DOI:
10.1039/D4MH01305K
(Communication)
Mater. Horiz., 2025,
12, 284-292
Remarkably boosted high-temperature energy storage of a polymer dielectric induced by polymethylsesquioxane microspheres†
Received
21st September 2024
, Accepted 22nd October 2024
First published on 29th October 2024
Abstract
Polymer dielectrics are the key materials in next-generation electrical power systems. However, they usually suffer from dramatic deterioration of capacitive performance at high temperatures. In this work, we demonstrate that polymethylsesquioxane (PMSQ) microspheres with a unique organic–inorganic hybrid structure can remarkably enhance the energy storage performance of a typical high-temperature dielectric polymer polyetherimide (PEI). Compared with traditional ceramic fillers, there exists –CH3 on the surface of PMSQ microspheres, which results in good compatibility between PMSQ and PEI. In addition, the PMSQ microspheres with excellent insulating properties can effectively block the charge transport, yielding significantly enhanced breakdown and energy storage performance. Consequently, the PEI based composite film with 5 wt% PMSQ microspheres exhibits ultrahigh energy storage densities of 12.83 J cm−3 and 9.40 J cm−3 with an efficiency (η) above 90% at 150 °C and 200 °C, respectively, which are 10.5 and 50.5 times those of the pure PEI film. This work demonstrates that microspheres with an organic–inorganic hybrid structure are excellent candidates for enhancing the high-temperature performance of polymer dielectrics, and these PMSQ/PEI composite films have huge potential for application in high-temperature film capacitors.
New concepts
In this work, we demonstrate that polymethylsesquioxane (PMSQ) microspheres with a unique organic–inorganic hybrid structure can remarkably enhance the energy storage performance of typical high-temperature dielectric polymer polyetherimide (PEI). PMSQ is an organosilicon compound microsphere, whose special molecular-scale organic–inorganic hybrid structure having a methyl group (–CH3) and silicon–oxygen (Si–O) bonds endows it with both good adaptability with a polymer matrix and great insulation, respectively. PMSQ microspheres could not only block the carriers, but also improve the mechanical strength of the composite film. This work demonstrates that microspheres with an organic–inorganic hybrid structure are excellent candidates for enhancing the high-temperature performance of polymer dielectrics, and these PMSQ/PEI composite films have huge potential for application in high-temperature film capacitors.
|
1. Introduction
Commercial energy storage devices mainly include fuel cells, chemical batteries, supercapacitors and dielectric capacitors. Compared with batteries, dielectric capacitors have the characteristics of high electric field and high power density which are suitable for equipment that needs to release a large amount of electrical energy in a short time, e.g., hybrid electric vehicles, wind turbine generators, and electromagnetic weaponry.1–5 Dielectric capacitors can be divided into ceramic capacitors and polymer capacitors. While dielectric materials of capacitors can be inorganics, polymers are preferred due to their flexibility, light weightness, cost-effective processability, and, most of all, their voltage scalability and graceful failure mode, which prevents any abrupt failure.6–9 The discharge energy density (Ue) of linear polymer dielectric materials can be calculated using:10,11 |  | (1) |
here, ε0, εr, and Eb refer to the vacuum dielectric constant, relative dielectric constant, and breakdown field strength, respectively. An excellent energy density simultaneously demands for a higher dielectric constant and larger breakdown field strength. In particular, Ue and Eb have a quadratic relationship, and an increase in Eb will significantly optimize the storage energy density, which is also conducive to tolerating ripple voltage and improving the safe operation of capacitors.12,13
Nowadays, dielectric materials with excellent high-temperature capacitive properties are in great demand because of the heat inevitably generated by compact high-power electronic systems.14–16 For example, the operating temperature of capacitors is 140–150 °C in green-energy vehicle inverters and reaches 200 °C in electrified aircraft. Currently, the most common commercially used dielectric polymer is the biaxially oriented polypropylene (BOPP). Unfortunately, BOPP can continuously operate only below 85 °C.17,18 The conductivity of the BOPP film increases rapidly by approximately three orders of magnitude when the temperature increases from room temperature to 150 °C, accordingly giving rise to an exponential increase in conduction loss. Therefore, there is an urgent need for a new generation of polymer dielectric capacitors that can work stably and exhibit excellent energy storage density at high temperatures.
One of the most effective ways is to add ceramic fillers to construct ceramic/polymer composites.19–21 The conduction loss in a polymer dielectric at high temperatures and electric fields is commonly determined by Schottky emission and hopping conduction.22 The Schottky emission occurs at the interface between a metal electrode and a dielectric surface, where the energized electrons in the metal electrode at high temperature and electric field can overcome the energy barrier and inject into the polymer dielectric. The hopping conduction occurs inside the bulk phase of polymer dielectrics, where the trapped charge carriers are thermally activated and thereby jump from one trap site to another inside polymer dielectrics due to the tunneling effect. Adding inorganic fillers with a wide bandgap, such as silicon oxide (SiO2), boron nitride (BNs), and aluminum oxide (Al2O3) in polymer dielectrics can effectively increase the barrier height and suppress the charge injection, accordingly leading to a reduction in conduction loss and enhancement of high-temperature capacitive performance.23–25 For example, Li et al. added BNNS into the c-BCB matrix.26 Finally, c-BCBs filled with 10 vol% of BN displayed a 50% increase of Eb at an extremely high temperature of 250 °C and a high Ue (≈4 J cm−3) at 150 °C is achieved. However, the interfaces in polymer composites consist of either organic or inorganic components, and achieving a good interfacial match between these phases is often challenging. This mismatched interface leads to weak combination between the polymers and the fillers, resulting in inevitable defects that hinder further improvements in the energy storage properties. In recent years, many researchers have focused on the surface modification of inorganic fillers to improve their adaptability with a polymer matrix. For example, a distinctive “metal-ion organic hybrid interface” (MOHI) between polyimide (PI) and calcium niobate (CNO) nanosheets is designed by Liu et al.27 The metal ions in the MOHI can achieve atomic-level matching not only with the inorganic CNO, but also with the PI chains, forming uniform and strong chemical bonds. Finally, the energy storage densities (Ue) of the composite dielectric reach 4.75 J cm−3 with an energy storage efficiency (η) of 90% at 150 °C. Although the surface modification can improve the adaptability of the interface between the inorganic fillers and polymer, it usually involves complicated chemical reactions. Therefore, organic fillers with heat tolerance properties and high insulation could be promising candidates for polymer dielectric composites.
To address the aforementioned challenges of ceramic/polymer composites, we made a composite film consisting of polyetherimide (PEI) and (polymethylsesquioxane) PMSQ microspheres. PEI is a thermoplastically engineered polymer in which the ether unit provides the mechanical flexibility and fluidity of the molecular chain, and the aromalimide unit enhances the thermal resistance and mechanical strength. PMSQ is an organosilicon compound microsphere, whose special molecular-scale organic–inorganic hybrid structure having a methyl group (–CH3) and silicon–oxygen (Si–O) bonds endows it with both good adaptability with a polymer matrix and great insulation, respectively (Fig. S1, ESI†).28,29 PMSQ microspheres could not only block the carriers, but also improve the mechanical strength of the composite film. The PMSQ/PEI composite film exhibits superior high-temperature capacitive performance with discharge energy densities of 12.84 J cm−3 and 9.40 J cm−3 at 150 °C and 200 °C with energy storage efficiency (η) above 90%, respectively, far outperforming those of the currently existing polymer dielectrics at high temperatures.
2. Results and discussion
A PMSQ/PEI composite film is fabricated by blending and casting and its schematic is shown in Fig. 1a. The resulting films with varied content of PMSQ are denoted as x wt% PMSQ/PEI, where x represents the mass fraction of PMSQ microspheres. Fig. 1(b and c) present the surface and cross-sectional SEM images of the composite film with 5 wt% PMSQ. As can be seen, PMSQ microspheres are evenly dispersed in the PEI matrix without any agglomeration or bubbles and the thickness of the composite film is about 10 μm. One reason is that –CH3 on the surface of PMSQ microspheres could increase the lubricity. The other is that the size of PMSQ is big and the surface energy of the microsphere is low. The average size of PMSQ is about 1.2 μm. The Si element is accurately dispersed in PMSQ microspheres as seen in energy-dispersive X-ray spectroscopy (EDS) elemental mapping (Fig. 1c and Fig. S2, ESI†). With the increase of the number of microspheres, the PMSQ microspheres have a tendency to agglomerate themselves (Fig. S3, ESI†). Chemical structures of composite films and PMSQ microspheres were examined by Fourier transform infrared spectroscopy (FTIR), and the characteristic absorption peaks of the composite film and PMSQ can be observed (Fig. 1d). It should be noted that the peaks at 763 cm−1, 1001 cm−1, and 1271 cm−1 corresponding to PMSQ become more obvious in the PMSQ/PEI composite film with the increasing amount of PMSQ and there are no other peaks generated which confirm that there occur no other chemical reactions after adding PMSQ microspheres into PEI. Furthermore, PMSQ can also improve the mechanical strength of the PEI film. As shown in Fig. 1e, compared with the pure PEI film, there are no pleats in the composite film which ensures its steady morphology in a high-temperature environment.
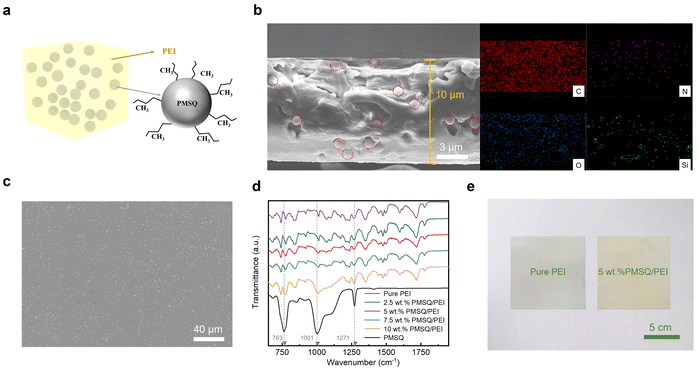 |
| Fig. 1 (a) Schematic diagram of the PMSQ/PEI composite film; (b) cross-sectional scanning electron microscopy (SEM) images and the energy dispersive spectra (EDS) of the 5 wt% PMSQ/PEI film; (c) SEM images of the surface morphologies of the 5 wt% PMSQ/PEI film; (d) FT-IR spectra of the pure PEI film and PMSQ/PEI composite films; and (e) the optical photograph of the pure PEI film and the 5 wt% PMSQ/PEI composite film. | |
To evaluate the effect of PMSQ on the dielectric performances of the composites, the dielectric constant (εr) and loss (tan
δ) of the composite films are shown in Fig. 2(a and b). Generally speaking, the dielectric loss of a composite film will increase after adding inorganic fillers because of the incompatibility between the polymer matrix and fillers. However, the composite film presents significantly suppressed tan
δ compared with the pure PEI film which contributes to the excellent compatibility and the redistribution of the electric field in the interface of PMSQ and the PEI matrix. The reduced dielectric constant could be mainly attributed to the intrinsic low dielectric constant of PMSQ (εr EI2–3). Besides, the dielectric loss increases with increasing temperature which can be attributed to the increasing relaxation time of polymer molecular chains in a high-temperature environment. The addition of rigid PMSQ can improve the mechanical strength of the film to reduce the thermal expansion coefficient of the film and decrease the relaxation time of polymer molecular chains. According to the formula (1), breakdown strength is a critical parameter that determines the energy storage densities of the film. The breakdown properties of the composite films with different amounts of PMSQ were further analyzed using a two-parameter Weibull statistic distribution function (Fig. S4, ESI†), expressed as follows:
| 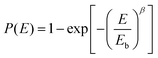 | (2) |
where
P(
E) denotes the cumulative probability of electric failure,
E is the measured electric field,
Eb is the breakdown strength at a cumulative failure probability of 63.2%, and
β epresents the shape parameter that evaluates the scatter of the breakdown data. As shown in
Fig. 2c,
Eb of the PMSQ/PEI film increased from 501 MV m
−1 (150 °C) and 449 MV m
−1 (200 °C) for the pure PEI film to 831 MV m
−1 (150 °C) and 712 MV m
−1 (200 °C) for the 5 wt% PMSQ/PEI film. In addition, the 5 wt% PMSQ/PEI film exhibited the highest
β among all the obtained films. The highly insulating PMSQ microspheres can effectively interdict the current channels generated by the interfacial charge carriers, thus enhancing the
Eb of the composites. Moreover, the smooth surface with –CH
3 of the filler may decrease the interfacial structural defects in the composites, alleviating the possibility of breakdown at the defects. With the increase of PMSQ microspheres, the breakdown strength (
Eb) of the films firstly increases and then decreases. The reason is that an overdose of PMSQ microspheres will lead to agglomeration of themselves, which will cause the local electric field distortion to create a channel through which electrons can easily pass through. Meanwhile, the leakage current density of the PMSQ/PEI film is greatly suppressed which also confirms the high
Eb of composites. The variation trend of leakage current density are opposite to that of breakdown strength (Fig. S5, ESI
†). With the increase of the filler content, it first decreases and then increases. As the temperature increases, the advantages of the PMSQ filler are fully reflected. The current density of the 5 wt% PMSQ/PEI composites at 200 °C was only 36% that of the PEI film. To better understand the remarkably improved
Eb, stress–strain curves of the films are displayed in Fig. S6 (ESI
†). Young's modulus provides a fast and effective assessment of how much coulombic force a material can withstand. Because coulomb forces are generated between the opposite positive and negative electrodes under an external electric field. The higher modulus indicates that the films can withstand higher coulomb forces under an applied electric field, thus protecting the dielectric material from electromechanical failures. According to Stark and Garton's theory, the theoretical
Eb is almost proportional to the root of Young's modulus:
30 | 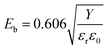 | (3) |
where
Y represents Young's modulus. With the increase of the filler content, Young's modulus first increases and then decreases. As shown in
Fig. 2d, the 5 wt% PMSQ/PEI film exhibits the maximum Young's modulus of 27.19 MPa, which is 168% that of the pure PEI film. This agrees well with the aforementioned results that the 5 wt% PMSQ/PEI film possesses the highest
Eb. To gain further insights into the impact of the PMSQ microspheres on the breakdown behavior of the polymer composite films, finite element simulations are conducted. The simulation models of the pure PEI film and PMSQ/PEI composite film were built based on their SEM images. The simulated electric field, polarization and leakage current distributions of these two models are shown in Fig. S7–S9 (ESI
†). The results indicate that the PMSQ microspheres could redistribute the electric field and leakage current to prevent the PEI matrix from bearing excessive electric stimuli. In addition, electrical tree simulations were also performed using a modified dielectric breakdown model (DBM) and the results are displayed in
Fig. 2e. Clearly, in contrast to the continuous development of the electrical tree in the pure PEI film, the electrical tree propagation is blocked by the PMSQ microspheres in the PMSQ/PEI composite film which can be attributed to the high insulation of PMSQ.
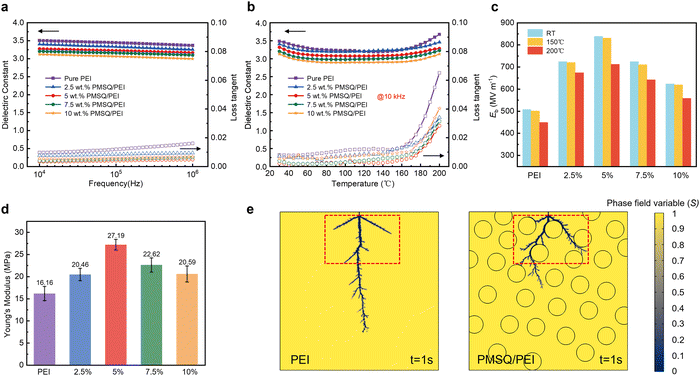 |
| Fig. 2 (a) Dielectric constant and dissipation factor as a function of frequency of the pure PEI film and PMSQ/PEI composite films at room temperature; (b) dielectric constant and dissipation factor as a function of temperature of the pure PEI film and PMSQ/PEI composite films at 10 kHz; (c) the breakdown strength of the pure PEI film and PMSQ/PEI composite films at room temperature, 150 °C and 200 °C; (d) Young's modulus of the PEI and composite films; and (e) simulated electrical tree propagation path of PEI and composite films. | |
Unipolar electric displacement-electric field (D–E) loops were used to characterize the energy storage performance of PEI and PMSQ/PEI films at different temperatures (Fig. S11–S14, ESI†). Compared with the pure PEI film, the PMSQ/PEI composite films exhibit a slimmer D–E loop and lower remanent polarization. As shown in Fig. 3a, the 5 wt% PMSQ/PEI film exhibits an excellent efficiency of 94.6% at 400 MV m−1 and 200 °C, which is much higher than that of the pure PEI film (75.3%). The energy loss of the pure PEI film growth is rapid at high electric fields while the PMSQ/PEI film maintains a high efficiency which was mainly attributed to the suppression of conduction loss by the PMSQ microspheres. The highly insulating PMSQ microspheres can effectively interdict the current channels generated by the charge carriers. Besides, the addition of PMSQ could improve the mechanical strength of the PEI film and maintain a good morphology in a high-temperature environment. Fig. 3(b–d) show the discharge energy densities (Ud) and discharge–charge efficiency (η) of the films at room temperature, 150 °C, and 200 °C under different electric fields, respectively. In agreement with the variation of breakdown strength with the amount of PMSQ, the films also show first an increase and then a decrease in Ud. The 5 wt% PMSQ/PEI film shows the highest discharge energy densities, for example, an Ud of 14.62 J cm−3 with a η of 93.4% at 830 MV m−1 and an Ud of 12.83 J cm−3 with a η of 90.6% at 830 MV m−1 and an Ud of 9.4 J cm−3 with a η of 90.7% at 710 MV m−1 are obtained at room temperature, 150 °C and 200 °C, respectively. In addition to Ue, the maximum discharge energy density above 90% charge–discharge efficiency (Ue90) is even more important for high-temperature energy storage. This is because an energy density achieved at low efficiencies (∼80% or lower) is inevitably accompanied by massive heat dissipation, and may cause thermal runaway of the device at high temperature that is close to the thermal limit of the material. As shown in Fig. 3e, at η ≥ 90%, the pure PEI film exhibits an Ud of 1.21 J cm−3 at 150 °C and 0.18 J cm−3 at 200 °C which are far below than those of the composite films with PMSQ microspheres. Accordingly, fast discharge-discharge tests were carried out to evaluate the power density of the composite film and pure PEI film. As shown in Fig. 3f and Fig. S15 (ESI†), at an applied electric field of 200 MV m−1, which is the working field of electrostatic capacitors in common power systems such as hybrid electric vehicles, the charge–discharge time of the 5 wt% PMSQ/PEI film is lower than that of the PEI film and displays a higher power density at different temperatures.
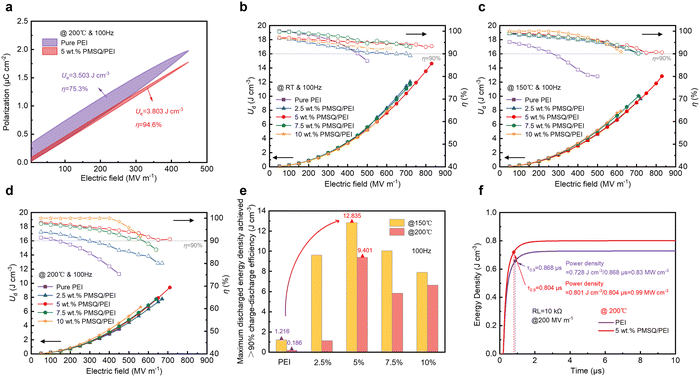 |
| Fig. 3 (a) The comparison of unipolar D–E loops of PEI and 5 wt% PMSQ/PEI films measured at 450 MV m−1 and 200 °C; discharge energy densities and charge–discharge efficiencies as a function of electric field for PEI and PMSQ/PEI composite films at (b) room temperature (c) 150 °C and (d) 200 °C; (e) maximum discharge energy density of the tested films with charging and discharging efficiency above 90%; and (f) variation of discharge energy density over time of pure PEI and 5 wt% PMSQ/PEI composite films. | |
In practical production, there are high requirements for the uniformity of film capacitors. To verify the potential of the composite film to form large-area high-quality films to address the bottleneck of scalable production, the Ud and η values of different regions are measured at 200 °C of a large composite film (Fig. 4a and Fig. S16, ESI†). All regions measured exhibit a high Ue over 9 J cm−3 and high efficiency exceeds 90% at 200 °C which shows a high homogeneity of the composite film. We know that stability is an important parameter for high-temperature applications. Therefore, we tested the film for 50
000 charge–discharge cycles at a high electric field and 200 °C (Fig. 4b and Fig. S17, ESI†). Consequently, at 400 MV m−1, the pure PEI film can operate only up to 1585 cycles at 200 °C. By contrast, Ud and η of 5 wt% the PMSQ/PEI film are highly stable during 50
000 continuous charge–discharge cycles at 200 °C. Compared with the pure PEI film, the D–E loops of the 5 wt% PMSQ/PEI composite film at different cycles are more stable and slimmer which further confirm its excellent Ue and η values and its potential for practical applications. Furthermore, the effect of the electrode area on the breakdown strength is also investigated. As displayed in Fig. 4c, a larger electrode area results in a decreased breakdown strength. As the electrode diameter increases from 3 to 17
mm, the retention of the characteristic breakdown strength of the PMSQ/PEI composite film is about 89% which is higher than that of the pure PEI film. It should be noted that, in practical applications, the operating frequency of film capacitors is usually fluctuating. Therefore, the consistency of the capacitive performance over different frequencies is particularly important. The main measurement frequencies in recent years are 10 Hz and 100 Hz. To verify the stability at different frequencies, we measured the capacitance performance of the 5 wt% PMSQ/PEI film at 10 Hz and 200 °C (Fig. 4d and Fig. S18, ESI†). The polarization of the film increases but η deteriorates rapidly with the decrease of the frequency. Finally, an Ud of 10.00 J cm−3 with a η of 84% at 710 MV m−1 is achieved at 10 Hz and 200 °C. At η ≥ 90%, the Ud of the composite film at 10 Hz is 6.27 J cm−3.
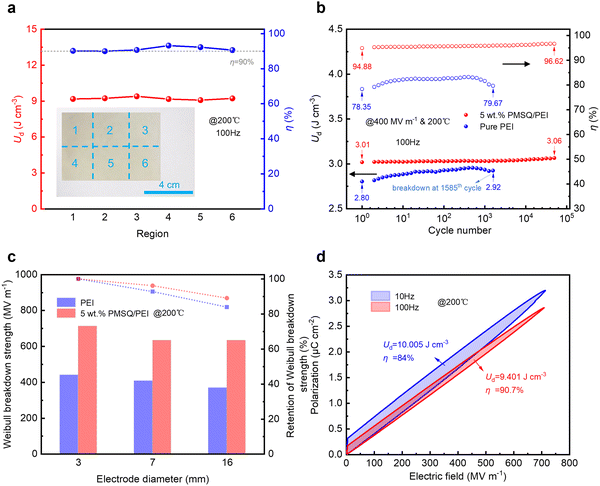 |
| Fig. 4 (a) Energy storage performances of different regions in the 5 wt% PMSQ/PEI film (as marked in the inset photograph) at 200 °C; (b) cycling performance of the 5 wt% PMSQ/PEI film and PEI film at 200 °C under 400 MV m−1; (c) the breakdown strength and retention rate of pure PEI and 5 wt% PMSQ/PEI films with different diameters of the electrode; and (d) D–E loops of the 5 wt% PMSQ/PEI film at different frequencies. | |
Finally, we compare the Ue90 of the 5 wt% PMSQ/PEI film with those of the recently reported studies (Fig. 5(a and b)).31–48 Obviously, Ue90 in this contribution exceeds most of the previously published results for PEI-based composites and other non-PEI dielectrics. The filler of the organic–inorganic hybrid structure in this contribution could be easily extended to other polymer dielectrics for the amelioration of high-temperature capacitive performance. Note that the material presented in this work is inexpensive and can be easily obtained commercially.
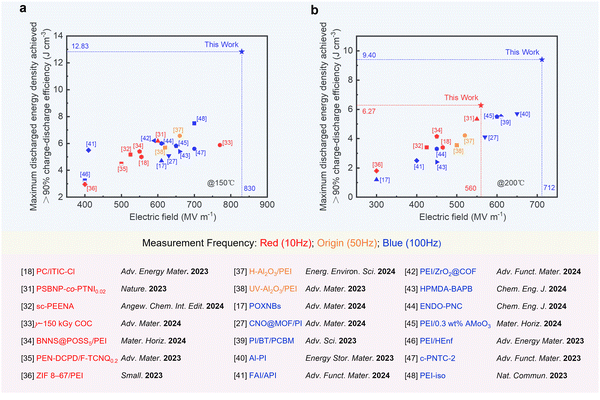 |
| Fig. 5 Property comparison of the high temperature dielectric materials at (a) 150 °C and (b) 200 °C. | |
3. Conclusions
In summary, a substantial improvement in high-temperature energy storage performance has been achieved by introducing PMSQ microspheres into a PEI dielectric. Our comprehensive experimental studies and simulation results demonstrate that PMSQ microspheres can effectively block the carriers and improve the mechanical strength of the film in a high-temperature environment. As a result, the presence of PMSQ leads to an improved electrical breakdown performance, as well as great enhancement of efficiency and suppression of loss. Finally, the PMSQ/PEI composite film delivers ultra-high discharge energy densities (Ue) of 14.62 J cm−3, 12.83 J cm−3 and 9.40 J cm−3 with an efficiency above 90% at room temperature, 150 °C and 200 °C, respectively, as high as 3.4 times, 10.5 times and 50.5 times those of the pure PEI film. More importantly, the 5 wt% PMSQ/PEI film displays excellent cycling stability and reliability even after 50
000 cycles. The above results cast new light on the design of high-temperature polymers, which establishes hybrid structures as a promising class of scalable dielectric materials for high temperature high-energy-density capacitors.
4. Experimental section
4.1 Materials
N-Methylpyrrolidone (NMP) was obtained from Sinopharm Chemical Reagent Co., Ltd. Polymethylsesquioxane (PMSQ) with an average size of 1.2 μm was purchased from Yuheng Technology (China). Polyetherimide (PEI) was purchased from poly-K (Amercian).
4.2 Preparation of the composite films
First, the NMP solution (5 mL) with PMSQ powder was ultrasound treated in ice water for 1 h. Then, the PEI pellets (1 g) were dissolved in the solution at 75 °C for 5 h under 200 rpm stirring. Subsequently, the solution was stirred overnight at room temperature with a rate of 100 rpm. Then, the solution was cast onto the glass plate using a doctor blade at a thickness of 10 μm. Finally, the solution was dried with a process: raise the room temperature to 100 °C which takes 70 min. Keep at 100 °C for 240 min. Raise the 100 °C to 200 °C which takes 50 min. Keep at 200 °C for 5 min.
4.3 Characterization and measurements
Surface morphology, cross-section morphology and energy dispersive spectra (EDS) of the modified films were observed with a Zeiss Gemini 300 scanning electron microscope. The microstructure of the films was characterized by FTIR-ATR (using a THS-108 instrument from 2200 to 500 cm−1). The dielectric constant and dielectric loss were obtained using an Agilent E4980A Precision LCR analyzer in the frequency range of 10 k Hz to 1 M Hz. The dielectric constant was calculated using εr = tCp/Aε0, where t is the thickness of the sample, Cp is the parallel capacitance, A is the area of the electrode, and ε0 is the absolute dielectric constant of free space (8.85 × 10−12 F m−1). The breakdown strength was tested using a machinery consisting of a Trek 610 C amplifier with a voltage ramping rate of 500 V s−1 at room temperature (PolyK Technologies, USA). Young's modulus was measured through a pharmaceutical packaging performance tester (Labthink, MED-01). The leakage current densities of the films under varied electric fields were measured using a source meter (2450, Keithley Instruments). The energy-storage performances were measured using the D–E loops which were collected at 10 Hz and100 Hz using a ferroelectric test system based on a modified Sawyer-Tower circuit (PolyK Technologies, USA). The fast charge–discharge performances were measured using a capacitor charge–discharge test system with a load resistor (RL) of 10 kΩ (PolyK Technologies, PA, USA). The electrode diameter is 3 mm unless otherwise mentioned.
4.4 Finite element phase field simulation
The simulation of the electric field and polarization distributions of the pure PEI film and PMSQ/PEI composite films was carried out using COMSOL. Simulation of breakdown paths was carried out using the weak form partial differential equations module. The total free energy functional of the system can be described as: |  | (4) |
where Wes(E, s) is the electrostatic energy density stored per unit volume of the medium, Wd(s) is the damage energy density, WC is the critical electrostatic energy density, Wi(∇s) is the gradient energy term and Γ is the approximate breakdown energy. f(s) is the interpolation function of the phase field variable (s), f(s) = 4s3 − 3s4, when s = 0, f(s) = 0, indicating that the material is broken down, and when s = 1, f(s) = 1, indicating that the material is complete. The dielectric constant is interpolated between the two extremes in any intermediate damage state, expressed by the following equation: | 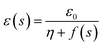 | (5) |
where η = 001. The time and electric potentials are normalized t = mΓ, φ = √(Γ/ε0/l) to obtain the governing equation in the dimensionless form, as shown in the following equation: | 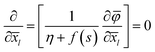 | (6) |
|  | (7) |
where t and φ represent the time and electric potential, respectively. All breakdown path simulations in this paper are implemented in a 2D model.
Author contributions
Zelong Chang: writing – original draft, writing – review and editing, formal analysis, conceptualization and methodology. Li Lei: supervision. Linwei Zhu: software. Yang Quan: validation. Zengliang Ren: investigation. Yihui Qian: visualization. Davoud Dastan: supervision. Zhicheng Shi: Resources, funding acquisition and writing – review and editing.
Data availability
The data supporting this study's findings are available from the corresponding author upon reasonable request.
Conflicts of interest
The authors declare that they have no known competing financial interests or personal relationships that could have appeared to influence the work reported in this paper.
Acknowledgements
This work was supported by the Project of Taishan Scholars (tsqn202306090), the Fundamental Research Funds for Central Universities (202241004), the Shandong Province Natural Science Foundation (ZR2021YQ39).
References
- T. D. Zhang, H. Sun, C. Yin, Y. H. Jung, S. Min, Y. Zhang, C. H. Zhang, Q. G. Chen, Q. J. Lee and Q. G. Chi, Prog. Mater. Sci., 2023, 140, 101207 CrossRef CAS
.
- J. R. Zhou, M. Dabaghian, Y. F. Wang, M. Sotzing, A. M. Lachance, K. Y. Shen, W. Q. Gao, A. Konstantinou, C. Wu, J. Hao, L. Y. Sun and Y. Cao, Nano Energy, 2024, 120, 109184 CrossRef CAS
.
- C. F. Yan, Y. T. Wan, H. P. Long, H. Luo, X. Liu, H. Luo and S. Chen, Adv. Funct. Mater., 2023, 34(8), 2312238 CrossRef
.
- Y. X. Zhang, D. F. Liu, X. Y. Wei, X. J. Wang, F. Y. Chen, Q. K. Feng, W. Y. Cao, W. Z. Dong, F. M. Shah, Y. X. Liu, Z. Y. Wu, J. T. Wang, S. L. Zhong and Z. M. Dang, IET Nanodielectrics, 2024, 7(2), 88–95 CrossRef
.
- Q. F. He, K. Sun, Z. C. Shi, Y. Liu and R. H. Fan, Mater. Today, 2023, 68, 298–333 CrossRef CAS
.
- Q. K. Feng, S. L. Zhong, J. Y. Pei, Y. Zhao, D. L. Zhang, D. F. Liu, Y. X. Zhang and Z. M. Dang, Chem. Rev., 2021, 122(3), 3820–3878 CrossRef
.
- B. H. Fan, M. Y. Zhou, C. Zhang, D. L. He and J. B. Bai, Prog. Polym. Sci., 2019, 97, 101143 CrossRef CAS
.
- M. Zhang, B. Li, J. J. Wang, H. B. Huang, L. Zhang and L. Q. Chen, Adv. Mater., 2021, 33(22), 2008198 CrossRef CAS
.
- H. Y. Zhu, X. H. Liu, H. R. Bai and T. Q. Yang, Chem. Eng. J., 2024, 479, 147572 CrossRef CAS
.
- Z. L. Ren, Z. C. Shi, Q. Y. Tang, S. M. Xia, L. Sun, R. H. Fan, H. Z. Cui and H. Wang, Adv. Funct. Mater., 2024, 2401907 CrossRef CAS
.
- B. Xie, T. T. Wang, J. X. Cai, Q. Y. Zheng, Z. Y. Liu, K. Guo, P. Mao, H. B. Zhang and S. L. Jiang, Chem. Eng. J., 2022, 434, 134659 CrossRef CAS
.
- H. Q. Wang, J. W. Wang, X. Z. Wang, X. H. Gao, G. C. Zhuang, J. B. Yang and H. Ren, Chem. Eng. J., 2022, 437(2), 135431 CrossRef CAS
.
- R. Guo, H. Luo, D. Zhai, Z. D. Xiao, H. R. Xie, Y. Liu, X. F. Zhou and D. Zhang, Chem. Eng. J., 2022, 437(2), 135497 CrossRef CAS
.
- Z. T. Meng, T. D. Zhang, C. H. Zhang, Y. N. Shang, Q. Q. Lei and Q. G. Chi, Adv. Mater., 2023, 2310272 CrossRef
.
- H. Li, Y. Zhou, Y. Liu, L. Li, Y. Liu and Q. Wang, Chem. Soc. Rev., 2021, 50(11), 6369–6400 RSC
.
- Z. Z. Pan, L. Li, L. N. Wang, G. F. Luo, X. W. Xu, F. Jin, J. F. Dong, Y. J. Niu, L. Sun, C. F. Guo, W. Q. Zhang, Q. Wang and H. Wang, Adv. Mater., 2022, 35(1), 2207580 CrossRef
.
- S. Shukla, C. Wu, A. Mishra, J. K. Pan, A. P. Charnay, A. Khomane, A. Deshmukh, J. R. Zhou, M. Mukherjee, R. Gurnani, P. Rout, R. Casalini, R. Ramprasad, M. D. Fayer, P. Vashishta, Y. Cao and G. Sotzing, Adv. Mater., 2024, 2402133 CrossRef
.
- Y. Zhou, Y. J. Zhu, W. H. Xu and Q. Wang, Adv. Energy Mater., 2023, 13(11), 2203961 CrossRef CAS
.
- M. Z. Yang, W. B. Ren, M. F. Guo and Y. Shen, Small, 2022, 18(50), 2205247 CrossRef CAS
.
- L. T. Li, J. F. Dong, R. C. Hu, X. Q. Chen, Y. J. Niu and H. Wang, Chem. Eng. J., 2022, 435(3), 135059 CrossRef CAS
.
- J. F. Dong, R. C. Hu, X. W. Xu, J. Chen, Y. J. Niu, F. Wang, J. Y. Hao, K. Wu, Q. Wang and H. Wang, Adv. Funct. Mater., 2021, 31(32), 2102644 CrossRef CAS
.
- J. W. Zha, M. Y. Xiao, B. Q. Wan, X. M. Wang, Z. M. Dang and G. Chen, Prog. Mater. Sci., 2023, 140, 101208 CrossRef CAS
.
- B. Z. Sun, P. H. Hu, X. M. Ji, M. Z. Fan, L. Zhou, M. F. Guo, S. He and Y. Shen, Small, 2022, 18(28), 2202421 CrossRef CAS PubMed
.
- K. Y. Zhang, Z. Y. Ma, H. Deng and Q. Fu, Adv. Compos. Hybrid Mater., 2021, 5(1), 238–249 CrossRef
.
- D. Ai, H. Li, Y. Zhou, L. L. Ren, Z. B. Han, B. Yao, W. Zhou, L. Zhao, J. M. Xu and Q. Wang, Adv. Energy Mater., 2020, 10(16), 1903881 CrossRef CAS
.
- Q. Li, L. Chen, M. R. Gadinski, S. H. Zhang, G. Z. Zhang, H. U. Li, E. Lagodkine, A. Haque, L. Q. Chen, T. N. Jackson and Q. Wang, Nature, 2016, 536(7614), 112 CrossRef CAS
.
- X. X. Liu, D. Y. Chen, J. L. Li, S. L. Zhong, Y. Feng, D. Yue, D. W. Sheng, H. N. Chen, X. D. Hao and Z. M. Dang, Adv. Mater., 2024, 36(28), 2402239 CrossRef CAS PubMed
.
- R. Ueoka, Y. Hara, A. Maeno, H. Kaji, K. Nakanishi and K. Kanamori, Nat. Commun., 2024, 15(1), 461 CrossRef CAS PubMed
.
- F. C. N. Hong and C. J. Yan, Adv. Powder Technol., 2017, 28(3), 1038–1046 CrossRef
.
- P. J. Wang, Y. Guo, D. Zhou, D. Li, L. X. Pang, W. F. Liu, J. Z. Su, Z. Q. Shi and S. K. Sun, Adv. Funct. Mater., 2022, 32(31), 2201455 Search PubMed
.
- J. Chen, Y. Zhou, X. Y. Huang, C. Y. Yu, D. L. Han, A. Wang, Y. K. Zhu, K. M. Shi, Q. Kang, P. L. Li, P. K. Jiang, X. S. Qian, H. Bao, S. T. Li, G. N. Wu, X. Y. Zhu and Q. Wang, Nature, 2023, 615, 62–66 CrossRef CAS PubMed
.
- W. H. Xu, C. Y. Zhou, W. H. Ji, Y. H. Zhang, Z. H. Jiang, F. Bertram, Y. S. Shang, H. B. Zhang and C. Shen, Angew. Chem., Int. Ed., 2024, 63(24), e202319766 CrossRef CAS
.
- Y. W. Wang, Z. W. Bao, S. Ding, J. H. Jia, Z. Z. Dai, Y. X. Li, S. C. Shen, S. C. Chu, Y. W. Yin and X. G. Li, Adv. Mater., 2024, 36, 2308597 CrossRef CAS
.
- Y. J. Zhou, Z. W. Zhang, Q. F. Tang, X. Y. Ma and X. Hou, Mater. Horiz., 2024, 11, 4348–4358 RSC
.
- J. Chen, Z. T. Pei, Y. J. Liu, K. M. Shi, Y. K. Zhu, Z. C. Zhang, P. K. Jiang and X. Y. Huang, Adv. Mater., 2023, 35(48), 2306562 CrossRef CAS
.
- F. Wang, J. M. Cai, C. C. Yang, H. Luo, X. N. Li, H. S. Hou, G. Q. Zou and D. Zhang, Small, 2023, 19(26), 2300510 CrossRef CAS
.
- M. H. Yang, Y. L. Zhao, Z. P. Wang, H. R. Yan, Z. R. Liu, Q. Li and Z. M. Dang, Energy Environ. Sci., 2024, 17(4), 1592–1602 RSC
.
- M. H. Yang, Z. P. Wang, Y. L. Zhao, Z. R. Liu, H. Pang and Z. M. Dang, Adv. Mater., 2023, 2309640 CrossRef
.
- M. X. Li, Y. J. Zhu, R. Wang, J. Fu, Z. Y. Ran, M. C. Yang, J. L. Li, J. Hu, J. L. He and Q. Li, Adv. Sci., 2023, 10(26), 2302949 CrossRef CAS
.
- W. B. Ren, M. Z. Yang, M. F. Guo, L. Zhou, J. Y. Pan, Y. Xiao, E. X. Xu, C. W. Nan and Y. Shen, Energy Storage Mater., 2024, 65, 103095 CrossRef
.
- M. Liu, J. H. Song, H. M. Qin, S. Y. Qin, Y. B. Zhang, W. L. Xia, C. X. Xiong and F. H. Liu, Adv. Funct. Mater., 2024, 34(21), 2313258 CrossRef CAS
.
- Z. L. Xie, K. Le, H. Li, X. Pang, T. L. Xu, V. Altoe, L. M. Klivanshy, Y. F. Wang, Z. Y. Huang, S. W. Shelton, X. D. Gu, P. Liu, Z. R. Peng and Y. Liu, Adv. Funct. Mater., 2024, 34(21), 2314910 CrossRef CAS
.
- S. Ding, J. H. Jia, Z. Z. Dai, Y. W. Wang, S. C. Shen, Y. W. Yin and X. G. Li, Chem. Eng. J., 2024, 493, 152623 CrossRef CAS
.
- H. M. Qin, M. Liu, S. Y. Qin, S. X. Zhang, X. N. Zhou, C. J. Li, Y. H. Wei, D. Chen, R. Fan, S. Wang, Q. L. Yang, C. X. Xiong and Q. Wang, Chem. Eng. J., 2024, 483, 149244 CrossRef CAS
.
- T. Zeng, Q. Li, D. D. Liu, J. Fu, L. P. Zhong, J. L. He, Q. Li and C. Yuan, Mater. Horiz., 2024, 11, 1539 RSC
.
- L. Dou, B. B. Yang, S. Lan, Y. Q. Liu, Y. Q. Liu, C. W. Nan and Y. H. Lin, Adv. Energy Mater., 2023, 13(11), 2203925 CrossRef CAS
.
- Z. T. Pei, Y. J. Liu, W. T. Zhao, C. Y. Yang, S. T. Li, P. K. Jiang, J. Chen and X. Y. Huang, Adv. Funct. Mater., 2024, 34(2), 2307639 CrossRef CAS
.
- R. Wang, Y. J. Zhu, J. Fu, M. C. Yang, Z. Y. Ran, J. L. Li, M. X. Li, J. Hu, J. L. He and Q. Li, Nat. Commun., 2023, 14(1), 2406 CrossRef CAS
.
|
This journal is © The Royal Society of Chemistry 2025 |
Click here to see how this site uses Cookies. View our privacy policy here.