DOI:
10.1039/D4RA05637J
(Review Article)
RSC Adv., 2024,
14, 39523-39542
Retracted Article: Bismuth-based nanoparticles and nanocomposites: synthesis and applications
Received
3rd August 2024
, Accepted 24th October 2024
First published on 16th December 2024
Abstract
In the vast landscape of materials science, bismuth emerges as a compelling element with unique properties and diverse applications. Its intriguing characteristics and advancements in nanotechnology have propelled bismuth-based nanoparticles to the forefront of scientific exploration, promising breakthroughs in various disciplines. This comprehensive review explores diverse methods for synthesizing bismuth-based nanoparticles and nanocomposites, ranging from conventional approaches such as hydrothermal and sol–gel to innovative techniques such as microwave-assisted, microemulsion, and green synthesis. The latter includes unique processes such as laser ablation, chemical vapor deposition methods, combustion as well as surface-mediated and bacterium-based synthesis. Each method's strengths, weaknesses, and specifications are critically examined. Further, the review delves into the adaptable applications of bismuth-based nanoparticles and nanocomposites, emphasizing their antibacterial activity, contribution to photovoltaic studies, potential in supercapacitors, and efficacy in photocatalytic degradations of various organic dyes. The objective of this review is to present a thorough summary of the synthesis methodologies and applications of bismuth-based nanoparticles and nanocomposites, offering valuable insights for researchers and professionals engaged in the burgeoning field of nanoparticles.
1. Introduction
Photocatalysis employs visible-light-responsive catalysts (e.g., TiO2, ZnO, ZnS, CdS, and BiVO4, and g-C3N4) for eco-friendly pollutant removal and solar-driven energy production, including diverse semi-conductors (metal selenides, phosphides, and halides).1 Bismuth, a metalloid, adopts a rhombohedral lattice with a two-atom unit cell structure.2 Bismuth, initially mistaken for lead and tin, was differentiated by Claude François Geoffroy in 1753 and later utilized in an 1860s London Stock Exchange scam falsely promising its conversion into silver.3 Bismuth's relative crustal abundance is 0.008 ppm. It is found in ores such as bismuthinite and bismite as well as in native form, which is non-toxic and non-carcinogenic.4
Bismuth's band structure was determined through multiple experiments, with their limited influence on expected outcomes.5 Transformative nanostructures, bridging atomic and bulk scales at a high surface-to-volume ratio, drive diverse applications through manipulation and integration of novel attributes.6 “Nano”, which is Latin and Greek for “dwarf”, represents a 10−9 scale, driving transformative nanotechnology with unique materials impacting diverse fields.6 Nanotechnology involves exploring and advancing substances, structures, and apparatuses at the molecular or atomic level, often centered on matter around 100 nm in size.7 Nanotechnology produces novel nanomaterials with distinct properties via atom-level manipulation, which are applicable across electronics, energy, healthcare, and other fields, and are driven by a high surface-to-volume ratio and quantum phenomena.8 Nanotechnology revolutionizes the food industry by enhancing packaging, shelf life, impurity detection, and additive integration while preserving taste neutrality.9 Nanotechnology in medicine utilizes nanoparticles for disease detection/treatment, including drug/gene therapy, cancer treatment, MRI contrast agents, tissue regeneration, and pathogen identification.10
Nanotechnology enables small, fast, high-storage, low-power devices such as smart cards, digital cameras, liquid crystals, LEDs, and nano-transistors.11 Nanotechnology improves renewable energy utilizing nanomaterials for increased efficiency, corrosion resistance, and lowered fuel consumption.12 Nanotechnology employs nanoparticles to detect and eliminate environmental contaminants, enhancing environmental protection.13 Nanomaterials have proven valuable in treating wastewater, thus effectively addressing carbon-based dyes, nitrates, cations, heavy metals, natural organic matter, and viruses.14 Sub-100 nm nanoparticles display diverse benefits, including improved solar cell absorption, stronger polymer composites, tunable properties, and versatile industrial applications.14
Zinc oxide nanoparticles serve multiple purposes, such as blocking UV rays, acting as antimicrobial agents, functioning as sensors, and improving food packaging capabilities.15 Titanium dioxide nanoparticles exhibit properties that enable self-cleaning, photocatalysis, cosmetic enhancement, and water purification uses, exhibiting size-dependent properties among four material types.16 Rare-earth (RE) element-doped inorganic matrix nanocrystals, or nano phosphors, have garnered notoriety owing to their capacity to create translucent; thin coatings that are helpful in optoelectronics, security, and labeling.17 It was shown that when exposed to visible light, the BFO/TiO2-NTs composites (formed on a Ti sheet) displayed much higher photo-conversion effectiveness than the TiO2-NTs/Ti electrodes that were not changed.18
Carbon-based nanomaterials, such as nanotubes, fullerenes, graphene, and nanofibers, are produced using arc discharge, chemical vapor deposition, and laser ablation.19 Exceptional carbon-based nanomaterials exhibit widespread industrial utility owing to their remarkable mechanical, optical, electrical, and thermal properties.20 Inorganic nanomaterials encompass metal, metal oxide, and semiconductor nanoparticles.21 Developing new synthetic pathways using diverse solvents is vital for creating unique inorganic nanomaterials with applications beyond traditional options while considering advantages and limitations.22
Organic nanoparticles, 10 nm to 1 μm in size, comprising polymers and lipids, have substantial high-tech application value although they are often overshadowed by inorganic counterparts, such as gold and quantum dots.23 Organic and inorganic nanomaterials undergo noncovalent interactions to achieve desired structures, such as micelles, polymers, dendrimers, and liposomal nanoparticles.24 Composite nanomaterials are intricate multiphase nanoparticles that merge diverse materials for versatile applications.25 Precisely engineered composite nanomaterials exhibit immense technological potential as sensors, film modifiers, semiconductor–metal junctions, and catalysts, capitalizing on their unique nanoscale properties.26 Synthetic nanoparticle manufacturing employs chemical, physical, and biological methods with chemical reduction utilizing agents, such as NaBH4, N2H4, H2 gas, B2H6, gas, and alcohols for cost-effective metal salt reduction.27 Stabilizing agents regulate nanoparticle features based on their organic, inorganic, or biomolecular nature, encompassing morphology, aggregation, and properties.28
The solvothermal method includes dissolving precursor metals in a solvent inside an enclosed system and exposing them to elevated temperature and pressure conditions.29 Hydrothermal single-crystal growth utilizes a pressurized autoclave with hot water and a nutrient to dissolve minerals at high pressure, enabling crystal growth on the cooler side.30 Hydrothermal synthesis utilizes water as a solvent to create nanomaterials, with reaction conditions and starting material characteristics influencing the resulting properties.31 The sol–gel process combines liquid precursors, hydrolysis, polycondensation, and gel formation to produce transparent sols, which transform into gel networks and yield nanoparticles upon thermal treatment.32 Co-precipitation is a popular technique for producing metal oxide nanoparticles, with reagent concentration, pH, and heating influencing particle characteristics.32 Treatment of homogeneous solutions of raw material chlorides/nitrates in solvents with NaOH/NH4OH base results in precipitates that, after salt washing and heating, lead to the production process of metal oxide NPs.29 The microemulsion method involves water and oil phases separated by a surfactant to create nanoemulsions with controlled droplet sizes through precise oil/surfactant ratio adjustment via room temperature stirring.33 CVD is a versatile technique involving gaseous reactants undergoing surface reactions on a substrate, resulting in solid deposits through heterogeneous reactions while eliminating by-products via diffusion.34 The melt mixing method utilizes elevated temperature and shear stress to uniformly disperse metal nanoparticles in a polymer matrix above its Tg, creating thermoplastic polymer-based nanocomposites.35 High-energy ball milling involves ball collisions in a mill to generate energy for synthesizing oxide nanoparticles, particularly in difficult materials, such as nickel-based superalloys.36 Biosynthesis utilizes viruses, bacteria, plant extracts, and fungi for eco-friendly nanoparticle preparation, differing from toxic chemical methods.37 Efficiently produces eco-friendly nanoparticles at scale with precise attributes, minimizing pollution.38 Green chemistry-based nanomaterial synthesis employs safe capping agents and eco-friendly solvents and eliminates hazardous reducing agents for sustainable and safe production.39
Plant extract-enabled nanoparticle preparation: a single-step, rapid, safe, and cost-effective synthesis that utilizes diverse plant metabolites as reductants and stabilizers.40 Algae and fruit waste can synthesize metal nanoparticles using algal biomolecules as capping agents, yet toxicity concerns arise, while fruit waste allows for direct metal oxide nanoparticle preparation.41 Nanocomposites feature nano-sized particles for enhanced reinforcement and dispersion within the matrix compared to conventional composites.42
Nanocomposites synergize continuous matrices and discontinuous reinforcements for heightened optical, mechanical, and thermal conductivities.43 Natural nanocomposites combine polymers with other components in structures, such as bones and shells, while synthetic polymer nanocomposites exhibit inferior strength and modulus compared to metal and ceramic counterparts.44 Polymer nanocomposites optimize mechanical properties through diverse nanoparticles, compositions, flexibility, temperature modulation, and eco-friendly strength, making them ideal for car parts.45
Nanoscale Bi-based photocatalysts show potential for water and air toxin removal via visible-light activation, demanding optimization in electron–hole utilization through morphology, heterojunctions, and surface modifications; TiO2 is a well-explored benchmark.46 Bi nanomaterials are photocatalysts due to their appropriate energy band structure, chemical stability, and eco-friendliness.47 Bi exhibits significant metallic properties due to its lower effective mass, higher Fermi surface, and semiconductor transition ability.48 Bismuth oxide (Bi2O3), when combined with TiO2 in composites, exhibits enhanced visible-light photocatalytic efficiency compared to individual use, finding application in various fields.49 Bi2O3 demonstrates p-type semiconductor characteristics; the valence band edges are positioned around +0.131, while the conduction band edges are at approximately +0.334.50 Bi2O3 demonstrates p-type semiconductor characteristics, and the locations of the valence band and conduction band edges are identified at around +0.131 and +0.334 (relative to the normal hydrogen electrode), respectively.51 The evaluation encompassed their effectiveness in visible-light photocatalysis and their potential for reuse.
2. Synthesis of bismuth oxide nanoparticles
The three chemical methods for making nano-bismuth oxide are the sol–gel approach, hydrothermal technique, and combustion technique.52–54
2.1 Hydrothermal approach for the synthesis of bismuth nanoparticles
The hydrothermal approach is a viable alternative synthetic method due to the low temperature needed for the process and the ease of controlling particle size.55 Compared to other growth techniques, the hydrothermal approach has many benefits, such as employing less complex equipment, lacking a catalyst throughout development, cheaper cost, large-area uniform output, eco-benign, and lower hazard. Because of the low reaction temperatures needed, this method is appealing for use in microelectronics and plastic electronics. Bismuth oxide and other brilliant chemicals have also been successfully synthesized at the nanoscale using this approach. By manipulating the reaction's temperature, time, and precursor concentration, the hydrothermal process permits control over the properties of the particles, such as their size and form.56 The hydrothermal method for creating cobalt-doped bismuth oxide nanoparticles is briefly explained here. Initially, the beginning materials for the synthesis were sodium hydroxide [NaOH], cobalt nitrate [Co(NO3)2·6H2O], and bismuth nitrate pentahydrate [Bi(NO3)3·5H2O]. They were dissolved in deionized water and stirred continuously to produce a uniform solution. The mixture was then placed in a Teflon-lined autoclave and heated to 150 °C for nine hours. During this procedure, the precursors were hydrolyzed, and cobalt-doped bismuth oxide nanoparticles were formed by nucleation. After hydrothermal treatment, the generated nanoparticles were collected by centrifugation, and any leftover impurities were repeatedly washed with ethanol and deionized water. Then, the nanoparticles were dried at 80 °C for a few hours. The generated nanoparticles were examined using several techniques, such as UV-visible spectroscopy, FTIR spectroscopy, scanning electron microscopy, and X-ray diffraction. XRD measurements revealed the formation of cobalt-doped bismuth oxide nanoparticles with a crystalline structure. SEM and XRD analyses showed that the generated NPs were sphere-shaped and averaged 20–30 nm in size (Fig. 1).57
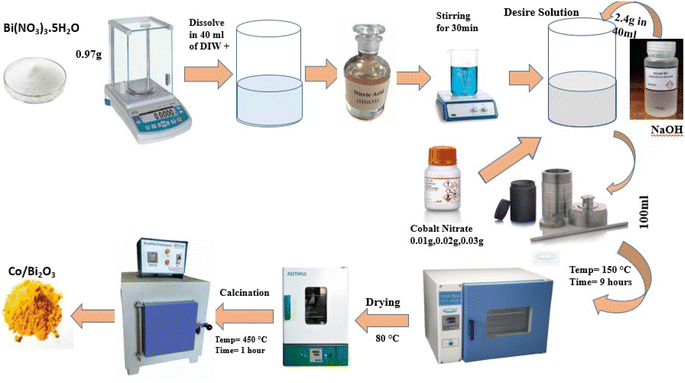 |
| Fig. 1 Hydrothermal synthesis of cobalt-doped bismuth oxide nanoparticles. | |
2.2 Sol–gel approach synthesis of bismuth nanoparticles
The primary processes in the sol–gel technique are the hydrolysis of precursors for metal–organic compounds, such as alkoxysilane,58 to yield the appropriate oxo hydroxide and then condensed to create a network of the metal hydroxide. A thick porous gel is produced by the polymerization of hydroxide, which may then be dried and heated to form ultrafine porous oxides in the necessary crystal phase.31 When exposed to visible light, most bio-based systems have been shown to be highly photostable in removing dangerous pollutants from wastewater and water.59 Numerous metal oxide nanoparticles have been produced using this technique, such as TiO2,60 zinc oxide,61 magnesium oxide,62 CuO,63 ZrO2 and Nb2O5,64 and nanocomposites, such as LiCo2 thin film,65 Cu decorated ZnO nanoparticles,66 CuO/Cu2O nano composites,67 Ce-doped ZrO2,68 oxides of Hf, Ta, and Nb.69 Mallahi M. et al. published a paper titled “Synthesis and characterization of bismuth oxide nanoparticles via sol–gel technique.”70 According to AJER 3.4 (2014): 162–165, the bismuth nitrate and citric acid used to generate Bi2O3 were of AR grade, and bismuth oxide was synthesized using the sol–gel technique. A known amount of Bi (NO3)3·5H2O was combined with citric acid in a 1
:
1 molar ratio after being dissolved in a nitric acid solution. A tiny quantity of PEG600 was used as a surfactant to stop agglomeration. The solution's pH decreased to 3. After two hours of stirring the solution above, a sol developed. After three hours at 80 °C, the sol solution solidified into a yellowish gel. A temperature of 120 °C was used to break down this gel. A frothy forerunner was first produced when the gel began to grow and fill the beaker. Every particle size in this foam is uniform, with relatively small flakes (Fig. 2).
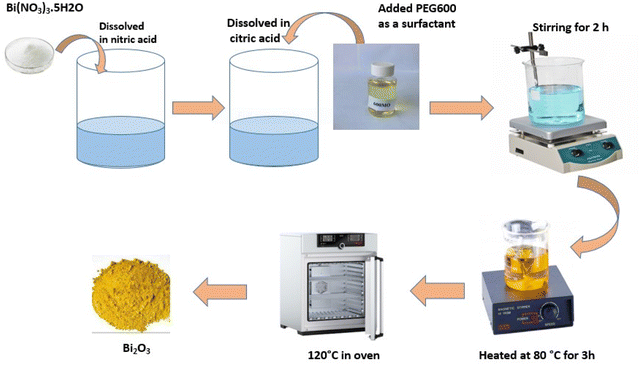 |
| Fig. 2 Sol–gel method for the synthesis of bismuth oxide nanoparticles. | |
2.3 Bismuth nanoparticle production using a microwave-assisted approach
Due to its minimal energy and time requirements, this approach is gaining popularity.71 The primary benefit of this technique is that it may shorten response times from hours to minutes while maintaining particle size integrity. Two different routes of bismuth oxide preparation were studied. There are two steps in the first one. The first stage involved precipitating bismuth nitrate with a 1 M NH4OH solution to create bismuth hydroxide, after separating and cleaning the precipitated bismuth hydroxide with water to neutralize pH. In the second phase, ammonium hydroxide or nitric acid was used to reduce the pH of the bismuth hydroxides to a value between 6 and 12. Suspensions were hydrothermally changed at 100–220 °C under a microwave field. A microwave reactor with a maximum output of 1400 W and a frequency of 2.45 GHz was employed for the tests. The second synthesis method examined the impact of the chelating agent (polyethylene glycol) on product precipitation. After cooling to a temperature below 100 °C, aqueous solutions of reactants made by dissolving sodium hydroxide (4.0 M), bismuth nitrate (2.0 M), and polyethylene glycol (PEG 4000–0.05 M) were combined in molar ratios of 0.12, 0.44, and 0.002, respectively. After mixing the reactants, the suspensions produced were put in the microwave reactor and treated at temperatures ranging from 40 to 60 °C, either with or without stirring. Centrifugation was used for product separation, followed by water washing to a neutral pH and 110 °C drying (Fig. 3).72
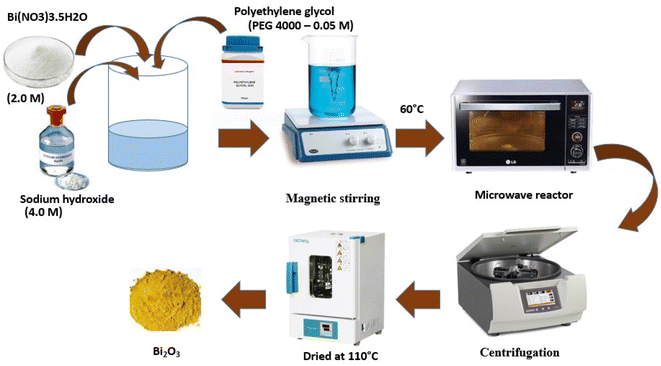 |
| Fig. 3 Synthesis of bismuth oxide nanoparticles using a microwave-assisted approach. | |
2.4 Microemulsion method for the synthesis of Bi-NPs
Using a microemulsion technique, Fang et al.73 synthesized bismuth oxide. An 8
:
1 weight ratio pre-mixing of surfactants NP5 and NP9 was done. Next, an inverse microemulsion system was created, comprising 60.30 weight percent petroleum ether, 28.20 weight percent mixed surfactant (NP5 + NP9), and 11.50 weight percent aqueous solution of 0.50 M NaBH4 in 1.00 M NH3·H2O. Concurrently, another ternary system comprising 60.30 weight percent petroleum ether, 28.20 weight percent mixed surfactant (NP5 + NP9), and 11.50 weight percent aqueous solution of 0.10 M bismuth(III) citrate in 1.00 M NH3·H2O was also created. Next, while vigorously swirling, the bi-containing system was titrated into the microemulsion system at a speed of thirty drops per minute. After being separated by high-speed centrifugation, the resultant nano-bismuth powder was finally recovered by centrifugal recovery, vacuum drying, and repeated washing away of the oil and surfactant with ethanol. Every procedure listed above was carried out in a glove box in a nitrogen environment. This technique also synthesizes nanocomposites, such as cerium oxide nanoparticles,74 NiO,75 Fe3O2,76 TiO2,77 ZnO,78 CuO,79 BaAlO2,80 and iron-oxide-doped alumina nanoparticles.81 A vital advantage of this method is its capacity to regulate the creation of various core–shell structure types with sub-nonmetric precision.82 This method's drawback is that the generated nanoparticles agglomerate, necessitating multiple washing procedures and further stabilization treatments (Fig. 4).76
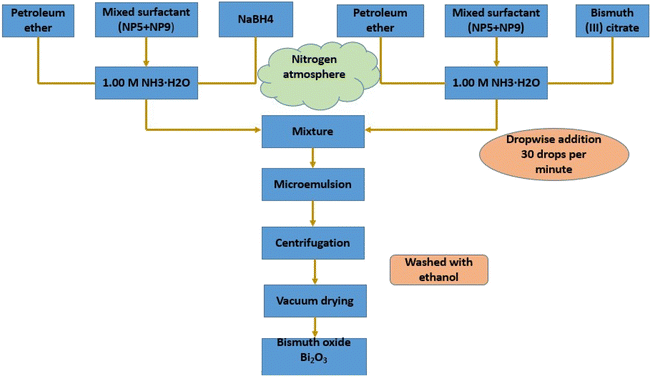 |
| Fig. 4 Flowchart for the synthesis of bismuth oxide nanoparticles using the microemulsion method. | |
2.5 Vapor state synthesis for the synthesis of bismuth nanoparticles
Broadly, there are two types of vapor state synthesis through which bismuth oxide nanoparticles are prepared.
2.5.1 Laser ablation method for the synthesis of bismuth nanoparticles. Using this technique, colloidal solutions from bulk materials submerged in aqueous or non-aqueous solvents are laser-irradiated on submerged targets, producing nanoparticles.83 The method has been used to synthesize ternary metal oxides, such as ZnO,84 NiO,85 SnO2,86 ZrO2,87 iron-oxide,88 Al2O3,89 Au–SnO2 (ref. 90) and Cu/Cu2O.91 Two parameters may be manipulated to influence the size of the nanoparticles: the composition of the liquid medium and the fluence of the laser.92,93 A. Ismail et al.94 developed a laser ablation method to produce bismuth oxide. First, they fixed a 99.99 percent pure bismuth target to the plastic vessel's bottom. Throughout the pulsed ablation in liquid (PLAL) process, they avoided the formation of undesired precipitates of the synthesized products using pure water as a liquid accumulation at the electrode and in the solution. UV-vis spectrometers are used to study the optical characteristics of bismuth oxide nanoparticles. Using a diffractometer and Cu Kα radiation, the Bi2O3 NPs' XRD (X-ray diffraction) is studied. Atomic force microscopy (AFM) is used to examine the morphology of the materials. EDX (energy dispersive X-ray) is employed to assess the bulk atomic composition of the nanoparticles, while field emission-SEM is utilized for research on morphology. A few colloidal droplets are deposited onto single-crystal silicon for these experiments. The measurements shown above were taken at room temperature. Some drawbacks of laser ablation include the need for capping, the propensity for nanoparticle aggregation, and the lack of long-term stabilization in solution (Fig. 5).95
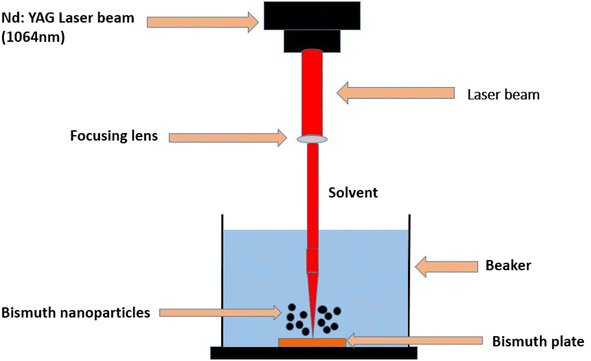 |
| Fig. 5 Schematic of the laser ablation method synthesis of bismuth nanoparticles. | |
2.5.2 Chemical vapor-based methods for the synthesis of bismuth nanoparticles. Materials are subjected to elevated temperature and gaseous predecessor substances during chemical vapor deposition (CVD). The reactions or breakdowns of the precursors create nanomaterials on the substrate surface.59 The chemical vapor synthesis (CVS) technique heats pure or metal–organic salts to the vapor phase. Then, the metals are inserted into a hot-wall reactor, interacting with an oxidizing chemical in a favorable chemical environment.96,97In this approach, the bismuth oxide was synthesized by Kumari, L., Lin, J. H., & Ma, Y. R. (2007) et al.98 An oxidative metal vapor phase deposition process created large-area arrays of 1D Bi2O3 nanostructures. The nanostructure formation occurred in a heated filament vapor depositing chamber by employing a molybdenum (Mo) filament that melted the bismuth metal grains. Two copper electrodes were linked to a Mo wire with a 99.9% purity in a vacuum chamber. The Mo filament was first used to insert the Bi grains into the carbon holder to support the carbon holder. An acetone, ethyl alcohol, and de-ionized water ultrasonically cleaned p-type Si (100) wafer for thirty minutes each. Then, it was positioned atop the carbon holder approximately three millimeters above the coil for sample deposition. The chamber was filled with an argon (Ar) flow of 180 sccm at a pressure of 1 × 10−3 torr, and the pressure required for work was kept at roughly 10 torr during the procedure used to create 1D nano-structures. The two copper electrodes were placed in series with a voltage regulator to generate a current that flowed across the Mo coil, quickly warming it up and melting the Bi grains when the necessary continuous operating pressure was achieved. Repeated experiments were used to determine the ideal current required to melt and evaporate the Bi. The chamber was first filled with an oxygen flow of 0.6 ccm for approximately 30 s, and it was subsequently filled again for 5 seconds each and separated for 10 minutes. O2 was not delivered into the chamber for the last ten minutes, yet the growth process was still ongoing due to the internal O2 pressure in the chamber. The synthesis procedure required a total of thirty minutes. It was determined that the substrates were below 350 °C, while the Mo filament was measured between 800 and 830 °C. A noticeable coating of light-yellow product was produced on the Si substrate once the system had cooled to room temperature. The growth of Bi2O3 nano flowers was similar, with the working pressure kept constant at 30 torr. A benefit of this method is that it is simple to regulate the formation of the nanostructures by varying the working pressure and the evaporation temperature. A field emission scanning electron microscope (FESEM, JEOL JSM-6500F) equipped with energy-dispersive X-ray spectroscopy (EDS, Oxford Instrument INCAx-sight 7557) was used to examine the surface morphology of the 1D nanostructures. The microscope was operated at an accelerating voltage of 15 kV. Using an accelerating voltage of 200 kV, Transmission Electron Microscopy pictures and selected-area electron diffraction (SAED) patterns were obtained using the JEOL-3010 apparatus fitted with EDS. The nanowire products were scattered over the carbon-coated copper grids after being ultrasonically dispersed in ethanol for TEM investigation. Structural investigation was performed by applying an X-ray diffractometer (Philips X'Pert) with Cu Kα radiation (λ = 1.5406 A). To obtain Raman scattering spectra, a micro-Raman spectrometer (Jobin Yvon Horiba T64000) fitted with a liquid nitrogen-cooled CCD detector was used. The instrument received 532 nm incident photons from a diode-pump solid-state laser at a maximum power of 50 mW. The photoluminescence of these nanostructures was examined using a 488 nm excitation laser and a scanning near-field optical microscope (Alpha SNOM 300 series). These methods are widely used to create homogeneous and devoid-of-impurities metal oxide nanoparticles and films; examples include ZnO nanowires and films,99 defect-free ZnO nanoparticles,100 magnetite nanotubes and nano spheres,101 Cu2O,102 MgO and calcium oxide,103 SnO2,104 SrO,105 and CO and Co3O4.106 This method permits the manufacture of B-doped ZnO,107 europium-doped yttria (YO:Eu),108 Li-doped MgO,109 and Ca-doped82 when multi-metal oxides are considered.
2.6 Combustion method for the synthesis of bismuth nanoparticles
This synthesis involves heating a pure metallic precursor using various approaches to evaporate it into a background gas, introducing an oxidizing agent (the second reactant).59 This approach was used to synthesize bismuth oxide nanoparticles by burning, as described by La J. et al.110 In a typical instance, 10 mL of HNO3 (0.04 mol L) was used to dissolve 2.9106 g of Bi (NO3)3·5H2O and 1.471 g of C6H8O7H2O. Then, 0.04 g of PEG-20000 was added to the solution. A clean, transparent solution was created after five minutes of vigorous churning. After two hours of heating at 300 °C, the solution spontaneously cooled to ambient temperature. The yellow granules collected were stored for further analysis.
Nevertheless, as demonstrated in the instance of MgO nanosmoke,111 control over the partial pressure of the oxidizing agent governing nucleation and growth can have some effect on particle size during this process. ZnO,112 FeO,113 copper oxide, manganese oxide, MgO,114 CdO, and Co3O4 (ref. 115) nanoparticles or Ag supported on the MgO surface,116 Co3O4 on CuO nanowire arrays (Co3O4CuO)117 and La0.82Sr0.18MnO3 are examples of nanoparticles. The link between flame chemistry and particle generation makes this process complicated and challenging to regulate despite its commercial success (Fig. 6).59
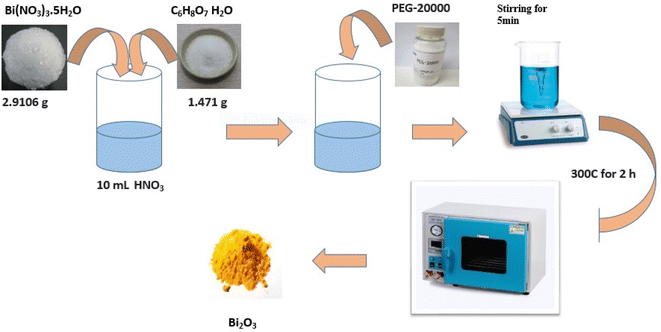 |
| Fig. 6 Synthesis flowchart of bismuth oxide using the combustion method. | |
2.7 Surface-mediated synthesis of bismuth nanoparticles
The main techniques in this kind of manufacturing include electrochemical,118 electrolysis and sol–gel,119 chemical polymerization,120 and CVD.121 Many metal oxides are created in this fashion example, including MoO2 NPs with better electrochemical characteristics,122 α-Fe3O4 and Co3O4,123 Fe2O3,124 SrO125 and Ag NPs.126 Using MW methods, Sonkusare et al.127 produced bismuth oxide by dissolving PVP (0.5 g) and Bi(NO3)3·5H2O (0.4 g) separately in ten milliliters of EG. The reaction mixture was then spread to create a homogenous solution (HS). After that, HS was moved inside the MW (MS-2049UW/1200 W/2450 MHz) and exposed to radiation for ten and fifteen minutes, respectively. After that, five ml of N2H4 was added drop by drop and left for another minute or so. Following cooling, the sample was centrifuged to extract the black residue; then, it was cleaned and allowed to dry under Hoover for five hours at 80 °C. Track-etch membranes, porous alumina, and other nonporous materials, such as mesoporous zeolites, are the primary templates for these synthesis techniques (Fig. 7).128,129
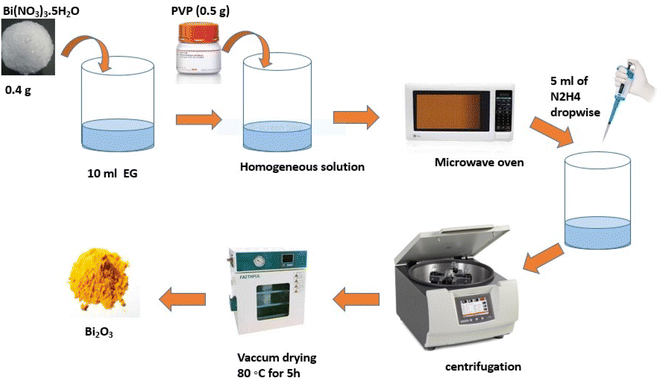 |
| Fig. 7 Flowchart for the production of bismuth nanoparticles using a green synthesis approach. | |
2.8 Producing bismuth nanoparticles using a green synthesis approach
Compared to microorganism-derived Bi2O3 nanoparticles, green synthesized nanoparticles are less expensive, easier to make, safer to use, and more environmentally friendly. Furthermore, because purified water and ethanol are typically used to produce plant extracts, Bi2O3 nanoparticles derived from microorganisms are more hazardous than green-synthesized bismuth oxide nanoparticles.130 Plant extracts from various tree parts, including the roots, bark, leaves, flowers, fruit extract, and peels, create Bi2O3 nanoparticles.131 Plant extracts have been reported to contain high concentrations of antioxidants,132–134 which are active substances and aid in neutralizing free radicals, reactive oxygen species, and chelated molecules.135 These compounds include saponins, flavonoids, phenolic carboxylic acids, and methyl xanthines. Thus, it is evident that plant extracts can function as stabilizers and bio-reduction.136 Bismuth nanoparticles were created by Das P. E. et al.137 via a hydro-alcoholic extract of Moringa oleifera leaves. M. oleifera leaves contain polyphenols that help convert Bi3+ into Bi0. Prakash et al. created bismuth nanoparticles aided by Eclipta alba.130 Bismuth nanoparticles have outstanding antimicrobial properties and broad potential applications in public areas (Fig. 8).
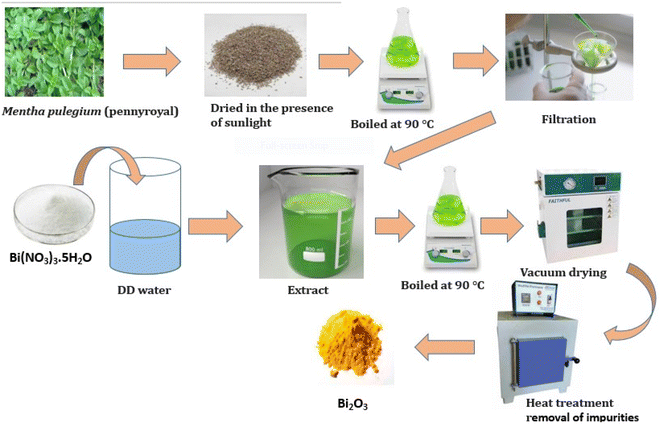 |
| Fig. 8 Flowchart for the producing bismuth nanoparticles using a green synthesis approach. | |
2.9 Bismuth oxide green synthesis using bacteria
Using Delftia species, Shakibaie et al.138 developed bismuth-based NPs through a 16SrDNA sequence study. The scientists reported that as-synthesized BBNs demonstrated radical solid scavenging and lowered power Nazari et al.139 created bismuth NPs utilizing C8H15NaO8 as a surfactant and Serratia marcescens from the Caspian Sea, while Xu et al.140 created Bi2Se3-layered nano sheets composed of several thin nanosheets. Yaqoubi et al.141 and Yadav M. et al. created bismuth oxide nanocrystals using Mentha pulegium extract from water as an antioxidant.142 Jayapriya et al. effectively synthesized nanocomposites based on BiOX (X = Br, Cl, or I) utilizing leaf extract from neem and an extract from Anisomeles malabarica.143 Focused on the creation of bismuth-based NPs. Xue et al.‘s144 recent work used microwave radiation to create bismuth sulfide nanorods using gelatin as a template. Furthermore, Mohamed et al. made bismuth vanadate nanostructures145 using an extract from Callistemon viminalis (Table 1).
Table 1 Various methods for the green synthesis of bismuth compounds and their applications
S. no. |
Method |
Plant used |
Size of particles (nm) |
Nanomaterials morphology |
Application carried out |
References |
01 |
Plant mediated synthesis |
Mentha pulegium |
150 |
Round |
Anti-bacterial activity |
141 |
02 |
Plant mediated synthesis |
Sapindus mukorossi |
50 |
Cubical |
Dye degradation |
146 |
03 |
Plant mediated synthesis |
Gossypium |
90 |
Polygonal |
X-ray shielding caskets, anti-bacterial activity |
147 |
04 |
Plant mediated synthesis |
Moringa oleifera |
40.4 |
Amorphous |
Anti-bacterial activity, anti-fungal activity |
137 |
05 |
Plant mediated synthesis |
Beta vulgaris |
30.28 |
Sheet cluster |
Anti-microbial |
148 |
06 |
Bacteria mediated synthesis |
Spirulina platensis |
45 |
Irregular |
Cancer treatment |
149 |
07 |
Plant mediated synthesis |
Zingiber officinale |
35 |
Spherical |
Cancer treatment |
150 |
08 |
Plant mediated synthesis |
Euphorbia royleana |
60 |
Irregular |
Bio-diesel production |
151 |
09 |
Plant mediated synthesis |
Citrus limon |
10 |
Irregular |
Catalytic reduction of organic dye |
152 |
10 |
Plant mediated synthesis |
Chenopodium album |
79.99 |
Irregular |
Anti-fungal activity |
153 |
11 |
Plant mediated synthesis |
Carrageenan seaweed |
80–90 |
Rhombohedral |
Dye degradation |
154 |
12 |
Plant mediated synthesis |
Artocarpus heterophyllus |
200 |
Spherical |
Photo catalysis, anti-microbial |
155 |
3. Application of bismuth-based nanoparticles
Due to its stability and appropriate band structure, bismuth oxide is frequently used in photocatalytic processes. Electrodes, fuel cells, supercapacitors, and semiconductors are just a few of the many applications of bismuth oxide. The next section discusses its few uses in environmental sciences, medicine, and photocatalysis.
3.1 Bismuth-based nanoparticles for anti-microbial activity
Bacterial resistance is a critical global issue that has prompted several investigations in metal-based nanomedicine and antibacterial nanoparticles (NPs).156,157 Due to their robust antibacterial activities at tiny dosages, bismuth-based NPs are currently regarded as potent antibiotics that can potentially prevent or lower the emergence of antibiotic resistance.158 Metal-based NPs exert their antibacterial effect through reactive oxygen species generation, metal-based NP cation release, ATP depletion, membrane damage and altered respiratory function, protein malfunction, and disruption of nutritional absorption. By dephosphorylating peptide substrates in tyrosine, sites can interfere with the transmission of signals and alter the transcriptome and proteome profiles of microorganisms, leading to the deactivation of signals and inhibition of bacterial growth.159 Recent studies160 showed that doping bismuth oxide nanoparticles with FA and 5-ALA significantly reduced the number of KB tumor cells and A549 cells. When BSA protein and W6/32 antibody are added to Bi-germanate NPs, they can also identify human acute monocytic leukemia cells.161 Aspergillus niger and Penicillium chrysogenum were two examples of the bacterial strains that BBNs actively responded to, along with S. aureus, P. aeruginosa, B. subtilis, and several other species.162 Bi(III)ephedrine thiocarbamate complexes demonstrated high effectiveness against both Gram-positive and Gram-negative bacteria, including E. coli, P. aeruginosa, S. Dublin, K. pneumoniae, and E. cloacae, as well as specific Gram-positive bacteria like S. aureus, E. caseofluvialis, and S. sciuri.163 The remarkable antibacterial activity of Bi2O3 nanoparticles against S. aureus should be mentioned.164 Extensive research has shown that BBNs have potent antibacterial efficiency in every pathogen investigated, including Salmonella typhimurium, Campylobacter jejuni, Y. enterocolitis, E. coli, E. arginine, M. arginine, B. anthracis, and L. pomona, which may cause diseases in humans and animals.165 According to the most recent publication by Torrisi et al., bismuth nanoparticles are successful in eliminating tumor cells in mice.166 Based on the findings above, it is apparent that Bayesian Belief Networks (BBNs) can impede the expansion of colonies of bacteria and limit the replication of microbes. Moreover, it is worth noting that broad-spectrum bactericidal nanoparticles (BBNs) demonstrate inhibitory properties against a wide range of bacterial species, including both Gram-positive and Gram-negative strains. This inhibition is achieved by interacting BBNs with the peptidoglycan layer in the bacterial cell wall. Significantly, using BBNs as composites exhibits considerable improvement in their antifungal efficacy.
In summary, it has been observed that BBNs can specifically impede the proliferation of malignant cells. Changes in the permeability of tumor cell membranes and the start of cellular damage to genomic DNA are believed to be responsible for this result (Fig. 9).
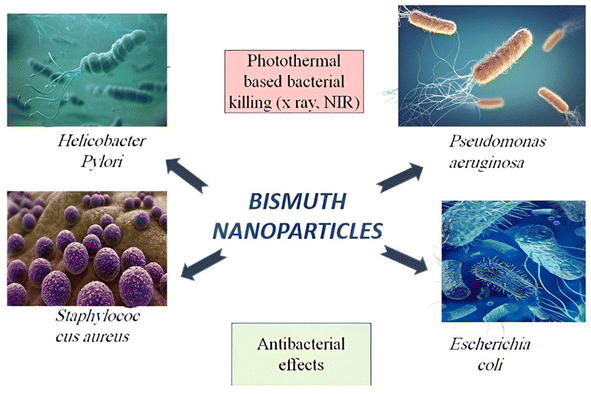 |
| Fig. 9 Bismuth-based nanoparticles as the perfect photothermal and antimicrobial agents to prevent bacterial illnesses. | |
3.2 Bismuth-based nanoparticles for photovoltaic studies
The diminishment of non-renewable resources has emerged as a substantial factor in exacerbating global warming, the intensification of air pollution, and the consequent elevation of sea levels. Consequently, the pursuit of feasible alternatives has become of utmost importance. Fuel cells, solar cells, and batteries are anticipated to be crucial in facilitating the shift away from fossil fuels. Significantly, these entities can produce water and hydrogen as byproducts, exhibiting enhanced environmental safety and more excellent value than carbon-based alternatives. In the present context, it is noteworthy to emphasize the remarkable efficacy exhibited by materials containing bismuth, specifically in the domain of hydrogen storage, surpassing the performance of alternative metallic elements. Bismuth-based materials offer a compelling alternative to lead-containing compounds, rendering them a captivating area of investigation in the field of sustainable energy solutions. Because bismuth has few commercial uses and is a byproduct of lead, copper, and tin refinement, its price has remained low despite its relative abundance in the earth's crust. Alkali metal and air batteries have recently employed BiOMS-2 as cathode catalysts167 and in the fabrication of photovoltaic devices.168,169 A3Bi2X9 is the chemical formula for bismuth perovskites, where X is a halogen anion (such as Cl, Br, and I) and A is a monovalent cation (such as Cs+ or CH3NH3+). Because they resemble their highly efficient Pb counterparts, CH3NH3PbI3 and CsPbI3, respectively, the bismuth perovskite materials (CH3NH3)3Bi2I9 and Cs3Bi2I9 have been explored. Recently, a multiferroic Bi6Fe1.6Co0.2Ni0.2Ti3O18/Bi2FeCrO6 hetero junction photo electrode based on Zn2SnO4 has been studied. This electrode modifies the charge carrier transit and the intrinsic electric field to disengage high-performing multiferroic oxide photovoltaic systems.170 An experiment was conducted by manufacturing samarium and cobalt-co-doped bismuth ferrite nanoparticles to achieve an ideal decrease in band gap energy of 1.40 electron volts, thereby achieving maximum solar cell power transformation performance.171 Applications for bismuth-based materials include photodetectors, solar-powered hydrogen generation, photocatalytic pollution degradation, renewable energy devices, such as batteries and thermal electricity devices, and bioimaging, such as therapeutic substances. Bismuth-based materials are essential in many applications, encompassing photodetectors, solar-powered hydrogen generation, photocatalytic pollution degradation, renewable energy devices, including battery and thermal electricity gadgets, and even therapeutic substances in bioimaging. The anisotropy of the crystalline structures of these materials poses a notable difficulty, which is attributed to the influence of the distinctive ns2 lone pair of bismuth atoms. Enhancing our comprehension and refining the characteristics of materials based on bismuth could provide significant advancements in these many domains (Fig. 10).
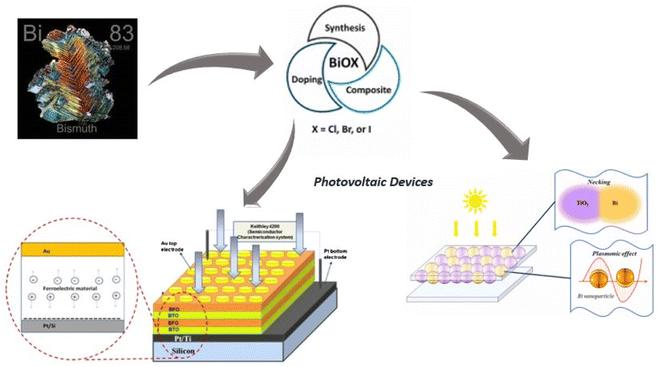 |
| Fig. 10 A schematic for the application of bismuth-based nanoparticles in photovoltaic devices. | |
3.3 Bismuth-based nanoparticles for supercapacitors
The supercapacitor, which gained popularity years ago in its use as a storage of energy, serves as a workable substitute that may be used to mimic upcoming battery advancements. The final step in fulfilling this critical duty is researching substances for electrodes with substantial power intensities and electrochemical durability for long-lasting and affordable implementations. The remarkable capacitive efficiency of the Bi2O3/rGO composite should be emphasized.172 High-specific capacitance and electrochemical solid energy storage are two other potential uses for Bi2S3.140 Furthermore, it has been observed that Bi2Se3 nanoparticles are frequently used to enhance the properties of materials intended for use in lithium-ion batteries.173 Furthermore, bismuth-based nanoparticles work in a negative potential window of −1–0 V in aqueous alkaline electrolytes depending on the electrolyte. Asymmetric supercapacitors with specific capacities of 443 C g−1 (at two mA cm−2) within the potential window of −1.1 to 0 V, encompassing long-lasting periodic stability, were recently constructed using advanced nanostructured nickel-based bismuth oxide as negative electrodes.174 Using carbonaceous materials, such as GO and conducting polymers, to create bismuth, nanocomposites can increase performance because of the enhanced charge transfer introduced by the availability of large surface areas or rapid ion transit along the conducting network. The specific capacitance and charge storage capacity of nano composites are determined by their shapes, dimensions, and surfaces. In summary, more investigation into the kinetics of ion mobility and mass transfer at the electrode/electrolyte interface is necessary to understand the reaction kinetics in the bismuth electrochemical system fully (Fig. 11).
 |
| Fig. 11 Schematic of bismuth-based nanoparticles for supercapacitors. | |
3.4 Bismuth-based nanoparticles for sensors
Both bismuth-based nanoparticles and their composites are effective heavy metal and electrochemical sensors.175,176 In contemporary electro-analysis, bismuth nanoparticles (BiNPs), Bi2O3 or Bi2S3, and Bismuth alloy NPs alongside more metals, such as titanium or silver, have all gained significant importance. In keeping with this area of research, a unique technique for creating a nanocomposite made of graphene oxide and BBN has been designed to more precisely determine cadmium(II) and lead(II).177
A new 3D honeycomb-shaped n-doped carbon nanosheet structure with a particular surface area has been developed to identify heavy metal ions, such as Pb2+ and Cd2+.178 It is studded with BBN porous network structures. The production process for this framework is low-cost. To detect mercury (Hg II), a 3-D hierarchy arrangement of bismuth-based nanoparticles formed from carbon–graphene nanotube nanocomposites has been developed and employed electrocatalytically. In contrast, palladium-doped perovskite bismuth ferrite demonstrated excellent sensitivity and selectivity for NO2-gas sensing capabilities.179 The development of pesticide sensors has garnered significant attention. Consequently, research has been conducted on an electrode made of carbon paste and augmented with bismuth ferrite microflowers. The results show that it has a meager 0.81 M detection limit. Moreover, cobalt-modified copper bismuth oxide with a current density of 0.80 mA cm2 was created and used for photoelectrochemical applications. An electrochemical sensor consisting of BBNs with large surfaces and exceptional ability to conduct electricity, carbon nanofiber, and the ionic liquid was created180 to detect Pb and Cd at concentrations range of 2–120 g L−1. Consequently, numerous studies have shown that bismuth-based nanoparticles are excellent options for gas detection, heavy metal identification, and electrochemical detection (Fig. 12).
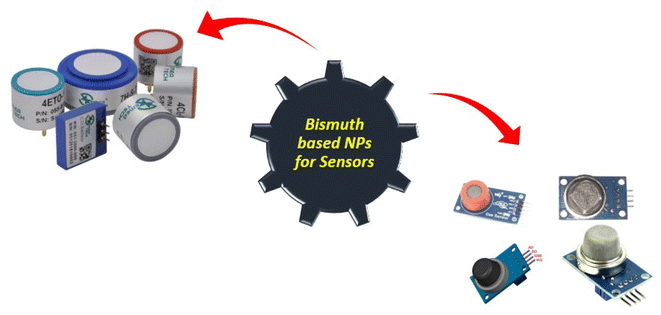 |
| Fig. 12 Schematic of bismuth-based nanoparticles for sensor application. | |
3.5 Bismuth-based nanoparticles for photocatalytic degradation of dyes
Of all the cutting-edge technologies available to address environmental issues, photocatalysis is the most promising.181 A possible technique for breaking down resistant organic contaminants in water is photo catalysis.182 Photo catalysts are highly versatile and offer advantages such as enhanced efficiency, reduced toxicity, economical cost, and favorable chemical and physical characteristics. The ability of semiconductor photocatalysis to function under ambient settings without the need for additional energy sources is one of its main advantages.183 Semiconductors based on bismuth are a new and exciting family of enhanced photocatalytic materials that have recently come to light. Semiconductors based on bismuth feature a broadband gap for visible-light sensitivity and a well-dispersed valence band composed of hybrid Bi 6s and O2 p orbitals, making them a viable option for other metal oxide semiconductors. Hydrothermal synthesis and in situ precipitation were used to manufacture ZnO/BiOCl nano composites modified with Ag nanoparticles.184 It has been demonstrated that Bi2O3, with a band gap of 2.58–2.85 eV, is a very effective visible-light-driven photocatalyst for water splitting and pollutant breakdown.185,186 The three different organic dyes, Acid Yellow (AY-29), Coomassie Brilliant Blue G250 (CBBG-250), and Acid Green 25 (AG-25), were degraded using bismuth oxide doped with Ce and Nd. The outcome indicates that the doped α-Bi2O3 is more effective at photo-catalytic decomposition than the pure α-Bi2O3 nanoparticle.187 Similarly, as documented earlier in the literature, BBNs can effectively break down phenol, decrease Cr4+ to Cr3+, and break down Rhodamine B.188–194 We were also interested in the PCP degradation and sun irradiation MO degradation, as described for Bi4TaO8I.195 When BiOBr (made with different solvents) is exposed to UV light, it degrades phenol more quickly and on a larger surface area.196 Due to the lowest band gap under UV, the hydrogen evolution rate was higher in 0.2 weight percent Pt distributed on Bi2YVO8 than in 0.2 weight percent Pt scattered across Bi2GaVO7,197 Bi2YTaO7,198 and Bi2InTaO7. Based on the literature reviews, it can be inferred that bismuth chemistry might play a significant role in creating high-performance photocatalysts that reduce pollution more effectively than most similar commercial goods (Table 2).
Table 2 Photocatalytic performance of various bismuth-based compounds against different dyes
S. no |
Bismuth compounds |
Crystal morphology of compounds |
Band gap (eV) |
Dye degraded |
Time for degradation (min) and % removal |
References |
01 |
RGO-Bi2O3 |
Needle-like |
2.8 |
Methylene blue |
240 and 98 |
198 |
02 |
Gd:BFO |
Rhombohedral |
2.21 |
Crystal violet |
180 and 84.5 |
199 |
03 |
BiFeO3(BFO) |
Spherical |
2.07 |
RB5 |
50 and 99.9 |
200 |
04 |
Bi-TNT |
Tubular |
3.18 |
Rhodamine-B |
180 and 100 |
201 |
05 |
BGFSO/GNP |
Sheet and granular |
2.1 |
Congo-red (CR) |
100 and 74 |
202 |
06 |
BiFe(1−x)NixO3 |
Agglomerated and irregular |
2.02 |
Acid red-85 |
40 and 100 |
203 |
07 |
BFO |
Hexahedral |
1.9 |
Azo |
135 and 95 |
204 |
08 |
BFO |
Rhombohedral |
2.17 |
Methylene blue |
90 and 100 |
205 |
09 |
BiFeO3 |
Spherical |
2.00 |
Methylene blue |
120 and 94.4 |
206 |
10 |
Bi2O3 |
Irregular |
2.25 |
Alizarin red |
120 and 99.25 |
207 |
11 |
G-BiOBr |
Irregular spherical shapes |
2.66 |
Rhodamine-B |
70 and 100 |
208 |
12 |
Ce/Nd–Bi2O3 |
Needle-/rod-like |
— |
Acid yellow-coomassie brilliant blue |
120 and 85, 82 |
186 |
120 and 84, 88 |
13 |
TiO2/Bi2O3 |
Agglomerated |
3.07 and 2.94 |
Orange II |
180 and 94.7, 81.8 |
209 |
14 |
Au–BiVO4 |
Spherical, triangular, square, rhombic, pentagonal |
— |
Methylene blue |
360 and 95 |
210 |
15 |
Bi2WO6 |
Spherical shape |
2.8 |
Eriochrome black T (EBT) |
180 and 74 |
211 |
16 |
Ag–BiOCl |
Flower-like |
— |
Rhodamine B |
100 and 99 |
212 |
17 |
Bi@SiNWs |
— |
1.20 |
Methylene blue (MB) |
120 and 89 |
213 |
18 |
BiFeO3 |
Agglomerated |
2.2 |
Brilliant blue |
450 and 90 |
214 |
19 |
Bi2(CO3)O2 |
Cubic |
3.3 |
Rhodamine B |
480 and 98, 84 |
215 |
Bi12SiO20 |
3.6 |
5-HMF |
20 |
SnS2/AgBiS2/GO |
Flower-like, sea urchin-like, two-dimensional |
— |
Acetaminophen |
— |
216 |
21 |
Polymer/BiPO4/BiOCl |
Nanoparticles, nanosheets, tubular |
— |
Catechol |
— |
217 |
Discussing the efficiency and versatility of bismuth oxide nanoparticles in medical applications is important. With their inherent antibacterial qualities, these nanoparticles show versatility in their ability to perform various functions, including therapeutic agents and efficient contrast agents in imaging techniques. Because of their low toxicity and biocompatibility, they are excellent choices for targeted drug delivery systems that increase the therapeutic index of various drugs. Furthermore, bismuth oxide nanoparticles distinct for optical and electrical characteristics demonstrate their versatility by opening up their possible uses in photothermal therapy and diagnostic imaging. According to recent research, these nanoparticles can successfully stop the growth of bacteria, suggesting that they may be used to treat infections resistant to antibiotics. To enhance their effectiveness in clinical settings, further research endeavors are required to optimize their synthesis and functionalization. The increasing amount of data highlights the revolutionary potential of bismuth oxide nanoparticles in improving therapeutic approaches and medical technologies (Fig. 13).
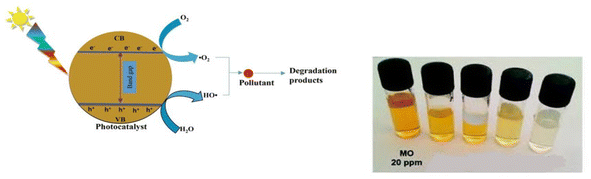 |
| Fig. 13 Schematic of bismuth-based nanoparticles for photocatalytic degradation of dyes. | |
4. Conclusion and future perspective
This review emphasizes the vast potential of bismuth-based nanoparticles and nanocomposites, highlighting their diverse synthesis methods and applications. The focus on greener synthesis and interdisciplinary collaboration can pave the way for innovative advancements. Exploring bio-inspired and eco-friendly methods for the production of bismuth-based nanoparticles is crucial for reducing environmental impacts. The adoption of continuous-flow synthesis techniques and automation can enhance the scalability and reproducibility of these materials, making them more suitable for industrial applications. Furthermore, the investigation into novel application areas, such as targeted drug delivery, theranostics, and bioimaging, could open new frontiers in medicine, leveraging bismuth's low toxicity compared to other heavy metals.
The integration of bismuth nanoparticles with innovative materials, such as graphene or carbon nanotubes, could yield hybrid nanocomposites with enhanced performance and multifunctionality. This approach can broaden applications in electronics, sensors, and catalysis. Additionally, the exploration of bismuth-based nanoparticles in energy storage devices, particularly supercapacitors, holds promise for advancing emerging energy technologies. However, it is essential to address and mitigate potential environmental and health concerns associated with bismuth nanoparticles to ensure their responsible and sustainable development. By fostering continued exploration in these domains, researchers can significantly contribute to the field of nanoscience and facilitate impactful advancements that align with sustainability goals.
Data availability
The datasets used and analysed during the current study are available from the corresponding author upon reasonable request.
Conflicts of interest
There is no conflict of interest.
References
- R. He, D. Xu, B. Cheng, J. Yu and W. Ho, Nanoscale Horiz., 2018, 3, 464–504 RSC.
- J. C. Gallo, J. L. Craycraft and S. C. Bush, Rev. Ind. Organ., 1985, 2, 106–130 CrossRef.
- K. H. Barad, D. S. Sharma and V. Vyas, Procedia Eng., 2013, 51, 770–775 CrossRef.
- S. S. Vedam, P. J. Keall, V. R. Kini, H. Mostafavi, H. P. Shukla and R. Mohan, Phys. Med. Biol., 2003, 48, 45–62 CrossRef PubMed.
- C. F. Gallo, B. S. Chandrasekhar and P. H. Sutter, J. Appl. Phys., 1963, 34, 144–152 CrossRef.
- F. Aricak and E. Caglarer, in Sosyal Beşeri Ve İdari Bilimler Alanında Uluslararası Araştırmalar X, 2023, pp. 157–172 Search PubMed.
- A. Tripathi, J. Debelius, D. A. Brenner, M. Karin, R. Loomba, B. Schnabl and R. Knight, Nat. Rev. Gastroenterol. Hepatol., 2018, 15, 397–411 CrossRef.
- Z. Klimont, K. Kupiainen, C. Heyes, P. Purohit, J. Cofala, P. Rafaj, J. Borken-Kleefeld and W. Schöpp, Atmos. Chem. Phys., 2016, 17(14) DOI:10.5194/acp-17-8681-2017.
- I. Puzanov, A. Diab, K. Abdallah, C. O. Bingham, C. Brogdon, R. Dadu, L. Hamad, S. Kim, M. E. Lacouture, N. R. LeBoeuf, D. Lenihan, C. Onofrei, V. Shannon, R. Sharma, A. W. Silk, D. Skondra, M. E. Suarez-Almazor, Y. Wang, K. Wiley, H. L. Kaufman and M. S. Ernstoff, J. ImmunoTher. Cancer., 2017, 5, 95 CrossRef PubMed.
- O. Salata, J. Nanobiotechnol., 2004, 2, 3 CrossRef.
- P. Bhattacharya and A. F. Keating, Toxicol. Appl. Pharmacol., 2012, 261, 227–235 CrossRef PubMed.
- L. Yan, C. Rong and G. Zhao, Strengthen Cloud Computing Security with Federal Identity Management Using Hierarchical Identity-Based Cryptography, 2009, pp. 167–177, https://link.springer.com/chapter/10.1007/978-3-642-10665-1_15 Search PubMed.
- B. Karn, T. Kuiken and M. Otto, Environ. Health Perspect., 2009, 117, 1813–1831 CrossRef PubMed.
- T. H. A. Alabri, A. H. S. Al Musalami, M. A. Hossain, A. M. Weli and Q. Al-Riyami, J. King Saud Univ. Sci., 2014, 26, 237–243 CrossRef.
- T. Sruthi, R. Gandhimathi, S. T. Ramesh and P. V. Nidheesh, Chemosphere, 2018, 210, 38–43 CrossRef.
- C. Buzea, I. I. Pacheco and K. Robbie, Biointerphases, 2007, 2, MR17–MR71 CrossRef PubMed.
- M. Shahzad, R. Ali, M. Khan, H. Hou, S. Azam, A. Deifalla, A. E. Ragab, A. Zada, Z. Ali, M. Khan, S. Batool and M. Z. Ansari, Opt. Mater., 2023, 144, 114288 CrossRef.
- M. Humayun, A. Zada, Z. Li, M. Xie, X. Zhang, Y. Qu, F. Raziq and L. Jing, Appl. Catal., B, 2016, 180, 219–226 CrossRef.
- T. Gilkerson, W. Sanford, Y. Li and M. Ronayne, Understanding
carbon nanoparticle transport in saturated porous media: the influence of dissolved organic matter, Theses and Dissertations, Colorado State University, 2020 Search PubMed.
- Z. Wei Seh, W. Li, J. J. Cha, G. Zheng, Y. Yang, M. T. McDowell, P.-C. Hsu and Y. Cui, Nat. Commun., 2013, 4, 1331 CrossRef PubMed.
- R. Ferrando, J. Jellinek and R. L. Johnston, Chem. Rev., 2008, 108, 845–910 CrossRef PubMed.
- S. Li, S. Gu, W. Liu, H. Han and Q. Zhang, Catena, 2008, 75, 216–222 CrossRef.
- M. Uddin and A. Raj Chowdhury, in International Conference on Engineering Education, 2001 Search PubMed.
- J. Jeevanandam, A. Barhoum, Y. S. Chan, A. Dufresne and M. K. Danquah, Beilstein J. Nanotechnol., 2018, 9, 1050–1074 CrossRef PubMed.
- M. Calandra, Phys. Rev. B: Condens. Matter Mater. Phys., 2013, 88, 245428 CrossRef.
- G. Della Porta and E. Reverchon, in Modular Tissue Engineering: An Artificial Extracellular Matrix to Address and Stimulate Regeneration/Differentiation, 2018, pp. 191–210 Search PubMed.
- F. Lenzini, J. Janousek, O. Thearle, M. Villa, B. Haylock, S. Kasture, L. Cui, H.-P. Phan, D. V. Dao, H. Yonezawa, P. K. Lam, E. H. Huntington and M. Lobino, Sci. Adv., 2018, 4(12), eaat9331 CrossRef.
- B. Burtness, K. J. Harrington, R. Greil, D. Soulières, M. Tahara, G. de Castro, A. Psyrri, N. Basté, P. Neupane, Å. Bratland, T. Fuereder, B. G. M. Hughes, R. Mesía, N. Ngamphaiboon, T. Rordorf, W. Z. Wan Ishak, R.-L. Hong, R. González Mendoza, A. Roy, Y. Zhang, B. Gumuscu, J. D. Cheng, F. Jin, D. Rischin, G. Lerzo, M. Tatangelo, M. Varela, J. J. Zarba, M. Boyer, H. Gan, B. Gao, B. Hughes, G. Mallesara, D. Rischin, A. Taylor, M. Burian, T. Fuereder, R. Greil, C. H. Barrios, D. O. de Castro Junior, G. Castro, F. A. Franke, G. Girotto, I. P. F. Lima, U. R. Nicolau, G. D. J. Pinto, L. Santos, A.-P. Victorino, N. Chua, F. Couture, R. Gregg, A. Hansen, J. Hilton, J. McCarthy, D. Soulieres, R. Ascui, P. Gonzalez, L. Villanueva, M. Torregroza, A. Zambrano, P. Holeckova, Z. Kral, B. Melichar, J. Prausova, M. Vosmik, M. Andersen, N. Gyldenkerne, H. Jurgens, K. Putnik, P. Reinikainen, V. Gruenwald, S. Laban, G. Aravantinos, I. Boukovinas, V. Georgoulias, A. Psyrri, D. Kwong, Y. Al-Farhat, T. Csoszi, J. Erfan, G. Horvai, L. Landherr, E. Remenar, A. Ruzsa, J. Szota, S. Billan, I. Gluck, O. Gutfeld, A. Popovtzer, M. Benasso, S. Bui, V. Ferrari, L. Licitra, F. Nole, T. Fujii, Y. Fujimoto, N. Hanai, H. Hara, K. Matsumoto, K. Mitsugi, N. Monden, M. Nakayama, K. Okami, N. Oridate, K. Shiga, Y. Shimizu, M. Sugasawa, M. Tahara, M. Takahashi, S. Takahashi, K. Tanaka, T. Ueda, H. Yamaguchi, T. Yamazaki, R. Yasumatsu, T. Yokota, T. Yoshizaki, I. Kudaba, Z. Stara, W. Z. Wan Ishak, S. K. Cheah, J. Aguilar Ponce, R. Gonzalez Mendoza, C. Hernandez Hernandez, F. Medina Soto, J. Buter, A. Hoeben, S. Oosting, K. Suijkerbuijk, A. Bratland, M. Brydoey, R. Alvarez, L. Mas, P. Caguioa, J. Querol, E. E. Regala, M. B. Tamayo, E. M. Villegas, A. Kawecki, A. Karpenko, A. Klochikhin, A. Smolin, O. Zarubenkov, B. C. Goh, G. Cohen, J. du Toit, C. Jordaan, G. Landers, P. Ruff, W. Szpak, N. Tabane, I. Brana, L. Iglesias Docampo, J. Lavernia, R. Mesia, E. Abel, V. Muratidu, N. Nielsen, V. Cristina, T. Rordorf, S. Rothschild, R.-L. Hong, H.-M. Wang, M.-H. Yang, S.-P. Yeh, C.-J. Yen, N. Ngamphaiboon, N. Soparattanapaisarn, V. Sriuranpong, S. Aksoy, I. Cicin, M. Ekenel, H. Harputluoglu, O. Ozyilkan, K. Harrington, S. Agarwala, H. Ali, R. Alter, D. Anderson, J. Bruce, B. Burtness, N. Campbell, M. Conde, J. Deeken, W. Edenfield, L. Feldman, E. Gaughan, B. Goueli, B. Halmos, U. Hegde, B. Hunis, R. Jotte, A. Karnad, S. Khan, N. Laudi, D. Laux, D. Martincic, S. McCune, D. McGaughey, K. Misiukiewicz, D. Mulford, E. Nadler, P. Neupane, J. Nunnink, J. Ohr, M. O'Malley, B. Patson, D. Paul, E. Popa, S. Powell, R. Redman, V. Rella, C. Rocha Lima, A. Sivapiragasam, Y. Su, A. Sukari, S. Wong, E. Yilmaz and J. Yorio, Lancet, 2019, 394, 1915–1928 CrossRef PubMed.
- M. A. Soytas, M. Denizel and D. Durak Usar, Int. J. Prod. Econ., 2019, 210, 56–71 CrossRef.
- A. V. Rane, K. Kanny, V. K. Abitha and S. Thomas, in Synthesis of Inorganic Nanomaterials, Elsevier, 2018, pp. 121–139 Search PubMed.
- S. Stankic, S. Suman, F. Haque and J. Vidic, J. Nanobiotechnol., 2016, 14, 73 CrossRef PubMed.
- N. N. Wijayawardene, K. D. Hyde, K. C. Rajeshkumar, D. L. Hawksworth, H. Madrid, P. M. Kirk, U. Braun, R. V. Singh, P. W. Crous, M. Kukwa, R. Lücking, C. P. Kurtzman, A. Yurkov, D. Haelewaters, A. Aptroot, H. T. Lumbsch, E. Timdal, D. Ertz, J. Etayo, A. J. L. Phillips, J. Z. Groenewald, M. Papizadeh, L. Selbmann, M. C. Dayarathne, G. Weerakoon, E. B. G. Jones, S. Suetrong, Q. Tian, R. F. Castañeda-Ruiz, A. H. Bahkali, K.-L. Pang, K. Tanaka, D. Q. Dai, J. Sakayaroj, M. Hujslová, L. Lombard, B. D. Shenoy, A. Suija, S. S. N. Maharachchikumbura, K. M. Thambugala, D. N. Wanasinghe, B. O. Sharma, S. Gaikwad, G. Pandit, L. Zucconi, S. Onofri, E. Egidi, H. A. Raja, R. Kodsueb, M. E. S. Cáceres, S. Pérez-Ortega, P. O. Fiuza, J. S. Monteiro, L. N. Vasilyeva, R. G. Shivas, M. Prieto, M. Wedin, I. Olariaga, A. A. Lateef, Y. Agrawal, S. A. S. Fazeli, M. A. Amoozegar, G. Z. Zhao, W. P. Pfliegler, G. Sharma, M. Oset, M. A. Abdel-Wahab, S. Takamatsu, K. Bensch, N. I. de Silva, A. De Kesel, A. Karunarathna, S. Boonmee, D. H. Pfister, Y.-Z. Lu, Z.-L. Luo, N. Boonyuen, D. A. Daranagama, I. C. Senanayake, S. C. Jayasiri, M. C. Samarakoon, X.-Y. Zeng, M. Doilom, L. Quijada, S. Rampadarath, G. Heredia, A. J. Dissanayake, R. S. Jayawardana, R. H. Perera, L. Z. Tang, C. Phukhamsakda, M. Hernández-Restrepo, X. Ma, S. Tibpromma, L. F. P. Gusmao, D. Weerahewa and S. C. Karunarathna, Fungal Divers., 2017, 86, 1–594 CrossRef.
- N. Anton and T. F. Vandamme, Pharm. Res., 2011, 28, 978–985 CrossRef PubMed.
- J. M. Alonso, A. N. Stepanova, T. J. Leisse, C. J. Kim, H. Chen, P. Shinn, D. K. Stevenson, J. Zimmerman, P. Barajas, R. Cheuk, C. Gadrinab, C. Heller, A. Jeske, E. Koesema, C. C. Meyers, H. Parker, L. Prednis, Y. Ansari, N. Choy, H. Deen, M. Geralt, N. Hazari, E. Hom, M. Karnes, C. Mulholland, R. Ndubaku, I. Schmidt, P. Guzman, L. Aguilar-Henonin, M. Schmid, D. Weigel, D. E. Carter, T. Marchand, E. Risseeuw, D. Brogden, A. Zeko, W. L. Crosby, C. C. Berry and J. R. Ecker, Science, 2003, 301, 653–657 CrossRef PubMed.
- S. K. Pramanik, F. B. Suja, S. M. Zain and B. K. Pramanik, Bioresour. Technol. Rep., 2019, 8, 100310 CrossRef.
- A. Rane and A. Kumar, in IEEE 42nd Annual Computer Software and Applications Conference (COMPSAC), IEEE, 2018, pp. 769–773 Search PubMed.
- J. Varughese Jose, A. Mary Ealias, M. Saravanakumar and M. P. Saravanakumar, Nat. Environ. Pollut. Technol., 2017, 16, 89–97 Search PubMed.
- A. K. Mittal, Y. Chisti and U. C. Banerjee, Biotechnol. Adv., 2013, 31, 346–356 CrossRef PubMed.
- H. Zhou, Q. Chen, G. Li, S. Luo, T. Song, H.-S. Duan, Z. Hong, J. You, Y. Liu and Y. Yang, Science, 2014, 345, 542–546 CrossRef.
- V. V Makarov, A. J. Love, O. V. Sinitsyna, S. S. Makarova, I. V. Yaminsky, M. E. Taliansky and N. O. Kalinina, Acta Naturae, 2014, 6, 35–44 CrossRef.
- C. M. O’Reilly, S. Sharma, D. K. Gray, S. E. Hampton, J. S. Read, R. J. Rowley, P. Schneider, J. D. Lenters, P. B. McIntyre, B. M. Kraemer, G. A. Weyhenmeyer, D. Straile, B. Dong, R. Adrian, M. G. Allan, O. Anneville, L. Arvola, J. Austin, J. L. Bailey, J. S. Baron, J. D. Brookes, E. de Eyto, M. T. Dokulil, D. P. Hamilton, K. Havens, A. L. Hetherington, S. N. Higgins, S. Hook, L. R. Izmest’eva, K. D. Joehnk, K. Kangur, P. Kasprzak, M. Kumagai, E. Kuusisto, G. Leshkevich, D. M. Livingstone, S. MacIntyre, L. May, J. M. Melack, D. C. Mueller-Navarra, M. Naumenko, P. Noges, T. Noges, R. P. North, P. Plisnier, A. Rigosi, A. Rimmer, M. Rogora, L. G. Rudstam, J. A. Rusak, N. Salmaso, N. R. Samal, D. E. Schindler, S. G. Schladow, M. Schmid, S. R. Schmidt, E. Silow, M. E. Soylu, K. Teubner, P. Verburg, A. Voutilainen, A. Watkinson, C. E. Williamson and G. Zhang, Geophys. Res. Lett., 2015, 42(24), 773–781 Search PubMed.
- N. Mansbridge, J. Mitsch, N. Bollard, K. Ellis, G. G. Miguel-Pacheco, T. Dottorini and J. Kaler, Sensors, 2018, 18, 3532 CrossRef PubMed.
- D. Elbaz, M. Dickinson, H. S. Hwang, T. Díaz-Santos, G. Magdis, B. Magnelli, D. Le Borgne, F. Galliano, M. Pannella, P. Chanial, L. Armus, V. Charmandaris, E. Daddi, H. Aussel, P. Popesso, J. Kartaltepe, B. Altieri, I. Valtchanov, D. Coia, H. Dannerbauer, K. Dasyra, R. Leiton, J. Mazzarella, D. M. Alexander, V. Buat, D. Burgarella, R.-R. Chary, R. Gilli, R. J. Ivison, S. Juneau, E. Le Floc'h, D. Lutz, G. E. Morrison, J. R. Mullaney, E. Murphy, A. Pope, D. Scott, M. Brodwin, D. Calzetti, C. Cesarsky, S. Charlot, H. Dole, P. Eisenhardt, H. C. Ferguson, N. Förster Schreiber, D. Frayer, M. Giavalisco, M. Huynh, A. M. Koekemoer, C. Papovich, N. Reddy, C. Surace, H. Teplitz, M. S. Yun and G. Wilson, Astron. Astrophys., 2011, 533, A119 CrossRef.
- B. W. Coad and N. A. Hussain, Zool. Middle East, 2007, 40, 107–109 CrossRef.
- M. A. Khan, H. H. Ngo, W. S. Guo, Y. Liu, L. D. Nghiem, F. I. Hai, L. J. Deng, J. Wang and Y. Wu, Bioresour. Technol., 2016, 219, 738–748 CrossRef.
- F. Iazdani and A. Nezamzadeh-Ejhieh, Environ. Sci. Pollut. Res., 2021, 28, 53314–53327 CrossRef.
- J. M. Cénat, N. Felix, C. Blais-Rochette, C. Rousseau, J. Bukaka, D. Derivois, P.-G. Noorishad and J.-P. Birangui, Psychiatr. Res., 2020, 289, 113033 CrossRef PubMed.
- A. Matilla, J. Mariné, J. Pérez, C. Cadevall and R. Artigas, in Three-dimensional measurements with a novel technique combination of Confocal and Focus Variation with a simultaneous scan, ed. C. Gorecki, A. K. Asundi and W. Osten, 2016, p. 98900B Search PubMed.
- J. Wu, D. Zhao, S. Wu and D. Wang, Eur. J. Pharmacol., 2015, 748, 30–36 CrossRef.
- J. R. Cole, Q. Wang, E. Cardenas, J. Fish, B. Chai, R. J. Farris, A. S. Kulam-Syed-Mohideen, D. M. McGarrell, T. Marsh, G. M. Garrity and J. M. Tiedje, Nucleic Acids Res., 2009, 37, D141–D145 CrossRef.
- J. Yang, S. Li, J. Su and X. Yu, Automatica, 2013, 49, 2287–2291 CrossRef.
- M. Anilkumar, R. Pasricha and V. Ravi, Ceram. Int., 2005, 31, 889–891 CrossRef.
- Q. Yang, Y. Li, Q. Yin, P. Wang and Y.-B. Cheng, Mater. Lett., 2002, 55, 46–49 CrossRef.
- V. C. de Sousa, M. R. Morelli and R. H. G. Kiminami, Ceram. Int., 2000, 26, 561–564 CrossRef.
- M. Kashif, S. Muhammad, A. Ali, K. Ali, S. Khan, S. Zahoor and M. Hamza, J. Xi'an Shiyou Univ., Nat. Sci. Ed., 2023, 19, 521–544 Search PubMed.
- P. M. Aneesh, K. A. Vanaja and M. K. Jayaraj, Synthesis of ZnO nanoparticles by hydrothermal method, in Nanophotonic Materials IV, ed. Z. Gaburro and S. Cabrini, SPIE, 2007, vol. 6639, p. 66390J Search PubMed.
- I. Ghani, M. Kashif, O. Ali Khattak, M. Shah, S. Nawaz, S. Ullah, S. Murad, S. Naz, H. W. Khan, S. Muhammad and M. Jamal, J. Xi'an Shiyou Univ., Nat. Sci. Ed., 2023, 19, 1195–1217 Search PubMed.
- S. A. Corr, Y. K. Gun'ko, A. P. Douvalis, M. Venkatesan, R. D. Gunning and P. D. Nellist, J. Phys. Chem. C, 2008, 112, 1008–1018 CrossRef.
- S. S. Madani, A. Habibi-Yangjeh, S. Asadzadeh-Khaneghah, H. Chand, V. Krishnan and A. Zada, J. Taiwan Inst. Chem. Eng., 2021, 119, 177–186 CrossRef.
- D. M. Antonelli and J. Y. Ying, Angew Chem. Int. Ed. Engl., 1995, 34, 2014–2017 CrossRef.
- R. M. Alwan, Q. A. Kadhim, K. M. Sahan, R. A. Ali, R. J. Mahdi, N. A. Kassim and A. N. Jassim, Nanotechnol. Nanosci., 2015, 5, 1–6 Search PubMed.
- R. Wahab, S. G. Ansari, M.
A. Dar, Y. S. Kim and H. S. Shin, Mater. Sci. Forum, 2007, 558–559, 983–986 Search PubMed.
- L. Armelao, D. Barreca, M. Bertapelle, G. Bottaro, C. Sada and E. Tondello, Thin Solid Films, 2003, 442, 48–52 CrossRef.
- D. J. Suh and T.-J. Park, Chem. Mater., 1996, 8, 509–513 CrossRef.
- G. Li and J. Zhang, Appl. Surf. Sci., 2012, 258, 7612–7616 CrossRef.
- X. Liang, M. Sun, L. Li, R. Qiao, K. Chen, Q. Xiao and F. Xu, Dalton Trans., 2012, 41, 2804 RSC.
- P. Mallick, Proc. Natl. Acad. Sci. India Sect. A, 2014, 84, 387–389 CrossRef.
- C. Gionco, M. C. Paganini, E. Giamello, R. Burgess, C. Di Valentin and G. Pacchioni, J. Phys. Chem. Lett., 2014, 5, 447–451 CrossRef.
- J. Buha, D. Arčon, M. Niederberger and I. Djerdj, Phys. Chem. Chem. Phys., 2010, 12, 15537 RSC.
- M. Mallahi, S. Ali, M. R. Vaezi, A. Esmaeilirad and V. Mazinani, Am. J. Eng. Res., 2014, 3, 162–165 Search PubMed.
- M. Baghbanzadeh, L. Carbone, P. D. Cozzoli and C. O. Kappe, Angew. Chem., Int. Ed., 2011, 50, 11312–11359 CrossRef CAS.
- E. Bartonickova, J. Cihlar and K. Castkova, Process. Appl. Ceram., 2007, 1, 29–33 CrossRef.
- J. Fang, K. L. Stokes, J. A. Wiemann, W. L. Zhou, J. Dai, F. Chen and C. J. O'Connor, Mater. Sci. Eng. B, 2001, 83, 254–257 CrossRef.
- M. Sanchez-Dominguez, M. Boutonnet and C. Solans, J. Nanopart. Res., 2009, 11, 1823–1829 CrossRef.
- S. Karandikar, A. Mirani, V. Waybhase, V. B. Patravale and S. Patankar, in Nanostructures for Oral Medicine, Elsevier, 2017, pp. 263–293 Search PubMed.
- W. Wu, Q. He and C. Jiang, Nanoscale Res. Lett., 2008, 3, 397 CrossRef PubMed.
- R. Zhang and L. Gao, Mater. Res. Bull., 2002, 37, 1659–1666 CrossRef.
- A. Bumajdad and M. Madkour, Nanoscale Res. Lett., 2015, 10, 19 CrossRef PubMed.
- A. Kumar, A. Saxena, A. De, R. Shankar and S. Mozumdar, RSC Adv., 2013, 3, 5015 RSC.
- A. J. Zarur and J. Y. Ying, Nature, 2000, 403, 65–67 CrossRef PubMed.
- P. Tartaj and J. Tartaj, Chem. Mater., 2002, 14, 536–541 CrossRef.
- S. Stankic, M. Sterrer, P. Hofmann, J. Bernardi, O. Diwald and E. Knözinger, Nano Lett., 2005, 5, 1889–1893 CrossRef.
- S. I. Dolgaev, A. V. Simakin, V. V. Voronov, G. A. Shafeev and F. Bozon-Verduraz, Appl. Surf. Sci., 2002, 186, 546–551 CrossRef.
- R. K. Thareja and S. Shukla, Appl. Surf. Sci., 2007, 253, 8889–8895 CrossRef.
- A. Rahman and G. Guisbiers, Metals, 2024, 14, 224 CrossRef.
- Z. Liu, D. Zhang, S. Han, C. Li, T. Tang, W. Jin, X. Liu, B. Lei and C. Zhou, Adv. Mater., 2003, 15, 1754–1757 CrossRef.
- A. K. Mahmoud, Z. Fadhill, S. I. Al-nassar, F. Ibrahim Husein, E. Akman and A. Demir, J. Mater. Sci. Eng. B, 2013, 3(6), 364–368 Search PubMed.
- S. Dadashi, R. Poursalehi and H. Delavari, Procedia Mater. Sci., 2015, 11, 722–726 CrossRef.
- M. Kusper and G. Guisbiers, MRS Adv., 2018, 3, 3899–3903 CrossRef.
- G. Bajaj and R. K. Soni, J. Nanopart. Res., 2010, 12, 2597–2603 CrossRef.
- M. A. Gondal, T. F. Qahtan, M. A. Dastageer, Y. W. Maganda and D. H. Anjum, J. Nanosci. Nanotechnol., 2013, 13, 5759–5766 CrossRef PubMed.
- F. Bozon-Verduraz, F. Fiévet, J.-Y. Piquemal, R. Brayner, K. El Kabouss, Y. Soumare, G. Viau and G. Shafeev, Braz. J. Phys., 2009, 39, 134–140 CrossRef.
- G. Dorcioman, D. Ebrasu, I. Enculescu, N. Serban, E. Axente, F. Sima, C. Ristoscu and I. N. Mihailescu, J. Power Sources, 2010, 195, 7776–7780 CrossRef.
- R. A. Ismail and F. A. Fadhil, J. Mater. Sci.: Mater. Electron., 2014, 25, 1435–1440 CrossRef CAS.
- R. Zamiri, A. Zakaria, H. A. Ahangar, M. Darroudi, A. K. Zak and G. P. C. Drummen, J. Alloys Compd., 2012, 516, 41–48 CrossRef CAS.
- M. T. Swihart, Curr. Opin. Colloid Interface Sci., 2003, 8, 127–133 CrossRef CAS.
- P. Hofmann, K. -H. Jacob and E. Knözinger, Ber. Bunsenges. Phys. Chem., 1993, 97, 316–318 CrossRef.
- L. Kumari, J.-H. Lin and Y.-R. Ma, Nanotechnology, 2007, 18, 295605 CrossRef.
- T. Terasako, M. Yagi, M. Ishizaki, Y. Senda, H. Matsuura and S. Shirakata, Surf. Coat. Technol., 2007, 201, 8924–8930 CrossRef.
- S. Polarz, A. Roy, M. Merz, S. Halm, D. Schröder, L. Schneider, G. Bacher, F. E. Kruis and M. Driess, Small, 2005, 1, 540–552 CrossRef PubMed.
- D. Amara, J. Grinblat and S. Margel, J. Mater. Chem., 2012, 22, 2188–2195 RSC.
- A. El Kasmi, Z.-Y. Tian, H. Vieker, A. Beyer and T. Chafik, Appl. Catal., B, 2016, 186, 10–18 CrossRef.
- S. Stankic, J. Bernardi, O. Diwald and E. Knözinger, J. Phys. Chem. B, 2006, 110, 13866–13871 CrossRef.
- R. Naeem, S. Ahmed, K. M. Lo, W. J. Basirun, R. Yahya, M. Misran, T. A. N. Peiris, J. S. Sagu, K. G. U. Wijayantha, A. K. Thapa, G. U. Sumanasekera and M. Mazhar, Chem. Vap. Deposition, 2015, 21, 360–368 CrossRef.
- S. Stankic, J. Bernardi, O. Diwald and E. Knözinger, J. Phys. Chem. C, 2007, 111, 8069–8074 CrossRef.
- P. Haniam, C. Kunsombat, S. Chiangga and A. Songsasen, Sci. World J., 2014, 2014, 1–6 CrossRef.
- S. C. Yadav and M. Dattatraya Uplane, Int. J. Eng. Sci. Technol., 2012, 4, 4893–4898 Search PubMed.
- R. Schmechel, M. Kennedy, H. von Seggern, H. Winkler, M. Kolbe, R. A. Fischer, L. Xaomao, A. Benker, M. Winterer and H. Hahn, J. Appl. Phys., 2001, 89, 1679–1686 CrossRef CAS.
- T. Berger, J. Schuh, M. Sterrer, O. Diwald and E. Knozinger, J. Catal., 2007, 247, 61–67 CrossRef CAS.
- J. La, Y. Huang, G. Luo, J. Lai, C. Liu and G. Chu, Part. Sci. Technol., 2013, 31, 287–290 CrossRef CAS.
- S. Stankic, M. Cottura, D. Demaille, C. Noguera and J. Jupille, J. Cryst. Growth, 2011, 329, 52–56 CrossRef CAS.
- R. Shashanka, K. Yasemin, T. Recep, C. Yusuf, A. Savaş Bülbül, O. Uzun and A. Cahit Karaoğlanlı, Res. Lett. Phys. Chem., 2019, 7, 1–14 Search PubMed.
- K. Deshpande, A. Mukasyan and A. Varma, Chem. Mater., 2004, 16, 4896–4904 CrossRef.
- R. Das, P. Pachfule, R. Banerjee and P. Poddar, Nanoscale, 2012, 4, 591–599 RSC.
- S. Stankic, R. Cortes-Huerto, N. Crivat, D. Demaille, J. Goniakowski and J. Jupille, Nanoscale, 2013, 5, 2448 RSC.
- Y. Feng, I. S. Cho, P. M. Rao, L. Cai and X. Zheng, Nano Lett., 2013, 13, 855–860 CrossRef PubMed.
- R. Epherre, E. Duguet, S. Mornet, E. Pollert, S. Louguet, S. Lecommandoux, C. Schatz and G. Goglio, J. Mater. Chem., 2011, 21, 4393 RSC.
- T. M. Whitney, P. C. Searson, J. S. Jiang and C. L. Chien, Science, 1993, 261, 1316–1319 CrossRef PubMed.
- J. C. Hulteen and C. R. Martin, J. Mater. Chem., 1997, 7, 1075–1087 RSC.
- C. R. Martin, Science, 1994, 266, 1961–1966 CrossRef PubMed.
- V. M. Cepak, J. C. Hulteen, G. Che, K. B. Jirage, B. B. Lakshmi, E. R. Fisher, C. R. Martin and H. Yoneyama, Chem. Mater., 1997, 9, 1065–1067 CrossRef.
- Y. Shi, B. Guo, S. A. Corr, Q. Shi, Y.-S. Hu, K. R. Heier, L. Chen, R. Seshadri and G. D. Stucky, Nano Lett., 2009, 9, 4215–4220 CrossRef PubMed.
- J. Zhu, X. Ouyang, M.-Y. Lee, R. C. Davis, S. L. Scott, A. Fischer and A. Thomas, RSC Adv., 2012, 2, 121–124 RSC.
- X. Sun, Y. Shi, P. Zhang, C. Zheng, X. Zheng, F. Zhang, Y. Zhang, N. Guan, D. Zhao and G. D. Stucky, J. Am. Chem. Soc., 2011, 133, 14542–14545 CrossRef.
- S. Zaman, M. Kashif, M. Shah, A. Hameed, N. Majeed, M. Ismail, I. Khan, S. Ullah and N. Khan, Braz. J. Sci., 2023, 3, 102–114 CrossRef.
- S. Muhammad, A. Ali, J. Shah, M. Hamza, M. Kashif, B. K. Ajat Khel and A. Iqbal, Nat. Appl. Sci. Int. J., 2023, 4, 80–97 CrossRef.
- V. N. Sonkusare, R. G. Chaudhary, G. S. Bhusari, A. R. Rai and H. D. Juneja, Nano-Struct. Nano-Objects, 2018, 13, 121–131 CrossRef.
- J. S. Beck, J. C. Vartuli, W. J. Roth, M. E. Leonowicz, C. T. Kresge, K. D. Schmitt, C. T. W. Chu, D. H. Olson, E. W. Sheppard, S. B. McCullen, J. B. Higgins and J. L. Schlenker, J. Am. Chem. Soc., 1992, 114, 10834–10843 CrossRef.
- C. J. Brumlik, V. P. Menon and C. R. Martin, J. Mater. Res., 1994, 9, 1174–1183 CrossRef.
- M. Prakash, H. P. Kavitha, S. Abinaya, J. P. Vennila and D. Lohita, Sustainable Chem. Pharm., 2022, 25, 100547 CrossRef.
- M. Bandeira, M. Giovanela, M. Roesch-Ely, D. M. Devine and J. da Silva Crespo, Sustainable Chem. Pharm., 2020, 15, 100223 CrossRef.
- A. Altemimi, N. Lakhssassi, A. Baharlouei, D. Watson and D. Lightfoot, Plants, 2017, 6, 42 CrossRef PubMed.
- P. Maisuthisakul, S. Pasuk and P. Ritthiruangdej, J. Food Compos. Anal., 2008, 21, 229–240 CrossRef.
- D.-P. Xu, Y. Li, X. Meng, T. Zhou, Y. Zhou, J. Zheng, J.-J. Zhang and H.-B. Li, Int. J. Mol. Sci., 2017, 18, 96 CrossRef PubMed.
- S. J. S. Flora, Oxid. Med. Cell. Longev., 2009, 2, 191–206 CrossRef PubMed.
- S. Ahmed, Annu, S. A. Chaudhry and S. Ikram, J. Photochem. Photobiol., B, 2017, 166, 272–284 CrossRef PubMed.
- P. E. Das, A. F. Majdalawieh, I. A. Abu-Yousef, S. Narasimhan and P. Poltronieri, Materials, 2020, 13, 876 CrossRef PubMed.
- M. Shakibaie, P. Amiri-Moghadam, M. Ghazanfari, M. Adeli-Sardou, M. Jafari and H. Forootanfar, Mater. Res. Bull., 2018, 104, 155–163 CrossRef.
- P. Nazari, M. A. Faramarzi, Z. Sepehrizadeh, M. R. Mofid, R. D. Bazaz and A. R. Shahverdi, IET Nanobiotechnol., 2012, 6, 58–62 CrossRef PubMed.
- H. Xu, G. Chen, R. Jin, D. Chen, Y. Wang and J. Pei, RSC Adv., 2014, 4, 8922 RSC.
- N. Motakef-Kazemi and M. Yaqoubi, IJ Pharmaceut. Res., 2019, 19, 70–79 Search PubMed.
- M. Yadav, S. Garg, A. Chandra and K. Hernadi, J. Colloid Interface Sci., 2019, 555, 304–314 CrossRef.
- G. Jayapriya, T. Maheswari and M. Vennila, Int. J. Eng. Res. Dev., 2019, 7, 1–9 Search PubMed.
- B. Xue, T. Sun, F. Mao and J. Xie, Mater. Lett., 2014, 122, 106–109 CrossRef.
- H. E. A. Mohamed, B. T. Sone, S. Khamlich, E. Coetsee-Hugo, H. C. Swart, T. Thema, R. Sbiaa and M. S. Dhlamini, Mater. Today Proc., 2021, 36, 328–335 CrossRef CAS.
- M. Rani, Keshu and U. Shanker, J. Environ. Manage., 2021, 300, 113777 CrossRef CAS PubMed.
- S. Verma, M. Mili, C. Sharma, H. Bajpai, K. Pal, D. Qureshi, S. A. R. Hashmi and A. K. Srivastava, Green Chem. Lett. Rev., 2021, 14, 272–285 CrossRef.
- A. O. Flayyih, W. K. Mahdi, Y. I. M. Abu Zaid and F. H. Musa, Chem. Methodol., 2022, 6, 620–628 Search PubMed.
- M. Khorami, A. Jalali and J. Sargolzaei, J. Epigenet., 2022, 3, 29–38 Search PubMed.
- Y. Zhou, H. Zhang, Z. Cheng and H. Wang, Arab. J. Chem., 2022, 15, 103607 CrossRef.
- M. A. Sawaira, M. Ahmad, M. Munir, M. Zafar, S. Sultana, S. Dawood, A. I. Almohana, M. H. Al-Marzouki Hassan, A. F. Alharbi and Z. Ahmad, Chemosphere, 2023, 310, 136838 CrossRef PubMed.
- M. Mahiuddin and B. Ochiai, ACS Omega, 2022, 7, 35626–35634 CrossRef PubMed.
- K. Palanisamy, V. Gurunathan and J. Sivapriya, Orient. J. Chem., 2023, 39(3) DOI:10.13005/ojc/390310.
- N. S. Abdul Satar, R. Adnan, H. L. Lee, S. R. Hall, T. Kobayashi, M. H. Mohamad Kassim and N. H. Mohd Kaus, Ceram. Int., 2019, 45, 15964–15973 CrossRef.
- C. Mallikarjunaswamy, S. Pramila, G. S. Shivaganga, H. N. Deepakumari, R. Prakruthi, G. Nagaraju, P. Parameswara and V. Lakshmi Ranganatha, Mater. Sci. Eng. B, 2023, 290, 116323 CrossRef.
- Y. N. Slavin, J. Asnis, U. O. Häfeli and H. Bach, J. Nanobiotechnol., 2017, 15, 65 CrossRef PubMed.
- A. Gupta, S. Mumtaz, C.-H. Li, I. Hussain and V. M. Rotello, Chem. Soc. Rev., 2019, 48, 415–427 RSC.
- R. Y. Pelgrift and A. J. Friedman, Adv. Drug Deliv. Rev., 2013, 65, 1803–1815 CrossRef PubMed.
- F. Akbarzadeh, K. Khoshgard, L. Hosseinzadeh, E. Arkan and D. Rezazadeh, Adv. Pharm. Bull., 2018, 8, 627–635 CrossRef PubMed.
- M. J. Oviedo, O. E. Contreras, Y. Rosenstein, R. Vazquez-Duhalt, Z. S. Macedo, G. G. Carbajal-Arizaga and G. A. Hirata, J. Nanomater., 2016, 2016, 1–10 CrossRef.
- S. Joshi, H. P. S. Chauhan and N. Carpenter, J. Mol. Struct., 2017, 1128, 221–229 CrossRef.
- A. O. Ariza-Roldán, E. M. López-Cardoso, M. E. Rosas-Valdez, P. P. Roman-Bravo, D. G. Vargas-Pineda, R. Cea-Olivares, M. Acevedo-Quiroz, R. S. Razo-Hernández, P. Alvarez-Fitz and V. Jancik, Polyhedron, 2017, 134, 221–229 CrossRef.
- L. Firouzi Dalvand, F. Hosseini, S. Moradi Dehaghi and E. Siasi Torbati, Iran. J. Biotechnol., 2018, 16, 279–286 CrossRef PubMed.
- B. E. Castro-Valenzuela, M. A. Franco-Molina, D. G. Zárate-Triviño, L. Villarreal-Treviño, J. R. Kawas, P. L. García-Coronado, G. Sobrevilla-Hernández and C. Rodríguez-Padilla, Front. Microbiol., 2024, 15, 1376669 CrossRef PubMed.
- L. Torrisi, N. Restuccia, L. Silipigni, S. Cuzzocrea and M. Cordaro, Atti della Accad. Peloritana dei Pericolanti, 2019, 97, 1–7 Search PubMed.
- N. Vilas Bôas, J. B. Souza Junior, L. C. Varanda, S. A. S. Machado and M. L. Calegaro, Appl. Catal., B, 2019, 258, 118014 CrossRef.
- R. Piras, M. Aresti, M. Saba, D. Marongiu, G. Mula, F. Quochi, A. Mura, C. Cannas, M. Mureddu, A. Ardu, G. Ennas, V. Calzia, A. Mattoni, A. Musinu and G. Bongiovanni, J. Phys. Conf., 2014, 566, 012017 CrossRef.
- W. E. Mahmoud and A. A. Al-Ghamdi, Polym. Adv. Technol., 2011, 22, 877–881 CrossRef.
- K. Guo, R. Zhang, Z. Fu, L. Zhang, X. Wang and C. Deng, ACS Appl. Mater. Interfaces, 2021, 13, 35657–35663 CrossRef.
- M. M. Rhaman, M. A. Matin, M. A. Hakim and M. F. Islam, Mater. Sci. Eng. B, 2021, 263, 114842 CrossRef.
- S. Liu, Y. Wang and Z. Ma, Int. J. Electrochem. Sci., 2018, 13, 12256–12265 CrossRef.
- A. Moyseowicz, J. Solid State Electrochem., 2019, 23, 1191–1199 CrossRef.
- J. Johnson William, I. Manohara Babu and G. Muralidharan, Chem. Eng. J., 2021, 422, 130058 CrossRef.
- K. S. Martirosyan, L. Wang, A. Vicent and D. Luss, Nanotechnology, 2009, 20, 405609 CrossRef.
- A. P. Periasamy, S. Yang and S.-M. Chen, Talanta, 2011, 87, 15–23 CrossRef.
- X. Gou, R. Li, G. Wang, Z. Chen and D. Wexler, Nanotechnology, 2009, 20, 495501 CrossRef.
- E. H. Bindewald, A. F. Schibelbain, M. A. P. Papi, E. G. C. Neiva, A. J. G. Zarbin, M. F. Bergamini and L. H. Marcolino-Júnior, Mater. Sci. Eng., C, 2017, 79, 262–269 CrossRef.
- Z. Lu, W. Dai, X. Lin, B. Liu, J. Zhang, J. Ye and J. Ye, Electrochim. Acta, 2018, 266, 94–102 CrossRef.
- S. D. Waghmare, S. D. Raut, B. G. Ghule, V. V. Jadhav, S. F. Shaikh, A. M. Al-Enizi, M. Ubaidullah, A. Nafady, B. M. Thamer and R. S. Mane, J. King Saud Univ. Sci., 2020, 32, 3125–3130 CrossRef.
- L. Oularbi, M. Turmine, F. E. Salih and M. El Rhazi, J. Environ. Chem. Eng., 2020, 8, 103774 CrossRef.
- Z. Zafar, S. Yi, J. Li, C. Li, Y. Zhu, A. Zada, W. Yao, Z. Liu and X. Yue, Energy Environ. Mater., 2022, 5, 68–114 CrossRef.
- R. Ullah, F. Khitab, H. Gul, R. Khattak, J. Ihsan, M. Khan, A. Khan, Z. Vincevica-Gaile and H. A. Aouissi, Catalysts, 2023, 13, 1061 CrossRef.
- K. Qi, X. Xing, A. Zada, M. Li, Q. Wang, S. Liu, H. Lin and G. Wang, Ceram. Int., 2020, 46, 1494–1502 CrossRef.
- Z. Zhang, A. Zada, N. Cui, N. Liu, M. Liu, Y. Yang, D. Jiang, J. Jiang and S. Liu, Crystals, 2021, 11, 981 CrossRef.
- Z. Xu, I. Tabata, K. Hirogaki, K. Hisada, T. Wang, S. Wang and T. Hori, Catal. Sci. Technol., 2011, 1, 397 RSC.
- W. Raza, M. M. Haque, M. Muneer, T. Harada and M. Matsumura, J. Alloys Compd., 2015, 648, 641–650 CrossRef.
- D. Sánchez-Rodríguez, M. G. Méndez Medrano, H. Remita and V. Escobar-Barrios, J. Environ. Chem. Eng., 2018, 6, 1601–1612 CrossRef.
- M. B. Hussain, M. S. Khan, H. M. Loussala and M. S. Bashir, RSC Adv., 2020, 10, 4763–4771 RSC.
- D. P. Jaihindh, B. Thirumalraj, S.-M. Chen, P. Balasubramanian and Y.-P. Fu, J. Hazard. Mater., 2019, 367, 647–657 CrossRef CAS PubMed.
- H. Huang, X. Han, X. Li, S. Wang, P. K. Chu and Y. Zhang, ACS Appl. Mater. Interfaces, 2015, 7, 482–492 CrossRef CAS.
- A. Phuruangrat, P. Dumrongrojthanath, N. Ekthammathat, S. Thongtem and T. Thongtem, J. Nanomater. DOI:10.1155/2014/138561.
- T. Senasu, T. Narenuch, K. Wannakam, T. Chankhanittha and S. Nanan, J. Mater. Sci.: Mater. Electron., 2020, 31, 9685–9694 CrossRef CAS.
- H. Oudghiri-Hassani, S. Rakass, F. T. Al Wadaani, K. J. Al-ghamdi, A. Omer, M. Messali and M. Abboudi, J. Taibah Univ. Sci., 2015, 9, 508–512 CrossRef.
- L. Zhang, D. Chen and X. Jiao, J. Phys. Chem. B, 2006, 110, 2668–2673 CrossRef CAS PubMed.
- J. Fan, X. Hu, Z. Xie, K. Zhang and J. Wang, Chem. Eng. J., 2012, 179, 44–51 CrossRef CAS.
- L. Zhang, X.-F. Cao, X.-T. Chen and Z.-L. Xue, J. Colloid Interface Sci., 2011, 354, 630–636 CrossRef CAS.
- J. Luan, H. Cai, S. Zheng, X. Hao, G. Luan, X. Wu and Z. Zou, Mater. Chem. Phys., 2007, 104, 119–124 CrossRef CAS.
- M. Suresh and A. Sivasamy, J. Environ. Chem. Eng., 2018, 6, 3745–3756 CrossRef CAS.
- S. Kossar, I. B. S. Banu, N. Aman and R. Amiruddin, J. Dispersion Sci. Technol., 2021, 42, 2053–2062 CrossRef CAS.
- T. Soltani and M. H. Entezari, Ultrason. Sonochem., 2013, 20, 1245–1253 CrossRef CAS PubMed.
- T. S. Natarajan, K. Natarajan, H. C. Bajaj and R. J. Tayade, J. Nanopart. Res., 2013, 15, 1669 CrossRef.
- S. Fatima, S. I. Ali, M. Z. Iqbal and S. Rizwan, Catalysts, 2020, 10, 367 CrossRef CAS.
- C. Ponraj, G. Vinitha and J. Daniel, Mater. Res. Express, 2019, 6, 084006 CrossRef CAS.
- S. Kalikeri and V. Shetty Kodialbail, Environ. Sci. Pollut. Res., 2021, 28, 12144–12152 CrossRef CAS PubMed.
- T. Soltani and M. H. Entezari, J. Mol. Catal. A:Chem., 2013, 377, 197–203 CrossRef CAS.
- A. Indriyani, Y. Yulizar, R. Tri Yunarti, D. Oky Bagus Apriandanu and R. Marcony Surya, Appl. Surf. Sci., 2021, 563, 150113 CrossRef CAS.
- P. L. Meena, A. K. Surela, K. Poswal, J. K. Saini and L. K. Chhachhia, Biomass Convers. Biorefin., 2024, 14, 3793–3809 CrossRef CAS.
- A. M. Alansi, M. Al-Qunaibit, I. O. Alade, T. F. Qahtan and T. A. Saleh, J. Mol. Liq., 2018, 253, 297–304 CrossRef CAS.
- L. An, G. Wang, Y. Cheng, L. Zhao, F. Gao and Y. Tian, Res. Chem. Intermed., 2015, 41, 7449–7461 CrossRef CAS.
- J. S. Souza, F. T. H. Hirata and P. Corio, J. Nanopart. Res., 2019, 21, 35 CrossRef.
- M. T. L. Lai, C. W. Lai, K. M. Lee, S. W. Chook, T. C. K. Yang, S. H. Chong and J. C. Juan, J. Alloys Compd., 2019, 801, 502–510 CrossRef CAS.
- Y. Gao, L. Wang, Z. Li, C. Li, X. Cao, A. Zhou and Q. Hu, Mater. Lett., 2014, 136, 295–297 CrossRef CAS.
- M. Naffeti, M. A. Zaïbi, C. Nefzi, A. V. García-Arias, R. Chtourou and P. A. Postigo, Environ. Technol. Innovation, 2023, 30, 103133 CrossRef CAS.
- F. Shahrab and A. Tadjarodi, J. Mol. Struct., 2024, 1295, 136806 CrossRef CAS.
- A. G. Golubovskaya, D. A. Goncharova, E. D. Fakhrutdinova, T. S. Kharlamova, O. V. Vodyankina and V. A. Svetlichnyi, Mater. Chem. Phys., 2024, 314, 128800 CrossRef CAS.
- R. Li, C. Wang, Y. Wang, J. Chen, Y. Yang, C. Li, Y. Xie, P. Zhao and J. Fei, Anal. Chim. Acta, 2023, 1239, 340681 CrossRef CAS PubMed.
- Y. Wang, Q. Fu, J. Chen, Y. Lin, Y. Yang, C. Wang, Y. Xie, P. Zhao and J. Fei, Colloids Surf., A, 2023, 657, 130543 CrossRef CAS.
|
This journal is © The Royal Society of Chemistry 2024 |
Click here to see how this site uses Cookies. View our privacy policy here.