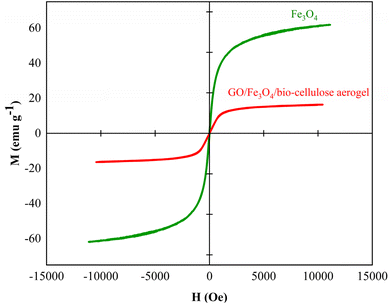 |
| Fig. 6 Magnetization hysteresis curve of Fe3O4 and the GO/Fe3O4/bio-cellulose aerogel. | |
3.2 Adsorption studies
3.2.1 Effect of solution pH. The ionization level of the surface functional groups of materials can be governed by adjusting the solution, consequently determining their adsorption capacity.103 The speciation of TC is also dependent on solution pH since its pKa1, pKa2, and pKa3 values are 3.3, 7.7, and 9.7, respectively.104 When the solution pH is between 3.3 and 7.7, TC exists as a zwitterionic species. At pH below 3.3, TC predominates in a cationic form (TCH3+), while negatively charged species (TCH− and TC2−) are found when pH is above 7.7. In order to study the effect of the solution pH on the adsorption performance of the aerogel, the adsorption processes were carried out at the initial pH values ranging from 3.0 to 10.0. As illustrated in Fig. 7a, the adsorption performance of the aerogel in eliminating TC witnessed a remarkable improvement with the increment of pH from 2.0 to 5.0. It is noticeable that there was no statistically significant difference in the adsorption capacity of the aerogel at pH 5.0 and pH 6.0 (t-test, P = 0.23) with a 95% confidence interval (α = 0.05). When the pH rose from 6.0 to 10.0, the adsorption capacity had a downward tendency. To elucidate these results, the determination of the pHpzc of the aerogel was conducted, revealing the pHpzc value of 3.5 (Fig. 7b). This finding indicates that the surface of the aerogel was negatively charged at pH over 3.5 and positively charged at pH below 3.5. The effect of solution pH on adsorption capacity could be then ascribed to the electrostatic interaction between the charged surface of the aerogel and different forms of TC. At pH below 3.5, the electrostatic repulsion between the cationic form of TC and positively charged aerogel caused the low adsorption capacity. When the pH reached 5.0, TC transferred to the zwitterionic form (TCH2±).104 The electrostatic attraction between the positive charge of TC and the negative charge of the aerogel surface turned out to be preferable, thereby enhancing the adsorption capacity. It is worth noting that the zwitterion existed at maximum concentration in the pH range of 5.0–6.0,104 leading to the highest adsorption capacity of TC at this pH range. When the pH increased from 6.0 to 10.0, the formation of anionic TC (TCH− and TC2−) promoted the electrostatic repulsion between these anions and the negatively charged surface of the aerogel. As a result, a reduction in the adsorption capacity was attained. From all the results, the initial pH of 5.0 was selected for subsequent adsorption experiments.
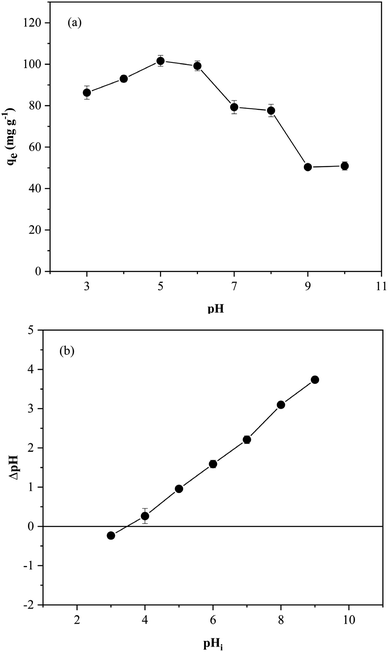 |
| Fig. 7 (a) Effect of pH on TC adsorption, and (b) point of zero charge of GO/Fe3O4/bio-cellulose aerogel. | |
3.2.2 Effect of adsorbent dose. Fig. 8 displays the effect of the adsorbent dose on the removal of TC. It can be observed that the adsorption capacity of the aerogel showed a drastic decline from the peak value of 101.6 ± 2.6 mg g−1 at a dose of 0.50 g L−1 to the bottom of 51.7 ± 0.02 mg g−1 at a dose of 1.33 g L−1. These results could be assigned to the agglomeration of the materials at high doses, resulting in a significant obstruction of available active sites.105–107 Notably, the noteworthy adsorption capacity at a low adsorbent dose demonstrated the promising adsorption performance of the aerogel in far-reaching applications. This not only lowers the cost of adsorption but also mitigates the risk of secondary pollution associated with the excess use of adsorbent in the treatment process.108 Therefore, the adsorbent dose for the TC removal was established at 0.5 g L−1 for further experiments.
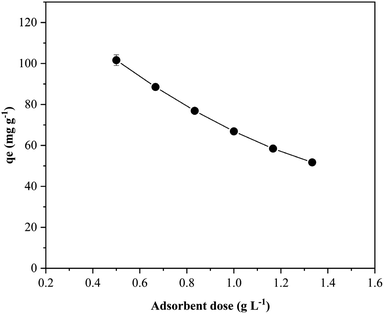 |
| Fig. 8 Effect of the adsorbent dose on TC adsorption capacity. | |
3.2.3 Adsorption kinetics. The investigation of adsorption kinetics of a specific adsorbent/adsorbate system is necessary to provide the information of kinetic parameters for the design of adsorption processes on studied materials.105,109 The adsorption of the aerogel was therefore carried out at different contact times, ranging from 5 to 960 min. As depicted in Fig. 9, the adsorption capacity increased significantly with the extension of contact time from 5 to 120 min and followed by a slower increase between 120 and 960 min. The experimental data were subsequently examined through three distinct non-linear kinetic models, encompassing the pseudo-first-order, pseudo-second-order, and Elovich.110–112 The equations and non-linear graphs for each model are detailed in Table 2 and illustrated in Fig. 9, respectively. The corresponding parameters are also presented in Table 2. The experimental kinetic data in this study displayed the best fit with the Elovich model, with the highest regression coefficient (R2 = 0.991). The initial rate of the adsorption process determined by this model was found to be 0.89 g g−1 min−1. After the initial stage with a high adsorption rate, the rate decreased over time due to an increase in occupied surface sites.113,114 This is contributed by the assumption of the model that the adsorption process occurs on the heterogeneous surfaces of materials where different surface sites have different adsorption energies.112,113 The surface heterogeneity is intrinsic to composite materials like the magnetic GO/Fe3O4/bio-cellulose composite aerogel in this study, which consists of different components possessing different chemical functionalities and surface characteristics. The organic pollutant tended to be quickly adsorbed on favorable sites or high-energy sites, leading to a rapid adsorption rate. The remaining low-energy sites were then occupied, which slowed down the adsorption rate over time.
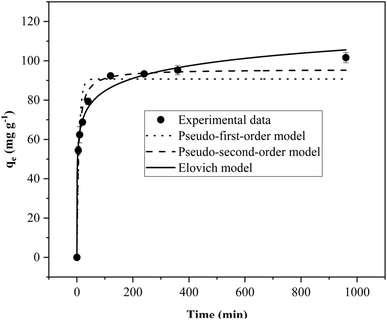 |
| Fig. 9 Non-linear kinetic models for the TC adsorption onto the GO/Fe3O4/bio-cellulose aerogel. | |
Table 2 Kinetic parameters for the TC adsorption onto the GO/Fe3O4/bio-cellulose aerogela
Kinetic models and corresponding equations |
Kinetic model parameters and regression coefficients |
qe/qt (mg g−1): adsorption capacity at equilibrium/at time t; k1 (min−1)/k2 (g mg−1 min−1): the respective rate constants of kinetics models; α (g g−1 min−1): initial sorption rate of the Elovich model; β (g mg−1): the Elovich constant. |
Pseudo-first-order |
k1 (min−1) |
qe (mg g−1) |
R2 |
qt = qe (1 − exp(−k1t)) |
0.12 |
90.7 |
0.920 |
Pseudo-second-order |
k2 (g mg−1 min−1) |
qe (mg g−1) |
R2 |
 |
0.002 |
95.7 |
0.977 |
Elovich |
α (g g−1 min−1) |
β (g mg−1) |
R2 |
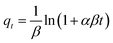 |
0.89 |
0.11 |
0.991 |
3.2.4 Adsorption isotherms. The equilibrium performance of the adsorbents was investigated by carrying out the adsorption isotherm experiments. Four popular non-linear isotherm models, including Langmuir,115 Freundlich,116 Sips,117 and Temkin,118 were used to analyze the experimental equilibrium data. The impact of the initial TC concentration on the adsorption capacity, along with the non-linear graphs of the three adsorption isotherm models, are illustrated in Fig. 10. As the initial TC concentration increased, the adsorption capacity also showed an enhancement. The equations of the studied models and the calculated parameters are provided in Table 3. Based on the correlation coefficient (R2) values, it is clear that the Sips and Freundlich were the most appropriate models for the experimental data. The Freundlich model describes multilayer adsorption that happens with heat and affinities scattering over a heterogeneous surface.119,120 The Freundlich constant (1/n) represents the adsorption intensity, heterogeneity factor, and the heterogeneity of site energies.120,121 According to Tseng et al.,121 the favorable adsorption level can be inferred by this constant (Table 4). The 1/n value obtained in this study was found to be 0.21, indicating the favorable adsorption of TC on the heterogeneous surface of the desired GO/Fe3O4/bio-cellulose aerogel. The Sips isotherm model is a combination of Freundlich and Langmuir expressions.122 The Sips constant (n) represents the degree of surface heterogeneity of adsorbents and characteristics of adsorption processes. When n reaches 1, the Sips model reduces to Langmuir isotherm model with the assumption of monolayer adsorption on a homogeneous surface.123 On the other hand, it resembles the Freundlich isotherm model when n deviates from 1, which accounts for the adsorption on heterogeneous surface with different adsorption site energies. In this study, it can be observed that the Sips constant (n = 0.23) is much lower than 1, which is Freundlich-like behavior.123 This is in good agreement with the findings when fitting experiment data with individual Langmuir and Freundlich models. Moreover, it is worth mentioning that the findings from the study of adsorption isotherm were consistent with those from the adsorption kinetics, confirming that the adsorption of TC occurred on the heterogeneous surface of GO/Fe3O4/bio-cellulose composite aerogel with a wide distribution of adsorption site energies.
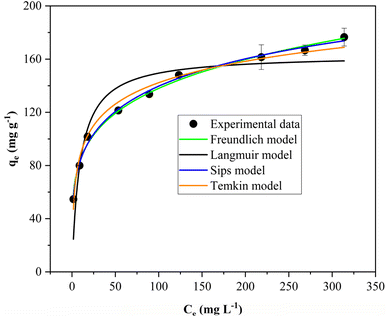 |
| Fig. 10 Non-linear isotherm plots for the TC adsorption onto the GO/Fe3O4/bio-cellulose aerogel. | |
Table 3 Isotherm parameters for the TC adsorption onto the GO/Fe3O4/bio-cellulose aerogela
Isotherm models and corresponding equations |
Adsorption isotherm model parameters |
qe: equilibrium adsorption capacity; nF: the Freundlich constant; Ce: equilibrium concentration of adsorbate; KF: a Freundlich constant related to adsorption capacity; qm: maximum adsorption capacity of adsorbent; KL: Langmuir constant related to energy of adsorption; bS: Sips constant; nS: the heterogeneity factor; bT: Temkin constant; AT: Temkin isotherm constant. |
Freundlich |
|
KF (mg g−1) |
1/nF |
R2 |
 |
|
52.3 |
0.21 |
0.994 |
Langmuir |
qm (mg g−1) |
KL (L mg−1) |
|
R2 |
 |
163.4 |
0.11 |
0.863 |
Sips |
qm (mg g−1) |
bs (mg −1/n.L−1/n) |
nS |
R2 |
 |
238.7 |
0.001 |
0.23 |
0.995 |
Temkin |
|
bT (kJ mol−1) |
AT (L mg−1) |
R2 |
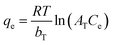 |
|
0.11 |
4.6 |
0.983 |
Table 4 Freundlich favorable parameters121
1/n |
Favorable level |
1/n < 0.01 |
Pseudo-irreversible |
0.01 < 1/n < 0.1 |
Strong favorable |
0.1 < 1/n < 0.5 |
Favorable |
0.5 < 1/n < 1 |
Pseudo-linear |
1/n = 1 |
Linear |
1/n > 1 |
Unfavorable |
The maximum adsorption capacity obtained from the Sips isotherm model in this study was compared to other similar reported adsorbents (Table 5). It is apparent that the synthesized composite aerogel offers a comparable adsorption capacity to other adsorbents previously reported. Considering that banana peels are one of the most abundant agro-wastes worldwide, there is a great possibility of developing potentially valuable material derived from this agricultural waste for the removal of antibiotics from aqueous media. Furthermore, the composite aerogel obtained in this study offers the advantage of a convenient separation using external magnetic fields.
Table 5 Comparison of maximum adsorption capacity (qm) according to the Sips isotherm model for tetracycline removal using bio-based adsorbent
Biochar-based adsorbents |
qm (mg g−1) |
Reference |
Fe3O4/coffee residue composite |
179.85 |
124 |
Iron- and nitrogen-modified walnut shell-based biochar |
238.94 |
125 |
Sludge-bamboo biochar |
122.68 (308 K) |
126 |
Graphene oxide loaded with titanium dioxide composites |
173.44 |
127 |
Magnetic graphene oxide nanocomposite modified with polyvinylpyrrolidone |
193.8 (308 K) |
128 |
Magnetic graphene oxide/Fe3O4/banana peel-derived cellulose composite aerogels |
238.7 |
This study |
3.2.5 Adsorption mechanism. To study the adsorption mechanism, the FTIR spectrum and XRD pattern of the GO/Fe3O4/bio-cellulose aerogel after being used for the TC adsorption were measured and presented in Fig. 1f and 3f, respectively. With respect to the XRD patterns in Fig. 3, the XRD pattern of the aerogel after being used was similar to that of the original aerogel, indicating the crystalline structure of the aerogel was maintained during the adsorption process. This implied that the adsorption occurred on the surface or within the porous structure of the aerogel. As shown from the FTIR spectrum of TC in Fig. 1g, the adsorption peaks at around 3300 cm−1 (O–H), 1654 cm−1 (C
O), 1620 cm−1 (N–H primary amine), 1530 cm−1 (C
C), 1450 cm−1 (C–N), 1350 cm−1 (C–O in the amide group), and 1030 cm−1 (NH2 amino group) were assigned to the vibrational features of TC.129–132 In comparison to the FTIR spectra of the GO/Fe3O4/bio-cellulose aerogel before the TC adsorption, the presence of the additional vibrations around 1620, 1450, and 1350 cm−1 in that of the aerogel after the TC adsorption could be ascribed to the existence of TC. This confirmed that TC was adsorbed by the GO/Fe3O4/bio-cellulose aerogel. Moreover, it is worth noting that a translation was observed in the absorption band of aromatic C
C of the aerogel before (1630 cm−1) and after (1595 cm−1) the adsorption process. This could deduce that the aromatic C
C with π electrons of TC could create π–π interactions with the aromatic rings in the aerogel.130In addition to FTIR and XRD characterizations, based on the results obtained regarding the effect of the solution pH, the adsorption was found to be preferable at the solution pH that promoted the electrostatic attraction between the charged site of TC and the charged surface of the aerogel. Hence, the major mechanism proposed in this study is electrostatic interactions. It is worth noting that the TC removal also took place at low pH values, which advocated the electrostatic repulsion despite low adsorption performance. Therefore, there was a potential for TC to interact with the aerogel through the pore-filling effect. Additionally, hydrogen bonds are associated with the origin of numerous physicochemical properties of compounds containing N and O elements.133,134 From all the results collected from this study, a proposed adsorption mechanism of TC onto the magnetic GO/Fe3O4/bio-cellulose aerogels is depicted in Fig. 11. Potential interactions may involve the electrostatic interactions, hydrogen bonds, the pore-filling effects, and π–π interactions between the magnetic GO/Fe3O4/bio-cellulose aerogel and TC.
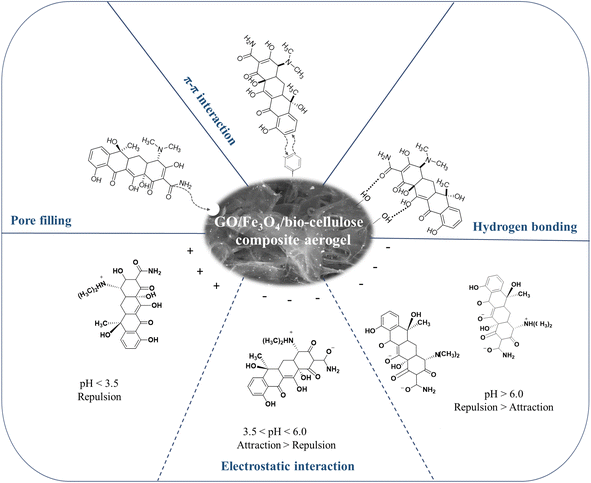 |
| Fig. 11 Proposed mechanism of the TC adsorption onto the GO/Fe3O4/bio-cellulose aerogel. | |
4 Conclusions
The characterization results demonstrate that the magnetic GO/Fe3O4/bio-cellulose aerogel was successfully synthesized using the ultrasound-assisted mechanical mixing method and freeze-drying technique. Remarkably, the aerogel could be simply prepared using cellulose isolated from abundant banana peels and GO, with the aim of promoting adsorption performance. The VSM findings confirmed the magnetism of the aerogels, paving the way for convenient separation of the material from aqueous media after the adsorption experiments. The effects of solution pH and adsorbent dose on the adsorption capacity, along with the comprehensive elaborations of adsorption kinetics, isotherms, and mechanisms, were thoroughly elucidated in this study. The adsorption studies proved the promising potential of the magnetic GO/Fe3O4/bio-cellulose aerogel for TC removal. Subsequent studies focusing on the treatment of practical antibiotics-containing wastewater will probably be essential to completely assess the adsorption performance of the magnetic GO/Fe3O4/bio-cellulose composite aerogel.
Data availability
The data used to support the findings of this study are included within the manuscript.
Conflicts of interest
The authors declare that there are no competing interests that could have appeared to influence the work reported in this paper.
Acknowledgements
The authors declare that no funds or grants were received during the preparation of this manuscript.
References
- N. C. Joshi and P. Gururani, Curr. Res. Green Sustainable Chem., 2022, 5, 100306 CrossRef CAS.
- P. Joshi, O. P. Sharma, S. K. Ganguly, M. Srivastava and O. P. Khatri, J. Colloid Interface Sci., 2022, 608, 2870–2883 CrossRef CAS PubMed.
- A. Dang, Y. Wang, Y. Liu, T. Cheng, A. Zada, F. Ye, W. Deng, Y. Sun, T. Zhao and T. Li, J. Hazard. Mater., 2023, 457, 131846 CrossRef CAS PubMed.
- L. Zhang, X. Li, S. Chen, J. Guan, Y. Guo and W. Yu, Catal. Commun., 2023, 176, 106627 CrossRef CAS.
- N. Baig, M. Sajid and T. A. Saleh, J. Environ. Manage., 2019, 244, 370–382 CrossRef CAS PubMed.
- F. Wei, Q. Ren, H. Zhang, L. Yang, H. Chen, Z. Liang and D. Chen, RSC Adv., 2021, 11, 9977–9984 RSC.
- Y. Kong, Y. Zhuang, K. Han and B. Shi, Colloids Surf., A, 2020, 588, 124360 CrossRef CAS.
- Y. Zhao, Q. E. Yang, X. Zhou, F.-H. Wang, J. Muurinen, M. P. Virta, K. K. Brandt and Y.-G. Zhu, Crit. Rev. Environ. Sci. Technol., 2021, 51, 2159–2196 CrossRef CAS.
- M. Beiranvand, S. Farhadi and A. Mohammadi-Gholami, RSC Adv., 2022, 12, 34438–34453 RSC.
- G. Gopal, S. A. Alex, N. Chandrasekaran and A. Mukherjee, RSC Adv., 2020, 10, 27081–27095 RSC.
- L. Xu, H. Zhang, P. Xiong, Q. Zhu, C. Liao and G. Jiang, Sci. Total Environ., 2021, 753, 141975 CrossRef CAS PubMed.
- Y. Dai, M. Liu, J. Li, S. Yang, Y. Sun, Q. Sun, W. Wang, L. Lu, K. Zhang and J. Xu, Sep. Sci. Technol., 2020, 55, 1005–1021 CrossRef CAS.
- Q. Liao, H. Rong, M. Zhao, H. Luo, Z. Chu and R. Wang, Sci. Total Environ., 2021, 757, 143981 CrossRef CAS PubMed.
- J. Leichtweis, Y. Vieira, N. Welter, S. Silvestri, G. L. Dotto and E. Carissimi, Process Saf. Environ. Prot., 2022, 160, 25–40 CrossRef CAS.
- A. Balakrishnan, M. Chinthala, R. K. Polagani and D.-V. N. Vo, Environ. Res., 2023, 216, 114660 CrossRef CAS PubMed.
- M. Minale, Z. Gu, A. Guadie, D. M. Kabtamu, Y. Li and X. Wang, J. Environ. Manage., 2020, 276, 111310 CrossRef CAS PubMed.
- C. Zhao, J. Ma, Z. Li, H. Xia, H. Liu and Y. Yang, RSC Adv., 2020, 10, 5066–5076 RSC.
- J. Li, J. Tao, C. Ma, J. Yang, T. Gu and J. Liu, RSC Adv., 2020, 10, 42038–42053 RSC.
- D. Morales-Serrato, J. Torres-Pérez, Á. de Jesús Ruíz-Baltazar and S. Y. Reyes-López, Int. J. Res. GRANTHAALAYAH, 2021, 9, 446–491 Search PubMed.
- O. A. Ajala, S. O. Akinnawo, A. Bamisaye, D. T. Adedipe, M. O. Adesina, O. A. Okon-Akan, T. A. Adebusuyi, A. T. Ojedokun, K. A. Adegoke and O. S. Bello, RSC Adv., 2023, 13, 4678–4712 RSC.
- M. A. Islam, B. Hameed, M. Ahmed, W. Khanday, M. A. Khan and F. Marrakchi, Biomass Convers. Biorefin., 2023, 13, 13153–13162 CrossRef CAS.
- J. Yang, Y. Dou, H. Yang and D. Wang, Appl. Surf. Sci., 2021, 538, 148110 CrossRef CAS.
- P. T. T. Ninh, N. D. Dat, M. L. Nguyen, N. T. Dong, H.-P. Chao and H. N. Tran, Environ. Res., 2023, 218, 114927 CrossRef CAS PubMed.
- J. Miao, F. Wang, Y. Chen, Y. Zhu, Y. Zhou and S. Zhang, Appl. Surf. Sci., 2019, 475, 549–558 CrossRef CAS.
- J. W. P. Lye, N. Saman, A. M. M. Noor, S. S. Mohtar, N. S. Othman, S. S. N. Sharuddin, H. Kong and H. Mat, Chem. Eng. Technol., 2020, 43, 1285–1296 CrossRef CAS.
- S. Al-Salihi, M. M. Fidalgo and Y. Xing, ACS ES&T Water, 2023, 3, 838–847 Search PubMed.
- F. K. Mostafapour, M. Yilmaz, A. H. Mahvi, A. Younesi, F. Ganji and D. Balarak, Desalin. Water Treat., 2022, 247, 216–228 CrossRef CAS.
- G. Yang, Q. Gao, S. Yang, S. Yin, X. Cai, X. Yu, S. Zhang and Y. Fang, Chemosphere, 2020, 239, 124831 CrossRef CAS PubMed.
- M. Foroughi, M. H. A. Azqhandi and S. Kakhki, J. Hazard. Mater., 2020, 388, 121769 CrossRef CAS PubMed.
- L. Vazirova and G. Abbasova, Adv. Sci. Technol., 2024, 148, 13–19 Search PubMed.
- A. Maged, J. Iqbal, S. Kharbish, I. S. Ismael and A. Bhatnagar, J. Hazard. Mater., 2020, 384, 121320 CrossRef CAS PubMed.
- J. Shang, M. Huang, L. Zhao, P. He, Y. Liu, H. Pan, S. Cao and X. Liu, ACS Omega, 2023, 9, 692–699 CrossRef PubMed.
- M. I. Al-Wabel, M. Ahmad, A. R. Usman, A. S. Sallam, Q. Hussain, R. B. Binyameen, M. R. Shehu and Y. S. Ok, J. Hazard. Mater., 2020, 384, 121500 CrossRef CAS PubMed.
- W. Wang, Z. Zhu, M. Zhang, S. Wang and C. Qu, J. Taiwan Inst. Chem. Eng., 2020, 106, 130–137 CrossRef CAS.
- Y. Zhu, J. Shen, M. Guo, H. Zheng and Y. Cao, Environ. Sci. Pollut. Res., 2023, 30, 27315–27327 CrossRef CAS PubMed.
- S. K. Sharma, P. Ranjani, H. Mamane and R. Kumar, Sci. Rep., 2023, 13, 16448 CrossRef CAS PubMed.
- E. Tao, D. Ma, S. Yang and X. Hao, J. Alloys Compd., 2020, 832, 154833 CrossRef CAS.
- P. Joshi, A. Raturi, M. Srivastava and O. P. Khatri, J. Environ. Chem. Eng., 2022, 10, 108597 CrossRef CAS.
- A. K. Geim and K. S. Novoselov, Nat. Mater., 2007, 6, 183–191 CrossRef CAS.
- M. S. Iqbal, A. A. Aslam, R. Iftikhar, M. Junaid, S. M. Imran, M. S. Nazir, Z. Ali, M. Zafar, A. Kanwal and N. K. Othman, J. Water Process Eng., 2023, 53, 103809 CrossRef.
- D. R. Rout, H. M. Jena, O. Baigenzhenov and A. Hosseini-Bandegharaei, Sci. Total Environ., 2023, 863, 160871 CrossRef CAS PubMed.
- N. H. Dang, T. H. Tu, V. N. P. Linh, L. T. M. Thy, H. M. Nam, M. T. Phong and N. H. Hieu, Synth. Met., 2019, 255, 116106 CrossRef.
- X. Hao, S. Yang, E. Tao, L. Liu, D. Ma and Y. Li, J. Alloys Compd., 2022, 923, 166335 CrossRef CAS.
- H. Zhang, X. Liu, B. Wang, Z. Shi, Z. Wei, Z. Wu, Y. Zhu, Q. Guo and X. Wang, Chem. Eng. J., 2023, 465, 142943 CrossRef CAS.
- Q. Wu, W. Wu, X. Zhan and X. Hou, New J. Chem., 2020, 44, 10654–10661 RSC.
- D. B. Thinh, T. H. Tu, N. M. Dat, T. T. Hong, P. T. N. Cam, D. N. Trinh, H. M. Nam, M. T. Phong and N. H. Hieu, Surf. Interfaces, 2021, 26, 101309 CrossRef.
- L. Lentz, D. A. Mayer, M. Dogenski and S. R. S. Ferreira, Mater. Chem. Phys., 2022, 283, 125981 CrossRef CAS.
- A. Masud, C. Zhou and N. Aich, Environ. Sci.: Nano, 2021, 8, 399–414 RSC.
- J.-b. Huo, G. Yu and J. Wang, Chemosphere, 2021, 278, 130492 CrossRef CAS PubMed.
- Y. He, C. Yi, X. Zhang, W. Zhao and D. Yu, TrAC, Trends Anal. Chem., 2021, 136, 116191 CrossRef CAS.
- D. Qiao, Z. Li, J. Duan and X. He, Chem. Eng. J., 2020, 400, 125952 CrossRef CAS.
- N. Shah, T. Rehan, X. Li, H. Tetik, G. Yang, K. Zhao and D. Lin, RSC Adv., 2021, 11, 7187–7204 RSC.
- P. M. Tu, T. H. Lin, T. Q. Thang, D. N. C. Vy, C. V. Lam, N. T. Son, M. T. Phong and N. H. Hieu, J. Mol. Struct., 2023, 1287, 135737 CrossRef CAS.
- V. T. Nguyen, L. Q. Ha, L. C. T. Van, P. T. B. Huynh, D. M. Nguyen, V. P. Nguyen, T. H. Tran and D. Hoang, J. Environ. Chem. Eng., 2023, 11, 109523 CrossRef CAS.
- H. Dan, N. Li, X. Xu, Y. Gao, Y. Huang, M. Akram, W. Yin, B. Gao and Q. Yue, Sci. Total Environ., 2020, 739, 139983 CrossRef CAS PubMed.
- C. Ji, S. Yang, E. Tao, Y. Cheng, X. Hao and Y. Li, J. Environ. Chem. Eng., 2021, 9, 106819 CrossRef CAS.
- T. T. P. N. X. Trinh, T. H. Quan, T. N. M. Anh, D. B. Thinh, N. T. Lan, D. N. Trinh, N. M. Dat, H. M. Nam, M. T. Phong and N. H. Hieu, Surf. Interfaces, 2021, 23, 101023 CrossRef CAS.
- B. El Allaoui, H. Benzeid, N. Zari and R. Bouhfid, J. Drug Delivery Sci. Technol., 2023, 104899 CrossRef CAS.
- H. Seddiqi, E. Oliaei, H. Honarkar, J. Jin, L. C. Geonzon, R. G. Bacabac and J. Klein-Nulend, Cellulose, 2021, 28, 1893–1931 CrossRef CAS.
- S. S. Jayan, J. S. Jayan and A. Saritha, Int. J. Biol. Macromol., 2023, 125928 CrossRef CAS PubMed.
- A. H. Hashem, E. Saied and M. S. Hasanin, Sustainable Chem. Pharm., 2020, 18, 100333 CrossRef.
- S. Mishra, P. S. Kharkar and A. M. Pethe, Carbohydr. Polym., 2019, 207, 418–427 CrossRef CAS PubMed.
- B. Yu, X. Zeng, L. Wang and J. M. Regenstein, Carbohydr. Polym., 2021, 254, 117415 CrossRef CAS PubMed.
- B. Ameha, T. T. Nadew, T. S. Tedla, B. Getye, D. A. Mengie and S. Ayalneh, RSC Adv., 2024, 14, 3675–3690 RSC.
- V. S. Munagapati, J.-C. Wen, C.-L. Pan, Y. Gutha, J.-H. Wen and G. M. Reddy, Int. J. Phytorem., 2020, 22, 267–278 CrossRef CAS PubMed.
- M. Imran, A. Islam, M. U. Farooq, J. Ye and P. Zhang, Environ. Sci. Pollut. Res., 2020, 27, 43493–43504 CrossRef CAS.
- N. Zaaba, K. Foo, U. Hashim, S. Tan, W.-W. Liu and C. Voon, Procedia Eng., 2017, 184, 469–477 CrossRef CAS.
- T. T. T. Le Hoang, F. Unob, S. Suvokhiaw and N. Sukpirom, J. Environ. Chem. Eng., 2020, 8, 103653 CrossRef.
- S. Mishra, B. Prabhakar, P. S. Kharkar and A. M. Pethe, ACS Omega, 2022, 8, 1140–1145 CrossRef PubMed.
- L.-T.-T.-T. Hoang, H.-V.-T. Phan, P.-N. Nguyen, T.-T. Dang, T.-N. Tran, D.-T. Vo, V.-K. Nguyen and M.-T. Dao, Arch. Environ. Contam. Toxicol., 2024, 86, 48–57 CrossRef CAS PubMed.
- L.-T.-T.-T. Hoang, H.-V.-T. Phan, N.-N. Nguyen, T.-T. Dang, T.-N. Tran, V.-K. Nguyen and M.-T. Dao, Int. J. Phytorem., 2024, 1–12 CrossRef PubMed.
- D. B. Thinh, N. T. Tien, N. M. Dat, H. H. T. Phong, N. T. H. Giang, D. T. Y. Oanh, H. M. Nam, M. T. Phong and N. H. Hieu, Synth. Met., 2020, 270, 116583 CrossRef CAS.
- M. Muniyalakshmi, K. Sethuraman and D. Silambarasan, Mater. Today: Proc., 2020, 21, 408–410 CAS.
- P. Moradi and M. Hajjami, RSC Adv., 2021, 11, 25867–25879 RSC.
- J. Li, J. Guo and H. Dai, Sci. Adv., 2022, 8, eabo0399 CrossRef CAS PubMed.
- R. Md Salim, J. Asik and M. S. Sarjadi, Wood Sci. Technol., 2021, 55, 295–313 CrossRef CAS.
- N. T. Tin, N. T. T. Huyen, P. M. Tu, P. P. D. Minh, N. T. H. Nam, C. Q. Cong, N. D. Hai, H. An, N. M. Dat and H. T. Duong, Mater. Lett., 2023, 342, 134304 CrossRef CAS.
- X. Li, D. Zeng, P. Ke, G. Wang and D. Zhang, RSC Adv., 2020, 10, 7163–7169 RSC.
- N. T. T. Van, P.-a. Gaspillo, H. G. T. Thanh, N. H. T. Nhi, H. N. Long, N. Tri, N. T. T. Van, T.-T. Nguyen and H. K. P. Ha, Heliyon, 2022, 30, 103041 Search PubMed.
- D. L. T. Cuong, D. N. Trinh, N. T. T. Linh, N. D. Hai, P. T. L. Chau, N. T. Hoang, M. T. Phong and N. H. Hieu, Mater. Res. Bull., 2022, 156, 112000 CrossRef CAS.
- P. W. Albers, V. Leich, A. J. Ramirez-Cuesta, Y. Cheng, J. Hönig and S. F. Parker, Mater. Adv., 2022, 3, 2810–2826 RSC.
- D. Li, J. Huang, L. Huang, S. Tan and T. Liu, Langmuir, 2021, 37, 1521–1530 CrossRef CAS PubMed.
- P. Moradi, RSC Adv., 2022, 12, 33459–33468 RSC.
- N. A. D. Ms, S. N. Ms, S. S. Mr, R. B. Ms, S. R. Ms, W. I. S. Mr and B. P. Swain, Diamond Relat. Mater., 2020, 104, 107756 CrossRef.
- J. Geng, Y. Men, C. Liu, X. Ge and C. Yuan, RSC Adv., 2021, 11, 16592–16599 RSC.
- U. P. Agarwal, Front. Plant Sci., 2014, 5, 490 CrossRef PubMed.
- R. S. Dassanayake, N. Dissanayake, J. S. Fierro, N. Abidi, E. L. Quitevis, K. Boggavarappu and V. D. Thalangamaarachchige, Appl. Spectrosc. Rev., 2023, 58, 180–205 CrossRef CAS.
- S. Prabhu, L. Cindrella, O. J. Kwon and K. Mohanraju, Sol. Energy Mater. Sol. Cells, 2017, 169, 304–312 CrossRef CAS.
- E. A. Bakr, M. N. El-Nahass, W. M. Hamada and T. A. Fayed, RSC Adv., 2021, 11, 781–797 RSC.
- M. Aghaei-Hashjin, A. Yahyazadeh and E. Abbaspour-Gilandeh, RSC Adv., 2021, 11, 23491–23505 RSC.
- J. Gupta, P. Hassan and K. Barick, AIP Adv., 2021, 11, 025207 CrossRef CAS.
- A. Zaman, J. T. Orasugh, P. Banerjee, S. Dutta, M. S. Ali, D. Das, A. Bhattacharya and D. Chattopadhyay, Carbohydr. Polym., 2020, 246, 116661 CrossRef CAS PubMed.
- K. Phasuksom, W. Prissanaroon-Ouajai and A. Sirivat, RSC Adv., 2020, 10, 15206–15220 RSC.
- W. Li, M. Xu, Q. Cao, J. Luo, S. Yang and G. Zhao, RSC Adv., 2021, 11, 19387–19394 RSC.
- F. Asghar, B. Shakoor, S. Fatima, S. Munir, H. Razzaq, S. Naheed and I. S. Butler, RSC Adv., 2022, 12, 11750–11768 RSC.
- A. G. de Souza, R. F. Barbosa and D. S. Rosa, J. Polym. Environ., 2020, 28, 1851–1868 CrossRef CAS.
- O. Akatwijuka, M. A.-H. Gepreel, A. Abdel-Mawgood, M. Yamamoto, Y. Saito and A. H. Hassanin, Biomass Convers. Biorefin., 2024, 14, 7449–7465 CrossRef.
- G. Flores-Jerónimo, J. Silva-Mendoza, P. Morales-San Claudio, A. Toxqui-Terán, J. Aguilar-Martínez and L. Chávez-Guerrero, Waste Biomass Valorization, 2021, 1–9 Search PubMed.
- H.-A. S. Tohamy, M. El-Sakhawy and S. Kamel, J. Renewable Mater., 2022, 10, 1889 CAS.
- K. K. Khichar, S. B. Dangi, V. Dhayal, U. Kumar, S. Z. Hashmi, V. Sadhu, B. L. Choudhary, S. Kumar, S. Kaya and A. E. Kuznetsov, Polym. Compos., 2020, 41, 2792–2802 CrossRef CAS.
- X. Wei, T. Huang, J.-h. Yang, N. Zhang, Y. Wang and Z.-w. Zhou, J. Hazard. Mater., 2017, 335, 28–38 CrossRef CAS PubMed.
- K. Ali, A. K. Sarfraz, I. M. Mirza, A. Bahadur, S. Iqbal and A. ul Haq, Curr. Appl. Phys., 2015, 15, 925–929 CrossRef.
- V. S. Munagapati, H.-Y. Wen, Y. Vijaya, J.-C. Wen, J.-H. Wen, Z. Tian, G. M. Reddy and J. Raul Garcia, Int. J. Phytorem., 2021, 23, 911–923 CrossRef CAS PubMed.
- J. L. Colaizzi and P. R. Klink, J. Pharm. Sci., 1969, 58, 1184–1189 CrossRef CAS PubMed.
- M.-T. Dao, T.-P.-L. Tran, D.-T. Vo, V.-K. Nguyen and L.-T.-T.-T. Hoang, Adv. Mater. Sci. Eng., 2021, 2021, 1–10 Search PubMed.
- B. N. Mahato, T. Krithiga and M. M. Thangam, Surf. Interfaces, 2021, 23, 100636 CrossRef CAS.
- V. S. Munagapati, H.-Y. Wen, J.-C. Wen, A. R. Gollakota, C.-M. Shu, K.-Y. A. Lin and J.-H. Wen, Int. J. Phytorem., 2022, 24, 131–144 CrossRef CAS.
- S. S. Ray, R. Gusain and N. Kumar, Carbon Nanomaterial-Based Adsorbents for Water Purification: Fundamentals and Applications, Elsevier, 2020 Search PubMed.
- S. Figaro, J. P. Avril, F. Brouers, A. Ouensanga and S. Gaspard, J. Hazard. Mater., 2009, 161, 649–656 CrossRef CAS PubMed.
- Y. S. Ho and G. McKay, Process Biochem., 1999, 34, 451–465 CrossRef CAS.
- S. Y. Elovich, O. Larinov, I. Akad, N. SSSR and O. Khim, Nauk, 1962, 2, 209–216 Search PubMed.
- J. Wang and X. Guo, J. Hazard. Mater., 2020, 390, 122156 CrossRef CAS PubMed.
- C. Aharoni and F. Tompkins, in Advances in Catalysis, Elsevier, 1970, vol. 21, pp. 1–49 Search PubMed.
- F.-C. Wu, R.-L. Tseng and R.-S. Juang, Chem. Eng. J., 2009, 150, 366–373 CrossRef CAS.
- I. Langmuir, J. Am. Chem. Soc., 1916, 38, 2221–2295 CrossRef CAS.
- H. Freundlich, Z. Phys. Chem., 1907, 57, 385–470 CrossRef CAS.
- R. Sips, J. Chem. Phys., 1948, 16, 490–495 CrossRef CAS.
- M. I. Temkin and Zh. Fiz, Chim., 1941, 15, 296–332 CAS.
- A. W. Adamson and A. P. Gast, Physical Chemistry of Surfaces, Interscience publishers, New York, 1967 Search PubMed.
- M. A. Al-Ghouti and D. A. Da'ana, J. Hazard. Mater., 2020, 393, 122383 CrossRef CAS PubMed.
- R.-L. Tseng and F.-C. Wu, J. Hazard. Mater., 2008, 155, 277–287 CrossRef CAS PubMed.
- R. Sips, J. Chem. Phys., 1948, 16, 490–495 CrossRef CAS.
- T. A. Saleh, in Interface Science and Technology, ed. T. A. Saleh, Elsevier, 2022, vol. 34, pp. 99–126 Search PubMed.
- A. A. Oladipo, M. A. Abureesh and M. Gazi, Int. J. Biol. Macromol., 2016, 90, 89–99 CrossRef CAS PubMed.
- X. Li and J. Shi, Chemosphere, 2022, 293, 133574 CrossRef CAS PubMed.
- L. Chen, H. Yang, R. Hong, X. Xie, R. Zuo, X. Zhang, S. Chen, D. Xu and Q. Zhang, J. Environ. Chem. Eng., 2024, 114121 CrossRef CAS.
- J. Wang, R. Liu and X. Yin, J. Chem. Eng. Data, 2018, 63, 409–416 CrossRef CAS.
- M. A. Ahmed, M. A. Ahmed and A. A. Mohamed, React. Funct. Polym., 2023, 191, 105701 CrossRef CAS.
- Q. Yao, B. Fan, Y. Xiong, C. Jin, Q. Sun and C. Sheng, Sci. Rep., 2017, 7, 45914 CrossRef CAS PubMed.
- A. Chowdhury, S. Kumari, A. A. Khan, M. R. Chandra and S. Hussain, Colloids Surf., A, 2021, 611, 125868 CrossRef CAS.
- A. Nasiri, S. Rajabi, A. Amiri, M. Fattahizade, O. Hasani, A. Lalehzari and M. Hashemi, Arabian J. Chem., 2022, 15, 104014 CrossRef CAS.
- Q. Liao, H. Rong, M. Zhao, H. Luo, Z. Chu and R. Wang, J. Hazard. Mater., 2022, 422, 126863 CrossRef CAS PubMed.
- R. Rehman and S. Majeed, Int. J. Phytorem., 2022, 24, 1004–1013 CrossRef CAS PubMed.
- M. K. Uddin, N. N. Abd Malek, A. H. Jawad and S. Sabar, Int. J. Phytorem., 2023, 25, 393–402 CrossRef CAS PubMed.
|
This journal is © The Royal Society of Chemistry 2024 |
Click here to see how this site uses Cookies. View our privacy policy here.