Enhanced electrochemical performance of NiSbS/NiSb/NiS nanocomposites anchored on graphite nanosheets for sodium-ion battery applications†
Received
14th October 2024
, Accepted 14th November 2024
First published on 15th November 2024
Abstract
In the realm of scalable fabrication of anodes through ball milling, ensuring high electrochemical performance and robust cycling stability of anodes for sodium-ion batteries is paramount, but it presents a formidable hurdle. In pursuit of these goals, a distinctive hybrid composite distinguished by its intricate multiphase composition has been devised. This entails the integration of innovative NiSbS/NiSb/NiS nanomaterials onto exfoliated graphite nanosheets (Ni–Sb–S/GN) via a straightforward technique. Analyses indicate that the interplay between the graphite nanosheets and the hybrid Ni–Sb–S in conjunction with the discharge byproducts of Na2S substantially augment the stability and Na-ion diffusion kinetics of Ni–Sb–S/GN anodes. The novel Ni–Sb–S/GN exhibits markedly superior electrochemical performance in comparison to its Ni–Sb–S counterpart. Specifically, Ni–Sb–S/GN retains a reversible capacity of 238.7 mA h g−1 at 0.2 A g−1 after 300 cycles and 200 mA h g−1 at 1 A g−1 after 1000 cycles, corresponding to a high capacity retention rate of 83.8% compared to the 2nd cycle. This contribution presents a novel avenue for the exploitation of advanced multiphase anodes exhibiting superior capacity, rate capability, and cycling durability.
1. Introduction
The escalating requirements for efficient utilization of renewable energy sources have spurred huge advancements in electrical energy storage methodologies.1–5 Among these, sodium-ion batteries (SIBs) have emerged as promising alternatives to lithium-ion batteries (LIBs) due to their analogous electrochemical mechanisms and abundant resources.6–8 Substantial progress has been achieved in the realm of cathode electrodes, encompassing high-performance materials such as NaFePO4, Na2FeP2O7, Na3V2(PO4)3, Na4Fe3(PO4)2P2O7, Na3MnZr(PO4)3, and P2-Na0.67Ni0.33Mn0.67O2, eliciting considerable satisfaction.9–15 Nonetheless, a pressing challenge in the advancement of SIBs lies in the quest for suitable anodes that meet the requisites of prolonged cycling stability and high energy density.
Extensive research has focused on various materials, including phosphides,16–18 borides,19,20 carbides,21–23 nitrides,24–26 oxides,27–29 selenides30–32 and transition-metal sulfides33,34 as promising candidates for anodes in both LIBs and SIBs. Hybrid electrodes employing conversion-alloy reactions demonstrate superior and more robust overall performance than other types of anodes.35–39 Among these materials, transition metal-based sulfides are particularly promising due to their dual functionality in both electrochemical reactions, which enables them to perform effectively as anodes in both LIBs and SIBs.40,41 Yin et al. introduced a long-chain heterostructure comprising Co9S8 and SnS capable of generating abundant phase interfaces and small crystal domains. The distinctive structure facilitates electrochemical reactivity, conductivity, and ion diffusion rate. The combined effect of Co9S8/SnS heterostructures and the encapsulating carbon layer significantly enhances the energy storage capacity and cycling stability.42 As an anode electrode, the N-doped carbon (N-DC@(CoSn)S) delivers a high specific capacity of 820.6 mA h g−1 at 1.0 A g−1 after 500 cycles for LIBs and a capacity of 339.2 mA h g−1 at 0.5 A g−1 after 1000 cycles for SIBs. Additionally, Han et al. introduced Ti3C2Tx/CuS composites, which exhibited remarkable long-term stability, boasting a 347.0 mA h g−1 specific capacity post 800 cycles at 3 A g−1, alongside an outstanding rate capacity of 346.3 mA h g−1 at 8 A g−1.43 Despite extensive endeavors, numerous transition metal-based sulfides have grappled with challenges stemming from intricate fabrication methodologies. Moreover, the active components often experience phase transformation during repeated charging–discharging cycles. This phenomenon results in significant migration of sulfur compounds into the electrolyte, thereby negatively impacting the electrochemical stability.
There is an urgent necessity to develop advanced sulfides based on transition metals that can maintain high phase stability and achieve desirable electrochemical performance over extended cycling periods. Previous research has shown that carbon substrates effectively disperse heterojunction composites and enhance electrochemical stability.44–46 Moreover, the heterojunction effect facilitates electron transport between carbon and active materials. This architecture not only modulates the electronic structure of active sites but also generates an internal electric field to facilitate electron transfer, thereby improving electrode electrochemical performance. Therefore, the design of efficient and stable carbon-based heterojunction anodes for SIBs is critically important. Zhao et al. explored the fabrication and properties of a novel tri-phasic heterostructure, Fe3O4/Fe/FeS, doped with nitrogen on carbon nanotube scaffolds (FHNCS), synthesized using modified MIL-88B(Fe) as a template and employing catalytic growth and sulfurization techniques. Nitrogen-doped carbon facilitates electron transfer among the Fe3O4/Fe/FeS components, while the heterostructure promotes electron diffusion at the interfaces, establishing a conductive three-dimensional network. The unique scaffold structure enhances active site availability, reducing the diffusion path of sodium ions. Consequently, FHNCS demonstrates a high specific capacity of 436 mA h g−1 at 0.5 A g−1 and maintains a capacity retention rate of 73.4% after 1100 cycles at 1.0 A g−1.47 In another study, Luo et al. described the synthesis of Co9S8/MoS2/C composites. The results reveal unique electronic structures at the interfaces within the heterogeneous materials, highlighting their characteristic metallic natures with good electronic conductivity. Notably, the Co9S8/MoS2/C demonstrates the most stable structure and outstanding electrochemical property. The discharge capacity of Co9S8/MoS2/C-700 demonstrates full recovery from 368 mA h g−1 to 571 mA h g−1, stabilizing at 543 mA h g−1 as the current density is reduced from 4 A g−1 to 40 mA g−1.41
Presently, the fabrication of high-quality heterostructured transition metal sulfides often entails intricate procedures or specialized equipment, leading to elevated costs and restricted scalability. The establishment of a straightforward and environmentally sustainable synthesis approach for these materials is in line with the principles of green chemistry, facilitating decreased energy usage and reduced manufacturing expenses. This study investigates the synthesis of multiphase nanostructures of Ni–Sb–S using first-principles calculations based on density functional theory (DFT). Following this theoretical exploration, the compound was successfully synthesized from Sb2S3 and Ni starting materials. The resulting Ni–Sb–S formed a heterojunction-like structure, marking a significant advancement in anode composite research. This efficient two-step synthesis process enables the rapid scalability of Ni–Sb–S production, showcasing adaptability and promising applications across different fields. The selection of antimony (Sb) in this investigation arises from the underexplored realm of ternary compounds containing Sb for anode electrode studies, offering abundant prospects for exploration. Sb-based compounds exhibit a range of attributes such as superior electrical conductivity, exceptional thermal endurance, and interesting magnetic properties. These features render Sb-based materials highly sought-after for diverse technological uses encompassing catalysis, electronics, and energy storage.48–50
In order to enhance the heterojunction-like structure of Ni–Sb–S, the resulting powder underwent additional ball milling with graphite. This procedure yielded a distinctive hybrid material where Ni–Sb–S composites adhered to the surface of the exfoliated graphite, resulting in Ni–Sb–S/GN. As anticipated, both theoretical calculations and empirical findings validated that incorporating graphite nanosheets substantially improved the reaction kinetics of ternary Ni–Sb–S (i.e., products of 4 mol Ni react with 1 mol Sb2S3). Moreover, 4Ni–Sb–S/GN exhibited robust morphological stability throughout extended charge/discharge cycling. The as-synthesized 4Ni–Sb–S/GN demonstrated high initial coulombic efficiency (IEC) and exceptional rate performance. Notably, the 4Ni–Sb–S/GN anode electrodes delivered 200 mA h g−1 after 1000 cycles at 1 A g−1 while maintaining apparent stability. This facile and practical approach offers a new pathway for developing advanced anodes tailored for scalable energy conversion applications.
2. Experimental section
2.1 Materials and synthesis
Nickel powder and Sb2S3 were obtained from Mairel Biochemical Technology Co., LTD and used as received. The Gibbs free energy (ΔG) values for the reaction between Ni and Sb2S3 were calculated using density functional theory (DFT). Final energy/products for a series of reactants and variations in ΔG for various reactions are listed in Table S1† and eqn(1)–(22) as follows. | 2Ni + Sb2S3 = 2NiSbS + S, ΔG = −0.6442 eV | (1) |
| 2Ni + Sb2S3 = NiSbS + NiS2 + Sb, ΔG = −0.4697 eV | (2) |
| 3Ni + Sb2S3 = NiSbS + NiSb + NiS2, ΔG = −1.0115 eV | (3) |
|  | (4) |
|  | (5) |
| 4Ni + Sb2S3 = NiSbS + NiSb + 2NiS, ΔG = −1.6753 eV | (6) |
| 4Ni + Sb2S3 = NiSbS + Ni3S2 + Sb, ΔG = −1.5530 eV | (7) |
| 4Ni + Sb2S3 = NiSb2 + 3NiS, ΔG = −1.4977 eV | (8) |
|  | (9) |
|  | (10) |
|  | (11) |
| 5Ni + Sb2S3 = NiSbS + Ni3Sb + NiS2, ΔG = −1.0629 eV | (12) |
| 5Ni + Sb2S3 = NiSbS + NiSb + Ni3S2, ΔG = −2.0948 eV | (13) |
|  | (14) |
| 6Ni + Sb2S3 = Ni3Sb + 3NiS + Sb, ΔG = −1.4986 eV | (15) |
|  | (16) |
|  | (17) |
| 7Ni + Sb2S3 = NiSbS + Ni3Sb + Ni3S2, ΔG = −2.1462 eV | (18) |
|  | (19) |
| 8Ni + Sb2S3 = Ni5Sb2 + 3NiS, ΔG = −2.0986 eV | (20) |
|  | (21) |
|  | (22) |
Typically, a lower ΔG indicates a more favorable chemical reaction. These analyses reveal that nickel (Ni) can react with antimony trisulfide (Sb2S3) to form NixSbySz, NiaSbb, and NimSn hybrids by adjusting their molar ratios, thus enabling the synthesis of various Ni–Sb–S alloys and compounds. It is noteworthy that eqn (3)–(6), eqn (8)–(14), and eqn (16)–(22) indicate the potential to yield NixSbySz, NiaSbb, and NimSn hybrids (x, y, z, a, b, m, n are coordination number, respectively, based on their ΔG values.
The schematic of Ni–Sb–S/GN synthesis is shown in Fig. 1. Firstly, Ni and Sb2S3 were mixed in a quartz tube at mole ratios of 3
:
1 and 4
:
1, and then the tube was evacuated. The quartz tube was subsequently heated to 600 °C at a rate of 5 °C min−1 in a tube furnace and maintained at this temperature for 6 h. After cooling down to room temperature, the resulting samples were ground. Four different products were obtained and subjected to XRD measurements. Specifically, the Ni–Sb–S compounds were synthesized by mixing Ni and Sb2S3 in a 4
:
1 molar ratio (eqn (6)), chosen for the completion of reaction and minimum ΔG value. The mixture was then ball-milled with 15 wt% graphite at 900 rpm for 10 h to produce Ni–Sb–S/GN. Briefly, Ni and Sb2S3 ground in mole ratios of 3
:
1 and 4
:
1 are labeled as 3Ni–Sb–S/GN and 4Ni–Sb–S/GN in the following discussion.
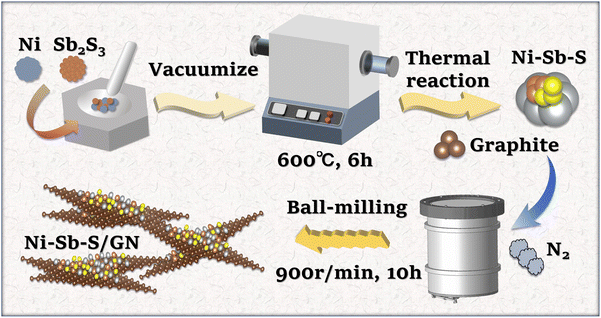 |
| Fig. 1 Schematic of the synthesis procedure of Ni–Sb–S/GN. | |
2.2 Material characterizations
The X-ray diffractometer (D8 ADVANCE, XRD) was employed to characterize the crystal structure and purity of the prepared samples. Cu Kα radiation served as the diffraction source, and measurements were conducted within the 2θ angle range of 10–80°. Operating at 40 kV and 40 mA, the instrument provided accurate analysis. Surface valence states were examined using X-ray photoelectron spectroscopy (XPS) via the PHI 5000 instrument. Morphology and structural analysis were performed using the ultra-high resolution field emission SEM (Nova 200 NanoSEM) and TEM (JEM-2100F).
2.3 Electrode preparation and electrochemical performance evaluation
After blending the composites with sodium carboxymethyl cellulose and acetylene black in an 8
:
1
:
1 mass ratio, deionized water is introduced and stirred for 2 h to form a paste. This paste is then applied onto copper foils, followed by drying in a vacuum oven. The dried, coated copper foils are cut into 12 mm diameter discs for use as anodes, ensuring an electrode mass loading of 1.5 ± 0.1 mg cm2. These electrodes are transferred into a glove box filled with Ar gas to maintain water and oxygen levels below 0.5 ppm and 1 ppm, respectively. A CR2032 coin cell is assembled using an electrolyte consisting of 1.0 M NaPF6 in a 1
:
1
:
1 volume ratio of EC
:
DMC
:
EMC, with a 5.0% FEC additive (Keluder). Whatman GF/D glass paper discs serve as separators. Subsequent analyses involve cyclic voltammetry performed on an EC-100B electrochemical workstation, alongside evaluations of charge/discharge characteristics, rate capability, and galvanostatic intermittent titration technique (GITT) using a LAND battery tester.
2.4 Theoretical calculations
The study employed several computational tools and methods: VASP software for molecular dynamics (MD) simulations, work function, and charge density difference calculations; CASTEP (academic version) for band-structure calculations; and VESTA for structure visualization. Initial CIFs were sourced from the Materials Project website for DFT calculations, with structures optimized geometrically beforehand. The generalized gradient approximation (GGA) method Perdew–Burke–Ernzerhof (PBE) function was used to describe the electron exchange effects. Gibbs free energy of the reactions' formula calculations relied on crystal final energy per atom data from the Materials Project website. Self-consistent field (SCF) calculations were conducted with a cut-off energy of 520 eV and convergence criterion of 1 × 10−5 eV. Charge density differences were assessed by first computing the SCF of the AB structure, followed by extracting SCFs for segments A and B. Band structures were computed using the GGA-PBE method with a 0.06 eV K-point grid resolution. In MD simulations, the gamma point was selected for K-point sampling.
3. Results and discussion
The XRD patterns of reacted nNi
:
Sb2S3 (n = 3, 4) are presented in Fig. 2a and b. The product obtained from the 2
:
1 reaction, NiSbS + S, as per eqn (1), shows a minor sulfur volatilization. The synthesis of Ni–Sb–S/GN has consistently followed a fundamental principle: zero loss of raw materials, achieving 100% utilization efficiency. The sulfur loss in the 2
:
1 reaction, as indicated in eqn (1), highlights suboptimal conditions. Three-component phases consisting of NiSbS/NiSb/NiS2 and NiSbS/NiSb/NiS were obtained at 3
:
1 and 4
:
1 ratios of Ni to Sb2S3. All diffraction peaks of the 3Ni–Sb–S/GN crystals corresponded well with the standard NiSbS (PDF#41-1472), NiSb (PDF#41-1439), and NiS2 (PDF#89-1495) phases. All diffraction peaks of the 4Ni-Sb-S/GN crystals corresponded well with the standard NiSbS (PDF#41-1472), NiSb (PDF#41-1439), and NiS (PDF#77-1624) phases. This suggests that 3
:
1 and 4
:
1 molar ratios are optimal for obtaining the desired Ni–Sb–S active material with 100% raw material utilization, where high-purity NiSbS/NiSb/NiS2/GN and NiSbS/NiSb/NiS/GN crystals were obtained through vacuum-heating and ball-milling treatments.
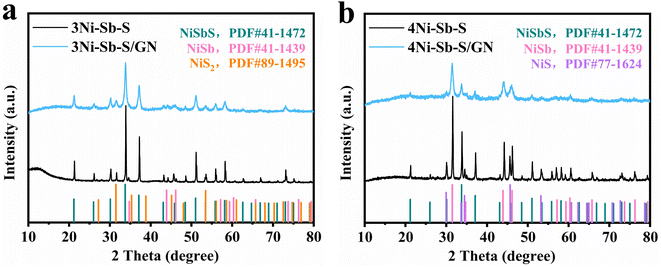 |
| Fig. 2 XRD patterns of (a) 3Ni–Sb–S and 3Ni–Sb–S/GN; (b) XRD patterns of 4Ni–Sb–S and 4Ni–Sb–S/GN. | |
Research indicates that NiS2 shows lower reversibility as an anode material in SIBs compared to NiS. Electrodes were fabricated using 3Ni–Sb–S/GN, and their charge–discharge capacities and stability were measured at 1 A g−1, as depicted in Fig. S1a and S1b.† The 3Ni–Sb–S/GN only delivered 29.4 mA h g−1 post 1000 cycles and displays poor stability. Therefore, it is expected that 4Ni–Sb–S/GN will exhibit improved reversible capacity and better cycling stability. Given the significant impact of structure on performance, an in-depth structural analysis of 4Ni–Sb–S/GN was conducted. The dimensions of the 4Ni–Sb–S composite witnessed notable changes following mixed ball milling with graphite. Prior to milling, the 4Ni–Sb–S particles were relatively large in size, measuring several micrometers, and exhibited a smooth surface (Fig. 3a). However, the 4Ni–Sb–S/GN composite, obtained via ball milling, displayed smaller and more uniformly distributed particles within graphite nanosheets (Fig. 3b). This milling process was intentionally carried out to enhance the dispersion of 4Ni–Sb–S on the graphene surface. Consequently, the composite material became firmly attached to the graphite nanosheets after milling, establishing close contact and improved adhesion to the graphite nanosheets, ultimately leading to enhanced material dispersion. This enhancement is anticipated to boost the performance of the composites.
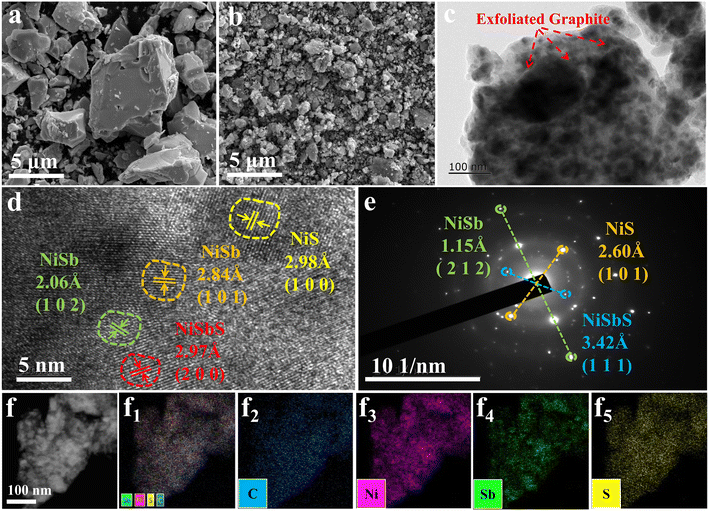 |
| Fig. 3 SEM images of (a) 4Ni–Sb–S, (b) 4Ni–Sb–S/GN; (c and d) TEM images of 4Ni–Sb–S/GN; (e) SAED images of 4Ni–Sb–S/GN; (f and f1) elemental distribution mapping images of (f2) C, (f3) Ni, (f4) Sb and (f5) S elements in 4Ni–Sb–S/GN. | |
The specific surface areas of 4Ni–Sb–S, 4Ni–Sb–S/GN, and ball milled graphite were determined using the Brunauer–Emmett–Teller (BET) method, as shown in the N2 adsorption/desorption curves in Fig. S2.† 4Ni–Sb–S, 4Ni–Sb–S/GN, and ball milled graphite exhibit nearly non-porous structures. The specific surface area of 4Ni–Sb–S is only 0.4 m2 g−1. In contrast, after ball milling, the specific surface area of the 4Ni–Sb–S/GN composite significantly increased to 14.8 m2 g−1. Furthermore, the graphite that was solely ball milled exhibited an impressive specific surface area of 154.4 m2 g−1. The results indicate that the high specific surface area of the exfoliated graphite achieved through ball milling provides ample attachment sites for 4Ni–Sb–S.
The TEM and SAED results of 4Ni–Sb–S/GN are displayed in Fig. 3c–e, confirming the successful synthesis of multiphase nano-crystal 4Ni–Sb–S species. The TEM images revealed that the nano-crystal 4Ni–Sb–S was enclosed within the graphite layers, indicating that both 4Ni–Sb–S and graphite were pulverized into nanoscale dimensions during ball milling. Furthermore, the high-resolution TEM image of 4Ni–Sb–S/GN in Fig. 3d revealed clear lattice fringes, indicating d-spacing values of 2.97 Å corresponding to the (2 0 0) crystal plane of NiSbS. Additionally, d-spacing values of 2.06 Å and 2.84 Å were observed for the (1 0 2) and (1 0 1) planes of NiSb, while a d-spacing value of 2.98 Å matched the (1 0 0) plane of NiS. The bright dot ring-like arrangement of the electron diffraction points in the SAED pattern (Fig. 3e) indicated the crystallinity of NiSbS/NiSb/NiS. Elemental distribution mapping images of 4Ni–Sb–S/GN composites are presented in Fig. 3f, showcasing the well distributed C, Ni, Sb, and S elements.
To further investigate the changes in graphite exfoliation during the synthesis of 4Ni–Sb–S/GN composites, Raman spectroscopy was performed on samples ball milled for 2, 4, 6, 8, and 10 hours. In a Raman spectrum, the D bands and G bands correspond to defects on the ab planes and the graphitic structure, respectively. The presence of these bands is closely related to the degrees of graphitization and local disorder.51,52 As shown in Fig. S3,† 4Ni–Sb–S does not exhibit the characteristic D bands and G bands of graphite, as no graphite was added. As the ball milling time increased, the changes in the ID/IG ratio of 4Ni–Sb–S/GN reflected the extent of graphite exfoliation in the material. The coherence length La, which quantitatively describes the structural order on the ab planes, is calculated according to eqn (23):53
| 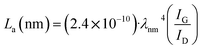 | (23) |
Here,
λ is the Raman laser wavelength.
Specifically, after 2 hours of ball milling, the ID/IG ratio was 0.771, and the coherence length La was 24.89 nm. After 4 hours of ball milling, the ID/IG ratio slightly increased to 0.779, and the coherence length decreased to 24.68 nm, indicating the presence of some graphitic regions in the material. As the ball milling time increased to 6 hours, the ID/IG ratio further increased to 0.893, and the coherence length decreased to 21.55 nm. After 8 hours of ball milling, the ID/IG ratio significantly increased to 1.156, and the coherence length decreased to 16.61 nm, indicating increased disorder and a further reduction in graphitization. Finally, after 10 hours of ball milling, the ID/IG ratio slightly increased to 1.182, and the coherence length remained at 16.24 nm. The reduction in coherence length suggests a decrease in crystallinity along the ab planes. This change confirms that prolonged ball milling gradually damages the ordered structure within the graphite layers, weakening the interlayer bonding forces, leading to exfoliation. It is worth noting that Raman testing on the graphite before and after ball milling showed that the ID/IG ratio of the un-milled graphite was 0.129 with a high coherence length, indicating its excellent graphitic properties. In contrast, the ID/IG ratio of the ball milled graphite increased to 0.955, with the coherence length decreasing to 20.12 nm, further indicating significant exfoliation and structural changes during the ball milling process. In 4Ni–Sb–S/GN, the 4Ni–Sb–S particles act as dispersants for the exfoliated graphite. Consequently, the coherence length of the graphite in 4Ni–Sb–S/GN is much lower than that of the pure ball-milled graphite.
The CV profiles for 4Ni–Sb–S and 4Ni–Sb–S/GN composite electrodes are depicted in Fig. 4a and b. It is crucial to note that incorporating carbon into the electrode markedly influences the morphology of the redox peaks in the CV profiles. Therefore, 4Ni–Sb–S was selected as the benchmark for analysis to reduce interference in charge and discharge evaluations. In the 1st and 2nd scans, irreversible reactions were observed, but the irreversible reactions were less prevalent in following scans. Consequently, the 3rd and 4th scans were utilized to analyze the charge/discharge behaviors. Na-ion storage mechanisms in 4Ni–Sb–S anodes are delineated as follows: significant research indicates that the NiS phase is reversible with a reduction/oxidation peak at approximately 0.9–0.95/1.63–1.65 V. The initial reaction between NiSbS and sodium also produces Na2S and NiSb at 0.9–0.95 V, marking this as the reduction peak for both NiSbS and sodium forming Na2S and resulting in the simultaneous generation of Ni. Upon reduction from 0.9 V to 0 V, NiSb converts to Ni and Na3Sb at 0.5–0.56 V.54 To further substantiate the outlined discharge process, Gibbs free energy calculations and the theoretical discharge voltages for each step were computed and are presented as eqn (24)–(26).
| 0.9–0.95 V: NiS + 2Na → Ni + Na2S, ΔG = −2.4941 eV, ΔE = 1.24705 V | (24) |
| NiSbS + 2Na → NiSb + Na2S, ΔG = −2.8078 eV, ΔE = 1.4039 V | (25) |
| 0.5–0.56 V: NiSb + 3Na → Ni + Na3Sb, ΔG = −1.2022 eV, ΔE = 0.4007 V | (26) |
 |
| Fig. 4 CV curves of (a) 4Ni–Sb–S and (b) 4Ni–Sb–S/GN. | |
ΔE represents the average reaction voltage calculated from ΔG given by ΔE = |−ΔG|/nF, n represents the number of electrons transferred, and F is the Faraday constant. Despite minor discrepancies between the theoretical calculations and experimental test voltages, the sodiation/de-sodiation order between 4Ni–Sb–S and Na was clarified: eqn (25) → eqn (24) → eqn (26) upon discharging and eqn (26) → eqn (24) → eqn (25) upon charging. Specifically, the reduction peak located at 0.9–0.95 V was a combined reaction of eqn (24) and eqn (25). The theoretical calculations and analyses were consistent with experimental findings, showing that the reduction peaks at 0.9–0.95 V could be ascribed to 4 Na and those at 0.5–0.56 V to 3 Na. After the ball-milling process that forms 4Ni–Sb–S/GN from 4Ni–Sb–S and graphite, it's notable that the oxidation-reduction peaks in eqn (26) significantly broaden. This effect arises because ball milling crushes the layered structure of NiSb into very small nanoparticles or even near-amorphous states, reducing the lattice energy of NiSb and widening the CV peaks. Such phenomena are commonly observed in SIBs anode materials.
S. Sarkar et al. demonstrated the partial reversibility of CoSb when used as an anode material for SIBs.55 Herein, the significant similarity between NiSb and CoSb suggests that NiSb may also exhibit partial reversibility. To further verify the charge/discharge mechanisms, 4Ni–Sb–S was tested by ex situ XRD (Fig. S4†). It can be observed that the strong peaks of Na2S and NiSb are present when initially discharged to 0.6 V, discharged to 0 V, and discharged to 0 V again, followed by charged to 1 V. When discharged to 0 V and recharged to 3 V, the Na2S vanished, and NiSb was still detected, proving that Na2S, NiSbS, and NiS are fully reversible, whereas NiSb is partially reversible. This result confirms that NiSb shares significant similarity with CoSb, also exhibiting partial reversibility.
As NiSbS and NiS were not observed by ex situ XRD, to further understand the detailed structure during the charge/discharge process of 4Ni–Sb–S/GN and to confirm the reversibility of NiSbS and NiS, the TEM images of the anode electrode that was discharged to 0 V, followed by charged to 3 V were obtained (Fig. 5 and S5†). As seen in Fig. S5a, b, d and e,† smaller nanoparticles can be clearly observed in the electrode sheets, with particle sizes ranging from 10 to 200 nm. High-angle annular dark field imaging and elemental distribution images ( Fig. 5a, a1–7, d and d1–7) confirm the phase separation within the particles, showing a very uniform elemental distribution, which indicates good dispersion of the materials, facilitating rapid Na+ diffusion. Moreover, in the high-resolution TEM images, the presence of Ni, Na2S, and Na3Sb was observed when discharged to 0 V (Fig. 5b); upon discharging to 0 V and recharging to 3 V (Fig. 5c), the presence of NiSbS, NiSb, and NiS was observed. Additionally, in the SAED patterns of Fig. S5c and f,† the diffraction spots of these materials were confirmed and identified, providing strong evidence for the reversibility of NiSbS and NiS. The TEM observation of the materials was consistent with the charge/discharge mechanism analysis, which further proved the charge/discharge mechanism of the materials.
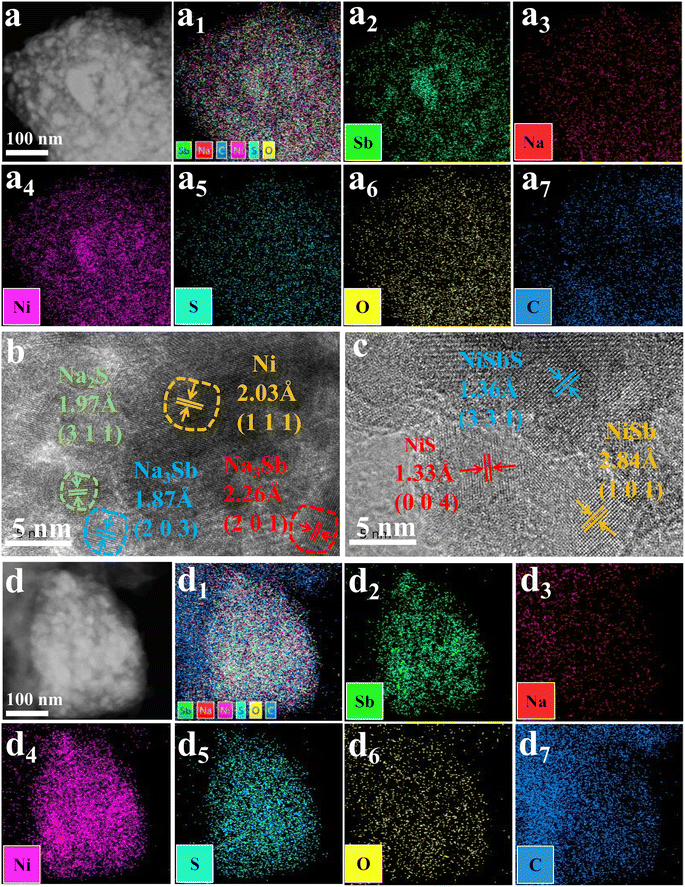 |
| Fig. 5 (a and a1–7) TEM and the corresponding elemental distribution mapping images of 4Ni–Sb–S/GN electrode after discharging to 0 V; (b) TEM image of 4Ni–Sb–S/GN electrode after discharging to 0 V; (c) TEM image of 4Ni–Sb–S/GN electrode after discharging to 0 V followed by charging to 3 V; (d and d1–7) the corresponding elemental distribution mapping images of 4Ni–Sb–S/GN electrode after discharging to 0 V followed by charging to 3 V. | |
The charge/discharge curves of 4Ni–Sb–S and 4Ni–Sb–S/GN under 0.2 A g−1 are presented in Fig. S6a and b.† Notably, the capacity of 4Ni–Sb–S/GN at 0.2 A g−1 was lower than that of its 4Ni–Sb–S counterparts, with 331.2, 249.8, 245.2, 242.8, and 242.1 mA h g−1 at the 1st – 5th cycles for 4Ni–Sb–S/GN. It is important to note that while the contribution of graphite to the effective mass of 4Ni–Sb–S/GN reduced the discharge specific capacity, it significantly improved its cyclic stability following. The initial coulombic efficiency of the 4Ni–Sb–S/GN electrode was an impressive 76.8%. Additionally, the voltage plateaus during charging and discharging in the 4Ni–Sb–S electrodes closely corresponded to the peaks observed in the cyclic voltammetry (CV) profiles associated with oxidation and reduction, respectively.
The cycling property of 4Ni–Sb–S/GN electrodes was evaluated via charge/discharge test under 0.2 A g−1 (Fig. 6a). The electrodes achieved a capacity of 331.2 mA h g−1 and retained 238.7 mA h g−1 at the 300th cycle; the capacity retention ratio reached 95.6% at the 2nd cycle (249.8 mA h g−1). In contrast, 4Ni–Sb–S electrodes exhibited higher initial discharge capacity (429.0 mA h g−1) but experienced rapid decay, particularly after the 20th cycle. The charge/discharge curves of 4Ni–Sb–S and 4Ni–Sb–S/GN electrodes are illustrated in Fig. 6b. Remarkably, the voltage plateau of 4Ni–Sb–S/GN was distinctly visible at each rate cycling, whereas it gradually became less defined for 4Ni–Sb–S. Rate performance tests are presented in Fig. 6c for both 4Ni–Sb–S and 4Ni–Sb–S/GN electrodes and the corresponding coulombic efficiencies are shown in Fig. S7.† 4Ni–Sb–S/GN exhibited reversible discharge capacities of 260.7, 236.3, 215.1, 194.0, 168.1, 137.4, 116.1, 103.8, and 93.0 mA h g−1 at 0.1 (5th), 0.2 (10th), 0.5 (15th), 1.0 (20th), 2.0 (25th), 4.0 (30th), 6.0 (35th), 8.0 (40th), and 10.0 A g−1 (45th), respectively. Notably, when the current density decreased to 1.0 and 0.1 A g−1 from 10 A g−1, 4Ni–Sb–S/GN exhibited rapid recovery to high values of 199.8 and 263.0 mA h g−1. It was observed that the coulombic efficiency fluctuates significantly during changes in current density, particularly during the 47th and 52nd cycles. This fluctuation is due to the time required for the electrode's chemical reactions and ion diffusion processes to adjust to the new conditions when the current density is altered, resulting in a variation in coulombic efficiency. The 4Ni–Sb–S/GN demonstrated a significantly more stable rate capability compared to 4Ni–Sb–S. The rate capability of 4Ni–Sb–S/GN electrodes compared to some of the previously reported Co-, Ni-, Fe-, Sn-, and Bi-based anodes for SIBs is shown in Fig. 6d.55–64
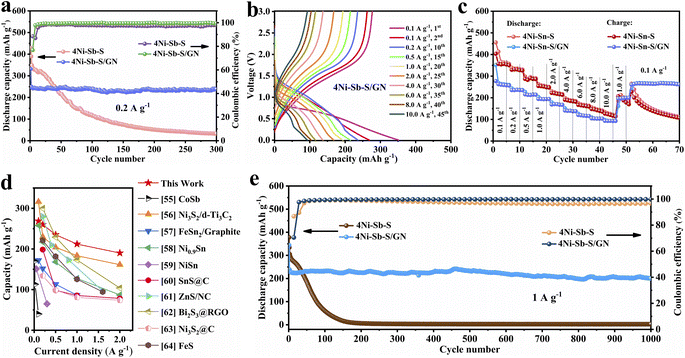 |
| Fig. 6 (a) Cycling stabilities of 4Ni–Sb–S and 4Ni–Sb–S/GN at a current density of 0.2 A g−1; (b) galvanostatic charge/discharge profiles of 4Ni–Sb–S/GN; (c) rate performances of 4Ni–Sb–S and 4Ni–Sb–S/GN; (d) comparison of rate performance with reported literature; (e) cycling stabilities of 4Ni–Sb–S and 4Ni–Sb–S/GN at 1.0 A g−1. | |
The long cycling performance and discharge/charge profiles of 4Ni–Sb–S and 4Ni–Sb–S/GN composites under 1.0 A g−1 are depicted in Fig. 6e, S1c and d.† The 4Ni–Sb–S electrodes exhibited rapid capacity fading during repeated charge/discharge cycles, attributed to low electrical conductivity. In contrast, the 4Ni–Sb–S/GN electrodes delivered 344.5 mA h g−1 at the 1st cycle and displayed 200.0 mA h g−1 at the 1000th cycle; the capacity retention ratios of the 1000th cycle reached 83.8% of the capacity of the 2nd cycle, and the initial coulombic efficiency reached 70.47%. 4Ni–Sb–S/GN exhibited high capacity and superior capacity retention compared to 4Ni–Sb–S. Additionally, our previous experiments indicate that the exfoliated graphite delivered 149.1 mA h g−1 at the 500th cycle at 1 A g−1. Given that exfoliated graphite nanosheets constitute 15 wt% of the 4Ni–Sb–S/GN composite, their contribution to the total capacity was about 22.4 mA h g−1,46 significantly less than the 232.4 mA h g−1 from 4Ni–Sb–S/GN. This indicates the main functions of the exfoliated graphite in electrode materials are to enhance the electrical conductivity, improve the structural stability, and accelerate the Na+ transport. Excitingly, compared to previously reported high-capacity Ni3Bi2S2/NiS nanocomposites anchored with graphite nanosheets and NiS/carbon composites,46,65 the results of this study demonstrate superior capacity retention and reversibility. The cycling stability was improved to 1000 cycles, with a capacity retention of 83.8% starting from the second cycle.
To further investigate the mechanism for the significant changes in cycling stability of the 4Ni–Sb–S electrode after the addition of graphite, SEM was employed to observe the original electrodes of 4Ni–Sb–S and 4Ni–Sb–S/GN, as well as the evolution of the electrodes after 1000 cycles at 1.0 A g−1. As shown in Fig. S8a and c,† neither of the original electrodes exhibited cracks. After undergoing 1000 cycles, cracks of several micrometers can be detected (Fig. S8b and d†), although the cracks in the 4Ni–Sb–S/GN electrode were significantly smaller than those in the 4Ni–Sb–S electrode and the particle size of 4Ni–Sb–S/GN was also smaller. This indicates that the mixed ball milling of the 4Ni–Sb–S composite with graphite enhanced the cycling stability of the electrode.
Fig. 7a and b illustrate the rate-dependent CV curves for 4Ni–Sb–S and 4Ni–Sb–S/GN. As the scanning rate increased, small peak shifts in 4Ni–Sb–S and 4Ni–Sb–S/GN were observed, indicating reduced polarization and enhanced electrochemical reaction stability in 4Ni–Sb–S/GN. This attribute is essential for ensuring stable reversibility and enhancing reaction kinetics. To gain a deeper understanding, the diffusion/capacitance control ratio of Na+-storage was calculated based on eqn (27) and (28).39
| log(i) = b log(v) + log(a) | (28) |
Here, ‘
a’ and ‘
b’ are adjustable parameters, and a ‘
b’ value equal to 0.5 represents diffusion-controlled processes, while a ‘
b’ equal to 1.0 represents capacitive-controlled processes.
Fig. 7c and d show that the ‘
b’ values of the 4Ni–Sb–S and 4Ni–Sb–S/GN range from 0.5 to 1.0, suggesting a mixed sodium storage mode of diffusion-controlled and capacitive-controlled processes. Moreover, the diffusion-controlled part and capacitive-controlled part of the Na
+-storage capacity can be divided by
eqn (29):
46In the given formula,
i(
V) is the current density at the oxidation or reduction peak voltage, and
k1v and
k2v0.5 correspond to the ratios of the capacitive-controlled part and the diffusion-controlled part. The capacitive and diffusion contributions for both 4Ni–Sb–S and 4Ni–Sb–S/GN across various scan rates are shown in
Fig. 7e and f. The capacitive-controlled ratios for 4Ni–Sb–S and 4Ni–Sb–S/GN increased with the scan rate, reaching 65.7% and 87.3%, respectively, at 1.0 mV s
−1. Notably, the 4Ni–Sb–S/GN electrode consistently exhibited a higher capacitive contribution than 4Ni–Sb–S, suggesting that its greater surface capacitance dominance enhances electrochemical reactions and improves rate performance. Furthermore, the GITT results for both composites are presented in
Fig. 7g, where the sodium-ion diffusion coefficient
DNa+ was calculated using
eqn (30), based on charge/discharge times of 10 minutes and 30 minutes, respectively.
| 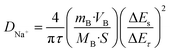 | (30) |
in the equation,
mB is the mass loading of the 4Ni–Sb–S in the electrode,
VB/
MB is the density of 4Ni–Sb–S, and
τ is the interspersed time between two adjacent titrations.
Fig. 7h and i indicate that the sodium-ion diffusion coefficient
DNa+ of 4Ni–Sb–S/GN across all voltage ranges is significantly higher—by two orders of magnitude—than that of the 4Ni–Sb–S. This enhancement suggests that the addition of graphite nanosheets substantially increases the
DNa+ in 4Ni–Sb–S/GN hybrids, contributing to their superior cycling performance.
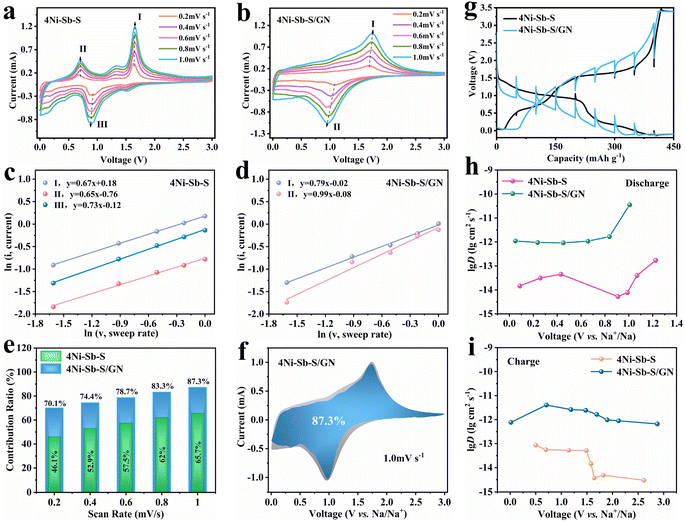 |
| Fig. 7 The rate-dependent CV curves for (a) 4Ni–Sb–S and (b) 4Ni–Sb–S/GN; the calculated b values for (c) 4Ni–Sb–S and (d) 4Ni–Sb–S/GN; the capacitive-controlled ratios for (e) 4Ni–Sb–S and 4Ni–Sb–S/GN; the capacitive-controlled ratios at 1.0 mV s−1 for (f) 4Ni–Sb–S/GN; the GITT curves for (g) 4Ni–Sb–S and 4Ni–Sb–S/GN; and the DNa+ curves during the charge (h) and discharge (i) processes for both 4Ni–Sb–S and 4Ni–Sb–S/GN. | |
To further investigate the superior electrochemical behavior of 4Ni–Sb–S/GN, electrochemical impedance spectroscopy (EIS) was performed, comparing the Nyquist plots of the 4Ni–Sb–S and 4Ni–Sb–S/GN electrodes before and after 100 cycles at voltages of 3, 2.5, 2, 1.5, 1, 0.5, and 0 V. As shown in Fig. S9,† the semicircle displayed by the 4Ni–Sb–S/GN electrode in the high-frequency region before cycling is significantly smaller than that of the 4Ni–Sb–S electrode. Additionally, the charge transfer resistance (Rct, approximately equal to the diameter of the semicircle in the high-frequency region) for 4Ni–Sb–S/GN decreased further to below 80 Ω after 100 cycles. In contrast, the Rct of the 4Ni–Sb–S electrode was approximately 200–400 Ω before cycling and remained around 200 Ω after 100 cycles, which is much higher than that of 4Ni–Sb–S/GN, indicating slower charge transfer. Therefore, the impedance of 4Ni–Sb–S/GN is much lower than that of 4Ni–Sb–S, suggesting that sodium ion diffusion within 4Ni–Sb–S/GN is faster, which is attributed to the reduced particle size after ball milling. Furthermore, in the low-frequency range, the slope of the inclined line reflects the diffusion speed of sodium ions in the battery. A steeper slope indicates faster diffusion of sodium ions. The slope of 4Ni–Sb–S/GN is greater than that of 4Ni–Sb–S, which further confirms the superior electrochemical performance of 4Ni–Sb–S/GN.
The band gap values for Sb2S3, NiSbS, NiSb, and NiS were found to be 1.318, 0, 0, and 0 eV, as shown in Fig. S10.† Those results indicate the enhanced electronic conductivity of NiSbS, NiSb, and NiS compared to Sb2S3. Na+ adsorption models were constructed on NiS, NiSb, NiSbS, NiS/GN, NiSb/GN, and NiSbS/GN. As shown in Fig. 8a–c, the model describes the adsorption of Na+ on the hollow site. It is worth noting that the Na+ adsorption energies of NiS/GN, NiSb/GN, and NiSbS/GN are −2.267, −1.612, and −2.348 eV, respectively, while the Na+ adsorption energies of NiS, NiSb, and NiSbS are −2.162, −1.535, and −1.932 eV, respectively, which indicates that the electrodes with added graphite exhibit more stable adsorption phenomena. Additionally, to simulate the Na+ adsorption environment during the use of the electrode material, the effects of solvent (EC: DMC: EMC) on Na+ adsorption were considered, as shown in Fig. S11.† After the addition of electrolyte solvent molecules, the Na+ adsorption energies of NiS/GN, NiSb/GN, and NiSbS/GN were −2.395, −1.884, and −1.981 eV, respectively, while the Na+ adsorption energies of NiS, NiSb, and NiSbS were −1.809, −1.678, and −1.721 eV, respectively. The computational results indicate that the presence of exfoliated graphite enhances the wettability of the electrolyte towards the electrode materials. Charge density differences for NiSbS/GN, NiSb/GN, and NiS/GN are illustrated in Fig. 8d–f, as calculated using eqn (31).
in this context, ρ denotes the charge density within the structure. Yellow denotes charge accumulation, while light blue indicates charge dissipation. The yellow lines connecting two atoms signify strong electrostatic interactions, indicating the formation of a chemical bond. The interaction of electron clouds between NiSbS, NiSb, and NiS species and graphite nanosheets is evident, indicating the formation of chemical bonds in the NiSbS/GN, NiSb/GN, and NiS/GN components. This interaction is advantageous for dispersing and anchoring the active species onto graphite. Moreover, the electronic escape energies of NiSbS, NiSb, NiS, and GN were determined using
eqn (32) according to the (Fig. S12
†) TEM images [(0 0 1) for GN, (1 1 1) and (2 0 0) for NiSbS, (1 0 1), (1 0 2) and (2 1 2) for NiSb, (1 0 0) and (1 0 1) for NiS]. These calculations aim to elucidate the interactions of electron clouds. As shown in
Fig. 8g, variations in work function values among graphite, NiS, NiSb, and NiSbS highlight the ease of electron transfer when two different phases make contact, promoting chemical bond formation. Notably, the electronic escape energies for NiSbS and NiSb were lower than that for graphite. A lower electronic escape energy suggests higher metallic or electronic conductivity characteristics, facilitating rapid electron transmission. Due to varying contact surface work functions, electron transfer facilitates the formation of chemical bonds. Robust chemical bonds develop between NiSb, NiSbS, NiS, and GN, securely anchoring NiSb, NiSbS, and NiS onto the surface of GN flakes. Even after numerous charge–discharge cycles, NiSb, NiSbS, and NiS maintain excellent dispersion.
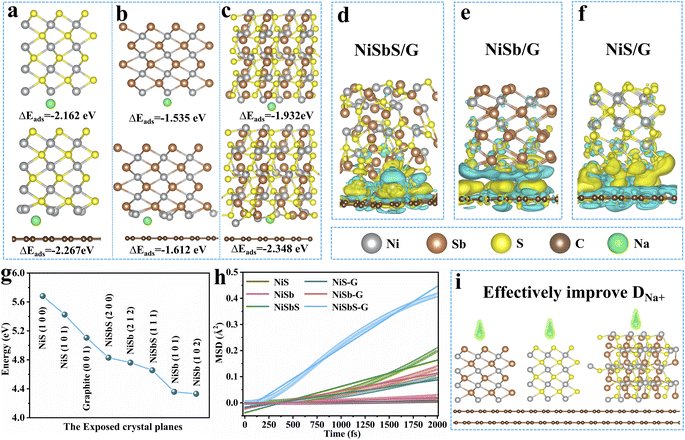 |
| Fig. 8 Adsorption models and energies of (a) NiS, NiS/GN, (b) NiSb, NiSb/GN, and (c) NiSbS, NiSbS/GN; the charge-density differences for (d) NiSbS/GN, (e) NiSb/GN, and (f) NiS/GN; the work functions of (g) exfoliated graphite, NiSbS, NiSb, and NiS; the mean square displacements (MSD) of Na in (h) NiSbS, NiSb, NiS, NiSbS/GN, NiSb/GN, and NiS/GN; and (i) a schematic illustrating the internal linkages among active materials. | |
To further investigate whether Ni–Sb–S interact with exfoliated graphite, XPS was carried out (Fig. S13†). The examination proves that no oxidation occurred on 4Ni–Sb–S and 4Ni–Sb–S/GN, indicating that the materials have high purity. Using the C 1s spectrum as the reference peak, it was observed that the spectral positions of Sb 3d and Ni 2p in 4Ni–Sb–S/GN shifted significantly towards higher binding energies compared to 4Ni–Sb–S. This indicates that Ni–Sb–S indeed interact strongly with graphite, thus confirming that they are anchored onto the exfoliated graphite. As a supplement, to further confirm the interactions between graphite nanosheets and the NiSbS, NiSb, and NiS components, NiSbS, NiSb, and NiS were synthesized separately, and the composites NiSbS/GN, NiSb/GN, and NiS/GN were prepared using the same ball milling process. XRD analysis confirmed the successful synthesis of the materials (Fig. S14a, S15a and S16a†), and XPS measurements were performed on these electrode materials. The test results show that, as seen in Fig. S14b–e, S15b–e and S16b–f,† the spectral positions of Ni 2p and S 2p in NiS/GN shifted significantly compared to those in NiS. The same phenomenon was observed in NiSb/GN and NiSb, and NiSbS/GN and NiSbS, respectively. Additionally, in the S 2p spectrum of NiS/GN, peaks at 163.36 eV and 164.66 eV were observed, indicating the presence of C–S bonds. These results indicate that strong interactions occurred between the graphite nanosheets and the NiSbS, NiSb, and NiS components.
Additionally, the DNa+ for species such as NiSbS, NiSb, NiS, NiSbS/GN, NiSb/GN, and NiS/GN were calculated through molecular dynamics simulations, with DNa+ determined using eqn (33).
| 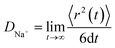 | (33) |
Here,
Ev is the surface vacuum energy level,
EF is the Fermi energy level, and 〈
r2(
t)〉/
t represents the slope of the mean squared displacement (MSD). According to
Fig. 8h, the
DNa+ values for NiSbS, NiSb, NiS, NiSbS/GN, NiSb/GN, and NiS/GN were found to be 1.681 × 10
−5 cm s
−1, 1.998 × 10
−6 cm s
−1, 7.144 × 10
−7 cm s
−1, 2.936 × 10
−5 cm s
−1, 1.136 × 10
−5 cm s
−1, and 8.715 × 10
−6 cm s
−1, respectively. The discrepancy between the theoretically calculated
DNa+ and experimentally tested values, which spans several orders of magnitude, arises because theoretical models assume perfect crystal structures (Fig. S17
†), whereas actual crystals have defects. Nonetheless, these do not impede the assessment of relative Na-ion diffusion speeds across different materials. It is important to highlight that the
DNa+ values for species with incorporated graphite were notably higher than their non-graphite counterparts, likely due to the negatively charged graphite attracting the Na
+. The interaction of NiSb, NiSb, and NiS with exfoliated graphite improves the
DNa+, enhancing the overall performance, as shown in
Fig. 8i.
4. Conclusions
A new ternary 4Ni–Sb–S nanomaterial was prepared efficiently using a combination of vacuum heating techniques. To enhance the durability of the anode, ball milling with graphite was employed, yielding the formation of 4Ni–Sb–S/GN composite. Experimental results showcased the exceptional structural stability of the multiphase 4Ni–Sb–S architecture during prolonged charge/discharge cycles. Furthermore, DFT calculations elucidated that the 4Ni–Sb–S hybrids facilitated extensive diffusion pathways for Na-ion, which were further augmented by the integration of exfoliated graphite. Remarkably, 4Ni–Sb–S/GN exhibited outstanding sodium storage properties, yielding 228.1 mA h g−1 at the 300th cycle under 0.2 A g−1. Even at 1 A g−1, 4Ni–Sb–S/GN still delivered 200 mA h g−1 at the 1000th cycle. These findings resulted in remarkable capacity retention rates of 83.8% from the 2nd cycle, accompanied by a corresponding ICE of 70.5%. This research offers a promising approach toward the development of high-performance anode materials for SIBs.
Data availability
The data supporting this article have been included as part of the ESI.†
Author contributions
S. D. Huang and T. B. Zeng co-designed the project; S. D. Huang and T. B. Zeng co-performed the experiment; S. D. Huang and Y. H. Ding analyzed the experimental data, performed the theoretical calculations; Y. Z. Zhu conducted partial experiments; D. L. Xie and Y. Mei guided the use of partial instruments; S. D. Huang and D. Feng co-wrote and revised the manuscript; All authors discussed the results and commented on the manuscript.
Conflicts of interest
The authors affirm that they do not have any known conflicting financial interests or personal associations that could have influenced the findings presented in this paper.
Acknowledgements
This work was supported by the Applied Basic Research Program of Yunnan Province (202101AU07110), and the National Natural Science Foundation of China (22073069 and 21773082).
References
- V. Khare, S. Nema and P. Baredar, Renewable Sustainable Energy Rev., 2016, 58, 23–33 CrossRef
.
- Y. Chen, Y. Meng, J. Zhang, Y. Xie, H. Guo, M. He, X. Shi, Y. Mei, X. Sheng and D. Xie, Nano-Micro Lett., 2024, 16, 196 CrossRef CAS PubMed
.
- E. T. Sayed, A. G. Olabi, A. H. Alami, A. Radwan, A. Mdallal, A. Rezk and M. A. Abdelkareem, Energies, 2023, 16, 1415 CrossRef CAS
.
- Y. Cao, P. Lian, Y. Chen, L. Zhang and X. Sheng, Sol. Energy Mater. Sol. Cells, 2024, 268, 112747 CrossRef CAS
.
- H. Song, H. Mu, J. Yuan, B. Liu, G. Bai and S. Lin, SusMat, 2023, 3, 543–554 CrossRef CAS
.
- L. Zhang, X. Li, M. Yang and W. Chen, Energy Storage Mater., 2021, 41, 522–545 CrossRef
.
- T. Wang, D. Su, D. Shanmukaraj, T. Rojo, M. Armand and G. Wang, Electrochem. Energy Rev., 2018, 1, 200–237 CrossRef CAS
.
- Y. Jin, P. M. L. Le, P. Gao, Y. Xu, B. Xiao, M. H. Engelhard, X. Cao, T. D. Vo, J. Hu, L. Zhong, B. E. Matthews, R. Yi, C. Wang, X. Li, J. Liu and J.-G. Zhang, Nat. Energy, 2022, 7, 718–725 CrossRef CAS
.
- J. Shao, X. Li, J. Wei, H. Pang and C. Chen, Adv. Sustainable Syst., 2018, 2, 1700154 CrossRef
.
- P. Gupta, S. Pushpakanth, M. A. Haider and S. Basu, ACS Omega, 2022, 7, 5605–5614 CrossRef CAS PubMed
.
- Z. Yang, G. Li, J. Sun, L. Xie, Y. Jiang, Y. Huang and S. Chen, Energy Storage Mater., 2020, 25, 724–730 CrossRef
.
- G. Kucinskis, I. Nesterova, A. Sarakovskis, L. Bikse, J. Hodakovska and G. Bajars, J. Alloys Compd., 2022, 895, 162656 CrossRef CAS
.
- W. Fei, Y. Wang, X. Zhang, J. Zhang, S. Lu, K. Rao, K. Sun, M. Deng, Y. Liu, Q. Li, L. Wu and Y. Sui, Chem. Eng. J., 2024, 493, 152523 CrossRef CAS
.
- G. Wan, B. Peng, L. Zhao, F. Wang, L. Yu, R. Liu and G. Zhang, SusMat, 2023, 3, 58–71 CrossRef CAS
.
- S. Fan, Y. Liu, Y. Gao, Y. Liu, Y. Qiao, L. Li and S.-L. Chou, SusMat, 2023, 3, 749–780 CrossRef CAS
.
- L. Liu, Q. Li, Z. Wang, J. Yan and Y. Chen, Funct. Mater. Lett., 2018, 11, 1830001 CrossRef CAS
.
- L. He, J. Guo, S. Liu, F. Wang, X. Li and Z. Su, J. Alloys Compd., 2024, 997, 174924 CrossRef CAS
.
- Z. Li, Y. Zheng, Q. Liu, Y. Wang, D. Wang, Z. Li, P. Zheng and Z. Liu, J. Mater. Chem. A, 2020, 8, 19113–19132 RSC
.
- Y. Wang, S. Wang, N. Song, X. Wu, J. Xu, S. Luo, B. Xu and F. Wang, Comput. Mater. Sci., 2024, 233, 112710 CrossRef CAS
.
- T. Bo, P.-F. Liu, J. Xu, J. Zhang, Y. Chen, O. Eriksson, F. Wang and B.-T. Wang, Phys. Chem. Chem. Phys., 2018, 20, 22168–22178 RSC
.
- B. Ahmed, D. H. Anjum, Y. Gogotsi and H. N. Alshareef, Nano Energy, 2017, 34, 249–256 CrossRef CAS
.
- Y. Dall'Agnese, P.-L. Taberna, Y. Gogotsi and P. Simon, J. Phys. Chem. Lett., 2015, 6, 2305–2309 CrossRef PubMed
.
- M. S. Javed, A. Mateen, S. Ali, X. Zhang, I. Hussain, M. Imran, S. S. A. Shah and W. Han, Small, 2022, 18, 2201989 CrossRef CAS PubMed
.
- H. Wang, J. Li, K. Li, Y. Lin, J. Chen, L. Gao, V. Nicolosi, X. Xiao and J.-M. Lee, Chem. Soc. Rev., 2021, 50, 1354–1390 RSC
.
- P. Liu, Z. Zhang, R. Hao, Y. Huang, W. Liu, Y. Tan, P. Li, J. Yan and K. Liu, Chem. Eng. J., 2021, 403, 126425 CrossRef CAS
.
- M. S. Kim, Z. Zhang, J. Wang, S. T. Oyakhire, S. C. Kim, Z. Yu, Y. Chen, D. T. Boyle, Y. Ye, Z. Huang, W. Zhang, R. Xu, P. Sayavong, S. F. Bent, J. Qin, Z. Bao and Y. Cui, ACS Nano, 2023, 17, 3168–3180 CrossRef CAS PubMed
.
- Y. Kim, Y. Park, M. Kim, J. Lee, K. J. Kim and J. W. Choi, Nat. Commun., 2022, 13, 2371 CrossRef CAS PubMed
.
- L. Wang, X. Zhang, C. Li, Y. Xu, Y. An, W. Liu, T. Hu, S. Yi, K. Wang, X. Sun, Y. Gong, Z.-S. Wu and Y. Ma, Chem. Eng. J., 2023, 468, 143507 CrossRef CAS
.
- X. Ou, T. Liu, W. Zhong, X. Fan, X. Guo, X. Huang, L. Cao, J. Hu, B. Zhang, Y. S. Chu, G. Hu, Z. Lin, M. Dahbi, J. Alami, K. Amine, C. Yang and J. Lu, Nat. Commun., 2022, 13, 2319 CrossRef CAS PubMed
.
- Z. Hu, Q. Liu, S.-L. Chou and S.-X. Dou, Adv. Mater., 2017, 29, 1700606 CrossRef PubMed
.
- H. Tian, Z. Xu, K. Liu, D. Wang, L. Ren, Y. Wei, L. Chen, Y. Chen, S. Liu and H. Yang, J. Colloid Interface Sci., 2024, 670, 152–162 CrossRef CAS PubMed
.
- Z. Hao, X. Shi, Z. Yang, L. Li and S.-L. Chou, Adv. Funct. Mater., 2022, 32, 2208093 CrossRef CAS
.
- J. Zhao, Y. Zhang, Y. Wang, H. Li and Y. Peng, J. Energy Chem., 2018, 27, 1536–1554 CrossRef
.
- P. Geng, S. Zheng, H. Tang, R. Zhu, L. Zhang, S. Cao, H. Xue and H. Pang, Adv. Energy Mater., 2018, 8, 1703259 CrossRef
.
- A. Skurtveit, A. Brennhagen, H. Park, C. Cavallo and A. Y. Koposov, Front. Energy Res., 2022, 10, 897755 CrossRef
.
- C. Chen, L. Peng, Y. Li, L. Zhang, J. Xiang, P. Hu, S. Cheng, Y. Huang and J. Xie, ACS Appl. Mater. Interfaces, 2017, 9, 15470–15476 CrossRef CAS PubMed
.
- J. J. A. Kreissl, H. A. Dang, B. Mogwitz, M. Rohnke, D. Schröder and J. Janek, ACS Appl. Mater. Interfaces, 2024, 16, 26195–26208 CrossRef CAS PubMed
.
- J. Asenbauer, M. Kuenzel, T. Eisenmann, A. Birrozzi, J.-K. Chang, S. Passerini and D. Bresser, J. Phys. Chem. Lett., 2020, 11, 8238–8245 CrossRef CAS PubMed
.
- H. Guan, D. Feng, X. Xu, Q. Chen, Y. Mei, T. Zeng and D. Xie, Adv. Compos. Hybrid Mater., 2024, 7, 112 CrossRef CAS
.
- Y.-L. Hou, J.-Z. Chen, B.-H. Zhang, H.-Y. Wang, W.-X. Wen and D.-L. Zhao, Chem. Eng. J., 2024, 479, 147914 CrossRef CAS
.
- H. Chen, J.-J. Mu, Y.-H. Bian, X.-W. Gao, D. Wang, Z.-M. Liu and W.-B. Luo, New Carbon Mater., 2023, 38, 510–519 CrossRef CAS
.
- J. Luo, S.-L. Xiang, D.-Y. Han, A. Liu, J. Cunha, G.-Y. Li, Z.-H. Hou and H. Yin, Rare Met., 2024, 43, 612–623 CrossRef CAS
.
- P. Huang, H. Ying, S. Zhang, Z. Zhang and W.-Q. Han, J. Mater. Chem. A, 2022, 10, 22135–22144 RSC
.
- T. Zhang, M. Wu, H. Gu, H. Yu, M. Zhou, X. Guo, Y. Liu, X. Zheng, Q. Kong and J. Zhang, J. Energy Storage, 2023, 73, 108981 CrossRef
.
- C. Peng, L. Yue, Y. Cui, X. He, S. Xu, C. Guo, M. Guo and H. Chen, J. Colloid Interface Sci., 2023, 648, 527–534 CrossRef CAS PubMed
.
- X. Wang, D. Feng, X. Xu, S. Huang, Y. Ding, J. Lin, Y. Xie, F. Wu, W. Zhao, T. Zeng and D. Xie, Chem. Eng. J., 2024, 493, 152853 CrossRef CAS
.
- Y. Liu, Q. Lin, X. Chen, X. Meng, B. Hou, H. Liu, S. Zhang, N. Shang, Z. Wang, C. Zhang, J. Song and X. Zhao, Energy Environ. Mater., 2023, e12684 Search PubMed
.
- Z. Wang, Y. Li, Q. Cheng, X. Wang, J. Wang and G. Zhang, J. Cleaner Prod., 2022, 367, 133060 CrossRef CAS
.
- Z. Liu, T. Song and U. Paik, J. Mater. Chem. A, 2018, 6, 8159–8193 RSC
.
- Z. Yi, Q. Han, X. Li, Y. Wu, Y. Cheng and L. Wang, Chem. Eng. J., 2017, 315, 101–107 CrossRef CAS
.
- L. Cheng, C. Ma, W. Lu, X. Wang, H. Yue, D. Zhang and Z. Xing, Chem. Eng. J., 2022, 433, 133527 CrossRef CAS
.
- Z. Li, L. Deng, I. A. Kinloch and R. J. Young, Prog. Mater. Sci., 2023, 135, 101089 CrossRef CAS
.
- W. Li, D. Peng, W. Huang, X. Zhang, Z. Hou, W. Zhang, B. Lin and Z. Xing, Carbon, 2023, 204, 315–324 CrossRef CAS
.
- X. Zheng, J. You, J. Fan, G. Tu, W. Rong, W. Li, Y. Wang, S. Tao, P. Zhang, S. Zhang, S. Shen, J. Li, L. Huang and S. Sun, Nano Energy, 2020, 77, 105123 CrossRef CAS
.
- S. Sarkar, A. Chaupatnaik, S. D. Ramarao, U. Subbarao, P. Barpanda and S. C. Peter, J. Phys. Chem. C, 2020, 124, 15757–15768 CrossRef CAS
.
- C. Li, D. Zhang, J. Cao, P. Yu, J. Qin and X. Zhang, ACS Appl. Energy Mater., 2021, 4, 2593–2599 CrossRef CAS
.
- E. Edison, W. C. Ling, V. Aravindan and S. Madhavi, ChemElectroChem, 2017, 4, 1932–1936 CrossRef CAS
.
- J. Li, X. Xu, Z. Luo, C. Zhang, X. Yu, Y. Zuo, T. Zhang, P. Tang, J. Arbiol, J. Llorca, J. Liu and A. Cabot, Electrochim. Acta, 2019, 304, 246–254 CrossRef CAS
.
- M. Bhar, S. Pappu, U. Bhattacharjee, S. V. Bulusu, T. N. Rao and S. K. Martha, J. Electrochem. Soc., 2023, 170, 040501 CrossRef CAS
.
- Y. Zhang, H. Su, C. Wang, D. Yang, Y. Li, W. Zhang, H. Wang, J. Zhang and D. Li, Nanoscale, 2019, 11, 12846–12852 RSC
.
- Z. Zhang, Y. Huang, X. Liu, C. Chen, Z. Xu and P. Liu, Carbon, 2020, 157, 244–254 CrossRef CAS
.
- W. Chai, W. Yin, K. Wang, W. Ye, X. Li, B. Tang and Y. Rui, Energy Technol., 2019, 7, 1900668 CrossRef CAS
.
- M. Duan, Y. Meng, M. Xiao, W. H. Z. Ahmed, X. Wang, H. Gao, Y. Zhang and F. Zhu, J. Electroanal. Chem., 2021, 899, 115681 CrossRef CAS
.
- P. Xie, X. Wang, Z. Qian, T. Liu, J. Yu and L. Zhang, J. Colloid Interface Sci., 2023, 640, 791–800 CrossRef CAS PubMed
.
- J. Wang, D. Cao, G. Yang, Y. Yang and H. Wang, J. Solid State Electrochem., 2017, 21, 3047–3055 CrossRef CAS
.
|
This journal is © The Royal Society of Chemistry 2025 |
Click here to see how this site uses Cookies. View our privacy policy here.