DOI:
10.1039/D4EE03956D
(Perspective)
Energy Environ. Sci., 2025,
18, 194-213
Perspectives for sustainability analysis of scalable perovskite photovoltaics†
Received
31st August 2024
, Accepted 17th October 2024
First published on 23rd October 2024
Abstract
Halide perovskite photovoltaics (PVs) are poised to become a critical high-efficiency renewable energy technology in the fight against climate change. This perspective aims to ensure the viability of perovskite PV as a sustainable technology by focusing on key areas such as end-of-life management and sustainability analysis. It highlights the current lack of comprehensive frameworks that incorporate circular solar economy principles, ecosystem impacts, and climate commitments. To address this gap, we propose a multi-scale analytical and modeling framework specifically designed for perovskite PVs. This approach integrates dynamic material flow analysis and life cycle assessment to reshape our understanding of material usage, with an emphasis on critical material demand and recycling opportunities. It seeks to provide in-depth insights into the socio-economic and environmental impacts of material consumption, particularly as perovskite PVs become more prevalent. Additionally, future research should explore distributed manufacturing to optimize costs and reduce environmental impacts, as well as evaluate the benefits of integrating perovskite PVs with agriculture to promote sustainable sector coupling.
Broader context
The rapid development of perovskite photovoltaics (PVs) has garnered substantial research interest due to their potential to significantly contribute to the multi-terawatt PV deployment era, which began in 2022. This review highlights key advances in perovskite solar cells, particularly in scalable deposition techniques, critical materials, and end-of-life management. Recent studies focus heavily on material and manufacturing optimization to achieve high-performance, stable devices with scalable, cost-effective production processes. However, to fully realize the potential of perovskite PVs, these efforts must be framed within a broader context that considers the circular solar economy, ecosystems, and climate goals. This review addresses three core perspectives: first, predicting critical material needs, recycling possibilities, and their economic, environmental, and social impacts through a model integrating dynamic material flow analysis and life cycle assessment; second, evaluating the techno-economic viability and environmental sustainability of distributed manufacturing for perovskite solar panels, with a focus on reducing costs, carbon emissions, and supply chain vulnerabilities; and third, exploring the synergistic advantages and sustainability of perovskite PV within the energy-food-water nexus, particularly through integrating these PV systems into agricultural activities to promote sustainable sector coupling. This interdisciplinary approach is essential to advancing perovskite PV technology sustainably, balancing environmental, economic, and social considerations.
|
Introduction
With the development of increasingly reliable and cost-effective photovoltaic (PV) modules, a gateway has opened for an amplified integration of solar PV into the electricity grid. This paves the way for a dynamic clean energy transition, driving us towards the attainable goal of Net Zero Emissions by 2050.1 According to the Energy Information Administration (EIA),2 solar electricity accounted for 4% of the US total electricity generation from all energy sources in 2023 and is projected to reach 7% by 2025. The most rapidly increasing sector is utility solar which as of 2023 has reached 73.5 GW that is 6% of the US power capacity.2 The International Energy Agency (IEA) also forecasts the installed power capacity of solar PV systems is on track to overtake that of natural gas by 2026 and coal by 2027, becoming the largest in the world.3 In light of such trends, the solar industry stands on the brink of unprecedented opportunities, while also grappling with unique challenges.
PV technologies offer an environmentally friendly means of converting solar energy into electricity. Over the past few decades, these technologies have made significant strides, positioning themselves as a leading and critical source of renewable energy production. The first-generation solar cells, which continue to dominate the PV market,4 are primarily based on silicon wafers and have achieved laboratory-based power conversion efficiencies (PCEs) of ∼27% and ∼20–23% for the best modules operating in the field.5,6 The second-generation PV technologies are based on thin-film amorphous silicon (a-Si), cadmium telluride (CdTe), and copper indium gallium selenide (CIGS), with a chemical formula of CuInxGa(1−x)Se2, where the value of x can vary from 0 (pure copper gallium selenide) to 1 (pure copper indium selenide).7,8 Third-generation PV technologies incorporate solar dyes, inks, conductive polymers and nanomaterials, with enhanced scalability and increased flexibility over traditional counterparts. This latest generation of PV modules shows promise towards higher efficiency beyond single junction limits by virtue of not only new materials but also device architectures, such as tandems, thus enabling further cost reductions.
Since their initial demonstration in 2009, perovskite solar cells have rapidly ascended as a promising contender in the realm of third-generation PV technologies, thanks to their high PCEs and potentially low production costs for both single-junction and tandem devices. The PCE of perovskite solar cells has risen dramatically from 3.8% in 2009 to a certified record of 26.7% in 2024.9 Perovskite-based tandem solar cells, meticulously engineered to capture a wider range of the solar spectrum, exhibit superior efficiency compared to their single-junction counterparts and outperform certified record single-junction silicon cells, with minimal supplementary energy and material consumption. Recently, all-perovskite tandem cells have achieved a certified record PCE of 29.1%,6 while devices incorporating established silicon technology as the bottom cell have reached an impressive 33.7% PCE.9,10 Composed of abundant elements,11 perovskite materials exhibit low formation energy during deposition,12 positioning them as an ideal candidate for high-volume manufacturing processes.13 Perovskite solar cells embrace the potential to be compatible with high-throughput production methods, such as roll-to-roll manufacturing,14 ultimately facilitating widespread adoption and deployment of this PV technology.
The favorable attributes of perovskite are the main reason behind its prominent standing, primarily due to certain key material properties. These include, but are not limited to, free charge generation at room temperature, high absorption coefficients,15,16 excellent charge transport,5 readily tunable bandgaps,17 and long carrier diffusion lengths.5 While perovskite PV is also indeed an appealing contender for harvesting and recycling indoor light into usable electrical power,18 the discussion in this paper is related to outdoor PV; thus, unless specifically stated, perovskite PV mentioned in this paper refers to outdoor PV.
In spite of the multi-fold benefits and incredible potential of perovskite solar cells, a series of current challenges create obstacles to the large-scale integration of perovskite-based PV technology. The foremost challenge is achieving long-term stability alongside maximum efficiency, due to operational stability challenges caused by instabilities in absorbers and interfaces, including ion migration during operation. Addressing these issues is critical to enhancing the competitiveness of both single and tandem cells for long-term deployment, ensuring they maintain efficiency and stability over time. Second, the majority of perovskite solar cells, initially devised at a laboratory scale, encounter significant hurdles in adhering to the same fabrication protocol during the scale-up process.11 It is imperative to develop and employ scalable deposition strategies for high-throughput and uniform coating of all functional layers. Third, like established silicon-based and thin-film PV technologies, commercial products inevitably generate considerable waste, and adequate end-of-life management is necessary to avoid significant environmental impacts.19,20 Addressing these challenges in perovskite PV research and pinpointing promising future research trajectories necessitate a comprehensive and systematic review of pertinent studies. This approach will shed light on the existing panorama of perovskite solar cell advancement and the knowledge gaps therein, while offering insights to inform future research and development perspectives.
In our main analysis of existing literature, we prioritize the sustainability aspects of perovskite solar cells, with a particular emphasis on end-of-life management and life cycle assessment. These two research directions are relatively nascent with limited investigations on these topics thus far. To support our primary analysis towards future perspectives in perovskite PV research, the following five sections delve into the evolution of perovskite solar cells over the past decade, which highlight significant advancements in materials, scalable manufacturing processes, and additive engineering, all of which have markedly improved the devices’ stability and PCE. By examining hazardous materials like lead and critical materials like indium, we highlight the challenges and opportunities in optimizing performance while managing toxicity and supply risks. In this context, our analysis of existing literature elucidates a gap in the current body of perovskite PV research, in integrating aspects of circular solar economy, ecosystems, and climate commitments. To address this knowledge gap, we propose a multi-scale systems analytical and modeling framework, tailored specifically for perovskite PVs. Three perspectives assessing the projected critical material needs, the potentials of perovskite PVs in distributed manufacturing, and energy-food-water nexus are then discussed within this framework. The connection of the aforementioned reviewed content and proposed future perspectives in this study is shown in Fig. 1.
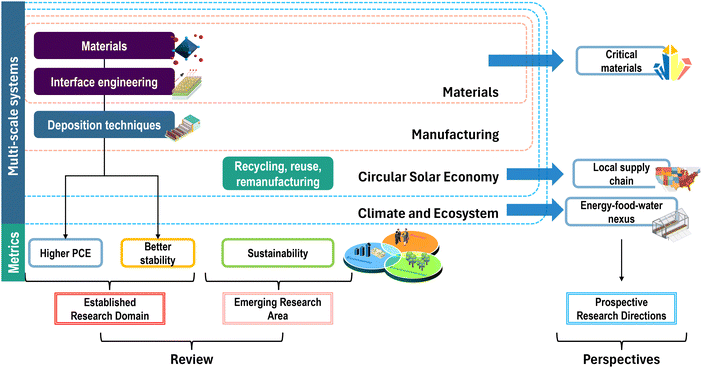 |
| Fig. 1 Connection of reviewed content and proposed future perspectives in this study. This diagram illustrates how the emerging research area of perovskite PV is situated within the broader context of established research domains (in the following five sections), paving the way for the proposed future research directions. PCE: power conversion efficiency. | |
Device architectures of perovskite solar cells
Over the years, single-junction perovskite solar cells have been developed in various layered structures, broadly classified into four types: mesoporous, planar, inverted planar, and inverted mesoporous,21 as shown in Fig. 2(a)–(d). Recently, there has been a notable shift in focus away from mesoporous types, indicating a trend towards exploring and optimizing the other structural configurations for improved performance and applicability. A typical perovskite solar cell consists of an electron transport layer (ETL), a perovskite absorber layer, and a hole transport layer (HTL), which are deposited between a transparent conductive oxide (TCO)-coated glass substrate and a metal back electrode. The order of layer deposition and structure differentiate the four types of perovskite single junctions. Cascading two or even more sub-cells with complementary absorbers to form tandem or multi-junction configurations has the promise for a higher PCE exceeding the Shockley–Queisser limit for single junctions, by minimizing the absorption loss of low-energy photons and thermalization of high-energy photons. Typical tandem architectures include four-terminal (4T)22 and two-terminal (2T) perovskite solar cells,23 as shown in Fig. 2(d) and (e), where perovskite top-cells are electrically connected with bottom cell, typically silicon,24 CIGS,22 or perovskite itself.25–27 In 4T tandem, the top- and bottom-cells are stacked mechanically and contacted individually, enabling both sub-cells to operate at their best performances. In contrast, the two sub-cells in 2T tandem are monolithically connected in series to make a single electrical device, requiring only one transparent electrode thus potentially lowering the material and energy inputs, as well as the manufacturing costs.
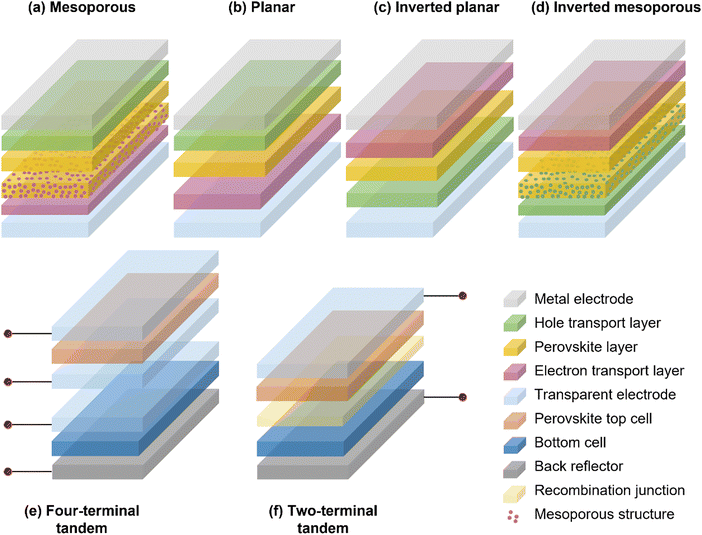 |
| Fig. 2 Schematic of widely investigated layered structures in perovskite single junctions and tandems. (a) Mesoporous. (b) Planar. (c) Inverted planar. (d) Inverted mesoporous. (e) Four-terminal tandem. (f) Two-terminal tandem. | |
Recent advances of perovskite solar cells
Power conversion efficiency and stability
In this section, we briefly review and analyze relevant research articles published since 2009, focusing on the record evolution of different perovskite solar cell designs. Particular attention is given to metrics such as PCE, total cell area, and long-term stability. T80, the time at which the performance of a perovskite solar cell attains 80% of its initial value in ambient conditions,28 is selected as the stability indicator because specific stability testing standards, such as the International Summits on Organic Photovoltaics Stability (ISOS) protocols, have not yet been uniformly adopted for perovskite solar cells.29,30 The first organic–inorganic lead halide perovskite solar cell was unveiled in 2009, featuring a liquid electrode, a modest PCE of only 3.8% and a lifetime of just a few minutes.31 To develop competitive alternatives to conventional PVs, three primary research goals have been identified: achieving higher PCE, enlarging the active area of perovskite solar cells, and enhancing stability against oxygen, moisture, and chemical degradation to extend the device lifetime. Fig. 3(a) and (b) tracks the historical evolution of PCEs and total cell area of the annual champion perovskite solar cells since 2009. The certified record PCE of single junction perovskite solar cells has attained 26.7%,9 close to that of the certified silicon PV (27.6%). A highly promising approach for surpassing the approximately 33% radiative efficiency limit of single-junction cells involves the use of multijunction configurations. These systems utilize multiple absorber layers, each designed to capture different, complementary regions of the solar spectrum, thereby enhancing overall efficiency. Perovskite–perovskite tandems recently achieved a certified record PCE of 29.1%,6 and devices using established silicon technology as the bottom cell has reached 33.7% PCE.9,10 All-perovskite triple-junction solar cells have achieved an efficiency of 24.3%
(23.3% certified quasi-steady-state efficiency).32 Though multi-decade lifetimes are yet to be proven for the emerging perovskite solar cells, increasing perovskite solar cells have a T80 lifetime of multi-thousand hours under full maximum power point operations, as shown in Fig. 3(a).
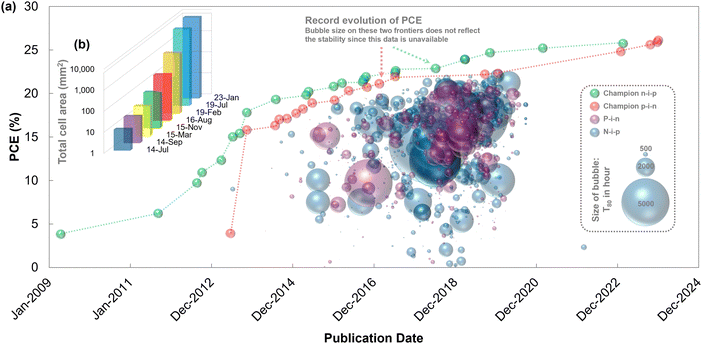 |
| Fig. 3 Chronological evolution of perovskite solar cells. (a) power conversion efficiency (PCE) and T80 lifetime of perovskite solar cells in bubble chart.33 (b) total cell area of annual champion perovskite solar cells.33T80 refers to the time at which the performance of a perovskite solar cell attains 80% of its initial value in ambient conditions. | |
Current commercialization activities and significant achievements
Perovskite PV technology has made remarkable strides toward commercialization, driven by advancements in efficiency, scalability, and innovative production techniques. Companies like Oxford PV and Swift Solar have established pilot production facilities to refine manufacturing techniques and increase output.34,35 Other companies like Microquanta Semiconductor and Wuxi Utmost Light Technology (UtmoLight) are at the forefront of these efforts, producing certified high-efficiency, large-area perovskite modules, such as the 21.8% perovskite minimodule (19.35 cm2), 19.5% submodule (810.1 cm2), and 18.2% standard module (0.72 m2).36 A global map of prominent perovskite PV companies showcases the widespread interests and investment in this technology (Fig. 6). Key innovations, including slot-die coating, enable the fabrication of high-quality, large-area films,11 while the solution-processable nature of perovskites facilitates integration with existing high-volume manufacturing technologies, further reducing costs and enhancing scalability. These advancements position perovskite PVs for large-scale energy production, with a low levelized cost of electricity comparable to market-leading PV technologies,37 making them a strong candidate for future terawatt-scale renewable energy generation.
However, the foremost challenge toward commercialization remains achieving long-term stability alongside maximum efficiency in large-area modules. Significant progress has been made in improving stability through advanced encapsulation techniques,31 which enhance the durability of perovskite PVs, ensuring their suitability for commercial deployment. Further efforts to develop a circular solar economy for perovskite PVs, through recycling and remanufacturing components like glass and aluminum, enhance their sustainability.38–40 This recycling strategy could accelerate the market entry of perovskite tandem solar cells, despite their relatively shorter lifespan.38 With ongoing efforts to improve both stability and scalability, perovskite PV technology is well-positioned for large-scale adoption in the future.
A wide variety of materials for perovskite solar cells
One of the paramount benefits of perovskite-based technology lies in its versatility. An extensive range of materials can be utilized in the fabrication of perovskite solar cells without compromising its efficiency.
Transparent conductive oxide
Analogous to the thin-film PVs, TCOs, including indium tin oxide (ITO) and fluorine tin oxide (FTO) are widely adopted in perovskite solar cells as the front electrodes. Though ITO have been mainly used due to its low electrical resistivity and high transparency, this material is not compatible with commercial perovskite solar cell manufacturing since it contains indium, which has limited resource reserve and has been classified as critical metal by the Department of Energy (DOE).28 To this end, more cost-effective aluminum-doped zinc oxide (AZO) and FTO are investigated more to substitute the ITO film. Another indium-free substitute, Nb:TiO2−x (NTO), derived from earth-abundant materials, exhibits both low electrical resistivity and ideal transparency. However, its synthesis necessitates high-temperature processing steps,41 which inadvertently makes it even more expensive than the ITO film.
Electron transport layer and hole transport layer
Perovskite solar cells are distinguished by their unique structure, operating either in n–i–p or p–i–n configurations, which have different requirements in terms of stability, fabrication methods, etc. Titanium oxide (TiO2) was the most selected ETL in n–i–p perovskite solar cells due to its suitable band alignment in early stage.42 Over the past five years, tin oxide (SnO2) has become the material of choice to replace the TiO2, due to its better long-term stability, high open-circuit voltage, small current–voltage (J–V) hysteresis and negligible photocatalytic effect. The most efficient perovskite solar cells typically utilize an n–i–p architecture. In this configuration, the perovskite layer is applied over an n-type electron-selective collecting layer, often made of high-quality SnO2 coated on FTO-coated glass substrate. A p-type collecting layer, usually consisting of doped small molecules like Spiro-OMeTAD or conducting polymers, is then deposited on top of the perovskite layer. This assembly is completed with the addition of metal electrodes. However, implementing SnO2 at a large scale for perovskite solar cell manufacturing is still challenging due to the difficulty in depositing thin pinhole-free layer on substrate, especially rough substrates like FTO, and poor thermal stability against high-temperature processing.11 Also, the electrochemical reaction of these oxides with perovskite, particularly under Ultraviolet (UV) light, may impose a big threaten to the stability of perovskite solar cells. The high cost of commonly used HTL materials, like Spiro-OMeTAD and PTAA, is primarily driven by their complex synthesis processes.43 Spiro-OMeTAD costs between $170 and $475 per gram,44 accounting for approximately 10% of the total cost of perovskite solar modules.45,46 PTAA, however, is more than twice as expensive as Spiro-OMeTAD.47 These high costs, combined with issues of long-term instability, may hinder the practicality of these materials for large-scale production. Currently, no effective alternatives have been identified for these organic compounds in high-performance n–i–p perovskite solar cells,48 posing a significant challenge for further commercialization efforts.
In addition to the n–i–p setup, the p–i–n or “inverted” architecture is gaining traction. Although it operates similarly to n–i–p systems and achieves comparable efficiencies, it follows a reverse deposition order.5 In the p–i–n structure, the HTL is deposited first, using materials such as organic PTAA, inorganic NiOx, or emerging carbazole-based self-assembled monolayers (SAMs) like 2PACz,49 which are anchored to an ITO-coated glass substrate. This is followed by the deposition of a ETL, typically consisting of C60 or solution-processed fullerene derivatives, and finally the metal electrodes,50 further exemplifying the versatility and adaptability of perovskite solar cell designs. While NiOx is a low-cost alternative to organic HTL materials, it tends to result in lower efficiencies.51 Additionally, fullerenes are expensive both economically and environmentally,52 with no effective alternatives yet available. Therefore, finding more affordable and stable HTL and ETL materials is essential for the large-scale production of perovskite solar cells.
Perovskite layer
Hybrid organic–inorganic perovskites have been recognized as a transformative category in the field of light-harvesting materials. The most explored three-dimensional (3D) perovskites generally adhere to the ABX3 formula. Herein, A represents a monovalent cation, which could be methylammonium (MA+), formamidinium (FA+), or caesium (Cs+). B signifies a divalent metallic cation such as lead (Pb2+), tin (Sn2+). or germanium (Ge2+). X corresponds to a halide anion, which could be chlorine (Cl−), bromine (Br−), or iodine (I−).53,54 While MAPbI3 is the most frequently employed composition in early stage, it tends to decompose much faster than others due to its easy deprotonation capability.55,56 FAPbI3, when considered independently, also presents instability within a cubic structure. Therefore, to stabilize the perovskite structure, FAPbI3 is alloyed with smaller cations, including but not limited to MA+ or Cs+.11,57 Moreover, hybrid lead–tin perovskite solar cells have garnered significant attention due to their compelling advantages, including low toxicity, adjustable bandgap, and potential applicability in the development of all-perovskite tandem solar cells.58
Additionally, recent advances have been directed to 2D perovskite with enhanced stability because the bulky organic cations serve as a protective layer shielding the inorganic perovskite slabs from moisture and minimizing ion migration,59 paving a promising avenue for achieving stable tin-based perovskite solar cells. However, 2D perovskites come with their own challenges, including the large bandgap, inadequate charge transportation, high exciton binding energies,60,61 and reaction of many 2D large cations with FA+.62 These factors contribute to a compromised PCE in perovskite solar cells. To overcome these individual limitations inherent in both 3D and 2D perovskites while simultaneously capitalizing on their respective strengths, a 3D layer with a thin 2D capping passivation layer is proposed to concurrently increase their efficiency and stability.63,64 Another promising strategy involves the use of anion engineering to control the growth and orientation of quasi-2D perovskites, bypassing the need for 3D structures and thereby distinguishing it from the traditional 2D/3D structures.59,65–68 This method demonstrates promising potential of attaining an optimal balance of increased stability and PCE.
Back electrode
The back-contact layer of perovskite solar cells is typically composed of metals with high conductivity, including nickel (Ni), copper (Cu), silver (Ag), gold (Au), and aluminum (Al), mostly deposited via thermal evaporation in laboratory-scale perovskite solar cell fabrication. However, this protocol can hardly be extrapolated from laboratory scale to industrial scale. Replacement of the thermally evaporated metal electrode is a major challenge to overcome and is a key to realizing high-throughput perovskite solar cell manufacturing. It is clear that industry and academia have different preferences when it comes to the tools they use, particularly in the context of high vacuum point source tools. While academic labs often employ these tools for evaporating metals, this practice is largely dictated by the resources and equipment readily available to them. In contrast, the industry might not opt for such methods, seeking alternatives that align better with their operational scales and efficiency requirements. Sputtering has been less explored for electrode deposition in perovskite solar cells, although the process is more favorable for large-scale fabrication as it is less dependent on the vacuum level and generally has shorter processing times than evaporation, and its damage could be minimized by lowering the sputter power density.69 Sputtering can be used to deposit not only metallic films, but also alloys or more complex compounds, such as TCOs including ITO and AZO, commonly used in semi-transparent devices and tandem applications. Processes that do not require a vacuum for depositing back contacts are highly sought after to fully harness the benefits of solution processing in perovskite solar cells. Recently, printed electrodes made from carbon-based pastes and inks have emerged as a feasible vacuum-free substitute for evaporated metal electrodes, displaying high electrical conductivity and an appropriate work function for charge transfer.70–74 Carbon-based electrodes are more cost-effective and possess the necessary mechanical strength to endure repeated bending stress.75,76
Critical materials in perovskite solar cells
In this section, we conduct a review of the potential critical materials used in perovskite solar cells. This analysis forms the foundational basis for the primary analysis in the “Recycling, reuse, and re-manufacturing of perovskite solar cells” section. The US DOE's Critical Materials Institute defines critical materials as substances employed in technology with supply risks and limited substitute options. Different governmental organizations, however, categorize critical materials distinctively. For instance, the DOE classifies rare earths such as dysprosium, terbium, europium, neodymium, yttrium, lithium, and tellurium, as well as Cu, as critical materials,77,78 while the European Commission also includes natural graphite and titanium metal in a similar list.79 In the context of perovskite solar cells, indium, an essential component of TCOs, is globally recognized as a critical material, due to its scarcity and high cost – with high usage already in the display industry. FTO has been employed as a substitute for ITO, offering satisfactory performance, straightforward processing, and minimal stability reduction. Nevertheless, FTO still contains tin, which is regarded as a strategic material in the European Union (EU) owing to its limited substitution potential and the small number of producing countries. The back electrode of perovskite solar cells incorporates metals such as gold, silver, copper, aluminum, and nickel, which are costly and widely utilized in various industries. Though gold and silver can facilitate easy prototyping of perovskite solar cells in academic laboratories, they are not likely to be adopted in commercialized devices.48 Additionally, the European Commission also assesses copper and nickel as strategic raw materials in line with the Critical Raw Materials Act,80 though they do not meet the critical raw material thresholds. The ambitious energy policy objectives, coupled with the rapidly soaring demand for PV panels, present a great challenge to the PV industry. Meeting this need in the forthcoming decades will require a concerted effort in addressing the escalating critical metal supply. Lead, another crucial element in perovskite structures, is considered a critical material by both the Canadian and Dutch governments. While lead-free perovskite solar cells, such as tin-based devices, have been developed to bypass the contentious toxicity of lead-based alternatives, they exhibit lower PCE, and stability compared to their lead-based counterparts. Unexpected PV module failure scenarios, such as fire accidents may also lead to the accidental leaching of lead.81 Therefore, it is crucial to thoroughly address and evaluate the potential toxicity issues associated with lead in the development of perovskite solar cells. Iodine is one of the Earth's rarest non-metallic elements, with production concentrated in Chile and Japan, making it susceptible to price volatility due to geographic and environmental factors. For instance, the price of iodine has experienced significant fluctuations, dropping from $93 to $30 per kilogram in 2013, underscoring its economic sensitivity and scarcity.28,82
Scalable, high-performance perovskite solar cell deposition
Solution-based deposition techniques
In laboratory-scale deposition, perovskites are first dissolved in organic solvents, including N,N-dimethylformamide (DMF), dimethyl sulfoxide (DMSO), etc. to form the precursor solution, which is then deposited layer-by-layer via spin coating. Generally, spin coating has extremely low material utilization efficiency (even lower than 10%).11,83 Additionally, the wet-solution film is thinned and smoothed by centrifugal force from spinning, which is hard to replicate in scaled deposition processes.
Scalable solution-based deposition techniques for perovskite solar cells, include, but are not limited to, blade coating, slot die coating, spray coating, inkjet printing, screen printing, and electro-deposition.11 In the blade-coating deposition, the precursor solution can be uniformly bladed across substrates to form wet thin films. The film thickness is controlled by the concentration of the precursor ink, the gap between the blade and substrate, and the speed of blade motion along the substrate, with much higher material utilization efficiency of 95% than spin coating.84 In the roll-to-roll case, the blade is stationary and flexible substrate moves with the roller. In slot die coating, an ink reservoir with a thin slit is used to apply precursor onto the substrate. Slot die coating generally presents higher throughput and reproducibility compared to blade coating, with material waste of less than 5%.85,86 As for spray coating, a nozzle is used to disperse tiny liquid droplets onto substrates, with 5% of material waste.87,88 Spray coating methods can be further categorized based on the techniques employed to create droplets. These include pneumatic spraying, which utilizes rapid gas flow; ultrasonic spraying, facilitated by ultrasonic vibrations; and electro-spraying, achieved through electrical repulsion.11 In inkjet printing, nozzles are adopted to disperse the precursor ink, with fine control of the droplet size and trajectory. This approach can generate a material waste of less than 1%.89,90 In screen printing, a patterned mesh screen is used to hold and transfer ink onto the substrate. The film thickness is controlled by the mesh size and thickness of the emulsion layer, which is compatible with thicker film deposition (1–10 μm).91 The advantage of electrodeposition is the use of a non-toxic and environmentally friendly solvent,11 typically an aqueous solution. Other solution-based deposition techniques, such as brush coating,92 dip coating,92 and air-knife-assisted coating,93 have also been demonstrated for perovskite layer deposition.
Vapor-based deposition techniques
Despite the dominance of solution-processed perovskites, there is an increasing shift towards exploring solvent-free deposition methods, driven by their potential for better scalability and reproducibility.94 Thermal evaporation of perovskite precursors is a particularly promising solvent-free technique. It provides precise control over the thickness and composition of films, enabling the production of multilayer stacks on a wide range of substrates.95–97 This versatility underscores its potential to significantly advance perovskite-based technologies. However, the adoption of co-evaporated precursors in perovskite solar cells achieving PCE over 20% remains limited,98–102 largely due to a relatively shallow understanding of thermally evaporated perovskites. A major challenge with the vapor deposition method is its difficulty in introducing passivators to the grain boundaries, although surface passivation can still be achieved through vacuum-based deposition techniques. Recognizing these challenges, the need for a dual approach in analysis to pinpoint areas for improvement has been emphasized,103 which is crucial for driving further advancements in this promising technology.
Additive engineering
Over the last decade, additive engineering has emerged as a crucial factor in optimizing both the performance and long-term stability of perovskite single-junction and multi-junction PVs due to passivation of defects,104,105 in addition to advancements in device preparation methods, the optimization of halide perovskite compositions as mentioned above. Additive engineering can be categorized into two main approaches based on the processing route: (1) additive engineering during perovskite formation and (2) additive-assisted interface optimization (referred to as interface engineering hereafter).106 In the case of additive engineering during perovskite formation, additives play a crucial role in influencing perovskite crystallization, film formation, and defect passivation within the bulk material. Common additives used for this purpose include Lewis acids (metal cations and fullerene derivatives), Lewis bases, ammonium salts, low-dimensional perovskites, and ionic liquids.106
Data indicates that nearly half of the perovskite solar cells reporting a PCE over 21% benefited from interface engineering, highlighting its critical role in device optimization.107 Interface engineering addresses two main challenges: the impact of interface defects on the device's photoelectric performance, including issues related to energy band alignment and charge distribution, and the influence of the interface on device stability, particularly through its effects on ion migration and material degradation. To mitigate these issues, strategies have involved modifying interface characteristics or adding additional interlayers, with a significant focus on the ETL/perovskite and perovskite/HTL interfaces. The interface between perovskite and ETL plays a vital role in device performance due to its considerable influence on electron extraction and J–V hysteresis. Modifications at the ETL/perovskite interface primarily aim to passivate surface defects in the perovskite layer, inhibit ion migration, and optimize interfacial energy-band alignment. These modifications help reduce non-radiative recombination at the interface and maximize the open-circuit voltage (VOC). In comparison to the modifications at the ETL/perovskite interface, there seem to be fewer material limitations at the perovskite/HTL interface.107 Moreover, modifying the external interfaces between the perovskite layer and the charge-transport layers above can shield the perovskite absorber from moisture and oxygen-induced degradation, thereby enhancing device stability. Additionally, interface modification is essential in controlling the morphology of the perovskite film, which is critical for achieving optimal device performance and durability. Improving the interior interface between the perovskite layer and the underlying charge-transport layer can boost the crystallinity and film quality of the perovskite absorber. Such improvements lead to perovskite films with larger grains, fewer pinholes, and a more uniform distribution, all of which are beneficial for advancing device performance.
Recycling, reuse, and re-manufacturing of perovskite solar cells
Recycling end-of-life solar modules involves dismantling and processing worn-out solar cells to recover valuable materials for the production of new products. Reuse, in contrast, focuses on repurposing still-functional components without altering their original form. Remanufacturing, a combination of recycling and reuse processes, rejuvenates used PV cells to like-new condition by properly repairing or replacing specific layers, thereby extending their operational lifespan.108 Based on our review of critical materials in the previous section, recovering valuable components and recycling toxic metals from end-of-life devices is essential to comply with international regulations and address public concerns about potential risks associated with lead. The current challenge with recycling mature PV technologies, such as silicon-based PVs, primarily stems from the insufficient scale and separation processes necessary to render recycling economically viable. Emerging perovskite solar cells present a prime opportunity to develop recyclable modules from the very beginning. In this section, we review and analyze the recycling strategies implemented for perovskite solar cells in recent studies. Further, we provide insights and information regarding future recycling, reuse, and re-manufacturing strategies to enhance the circularity of perovskite solar cells.
The options for end-of-life management of PVs are region- or country-specific and should be adapted appropriately before implementation. Since 2012, PV-specific waste regulations have come into place in the EU. EU regulations mandate 85% collection and 80% recycling of the materials used in PV panels through the Waste Electrical and Electronic Equipment (WEEE) Directive.109–111 Similar regulations are proposed in China,112,113 one of the largest PV markets worldwide. In the US, the end-of-life disposal of solar products is regulated by the Federal Resource Conservation and Recovery Act (RCRA), which is based on leaching potential, as well as state policies that govern waste disposal and other forms of disposition. A previous study estimated that the leached lead concentration from perovskite films on both glass and PET substrates exceeds the RCRA limit of 5 mg L−1 and thus direct landfilling of these hazardous wastes is not permitted.114 There is currently a lack of recyclability of mature PV technologies, such as silicon PVs, because the panels are not designed in a way to be deconstructed easily, making crushing of the panels, after removing the junction box, copper wire and aluminum frame,115 the most viable waste management method. In addition, the recovery of components through crude processing, such as metals, is insufficient to ensure the economic viability of the whole recycling process without relevant incentives. Rich opportunities exist for emerging PV technologies to develop recyclable modules from the outset and thus better future-proof their sustainability. Extensive research efforts have been directed to explore the recycling and reuse potentials of perovskite solar cells, focusing on the TCO-coated substrate (possibly along with ETL materials),116 absorbers, and back electrodes,117 due to their toxicity, high economic value, and limited resource. Selective dissolution has been widely investigated to recover FTO-coated glass with or without the ETL made of TiO2 using DMF,118–120 and to recover ITO-coated glass using KOH aqueous solution.121 The recovered TCO-coated substrate can then be reused for perovskite solar cell re-fabrication after cleaning without substantial performance loss. DMSO, DMF, chlorobenzene have been identified as effective solvents for the selective recovery of degraded perovskite layers.119,122,123 Lead within the absorber can typically be recovered in the form of PbI2, which could be reused for perovskite deposition for cyclic utilization, either via water extraction followed by DMF dissolution,124 through NH3·H2O and HI treatment,125 or through dissolution–recrystallization by butylamine.126 A low-cost and environmentally friendly method via selective dissolution and electrodeposition using a deep eutectic solvent is proposed by Poll et al. to recover pure lead from the absorber.127 To sustainably recover lead from the non-aqueous liquid pollutants generated during perovskite solar cell fabrication, synthesized iron-incorporated hydroxyapatite has been reported as a novel method for both the separation and recovery of lead.128 Back electrodes are typically recovered using straightforward adhesive methods124 or by filtration after dissolving other components in strong solvents.116,117 Additionally, specialized processing is developed to recover and reuse all major components within the degraded perovskite solar cells, from back electrodes, through absorbers, to the substrates.129–132
Although there have been significant advancements in laboratory-scale recycling strategies for perovskite solar cells, there remains a substantial gap in the thorough and systematic investigation of scalability and the lack of comprehensive techno-economic analyses. These recycling strategies are often complex and tailored to specific structures, which may lead to suboptimal economic outcomes. Apart from a notable exception by Chen et al.,132 there is a significant lack of in-depth evaluation that could hinder their applicability to a broader range of perovskite solar cell types. This limitation underscores the need for more generalized and economically viable recycling methods that can be applied across different perovskite solar cell configurations and at different scales. Trade-offs between the complexity of recovery processes and component recovery rate must be meticulously evaluated. Since most reviewed studies use organic solvents for key component recovery, the regeneration of exhausted solvent should be also considered towards scaled remanufacturing routes.
Sustainability analysis of perovskite PVs
Life cycle assessment (LCA) is a comprehensive scientific methodology designed to evaluate the environmental impacts and overall sustainability of a product or system across its entire life cycle. Early LCA studies on perovskite solar cells primarily focused on laboratory-scale designs, aiming to identify energy and environmental hotspots in existing technologies. However, these studies lacked a forward-looking perspective and faced challenges related to scalability and commercial viability. Recognizing the limitations of these early assessments, researchers in the LCA field have shifted their focus toward more industry-relevant architectures, materials, and manufacturing processes inspired by advancements in perovskite solar cell research. This transition marks a critical step in aligning LCA practices with the practical demands of commercialization. Numerous LCA studies have since been conducted to support the development of perovskite solar cells towards market readiness.21,39,133–141 Early research aimed at commercializing perovskite PV modules has explored cost-effective production methods. Notably, one study evaluated the environmental impacts of two perovskite devices fabricated using spray and co-evaporation techniques, assessing their footprint from cradle to gate.133 Subsequent analyses compared several tandem configurations incorporating perovskite,21,134–137 where the potential to outcompete the silicon benchmarks was identified. Numerous studies have also scrutinized the substitution of lead with tin in the perovskite layer, meticulously evaluating the benefits and drawbacks of this alteration.135,138 Several studies have investigated the environmental benefits of alternative electrode materials and processing steps that are more suitable for large-scale manufacturing. These alternatives include carbon electrodes replacing conventional metal electrodes,139,142 graphene transparent electrodes replacing their ITO-based counterparts,143 and inkjet printing replacing spin-coating.144 Leccisi et al. introduced the concept of scalability factor for perovskite PVs,140 and conducted an LCA on crystalline-Si-perovskite tandem solar cells, which are nearing the production stage.141 However, most studies at this stage used a truncated system boundary, typically limited to “cradle-to-gate” or, at best, “cradle-to-grave,” with insufficient attention given to end-of-life management considerations. Potential material recovery methods were investigated at laboratory scale, inspiring the “cradle-to-cradle” analyses with recycling as the end-of-life scenario. Since then, multiple studies have incorporated recycling processes into their LCA system boundaries and concluded effective recycling of exhausted perovskite solar modules has the potential to significantly reduce both the energy demands and the environmental repercussions associated with their production and deployment.39,108,145 The integration of experimental investigation with systems-level analysis has also opened up innovative solutions that could accelerate the commercial deployment of perovskite PV in the near term, such as periodic module rejuvenation. This approach, aimed at enhancing the longevity and circularity of perovskite tandem PVs, offers a promising avenue for overcoming initial stability challenges and facilitating early market entry.38 Note that the solution processability of perovskite PV can be a double-edged sword. While it allows for low-cost, fast production and facilitates material recovery through selective dissolution,145 it can also impose a significant environmental burden due to the extensive use of solvents in the manufacturing process. To address this issue, multiple studies have been conducted to assess the environmental benefits of solvent recycling or the use of green solvents.146,147 Such advancements underscore the evolving nature of LCA studies in perovskite solar cell research, reflecting a growing synergy between experimental developments and environmental sustainability efforts.
Perspectives for sustainability analysis of perovskite PVs for circular solar economy and climate commitments
Analysis of existing literature highlights the nascent state of research in both end-of-life management and sustainability analysis of perovskite PVs. By contrast, amplified research efforts have been directed to improvements in materials, manufacturing processes, and additive engineering that have contributed to better stability and PCE, contextualized in previous sections. To bridge the absence of an established framework that integrates circular economy principles with ecosystem and climate commitments for perovskite PVs, we propose a multi-scale analytics and modeling framework with the aim to provide a comprehensive view, seamlessly integrating different components of the perovskite PV value chain. The schematic of the proposed multi-scale modeling and analytics framework is depicted in Fig. 4. This comprehensive framework consists of four intricately interconnected layers: materials, manufacturing processes and systems, the circular solar economy, and the climate and ecosystem. Each of these layers, arranged from the foundational to the highest level, lends its distinct and vital contribution to the framework's collective structure. Materials science and investigation on advanced manufacturing technologies should be organically integrated with the context of circular solar economy, ecosystems, and climate commitment. In the Circular Solar Economy panel (Fig. 4), we aim to incorporate effective end-of-life recycling and re-manufacturing strategies into the sustainability analysis of the perovskite PV supply chain. This “cradle-to-cradle” approach encompasses the entire life cycle of perovskite PV, integrating various sectors such as manufacturing, transportation, potential applications like co-location with agriculture, and end-of-life management. To address geographical variations, we emphasize regional differences in solar incentives and electricity mix, which can significantly impact the sustainability outcomes in different locations. In the Climate and Ecosystem panel (Fig. 4), our goal is to introduce a temporal dimension to systematically forecast the environmental consequences of transitioning from silicon PV to perovskite PV in the context of long-term climate goals and various transition pathways. These pathways are shaped by a combination of factors, including socio-economic development trajectories, global warming temperature limit, and technological advancements, such as improvements in PCE, lifespan, and varying market share and end-of-life module recycling. Recent studies have underscored the potential of perovskite PV in agrivoltaic settings,148 exploring their role within a broader energy-food-water nexus, rather than merely focusing on energy generation. Perovskite PV-based agrivoltaics represent an emerging system that warrants comprehensive, systems-level investigation to fully understand its diverse environmental, economic, and social impacts. This includes examining the system's metabolism and resilience. To navigate these complexities, we propose three key perspectives for evaluating perovskite PV in terms of materials, manufacturing, and potential applications. These perspectives will guide our exploration of their sustainability within the frameworks of a circular solar economy and climate commitments. Through this holistic analysis, we aim to advance the understanding of perovskite PV's role in achieving sustainability goals across multiple dimensions.
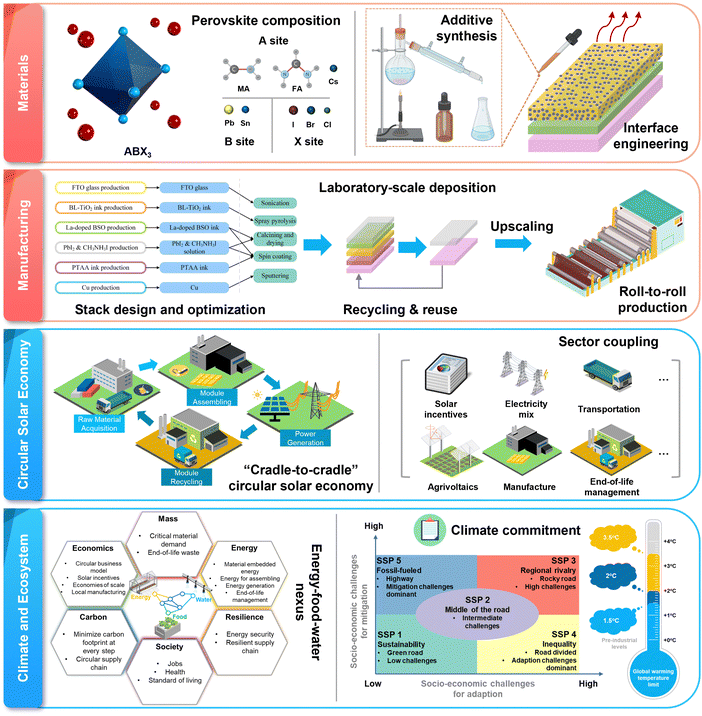 |
| Fig. 4 Schematic of the multi-scale analytics and modeling of perovskite PV value chain. From top to bottom, four systems layers regarding different temporal and spatial scales typify the level of materials, manufacturing, circular solar economy, and climate and ecosystem, respectively. The systems scale grows from top to bottom, whereas the modeling details and resolutions increase from bottom to top. | |
Critical materials and environmental footprint in scaling perovskite PVs under climate commitments
While perovskite solar cells are not expected to see widespread outdoor use in the near future, they hold significant promise for large-scale applications in the longer term. Perovskite technology has the potential to revolutionize solar energy markets due to its use of earth-abundant elements, low energy requirements during deposition, and low-tech, high-throughput processing techniques similar to those used in nano-Si and CIGS PV systems. Current research primarily employs static LCA methods, which rely on average or device-specific inventory data and offer limited forward-looking perspectives.149 This approach may result in conservative or inaccurate estimates of future scenarios, particularly concerning climate commitments for decarbonization.43,150 Since it will take several years for perovskite tandems to gain a substantial market share, it is essential to assess the long-term environmental impacts of this technology through prospective LCA.
The Integrated Assessment Model (IAM) is a comprehensive and powerful tool for investigating the long-term, systems-level environmental consequences of deploying perovskite solar cells. As shown in Fig. 5, the dynamic material flow analysis (DMFA) proposed in this study, provides fresh insights into the patterns and proportions of material usage, the impacts of material stocks on raw material requirements, and the potential for waste recycling, while enabling a comprehensive understanding of the associated economic, environmental, and societal profiles.151,152 DMFA itself could offer prospective insights into critical material requirements across various scenarios of perovskite PV penetration and climate commitments. Moreover, it could generate input data for LCA and techno-economic analysis, resulting in more accurate forecasts of future perovskite solar cell deployments (Fig. 5). For energy transition scenarios, two frameworks – Shared Socio-economic Pathways (SSPs) and Representative Concentration Pathways (RCPs) – are combined, resulting in an integrated set of SSP-RCP scenarios. The SSP framework outlines five primary scenarios, each reflecting distinct socio-economic development trajectories. These include sustainable development (SSP1), a middle-of-the-road scenario (SSP2), regional rivalry (SSP3), inequality (SSP4), and a fossil-fueled development (SSP5).151,153 On the other hand, the RCP offers a model of greenhouse gas concentration trajectories, not emissions, endorsed by the Intergovernmental Panel on Climate Change (IPCC).154 These trajectories are denoted according to potential radiative forcing values by the year 2100. IAM model such as IMAGE could be organically integrated with Ecoinvent database to generate the corresponding prospective life cycle inventory dataset and streamline future scenario analyses.
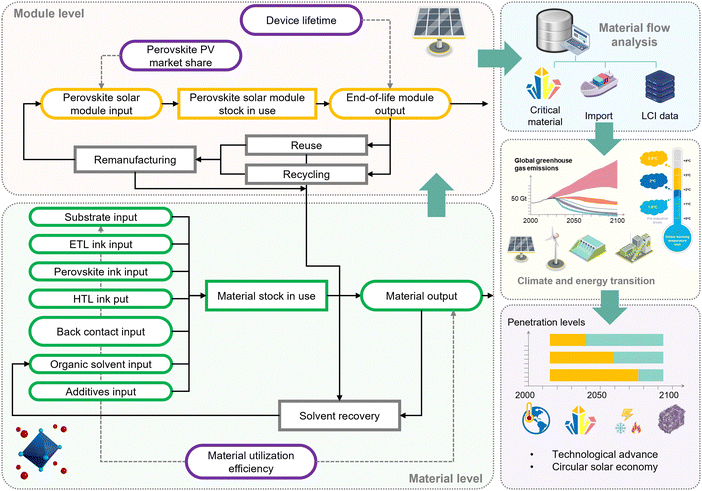 |
| Fig. 5 Overview of the dynamic material flow analysis-based life cycle assessment of perovskite PV. The methodology is comprised of two components, including a two-level dynamic material flow analysis (material and module levels) and life cycle assessment. The climate and energy transition pathways could be modeled based on the Shared Socio-economic Pathways (SSPs) and bridged with decarbonization and climate targets. Different perovskite PV penetration scenarios are examined to assess the impacts on the solar economy, compared to the silicon or thin-film PV-dominant market. | |
To fully understand the long-term socioeconomic dynamics and development trajectories of the solar industry due to the rise of perovskite technology, it is necessary to expand the aforementioned IAM scenarios. These scenarios should be based on not only SSP and RCP, but also capture the uncertainties in technological advancements, such as improvements in PCE and lifespan, as well as varying levels of market penetration. The transition from silicon PV technology to perovskite will be gradual, with hybrid perovskite–silicon systems likely serving as an intermediate step before moving toward silicon-free, all-perovskite systems. This expanded scenario setting will provide a more accurate picture of how the solar industry might evolve in response to technological innovations and market dynamics. A lower global temperature rise limit indicates a greater degree of decarbonization in sectors such as transportation and energy. Similarly, a higher penetration of perovskite PV by the target year suggests that more silicon PV will be replaced by perovskite tandem technologies. In the long term, all-perovskite tandem cells are expected to replace perovskite–silicon tandems (as an intermediary step in the short term), offering significantly lower embedded emissions in both material and energy consumption during production, while maintaining comparable PCE to silicon PV. Consequently, the combination of a stricter temperature rise limit and increased market share of all-perovskite tandem cells would lead to a substantial reduction in greenhouse gas emissions. The derived insights could be efficiently leveraged to evaluate the potential impacts of the transition to perovskite PV technology on the solar economy of a specific region or country, thereby informing policy decisions.
Evaluating the long-term demand for critical materials and the environmental impacts of perovskite PV is essential for guiding the transformation of the PV industry toward a circular, perovskite solar economy and meeting climate commitments. However, this evaluation presents several research challenges. The first challenge involves gathering comprehensive and reliable data on various factors, including geographical scope and territorial division, market data for silicon and perovskite solar technologies, the remaining lifetimes of devices in service, total solar capacity, energy mix, and material recycling and climate policies across different regions. The second challenge is establishing representative future scenarios that expand on the SSP and RCP. These scenarios should consider evolving device efficiency, lifespan, technological diffusion rates, and final penetration levels specific to perovskite PV. The third challenge is managing the combinatorial uncertainty that arises from each layer of the dynamic material flow analysis DMFA model, as well as the LCA implementation. This is necessary to generate robust projections of perovskite solar deployment from a forward-looking perspective. Addressing these challenges will help fill the knowledge gap related to the limited exploration of long-term critical material demand and the environmental implications of perovskite solar deployment under various socioeconomic scenarios, which has been hindered by uncertainties about the future and data availability.
Local material acquisition for resilient perovskite PV supply chains under circular solar economy
To support the fast growth of PV that is much needed for climate change mitigation, it is imperative that the PV industry further improves resource sustainability and addresses end-of-life management. Responsible upscaling requires that the industry reduces costs, material utilization, and environmental impact at every step.155 Throughout the solar PV supply chain, raw material and module shipping as well as the energy mix used in PV manufacture are two critical factors.156
As solar PV has become a strategic technology to fight against climate change, the importance of delocalization of the PV supply chain is highlighted, not only to reduce logistics costs and embedded emissions but also to ensure uninterrupted component supply. Distributed manufacturing poses a challenge for conventional silicon PV, since the cost of silicon PV modules is significantly sensitive to the manufacturing capacity owing to economies of scale.37 A recent study reveals that the low-tech processing involved in perovskite solar cell manufacturing makes it not only feasible but also affordable even for low- and lower-middle income countries (LLMICs).37 For countries or regions where distributed manufacturing of perovskite solar cell is viable, this strategy presents multifold advantages: (1) for solution-processed PVs, it is possible to achieve relatively low manufacturing costs at smaller scales due to the minimal contribution of roll-to-roll tooling capital expenditures to the final module cost.157 (2) It boosts the local economy by enhancing competitiveness, creating jobs, and reducing unemployment, especially in low-income areas. (3) Reduces dependency on international supply chains, which are often vulnerable to disruptions, thereby enhancing energy security and supply chain resilience.158 (4) Minimizes carbon emissions and energy use by eliminating the need for long-distance transport of materials and products. (5) Avoids import tariffs that can significantly increase retail prices,37 promoting local energy independence.
Developed countries, such as the US, stand on the brink of an unprecedented opportunity amid their energy transition projected towards 2050. Enhanced manufacturing capabilities for solar panel components, coupled with favorable policy incentives like the Inflation Reduction Act (IRA),159,160 and competitive electricity prices relative to many developed nations,161 position the US as a viable contender for advancing the distributed production of perovskite solar cells. Fig. 6 shows the current locations of perovskite PV companies in the US. This proposition necessitates a comprehensive exploration of its potential benefits not only to the PV industry and energy sector, but also to society at large. Consequently, a rigorous multi-scale analysis is essential to systematically examine the economic, environmental, and social impacts of distributed perovskite solar cell production. Such an investigation should consider factors such as the state-specific electrical grid, policy incentives, and the availability of solar panel developers and perovskite material providers (Fig. 6).
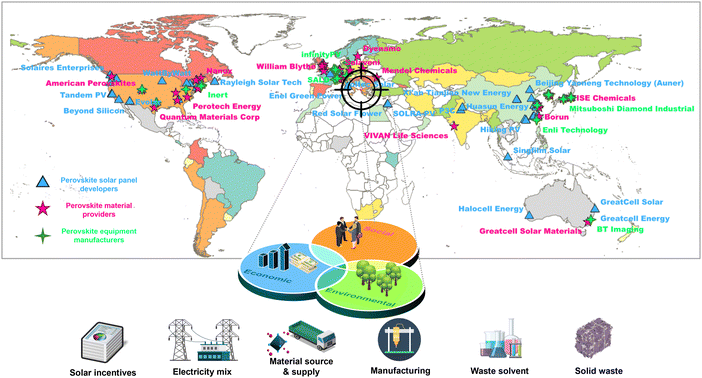 |
| Fig. 6 Overview of distributed manufacturing of perovskite solar panels. Herein, “distributed manufacturing” denotes a production method that prioritizes the use of locally or domestically sourced materials through a shortened supply chain, emphasizing geographical origin over production scale. Given geographical scope and territorial division, differences lying in the solar incentives, electricity mix, material source and supply, manufacturing process, and treatment of waste solvent and solid waste are explicitly considered. Future analyses should investigate the economic, environmental, and sociological standings of perovskite PV systems to identify potential distributed manufacturing sites. The data identifying the locations of perovskite solar panel developers, material providers, and equipment manufacturers are presented in Tables S1–S3 of the ESI.† | |
There are multiple research challenges to surmount for developing a holistic multi-scale analysis model to determine the most favorable region for distributed perovskite PV manufacturing. The first challenge is associated with data collection of information of perovskite material providers, such as material categories, annual yield, feedstock manufacturing route, since the manufacturing of perovskite solar cell involves a variety of niche materials, whose market is still immature at the current stage. The second challenge is incorporating recycling processes into the manufacturing infrastructure. Due to the shorter device lifetime of perovskite solar cells compared to established PV technologies, it is essential to model end-of-life management strategies from the outset to enhance their competitiveness under circular solar economy, with explicit considerations of solvent and solid waste treatment. The third challenge is to continuously assess the impact of increased perovskite PV penetration in the grid on future perovskite solar cell manufacturing and related policymaking. This recursive evaluation will help to understand the evolving dynamics and growth of the perovskite PV sector. Another challenge is associated with the quantification of the improved supply chain resilience by virtue of distributed manufacturing, compared to delocalized supply chain.
Perovskite PVs in energy-food-water nexus for energy and ecological transition
The global population is expected to reach 9.8 billion by 2050,162 which underscores a growing demand for energy, food, and water. This projection highlights the critical nature of the energy-food-water nexus, emphasizing the need for integrated solutions to manage these interdependent resources efficiently. Agriculture, occupying 52% of the US base land as of 2021,39 stands as the primary land user, positioning the sector at the center of increasing land competition. Such competition not only exacerbates environmental challenges, including biodiversity loss and increased water use, but may also contribute to emissions due to indirect land use changes.163 In response to these challenges, fostering a synergistic relationship between solar PVs and agriculture emerges as an effective strategy. This approach not only addresses the imminent issues by offering a dual-purpose solution that enhances energy production and agricultural productivity but also delivers ecological benefits, thereby mitigating the environmental impacts associated with land use intensification.
Agrivoltaics, conceived from the symbiotic integration of agriculture and PVs, fundamentally represents a comprehensive energy-food-water nexus system. Both agriculture and PV systems require land, and in some cases, the same land may be suitable for both purposes. Typical dual-use applications encompass: (1) PV greenhouse, with solar panels installed on the surface of greenhouse for power and heat supply, wind prevention, evaporation reduction, and precipitation collection, etc.; (2) integrated open-field PV and crop production, with crops grown in between and/or underneath solar panels; (3) integrated open-field PV and animal husbandry, with grazing in between and/or underneath solar panels.164 (Fig. 7(a)) This co-location strategy enhances land-use efficiency, conserves water, reduces soft costs, and can improve crop yields. In water-scarce regions, agrivoltaics moderates climate challenges by passively redistributing limited rainfall, reducing evaporation and thus lowering plant water demands, and increasing soil moisture retention (Fig. 7(b)),165,166 while also creating resilient microclimates that counter environmental stresses such as heat and drought.167 In summary, agrivoltaics systems offer multiple potential ecosystem services, including energy and economic benefits, increased crop yields, water conservation, biodiversity preservation, etc.168 (Fig. 7(c)) However, potential risks, such as human toxicity from the leakage of critical elements from PV panels, should not be overlooked and require careful management to maximize the benefits while mitigating any environmental and health concerns.
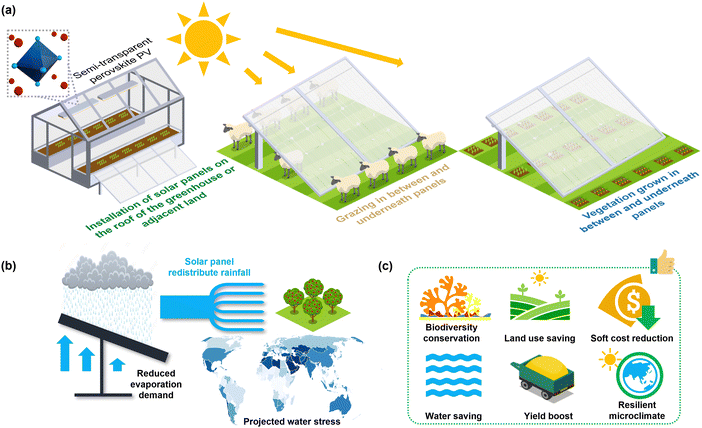 |
| Fig. 7 Overview of the sustainable energy-food-water nexus by integrating semi-transparent perovskite PVs for agrivoltaics applications. (a) three typical agrivoltaics applications include greenhouse solar, animal husbandry, and crop production, with installation of perovskite solar panels on the roof of the greenhouse or adjacent land, grazing in between and underneath panels, and vegetation grown in between and underneath panels, respectively. (b) agrivoltaics’ role in water saving. (c) Potential benefits associated with agrivoltaics systems. | |
Though most existing agrivoltaics systems rely on monocrystalline PV for grazing, habitat, or crop production applications, silicon PVs are not the most suitable option for agrivoltaics applications. First, crystalline silicon is not suitable for developing transparent PVs due to the intrinsic opaqueness of the material itself. Tuning the crystalline silicon PVs for higher transparency that ensure sufficient light can pass through the solar cells to be utilized by photosynthesis of crops would further increase the already high manufacturing cost through specialized processing and significantly compromise the PCE.169 Second, being rigid and brittle in nature is another challenge that impedes the conventional silicon crystalline PV in agrivoltaics applications.170
There is an urgent need for innovative PV technologies to rejuvenate the field of agrivoltaics, and perovskite PVs stand as a particularly promising option. First, semi-transparency of perovskite solar cells can be achieved in various ways: (1) utilizing a thin perovskite film; (2) enabling self-assembly of the perovskite on a photoanode, which creates transparent regions without compromising light-harvesting efficiency; (3) leveraging solvent properties to induce dewetting, forming perovskite islands on the surface; and (4) incorporating transparent contacts that render the solar cell fully semi-transparent.171 In this paper, we do not explore the details of processes such as the self-assembly of perovskite for semi-transparency, as these are more relevant to innovations in materials science and fall outside the scope of this review. Instead, our primary focus is on highlighting key developments and overarching trends in the sustainability analysis of scalable perovskite solar cells. For a more comprehensive understanding of self-assembly processes for semi-transparency, we encourage readers to consult recent publications dedicated to this topic.172–174 Moreover, the adjustable bandgap of perovskite materials offers the flexibility to tailor the solar spectrum and intensity, which are crucial for optimizing plant growth conditions. Second, perovskite solar cells are compatible with flexible substrate for light-weight applications, making temporarily removing or adjusting the solar panels for maximum sunlight exposure easy. Though organic solar cells also present outstanding PV performance while benefiting the survival rate and growth of the crops,175 its PCE is much lower than that of perovskite PV. It is important to recognize that CIGS, CdTe, a-Si, and nano-Si PV technologies are also suitable for use with flexible substrates and semi-transparent applications. Consequently, when evaluating the performance of perovskite-based agrivoltaics systems, a thorough comparison with these other PV technologies is essential to ensure a comprehensive understanding of their relative efficiencies, applicability, and sustainability.
The solar industry is increasingly shifting its focus toward perovskite–silicon tandem solar cells, largely due to their potential to significantly enhance PCE while incurring minimal additional cost and weight. These tandem cells are particularly advantageous in that they capture a broader spectrum of sunlight, thereby increasing energy output per unit area. This gain in efficiency is especially critical in agrivoltaics systems, where land must be efficiently utilized for both energy generation and crop cultivation. Nevertheless, it is important to acknowledge that perovskite–silicon tandem solar panels present their own set of challenges. The increased complexity of their structure may render them more cumbersome in operational contexts, such as installation, removal, or cleaning. While their improvements in efficiency are evident, these operational difficulties may be comparable to those encountered with traditional silicon systems. As such, despite the clear technical advantages offered by tandem configurations, they do not necessarily address all practical challenges associated with agrivoltaics applications in the short term. Looking toward the future, the potential transition away from silicon-only systems in agricultural settings signals a broader movement toward more advanced and adaptable technologies. The long-term objective in agrivoltaics development is the implementation of semi-transparent perovskite–perovskite tandem solar cells, which would eliminate reliance on silicon entirely. These semi-transparent panels offer the added benefit of allowing greater sunlight penetration to crops beneath them, thereby enhancing plant growth while simultaneously generating electricity. Additionally, their lightweight nature and potentially simpler maintenance requirements address many of the logistical challenges associated with conventional silicon PV systems. In conclusion, while the current perovskite–silicon tandem systems present notable improvements in efficiency, they do not fully resolve the operational challenges associated with agricultural applications. The ongoing transition toward silicon-free systems, particularly semi-transparent perovskite–perovskite tandem solar cells, represents the most promising path forward in overcoming the limitations of traditional silicon PV, ultimately achieving an optimal balance between energy production and agricultural productivity.
Systematically evaluating the potential of implementing perovskite solar cells in agrivoltaics applications poses several challenges. Food security for the perovskite agrivoltaics should be systematically evaluated due to the Pb-related risks. Certainly, the concern of Pb leaching from perovskite solar cells in the case of encapsulation failure introduces a specific challenge to the application of perovskite agrivoltaics,176,177 particularly as crops are grown directly beneath the panels. It is crucial to implement effective safeguards to monitor and prevent the inadvertent release of lead leachate, ensuring the protection of agricultural productivity and environmental health. Among the methods for lead retention are the use of self-healing polymers for encapsulation modification178 and lead-adsorbing molecular films with phosphonic acid groups.179 While these methods hold promise, they could potentially increase manufacturing costs. Hence, the primary challenge lies in striking a balance between developing cost-effective perovskite agrivoltaics and effectively managing lead exposure.180 The second challenge is to determine the material selection and device architecture of the perovskite solar cells suited for various agrivoltaics applications. This requires a systems-level rigorous evaluation and screening among the various potential perovskite solar cells, while accounting for maximization of compatibility and synergistic benefits between each stack design and agricultural activity. The synergistic benefits include improved systems resilience, increased yield, and reduced water consumption, etc. Simultaneously accounting for the three dimensions of the energy-food-water nexus is also challenging. There are also challenges associated with the system boundary definition, data collection for sustainability analyses benchmarked against the silicon PV-based agrivoltaics systems and conventional agriculture or PV systems alone. The fifth challenge is associated with modeling the periodic cleaning and replacement schemes of perovskite solar cells to ensure the normal operations of the co-located systems under circular solar economy. The final challenge is to quantitatively model such land use change and its impacts and footprints on the ecosystems under the future projected environmental stress involving increased global temperatures and water stress.
Conclusions
Perovskite materials offered excellent light absorption, charge-carrier mobilities, and lifetimes, resulting in high device efficiencies with opportunities to realize a low-cost, industry-scalable technology. Achieving this potential would require overcoming barriers related to stability and environmental compatibility, but if these concerns were addressed, perovskite-based technology held transformational potential for rapid TW-scale solar deployment. The basic materials properties had also sparked interest in using hybrid perovskite semiconductors in a broader class of energy applications that spanned traditional electronic and optical systems. We comprehensively reviewed recent advances of perovskite solar cells in terms of embedded critical materials, scalable deposition approaches, and end-of-life management. Future research that employs the integrated DMFA and LCA methodology proposed in this study would offer new perspectives on material usage trends and ratios, the influence of material stocks on raw material demands, and the recycling possibilities of waste. This approach facilitated a holistic understanding of the economic, environmental, and social impacts associated with material use during the PV transition across various scenarios of perovskite PV penetration and climate commitments. Further research could be directed to exploring the potential of distributed manufacturing of perovskite solar panels for costs, embedded energy, and environmental impacts minimization to determine the best region for investment in perovskite solar panel manufacturing by considering technical, economic, environmental, and social aspects; assessing the synergistic benefits and sustainability of co-location of perovskite PVs with agricultural activities in energy-food-water nexus with a sector coupling consideration. The sustainability analysis of perovskite PVs should not be examined in isolation at the material and manufacturing levels. Instead, it should be comprehensively contextualized within the broader framework of a circular solar economy and under climate commitment.
Data availability
All data needed to evaluate the conclusions in this paper are present in the main text and ESI.† Additional data are available from the authors upon request.
Conflicts of interest
S. D. S. is a co-founder of Swift Solar, Inc. J. H. is a founder of Perotech Inc.
Acknowledgements
This work is supported in part by the National Science Foundation (NSF) CAREER Award (CBET-1643244). F. Y. acknowledges the partial supported by the Schmidt Sciences, LLC. S. D. S. thanks the Royal Society and Tata Group (UF150033). J. H. thanks the support from the U.S. Department of Energy, Office of Science, under award DE-SC0025281. V. M. F. acknowledges partial support by the U.S. Department of Energy's Office of Energy Efficiency and Renewable Energy (DOE-EERE) under the Solar Energy Technologies Office (SETO) Award Number DE00008453 and from National Science Foundation (NSF) research grant CBET-1705606.
References
- IEA Solar PV, Finland 2023: Energy Policy Review, https://www.iea.org/reports/solar-pv, (accessed May 1st, 2023).
- U.S. EIA, Today in energy, https://www.eia.gov/todayinenergy/, (accessed May 1st, 2023).
- IEA Renewables 2022, Executive summary, https://www.iea.org/reports/renewables-2022/executive-summary, (accessed Feb 1st, 2024).
- J. J. Berry, J. van de Lagemaat, M. M. Al-Jassim, S. Kurtz, Y. Yan and K. Zhu, ACS Energy Lett., 2017, 2, 2540–2544 CrossRef CAS.
- S. D. Stranks, Contemp. Phys., 2022, 63, 280–304 CrossRef.
- M. A. Green, E. D. Dunlop, M. Yoshita, N. Kopidakis, K. Bothe, G. Siefer and X. Hao, Prog. Photovoltaics Res. Appl., 2023, 31, 651–663 CrossRef.
- D. Bonnet, Int. J. Sol. Energy, 1992, 12, 1–14 CrossRef.
- V. Fthenakis, Renewable Sustainable Energy Rev., 2009, 13, 2746–2750 Search PubMed.
- NREL, Transforming Energy: Best Research-Cell Efficiency Chart, https://www.nrel.gov/pv/cell-efficiency.html/, (accessed Aug 16th, 2024).
- D. Khan, G. Qu, I. Muhammad, Z. Tang and Z.-X. Xu, Adv. Energy Mater., 2023, 13, 2302124 CrossRef CAS.
- Z. Li, T. R. Klein, D. H. Kim, M. Yang, J. J. Berry, M. F. A. M. van Hest and K. Zhu, Nat. Rev. Mater., 2018, 3, 18017 CrossRef CAS.
- D. A. Egger, E. Edri, D. Cahen and G. Hodes, J. Phys. Chem. Lett., 2015, 6, 279–282 CrossRef CAS.
- Z. Huang, X. Hu, Z. Zhao, X. Meng, M. Su, T. Xue, J. Chi, H. Xie, Z. Cai and Y. Chen, Adv. Energy Mater., 2021, 11, 2101291 CrossRef CAS.
- Y. Y. Kim, T.-Y. Yang, R. Suhonen, A. Kemppainen, K. Hwang, N. J. Jeon and J. Seo, Nat. Commun., 2020, 11, 5146 CrossRef CAS.
- Y. Wang, Y. Zhang, P. Zhang and W. Zhang, Phys. Chem. Chem. Phys., 2015, 17, 11516–11520 RSC.
- B. Shi, L. Duan, Y. Zhao, J. Luo and X. Zhang, Adv. Mater., 2020, 32, 1806474 CrossRef CAS.
- E. L. Unger, L. Kegelmann, K. Suchan, D. Sörell, L. Korte and S. Albrecht, J. Mater. Chem. A, 2017, 5, 11401–11409 RSC.
- B. T. Muhammad, S. Kar, M. Stephen and W. L. Leong, Mater. Today Energy, 2022, 23, 100907 CrossRef CAS.
- J. Walzberg, A. Carpenter and G. A. Heath, Nat. Energy, 2021, 6, 913–924 CrossRef.
-
T. L. Curtis, H. Buchanan, G. Heath, L. Smith and S. Shaw, Solar Photovoltaic Module Recycling: A Survey of US Policies and Initiatives, National Renewable Energy Lab. (NREL), Golden, CO (United States), 2021 Search PubMed.
- E. Leccisi and V. Fthenakis, Prog. Photovoltaics Res. Appl., 2021, 29, 1078–1092 CrossRef CAS.
- H. Shen, T. Duong, J. Peng, D. Jacobs, N. Wu, J. Gong, Y. Wu, S. K. Karuturi, X. Fu, K. Weber, X. Xiao, T. P. White and K. Catchpole, Energy Environ. Sci., 2018, 11, 394–406 RSC.
- D. Zhao, C. Chen, C. Wang, M. M. Junda, Z. Song, C. R. Grice, Y. Yu, C. Li, B. Subedi, N. J. Podraza, X. Zhao, G. Fang, R.-G. Xiong, K. Zhu and Y. Yan, Nat. Energy, 2018, 3, 1093–1100 CrossRef CAS.
- F. Fu, J. Li, T. C.-J. Yang, H. Liang, A. Faes, Q. Jeangros, C. Ballif and Y. Hou, Adv. Mater., 2022, 34, 2106540 CrossRef CAS PubMed.
- J. Thiesbrummel, F. Peña-Camargo, K. O. Brinkmann, E. Gutierrez-Partida, F. Yang, J. Warby, S. Albrecht, D. Neher, T. Riedl, H. J. Snaith, M. Stolterfoht and F. Lang, Adv. Energy Mater., 2023, 13, 2202674 CrossRef CAS.
- R. Lin, J. Xu, M. Wei, Y. Wang, Z. Qin, Z. Liu, J. Wu, K. Xiao, B. Chen and S. M. Park, Nature, 2022, 603, 73–78 CrossRef CAS PubMed.
- K. Datta, J. Wang, D. Zhang, V. Zardetto, W. H. M. Remmerswaal, C. H. L. Weijtens, M. M. Wienk and R. A. J. Janssen, Adv. Mater., 2022, 34, 2110053 CrossRef CAS.
- F.-W. Liu, G. Biesold, M. Zhang, R. Lawless, J.-P. Correa-Baena, Y.-L. Chueh and Z. Lin, Mater. Today, 2021, 43, 185–197 CrossRef CAS.
- D. Wang, M. Wright, N. K. Elumalai and A. Uddin, Sol. Energy Mater. Sol. Cells, 2016, 147, 255–275 CrossRef CAS.
- M. O. Reese, S. A. Gevorgyan, M. Jørgensen, E. Bundgaard, S. R. Kurtz, D. S. Ginley, D. C. Olson, M. T. Lloyd, P. Morvillo, E. A. Katz, A. Elschner, O. Haillant, T. R. Currier, V. Shrotriya, M. Hermenau, M. Riede, K. R. Kirov, G. Trimmel, T. Rath, O. Inganäs, F. Zhang, M. Andersson, K. Tvingstedt, M. Lira-Cantu, D. Laird, C. McGuiness, S. Gowrisanker, M. Pannone, M. Xiao, J. Hauch, R. Steim, D. M. DeLongchamp, R. Rösch, H. Hoppe, N. Espinosa, A. Urbina, G. Yaman-Uzunoglu, J.-B. Bonekamp, A. J. J. M. van Breemen, C. Girotto, E. Voroshazi and F. C. Krebs, Sol. Energy Mater. Sol. Cells, 2011, 95, 1253–1267 CrossRef CAS.
- S. Ma, G. Yuan, Y. Zhang, N. Yang, Y. Li and Q. Chen, Energy Environ. Sci., 2022, 15, 13–55 RSC.
- Z. Wang, L. Zeng, T. Zhu, H. Chen, B. Chen, D. J. Kubicki, A. Balvanz, C. Li, A. Maxwell, E. Ugur, R. dos Reis, M. Cheng, G. Yang, B. Subedi, D. Luo, J. Hu, J. Wang, S. Teale, S. Mahesh, S. Wang, S. Hu, E. D. Jung, M. Wei, S. M. Park, L. Grater, E. Aydin, Z. Song, N. J. Podraza, Z.-H. Lu, J. Huang, V. P. Dravid, S. De Wolf, Y. Yan, M. Grätzel, M. G. Kanatzidis and E. H. Sargent, Nature, 2023, 618, 74–79 CrossRef CAS.
- The Perovskite Database, https://www.perovskitedatabase.com/, (accessed May 20th, 2023).
- Oxford PV - Tandem cell production, https://www.oxfordpv.com/tandem-cell-production, (accessed Oct 1st, 2024).
- Swift Solar – Next generation lightweight and efficient solar technology, https://www.swiftsolar.com/about/, (accessed Oct 1st, 2024).
- P. Zhu, C. Chen, J. Dai, Y. Zhang, R. Mao, S. Chen, J. Huang and J. Zhu, Adv. Mater., 2024, 36, 2307357 CrossRef CAS.
- B. Roose, E. M. Tennyson, G. Meheretu, A. Kassaw, S. A. Tilahun, L. Allen and S. D. Stranks, Energy Environ. Sci., 2022, 15, 3571–3582 RSC.
- X. Tian, B. Roose, S. D. Stranks and F. You, Energy Environ. Sci., 2023, 16, 5551–5567 RSC.
- X. Tian, S. D. Stranks and F. You, Nat. Sustain., 2021, 4, 821–829 CrossRef.
- M. L. Parisi and A. Sinicropi, Nat. Sustain., 2021, 4, 754–755 CrossRef.
- J.-H. Lee, D. G. Lee, H. S. Jung, H. H. Lee and H.-K. Kim, J. Alloys Compd., 2020, 845, 155531 CrossRef CAS.
- M. M. Tavakoli, P. Yadav, R. Tavakoli and J. Kong, Adv. Energy Mater., 2018, 8, 1800794 CrossRef.
- N. Espinosa, L. Serrano-Luján, A. Urbina and F. C. Krebs, Sol. Energy Mater. Sol. Cells, 2015, 137, 303–310 CrossRef CAS.
- M. L. Petrus, T. Bein, T. J. Dingemans and P. Docampo, J. Mater. Chem. A, 2015, 3, 12159–12162 RSC.
- B. Pashaei, S. Bellani, H. Shahroosvand and F. Bonaccorso, Chem. Sci., 2020, 11, 2429–2439 RSC.
- A. Connell, Z. Wang, Y.-H. Lin, P. C. Greenwood, A. A. Wiles, E. W. Jones, L. Furnell, R. Anthony, C. P. Kershaw, G. Cooke, H. J. Snaith and P. J. Holliman, J. Mater. Chem. C, 2019, 7, 5235–5243 RSC.
- J. H. Heo, D. S. Lee, D. H. Shin and S. H. Im, J. Mater. Chem. A, 2019, 7, 888–900 RSC.
- K. J. Prince, H. M. Mirletz, E. A. Gaulding, L. M. Wheeler, R. A. Kerner, X. Zheng, L. T. Schelhas, P. Tracy, C. A. Wolden, J. J. Berry, S. Ovaitt, T. M. Barnes and J. M. Luther, Nat. Mater., 2024 DOI:10.1038/s41563-024-01945-6.
- I. Levine, A. Al-Ashouri, A. Musiienko, H. Hempel, A. Magomedov, A. Drevilkauskaite, V. Getautis, D. Menzel, K. Hinrichs, T. Unold, S. Albrecht and T. Dittrich, Joule, 2021, 5, 2915–2933 CrossRef CAS.
- A. Al-Ashouri, A. Magomedov, M. Roß, M. Jošt, M. Talaikis, G. Chistiakova, T. Bertram, J. A. Márquez, E. Köhnen, E. Kasparavičius, S. Levcenco, L. Gil-Escrig, C. J. Hages, R. Schlatmann, B. Rech, T. Malinauskas, T. Unold, C. A. Kaufmann, L. Korte, G. Niaura, V. Getautis and S. Albrecht, Energy Environ. Sci., 2019, 12, 3356–3369 RSC.
- S. Sajid, A. M. Elseman, H. Huang, J. Ji, S. Dou, H. Jiang, X. Liu, D. Wei, P. Cui and M. Li, Nano Energy, 2018, 51, 408–424 CrossRef CAS.
- A. Yi, S. Chae, H. Yoon and H. J. Kim, ACS Sustainable Chem. Eng., 2022, 10, 16440–16449 CrossRef.
- Y. Liu, Z. Yang and S. Liu, Adv. Sci., 2018, 5, 1700471 CrossRef.
- Y. Zhang, Y. Liu and S. Liu, Adv. Funct. Mater., 2023, 33, 2210335 CrossRef CAS.
- J. S. Manser, M. I. Saidaminov, J. A. Christians, O. M. Bakr and P. V. Kamat, Acc. Chem. Res., 2016, 49, 330–338 CrossRef CAS.
- X. Wang, Y. Fan, L. Wang, C. Chen, Z. Li, R. Liu, H. Meng, Z. Shao, X. Du and H. Zhang, Chem, 2020, 6, 1369–1378 CAS.
- N. Pellet, P. Gao, G. Gregori, T.-Y. Yang, M. K. Nazeeruddin, J. Maier and M. Grätzel, Angew. Chem., Int. Ed., 2014, 53, 3151–3157 CrossRef CAS.
- Y. Deng, G. Ren, D. Han, W. Han, Z. Li, C. Liu and W. Guo, J. Energy Chem., 2022, 73, 615–638 CrossRef CAS.
- H. Li, Y. Xu, S. Ramakrishnan, Y. Zhang, M. Cotlet, T. L. Xu and Q. Yu, Cell Rep. Phys. Sci., 2022, 3, 101060 CrossRef CAS.
- K.-z Du, Q. Tu, X. Zhang, Q. Han, J. Liu, S. Zauscher and D. B. Mitzi, Inorg. Chem., 2017, 56, 9291–9302 CrossRef CAS.
- R. Younts, H. S. Duan, B. Gautam, B. Saparov, J. Liu, C. Mongin, F. N. Castellano, D. B. Mitzi and K. Gundogdu, Adv. Mater., 2017, 29, 1604278 CrossRef PubMed.
- M. Wang, Z. Shi, C. Fei, Z. J. D. Deng, G. Yang, S. P. Dunfield, D. P. Fenning and J. Huang, Nat. Energy, 2023, 8, 1229–1239 CrossRef CAS.
- C. Ma, C. Leng, Y. Ji, X. Wei, K. Sun, L. Tang, J. Yang, W. Luo, C. Li, Y. Deng, S. Feng, J. Shen, S. Lu, C. Du and H. Shi, Nanoscale, 2016, 8, 18309–18314 RSC.
- G. Grancini, C. Roldán-Carmona, I. Zimmermann, E. Mosconi, X. Lee, D. Martineau, S. Narbey, F. Oswald, F. De Angelis, M. Graetzel and M. K. Nazeeruddin, Nat. Commun., 2017, 8, 15684 CrossRef CAS PubMed.
- X. Jiang, H. Li, Q. Zhou, Q. Wei, M. Wei, L. Jiang, Z. Wang, Z. Peng, F. Wang, Z. Zang, K. Xu, Y. Hou, S. Teale, W. Zhou, R. Si, X. Gao, E. H. Sargent and Z. Ning, J. Am. Chem. Soc., 2021, 143, 10970–10976 CrossRef CAS PubMed.
- J. Jeong, M. Kim, J. Seo, H. Lu, P. Ahlawat, A. Mishra, Y. Yang, M. A. Hope, F. T. Eickemeyer, M. Kim, Y. J. Yoon, I. W. Choi, B. P. Darwich, S. J. Choi, Y. Jo, J. H. Lee, B. Walker, S. M. Zakeeruddin, L. Emsley, U. Rothlisberger, A. Hagfeldt, D. S. Kim, M. Grätzel and J. Y. Kim, Nature, 2021, 592, 381–385 CrossRef CAS.
- F. Wang, X. Jiang, H. Chen, Y. Shang, H. Liu, J. Wei, W. Zhou, H. He, W. Liu and Z. Ning, Joule, 2018, 2, 2732–2743 CrossRef CAS.
- J. Wang, H. Shen, W. Li, S. Wang, J. Li and D. Li, Adv. Sci., 2019, 6, 1802019 CrossRef.
- M. Härtel, B. Li, S. Mariotti, P. Wagner, F. Ruske, S. Albrecht and B. Szyszka, Sol. Energy Mater. Sol. Cells, 2023, 252, 112180 CrossRef.
- M. Que, B. Zhang, J. Chen, X. Yin and S. Yun, Mater. Adv., 2021, 2, 5560–5579 RSC.
- H. Zhang, Y. Li, S. Tan, Z. Chen, K. Song, S. Huang, J. Shi, Y. Luo, D. Li and Q. Meng, J. Colloid Interface Sci., 2022, 608, 3151–3158 CrossRef CAS.
- Q.-Q. Chu, B. Ding, J. Peng, H. Shen, X. Li, Y. Liu, C.-X. Li, C.-J. Li, G.-J. Yang, T. P. White and K. R. Catchpole, J. Mater. Sci. Technol., 2019, 35, 987–993 CrossRef CAS.
- H. Zhang, J. Xiao, J. Shi, H. Su, Y. Luo, D. Li, H. Wu, Y.-B. Cheng and Q. Meng, Adv. Funct. Mater., 2018, 28, 1802985 CrossRef.
- Q. Luo, H. Ma, Q. Hou, Y. Li, J. Ren, X. Dai, Z. Yao, Y. Zhou, L. Xiang, H. Du, H. He, N. Wang, K. Jiang, H. Lin, H. Zhang and Z. Guo, Adv. Funct. Mater., 2018, 28, 1706777 CrossRef.
- C. Peng, H. Su, J. Li, Q. Duan, Q. Li, J. Xiao, Z. Ku, J. Zhong, W. Li, Y. Peng, F. Huang and Y.-B. Cheng, Sol. Energy Mater. Sol. Cells, 2021, 230, 111226 CrossRef CAS.
- Y. Cai, L. Liang and P. Gao, Chin. Phys. B, 2018, 27, 018805 CrossRef.
-
S. Chu, Critical materials strategy, DIANE publishing, 2011 Search PubMed.
- US adds copper to critical raw materials list, https://www.mining-technology.com/news/us-government-adds-copper-to-critical-materials-list/, (accessed Aug 4th, 2023).
- A. Rizzo, S. Goel, M. Luisa Grilli, R. Iglesias, L. Jaworska, V. Lapkovskis, P. Novak, B. O. Postolnyi and D. Valerini, Materials, 2020, 13, 1377 CrossRef CAS.
- European Commission, Critical raw materials, https://single-market-economy.ec.europa.eu/sectors/raw-materials/areas-specific-interest/critical-raw-materials_en, (accessed Jun 17th, 2023).
- B. Conings, A. Babayigit and H.-G. Boyen, ACS Energy Lett., 2019, 4, 873–878 CrossRef CAS.
- J. M. Kadro and A. Hagfeldt, Joule, 2017, 1, 29–46 CrossRef.
- M. Remeika and Y. Qi, J. Energy Chem., 2018, 27, 1101–1110 CrossRef.
- J. H. Kim, S. T. Williams, N. Cho, C.-C. Chueh and A. K.-Y. Jen, Adv. Energy Mater., 2015, 5, 1401229 CrossRef.
- T. Qin, W. Huang, J.-E. Kim, D. Vak, C. Forsyth, C. R. McNeill and Y.-B. Cheng, Nano Energy, 2017, 31, 210–217 CrossRef CAS.
- G. Cotella, J. Baker, D. Worsley, F. De Rossi, C. Pleydell-Pearce, M. Carnie and T. Watson, Sol. Energy Mater. Sol. Cells, 2017, 159, 362–369 CrossRef CAS.
- W.-C. Chang, D.-H. Lan, K.-M. Lee, X.-F. Wang and C.-L. Liu, ChemSusChem, 2017, 10, 1405–1412 CrossRef CAS PubMed.
- S. C. Hong, G. Lee, K. Ha, J. Yoon, N. Ahn, W. Cho, M. Park and M. Choi, ACS Appl. Mater. Interfaces, 2017, 9, 7879–7884 CrossRef CAS.
- S.-G. Li, K.-J. Jiang, M.-J. Su, X.-P. Cui, J.-H. Huang, Q.-Q. Zhang, X.-Q. Zhou, L.-M. Yang and Y.-L. Song, J. Mater. Chem. A, 2015, 3, 9092–9097 RSC.
- F. Mathies, H. Eggers, B. S. Richards, G. Hernandez-Sosa, U. Lemmer and U. W. Paetzold, ACS Appl. Energy Mater., 2018, 1, 1834–1839 CrossRef CAS.
- A. Mei, X. Li, L. Liu, Z. Ku, T. Liu, Y. Rong, M. Xu, M. Hu, J. Chen, Y. Yang, M. Grätzel and H. Han, Science, 2014, 345, 295–298 CrossRef CAS.
- J.-W. Lee, S.-I. Na and S.-S. Kim, J. Power Sources, 2017, 339, 33–40 CrossRef CAS.
- L.-L. Gao, C.-X. Li, C.-J. Li and G.-J. Yang, J. Mater. Chem. A, 2017, 5, 1548–1557 RSC.
- J. Li, H. Wang, X. Y. Chin, H. A. Dewi, K. Vergeer, T. W. Goh, J. W. M. Lim, J. H. Lew, K. P. Loh and C. Soci, Joule, 2020, 4, 1035–1053 CrossRef CAS.
- I. Susic, L. Gil-Escrig, F. Palazon, M. Sessolo and H. J. Bolink, ACS Energy Lett., 2022, 7, 1355–1363 CrossRef CAS PubMed.
- B.-S. Kim, L. Gil-Escrig, M. Sessolo and H. J. Bolink, J. Phys. Chem. Lett., 2020, 11, 6852–6859 CrossRef CAS.
- E. Pérez-Gutiérrez, M. J. Percino, P. Santos, M. Cerón, P. Ceballos, D. M. Montoya, O. Barbosa-García and S. Thamotharan, Mater. Today Commun., 2020, 25, 101384 CrossRef.
- A. M. Igual-Muñoz, A. Castillo, C. Dreessen, P. P. Boix and H. J. Bolink, ACS Appl. Energy Mater., 2020, 3, 2755–2761 CrossRef.
- L. Gil-Escrig, C. Dreessen, F. Palazon, Z. Hawash, E. Moons, S. Albrecht, M. Sessolo and H. J. Bolink, ACS Energy Lett., 2021, 6, 827–836 Search PubMed.
- C. Momblona, L. Gil-Escrig, E. Bandiello, E. M. Hutter, M. Sessolo, K. Lederer, J. Blochwitz-Nimoth and H. J. Bolink, Energy Environ. Sci., 2016, 9, 3456–3463 RSC.
- C. Zhang, X. Ren, X. He, Y. Zhang, Y. Liu, J. Feng, F. Gao, N. Yuan, J. Ding and S. Liu, J. Energy Chem., 2022, 64, 8–15 CrossRef CAS.
- H. Li, J. Zhou, L. Tan, M. Li, C. Jiang, S. Wang, X. Zhao, Y. Liu, Y. Zhang, Y. Ye, W. Tress and C. Yi, Sci. Adv., 2022, 8, eabo7422 CrossRef PubMed.
- C. Dreessen, K. P. S. Zanoni, L. Gil-Escrig, N. Rodkey, J. I. Khan, F. Laquai, M. Sessolo, C. Roldán-Carmona and H. J. Bolink, Adv. Opt. Mater., 2024, 12, 2301019 CrossRef CAS.
- X. Y. Chin, D. Turkay, J. A. Steele, S. Tabean, S. Eswara, M. Mensi, P. Fiala, C. M. Wolff, A. Paracchino, K. Artuk, D. Jacobs, Q. Guesnay, F. Sahli, G. Andreatta, M. Boccard, Q. Jeangros and C. Ballif, Science, 2023, 381, 59–63 CrossRef CAS.
- Y. Li, H. Xie, E. L. Lim, A. Hagfeldt and D. Bi, Adv. Energy Mater., 2022, 12, 2102730 CrossRef CAS.
- F. Zhang and K. Zhu, Adv. Energy Mater., 2020, 10, 1902579 CrossRef CAS.
- W. Yu, X. Sun, M. Xiao, T. Hou, X. Liu, B. Zheng, H. Yu, M. Zhang, Y. Huang and X. Hao, Nano Res., 2022, 15, 85–103 CrossRef CAS.
- D. Bogachuk, P. van der Windt, L. Wagner, D. Martineau, S. Narbey, A. Verma, J. Lim, S. Zouhair, M. Kohlstädt, A. Hinsch, S. D. Stranks, U. Würfel and S. W. Glunz, ACS Sustainable Resour. Manage., 2024, 1, 417–426 CrossRef CAS.
-
S. Weckend, A. Wade and G. A. Heath, End of life management: solar photovoltaic panels, National Renewable Energy Lab.(NREL), Golden, CO (United States), 2016 Search PubMed.
- M. S. Chowdhury, K. S. Rahman, T. Chowdhury, N. Nuthammachot, K. Techato, M. Akhtaruzzaman, S. K. Tiong, K. Sopian and N. Amin, Energy Strategy Rev., 2020, 27, 100431 CrossRef.
- D. Sica, O. Malandrino, S. Supino, M. Testa and M. C. Lucchetti, Renewable Sustainable Energy Rev., 2018, 82, 2934–2945 CrossRef.
- S. Salhofer, B. Steuer, R. Ramusch and P. Beigl, Waste Manage., 2016, 57, 27–35 CrossRef CAS PubMed.
- X. Zeng, R. Gong, W.-Q. Chen and J. Li, Environ. Sci. Technol., 2016, 50, 1347–1358 CrossRef CAS PubMed.
- N. Moody, S. Sesena, D. W. deQuilettes, B. D. Dou, R. Swartwout, J. T. Buchman, A. Johnson, U. Eze, R. Brenes and M. Johnston, Joule, 2020, 4, 970–974 CrossRef.
- M. Tao, V. Fthenakis, B. Ebin, B.-M. Steenari, E. Butler, P. Sinha, R. Corkish, K. Wambach and E. S. Simon, Prog. Photovoltaics Res. Appl., 2020, 28, 1077–1088 CrossRef CAS.
- G. Rodriguez-Garcia, E. Aydin, S. De Wolf, B. Carlson, J. Kellar and I. Celik, ACS Sustainable Chem. Eng., 2021, 9, 15239–15248 CrossRef CAS.
- E. McCalmont, A. Ravilla, T. O’Hara, B. Carlson, J. Kellar and I. Celik, MRS Adv., 2023, 8, 317–322 CrossRef CAS.
- L. Huang, Z. Hu, J. Xu, X. Sun, Y. Du, J. Ni, H. Cai, J. Li and J. Zhang, Sol. Energy Mater. Sol. Cells, 2016, 152, 118–124 CrossRef CAS.
- L. Huang, J. Xu, X. Sun, R. Xu, Y. Du, J. Ni, H. Cai, J. Li, Z. Hu and J. Zhang, ACS Sustainable Chem. Eng., 2017, 5, 3261–3269 CrossRef CAS.
- W. Zhu, W. Chai, D. Chen, H. Xi, D. Chen, J. Chang, J. Zhang, C. Zhang and Y. Hao, ACS Appl. Mater. Interfaces, 2020, 12, 4549–4557 CrossRef CAS PubMed.
- B. Augustine, K. Remes, G. S. Lorite, J. Varghese and T. Fabritius, Sol. Energy Mater. Sol. Cells, 2019, 194, 74–82 CrossRef CAS.
- A. K. Jena, Y. Numata, M. Ikegami and T. Miyasaka, J. Mater. Chem. A, 2018, 6, 2219–2230 RSC.
- J. Xu, Z. Hu, L. Huang, X. Huang, X. Jia, J. Zhang, J. Zhang and Y. Zhu, Prog. Photovoltaics Res. Appl., 2017, 25, 1022–1033 CrossRef CAS.
- A. Binek, M. L. Petrus, N. Huber, H. Bristow, Y. Hu, T. Bein and P. Docampo, ACS Appl. Mater. Interfaces, 2016, 8, 12881–12886 CrossRef CAS PubMed.
- S. Zhang, L. Shen, M. Huang, Y. Yu, L. Lei, J. Shao, Q. Zhao, Z. Wu, J. Wang and S. Yang, ACS Sustainable Chem. Eng., 2018, 6, 7558–7564 CrossRef CAS.
- X. Feng, Q. Guo, J. Xiu, Z. Ying, K. W. Ng, L. Huang, S. Wang, H. Pan, Z. Tang and Z. He, Cell Rep. Phys. Sci., 2021, 2, 100341 CrossRef CAS.
- C. G. Poll, G. W. Nelson, D. M. Pickup, A. V. Chadwick, D. J. Riley and D. J. Payne, Green Chem., 2016, 18, 2946–2955 RSC.
- S. Y. Park, J.-S. Park, B. J. Kim, H. Lee, A. Walsh, K. Zhu, D. H. Kim and H. S. Jung, Nat. Sustain., 2020, 3, 1044–1051 CrossRef.
- B. J. Kim, D. H. Kim, S. L. Kwon, S. Y. Park, Z. Li, K. Zhu and H. S. Jung, Nat. Commun., 2016, 7, 11735 CrossRef CAS PubMed.
- J. M. Kadro, N. Pellet, F. Giordano, A. Ulianov, O. Müntener, J. Maier, M. Grätzel and A. Hagfeldt, Energy Environ. Sci., 2016, 9, 3172–3179 RSC.
- M.-H. Li, Y.-S. Yang, K.-C. Wang, Y.-H. Chiang, P.-S. Shen, W.-C. Lai, T.-F. Guo and P. Chen, ACS Appl. Mater. Interfaces, 2017, 9, 41845–41854 CrossRef CAS.
- B. Chen, C. Fei, S. Chen, H. Gu, X. Xiao and J. Huang, Nat. Commun., 2021, 12, 5859 CrossRef CAS.
- I. Celik, Z. Song, A. J. Cimaroli, Y. Yan, M. J. Heben and D. Apul, Sol. Energy Mater. Sol. Cells, 2016, 156, 157–169 CrossRef CAS.
- I. Celik, A. B. Philips, Z. Song, Y. Yan, R. J. Ellingson, M. J. Heben and D. Apul, IEEE J. Photovolt., 2018, 8, 305–309 Search PubMed.
- I. Celik, A. B. Phillips, Z. Song, Y. Yan, R. J. Ellingson, M. J. Heben and D. Apul, Energy Environ. Sci., 2017, 10, 1874–1884 RSC.
- M. Hauck, T. Ligthart, M. Schaap, E. Boukris and D. Brouwer, Renewable Energy, 2017, 111, 906–913 CrossRef CAS.
- X. Tian, S. D. Stranks and F. You, Sci. Adv., 2020, 6, eabb0055 CrossRef CAS PubMed.
- L. Serrano-Lujan, N. Espinosa, T. T. Larsen-Olsen, J. Abad, A. Urbina and F. C. Krebs, Adv. Energy Mater., 2015, 5, 1501119 CrossRef.
- J.-A. Alberola-Borràs, J. A. Baker, F. De Rossi, R. Vidal, D. Beynon, K. E. A. Hooper, T. M. Watson and I. Mora-Seró, iScience, 2018, 9, 542–551 CrossRef.
- E. Leccisi and V. Fthenakis, Prog. Energy, 2020, 2, 032002 CrossRef.
- E. Leccisi, A. Lorenz and V. Fthenakis, IEEE J. Photovolt., 2023, 13, 16–21 Search PubMed.
- S. Chaosukho, S. Meeklinhom, S. Rodbuntum, N. Sukgorn, A. Kaewprajak, P. Kumnorkaew and V. Varabuntoonvit, Environ. Impact Assess. Rev., 2024, 106, 107462 CrossRef.
- Q. Li, C. Monticelli and A. Zanelli, Renewable Energy, 2022, 195, 906–917 CrossRef CAS.
- T. Okoroafor, A. Maalouf, S. Oez, V. Babu, B. Wilk and S. Resalati, J. Cleaner Prod., 2022, 373, 133665 CrossRef CAS.
- Z. Wu, M. Sytnyk, J. Zhang, G. Babayeva, C. Kupfer, J. Hu, S. Arnold, J. Hauch, C. Brabec and I. M. Peters, Energy Environ. Sci., 2024, 17, 4248–4262 RSC.
- R. Vidal, J.-A. Alberola-Borràs, S. N. Habisreutinger, J.-L. Gimeno-Molina, D. T. Moore, T. H. Schloemer, I. Mora-Seró, J. J. Berry and J. M. Luther, Nat. Sustain., 2021, 4, 277–285 CrossRef.
- H. J. Kim, Y. J. Kim, G. S. Han and H. S. Jung, Sol. RRL, 2024, 8, 2300910 CrossRef CAS.
- M. B. Faheem, B. Khan, C. Feng, S. B. Ahmed, J. Jiang, M.-U. Rehman, W. S. Subhani, M. U. Farooq, J. Nie, M. M. Makhlouf and Q. Qiao, ACS Appl. Mater. Interfaces, 2022, 14, 6894–6905 CrossRef CAS PubMed.
- M. K. van der Hulst, D. Magoss, Y. Massop, S. Veenstra, N. van Loon, I. Dogan, G. Coletti, M. Theelen, S. Hoeks, M. A. J. Huijbregts, R. van Zelm and M. Hauck, ACS Sustainable Chem. Eng., 2024, 12, 8860–8870 CrossRef CAS PubMed.
- J. Gong, S. B. Darling and F. You, Energy Environ. Sci., 2015, 8, 1953–1968 RSC.
- C. Zhang, X. Zhao, R. Sacchi and F. You, Nat. Commun., 2023, 14, 1616 CrossRef CAS.
- J. Gao and F. You, ACS Sustainable Chem. Eng., 2018, 6, 11734–11752 CrossRef CAS.
- IIASA, Shared Socioeconomic Pathways Database Version 2.0, https://tntcat.iiasa.ac.at/SspDb/dsd?Action=htmlpage&page=about, (accessed Jun 13th, 2023).
- IPCC, IPCC Sixth Assessment Report, https://www.ipcc.ch/assessment-report/ar6/, (accessed Jun 13th, 2023).
- H. M. Wikoff, S. B. Reese and M. O. Reese, Joule, 2022, 6, 1710–1725 CrossRef CAS.
- H. Liang and F. You, Nat. Commun., 2023, 14, 1274 CrossRef CAS PubMed.
- I. Mathews, S. Sofia, E. Ma, J. Jean, H. S. Laine, S. C. Siah, T. Buonassisi and I. M. Peters, Joule, 2020, 4, 822–839 CrossRef.
-
R. Frischknecht, R. Itten, P. Sinha, M. de Wild-Scholten, J. Zhang, V. Fthenakis, H. Kim, M. Raugei and M. Stucki, International Energy Agency (IEA) PVPS Task 12, Report T12, 2015.
- J. Zhang, A. Knizley and H. Cho, AIMS Energy, 2017, 5, 974–996 Search PubMed.
- D. Wen, W. Gao, F. Qian, Q. Gu and J. Ren, Energy Explor. Exploit., 2021, 39, 1429–1456 CrossRef.
- U.S. EIA, During 2021, U.S. retail electricity prices rose at fastest rate since 2008, https://www.eia.gov/todayinenergy/detail.php?id=51438#:~:text=In%202021%2C%20the%20average%20nominal,our%20latest%20Electric%20Power%20Monthly., (accessed May 1st, 2023).
- C. Costello, L. Cao, S. Gelcich, M. Á. Cisneros-Mata, C. M. Free, H. E. Froehlich, C. D. Golden, G. Ishimura, J. Maier, I. Macadam-Somer, T. Mangin, M. C. Melnychuk, M. Miyahara, C. L. de Moor, R. Naylor, L. Nøstbakken, E. Ojea, E. O’Reilly, A. M. Parma, A. J. Plantinga, S. H. Thilsted and J. Lubchenco, Nature, 2020, 588, 95–100 CrossRef CAS PubMed.
- D.-J. van de Ven, I. Capellan-Peréz, I. Arto, I. Cazcarro, C. de Castro, P. Patel and M. Gonzalez-Eguino, Sci. Rep., 2021, 11, 2907 CrossRef CAS.
- NREL, Growing Plants, Power, and Partnerships Through Agrivoltaics, https://www.nrel.gov/news/program/2022/growing-plants-power-and-partnerships.html, (accessed Apr 15th, 2023).
- NREL, Benefits of Agrivoltaics Across the Food-Energy-Water Nexus, https://www.nrel.gov/news/program/2019/benefits-of-agrivoltaics-across-the-food-energy-water-nexus.html, (accessed Jun 13th, 2023).
- Colorado Energy Research Collaboratory, The Potential of Agrivoltaics: Research to Real Life, https://cercsymposium.org/the-potential-of-agrivoltaics-research-to-real-life/, (accessed Jun 11th, 2023).
- G. A. Barron-Gafford, M. A. Pavao-Zuckerman, R. L. Minor, L. F. Sutter, I. Barnett-Moreno, D. T. Blackett, M. Thompson, K. Dimond, A. K. Gerlak, G. P. Nabhan and J. E. Macknick, Nat. Sustain., 2019, 2, 848–855 CrossRef.
- L. J. Walston, T. Barley, I. Bhandari, B. Campbell, J. McCall, H. M. Hartmann and A. G. Dolezal, Front. Sustain. Food Syst., 2022, 6, 932018 CrossRef.
- K. Lee, N. Kim, K. Kim, H.-D. Um, W. Jin, D. Choi, J. Park, K. J. Park, S. Lee and K. Seo, Joule, 2020, 4, 235–246 CrossRef CAS.
- R. Meitzner, U. S. Schubert and H. Hoppe, Adv. Energy Mater., 2021, 11, 2002551 CrossRef CAS.
- S. Rahmany and L. Etgar, ACS Energy Lett., 2020, 5, 1519–1531 CrossRef CAS.
- S. Aharon, M. Layani, B.-E. Cohen, E. Shukrun, S. Magdassi and L. Etgar, Adv. Mater. Interfaces, 2015, 2, 1500118 CrossRef.
- S. Rahmany, M. Layani, S. Magdassi and L. Etgar, Sustainable Energy Fuels, 2017, 1, 2120–2127 RSC.
- M. Rai, S. Rahmany, S. S. Lim, S. Magdassi, L. H. Wong and L. Etgar, J. Mater. Chem. A, 2018, 6, 23787–23796 RSC.
- Y. Zhao, Z. Li, C. Deger, M. Wang, M. Peric, Y. Yin, D. Meng, W. Yang, X. Wang, Q. Xing, B. Chang, E. G. Scott, Y. Zhou, E. Zhang, R. Zheng, J. Bian, Y. Shi, I. Yavuz, K.-H. Wei, K. N. Houk and Y. Yang, Nat. Sustain., 2023, 6, 539–548 CrossRef.
- S. A. Khalifa, S. Spatari, A. T. Fafarman, V. M. Fthenakis, P. L. Gurian, M. S. Olson and J. B. Baxter, Environ. Sci. Technol., 2023, 57, 5190–5202 CrossRef CAS.
- P. Billen, E. Leccisi, S. Dastidar, S. Li, L. Lobaton, S. Spatari, A. T. Fafarman, V. M. Fthenakis and J. B. Baxter, Energy, 2019, 166, 1089–1096 CrossRef CAS.
- Y. Jiang, L. Qiu, E. J. Juarez-Perez, L. K. Ono, Z. Hu, Z. Liu, Z. Wu, L. Meng, Q. Wang and Y. Qi, Nat. Energy, 2019, 4, 585–593 CrossRef CAS.
- X. Li, F. Zhang, H. He, J. J. Berry, K. Zhu and T. Xu, Nature, 2020, 578, 555–558 CrossRef CAS PubMed.
- F. Körte, C. D. Wessendorf, T. Schnabel, M. Herrmann, B. Schröppel, K. Stadelmann, E. Arefaine, L. Busch, R. Daum, E. Ahlswede and H. Hartmann, RSC Adv., 2022, 12, 34381–34392 RSC.
|
This journal is © The Royal Society of Chemistry 2025 |
Click here to see how this site uses Cookies. View our privacy policy here.