DOI:
10.1039/D4RA05934D
(Paper)
RSC Adv., 2024,
14, 35498-35504
Superior low temperature activity over α-MnO2/β-MnOOH catalyst for selective catalytic reduction of NOx with ammonia†
Received
16th August 2024
, Accepted 24th October 2024
First published on 6th November 2024
Abstract
Manganese octahedral molecular sieves with an α-MnO2 crystal structure (OMS-2) and their related materials have attracted significant attention for the selective catalytic reduction of NOx using NH3 (NH3-SCR) at low temperatures. Further lowering their operating temperature should be an effective method to develop an environmentally friendly de-NOx system; however, their catalytic activity at low temperatures, especially below 100 °C, remains poor. This study describes a post-synthetic approach to develop Mn-based catalysts superior to those in the literature that operate at ultralow temperatures. Post-synthetic planetary ball milling for OMS-2 caused the partial conversion of OMS-2 into β-MnOOH. The obtained nanocomposite catalysts possessed abundant surface oxygen vacancies and strong surface acidity, allowing the milled catalyst to exhibit higher NO conversion at 90 °C (91%) than that in freshly prepared OMS-2 without planetary ball milling (29%). Lowering the operation temperature of OMS-2 catalysts contributed to the suppression of N2O evolution during NH3-SCR over manganese-based catalysts, resulting in high N2 selectivity over the milled OMS-2 catalyst (93%).
Introduction
Removal of harmful NOx is a critical process in industrial facilities such as thermal power stations and water-treatment plants because NOx causes acid rain, ozone depletion, and photochemical smog.1,2 Selective catalytic reduction of NOx with NH3 (NH3-SCR: 4NH3 + 4NO + O2 → 4N2 + 6H2O) is one of the main methods to reduce NOx.3,4 In a stationary system to reduce NOx, because exhaust gas also contains soot and SO2 species, SCR catalysts should be located behind the particle elimination and desulfurization configurations to avoid deactivation from ash and SO2.5 Passing through the apparatus decreases the temperature of the exhaust gas. Among various catalysts, V2O5–WO3/TiO2,6,7 V2O5–MoO3/TiO2,8 and Cu-exchanged zeolite (SSZ-13)4,9–12 have been widely accepted as suitable catalysts for practical use; however, their working temperatures are above 200 °C. Therefore, additional heat energy is required to activate vanadium-based and zeolite catalysts.
Manganese oxide is a popular catalyst attracting attention for environmental applications such as the catalytic decomposition of NOx13–16 and volatile organic compounds (VOCs),17–22 owing to its large storage capacity, low cost, excellent redox properties, and variable valence states. Recently, manganese oxide catalysts have been considered as de-NOx catalysts that work below 200 °C owing to their excellent redox properties and strong acidity. The different crystal structures of manganese oxides are α-, β-, γ-, θ-, and δ-, and previous studies have reported that α-MnO2, denoted as OMS-2, exhibited especially higher catalytic activity for NH3-SCR at low temperatures than that in MnO2 with other crystal structures.23,24 However, large amounts of N2O, a greenhouse gas, are generally produced during the NH3-SCR reaction,16,25,26 which is the main barrier to the commercial utilization of manganese oxide catalysts. According to the literature, the formation rates of undesirable N2O increase as temperatures increase.16,25 Therefore, further lowering the operating temperatures of manganese oxide catalysts should be an effective strategy in the development of an environmentally friendly de-NOx system. Although several techniques for enhancing the catalytic activity of OMS-2 at low temperatures have been investigated,25,27–31 their catalytic activities remain unsatisfactory.
Post-synthesis treatment is a major strategy for tuning the chemical and physical properties of heterogeneous catalysts. Ball milling is well known as a technique for improving the activity of heterogeneous catalysts by controlling their size and morphology,32 surface modification,33 and defect-engineering.34 Defect-rich surface structures have been proposed as preferable for enhancing the activity of Mn-based catalysts in NH3-SCR.31 Therefore, focusing on the possibility of introducing defect structures, post-synthesis ball milling has substantial potential for the enhancement of catalytic activity over OMS-2 catalysts at low temperatures.
This study demonstrates that the use of planetary ball milling as a post-synthetic treatment for OMS-2 allows to yield a de-NOx catalyst operating at low temperatures that is superior to those in the literature. Starting from KMnO4 and MnSO4·H2O, OMS-2 was prepared via a redox reaction in an acidic condition and followed by planetary ball milling at 400 rpm for different durations for OMS-2. This protocol allowed to yield nanocomposites of α-MnO2/β-MnOOH with more abundant oxygen vacancies and stronger acid strengths than before milling. Such features contributed to the higher NO conversion over a nanocomposite catalyst at less than 150 °C than that over freshly prepared OMS-2 without planetary ball milling, which also contributed to the suppression of undesirable N2O formation during low-temperature NH3-SCR.
Experimental section
Catalyst preparation
Synthesis of OMS-2. OMS-2 was prepared as described previously.35 5.89 g KMnO4 (FUJIFILM Wako Pure Chemical Corporation) was dissolved in 100 mL ultrapure water. The aqueous solution of KMnO4 was added to an aqueous solution (30 mL) containing 8.8 g MnSO4·H2O (Sigma-Aldrich) and 3 mL concentrated HNO3 (FUJIFILM Wako Pure Chemical Corporation) in a round-bottle flask. The mixture was refluxed at 100 °C for 24 h in an oil bath. The resultant dark brown solid was filtered, washed with a large amount of water, and dried under air at 120 °C overnight. Hereafter, the obtained sample was named as “as-synthesize OMS-2”.
Planetary ball milling for OMS-2. The milled samples were prepared by mechanically grinding of OMS-2 by using a planetary ball mill (Fritsch P6) equipped with silicon nitride balls and pot (Si3N4) ceramics sintered with Y2O3 and Al2O3 as additives. Milling was conducted using repeated rotation speed at 400 rpm for 5 min at 10 min intervals to avoid overheating the apparatus and reagents. The total milling time varied from 15 to 95 min (excluding the break time). The milled samples were recovered by water and dried at 80 °C overnight.
Characterization
Powder X-ray diffraction (PXRD) patterns of the samples were collected on a Rigaku Ultima IV instrument using Cu Kα radiation (λ = 0.15406 nm, 40 kV, 40 mA). Diffraction patterns were recorded in the angle range of 2θ = 5–70° with a scan speed of 0.1° min−1. Nitrogen adsorption–desorption isotherms at −196 °C were obtained using a volumetric gas adsorption apparatus (NOVAtouch, Anton Paar). Before the measurements, sample powders were pretreated at 150 °C under a vacuum condition for 4 h. The specific surface area (SBET) was estimated using the Brunauer–Emmett–Teller (BET) method. The morphologies of the samples were investigated using a field-emission scanning electron microscope (FE-SEM; JSM-IT800, JEOL) and a transmission electron microscope (TEM; JEM-F200, JEOL). The acidity and reducibility of the samples were examined using temperature-programmed desorption of NH3 (NH3-TPD) and temperature-programmed reduction of H2 (H2-TPR), respectively. NH3-TPD and H2-TPR profiles were recorded on a BELCAT II instrument (MicrotracBEL Corp.) using a thermal conductivity detector. For NH3-TPD measurements, the samples (50 mg) were pretreated at 400 °C in He (50 sccm), and adsorbed 5.19% NH3/He (50 sccm) at 50 °C for 30 min. He was passed through the reactor for another 15 min. Desorption was carried out under He flow (30 sccm) by increasing the temperature up to 500 °C at a rate of 10 °C min−1. For H2-TPR measurements, the samples (10 mg) were placed in the reactor, and the reactor was heated from room temperature to 700 °C with a heating rate of 10 °C min−1 in a reducing atmosphere of 5.03% H2/Ar (30 sccm). X-ray photoelectron spectroscopy (XPS) spectra were recorded by using X-ray photoelectron spectrometer (JPS-9030, JEOL) under Al Kα radiation. The reference of XPS binding energy position was C 1s (284.2 eV) peak for all scans.
Catalytic measurement
The NH3-SCR activity was conducted in a fixed-bed reactor operating at 60–240 °C. The concentrations of NOx (sum of NO and NO2), N2O, and NH3 in the outlet gas were determined using a chemiluminescence NOx analyzer (ECL-88A Lite, Anatec Yanaco), gas chromatograph (GC-8A, Shimadzu), and gas analyzer (LGD F200P2-H NH3, Axetris), respectively. An inlet gas containing 300 ppm NO, 300 ppm NH3, 5% O2, and balanced N2 at a flow rate of 100 cm3 min−1 was introduced to 50 mg of the catalyst. The following equation was used to calculate the NO conversion rate:
Results and discussion
Preparation of catalysts
Fig. 1 shows the PXRD patterns of as-synthesized and milled OMS-2 catalysts. The diffraction peaks of as-synthesized OMS-2 correspond to those of α-MnO2 (COD 9016667). The peak intensities decreased, and the diffraction peaks broadened in all diffraction patterns of the milled OMS-2, indicating the partial collapse/distortion of the original crystal structure. In the diffraction pattern of milled OMS-2 for 95 min, a sharp peak was also observed at 19.1° as highlighted by an arrow, which corresponds to a 00l reflection of feitknechtite, β-MnOOH.36 This suggests that a part of α-MnO2 was converted into β-MnOOH by the post-synthetic treatment.
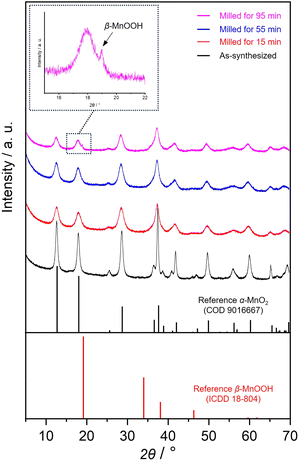 |
| Fig. 1 PXRD patterns of as-synthesized and milled OMS-2 for different periods. Black arrow at 19.1° indicates a 00l reflection of feitknechtite, β-MnOOH. | |
The specific surface areas, SEM images and TEM images of as-synthesized and milled OMS-2 catalysts are summarized in Fig. 2. As-synthesized OMS-2 exhibited a high specific surface area of 65 m2 g−1 and possessed rod-like morphology with a high aspect ratio (Fig. 2(a) and (b)), and these results are consistent with those in the literature.17,35 Planetary ball milling treatment for 15 min induced the collapse of rod-like morphology followed by the formation of coarse aggregates composed of spherical particles (Fig. 2(c) and (d)), decreasing specific surface area (SBET = 26 m2 g−1). Planetary ball milling treatments for 55 and 95 min caused growth of the thin-layered components (Fig. 2(e)–(h)). When comparing SEM images of milled samples for 55 and 95 min, long milling time induced the further growth of thin-layered components. Such thin-layered components would be presumably feitknechtite observed in X-ray diffraction (Fig. 1). The crystal structure of feitknechtite also predicted that the thin-layered components was feitknechtite (Fig. S1†). In particular, milled OMS-2 for 55 min certainly contained a tiny amount of feitknechtite which cannot be observed in XRD. Because of the formation of thin-layered components, milled OMS-2 for 55 and 95 min exhibited higher specific surface areas (SBET = 67 and 70 m2 g−1) than its counterpart milled for 15 min. It can be summarized that planetary ball milling treatment for OMS-2 allowed to form nanocomposites of OMS-2 and feitknechtite with high specific surface areas.
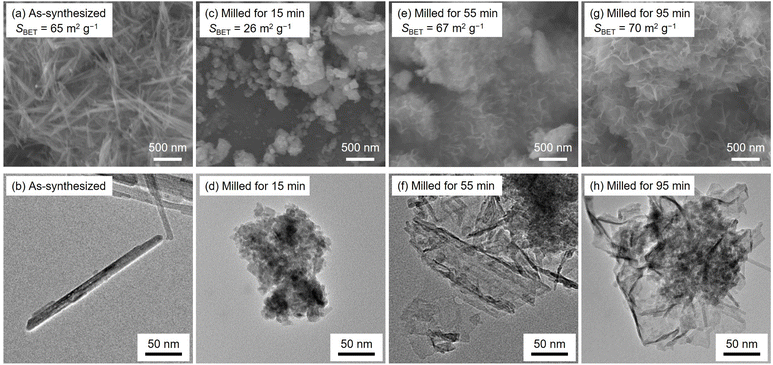 |
| Fig. 2 SEM images, TEM images and specific surface area (SBET) of (a and b) as-synthesized and (c–h) milled samples for different periods. | |
Catalytic properties of catalysts
Fig. 3 shows NO conversion during NH3-SCR over as-synthesized and milled OMS-2 catalysts. As-synthesized OMS-2 exhibited low NO conversion at 60 °C (8.7%). With the increase in reaction temperatures, NO conversion gradually increased and leached to 100% at 150 °C. 100% of NO conversion was maintained in the region of 150–210 °C. Milled OMS-2 for 15 min exhibited poor NO conversion in the wide temperature range due to the lower specific surface area (SBET = 26 m2 g−1) than that in as-synthesized OMS-2 (SBET = 65 m2 g−1). Milled OMS-2 for 55 min exhibited 91% of NO conversion at 90 °C, which is the highest value among the tested catalysts in this study. Repeating catalytic test confirmed that milled OMS-2 for 55 min stably worked in the tested temperature range (Fig. 4). Fig. 5(a) shows N2O evolution over as-synthesized and milled OMS-2 catalysts. All the tested catalysts showed low N2O evolution as a by-product in the low-temperature region below 90 °C, and the evolution amount of N2O gradually increased with an increase in reaction temperature, followed by poor N2 selectivity at high temperatures (Fig. 5(b)). Regarding suppression of N2O formation, low operating temperature is favored. Thus, milled OMS-2 for 55 min was the best catalyst among the tested catalysts because NO conversion over milled OMS-2 for 55 min reached 100% at a lower temperature range than that of the other tested catalysts and high N2 selectivity (93% at 90 °C) was also achieved due to the suppression of undesirable N2O formation by the improved low-temperature activity. The catalytic activity of NH3-SCR over OMS-2 depends on various factors such as the specific surface area, acidity, redox property, and oxygen vacancies. Except for milled OMS-2 for 15 min, the specific surface areas of the tested samples were almost the same. Therefore, the specific surface areas of the samples did not appear to affect their catalytic activity in this case.
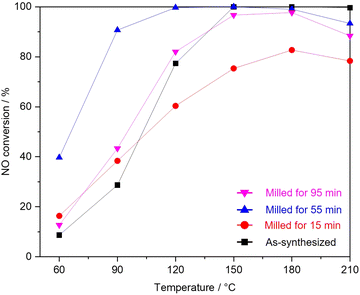 |
| Fig. 3 NO conversion over as-synthesized and milled OMS-2 catalysts. | |
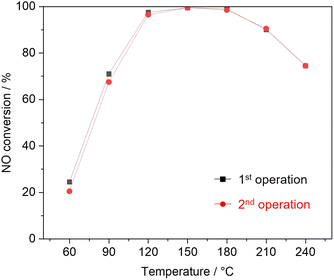 |
| Fig. 4 NO conversion over milled for 55 min in the recycling test. In the recycling test, after the 1st operation, the temperature of the catalyst was cooled down, and then raised again (2nd operation). | |
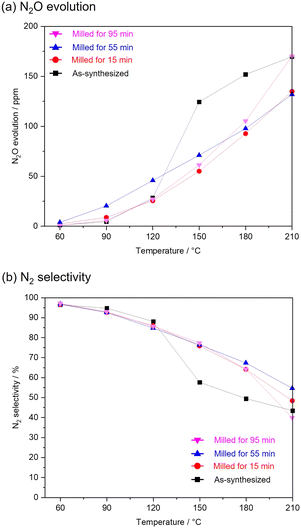 |
| Fig. 5 (a) N2O evolution and (b) N2 selectivity over as-synthesized and milled OMS-2 catalysts. | |
Fig. 6(a) shows XPS spectra of Mn 2p for as-synthesized and milled OMS-2 catalysts. The peak positions in as-synthesized OMS-2 were shifted toward low binding energy after mechanical milling. Mn species contained in metal oxides are generally in a mixed valence state. The peak position of Mn species shifted to low binding energy with the reduction of the valence state of manganese: Mn4+ (643.7 eV), Mn3+ (641.6 eV) and Mn2+ (640.0 eV) in Mn 2p3/2.37 Therefore, the peak shift suggests that the average valence of Mn species decreased after the post-synthetic mechanical treatment. In the NH3-SCR reaction, Mn4+ acts as an active center for the dehydrogenation of NH3.38 Therefore, the high proportion of Mn4+ would be favored to exhibit enhanced NH3-SCR activity in manganese-based catalysts. XPS analysis revealed that amounts of Mn4+ did not increase after the mechanical milling treatment. Thus, at least, there is no positive effect in terms of the valence state of Mn species. Because the valence state of manganese is known to be +3 in feitknechtite, the peak shift may imply the formation of feitknechtite in the vicinity of the surface of the catalysts.
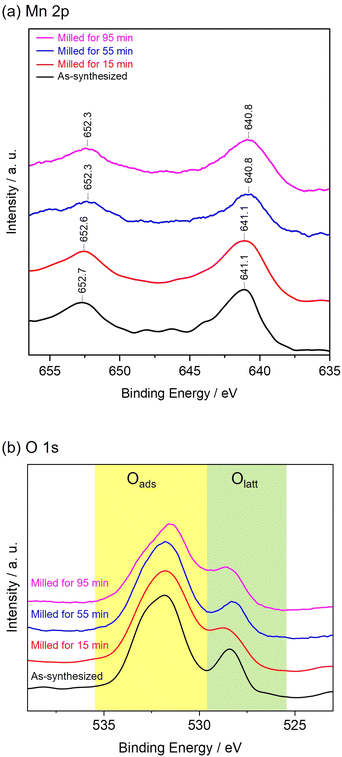 |
| Fig. 6 (a) Mn 2p and (b) O 1s XPS spectra of as-synthesized and milled OMS-2 catalysts. | |
Fig. 6(b) shows the O 1s for as-synthesized and milled OMS-2 samples. The spectra for O 1s could be divided into two characteristic peaks ascribed to the lattice oxygen species (Olatt) at 528.4 eV and adsorbed oxygen species (Oads) at 532.2 eV. Oads species are critical for NH3-SCR at low temperatures because they have higher mobility than that in the Olatt species.39 Three milled OMS-2 catalysts exhibited higher ratios of Oads/Olatt than those of as-synthesized OMS-2 (Table 1), indicating that the planetary ball milling treatment of as-synthesized OMS-2 introduced surface oxygen vacancy defects. In particular, milled OMS-2 for 55 min, showing the best catalytic activity among the tested catalysts, exhibited a highest ratio of Oads/Olatt. Even though milled OMS-2 for 15 min also exhibited a higher ratio of Oads/Olatt than as-synthesized OMS-2 and milled OMS-2 for 95 min, its NO conversion rates at low temperatures were not high due to its low specific surface area evidenced in Fig. 2(c). Wu et al. reported that Ce-doped OMS-2 exhibited enhanced catalytic activity in NH3-SCR at low temperatures owing to the increased oxygen vacancies.31 It was deduced that the increased oxygen vacancy defects introduced by planetary ball milling played a critical role to enhance the catalytic activity of the OMS-2 catalyst.
Table 1 Oads/Olatt and the amount of H2 consumption of as-synthesized and milled OMS-2 catalysts
Sample |
Oads/Olatta |
H2 consumptionb/mmol g−1 |
Calculated using the ratios of integral peak areas in XPS spectra. Determined using H2-TPR data. |
As-synthesized |
4.2 |
7.6 |
Milled for 15 min |
5.0 |
6.5 |
Milled for 55 min |
5.3 |
5.4 |
Milled for 95 min |
4.6 |
5.3 |
The acidities of the OMS-2 catalysts were analyzed using the NH3-TPD technique. Fig. 7 shows the NH3-TPD profiles of the prepared catalysts. The as-synthesized OMS-2 catalyst exhibited two distinct desorption peaks. The desorption peaks at 125 and 275 °C were associated with the weak and strong acid sites, respectively. Although the milled OMS-2 catalysts showed two distinct desorption peaks, the desorption peaks observed for the milled OMS-2 catalysts were located at higher temperatures than those observed for as-synthesized OMS-2 catalyst. This suggests that the milled OMS-2 catalysts have stronger acidic sites than that in as-synthesized OMS-2. Such surface feature would be also one of the factors that enhances the NH3-SCR catalytic activity at low temperatures because the enhancement of the acid strength would be beneficial for the adsorption and activation of NH3.
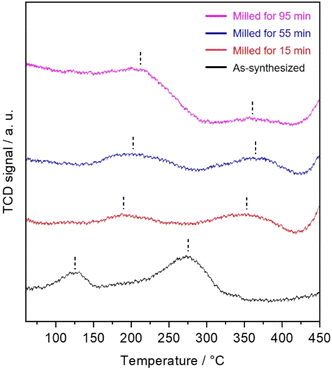 |
| Fig. 7 NH3-TPD profiles of as-synthesized and milled OMS-2 catalysts. | |
The H2-TPR technique was applied to examine the reducibility of the OMS-2 catalysts. Fig. 8 shows the H2-TPR profiles of the prepared catalysts. The as-synthesized OMS-2 catalyst showed three overlapping peaks at 270, 325, and 344 °C. The peak at 270 °C was ascribed to the reduction of MnO6-□ (where □ represents oxygen vacancies). The other overlapping peaks represent the reduction of MnO2 to Mn2O3/Mn3O4 and then to MnO. In the H2-TPR profiles of three milled OMS-2 catalysts, new peaks appeared above 350 °C. Decrease in H2 consumption was also observed in all milled samples compared to the as-synthesized OMS-2 (Table 1). Peak shift toward an increase in temperatures and a decrease in H2 consumption indicates that the milled OMS-2 catalysts have poorer reducibility than that in the as-synthesized OMS-2 catalyst. Therefore, the planetary ball milling has no positive effect on reducibility in this case. However, as the NH3-TPD analysis showed, the feitknechtite nanosheets passively acted as adsorption sites with enhanced acidity. The planetary ball milling allowed the OMS-2/feitknechtite heterointerface to form, where OMS-2 and feitknechtite are probably redox sites and NH3 adsorption sites for the NH3-SCR reaction, respectively, enhancing the low-temperature NH3-SCR activity.
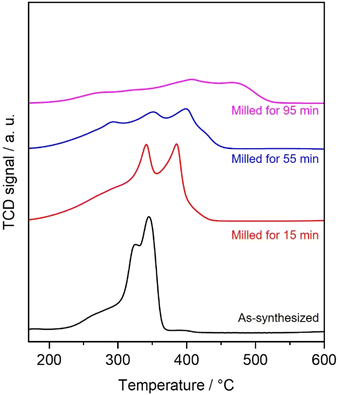 |
| Fig. 8 H2-TPR profiles of as-synthesized and milled OMS-2 catalysts. | |
As discussed above, post-synthetic treatment for OMS-2 by planetary ball milling allowed to tune structural and physicochemical properties, enhancing the conversion rate at low temperatures. In manganese-based SCR catalysts, metal doping is the latest trend toward the development of catalysts with outstanding low-temperature activity.29–31,40 However, this contribution using a facile planetary ball milling demonstrated the enhancement of catalytic activity of OMS-2 without metal doping (Table S1†). As a future perspective, further improvement of the NH3-SCR activity of OMS-2 can be expected with the aid of post-synthetic planetary ball milling and metal doping. Considering that the catalytic activity of the manganese oxide catalyst was improved by the mechanical process, which can be easily scaled up, findings from this study represent a significant advance forward the practical utilization of manganese-based catalysts.
Conclusions
Planetary ball milling was performed on OMS-2 with a nanorod morphology, resulting in a gradual decline in the crystallinity of OMS-2. SEM and HR-TEM observations of the milled OMS-2 samples revealed that feitknechtite with a layered morphology was formed from a part of OMS-2 by the post-synthetic planetary ball milling treatment. The catalytic activity of the as-synthesized and milled OMS-2 samples were compared in the NH3-SCR reaction. The milled OMS-2 catalyst prepared under the optimum conditions exhibited high NO conversion and high N2 selectivity at low temperatures. The enhanced low-temperature catalytic activity was probably due to the increased number of oxygen vacancy and enhanced acid strength.
Data availability
The data that support the findings of this study are openly available.
Conflicts of interest
There are no conflicts to declare.
Acknowledgements
This work was supported by New Energy and Industrial Technology Development Organization (NEDO) under Moonshot Project, the Japan Society for the Promotion of Science (JSPS), KAKENHI Grant-in-Aid for Transformative Research Areas (A) JP20A206/20H05880, Grant-in-Aid for Scientific Research (S) JP23H05454 and the Materials Processing Science project (“Materealize”) of MEXT, Grant Number JPMXP0219192801.
References
- K. Skalska, J. S. Miller and S. Ledakowicz, Sci. Total Environ., 2010, 408, 3976 CrossRef CAS PubMed.
- X. Cheng and X. T. Bi, Particuology, 2014, 16, 1 CrossRef CAS.
- D. Damma, P. R. Ettireddy, B. M. Reddy and P. G. Smirniotis, Catalysts, 2019, 9, 349 CrossRef CAS.
- S. Mohan, P. Dinesha and S. Kumar, Chem. Eng. J., 2020, 384, 123253 CrossRef CAS.
- L. Han, S. Cai, M. Gao, J. Y. Hasegawa, P. Wang, J. Zhang, L. Shi and D. Zhang, Chem. Rev., 2019, 119, 10916 CrossRef CAS PubMed.
- H. Li, X. Yi, J. Miao, Y. Chen, J. Chen and J. Wang, Catalysts, 2021, 11, 906 CrossRef CAS.
- Y. Inomata, H. Kubota, S. Hata, E. Kiyonaga, K. Morita, K. Yoshida, N. Sakaguchi, T. Toyao, K. I. Shimizu, S. Ishikawa, W. Ueda, M. Haruta and T. Murayama, Nat. Commun., 2021, 12, 557 CrossRef CAS PubMed.
- J. Xiang, X. Du, Y. Wan, Y. Chen, J. Ran and L. Zhang, Catal. Sci. Technol., 2019, 9, 6085 RSC.
- Y. Wang, T. Nishitoba, Y. Wang, X. Meng, F.-S. Xiao, W. Zhang, B. Marler, H. Gies, D. De Vos, U. Kolb, M. Feyen, R. McGuire, A.-N. Parvulescu, U. Müller and T. Yokoi, Ind. Eng. Chem. Res., 2020, 59, 7375–7382 CrossRef CAS.
- Y. Shan, X. Shi, J. Du, Z. Yan, Y. Yu and H. He, Ind. Eng. Chem. Res., 2019, 58, 5397–5403 CrossRef CAS.
- L. Liu, Y. Gao, S. Cheng, X. Wu, Y. Ma, X. Zhang, R. Ran, J. Liu, Z. Si, Z. Ren and D. Weng, J. Environ. Chem. Eng., 2022, 10, 108305 CrossRef CAS.
- M. Jablonska, RSC Adv., 2022, 12, 25240 RSC.
- G. Xu, X. Guo, X. Cheng, J. Yu and B. Fang, Nanoscale, 2021, 13, 7052 RSC.
- C. Liu, J.-W. Shi, C. Gao and C. Niu, Appl. Catal., A, 2016, 522, 54 CrossRef CAS.
- X. Wang, Y. Zheng, Z. Xu, X. Wang and C. Xiaoping, RSC Adv., 2013, 3, 11539 RSC.
- H. Fan, J. Fan, T. Chang, X. Wang, X. Wang, Y. Huang, Y. Zhang and Z. Shen, Catal. Sci. Technol., 2021, 11, 6553 RSC.
- T. Uematsu, Y. Miyamoto, Y. Ogasawara, K. Suzuki, K. Yamaguchi and N. Mizuno, Catal. Sci. Technol., 2016, 6, 222 RSC.
- J. Zhang, B. Dong, Y. Han, X. Zhan, S. Ge and S. He, Environ. Eng. Res., 2022, 28, 220156 CrossRef.
- Q. Huang, Z. Zhou, B. Lan, M. Sun, C. Sun and L. Yu, Colloids Surf., A, 2023, 666, 131302 CrossRef CAS.
- X. Min, M. Guo, K. Li, J. Gu, X. Guo, Y. Xue, J. Liang, S. Hu, J. Jia and T. Sun, Appl. Surf. Sci., 2021, 568, 150972 CrossRef CAS.
- S. Zhu, H. Li, L. Wang, Z. Cai, Q. Wang, S. Shen, X. Li and J. Deng, Chem. Eng. J., 2023, 458, 141415 CrossRef CAS.
- N. Huang, Z. Qu, C. Dong, Y. Qin and X. Duan, Appl. Catal., A, 2018, 560, 195 CrossRef CAS.
- B. Zhang, D. Chen, H. Liu, X. Zou and T. Chen, Aerosol Air Qual. Res., 2020, 20, 1155 CrossRef CAS.
- Y. Peng, H. Chang, Y. Dai and J. Li, Procedia Environ. Sci., 2013, 18, 384 CrossRef CAS.
- F. Zhao, G. Zhang, X. Huang, Z. Tang and F. Zha, Ind. Eng. Chem. Res., 2023, 62, 9077 CrossRef CAS.
- J. Guo, F. Gan, Y. Zhao, J. He, B. Wang, T. Gao, X. Jiang and S. Ma, RSC Adv., 2023, 13, 4032 RSC.
- L. Li, Y. Wang, L. Zhang, Y. Yu and H. He, Catalysts, 2020, 10, 396 CrossRef CAS.
- Y. Pan, B. Shen, L. Liu, Y. Yao, H. Gao, C. Liang and H. Xu, Fuel, 2020, 282, 118834 CrossRef CAS.
- X. Wu, X. Yu, Z. Chen, Z. Huang and G. Jing, Catal. Sci. Technol., 2019, 9, 4108 RSC.
- S. Ming, P. Wang, P. Liu, J. Duan, F. Mei, L. Pang, Z. Chen and T. Li, Chem. Eng. J., 2020, 379, 122287 CrossRef CAS.
- X. Wu, X. Yu, X. He and G. Jing, J. Phys. Chem. C, 2019, 123, 10981 CrossRef CAS.
- T. Kozawa, K. Fukuyama, A. Kondo and M. Naito, ACS Omega, 2019, 4, 5690 CrossRef CAS PubMed.
- A. V. Syugaev, K. A. Yazovskikh, A. A. Shakov, S. F. Lomayeva, A. N. Maratkanova and D. A. Petrov, Surf. Interfaces, 2021, 22, 100816 CrossRef CAS.
- Y. Yang, S. Zhang, S. Wang, K. Zhang, H. Wang, J. Huang, S. Deng, B. Wang, Y. Wang and G. Yu, Environ. Sci. Technol., 2015, 49, 4473 CrossRef CAS PubMed.
- K. Yamaguchi, H. Kobayashi, Y. Wang, T. Oishi, Y. Ogasawara and N. Mizuno, Catal. Sci. Technol., 2013, 3, 318 RSC.
- J. Luo, Q. Zhang and S. L. Suib, Inorg. Chem., 2000, 39, 741 CrossRef CAS PubMed.
- L. Zhang, D. Zhang, J. Zhang, S. Cai, C. Fang, L. Huang, H. Li, R. Gao and L. Shi, Nanoscale, 2013, 5, 9821 RSC.
- R. T. Guo, B. Qin, L. G. Wei, T. Y. Yin, J. Zhou and W. G. Pan, Phys. Chem. Chem. Phys., 2022, 24, 6363 RSC.
- T. Boningari, P. R. Ettireddy, A. Somogyvari, Y. Liu, A. Vorontsov, C. A. McDonald and P. G. Smirniotis, J. Catal., 2015, 325, 145 CrossRef CAS.
- L. Sun, Q. Cao, B. Hu, J. Li, J. Hao, G. Jing and X. Tang, Appl. Catal., A, 2011, 393, 323 CrossRef CAS.
|
This journal is © The Royal Society of Chemistry 2024 |
Click here to see how this site uses Cookies. View our privacy policy here.