DOI:
10.1039/D1RA08763K
(Paper)
RSC Adv., 2022,
12, 11164-11189
Diverse and efficient catalytic applications of new cockscomb flower-like Fe3O4@SiO2@KCC-1@MPTMS@CuII mesoporous nanocomposite in the environmentally benign reduction and reductive acetylation of nitroarenes and one-pot synthesis of some coumarin compounds†
Received
1st December 2021
, Accepted 17th January 2022
First published on 20th April 2022
Abstract
In this research, Fe3O4@SiO2@KCC-1@MPTMS@CuII as a new cockscomb flower-like mesoporous nanocomposite was prepared and characterized by various techniques including Fourier transform infrared (FT-IR) spectroscopy, powder X-ray diffraction (PXRD), scanning electron microscopy (SEM), transmission electron microscopy (TEM), SEM-based energy-dispersive X-ray (EDX) spectroscopy, inductively coupled plasma-optical emission spectrometry (ICP-OES), thermogravimetric analysis/differential thermal analysis (TGA/DTA), vibrating sample magnetometry (VSM), UV-Vis spectroscopy, and Brunauer–Emmett–Teller (BET) and Barrett–Joyner–Halenda (BJH) analyses. The as-prepared Fe3O4@SiO2@KCC-1@MPTMS@CuII mesoporous nanocomposite exhibited satisfactory catalytic activity in the reduction and reductive acetylation of nitroarenes in a water medium and solvent-free one-pot synthesis of some coumarin compounds including 3,3'-(arylmethylene)bis(4-hydroxy-2H-chromen-2-ones) (namely, bis-coumarins) (3a–n) and 2-amino-4-aryl-7,7-dimethyl-5-oxo-5,6,7,8-tetrahydro-4H-chromene-3-carbonitriles (6a–n) along with acceptable turnover numbers (TONs) and turnover frequencies (TOFs). Furthermore, the mentioned CuII-containing mesoporous nanocatalyst was conveniently recovered by a magnet from reaction environments and reused for at least seven cycles without any significant loss in activity, which confirms its good stability.
1. Introduction
From the green chemistry point of view, designing chemical reactions considering all their environmental aspects is very precious. To this purpose, twelve main protocols with many sub-branches have been introduced, which guide and assist chemistry scientists, particularly synthetic chemists, in designing efficient and environmentally benign chemical strategies.1 Catalysis is one of the most significant parts of green chemistry protocols, and plays a unique role in a wide range of organic transformations.2 For the sake of the demands of sustainable development and green chemistry, the use of heterogeneous catalytic systems instead of traditional homogeneous ones has received increasing attention.3 In recent years and among heterogeneous catalysts, magnetic core–shell-type nanostructures have received tremendous attention and have significantly grown.4 In these types, magnetic iron oxide nanoparticles (Fe3O4 NPs) have been widely used as the central part of the core in the core–shell system due to their fantastic properties, especially satisfactory and powerful magnetic behaviors that facilitate the separation of the multi-layer-containing core–shell-sort catalytic system from the reaction pot using a simple magnet. Another important element for the construction of suitable core–shell-type nanocatalysts is supporting easily functionalizable surfaces. In this regard, silica-based mesoporous materials such as Santa Barbara Amorphous-15 (SBA-15), Mobil Composition of Matter No. 41 and 48 (MCM-41 and MCM-48), hollow mesoporous silica (HMS), and KAUST Catalysis Center (KCC-1) have emerged as some of the most important platforms, for which in recent decades, the scientific community has witnessed a notable increase in the design and development. Among various types of mesoporous silica-based materials, dendritic fibrous nanosilica KCC-1 with three-dimensional (3D) center-radial wrinkle channels and hierarchical pores has unique structural characteristics including open-pore nanochannels, highly accessible internal spaces with a high surface area typically > 700 m2 g−1, large pore volumes, ease of surface modification, low density, satisfactory stability, low toxicity, and good biocompatibility compared with conventional mesoporous materials.5 During the last decade and after the first report for the hydrothermal preparation of KCC-1 by Polshettiwar and co-workers in 2010,6 considerable attention and experience rapidly developed in terms of synthetic techniques, formation mechanisms, functionalization approaches, and application fields upon mentioned dendritic fibrous nanosilica-based materials. Catalysis is one of the most substantial areas that KCC-1 has a unique effect on it. The literature survey shows that the use of KCC-1-containing catalytic systems in various organic transformations has been increasing day by day.7
Nitroarenes, especially 4-nitrophenol (4-NP), and related compounds are known as notorious organic pollutants present in industrial and agriculture wastewaters, unfortunately.8 In this regard and due to the increasing global environmental concerns, the transformation of these hazardous compounds to valuable organic molecules such as arylamines (via a green reduction process) and arylacetamides (via a direct one-pot reductive acetylation strategy) is desirable in the organic and industrial chemistry community. Till date, various catalytic methods have been reported for the mentioned chemical transformations. However, numerous efficient catalytic procedures have been widely used for the reduction and reductive acetylation of nitroarenes but introducing new, stable, non-hazardous, cost-effective, easily accessible active site(s), and efficient catalytic systems that are capable of carrying out these organic reactions in green solvents are still needed. Without a doubt, among green solvents, water is the best choice in every way because it is readily available, very cheap, safe, non-flammable, and so on.9
Coumarins and related compounds (namely, coumarin-fused or coumarin-linked heterocycles) are an outstanding family of oxygen-containing fused heterocyclic frameworks. These scaffolds have diverse biological properties including anticancer,10 antioxidant,11 antidepressant,12 antimicrobial,13 anti-nociceptive,14 anti-asthmatic,15 anti-inflammatory,16 anti-pyretic,17 antileishmanial,18 anti-coagulant,19 anti-tubercular,20 antiviral,21 antibacterial,22 antifungal,23 antimalarial,24 antidiabetic,25 anti-hepatitis C virus,26 anti-HIV,27 anti-proliferative,28 antiplatelet,29 and antiplasmodial30 activities. They are also well-known inhibitors of urease,31 acetylcholinesterase (AChE) and butyrylcholinesterase (BChE),32 cyclooxygenase (COX),33 lipoxygenase (LOX),34 monoamine oxidases A and B (MAO-A and MAO-B),35 tubulin polymerization,36 carbonic anhydrase,37 α-glucosidase,38 inositol-requiring enzyme 1 (IRE-1) RNase,39 mitochondria-targeting antitumor STAT3,40 selective cyclin-dependent kinase 9 (CDK9),41 selective aldehyde dehydrogenase 1A1,42 coagulation factor XIIa (FXIIa),43 casein kinase 2 (CK2),44 steroid sulfatase (STS),45 chitin synthase (CHS),46 etc. These heterocyclic scaffolds have antagonistic behavior against chemokine-like factor 1 (CKLF1),47 G-protein-coupled receptor 35 (GPR35),48 orphan G-protein-coupled receptor 55 (GPR55),49 A3 adenosine receptor,50 and many others. According to the various and significant biological attributes of the coumarin derivatives, introducing powerful and simple synthetic methods for the preparation of such valuable heterocyclic scaffolds along with respect to green chemistry protocols are undoubtedly precious. One-pot multi-component reactions (MCRs) could be a very suitable strategy for this purpose. These reactions are fast, convenient, atom-economic, safe, effective, and more economic than the classical multi-step synthetic manners.51
Herein, in continuation of our research program in organic synthesis52 and new catalytic systems design, we report a multi-step strategy for the preparation of a new magnetic core–shell-type cockscomb flower-like Fe3O4@SiO2@KCC-1@MPTMS@CuII mesoporous nanocomposite as an efficient, recoverable, reusable, and stable nano-based catalytic system in the environmentally benign reduction and reductive acetylation of aromatic nitro compounds in water and solvent-free one-pot synthesis of some coumarin compounds including 3,3'-(arylmethylene)bis(4-hydroxy-2H-chromen-2-ones) (namely, bis-coumarins) (3a–n) and 2-amino-4-aryl-7,7-dimethyl-5-oxo-5,6,7,8-tetrahydro-4H-chromene-3-carbonitriles (6a–n) (Fig. 1).
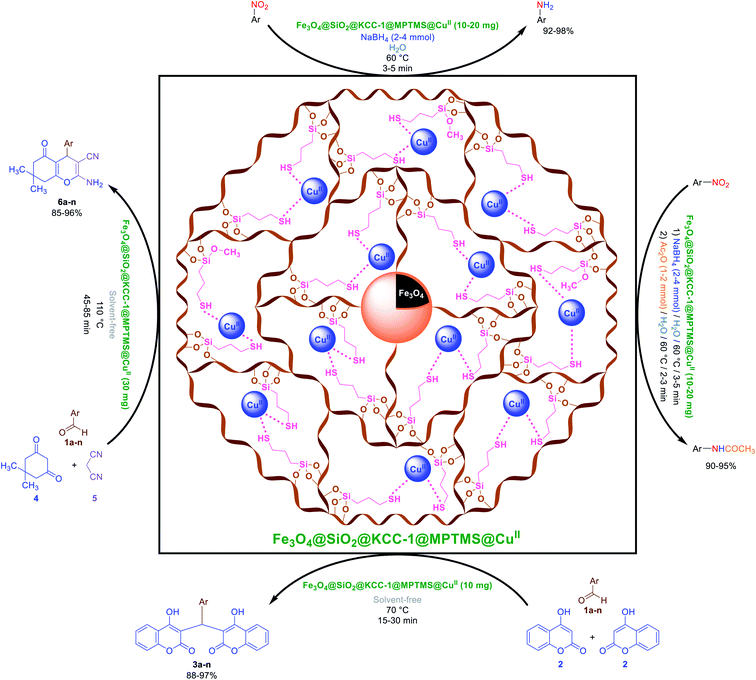 |
| Fig. 1 Catalytic applications of the cockscomb flower-like Fe3O4@SiO2@KCC-1@MPTMS@CuII mesoporous nanocomposite in the reduction and reductive acetylation of nitroarenes in water and solvent-free one-pot synthesis of some coumarin compounds. | |
2. Results and discussion
2.1 Preparation and characterization of the Fe3O4@SiO2@KCC-1@MPTMS@CuII mesoporous nanocomposite
Initially, we designed and implemented a five-step synthetic strategy for the preparation of the cockscomb flower-like Fe3O4@SiO2@KCC-1@MPTMS@CuII nanocomposite. First of all, and as shown in Scheme 1, the Fe3O4 nanoparticles (NPs) were prepared by a convenient and well-known chemical co-precipitation method of FeCl3·6H2O and FeCl2·4H2O in an aqueous ammonia solution under a nitrogen gas atmosphere. In the next step, the layering of SiO2 on the magnetic Fe3O4 NPs, which caused the formation of the Fe3O4@SiO2 core–shell structure, was carried out using tetraethyl orthosilicate (TEOS) at room temperature. In the third stage, the dendritic silica were grown around the surface of the Fe3O4@SiO2 nanocomposite using urea, cetyltrimethylammonium bromide (CTAB), and TEOS, and subsequently the whole mixture was heated (120 °C) in an autoclave and then calcined at 500 °C. After preparation of the magnetic Fe3O4@SiO2@KCC-1 nanocomposite, functionalization of the mentioned dendritic silica section was accomplished with (3-mercaptopropyl)trimethoxysilane (MPTMS), which afforded the fibrous Fe3O4@SiO2@KCC-1@MPTMS. In the final step, the immobilization of the copperII species on the dendritic Fe3O4@SiO2@KCC-1@MPTMS system yielded the cockscomb flower-like Fe3O4@SiO2@KCC-1@MPTMS@CuII mesoporous nanocomposite using copperII nitrate hexahydrate (Cu(NO3)2·6H2O) and sodium carbonate (Na2CO3) in a water medium. After building the Fe3O4@SiO2@KCC-1@MPTMS@CuII core–shell-type nanosystem, the structure of the as-prepared nanocomposite was elucidated by FT-IR, PXRD, SEM, TEM, SEM-based EDX, ICP-OES, TGA/DTA, VSM, UV-Vis, and BET and BJH analyses.
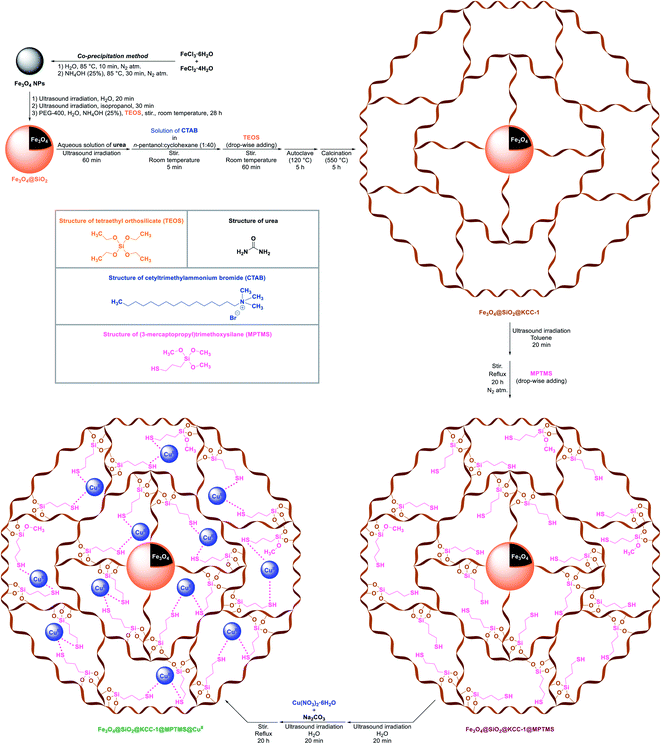 |
| Scheme 1 Preparation of the cockscomb flower-like Fe3O4@SiO2@KCC-1@MPTMS@CuII mesoporous nanocomposite. | |
The FT-IR spectroscopy analysis was used to elucidate the functional groups that exist in the structure of Fe3O4, Fe3O4@SiO2@KCC-1, Fe3O4@SiO2@KCC-1@MPTMS, and Fe3O4@SiO2@KCC-1@MPTMS@CuII. In the FT-IR spectrum of the bare Fe3O4 NPs (Fig. 2a), a strong absorption peak appeared at 575 cm−1 attributed to the vibration of Fe–O bonds and absorption peaks also appeared at 1625 cm−1 and 3400 cm−1 due to the O–H deforming and stretching vibrations of OH groups or adsorbed water on the Fe3O4 NPs surface, respectively. As shown in Fig. 2 (curves b and c), in the FT-IR spectrum of the Fe3O4@SiO2@KCC-1 and Fe3O4@SiO2@KCC-1@MPTMS, the absorption peaks appear at 808 cm−1 and 1091 cm−1 (strong), which are ascribed to the symmetric and asymmetric stretching vibrations of Si–O–Si, and there exists a peak at 2929 cm−1 assigned to the C–H stretching vibration of the aliphatic moiety in MPTMS. After adding copperII and forming the Fe3O4@SiO2@KCC-1@MPTMS@CuII nanocomposite, all the mentioned distinguished peaks existed and are visible (Fig. 2d).
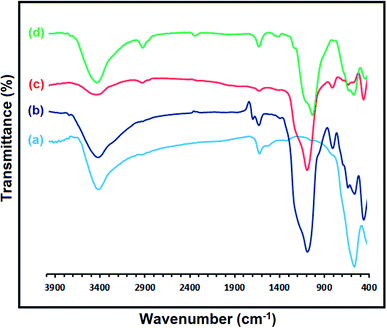 |
| Fig. 2 FT-IR spectra of the (a) Fe3O4, (b) Fe3O4@SiO2@KCC-1, (c) Fe3O4@SiO2@KCC-1@MPTMS, and (d) Fe3O4@SiO2@KCC-1@MPTMS@CuII nanosystems. | |
The phase purity and crystallinity character of the alone Fe3O4 NPs and as-prepared Fe3O4@SiO2@KCC-1@MPTMS@CuII nanocomposite were studied by PXRD analysis. The PXRD pattern of the Fe3O4 NPs (Fig. 3a) shows the reflection planes at nine diffraction peaks at (111), (220), (311), (400), (422), (511), (440), (620), and (553), which are indexed to the cubic spinel phase of Fe3O4, appeared and matched well with Joint Committee on Powder Diffraction Standards (JCPDS) card no. 65-3107. Comparing the PXRD patterns of the Fe3O4@SiO2@KCC-1@MPTMS@CuII nanocomposite (Fig. 3b) and alone Fe3O4 NPs (Fig. 3a) shows that both patterns have the same signal position and crystallinity character. The wide and weak peak at around 2θ = 20–23° is related to the amorphous silica and proved the effective coating of the silica on the Fe3O4 core. Notably, in the PXRD pattern of the Fe3O4@SiO2@KCC-1@MPTMS@CuII nanocomposite (Fig. 3b), the index reflection peaks of the corresponding CuII species (JCPDS card no. 00-004-0836) were not clearly recognizable due to the overlapping of its signals with Fe3O4.
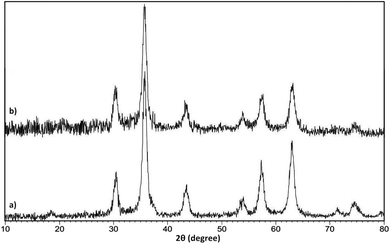 |
| Fig. 3 PXRD patterns of the (a) Fe3O4 and (b) Fe3O4@SiO2@KCC-1@MPTMS@CuII nanostructures. | |
SEM and TEM techniques were utilized for the exploration of the Fe3O4@SiO2@KCC-1@MPTMS@CuII nanocomposite morphology and size distribution. As shown in SEM images (Fig. 4), the as-prepared nanocomposite has an approximately cockscomb flower-like shape along with three-dimensional center-radial wrinkle channels and hierarchical pores. The SEM images also show that the thickness of wrinkled fibers is around eight to ten nanometers. Notably, this type of open hierarchical channel structure is more appropriate for extreme inter-collisions of the chemical reactants, and facilitates the accessibility of the active sites of the catalytic system. Besides, the TEM images (Fig. 5) reveal identical, well-defined, and ordered dendritic morphology of the as-prepared Fe3O4@SiO2@KCC-1@MPTMS@CuII, which comes out from the center of the mentioned nanocomposite and is distributed uniformly in all directions.
 |
| Fig. 4 SEM images of the cockscomb flower-like Fe3O4@SiO2@KCC-1@MPTMS@CuII nanocomposite. | |
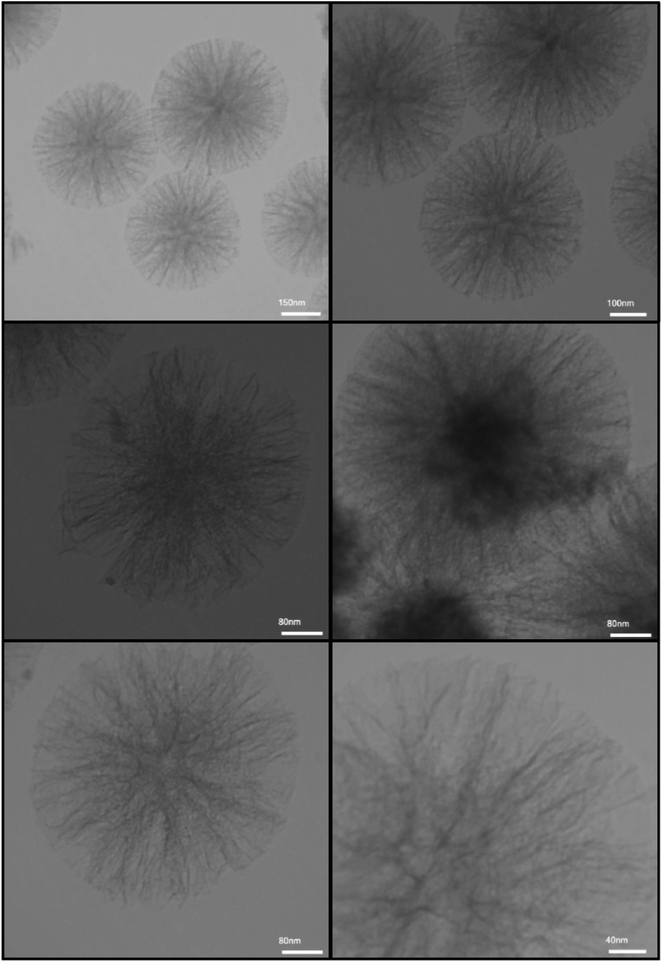 |
| Fig. 5 TEM images of the dendritic Fe3O4@SiO2@KCC-1@MPTMS@CuII nanocomposite. | |
The elemental composition of the dendritic CuII-containing nanocomposite was determined by SEM-based EDX spectroscopy analysis. As shown in Fig. 6, the EDX spectrum shows that in the structure of the mentioned nanocomposite system, the elements of Fe, O, Si, C, Cu, and S existed. Furthermore, using ICP-OES, the actual and exact amounts of the Cu and S species in the Fe3O4@SiO2@KCC-1@MPTMS@CuII core–shell-type system were determined to be 14.1% and 1.4%, respectively.
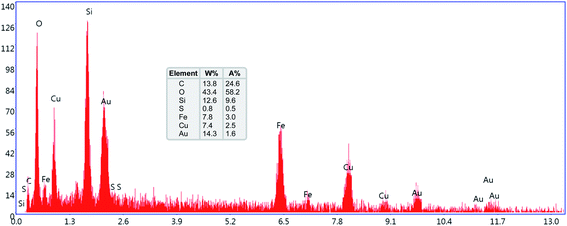 |
| Fig. 6 SEM-based EDX spectrum of the Fe3O4@SiO2@KCC-1@MPTMS@CuII nanocomposite. | |
The thermal stability of the as-prepared dendritic mesoporous Fe3O4@SiO2@KCC-1@MPTMS@CuII catalytic system was detected by TGA/DTA in a nitrogen atmosphere (Fig. 7). The first weight loss (around 7%) was observed at temperatures ranging from 60 °C to 200 °C, which could be assigned to trapped solvents (which were applied in the mentioned nanocomposite preparation steps) and adsorbed free water molecules. Moreover, weight losses (around 19%) that occurred in multi-stages between 200 °C and approximately 800 °C belong to the destruction of organic and silicate moieties.
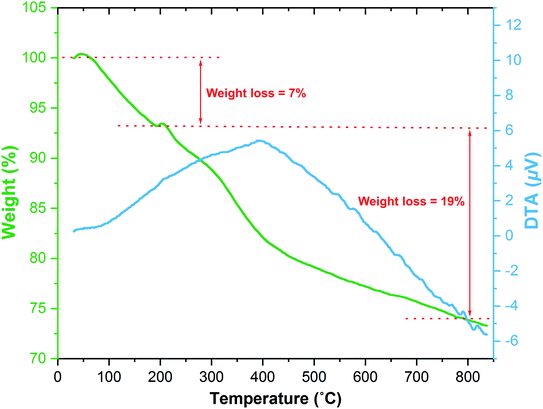 |
| Fig. 7 TGA/DTA diagram of the Fe3O4@SiO2@KCC-1@MPTMS@CuII nanocomposite. | |
The magnetic property and value of the alone Fe3O4 NPs and as-prepared Fe3O4@SiO2@KCC-1@MPTMS@CuII catalytic system were studied by VSM analysis. As shown in Fig. 8, the saturation magnetization (Ms) values of the bare Fe3O4 NPs and as-prepared dendritic CuII-containing catalyst are respectively 61.62 emu g−1 and 17.78 emu g−1. The Ms values demonstrate that via covering the surface of the Fe3O4 core with the layering of the amorphous and dendritic silica and then adding diamagnetic copper species to the Fe3O4@SiO2@KCC-1@MPTMS, the magnetization value of the Fe3O4@SiO2@KCC-1@MPTMS@CuII nanocomposite was intensively reduced compared with the bare Fe3O4 NPs.
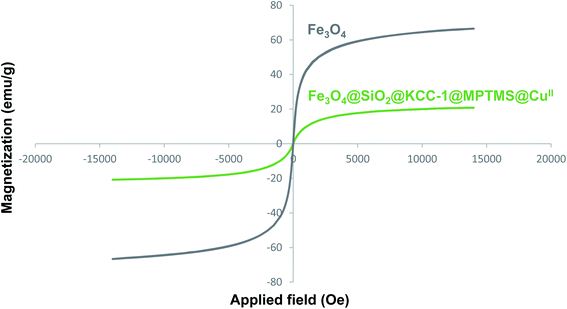 |
| Fig. 8 VSM diagram of the Fe3O4 NPs and Fe3O4@SiO2@KCC-1@MPTMS@CuII nanocomposite. | |
Determination of the exact form of the copper species in the structure of the as-prepared catalytic system was performed using the UV-Vis spectroscopy technique. In this context, UV-Vis spectra of the constructed dendritic nanocomposite system with different copper sources including copperII nitrate hexahydrate (Cu(NO3)2·6H2O), copperI oxide (Cu2O), and Cu0 were recorded (Fig. 9). The results indicated that the as-prepared cockscomb flower-like dendritic nanocomposite in the present work derived from the source of Cu(NO3)2·6H2O (viz. CuII) exhibited a broad absorption peak around 570–1100 nm. Notably, the constructed nanocomposite by the origins of Cu2O and Cu0 did not show any absorption peaks. Based on this explanation, the presence of CuII species in the mentioned nanocomposite system is confirmed.
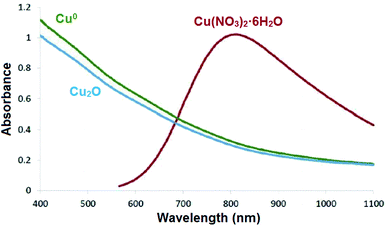 |
| Fig. 9 UV-Vis spectra of the nanocomposite derived from the sources of Cu(NO3)2·6H2O, Cu2O, and Cu0. | |
To determine the specific surface area and surface porosity in the as-prepared dendritic nanocomposite system, the nitrogen (N2) gas adsorption–desorption analysis was performed. Fig. 10 shows the N2 adsorption–desorption profile for the Fe3O4@SiO2@KCC-1@MPTMS@CuII nanocomposite. Based on the Brunauer–Deming–Deming–Teller (BDDT) and International Union of Pure and Applied Chemistry (IUPAC) classifications, the shape of the isotherm is closer to the isotherm of type IV with a H3-type hysteresis loop. It is worthy to note that this type of isotherm is a characteristic of mesoporous materials. The specific surface area, pore volume value, and average pore diameter of the as-synthesized mesoporous nanocomposite are 116.13 m2 g−1, 26.681 cm3 g−1, and 3.331 nm, respectively.
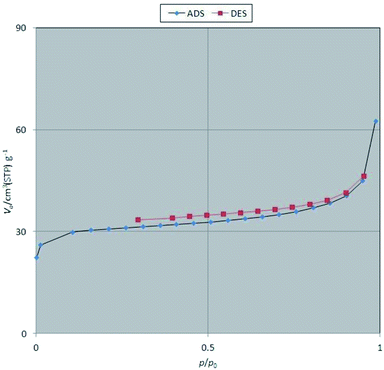 |
| Fig. 10 Nitrogen (N2) gas adsorption–desorption profile of the as-prepared Fe3O4@SiO2@KCC-1@MPTMS@CuII mesoporous nanocomposite. | |
2.2 Catalytic applications of the cockscomb flower-like Fe3O4@SiO2@KCC-1@MPTMS@CuII mesoporous nanocomposite
2.2.1 Reduction and one-pot reductive acetylation of nitroarenes. In the beginning, the catalytic application of the as-prepared magnetic cockscomb flower-like Fe3O4@SiO2@KCC-1@MPTMS@CuII mesoporous nanocomposite was investigated upon reduction of nitroarenes, which were converted into the corresponding arylamines using sodium borohydride (NaBH4) as a mild reducing agent. To this purpose, we selected nitrobenzene (PhNO2) as a simplistic aromatic nitro compound for this study. In the first experiment, the conversion of PhNO2 to aniline (PhNH2) using 2 mmol of NaBH4 in the presence of 10 mg of the as-prepared Fe3O4@SiO2@KCC-1@MPTMS@CuII catalyst in the water solvent at 60 °C after five minutes was 100% (Table 1, entry 1). The increasing amount of the aforesaid CuII-containing nanocatalyst from 10 mg to 20 mg had no positive effect on the reaction process (Table 1, entry 2). Moreover, the conversion rate of this transformation when carried out in common organic solvents (including CH3OH, CH3CH2OH, CH3CN, n-hexane, and CH2Cl2) was utterly unsatisfactory (Table 1, entries 3–7). After the optimization steps, the catalytic performance of the mentioned nanocatalyst was more studied in the reduction of various aromatic nitro compounds under optimal reaction conditions (Table 1, entry 1). As shown in Table 2, it was found that this imperative and valuable organic transformation was carried out with acceptable results in the presence of the Fe3O4@SiO2@KCC-1@MPTMS@CuII mesoporous catalytic system in water. Besides, the turnover numbers (TONs) and turnover frequencies (TOFs) of the catalyst in these reduction reactions were calculated, and are listed in Table 2. Also, according to the promising results of the reduction reaction of nitroarenes, we decided to design a new and green one-pot reductive acetylation reaction for the straightforward transformation of aromatic nitro compounds to the corresponding arylacetamides. For this purpose, we performed some optimization experiments to find the best optimal conditions for this valuable organic transformation (Table 3). After these experiments and having the optimal conditions in hand (Table 3, entry 1), we expanded this one-pot reaction using a wide range of nitroarenes under green and efficient reaction conditions (Table 4). Furthermore, based on our observations and authentic scientific papers and proofs in this field, we depicted a concise and plausible mechanism for the one-pot reductive acetylation of nitroarenes in the presence of the as-prepared mesoporous Fe3O4@SiO2@KCC-1@MPTMS@CuII nano-based catalytic system (Scheme 2).
Table 1 Optimization experiments for the reduction of PhNO2 to PhNH2 with NaBH4 catalyzed by the Fe3O4@SiO2@KCC-1@MPTMS@CuII nanocomposite
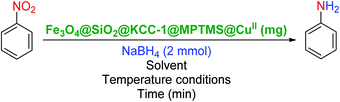
|
Entrya |
Catalyst loading (mg) |
Solvent |
Temperature conditions |
Time (min) |
Conversion (%) |
All reactions were carried out with 1 mmol of PhNO2 in 3 mL of solvent. |
1 |
10 |
H2O |
60 °C |
5 |
100 |
2 |
20 |
H2O |
60 °C |
5 |
100 |
3 |
10 |
CH3OH |
Reflux |
120 |
20 |
4 |
10 |
CH3CH2OH |
Reflux |
120 |
20 |
5 |
10 |
CH3CN |
Reflux |
120 |
10 |
6 |
10 |
n-Hexane |
Reflux |
120 |
0 |
7 |
10 |
CH2Cl2 |
Reflux |
120 |
0 |
Table 2 Reduction of nitroarenes to corresponding arylamines using NaBH4 catalyzed by the Fe3O4@SiO2@KCC-1@MPTMS@CuII nanocomposite in waterf
Table 3 Optimization experiments for the one-pot reductive acetylation of PhNO2 using the Fe3O4@SiO2@KCC-1@MPTMS@CuII nanocatalyst in water

|
Entrya |
Catalyst loading (mg) |
Ac2O (mmol) |
Yield (%) |
All reactions were carried out with 1 mmol of PhNO2 in 3 mL of the water solvent. |
1 |
10 |
1 |
95 |
2 |
20 |
1 |
95 |
3 |
10 |
2 |
95 |
4 |
30 |
1 |
95 |
Table 4 One-pot reductive acetylation of nitroarenes catalyzed by the Fe3O4@SiO2@KCC-1@MPTMS@CuII nanocomposite in waterf
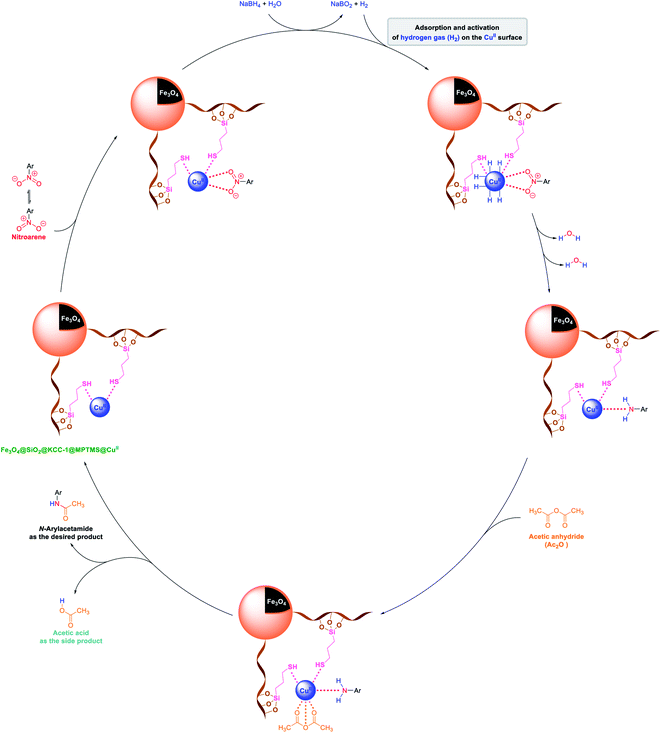 |
| Scheme 2 Plausible mechanism of the one-pot reductive acetylation of nitroarenes catalyzed by the Fe3O4@SiO2@KCC-1@MPTMS@CuII nanocomposite in water. | |
2.2.2 One-pot synthesis of coumarin compounds. The importance of the coumarins, as mentioned in the Introduction Section, drove us to introduce new, efficient, and environmentally benign approaches to the preparation of two different classes of such outstanding heterocyclic compounds. First of all, we decided to investigate the Fe3O4@SiO2@KCC-1@MPTMS@CuII mesoporous nanocomposite catalytic performance in the one-pot pseudo-three-component condensation of aromatic aldehydes (1a–n) and 4-hydroxycoumarin (2) for the preparation of bis-coumarins (3a–n). In this regard, we selected a model one-pot reaction between benzaldehyde (1a) and 4-hydroxycoumarin (2) in the presence of 10 mg of the mentioned as-prepared CuII-containing mesoporous nanocatalyst, which was carried out in different types of solvents including H2O, CH3OH, CH3CH2OH, CH3CN, n-hexane, EtOAc, and CH2Cl2 under reflux conditions (Table 5, entries 1–7). In addition, we tested the solvent-free conditions upon model reaction at 70 °C, and it was found that the mentioned protocol is efficient compared with others (Table 5, entry 8). Notably, the decreasing and or even increasing amount of the mentioned nanocatalyst had no positive effect on the reaction time or yield of the desired product (Table 5, entries 9 and 10). In addition, we designed and conducted some control experiments using component parts of the Fe3O4@SiO2@KCC-1@MPTMS@CuII nanocomposite (Table 5, entries 11–14). To our delight, the control experiments results indicated that the catalytic effect of the as-prepared nanocomposite is definitely better than that of its components. With the optimal and favorable conditions in hand (Table 5, entry 8), the scope and limitations of this Fe3O4@SiO2@KCC-1@MPTMS@CuII mesoporous nanocomposite-catalyzed solvent-free one-pot pseudo-three-component synthetic strategy were investigated using various aromatic aldehydes (1a–n). We were pleased to find that a wide range of bis-coumarins (3a–n) were successfully obtained in good-to-excellent yields along with acceptable TONs and TOFs (Scheme 3).
Table 5 Optimization reaction conditions for the pseudo-three-component synthesis of 3a
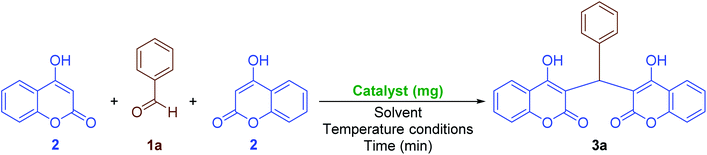
|
Entry |
Catalyst |
Catalyst loading (mg) |
Solvent |
Temperature conditions |
Time (min) |
Yield (%) |
1 |
Fe3O4@SiO2@KCC-1@MPTMS@CuII |
10 |
H2O |
Reflux |
60 |
70 |
2 |
Fe3O4@SiO2@KCC-1@MPTMS@CuII |
10 |
CH3OH |
Reflux |
60 |
50 |
3 |
Fe3O4@SiO2@KCC-1@MPTMS@CuII |
10 |
CH3CH2OH |
Reflux |
60 |
75 |
4 |
Fe3O4@SiO2@KCC-1@MPTMS@CuII |
10 |
CH3CN |
Reflux |
90 |
75 |
5 |
Fe3O4@SiO2@KCC-1@MPTMS@CuII |
10 |
n-Hexane |
Reflux |
120 |
— |
6 |
Fe3O4@SiO2@KCC-1@MPTMS@CuII |
10 |
EtOAc |
Reflux |
120 |
— |
7 |
Fe3O4@SiO2@KCC-1@MPTMS@CuII |
10 |
CH2Cl2 |
Reflux |
120 |
— |
8 |
Fe3O4@SiO2@KCC-1@MPTMS@CuII |
10 |
Solvent-free |
70 °C |
20 |
97 |
9 |
Fe3O4@SiO2@KCC-1@MPTMS@CuII |
5 |
Solvent-free |
70 °C |
20 |
80 |
10 |
Fe3O4@SiO2@KCC-1@MPTMS@CuII |
15 |
Solvent-free |
70 °C |
20 |
97 |
11 |
Fe3O4@SiO2@KCC-1@MPTMS |
10 |
Solvent-free |
70 °C |
120 |
25 |
12 |
Fe3O4@SiO2@KCC-1 |
10 |
Solvent-free |
70 °C |
120 |
10 |
13 |
Fe3O4@SiO2 |
10 |
Solvent-free |
70 °C |
120 |
— |
14 |
Fe3O4 |
10 |
Solvent-free |
70 °C |
120 |
— |
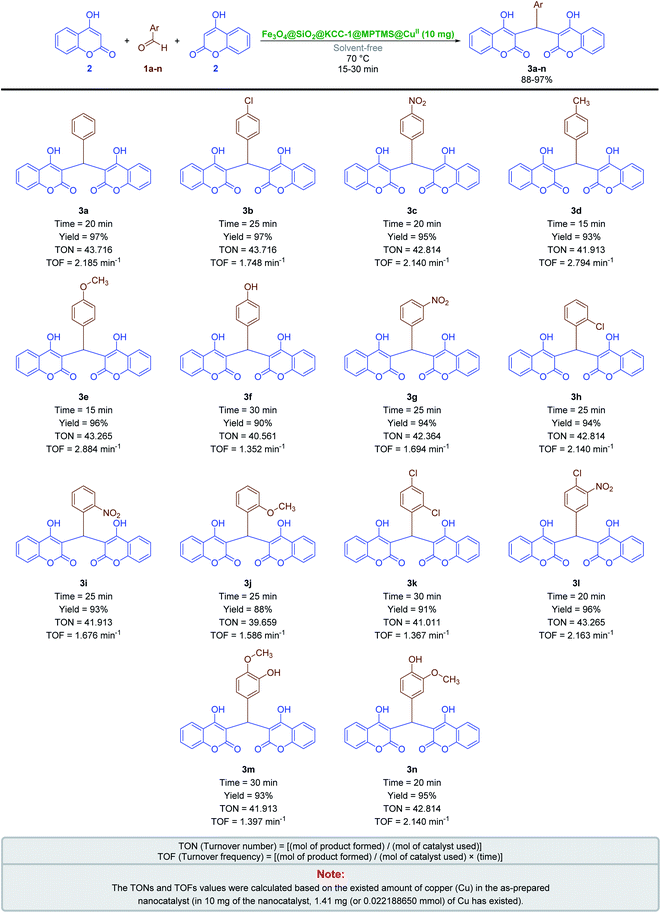 |
| Scheme 3 Solvent-free one-pot pseudo-three-component synthesis of bis-coumarins (3a–n) catalyzed by the Fe3O4@SiO2@KCC-1@MPTMS@CuII nanocomposite. | |
Also, due to the success in the one-pot synthesis of bis-coumarins (3a–n) using the Fe3O4@SiO2@KCC-1@MPTMS@CuII mesoporous catalytic system, we decided to carry out a one-pot three-component reaction between aromatic aldehydes (1a–n), dimedone (4), and malononitrile (5) for the synthesis of 2-amino-4-aryl-7,7-dimethyl-5-oxo-5,6,7,8-tetrahydro-4H-chromene-3-carbonitriles (6a–n) as another class of coumarin compounds in the presence of the mentioned copperII-containing mesoporous nanocatalyst. For this purpose, we carried out some optimization experiments to find the optimal conditions (Table 6), after which (Table 6, entry 8) a series of 2-amino-4-aryl-7,7-dimethyl-5-oxo-5,6,7,8-tetrahydro-4H-chromene-3-carbonitriles (6a–n) were successfully synthesized in the presence of 30 mg of the as-prepared dendritic Fe3O4@SiO2@KCC-1@MPTMS@CuII nanocomposite catalytic system under solvent-free conditions at 110 °C in good-to-excellent yields and suitable TONs and TOFs (Scheme 4).
Table 6 Optimization reaction conditions for the one-pot synthesis of 6a
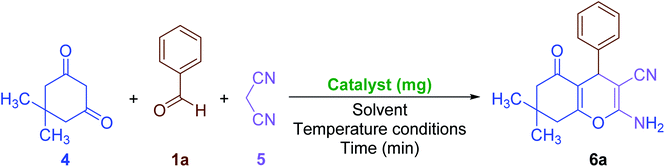
|
Entry |
Catalyst |
Catalyst loading (mg) |
Solvent |
Temperature conditions |
Time (min) |
Yield (%) |
1 |
Fe3O4@SiO2@KCC-1@MPTMS@CuII |
30 |
H2O |
Reflux |
120 |
60 |
2 |
Fe3O4@SiO2@KCC-1@MPTMS@CuII |
30 |
CH3OH |
Reflux |
60 |
50 |
3 |
Fe3O4@SiO2@KCC-1@MPTMS@CuII |
30 |
CH3CH2OH |
Reflux |
60 |
68 |
4 |
Fe3O4@SiO2@KCC-1@MPTMS@CuII |
30 |
CH3CN |
Reflux |
90 |
70 |
5 |
Fe3O4@SiO2@KCC-1@MPTMS@CuII |
30 |
n-Hexane |
Reflux |
120 |
— |
6 |
Fe3O4@SiO2@KCC-1@MPTMS@CuII |
30 |
EtOAc |
Reflux |
120 |
— |
7 |
Fe3O4@SiO2@KCC-1@MPTMS@CuII |
30 |
THF |
Reflux |
90 |
55 |
8 |
Fe3O4@SiO2@KCC-1@MPTMS@CuII |
30 |
Solvent-free |
110 °C |
60 |
96 |
9 |
Fe3O4@SiO2@KCC-1@MPTMS@CuII |
25 |
Solvent-free |
110 °C |
60 |
84 |
10 |
Fe3O4@SiO2@KCC-1@MPTMS@CuII |
35 |
Solvent-free |
110 °C |
60 |
96 |
11 |
Fe3O4@SiO2@KCC-1@MPTMS |
30 |
Solvent-free |
110 °C |
120 |
15 |
12 |
Fe3O4@SiO2@KCC-1 |
30 |
Solvent-free |
110 °C |
120 |
10 |
13 |
Fe3O4@SiO2 |
30 |
Solvent-free |
110 °C |
120 |
— |
14 |
Fe3O4 |
30 |
Solvent-free |
110 °C |
120 |
— |
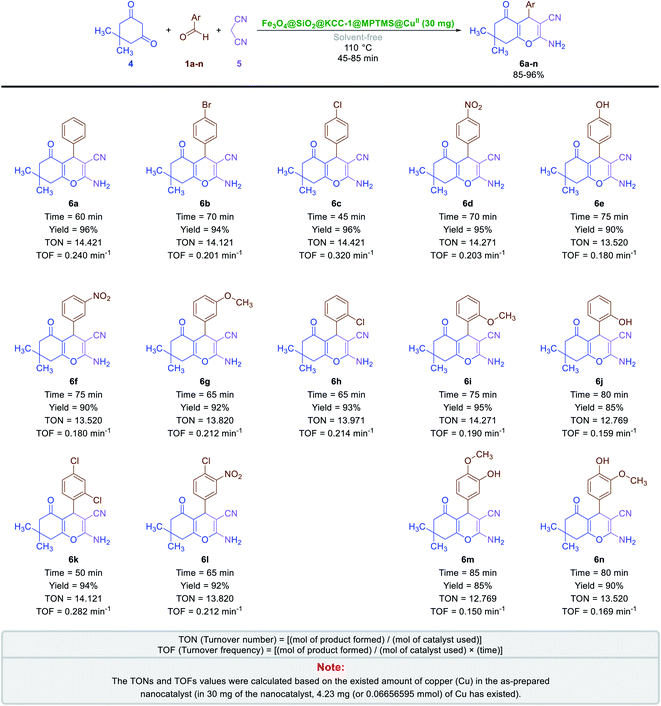 |
| Scheme 4 Solvent-free one-pot three-component synthesis of 2-amino-4-aryl-7,7-dimethyl-5-oxo-5,6,7,8-tetrahydro-4H-chromene-3-carbonitriles (6a–n) catalyzed by the Fe3O4@SiO2@KCC-1@MPTMS@CuII nanocomposite. | |
It is worthy to note that reasonable mechanisms for the solvent-free one-pot multi-component synthesis of 3a–n and 6a–n in the presence of the cockscomb flower-like Fe3O4@SiO2@KCC-1@MPTMS@CuII mesoporous catalytic system are depicted in Schemes 5 and 6, respectively.
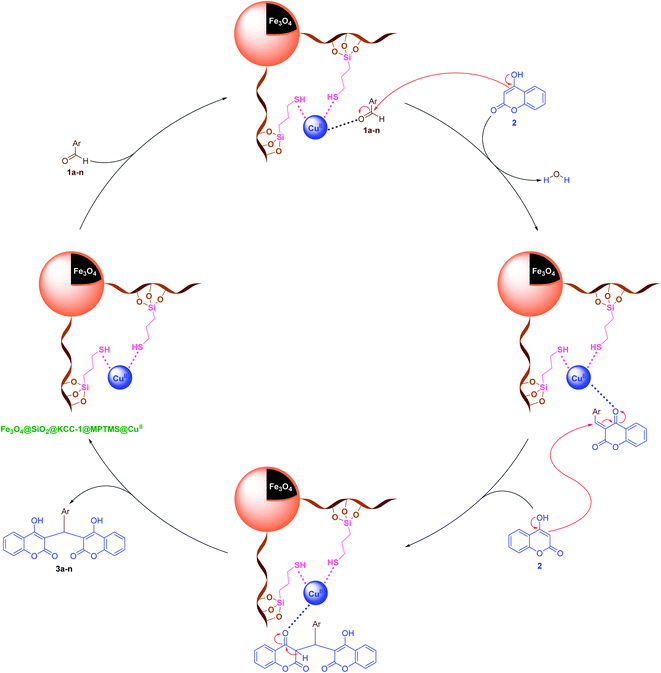 |
| Scheme 5 Plausible mechanism for the solvent-free one-pot pseudo-three-component synthesis of bis-coumarins (3a–n) catalyzed by the Fe3O4@SiO2@KCC-1@MPTMS@CuII nanocomposite. | |
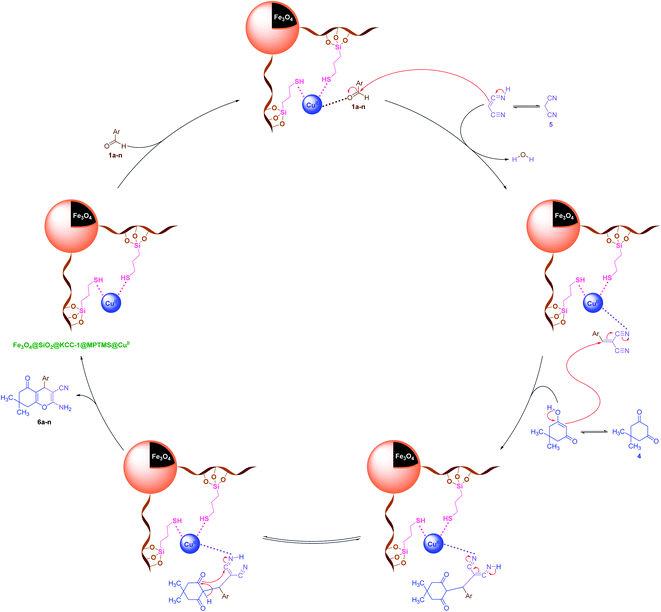 |
| Scheme 6 Plausible mechanism for the solvent-free one-pot three-component synthesis of 2-amino-4-aryl-7,7-dimethyl-5-oxo-5,6,7,8-tetrahydro-4H-chromene-3-carbonitriles (6a–n) catalyzed by the Fe3O4@SiO2@KCC-1@MPTMS@CuII nanocomposite. | |
2.3 A comparative study
The presented new protocols upon all the four mentioned organic transformations (namely, reduction and reductive acetylation of nitroarenes and one-pot synthesis of 3,3'-(arylmethylene)bis(4-hydroxy-2H-chromen-2-ones) (namely, bis-coumarins) (3a–n) and 2-amino-4-aryl-7,7-dimethyl-5-oxo-5,6,7,8-tetrahydro-4H-chromene-3-carbonitriles (6a–n)) using the cockscomb flower-like Fe3O4@SiO2@KCC-1@MPTMS@CuII mesoporous nanocatalyst are advantageous over most of the previously reported methods in various terms including catalyst loading, reaction time, favorable yield, and use of green reaction medium. In Table 7, a comparison of our protocols with some previously reported protocols upon reduction and reductive acetylation of nitrobenzene (PhNO2) and one-pot synthesis of 3a and 6a is presented.
Table 7 Comparison of the catalytic activity of the as-prepared Fe3O4@SiO2@KCC-1@MPTMS@CuII mesoporous nanocomposite with that of the samples reported in the literature upon reduction and reductive acetylation of nitrobenzene (PhNO2) and one-pot synthesis of 3a, and 6a
2.4 Recoverability, reusability, and leaching studies of the Fe3O4@SiO2@KCC-1@MPTMS@CuII mesoporous catalytic system
Uncomplicated recovery process and high reusability of catalytic systems are noteworthy aspects, exclusively for commercial and industrial applications and from the green chemistry point of view. In this regard, we performed some experiments to investigate the catalyst recyclability for all the four models titled organic reactions under the optimized reaction conditions. To do this and after each investigation, the as-prepared mesoporous catalyst was separated from the reaction pot using an external magnetic field. Then, the isolated Fe3O4@SiO2@KCC-1@MPTMS@CuII catalyst was washed, dried, and then directly used in the next run of the reaction. As shown in Fig. 11, the recoverability and reusability experiments of the Fe3O4@SiO2@KCC-1@MPTMS@CuII nanocomposite revealed satisfactory results even after seven runs for all the four mentioned organic reactions. Also, to evaluate the stability of the mesoporous Fe3O4@SiO2@KCC-1@MPTMS@CuII nanocomposite system in the reaction environments, we carried out leaching tests based on the ICP-OES measurements, and it was found that the amount of copper (Cu) after the seventh reaction cycle was reduced approximately 4% compared with the fresh one. Furthermore, the TEM image (Fig. 12) of the recycled dendritic Fe3O4@SiO2@KCC-1@MPTMS@CuII catalytic system after the seventh recycling step with those of the fresh ones displays that the morphology of the mentioned nanocomposite roughly remained intact.
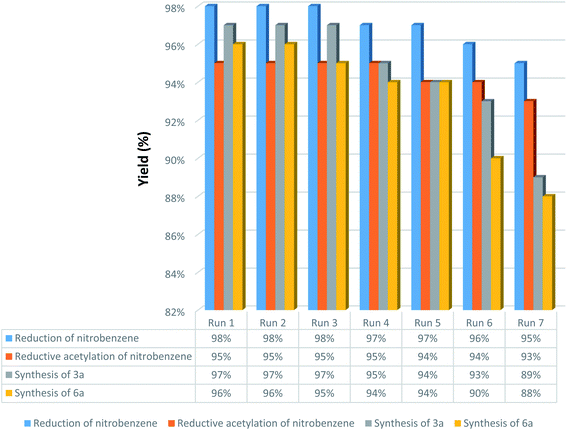 |
| Fig. 11 Recoverability and reusability experiments of the dendritic Fe3O4@SiO2@KCC-1@MPTMS@CuII mesoporous nanocomposite. | |
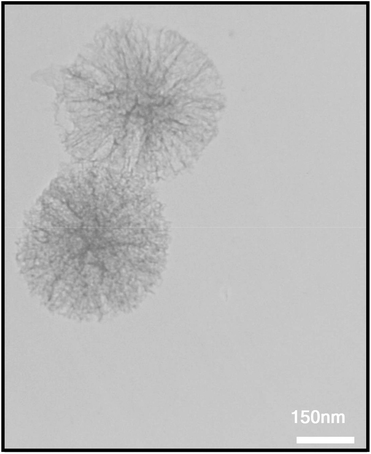 |
| Fig. 12 TEM image of the recycled Fe3O4@SiO2@KCC-1@MPTMS@CuII mesoporous nanocomposite. | |
3. Experimental
3.1 Reagents, samples, and apparatus
All starting materials, reagents, and solvents were commercially available (purchased from Merck, Sigma-Aldrich, and Fluka companies) and used directly without further purification. A SOLTEC SONICA 2400MH S3 (300 W) instrument was used for ultrasonic irradiation. FT-IR spectra were recorded using a Thermo Nicolet Nexus 670 spectrometer, and 1H NMR spectra were recorded using a Bruker Avance 300 MHz and 400 MHz spectrometer. The crystalline structures of the prepared nanocomposites were analyzed by Powder X-ray diffraction (PXRD) using a Philips PANalytical X'PertPro diffractometer (Netherlands) in 40 kV and 30 mA with a monochromatized Cu Kα radiation (λ = 1.5418 Å). The SEM images and EDX diagram were acquired using an FESEM-TESCAN MIR A3 electronic microscope. The TEM images were acquired using a Zeiss EM10C-100 kV transmission electron microscope. The elemental analysis was carried out by inductively coupled plasma-optical emission spectrometry (Optima 7300DV ICP-OES). The magnetic properties of the prepared samples were measured using a vibrating sample magnetometer (Meghnatis Daghigh, Iran) under magnetic fields up to 20 kOe. The nitrogen adsorption–desorption experiment was carried out using a Belsorp-Max, Japan. Thin-layer chromatography (TLC) was applied for the purity determination of the products and reaction monitoring over a silica gel 60 F254 aluminum sheet.
3.2 Preparation of the Fe3O4 MNPs
The Fe3O4 magnetic nanoparticles (MNPs) were prepared by a chemical co-precipitation method. Typically, in a two-neck round-bottom flask, a solution of FeCl3·6H2O (5.838 g, 21.6 mmol) and FeCl2·4H2O (2.147 g, 10.8 mmol) in distilled water (100 mL) was prepared. The solution was stirred vigorously at 85 °C in a nitrogen atmosphere for ten minutes. Then, an aqueous ammonia solution (25%, 10 mL) was quickly added to the resulting solution of the iron salts at 85 °C. Upon the addition, The black Fe3O4 NPs were immediately precipitated. The prepared mixture was continuously stirred at 85 °C for thirty minutes under the nitrogen atmosphere. After cooling to room temperature, the obtained black nanoparticles were separated from the reaction pot using an external magnetic field and washed with distilled water, a solution of sodium chloride (0.02 M), and again distilled water. Drying under an air atmosphere affords the pure Fe3O4 MNPs.
3.3 Preparation of the Fe3O4@SiO2 MNPs
First, the Fe3O4 MNPs (1.5 g) were dispersed in distilled water (20 mL) by sonication for twenty minutes. Then, isopropanol (200 mL) was added, and the resulting suspension was sonicated for thirty minutes. Consequently, PEG-400 (5.36 g), distilled water (20 mL), NH4OH (25%, 10 mL), and tetraethyl orthosilicate (TEOS) (2 mL) were respectively added, and the prepared mixture was stirred at room temperature for twenty-eight hours. The obtained Fe3O4@SiO2 MNPs were magnetically separated, washed with distilled water and ethanol, and subsequently dried under an air atmosphere.
3.4 Preparation of the Fe3O4@SiO2@KCC-1 magnetic nanocomposite
A suspension of the Fe3O4@SiO2 MNPs (0.25 g) in an aqueous solution of urea (0.3 g urea in 30 mL distilled water) was prepared. Then, the mentioned mixture was sonicated for one hour. In another vessel, a solution of cetyltrimethylammonium bromide (CTAB) (0.5 g) in a mixture of n-pentanol (0.75 mL) and cyclohexane (30 mL) was prepared. Next, the suspensions of the Fe3O4@SiO2 MNPs and CTAB were mixed together, and the resulting mixture was stirred at room temperature for five minutes. After that, TEOS (1.25 g) was added in a drop-wise manner, and the mixture was continuously stirred at room temperature for one hour, followed by the transfer of the mixture into an autoclave (120 °C) where it is kept for five hours. In this stage, the dendritic silica was grown on the surface of the Fe3O4@SiO2 MNPs, affording a fibrous Fe3O4@SiO2@KCC-1 composite system, which was magnetically separated from the reaction environment and washed with distilled water and then acetone. After that, the mentioned nanocomposite was dried in an oven at 40 °C and then calcined at 550 °C for five hours.
3.5 Preparation of the Fe3O4@SiO2@KCC-1@MPTMS magnetic nanocomposite
First, the prepared Fe3O4@SiO2@KCC-1 nanocomposite (0.5 g) was dispersed by sonication for twenty minutes in toluene (20 mL). Then, (3-mercaptopropyl)trimethoxysilane (MPTMS) (0.7 mL) was added into the mentioned suspension in a drop-wise manner. The resulting mixture was then stirred under reflux conditions for twenty hours under the nitrogen atmosphere. After that, the mixture was cooled to room temperature, and the prepared Fe3O4@SiO2@KCC-1@MPTMS nanocomposite was magnetically separated from the reaction pot, washed with ethanol, and then dried in an oven at 80 °C.
3.6 Preparation of the Fe3O4@SiO2@KCC-1@MPTMS@CuII magnetic nanocomposite
In a round-bottom flask, the prepared Fe3O4@SiO2@KCC-1@MPTMS (0.6 g) was dispersed in water (50 mL) by ultrasound irradiation for twenty minutes. Then, copperII nitrate hexahydrate (Cu(NO3)2·6H2O) (0.59 g, 2 mmol) and sodium carbonate (Na2CO3) (0.424 g, 4 mmol) were added into the mentioned reaction pot and sonicated for another twenty minutes. The resulting mixture was stirred under reflux conditions for twenty hours. The obtained cockscomb flower-like Fe3O4@SiO2@KCC-1@MPTMS@CuII mesoporous nanocomposite system was magnetically separated from the reaction pot, washed with ethanol, and then dried in an oven at 50 °C.
3.7 General procedure for the reduction of nitroarenes to arylamines catalyzed by the Fe3O4@SiO2@KCC-1@MPTMS@CuII nanocomposite
For example, in a round-bottom flask (15 mL) equipped with a magnetic stirrer, a mixture of PhNO2 (0.123 g, 1 mmol) and H2O (3 mL) was prepared. Then, 10 mg of the as-prepared Fe3O4@SiO2@KCC-1@MPTMS@CuII mesoporous nanocomposite was added, and the mixture was stirred. At the next step, NaBH4 (0.076 g, 2 mmol) was added, and the resulting mixture was continuously stirred at 60 °C for five minutes. After the completion of the reaction, the mixture was cooled to room temperature, and the mentioned CuII-containing catalytic system was separated from the reaction pot using an external magnet. The reaction mixture was extracted with dichloromethane (DCM) (3 × 5 mL) and then dried over anhydrous sodium sulfate (Na2SO4). Finally, the solvent was evaporated under reduced pressure to afford the the pure liquid aniline in 98% yield.
3.8 General procedure for the one-pot reductive acetylation of nitroarenes catalyzed by the Fe3O4@SiO2@KCC-1@MPTMS@CuII nanocomposite
As an example, PhNO2 (0.123 g, 1 mmol) was mixed with 3 mL of H2O in a 15 mL round-bottom flask equipped with a magnetic stirrer. Then, the Fe3O4@SiO2@KCC-1@MPTMS@CuII mesoporous nanocatalyst (10 mg) was added, and the mixture was stirred. Following this, NaBH4 (0.076 g, 2 mmol) was added, and the resulting mixture was stirred at 60 °C for five minutes. After the completion of the reduction reaction, acetic anhydride (Ac2O) (0.102 g, 1 mmol) was added to the reaction mixture, followed by stirring for further two minutes at the same temperature. Afterward, the mixture was cooled to room temperature, and the Fe3O4@SiO2@KCC-1@MPTMS@CuII mesoporous nanocatalyst was separated using an external magnet. Then, the reaction mixture was extracted with DCM (3 × 5 mL) and then dried over Na2SO4. Finally, evaporation of the solvent under reduced pressure afforded the pure acetanilide in 95% yield.
3.9 General procedure for the solvent-free one-pot pseudo-three-component synthesis of bis-coumarins (3a–n) catalyzed by the Fe3O4@SiO2@KCC-1@MPTMS@CuII nanocomposite
As a representative example, in a simple experimental tube, equipped with a magnetic stirrer, a mixture of benzaldehyde (0.106 g, 1 mmol), 4-hydroxycoumarin (0.324 g, 2 mmol), and the as-prepared Fe3O4@SiO2@KCC-1@MPTMS@CuII mesoporous nanocatalyst (10 mg) was prepared and heated at 70 °C under solvent-free conditions for twenty minutes. After completion, the mentioned one-pot pseudo-three-component reaction, the Fe3O4@SiO2@KCC-1@MPTMS@CuII nanocatalyst, was separated from the reaction pot using an external magnet. After cooling to room temperature, the resulting mixture was extracted with ethanol (2 × 5 mL), followed by drying over Na2SO4. The solvent evaporation under reduced pressure afforded the crude 3,3'-(phenylmethylene)bis(4-hydroxy-2H-chromen-2-one) (3a), which was purified by recrystallization with hot ethanol.
3.10 General procedure for the solvent-free one-pot three-component synthesis of 2-amino-4-aryl-7,7-dimethyl-5-oxo-5,6,7,8-tetrahydro-4H-chromene-3-carbonitriles (6a–n) catalyzed by the Fe3O4@SiO2@KCC-1@MPTMS@CuII nanocomposite
As a representative example, in a simple experimental tube, equipped with a magnetic stirrer, a mixture of benzaldehyde (0.106 g, 1 mmol), malononitrile (0.066 g, 1 mmol), 5,5-dimethyl-1,3-cyclohexanedione (0.140 g, 1 mmol), and the as-prepared Fe3O4@SiO2@KCC-1@MPTMS@CuII mesoporous nanocatalyst (30 mg) was prepared and heated at 110 °C under solvent-free conditions for sixty minutes. After completion of the mentioned one-pot three-component reaction and cooling down to room temperature, ethanol (3 mL) was added, and the reaction mixture was stirred for two minutes. Then, the Fe3O4@SiO2@KCC-1@MPTMS@CuII nanocatalyst was magnetically separated from the reaction environment. Drying over Na2SO4 and then evaporation of the solvent under reduced pressure afforded the pure 2-amino-4-phenyl-7,7-dimethyl-5-oxo-5,6,7,8-tetrahydro-4H-chromene-3-carbonitriles (6a).
4. Conclusion
In conclusion, our research group has successfully prepared Fe3O4@SiO2@KCC-1@MPTMS@CuII as a new cockscomb flower-like mesoporous nanocomposite, which was fully characterized by various techniques including FT-IR, PXRD, SEM, TEM, SEM-based EDX, ICP-OES, TGA/DTA, VSM, UV-Vis, and BET and BJH analyses. Then, the as-prepared Fe3O4@SiO2@KCC-1@MPTMS@CuII mesoporous nanocomposite was applied as an efficient catalytic system in the reduction and reductive acetylation of nitroarenes in a water medium and solvent-free one-pot synthesis of some coumarin compounds. The TONs and TOFs of the mentioned catalyst were calculated upon all the titled reactions. Notably, the mentioned as-prepared mesoporous nanocatalyst was recovered from the reaction pots using a simple magnet and reused for at least seven cycles without significant loss in activity, which ensures its good stability. In addition, in comparison with the previously reported methods (for all of the mentioned organic reactions), the presented new strategies are a viable alternative to most of them in many respects.
Conflicts of interest
There are no conflicts to declare.
Acknowledgements
The authors thank Urmia University for support of this work.
References
-
(a) H. C. Erythropel, J. B. Zimmerman, T. M. de Winter, L. Petitjean, F. Melnikov, C. H. Lam, A. W. Lounsbury, K. E. Mellor, N. Z. Janković, Q. Tu, L. N. Pincus, M. M. Falinski, W. Shi, P. Coish, D. L. Plata and P. A. Anastas, Green Chem., 2018, 20, 1929–1961 RSC;
(b) M. Pérez-Venegas and E. Juaristi, ACS Sustainable Chem. Eng., 2020, 8, 8881–8893 CrossRef;
(c) H. Mousavi, Int. J. Bio. Macromol., 2021, 186, 1003–1166 CrossRef CAS PubMed;
(d) M. Rimaz, H. Mousavi, B. Khalili and F. Aali, J. Chin. Chem. Soc., 2018, 65, 1389–1397 CrossRef CAS;
(e) M. Rimaz, H. Mousavi, M. Behnam and B. Khalili, Curr. Chem. Lett., 2016, 5, 145–154 CrossRef;
(f) M. Rimaz, Z. Jalalian, H. Mousavi and R. H. Prager, Tetrahedron Lett., 2016, 57, 105–109 CrossRef CAS;
(g) N. Nivetha and A. Thangamani, J. Mol. Struct., 2021, 1242, 130716 CrossRef CAS.
-
(a) A. Y. Li and A. Moores, ACS Sustainable Chem. Eng., 2019, 7, 10182–10197 CrossRef CAS;
(b) G. J. Hutching, ACS Cent. Sci., 2018, 4, 1095–1101 CrossRef PubMed;
(c) P. T. Anastas, M. M. Kirchhoff and T. C. Williamson, Appl. Catal., A, 2001, 221, 3–13 CrossRef CAS;
(d) G. Centi and S. Perathoner, Top. Catal., 2009, 52, 948–961 CrossRef CAS;
(e) A. C. Lamb, A. F. Lee and K. Wilson, Aust. J. Chem., 2020, 73, 832–852 CAS.
-
(a) E. D. Goodman, C. Zhao and M. Cargnello, ACS Cent. Sci., 2020, 6, 1916–1937 CrossRef CAS PubMed;
(b) R. Schlögl, Angew. Chem., Int. Ed., 2015, 54, 3465–3520 CrossRef PubMed;
(c) R. Lung, X. Du, Y. Huang, X. Jiang, Q. Zhang, Y. Guo, K. Liu, B. Qiao, A. Wang and T. Zhang, Chem. Rev., 2020, 120, 11986–12043 CrossRef PubMed;
(d) R. Lippi, C. J. Coghlan, S. C. Howard, C. D. Easton, Q. Gu, J. Patel, C. J. Sumby, D. F. Kennedy and C. J. Dooman, Aust. J. Chem., 2020, 73, 1271–1283 CrossRef CAS;
(e) N. Tadon, S. M. Patil, R. Tadon and P. Kumar, RSC Adv., 2021, 11, 21291–21300 RSC.
-
(a) V. Polshetiwar, R. Luque, A. Fihri, H. Zhu, M. Bouhara and J.-M. Basset, Chem. Rev., 2011, 111, 3036–3075 CrossRef PubMed;
(b) S. Shylesh, V. Schünemann and W. R. Thiel, Angew. Chem., Int. Ed., 2010, 49, 3428–3459 CrossRef CAS PubMed;
(c) D. Wang and D. Astruc, Chem. Rev., 2014, 114, 6949–6985 CrossRef CAS PubMed;
(d) M. B. Gawande, R. Luque and R. Zboril, ChemCatChem, 2014, 6, 3312–3313 CrossRef CAS;
(e) B. Karimi, F. Mansouri and H. M. Mirzaei, ChemCatChem, 2015, 7, 1736–1789 CrossRef CAS;
(f) G. Mohammadi Ziarani, Z. Kheilkordi, F. Mohajer, A. Badiei and R. Luque, RSC Adv., 2021, 11, 17456–17477 RSC;
(g) A. Pawar, S. Gajare, A. Patil, R. Kurane, G. Rashinkar and S. Patil, Res. Chem. Intermed., 2021, 47, 2801–2820 CrossRef CAS;
(h) M. Aghaei-Hashjin, A. Yahyazadeh and E. Abbaspour-Gilandeh, RSC Adv., 2021, 11, 23491–23505 RSC;
(i) F. Mohammadsaleh, M. Dehdashti Jahromi, A. R. Hajipour, S. M. Hosseini and K. Niknam, RSC Adv., 2021, 11, 20812–20823 RSC;
(j) N. Hosseini Mohtasham and M. Gholizadeh, Res. Chem. Intermed., 2021, 47, 2507–2525 CrossRef CAS.
-
(a) A. Maity and V. Polshettiwar, ChemSusChem, 2017, 10, 3866–3913 CrossRef CAS PubMed;
(b) X. Huang, Z. Tao, J. C. Praskavich, A. Goswami, J. F. Al-Sharab, T. Minko, V. Polshettiwar and T. Asefa, Langmuir, 2014, 30, 10886–10898 CrossRef CAS PubMed;
(c) M. Shaban and M. Hasanzadeh, RSC Adv., 2020, 10, 37116–37133 RSC;
(d) P. Hao, B. Peng, B.-Q. Shan, T.-Q. Yang and K. Zhang, Nanoscale Adv., 2020, 2, 1792–1810 RSC;
(e) A. Wang, X. Du, Z. Liu, S. Shi and H. Lv, J. Mater. Chem. A, 2019, 7, 5111–5152 RSC.
- V. Polshettiwar, D. Cha, X. Zhang and J. M. Basset, Angew. Chem., Int. Ed., 2010, 49, 9652–9656 CrossRef CAS PubMed.
-
(a) A. Hassankhani, S. M. Sadeghzadeh and R. Zhiani, RSC Adv., 2018, 8, 8761–8769 RSC;
(b) S. M. Sadeghzadeh, RSC Adv., 2016, 6, 99586–99594 RSC;
(c) A. Allahresani, E. Naghdi, M. A. Nasseri and K. Hemmat, RSC Adv., 2020, 10, 37974–37981 RSC;
(d) S. M. Sadeghzadeh, Catal. Sci. Technol., 2016, 6, 1435–1441 RSC;
(e) Z. Dong, G. Yu and X. Le, New J. Chem., 2015, 39, 8623–8629 RSC;
(f) S. M. Sadeghzadeh, R. Zhiani, S. Emrani and M. Ghabdian, RSC Adv., 2017, 7, 50838–50843 RSC;
(g) R. Zhiani, S. M. Sadeghzadeh and S. Emrani, RSC Adv., 2018, 8, 6259–6266 RSC;
(h) M. Dhiman and V. Polshettiwar, J. Mater. Chem. A, 2016, 4, 12416–12424 RSC;
(i) P. Gautam, M. Dhiman, V. Polshettiwar and B. M. Bhanage, Green Chem., 2016, 18, 5890–5899 RSC;
(j) X. Le, Z. Dong, Y. Liu, Z. Jin, T.-D. Huy, M. Le and J. Ma, J. Mater. Chem. A, 2014, 2, 19696–19706 RSC;
(k) S. M. Sadeghzadeh, RSC Adv., 2016, 6, 54236–54240 RSC;
(l) S. Azizi and N. Shadjou, Heliyon, 2021, 7, e05915 CrossRef PubMed.
-
(a) A. Ahmad, S. N. A. Shah, M. Arshad, F. Bélanger-Gariepy, E. R. T. Tiekink and Z. ur Rehman, Appl. Organomet. Chem., 2021, 35, e6065 CAS;
(b) S. Majhi, K. Sharma, R. Singh, M. Ali, C. S. P. Tripathi and D. Guin, ChemistrySelect, 2020, 5, 12365–12370 CrossRef CAS;
(c) A. H. T. N. Sorenson, Y. Wu, E. K. Orcutt, R. V. Kent, H. C. Anderson, A. J. Matzger and K. J. Stowers, J. Mater. Chem. A, 2020, 8, 15066–15073 RSC;
(d) B. J. Borah and P. Bharali, Appl. Organomet. Chem., 2020, 34, e5753 CAS;
(e) N. T. N. Anh and R.-a. Doong, ACS Appl. Nano Mater., 2018, 1, 2153–2163 CrossRef;
(f) M. Fu, M. Li, Y. Zhao, Y. Bai, X. Fang, X. Kang, M. Yang, Y. Wei and X. Xu, RSC Adv., 2021, 11, 26502–26508 RSC;
(g) S. Ansari, A. Khorshidi and S. Shariati, RSC Adv., 2020, 10, 3554–3565 RSC;
(h) N. Y. Baran, J. Mol. Struct., 2020, 1220, 128697 CrossRef;
(i) J. Xiao, Z. Wu, K. Li, Z. Zhao and C. Liu, RSC Adv., 2022, 12, 1051–1061 RSC.
-
(a) R. N. Butler and A. C. Coyne, Chem. Rev., 2010, 110, 6302–6337 CrossRef CAS PubMed;
(b) A. Chanda and V. V. Fokin, Chem. Rev., 2009, 109, 725–748 CrossRef CAS;
(c) M. Rimaz, J. Khalafy, H. Mousavi, S. Bohlooli and B. Khalili, J. Heterocycl. Chem., 2017, 54, 3174–3186 CrossRef CAS;
(d) M. Rimaz, J. Khalafy and H. Mousavi, Res. Chem. Intermed., 2016, 42, 8185–8200 CrossRef CAS;
(e) M. H. Sayahi, S. Bahadorikhalili, S. J. Saghanezhad, M. A. Miller and M. Mahdavi, Res. Chem. Intermed., 2020, 46, 491–507 CrossRef CAS;
(f) H. Mousavi, J. Mol. Struct., 2022, 1251, 131742 CrossRef CAS.
-
(a) S. Emami and S. Dadashpour, Eur. J. Med. Chem., 2015, 102, 611–630 CrossRef CAS PubMed;
(b) L. Zhang and Z. Xu, Eur. J. Med. Chem., 2019, 181, 111587 CrossRef CAS PubMed;
(c) M. Holiyachi, S. L. Shastri, B. M. Chougala, N. S. Naik, V. Pawar, L. A. Shastri, S. D. Joshi and V. A. Sunagar, J. Mol. Struct., 2021, 1237, 130424 CrossRef CAS;
(d) S. Mamidala, V. Vangala, S. R. Peddi, R. Chedupaka, V. Manga and R. R. Vedula, J. Mol. Struct., 2021, 1233, 130111 CrossRef CAS;
(e) S. Vaseghi, S. Emami, M. Shokerzadeh, Z. Hossaini and M. Yousefi, J. Mol. Struct., 2021, 1244, 130926 CrossRef CAS;
(f) S. Kecel-Gunduz, Y. Budama-Kilinc, B. Gok, B. Bicak, G. Akman, B. Arvas, F. Aydogan and C. Yolacan, J. Mol. Struct., 2021, 1239, 130539 CrossRef CAS;
(g) S. T. Bhaskaran and P. Mathew, J. Mol. Struct., 2022, 1251, 132071 CrossRef CAS;
(h) X.-F. Song, J. Fan, L. Liu, X.-F. Liu and F. Gao, Arch. Pharm., 2020, 353, 2000025 CrossRef CAS PubMed;
(i) M. Simic, M. Petkovic, P. Jovanovic, M. Jovanovic, G. Tasic, I. Besu, Z. Zizak, I. Aleksic, J. Nikodinovic-Runic and V. Savic, Arch. Pharm., 2021, 354, 2100238 CrossRef CAS PubMed.
-
(a) I. Kostova, S. Bhatia, P. Grigorov, S. Balkansky, V. S. Parmar, A. K. Prasad and L. Saso, Curr. Med. Chem., 2011, 18, 3929–3951 CrossRef CAS PubMed;
(b) K. O. Lamara, M. Makhloufi-Chebli, A. Benazzouz-Touami, S. Terrachet-Bouaziz, N. Hamid, A. M. S. Silva and J.-B. Behr, J. Mol. Struct., 2021, 1231, 129936 CrossRef CAS.
- N. A. Abdel-Latif, Sci. Pharm., 2005, 73, 193–216 CrossRef.
- K. Bhagat, J. Bhagat, M. K. Gupta, J. V. Singh, H. K. Gulati, A. Singh, K. Kaur, G. Kaur, S. Sharma, K. Rana, H. Singh, S. Sharma and P. M. Singh Bedi, ACS Omega, 2019, 4, 8720–8730 CrossRef CAS PubMed.
- B. V. Cheriyan, P. Kadhirvelu, J. Nadipelly, J. Shanmugasundaram, V. Sayeli and V. Subramanian, Pharmacogn. Mag., 2017, 13, 81–84 CAS.
- A. Sánchez-Recillas, G. Navarrete-Vázquez, S. Hidalgo-Figueroa, M. Y. Rios, M. Ibarra-Barajas and S. Estrada-Soto, Eur. J. Med. Chem., 2014, 77, 400–408 CrossRef.
- J. Grover and S. M. Jachak, RSC Adv., 2015, 5, 38892–38905 RSC.
- R. S. Keri, K. M. Hosamani, R. V. Shingalapur and M. H. Hugar, Eur. J. Med. Chem., 2010, 45, 2597–2605 CrossRef CAS PubMed.
- G. A. Gonçalves, A. R. Spillere, G. M. das Neves, L. P. Kagami, G. L. von Poser, R. F. S. Canto and V. Eifler-Lima, Eur. J. Med. Chem., 2020, 203, 112514 CrossRef.
- M. Monti, M. Pinotti, G. Appendino, F. Dallocchino, T. Bellini, F. Antognoni, F. Poli and F. Bernardi, Biochim. Biophys. Acta, Gen. Subj., 2007, 1770, 1437–1440 CrossRef CAS PubMed.
- D. S. Reddy, M. Kongot and A. Kumar, Tuberculosis, 2021, 127, 102050 CrossRef CAS PubMed.
- M. Z. Hassan, H. Osman, M. A. Ali and M. J. Ashan, Eur. J. Med. Chem., 2016, 123, 236–255 CrossRef CAS PubMed.
-
(a) Y. Hu, Y. Shen, X. Wu, X. Tu and G.-X. Wang, Eur. J. Med. Chem., 2018, 143, 958–969 CrossRef CAS PubMed;
(b) C. R. Sahoo, J. Sahoo, M. Mahapatra, D. Lenka, P. K. Sahu, B. Dehury, R. N. Padhy and S. K. Paidesetty, Arabian J. Chem., 2021, 14, 102922 CrossRef;
(c) D. Feng, A. Zhang, Y. Yang and P. Yang, Arch. Pharm., 2020, 353, 1900380 CrossRef CAS PubMed.
- R. Elias, R. I. Benhamou, Q. Z. Jaber, O. Dorot, S. L. Zada, K. Oved, E. Pichinuk and M. Fridman, Eur. J. Med. Chem., 2019, 179, 779–790 CrossRef CAS PubMed.
- K. V. Sashidhara, A. Kumar, R. P. Dodda, N. N. Krishna, P. Agarwal, K. Srivastava and S. K. Puri, Bioorg. Med. Chem. Lett., 2012, 22, 3926–3930 CrossRef CAS PubMed.
- H. Li, Y. Yao and L. Li, J. Pharm. Pharmacol., 2017, 69, 1253–1264 CrossRef CAS PubMed.
-
(a) J. Neyts, E. De Clercq, R. Singha, Y. H. Chang, A. R. Das, S. K. Chakraborty, S. C. Hong, S.-C. Tsay, M.-H. Hsu and J. R. Hwu, J. Med. Chem., 2009, 52, 1486–1490 CrossRef CAS PubMed;
(b) J. R. Hwu, S.-Y. Lin, S.-C. Tsay, E. De Clercq, P. Leyssen and J. Neyts, J. Med. Chem., 2011, 54, 2114–2126 CrossRef CAS PubMed.
- Z. Xu, Q. Chen, Y. Zhang and C. Liang, Fitoterapia, 2021, 150, 104863 CrossRef CAS.
- S. García, I. Mercado-Sánchez, L. Bahena, Y. Alcaraz, M. A. García-Revilla, J. Robles, N. Santos-Martínez, D. Ordaz-Rosado, R. García-Becerra and M. A. Vazquez, Molecules, 2020, 25, 5134 CrossRef PubMed.
- C. Zaragozá, F. Zaragozá, I. Gayo-Abeleira and L. Villaescusa, Molecules, 2021, 26, 3036 CrossRef PubMed.
- N. Yadav, D. Agarwal, S. Kumar, A. K. Dixit, R. D. Gupta and S. K. Awasthi, Eur. J. Med. Chem., 2018, 145, 735–745 CrossRef CAS PubMed.
- F. Yilmaz, E. Menteşe and B. B. Sökmen, J. Heterocycl. Chem., 2021, 58, 260–269 CrossRef CAS.
-
(a) P. Anand, B. Singh and N. Singh, Bioorg. Med. Chem., 2012, 20, 1175–1180 CrossRef CAS PubMed;
(b) M.-q. Song, W. Min, J. Wang, X.-X. Si, X.-J. Wang, Y.-W. Liu and D.-H. Shi, J. Mol. Struct., 2021, 1229, 129784 CrossRef CAS;
(c) A. Benazzouz-Touami, A. Chouh, S. Halit, S. Terrachet-Bouaziz, M. Makhloufi-Chebli, K. Ighil-Ahriz and A. M. S. Silve, J. Mol. Struct., 2022, 1249, 131591 CrossRef CAS.
-
(a) H. M. Revankar, S. N. A. Bukhari, G. B. Kumar and H.-L. Qin, Bioorg. Chem., 2017, 71, 146–159 CrossRef CAS PubMed;
(b) D. AL-Duhaidahawi, H. F. S. AL-Zubaidy, K. Al-Khafaji and A. Al-Amiery, J. Mol. Struct., 2022, 1247, 131377 CrossRef CAS.
- M. Roussaki, K. Zelianaios, E. Kavetsou, S. Hamilakis, D. Hadjipavlou-Litina, C. Kontogiorgis, T. Liargkova and A. Detsi, Bioorg. Med. Chem., 2014, 22, 6586–6594 CrossRef CAS PubMed.
- F. Chimenti, D. Secci, A. Bolasco, P. Chimenti, B. Bizzarri, A. Granese, S. Carradori, M. Yáñez, F. Orallo, F. Ortuso and S. Alcaro, J. Med. Chem., 2009, 52, 1935–1942 CrossRef CAS PubMed.
- D. Cao, Y. Liu, W. Yan, C. Wang, P. Bai, T. Wang, M. Tang, X. Wang, Z. Yang, B. Ma, L. Ma, L. Lei, F. Wang, B. Xu, Y. Zhou, T. Yang and L. Chen, J. Med. Chem., 2016, 59, 5721–5739 CrossRef CAS PubMed.
- M. Bozdag, M. Ferraroni, F. Carta, D. Vullo, L. Lucarini, E. Orlandini, A. Rossello, E. Nuti, A. Scozzafava, E. Masini and C. T. Supuran, J. Med. Chem., 2014, 57, 9152–9167 CrossRef CAS PubMed.
-
(a) Q. Shen, J. Shao, Q. Peng, W. Zhang, L. Ma, A. S. C. Chan and L. Gu, J. Med. Chem., 2010, 53, 8252–8259 CrossRef CAS PubMed;
(b) X.-T. Xu, X.-Y. Deng, J. Chen, Q.-M. Liang, K. Zhang, D.-L. Li, P.-P. Wu, X. Zheng, R.-P. Zhou, Z.-Y. Jiang, A.-J. Ma, W.-H. Chen and S.-H. Wang, Eur. J. Med. Chem., 2020, 189, 112013 CrossRef PubMed;
(c) S. Ansari, H. Azizian, K. Pedrood, A. Yavari, S. Mojtabavi, M. A. Faramarzi, S. Golshani, S. Hosseini, M. Biglar, B. Larijani, H. Rastegar, H. Hamedifar, M. Mohammadi-Khanaposhtani and M. Mahdavi, Arch. Pharm., 2021, 354, 2100179 CrossRef CAS PubMed.
- S. Ranatunga, C.-H. A. Tang, C. W. Kang, C. L. Kriss, B. J. Kloppenburg, C.-C. A. Hu and J. R. Del Valle, J. Med. Chem., 2014, 57, 4289–4301 CrossRef CAS PubMed.
- G. Cai, W. Yu, D. Song, W. Zhang, J. Guo, J. Zhu, Y. Ren and L. Kong, Eur. J. Med. Chem., 2019, 174, 236–251 CrossRef CAS PubMed.
- J. Xu, H. Li, X. Wang, J. Huang, S. Li, C. Liu, R. Dong, G. Zhu, C. Duan, F. Jiang, Y. Zhang, Y. Zhu, T. Zhang, Y. Chen, W. Tang and T. Lu, Eur. J. Med. Chem., 2020, 200, 112424 CrossRef CAS PubMed.
- D. Liang, Y. Fan, Z. Yang, Z. Zhang, M. Liu, L. Liu and C. Jiang, Eur. J. Med. Chem., 2020, 187, 111923 CrossRef CAS PubMed.
- C. Bouckaert, S. Serra, G. Rondelet, E. Dolušić, J. Wouters, J.-M. Dogné, R. Frédérick and L. Pochet, Eur. J. Med. Chem., 2016, 110, 181–194 CrossRef CAS PubMed.
- A. Chilin, R. Battistutta, A. Bortolato, G. Cozza, S. Zanatta, G. Poletto, M. Mazzorana, G. Zagotto, E. Uriarte, A. Guiotto, L. A. Pinna, F. Meggio and S. Moro, J. Med. Chem., 2008, 51, 752–759 CrossRef CAS PubMed.
- M. Daśko, M. Przybyłowska, J. Rachon, M. Masłyk, K. Kubiński, M. Misiak and A. Składnowska, Eur. J. Med. Chem., 2017, 128, 79–87 CrossRef PubMed.
- Q. Ji, Z. Ge, Z. Ge, K. Chen, H. Wu, X. Liu, Y. Huang, Y. Lvjiang, X. Yang and F. Liao, Eur. J. Med. Chem., 2016, 108, 166–176 CrossRef CAS.
- G. Li, D. Wang, M. Sun, G. Li, J. Hu, Y. Zhang, Y. Yuan, H. Ji, N. Chen and G. Liu, J. Med. Chem., 2010, 53, 1741–1754 CrossRef CAS PubMed.
-
(a) H. Deng, H. Hu, M. He, J. Hu, W. Niu, A. M. Ferrie and Y. Fang, J. Med. Chem., 2011, 54, 7385–7396 CrossRef CAS PubMed;
(b) L. Wei, T. Hou, J. Li, X. Zhang, H. Zhou, Z. Wang, J. Cheng, K. Xiang, J. Wang, Y. Zhao and X. Liang, J. Med. Chem., 2021, 64, 2634–2647 CrossRef CAS PubMed.
- V. Rempel, N. Volz, F. Gläser, M. Nieger, S. Bräse and C. E. Müller, J. Med. Chem., 2013, 56, 4798–4810 CrossRef CAS PubMed.
- M. J. Matos, S. Vilar, S. Vasquez-Rodriguez, S. Kachler, K.-N. Klotz, M. Buccioni, G. Delogu, L. Santana, E. Uriarte and F. Borges, J. Med. Chem., 2020, 63, 2577–2587 CrossRef CAS PubMed.
-
(a) A. Dömling, W. Wang and K. Wang, Chem. Rev., 2012, 112, 3083–3135 CrossRef PubMed;
(b) S. Abu-Melha, Z. A. Muhammad, A. S. Abouzid, M. M. Edrees, A. S. Abo Dena, S. Nabil and S. M. Gomha, J. Mol. Struct., 2021, 1234, 130180 CrossRef CAS;
(c) H. G. O. Alvim, E. N. da Silva Júnior and B. A. D. Neto, RSC Adv., 2014, 4, 54282–54299 RSC;
(d) S. Kamalifar and H. Kiyani, Res. Chem. Intermed., 2019, 45, 5975–5987 CrossRef CAS;
(e) L. Wu, S. Yan, W. Wang and Y. Li, Res. Chem. Intermed., 2020, 46, 4311–4322 CrossRef CAS;
(f) A. Patil, S. Shinde, G. Rashinkar and R. Salunkhe, Res. Chem. Intermed., 2020, 46, 63–73 CrossRef CAS;
(g) S. Zhi, X. Ma and W. Zhang, Org. Biomol. Chem., 2019, 17, 7632–7650 RSC;
(h) N. Nikooei, M. G. Dekamin and E. Valiey, Res. Chem. Intermed., 2020, 46, 3891–3909 CrossRef CAS;
(i) M. Rimaz and H. Mousavi, Turk. J. Chem., 2013, 37, 252–261 CAS;
(j) M. Rimaz, H. Mousavi, L. Ozzar and B. Khalili, Res. Chem. Intermed., 2019, 45, 2673–2694 CrossRef CAS;
(k) M. Rimaz, H. Mousavi, B. Khalili and L. Sarvari, J. Iran. Chem. Soc., 2019, 16, 1687–1701 CrossRef CAS;
(l) M. Rimaz, B. Khalili, G. Khatyal, H. Mousavi and F. Aali, Aust. J. Chem., 2017, 70, 1274–1284 CrossRef CAS;
(m) M. Rimaz, H. Mousavi, M. Behnam, L. Sarvari and B. Khalili, Curr. Chem. Lett., 2017, 6, 55–68 CrossRef;
(n) M. Rimaz, H. Mousavi, L. Nikpey and B. Khalili, Res. Chem. Intermed., 2017, 43, 3925–3937 CrossRef CAS;
(o) M. Rimaz, H. Mousavi, P. Keshavarz and B. Khalili, Curr. Chem. Lett., 2015, 4, 159–168 CrossRef;
(p) P. Mane, B. Shinde, P. Mundada, B. Karale and A. Burungale, Res. Chem. Intermed., 2021, 47, 1743–1758 CrossRef CAS;
(q) I. Yellapurkar, S. Bhabal, M. M. V. Ramana, K. Jangam, V. Salve, S. Patange and P. More, Res. Chem. Intermed., 2021, 47, 2669–2687 CrossRef CAS;
(r) R. L. Mohlala, E. M. Coyanis, M. A. Fernandes and M. L. Bode, RSC Adv., 2021, 11, 24466–24473 RSC;
(s) F. Haji Norouzi, N. Foroughifar, A. Khajeh-Amiri and H. Pasdar, RSC Adv., 2021, 11, 29948–29959 RSC;
(t) B. M. Bizzarri, A. Fanelli, L. Botta, M. De Angelis, A. T. Palamara, L. Nencioni and R. Saladino, RSC Adv., 2021, 11, 30020–30029 RSC;
(u) Z. Ghanbari and H. Naeimi, RSC Adv., 2021, 11, 31377–31384 RSC;
(v) P. Ghamari Kargar, G. Bagherzade and H. Eshghi, RSC Adv., 2021, 11, 4339–4355 RSC;
(w) P. Ghamari Kargar and G. Bagherzade, RSC Adv., 2021, 11, 23192–23206 RSC;
(x) P. Ghamari Kargar, M. Noorian, E. Chamani, G. Bagherzade and Z. Kiani, RSC Adv., 2021, 11, 17413–17430 RSC;
(y) S. Khajeh Dangolian, E. Niknam, O. Shahraki and A. Khalafi-Nezhad, J. Mol. Struct., 2021, 1245, 131061 CrossRef;
(z) F. Kamali and F. Shirini, J. Mol. Struct., 2021, 1227, 129654 CrossRef CAS.
-
(a) H. Mousavi, B. Zeynizadeh, R. Younesi and M. Esmati, Aust. J. Chem., 2018, 71, 595–660 CrossRef CAS;
(b) B. Zeynizadeh, R. Younesi and H. Mousavi, Res. Chem. Intermed., 2018, 44, 7331–7352 CrossRef CAS;
(c) B. Zeynizadeh, F. Mohammad Aminzadeh and H. Mousavi, Res. Chem. Intermed., 2019, 45, 3329–3357 CrossRef CAS;
(d) B. Zeynizadeh, H. Mousavi and S. Zarrin, J. Chin. Chem. Soc., 2019, 66, 928–933 CrossRef CAS;
(e) B. Zeynizadeh, F. Mohammad Aminzadeh and H. Mousavi, Green Process. Synth., 2019, 8, 742–755 CAS;
(f) B. Zeynizadeh, F. Sepehraddin and H. Mousavi, Ind. Eng. Chem. Res., 2019, 58, 16379–16388 CrossRef CAS;
(g) R. Bakhshi, B. Zeinizadeh and H. Mousavi, J. Chin. Chem. Soc., 2020, 67, 623–637 CrossRef CAS;
(h) B. Zeynizadeh, H. Mousavi and F. Sepehraddin, Res. Chem. Intermed., 2020, 46, 3361–3382 CrossRef CAS;
(i) B. Zeynizadeh, F. Mohammad Aminzadeh and H. Mousavi, Res. Chem. Intermed., 2021, 47, 3289–3312 CrossRef CAS;
(j) B. Zeynizadeh, H. Mousavi and F. Mohammad Aminzadeh, J. Mol. Struct., 2022, 1255, 131926 CrossRef CAS.
- X. Li, W. She, J. Wang, W. Li and G. Li, Appl. Organomet. Chem., 2021, 35, e6294 CAS.
- J. Shabir, C. Garkoti, P. Gupta, M. Sharma, S. Rani, M. Kumari and S. Mozumdar, ACS Omega, 2021, 6, 1415–1425 CrossRef CAS PubMed.
- C. Sharma, A. K. Srivastava, A. Soni, S. Kumari and R. K. Joshi, RSC Adv., 2020, 10, 32516–32521 RSC.
- J. Du, J. Chen, H. Xia, Y. Zhao, F. Wang, H. Liu, W. Zhou and B. Wang, ChemCatChem, 2020, 12, 2426–2430 CrossRef CAS.
- M. Gholinejad, E. Oftadeh, M. Shojafar, J. M. sansano and B. H. Lipshutz, ChemSusChem, 2019, 12, 4240–4248 CrossRef CAS PubMed.
- V. S. Sypu, M. Bhaumik, K. Raju and A. Maity, J. Colloid Interface Sci., 2021, 581, 979–989 CrossRef CAS PubMed.
- Y. Li, W. Jiang, G. Ma and M. M. Zanganeh, Int. J. Bio. Macromol., 2020, 163, 2162–2171 CrossRef CAS PubMed.
- M. Kaur, C. Sharma, N. Sharma, B. Jawal and S. Paul, ACS Appl. Nano Mater., 2020, 3, 10310–10325 CrossRef CAS.
- S. Yang, Z.-H. Zhang, Q. Chen, M.-Y. He and L. Wang, Appl. Organomet. Chem., 2018, 32, e4132 CrossRef.
- F. M. Moghaddam, V. Saberi and P. Kalvani, ChemistrySelect, 2018, 3, 6779–6785 CrossRef CAS.
- M. Pashaei and E. Mehdipour, Appl. Organomet. Chem., 2018, 32, e4226 CrossRef.
- B. Zeynizadeh, S. Rahmani and H. Tizhoush, Polyhedron, 2020, 175, 114201 CrossRef.
- M. Gilanizadeh and B. Zeynizadeh, J. Iran. Chem. Soc., 2018, 15, 2831–2837 Search PubMed.
- M. Piri, M. M. Heravi, A. Elhampour and F. Nemati, J. Mol. Struct., 2021, 1242, 130646 CrossRef CAS.
- Z. Shokri, B. Zeynizadeh and S. A. Hosseini, J. Colloid Interface Sci., 2017, 485, 99–105 CrossRef CAS PubMed.
- V. Bilakanti, N. Gutta, V. K. Velisoju, M. Dumpalapally, S. Inkollu, N. Nama and V. Akula, React. Kinet., Mech. Catal., 2020, 130, 347–362 CrossRef CAS.
- B. Zeynizadeh, Z. Shokri and I. Mohammadzadeh, J. Iran. Chem. Soc., 2020, 17, 859–870 CrossRef CAS.
- B. Akhlaghinia, P. Sanati, A. Mohammadinezhad and Z. Zarei, Res. Chem. Intermed., 2019, 45, 3215–3235 CrossRef CAS.
- C. Patil, S. K. Shinde, U. P. Patil, A. T. Birajdar and S. S. A. Patil, Res. Chem. Intermed., 2021, 47, 1675–1691 CrossRef.
- S. Rahmani and B. Zeynizadeh, Res. Chem. Intermed., 2019, 45, 1227–1248 CrossRef CAS.
- D. K. Agarwal, A. Sethiya, P. Teli, A. Manhas, J. Sani, N. Sahiba, P. C. Jha, S. Agarwal and P. K. Goyal, J. Heterocycl. Chem., 2020, 57, 3294–3309 CAS.
- F. Shirini, A. Fallah-Shojaei, L. Samavi and M. A. Abedini, RSC Adv., 2016, 6, 48469–48478 RSC.
- M. Seddighi, F. Shirini and M. Mamaghani, RSC Adv., 2013, 3, 24046–24053 RSC.
- X. Wu and W.-X. Peng, J. Chin. Chem. Soc., 2020, 67, 2129–2148 CrossRef CAS.
- N. O. Mahmoodi, Z. Jalalifard and G. Pirbasti Fathanbari, J. Chin. Chem. Soc., 2020, 67, 172–182 CrossRef CAS.
- R. Teimuri-Mofrad, S. Tahmasebi and E. Payami, Appl. Organomet. Chem., 2019, 33, e4773 CrossRef.
- S. Mathavan, K. Kannan and R. B. R. D. Yamajala, Org. Biomol. Chem., 2019, 17, 9620–9626 RSC.
- E. El hajri, Z. Benzekri, S. Sibous, A. Ouasri, S. Boukhris, A. Hassikou, A. Rhandour and A. Souizi, J. Mol. Struct., 2021, 1230, 129890 CrossRef.
- R. Pourhasan-Kisomi, F. Shirini and M. Golshekan, Appl. Organomet. Chem., 2018, 32, e4371 CrossRef.
- M. Ziyaadini, N. Nemat-Bakhsh, S. J. Roudbaraki and M. Ghashang, Polycyclic Aromat. Compd., 2022, 42, 460–474 CrossRef CAS.
- M. M. Khodaei, A. Alizadeh and M. A. Haghipour, Res. Chem. Intermed., 2020, 46, 1033–1045 CrossRef CAS.
- S. Abdolahi, M. Hajjami and F. Gholamian, Res. Chem. Intermed., 2021, 47, 1883–1904 CrossRef CAS.
- S. Amirnejat, A. Nosrati, R. Peymanfar and S. Javanshir, Res. Chem. Intermed., 2020, 46, 3683–3701 CrossRef CAS.
- H. Foroughi Niya, N. Hazeri, M. Rezaie Kahkhaie and M. T. Maghsoodlou, Res. Chem. Intermed., 2020, 46, 1685–1704 CrossRef.
- F. Hasaanzadeh, N. Daneshvar, F. Shirini and M. Mamaghani, Res. Chem. Intermed., 2020, 46, 4971–4984 CrossRef.
- A. Mahajan and M. Gupta, Appl. Organomet. Chem., 2021, 35, e6161 CrossRef CAS.
- P. Mohammadi and H. Sheibani, Mater. Chem. Phys., 2019, 228, 140–146 CrossRef CAS.
- M. Khaleghi Abbasabadi, D. Azarifar and H. R. Esmaili Zand, Appl. Organomet. Chem., 2020, 34, e6004 CAS.
Footnote |
† Electronic supplementary information (ESI) available. See DOI: 10.1039/d1ra08763k |
|
This journal is © The Royal Society of Chemistry 2022 |
Click here to see how this site uses Cookies. View our privacy policy here.