DOI:
10.1039/D4RA08474H
(Paper)
RSC Adv., 2025,
15, 912-923
Recovery of iron as hematite and separation of trivalent lanthanide ions from spent hard disk magnet leach liquor using [P66614][Cy272] ionic liquid
Received
1st December 2024
, Accepted 6th January 2025
First published on 13th January 2025
Abstract
The widespread use of neodymium–iron–boron (NdFeB) magnets has raised concerns about the environmental impact of their disposal, prompting the need for sustainable recycling strategies. Traditional solvents used in recycling are toxic and flammable, making them risky to use. Ionic liquids are safer and greener options with low vapor pressure, high stability, and less flammability. This study introduces an eco-friendly recycling approach utilizing the [P66614][Cy272] ionic liquid to selectively extract iron and recover rare earth elements (REEs) from the leach liquor of waste NdFeB magnets. Pre-treatment processes enhanced metal concentration before leaching, including demagnetization, grinding, and screening. Optimal leaching conditions: 2 mol L−1 HCl, 80 °C, 10 g L−1 pulp density, and 90 minutes, resulted in complete leaching of REEs (Dy, Pr, Nd), iron, and boron. Using 0.01 mol L−1 [P66614][Cy272] ionic liquid, 100% of the iron was removed from the leach liquor with minimal co-extraction of REEs (∼4%). Precipitation of iron leading to Fe2O3 (hematite) after calcination and is verified through XRD and SEM-EDS analyses. The ionic liquid also enabled 81.1% recovery of HCl from the leach liquor, reducing neutralization needs and operational costs. Subsequent REEs separation using 0.01 mol L−1 [P66614][Cy272] ionic liquid demonstrated high selectivity, achieving separation factors of 18.55 (Dy/Pr) and 15.52 (Dy/Nd) at pH 2.03. Dy(III) was successfully separated from NdFeB leach solutions using counter-current extraction, leaving 6.0 mg L−1 in the raffinate, requiring two extraction stages at a 2
:
3 organic-to-aqueous phase (O/A) ratio. The reusability of the ionic liquid further enabled a sustainable, closed-loop recycling process. This approach highlights the potential for integrating ionic liquids into green technologies for NdFeB magnet recycling, ensuring resource recovery while minimizing environmental impact.
1 Introduction
The transition to renewable energy and a green economy is heavily reliant on rare earth elements (REEs), resulting in a steady increase in demand.1 REEs play a crucial role across various industries, including permanent magnets, batteries, ceramics, glass, catalysts, electronics, automotive, and renewable energy sectors.2,3 The permanent magnet and catalyst industries, accounting for 23% and 24% of all REE consumption, respectively, have emerged as the primary consumers of REEs.4 Neodymium–iron–boron (NdFeB) magnets are the most common type of permanent magnets and are distinguished by their superior strength, with an energy output of 200–440 kJ m−3, far surpassing that of ordinary ferrite magnets. NdFeB magnets are typically composed of 20–30% of Nd, 0.5–7% of Pr, 0.2–6% of Dy, 60–70% of Fe, 0.3–1% of B, 0.1–0.9% of Al, and 0.4–3% of Co, predominantly in the form of Nd2Fe14B phase.5,6 They are utilized in various applications, including motors and generators (34.4%), hard disk drives (HDDs) and Digital Versatile Discs (DVDs) (13.6%), electrical vehicles (EVs) and e-bikes (10.9%), and energy production and storage (7.2%).7 The annual production of approximately 600 million computer hard disks consumes an estimated 6000–12
000 tons of NdFeB magnets.8 HDDs contain approximately 1 to 20 grams of NdFeB magnet, with a lifespan of about 2 to 5 years, depending on the application.9 The rising challenges of waste management, coupled with the rapid decline in REEs resources, have led to the growth of fields focused on recycling and sustainable solutions. As a result, the recycling of used NdFeB magnets has gained significant importance.10 The recycling process of end-of-life (EoL) HDDs is beneficial due to their high content of REEs, nearly about 30%, including the mixture of light REEs (Nd and Pr) and economically valuable heavy REEs as Dy. These NdFeB magnets also contain large amounts of iron along with smaller quantities of boron and are typically coated with nickel and cobalt for corrosion protection.
Various approaches have been proposed for treating NdFeB magnet waste, with pyrometallurgy and hydrometallurgy being the primary methods. Pyrometallurgical techniques, like chlorination, glass slag formation, selective oxidation, and liquid metal extraction, are commonly used but pose challenges in metal separation and require high energy due to elevated operating temperatures (600–1500 °C).11–14 On the other hand, hydrometallurgy is a well-established technique for obtaining high-purity products and involves various steps such as dismantling, physical separation, crushing, leaching, removing impurities, and solvent extraction.15–18 It is commonly used in recovering NdFeB magnet waste components through selective leaching,19,20 solvent extraction,21,22 and precipitation.23,24 Yoon et al.25 investigated the leaching of NdFeB magnet scrap using sulfuric acid (H2SO4) at various temperatures and concentrations. They found that the best conditions of leaching parameters were 70 °C temperature, 3 mol L−1 H2SO4, and leaching time of 4 hours. In 2013, Lee et al.10 conducted a study on the leaching of NdFeB magnets using various leaching agents, including sulfuric acid (H2SO4), hydrochloric acid (HCl), nitric acid (HNO3), and sodium hydroxide (NaOH). They found that HCl and H2SO4 provided the best leaching performance. The optimal conditions identified were solid-to-liquid (S
:
L) ratio of 20 g L−1, leaching time of 15 minutes, and concentrations of 3 mol L−1 HCl or H2SO4. However, they observed that Nd dissolved along with iron. Lyman et al.26 reported that H2SO4 leaching dissolved about 98% of Nd from spent magnets, and it was recovered through double salt precipitation. However, the high concentration of iron in the leachate posed significant challenges for separating REEs.27
Iron impurities in leaching solutions pose difficulties in separation processes. Although commonly used, traditional precipitation methods often face issues like low selectivity due to co-precipitation with other metals. Solvent extraction offers a more efficient alternative, allowing for the selective separation, purification, and concentration of metal ions, which leads to the production of pure products. Organic extractants such as di-(2-ethyl hexyl)phosphoric acid (D2EHPA), tri-n-butyl phosphate (TBP), methyl isobutyl ketone (MIBK), and phosphine oxides such as Cyanex 921 and Cyanex 923 have shown high efficiency in iron extraction.28,29 However, the use of organic solvents presents safety and environmental risks due to their toxicity and flammability. For the protection of the environment, the environmental regulations, and SDGs (sustainable development goals) mandates are accelerating the shift toward innovative green practices.30,31 Ionic liquids (ILs) have gained attention as eco-friendly and versatile solvents, supporting the development of sustainable technologies. ILs are categorized based on cations, anions, functional groups, and other properties, with their evolution divided into generations reflecting advancements in synthesis. The first ILs, ethyl ammonium nitrate, was reported by Paul Walden in 1914, initiating first-generation ILs characterized by simple cation–anion interactions. These ILs exhibited thermal stability and low vapor pressures but were highly sensitive to water and air, with environmentally harmful synthesis routes. Second-generation ILs addressed these issues by introducing functional groups, enhancing tunability, and expanding applications in metal separation, pharmaceuticals, gas purification, and rare earth extraction. To overcome the limitations of earlier generations, third-generation ILs, also called task-specific ILs (TSILs) were developed for specialized applications.32,33 Hydrophobic RTILs, such as Cyphos IL 101 and Cyphos IL 104 have shown great promise in metal extraction, providing a sustainable alternative to traditional solvent extraction methods.34–36 Kogelnig et al.37 studied the separation of iron(III) from nickel(II) using Cyphos IL 101 diluted in chloroform (CHCl3). The results showed that iron(III) was efficiently extracted from 6 mol L−1 hydrochloric acid solution, forming tetrachloroferrate in the organic phase, while nickel(II) remained unextracted. Cui et al.38 studied the extraction of iron from acidic chloride solutions using undiluted Cyphos IL 101, achieving rapid and efficient extraction with high selectivity. The maximum iron loading capacity reached 83.2 g L−1. The spectroscopic analysis confirmed the extraction mechanism, involving FeCl3 as ion association and anion exchange for [FeCl4]− with Cyphos IL 101.
In hydrometallurgical processes, metals are commonly dissolved using acids during the leaching stage. The resulting leach solution tends to be highly acidic, often requiring neutralization before metal extraction can occur. This neutralization step not only consumes large quantities of alkali but also introduces additional cations and anions into the solution, which can complicate the metal separation process during solvent extraction. To mitigate these issues, an alternative approach involves recovering the free acids directly from the leach liquor. This strategy can eliminate the need for neutralization, thereby preventing the introduction of unwanted ions and enhancing the efficiency of metal extraction. Traditional extractants like tris-(2-ethyl hexyl)amine (TEHA), Alamine 336, TBP, Cyanex 923, and ILs like Aliquat 336, and Cyphos IL 104 are commonly used for extracting mineral acids.39–42 Kumari et al.43 investigate the use of Cyphos IL 104 for recovering various mineral acids from waste solutions, showing effective acid extraction and regeneration, even in the presence of lanthanum(III) ions.
Numerous studies have explored the use of various cation exchange extractants, such as D2EHPA, Cyanex 272, Cyanex 301, and PC88A, for the separation of elements like lanthanum (La), neodymium (Nd), and praseodymium (Pr).44 Among these, Cyanex 272 demonstrated the highest extraction efficiency. However, acidic extractants release H+ ions, reducing their efficiency. To counter this, studies have investigated the use of saponified acidic extractants with NaOH or NH3 for better separation.45,46 For instance, saponified PC88A has been used to extract Nd(III) from chloride media and Nd2O3 with more than 97% purity was obtained.47 Despite the improved separation, challenges such as emulsification, third-phase formation, and environmental concerns related to Na+ or NH4+ ion release remain problematic. Exploring the ILs again for REEs extraction, one study examined the extraction of Dy, Pr, and Nd from waste NdFeB magnets, utilizing TBP and Aliquat 336 nitrate ([A336][NO3]) as diluent, showed significant Nd(III) extraction through repeated cycles.48 Trihexyl(tetradecyl)phosphonium nitrate was also employed to separate cobalt from REEs such as Nd and Dy.49 A comprehensive study on the extraction of neodymium using Cyanex 923 was conducted in the presence of ILs, composed of bis(trifluoromethylsulfonyl)imide anion and five different cations. The findings revealed that ILs containing hydrophilic cations, such as [N1444][Tf2N] and [C4mim][Tf2N], demonstrated greater efficiency in extracting Nd(III) compared to those with hydrophobic cations.50
So, in this piece of work, the ionic liquid [P66614][Cy272] has been chosen for the entire investigation, including iron removal, acid extraction, and the separation of REEs after leaching the waste NdFeB magnets. First, the leaching of REEs (Dy, Pr, and Nd), the transition metal (Fe), and boron (B) from waste NdFeB magnets using inorganic acid, HCl was investigated. The effects of various leaching parameters, like the effect of acid concentrations, temperature, and leaching time, were thoroughly examined. Following leaching, iron in the leach liquor was removed using solvent extraction with the ionic liquid mentioned above. Concurrently, acid extraction from the leach liquor was also performed using ionic liquid [P66614][Cy272]. The separation behavior of rare earth metal ions from the leach liquor was studied, where the influence of pH, extractant concentration, and the construction of McCabe–Thiele plots were analyzed to identify optimal separation conditions among Dy, Pr, and Nd. The extraction efficiency and separation factor values were analyzed to assess the selectivity between heavy REEs (Dy) and light REEs (Pr and Nd). Production of hematite (Fe2O3) has also been carried out.
2 Materials and methods
2.1 Sample collection and pretreatment process of waste HDDs magnets
The waste and end-of-life desktop HDDs were collected from the computer center of Siksha ‘O’ Anusandhan Deemed to be University, Bhubaneswar. Afterwards, the neodymium-rich magnets were removed from waste HDDs, and each HDD contained two magnets weighing approximately 6–8 grams. These magnets were typically coated with a thin layer of nickel, which had been manually peeled by hand using a cutter. Following the removal of the coating, the magnets were subjected to thermal treatment in a muffle furnace at temperatures exceeding the Curie point (350 °C) for 2 hours to eliminate their magnetic properties. Next, the demagnetized NdFeB magnets were crushed with a hammer and then put into the pulverizer to get the powder form. Also, the particle size was smaller than 100 μm and was ready for chemical processing. The complete pretreatment process of the waste HDDs magnet is summarized in Fig. 1.
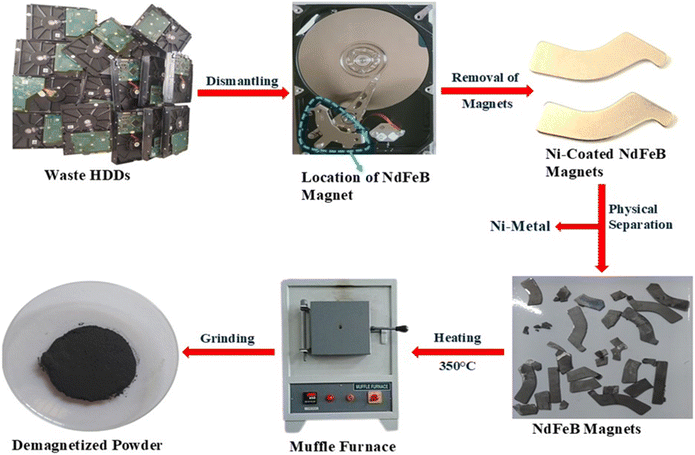 |
| Fig. 1 Flowchart of the pretreatment process of waste HDDs magnets. | |
2.2 Chemicals and apparatus
Cyanex 272 (bis(2,4,4-trimethylpentyl)phosphinic acid) and Cyphos IL 101 (trihexyl(tetradecyl)phosphonium chloride) were utilized as extractants to synthesize the task-specific ionic liquid [P66614][Cy272]. In this study, Cyanex 272 and Cyphos IL 101 were provided as gift samples by Cytec Solvay, Canada. Hydrochloric acid (HCl) with a purity of 37%, nitric acid (HNO3) with a purity of 69%, and all other chemicals were purchased from Merck of analytical grade. All solutions were prepared with Millipore water. The metal content in the aqueous solution was analyzed using ICP-OES (inductively coupled plasma optical emission spectroscopy) with iCAP PRO Thermo Scientific instrument. The elemental distribution and morphology of the NdFeB waste sample were examined using Scanning Electron Microscopy (SEM) with an EVO-18 microscope from Carl Zeiss, equipped with Energy Dispersive Spectroscopy (EDS). X-ray Diffraction (XRD) analysis, conducted on a PANalytical Empyrean Series 2 instrument, determined the phase composition using graphite monochromatized Cu Kα radiation (λ = 1.5418 Å). The ionic liquid [P66614][Cy272] was characterized using a Nicolet iS10 FTIR Spectrometer. The pH of the aqueous solution was measured with a Systronics digital pH meter 335.
2.3 Synthesis of [P66614][Cy272] ionic liquid
The ionic liquid [P66614][Cy272] was synthesized in the two steps. Initially, 100 mL of 0.1 mol L−1 Cyanex 272 and 0.1 mol L−1 Cyphos IL 101 are separately prepared by dissolving them in kerosene, then combined in a beaker and stirred at 25 °C for 2 hours using a magnetic stirrer. In the second step, the mixed solution was stirred with 200 mL of 0.1 mol L−1 sodium carbonate (Na2CO3) solution for 1 hour. To ensure all chloride ions are removed, the solution is washed again with more Na2CO3 for 30 minutes. The presence of chloride ions in the aqueous phase was tested using a titration method with 0.01 mol L−1 AgNO3. Finally, the solution is filtered using 1PS filter paper to obtain the purified [P66614][Cy272] ionic liquid, which is then used in extraction experiments.
2.4 Leaching process of HDDs magnet powder
The waste NdFeB magnet sample was leached using inorganic acid as HCl in a three-necked round-bottomed flask (500 mL) equipped with a magnetic stirrer, a vapor condenser, and a temperature monitor. A specific amount of the waste NdFeB magnet sample was accurately weighed, and hydrochloric acid solutions of varying concentrations were prepared as the leaching agents. After the leaching process, the metal content in the leach liquor was analyzed using Inductively Coupled Plasma Optical Emission Spectroscopy (ICP-OES). The leaching efficiency (% L) for various metals was calculated using eqn (1). |
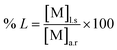 | (1) |
where [M]l.s and [M]a.r represents the metal content in the leach solution and aqua regia.
2.5 Solvent extraction and separation process
For the extraction and stripping experiments, 10 mL of each organic and aqueous phase were shaken together in a 60 mL separating funnel for 15 minutes at room temperature. After separating the phases, the aqueous phase metal concentration was analyzed using the ICP-OES instrument. The organic phase concentration is determined by subtracting metal ion concentrations from the aqueous phase before and after extraction. |
[Mn+](org) = [Mn+]i − [Mn+]f
| (2) |
where M(org)n+, Min+ and Mfn+ indicates the concentration of metal ions in the organic phase and metal ion concentrations before and after extraction, respectively. The distribution coefficient (D), percentage extraction efficiency (% E), separation factor (β), and percentage stripping (% S) have been calculated using the following formulas to interpret the data. |
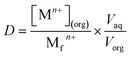 | (3) |
|
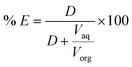 | (4) |
|
 | (5) |
|
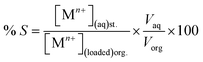 | (6) |
where, Vaq and Vorg represents volumes of aqueous and organic phases, respectively. Di and Dj represents the distribution ratio between two different metals. [Mn+](aq)st. and [Mn+](loaded)org. refers to the concentration of metals in the stripping and loaded organic phases. Separation studies on leach liquor from waste HDDs magnet systematically examined the effects of pH and extractant concentration variations to optimize the selective separation of Dy, Nd, and Pr. The McCabe–Thiele plot was applied to assess separation efficiency. The study identified crucial parameters for effective extraction, offering valuable insights into optimizing REEs separation.
2.6 Precipitation
After the extraction of iron, precipitation studies were performed in a beaker by adding the stoichiometric amount of sodium hydroxide (NaOH) under continuous stirring at room temperature. A hot plate with a magnetic stirrer was employed to regulate both the temperature and stirring speed, set at 30 °C and 200 rpm, respectively. The NaOH solution was gradually added until the precipitation of iron hydroxide was completed. The resulting precipitate was collected by filtration and thoroughly washed with distilled water to remove any residual impurities. The washed precipitate was then dried in an oven at 90 °C for 3 hours. Following drying, the precipitate was subjected to calcination at 500 °C for 4 hours to obtain iron in the form of hematite (Fe2O3).
3 Results and discussion
3.1 Characterization and analysis of waste HDDs magnet sample
After demagnetization and grinding, 1 gram of waste HDDs magnet sample was digested in 40 mL of aqua regia (HCl
:
HNO3 = 3
:
1), heated to boiling, and stirred for one hour. After cooling, the solution was filtered into a 100 mL volumetric flask, and the volume was adjusted to 100 mL with distilled water. The total metal content of the waste NdFeB magnet was then analyzed using ICP-OES. Table 1 represents the elemental composition of waste NdFeB magnet sample in weight percent (wt%). Iron is the major component, making up 45.76 wt% of the material, while the target metals include the light REEs neodymium (17.77 wt%) and praseodymium (5.03 wt%), along with the heavy rare earth element dysprosium (1.31 wt%). Minor components, such as boron (B) and nickel (Ni), are present at concentrations below 1 wt%, with nickel being excluded from the leaching studies due to its negligible amount. The X-ray diffraction pattern (Fig. 2) from the waste HDDs magnet confirmed the presence of the Nd2Fe14B phase (JCPDS file no. 96-154-0078). Scanning electron microscopy image, Fig. 3(a) revealed that the sample was solid rock with no visible porosity. Energy dispersive X-ray spectroscopy analyses Fig. 3(b), the specific areas in the SEM closely matched the overall chemical composition, indicating uniformity throughout the magnet sample.
Table 1 Chemical composition of waste NdFeB magnet in weight percentage
Elements |
Fe |
Nd |
Pr |
Dy |
B |
Ni |
Non-metals |
wt% |
45.76 |
17.77 |
5.03 |
1.31 |
0.96 |
0.05 |
Balance |
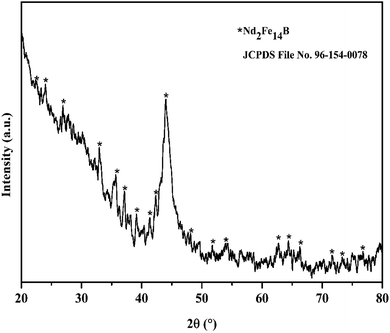 |
| Fig. 2 XRD graph of waste HDDs magnet sample. | |
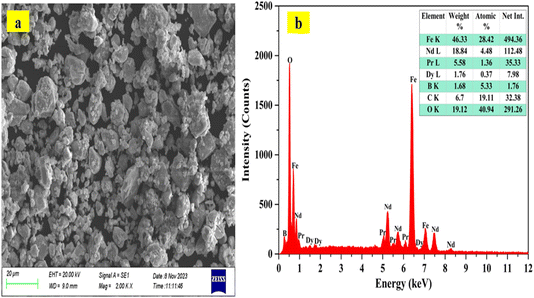 |
| Fig. 3 (a) SEM image and (b) EDS plot of the waste HDDs magnet sample. | |
3.2 Characterization of [P66614][Cy272] ionic liquid using FTIR studies
FTIR spectroscopic analysis was conducted to confirm the synthesis of the [P66614][Cy272] ionic liquid. The FTIR spectra of Cyanex 272 (blue line), Cyphos IL 101 (red line), and [P66614][Cy272] ionic liquid (black line) were compared in Fig. 4. Peaks at 1461 cm−1 and 1380 cm−1, observed in all three spectra, correspond to P–C stretching and C–H in-plane bending vibrations, respectively.51 Both Cyanex 272 and [P66614][Cy272] ionic liquid displayed a peak at 1168 cm−1, attributed to P
O stretching,34 while Cyanex 272 uniquely showed a P–O–H bending peak at 960 cm−1.52,53 After the synthesis of [P66614][Cy272] ionic liquid, the P–O–H peak disappeared, indicating the removal of the hydrogen ion from Cyanex 272 and chloride ion from Cyphos IL 101, forming the [P66614][Cy272] ionic liquid. A new peak appeared at 1027 cm−1, corresponding to P–O stretching vibrations of [P66614][Cy272] ionic liquid.43
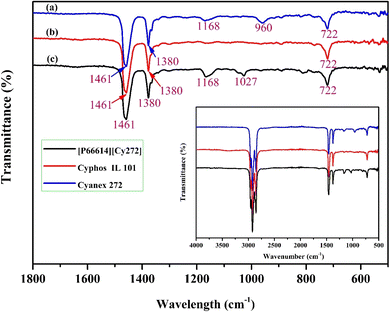 |
| Fig. 4 FTIR spectra of (a) Cyanex 272, (b) Cyphos IL 101 and (c) [P66614][Cy272] ionic liquid. | |
3.3 Effects of leaching concentration, temperature, and time
The effect of hydrochloric acid (HCl) concentration, ranging from 2 mol L−1 to 7 mol L−1 on the leaching of REEs (Dy, Pr, and Nd), B, and Fe from waste NdFeB magnet samples was studied under controlled conditions of 30 °C temperature, 10 g L−1 pulp density, and 400 rpm stirring speed over 90 minutes. As illustrated in Fig. 5(a), the investigation revealed that the leaching behavior of Dy, Pr, and Nd increased with higher HCl concentrations. With 2 mol L−1 HCl, the maximum leaching efficiency was achieved to be 78.4% for Dy, 62.9% for Pr, and 60.7% for Nd within 90 minutes. When the acid concentration was increased to 3 mol L−1, the leaching percentages slightly improved to 82.6% for Dy, 66% for Pr, and 63.8% for Nd. Additionally, the dissolution rates of Fe and B were 94.5% and 90%, respectively, in 2 mol L−1 HCl, both approaching nearly complete dissolution at 3 mol L−1 HCl.
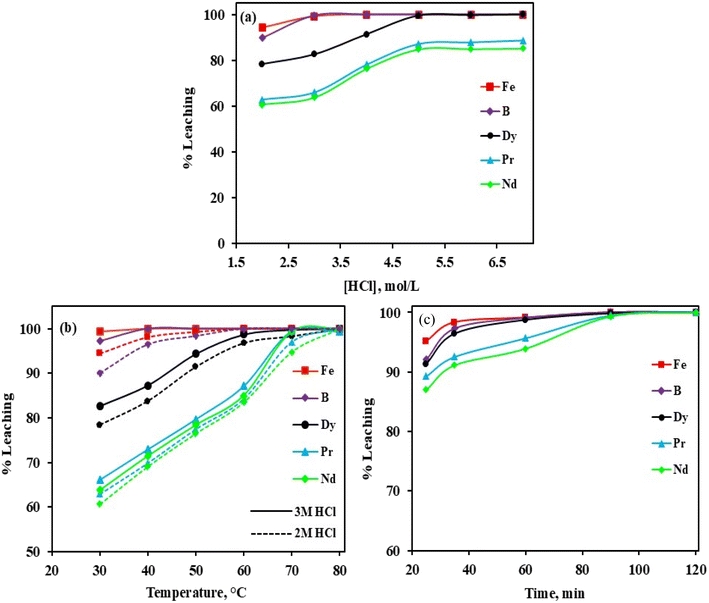 |
| Fig. 5 Effect of various parameters on leaching efficiency of REEs, B and Fe, (a) HCl concentration (temperature = 30 °C, PD = 10 g L−1, leaching time = 90 min, rpm = 400), (b) temperature ([HCl] = 2 mol L−1 and 3 mol L−1, PD = 10 g L−1, leaching time = 90 min, rpm = 400) and (c) leaching time ([HCl] = 2 mol L−1, PD = 10 g L−1, temperature = 80 °C, rpm = 400). | |
Next, the leaching of REEs, B, and Fe from the waste NdFeB magnet sample with varying temperatures in the range of 30 °C to 80 °C and using an acid concentration of 2 mol L−1 (dotted dash line) to 3 mol L−1 (solid line) HCl at 10 g L−1 pulp density and 400 rpm is shown in Fig. 5(b). The recovery of REEs (Dy, Pr, and Nd) increased with increasing temperature. Increasing temperature increases solute diffusivity, leading to an enhanced leaching rate. This is primarily because the probability of successful molecular collisions rises with temperature while being inversely affected by activation energy. The higher temperature results in increased kinetic energy, which accelerates the reaction, reduces the activation energy, and consequently improves the overall efficiency of the leaching process. At 70 °C, the three REEs were completely leached at a concentration of 3 mol L−1 HCl, while at 80 °C, the three REEs were 100% leached using 2 mol L−1 HCl. However, the leaching efficiency of Fe and B was almost 100% at 60 °C using 2 mol L−1 or 3 mol L−1 HCl. Thus, the optimal conditions for producing the leach liquor are 2 mol L−1 HCl concentration, pulp density of 10 g L−1, and temperature of 80 °C, allowing for further evaluation of the impact of leaching time.
The influence of leaching time was investigated by adjusting the duration from 25 to 120 minutes, maintaining other leaching parameters 2 mol L−1 HCl concentration, pulp density of 10 g L−1, stirring speed of 400 rpm, and temperature of 80 °C. The results, shown in Fig. 5(c), indicated that the leaching of Dy, Pr, and Nd is rapid: approximately 91.4% of Dy, 89.3% of Pr, and 87% of Nd extracted within the first 25 minutes. In contrast, the 100% leaching efficiencies of Dy, Pr, and Nd were reached after 90 minutes. As a result, the optimal leaching time was found to be 90 minutes. Based on the study, the optimal leaching conditions were identified as 2 mol L−1 HCl concentration, stirring speed of 400 rpm, stirring time of 90 minutes, temperature of 80 °C, and pulp density (PD) of 10 g L−1. Additionally, the composition of the primary elements in the leaching liquor is summarised in Table 2. Inorganic acids, being strong acids, promote ionization and are more effective in dissolving metals compared to organic acids, resulting in higher recovery rates of metals found in magnets.54 In the case of NdFeB magnets, REEs in solid form are converted into their ionic REE3+ state, as described in eqn (7). REEs in hydrochloric acid leaching turn into hydrogen gas and ion-containing chloride, respectively. Likewise, Fe and B are converted into Fe2+ and B3+ ions (eqn (8) and (9)), with hydrogen gas released as a byproduct.10
|
2REE(s) + 6HCl(aq) → 2REE3+(aq) + 3H2(g) + 6Cl−(aq)
| (7) |
|
Fe(s) + 2HCl(aq) → Fe2+(aq) + H2(g) + 2Cl−(aq)
| (8) |
|
B(s) + 6HCl(aq) → 2B3+(aq) + 3H2(g) + 6Cl−(aq)
| (9) |
Table 2 The concentration of primary elements in the leach liquor of NdFeB magnets
Elements |
Fe |
Nd |
Pr |
Dy |
B |
Concentration in g L−1 |
4.75 |
1.77 |
0.50 |
0.13 |
0.096 |
3.4 Selective removal of iron from leach liquor using solvent extraction method
The presence of iron in the leach solution adversely affects the extraction and purity of the target REE products, making its selective removal crucial. It has been reported that iron predominantly precipitates at pH above 3.0.55,56 In this study, the precipitation of iron using 4 mol L−1 NaOH was carried out, leading to an iron precipitation efficiency of 86.4% at pH 3.4. However, this approach led to significant co-precipitation of REEs, with 59% of Dy, 28.8% of Pr, and 11.6% of Nd. Consequently, iron extraction was conducted at room temperature using 0.01 mol L−1 [P66614][Cy272] ionic liquid, with an O/A volume ratio of 1
:
1. This extraction process successfully transferred 100% of the iron into the organic phase, with only ∼4% co-extraction of REEs. The concentrations of metals remaining in the leach liquor after iron removal are depicted in Table 3. Similar observations were reported by Hoogerstraete et al.,57 where they engaged the ionic liquid trihexyl(tetradecyl)phosphonium chloride, to efficiently extract iron from REEs. Their process successfully achieved over 99.98% extraction of iron from NdFeB magnets, demonstrating high separation efficiency.
Table 3 The concentration of metals present in leach liquor after iron removal
Elements |
Nd |
Pr |
Dy |
B |
Concentration in g L−1 |
1.74 |
0.48 |
0.13 |
0.096 |
The loaded iron in the organic phase was effectively stripped using 0.5 mol L−1 HNO3, leading to the complete stripping of iron. The stripped iron solution was precipitated by adding NaOH, resulting in the formation of iron hydroxide. This iron hydroxide was then calcined for 4 hours at 500 °C temperature, leading to the formation of iron oxide (Fe2O3) as hematite (Fig. 6(a)). XRD analysis confirmed the presence of Fe2O3, matching with JCPDS file number 00-024-0072 (Fig. 6(b)). Additionally, SEM-EDS (Fig. 7) analysis showed that the sample contained only iron, with no rare earth elements detected.
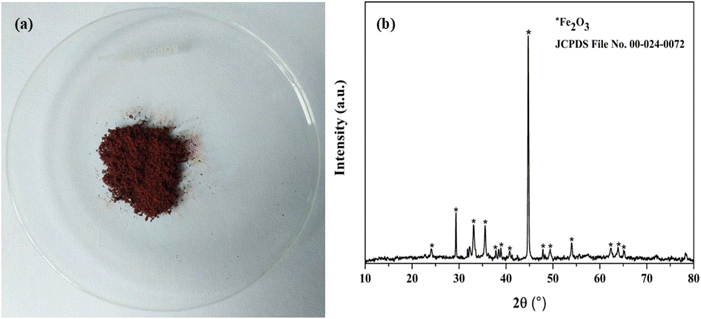 |
| Fig. 6 (a) Image of iron precipitate as hematite and (b) XRD graph of Fe2O3. | |
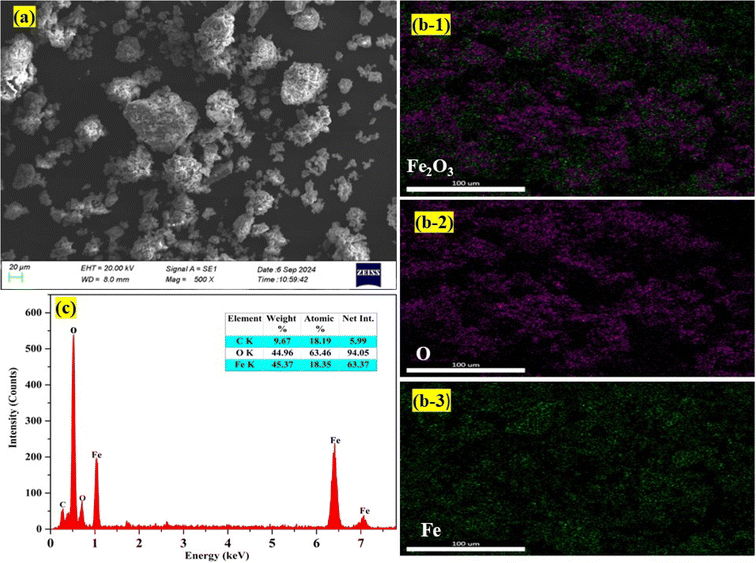 |
| Fig. 7 (a) SEM image, (b) elemental mapping and (c) EDS plot of Fe2O3. | |
3.5 Extraction of hydrochloric acid from leach liquor
The high acidity of the leach liquor, primarily caused by the presence of HCl (1.22 mol L−1), necessitates substantial amounts of alkali for neutralization before metal ion extraction, which increases operational costs. To address this challenge, experiments were carried out to recover or remove HCl using the [P66614][Cy272] ionic liquid as an extractant. The concentrations of the ionic liquid varied between 0.1 mol L−1 and 1 mol L−1 to determine the most effective recovery conditions. This method offers the potential to improve metal extraction efficiency by reducing the need for neutralization, thus lowering alkali consumption and minimizing both economic costs and environmental impacts. The experiments were conducted under controlled conditions with phase ratio (O/A) of 1
:
1. After the extraction of the acid from the leach liquor, the remaining acid concentration in the aqueous phase was measured using the acid–base titration method using phenolphthalein as an indicator. This analytical approach allowed precise quantification of the residual acidity, providing insight into the effectiveness of the ionic liquid in HCl recovery. The results revealed that increasing the concentration of the extractants led to higher HCl extraction efficiency. The highest extraction rate, 81.1%, was achieved with 1 mol L−1 [P66614][Cy272] ionic liquid (Table 4). After acid extraction, the concentration of Nd is 1.63 g L−1, Pr of 0.44 g L−1, Dy of 0.12 g L−1, and 0.096 g L−1 of B that is present in leach liquor. However, 6.3% of Nd, 8.3% of Pr, and 7.6% of Dy were lost during the acid extraction. This leach liquor concentration is further used for the separation of these three REEs. After the acid extraction process, the HCl-loaded organic phase was effectively stripped using distilled water, with up to 42.4% of the HCl (0.42 mol L−1) being recovered and stored for reuse in subsequent leaching operations, significantly reducing the demand for fresh acid. The [P66614][Cy272] ionic liquid is then regenerated by treating it with Na2CO3, a process that neutralizes and reactivates the ionic liquid, preparing it for reuse in the separation of REEs from the leach liquor. This closed-loop system conserves resources while ensuring the efficiency of both the ionic liquid and HCl, making the process cost-effective and eco-friendly. The [P66614][Cy272] ionic liquid is an organic salt (R4P+Aorg−) made up of the trihexyl(tetradecyl)phosphonium (R4P+) cation and the bis(2,4,4-trimethylpentyl)phosphinate (A−) anion. The extraction of acid by the ionic liquid is described by eqn (10).30 |
R4PAorg + Haq+ + Claq− ⇔ R4PClorg + HAorg
| (10) |
Table 4 Extraction of HCl from leach liquor using different concentrations of [P66614][Cy272] ionic liquid
[Extractant], mol L−1 |
[HCl]initial, mol L−1 |
[HCl]raffinate, mol L−1 |
[HCl]organic, mol L−1 |
% E |
0.1 |
1.22 |
1.14 |
0.08 |
6.6 |
0.25 |
1.22 |
0.99 |
0.23 |
18.9 |
0.5 |
1.22 |
0.73 |
0.49 |
40.2 |
0.75 |
1.22 |
0.48 |
0.74 |
60.7 |
1 |
1.22 |
0.23 |
0.99 |
81.1 |
3.6 Selective extraction of heavy rare earth metal (Dy) from the leach liquor using [P66614][Cy272] ionic liquid
The separation of REEs such as Dy, Nd, and Pr from NdFeB magnets is notably difficult due to their similar ionic radii and chemical properties. This study investigated the separation of Dy, Nd, and Pr from the leach liquor of NdFeB magnets using the [P66614][Cy272] ionic liquid. A pH variation experiment was performed across a range of 0.42 to 4.02 with 0.01 mol L−1 [P66614][Cy272] ionic liquid to determine the impact of pH on the extraction efficiency of these REEs. The results indicated that the extraction percentages of all three metals increased with the rise in pH. The extraction efficiencies were minimal at a low pH, for example, at pH 0.42, with less than 2.5% extraction for each ion. However, at pH 2.03, the extraction efficiency of Dy(III) reached 66.9%, while Nd(III) and Pr(III) had much lower extraction efficiencies of 14.9% and 12.8%, respectively (Fig. 8). At a higher pH of 4.02, Dy(III) extraction increased to 76.0%, and the extraction percentages of Nd and Pr also increased to around 34%. The highest separation factors for Dy/Pr (18.55) and Dy/Nd (15.52) were observed at pH 2.03 (Table 5), highlighting this as the optimal pH for selective Dy(III) extraction from NdFeB magnet leachate. To reduce the number of extraction stages needed for the separation of Dy from Nd and Pr, an extractant concentration variation study was performed at pH 2.03. The separation factors in relation to different concentrations of the extractant are presented in Fig. 9. The highest separation factors for Dy over Nd and Pr were achieved with 0.1 mol L−1 [P66614][Cy272] ionic liquid. However, at this concentration, the co-extraction of Nd(III) and Pr(III) exceeded 88%, along with 99% extraction of Dy(III). Due to the high co-extraction, 0.05 mol L−1 [P66614][Cy272] ionic liquid was selected for constructing the McCabe–Thiele plot.
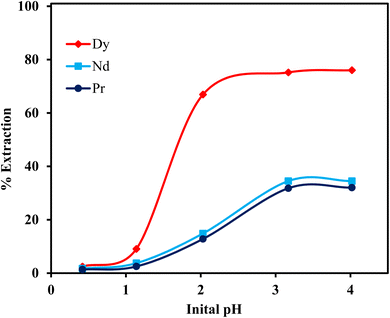 |
| Fig. 8 Effect of initial pH on the extraction of Dy(III), Nd(III), and Pr(III). Aqueous phase: [Dy3+] = 0.12 g L−1, [Nd3+] = 1.63 g L−1 and [Pr3+] = 0.44 g L−1. Organic phase: 0.01 mol L−1 [P66614][Cy272] ionic liquid, O/A = 1 : 1. | |
Table 5 Separation factor values of Dy/Pr, Dy/Nd, and Nd/Pr using 0.01 mol L−1 [P66614][Cy272] ionic liquid
Sl. no. |
Initial pH |

|

|

|
1 |
0.42 |
1.83 |
1.63 |
1.12 |
2 |
1.14 |
3.87 |
3.09 |
1.25 |
3 |
2.03 |
18.55 |
15.52 |
1.2 |
4 |
3.17 |
7.35 |
6.89 |
1.07 |
5 |
4.02 |
7.91 |
7.33 |
1.08 |
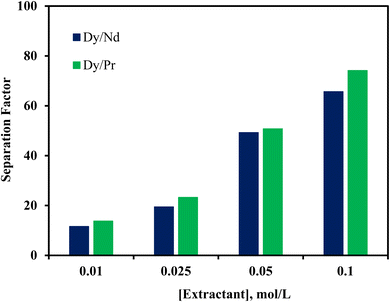 |
| Fig. 9 Dy/Pr and Dy/Nd separation factors at different concentrations. | |
A McCabe–Thiele plot (Fig. 10) was constructed to analyze the extraction of Dy(III), with the organic to aqueous phase ratio varied from 5
:
1 to 1
:
5 while maintaining a constant total volume at pH 2.03, using a 0.05 mol L−1 [P66614][Cy272] ionic liquid. The results indicated that two extraction stages at an O/A ratio of 2
:
3 were necessary for the complete removal of Dy(III). Subsequent counter-current extraction experiments revealed that 6.0 mg L−1 of Dy(III) remained in the raffinate, alongside 1.23 g L−1 of Nd(III) and 0.35 g L−1 of Pr(III). In this process, 172.5 mg L−1 of Dy(III) has been transferred to the loaded organic phase from the NdFeB leach solution showing some enrichment of Dy(III) as the organic volume is less than the aqueous volume. The findings suggest that [P66614][Cy272] ionic liquid shows significant potential as an extractant for the selective separation of heavy and light rare earth elements. The flow sheet (Fig. 11), outlines an optimized process for efficiently extracting REEs from waste NdFeB magnets, emphasizing selective leaching and separation. This method ensures high-purity recovery while promoting sustainable recycling practices.
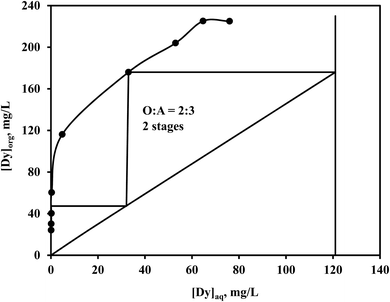 |
| Fig. 10 McCabe–Thiele plot for Dy(III) extraction. | |
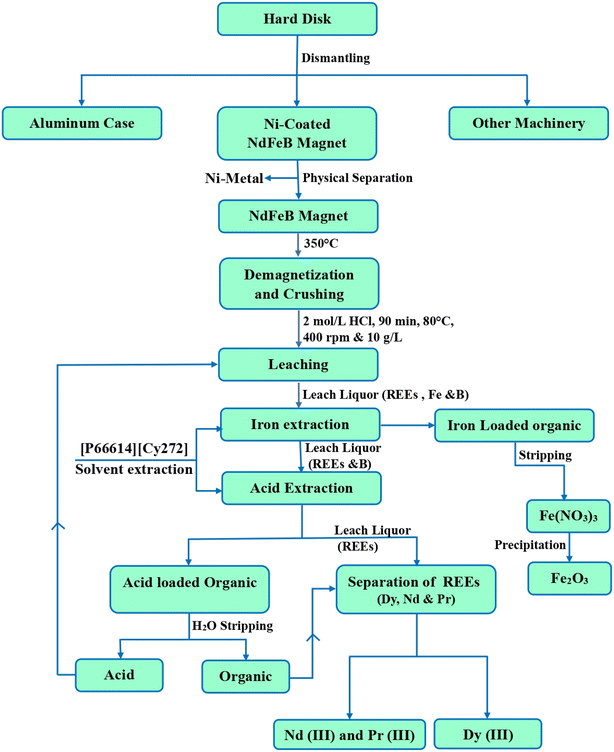 |
| Fig. 11 Flow sheet for recovery of REEs from waste HDDs magnet. | |
4 Conclusions
This study presents an innovative and sustainable method for recovering and separating REEs from waste NdFeB magnets. The process begins with physical pretreatment process, including demagnetization, grinding, and screening, to enrich the metal content for subsequent leaching steps. Optimal leaching conditions were identified as 2 mol L−1 HCl, 80 °C, 10 g L−1 pulp density, and leaching time duration of 90 minutes, achieving near-complete leaching of REEs (Dy, Pr, and Nd), Fe, and B. The selective removal of iron from the leach liquor using [P66614][Cy272] ionic liquid, was highly effective, achieving 100% iron extraction with minimal REEs co-extraction (∼4%). The recovered iron was converted into hematite (Fe2O3), as confirmed through XRD and SEM-EDS analyses, thereby increasing the purity of the REE products. To address the high acidity of the leach liquor, the same ionic liquid was employed for HCl extraction, achieving 81.1% recovery rate. This step significantly reduced the need for chemical neutralization, lowering alkali consumption and operational costs. Both the recovered HCl and regenerated ionic liquid showed promising potential for reuse, contributing to the development of closed-loop, environmentally friendly process. The separation process demonstrated excellent selectivity, achieving high separation factors of 18.55 for Dy/Pr and 15.52 for Dy/Nd at pH of 2.03. The counter-current extraction experiments revealed that 6.0 mg L−1 of Dy(III) remained in the raffinate, alongside 1.23 g L−1 of Nd(III) and 0.35 g L−1 of Pr(III). During the process, 172.5 mg L−1 of Dy(III) was successfully transferred to the organic phase from the NdFeB leach solution. This indicates some enrichment of Dy(III) due to the smaller volume of the organic phase compared to the aqueous phase. Overall, the proposed method not only improves the efficiency of REE recovery but also minimizes environmental impacts, offering scalable, cost-effective solution for recycling rare earth magnets.
Data availability
The data supporting the findings of this study are available from the corresponding author upon reasonable request (E-mail: niharbaladevi@soa.ac.in).
Conflicts of interest
The authors declare that there are no conflicts of interest associated with this publication.
Acknowledgements
The authors thank Siksha ‘O’ Anusandhan University and CSIR-Institute of Minerals and Materials Technology for providing the facilities to carry out the experimental work. One of the authors Mr Prasanjit Das would like to acknowledge the Department of Science and Technology (DST), Govt. of India for providing DST INSPIRE fellowship (INSPIRE Code: IF230104).
References
- E. Alonso, A. M. Sherman, T. J. Wallington, M. P. Everson, F. R. Field, R. Roth and R. E. Kirchain, Environ. Sci. Technol., 2012, 46, 3406–3414 CrossRef CAS PubMed.
- Y. Yang, A. Walton, R. Sheridan, K. Güth, R. Gauß, O. Gutfleisch, M. Buchert, B. M. Steenari, T. V. Gerven, P. T. Jones and K. Binnemans, Journal of Sustainable Metallurgy, 2017, 3, 122–149 CrossRef.
- T. Xu, X. Zheng, B. Ji, Z. Xu, S. Bao, X. Zhang, G. Li, J. Mei and Z. Li, Sep. Purif. Technol., 2024, 330, 125501 CrossRef CAS.
- B. Zhou, Z. Li and C. Chen, Minerals, 2017, 7, 203 CrossRef.
- B. Seo, H. K. Park, T. Na, S. Heo, R. Kim, H. S. Yoon, K. W. Chung and K. Park, Hydrometallurgy, 2024, 227, 106320 CrossRef CAS.
- Y. Zhang, F. Gu, Z. Su, S. Liu, C. Anderson and T. Jiang, Metals, 2020, 10, 841 CrossRef CAS.
- M. Kaya, Curr. Opin. Green Sustainable Chem., 2024, 46, 100884 CrossRef CAS.
- K. Binnemans, P. T. Jones, B. Blanpain, T. V. Gerven, Y. Yang, A. Walton and M. Buchert, J. Cleaner Prod., 2013, 51, 1–22 CrossRef CAS.
- M. Ueberschaar and V. S. Rotter, J. Mater. Cycles Waste Manage., 2015, 17, 266–281 CrossRef CAS.
- C. H. Lee, Y. J. Chen, C. H. Liao, S. R. Popuri, S. L. Tsai and C. E. Hung, Metall. Mater. Trans. A, 2013, 44, 5825–5833 CrossRef CAS.
- T. Lorenz and M. Bertau, J. Cleaner Prod., 2019, 215, 131–143 CrossRef CAS.
- M. Nakamoto, K. Kubo, Y. Katayama, T. Tanaka and T. Yamamoto, Metall. Mater. Trans. B, 2012, 43, 468–476 CrossRef CAS.
- Y. Bian, S. Guo, L. Jiang, K. Tang and W. Ding, Journal of Sustainable Metallurgy, 2015, 1, 151–160 CrossRef.
- H. W. Na, Y. H. Kim, H. T. Son, I. H. Jung, H. S. Choi and T. B. Kim, Curr. Nanosci., 2014, 10, 128–130 CrossRef CAS.
- O. Takeda and T. H. Okabe, Metall. Mater. Trans. E, 2014, 1, 160–173 CAS.
- A. R. Ray and S. Mishra, Sustainable Chem. Pharm., 2023, 36, 101311 CrossRef CAS.
- F. Mao, N. Zhu, W. Zhu, B. Liu, P. Wu and Z. Dang, Environ. Sci. Pollut. Res., 2021, 29, 25532–25543 CrossRef.
- A. Kumari, R. Raj, N. S. Randhawa and S. K. Sahu, Hydrometallurgy, 2021, 201, 105581 CrossRef CAS.
- C. Liu, Q. Yan, X. Zhang, L. Lei and C. Xiao, Environ. Sci. Technol., 2020, 54, 10370–10379 CrossRef CAS PubMed.
- Q. Yang, Y. Li, B. Li, P. Duan, Z. Ren and Z. Zhou, Sep. Purif. Technol., 2024, 329, 125137 CrossRef CAS.
- S. Pavón, A. Fortuny, M. T. Coll and A. M. Sastre, J. Environ. Manage., 2018, 222, 359–367 CrossRef.
- M. Carsky and V. Gruber, S. Afr. J. Chem. Eng., 2020, 33, 35–38 Search PubMed.
- Z. Liu, H. Zhou, W. Li, X. Luo, J. Wang and F. Liu, Sep. Purif. Technol., 2022, 282, 119795 CrossRef CAS.
- W. Lai, M. Liu, C. Li, H. Suo and M. Yue, Hydrometallurgy, 2014, 150, 27–33 CrossRef CAS.
- H. S. Yoon, C. J. Kim, K. W. Chung, S. J. Lee, A. R. Joe, Y. H. Shin, S. I. Lee, S. J. Yoo and J. G. Kim, Korean J. Chem. Eng., 2014, 31, 706–711 CrossRef CAS.
- J. W. Lyman and G. R. Palmer, High Temp. Mater. Process., 1993, 11, 175–188 CAS.
- D. Dupont and K. Binnemans, Green Chem., 2015, 17, 2150–2163 RSC.
- A. Azizitorghabeh, F. Rashchi, A. Babakhani and M. Noori, Sep. Sci. Technol., 2017, 52, 476–486 CrossRef CAS.
- R. K. Mishra, P. C. Rout, K. Sarangi and K. C. Nathsarma, Hydrometallurgy, 2010, 104, 298–303 CrossRef CAS.
- P. A. Khan, S. K. Johl and S. Akhtar, Journal of Risk and Financial Management, 2022, 15, 96 CrossRef.
- P. A. Khan, S. K. Johl and S. K. Johl, Business Strategy and the Environment, 2021, 30, 2922–2936 CrossRef.
- H. W. Khan, B. M. Negash, N. I. Zulkifli, M. D. H. Wirzal, S. Mishra and A. Azmi, J. Ind. Eng. Chem., 2024 DOI:10.1016/j.jiec.2024.09.047.
- B. M. Negash, A. J. Effiong, H. W. Khan and N. I. B. Zulkifli, J. Mol. Liq., 2024, 403, 124849 CrossRef CAS.
- B. B. Mishra, N. Devi and K. Sarangi, Monatshefte für Chemie, 2021, 152, 767–775 CrossRef CAS.
- A. M. El-Wakil, A. B. Farag and A. K. Ez-Eldin, Fresenius' Z. Anal. Chem., 1982, 311, 522 CrossRef CAS.
- S. Nayak and N. Devi, Turk. J. Chem., 2017, 41, 892–903 CrossRef CAS.
- D. Kogelnig, A. Stojanovic, F. Jirsa, W. Körner, R. Krachler and B. K. Keppler, Sep. Purif. Technol., 2010, 72, 56–60 CrossRef CAS.
- L. Cui, F. Cheng and J. Zhou, Ind. Eng. Chem. Res., 2015, 54, 7534–7542 CrossRef CAS.
- U. Kesieme, A. Chrysanthou, M. Catulli and C. Y. Cheng, J. Chem. Technol. Biotechnol., 2018, 93, 3374–3385 CrossRef CAS.
- K. Sarangi, E. Padhan, P. V. R. B. Sarma, K. H. Park and R. P. Das, Hydrometallurgy, 2006, 84, 125–129 CrossRef CAS.
- R. M. Machado, M. L. F. Gameiro, J. M. A. Rodrigues, M. R. C. Ismael, M. T. A. Reis and J. M. R. Carvalho, Sep. Sci. Technol., 2017, 52, 1333–1340 CrossRef CAS.
- F. J. Alguacil and F. A. Lopez, Hydrometallurgy, 1996, 42, 245–255 CrossRef CAS.
- A. Kumari, M. K. Sinha, S. K. Sahu and B. D. Pandey, Hydrometallurgy, 2016, 165, 159–165 CrossRef CAS.
- F. Xie, T. A. Zhang, D. Dreisinger and F. Doyle, Miner. Eng., 2014, 56, 10–28 CrossRef CAS.
- P. K. Parhi, T. R. Sethy, P. C. Rout and K. Sarangi, Sep. Sci. Technol., 2016, 51, 2232–2241 CrossRef CAS.
- H. S. Yoon, C. J. Kim, K. W. Chung, S. D. Kim, J. Y. Lee and J. R. Kumar, Hydrometallurgy, 2016, 165, 27–43 CrossRef CAS.
- M. S. Lee, J. Y. Lee, J. S. Kim and G. S. Lee, Sep. Purif. Technol., 2005, 46, 72–78 CrossRef CAS.
- Y. Kikuchi, M. Matsumiya and S. Kawakami, Solvent Extr. Res. Dev., Jpn., 2014, 21, 137–145 CrossRef CAS.
- S. Riaño and K. Binnemans, Green Chem., 2015, 17, 2931–2942 RSC.
- A. Rout and K. Binnemans, Dalton Trans., 2015, 44, 1379–1387 RSC.
- H. Mahandra, R. Singh and B. Gupta, Sep. Purif. Technol., 2017, 177, 281–292 CrossRef CAS.
- L. C. Thomas and R. A. Chittenden, Spectrochim. Acta, 1964, 20, 489–502 CrossRef CAS.
- D. C. Gonzalez, M. A. Rodriguez, G. Cote and A. Chagnes, J. Mol. Liq., 2013, 187, 165–170 CrossRef.
- M. Gergoric, A. Barrier and T. Retegan, Journal of Sustainable Metallurgy, 2019, 5, 85–96 CrossRef.
- K. S. Rao, N. B. Devi and B. R. Reddy, Hydrometallurgy, 2000, 57, 269–275 CrossRef CAS.
- M. Balintova and A. Petrilakova, Chem. Eng. Trans., 2011, 25, 345–350 Search PubMed.
- T. V. Hoogerstraete, S. Wellens, K. Verachtert and K. Binnemans, Green Chem., 2013, 15, 919–927 RSC.
|
This journal is © The Royal Society of Chemistry 2025 |
Click here to see how this site uses Cookies. View our privacy policy here.